Olson Technology CTG-2 User manual

CTG-2 with WinCTG2 Software Version 1.7
CONCRETE THICKNESS GAUGE (CTG
-
2)
System Reference Manual
PATENT PENDING

1
NOTICES
Errors and Omissions
This document is believed to be accurate, but Olson Instruments, Inc. will not be
responsible for any errors or omissions which may be found. Further, Olson Instruments
will not be responsible for any damages resulting from any errors or omissions.
Proprietary Information
This document, as well as all software written by Olson Instruments, Inc., is proprietary
to Olson Instruments, Inc. This manual may not be sold, reproduced, or used with any
other product other than the Olson Instruments CTG-2 unless approved by Olson
Instruments, Inc. Further, this manual and the accompanying software may not be used
by any party other than the original purchaser without prior approval of Olson
Instruments, Inc.
Warranty
(See Sales Contract Documents)
Copyright
Copyright 2016 by Olson Instruments, Inc. All rights reserved. No part of this publication
may be reproduced or utilized in any form or by any means, electronic or mechanical,
including photocopying, recording, or by any information storage or retrieval system,
without prior written permission of the above named copyright holder.
Written by:
Olson Instruments, Inc.
12401 W. 49
th
Avenue
Wheat Ridge, Colorado
USA 80033-1927
Office: (303)423-1212
Fax: (303)423-6071
E-Mail: equip@olsoninstruments.com
Revised: August 2017

2
Table of Contents
INTRODUCTION............................................................................................................................................................3
1.1 Organization and Scope of Manual ..................................................................................................................4
1.2 Test Methodology.............................................................................................................................................4
2.0 HARDWARE ........................................................................................................................................................5
2.1 Hardware Component Listing...........................................................................................................................5
2.2 Location and Replacement of Batteries............................................................................................................6
2.3 Hardware Setup ...............................................................................................................................................7
3.0 WinCTG2 SOFTWARE SETUP .........................................................................................................................10
3.1 Prerequisite Software.....................................................................................................................................10
3.2 Software Installation.......................................................................................................................................10
3.3 Software Updates...........................................................................................................................................10
3.4 Software Uninstallation...................................................................................................................................10
4.0 DATA AQUISITION............................................................................................................................................12
4.1 General Information about the WinCTG2 Software........................................................................................12
4.2 IE Data Acquisition without Velocity Calibration .............................................................................................13
4.3 IE Data Acquisition with Known-Thickness Velocity Calibration.....................................................................21
4.4 View Mode .....................................................................................................................................................23
4.5 Thick Concrete Testing ..................................................................................................................................24
4.6 Units...............................................................................................................................................................25
4.7 Volume...........................................................................................................................................................25
4.8 Save Parameters ...........................................................................................................................................25
4.9 Reset Parameters ..........................................................................................................................................26
4.10 Operation Notes and Tips ............................................................................................................................26
5.0 WinCTG2 SOFTWARE ANALYSIS....................................................................................................................29
5.1 Start Program.................................................................................................................................................29
5.2 Open Data Files .............................................................................................................................................30
5.3 Filtering ..........................................................................................................................................................30
5.4 Windowing......................................................................................................................................................31
5.5 Concrete Velocity ...........................................................................................................................................33
5.6 Open Next Data File.......................................................................................................................................33
6.0 WinCTG2 SOFTWARE EXPORTING OPTIONS ...............................................................................................34
6.1 Copy or Save Image.......................................................................................................................................34
6.2 Export Test Results to Comma Separated Format.........................................................................................34
6.3 Export Raw Data to Comma Separated Format.............................................................................................35
7.0 WinCTG2 SOFTWARE LANGUAGE OPTIONS ................................................................................................36
8.0 CARE AND MAINTENANCE..............................................................................................................................37
APPENDIX A................................................................................................................................................................38

3
INTRODUCTION
The Olson Instruments CTG-2 system is commonly used for thickness evaluation and
rapid flaw detection on concrete and masonry structural materials. The method is
normally applied to plate-like objects such as slabs and walls, but is also used on
columns, mat foundations, and beams. The method requires access to only one side for
testing.
The CTG-2 is a powerful, hand-held device meant to be used with most Windows 7 and
Windows 8 laptop computers or tablets. The CTG-2 is designed to measure the
thickness of concrete slabs and walls in the range of approximately 3.2 inches (8.1 cm)
out to about 6 feet (1.8 m) without the need for drilling, coring, or other means. Test
results are acquired and analyzed with Olson’s WinCTG2 software, making the CTG-2
system a fully functional Impact Echo (IE) based thickness measuring system, capable
of analyzing echoes from multiple cracks and other flaws. In addition, a summary of test
results can be saved in comma separated format for use in an excel spreadsheet.
The WinCTG2 software features a graphical display of both the raw time signal as well
as the received signal spectrum (which can be saved and recalled), which allows visual
indication of data quality, easy differentiation of bad data, and even the location of
partial cracking damage. This unit can also be used to determine relative concrete
quality (by measuring concrete compression wave velocity) for test cylinders and other
samples with known thicknesses. The device can also be used for thickness
measurements of many materials other than concrete, such as plastics, stone, etc.,
depending on the properties and internal structure of the material being tested.
The CTG-2, when used with the default concrete velocity value of 12,000 fps, has an
accuracy of up to approximately 10%. This accuracy can be improved to approximately
2% when the unit is calibrated for velocity at a location of known thickness.
To confirm functionality of the CTG-2, it is advised to test the unit on a slab of known
thickness or on a 6” x 12” concrete cylinder which can be readily obtained from a
concrete supplier.
The CTG-2 with automated solenoid and displacement transducer comes with a phone-
plug-to-phone-plug cable used to connect the unit to a laptop or tablet. A microphone
adaptor is included to ensure the cable will work with different microphone/headset
ports. A USB jump drive is supplied with the necessary software and a microUSB-to-
USB cable is included so the software on the USB jump drive can be downloaded onto
Windows devices. The user must supply a Windows 7 or Windows 8 laptop/tablet.
Details of the hardware and its usage are included in Section 2.0. Suggested Windows
devices that are known to work with the CTG-2 are listed in Appendix A.

4
1.1 O ganization and Scope of Manual
The CTG-2 is a sturdy battery powered unit designed for easy, fast, and reliable
operation by anyone with no special training required for basic operation. This manual
covers step-by-step hardware assembly, software setup, simplified operation
instructions for data acquisition, data analysis, and output generation. If any problems
with the system appear that are not covered in this manual, please call Olson
Instruments at the number included in the front of this manual.
1.2 Test Methodology
The Impact Echo tests performed with the CTG-2 involve impacting the
concrete/masonry member with an impactor solenoid and identifying the reflected wave
energy with a displacement transducer as shown in the figure below. Note that the
solenoid impactor and displacement transducer are built into the IE head. The test head
is pressed against the top of the tested member and held while tests are performed at
each test point. The resonant echoes of the displacement responses are usually not
apparent in the time domain, but are more easily identified in the frequency domain.
Therefore, amplitude spectra of the displacement responses are calculated by
performing a Fast Fourier transform (FFT) analysis to determine the resonant echo
peak(s). The relationship among the resonant echo depth frequency peak (f), the
compression wave velocity (V
P
) and the echo depth (D) is expressed in the following
equation:
D = βV
p
/(2*f) (1)
where βis a geometric shape factor ranging in value from 0.8 for a pier/column shape to
0.96 for a slab/wall shape. A slab/wall shape has a single thickness resonance while
beam and column shapes have multiple resonances due to their cross-sectional shape.

5
2.0 HARDWARE
The CTG-2 system consists of a few basic components
packaged into a carrying case. The carrying case with
foam insert stores the CTG-2 IE test head and cables. It
includes a small compartment to store four CR123A 3V
spare batteries. A description of each of the included
components as well as their connection and operation is
included in the following sections.
2.1 Ha dwa e Component Listing
COMPONENT NAME
COMPONENT NAMECOMPONENT NAME
COMPONENT NAME
QTY
QTYQTY
QTY
DESCRIPTION
DESCRIPTIONDESCRIPTION
DESCRIPTION
CTG
CTGCTG
CTG-
--
-2 IE
2 IE 2 IE
2 IE Test
Test Test
Test Head
HeadHead
Head
1
11
1
The test head includes an aut mated s len id
impact r t create the impact and a
displacement transducer sens r t receive the
signal. Includes f ur CR123A 3V lithium ph t
batteries.
Ph ne
Ph nePh ne
Ph ne-
--
-Plug
PlugPlug
Plug-
--
-t
tt
t -
--
-
Ph ne
Ph nePh ne
Ph ne-
--
-Plu
PluPlu
Plug
gg
g
Cable
CableCable
Cable
1
11
1
T c nnect the IE Test Head t the Micr ph ne
Adapt r.
Micr ph ne Adapt r
Micr ph ne Adapt rMicr ph ne Adapt r
Micr ph ne Adapt r 1
11
1
T c nnect the Ph ne-Plug-t -Ph ne-Plug
Cable t the Wind ws device.
Ols n Jump Drive
Ols n Jump DriveOls n Jump Drive
Ols n Jump Drive
1
11
1
Jump Drive with Ols n WinCTG2 S ftware.
USB t Micr USB
USB t Micr USB USB t Micr USB
USB t Micr USB
Adapt
AdaptAdapt
Adapt r
rr
r
1
11
1
T c nnect Jump Drive with Ols n WinCTG2
S ftware t Wind ws Device.

6
2.2 Location and Replacement of Batte ies
The CTG-2 is provided with four CR123A 3V nonrechargeable long life lithium photo
batteries to power the system. (If desired, rechargeable CR123A 3V batteries can be
purchased and used with the unit.) The CTG-2 unit is designed to turn on when the
toggle switch on the base of the unit is flipped into the on position, making the indicator
light at the top of the handle illuminate green.
When the batteries are losing power, the green light will not illuminate. Instead, the red
light will come on. To ensure accurate readings, the batteries must be replaced at this
time. When light fails to illuminate (either green or red), the batteries have lost power
and MUST be replaced.
Location of the Batteries: the four CR123A batteries that power the CTG-2 IE test
head are located inside the handle of the test head.
Battery Replacement: To replace the batteries, follow these steps:
1. Using the toggle switch located at the base of the IE head, turn off the unit and
make sure the green light on the handle is not illuminated.
2. Use a Phillips screwdriver to remove the 2 screws at the rear of the handle as
shown in the picture below. Remove the battery compartment cover.
We recommend carrying spare batteries, and have provided a space for
them in the carrying case.
i

7
3. Turn the front of the unit upward to allow the batteries to slide out.
4. Insert new batteries following the polarity diagram inside the handle as shown in
the pictures below.
5. Replace the battery cover and screws.
2.3 Ha dwa e Setup
1. Connect the Phone-Plug-to-Phone-Plug Cable to the IE Test Head as shown in the
picture below.
Do not expose the CTG-2 system or the batteries to water.
!

8
2. Connect the other end of the Phone-Plug-to-Phone-Plug Cable to the Microphone
Adaptor, if necessary (laptops and desktops will not normally require the microphone
adaptor). There are two jacks on the Microphone Adaptor. One is identified with a
microphone icon. The other is identified with a headset icon. Select the appropriate
jack. Tablets will normally require the microphone jack. Note: the CTG-2 unit will
NOT work with tablets that have only a headphone jack. The tablet MUST support a
headset OR microphone.
3. Connect the other end of the Microphone Adaptor to the Windows Device. Or, if
using a laptop/desktop, connect the other end of the Phone-Plug-to-Phone-Plug
Cable to the Windows Device.

9
4. Flip the toggle switch on the base of the IE test head to activate the unit. When the
green light is illuminated, the IE test head is powered up and ready to collect data.
5. The picture below shows the complete CTG-2 system ready to acquire data. In this
case, an 8” tablet is being used. We recommend a minimum 8” size tablet. We
recommend that the tablet be used in “landscape” mode.

10
3.0 WinCTG2 SOFTWARE SETUP
This section covers the steps required to install the WinCTG2 software on a tablet,
laptop or desktop computer from the supplied installation jump drive.
3.1 P e equisite Softwa e
Windows .Net Framework 4 is required for the WinCTG2 software and is installed
automatically with the program. The software is fully compatible with Windows 7 and
Windows 8 (32 or 64 bit) operating systems.
3.2 Softwa e Installation
1. Uninstall any previous version of WinCTG2.
2. Using the USB to MicroUSB adaptor, connect the provided jump drive to the
Windows device. Copy the WinCTG2 Setup directory on the jump drive to the
desktop on the device. On the Windows device, open WinCTG2
Setup/Release/setup.exe. The software will be installed using a Setup Wizard.
Select “Next” as appropriate. Select “Yes” when prompted to confirm changes.
Select “Close” to exit. The default location for the software installation is “C:/Olson
Instruments/WinCTG2” unless the user changes the location during the installation
process.
3.3 Softwa e Updates
To update the software, completely uninstall the WinCTG2 Setup software per Section
3.4 and install the new version of WinCTG2 Setup by selecting the “Setup” executable
in the “Release” directory. The program will install a shortcut on your desktop.
3.4 Softwa e Uninstallation
The following steps are required to uninstall the WinCTG2 Software on a desktop or
laptop computer.
1. Click on “Start/Control” Panel
2. Select “Programs and Features”
3. Highlight WinCTG2 Setup, select “Uninstall”
The following steps are required to uninstall the WinCTG2 Software on a tablet.
1. Turn on tablet. The “Start” panel should present.
2. Touching the screen, flick to reach the “Apps” panel below.

11
3. Touching the screen, flick to reach the Dell “Apps” panel to the right.
4. Select “Control Panel”.
5. Select “Programs”.
6. Select “WinCTG2 Setup”.
7. Select “Uninstall”.
8. Select “Yes” to confirm uninstallation.
9. Select “Yes” to confirm changes.
The uninstall process will begin automatically, removing all installed components
including shortcuts. This uninstall process might take up to five minutes. Do not exit the
installation until it is completed.

12
4.0 DATA AQUISITION
This section includes instructions for data collection with the WinCTG2 Software. If you
have an area of known thickness that can be used for velocity calibration, please refer
to Section 4.3 before testing.
4.1 Gene al Info mation about the WinCTG2 Softwa e
The WinCTG2 software is comprised of 3 different panels: the Data Parameter panel,
the Filter panel, and the Waveform Data panel. Each panel (except the waveform data
panel) is collapsible if not needed (especially during the data acquisition process) to
enlarge the waveform data panel. Figure 1 below shows an overview of the program
layout. The shortcuts to turn on each panel are located on the upper right corner of the
screen. The function of each shortcut is described below:
•Toggles the filter panel on/off
•Toggles the parameter panel on/off
Figure 1 – WinCTG2 Lay ut f r IE Test Results
Filter Panel
Waveform Data Panel
Parameter Panel

13
4.2 IE Data Acquisition without Velocity Calib ation
It is not necessary to calibrate for velocity in order to perform the Impact Echo test and
collect data using the system’s default value of 12,000 fps (3,657 m/s)
as an average
velocity for sound concrete. But the operator should understand that using the default
value results in up to approximately a 10% error in the results as compared to
approximately a 2% error when the unit is calibrated for velocity at a location of known
thickness.
1. Turn on your tablet or laptop (with the hardware connected and turned on as
described in Section 2.0) and select the WinCTG2 shortcut on the desktop. The
software will open as shown in Figure 2 below. Within the Waveform Data Panel, the
top plot box shows the current time domain data and the bottom plot box shows the
frequency spectrum. Per the “Status” field in the Main Menu, the program is currently
in “Stand by” mode.
Figure 2 – Main Screen f r WinCTG2 S ftware
2. Filename Feature: Fill in the “Date” field and “Project Name” field as desired.
3. Geometry Feature: If you have laid out a grid for data collection and want the
software to keep track of your X and Y coordinates, use the Geometry Feature to
document the coordinates. In the “Length (X)” field, enter the total length you plan to

14
test in the X direction and in the “Length (Y)” field, enter the total length you plan to
test in the Y direction. Select the “Moving X” checkbox if you plan to move from test
point to test point in the X direction. Select the “Moving Y” checkbox if you plan to
move from test point to test point in the Y direction. In the “Start X” field, enter a
value for the start point in the X direction as well as the “Interval X” (or distance
between test points) in the X direction. Finally, in the “Start Y” field, enter a value for
the start point in the Y direction as well as the “Interval X” (or distance between test
points) in the Y direction.
Unless changed, a default value of 6 inches will be used for “Expected Concrete
Thickness”. This value is used to limit the amount of data analyzed and presented by
the software so it is important to alter this number as appropriate, however, 6 inches
is an appropriate value to use for slabs ranging in thickness from 4 inches to 8
inches.
4. At this point, the user has two options for collecting and saving data. The “Setup
Filename” option in the Main Menu can be used to set up automatic file naming for
files that will be saved (this is the suggested mode). Or the “Start” option in the
Toolbar can be used to start testing without setting up automatic file naming. When
using this mode, the user will be prompted to name each file individually. Note that
the “View” option in the Toolbar can also be used as discussed in Section 4.4 to
view data without saving or recording files.

15
Set up Automatic File Naming: To set up sequential numbering of the files to be
collected, select the “Setup Filename” option found in the Main Menu. This will open
a dialogue box as shown in Figure 3 below. Enter the directory where the data is to
be saved along with an alphabetical prefix and a numerical suffix. (The alphabetical
prefix will remain fixed and the numerical suffix will increase with each test.) When
finished, select “Start” to close the dialogue box then select the “Start” option found
on the Toolbar to start collecting data.
Figure 3 – Set Up Filenames

16
Start Testing without Setting up Automatic File Naming: To start collecting data
without using the “Setup Filename” option, select the “Start” option found on the
Toolbar. A “Save As” dialogue box will open as shown in Figure 4 below. Enter the
individual filename desired. When finished, select “Save” to close the dialogue box
and proceed with testing.
Figure 4 – Start Testing with ut Setting up Filenames
5. After selecting the “Start” option on the Toolbar, the system is now waiting to receive
data (in the form of an impact) as reported in the “Status” field which is currently in
“Ready to Test” mode. See Figure 5 below.
Some Windows devices will trigger when the “Start” or “View”
option is selected. When this happens, reject the data and
proceed with the testing instructions below.
i
If the IE head is repositioned after the “Start” or “View” option is
selected, data acquisition will be triggered. When this happens,
reject the data and proceed with the testing instructions below.
i

17
Figure 5 – System Waiting t Receive Data
6. With the IE head powered up and the green light on the top of the handle
illuminated, press the trigger button on the underside of the handle. The unit will fire
the solenoid on the CTG-2 head and create an impact. The displacement transducer
sensor on the CTG-2 head will record the data and the software will display the data
on the screen as shown in Figure 6 below. The program is now waiting for you to
either accept or reject the data as reported in the “Status” field which is currently in
“Accept or Reject” mode.
When placing the CTG-2 on a test surface, place the rear feet
down first then rotate the unit down into position. This will
ensure proper contact between the sensor tip and the test
surface.
i
Gently rotate the sensor tip onto the test surface as a sudden
impact to the sensor might result in damage to the sensing
element.
!

18
Figure 6 – Data Displayed with Thickness Rep rted ab ve the Frequency Spectrum Pl t
7. Good data can be identified by a waveform signal in the Time Domain (top plot) that
ranges from 0.1 volt to 0.8 volt AND the presence of a prominent peak in the
Frequency Spectrum (bottom plot). (In Figure 6 above, the data was collected on a
6” x 12” cylinder so there are additional resonant peaks displayed in the data.) The
following Figures 7A through 7D, demonstrate both acceptable and unacceptable
data. It is recommended to verify repeatability of results by taking at least two tests
at the same location.
The default value for volume (or gain) is 10. The available volume
varies in different tablets/laptops and the initial setting might not
be appropriate to collect good data. If the waveform signal does
not range from 0.1 volt to 0.8 volt, carefully adjust the volume as
described in Section 4.6 and retest. Caution must be used when
adjusting the volume as a high volume can result in noisy data.
i

19
Figure 7A – Example f G d Data and a Single Pr minent Peak in the Frequency Spectrum
Figure 7B – Example f P r Data (N ise) and many Peaks/Hash in the Frequency Spectrum
Table of contents
Popular Measuring Instrument manuals by other brands
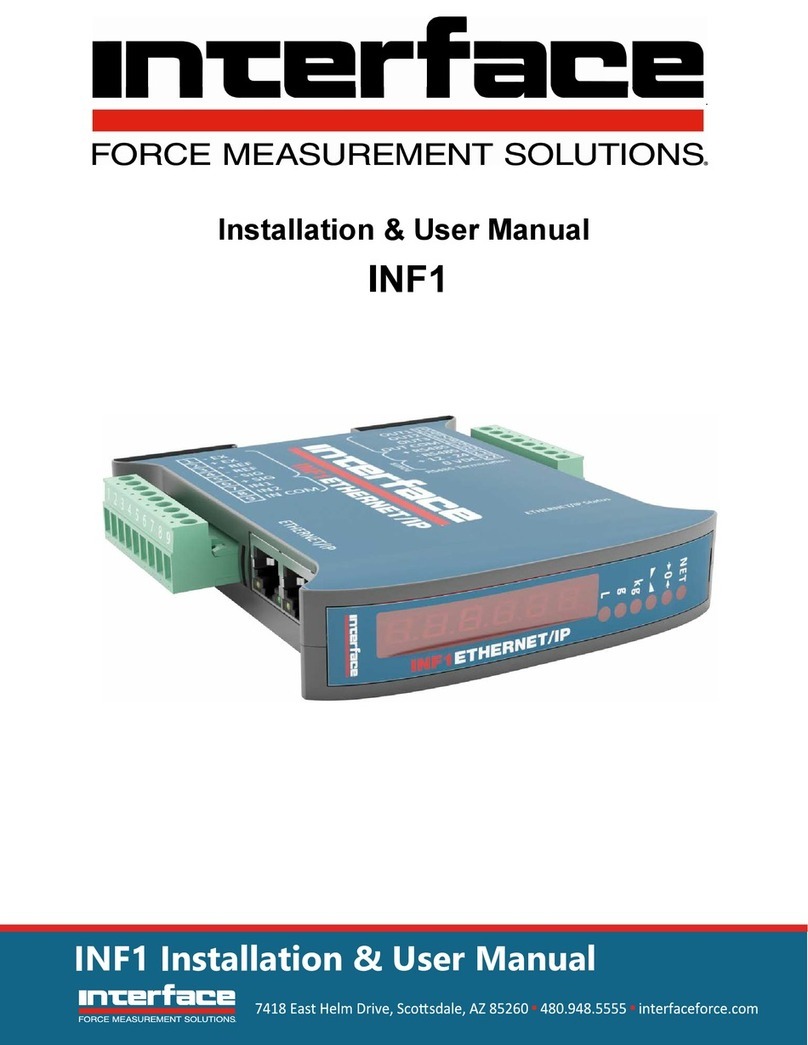
Interface
Interface INF1 Installation & user manual
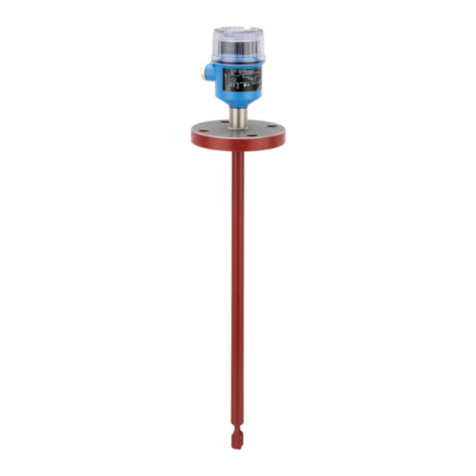
Endress+Hauser
Endress+Hauser FTL62 Series Functional safety manual

HEIDENHAIN
HEIDENHAIN ERA 4201 Mounting instructions

Hella
Hella 8PE 185 103-261 operating instructions
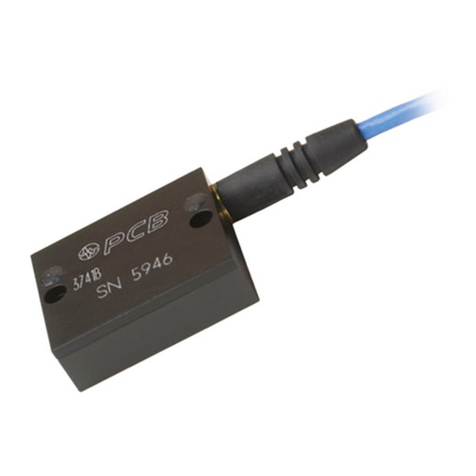
PCB Piezotronics
PCB Piezotronics 3741B1250G Installation and operating manual
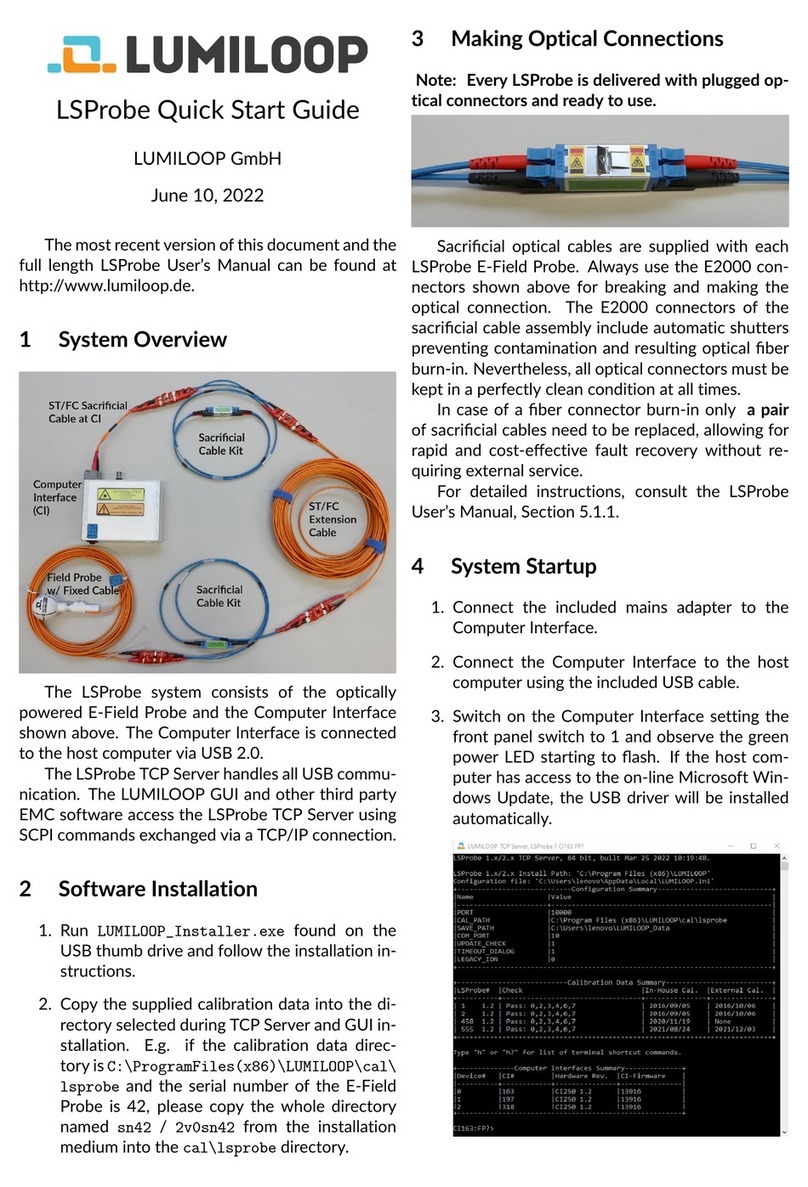
Lumiloop
Lumiloop LSProbe quick start guide
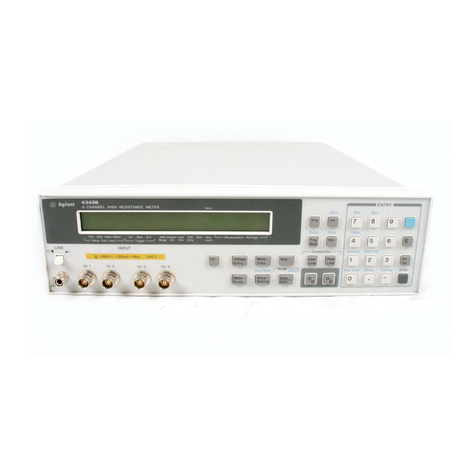
Agilent Technologies
Agilent Technologies 4349B manual
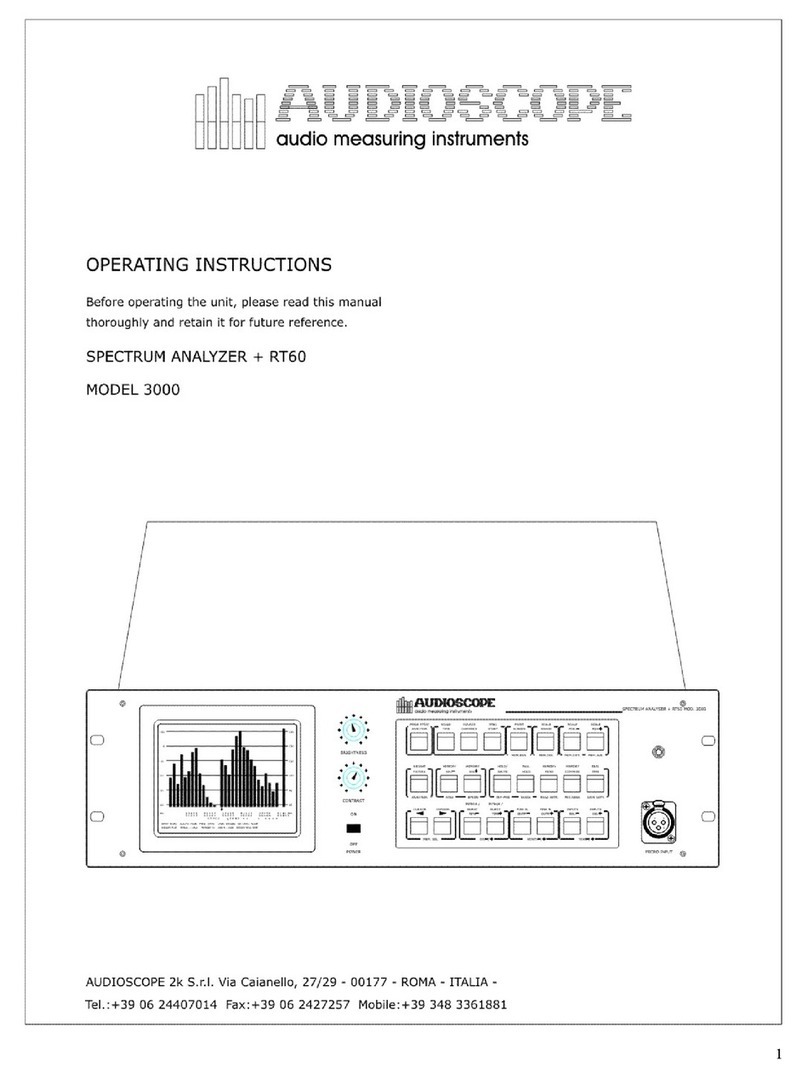
Audioscope
Audioscope 3000 operating instructions

Swema
Swema SwemaMan 60 instructions
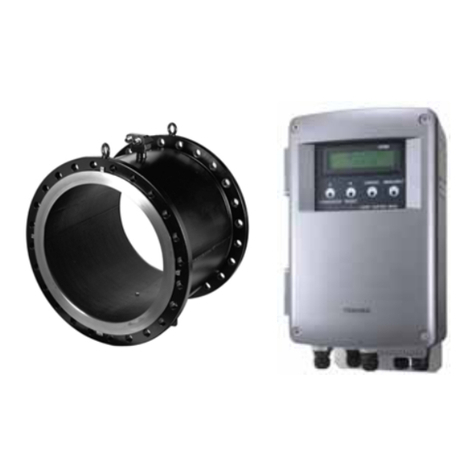
Toshiba
Toshiba LF232*F Series instruction manual
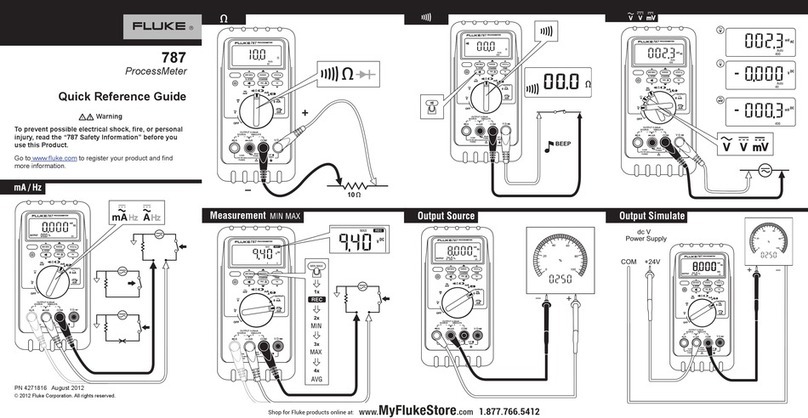
Fluke
Fluke ProcessMeter 787 Quick reference guide

GHM-Messtechnik
GHM-Messtechnik GREISINGER GMH 3611 operating manual