NANO NDL-2110 Manual

Maintenance & Service Manual
heatless desiccant air dryer
revision: 2021-224 document: 17-100-0141
www.n-psi.co.uk

Page 2
GENERAL INFORMATION
Copyright
This manual is copyrighted, all rights reserved. It may not, in whole or in part, be copied, photocopied, reproduced,
translated, or reduced to any electronic medium or machine readable form without prior consent in writing from nano
purification solutions limited. It may not be distributed through the internet or computer bulletin board systems without
prior consent from nano-purification solutions limited.
©2021 nano purification solutions limited
Heatless Desiccant Air Dryer: D-Series3 Service Manual
Models: NDL-2110, 2120,2130, 3130, 4130, 6120, 6130 (Including ES Model)
Document number: 17-100-0141
Issue: 001
Document Introduction
This manual provides manufacturers prescribed procedures for the maintenance and service procedures for a nano
purification solutions limited compressed air dryer. The procedures illustrated in this document are only to be performed
by authorised personnel. For further information regarding the procedures outlined in this document contact nano
purification solutions limited before proceeding. Read this document carefully before attempting to service the dryer.
General Safety
For your own safety, when carrying out maintenance work on the dryer, all relevant national safety regulations must be
complied with relating to pressurised and electrical systems. Only authorised, competent and trained personnel should
maintain the dryer. This user guide is intended solely for such personnel and is to be used only as a reference, it should
not be used to replace conventional training.
CAUTIONS: indicate any situation or operation that may result in potential damage to the product, injury to
the user, or render the product unsafe.
NOTES: highlight important sections of information where particular care and attention should be paid.
Warranty Guidelines
All dryers are supplied with a 2 year manufacturer’s warranty from the date of purchase. The dryer should be installed,
operated and maintained in accordance with the manufacturer’s guidelines. Only genuine service parts should be used
and no modifications made. For further information please refer to the ‘warranty guidelines’ section on our website:
www.n-psl.com

Page 3
MANUFACTURERS DETAILS AND SUPPORT
nano-puricaon soluons ltd. (Manufacturer)
address: Dukesway
Team Valley Trading Estate Gateshead
NE11 0PZ
United Kingdom
telephone: +44 (0) 191 497 7700
internet: www.n-psi.co.uk
email: [email protected]
usa - nano-puricaon soluons inc.
address: 5509 David Cox Road
Charlotte, NC 28269
USA
telephone: +1 (704) 897-2182
internet: www.n-psi.com
email [email protected]
canada - nano-puricaon soluons inc.
address 7 Petrie Street
St. Catharines,
Ontario
L2P 3J6
Canada
telephone: +1 (905) 684-626
internet: www.n-psi.com
email: [email protected]
germany - nano-puricaon soluons inc.
Mommenpesch, 46
D-47839 Krefeld
Germany
telephone: +49 2151 4828 418
internet: www.n-psi.de
email: [email protected]
CONTENTS
1. SERVICE INTERVALS 4
1.1 SERVICE KITS 5
2. PRODUCT ASSEMBLY 7
3. RECOMMENDED TOOLS 8
4. DRYER SHUT DOWN PROCEDURE 8
4.1 DRYER START-UP PROCEDURE 8
5 SERVICE ‘A’ INSTRUCTIONS - Silencers/Mufflers 9
6. SERVICE ‘B’ INSTRUCTIONS - Desiccantchange 10
6.1 SERVICE ‘C’ INSTRUCTIONS - Exhaust valves 12
6.2 SERVICE ‘C’ INSTRUCTIONS - Outlet valves 13
6.3 SERVICE ‘C’ INSTRUCTIONS - Inlet valve 14
6.4 SERVICE ‘C’ INSTRUCTIONS - Pilot valves 15
7. SERVICE ‘D’ INSTRUCTIONS - Dew point sensor 16
8. RE-SETTING THE DRYER 18
9. TOP & BOTTOM MANIFOLD TIGHTENING SEQUENCES 19
10. OTHER DRYER CHECKS & NON-SERVICEABLE ITEMS 21
11. TROUBLESHOOTING 22
12. SERVICE RECORD & NOTES 23
13. NOTES 24

Page 4
The following table details the recommended service intervals for this product and the service kits to be used.
1.1 SERVICE INTERVALS
Service Type
Recommended Service Intervals
Year 1
or 6.000 Hours
Year 2
or 12.000 Hours
Year 3
or 18.000 Hours
Year 4
or 24.000 Hours
APPPP
BP P
CP
D
(ES Models) PPPP
• ServiceA - Every year
Replace external exhaust silencers/muers
Applicable on all models
• ServiceB- Every 2 years
Replace desiccant and top cap ltraon
Replace top manifold gasket seals
Replace exhaust valves
Replace inlet valves
Replace outlet valves
Applicable on all models
• ServiceC- Every 4 years
Replace control valves
Applicable on all models
• ServiceD- Every 1 years
(Re-) Calibrate dew-point sensor
Applicable on ES models only
Note; The serial/part number of the nitrogen generator must be supplied when requesting any of the
services listed above, this is to ensure the correct service parts are selected.

Page 5
Model(example) Kitnumber Descripon
ServiceA-Replace external exhaust silencers/muers
40-110-GÜÜ-0000-ÜÜ BSP - 130 BSPT Exhaust Silencer element
40-110-AÜÜ-0000-ÜÜ NPT - 130 NPT Exhaust Silencer element
ServiceB- Desiccant Replacement kit
40-110-ÜÜT-2110-ÜÜ NDA-110 (x2)
Loose ll desiccant and gaskets
40-110-ÜÜT-2120-ÜÜ NDA-120 (x2)
40-110-ÜÜT-2130-ÜÜ NDA-130 (x2)
40-110-ÜÜT-3130-ÜÜ NDA-130 (x3)
40-110-ÜÜT-4130-ÜÜ NDA-130 (x4)
40-110-ÜÜT-6120-ÜÜ NDA-120 (x6)
40-110-ÜÜT-6130-ÜÜ NDA-130 (x6)
40-110-ÜÜS-2110-ÜÜ NDK-110 (x2)
desiccant cartridge and gaskets
40-110-ÜÜS-2120-ÜÜ NDK-120 (x2)
40-110-ÜÜS-2130-ÜÜ NDK-130 (x2)
40-110-ÜÜS-3130-ÜÜ NDK-130 (x3)
40-110-ÜÜS-4130-ÜÜ NDK-130 (x4)
40-110-ÜÜS-6120-ÜÜ NDK-120 (x6)
40-110-ÜÜS-6130-ÜÜ NDK-130 (x6)
40-110-ÜÜL-2110-ÜÜ NDA-110-LDP (x2)
Low point desiccant (LDP) cartridge and
gaskets
40-110-ÜÜL-2120-ÜÜ NDA-120-LDP (x2)
40-110-ÜÜL-2130-ÜÜ NDA-130-LDP (x2)
40-110-ÜÜL-3130-ÜÜ NDA-130-LDP (x3)
40-110-ÜÜL-4130-ÜÜ NDA-130-LDP (x4)
40-110-ÜÜL-6120-ÜÜ NDA-120-LDP (x6)
40-110-ÜÜL-6130-ÜÜ NDA-130-LDP (x6)
40-110-ÜÜM-2110-ÜÜ NDK-110-LDP (x2)
Loose ll low dew point (LDP) desiccant and
gaskets
40-110-ÜÜM-2120-ÜÜ NDK-120-LDP (x2)
40-110-ÜÜM-2130-ÜÜ NDK-130-LDP (x2)
40-110-ÜÜM-3130-ÜÜ NDK-130-LDP (x3)
40-110-ÜÜM-4130-ÜÜ NDK-130-LDP (x4)
40-110-ÜÜM-6120-ÜÜ NDK-120-LDP (x6)
40-110-ÜÜM-6130-ÜÜ NDK-130-LDP (x6)
1.2 SERVICE KITS

Page 6
Model(example) Kitnumber Descripon
ServiceC-ValveServicing(NOTE; you may require more than one kit)
ALL MODELS EVK-6130 2 internal exhaust valves
ALL MODELS IVK-6130 2 internal inlet valves
ALL MODELS OVK-6130 2 internal outlet valves
40-ÜÜÜ-ÜOÜ-0000-QÜPVKO-6130-024 24v pilot normally open operaon valves
40-ÜÜÜ-ÜOÜ-0000-SÜPVKO-6130-240 240v pilot normally open operaon valves
40-ÜÜÜ-ÜOÜ-0000-RÜPVKO-6130-110 110v pilot normally open operaon valves
40-ÜÜÜ-ÜCÜ-0000-QÜPVKC-6130-024 24v pilot normally closed operaon valves
40-ÜÜÜ-ÜCÜ-0000-SÜPVKC-6130-240 240v pilot normally closed operaon valves
40-ÜÜÜ-ÜCÜ-0000-RÜPVKC-6130-110 110v pilot normally closed operaon valves
Service C - OVERHALL KITS
40-ÜÜÜ-ÜOÜ-0000-QÜNOKO-6130-024 PVKO-6130-024, EVK-6130, IVK-6130 & OVK-6130
40-ÜÜÜ-ÜOÜ-0000-SÜNOKO-6130-240 PVKO-6130-240, EVK-6130, IVK-6130 & OVK-6130
40-ÜÜÜ-ÜOÜ-0000-RÜNOKO-6130-110 PVKO-6130-110, EVK-6130, IVK-6130 & OVK-6130
40-ÜÜÜ-ÜCÜ-0000-QÜNOKC-6130-024 PVKC-6130-024, EVK-6130, IVK-6130 & OVK-6130
40-ÜÜÜ-ÜCÜ-0000-SÜNOKC-6130-240 PVKC-6130-240, EVK-6130, IVK-6130 & OVK-6130
40-ÜÜÜ-ÜCÜ-0000-RÜNOKC-6130-110 PVKC-6130-110, EVK-6130, IVK-6130 & OVK-6130
ServiceD-Dewpointsensors(oponal)
40-ÜÜÜ-ÜÜS-0000-ÜE
40-ÜÜÜ-ÜÜT-0000-ÜENSK-130 Dew point sensor calibraon for standard -40C
(-40F)
40-ÜÜÜ-ÜÜL-0000-ÜE
40-ÜÜÜ-ÜÜM-0000-ÜENSK-130-LDP Dew point sensor calibraon for standard -70C
(-95F)
Energy saving upgrade kits
40-ÜÜÜ-ÜÜS-0000-ÜÜ
40-ÜÜÜ-ÜÜT-0000-ÜÜ ESU-130 Energy saving upgrade kit; Dewpoint sensor and
accessories
40-ÜÜÜ-ÜÜL-0000-ÜÜ
40-ÜÜÜ-ÜÜM-0000-ÜÜ ESU-130-LDP Energy saving upgrade kit; Low-dewpoint sensor
and accessories

Page 7
The following illustration details the basic assembly of the dryer. Model shown is an NDL-6130.
Column
Inlet Manifold
Bottom Manifold
Dryer Legs
Bottom Cover
Outlet
Assembly
Top Manifold
Shroud
Exhaust Manifold
PLC Display Unit
Purge Block
Top Cover
2. PRODUCT ASSEMBLY
Exhaust silencer
if tted; valve pilot tubing assembly
(Tubing not displayed)

Page 8
3. RECOMMENDED TOOLS
The following tools will be required to service the dryer:
Strap Wrench
Terminal Screw Driver
2mm, 3mm Allen Key
M10, M12 Socket
8mm, 11mm, 12mm Spanner
Small adjustable spanner
M12 Guide pins
Suitable Vacuum Cleaner
Large Flat Driver
4.1 DRYER SHUT DOWN PROCEDURE
Before performing any maintenance or service operations on this product, ensure the product
is isolated from the compressed air supply and fully depressurised. Also ensure the product is
switched o and/or isolated from the mains power.
PROCEDURES
• Isolatethecompressedairsupplytothedryer(Inletandoutlet)
In order to fully depressurise the dryer;
- Allow the dryer to cycle twice to ensure the dryer exhausts and is completely depressurised.
- When fully depressurised the‘clicking’of the exhaust valves will be heard but no air
exhausted.
- If Energy Saving enables, you may need to power down the dryer, wait 5 minutes, and restart to
prevent ES Mode enabling to fully shut down.
• Whenthedryerisfully depressurised, isolate from the power supply.
4.2 DRYER START-UP PROCEDURE
•Ensure all isolation valves are closed
•Ensure the inlet operating pressure parameters are between 58-145 psig (4-10 barg).
•Ensure the inlet air temperature is between 35°F - 122°F.
•Slowly open the inlet valve and allow dryer to pressurise.
•Turn on the power to the dryer.
•Open the outlet valve.
•The dryer will display its status and commence normal operation. When the dryer is powered up the display will
show“Starting”for approximately 20 seconds, untill displays the columns status,“purge” or “online”.
•Ensure all pipe work is connected.

Page 9
5. SERVICE‘A’ INSTRUCTIONS - Silencers/Muers
(Every year or 6,000 hours)
REPLACE EXTERNAL EXHAUST SILENCERS/MUFFLERS
1. Ensure the dryer is shut down and fully depressurised.
See Page 8, section 4.1.
2. Remove Exhaust Silencer/Muers from the unit and
discard (gure A.1)
3. Clean the thread and remove any sealing material debris
from external exhaust elbow (gure A.3)
4. Apply new thread sealing material to new Exhaust
Silencer/Muers, shown in gure A.4
5. Attach Exhaust Silencer/Muers, ensuring they are tight.
Figure A.1 Figure A.2
Figure A.3
Remove all debris
Figure A.4
Apply new thread sealing
material

Page 10
1.
2.
3.
4. In the front of the dryer
disconnect both inlet valves
supply pipe-work (gure B.2)
and the main compressed air
supply pipe. (Figure B insert)
5. At the rear of the dryer
disconnect the air inlet supply
pipe and both inlet valve supply
(gure B.2) connections (gure
B.3). If E.S. is tted remove the
4mm supply tube from the unit
6. SERVICE‘B’INSTRUCTIONS - Desiccant change
(Every 2 years or 12,000 hours)
Figure B: Model Shown NDL - 4130.
Figure B.1
REPLACING DESICCANT CONTENTS
1. Ensure the dryer is shut down and fully
depressurised. See Page 8, section 4.1
2. Remove the xing screws from the top
cover and remove cover. (Figure B)
3. Remove the 4 x M10 bolts from the outlet
connection ange at the rear of the dryer.
COLUMN CAPS
TOP MANIFOLD
2x M5 SOCKET
HEAD SCREWS
TOP COVER
M12 BOLTS AND
WASHERS
Black plastic conduit
Tubing not present on all units.
Tubing slides in the top manifold,
and around the column
Figure B.2 Figure B.3

Page 11
6. If a dewpoint sensor is tted, disconnect the nut attached at outlet block [Fig B.4] and
pull through the tubing, (maintain attachment to the sensor assembly).
7. Remove the black plastic conduit, if present, from the top of the dryer’s top manifold.
8. Remove the front door. Pins located inside on the left (The door will be unsupported
once the top manifold is removed).
9. Undo the M12 retaining bolts from the top manifold. (8 bolts per column)
10. Remove the top manifold (care should be taken not to damage the sealing face).
11. Remove all of the column caps exposing the drying media.
12. Using a suitable vacuum cleaner, remove the expended dessicant media from each
column.
13. Remove any contaminants from the columns internal surface.
14. Using a nano suitable snow storm ller, replace the dessicant media ensuring
continuous lling is maintained. A gap of 30mm must be left free at the top of each
column for the column cap [gure B.5].
15. Install a new 150mm diameter media disc onto the
top of the dessicant ll and t column caps.
16. New column top caps must be installed. (Caps
should stand approx.2mm above column length).
17. Clean top manifold and replace all gaskets (use a
suitable grease to hold gaskets into place).
18. Ensure all column sealing faces are clean and free
from dust.
19. Reassemble the dryer by replacing the top manifold
ensuring it is lined up correctly with the columns,
using Guide Pins (see parts list). Insert all M12 bolts
and torque to a setting of 80Nm following the
correct tightening sequence on page 19-20.
20. Ret the door.
21. Ret the black plastic conduit to the top of the
manifold and re-connect the 4 x plastic 6mm
tube to the exhaust valves and control solenoid
valves. (If E.S. is tted re-connect the 4mm clear
tube).
22. Re-connect the outlet manifold connection using 4 x
M10 bolts.
23. Replace the top cover.
24. Start up the Dryer (see page 8)
30mm
2mm
Figure B.4;
Disconnect nut to release
dewpoint sensor tube
Figure B.5

Page 12
If the exhaust valves are not intented to be serviced,
continue to page 13
1. Ensure the dryer is shut down and fully depressurised
(See page 8, section 4.1).
2. Remove the bottom cover attached by 3 screws.
3. Remove the 8 x M10 socket head cap screws and 8 x
washers to release the valve block from the bottom
manifold (gure C.1).
4. Remove the co-axial valves from the valve
orice within the bottom manifold and discard.
5. lightly grease and insert the new inlet valves into the valve block ensuring the ow direction arrow is pointing as
shown and the valve ridge details cover the spill port. (See gures C.1.1, and C.1.2).
6. Reassemble valve block to the bottom manifold (torque setting; 40Nm). Refer to page 19-20 and follow the correct
tightening sequence when replacing block.
7. Ret the bottom cover.
8. Start up the Dryer (page 8), or continue to complete service C
6.1 SERVICE‘C’INSTRUCTIONS - Exhaust valves
(Every 4 years or 24,000 hours)
REPLACING EXHAUST VALVES
CO-AXIAL VALVES
FLOW DIRECTION
ARROW
VALVE RIDGE
DETAILS
EXHAUST MANIFOLD
M10 SOCKET HEAD CAP
SCREW AND WASHER
BOTTOM COVER
Spill Port Positions
Figure C.1
The spill ports are 1.5mmØ holes
within the bottom manifold.
Figure C.1.1
Figure C.1.2

Page 13
6.2 SERVICE‘C’INSTRUCTIONS - Outlet valves
(Every 4 years or 24,000 hours)
REPLACING OUTLET NON-RETURN VALVES
OUTLET NON
RETURN VALVES
OUTLET MANIFOLD
Figure C.2
M10 SOCKET
HEAD CAP SCREWS
If the Outlet valves are not intented to be serviced, continue to page 14
1. Ensure the dryer is shut down and fully depressurised (See page 8, section 4.1).
2. Remove the 8 x M10 socket head cap screws and 8 x washers to release the outlet manifold from the top
manifold. Figure C.2
3. Remove 4 x M10 bolts holding the outlet ange
4. Remove the non return valve from the valve orice within the top manifold and discard.
5. Lightly grease and insert the new non return valves into the valve orices within the top manifold ensuring the
valve has been insert in the correct orientation. Refer to gure C.2.1
6. Place the valve block to the top manifold and insert the 8 x M10 socket head cap screws and the 8 x washers
to complete the assembly. Refer to page 19-20 and follow the correct tightening sequence when replacing the
valve block
7. Ret the ange
8. Start up the Dryer (page 8), or continue to complete service C
Note Flow Direction on
the Outlet NRV
TOP MANIFOLD
Figure C.2.1

Page 14
6.3 SERVICE‘C’INSTRUCTIONS - Inlet valve
(Every 4 years or 24,000 hours)
REPLACING INLET CONTROL VALVES
If the Inlet valves are not intented to be serviced, continue to
page 15
1. Ensure the dryer is shut down and fully depressurised
(See page 8, section 4.1).
2. Remove the ange and remove the 8 x M10 socket head
cap screws and washers to release the valve block from the
bottom manifold.
3. Remove the inlet valves from the orice within the botton
manifold and discard.
4. light grease and insert the valves into the orices within the bottom manifold ensuring the ow direction arrow
is pointing as shown and the valve ridge details [Fig C.3.1] cover the spill port. (See gure C.3.2).
5. Place the valve block to the bottom manifold and insert the 8 x M10 socket head cap screws and the 8 x washer,
tightening to a torque setting of 40Nm. Refer to page 19-20 and follow the correct tightening sequence when
replacing the valve block.
6. Ret the inlet ange and start up the Dryer (page 8)
INLET VALVES
INLET MANIFOLD
8x M10 SOCKET
HEAD CAP SCREW AND
WASHERS
Figure C.3
Figure C.3.2
Figure C.3.1
Spill Port Positions
The spill ports are 1.5mmØ holes
within the bottom manifold .

Page 15
6.4 SERVICE‘C’INSTRUCTIONS - Pilot valves
(Every 4 years or 24,000 hours)
REPLACING PILOT VALVES
If the pilot valves are not intented to be serviced, continue to start up the dryer, see page 8
1. Ensure the dryer is shut down and fully depressurised (See page 8, section 4.1)
2. Disconnect and note conguration of the tubing, cables and variation between the pilot valves (Normally Open
and/or Normally Closed)
3. Remove the 4 screws to release the pilot valve assembly
4. Remove the elbows and joints
5. Ret the elbows and joints with thread sealing material to the new pilot valve
6. Ret the pilot valve assembly and tubing
7. Start up the Dryer (page 8)
Figure C.4

Page 16
1. Ensure the dryer is shut down
and fully depressurised before
attempting any maintenance work.
(See Page 8, section 4.1)
2. Remove the top cover screws
and remove the cover. (See Figure
D.1)
3. Release the catches located at
the top and bottom of the shroud
to open it (See Figure D.1.1)
4. Remove the screw from the
sensor plug (Figure D.2) and
detach it from the dew point
sensor assembly. (See Figure D.2.1)
Figure D.1
TOP COVER
SCREWS
PLUG SCREW
SHROUD LATCH
DEW POINT PLUG
CONTROLLER
CHASSIS PLATE
Figure D.2
7. SERVICE‘D’INSTRUCTIONS - Dew point sensor
(Every 1 year or 6,000 hours)
REPLACING OR RECALIBRATING THE DEW POINT SENSOR - ES MODELS ONLY
Figure D.2.1
Figure D.1.1

Page 17
5. Loosen the 2x M3 socket head screws from the controller chassis plate
(See Figure D.3.1) and release the dew point sensor assembly. (See
Figure D.3)
6. Unscrew the dew point sensor from the sensor block and replace with
the new or re-calibrated sensor making sure the mating surfaces are
clean. (See Figure D.3.2)
7. Reattach the new or re-calibrated dew point sensor and sensor
block assembly to the controller chassis plate using the 2x xing
screws.
8. Replace the sensor plug and screw to complete the sensor assembly.
9. Close the shroud and ensure the latches are in position.
10. Replace the top cover and insert the M5 screws.
11. Start up the Dryer (page 8)
12. Allow for sensor‘bedding in’ time
Figure D.3
SENSOR BLOCK
DEW POINT SENSOR
Figure D.3.1
Figure D.3.2

Page 18
8. RE-SETTING THE DRYER
RESETTING THE PLC DISPLAY UNIT
1. Ensure the dryer is on and running, see dryer start up procedure on page 8.
2. Place a magnet over the controller reset area shown for 8-10 seconds until the dryer re-sets.
3. Once re-set the hours run counter will show‘00000’.
NOTE: Magnet not included in the service kit.
RESET AREA

Page 19
9. TOP & BOTTOM MANIFOLD TIGHTENING SEQUENCES
MODELS: NDL-2110, NDL-2120 & NDL-2130
MODEL(S): NDL-3130
MODEL(S): NDL-4130
29
23 5 13 2215 8
8
7
16 321321 5
5 1415
24
27
17 3 11 2010 1
1
1
10 261119 3
3 129
18
25
19 2 9 1812 4
4
4
12 28917 2
2 1011
20
31
21 7 16 2414 6
6
6
14 301523 7
8 1613
22
Repeat torque sequence to ensure all bolts are fully seated

Page 20
9.2 VALVE BLOCK TIGHTENING SEQUENCES
MODEL(S): NDL-6120 & NDL-6130
ALL MODELS
23
22
20
17
15
10
11
13
5
3 19 33 28 43
2 18 36 26 42
7
21
24
39
38
30
32
8
1
4
6
14
12 41 25 35
9 44 27 34
16
48
46
31
29
37
40
45
47
1
3
4
2
6
8
7
5
This manual suits for next models
6
Table of contents
Other NANO Dehumidifier manuals
Popular Dehumidifier manuals by other brands
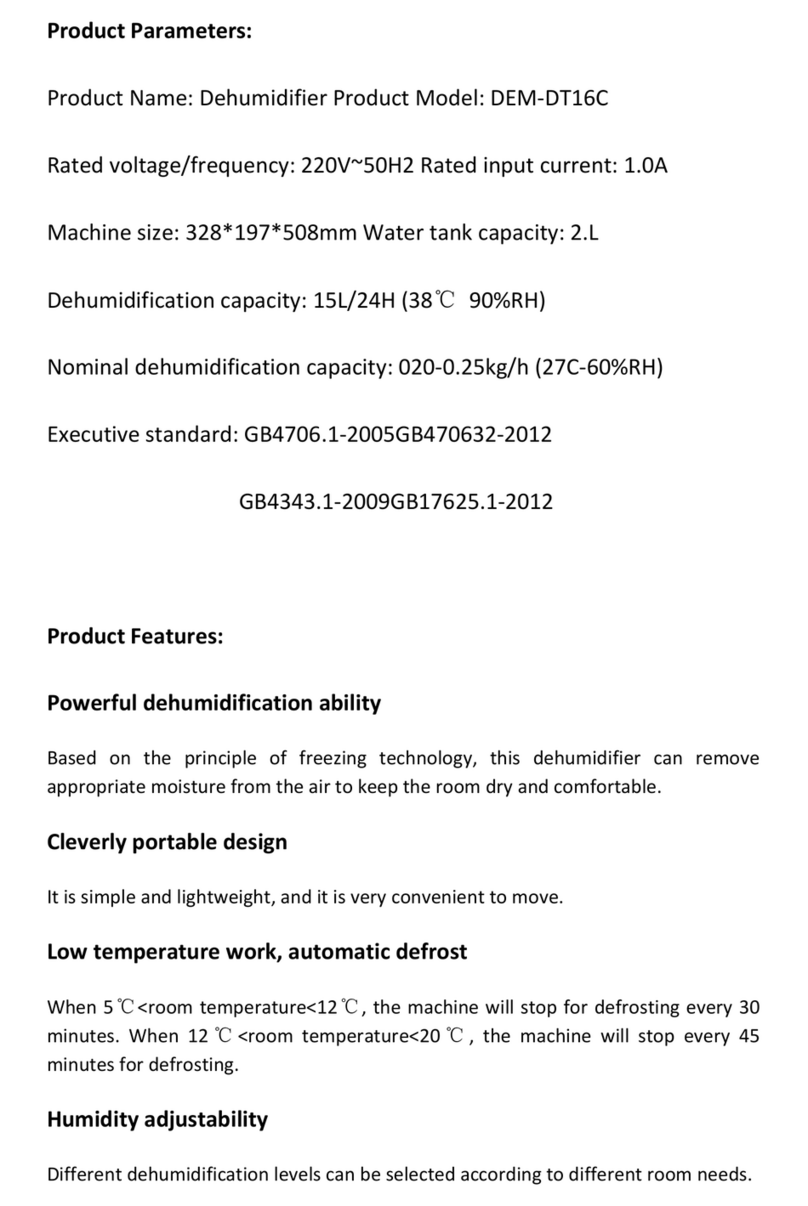
deerma
deerma DEM-DT16C manual
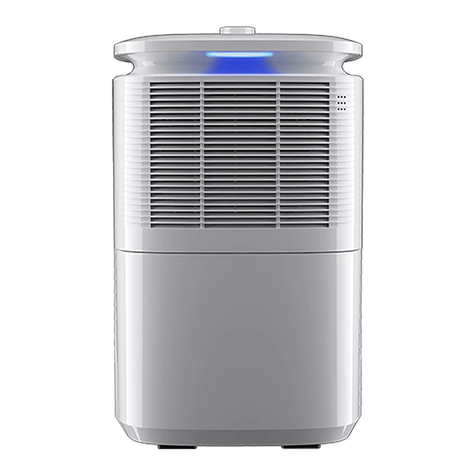
Vax
Vax Power Extract DCS1V1EP user manual
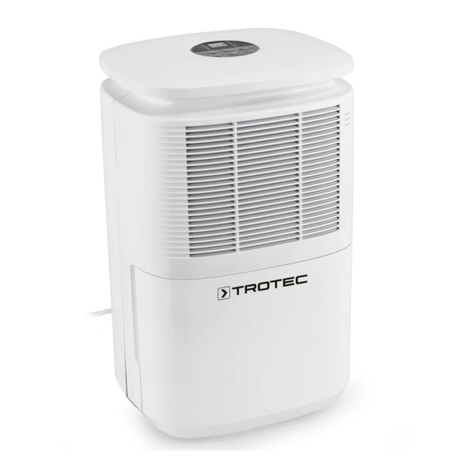
Trotec
Trotec TTK 30 E operating manual
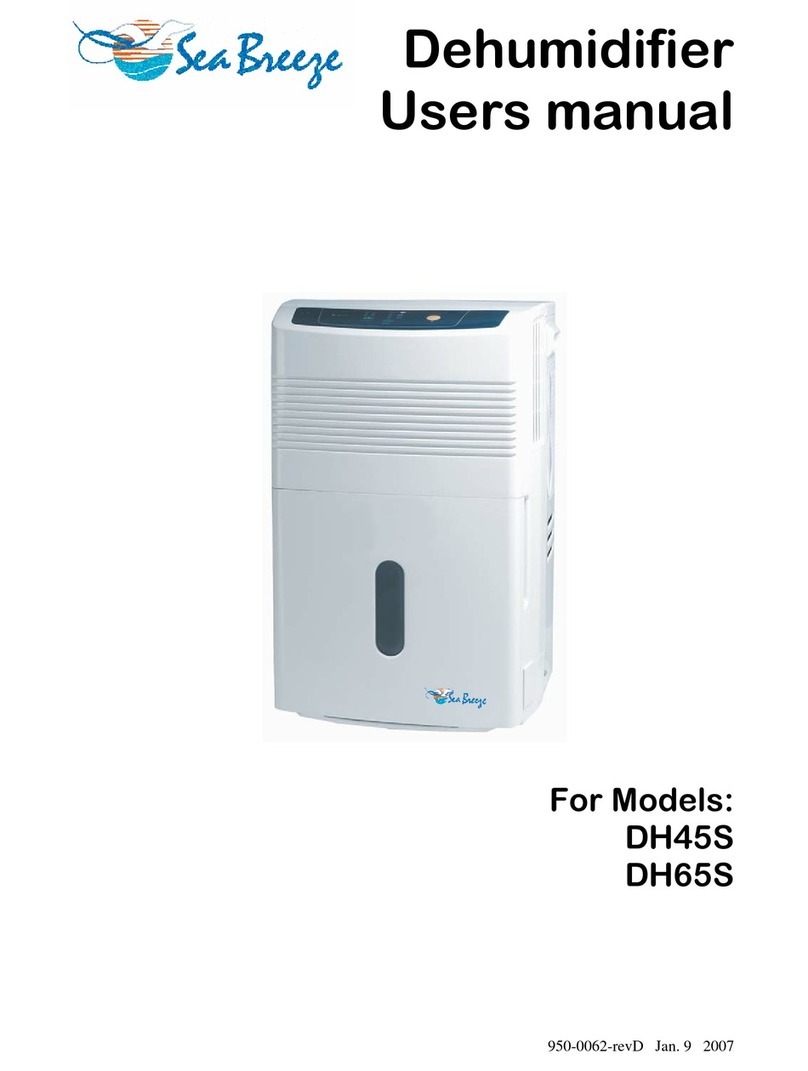
International Refrigeration Products
International Refrigeration Products DH45S user manual
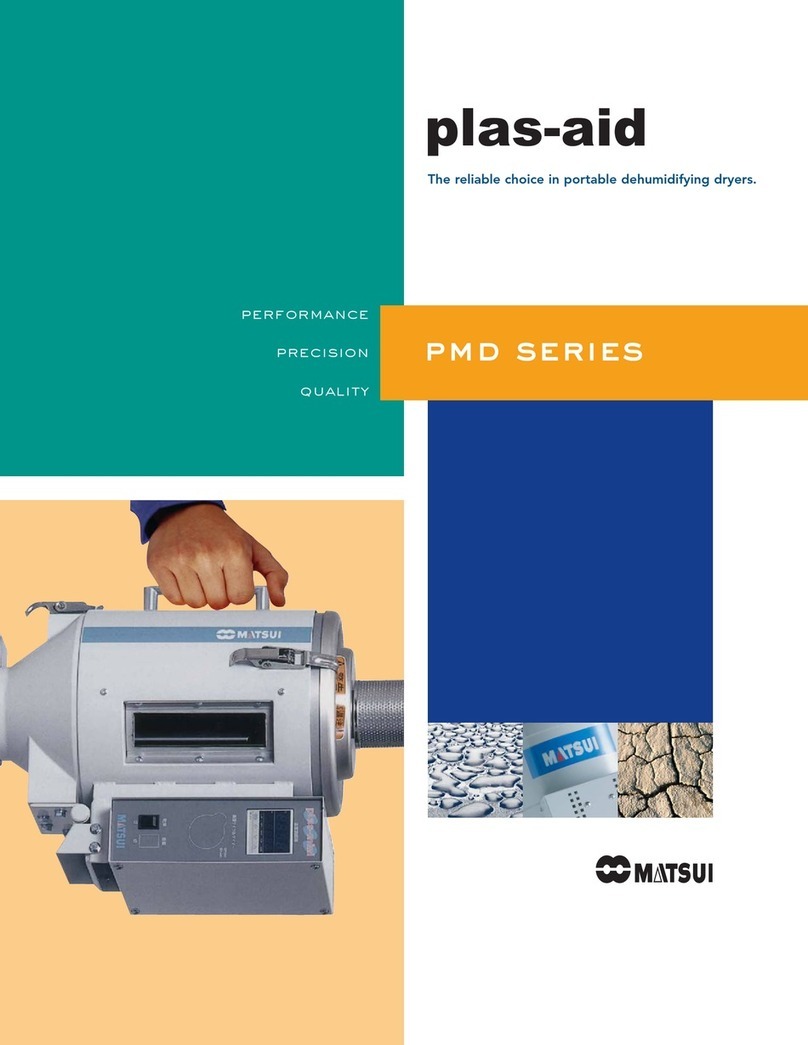
Matsui
Matsui plas-aid PMD Series specification
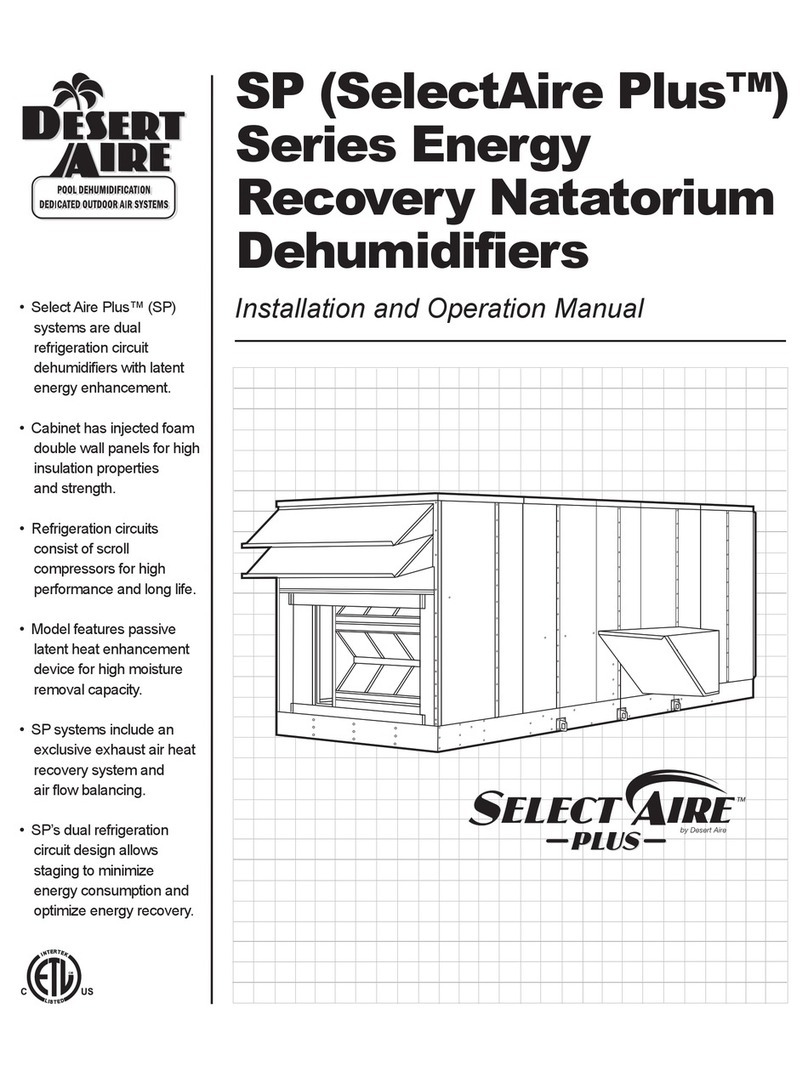
Desert Aire
Desert Aire SelectAire Plus SP Series Installation and operation manual