Muller Elektronik ISOBUS TRAIL-Control User manual

Operators Manual
ISOBUS TRAIL-Control
Version: V2.20160912
30322332-02-EN
Read and follow these operating instructions.
Keep these operating instructions in a safe place for later
reference.

Company details
Operators Manual
Product: ISOBUS TRAIL-Control
Document number: 30322332-02-EN
As of software version: 2x7g
Original language: German
Müller-Elektronik GmbH & Co.KG
Franz-Kleine-Straße 18
33154 Salzkotten
Germany
Phone: ++49 (0) 5258 / 9834 - 0
Fax: ++49 (0) 5258 / 9834 - 90
Email: info@mueller-elektronik.de
Homepage: http://www.mueller-elektronik.de
Document
Copyright ©

Table of contents
30322332-02-EN
V2.20160912
3
Table of contents
1
For your safety
5
1.1
Basic safety instructions
5
1.2
Hazard Area
5
1.3
User requirements
6
1.4
Layout and meaning of warnings
6
2
About these Operating Instructions
7
2.1
Diagrams in this manual
7
2.2
Directional information in these instructions
7
2.3
Layout of references
7
2.4
Layout of operating instructions
7
3
Product description
9
3.1
Functions of the ISOBUS-TRAIL-Control system
9
3.2
System Overview
10
3.3
Layout of the work screen
10
3.4
Rating plate
12
4
Mounting and installation
14
4.1
Mounting the gyroscope
14
4.1.1
Mounting the bracket for the gyroscope
14
4.1.2
Using the gyroscope
15
4.2
Checking the installation position of sensors
15
5
Operating the system
17
5.1
Switching TRAIL-Control on and off
17
5.2
Steering in automatic mode
18
5.3
Steering in manual mode
18
5.4
Driving in reverse
19
5.5
Steering the trailer device against the slope
19
5.6
Preparing TRAIL-Control for road driving
21
5.7
Locking TRAIL-Control
21
5.8
Using the joystick
22
6
Configuring TRAIL-Control
23
6.1
When should you configure what?
23
6.2
Adjusting the configuration to the tractor
23
6.3
Calibrating TRAIL-Control
26
6.3.1
Teaching-in the central position and limit stops
26
6.3.2
Calibrating the hydraulics of the proportional valve
28
6.4
Configuring the speed sensor
29
6.4.1
Calibrating the wheel sensor
29

Table of contents
4
V2.20160912
30322332-02-EN
6.4.2
Determining the pulses per 100 meters
30
6.4.3
Using other speed sensors
31
6.4.4
Configuring the reverse driving sensor
31
6.5
Configuring the automatic centering
31
6.5.1
Centering when exceeding the maximum speed
32
6.5.2
Centering when switching to manual mode
32
6.5.3
Centering when tapping the centering icon
33
6.6
Configuring automatisms when driving in reverse
33
6.6.1
Reaction to the reverse driving signal in manual mode
34
6.6.2
Reaction to the reverse driving signal in automatic mode
34
7
Technical specifications
35
7.1
Technical data for the job computer
35

For your safety
Basic safety instructions
1
30322332-02-EN
V2.20160912
5
For your safety
Basic safety instructions
Please read the following safety instructions carefully before using the product for the first time.
▪TRAIL-Control may only be used during field work. The system must be deactivated or switched
off on public roads and tracks.
▪Before you leave the vehicle cab, ensure that all automatic mechanisms are deactivated or
manual mode is activated.
▪Nobody must stay in the proximity of the tractor or trailed implement during operation.
▪Never remove any safety mechanisms or stickers from the product.
▪Read the operating instructions to the agricultural device which you want to control by using the
product.
▪Before charging the tractor battery, always disconnect the tractor from the job computer.
▪Before performing any welding on the tractor or the implement, always disconnect the power
supply to the job computer.
▪Before performing maintenance or repairs on the tractor, always disconnect the job computer
from the tractor.
▪Do not make any unauthorized modifications to the product. Unauthorized modifications or use
may impair safety and reduce the service life or operability of the unit. Modifications are
considered unauthorized if they are not described in the product documentation.
▪Keep children away from the implement and from the job computer.
Hazard Area
The hazard area covers several meters surrounding the tractor and the trailed implement in all
directions. The bigger the trailed implement, the bigger the hazard area. For example: The greater
the width of a spraying boom on a field sprayer, the greater the range when it is unfolded, and the
larger the hazard area.
WARNING
Risk of injury due to uncontrolled movements of the implement
◦Ensure that nobody enters the hazard area.
◦Switch the system off immediately as soon as someone enters the hazard area.
As soon as you have installed and switched on the system, ensure that nobody is in the hazard area.
When TRAIL-Control is switched on, there is a risk of uncontrolled movement of the drawbar or stud
axle caused by pressure fluctuations in the hydraulic system.
For example, pressure fluctuations can occur in the following situations:
▪If there is a failure in the hydraulic system.
▪If you use the hydraulic system for purposes other than controlling the drawbar and stud axle
steering.
The hazard area may only be entered if the following requirements are met:
▪System is switched off.
All maintenance, configuration, and inspection work is performed with the system switched off.
1
1.1
1.2

1
For your safety
User requirements
6
V2.20160912
30322332-02-EN
User requirements
▪Learn to operate the product in accordance with the instructions. Nobody must operate the
product before reading these Operating Instructions.
▪Please read and carefully observe all safety instructions and warnings contained in these
Operating Instructions and in the manuals of any connected vehicles and farm equipment.
▪If there is anything within these Operating Instructions that you do not understand, please do not
hesitate to contact us or your dealer. Müller-Elektronik's Customer Services department will be
happy to assist you.
Layout and meaning of warnings
All safety instructions found in these Operating Instructions are composed in accordance with the
following pattern:
WARNING
This signal word identifies medium-risk hazards, which could potentially cause death or serious
physical injury, if not avoided.
CAUTION
This signal word identifies hazards that could potentially cause minor or moderate physical injury or
damage to property, if not avoided.
NOTICE
This signal word identifies hazards that could potentially cause damage to property, if not avoided.
There are some actions that need to be performed in several steps. If there is a risk involved in
carrying out any of these steps, a safety warning will appear in the instructions themselves.
Safety instructions always directly precede the step involving risk and can be identified by their bold
font type and a signal word.
1. NOTICE! This is a notice.It warns that there is a risk involved in the next step.
2. Step involving risk.
1.3
1.4
Example

About these Operating Instructions
Diagrams in this manual
2
30322332-02-EN
V2.20160912
7
About these Operating Instructions
Diagrams in this manual
The screen shots of the software interface are intended to serve as a reference. They help you in
finding your way around the software screens.
The information shown on the screen depends on various factors:
▪the type of implement,
▪the configuration of the implement,
▪the status of the sensors and actuators.
For this reason, the pictures in these operating instructions may show different information than the
display on the terminal.
All screen shots used in this manual were made on a COMFORT-Terminal provided by Müller-
Elektronik. On other ISOBUS terminals, the layout of the function icons may be different, since every
ISOBUS terminal determines its own layout.
Several icons look different depending on whether the trailed implement has drawbar or stub axle
steering. They still both have the same function.
In the manual, we use the icons depicting a drawbar. For each of these icons, there is a
corresponding icon depicting an axle with wheels. You can find an overview in the table: Layout of the
work screen [➙11]
Directional information in these instructions
All directional information in these instructions, such as "left", "right", "forward", "back", is relative to
the movement direction of the vehicle.
Layout of references
If any references are given in these Operating Instructions, they will appear as:
Example of a reference: [➙7]
References can be identified by their square brackets and an arrow. The number following the arrow
shows you on what page the section starts where you can find further information.
Layout of operating instructions
The operating instructions explain step by step how you can perform certain operations with the
product.
We use the following symbols throughout these Operating Instructions to identify different operating
instructions:
Type of depiction
Meaning
1.
2.
Actions that must be performed in succession.
⇨
Result of the action.
2
2.1
2.2
2.3
2.4

2
About these Operating Instructions
Layout of operating instructions
8
V2.20160912
30322332-02-EN
Type of depiction
Meaning
This will happen when you perform an action.
⇨
Result of an operating instruction.
This will happen when you have completed all
steps.
Requirements.
In the event that any requirements have been
specified, these must be met before an action
can be performed.

Product description
Functions of the ISOBUS-TRAIL-Control system
3
30322332-02-EN
V2.20160912
9
Product description
Functions of the ISOBUS-TRAIL-Control system
ISOBUS-TRAIL-Control serves to steer the trailed implement during field operation. In doing so, it
supports the driver in the following ways:
▪It keeps the trailed implement in the tractor track.
▪When working on slopes, it steers the trailed implement up the slope so that it does not slip out
of the tractor track.
The system can control two types of steering systems:
▪Drawbar steering - These systems only steer the drawbar to the left or right to influence the
course of the trailed implement.
▪Stub axle steering - These systems steer the steering axle of the trailed implement to the left or
right to influence the course of the trailed implement.
The following requirements must be met for TRAIL-Control to work:
▪Minimum speed = 3 km/h. Steering is not possible at lower speeds.
▪(Default) Maximum speed = 15 km/h. If you drive faster than 15 km/h, the TRAIL-Control function
will be automatically switched off.
Note: The implement manufacturer is capable of increasing or decreasing the maximum speed
before delivering the field sprayer to adjust it for the characteristics of the field sprayer and its
intended use.
▪The maximum speed can be adjusted for the trailed implement and increased by the implement
manufacturer.
▪Minimum oil throughput for the hydraulic system of the tractor = 25 l/min. The minimum oil
throughput may be greater for large field sprayers.
3
3.1
Functions
Versions
Preconditions

3
Product description
System Overview
10
V2.20160912
30322332-02-EN
System Overview
Example for a system with drawbar steering
Main cable harness
Ladder sensor*
The ladder sensor serves to detect whether a ladder has been extended on the trailed implement. In
this case, TRAIL-Control is blocked and cannot be activated.
Proportional valve
Angle sensor
Determines the angle of a hydraulic cylinder on the drawbar or on a stub axle.
For systems with stub axle steering, this sensor is installed on a stub axle.
Drawbar locking sensor*
Sensor that detects when the drawbar has been locked with a pin.
Gyroscope with two brackets
Detects changes in the driving direction of the tractor.
ISOBUS cable with plug
Cable from the ISOBUS job computer to the ISOBUS socket on the tractor.
ISOBUS job computer
Control unit that is responsible for system operation.
"Boom unfolded" position sensor*
Sensor that detects when the boom has been unfolded and is ready for field work. This is mandatory
for using TRAIL-Control. The system is locked when the boom is folded in.
Sprayer slope sensor
Sensor that detects the tilt of the trailed implement to enable the slope counter-steering function.
Wheel sensor*
Serves to determine the vehicle speed.
* - Optional sensors. Because there is a limited number of sensor inputs, not all of the optional
sensors can be installed and used on the implement.
Layout of the work screen
The work screen is the screen that should be called up after activating the system.
This screen allows you to:
3.2
3.3

Product description
Layout of the work screen
3
30322332-02-EN
V2.20160912
11
▪see the status of the system,
▪operate the system using function icons.
Work screen when the implement is standing still. Left: System with drawbar steering; Right: System with stub
axle steering
Current speed
Icon: manual mode is activated
Animation of the steering angle
Scale of the deflection
Icon: Slope counter-steering is activated
Icon: The boom is in transport position.
Automatic mode is not possible.
Work screen when steering in automatic mode: The tractor drives to the right, the trailed implement is steered to
the left.
By looking at the displayed position of the drawbar / stub axle, you can see whether the trailed
implement is being steered.
The arrow shows the direction in which the trailed implement is being steered.
The deflection is also shown on a scale.
Beside the work screen, there are function icons that serve to operate the system.
Function icon for
drawbar steering
Function icon for
axle steering
Meaning
Activates and deactivates the system.
Activates and deactivates the automatic mode.
Steers the implement to the left.
Steers the implement to the right.
Function icons

3
Product description
Rating plate
12
V2.20160912
30322332-02-EN
Function icon for
drawbar steering
Function icon for
axle steering
Meaning
Centers the implement.
Activates the slope counter-steering function.
Calls up the screens with settings.
Possible icons
Icon
Meaning
Slope counter-steering function is active.
Shows the direction in which the trailed implement is being steered.
Manual mode is activated
The boom is folded for driving on roads. Automatic mode is not possible.
A locking device is activated: Drawbar locking device or ladder sensor. TRAIL-
Control is locked. The hydraulic valve is not being controlled.
Reverse driving signal has been detected.
If the TANK-Control system is connected to the TRAIL-Control system, the
current tank content appears on the work screen.
Rating plate
Abbreviations on the rating plate
Abbreviation
Meaning
Customer number
If the product was manufactured for an agricultural machinery
manufacturer, the agricultural machinery manufacturer's item number
will be shown here.
Hardware version
3.4

Product description
Rating plate
3
30322332-02-EN
V2.20160912
13
Abbreviation
Meaning
Müller-Elektronik item number
Operating voltage
The product may only be connected to voltages within this range.
Software version
Serial number

4
Mounting and installation
Mounting the gyroscope
14
V2.20160912
30322332-02-EN
Mounting and installation
Mounting the gyroscope
The gyroscope is a sensor that determines the angular speed when the tractor changes direction.
To mount the gyroscope you must carry out the following:
▪Mount the bracket on the tractor.
Mounting the bracket for the gyroscope
Bracket
Gyroscope in the bracket
Mounting the bracket on the tractor
The bracket on the tractor is used for fastening the gyroscope to the tractor for the duration of work in
the field.
1. Determine the position for mounting the bracket on the tractor.
The bracket must be mounted vertically and without vibration on the rear of the tractor.
Make sure that the connection cable of the gyroscope does not become too tight when fastened
in the bracket.
2. CAUTION! Before drilling a hole, make sure that for drilling you are not going to damage
any cables.
3. Drill the holes for the screws.
4. Fasten the bracket.
The bracket must be fastened securely to prevent shaking while driving.
4
4.1
4.1.1
Procedure

Mounting and installation
Checking the installation position of sensors
4
30322332-02-EN
V2.20160912
15
Using the gyroscope
1. Fasten the gyroscope into the bracket on the tractor and screw tight with the wing screw.
The side with the TOP-OBEN label must be on the top:
2. After work, fasten the gyroscope into the bracket on the trailed implement and screw tight with
the wing screw.
Checking the installation position of sensors
The system is capable of measuring the voltage on the sensor input of the job computer and
displaying it on the screen.
This allows you to check whether selected sensors are properly installed.
Sensor voltages
Sensor type
Position during measurement
Correct voltage
Angle sensor
Center position: The drawbar (or wheels of the trailed
implement) is (are) aligned to drive straight ahead.
2.5V
(+/- 0.1V)
Voltages when the trailed implement is steered to the
maximum left or right.
Approx. 1.5V and
3.5V
(+/- 0.1V)
Short circuit:
0.1V
Slope sensor
The trailed implement is standing on level ground.
2.5V (+/- 0.1V)
Gyroscope
Sensor is in the bracket on the tractor. The tractor is at a
standstill.
2.5V (+/- 0.1V)
This allows you to check whether the sensors are properly installed:
The diagnostic function was activated during the initial configuration.
Start screen is called up.
4.1.2
Procedure
4.2
Procedure

4
Mounting and installation
Checking the installation position of sensors
16
V2.20160912
30322332-02-EN
1. Switch to the "TRAIL Control" screen:
⇨The "TRAIL Control" screen appears:
⇨The voltages appear in the bottom half of the screen.
⇨For the speed sensor, the number of pulses / second (hertz) is displayed.

Operating the system
Switching TRAIL-Control on and off
5
30322332-02-EN
V2.20160912
17
Operating the system
Switching TRAIL-Control on and off
WARNING
Moving implement
Before you switch on the system, make sure that there are no persons or objects nearby.
To switch on the system:
The vehicle is standing on the field.
There are no persons close to the vehicle.
The boom is unfolded. The "Boom unfolded" sensor (if the sensor is installed) is activated.
The drawbar is not mechanically locked.
The ladder is not extended or unfolded. (If the ladder sensor is installed).
1. Fasten the gyroscope onto the tractor.
2. Connect the ISOBUS cable of the job computer to the ISOBUS socket of the tractor.
3. Start the terminal.
4. In the terminal selection menu, open the application:
⇨The work screen appears.
⇨On systems with drawbar steering:
⇨On systems with stub axle steering:
⇨Only the current speed appears on the screen. The system is not yet activated.
5
5.1
Procedure

5
Operating the system
Steering in automatic mode
18
V2.20160912
30322332-02-EN
5. or - Switch on TRAIL-Control. By pressing again, you can switch off
the system.
⇨The system is switched on, however, it is only working in manual mode. This means that
you must actuate a function icon to steer the trailed implement. [➙18]
⇨New icons appear on the work screen [➙10].
⇨On systems with drawbar steering:
⇨On systems with stub axle steering:
You can now read the following chapter:
▪To obtain more information on the icons on the screen: Layout of the work screen [➙10]
▪If you still have to configure the system: Configuring TRAIL-Control [➙23]
▪If the system has already been configured:
–Steering in automatic mode [➙18]
–Steering in manual mode [➙18]
Steering in automatic mode
When you work in automatic mode, the trailed implement is steered automatically.
The gyroscope measures the change in direction of the tractor and the job computer calculates the
required angle for steering the trailed implement.
The icons on the work screen show the direction in which the trailed implement is being steered.
Steering in manual mode
In manual mode, you must steer the trailed implement manually.
Drive in a curve to the right as follows:
5.2
5.3
Procedure

Operating the system
Driving in reverse
5
30322332-02-EN
V2.20160912
19
1. Drive the tractor to the right
2. / - Steer the trailed implement for driving to the right.
⇨With drawbar steering: The drawbar is steered to the left.
⇨With axle steering: The wheels are steered to the left.
⇨An arrow pointing left appears on the work screen:
To drive straight ahead again:
1. Drive the tractor straight ahead.
2. / - Steer the trailed implement to the middle position.
⇨The trailed implement slowly moves to the middle position.
⇨An arrow appears on the work screen. It shows the direction in which the drawbar or axle is
steering.
Drive in a curve to the left as follows:
1. Drive the tractor to the left
2. / - Steer the trailed implement for driving to the left
⇨With drawbar steering: The drawbar is steered to the right.
⇨With axle steering: The wheels are steered to the right.
⇨An arrow pointing right appears on the work screen:
Driving in reverse
The operation of the trailed implement when driving in reverse depends on several factors:
▪If no reverse driving signal [➙31] is available, you can deactivate TRAIL-Control or set it to
manual mode before driving in reverse.
▪As a standard, TRAIL-Control stops working if a reverse driving signal is detected. In this case,
the automatic mode remains activated, but the hydraulic valves are not being controlled.
▪You can configure the reaction for TRAIL-Control when a reverse driving signal is detected. To
do so, read section: Configuring automatisms when driving in reverse [➙33]
When a reverse driving signal is detected, a flashing icon always appears on the work screen.
Steering the trailer device against the slope
For working on slopes, you can use the 'slope counter-steering' function.
When you activate the 'slope counter-steering' function, you can offset the track of the trailed
implement to the left or right. The direction in which the track is offset depends on if the slope climbs
or declines to the left or right of the implement.
The aim of the "slope counter-steering" function is to prevent the trailed implement from driving
inclined to the direction of work on a slope.
Procedure
Procedure
5.4
5.5
Mode of operation

5
Operating the system
Steering the trailer device against the slope
20
V2.20160912
30322332-02-EN
Steering the trailed implement against the slope. The trailed implement is pulled down by gravity because it is
standing on a slope.
Without TRAIL-Control
TRAIL-Control with stub axle steering
TRAIL-Control with drawbar steering
In manual mode, you steer the trailed implement manually.
In automatic mode, the trailed implement should be automatically steered to the correct position.
However, this depends on several factors:
▪on the slope inclination,
▪on the weight of the trailed implement,
▪on the type and condition of the ground.
For this reason, in automatic mode you first have to manually adjust the correct position for each
slope. Afterwards, it will be automatically maintained by the system.
To steer against the slope in automatic mode:
The trailed implement is equipped with a slope sensor.
Automatic mode is activated.
Slope counter-steering function is active.
The vehicle with the trailed implement is moving on the slope.
1. , or , - Manually steer the trailed implement
to the correct position behind the tractor.
⇨On the scale on the work screen, a thin line appears marking the target position:
⇨The line moves each time you actuate the function icons.
⇨TRAIL-Control will try to steer the trailed implement into this position, until you correct the
position manually again.
2. After turning, when the slope lies on the other side of the trailed implement, the angle will be
reproduced on the other side.
Manual mode
Automatic mode
Procedure
Table of contents
Other Muller Elektronik Controllers manuals
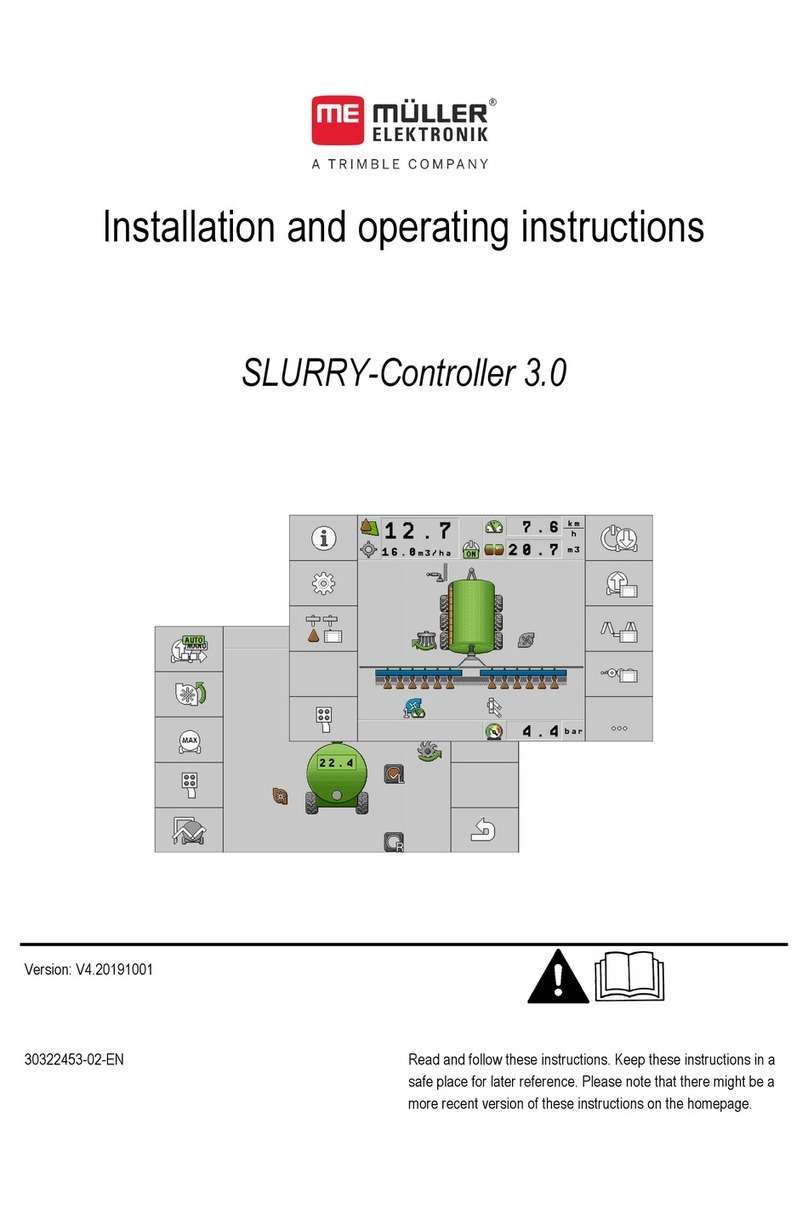
Muller Elektronik
Muller Elektronik SLURRY-Controller 3.0 User manual
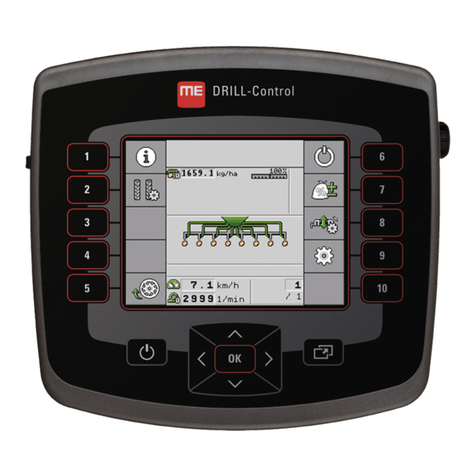
Muller Elektronik
Muller Elektronik DRILL-Control User manual

Muller Elektronik
Muller Elektronik SPRAYER-Controller Orchard/Vineyard MIDI 3.0 User manual
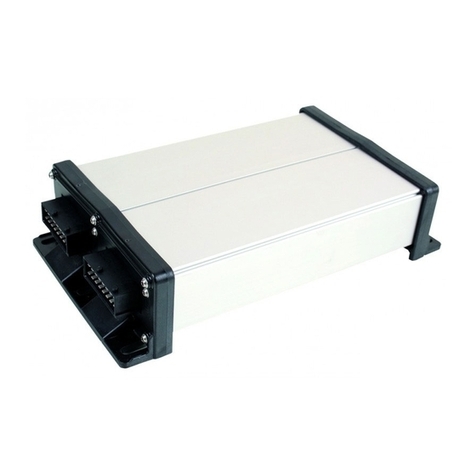
Muller Elektronik
Muller Elektronik SPRAYER-Controller Orchard/Vineyard MIDI 3.0 User manual