Nexen WEB CONTROL TM140A User manual

(i)
Tension Meter
Model TM140A
FORM NO. L-20185-B-0501
WEB CONTROL PRODUCTS
User Manual

(ii)
In accordance with Nexen’s established policy of constant product improvement, the specifications contained in this
manual are subject to change without notice. Technical data listed in this manual are based on the latest information
available at the time of printing and are also subject to change without notice.
Technical Support:
800-843-7445
(651)484-5900
www.nexengroup.com
Nexen Group, Inc.
560 Oak Grove Parkway
Vadnais Heights, Minnesota 55127
ISO 9001 Certified
Copyright 2000 Nexen Group, Inc.
Read this manual carefully before installation and operation.
Follow Nexen's instructions and integrate this unit into your system with care.
This unit should be installed, operated and maintained by qualified personnel ONLY.
Improper installation can damage your system or cause injury or death.
Comply with all applicable codes.
WARNING

(iii)
TABLE OF CONTENTS
Introduction---------------------------------------------------------------------------------------------------------------------------------------- 1
Theory of Operation--------------------------------------------------------------------------------------------------------------------------- 1
Installation ---------------------------------------------------------------------------------------------------------------------------------------- 2
Electrical Connections------------------------------------------------------------------------------------------------------------------------ 3
Sensor Calibration------------------------------------------------------------------------------------------------------------------------------ 4
Operation ----------------------------------------------------------------------------------------------------------------------------------------- 6
Maintenance -------------------------------------------------------------------------------------------------------------------------------------- 7
Fuse Replacement----------------------------------------------------------------------------------------------------------------------------- 7
Checking Terminal Values------------------------------------------------------------------------------------------------------------------- 8
Troubleshooting---------------------------------------------------------------------------------------------------------------------------------- 9
Mounting Dimensions -----------------------------------------------------------------------------------------------------------------------11
Specifications --------------------------------------------------------------------------------------------------------------------------------- 12
Replacement Parts --------------------------------------------------------------------------------------------------------------------------- 12
Warranties --------------------------------------------------------------------------------------------------------------------------------------- 13

1FORM NO. L-20185-B-0501
INTRODUCTION
Read this manual carefully, making full use of its explanations and instructions. The “Know How” of safe, continuous,
trouble-free operation depends on the degree of your understanding of the system and your willingness to keep all
components in proper operating condition. Pay particular attention to all NOTES, CAUTIONS, and WARNINGS to avoid
the risk of personal injury or property damage. It is important to understand that these NOTES, CAUTIONS, and
WARNINGS are not exhaustive. Nexen cannot possibly know or evaluate all conceivable methods in which service may
be performed, or the possible hazardous consequences of each method. Accordingly, anyone who uses a procedure
that is not recommended by Nexen must first satisfy themselves that neither their safety or the safety of the product will
be jeopardized by the service method selected.
THEORY OF OPERATION
Nexen’s TM140A Tension Meter measures, displays, and
provides proportional output signals, based upon tension
generated in a continuous strip process. The TM140A
provides excitation for two LDVT based MB Series
tension sensing load cells or one of two Nexen strain
gage sensors (type S or CFL). The load cells measure
web tension and provide a proportional low voltage
output signal.
The TM140A amplifies the signals from the two load cells
separately (See Figure 1) and feeds the Tension Indicator
and several output circuits with the resultant amplified
signals. The Read Out Selector Switch determines which
of the buffered signals are displayed on the Tension
Indicator and Recorder Terminals. The Tension Indicator
has a dual-range scale. The high-range, low-range
control is made through the Range Switch, which also
controls output at the Recorder Terminals.
FIGURE 1
Buffered signals are also present at Terminals 26, 27,
and 28 located on the back panel of the TM140A. These
three terminals are not affected by the position of the
Read Out Selector Switch or the Range Switch. The
total tension signal is also presented as a 4-20 mA signal
at Terminals 10 and 11, and as a 0-10VDC signal at
Terminals 29 and 30. These two signals are not buffered
or filtered.
A zero tension circuit is also provided. The zero tension
circuit closes a Normally Open (N.O.) relay when tension
drops to a low level, as would occur during a web break.
This circuit is controlled with a front panel switch and may
be disabled when running at extremely low tensions to
prevent nuisance tripping.
No. 2
Total
High
Low
Range
Switch
Terminal Block
Connections on
Back Panel
Read Out
Selector
Switch
Tension
Indicator
Recorder
Terminals
MB #1
No. 1
Amp
MB #2
No. 2
Amp
Buffer
Buffer
Buffer
+
No. 1
Amp
Amp
0-10VDC
4-20 mA

2FORM NO. L-20185-B-0501
MO2MO1
MO1
TOTAL
TOTAL
POWER
ON
POWER
ON
RECORDER
+-
ON
ON
OFF
OFF
ZERO
TEN
ZERO
TEN
III
II
II
II
III
II
III
IIII
II
III
III
II
III
II
II
III
I
III
II
II
II
III
II
III
IIII
II
III
III
II
III
II
II
III
I
0
50
30
20
10
40
kg
Nireco TM-140A
Nireco TM-140A
INSTALLATION
NOTE: The TM140A is an electronic component and should be mounted in a dry, dust free, shock, and vibration free
area with an ambient temperature of more than 32oF [0oC] and less than 122oF [50oC].
Wing
Screws
SHELF or WALL MOUNTING
1. Remove two screws located in the TM140A front
panel (See Figure 2).
2. Remove the TM140A from the Mounting Shell (See
Figure 2).
3. Install Mounting Brackets.
a. For shelf mounting, use the two Mounting
Brackets and four Wing Screws provided
(See Figure 3).
NOTE: Brackets may also be mounted to the upper
screw holes to allow under shelf mounting.
b. For wall mounting, secure the two Mounting
Brackets with the four Wing Screws
provided (See Figure 4).
4. Secure the Mounting Shell to a shelf or wall using the
customer provided screws.
5. Reinsert the TM140A into the Mounting shell and
secure it with the two screws removed in Step 1
(See Figure 2).
FIGURE 2
FIGURE 3
FIGURE 4
Remove
screws.
TM140A
Mounting
Shell
Mounting
Bracket
Mounting
Bracket
Wing
Screws
PANEL MOUNTING
1. Insert the TM140A into the cut out in panel (See
Figure 5 for panel cut out dimensions).
2. Insert the slides into grooves of the TM140A
Mounting Shell.
FIGURE 5
Panel Cut Out
7.44 In.
189 mm
3.66 In.
93 mm

3FORM NO. L-20185-B-0501
3. Using the four Wing Screws provided, secure the
Mounting Brackets to the Mounting Shell (See
Figure 6).
4. Insert the Adjustment Screw and jam nuts into the
center hole of Mounting Brackets (See Figure 6).
5. Adjust the screws until the panel is firmly clamped
between the TM140A front panel bezel and slides
(See Figure 6).
6. Tighten the jam nuts.
Adjustment
Screw
FIGURE 6
ELECTRICAL CONNECTIONS
NOTE: Use the cables provided with MB, CFL, and S
Tension Sensors to connect the sensors to the
TM140A. Use 18 AWG wire for all other
connections (See Figure 7).
SENSOR WIRING
Single Sensor
1. Connect the sensor cable for Sensor No. 1 (See
Figure 7).
2. Short across Terminals 5and 6 with a jumper wire.
Two Sensors
1. Connect both sensor cables to the TM140A.
2. Connect both shields to Terminal 9.
REVERSE TENSION SENSING
(MB Tension Sensor)
Reverse the connections of the green and yellow wires on
each Tension Sensor.
1. For Tension Sensor No. 1, connect the yellow wire to
Terminal 1 and the green wire to Terminal 2.
2. For Tension Sensor No. 2, connect the yellow wire to
Terminal 5 and the green wire to Terminal 6.
NOTE: For Strain Gauge Tension Sensors, reorient
the center line of the sensor to the resultant
of the force (See the corresponding
maintenance manual for further electrical
connectioninformation).
FIGURE 7
1
2
3
4
5
6
7
8
9
10
11
12
13
14
15
16
17
18
19
20
21
22
23
24
25
26
27
28
29
30
Tension
Sensor
No. 1
Tension
Sensor
No. 2
GN
YL
RD
BK
GN
YL
RD
BK
WH
ExternalTerminals
Zero
Tension
Contact
Control Output
4 to 20 mA
Zero Tension
Output
External Meter
Output (1 mA)
AC Power Supply
Power
Supply
Voltage
Selecting
Wiring
100V
110V
120V
200V
220V
240V
+
-
+
-
Ground
No. 1 Tension
No. 2 Tension
TOTAL Tension
COM
Measuring
Output
0 to 10V
Control Output 0 to 10V
+
+
+
-
+

4FORM NO. L-20185-B-0501
No.2
ZERO SPAN
No.1
ZERO SPAN
No.2
RANGE
No.1
TOTAL
POWER
ON
RECORDER
+ -
ON OFF HIGH LOW
ZERO
TEN
III
II
II
II
III
II
III
IIII
II
III
III
II
III
II
II
III
I
III
II
II
II
III
II
III
IIII
II
III
III
II
III
II
II
III
I
0
100
50
60
30
40
20
20
10
80
40
lb
AC POWER WIRING
1. Apply AC power to Terminals 16 and 17.
2. Connect Ground to Terminal 25.
NOTE: The Voltage Select Jumper wire connected
to Terminal 18 is connected to Terminal 24
(240 V) from the factory. If another voltage
is applied at Terminals 16 and 17, remove
the jumper from Terminal 24 and connect it
to the proper terminal.
The No. 1, No. 2, and Total signals at Terminals, 26, 27,
28, and 29 on the back panel are also proportional at 0-
10 volts equal to maximum full scale, but are not controlled
by the Read Out Selector Switch or the Range Switch.
They constantly put out the appropriate proportional and
buffered signal with 0-10VDC equals 0 to full scale in
high range.
The External Meter Output Terminals 14 and 15 present
a 0-1mA buffered output which is also proportional to full
scale.
The 4-20 mA signal at Terminals 10 and 11 and the 0-10
volt signal at Terminals 29 and 30 are also proportional to
0 to maximum full scale but are not buffered.
When the tension falls to zero, the normally open Zero
Tension Relay contacts close. This relay signal can be
picked up at Terminals 12 and 13. The contacts are rated
at 250VAC, 0.2 Amp.
SENSOR CALIBRATION (See Figure 8)
FIGURE 8
Variable
Resistors Read Out
Selector Switch
Zero Tension
Switch
Range
Switch
Power
Switch
Tension
Indicator
REMOTE TENSION INDICATOR WIRING
1. Remove the jumper from Terminals 14 and 15.2. Connect the 1mA remote meter leads to Terminals
14 and 15. AC power can be 100, 110, 120, 200,
220, or 240VAC either 50 or 60 Hz.

5FORM NO. L-20185-B-0501
ZERO ADJUSTMENT
NOTE: Only perform Zero Adjustment when there is no
web on the sensing roll and no other objects are
sitting or leaning on the roll or sensors.
1. Set the Power Switch to ON.
2. Set the Zero Tension Switch to OFF.
3. Set the Read Out Selector Switch to No. 1 and
adjust the No. 1 Zero Variable Resistor until the
Tension Indicator displays 0.
4. Set the Read Out Selector Switch to No. 2 and
adjust the No. 2 Zero Variable Resistor until the
Tension Indicator displays 0.
NOTE: When using only one sensor, make sure a
jumper wire is provided between Terminals 5
and 6.
5. Set the Read Out Selector Switch to TOTAL. The
Tension Indicator must still show 0.
6. Set the Zero Tension Switch to ON.
7. Set the Power Switch to OFF.
SPAN ADJUSTMENT (See Figure 9)
NOTE: Zero Adjustment must be performed prior to
conducti/ng Span Adjustment.
1. Thread a rope or narrow web over the sensor roll in
the normal web path, making sure the rope is in the
center of the sensor roll. Hang a known weight
(weight must be less than the full scale, high range
on the Tension Indicator) on one end of the rope.
Secure the other end of the rope to the machine with
the known weight held off the ground.
2. Set the Power Switch to ON.
Single Sensor Calibration
1. Set the Read Out Selector to No. 1 and adjust the
No. 1 span Variable Resistor until the Tension
Indicator shows the total known weight on the rope.
2. Set the Read Out Selector to No. 2 and turn the No.
2span Variable Resistor counterclockwise to ZERO.
FIGURE 9
Dual Sensor Calibration
1. Set the Read Out Selector Switch to No. 1 and
adjust the No. 1 span Variable Resistor until the
Tension Indicator shows one half the known weight
on the rope.
2. Set the Read Out Selector Switch to No. 2 and
adjust the No. 2 span Variable Resistor until the
Tension Indicator shows one-half the known weight
on the rope.
3. Set the Read Out Selector Switch to TOTAL. The
Tension Indicator must read the total known weight
on the rope.
4. Set the Power Switch to OFF.
3. Set the Read Out Selector Switch to TOTAL. The
Tension Indicator must read the known weight on the
rope.
4. Set the Power Switch to OFF.

6FORM NO. L-20185-B-0501
No.2
ZERO SPAN
No.1
ZERO SPAN
No.2
RANGE
No.1
TOTAL
POWER
ON
RECORDER
+ -
ON OFF HIGH LOW
ZERO
TEN
III
II
II
II
III
II
III
IIII
II
III
III
II
III
II
II
III
I
III
II
II
II
III
II
III
IIII
II
III
III
II
III
II
II
III
I
0
100
50
60
30
40
20
20
10
80
40
lb
FIGURE 10
Read Out
Selector Switch
Zero Tension
Switch
Range
Switch
Power
Switch
OPERATION
NOTE: Start the machine in operation with a web in place. Set the TM140A Power Switch to ON.
Recorder
Terminals
The Tension Indicator will display tension at the No. 1
Sensor, No. 2 Sensor, or Total Web Tension, as
commanded by the Read Out Selector Switch (See
Figure 10).
The Range Switch determines whether the display is in
the black (upper) or red (lower) range on the Tension
Indicator (See Figure 10).
The Recorder Terminals will put out a buffered signal,
proportional to the Tension Indicator, with 0-10 volts
being equal from zero to maximum full scale in high range.
The Recorder Terminals are also controlled by the Read
Out Selector Switch and Range Switch (See Figure 10).
The Zero Tension Switch enables or disables the Zero
Tension Circuit. When running at very low tensions, it
may be helpful to trun the Zero Tension Circuit OFF to
prevent nuisance tripping (See Figure 10).
The Power Switch applies AC power ot the unit (the red
LED illuminates) or turns the unit OFF (the red LED
extinguishes) (See Figure 10).

7FORM NO. L-20185-B-0501
120
COM
MAINTENANCE
Nexen’s TM140A does not require routine maintenance.
Periodically check that the pillow block bearings mounted
to the Tension Sensors have not moved. It is also advisable
to periodically check the Zero and Span Adjustment (See
OPERATION) if close accuracy is required.
FIGURE 11
AC Line Fuse
Zero Tension
Fuse
FUSE REPLACEMENT (See Figure 11)
The TM140A has two protective fuses; one fuse is in the
incoming AC line and the other fuse protects the Zero
Tension circuit from feed back voltage resulting from
damage to the device connected to the Zero Tension
Terminals.
The AC Line Fuse is rated 0.2 Amp Slow Blow and is
located on the back panel near the terminal block. To
replace the AC Line Fuse, turn off the AC power. Lift the
catch below the fuse holder and remove the fuse holder.
Replace the fuse with the 0.2 Amp Slow Blow spare fuse
provided. Reinstall the fuse holder, making sure it clicks
into place when the catch is closed.
The Zero Tension Fuse is located on the main printed
circuit board. It is rated at 0.2 Amp Instant Blow. To
replace the Zero Tension Fuse, turn off the AC power.
Remove the two screws from the front panel of the
TM140A and remove the TM140A from the Mounting
Shell. Remove the defective fuse from the fuse holder
and replace it with the 0.2 Amp Instant Blow fuse
provided. Slide the TM140A into the Mounting Shell and
tighten the two screws.

8FORM NO. L-20185-B-0501
FIGURE 12
TABLE 1TABLE 1
TABLE 1TABLE 1
TABLE 1
Check Terminal ValuesCheck Terminal Values
Check Terminal ValuesCheck Terminal Values
Check Terminal Values
CHECKING TERMINAL VALUES
Remove the two screws from the TM140A front panel
and slide the TM140A out of the mounting shell. This
will expose the Check Terminal and Common Pin.
The Common Pin is used for checking all voltages
except the power supply for the Tension Sensor.
When checking the Tension Sensor circuit, Check
Terminal 6 is used as Common (See Figure 12 and
Table 1).
1
Common
Pin
CheckTerminal
20
COM
CHECK CHECK ITEMS NORMAL CONDITION
POWER
SUPPLY
SIGNAL
LINE
About + 6VDC
(fluctuating DC)
About + 15VDC
About - 15VDC
Value corresponding to tension with
0 to full scale = 0 - 10 V
Same as CP3 at HIGH
2 x CP3 at LOW Range
Power Supply for
Sensor Common
Power Supply for
Operational Amplifier
Power Supply for
Operational Amplifier
Tension at No. 1 Sensor
Tension at No. 2 Sensor
Total Tension
Tension Value on the
Tension Indicator
CP5
CP6
CP7
CP8
CP1
CP2
CP3
CP4

9FORM NO. L-20185-B-0501
TROUBLESHOOTING
PROCEDURE1
START
Are the DC power supply
voltages normal?
Is tension normally indicated
when a load is applied/released
to/from the sensor roll?
No fault.
Are each of the
external output terminal
readings normal?
The main board
is defective.
Go to "B Tension
Sensor Check."
Go to "A Power
Supply Circuit Check."
NN
NN
NOO
OO
O
NO
A Power Supply Circuit Check.
Is the Voltage Selector Jumper
set to the AC power supply
voltage used?
Set it to the power supply voltage
being used.
Is the AC power supply voltage
within the tolerance (+10%)? Adjust the voltage within the
tolerance.
Is the power fuse blown?
NO
• Does the indication of the meter
return to zero when the load is
removed?
• Does the indicated reading
change as the Readout Selector
switch and Range Switch are
cycled?
• Check voltages using the check
terminals for the power supply.
YES
YES
YES
YES
NN
NN
NOO
OO
O
Replace it with the specified fuse
(0.2Amp Slow Blow) (See Fuse
Replacement, Page 7).
Thepowersupplycircuitboardis
defective.
NO
YES
NO
YES

10FORM NO. L-20185-B-0501
B Tension Sensor Check.
Is a voltage proportional to the
tension generated at check
terminal CP4? Is the connector for Tension
Indicator connected to the
specified terminal?
ConnecttheTensionIndicatortothe
specified connector terminals.
• AX1 is defective.
• External Terminals 14 and 15
are not short circuited or
external indicator (1mA
ampmeter) is not connected.
Is a voltage proportional to
the tension value generated at
CP1 and CP2?
Is the sum of CP1 and CP2
generated at CP3? The HIC is defective.
• RANGE Switch is defective.
• HIC is defective.
Can Zero Adjustment be made?
Do the voltages between external
Terminals 2 and 29 and between
Terminals 6 and 29 change when
turning No. 1 and No. 2 Zero
Adjustment VRs?
Is the Sensor's load plate in
contact with limiting stops?
The Zero Adjustment circuit is
defective.
Do the voltages between
Terminals 1 and 29 and between
5 and 29 change as above?
• Span is outside of specified
range.
• The HIC is defective.
Incorrect external wiring or
defective Sensor.
The HIC is defective.
Can Span Adjustment be made?
Is a voltage proportional to
the tension value generated
between external Terminals 1
and 2 or Terminals 5 and 6?
• Working force is small compared
to Sensor's load range.
• Unsuitable wrap angle.
• The Sensor is defective.
Does the Tension Indicator return
to zero when tension
is reduced to zero? Are the sensor roll and Sensor
mounted as specified (MB Tensor
Sensor Instruction Manual)?
No fault in the Tension Sensor. The Sensor is defective.
YES
NO
• Unsuitable pillow block mounting.
• Sensor roll weight too high.
• Sensor is defective.
• Do not apply excessive force to
Sensor or hysteresis will occur.
YES
NN
NN
NOO
OO
O
YES
NN
NN
NOO
OO
O
YES
NN
NN
NOO
OO
O
YES
NO
YES
NO
YES
NN
NN
NOO
OO
O
YES
NN
NN
NOO
OO
O
YES
NN
NN
NOO
OO
O
YES
NN
NN
NOO
OO
O
YES
NN
NN
NOO
OO
O
YES
NN
NN
NOO
OO
O

11 FORM NO. L-20185-B-0501
MOUNTING DIMENSIONS
FIGURE 13
MO2
MO2
MO1
MO1
TOTAL
TOTAL
POWER
ON
POWER
ON
RECORDER
+-
ON
ON
OFF
OFF
ZERO
TEN
ZERO
TEN
0.531
[13.5] 0.531
[13.5]
7.440
[189]
0.709
[18]
0.629
[16]
0.551
[14]
7.953
[202]
0.354
[9]
0.354
[9]
2.755
[70]
8.150
[207]
3.858
[98]
7.598
[193]
2.755
[70]
4.704
[119.5]
0.512 [13]
0.629
[16]
0.629
[16]
3.582
[91]
3.661
[93]
Panel Cut Out
Dimensions
In
[mm]
7.362
[187]

12FORM NO. L-20185-B-0501
REPLACEMENT PARTS
SPECIFICATIONS
Rated Tension 5, 10, 20, 50, 100, 200, 300,
500,1000, 2000 Lbs.
Power Supply 100, 110, 120, 200, 220, and
240VAC, 50/60 Hz
Ambient Temperature 32oto 122oF [0oto 50oC]
Weight 3.3 Lbs. [1.5 Kg ]
DESCRIPTION P/N
Power Supply P.C. Board 3296
Power Supply Transformer 3300
Main P.C. Board 3298
Selector Switch (No. 1, No. 2, and Total) 3301
Zero Tension ON-OFF Switch 3302
Range HIGH-LOW Switch 3302
Power ON-OFF Switch 3303
Meter Face (5 Lb.) 10207
Meter Face (10 Lb.) 10211
TABLE 2TABLE 2
TABLE 2TABLE 2
TABLE 2
External OutputExternal Output
External OutputExternal Output
External Output
DESCRIPTION P/N
Meter Face (20 Lb.) 10218
Meter Face (50 Lb.) 10222
Meter Face (100 Lb.) 2144
Meter Face (200 Lb.) 10227
Meter Face (300 Lb.) 10231
Meter Face (500 Lb.) 10236
Meter Face (1,000 Lb.) 10240
Meter Face (2,000 Lb.) 10650
MEASUREMENT OUTPUT
CONTROL OUTPUT
OUTPUT for EXTERNAL INDICATOR
ZERO TENSION CONTACT
TOTAL: 0 to 10VDC (2mA)
No. 1: 0 to 5VDC (2mA)
No. 2: 0 to 5VDC (2mA)
0 to 10VDC (2mA)
TOTAL: 0 to 10VDC (2mA)
TOTAL: 4 to 20 mA DC
(500W Load)
0 to 1 mA DC
Rated 250VAC, 30VAC, 0.2 A
28-29
26-29
27-29
Front Panel
30-29
10-11
14-15
12-13
OUTPUT TERMINAL NO.

13 FORM NO. L-20185-B-0501
WARRANTIES
Warranties
Nexen warrants that the Products will be free from any defects in material or workmanship for a period of 12 months
from the date of shipment. NEXEN MAKES NO OTHER WARRANTY, EXPRESS OR IMPLIED, AND ALL IMPLIED
WARRANTIES, INCLUDING WITHOUT LIMITATION, IMPLIED WARRANTIES OF MERCHANTABILITY AND
FITNESS FOR A PARTICULAR PURPOSE ARE HEREBY DISCLAIMED. This warranty applies only if (a) the Product
has been installed, used and maintained in accordance with any applicable Nexen installation or maintenance manual
for the Product; (b) the alleged defect is not attributable to normal wear and tear; (c) the Product has not been altered,
misused or used for purposes other than those for which it was intended; and (d) Buyer has given written notice of the
alleged defect to Nexen, and delivered the allegedly defective Product to Nexen, within one year of the date of
shipment.
Exclusive Remedy
The exclusive remedy of the Buyer for any breach of the warranties set out above will be, at the sole discretion of Nexen,
a repair or replacement with new, serviceably used or reconditioned Product, or issuance of credit in the amount of the
purchase price paid to Nexen by the Buyer for the Products.
Limitation of Nexen’s Liability
TO THE EXTENT PERMITTED BY LAW NEXEN SHALL HAVE NO LIABILITY TO BUYER OR ANY OTHER PERSON
FOR INCIDENTAL DAMAGES, SPECIAL DAMAGES, CONSEQUENTIAL DAMAGES OR OTHER DAMAGES OF
ANY KIND OR NATURE WHATSOEVER, WHETHER ARISING OUT OF BREACH OF WARRANTY OR OTHER
BREACH OF CONTRACT, NEGLIGENCE OR OTHER TORT, OR OTHERWISE, EVEN IF NEXEN SHALL HAVE
BEENADVISEDOFTHE POSSIBILITY OR LIKELIHOOD OF SUCH POTENTIAL LOSS OR DAMAGE. For all of
the purposes hereof, the term “consequential damages” shall include lost profits, penalties, delay images, liquidated
damages or other damages and liabilities which Buyer shall be obligated to pay or which Buyer may incur based upon,
related to or arising out of its contracts with its customers or other third parties. In no event shall Nexen be liable for
any amount of damages in excess of amounts paid by Buyer for Products or services as to which a breach of contract
has been determined to exist. The parties expressly agree that the price for the Products and the services was
determined in consideration of the limitation on damages set forth herein and such limitation has been specifically
bargained for and constitutes an agreed allocation of risk which shall survive the determination of any court of
competent jurisdiction that any remedy herein fails of its essential purpose.
Limitation of Damages
In no event shall Nexen be liable for any consequential, indirect, incidental, or special damages of any nature whatso-
ever, including without limitation, lost profits arising from the sale or use of the Products.
Warranty Claim Procedures
To make a claim under this warranty, the claimant must give written notice of the alleged defect to whom the Product
was purchased from and deliver the Product to same within one year of the date on which the alleged defect first
became apparent.
Nexen Group, Inc.
560 Oak Grove Parkway
Vadnais Heights, MN 55127
800.843.7445
Fax: 651.286.1099
www.nexengroup.com
ISO 9001 Certified
Table of contents
Other Nexen Measuring Instrument manuals
Popular Measuring Instrument manuals by other brands
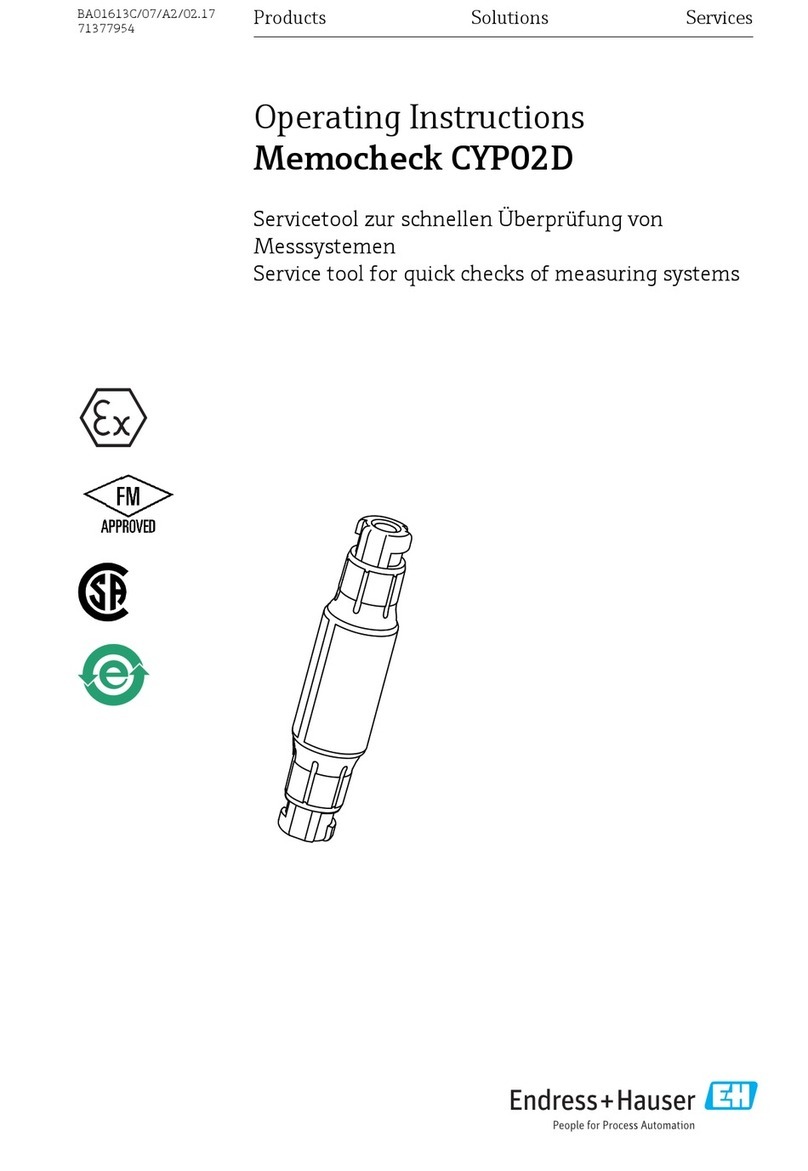
Endress+Hauser
Endress+Hauser Memocheck CYP02D operating instructions
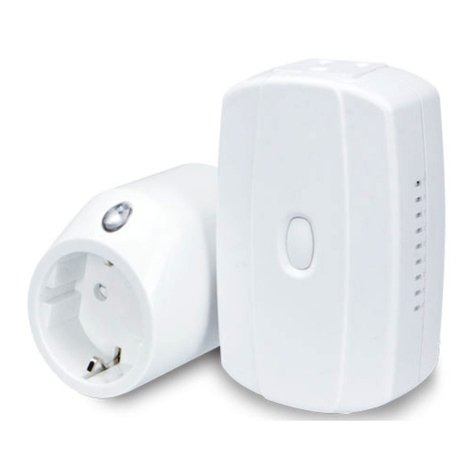
Planet Networking & Communication
Planet Networking & Communication HZS-532E-DE user manual

Landis & Gyr
Landis & Gyr FOCUS kWh Technical manual

Extech Instruments
Extech Instruments MO297 user guide
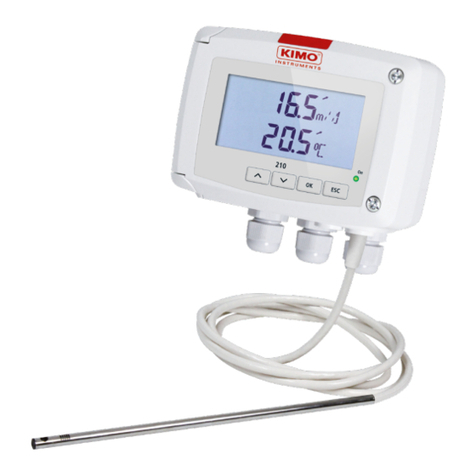
sauermann
sauermann CTV 210-R quick start guide
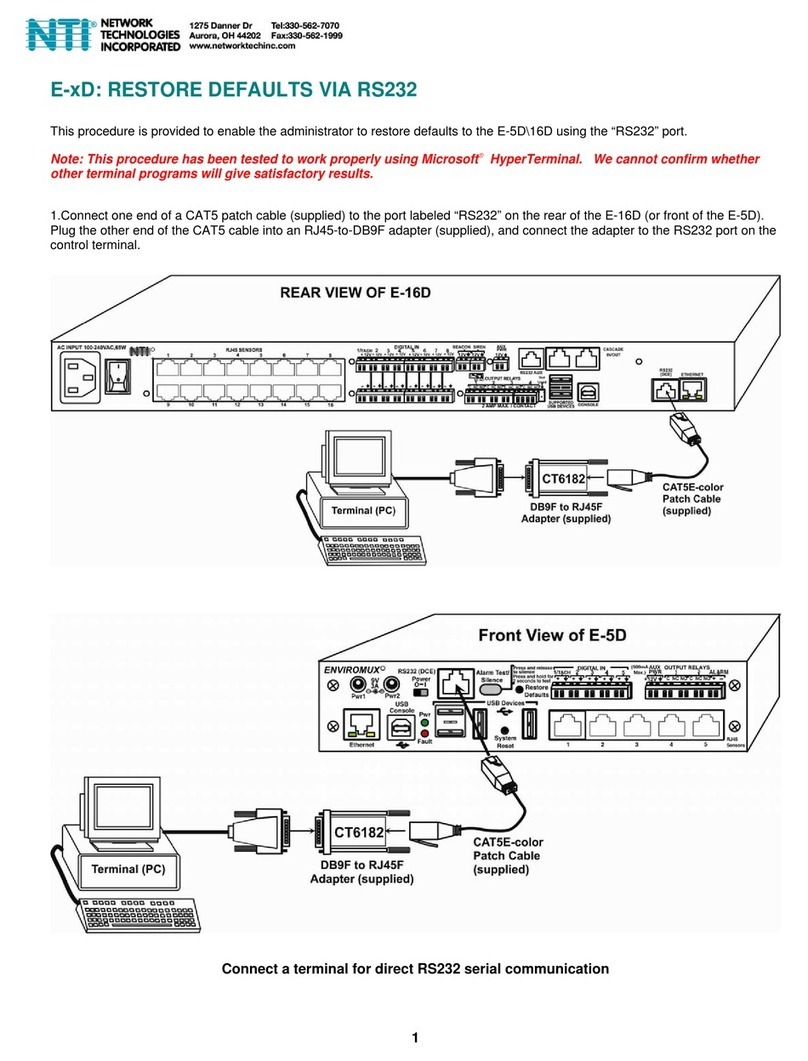
NTI
NTI ENVIROMUX E-5D manual