NTM SSQ MultiPro User manual


TABLE OF CONTENTS
i
CHAPTER 1……....
CHAPTER 2…........
CHAPTER 3……….
CHAPTER 4……….
CHAPTER 5……….
CHAPTER 6……….
CHAPTER 7……….
CHAPTER 8……….
CHAPTER 9………
CHAPTER 10……..
CHAPTER 11……..
CHAPTER 12……..
CHAPTER 13……..
CHAPTER 14……..
CHAPTER 15……..
CHAPTER 16……..
CHAPTER 17……..
CHAPTER 18……..
CHAPTER 19……..
APPENDEX A..…...
APPENDEX B…….
SPECIFICATIONS ..........................................................................................1
PRECAUTIONS ..............................................................................................2
MACHINE ORIENTATION ...........................................................................3
GENERAL MAINENANCE ...........................................................................5
Recommended Lubricants and Fluids......................................................6
ELECTRICAL CONTROLS AND OPERATION ..........................................9
REEL STANDS, REELS AND EXPANDABLE ARBORS.........................16
HYDRAULIC SYSTEMS .............................................................................22
Maintenance...........................................................................................22
Hydraulic Fluid Troubleshooting...........................................................22
Changing Hydraulic Fluid and Filter .....................................................22
DRIVE SYSTEM ...........................................................................................26
SHEAR ASSEMBLY.....................................................................................30
BEAD AND STRIATION ROLLER ASSEMBLY.......................................34
ENTRY GUIDE ADJUSTMENT ..................................................................36
CLIP RELIEF ROLLER ASSEMBLY..........................................................39
ENTRY DRUM ASSEMBLY .......................................................................40
WIDTH CHANGE PROCEDURE ................................................................41
PROFILE CHANGEOVER PROCEDURE ..................................................49
ROLLER SYSTEMS AND PANEL PROFILE DRAWINGS ......................64
RUN OUT TABLES AND REMOTE LIMIT SWITCH...............................85
QUICK CHANGE POWER PAC..................................................................88
TROUBLESHOOTING .................................................................................90
COMPUTER BATCH AND LENGTH CONTROLLER................................1
Introduction..............................................................................................2
Manual Operations...................................................................................3
Production Procedures .............................................................................3
Administrative Screens and Functions.....................................................6
Troubleshooting .......................................................................................7
ELECTRICAL SCHEMATICS .......................................................................1

LIST OF FIGURES
ii
Figure 1: Machine Orientation............................................................................................................ 3
Figure 2: Mounting Foot Detail ..........................................................................................................4
Figure 3: Entry Guide .........................................................................................................................7
Figure 4: Acme Shafts and Left Side Adjustment ..............................................................................8
Figure 5: Controls .............................................................................................................................12
Figure 6: Control Cables...................................................................................................................13
Figure 7: Run Out Table and Remote Limit Switch .........................................................................14
Figure 8: Main Control Box Fuse .....................................................................................................15
Figure 9: QCPP E 1-6 Fuse Location ...............................................................................................15
Figure 10: Expandable Arbor Set-Up ............................................................................................... 17
Figure 11: Expandable Reel Assembly............................................................................................. 19
Figure 12: Material Routing..............................................................................................................21
Figure 13: Hydraulic System – Overview ........................................................................................23
Figure 14: Hydraulic System – Details.............................................................................................24
Figure 15: Hydraulic Fluid Level .....................................................................................................25
Figure 16: Drive Roll Assembly View ............................................................................................. 27
Figure 17: Gears and Shafts.............................................................................................................. 28
Figure 18: Chains Upper and Lower.................................................................................................29
Figure 19: Entry/Exit Views .............................................................................................................31
Figure 20: Shear Die Detail Views ...................................................................................................32
Figure 21: Bead Roller Assembly.....................................................................................................35
Figure 22: Right Entry Guide ........................................................................................................... 36
Figure 23: Entry Guide Assembly ....................................................................................................37
Figure 24: Tooling Rail Adjustment Handle ....................................................................................38
Figure 25: Marker Plate & Alignment Pin........................................................................................ 38
Figure 26: Disengaged ......................................................................................................................38
Figure 27: Engaged ........................................................................................................................... 38
Figure 28: Clip Relief Roller Assembly ...........................................................................................39
Figure 29: Entry Drum......................................................................................................................40
Figure 30: Entry Guide Bolts "A"..................................................................................................... 41
Figure 31: Expandable Arbor Setup ................................................................................................. 42
Figure 32: Loading Material .............................................................................................................43
Figure 33: Bead Roller Alignment....................................................................................................44
Figure 34: Bead Roller Width Change..............................................................................................45
Figure 35: Shear Bolts ...................................................................................................................... 46
Figure 36: Exit Die Adjustment........................................................................................................ 47
Figure 37: Remove Top Covers........................................................................................................ 49
Figure 38: Removing Tooling Rails .................................................................................................50
Figure 39: Block Chart......................................................................................................................50
Figure 40: Inboard/Outboard Positions............................................................................................. 51
Figure 41: April 2009 and later.........................................................................................................52
Figure 42: Machines made before April 2009 ..................................................................................52
Figure 43: Right Side Fixed Mount Rail...........................................................................................53
Figure 44: Profile Chart .................................................................................................................... 53
Figure 45: Left Side Fixed Mount Rail.............................................................................................54
Figure 46: Shown in the “A” position............................................................................................... 54

LIST OF FIGURES
iii
Figure 47: Tooling Rail Identification .............................................................................................. 55
Figure 48: R1 Tooling Rail Spacers.................................................................................................. 55
Figure 49: L1-1 Special Instructions.................................................................................................56
Figure 50: Entry Guide Alignment Notches and Pins ...................................................................... 57
Figure 51: Tooling Rail Adjustment Handle ....................................................................................57
Figure 52: Marker Plate Notch and Pin ............................................................................................ 58
Figure 53: Preparing Coil for Loading..............................................................................................58
Figure 54: Jogging Material thru Machine .......................................................................................59
Figure 55: Spacing Bead Rollers ......................................................................................................59
Figure 56: Removing Shear Cover ...................................................................................................60
Figure 57: Removing Photo Eye and Bracket (If Equipped)............................................................61
Figure 58: Remove Shear Bolts ........................................................................................................61
Figure 59: Exit Die Adjustment........................................................................................................ 62
Figure 60: SSQ100 Roller System.................................................................................................... 64
Figure 61: SS100 Panel Profile......................................................................................................... 65
Figure 62: SSQ150 Roller System.................................................................................................... 66
Figure 63: SS150 Panel Profile......................................................................................................... 67
Figure 64: SSQ200/210A Roller System..........................................................................................68
Figure 65: SS200 Panel Profile......................................................................................................... 69
Figure 66: SS210 Panel Profile......................................................................................................... 70
Figure 67: SSQ450/450SL Roller System ........................................................................................71
Figure 68: SS450 Panel Profile......................................................................................................... 72
Figure 69: SS450SL Panel Profile ....................................................................................................73
Figure 70: SSQ550 Roller System.................................................................................................... 74
Figure 71: SS550 Panel Profile......................................................................................................... 75
Figure 72: SSQ675 Roller System.................................................................................................... 76
Figure 73: SS675 Panel Profile......................................................................................................... 77
Figure 74: FFQ100 Roller System.................................................................................................... 78
Figure 75: FF100 Panel.....................................................................................................................79
Figure 76: FFQ150 Roller System.................................................................................................... 80
Figure 77: FF150 Panel Profile.........................................................................................................81
Figure 78: SSQBP Roller System .....................................................................................................82
Figure 79: BP 1” Panel .....................................................................................................................83
Figure 80: BP 1 1/2” Panel ...............................................................................................................84
Figure 81: Run Out Table ................................................................................................................. 86
Figure 82: Run Out Table Setup .......................................................................................................87
Figure 83: Cable Connections and Fasteners....................................................................................89
Figure 84: Pressure Switch Adjustment............................................................................................ 90
Figure 85: Limit Switch Adjustment ................................................................................................92
Appendices:
Figure 86: AMS Box Without Cables................................................................................................. 1
Figure 87: AMS Box With Cables...................................................................................................... 2
Figure 88: AMS Controls MP465 Controller ..................................................................................... 2

CHAPTER 1
SSQ SPECIFICATIONS
1
SPECIFICATIONS
SSQ Dimensions: Length-13’ 7” (4.1m)
Width-5’ (1.5m)
Height-4’ 3” (1.3m) w/Over Head Rack
1’ 10” (.6m) w/o Over Head Rack
Weight-2200 lbs. (1450kg)
SSQ on Trailer: Length-17’ 6” (5.3m)
Width-7’ (2.1m)
Height-6’ 3” (1.9m) with reel
Weight-4800 lbs. (2200kg)
Speed: 75 ft./min. Approx. (23m/min.) Approx.
Drive: Hydraulic via chain, sprocket and gear using16 polyurethane drive
rollers.
Shear: Hydraulically Powered, Infinitely adjustable, hardened tool steel dies
and blades w/Panel Recognition Proximity Sensor
Hydraulic Fluid: 18 Gallons - 32AW
Coil Width: 15” to 30” (380mm to 760mm) Note:30” coil width requires
Expandable Arbor or Remote De-coiler Stand.
Materials Formed: Painted Steel 30ga. to 22ga. (.3mm to .8mm)
Painted, Galvanized, Aluminized
Painted Aluminum .019” to .040” (.5mm to 1.0mm)
Copper 16 oz. to 20 oz. ¾ Hard
(.5mm to .7mm)
Turne-Coat Stainless Steel 26ga. (.5mm)
Controls: Standard: 12v Manual Control Box w/Length Control
Limit Switch
Optional: Computer Batch and Length Control

CHAPTER 2
PRECAUTIONS
2
PRECAUTIONS
1. Make sure the operator of the machine has read and understands this manual in its
entirety before attempting to operate this equipment.
2. ALWAYS keep covers, guards and lids mounted to machine during operation
3. OBSERVE and OBEY all safety and warning signs affixed to the machine.
4. ALWAYS adhere to and follow all local and national safety codes concerning the loading
and un-loading of reeled coils.
5. USE ONLY properly rated devices for lifting reeled coils into or out of the reel stand
assembly.
6. DO NOT wear loose clothing, jewelry etc. that could become entangled in the moving
parts of the machine when operating.
7. STOP THE MACHINE and disconnect the power before attempting to make any
adjustments, perform any maintenance or changeover procedures.
8. AVOID storing the machine outdoors for long periods of time. Cover with a tarp but
provide good ventilation to prevent condensation and rust.
9. DO NOT USE SOLVENTS TO CLEAN DRIVE ROLLERS!
10. ALWAYS EMPTY MACHINE OF MATERIAL BEFORE TRANSPORT AND
STORAGE.

CHAPTER 3
MACHINE ORIENTATION
3
MACHINE ORIENTATION
Figure 1: Machine Orientation

CHAPTER 3
MACHINE ORIENTATION
4
Figure 2: Mounting Foot Detail

CHAPTER 4
GENERAL MAINTENANCE
5
GENERAL MAINENANCE
1. Always keep covers on during operation and storage. The covers are for operator safety, but
also protect the internal components of the machine from the environment.
2. Avoid storage of the machine outdoors for long periods of time. Cover your machine with a
tarp to protect it but provide good ventilation to prevent condensation and rust.
3. Keep your machine clean. This will increase the life of the machine and make maintenance
easier. A clean machine will provide a clean product.
4. Before operating your machine, visually inspect for foreign objects debris or anything unusual.
If something doesn’t seem correct, inspect and remedy prior to operation.
5. Keep chains properly tensioned. This will add to the life of the chains and sprockets. The chains
should be just snug. An over-tightened chain is just as bad for the machine as a loose chain.
Idler sprockets are provided on each chain for this purpose.
6. Lubricate the chains a minimum of every 40 hours of operation. It is preferable to use a dry
motorcycle chain lube or equivalent.
7. Lubricate the 3 main drive gears a minimum of every 30 hours of operation. Use of an Open
Gear Spray Lubricant is recommended. (Figure 17 & Figure 18 on page 28).
8. Keep Entry Guide Carriage (Figure 3 on page 7) clean and lubricate as needed Spray Lube.
9. Keep Bead Roller Carriage Shafts (Figure 21 on page 35) clean and lubricate with Spray Lube.
10. Lubricate 5 Acme Shafts (Figure 4 on page 8) with Spray Lube as needed.
11. Lubricate Mitre-Gears (Figure 4 on page 8) on ends of Acme Shafts with Spray Lube as needed.
12. Keep Arbor Cradles (Figure 11 on page 19) lubricated with Clear Grease.
13. Lubricate Arbor Nut (Figure 31 on page 42) using a grease gun with EP Grease when threads
begin to look dry.
14. Clean Forming Rollers as needed with a Scotch Brite Pad and a small amount of solvent.
15. Clean Drive Rollers with soap and water or mild solvent free spray cleaner. CAUTION: Do not
use harsh chemicals or solvents or damage will occur.
16. Lubricate both faces of the Shear Blades and Dies (Figure 19 on page 31) a minimum of once
daily with Spray Lube. More should be added as needed before the cut edges begin to
deteriorate.

CHAPTER 4
GENERAL MAINTENANCE
6
Recommended Lubricants and Fluids
Spray Lube for:
Shear Blades, Dies, Entry Guide, Bead Roller Carriage Shafts, Acme Shafts and Mitre Gears
Super Lube - Multi-Purpose Synthetic Dri Film Aerosol Lubricant with Syncolon (PTFE)
Catalog No. 11016
11 oz. Aerosol Can
Available from:
MSC Supply at 1-800-645-7270
Clear Grease for:
Arbor Cradles
Synthetic Extreme Pressure, High Temperature Grease with Syncolon (PTFE)
Catalog No. 71160
400 gram container
Available from:
MSC Supply at 1-800-645-7270
EP Grease for:
Arbor Nuts and Pillow Blocks
Grease - Lubricants Type: Moly Ep Grease
Catalog No. 11335
14 Ounce Container
Available from:
MSC Supply at 1-800-645-7270
Open Gear Spray Lubricant for:
Main Drive Gears
Open Gear and Wire Rope Lubricant
Catalog No. 00257659
11 oz. Aerosol Can
Available from:
MSC Supply at 1-800-645-7270
Hydraulic Fluid (32AW) for:
Hydraulic Tank
Various Manufacturers

CHAPTER 4
GENERAL MAINTENANCE
7
Figure 3: Entry Guide

CHAPTER 4
GENERAL MAINTENANCE
8
Figure 4: Acme Shafts and Left Side Adjustment

CHAPTER 5
ELECTRICAL CONTROLS AND OPERATION
9
ELECTRICAL CONTROLS AND OPERATION
POWER CORD REQUIREMENTS
For machines equipped with a QCPP-E it is very important to follow the power cord
requirement prescribed by the motor and electrical control manufacturers to maintain their
respective warranties. Make sure the cord you are using is marked properly. Do not assume
that because an extension cord looks heavy enough that it is the right gauge. Use of the
wrong gauge extension cord will void the warranty on motor and electrical controls.
GENERATOR USE FOR ELECTRIC MOTOR MACHINES
If a generator will be used to power the machine it must be large enough to handle the amp
draw requirements of the motor. Contact your local generator supplier for proper sizing and
refer to the specification plate on the electric motor. Use of an improperly sized generator
will cause a low voltage situation of the electric motor and controls which will void the
warranty.
MANUAL CONTROL PANEL OPERATION:
(See Figure 5)
A. FORWARD-REVERSE Switch
This selector switch controls the direction of movement of the material through the
machine. Select forward to feed material and run panel through the machine.
NOTE: For operator safety, your machine will not run continuously in reverse.
B. JOG-RUN Switch
This selector switch allows you to run the machine continuously, or jog material
through the machine. Select JOG to load coil into machine and to move material
through the machine in small increments until it clears the shear dies. Select run
after material has cleared the shear, and you are ready to run panel.
NOTE: The LENGTH CONTROL LIMIT SWITCH must be plugged in to the
Limit Switch Plug at the bottom of the Manual Control Box Assembly to run
continuously.
C. START FEED (Green button at Entry and Exit End)
This button is used to activate the drive system of the machine. (Jog only unless limit
switch is plugged in)
D. STOP FEED (Red button at Entry and Exit End)
This button acts as an emergency stop for the drive system when using the Length
Control Limit Switch. Pressing either the entry or exit button will stop the drive
system of the machine in case of an emergency.
E. SHEAR DOWN (Green button)
Pressing this button once will cycle the shear to the bottom of its stroke and return it
back to the top or home position. This is one shear cycle
F. SHEAR UP (Red button)
Pressing this button during the down cycle of the shear will immediately send it back
to the top or home position.
G. EMERGENCY STOP-POWER ON (Raised Red Mushroom button)

CHAPTER 5
ELECTRICAL CONTROLS AND OPERATION
10
Function #1 (Power On)
Pull this button OUT prior to starting the machine.
Function #2 (Emergency Stop-Power Off)
Once the machine is running, pushing this button in will stop all functions and
completely shut down the machine including the engine. If the shear is in the down
cycle it will freeze it in position. The shear will default back to the top or home
position once the engine or motor is re-started. This button is also used to shut the
machine down when not in use. Failure to push this button in prior to storage, even
overnight, could result in a dead battery on gas engine models.
H. MOTOR START (Green button)
You must pull the Emergency Stop-Power On button out before the Start
Button will function.
Press this button momentarily to start the Electric Motor machine.
Press and hold this button until the engine starts on a Gas Engine model.
MAIN CONTROL CABLE
(See Figure 6)
A. The main control cable is the communication cable for the Manual Control Panel
described above and the AMS Computer Batch and Length Control Computer
covered in Appendix B. This cable must be connected to one or the other in order
for the machine to operate.
B. The Main Control Cable exits thru the panel below and under the left corner of the
Manual Control Panel. There are two cables there and it is the larger diameter plug
of the two. It has a key and slot configuration that must be aligned before the
male/female connection can be made on the Manual Control Panel or Batch and
Length Control Computer. This prevents misalignment and damage to the pins.
Manual Control Panel Connection
Connect the Female end of the Main Control Cable to the panel mounted male
connection located at the bottom left corner of the Manual Control Panel. Make sure
that the key and slot are aligned and carefully start the threads on the connection and
turn clockwise until snug. Caution: Do Not rotate the cable clamp on the back of
the plug to tighten this connection. You must only turn the threaded ring of the
plug or damage will occur.
Batch and Length Control Computer Connection (See Figure 86)
Connect the Female end of the Main Control Cable to the panel mounted male
connection located in the bottom of the computer on the right side. Make sure that
the key and slot are aligned and carefully start the threads on the connection and turn
clockwise until snug. Caution: Do Not rotate the cable clamp on the back of the
plug to tighten or loosen this connection. You must only turn the threaded ring
of the plug or damage will occur.

CHAPTER 5
ELECTRICAL CONTROLS AND OPERATION
11
REMOTE LIMIT SWITCH
(See Figure 7)
Note: Your machine will not run continuously in the forward direction unless the
REMOTE LIMIT SWITCH is plugged into the machine. The Remote Limit Switch
is used for panel length control. It is designed to attach to the right side of the
optional RUN OUT TABLES available for your machine. Plug the female end of a
3-wire 14-gage extension cord into the limit switch, and the male end into the female
Limit Switch Plug located at the bottom of the Control Panel Assembly. The length
of the panel you intend to run determines length of the extension cord needed. Run
out a panel to the desired length and stop the machine. Slide the Remote Limit
Switch onto the bottom let of the angle on the right side of the run out table so that
the ARM of the switch is against the end of the panel. Pull the limit switch back
toward the shear until you hear a click in the Limit Switch Head and secure the limit
switch at this location. Cut and remove the set up panel from the table. Push the
start button and run the next panel allowing the limit switch to stop the machine.
Measure this second panel before cutting to determine if it stopped in the correct
position and make the necessary adjustment to the limit switch to obtain the desired
length. Repeat as necessary.
FUSES
(Figure 8)
All machines, gas or electric powered, have a 10-amp time delay fuse inside the Electrical
Control Panel Assembly. This fuse protects the electrical components. If the fuse is blown,
you will lose all functions of the machine except Motor Start. To replace this fuse: Loosen
all 4 cover screws and open the front panel of the Control Box. Locate the automotive style in-
line fuse near the bottom right hand corner. It is a spring loaded twist lock holder. Push
together and turn to open. Check the fuse with a continuity tester. If it is bad, replace with a
new fuse and re-connect spring loaded holder.
ELECTRIC MOTOR MACHINES
(Figure 9)
Electric motor machines have an additional 10-amp time delay fuse protecting the logic circuit
of the Contactor Box. This fuse holder is mounted in the side or top cover of the contactor box
located approximately mid machine on the right side. Access can be gained by removing the
center left side cover. This is a panel mounted, spring loaded fuse holder. To replace this
fuse: Push in on the cap and turn counterclockwise to release fuse. Check fuse with a
continuity tester. If the fuse is bad replace with a new fuse. To re-install, insert fuse into cap.
Install fuse and cap assembly into receptacle, push down and turn clockwise to lock in place.

CHAPTER 5
ELECTRICAL CONTROLS AND OPERATION
12
Figure 5: Controls

CHAPTER 5
ELECTRICAL CONTROLS AND OPERATION
13
Figure 6: Control Cables

CHAPTER 5
ELECTRICAL CONTROLS AND OPERATION
14
Figure 7: Run Out Table and Remote Limit Switch

CHAPTER 5
ELECTRICAL CONTROLS AND OPERATION
15
Figure 8: Main Control Box Fuse
Figure 9: QCPP E 1-6 Fuse Location

CHAPTER 6
REEL STANDS, REELS, AND EXPANABLE ARBORS
16
REEL STANDS, REELS AND EXPANDABLE ARBORS
EXPANDABLE ARBOR
(Figure 10)
The Expandable Arbor adjusts to accommodate coils with 16” to 20” inside diameters by expanding
into the ID of the coil.
THREADED NUT
The threaded nut should always be on the right side of the machine and the tail of the coil should
always be routed over the top and pointing toward the exit or shear end of the machine.
This threaded nut is used to increase or decrease the outside diameter of the arbor. Turning the nut
clockwise will increase the outside diameter of the arbor, and counter-clockwise rotation will
decrease the arbor size. There is a grease zerk in the collar of the threaded nut that should be
lubricated at least twice a year, or whenever grease in not visible on the threads of the shaft.
END COLLAR
The End Collar has two positions.
Position “A” is used for coils with inside diameters of 16”.
Position “B” is used for coils with inside diameters of 20”.
To adjust from one position to the other, remove 2 screws “C” until end collar is free to slide. Slide
it to the inside position for 20” ID or outside position for 16” ID coil. Align it to the respective
threaded holes in the reel shaft. Re-insert and tighten "C" bolts to lock the end collar to the shaft.
LOADING EXPANDABLE ARBORS WITH COIL
1. Using the Threaded Nut, collapse the arbor small enough to fit into the inside diameter of
the coil.
2. Slide the Expandable Arbor into the center of the coil making sure the threaded nut is on the
right and the tail of the coil is over the top and pointed toward the exit end of the machine.
3. Turn the Threaded Nut clockwise until the Support Bars on the arbor are just snug against
the inside of the coil.
4. Using the Reel Set Up Chart, (Figure 10), find the “D” dimension that corresponds to the
profile you are using.
5. Slide the arbor left or right to get the correct “D” dimension measuring from the edge of the
coil to the end of the Support Bar on the Threaded Nut side.
6. Finish by rotating the Threaded Nut clockwise until the Support Bars are very tight against
the inside of the coil. Verify that dimension “D” is correct, and re-adjust if necessary. The
Coil and Arbor are now ready for loading. (see LOADING REELED COIL on page 20)
Other manuals for SSQ MultiPro
1
Table of contents
Other NTM Cutter manuals
Popular Cutter manuals by other brands
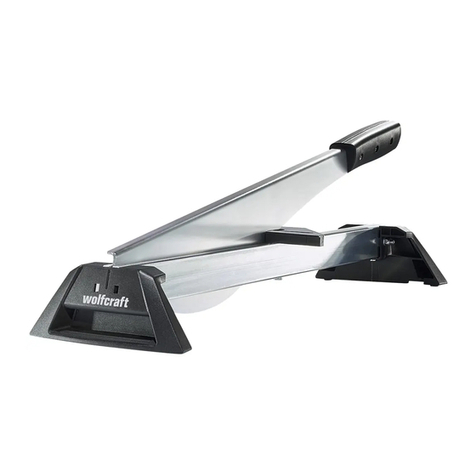
Wolfcraft
Wolfcraft LC 100 operating instructions

Hitachi Koki
Hitachi Koki CM 4SB2 Handling instructions
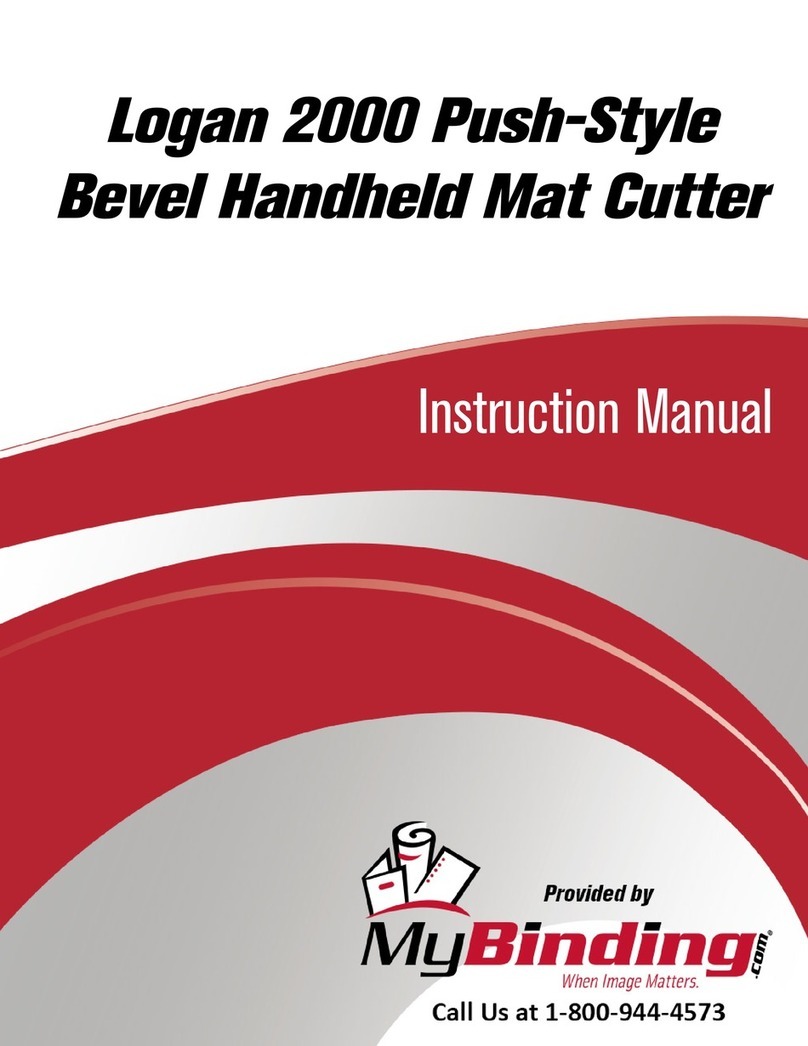
Logan
Logan 2000 instruction manual
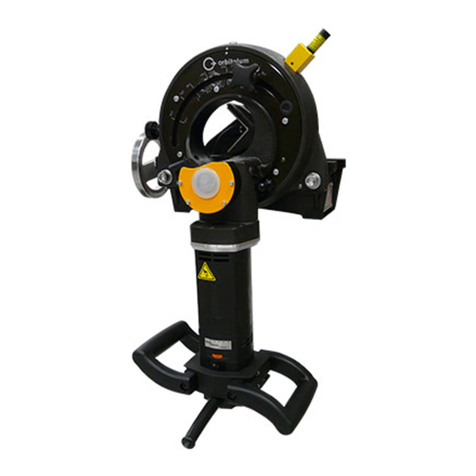
ITW
ITW orbitalum GFX 3.0 Translation of Original Operating Instructions and Spare Parts List
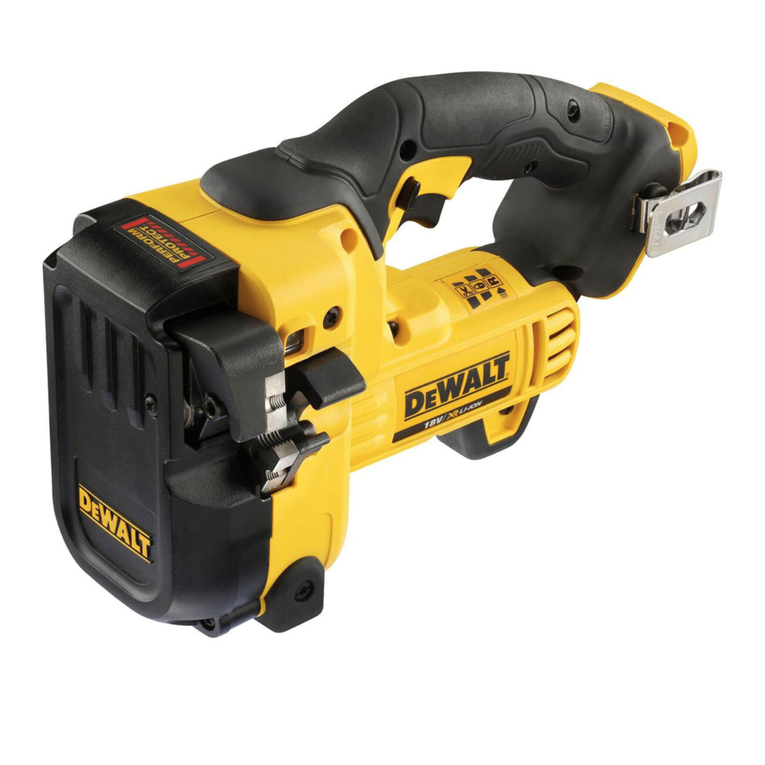
DeWalt
DeWalt DCS350 instructions

Metabo
Metabo Kn 6875 Original instructions