NANO 3 series User manual

HEATLESS DESICCANT AIR DRYER
SERIES 3 AIR DRYER USER GUIDE

Page 2
nano purication solutions.
17-110-0140
1. General information 3
1.1. Document introduction 3
1.2. North America Support Details | Manufacturers details 3
1.3. Warranty Guidelines 4
1.4. Packaging 4
2. General safety 5
2.1. Intended Use 5
2.2. Personnel 5
2.3. Safe Handling 5
3. Technical Description 6
4. TechnicalSpecication 6
5. Product Contents 7
6. Unpacking Guide 8
7. Product Dimensions 9
8. Equipment Overview 10
9. System Layout 11
10. Mechanical Installation 12
11. Electrical Installation 13
12. Dryer Operation 14
12.1. Dryer Remote Control 14
12.2. Dryer Start up 15
12.3. Monitoring Dryer Performance 16
12.4. Shutdown Procedure 16
13. Maintenance 17
13.1. Maintenance guidelines 17
13.2. Cleaning 17
13.3. Daily checks 17
14. Servicing 17
14.1. Guidelines 18
14.2. Procedures 19
14.3. Additional Kits 19
15. Troubleshooting 20
Contents Page

Page 317-110-0140
1. General Information
This manual is copyrighted, all rights reserved. It may not, in whole or in part, be copied, photocopied,
reproduced, translated, or reduced to any electronic medium or machine readable form without prior consent
in writing from It may not be distributed through the internet or computer bulletin
1.1 Document Introduction
solutions compressed air dryer. The procedures illustrated in this document are only to be performed by
authorized personnel. For further information regarding the procedures outlined in this document contact nano
Read this document carefully before attempting to install or operate the dryer. This document should be
permanently available at the dryer installation site and be kept in an easily accessible place alongside the
dryer.
©2014 nano solutions.
Product: Series 3 Desiccant Air Dryer
Document number: 17-110-0140
Issue: 003
NOTES: highlight important sections of information where particular care and attention should
be paid.
CAUTIONS: indicate any situation or operation that may result in potential damage to
the product, injury to the user, or render the product unsafe.
Annotations:
1.2 Support
For parts and technical support please contact:
solutions
11330 Vanstory Drive
Huntersville, NC 28078
USA
Telephone: (704) 897-2182
Fax: (704) 897-2183
Internet: www.n-psi.com
E-mail: [email protected]
Manufactured in the UK
in an ISO 9001 certified facility

Page 4
nano purication solutions.
17-110-0140
1.3 Warranty Guidelines
All products are supplied with a 5 year manufacturer’s warranty from the date of purchase,
when purchased with an ES (Energy Saving) system and installed and maintained in
accordance with the manufacturers guidelines. Only genuine service parts should be used
and no modications made. For further information please contact nano purication solutions.
1.4 Packaging
All products are securely packaged in a specically designed wooden packing box. The dryer
will be held in a horizontal position by wooden struts; using straps to secure the product to
the box base. The box top cover can be removed by removing the 4 xing screws and lifting
off in one piece.
The support packing box permits longitudinal stacking; however the central section
of the packing box should not be considered load bearing.
Damage to Packaging
• Check immediately to establish whether damage has occurred to the external packaging
and if the damage extends to the product inside.
• If there is damage to a product, contact the relevant supplier immediately.
In no circumstances must a damaged product be used in operation. Using damaged
products can lead to irreparable functional faults or cause serious physical harm.

Page 5
17-110-0140
2. General safety
For your own safety, when carrying out work on this product, all relevant
national safety regulations must be complied with relating to pressurized
and electrical systems.
2.1. Intended use of the Product
The dryer is exclusively intended for the treatment of compressed air, which is free from
bulk water, oil and solid matter constituents.
The product should be located within a building and protected. The dryer must be operated
only in accordance with the data on the rating plate. Any operations that do not comply with
those stated on the product rating plate will render the warranty void.
This product is only designed to operate at pressures of between 58 - 145
psig (4 - 10 barg).
It is not suitable for pressures in excess of 145 psig (10 barg).
No modications must be made to the product. Any modications may reduce the
operational safety of the product and invalidate the manufacturer’s warranty. This could
potentially result in damage to the product and serious personal injury.
2.2. Personnel
Only authorized, competent and trained personnel are permitted to work on this product.
This user guide is intended solely for such personnel and is to be used only as a reference;
it should not be used to replace conventional training.
2.3. Safe Handling
Please ensure the relevant safe engineering practices and handling procedures are
employed when handling, installing and operating this product. Ensure that the equipment
is depressurized and electically isolated prior to carrying out any of the scheduled
maintenance instructions specied within this user guide.
A suitable lifting aid must be used to minimize the risk of physical injury or
damage to the product.
In no circumstances must a damaged product be used in operation. Using
damaged products can lead to irreparable functional faults or cause serious
physical harm.

Page 6
nano purication solutions.
17-110-0140
3. Technical Description
The n-psi dryer uses the pressure swing adsorption principle of drying compressed air,
utilizing two identical columns each containing a hygroscopic desiccant bed.
• Inlet ltration removes water, oil aerosols and particles (Inlet ltration supplied
separately).
• Wet air enters the dryer through the inlet valve and is directed into one of the columns.
• Each column contains a densely lled desiccant bed.
• Air then passes through the desiccant bed where any remaining moisture is adsorbed.
• Simultaneously, a small amount of dry ltered air is counter owed down through
the other desiccant bed and exhausted to atmosphere, removing the moisture and
regenerating the desiccant bed.
• The dryer controller periodically switches columns after top end repressurization;
ensuring a continuous supply of dry air at constant pressure. The dryer can also be
controlled using a Zero Volt signal from the compressor. This energy saving mode
senses when the compressor is switched off and stops the dryer operation until the
compressor restarts.
• The dry air passes out through the nal particulate lter (<1micron/ISO8573.1 Class 2).
Specication
ISO 8573 - 2:2001 Quality Classes Class 2: Water: -40°F (-40°C) PDP / Class 2: Dirt: 1µm
Optional Class 1 (-100°F) and Class 3 (0°F)
Minimum working pressure 58 psig (4 bar)
Maximum working pressure 145 psig (10 bar) - higher pressures available upon request
Power Supply 100 - 240v AC / 50 - 60Hz
Minimum inlet temperature 34.7°F (1.5°C)
Maximum inlet temperature 122°F (50°C)
Ambient Temperature 34-122°F (1-50°C)
IP Rating IP54 / NEMA 3
Power 38W
4. TechnicalSpecication
• Flow rate based on air inlet pressure of 100 psig (7.0 barg) and temperature of 95°F
(35°C).
• For dryer performance at other inlet conditions or -100°F (-70°C) dewpoint
• All dryers should be proceeded by a coalescing lter regardless of oil or oil free
applications, a nano M01 grade coalescing lter must be installed on the inlet to the
dryer.

Page 7
17-110-0140
5. Product Contents
1. Series 3 Compressed Air Dryer
2. Documentation
• 1 x User Guide
• 1 x Declaration of Conformity
3. Packaging
• 1 x Dryer support base and box cover
Figure 1: Contents Layout

Page 8
nano purication solutions.
17-110-0140
6. Unpacking Guide
The dryer is supplied in a wooden crate. It is recommended that the crate be moved into
position using a forklift truck or pallet truck. Remove the dryer from the wooden crate using
an overhead crane. Use the following illustrations for correct guidance on safe handling and
lifting techniques.
• Cut packaging straps rst, before lifting.
21
3
5 6
4
Ensurethattheexternalsilencers/mufersareremovedbeforeattempting
toliftthepurier.

Page 9
17-110-0140
7. Product Dimensions
MODEL
CONNECTION
A
ins
(mm)
B
ins
(mm)
C
ins
(mm)
D
ins
(mm)
E
ins
(mm)
WEIGHT
lbs
(KG)
NDL - 2110 2” NPT 26
(678)
15
(382)
50
(1289)
16
(400)
14
(360)
366
(166)
NDL - 2120 2” NPT 26
(678)
15
(382)
60
(1538)
16
(400)
14
(360)
441
(200)
NDL - 2130 2” NPT 26
(678)
15
(382)
73
(1889)
16
(400)
14
(360)
547
(248)
NDL - 3130 2” NPT 31
(781)
21.6
(550)
73
(1889)
16
(400)
14
(360)
778
(353)
NDL - 4130 2.5” NPT 38
(949)
28
(718)
73
(1889)
16
(400)
14
(360)
1010
(548)
NDL - 6120 2.5” NPT 51
(1285)
41.5
(1054)
60
(1538)
16
(400)
14
(360)
1155
(524)
NDL - 6130 2.5” NPT 51
(1285)
41.5
(1054)
73
(1889)
16
(400)
14
(360)
1473
(668)
A
B
D
E
C

Page 10
nano purication solutions.
17-110-0140
8. Equipment Overview
1
2
3
4
9
8
7
5
6
Controller Display UnitDryer Top Cover
Front Shroud
Air Outlet Air Inlet
Dryer Column
1
5 6
3
2
4
External Silencers/Mufers Mains Power
7 8
Remote Stop/Start Control
(if required)
9

Page 11
17-110-0140
9. System Layout
9.1. Site Location
When selecting an installation site for the dryer, ensure the following conditions are met:
• Installation site should be located indoors on a at surface protected from the weather
and other harmful conditions.
• The ambient temperature must not drop below 33.8°F (+1°C) or exceed 122°F (50°C).
• The installation site should be level and able to support the weight of the product.
• Ensure sufcient space around the product, to allow access for operation and
maintenance.
• Take into account the noise generated by the dryer exhausting while in use when
considering location.
Ref
1
Description
Compressor
Ref
5
Description
Series 3 Dryer
26Bypass line
3Water separator 7Oil / Water separator
4
Wet air receiver
Dryerpre-ltration
5
7
6
43
2
1
8
8Pressure Relief Valve*
*Note: It is the customers responsibility to t pressure relief valves to the compressed air system.

Page 12
nano purication solutions.
17-110-0140
10. Mechanical Installation
Once the dryer has been located into position, install ball valves and pipe work to ready the
unit for connection to inlet and outlet pressure piping.
The diameter of the pipes must be sufcient to allow unrestricted inlet air supply to the dryer
and to the application as shown in the table below.
Pre and high efciency ltration is recommended at the inlet to the dryer. In extreme
conditions a water separator is recommended at the inlet.
Ensure that each lter condensate drain is suitably piped away and any efuent is disposed
of in accordance with local regulations.
It is important to ensure that all piping materials are suitable for the application, clean and
debris free. The diameter of the pipes must be sufcient to allow unrestricted inlet air supply
to the equipment and outlet gas / air supply to the application.
The dryer is supplied with an integrated exhaust silencer.
All components used within the system must be rated to at least the maximum operating
pressure of the equipment. It is recommended that the system be protected with suitably
rated pressure relief valves. It is also recommended to install the dryer with a bypass to
facilitate servicing.
Ref. Ref.Description Description
15
Ball Valve 2” or 2.5” Piping (as required by the dryer)
26
Water Separator Series 3 Dryer
3Pre-lter(Inlet)
4Highefciencylter
5
5
1
2
6
3 4
1

Page 13
17-110-0140
11. Electrical Installation
Mains Power Connection
To install the mains power cable:
1. Remove the two screws from the top cover and lift from the purier.
2. Locate the two catches at the top and bottom of the shroud and pull them towards each other and open
the shroud to expose the controller.
3. Remove the IEC plug from the controller
4. Unscrew the cap head screw to remove the plug top cover.
5. Feed the mains power cable through the holes located on the bottom of the shroud.
6. Wire the mains power cable into the IEC plug (see gure 2).
7. Once the mains cable is correctly wired into the IEC plug, reattach the plug into its socket.
Electrical Power Requirements
Supply: 100 - 240VAC
50 -60 Hz
Input Current: 1.3 / 0.8A
(115/23O VAC)
Figure 2.
IEC Plug
Figure 1.
Figure 3.
Top Cover
Shroud Latches
Controller

Page 14
nano purication solutions.
17-110-0140
12. Dryer Operation
Electrical Connector
Figure 1.
Under no circumstances should external voltage/current be applied to pins 1 and 4,
damage to the controller will occur, negating the warranty.
• To set up for remote control eco mode.
Remove the link between pins 1 and 4 (3)
in the electrical connector plug. A zero volt
switching signal from the remote control needs
to be connected between pins 1 and 4 (4).
• When the connection is made, the dryer will
operate normally. If the connection is broken,
i.e. the purier has been remotely switched off,
the dryer will stop cycling and go into standby
mode, displaying “STANDBY” on the display
once completed.
• Using remote stop / start ensures the correct
shut-down sequence is implemented.
Dryer Remote Stop/Start Control (if required)
Locate the electrical connector on the underside of the controller in the shroud.
8.16PinElectricalConnectorConguration
Links 1/4
Remote stop/start link
1. 2. 3.
4.
Links 2/3
General (no-volt) alarm output
Links 5/6 (-Ve/+Ve)
4-20mA Retransmission
(Optional - where tted)

Page 15
17-110-0140
12.2. Dryer Start-up
• Ensure the purier is securely hardwired into the power source.
• Connect all pipe work.
• Ensure the inlet operating pressure parameters are between 80 - 145 psig (5.5 - 10
barg).
• Ensure the inlet air temperature is between 35°F - 86°F (1.5 - 30°C).
• Slowly open the inlet valve until fully open and allow dryer to pressurize.
• Turn on the power to the dryer.
• Open the outlet valve.
• The dryer will display its status and commence normal operation.
Donotallowthedryertoowairunlesspoweredup,switchedonand
cycling. Resulting effect could be bed contamination; requiring replacement
cartridges.
Ensurethattheexternalsilencers/mufersarere-installedbefore
attempting to start the dryer.

Page 16
nano purication solutions.
17-110-0140
• The dew-point is displayed on the control panel. When the dew-point displayed is better
than -54°F PDP the dryer will switch into economy mode and stop cycling. When the
dew-point degrades to -43°F the dryer will restart cycling ensuring the dew-point is
maintained at or better than -40°F.
• If the dryer fails to achieve dew-point (falls below -22°F) the alarm output will be
indicated on the front screen and the remote alarm output will activate.
• Close the inlet and outlet valves.
• When the dryer is fully depressurized, isolate from the power supply.
• Cycle the dryer at least twice to ensure the dryer exhausts and is completely
depressurized.
• When fully depressurized the ‘clicking’ of the exhaust valves will be heard but
no air exhausted.
12.3. Monitoring dryer performance (Energy saving option)
12.4. Shutdown Procedure
The dryer will still be pressurized! In order to depressurize the dryer;
ensure the dryer is isolated from the compressed air supply source:
SERVICE L.E.D
DISPLAY PANEL
OPERATION L.E.D
HOURS RUN / DEW-POINT
COLUMN A / B ONLINE
ILLUMINATED WHEN
SERVICE REQUIRED
ILLUMINATED WHEN
IN OPERATION
Beware this is only an example as the dew-point set-points and alarms are
adjustable through the display panel.

Page 17
17-110-0140
13. Maintenance
Maintenance operations should only be carried out by authorized, suitably
trained personnel.
• Maintenance operations only to be conducted when the system has been shut down and
fully depressurized.
• All connections must be undone with care, paying particular attention to the areas that
become pressurized.
• Do not modify or adjust the control settings.
• Only certied n-psi approved replacement parts to be used.
• Always check all connections for leakage and secure seating.
• Ensure all loose parts are removed or secured to the dryer before operation.
13.1. Maintenance Guidelines
Visual and functional check of the dryer should be carried out daily:
• Check the dryer for any external damage.
Assess and eliminate any defects found.
• If the red service light appears, the dryer must be serviced.
Contact the service department and request a dryer service kit.
• Remove any loose dust or dirt from the dryer; clean all surfaces that appear to have
attracted unwanted contaminants.
• Check the dewpoint sensor display (if installed). If the dewpoint is not maintained at
<-22°F the reading on the display will alternate with “dewpoint alarm” every 5 seconds.
The no-volt alarm will also activate.
Contact the service department and request a product service.
13.3. Daily Checks
13.2. Cleaning
Clean the equipment with a damp cloth only and avoid excessive moisture around any
electrical sockets. If required a mild detergent may be used, however do not use abrasives
or solvents as they may cause damage.

Page 18
nano purication solutions.
17-110-0140
14. Servicing
Maintenance operations should only be carried out by authorized,
competent and suitably trained personnel.
14.1. Serving Guidelines
• Maintenance operations only to be conducted when the system has been shut down,
fully depressurized and isolated completely from the compressed air and electrical
supply.
• Ensure the system is in a safe condition for maintenance to be carried out on.
• Dismantle and assemble with care, paying particular attention to the areas that become
pressurized.
• All gaskets removed during maintenance operations must be replaced with new gaskets.
• Do not modify or adjust the control settings.
• Only certied n-psi approved replacement parts to be used.
• Always check all connections / sealing faces for cleanliness and secure seating prior to
assembly.
• Ensure all components are retted to the product before operation.
• Ensure the dryer is left operating in a safe working condition after completion of
maintenance.

Page 19
17-110-0140
A dryer service should take place every 2 years or 12,000 hours of operation (whichever
occurs rst). Service kits are available which include: replacement desiccant, integral
lters, seals and valves.
Service A - 12,000 hours (or 2 years) service.
• Replace Desiccant & integrated Afterlters
• Replace ICF valves (inlet, outlet, exhaust)
• Replace all gaskets and seals removed while servicing the dryer (included in relevant
service kits)
Service B - 24,000 hours (or 4 years) service.
• Service as above
• Replace pilot valves
Service C - 6,000 hours (or 1 year) service.
• Dewpoint sensor service – NSK-0130 (ES models only) – contact technical support at
n-psi
14.2. Service Procedures
Please refer to the Series 3 Dryer service guide for instruction regarding carrying
out a service.
SERVICE A SERVICE B
MODEL Desiccant & Afterlter
Service Kit Inlet Valve Kit Outlet Valve Kit Exhaust Valve Kit Pilot Valve Kit
NDL - 2110 NDA 110 - 2 NVK D3 2 NVK D3 1 NVK D3 2 NVK 0100
NDL - 2120 NDA 120 - 2 NVK D3 2 NVK D3 1 NVK D3 2 NVK 0100
NDL - 2130 NDA 130 - 2 NVK D3 2 NVK D3 1 NVK D3 2 NVK 0100
NDL - 3130 NDA 130 - 3 NVK D3 2 NVK D3 1 NVK D3 2 NVK 0100
NDL - 4130 NDA 130 - 4 NVK D3 2 NVK D3 1 NVK D3 2 NVK 0100
NDL - 6120 NDA 120 - 6 NVK D3 2 NVK D3 1 NVK D3 2 NVK 0100
NDL - 6130 NDA 130 - 6 NVK D3 2 NVK D3 1 NVK D3 2 NVK 0100
14.3. Additional Kits
ES Upgrade Kit:
Converts a standard dryer to an energy saving model.

Page 20
nano purication solutions.
17-110-0140
1. Insufcient inlet pressure
2. Electrical Fault
3. Moist or contaminated
desiccant
4. Too high air consumption
5. Excessive inlet air temperature
6. Insufcient purge air.
7. Exhaust silencer blocked
1. Inlet pressure min 58 psig (4 barg). If not adjust inlet
presure settings.
2. Ensure the power is on and the dryer front panel is
illuminated; check the dryer is cycling correctly.
3. Eliminate the cause of contamination. Replace desiccant
– do not re-use.
4. Ensure the performance of the dryer matches the
required system air consumption.
5. Check against technical specication.
6. Purge incorrectly adjusted. Consult service personnel to
adjust settings (Factory pre-set).
7. Consult service personnel.
8. Controller not functioning
correctly
9. Controller not illuminated
10. Insufcient inlet pressure
11. Failure to de-pressurize when
cycling.
12. Outlet ow stops
8. Ensure the controller is powered; check the on screen
column status to ensure it is powering the solenoid
valves during normal cyclic operation.
9. Inlet pressure min 58 psig (4 barg). If not adjust inlet
presure settings.
10. Check power to unit & fuse.
11. Solenoid valve not functioning correctly; if there is power
to the coil, replace valve. A correctly working valve
outputs an audible click when it energizes.
12. Check inlet air supply.
13. Failure to initialize dryer
14. Erratic air ow from exhaust
13. Switch off and restart dryer. Ensure dryer is pressurized
before powering dryer to allow dryer to initialize before
commencing operation.
14. Faulty or damaged valve; service required.
Poor dew point
performance
Problem CausedProblem Solution
Failure of dryer to
cycle
Constant
depressurization
15. Troubleshooting
Reference to known issue
Opening the inlet valve too quickly
Valve should be opened slowly allowing the pressure to build up gradually.
Inlet/outlet head pipe
Diameter too small.
Pipe work unsupported.
Inlet pipe work from low point in system, allowing bulk water to collect and enter the dryer.
Electrical controller
Incorrect fuse tted or fuse blown. Check the plug and fuse located on top of the controller
back plate inside the dryer front cover.
Additional Items
Use of non-authorized components.
Untrained / unauthorized maintenance / installation personnel used.
Increase in air consumption without relation to the ow capacity of the dryer.
Purging the dryer with cleaning agents that could damage the components or the desiccant.
Covers removed or loose during operation.
Failure to carry out a service when indicated by the dryer.
Do not allow the dryer to ow air unless powered up, switched on and cycling. Resulting
effect could be desiccant contamination; requiring replacement desiccant.
This manual suits for next models
7
Table of contents
Other NANO Dehumidifier manuals
Popular Dehumidifier manuals by other brands
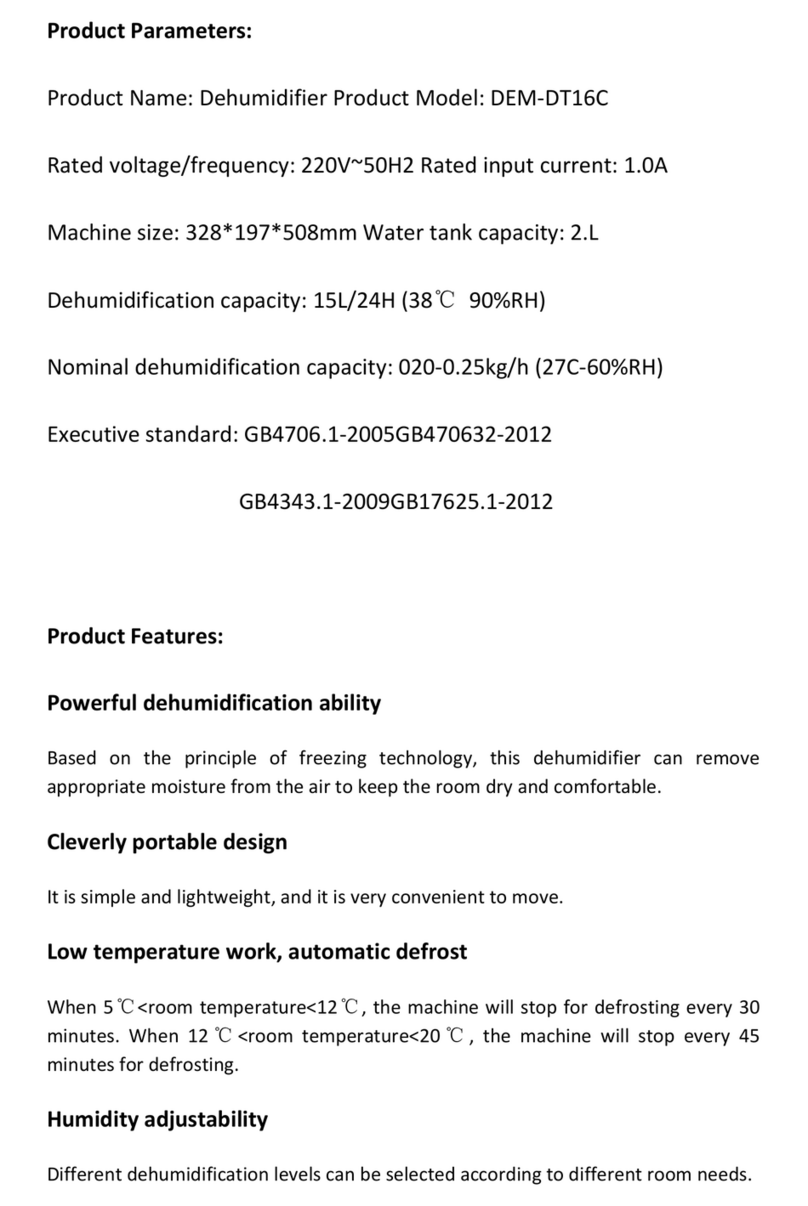
deerma
deerma DEM-DT16C manual
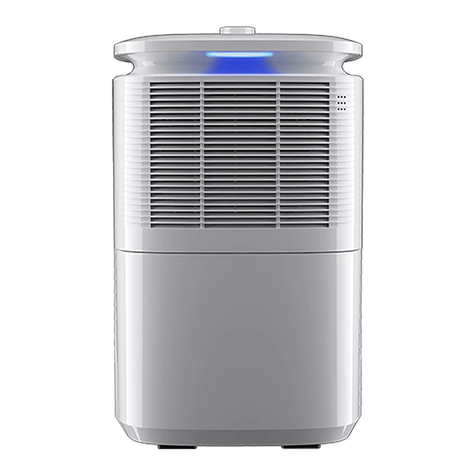
Vax
Vax Power Extract DCS1V1EP user manual
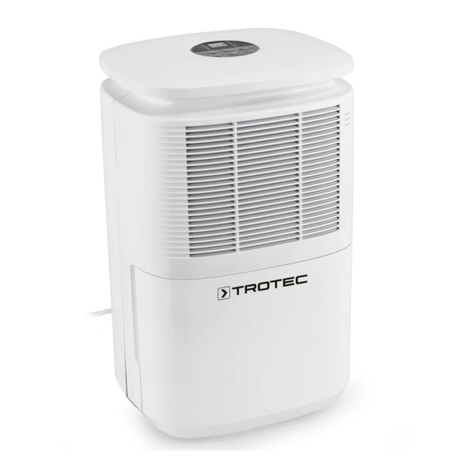
Trotec
Trotec TTK 30 E operating manual
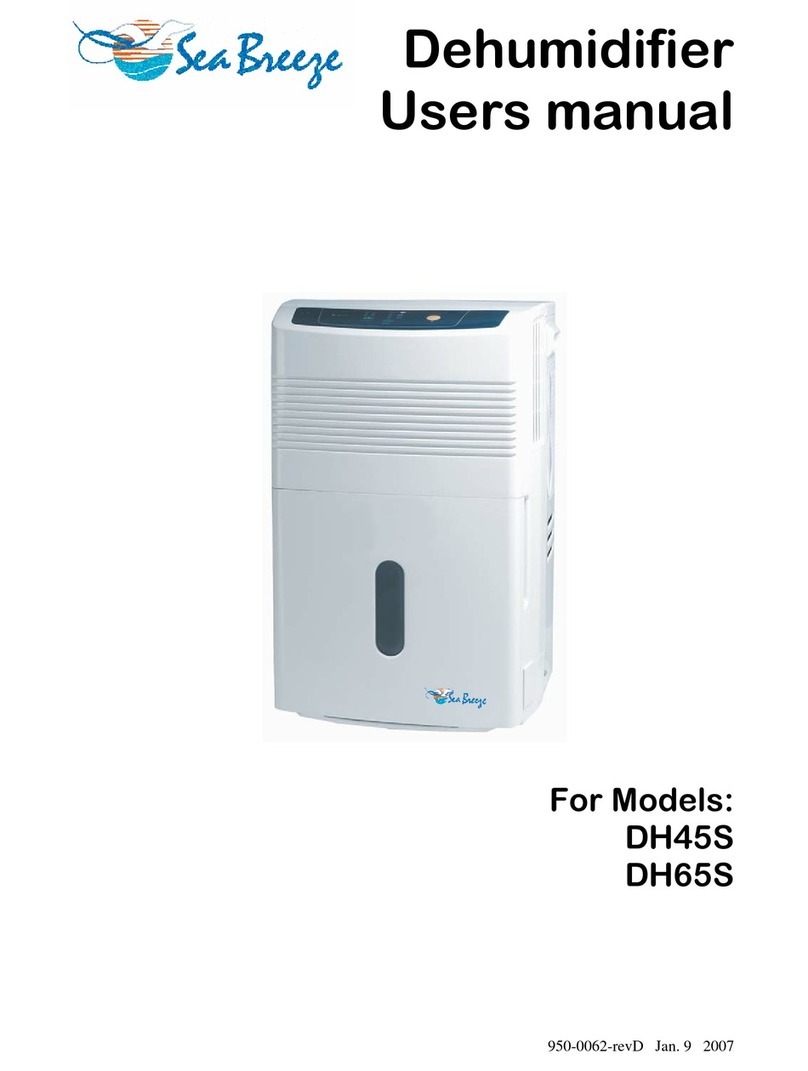
International Refrigeration Products
International Refrigeration Products DH45S user manual
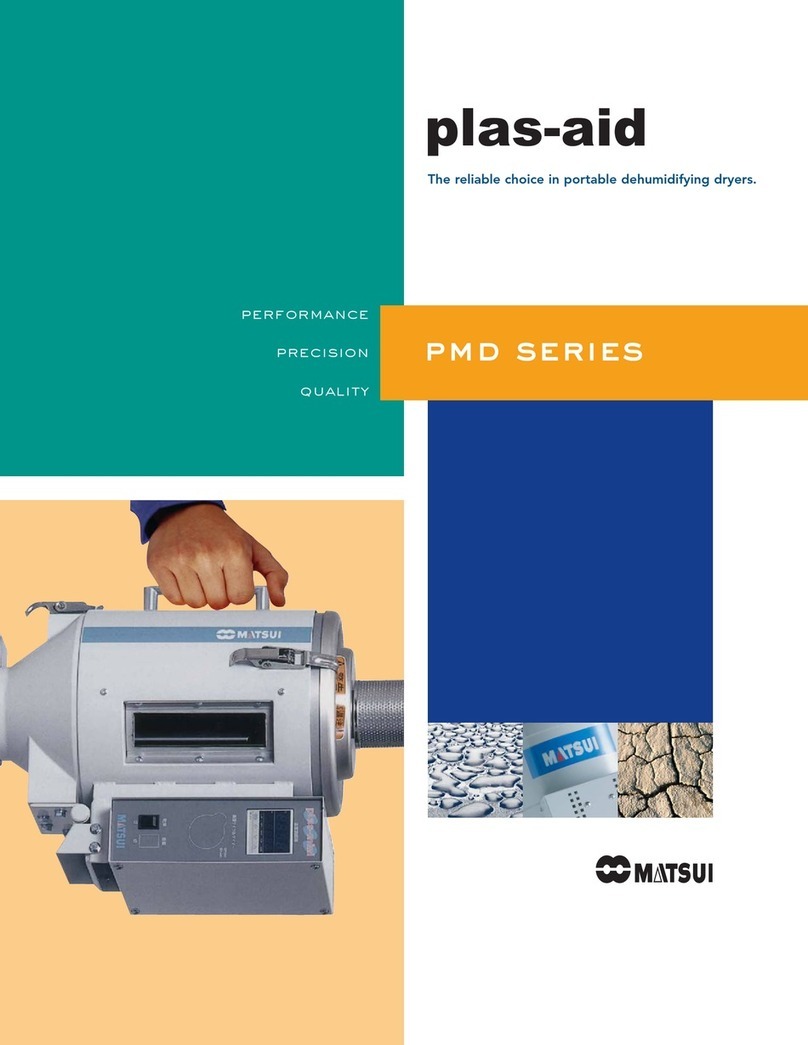
Matsui
Matsui plas-aid PMD Series specification
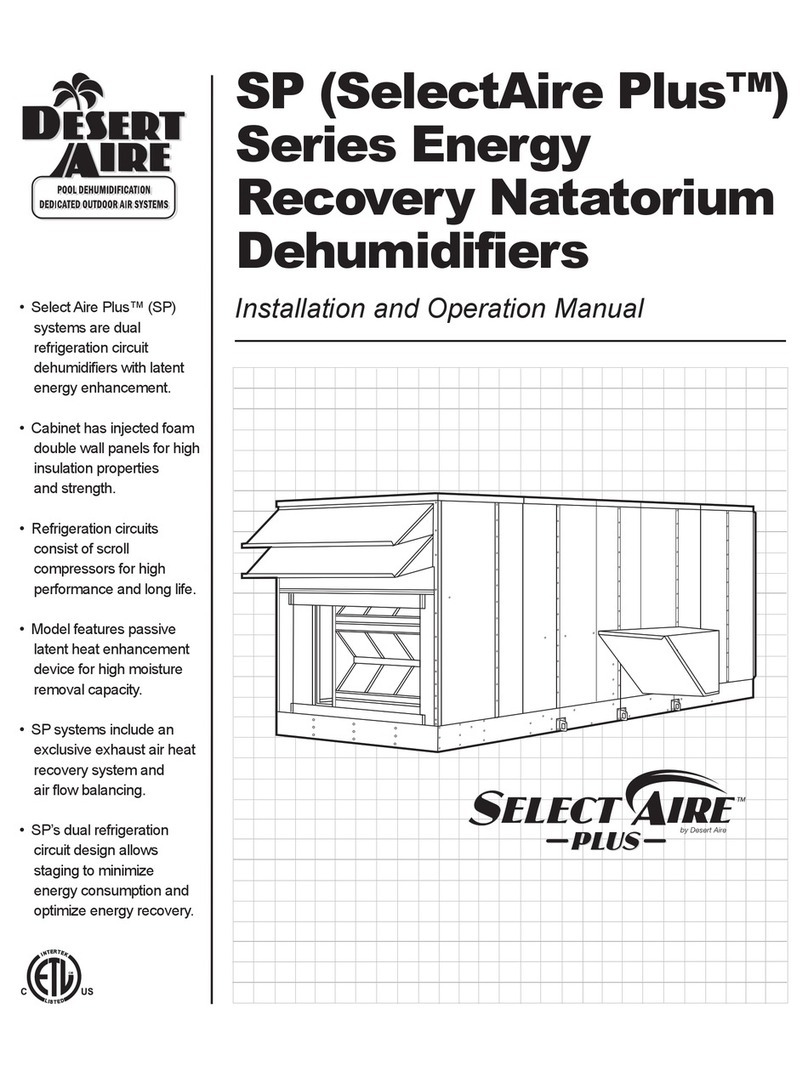
Desert Aire
Desert Aire SelectAire Plus SP Series Installation and operation manual