New lift FST User manual

Manual
Field Bus Controller

FST_HB.EN04/03
Publisher NEW LIFT Steuerungsbau GmbH
Lochhamer Schlag 8
D-82166 Gräfelfing
Phone: +49 (0) 89 / 89 866 - 0
Fax: +49 (0) 89 / 89 866 - 300
Doc. No. FST_HB.EN04/03
Date of issue 04/03
Software version V1.100-0233
Copyright © 2003, NEW LIFT Steuerungsbau GmbH
All rights including those of copying and reproduction of parts of this
description and of the translation are reserved by the publisher.
No part of this description may be reproduced in any form or copied with an
electronic replication system without the written permission of the
publisher.

Table of Contents
FST_HB.EN04/03 1
1 About this manual ..............................................................................................5
1.1 General........................................................................................................................... 5
1.2 Signs and Symbols used ....................................................................................... 5
1.3 Further information................................................................................................... 6
2 General Safety Regulations .........................................................................7
2.1 Standards and regulations applied.................................................................... 7
2.2 Electromagnetic compatibility (EMC)................................................................ 8
2.3 Handling electronic components........................................................................ 8
3 FST-Controller user interface .....................................................................9
3.1 LC-Display and messages................................................................................... 10
Main screen..................................................................................................................... 10
Line A .............................................................................................................................. 10
Line B .............................................................................................................................. 11
Line C.............................................................................................................................. 14
Line D.............................................................................................................................. 27
Information texts.............................................................................................................. 28
Information page.............................................................................................................. 30
3.2 Keypad functions................................................................................................... 32
When switching on .......................................................................................................... 32
Main screen..................................................................................................................... 32
Main menu and test menu............................................................................................... 33
Error list........................................................................................................................... 33
Information page.............................................................................................................. 33
3.3 LEDs.............................................................................................................................. 34
3.4 HHT handheld terminal......................................................................................... 35
Selection of the FST when using a group controller........................................................ 36
4 Technical Data ..................................................................................................... 37
4.1 Component overview – bus plan...................................................................... 38

Table of Contents
2FST_HB.EN04/03
4.2 FST-Controller........................................................................................................... 39
4.3 VSM pre-selection module................................................................................... 49
4.4 VSE pre-selection extension............................................................................... 55
4.5 FSM car control module........................................................................................ 58
4.6 FPM car operating panel module...................................................................... 65
4.7 FPE car control panel extension module..................................................... 73
4.8 FPA car control panel adapter........................................................................... 78
4.9 ADM landing button module............................................................................... 82
4.10 RIO-ADM remote I/O module............................................................................... 86
4.11 RIO-FPM remote I/O module ............................................................................... 89
4.12 LON bus....................................................................................................................... 93
4.13 Trailing cable............................................................................................................. 95
5 Menu tree ...............................................................................................................101
5.1 General....................................................................................................................... 101
5.2 MAIN MENU – Service.......................................................................................... 111
5.3 MAIN MENU – Drive.............................................................................................. 113
5.4 MAIN MENU – Config........................................................................................... 117
5.5 MAIN MENU – Positioning.................................................................................. 132
5.6 MAIN MENUE – Calls............................................................................................ 139
5.7 MAIN MENUE – System....................................................................................... 141
5.8 MAIN MENUE – Doors.......................................................................................... 144
5.9 MAIN MENU.............................................................................................................. 148

Table of Contents
FST_HB.EN04/03 3
5.10 TEST MENU.............................................................................................................. 149
6 Error List ................................................................................................................151
6.1 LC-Display................................................................................................................ 151
6.2 Keypad functions.................................................................................................. 151
6.3 Event messages..................................................................................................... 152
6.4 Error messages...................................................................................................... 153
7 Index of Key words ........................................................................................159

Table of Contents
4FST_HB.EN04/03

1 About this manual
1.1 General
FST_HB.EN04/03 5
1 About this manual
1.1 General
The FST manual is a comprehensive reference work for experienced lift
service experts.
Aims of this manual
- describe the characteristics of the LON bus technology
- describe the characteristics and functions of the FST and its
components
- describe the operation of the FST
- describe the configuration of the FST
- describe the FST menu and its settings
- describe the messages of the FST
1.2 Signs and Symbols used
Below you can find a description of the signs and symbols used in this
manual.
Symbols +Key combination:
Press the linked keys simultaneously.
³
Action:
Actions are executed immediately and will not be saved as permanent
settings.

1 About this manual
1.3 Further information
6FST_HB.EN04/03
LC-Display and keypad In the left column you will find the LC-Display of the FST-Controller with a
grey background. The displays and messages or possible keypad
functions are explained in the table.
1.3 Further information
The following documentation is available for the FST-Controller and its
components:
- Description of FST-Controller
- FST Installation & Commissioning
- FST Quick Guide
- FST Manual (this document)
- GST Manual
- System description – Holding Device
- Installation & Commissioning – FAX Modem
- Quick Guide EAZ-256
- Quick Guide EAZ-VFD
- Quick Guide EAZ-LCD
- Quick Guide FST-IRT
- Manual for Fireman Mode
- System description – Speech Output
- System description – Attika Control
- System description – Bank-Control
- System description – Ramp-Drive
- System description – Panel Test
- System description – Safety curtain
NEW LIFT is happy to provide this documentation on request. Please
contact our marketing department.
Line or
key Description of display or keypad functions
LC-Display

1 General Safety Regulations
1.1 Standards and regulations applied
FST_HB.EN04/03 7
1 General Safety Regulations
The FST-Controller must be in technically perfect condition and may only
be used in accordance with regulations and in awareness of safety and
risks. The “FST Installation & Commissioning” manual as well as the
relevant guidelines for the prevention of accidents and the guidelines of
local power utilities must be observed.
1.1 Standards and regulations applied
The FST-Controller complies with:
- Regulation for lift systems
(German regulation for lift systems, AufzV)
- Safety regulations for the construction and installation of passenger
lifts, building hoists and service lifts (DIN EN 81 Parts 1 and 2)
- Technical regulations for lifts (TRA, Technische Regeln für Aufzüge)
Operation of lift systems (TRA 007)
Testing parts and components (TRA 101)
Passenger lifts, building hoists and service lifts (TRA 200)
- Regulations for the erection of power installations with rated voltages of
up to 1kV (DIN VDE 0100)
- Measures for contact voltage protection in the engine room (DIN EN
60990)
- Data sheet on safety measures during installation, maintenance and
servicing or repair of lift systems (ZH 1/312)

1 General Safety Regulations
1.2 Electromagnetic compatibility (EMC)
8FST_HB.EN04/03
1.2 Electromagnetic compatibility (EMC)
An accredited inspection body has verified that the FST-Controller and its
components comply with the standards, limits and test intensities
according to EN 12015/1995 and EN 12016/1995.
The FST-Controller and its components are:
- resistant against electrostatic discharges
(EN 61000-4-2/1995)
- resistant against electrostatic fields
(EN 61000-4-3/1997)
- resistant against transient disturbances
(EN 61000-4-4/1995)
The field strengths of the electromagnetic disturbances radiated by the
FST-Controller and its components do not exceed the permitted limits.
(EN 55011/1997)
1.3 Handling electronic components
Leave electronic components in their original packaging until installation.
Touch a grounded piece of metal prior to opening the original packaging to
prevent damage from static charges.
All bus inputs and outputs not in use must be equipped with a terminal
resistance (terminator).

3 FST-Controller user interface
FST_HB.EN04/03 9
3 FST-Controller user interface
The user interface of the FST-Controller is located on the FST board in the
control cabinet of the list system. The FST user interface consists of front
panel, LCD screen, keyboard and LEDs.
Fig. 3.1 FST-Controller user interface

3 FST-Controller user interface
3.1 LC-Display and messages
10 FST_HB.EN04/03
3.1 LC-Display and messages
The LC-Display consists of four lines A, B, C and D with 20 digits each.
After switching on and during normal operation theFST-Controller displays
the main screen.
Main screen
Line C has a special status. In normal mode (after switching on) it displays
status messages, see “Status messages in line C” on page 14. When
switching with key combination
S
+
¥
+
¤
it displays diagnostic
messages, see “Diagnostic messages in line C” on page 15.
Also see “Keypad functions” on page 32.
Line A
Safety circuit messages
in Line A
The messages
DOOR C OPEN
,
MANUAL DOOR OPEN
and
EMERGENCY
END SWITCH
are triggered by the same safety circuit input of the pre-
A Maximum active state of the safety circuit
B Active state or error
C Status of the lift system / diagnostic message
D Data for current drive mode
SAFETY CCT CLOSED
>AX< ###@###-
00 13:06:56
Display Description
SAFETY CCT CLOSED
The safety circuit is completely closed.
DOOR LOCK OPEN
A shaft door contact is open (interruption
between terminals VSM X1.2 and VSM X1.3).
DOOR A OPEN
Car door A is open (interruption between
terminals VSM X1.3 and VSM X1.4).
DOOR B OPEN
Car door B is open (interruption between
terminals VSM X1.4 and VSM X1.5).
DOOR C OPEN
Car door C is open (interruption between
terminals VSM X1.5 and VSM X1.6).
EMERGENCY STOP
An emergency switch has triggered
(interruptionbeforeterminalVSM X1.6). The lift
is not ready for operation.
MANUAL DOOR OPEN
A manual door contact is open (interruption
between terminals VSM X1.5 and VSM X1.6).
EMERGENCY END
SWITCH
The top emergency end switch of an hydraulic
lift is interrupted according to EN 81
(interruption between terminals VSM X1.5 and
VSM X1.6).

3 FST-Controller user interface
3.1 LC-Display and messages
FST_HB.EN04/03 11
selection module (TC input: VSM X1.5) and exclude each other.
Line B
State messages in line B Display Description
24V LOW!
The 24V supply of the FST board (FST X7.1
and X7.2) is below the permitted range of 24V
–10%. Check power supply and cables.
LANDING CALLS OFF
Landing control is blocked by a safety circuit
interruption (interruption of before terminal
VSM X1.6), line A displays
EMERGENCY
STOP
, see “
EMERGENCY STOP
” on page 10.
LANDING CONTROL OFF
The landing control has been switched off
manually. Possible switch-off points:
-
¥
key of the FST keypad
-Programmable input of an external RIO
module
-Input FST X7.15
-Programmable input of the FST-Controller
-Key switch on the in-car control panel (FPM
input X4.34)
-Key switch on the landing control panel (ADM
input X3.12 / X3.13)
See “Source of special drive signals
SRC:00
00 00 00
” on page 24.
FIREMAN
A fire input is active. Possible reasons:
-Fire input on the landing control panel (ADM
input X3.12 / X3.13)
-Programmable input of the FST-Controller
-GST Group Controller (see GST Manual)
See “Source of special drive signals
SRC:00
00 00 00
” on page 24..
END-SWITCH TEST
The manual end switch test is running, see
“TEST MENU” on page 149.
ES-SPEED MON. TEST
The manual test of the deceleration monitoring
function at the top and bottom limits is running,
see “TEST MENU” on page 149.
EVACUATION
The controller is in evacuation mode. The
source of the evacuation signal is a
programmable input on the FST-Controller.
SEND FAX
The controlleris in fax mode (see Installation &
Commissioning – Fax modem).

3 FST-Controller user interface
3.1 LC-Display and messages
12 FST_HB.EN04/03
LIFT OFF
The controller has been switched off. Possible
switch-off points:
-Car light failure
-Input “Car Light OFF”, FST X7.14
-Programmable input/output of a RIO module
(external)
-Programmable input/output of the FST-
Controller
-Externallyby theGST Group Controlleror the
LMS lift monitoring system
See “Source of special drive signals
SRC:00
00 00 00
” on page 24.
FIREMAN MODE
Fireman mode has been activated. Possible
sources:
-Key switch on the in-car control panel (FPM
X4.4)
-Programmable input/output of the FST-
Controller
-The state was saved after a powerfailureand
hasbeenreconstructed.Function
Fireman
Mode Reset
must be used to reset this
state, see “Fireman Options” on page 123.
-Key switch on the landing control panel(ADM
input X3.12 / X3.13)
-GST Group Controller (see GST Manual)
See “Source of special drive signals
SRC:00
00 00 00
” on page 24.
FILE TRANSFER
ACTIVE
The controller is in remote data transmission
mode to transfer files to a GST Group
Controller or to a PC.
INSPECTION
The controller isin inspection mode (inputFSM
X12.2).
Attention:Line A of the FST display must show
EMERGENCY STOP
!
CALIBRATION -
The calibration drive has been started. The
number of remaining drives is displayed (see
“Calibration drive” on page 117).
LEARN DRIVE ACTIVE
The controller performs a learn drive, see
“Learn drive” on page 117.
LEARN DRIVE-START
The controller performs a learn drive, see
“Learn drive” on page 117.
LEARN DRIVE-OK!
The learn drive has been completed, see
“Learn drive” on page 117.
LEARN DRIVE-ABORT!
The learn drive hasbeen aborted due to a fault.
The reason for the abortion is entered in the
error list, see “Learn drive” on page 117 and
“Error List” on page 151.
SAFETY CURTAIN
The safety curtain replacing the car door has
been interrupted. The contact is in the safety
circuit instead of the car door contacts (see
System description – Safety curtain).
Display Description

3 FST-Controller user interface
3.1 LC-Display and messages
FST_HB.EN04/03 13
DRM ...
An drive monitoring error has occurred. There
are different types of drive monitoring functions
that can shut down the lift, see “Error List” on
page 151.
INSTALLATION MODE
The controller is in installation mode, see
“Installation Mode” on page 117.
ORIENTATION
The controller performs an orientation drive to
the top or bottom limit after switching on (only
when using incremental positioning). The
orientation drivecan takeplaceautomaticallyor
when the first call is placed, see “Auto-Orien.”
on page 135.
PARK DRIVE ACTIVE
The controller sends the car to a programmed
parking floor, see “Park Drive –” on page 118.
PRIORITY LANDING
A priority landing drive has been triggered.
Possible sources:
-Key switch on the landing control panel (ADM
input X3.12 / X3.13)
-Programmable input of the FST-Controller
-Programmable input of an external RIO
module
PRIORITY CAR
A priority car drive has been triggered. Possible
sources:
-Key switch on the in-car control panel (FPM
input X4.37)
-Automatically after a type Auto 2 priority
landing drive, see “Prio-Landing/Car –” on
page 117.
AUXILIARY
The controller is in auxiliary mode (input VSM
X6.2).
Attention:Line A of the FST display must show
EMERGENCY STOP
!
HOMING ACTIVE
The hydraulic lift is sent to the lowest landing,
see “Homing Time” on page 114.
SERVICE ACTIVE
The controller is in service mode, see
description of the controller and “Source of
special drive signals
SRC:00 00 00 00
” on
page 24.
SERVICE REQUIRED!
A set limit of one of the service-counters has
been exceeded, see “Service-Counters –” on
page 111.
SYSTEM STOP
The controller has been stopped via the FST
Menu.
OVERLOAD
The overload input on the FSM or on one of the
programmable inputs is active, see“FSM: X11”
on page 63.
USER ERROR -
An user error has occurred. The number of the
error is displayed.
FULL LOAD
The full load input on the FSM is active, see
“FSM: X11” on page 63.
Display Description

3 FST-Controller user interface
3.1 LC-Display and messages
14 FST_HB.EN04/03
Line C
Status messages in line C Line C is divided and displays one of the following status messages in the
left and in the right part. For scrolling the status messages in the left part
use the key combination
S
+
¤
and for the right part the key combination
S
+
¥
.
The door positions marked with
A
also apply to doors
B
and
C
.
Status Display Description
Car doors
<A>
Door A completely open
>A<
Door A closed
<-A->
Door A is opening
->A<-
Door A is closing
<A*>
PhotocellorreversingcontactdoorA
active
<AX>
Door A is locked (test menu)
<AL>
Door is in loading mode (loading
button has been pressed)
-A-
Door A is stopped
?A?
State of door A is unknown (check
door limit switches)
<<>>
Door open button active
<><>
Door close button active
Shaft positioning
Z
Zone message active
F
Zone message missing
-
Car is in levelled position
###@###
Car position relative to levelled
position (each pixel = 2.5 mm)
ö
Correction switch bottom active
ä
Correction switch top active
Car position
P=6200
Current position of the car relative to
levelling position of lowest landing in
[mm]
Levelling
Pd= 02
Current position of the car relative to
closest levelling position in [mm]
Car speed
V=1300
Current speed of the car in [mm/s]
Set / current speed
@######V2
Comparison between set and actual
speed of the car. The left bar is a
graphic display of the relation
between actual speed and the set
speed on the right.
Motor-Hours
BS=4351
Operating hours of the drive
Drive counter
FZ=123456
Number of completed drives
Memory occupied
Rec: 45%
Memory occupied on the PC-Card
when recording.

3 FST-Controller user interface
3.1 LC-Display and messages
FST_HB.EN04/03 15
Diagnostic messages in line C Line C can be switched from status messages to diagnostic messages with
key combination
S
+
¥
+
¤
. Use key combination
S
+
¥
and
S
+
¤
to
scroll through the diagnostic messages.
Display Description
LIK-Errs:00000 00000
Diagnosis of absolute value encoder
function (see page 16), this display is
irrelevant when using incremental
positioning.
ENC:10000000[989680]
Real-time display of counted increments of
the encoder on plug X2. The counted
increments together with the covered
distance can help when calculating the
required
Resolution
.
Door-A: F1=00 F2=00
Current state of the FSM for door A (see
page 17)
Door-B: F1=00 F2=00
Current state of the FSM for door B (see
page 17)
Door-C: F1=00 F2=00
Current state of the FSM for door C (see
page 17).
Motor=00 VST=0000
Internal motor state (see page 20) and
states of the pre-selection contact outputs
(see page 21).
Kop:Virt=0b Real=00
Generated and actual position messages
from the car (see page 21).
SHK=SABCN
State of the safety circuit (see page 21).
Mgr1:Drv=00 Call=00
Internal NEW LIFT diagnostic message.
Mgr2:A=02 B=00 C=00
Internal NEW LIFT diagnostic message.
NextPoss=ff VT=V2
Next possible stop (
NextPoss
) that can
be approached and theset speed (
UT
), see
page 22.
Port EXIN1=EGALPUDR
State of input EXIN1, see page 22.
Port EXIO2=00000000
State of input EXIN2, see page 23.
Port H8IN1=ZBSMVO
State of input H8IN1, see page 23.
FSM-X6: L=1 V=0 K=0
State of the outputs on FSM X6, see
page 23.
SRC:00 00 00 00 00
Source of the special drive signals fireman,
fireman mode, landing control OFF, lift off
and service mode, see page 24.
LWE: 255% E0 F0 O0
State of the weight sensor, see page 25.
Proj.Status=........
State of the project specific parts of the
program (internal).
PC:s0 m1 c0 f0 Mb005
State of the PC-Card slot, see page 26.
Pkt\s In=005 Out=002
Incoming and outgoing data packets of the
FST-Controller in [packets/sec].
ASV: 0000000 P=[00]
State of the holding device, see page 26.
FSM msgs=00123
Number of message packets from the FSM
car control module to the FST-Controller.

3 FST-Controller user interface
3.1 LC-Display and messages
16 FST_HB.EN04/03
Absolute value encoder
function
LIK-Errs:00000 00000
The two numbers of the display show the number of encoderfailures since the last
activation of the system. The left number shows the different values resulting from
double scanning, the right number shows the number of failed plausibility checks.
Sporadic errors are compensated by the FST-Controller and can be tolerated. A
continuous increase of one of these values indicates an encoder or cable failure.
Left number:
Right number:
States of the FSM car
control module
Door-A: F1=00 F2=00
State bytes F1 and F2 describe the states of 8 functions each in real-time
Display Description
00000
or constant value Communication between the FST-Controller
and the absolute value encoder is working
correctly. Double scanning to suppress electric
interference does not show any differences.
constantly rising value Double scanning to suppress electric
interference does show differences. There is
electric interference on the connection cable
between FST-Controller and encoder. Check
connection cable and inform your NEW LIFT
Hotline.
Display Description
00000
The position values of the absolute value
encoder are plausible (are within the regular
shaft). There are no invalid jumps in the
position value.
RANGE
The position values of the absolute value
encoder are not plausible (are outside the
regular shaft). Check direction of rotation of the
encoder and commission the linear positioning
function, (see Installation and Commissioning
Manual).
DELTA
There are invalid jumps in the position value.
Absolute value encoder faulty.
Fig. 3.2 Hexadecimal encoding of an 8-bit register

3 FST-Controller user interface
3.1 LC-Display and messages
FST_HB.EN04/03 17
(8 bits, hexadecimal code). Hexadecimal bytes are decoded digit by digit.
Each digit has a decimal value according to the following table:
Each number codes four functions (bits) of the F1/F2 table with its decimal
value. The decimal value of the number corresponds to the sum of the
values of the activated functions according to the following tables.
* Signal only relevant for door versions A and B.
Hexadecimal
number Decimal
value
0
0
1
1
2
2
3
3
4
4
5
5
6
6
7
7
8
8
9
9
a
10
b
11
c
12
d
13
e
14
f
15
Bit Number Value Setting
F1 =
Byte F1
0digit 1
(right number)
1 active FSM car control module configured
1 2 active Door locked
2 4 active Door reversing
3 8 Doorcompletely
open Limit switch “door open”
4digit 2
(left number)
1 Doorcompletely
closed Limit switch “door closed”
5 2 active Photocell interrupted
6 4 active Reversing contact
7 8 active Minimum load input*

3 FST-Controller user interface
3.1 LC-Display and messages
18 FST_HB.EN04/03
Example:
State byte F1 = 6c and state byte F2 = 21
This results in the following hexadecimal numbers:
F1:
Digit 1 = “c” (decimal = 12)
Digit 2 = “6” (decimal = 6)
F2:
Digit 1 = “1” (decimal = 1)
Digit 2 = “2” (decimal = 2)
The decimal numbers are calculated from the following values:
F1:
Digit 1 = 12 = 8 + 4
Digit 2 = 6 = 4 + 2
F2:
Digit 1 = 1
Digit 2 = 2
This results in the following active bits:
F1:
Digit 1 = 8 + 4
=>according to the table for F1 (Digit 1) bits 2 and 3 are active
=>the door is reversing and limit switch “open” has switched
Digit 2 = 4 + 2
=>according to the table for F1 (Digit 2) bits 5 and 6 are active
=>the photocell is interrupted and the reversing contact has
switched
F2:
Digit 1 = 1
=>according to the table for F2 (Digit 1) bit 0 is active
Bit Number Value Setting
F2 =
Byte F2
0digit 1
(right number)
1 on Car light sensor*
1 2 active Inspection signal “fast”
2 4 active Inspection signal “down”
3 8 active Inspection signal “up”
4digit 2
(left number)
1 active Inspection signal “ON”
5 2 active Door closing motor
6 4 active Door opening motor
7 8 active Door ready for drive
SAFETY CCT CLOSED
Door-A: F1=6c F2=21
00 13:06:56
Other manuals for FST
1
Table of contents
Other New lift Controllers manuals
Popular Controllers manuals by other brands
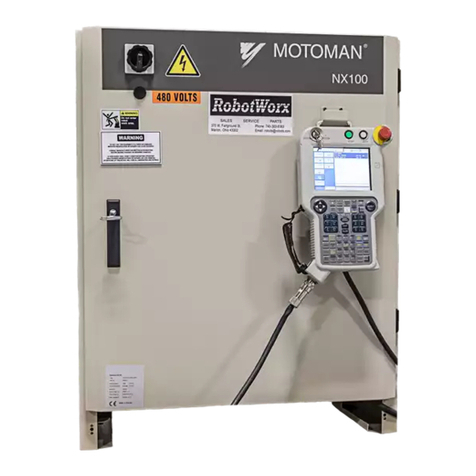
Motoman
Motoman NX100 user manual
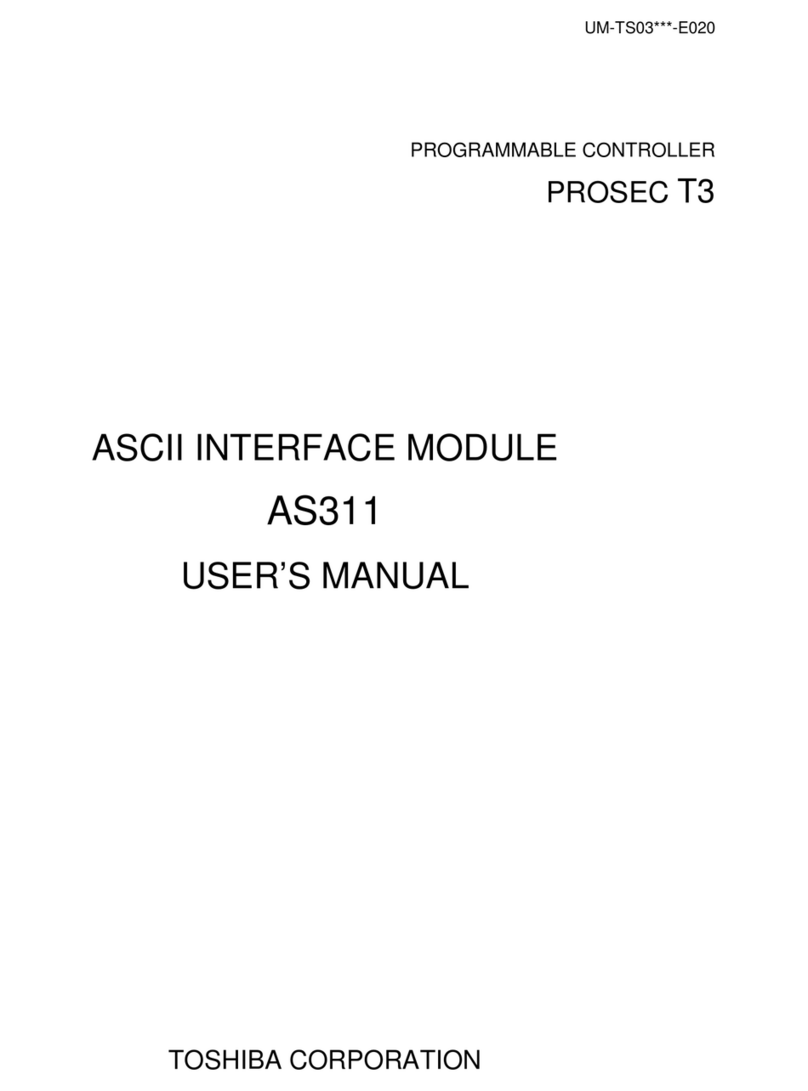
Toshiba
Toshiba AS311 user manual
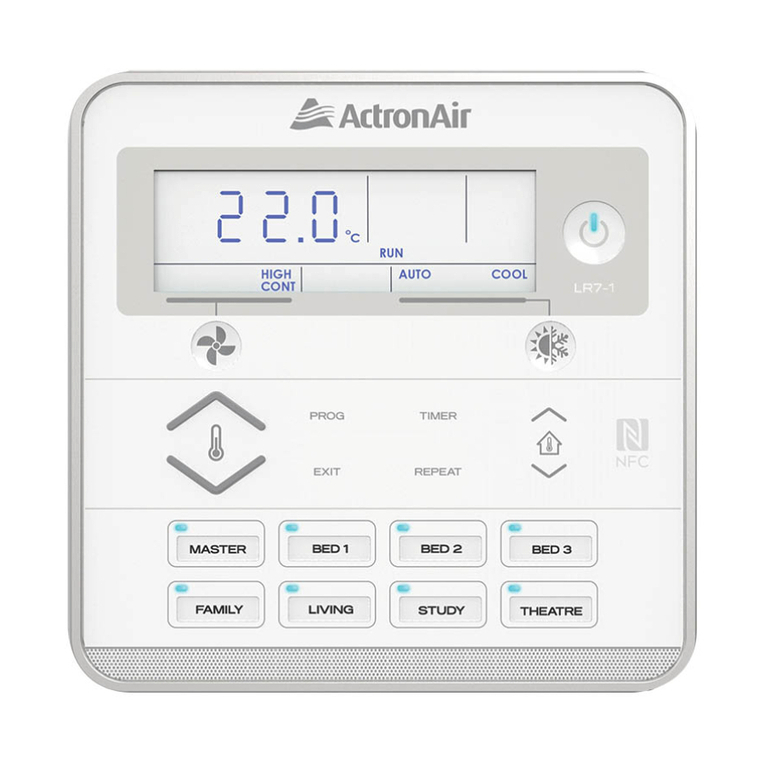
ActronAir
ActronAir LR7-1W Operation manual
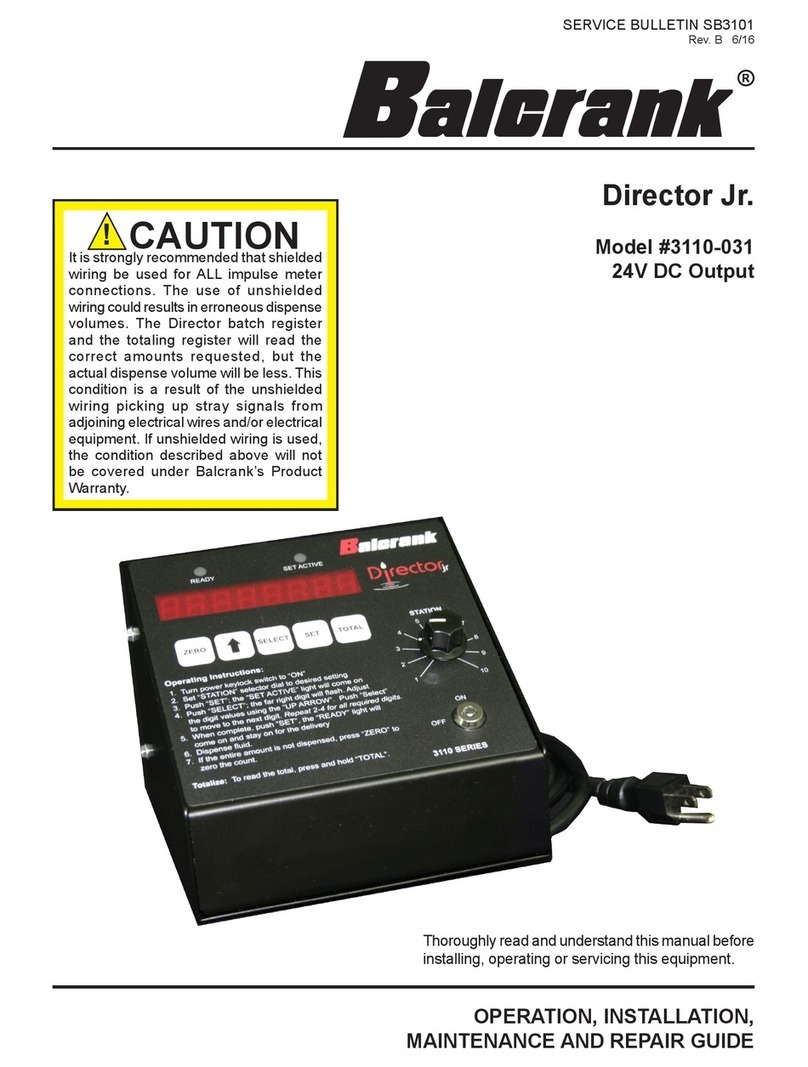
Balcrank
Balcrank Director Jr. 3110-031 Operation, installation, maintenance and repair guide
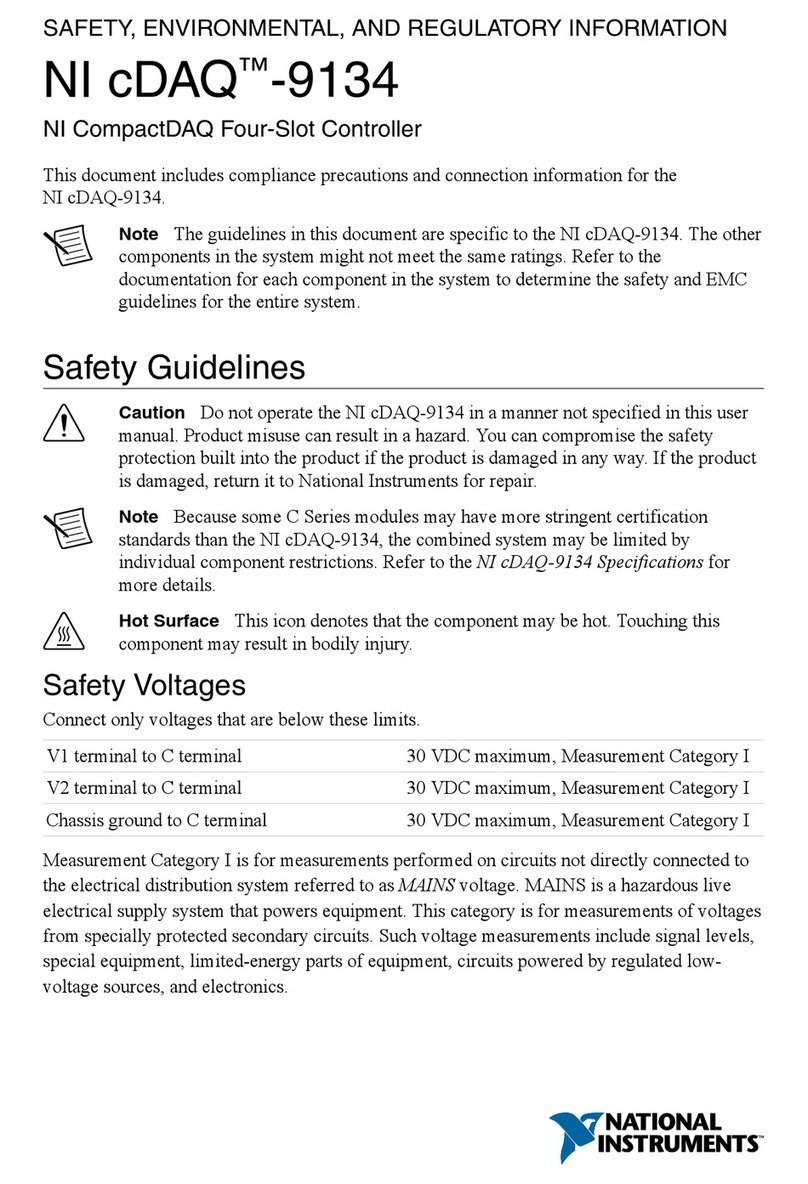
National Instruments
National Instruments NI cDAQ-9134 SAFETY, ENVIRONMENTAL, AND REGULATORY INFORMATION
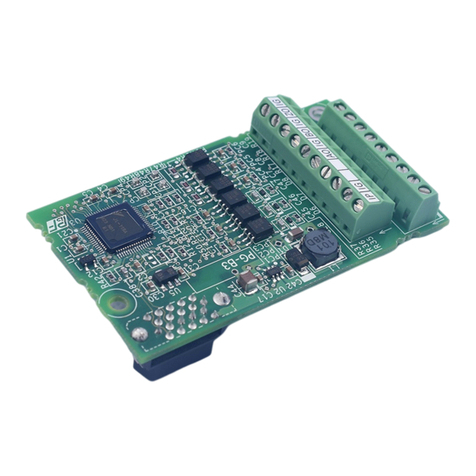
YASKAWA
YASKAWA pg-b3 installation manual