NCD PR60-12 MIRCC8 WIFI User manual

NATIONAL CONTROL DEVICES
Push Notification - WiFi Quick Start Guide

N A T I O N A L C O N T R O L D E V I C E S
Push Notification WiFi Quick Start Guide
National Control Devices, LLC
PO Box 455
Osceola, MO 64776
Phone 417.646.5644 • Fax (866) 562-0406
© Copyright 2013
All Rights Reserved.
Notice: Portions of this manual require internet access.

Table of Contents
Introduction..............................................................................1
What is the Push Notification Series?.......................................................1
What can this device be used for?............................................................1
How do Push Notification series products work? .....................................1
Getting Started.........................................................................2
WiFi Module Configuration..............................................................2
WiFi Network Setup..................................................................................2
TCP Notification Setup .............................................................................4
UDP Notification Setup.............................................................................4
Initial Testing.............................................................................................5
Hardware Reference................................................................6
Compatible Sensors (Understanding Inputs)............................................6
Power Supply Specifications ....................................................................6
Environmental Specifications....................................................................7
Break-Away Tabs......................................................................................7
Communication Overview ........................................................ 8
Sensor Packet Breakdown .......................................................................8
Direct query command set........................................................................9

Advanced Configuration.........................................................10
Input Configuration..................................................................................10
User Definable Transmitted Bytes..........................................................11
Troubleshooting .....................................................................12
Technical Support ..................................................................13
Contact Information.......................................................................14
Notice:.....................................................................................................14

1
Introduction
What is the Push Notification Series?
The push notification series was designed for customers requiring contact closure
input monitoring via push notification rather than a query based method. This
means your application is free to process other tasks while listening for input
status change. This opens the door to many new and exciting applications such as
email/text message notification, data logging, security monitoring, and much
more. These controllers can be configured to send information to a specific
server via internet connection when their input status changes, or alternatively
they can broadcast their input status change across all devices a local area network
so many applications can be informed of the recent closure.
What can this device be used for?
The possibilities are endless. Just think, a closure generated by someone walking
through a door could trigger a notification on 5 managers’ Android devices
informing them a customer has entered the building. A notification could be sent
to a small local server such as the WiNet which can in turn send an email
notification when the float switch on a reservoir has been tripped by excess water.
Several types of devices can be connected to the Push Notification Series
product’s inputs such as motion detectors, push buttons, switches, relay outputs,
float switches, virtually any device that generates a dry contact closure. The Push
Notification series offers controllers with 1, 2, 4, and 8 contact closure inputs.
We believe this product is the missing link in so many applications. When
combined with our current products such as the WiNet and Fusion series your
imagination really is the limit to what can be done.
How do Push Notification series products work?
PN series products send a packet via TCP or UDP sockets when the status of
their inputs change. They can be configured to send this packet when the input is
open/closed, opened, or closed. Setup of the socket and a breakdown of the
packet will be covered later in this guide.
Chapter
1

2
Getting Started
WiFi Module Configuration
Setup of the WiFi module configures it for connection to your wireless network. It
also specifies where the notification packet it sent. This configuration is very simple
using our NCD Base Station Software.
Things you will need
Push Notification series controller with included WiFi module
WiFi configuration kit (Zigmo configuration board and USB cable)
A windows based computer (XP, 7, or 8)
WiFi Network Setup
Step 1: Install the Wi-Fi module into the WiFi Module Configuration board (Zigmo)
Step 2: Connect USB cable from Zigmo board to computer
Step 3: Install NCD Base Station Software for configuration/testing purposes
Chapter
2

3
http://www.controlanything.com/start
Step 4: Launch NCD Base Station Software. On the Select Connection window that
appears click the drop down menu under com port, select the USB Serial port which
was created when the Zigmo board was connected to the computer. Make sure
Baudrate is set to 115200. Click the More button in the upper right corner of the
window to expand it. Click the MirCC WiFi Module Setup button.
Step 5: The MirCC WiFi Module configuration window will read the stored settings in
your module at launch. These settings need to be changed for your particular network.
Making sure the WiFi module is within wireless range of the network you wish
to attach it to click the Scan for Networks Button. A window will pop up
displaying all wireless networks within range, select the network you wish the
module to connect to, then click the Select button.
Type the passphrase for your WLAN network in the Enter Network
Passphrase box.
Enter a device name in the Enter Device Name box if you wish.
Enter the TCP port you wish the module to listen on in the Device Local TCP
Port box (this will be used for connecting to the module and reading its input’s
status if needed).
We recommend that you leave the Join Network On Power Up box checked,
this means as soon as the module powers up it will associate with the network
stored. Alternatively if you do not check this box it will only connect to the
network when it needs to transmit data.
You can enable a socket connection timeout on the module which is
recommended by checking the Enable TCP Socket Timeout, then type a
timeout duration in the box that appears in seconds. When enabled the
module will forcibly close any TCP socket connections after no data is
transmitted or received for the specified period of time.
Select DHCP or Static IP. DHCP is recommended whenever possible but you
may store a static IP address into the controller if desired. If you do not know
what a Static IP address is leave DHCP enabled.
This concludes configuration of the module for your WLAN. Don’t press the Save to
WiFly button yet though.
Step 6: Now we will configure where the controller is to transmit its input status on
change. There are two main methods for this (TCP or UDP). IF the module will be
transmitting its data to a remote server or if security is a concern TCP should be used.
UDP is a good solution if multiple devices on the network need to receive information
(UDP Broadcast).

4
TCP Notification Setup
Select the Send Notification via TCP radio button. A window will appear allowing
you to enter the destination IP address and Port Number. A listener application will
need to be present at that location listening on the specified port number.
UDP Notification Setup
Select the Send Notification via UDP radio button. A window will appear with
three variables: a checkbox for Use UDP broadcast, a Server IP, and a Port. When
Use UDP broadcast is checked and device on the network can receive the broadcast
since the IP is set to 255.255.255.255. When not checked you must specify a
specific Server IP address. A port number must be specified in the Port text box,
your listener application(s) will need to listen for USP broadcasts on this port
number.
Step 7: Click the Save to WiFly button. You will see several commands exchanged
between Base Station and the WiFi module in the Log window. At the end you should
see Associated, and then farther down a line that says IP = the address next to this line
will be the IP address of your module. If a Static IP address was assigned it will say
using specified static IP. You should also now see the Green LED on you WiFi
module flashing slowly which means it is associated with your network.
Step 8: Close Base Station. Disconnect the Zigmo from your computer. Remove the
WiFi module from the Zigmo configuration board. With no power applied install the
WiFi module into your Push Notification series controller, then to apply power using a
regulated 12VDC power supply (see Power Supply specifications section under
Hardware Reference for more info on Power supply requirements). You should see
the busy and ready LEDs on the PM controller turn on solid initially, after a moment
you will see them flash as well as the amber LED on the WiFi module, once this
flashing stops and the Ready LED on the controller turns on solid you are ready.

5
Initial Testing
Step 9: (This will only work if the module was configured for UDP broadcast or if this
is done on the computer specified as the server IP). For testing purposes open Base
Station once more on a windows computer connected to the same network as the PN
controller. Click the More button in the upper right corner of the select connection
window. Click the Com Operator button which appears below. When asked to
register you can specify register later. Click the Chain icon button in the upper left
corner of Com operator to open a new connection. If you set the module up for UDP
broadcast click the UDP tab, enter the port number specified as the notification port in
the WiFi module in the Listen Port box, then click OK. If you setup the module for a
TCP socket connection click the TCP Server tab and enter the port number specified
during setup as the server port number is the Listen port box and click ok. You will
now see a send/receive window. Trip and input on the controller using a dry contact
and you should see data received in Com operator. This concludes the setup of your
controller.

6
Hardware Reference
Compatible Sensors (Understanding Inputs)
Warning
Users must NEVER apply any voltage to an input on PM
series product!
Inputs are for dry contact closures only!
Inputs are capable of reading Contact Closure generating
devices such as buttons and switches. A wire connected
from the ground terminal to the input terminal would
trigger in the input, as this would be considered a contact
closure. Any device that generates a dry contact closure
can be used to trop the inputs on PM series controllers.
Push Notification Inputs play a vital role in the use of a
PM series controller. Before we begin using the controller,
it is essential that users understand the role of these inputs.
Improper use of these inputs can cause Irreparable
Damage to the PM controller.
Power Supply Specifications
PM controllers require a 12VAC or 12VDC power supply to power the logic and
relays of the controller. The PWR12 is our stock power supply suitable for use with
ALL PM Series controllers. While it is possible to operate from an automotive 13.8V
power supply, higher voltages are not recommended. Additional power filtering may
be required for proper operation in automotive electrical systems. The absolute
minimum recommended operating voltage is 11VAC or 11VDC. PM controllers
require approximately 100ma for standby and 60ma for each activated relay.
Communication Modules may require up to an additional 240ma, this is documented
on the Electrical Specifications Page.
Power polarity is not important on the PM Series controllers. There is no positive or
negative terminal. Simply apply power to the controller as it is convenient to make
wired connections. The PM controller will rectify your power supply and attempt to
filter noise to safe levels for proper operation.
Chapter
3

7
Environmental Specifications
Certain components of a PM controller may run at temperatures exceeding 120°
Degrees Fahrenheit. This is normal for a PM controller and does not indicate a defect.
The recommended operating temperature for all PM controllers is -25 to +85°C. This
temperature rating is based on temperature specifications of the components used to
build a PM controller and is not based on actual testing. We have speculated that PM
controllers may be able to withstand lower temperatures due to the fact that PM
controllers tend to have hot components in critical areas of the design.
Break-Away Tabs
Physically, most MirC controllers are actually 2 sizes. When you receive your
MirC, the unusual shape and size ensures the MirC can fit into a standard
enclosure. Optionally, you can make the controller smaller by breaking away the
out tabs. Break Away tabs are useful in applications where space may be a
concern. This allows your MirC to offer the same functionality in the smallest
possible profile. Break Away tabs are unique to the NCD product line and are a
standard option for most devices released in 2010 and later.
Before breaking the tabs on your controller, please be advised that your MirC
controller will not be returnable for refund or credit if the Break Away Tabs have
been removed.
To break away the tabs, gently but firmly grab each break-away tab with a pair of
pliers and bend the tab back and forth until it breads away from the main circuit
board. This will NOT damage the controller in any way.
Breaking the Tabs from a controller DOES NOT VOID the warranty. Please see
the NCD return policy if you would like more information on the policies that
apply to Surface Mount devices.

8
Communication Overview
Sensor Packet Breakdown
The packet transmitted by the controller contains 22 bytes of data. Below is a
breakdown of the packet:
Byte Position
Byte
0
1
2-3
4-9
10-17
18
19
20
21
Data
Type
Header
ID
F. ver
MAC
User
Def.
Status
Type
Prior
state
Current
state
Chk
sum
Byte 0 is a header byte. This will always be 180 for PN series products.
Byte 1 is a transmission id. This id will increase 1 increment for each broadcast
sent by the controller. Note that this will reset after power cycle.
Bytes 2-3 indicate the controller’s firmware version. 01 00 would indicate v1.0
Bytes 4-9 indicate the WiFi module’s Mac address. Convert these bytes to
Hexadecimal bytes for Mac format.
Bytes 10-17 are user definable. This can be used for any purpose required by the
customer. These bytes can be customized under Scratch pad memory in Base
Station.
Byte 18 indicates the transmission data type. For current PN products this will be
1 indicating this is the status of contact closure inputs.
Byte 19 indicates the status of inputs prior to the input status change which
triggered this notification.
Byte 20 indicates the status of inputs after the input status change which triggered
this notification.
Byte 21 is a checksum for the whole packet. See API Codec guide which explains
how this check sum is calculated.
Chapter
4

9
Direct query command set
The only command required for this product is to query the status of the inputs if
needed. This may need to be done after a server reboot in order to get the current
status of inputs on the controller. This will be done via a TCP socket connection
to the controller’s IP address on the port number configured in the Listening Port
field during WiFi module setup in Base Station. While these are technically A/D
inputs we are simply using them as contact closure inputs. All inputs are pulled
low on the controller so if the input is not tripped its value will be 0. When the
input is tripped it will be pulled high and its status will be 255. It is recommended
that you assume any input above 200 is tripped with a contact.
Reads the 8-Bit Analog Input of Channels
This command will read the Analog Input value of the specified input and return a
value from 0-255.
Send Bytes: Byte 1: Byte 2:
Function: Command Parameter (Channel 1-8)
Decimal Values: 254 150-157
Hex Values 0xFE 0x96 - 0x9D
Receive Byte:
Decimal: 0-255
Hex: 0x00-0xFF
Multi Channel 8-Bit
Reads all 8 Analog Input Channels and replies with 8 bytes indicating the 8-bit
value of each Analog Input.
Send Bytes: Byte 1: Byte 2:
Function: Command Returns AD1 - AD8
Decimal Values: 254 166
Hex Values 0xFE 0xA6
Receive Byte:
Decimal: 0-255 (AD1-AD8)
Hex: 0x00-0xFF

10
Advanced Configuration
Input Configuration
Inputs on PN series controller can be configured to send notifications when the
input is opened or closed, only when they are closed, or only when they are
opened. This configuration is done through Base Station as follows:
Step 1: Open Base Station, Select the Network Radio button on the Select
Connection window. Enter the IP address of the WiFi module in the IP address
text field. Enter the Port defined as the TCP Listener port in the WiFi module(by
default this is set to 2101). Then click the OK button below.
Step 2: Base Station will communicate to the controller and display a window with
control software options. Select AD8 Relay Activator/Event Generator.
Step 3: The AD8 Relay Activator/Event Generator window will now be
displayed. You will notice that each input can be tied to a function. The
functions are labeled for controlling relays but just know that rather than switch a
relay we will be triggering the notification. Inputs should only be set to
momentary or toggle at this time. If Input 1 function is being configured you may
set to to Momentarily Control Relay 1 or Toggle Relay 1. Do not set it to any
other feature or set it to a different relay number as this will cause confusion.
Step 4: Once
settings are
configured
click the save
settings button
in the bottom
right corner to
save the
changes to the
controller.
Chapter
5

11
User Definable Transmitted Bytes
8 bytes in the Notification packet are definable by the user. These bytes can be
used in any way required by the user. Configuration of these bytes is done using
Base Station as follows:
Step 1: Open Base Station; Select the Network Radio button on the Select
Connection window. Enter the IP address of the WiFi module in the IP address
text field. Enter the Port defined as the TCP Listener port I the WiFi module (by
default this is set to 2101). Then click the OK button below.
Step 2: Base Station will communicate to the controller and display a window
with control software options. Select Scratchpad Memory Command Set.
Step 3: A new window will appear with 8 byte positions. The user may change
any of the 8 bytes as required.
Step 4: After configuration is complete click the Store Above Data into
Scratchpad Memory to store the changes into the controller.

12
Troubleshooting
Problem: Zigmo device does not appear in drop down Com Port box in Base
Station.
Fix: Make sure USB cable is good. USB LED on Zigmo should be on solid. If
not download driver from FTDI here:
http://www.ftdichip.com/Drivers/CDM/CDM20830_Setup.exe
Problem: WiFi module will not associate with network.
Fix: Make sure the Network SSID does not contain a Space such as My Network
(This should be changed to My_Network). Temporarily disable network security,
there are known compatibility issues between WiFly modules and WPA security.
Problem: Broadcast transmission from controller is not received on
server/computer.
Fix:
Make sure you do not have any type of antivirus software which could
block TCP/UDP sockets (McAfee is known for this).
Windows firewall can also sometimes block these socket connections, you
can open a port number in Windows Firewall under configuration.
Check Settings in module for server connection. Ensure server is listening
on the transmit port used by the controller.
Make sure WiFi module is associated with network, the flashing green
LED on the module indicates valid connection with the network.
If server/computer is on a remote/sub network (separate network from
the module) make sure port forwarding is configured correctly.
Make sure sensor connected to controller is functioning properly using a
continuity tester (volt meter).
Chapter
6

13
Technical Support
echnical support is available through our website, controlanything.com.
AccessNCD is the way we connect NCD engineers to our customers.
Click on the AccessNCD button located on the top right of the header of
each page of our website.
For technical support and application information, contact Travis Elliott, our
technical engineer. If you feel that you have discovered a bug in the firmware of
our controllers, contact Ryan Sheldon, our hardware developer. If you have
programming-related questions or have discovered a bug in our software, please
contact Shirui Xu, our software engineer.
Click the ‘Tech Support Staff’ tab and click on the appropriate engineer link for assistance.
Click on our ‘Forum’ tab if you would like to post publicly or review problems that other
customers have had and our recommended solutions.
Chapter
7
T

14
Our engineers monitor questions and respond continually throughout the day.
Before requesting telephone technical support, we ask that customers please try to
resolve their problems through AccessNCD first. However, for persistent
problems, NCD technical support engineers will schedule a phone consultation.
Contact Information
National Control Devices, LLC
PO Box 455
Osceola, MO 64776
417-646-5644 phone
866-562-0406 fax
Open 9 a.m. - 4 p.m. CST
All orders must be placed online at our website, www.controlanything.com
Notice:
The only authorized resellers of NCD products are
www.controlanything.com
www.relaycontrollers.com
www.relaypros.com
www.amazon.com
All other websites are not authorized dealers; we have noticed some retailers
offering our products fraudulently.
Copyright © 2013
National Control Devices
All Rights Reserved.
This manual suits for next models
3
Table of contents
Other NCD Network Hardware manuals
Popular Network Hardware manuals by other brands
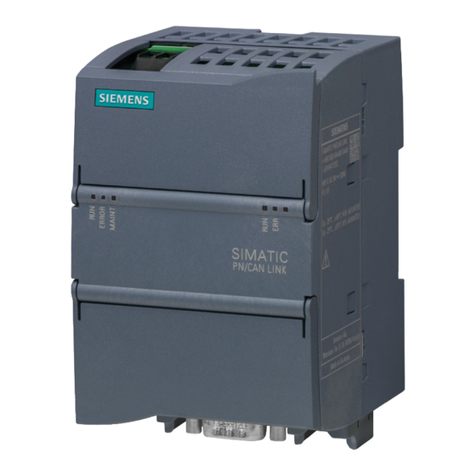
Siemens
Siemens SIMATIC PN/CAN LINK operating instructions
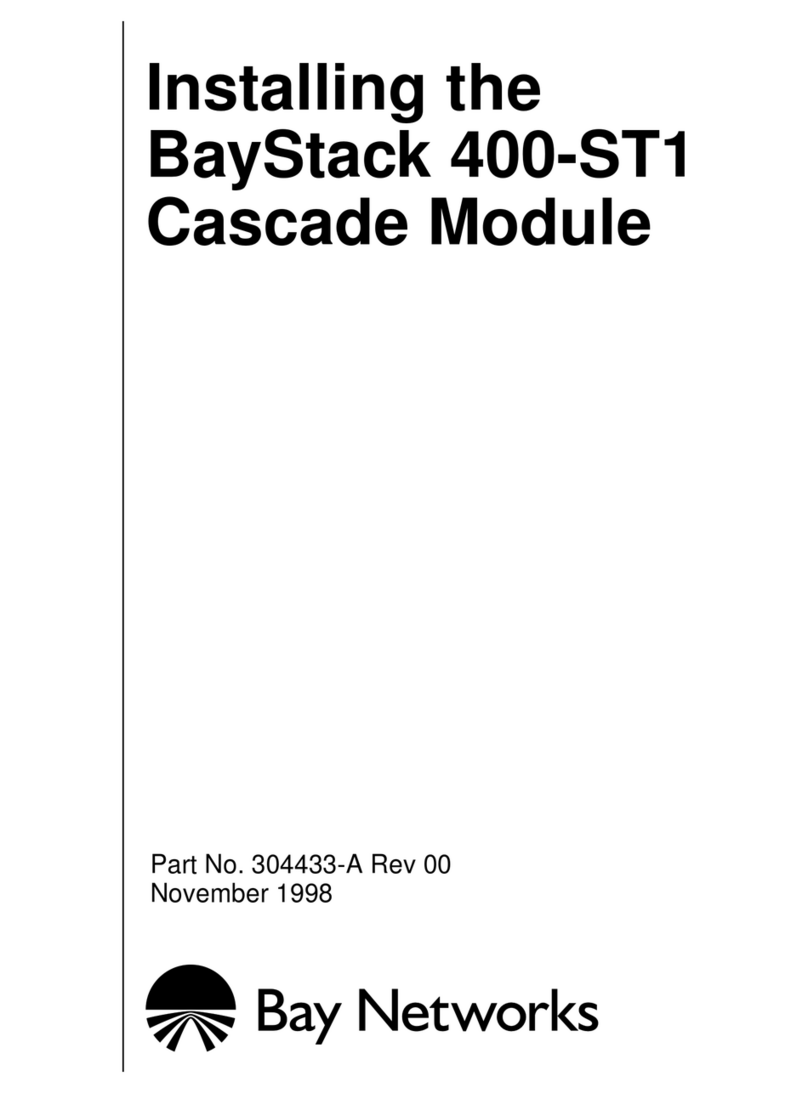
Bay Networks
Bay Networks BayStack 400-ST1 installation manual
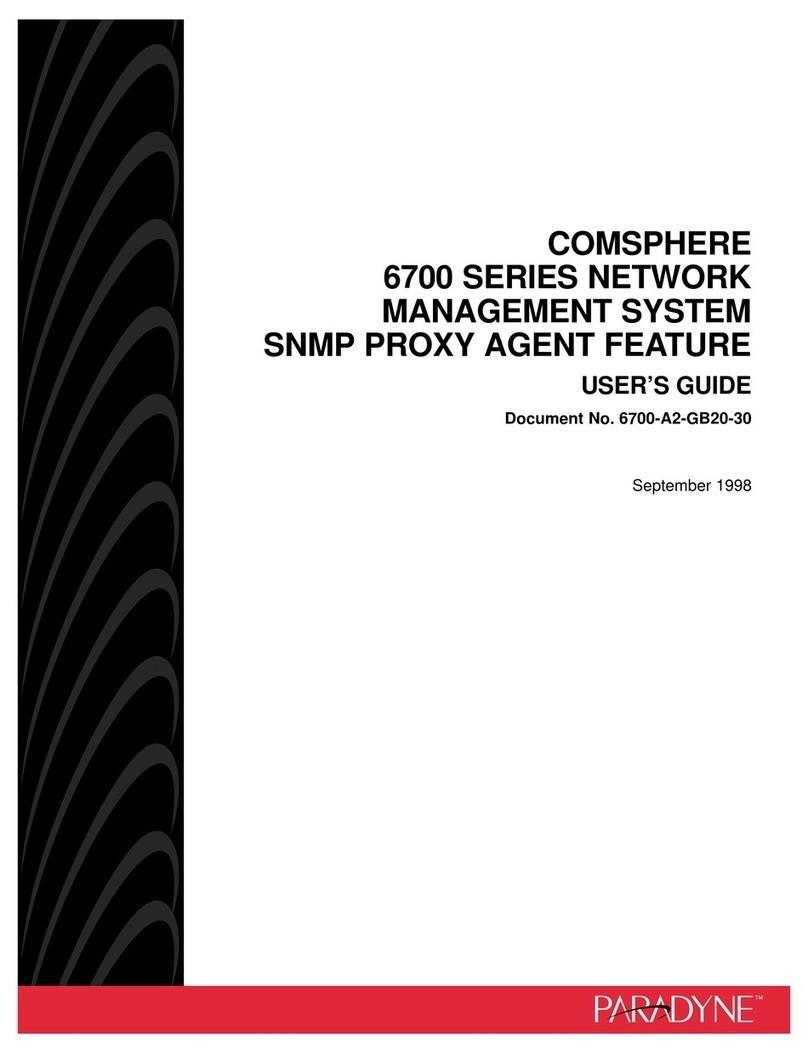
Paradyne
Paradyne COMSPHERE 6700 Series user guide
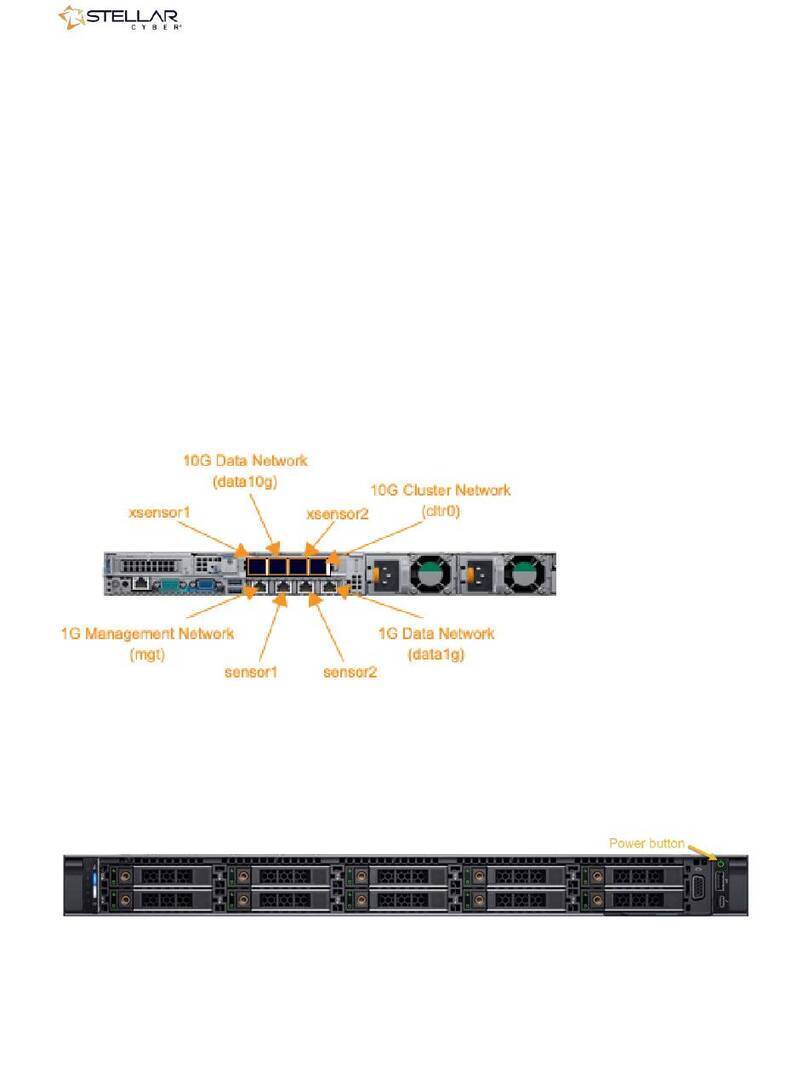
Stellar Cyber
Stellar Cyber 3000C quick start
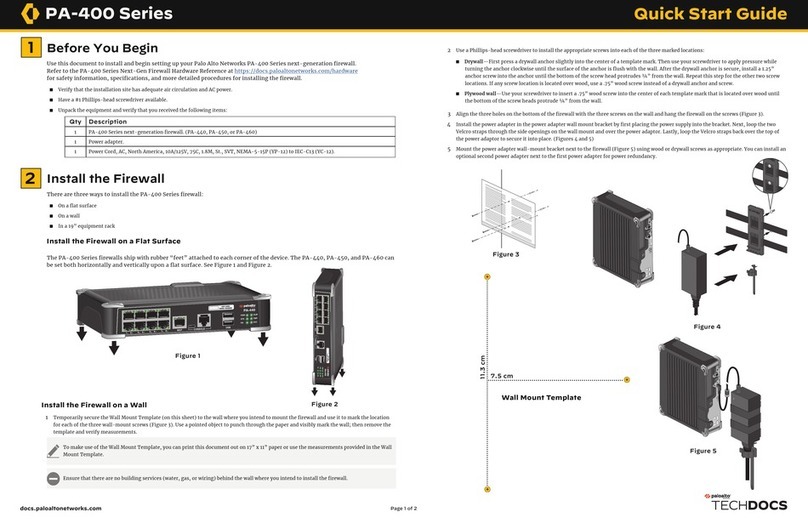
PaloAlto Networks
PaloAlto Networks PA-400 Series quick start guide
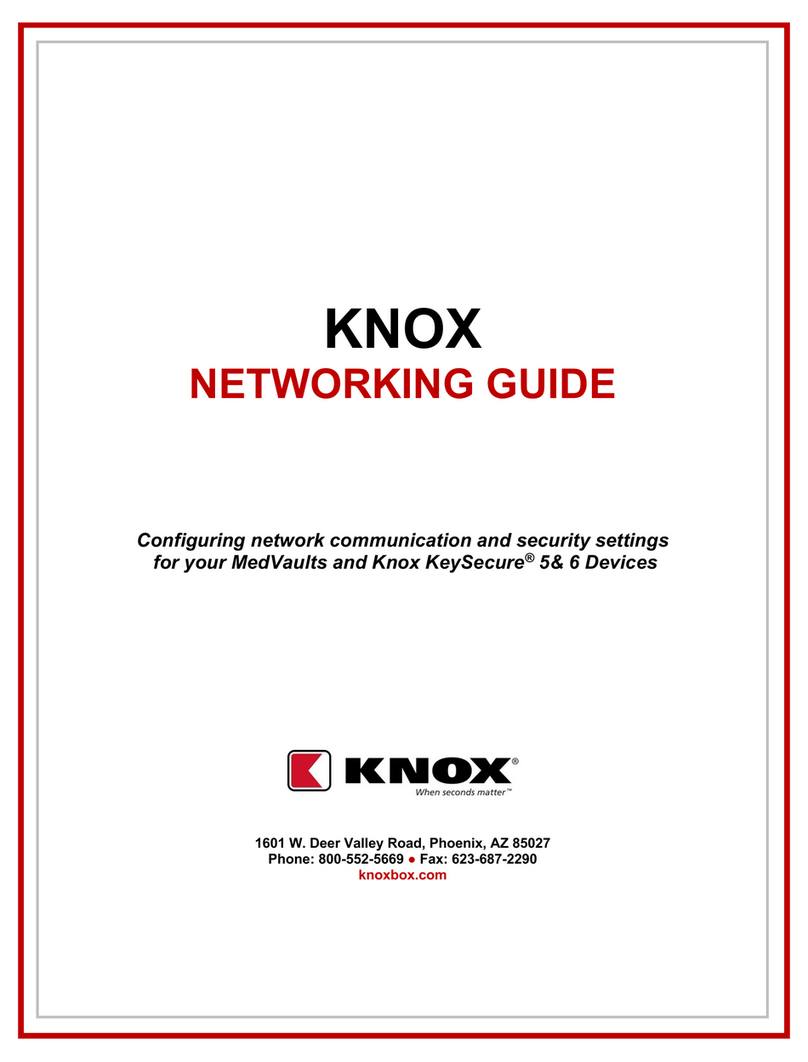
Knox
Knox KeySecure 5 Networking guide
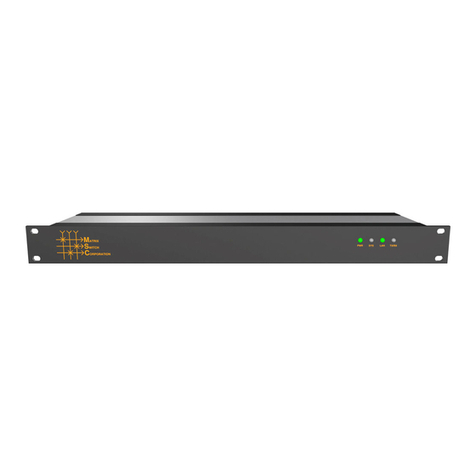
Matrix Switch Corporation
Matrix Switch Corporation MSC-HD121AAS product manual
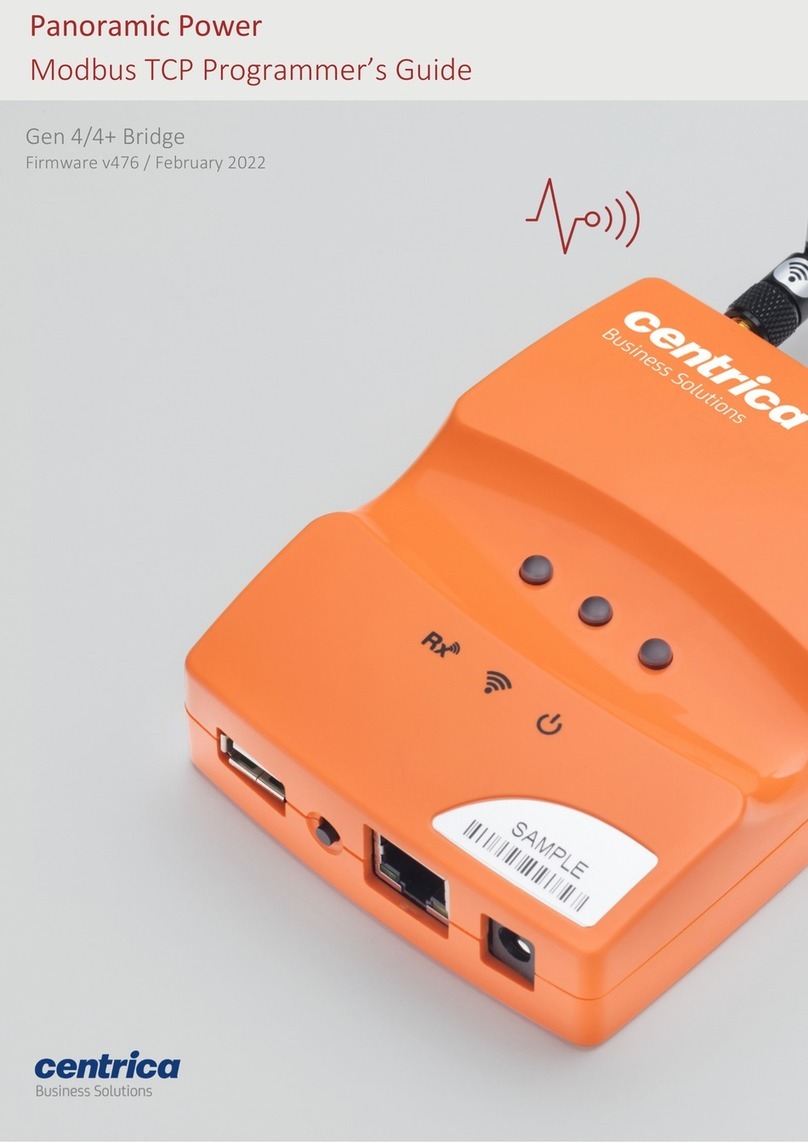
Centrica
Centrica Panoramic Power Programmer's guide
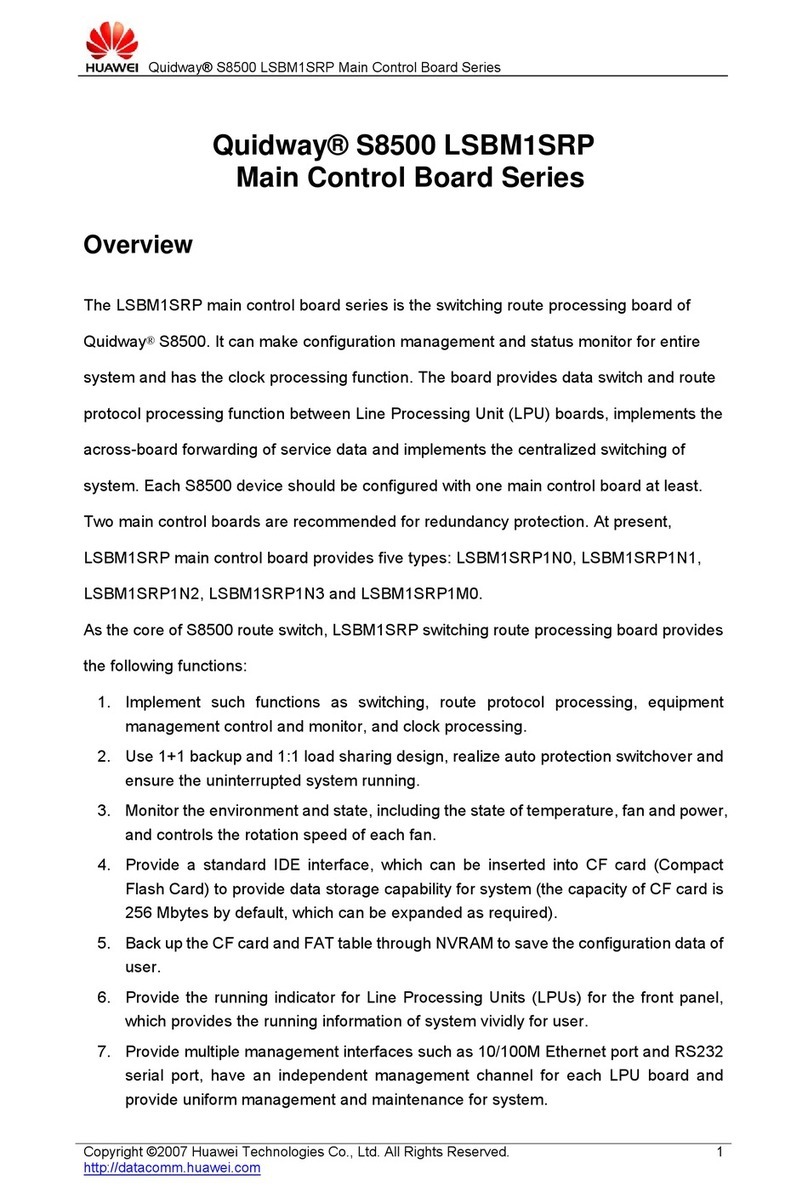
Huawei
Huawei LSBM1SRP Specifications
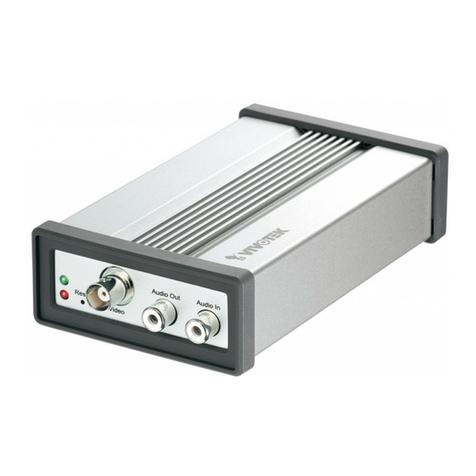
Vivotek
Vivotek VS7100 Quick installation guide
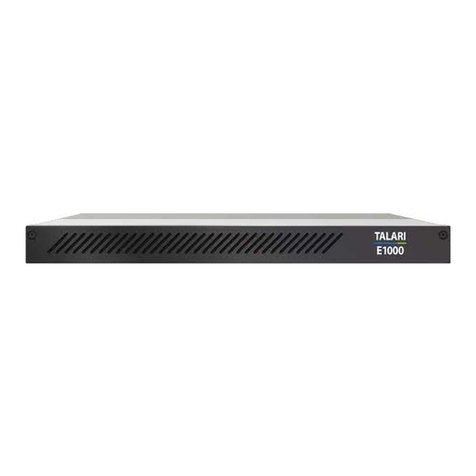
Oracle
Oracle Talari E1000 installation guide

Renkforce
Renkforce 1713217 operating instructions