NDW BC50 User manual

BC50 Motor Controller
Product Manual
02.06
11-10-2019

NDW | We’ll keep you rolling | 2
Manufacturer details
NDW
Sluisweg 32,
5154 PE Waalwijk,
The Netherlands
T: +31 (0) 416 67 44 44
www.ndwrollers.com
Condentiality & Duplication
The contents of this document must be treated confidentially. It is prohibited
to distribute or copy this document or parts of this document in any form
(photography, photocopy, recording or any other distribution method)
without the approval of NDW in written form.
Disclaimer
The information in this document is related to designed products and services
developed and owned by NDW. However, no intellectual property, licensing
or patent rights are granted with this document. If in the general terms and
conditions has been described that such intellectual property, licensing or
patent rights have been granted, this will overrule the disclaimer statement
above. Furthermore, all other disclaimers can be found in the general
terms and conditions. NDW reserves the right to change the document,
specifications and product descriptions at any time without further notice.
However, NDW is not committed to change or update the information in this
document. NDW has used all possible eorts to ensure the information in this
manual is precise and correct. However, NDW cannot be held responsible for
any errors, missing information or damages, direct and/or indirect, resulting
from procedures or information related to this document.
Table of contents
INTRODUCTION 4—5
PRODUCT INFORMATION 6—9
TRANSPORT AND STORAGE 10
ASSEMBLY 11—14
INITIAL STARTUP AND OPERATION 15
QUICK START GUIDE FOR CONFIGURING THE BC50 16—17
SETTINGS 18—24
CLEANING AND MAINTENANCE 25
TROUBLESHOOTING 26
REMOVAL AND DISPOSAL 26
ACCESSOIRIES/ NOTES 27
DECLARATION OF CONFORMITY 28

NDW | We’ll keep you rolling | 4
NDW | We’ll keep you rolling | 5
Contents
This manual contains important product information of the NDW BC50 motor
controller. It provides the intended use, integral safety measures and guides
for servicing, transport and storing conditions. Also, technical support for
installation, maintenance and troubleshooting is provided.
This guide is part of the product. Therefore, the product cannot be used
without consulting the guide prior to installation or use.
General Safety Measures
The BC50 motor controller has been designed and configured in order to
meet safety standards when in operation. However, risks may still occur.
Therefore, it is important to study and follow the manual prior to usage.
• For optimal and safe use of the system it is required to study and follow
the manual.
• Keep this manual in a safe and visual location near the system.
• The supplier cannot be held responsible for faults and defects that would
have been avoided by following this manual.
• The supplier cannot be held responsible when changes are made and/or
added to the system which has not been described and/or allowed in
the manual.
• Do not use the system when one or more components are damaged
or malfunctioning.
• Questions concerning the manual can be addressed to NDW located
in Waalwijk.
Dangers
While working with the BC50 motor controller, certain dangers may occur.
This list provides the general dangers that may happen and instructs on how
to avoid accidents:
• Maintenance and repair may only be executed by authorized and qualified
personnel according to the appropriate national safety regulations.
Otherwise serious bodily injury may arise.
• Before initiating or using the BC50 controller, make sure all unauthorized
personnel has cleared the working area of the conveyor.
• Make sure the BC50 controller is only operated with control voltages
compliant with a SELV environment.
• The power must always be switched o when maintenance or installation
work is performed on the BC50 controller. Ensure the power cannot
accidentally be switched on.
• Check for visible damage regularly. Also make sure mounts and screws have
correct tension.
• If you notice any faulty behaviour of the controller or the system,
immediately cut the power and make sure it cannot accidentally be
switched on. Contact qualified personnel in order to perform
troubleshooting.
• Make sure no unnecessary tools or equipment are near the system when
in operation. Tools or screws falling on the conveyor may cause serious
damage to the system.
• When installing or troubleshooting the conveyor system, be aware that
sensors or other signals may be triggered unintentionally, leading to
hazardous situations. Be sure to always turn the power o in an event
of installation or maintenance/troubleshooting.
• Never try to open a BC50 motor controller.
Intended use
The BC50 controller must only be used for industrial applications in an
industrial, dry environment. The controller must be integrated in automated
conveyor modules or systems with NDW motorized E-rollers installed. Any
other use is prohibited. If external tools and machinery are integrated, it is
required to validate the safety before using the system.
Qualied persons
Only qualified personnel are allowed to work with- or integrate the BC50
controller. Qualified personnel are expected to understand this manual
and have knowledge on national safety regulations regarding industrial
appliances. While working with the controller, the following points should be
taken into account by the qualified personnel:
• Relevant diagrams and user manuals of the BC50 motor controller.
• Regulations and requirements that are specific for this product.
• Safety and warning instructions as provided by this document.
• National and/or local safety regulations.
INTRODUCTION

NDW | We’ll keep you rolling | 6
NDW | We’ll keep you rolling | 7
Product description
The BC50 motor controller is designed to control the NDW motorized
E-rollers. It is created to control both the speed and the direction of the
E-roller through a user-friendly interface or controlled with an external I/O
control device.
User friendly interface
The BC50 controller has a user-friendly interface, which makes it easy to
change the settings on the controller. A graphical user interface (UI) and
straightforward buttons can be used to change the settings. As a result,
no DIP switches are required on this controller. In the user manual all the
dierent settings and how to change them is explained.
Overvoltage protection
The BC50 controller is equipped with a protection against induced
overvoltage of the motorized E-roller when it acts as a generator.
Stall protection
When the rotation of the motor is blocked, the controller will initiate a stall
protection to protect the E-roller. The controller will try to resolve the stalled
motor for a couple of times. When the motor remains stalled, the controller
will display an error message on the screen and send an I/O error signal.
Control modes
The BC50 controller can be controlled in two modes: Manual and I/O-mode.
In Manual mode the user can operate the complete E-roller (Run, Direction,
Speed) by simply using the integrated buttons and UI. In I/O-mode the
operational settings of the E-roller can be controlled via external I/O, giving
the user more control during operation of the controller.
PRODUCT INFORMATION
BC50 Motor Controller
Control Modes
Manual mode
• Control with integrated UI
• Control motor Run, Direction and Speed
• Useful during initial testing
• Use for simple integrations
Manual I/O
I/O mode
• Control with external I/O signals
• Control motor Run, Direction and Speed
• Use for more complex integrations
1
E-roller connection
2
3
4
15
6
2
Mounting brackets
3
Graphical user interface
6
Power supply connection
5
I/O communication connection
4
Navigation buttons
Surface finish:
Deburr and break all sharp edges
NAME
DATE
Material:
3D file is leading
Revision:
Title:
Drawing name:
SCALE:1:1
SHEET 3 OF 3
A3
TvL
TvL
11/09/2019
11/09/2019
Budget_Asm_R01
R01
Weight [kg]:
According to ISO 2768-mK unless
specified otherwise
Drawn by
Checked by
Tolerances:
All units are in mm unless specified otherwise
Remarks
A A
B B
C C
D D
E E
F F
8
8
7
7
6
6
5
5
4
4
3
3
2
2
1
1

NDW | We’ll keep you rolling | 8
NDW | We’ll keep you rolling | 9
Technical Data
Rated voltage 24Vdc
Voltage range 18Vdc to 26Vdc
Current consumption (idle) 0.1A
Current consumption (max load) 2A (1)
Startup current limit 2A (2)
Power consumption (max load) 50W (1)
Number of motorized E-roller connections 1
Protection rate IP20
Ambient temperature in operation 0 ˚C to +40 ˚C, non-condensing
Compatible NDW E-rollers ER-Series: 100, 200, 400 RPM
Speed and direction control Graphical UI or via external I/O (PLC)
Stall protection for E-roller Yes
Overvoltage protection for E-roller Yes
Compatibility PNP and NPN
Signaling Graphical UI and Error signal (I/O)
Dimensions 133 x 55 x 27 mm
Max installation height 1000 m
1. Actual power consumption depends on the application conditions, such as actual load, section length, slope etc.
2. A very short current peak of <40ms will occur during startup of the E-roller.
Scope of delivery
The delivery of the BC50 motor controller contains the following parts:
• BC50 motor controller
• Optional*:
• E-roller extension cable
(order code: 901-CABMOT-L)
• Open end power cable
(order code: 901-CABP24-1-L)
• Open end IO cable
(order code: 901-CABCOM-1-L)
*Can be ordered separately.
The “L” stands for required length. Available in dierent standard lengths.
Custom lengths can be made on request. A full overview of accessories in
shown on page 27.
Dimensions
Label
26,5 40,6
122,0
133,0
113,3
5 (2x)
BC50 - Budget controller
Mounting dimensions
Surface finish:
Deburr and break all sharp edges
NAME
DATE
Material:
3D file is leading
Revision:
Title:
Drawing name:
SCALE:1:1
SHEET 1 OF 3
A3
TvL
TvL
11/09/2019
11/09/2019
Budget_Asm_R01
R01
Weight [kg]:
According to ISO 2768-mK unless
specified otherwise
Drawn by
Checked by
Tolerances:
All units are in mm unless specified otherwise
Remarks
A A
B B
C C
D D
E E
F F
8
8
7
7
6
6
5
5
4
4
3
3
2
2
1
1
1
2
3
BC50 Motor Controller
NDW101AAABBBB
YYYY/WW
NDW
Sluisweg 32
5145 PE Waalwijk, Netherlands
www.ndwrollers.com
101 = Product code
AAA = Batch number
BBBB = Unique serial number
YYYY = Year
WW = Week number
4 5 6
BC 50 Motor controller sticker
1
2
3
4
5
6
Manufacturer
Product name
Contact information
Week and year of production
Unique serial number
CE certification mark
NDW BC50 Motor controller label guide
Original size:
BC50 Motor Controller
NDW101AAABBBB
YYYY/WW
NDW
Sluisweg 32
5145 PE Waalwijk, Netherlands
www.ndwrollers.com
This guide explains how to make the labels for the NDW BC50 Motor Controller using
the corresponding “NDW BC50 label.ai” Illustrator file. Numbers 1, 2, 3 and 6 are fixed,
numbers 4 and 5 should be filled in according to the product, the batch and the produc-
tion week.

NDW | We’ll keep you rolling | 10
NDW | We’ll keep you rolling | 11
TRANSPORT AND STORAGE ASSEMBLY
Transport Warning notice concerning assembly
and electrical installation
Not following the safety instructions might lead to failure or shortened
lifetime of the BC50 controller.
Ambient conditions for Storage
Permissible ambient temperature -20 �C to 60 �C
Permissible relative humidity 5% to 95%, non-condensing
Permissible ambient temperature -20 �C to 60 �C
Permissible relative humidity 5% to 95%, non-condensing
Each BC50 motor controller is separately packaged in a cardboard box.
The transport of the controller must be executed by qualified personnel
only. A risk of injury persists when transporting the product incorrectly. The
instructions below must always be followed during transport:
• Not more than four boxes may be stacked on top of each other. This is due
to the risk of tipping over stacked boxes, potentially resulting in a
damaged product.
• Before transportation, make sure that each box is properly fixed.
• Every package should be checked for damage and completeness according
to the “Scope of Delivery” (page 8).
• Impacts on the product must be avoided at all times.
• If any damage occurred during transportation, you are advised to take
photos that will serve as evidence. Immediately report the damage to
the transport company and NDW otherwise compensation cannot
be guaranteed.
• Prevent significant temperature fluctuations while transporting the BC50
controller, since this may lead to condensation, causing serious damage
to the product.
Safety instructions
• Do not drop or otherwise physically mishandle the controller to avoid
internal damage.
• Before assembly check each controller visually for damage.
• Only qualified and authorized personnel should perform electrical work.
• Before installing or making any changes to the wiring of the controller
disable and disconnect the power supply.
• Make sure that the connections and the housing never come in contact with
any hazardous voltages, not even during the malfunction of a controller.
• Do not connect AC current to the E-roller or the controller at any time, as
this will cause irreparable damage to the device.
• The motor plug should be handled with care. Applying too much tension
or load could potentially damage the cable which could lead to failure of
the E-roller.
• Make sure that there is no interference between any existing electrical
installation and the controller or E-roller.
• Make sure that all cables used are the right dimensions for the application.
• Ensure that the power supply unit delivers a nominal DC voltage of 24 V
to the controller.
• Both the E-roller, the controller and the voltage source should be connected
to a conveyor frame or supporting structure in such a way that they
are properly earthed. Earthing incorrectly could potentially result in the
build-up of static charge, causing both the E-roller and the controller to
malfunction.
• Only use the specified connectors.
• Only when all cables have been connected the operating voltage should
be applied.
While storing the BC50 controllers, ensure no more than four boxes are
stacked on top of each other, as this may result in tipping over and possibly
damaging the product. When a controller is taken out of storage, please
inspect for damage prior to usage.

NDW | We’ll keep you rolling | 12
NDW | We’ll keep you rolling | 13
Mounting the controller
• Locate a flat surface to mount the BC50 controller.
• Mark the center for the two mounting holes using the BC50 controller as
a template.
• The precise dimensions and distance between holes can be found in the
dimensions page.
• Drill two mounting holes at the marked spots. Mount the BC50 controller.
• Make sure the mounting surface and bolts are properly earthed.
Electrical installation
Connection of the power
The BC50 controller is powered by an external 24V power supply. Choose
a power supply that is suciently powerful for the number of E-rollers and
their application.
The use of standard NDW 24V power cables is recommended. Order code:
901-CABP24-1-L.
The “L” stands for required length. Available in dierent standard lengths.
Custom lengths can be made on request. A full overview of accessories is
shown on page 27.
The 24V power cable must be plugged into the green connector on the BC50
controller. Make sure the polarity of the power cable is correct.
Connection of the communication cable
The BC50 controller can operate in stand-alone mode by using the integrated
user-interface to control the E-roller. If external I/O control is required, the
communication cable must be connected. Via this cable, the controller can
be controlled with external I/O signals. For example, using a PLC or similar
device.
The use of standard NDW communication cables is required. Order code:
901-CABCOM-1-L.
The “L” stands for required length. Available in dierent standard lengths.
Custom lengths can be made on request. A full overview of accessories is
shown on page 27.
Surface finish:
Deburr and break all sharp edges
NAME
DATE
Material:
3D file is leading
Revision:
Title:
Drawing name:
SCALE:1:1
SHEET 2 OF 3
A3
TvL
TvL
11/09/2019
11/09/2019
Budget_Asm_R01
R01
Weight [kg]:
According to ISO 2768-mK unless
specified otherwise
Drawn by
Checked by
Tolerances:
All units are in mm unless specified otherwise
Remarks
A A
B B
C C
D D
E E
F F
8
8
7
7
6
6
5
5
4
4
3
3
2
2
1
1
Type Connector Cable specification Remarks
24Vdc power cable Phoenix: 1754568 2x1 mm²Use 1 mm²ferrules
Type Connector Cable specification Remarks
Communication cable JST-PHR-7 7x0.14 mm²-
124VDC
2Ground
Power Supply Connection
1
2
6
124VDC
2Ground
Power Supply Connection
1
2
6
1O / Speed 1
2Speed 2 / SPeed 3
3Direction
I/O Connection
1
23
45
67
4Error
5Ground
6Digital A
7Digital B
5
1O / Speed 1
2Speed 2 / SPeed 3
3Direction
I/O Connection
1
23
45
67
4Error
5Ground
6Digital A
7Digital B
5
ID Name Type Parameters
1O / Speed 1 Input
2Speed 2 / Speed 3 Input
3Direction Input
4Error Output Outputs: ≤10mA
“inactive <2V” / “active” > 22V (PNP)
“active <2V” / “inactive” > 22V* (NPN)
*For NPN: requires pull-up at PLC or IO device.
5Ground Ground
6Digital A (Not used) -
7Digital B (Not used) -
24Vdc (PNP or NPN)
Inputs: “inactive” ≤3V / “active” ≥6V (PNP)
“active” ≤3V / “inactive” ≥6V (NPN)
All inputs and outputs are galvanically isolated from the external 24Vdc power supply.
Therefore, the ground connection (ID5) must always be connected when using I/O control.
Surface finish:
Deburr and break all sharp edges
NAME
DATE
Material:
3D file is leading
Revision:
Title:
Drawing name:
SCALE:1:1
SHEET 4 OF 5
A3
TvL
TvL
19/09/2019
19/09/2019
BC50_Asm_R02
R01
Weight [kg]:
According to ISO 2768-mK unless
specified otherwise
Drawn by
Checked by
Tolerances:
All units are in mm unless specified otherwise
Remarks
A A
B B
C C
D D
E E
F F
8
8
7
7
6
6
5
5
4
4
3
3
2
2
1
1

NDW | We’ll keep you rolling | 14
NDW | We’ll keep you rolling | 15
M8-5pin Adapter cable
If desired, it is possible to order an adapter cable that combines the 24V
power and communication cable to a standard M8-5pin connector which
allows for integration with existing electrical infrastructure and control
platforms (i.e. ASI, B&W, P&F, MOLEX etc).
Order code: 901-ADP-B-SC/SN. A full overview of accessories is shown on
page 27. For more information, please contact NDW.
Connection of the NDW E-roller
The NDW motorized E-roller can directly be plugged into the BC50 controller.
Use the screw connection to fixate the cable.
If required, the cable of the E-roller can be extended using NDW motor
extension cables. Order code: 901-CABMOT-L. Only use original NDW motor
extension cables since they guarantee the required ratings.
The “L” stands for required length. Available in dierent standard lengths. A
full overview of accessories is shown on page 27.
NOTE: The total length of the E-roller cable may not exceed 6 meters.
Only connect the E-roller when the controller has no power.
310
Available in two configuration:
- M8 screw connection (901-ADP-B-SC)
- M8 snap-in connection (901-ADP-B-SN)
Pin No. 2
Pin No. 5
Pin No. 3
Pin No. 1 Pin No. 1
Pin No. 4
Pin No. 1
Front view of COM connector
Front view of PWR connector
*Required speed must be set on the NDW controller
Front view of M8 connector
Pin No.
Color
Function
1
Green
Off / Spd 1
2
Orange
Spd 2 / Spd 3
3
White
Direction
4
Black
Error
5
Blue
Ground
6
Red
Digital A
7
Yellow
Digital B
Pin No.
Color
Function
1
Red
24V+
2
Black
0V-
Pin No.
Function (901-ADP-B-SC)
Function (901-ADP-B-SN)
1
24V+ 24V+
2
Direction Direction
3
0 V- 0V-
4
Start/Stop (24V+)
Error output
5
Not Used
Start/Stop (24V+)
Surface finish:
Deburr and break all sharp edges
NAME
DATE
Material:
3D file is leading
Revision:
Title:
Drawing name:
SCALE:1:2
SHEET 1 OF 1
A3
TvL
TvL
30/09/2019
30/09/2019
901-ADP-B
R01
Weight [kg]:
According to ISO 2768-mK unless
specified otherwise
Drawn by
Checked by
Tolerances:
All units are in mm unless specified otherwise
Remarks
A A
B B
C C
D D
E E
F F
8
8
7
7
6
6
5
5
4
4
3
3
2
2
1
1
Type Connector Cable specification Remarks
E-Roller cable M8-6pin screw 6x0.25 mm²-
1
1
5
6
3
4
2
1 24V
2 Speed feedback
3 Direction
4 0V
5 Speed control
6 Run / Stop
Motor Connection
1
1
5
6
3
4
2
1 24V
2 Speed feedback
3 Direction
4 0V
5 Speed control
6 Run / Stop
Motor Connection
Surface finish:
Deburr and break all sharp edges
NAME
DATE
Material:
3D file is leading
Revision:
Title:
Drawing name:
SCALE:1:1
SHEET 5 OF 5
A3
TvL
TvL
19/09/2019
19/09/2019
BC50_Asm_R02
R01
Weight [kg]:
According to ISO 2768-mK unless
specified otherwise
Drawn by
Checked by
Tolerances:
All units are in mm unless specified otherwise
Remarks
A A
B B
C C
D D
E E
F F
8
8
7
7
6
6
5
5
4
4
3
3
2
2
1
1
INITIAL STARTUP AND OPERATION
Checks before initial start up
• Make sure that the BC50 controller is mounted correctly and that all the
screws have been tightened.
• Check the area around the controller and the motorized roller to make sure
there are no other components creating dangerous situations.
• Make sure that the wiring is in accordance with the specification and
legal directives.
• Check all protective measurements.
• Check if the motorized roller is properly mounted to prevent damage to the
motor cable due to rotation.
• Check the conveyor system and make sure no personnel stands in
hazardous areas.
Checks before operation
• Check the BC50 controller for visible damage.
• Check all protective measurements.
• Make sure there is no blockage of the E-roller.
• Check the conveyor system and make sure no personnel stands in
hazardous areas.
WARNING!
Accidental start-up of the E-roller
Hazardous situation for both personnel and goods. Make sure no
unauthorized persons are near the conveyor before switching on
the power supply.

NDW | We’ll keep you rolling | 16
NDW | We’ll keep you rolling | 17
QUICK START GUIDE FOR
CONFIGURING THE BC50
Each BC50 controller will be delivered with a default configuration of all
settings (Factory settings). In this section some guidelines will be provided to
ease the initial configuration of the BC50 controller. At any time, it is possible
to restore the controller to its original factory settings if something goes
wrong.
Mount the BC50 controller and connect all required cables such as power,
communication, and E-roller as described in previous sections.
The first step to configure the BC50 controller is to select the type of E-roller
connected. It is important to select the correct Roller Diameter and Motor
Type. This will make sure the E-roller turns at the correct speed. For more
info, see “Speedcode and Diameter” in the Settings chapter on page 22.
Once the correct E-roller is configured, the Direction and Speed Setpoints
must be set. If only a single speed is required for the application, it is
recommended to change Speed Setpoint 1 (SPD1) to the required speed.
If multiple speeds are required, one can set multiple Speed Setpoints. If
desired, you can turn on the E-roller by setting Motor Run to ON. For more
information on setting the Motor Run, Speed and Direction, see the operating
settings on page 17.
If you want to control the BC50 controller with external IO, switch Mode from
Manual to I/O. With this setting active, the controller will actively listen to the
external I/O connections via the communication cable. Note that Motor Run
and Speed Setpoint become unavailable in I/O-mode since these settings are
now controlled with the external I/O.
For more info, see the operating settings on page 17.
When controlling the BC50 without external IO, your device is now completely setup
and ready to use. For control with I/O, please continue to step 3.
Your device is now completely setup and ready to use.
0
1
2
3
Operating settings
All the settings within the BC50 controller can be easily changed using the
user interface on the integrated display. All the settings and how to change
them are explained within this user manual.
Control using I/O
The BC50 controller oers simple control using the I/O connections. These
can be controlled using an external I/O device or power source (24V PNP
or NPN). Settings such as Motor Run, Direction and Speed can be easily
controlled with this. The pins used for this are the O/Spd1-, Spd2/Spd3- and
the Direction-pin. Furthermore, an I/O Error output can be detected with
your I/O device. The I/O connections are electrically isolated, therefore the
Ground-pin must always be connected when controlling the device via I/O.
To control the device with I/O, set Mode from Manual to I/O in the settings.
Direction setting
When the I/O Direction pin is not connected, the Direction can directly be set
in the controller. Alternatively, to control the direction with I/O, use the “
IO-driven” setting to control the direction according to the table. See also
page 21.
Speed settings
One can turn on the connected E-roller and adjust its speed through I/O
connection. Three pre-defined speed set-points can be used. Using the I/O,
one can easily activate one of these setpoints. The dierent I/O combinations
are shown in the table. If only a single constant speed is required, only O/
Spd1 needs to be connected to switch the E-roller on and o.
Direction pin Direction E-roller
Low Clockwise (CW)
High Counter-clockwise (CCW)
Motor type Selectable speed range (50 mm)
100 RPM 0.05 to 0.26 m/s
200 RPM 0.10 to 0.52 m/s
400 RPM 0.20 to 1.04 m/s
O / Spd 1 Spd 2 / Spd 3 Speed setpoint
Low Low E-roller o
High Low 1
Low High 2
High High 3
The default settings of the speed setpoints depend on the motor type and
diameter of the E-roller. The selectable speed ranges for the ER50 series
are shown in the table. All speed setpoints can be altered with a 0.01 m/s
stepsize.

NDW | We’ll keep you rolling | 18
SETTINGS
Interface Basics
The straightforward interface of the BC50 controller makes it easy to change
any setting. The graphical UI makes it possible to let the user know any of
the current settings and what kinds of settings can be adjusted. The buttons
are used to select and change settings of the controller and rollers through
the user interface. Changing the settings can be done on the menu shown on
the user interface. All the dierent settings and how to change them will be
discussed in the upcoming chapters.
Menu explanation
Digital B
Digital A
Ground
Error
Direction
Spd 2 / Spd 3
O / Spd 1
Ground
24VDC
BC50 Motor Controller | 50W 24VDC
OK
Confirm / Select Back
Previous / Decrease Next / Increase
Graphical UI
The display will show all
settings and monitors the
conveyor systems. Settings
can be changed through the
menu.
NDW | We’ll keep you rolling | 19
First step in changing a setting
is selecting the menu in which
the setting is located. You can
scroll through the dierent
menus using the arrow buttons
and select the desired menu
using the OK button.
When the setting is selected,
you can change it using
the arrow keys and confirm
your selection using the OK
button. If you do not want to
change the setting you have
selected, you can press the
BACK button to return to the
previous menu.
After selecting a menu you
can scroll through the settings
located in this menu. You do
this using the arrow buttons
and select the setting you
want to change using the
OK button. You can also go
back to the menu selection by
pressing the BACK button.
After changing your setting,
you have to press OK to
confirm the changes you
made. At this point you can
still decide to press BACK to
cancel the changes you made.
OK
MTR
SPD
DEV
MOD
Motor Run:
Direction:
O
CW
Scroll through menus
Select desired menu
MTR
SPD
DEV
MOD
OK
Motor Run:
Direction:
O
CW
Scroll through menus
Select desired menu Back
Motor Run:
Direction:
On
CW
MTR
SPD
DEV
MOD
OK
Change setting
Confirm selection Back
OK
Confirm selection Back
Press OK to confirm

NDW | We’ll keep you rolling | 20
NDW | We’ll keep you rolling | 21
Motor settings (MTR)
Within the motor settings, the Run state, Direction, Motor Type and Diameter
of the motor can be altered. These settings can be changed in the MTR menu.
These settings are all focused directly on the E-roller and its functionalities. A
detailed description of each setting is described below.
Motor run
With the Run setting, the E-roller can be switched On or O. Using this
setting, the motor can be switched on and o without using an external I/O
signal. For example, this can be very useful for testing the E-roller during
installation.
Direction
The direction setting is used to alter the spin direction of the E-roller. The
motor can spin clockwise or counter- clockwise (CW or CCW). In IO-mode
one can also select “IO-Driven”. With this setting active, the controller will
follow the direction provided via external I/O. “Low” signal means CW, “High”
signal means CCW.
Sub-menu explanation
There are some menus that
contain submenus with more
settings. To open the settings
within these submenus, first
open the desired menu in
which you want to change a
setting using the OK button.
Opening this submenu opens
up more settings to select
and change. You can close
this submenu by pressing the
BACK button. You can also
select one of the new settings
using the OK button. After
which you can change the
setting like any other setting.
After selecting a menu you
can scroll through the settings
located in this menu. In here
you can find the submenu
containing more settings, you
can open this submenu using
the OK button.
MTR
SPD
DEV
MOD
OK
Motor Run:
Direction:
O
CW
Scroll through menus
Select desired menu
MTR
SPD
DEV
MOD
CW
> Setup
Direction:
OK
Scroll through settings
Select desired submenu Back
MTR
SPD
DEV
MOD
OK
200 rpm
50 mm
+ Diameter:
+ Type:
Change setting
Select desired setting Back
Motor Run:
Direction:
On
CW
MTR
SPD
DEV
MOD
OK
Change setting
Confirm selection Back
MTR
SPD
DEV
MOD
OK
Motor Run:
Direction:
On
CW
CW
Scroll through settings
Confirm selection Back
MTR
SPD
DEV
MOD
OK
Motor Run:
Direction:
On
CW
IO Driven
Scroll through settings
Confirm selection Back

NDW | We’ll keep you rolling | 22
NDW | We’ll keep you rolling | 23
Motor type and diameter
The Motor Type is determined by the type of E-roller you are using. The NDW
E-roller series oers three dierent motor types: 100, 200 and 400 RPM. The
BC50 controllers are specifically designed for these motorized rollers. Besides
the motor type, the diameter of the E-roller must be set. This can be done
in the same sub-menu. It is important to set the Motor Type and Diameter
correctly to the used E-roller. By changing these settings, the controller
makes sure the E-roller will run at the desired speed and the correct speed
values are shown on the display.
Speed Settings (SPD)
Within the speed settings, the speed of the rollers can be altered. This is done
by selecting standard ‘set-points’, which are pre-defined speeds. It is possible
to set up to 3 dierent speed set-points, with the speed given in m/s. These
set-points can be quickly accessed and chosen within this menu. In the
controller these setpoints are called “SPD1”, “SPD2” and “SPD3” respectively.
Customizing the set-points can be done in the same menu as selecting a set-
point. These set-points are also used while controlling the controller in IO-
mode. For every set-point, any speed value can be selected (with a resolution
of 0.01 m/s). Depending on the diameter and motor type of the E-roller, a
range of speeds can be selected. The selectable speed range for a 50 mm
diameter roller is shown below. For larger roller diameters, the transport
speed will obviously be higher.
MTR
SPD
DEV
MOD
OK
200 rpm
+ Diameter:
+ Type:
50 mm
Change setting
Select desired setting Back
Motor type Selectable speed range (50 mm)
100 RPM 0.05 to 0.26 m/s
200 RPM 0.10 to 0.52 m/s
400 RPM 0.20 to 1.04 m/s
Mode settings (MOD)
The BC50 controller can operate in two modes: Manual and IO-mode. In
Manual mode the controller is fully operated from the UI without external
connections. This is ideal for testing and simple applications. In IO-mode the
controller is operated with external IO signals. This provides more control
during operation of the BC50. When IO-mode is active, the Motor Run and
Speed setpoint become unavailable since these settings are controlled with
IO. The mode of the controller can be selected in the MOD menu.
Device settings (DEV)
The device settings are there to set and check multiple settings regarding
the controller itself, especially its screen and versioning. Settings such as
brightness, contrast and screensaver. However, most of the settings within
this menu can not be changed but contain information about the controller
hardware and software.
PNP/NPN
The controller can operate in PNP or NPN mode. This is related to the type of
IO inputs and outputs of the device controlling the BC50.
MTR
SPD
DEV
MOD
OK
Mode: Manual
IO
Scroll through modes
Select desired mode Back

NDW | We’ll keep you rolling | 24
NDW | We’ll keep you rolling | 25
Lock / Unlock device
While in operation you can lock the controllers to make sure nonauthorized
personnel is not able to change any of the settings. You can do this by
holding the back button for 3 seconds. To unlock the controller again hold
both the back and the OK button for 3 seconds.
Brightness
The brightness setting will change the brightness of the device’s screen.
Hardware info
The device hardware will show information regarding which hardware is in
use, which controller and what version it is. This is not a setting that is able to
be changed, only to be viewed.
Contrast
The contrast setting will change the contrast of the device’s screen.
Software info
The device software will show information about which software is in use, this
can dier per revision. This is not a setting that is able to be changed, only to
be viewed.
Screensaver
The screensaver time of the device will change after how many seconds the
device will show the information screen after not being used or being idle.
Factory reset
The factory reset will reset every setting of the device back to the initial
settings that were set on the device when leaving the factory.
OK
Motor info
0.50 m/s
Hold 3 secondsHold 3 seconds
OK
Motor info
0.50 m/s
Hold 3 seconds
Lock: Unlock:
Beware of the risk of injuries while cleaning or performing maintenance on
the BC50 controller. Only authorized and qualified personnel is allowed to
perform these kinds of tasks. Make sure that the power is switched o and
cannot be accidentally switched on again during cleaning or maintenance.
Also make sure to indicate cleaning or maintenance work is in progress on-
site to inform co-workers.
Cleaning
In order to avoid potential damage, the BC50 controller should be
periodically cleaned with a vacuum cleaner or dry cloth. Wet cleaning
methods are not allowed. This could cause unrepairable damage to the
controller.
Maintenance
The BC50 controller itself does not require maintenance. It is however
advised to periodically check whether screws, mounts and cables are still
correctly and tightly positioned. Also check whether cables are still correctly
connected to the product’s connectors and if cables have not suered any
visible damage.
In case a BC50 controller is damaged and does not function properly it has to
be replaced. Consult the “Removal” section and “Disposal” section (page 25)
to properly discard the broken product, and the “Assembly” section (page 11)
for re-installing a new BC50 controller. Never try to open a controller.
CLEANING AND MAINTENANCE

NDW | We’ll keep you rolling | 26
NDW | We’ll keep you rolling | 27
TROUBLESHOOTING
REMOVAL AND DISPOSAL
Problem Possible cause Solution
BC50 controller is not
working (graphical UI
remains black)
• No or incorrect power supply.
• Controller defect
• Ensure the specified voltages are
correct for the current setup.
• Ensure the connections from the
power supply to the BC50 controller
are correctly inserted, and if neces-
sary, correct them.
• Replace controller
Motor is not running • Motor not properly connected.
• Motor run is turned o in the
settings.
• Motor is stalled/blocked.
• Motor is broken
• Check motor cable.
• Change settings or I/O input signals.
• Check UI and remove blockage.
• Replace motor.
Motor speed does not
correspond to actual
speed
• Motor type or diameter is set
incorrectly
• Change motor type and diameter to
the correct setting
Removal
Beware of the risk of injuries while removing the BC50 controller from the
conveyor system. Only authorized and qualified personnel is allowed to
perform these kinds of tasks. Make sure that the power is switched o and
cannot be accidentally switched on again during removal. When removing
the controller from the conveyor system, make sure the following tasks are
being executed in this specific order:
• Cut all power from the system or, if applicable, the specific segment.
• If necessary, label the cables in order to ensure they are put back in the
right place.
• Disconnect all the cables from the BC50 controller.
• Remove the mounting screws that secure the controller to the
conveyor system.
• Gently remove the controller. Make sure not to drop or bump the controller,
this might result in irreversible damage.
• Make sure any loose cables are o the floor and cannot be damaged
by accident.
Disposal
The disposal of the BC50 controller must be compliant to industry-specific
national or local provisions. The responsibility for correct disposal of the
BC50 controller and the accompanying packaging and accessories lies
completely with the industrial operator which should consider the proper
regulations surrounding disposal of electronic devices.
ACCESSOIRIES
Cable accessories
Power cable 24V
5000mm, one-sided connector, order code: 901-CABP24-1-5000
COM cable
5000mm, one-sided connector, order code: 901-CABCOM-1-5000
E-roller extension cable
Standard lengths
1500mm, two-sided connector, male/female, order code: 901-CABMOT-1500
3000mm, two-sided connector, male/female, order code: 901-CABMOT-3000
M8-5pin Adapter cable
Standard lengths
310mm, two-sided connector, M8 male/24V PWR&COM, order code:
901-ADP-B-SC (M8 Screw-in)
310mm, two-sided connector, M8 male/24V PWR&COM, order code:
901-ADP-B-SN (M8 Snap-in)
*Custom lengths on request. L stands for required cable length.
NOTES

NDW | We’ll keep you rolling | 28
DECLARATION OF CONFORMITY
EU Declaration of conformity
(Translation of original)
The manufacturer:
NDW B.V.
Sluisweg 32,
5154 PE Waalwijk
The Netherlands
T: +31 (0) 416 67 44 44
W: www.ndwrollers.com
Hereby declares that the following product:
• NDW BC50 motor controller
is in conformity with the following standards and/or other normative documents:
2014/30/EU - EMC Directive
Furthermore, whenever relevant, the following harmonized standards are used
EN 61010-1:2010 - Safety requirements for control equipment
EN 61800-3:2018 - Adjustable speed electrical power drive systems
- EMC requirements
Eindhoven, 29-10-2019
Ir. T.S. van Loon Ir. M.P Karapun
Head of operations Managing Director
NDW, Sluisweg 32, 5145 PE Waalwijk | +31 (0) 416 67 44 44 | info@ndw.nl | www.ndwrollers.com
Table of contents
Popular Controllers manuals by other brands
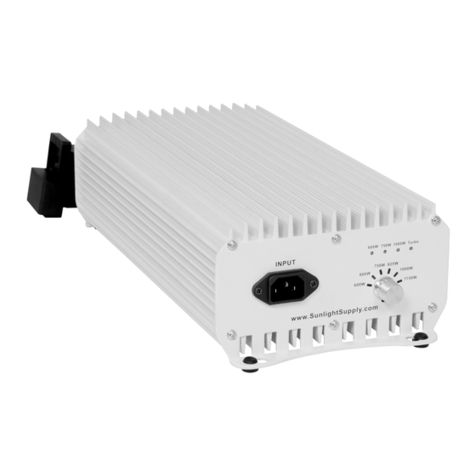
Sunsystem
Sunsystem One DE Installation & operating instructions
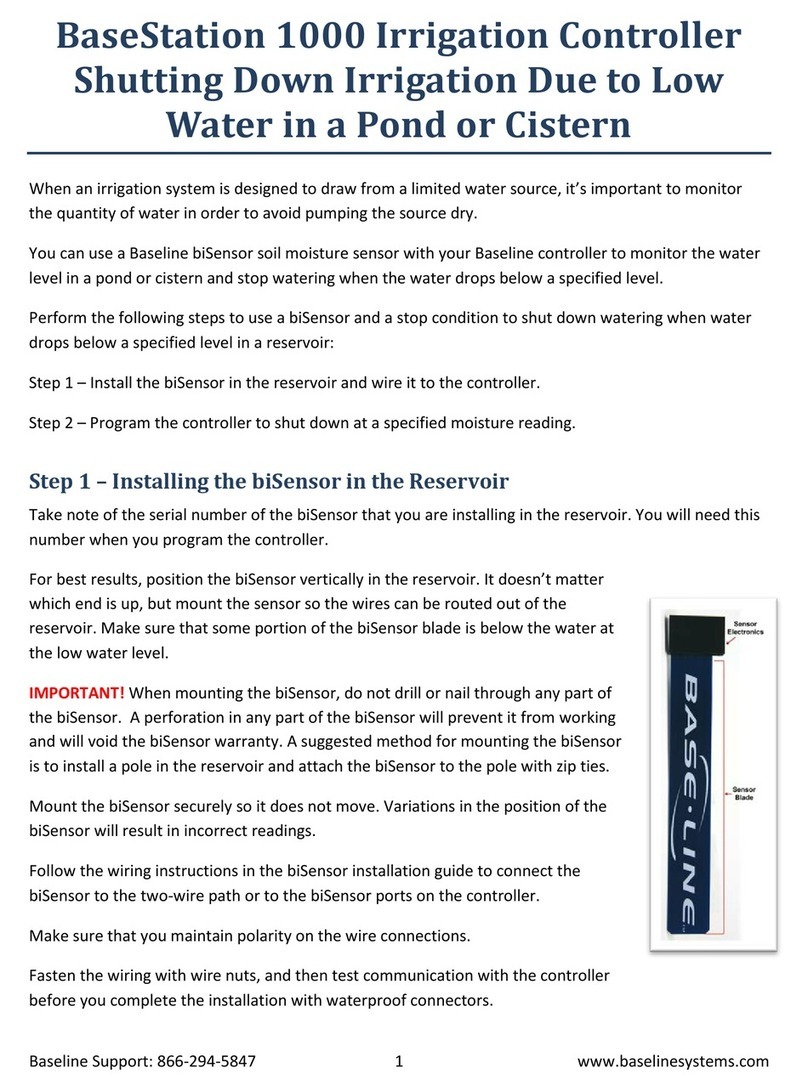
Base Line
Base Line BaseStation 1000 manual
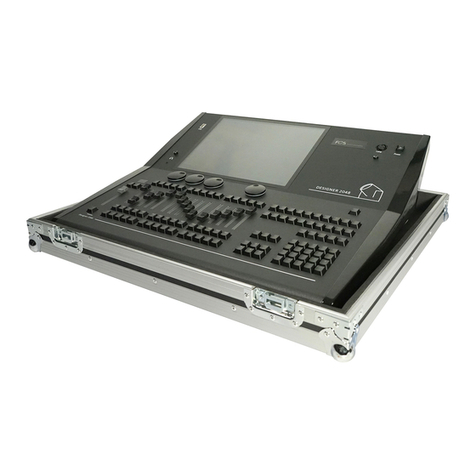
FOS Technologies
FOS Technologies Designer 2048 user manual
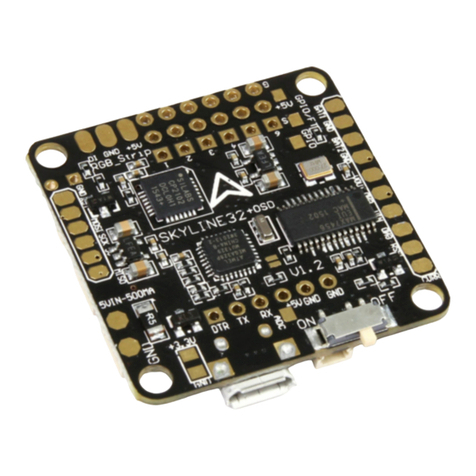
Emax
Emax SKYLINE32 instruction manual
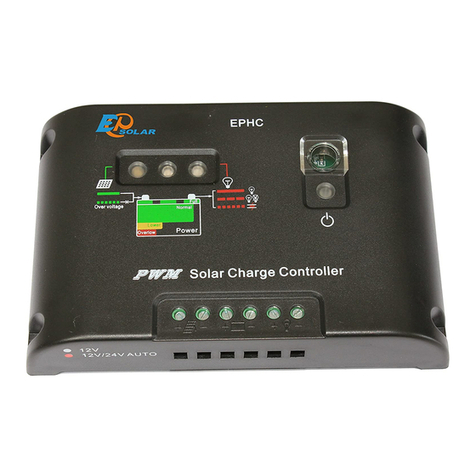
EP Solar
EP Solar EPHC10-EC series instruction manual
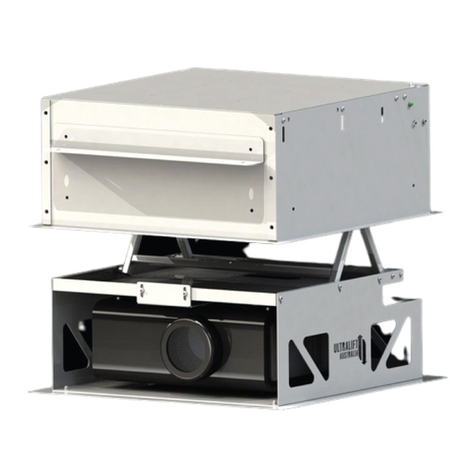
UltraLift
UltraLift Prolift Advanced Programming guide