NS system Tango-B series User manual

User's Manual
1-AXIS AC SERVO DRIVE & CONTROLLER
TANGO-B Series
NS SYSTEM Co., Ltd.
NS SYSTEM SinYong B/D 4F #942-6 Ingye-Dong, Paldal-Gu, Suwon-City, Kyungki-Do, Korea
Homepage : www.nssystem.co.kr TEL: 82-31-235-7492~6 FAX: 82-31-235-7497

CONTENTS
Safety Instructions 1
CHAPTER 1. FUNCTIONS AND SPECIFICATIONS 4
1-1. FEATURES AND THE PRODUCT 4
1-2. OPERATION MODE 4
1-3. STANDARD SPECIFICATIONS 5
1-4. MODEL CODE DEFINITION 9
1-4-1. NAME PLATE 9
1-4-2. MODEL CODE 9
1-5. COMBINATION WITH SERVO MOTOR 9
1-6. DIMENSIONS OF SERVO AMPLIFIER 10
1-6-1. DIMENSIONS OF BOOK TYPE1 ( TANGO-B01/B02/B04/B06 ) 10
1-6-2. DIMENSIONS OF BOOK TYPE2 ( TANGO-B08/B12/B18 ) 10
1-6-3. DIMENSIONS OF BASE MOUNT TYPE1 ( TANGO-B24/B30/B35 ) 11
1-6-4. DIMENSIONS OF BASE MOUNT TYPE2 ( TANGO-B40/B50/B75 ) 11
1-7. DIMENSIONS OF OPERATING LOADER 12
CHAPTER 2. INSTALLATION 13
2-1. CHECK ITEMS WHEN PRODUCT DELIVERED 13
2-2. INSTALLATION DIRECTION AND CLEARANCES 13
2-2-1. INSTALLATION OF SERVO AMPLIFIER 13
2-2-2. INSTALLATION OF SERVO MOTOR 14
2-2-3. ENVIRONMENTAL CONDITIONS 14
2-2-4. ALLOWABLE WEIGHT OF MOTOR SHAFT 14
2-2-5. AUXILIARY EQUIPMENTS AND WIRES 15
CHAPTER 3. PARTS IDENTIFICATION 16
3-1. PARTS IDENTIFICATION OF SERVO AMPLIFIER 16
3-1-1. PARTS IDENTIFICATION OF BOOK TYPE1 / TYPE2 16
3-1-2. PARTS IDENTIFICATION OF BASE MOUNT TYPE1 / TYPE2 16
3-1-3. SERVO KEY UNIT 16
3-2. PARTS IDENTIFICATION OF OPERATING LOADER 17
CHAPTER 4. SIGNALS AND WIRING 18
4-1. CONNECTION DIAGRAM OF BOOK TYPE1 / TYPE2 18
4-2. CONNECTION DIAGRAM OF BASE MOUNT TYPE1 / TYPE2 18
4-3. I/O SIGNALS OF CN1 (CONTROL SIGNALS) 19
4-3-1. SIGNAL LAYOUTS AND ASSIGNMENT 19
4-3-2. INPUT INTERFACE 19
4-3-3. OUTPUT INTERFACE 20
4-3-4. IN/OUT SIGNALS OF CN1 20
4-4. MOTOR ENCODER SIGNALS OF CN3 23
4-5. SIGNALS AND WIRING OF CN4, CN5 (POWER, MOTOR, REGENERATIVE BRAKE) 23

CHAPTER 5. SETUP PARAMETER MODE 24
5-1. DEFINITION OF SETUP PARAMETER 24
5-2. SELECTION OF SETUP PARAMETER MODE 24
5-3. OPERATION OF THE LOADER 24
5-4. OPERATION OF THE SERVO KEY UNIT 25
5-5. DETAILED DESCRIPTION OF SETUP PARAMETERS 26
CHAPTER 6. SERVO PARAMETER MODE 37
6-1. DEFINITION OF SERVO PARAMETER 37
6-2. SELECTION OF SERVO PARAMETER MODE 37
6-3. OPERATION OF THE LOADER 37
6-4. OPERATION OF THE SERVO KEY UNIT 38
6-5. DETAILED DESCRIPTION OF SERVO PARAMETERS 39
6-6. SPECIAL SERVO PARAMETERS 43
CHAPTER 7. PROGRAM MODE 44
7-1. SELECTION OF PROGRAM MODE 44
7-2. OPERATION OF THE LOADER 44
7-3. OPERATION OF THE SERVO KEY UNIT 46
7-4. DETAILED DESCRIPTION OF PROGRAM COMMANDS 47
CHAPTER 8. RUN READY MODE 64
8-1. STATUS DISPLAY 64
8-2. OPERATION 65
8-2-1. OPERATION OF THE LOADER 65
8-2-2. OPERATION OF THE EXTERNAL INPUT 66
8-3. SELECTION OF DISPLAY MODE BY THE SERVO KEY UNIT 67
CHAPTER 9. AUTO RUN MODE 68
9-1. START OF AUTO RUN 68
9-2. STATUS DISPLAY 68
9-3. PAUSE OF AUTO RUN 68
9-4. RESET AND EMERGENCY STOP 69
9-5. STEP BY STEP RUN 69
9-6. PROTECTION OF MECHANICAL SYSTEM 69
9-7. ESCAPING FROM LIMIT STATE 70
CHAPTER 10. MANUAL MODE 71
10-1. OPERATION OF THE LOADER 71
10-2. OPERATION OF THE EXTERNAL INPUT 72
10-3. LIMIT ALARM 72
10-4. POINT TEACHING 72

CHAPTER 11. HOME RETURN MODE 73
11-1. HOME RETURN METHOD 73
11-2. SETUP PARAMETERS FOR HOME RETURN 74
11-3. HOME RETURN SEQUENCE 76
11-4. HOME RETURN ERROR 76
11-5. PRECAUTIONS OF HOME RETURN 77
CHAPTER 12. CHECK MODE 78
12-1. SELECTION OF CHECK MODE 78
12-2. INPUT CHECK MODE 78
12-3. OUTPUT CHECK MODE 78
12-4. RETURN TO RUN READY MODE 78
CHAPTER 13. SERVO CHECK MODE 79
13-1. SELECTION OF SERVO CHECK MODE 79
13-2. DETAILED DESCRIPTION OF SERVO CHECK ITEMS 79
CHAPTER 14. ERROR (ALARM) STATUS 82
14-1. TYPE OF ERROR 82
14-2. DETAILED DESCRIPTION OF ERROR ITEMS 83
CHAPTER 15. SERVO GAIN TUNING 88
15-1. MANUAL GAIN TUNING 88
15-2. SEMI-AUTO GAIN TUNING 89
15-3. FULL-AUTO GAIN TUNING 89
CHAPTER 16. SIGNAL TIMING 90
16-1. POWER ON SEQUENCE 90
16-2. SERVO ON / OFF SEQUENCE 90
16-3. BRAKE ON / OFF SEQUENCE 90
CHAPTER 17. OPTIONS 91
17-1. ENCODER AND MOTOR CABLE 91
17-2. IN/OUT CABLE 91
17-3. OPTIONAL REGENERATIVE BRAKE RESISTOR 92
CHAPTER 18. OPTIONAL SPECIAL FUNCTION 93
18-1. EXTERNAL ENCODER (MPG) FUNCTION 93
18-2. ANALOG INPUT FUNCTION 94
18-3. EXTERNAL DECIMAL ROTARY SWITCH AND DISPLAY UNIT 94
CHAPTER 19. MAINTENANCE AND INSPECTION 95
19-1. INSPECTION 95
19-2. LIFE 95

CHAPTER 20. SUMMARY OF LISTS 96
20-1. SETUP AND SERVO PARAMETER LISTS 96
20-2. INSTRUCTION (CODE) LISTS 97
20-3. ERROR (ALARM) LISTS 97
20-4. DISPLAY MODE LISTS 98
20-5. CHECK MODE LISTS 98
20-6. COMBINATION OF AMPLIFIERS AND MOTORS 98
20-7. SERVO PARAMETER INITIAL VALUE AT FACTORY SETTING 98
CHAPTER 21. COMMUNICATION FUNCTIONS 99
21-1. COMMUNICATION CONNECTOR 99
21-2. COMMUNICATION SPECIFICATIONS 99
21-3. RS-232C 100
21-4. RS-422 100
21-5. PROTOCOL 101
21-5-1. DOWN LOAD 101
21-5-2. UP LOAD 101
21-6. COMMUNICATION CODES 102
APPENDIX 106
APPENDIX A. SERVO MOTOR CONFIGURATIONS 107
APPENDIX B. SERVO MOTOR CLASSIFICATION 108
APPENDIX C. SERVO MOTOR SPECIFICATIONS AND CHARACTERISTICS 109
APPENDIX C-1. KANZ/Q SERIES SERVO MOTOR SPECIFICATIONS 109
APPENDIX C-2. KAND/S SERIES SERVO MOTOR SPECIFICATIONS 110
APPENDIX C-3. KANH/F SERIES SERVO MOTOR SPECIFICATIONS 111
APPENDIX C-4. KAFX/N SERIES SERVO MOTOR SPECIFICATIONS 112
APPENDIX D. SERVO MOTOR DIMENSIONS 113
APPENDIX E. ELECTROMAGNETIC BRAKE SPECIFICATIONS 116
APPENDIX F. SHAFT END SPECIFICATIONS 117
APPENDIX G. CONNECTOR PIN ARRANGEMENT 118

Safety Instructions
(After being familiar with this user's manual, use the TANGO Series Servo Drive.)
Do not attempt to install, operate, maintain or inspect the servo amplifier and motor until you have
read through this User's Manual and appended documents carefully.
After reading all, keep the manual well in order that the user of product can easily access it.
In this User's Manual, the safety instruction levels are classified into "DANGER" and "CAUTION".
DANGER : Indicates that incorrect handling may cause hazardous
conditions to make the death or severe injury
CAUTION : Indicates that incorrect handling may cause hazardous
conditions to make the medium and slight injury to
personnel or may cause physical damage.
☞Note that the "CAUTION" level may lead to a serious result according to conditions.
Please follow the instructions of both levels because they are important to personnel safety.
Be sure to keep it.
DANGER To prevent electric shock, note the following:☞
▶Before wiring or inspection, switch power off and wait for more than 10 minutes. Then, confirm the
voltage is safe with voltage tester. Otherwise, you may get an electric shock.
▶Connect the servo amplifier and motor to ground(class 3). There might be the electric shock or
fire.
▶Operate the switches with dry hand to prevent from an electric shock.
▶The cables should not be damaged, stressed loaded or pinched. Otherwise, youmaygetan
electric shock.
▶Thewiringshouldbedonebytheprofessional electrician. There might be the electric shock or fire.
DANGER To prevent fire, note the following:☞
▶Do not install the servo amplifier, motor and regenerative brake resistor onornearcombustibles.
Otherwise, a fire may cause.
▶When the servo amplifier has becomes faulty, switch off the main power side.
Continuous flow of a large current may cause a fire.
▶When a regenerative brake resistor is used, use an alarm signal to switch main power off.
Otherwise, a regenerative brake resistor fault or the like may overheat the regenerative brake
resistor, cause a fire.
▶When installing the servo amplifier in enclosed space, install the cooling fan to make the ambient
temperature around the servo amplifier less than 55 .℃

CAUTION To prevent injury, note the following:☞
▶Care must be taken during the transportation. Falling to the foot may cause the injury.
▶Only the voltage specified in the User's Manual should be applied to each terminal.
Otherwise, a burst, damage, etc. may occur.
▶Connect the terminals correctly to prevent a burst, damage, etc.
▶During power-on or some time after power-off, do not touch the servo amplifier fins, regenerative
brake resistor, servo motor. Their temperatures may be high and you may get burnt.
CAUTION Transportation☞
▶Do not carry the motor by the cables, shaft or encoder.
▶Donotholdthecovertotransporttheservo amplifier. The servo amplifier may drop.
▶Transport the products correctly according to their weights.
▶Do not climb or stand on servo equipment. Do not put heavy objects on equipment.
CAUTION Installation and Storage☞
▶Install the servo amplifier in a load-bearing place in accordance with the User's Manual.
▶The servo amplifier and motor must be installed in the specified direction.
▶Leavespecifiedclearancebetweentheservoamplifierandcontrolenclosure walls or other
equipment.
▶Provide adequate protection to prevent screws and other conductive matter,oilandother
combustible matter from enteringtheservoamplifier.
▶Securely attach the servo motor to the machine. if attach insecurely, the servo motor may come off
during operation.
▶For safety of personnel, always cover rotating and moving parts.
▶Never hit the servo motor or shaft, especially when coupling the servo motor to the machine.
The encoder may become faulty.
▶The servo motor with reduction gear must be installed in the specified direction to prevent
from oil leakage.
▶Do not subject the servo motor shaft to more than the permissible load. Otherwise, the shaft may
break
▶Use the servo motor and amplifier under the following environmental conditions.
Environment Servo Amplifier Servo Motor
Ambient
Temperature operate 0 +55 (non-freezing)℃ ~ ℃ 0 +40 ((non-freezing)℃~ ℃
storage -20 +65 ((non-freezing)℃ ~ ℃ -15 +70 ((non-freezing)℃~ ℃
Ambient
Humidity operate 80%RH or less (non-condensing) 80%RH or less (non-condensing)
storage 90%RH or less (non-condensing) 90%RH or less (non-condensing)
Ambience Indoor(no direct sunlight)
free from corrosive gas, flammable gas, oil mist, dust and dirt
Altitude Max. 1000m above sea level
Vibration 0.6G or less 2.5G or less

CAUTION Wiring☞
▶Wire the equipment correctly. Otherwise, the servo motor and amplifier may be damaged.
▶Connect the output terminals(U, V, W, FG) correctly. Otherwise, the servo and amplifier may be
damaged.
▶Do not install a power capacitor, surge absorber or radio noise filter between the servo motor
and servo amplifier.
▶The surge absorbing diode installed on the DC output signal relay must be wired in the specified
direction. Otherwise, the servo amplifier output damaged by over-current permanently.
▶Do not connect AC power directly to the servo motor.
If then, the servo motor damaged by over-current permanently.
CAUTION Test run and Usage☞
▶Before operation, check the parameter setting. Improper settings cause some machines to perform
unexpected operation.
▶The parameter settings must not be changed excessively. Operation will be unstable.
▶Provide an external emergency stop circuit to ensure that operation can be stopped and power
switched off immediately.
▶Do not modify the equipment.
▶Use the servo motor with the specified amplifier.
▶Do not change the wiring or do not remove the connector during being energized.
▶The electromagnetic brake on the servo motor is designed to hold the shaft and should not to be
used for ordinary braking.
▶When power is restored after an instantaneous power failure, keep away from the machine because
themachinemayberestartedsuddenly.
▶Use a noise filter to minimize the influence of electromagnetic interference.
▶Before resetting an alarm, make sure that the run signal is off to prevent an accident running.
A sudden restart is made if an alarm is reset with the run signal on.
▶When any alarm has occurred, eliminate its cause, ensure safety, and deactivate the alarm before
restarting operation.
CAUTION Maintenance and Inspection☞
▶With age, the electrolytic capacitor will deteriorate. To prevent a second accident due to fault, it is
recommendedtoreplacetheelectrolytic capacitor every 5 years when used in general environment.
▶After cutting off the main power and enough time passed, check and maintain. Due to the residual
voltage at capacitor, it is very dangerous.
▶Since the servo amplifier is designed with the electronic circuit, foreign material or dust cause the
malfunction, periodic (1 year) cleansing and tightening of screw is required.

CHAPTER 1. FUNCTIONS AND SPECIFICATIONS
1-1. FEATURES AND THE PRODUCT
The NS SYSTEM "TANGO-B" series general purpose AC servo motor drive and controller is the
full-digital AC servo for high speed and accuracy by use of 32bit intelligent DSP. It is applicable to
wide range of FA fields, not only precision positioning of machine tools and general automatic
industrial machines but also line speed control and 1-axis robot control. In addition, the I/O function is
able to be applied in the various way such as sensor detection, cylinder control and interface with the
hostdevice.Alsoautotuningfunctionmakesthefirstlearneroperateeasily. Serial communication
function(RS-232C, RS-422) allows a PC or similar device to be for parameter setting, remote control,
test operation and system monitoring, etc.
"TANGO-B" series is the best servo drive and controller to realize the fantastic function and
cost-effective performance.
■FEATURES OF PRODUCT
- It is easy to implement complex motions by virtue of the convenient and diverse commands.
- Convenient editing and powerful program check-up make it easier and faster to input program.
- Big program space (16 file X 96 step).
- Owing to the system set-up functions, the design and modification of the system is convenient.
- Interface with external device is easy with the help of large I/O (input:14,output:8).
- It is possible to edit program and parameters by only servo amplifier without operating loader.
- It is easy to implement the operating panel by virtue of panel type loader.
- Indication of the system's malfunction makes it possible for users to make afastcorrection.
- Initial wiring check and corrective maintenance are easily performed by the exact check mode.
- It provides the most smoothing acceleration/deceleration by virtue of theS-curvemethod.
- Torque limit function for the protection of mechanical systems.
- Mechanical systems are safely protected by the following functions : Prevention from leaving off
the operation range(over-travel) by H/W & S/W,Driver error detection, Allowed time for home
return, Torque limit function for the fragile mechanical systems etc.
- It is possible to interface with analog input and MPG (external encoder).
- Remote control is available for the following operations : program input, automatic operation,
manual operation, system check etc.
1-2. OPERATION MODE
AUTO RUN MODE
An user program is used to control the speed and direction of a servo motor and performs precision
positioning(10000 pulse/rev.). It is easy to implement complex motions by virtue of the convenient
and diverse commands and big program space. It has a scaling factor that is thefunctiontosetthe
pulse movement amount per unit length (mm or inch) or unit revolution (360 deg.).
MANUAL MODE
It performs manual operation by the loader or external switch input. This mode is used for checking
of machine and servo amplifier status, measuring machine stroke, deciding desired operation speed
etc. Point teaching provides very useful distance input method when the exact estimation of the
distance is difficult.
HOME RETURN MODE
It performs home return operation by the loader or external switch input. After the mechanical home
is set by home sensor or ZPH of encoder, the 2nd(work) home can be set by moving the amount of
offset value.

1-3. STANDARD SPECIFICATIONS
[ SMALL SIZED STANDARD SERVO CONTROLLER SPECIFICATIONS ]
Model
Item TANGO
B01 TANGO
B02 TANGO
B04 TANGO
B06
Power
supply Voltage/frequency 3-phase AC 220 [V] +10~-15%, 50/60[Hz]±5%
Capacity [kVA] 0.2 0.4 0.8 1.2
Applicable
motor
Flux shape 3-phase sine-wave AC servo motor
Rated output 30 / 50 /
100[W] 200[W] 300 / 400 /
450[W] 500 / 600[W]
Max. current [rms A] 3.0 5.0 11 14.0
Encoder Standard : incremental encoder (2500/5000CT) , Line driver output
Max. speed [rpm] 2000 / 2500 / 3000 / 4500 / 5000
Control method 3-phase sine-wave PWM control
Position
Unit Linear system 0.01 / 0.001 / 0.1 [mm] or [inch]
Index system 0.01 / 0.001 / 0.1 [deg]
Max.
position Linear system ±9999.99 / 999.999 / 99999.9 [mm] or [inch]
Index system ±9999.99 / 999.999 / 99999.9 [deg]
Scaling factor 1/1000 ~ 60000 [pulse/mm], [pulse/inch], [pulse/deg]
Operation mode Auto run, Step by step run, Manual run
Home return Manualhome,Filerunhome,Programhome
Program Input device Built-in servo key, Handy loader, Panel loader, PC
Capacity 1600 step ( 16 file x 96 step )
File selection Internal parameter or external switch input
In/out Input 14 point, photo-coupler isolation
Output 8 point, photo-coupler isolation
Instruction
Positioning G00(positioning), G05(point positioning), G06(external point positioning)
G26(saved point positioning), G99(block positioning), G93(home return),
G31(BCD positioning)
Continuous running G22(continuous speed running), G39(position compare jump)
Preparatory
function G04(dwell), G08(acc. time), G90(abs.), G91(inc.), G25(save position)
G29(compare position), G92(set coordinate), G94(set home position)
Program
control
M00(pause), M10,M11,M12,M13(loop control), M30,M31(end program)
M40(call subroutine), M42(return to main), M50(jump), M56(ext. jump)
M64(error stop), M65(user error stop), M99(no operation)
Counter M20,M21,M22(work), M23,M24,M25,M26,M27,M28,M29(general)
In/out M60(output on), M61(output off), M62(multi output on), M63(multi output
off), M57(multi input compare and jump), M70(wait input on), M71(wait
inputoff),M52(inputonjump),M53(inputoffjump)
Speed F00(speed). F01(analog speed), F10(BCD speed)
Protective
functions
Amplifier Over-current, Over-voltage, Under-voltage, Over-regeneration,
Over-voltage, Encoder fault, Over-load, Over-speed, Excessive error,
A/D error, Memory error
Controller Loader error, H/W limit, S/W limit, home error, emergency stop
switch input error, program error
Option Panel loader, Handy loader, BCD panel, I/O terminal board, I/O cable,
Motorcable,Encodercable,Regenerativebrakeresistor,MPGfunction
Communication RS232C, RS422(Option)
Environment
Ambient
temperature 0~55℃
Ambient
humidity 80%RH or less (non-condensing)
Insulation res. DC 500[V], 10[M ] or moreΩ
Structure Book Type1
Cooling method Natural air cooling
Weight 0.9Kg

[ MIDDLE SIZED STANDARD SERVO CONTROLLER SPECIFICATIONS ]
Model
Item TANGO
B08 TANGO
B12 TANGO
B18
Power
supply Voltage/frequency 3-phase AC 220 [V] +10~-15%, 50/60[Hz]±5%
Capacity [kVA] 1.6 2.4 3.6
Applicable
motor
Flux shape 3-phase sine-wave AC servo motor
Rated output 750 / 850[W] 0.9 / 1.0 / 1.2 /
1.3[KW] 1.5 / 1.8 / 2.0[KW]
Max. current [rms A] 17.0 28.0 37.0
Encoder Standard : incremental encoder (2500/5000CT) , Line driver output
Max. speed [rpm] 2000 / 2500 / 3000
/4500 2000 / 2500 / 3000 2000 / 2500 / 3000
Control method 3-phase sine-wave PWM control
Position
Unit Linear system 0.01 / 0.001 / 0.1 [mm] or [inch]
Index system 0.01 / 0.001 / 0.1 [deg]
Max.
position Linear system ±9999.99 / 999.999 / 99999.9 [mm] or [inch]
Index system ±9999.99 / 999.999 / 99999.9 [deg]
Scaling factor 1/1000 ~ 60000 [pulse/mm], [pulse/inch], [pulse/deg]
Operation mode Auto run, Step by step run, Manual run
Home return Manual home, File run home, Program home
Program Input device Built-in servo key, Handy loader, Panel loader, PC
Capacity 1600 step ( 16 file x 96 step )
File selection Internal parameter or external switch input
In/out Input 14 point, photo-coupler isolation
Output 8 point, photo-coupler isolation
Instruction
Positioning G00(positioning), G05(point positioning), G06(external point positioning)
G26(saved point positioning), G99(block positioning), G93(home return),
G31(BCD positioning)
Continuous running G22(continuous speed running), G39(position compare jump)
Preparatory
function G04(dwell), G08(acc. time), G90(abs.), G91(inc.), G25(save position)
G29(compare position), G92(set coordinate), G94(set home position)
Program
control
M00(pause), M10,M11,M12,M13(loop control), M30,M31(end program)
M40(call subroutine), M42(return to main), M50(jump), M56(ext. jump)
M64(error stop), M65(user error stop), M99(no operation)
Counter M20,M21,M22(work), M23,M24,M25,M26,M27,M28,M29(general)
In/out M60(output on), M61(output off), M62(multi output on), M63(multi output
off), M57(multi input compare and jump), M70(wait input on), M71(wait
inputoff),M52(inputonjump),M53(inputoffjump)
Speed F00(speed). F01(analog speed), F10(BCD speed)
Protective
functions
Amplifier Over-current, Over-voltage, Under-voltage, Over-regeneration,
Over-voltage, Encoder fault, Over-load, Over-speed, Excessive error,
A/D error, Memory error
Controller Loader error, H/W limit, S/W limit, home error, emergency stop
switch input error, program error
Option Panel loader, Handy loader, BCD panel, I/O terminal board, I/O cable,
Motor cable, Encoder cable, Regenerative brake resistor, MPG function
Communication RS232C, RS422(Option)
Environment
Ambient
temperature 0~55℃
Ambient
humidity 80%RH or less (non-condensing)
Insulation res. DC 500[V], 10[M ] or moreΩ
Structure Book Type2
Cooling method Natural air cooling
Weight 1.5Kg

[ LOWER LARGE SIZED STANDARD SERVO CONTROLLER SPECIFICATIONS ]
Model
Item TANGO
B24 TANGO
B30 TANGO
B35
Power
supply Voltage/frequency 3-phase AC 220 [V] +10~-15%, 50/60[Hz]±5%
Capacity [kVA] 4.8 6.0 7.0
Applicable
motor
Flux shape 3-phase sine-wave AC servo motor
Rated output 1.8 / 2.0 / 2.5[KW] 2.9 / 3.0[KW] 3.5[KW]
Max. current [rms A] 40.0 57.0 65.0
Encoder Standard : incremental encoder (2500/5000CT) , Line driver output
Max. speed [rpm] 2000 / 2500 / 3000 2000 /2500 / 3000 2000 / 2500 / 3000
Control method 3-phase sine-wave PWM control
Position
Unit Linear system 0.01 / 0.001 / 0.1 [mm] or [inch]
Index system 0.01 / 0.001 / 0.1 [deg]
Max.
position Linear system ±9999.99 / 999.999 / 99999.9 [mm] or [inch]
Index system ±9999.99 / 999.999 / 99999.9 [deg]
Scaling factor 1/1000 ~ 60000 [pulse/mm], [pulse/inch], [pulse/deg]
Operation mode Auto run, Step by step run, Manual run
Home return Manual home, File run home, Program home
Program Input device Built-in servo key, Handy loader, Panel loader, PC
Capacity 1600 step ( 16 file x 96 step )
File selection Internal parameter or external switch input
In/out Input 14 point, photo-coupler isolation
Output 8 point, photo-coupler isolation
Instruction
Positioning G00(positioning), G05(point positioning), G06(external point positioning)
G26(saved point positioning), G99(block positioning), G93(home return),
G31(BCD positioning)
Continuous running G22(continuous speed running), G39(position compare jump)
Preparatory
function G04(dwell), G08(acc. time), G90(abs.), G91(inc.), G25(save position)
G29(compare position), G92(set coordinate), G94(set home position)
Program
control
M00(pause), M10,M11,M12,M13(loop control), M30,M31(end program)
M40(call subroutine), M42(return to main), M50(jump), M56(ext. jump)
M64(error stop), M65(user error stop), M99(no operation)
Counter M20,M21,M22(work), M23,M24,M25,M26,M27,M28,M29(general)
In/out M60(output on), M61(output off), M62(multi output on), M63(multi output
off), M57(multi input compare and jump), M70(wait input on), M71(wait
inputoff),M52(inputonjump),M53(inputoffjump)
Speed F00(speed). F01(analog speed), F10(BCD speed)
Protective
functions
Amplifier Over-current, Over-voltage, Under-voltage, Over-regeneration,
Over-voltage, Encoder fault, Over-load, Over-speed, Excessive error,
A/D error, Memory error
Controller Loader error, H/W limit, S/W limit, home error, emergency stop
switch input error, program error
Option Panel loader, Handy loader, BCD panel, I/O terminal board, I/O cable,
Motorcable,Encodercable,Regenerativebrakeresistor,MPGfunction
Communication RS232C, RS422(Option)
Environment
Ambient
temperature 0~55℃
Ambient
humidity 80%RH or less (non-condensing)
Insulation res. DC 500[V], 10[M ] or moreΩ
Structure Base Mount Type1
Cooling method Forced air cooling
Weight 5.3Kg

[ LARGE SIZED STANDARD SERVO CONTROLLER SPECIFICATIONS ]
Model
Item TANGO
B40 TANGO
B50 TANGO
B75 TANGO
BH1
Power
supply Voltage/frequency 3-phase AC 220 [V] +10~-15%, 50/60[Hz]±5%
Capacity [kVA] 8.0 10.0 15.0
Applicable
motor
Flux shape 3-phase sine-wave AC servo motor
Rated output 4.0[KW] 4.4/4.5/5.0[KW] 6.0/6.5/7.5[KW] 11.0[KW]
Max. current [rms A] 75.0 85.0 105.0 198.0
Encoder Standard : incremental encoder (2500/5000CT) , Line driver output
Max. speed [rpm] 2000 / 2500 / 3000
Control method 3-phase sine-wave PWM control
Position
Unit Linear system 0.01 / 0.001 / 0.1 [mm] or [inch]
Index system 0.01 / 0.001 / 0.1 [deg]
Max.
position Linear system ±9999.99 / 999.999 / 99999.9 [mm] or [inch]
Index system ±9999.99 / 999.999 / 99999.9 [deg]
Scaling factor 1/1000 ~ 60000 [pulse/mm], [pulse/inch], [pulse/deg]
Operation mode Auto run, Step by step run, Manual run
Home return Manual home, File run home, Program home
Program Input device Built-in servo key, Handy loader, Panel loader, PC
Capacity 1600 step ( 16 file x 96 step )
File selection Internal parameter or external switch input
In/out Input 14 point, photo-coupler isolation
Output 8 point, photo-coupler isolation
Instruction
Positioning G00(positioning), G05(point positioning), G06(external point positioning)
G26(saved point positioning), G99(block positioning), G93(home return),
G31(BCD positioning)
Continuous running G22(continuous speed running), G39(position compare jump)
Preparatory
function G04(dwell), G08(acc. time), G90(abs.), G91(inc.), G25(save position)
G29(compare position), G92(set coordinate), G94(set home position)
Program
control
M00(pause), M10,M11,M12,M13(loop control), M30,M31(end program)
M40(call subroutine), M42(return to main), M50(jump), M56(ext. jump)
M64(error stop), M65(user error stop), M99(no operation)
Counter M20,M21,M22(work), M23,M24,M25,M26,M27,M28,M29(general)
In/out M60(output on), M61(output off), M62(multi output on), M63(multi output
off), M57(multi input compare and jump), M70(wait input on), M71(wait
inputoff),M52(inputonjump),M53(inputoffjump)
Speed F00(speed). F01(analog speed), F10(BCD speed)
Protective
functions
Amplifier Over-current, Over-voltage, Under-voltage, Over-regeneration,
Over-voltage, Encoder fault, Over-load, Over-speed, Excessive error,
A/D error, Memory error
Controller Loader error, H/W limit, S/W limit, home error, emergency stop
switch input error, program error
Option Panel loader, Handy loader, BCD panel, I/O terminal board, I/O cable,
Motorcable,Encodercable,Regenerativebrakeresistor,MPGfunction
Communication RS232C, RS422(Option)
Environment
Ambient
temperature 0~55℃
Ambient
humidity 80%RH or less (non-condensing)
Insulation res. DC 500[V], 10[M ] or moreΩ
Structure Base Mount Type2
Cooling method Forced air cooling
Weight 7.2Kg

1-4. MODEL CODE DEFINITION
1-4-1. NAME PLATE
Model name
Capacity
Input power
Serial number
1-4-2. MODEL CODE
TANGO -□ □□
Series Capacity
name Amplifier type
1-5. COMBINATION WITH SERVO MOTOR
Thefollowingtablelistscombinations of servo amplifier and servo motor. Thesamecombinations
apply to the models with electromagnetic brakes, the models with reduction gears.
Contact us when using a non-standard servo motor.
Servo
Amplifier Servo Motor
KANZ KANQ KAND KANS KANH KANF KAFX KAFN
TANGO-B01 KANZ-A5B
KANZ-01B KANQ-01B
TANGO-B02 KANZ-02B KANQ-02B
TANGO-B04 KANZ-04B KANQ-04B KANF04 KAFN03
TANGO-B06 KANZ-06B KAFX05
TANGO-B08 KANZ-08B KANH05 KANF08 KAFX09 KAFN06
TANGO-B12 KANZ-10B KAND10 KANH10 KAFN09
TANGO-B18 KAND15 KANH15 KANF15 KAFX13 KAFN12
TANGO-B24 KAND20 KANH20 KANF25 KAFX20 KAFN20
TANGO-B30 KAND25 KAFX30S KAFN30
TANGO-B35 KAND30
KAND45S KANH30
KANH40S KANF35S KAFX30
TANGO-B40 KAND45 KANS40 KANH40 KANF35 KAFX45
TANGO-B50 KAND50 KANS45
KANS50S KANH50 KANF45
TANGO-B75 KANS50
TANGO-BH1 KANF110
model type
AGeneral-purpose
B1axiscontroller
CLowcost
DOrdermade
E Multi-axis
F~Z Special-purpose
symbol output symbol output symbol output symbol output
01 0.1kw 08 0.8kw 30 3.0kw 75 7.5kw
02 0.2kw 12 1.2kw 35 3.5kw H1 11kw
04 0.4kw 18 1.8kw 40 4.0kw
06 0.6kw 24 2.4kw 50 5.0kw

1-6. DIMENSIONS OF SERVO AMPLIFIER
1-6-1. DIMENSIONS OF BOOK TYPE1 ( TANGO-B01/B02/B04/B06 )
1-6-2. DIMENSIONS OF BOOK TYPE2 ( TANGO-B08/B12/B18 )

1-6-3. DIMENSIONS OF BASE MOUNT TYPE1 ( TANGO-B24/B30/B35 )
1-6-4. DIMENSIONS OF BASE MOUNT TYPE2 ( TANGO-B40/B50/B75 )

1-7. DIMENSIONS OF OPERATING LOADER
( Dimensions of panel loader ) ( Dimensions of handy loader )
( Dimensions of panel loader cutting)

CHAPTER 2. INSTALLATION
2-1. CHECK ITEMS WHEN PRODUCT DELIVERED
Check the following items first when the product is delivered.
1. Check whether the product conforms to the ordered specifications.
2. Check whether the product is not damaged.
3. Check whether the coupling part is loosened.
4. Check whether the motor shaft is smooth and no stalled feeling when turned by hand.
5. Check whether the combinations of servo amplifier and servo motor is matched.
If any trouble, immediately contact the distributor you bought or us.☞
2-2. INSTALLATION DIRECTION AND CLEARANCES
2-2-1. INSTALLATION OF SERVO AMPLIFIER
Servo amplifier is designed for vertical installation type. For natural cooling, the vertical installation
direction should be observed as the following figure.
Amplifier Mounted wall
Ventilation
If the ambient temperature excess the allowable temperature range(55 ), thecoolingfanshouldbe℃
installed in the control box. Since the ambient temperature has the close relationship with the lifetime,
keep it at the lower temperature as possible. Install the servo amplifier under the following clearance
conditions.
A
BC
D
When installing the servo amplifier in a control box, prevent drill chips and wire fragments from the
servoamplifier.Wheninstallingthecontrolboxinaplacewheretherearetoxic gas, dirt and dust,
provide positive pressure in the control box by forcing in clean air to prevent such materials from
entering the control box.
The way of clamping the cable must be fully examined so that flexing stress andcable'sownweight
stress are not applied to the cable connection.
ABCD
50mm
or more 30mm
or more 10mm
or more 50mm
or more

2-2-2. INSTALLATION OF SERVO MOTOR
The servo motor is available for both vertical and horizontal installation. But since the bad environment
of the installation condition affects the lifetime of motor and the unexpected accident, it should be
installed according to the following descriptions.
☞Since the rust-preventative is coated on the shaft and flange surface for rust-proof during the
preservation,besuretocleantherust-preventative before installation.
☞The servo motor is subject to be used in indoor environment. If there are much water and oil
drops around, the cover should be attached.
☞When connecting with load, the shaft of motor should be aligned exactly with that of the counter
load. Otherwise, it cause the vibration, acoustic noise and damages.
The concentricity and gap should be less than 3/100mm.
☞The excessive external shock may break the motor bearing and encoder.
If the reducer, pulley and coupling are used, do not apply the excessive shock(50G and above)
to the motor shaft.
2-2-3. ENVIRONMENTAL CONDITIONS
Environment Servo Amplifier Servo Motor
Ambient
Temperature operate 0 +55 (non-freezing)℃ ~ ℃ 0 +40 ((non-freezing)℃~ ℃
storage -20 +65 ((non-freezing)℃ ~ ℃ -15 +70 ((non-freezing)℃~ ℃
Ambient
Humidity operate 80%RH or less (non-condensing) 80%RH or less (non-condensing)
storage 90%RH or less (non-condensing) 90%RH or less (non-condensing)
Ambience Indoor(no direct sunlight)
free from corrosive gas, flammable gas, oil mist, dust and dirt
Altitude Max. 1000m above sea level
Vibration 0.6G or less 2.5G or less
2-2-4. ALLOWABLE WEIGHT OF MOTOR SHAFT
Radial weight Trust weight
NkgfNkgf
196 20 49 5

2-2-5. AUXILIARY EQUIPMENTS AND WIRES
Power supply : 3-phase AC 200V ~ 230V■
No-fuse breaker(NFB)■
Noise filter■
■Magnetic contactor
Magnetic contactor may be installed when needed. The capacity of that
is same as NFB
■Regenerative brake resistor
■Motor power
■Grounding: Class D grounding is recommended(100 ohm or less).
Be sure to perform one point grounding(do not make the loop).
Amplifier Wire[ ]㎟ Amplifier Wire[ ]㎟ Amplifier Wire[ ]㎟
TANGO-B01 2(AWG14) TANGO-B12 2(AWG14) TANGO-B40 5.5(AWG10)
TANGO-B02 2(AWG14) TANGO-B18 3.5(AWG12) TANGO-B50 5.5(AWG10)
TANGO-B04 2(AWG14) TANGO-B24 3.5(AWG12) TANGO-B75 8(AWG8)
TANGO-B06 2(AWG14) TANGO-B30 5.5(AWG10) TANGO-BH1 13(AWG6)
TANGO-B08 2(AWG14) TANGO-B35 5.5(AWG10)
Amplifier NFB Amplifier NFB Amplifier NFB
TANGO-B01 250V/5A TANGO-B12 250V/20A TANGO-B40 250V/50A
TANGO-B02 250V/5A TANGO-B18 250V/30A TANGO-B50 250V/75A
TANGO-B04 250V/10A TANGO-B24 250V/30A TANGO-B75 250V/100A
TANGO-B06 250V/15A TANGO-B30 250V/40A TANGO-BH1 250V/150A
TANGO-B08 250V/15A TANGO-B35 250V/40A
Amplifier Rating Amplifier Rating Amplifier Rating
TANGO-B01 250V/5A TANGO-B12 250V/20A TANGO-B40 250V/50A
TANGO-B02 250V/5A TANGO-B18 250V/30A TANGO-B50 250V/75A
TANGO-B04 250V/10A TANGO-B24 250V/30A TANGO-B75 250V/100A
TANGO-B06 250V/15A TANGO-B30 250V/40A TANGO-BH1 250V/150A
TANGO-B08 250V/15A TANGO-B35 250V/40A
Amplifier Wire[ ]㎟
TANGO-B35 or less 2(AWG14)
TANGO-B40/B50/B75/BH1 3.5(AWG12)
Amplifier Wire[ ]㎟ Amplifier Wire[ ]㎟ Amplifier Wire[ ]㎟
TANGO-B01 1.25(AWG16) TANGO-B12 2(AWG14) TANGO-B40 5.5(AWG10)
TANGO-B02 1.25(AWG16) TANGO-B18 3.5(AWG12) TANGO-B50 5.5(AWG10)
TANGO-B04 1.25(AWG16) TANGO-B24 3.5(AWG12) TANGO-B75 8(AWG8)
TANGO-B06 1.25(AWG16) TANGO-B30 5.5(AWG10) TANGO-BH1 13(AWG6)
TANGO-B08 2(AWG14) TANGO-B35 5.5(AWG10)
Amplifier Wire[ ]㎟
TANGO-B35 or less 2(AWG14)
TANGO-B40/B50/B75/BH1 3.5(AWG12)
Table of contents
Popular Servo Drive manuals by other brands

SEW-Eurodrive
SEW-Eurodrive CMP Series Addendum to the operating instructions
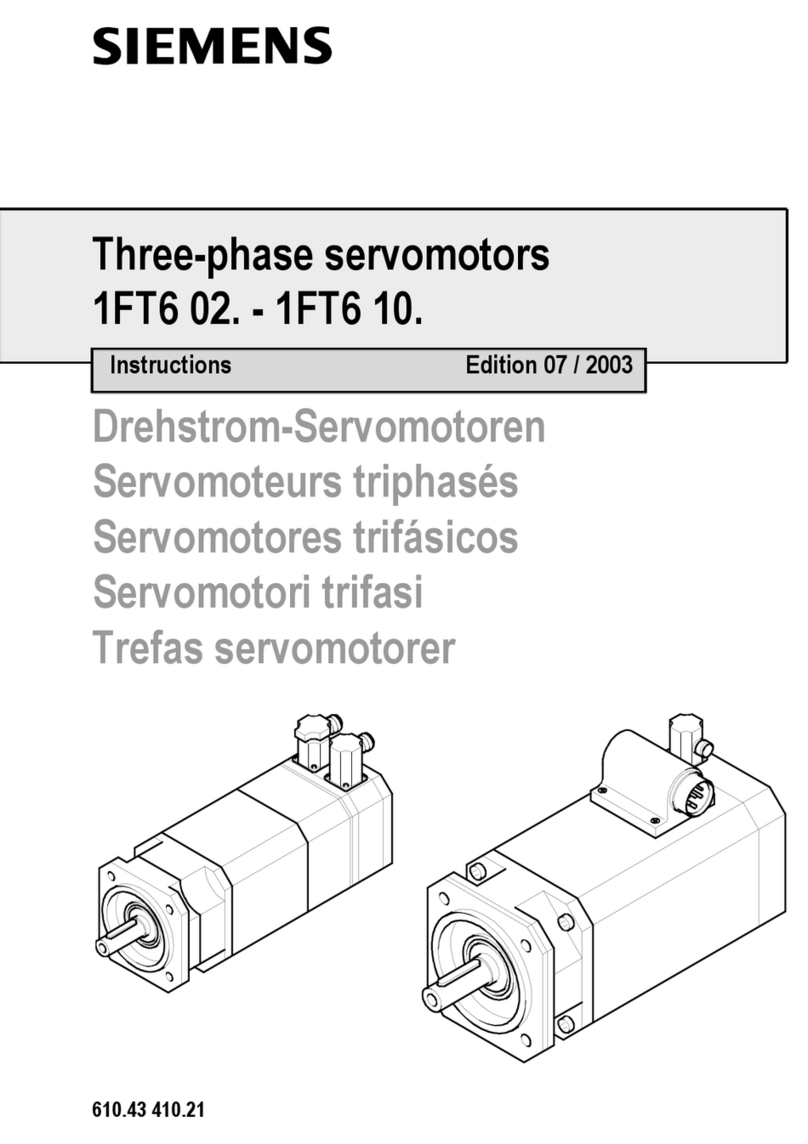
Siemens
Siemens 1FT6 02 Series instructions
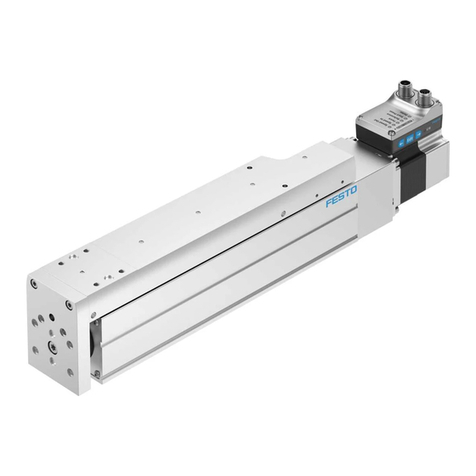
Festo
Festo EGSS-BS operating instructions

Rockwell Automation
Rockwell Automation Reliance electric GV3000/SE instruction manual
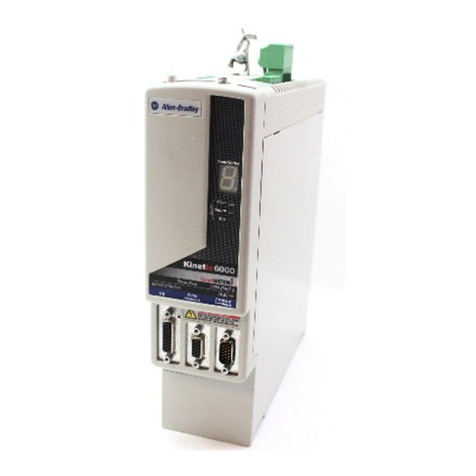
Allen-Bradley
Allen-Bradley Kinetix 6000 Design guide
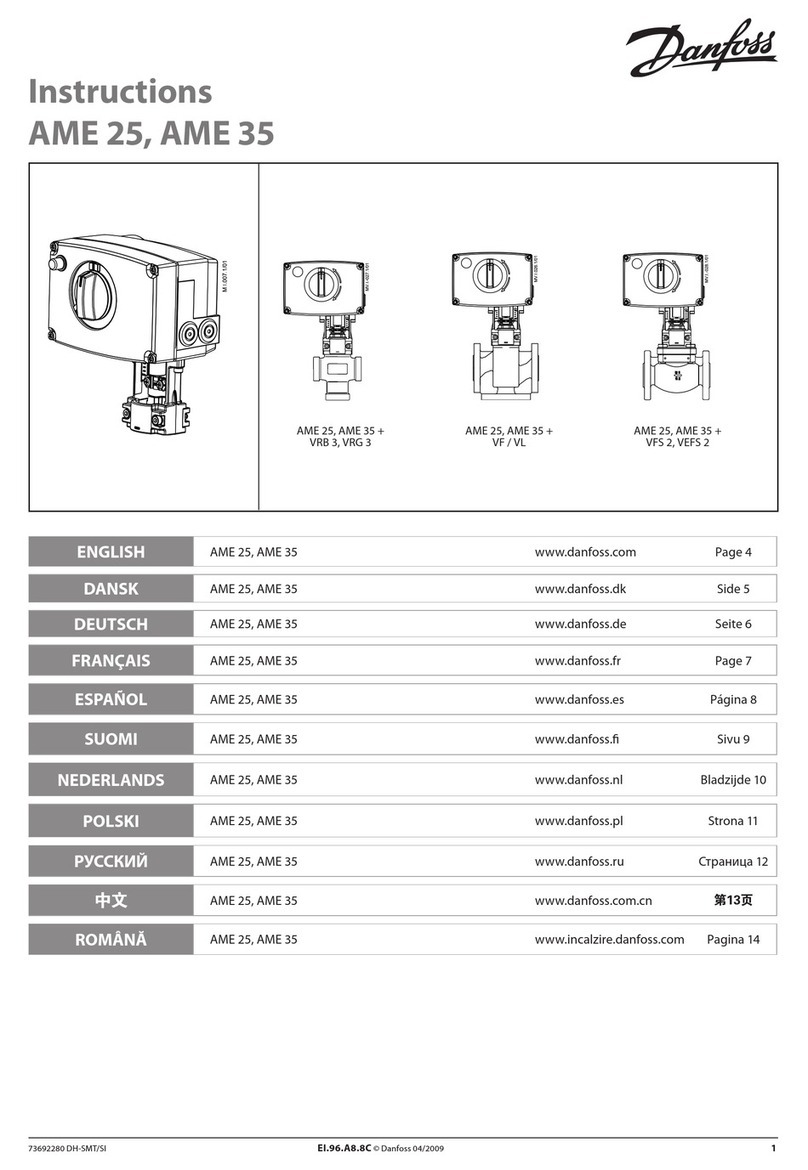
Danfoss
Danfoss AME 25 instructions