Oppermann Regelgeräte OPP-ROOM C1 Series User manual

OPP-ROOM®
Room Temperature Controller C1-…
Temperature and humidity sensors | Data sheet No. 20530 | Version 10-2020 | 1| 12
Technical Data Valid from Firmware V 2.14
Power supply: 24 V AC/DC -10% /+15%, max. 1 W
Outputs:
C1-TV 3 x 0 – 10 V DC < 5mA
C1-MOD / BAC digital + 3 x 0 – 10 V DC
2 switching outputs 24 V AC (Triac),
2 A max.
Temperature sensor range:
0 – 50 °C
Accuracy ± 0.5 °C
Ambient conditions:
Operating temperature: 0 – 50 °C
Operating ambient humidity:
0 – 95% RH
(non-condensing)
Storage temperature
:
-30 – 70 °C
Storage ambient humidity:
0 – 95% RH
(non-condensing)
Option L LED blue and red
for displaying cooling and
heating mode
Option D LCD display
for displaying
temperature, setpoint, and
controller state with
backlighting
(software-congurable)
Protection type: IP 20
Housing: ABS plastic, self-extinguishing,
white, similar to: RAL 9010
Wall installation
Dimensions:
(L x W x D) approx. 86 x 120 x 25 mm
Weight: 180g
Cable connection: Screw terminals 0.05 – 1.5 mm²
Function
For controlling interior air temperatures.
Installation
All work (such as installation, electrical connection, startup,
operation, and maintenance) must only be performed by suf-
ciently qualied tradesmen. The respectively applicable local
rules and regulations (e.g. national building codes, electrical/
VDE regulations, etc.) must be observed. Installers and opera-
ting entities are required to suciently familiarize themselves
before startup. Read the product description before operating
the equipment. Verify that the product can be used for the
relevant application without restrictions. We are not liable for
printing errors and changes after printing. Appropriate use
implies compliance with operating and installation instructions.
We are not liable for losses due to inappropriate use. Unautho-
rized or inappropriate manipulations or modications of the
device render the operating permit, the product warranty and
warranty claims null and void.
• New„Longline“ design
- design-protected
• Large LCD display with backlight
• Setpoint potentiometer with individually
adjustable midpoint and min/max limits
• Analog outputs voltage (0 – 10 V DC)
• Convenient parameter programming with
OR-C conguration Software
• Also available as BACnet / Modbus

Room Temperature Controller C1-…
2| 12 | Temperature and humidity sensors | Data sheet No. 20530 | Version 10-2020
Electrical Connection
Order codes
Voltage transmitter C1-TV-R...
Modbus-Transmitter C1-MOD-R und
BACnet-Transmitter C1-BAC-R
Precautionary measures for wiring
Switch o the power supply before changing wiring of any kind. If the sensor is equipped with an LCD display, disconnect the LCD
display and wire the power supply and all outputs if applicable. After completing the wiring, seat the display into the socket and
switch on the sensor.
DO1 + DO2
Voltage output with Triac,
requires 24 V AC power supply.
GPower supply 24 V AC/DC
G0 Common ground connection
Y1, Y2, Y3 Analog output 0 – 10 V DC
G0 Common ground connection
A + RS485, Bus A +
B – RS485, Bus B –
G0 Ground, resp. bus shield
RI1 Resistance input 0 – 50 kΩ, e. g. NTC10
DI1 Switching input, potential-free
Controller type
-R-P1L -R-D-P1
without display,
with two LEDs (heating / cooling)
with display,
without separate LEDs
C1-TV Voltage transmitter
103 919 103 920
C1-MOD Modbus transmitter (Modbus RTU)
103 921 103 922
C1-BAC BACnet transmitter (MS/TP)
103 923 103 924
RS485 Bus A
+
Network
24 VAC/DC
0 V
A +
B –
RS485 Bus B
–
0 V GND (Shield)
Go
G
Y3
Supply
only with 24 VAC power supply
24 VAC/DC
Output 0 – 10 V DC
Y1
Y2
Output 0 – 10 V DC
0 V GND
Output 0 – 10 V DC
DO2
DO1
Digital output 2
Go
Digital output 1
24 VAC
24 VAC
RI2
Resistor input 1 (0 – 50 kΩ, e.g. NTC10)
RI1
DI1
Switching input 1 (closing contact, potential-free)
not assigned
not assigned
DI2
Go
Bus DIP switch
OFF
ON
Bit Rate 1
Bit Rate 2
1
2
4
8
16
32
Network
Address
Jumper for bus
terminating resistor
Programming
connector
LED Bus communication
CAB-02
SET POINT
POTENTIOMETER
Configuration
keys
24 VAC/DC
0 V
0 V GND (Shield)
Go
G
Y3
Supply
24 VAC/DC
Output 0 – 10 V DC
Y1
Y2
Output 0 – 10 V DC
0 V GND
Output 0 – 10 V DC
DO2
DO1
Digital output 2
Go
Digital output 1
24 VAC
24 VAC
Resistor input 1 (0 – 50 kΩ, e.g. NTC10)
RI1
DI1
Switching input 1 (closing contact, potential-free)
Go
Programming
connector
CAB-02
SET POINT
POTENTIOMETER
Configuration
keys
DO1 + DO2 Voltage output with Triac,
requires 24 V AC power supply.
GPower supply 24 V AC/DC
G0 Common ground connection
Y1, Y2, Y3 Analog output 0 – 10 V DC
G0 Common ground connection
RI1 Resistance input 0 – 50 kΩ, e. g. NTC10
DI1 Switching input, potential-free

Temperature and humidity sensors | Data sheet No. 20530 | Version 10-2020 | 3| 12
Room Temperature Controller C1-…
For all following pages, please also note the instructions in specication sheet 20560 (OR-C conguration software)!
Accessories (ordered separately):
Description Type
Windows conguration software
1.8 m USB cable
OR-C
CAB-02
Controllers of type C1-..-R-D-P1 have on on-board LCD used to display the current controller status.
The display is also used to show the conguration settings. The following gures illustrate the various display options.
The LCD display shows the current
operating status to the user.
• Actual temperature value
• Cooling or heating mode (appropriate icon
is shown in the display)
• If neither cooling nor heating is displayed,
none of the controller settings are active.
Note: With PI control, the outputs are also
active within the deadzone.
Models C1-..-R-P1L without LCD display show
the respective operating mode with two
LEDs. When the current sensor temperature is
below the selected lower deadzone limit, the
red heating LED lights up. When the current
sensor temperature is above the upper limit of
the deadzone, the cooling LED is switched on.
When the current sensor temperature is within
the deadzone, both LEDs are switched o.
Setpoint
controller button
Display symbols
Heating mode
Cooling mode
setpoint display
Actual temperature /
User mode display
TEMPERATURE
DISPLAY
WITH CURRENT
VALVE POSITION
HEATING
DISPLAY
SETPOINT VALUE
ADJUSTMENT
(+/-3K UM SETPOINT
MIDPOINT)
SETPOINT ADJUSTMENT IS DISPLAYED
AS SOON AS CONTROL BUTTON IS ROTATED
current
valve position
Setpoint
controller button
LED Heating
LED Cooling
LCD display (types C1-..-R-D-P1)
Controller with LED display (types C1-..-R-P1L)

Room Temperature Controller C1-…
4| 12 | Temperature and humidity sensors | Data sheet No. 20530 | Version 10-2020
Controller conguration on the unit
The controller is normally congured with the PC-based OR-C
conguration software and the USB-cable CAB-02 (accessory).
In certain cases, e.g. when a PC is not available, the controller
can be adjusted with the two buttons on the upper right side of
the circuit board.
The following describes how the controller can be congured
with the help of the displays and the buttons.
1. The selection menu for the parameters is reached by pressing
the UP or DOWN buttons. A three-letter abbreviation shows
the currently selected parameter and blinks while doing so. The
display backlighting is switched on. The rst parameter is for the
midpoint of the setpoint range (default: 21°C).
2. The other conguration parameters are displayed by pressing
the UP and DOWN buttons again as long as the three-character
abbreviation blinks.
3. After you have reached the desired parameter and waited
approx. 3 seconds, the display changes the backlighting color
to amber, and you are now in parameter adjustment mode. The
currently set value blinks. By pressing the UP or DOWN button,
you can now change the parameter value. If no button was
pressed for three seconds, the last set value is accepted and the
display changes back to the next higher level, e.g. the parame-
ter selection. The background returns to white.
4. As soon as the conguration for all parameters has been com-
pleted, the controller automatically returns back to the normal
temperature control and display mode.
CAUTION! Whenever possible, switch the device o before
installing or removing the LCD display to avoid damaging the
electronics.
Conguration parameters and programming
Parameters can be adjusted with the help of the sensor conguration software.
A USB cable is used to connect the PC with previously installed OR-C to the program-
ming head of the sensor, as shown in the gure on the right.
The correct procedure for connecting the sensor via USB is as follows:
• Disconnect the USB connector from the PC.
• Disconnect the sensor from the power supply.
• Connect the 4-way connector to the sensor.
Observe the sequence of the cable colors:
Contact No. Color
1 Red
2 White
3 Green
4 Black
• Connect the USB connector to the PC.
• Reconnect the power supply to the sensor.
Important instructions: Always disconnect the USB connector from the PC before connecting the cable to the sensor.
The right sequence of the cable colors must be observed. Non-compliance with these instructions can damage the transmitter!
Setpoint value adjustments (user mode)
The desired temperature is selected by rotating the setpoint
button. In conguration mode or with the conguration tool, it
is possible to oset the midpoint (default: 21°C) and the min./
max. limits of the setpoint range (default: +/- 3K).
When the potentiometer is rotated, the current setpoint is
shown on the display (if available); the backlighting is briey
switched on. The display reverts back to the current temperature
setpoint value after approx. ve seconds.
Programming interface
PROG
USB-Cable CAB-02
PROG
USB PROGRAMMING-
CABLE CAB-02
White
Red
Green
Black
Programming interface

Temperature and humidity sensors | Data sheet No. 20530 | Version 10-2020 | 5| 12
Room Temperature Controller C1-…
Control Loop Operation
The controller can supply up to 2 heating levels and up to 2 cooling levels (one heating level and two cooling levels by default). The
controller modulates heating and cooling demand on the outputs based on the calculated setpoint and the current temperature.
The control can be either P-control or PI-control.
By default, heating level 1 is connected to output Y1 for the fully modulated 0 – 10 V DC control; cooling level 1 is connected to the
analog output Y2 and cooling level 2 is connected to analog output Y3. The controller has two digital outputs congured to work as
PWM or 3-point controls. The PWM or 3-point-regulation can then be linked to a control level (heating level 1/2 or cooling level 1/2)
based on demand. By default, DO1 is connected as PWM control for heating level 1 and DO2 with cooling level 1.
Please note that it is possible to set the control loop outputs to direct or inverted direction, which for instance inverts the operating
direction for a valve. This can individually be programmed for each level with the conguration software. The buttons on the unit
and the output in the display can also be used to invert heating level 1 and cooling level 1 without the software.
PARAMETER CONFIGURATION DISPLAY
ADJUSTMENTS
SETPOINT CENTER
(RANGE – 12 – 86°C,
DEFAULT: 21°C,
RESOLUTION: 0.1°)
PARAM 1:
NUMBER OF
HEATING LEVELS
(0 to 2,
DEFAULT: 1)
PARAM 5:
ADJUSTMENTS
DEADZONE/
DEADZONE
(0.0 to 6.0K)
DEFAULT: 1.5K)
PARAM 4:
ADJUSTMENTS
PROPORTIONAL BAND
(default: 4°C,
RANGE 1 to 50)
PARAM 2:
SELECTION ANALOG OUTPUT 1 (AO1)
0 - Bus
PARAM 9:
2 - Heating level 1
1 - Off
3 - Heating level 2
4 - Cooling level 1
5 - Cooling level 2
6 - Air-Side
7 - Change-Over /
PARAM 10:
SELECTION ANALOG OUTPUT 2 (AO2)
0 - Bus
2 - Heating level 1
1 - Off
3 - Heating level 2
4 - Cooling level 1
5 - Cooling level 2
6 - Air-Side
7 - Change-Over /
HEATING LEVEL 1,
DIRECTION OF ACTION:
0 - direct (/),
1 - inverse (\ default)
PARAM 6:
ADJUSTMENTS
INTEGRATION TIME/
ADJUSTMENT LAG TIME
(DEFAULT: 600 s,
RANGE 0 to 1200 s)
SET IA = 0
TO RECEIVE
P CONTROL ONLY
PARAM 3:
SELECTION
TEMPERATURE UNIT
0 - Celsius (default)
1 - Fahrenheit
PARAM 20:
PARAM 17:
3-POINT ACTUATOR
LAG TIME
(0 to 30 s,
DEFAULT: 6s)
PARAM 18:
INTERNAL SENSOR
OFFSET
(-10 to +10 °C/°F,
DEFAULT: 0)
PARAM 19:
EXTERNAL SENSOR
OFFSET
(-10 to +10 °C/°F,
DEFAULT: 0)
NUMBER OF
COOLING LEVELS
(0 to 2,
DEFAULT: 1)
PARAM 7:
COOLING LEVEL 1
DIRECTION OF ACTION:
0 - direct (/ default)
1 - inverse (\ )
PARAM 8:
PARAM 13:
SELECTION / THERM. OUTPUT 2 (DO2)
0 - Bus
2 - Heating level 1
1 - Off
3 - Heating level 2
4 - Cooling level 1
5 - Cooling level 2
6 - Air-Side
7 - Change-Over /
PARAM 12:
SELECTION / THERM. OUTPUT 1 (DO1)
0 - Bus
2 - Heating level 1
1 - Off
3 - Heating level 2
4 - Cooling level 1
5 - Cooling level 2
6 - Air-Side
7 - Change-Over /
PARAM 14:
SELECTION / THERM.
MODE
0 - On – Off (0 – 1)
1 - PWM (PLSE)
PARAM 11:
SELECTION ANALOG OUTPUT 3 (AO3)
0 - Bus
2 - Heating level 1
1 - Off
3 - Heating level 2
4 - Cooling level 1
5 - Cooling level 2
6 - Air-Side
7 - Change-Over /
PARAM 25:
PARAM 15:
SELECTION, 3-POINT MODE(DO1 & DO2)
0 - Bus
2 - Heating level 1
1 - Off
3 - Heating level 2
4 - Cooling level 1
5 - Cooling level 2
6 - Air-Side
7 - Change-Over /
PARAM 16:
3-POINT ACTUATOR
STROKE TIME
(30 to 600 s,
DEFAULT: 150s)
SELECTION / DIGITAL INPUT
0 - Night mode =
everything off (default)
1 - Cooling off
PARAM 21:
2 - Without function
3 - Change-Over /
PARAM 22:
ADJUSTMENTS / SETPOINT
MINIMUM
(-20 to +20 Kelvin,
DEFAULT: -3)
PARAM 23:
ADJUSTMENTS / SETPOINT
MAXIMUM
(-20 to +20 Kelvin,
DEFAULT: +3)
PARAM 24:
LCD BRIGHTNESS
(0 to 100%),
DEFAULT: 0)
PARAM 31:
LOAD
FACTORY SETTINGS
0 - No
1 - Yes (factory settings
are loaded)
PARAM 28:
LIMIT RATIO
(RANGE 0 -5
DEFAULT : 0 = OFF)
PARAM 30:
NIGHT MODE DEADBAND
(RANGE 0-40 °C/°F
DEFAULT : 6°C
0.1 DEG RESOLUTION)
PARAM 26:
HIGH LIMIT SETPOINT
(RANGE 12 -86 °C/°F
DEFAULT : 35°C
0.1 DEG RESOLUTION)
PARAM 27:
LOW LIMIT SETPOINT
(RANGE 12 -86 °C/°F
DEFAULT : 16°C
0.1 DEG RESOLUTION)
PARAM 29:
NIGHT MODE OPERATION
(rEL = RELAXED SETPOINT,
OFF = NIGHT OFF MODE
DEFAULT: rEL)
AntiJAM VALVE
EXERCISE PERIOD
(0-14 Days,
DEFAULT: 0 = OFF)

Room Temperature Controller C1-…
6| 12 | Temperature and humidity sensors | Data sheet No. 20530 | Version 10-2020
CONTROLLER
OUTPUT
HEATING LEVEL 1 COOLING LEVEL 1
CNTSP
0 – 10VDC, PWM or 3-point
0 – 10VDC, PWM or 3-point
DZ = Deadzone (default: 1.5K)
CNTSP = SETPOINT CENTER (default: 21°C)
DZ
MEASURED
TEMPERATURE
100%
0% +-
COOLING LEVEL 2
0 – 10VDC, PWM or 3-point
HEATING LEVEL 2
0 – 10VDC, PWM or 3-point
NOTES:
•The number of heating and cooling levels can be set to 0, 1, or 2.
• Each analog output Y1, Y2 or Y3 can be linked with each heating or cooling level.
• The PWM or 3-point control can be linked with each heating or cooling level.
Air-side temperature control
A deadzone is located between heating cooling level 1. This prevents rapid switching over (utter) between heating and cooling.
The extent of the deadzone is adjusted in the conguration parameters.
Digital input DI1 can be used to either only suppress the cooling level or all outputs (digital and analog). The parameter is con-
gured with the OR-C software or directly on the device. In night mode (default), all outputs are switched o, and the display shows
the current temperature and the night symbol () as soon as DI1 is short-circuited with G0.
The air-side temperature control is achieved by combining heating level 1 with cooling level 1. For this purpose, the number of
heating levels must be set to 1 or more and the number of cooling levels is also set to 1 or more. The direction of action of the
outputs for heating 1 and cooling 1 must be the same (both outputs work in direct or inverse mode).
Note: The eective proportional band of the air-side temperature control is twice that of heating level 2 and
cooling level 2 due to the fact that there is only one proportional band for all levels.
CONTROL OUTPUT
HEATING
STAGE 1
COOLING
STAGE 1
CNTSP
0..10Vdc, PWM or 3-P
0..10Vdc, PWM or 3-P
Dz = Dead Zone (Default 1.5°C)
CNTSP= Setpoint Middle Point (Default 21°C)
Dz
MEASURED
TEMPERATURE
100%
0% +-
COOLING
STAGE 2
0..10Vdc, PWM or 3-P
HEATING
STAGE 2
0..10Vdc, PWM or 3-P
NOTE: Note the number of heating and cooling stages can be set to NONE, 1 or 2.
NOTE: Each analogue output (Y1, Y2, Y3) can be configured tofollow any of the stages.
NOTE: PWMcontrol or 3-Point control can be configured tofollow any of the stages.
CONTROLLER
OUTPUT
HEATING LEVEL 1 COOLING LEVEL 1
CNTSP
DZ = Deadzone (default: 1.5K)
CNTSP = SETPOINT CENTER (default: 21°C)
DZ
MEASURED
TEMPERATURE
100%
0% +-
COOLING LEVEL 2HEATING LEVEL 2
NOTES:
•The number of cooling and heating levels must be at least 1.
• The heating and cooling level 1 must work in the same direction of action (e.g. inverse).
• Each analog output Y1, Y2 or Y3 can be linked with the air-side temperature control.
(combination of heating and cooling level 1).
• The PWM or 3-point control can be linked with the air-side temperature control.
(combination of heating and cooling level 1).
50%
Air-side temperature control (heating and cooling level 1 combined)

Temperature and humidity sensors | Data sheet No. 20530 | Version 10-2020 | 7| 12
Room Temperature Controller C1-…
+
-
M
24 V~
Digital output 1
Digital output 2
0 V GND
Output 0 – 10 V DC
Output 0 – 10 V DC
Output 0 – 10 V DC
24 V AC/DC
Supply
24 V~
THA1
THA2
Heang loop
Cooling coil
Digital output 1
Digital output 2
24 V AC/DC
Supply
0 V GND
Output 0 – 10 V DC
Output 0 – 10 V DC
Output 0 – 10 V DC
THY1
THY2
24 V~
Heang loop
Cooling coil
Digital output 1
Digital output 2
24 V AC/DC
Supply
0 V GND
Output 0 – 10 V DC
Output 0 – 10 V DC
Output 0 – 10 V DC
Digital outputs - operating modes and wiring examples
The digital outputs (24 V AC Triacs, 2 A max.) can be congured as outputs for a 3-point control, as PWM control (pulse width
modulation) or simple on/o switches (2-point control). The type of control is selected with a conguration parameter. When 3-point
control is selected, the controller will open, e.g. the actuator drive for a valve, via DO1, and close it via DO2. It is also possible to
invert the output operation. Since the 3-point control uses both outputs – DO1 and DO2 –, this function can only be assigned to one
control level, e.g. heating level 1 or cooling level 1 but never to several at once.
When 3-point output is selected and the connected drive is to be
fully opened or closed, the corresponding output receives a con-
trol signal for a dened lagtime (default: 6 sec.) This is repeated
every 10 minutes. The lagtime is programmable with a congura-
tion parameter and can be switched o by setting it to 0.
3-point control: M can for instance be a motor drive. Since both
digital outputs are used, only one control level (heating or coo-
ling) can be assigned!
Note: Please note the max. current load rating of 2A per
digital output!
When the PWM function is needed, the duty cycle can be programmed with a further parameter in the conguration software. The default
is 30 seconds, e.g. when the output is at 50%, it is switched on for 15 seconds and switched o for 15 seconds.
When the PWM mode is set to„On / OFF“, the corresponding digi-
tal output is switched on when the max. level is reached (default
setting: 100%) and switched back o at min. level.
PWM or 2-point control: THA1 and 2 are thermal drives 0 – 24 V
The Triacs on DO1 and DO2 close the electrical circuit to G0
(ground).
Note: Please note the max current load rating of 2A per digital
output!
Analog outputs – connection example
Analog controller outputs: THY1 and THY2 are thermal drives
0 – 10 V DC with 24 V AC power supply.
Note: Analog and digital controller outputs can be combined!

Room Temperature Controller C1-…
8| 12 | Temperature and humidity sensors | Data sheet No. 20530 | Version 10-2020
THY1
24 V
Kreislauf wahlw. von Heiz-oder
Kühlmedium durchströmt
Digital input DI1 bridge mode
When the digital input is set to„cooling disable“, the outputs connected with cooling levels are reduced to 0% as soon as DI1
(potential-free switching contact) is connected with G0. When DI1 is set to„Night Mode“, all contacts are closed as soon as the
contact on DI1 is closed.
If “Change-over”mode is selected, all outputs with the setting“Change-over” will operate as follows:
External sensor input
By default, the controller uses an internal temperature sensor. When an external NTC10 temperature sensor is connected with input
RI1 and a valid value is measured, the controller automatically begins to use the external temperature sensor for the measurement,
and shows the present temperature in the display (if available).
Change-Over Coil: In this example THY1 is a
thermal drive for a valve. THY1 has a 24 V power
supply, and its position is determined via an
analog signal 0 - 10 V. However the uid owing
through the valve is a cooling agent during the
summer and a heating agent during the winter.
The controller is informed via Modbus-/BACnet
command or via the DI1 output whether it is cur-
rently operating in summer or winter mode. For
this purpose the relevant output – in this case Y1
– must be set to“Change-over”.
Circuit carrying either a
heating or cooling agent
Connection DI1 to GND Controller output indicates… (heating or cooling
symbol or red or blue LED lit)
Digital / Analog output
Open (= winter mode) Cooling O / 0 V
Open (= winter mode) Heating On / 0…10 V
Closed (= summer mode) Cooling On / 0…10 V
Closed (= summer mode) Heating O / 0 V
Digital output 1
Digital output 2
24 V AC/DC
Supply
0 V GND
Output 0 – 10 V DC
Output 0 – 10 V DC
Output 0 – 10 V DC

Temperature and humidity sensors | Data sheet No. 20530 | Version 10-2020 | 9| 12
Room Temperature Controller C1-…
BACnet MS/TP
You can nd the OPP-ROOM BACnet documentation (PICS) on our homepage
www.oppermann-regelgeraete.de
Underoor high/low limit control (HSP/LSP)
Room temperature is controlled by modulating valve controlling the water supply to the underoor heating. The C1-controller
modulates the valve according to the setpoint (SP) set by the user. The speed of the response is controlled by the PI control set-
tings. In practice the speed of response is limited by the response speed of the oor.
In some cases the oor surface is covered by materials where high temperature can cause a damage (e.g. wooden ooring). Con-
trolling the oor temperature simply by the space temperature does not take into account the oor surface temperature.
To protect the surface we need to install an additional oor sensor to monitor the surface temperature. Then applying high limit
reset strategy the high oor temperature is prevented.
This feature is carried out by resetting the control setpoint (SP), causing the control valve to“back o” when high oor tempera-
ture is detected. This is calculated by equation:
RoomReset = (FloorSP – FloorTemp) * Ratio Example:
Room SP = 21°C
Floor SP = 35°C
Reset Ratio (Lrt) = 0.5
FloorTemp = 37°C
RoomReset = (35-37)*0.5 = -1.0°C
Adjusted Room Setpoint (SP) is 21°C – 1.0°C =20.0°C
The correction is made correspondingly in the reverse direction, i.e.
at low temperatures.

Room Temperature Controller C1-…
10 | 12 | Temperature and humidity sensors | Data sheet No. 20530 | Version 10-2020
Adjusting the Modbus address and the baud rate
Modbus register
The Modbus address and the baud rate can be programmed either with the OR-C conguration tool together with the
CAB-02 data cable or directly on the unit with the bit switches.
The Modbus address and the baud rate can be programmed either
with the OR-C conguration tool together with the CAB-02 data
cable or directly on the unit with the bit switches. The Modbus con-
troller supports the following Modbus register and function codes:
The default communication speed is 9600 bps, eight data bits,
parity„even“, and 1 stop bit. The default Modbus slave address is 1.
The parity can be changed to„Odd“ or„None“. The baud rate can
be selected between 9600, 19200, 38400 and 57600 bps. The baud
rate can be selected with the integrated DIP switch or the OR-C
conguration tool when switches 7 and 8 (far right) are switched
o („OFF“). The device addresses 1 to 63 can be programmed with
DIP switches 1 to 6; the adjustable range extends from 1 to 247
via the OR-C conguration tool. However, this presupposes that
switches 1to 6 are set to„OFF“.
Please note that the Modbus register space is specied by the
Master in accordance with the Modbus application protocol.The
Modbus registers for function codes 02, 03, 06 and 16 represent the
Modbus address blocks as well as actual Modbus register osets.
Some Modbus Masters require the entry function code 04 and
register 1 for this purpose, while others poll the register with 30.001
and function code 04. The Modbus addressing begins with 0 (base
address). Some Modbus Masters begin their addressing from 1; in
this case, you will need to raise the listed register address values by 1.
DIP SWITCHES
OFF
ON
Bit Rate 1
Bit Rate 2
1
2
4
8
16
32
Bus
address
BAUD RATE
57600 Modbus
76800 BACnet
OFF
ON
BAUD RATE
38400
OFF
ON
BAUD RATE
19200
OFF
ON
BAUD RATE
9600 / Bus
OFF
ON
Note: When switches 7 and 8 are switched to "OFF",
the baud rate address can also be programmed via
bus or OR-C configuration software.
PROGRAMMING THE BAUD RATE
DIP SWITCHES
OFF
ON
Bit Rate 1
Bit Rate 2
1
2
4
8
16
32
Bus
address
ADDRESS „2“
OFF
ON
ADDRESS „9“
OFF
ON
Note: When all switches are switched to "OFF",
the address can also be programmed via bus or the
OR-C configuration software.
PROGRAMMING THE TRANSMITTER BUS ADDRESS
The bus address is programmed with switches
1 to 6 in binary code. Each switch represents
a binary value, and the address results from the
combination of the individual switches. Examples:
1
2
4
8
16
32
1
2
4
8
16
32
Register Parameter description Data type Raw data Range
FUNCTION CODE 01 - READ BITS
FUNCTION CODE 05 - WRITE ONE BIT
FUNCTION CODE 15 - WRITE SEVERAL BITS
0 Overwrite digital output 1
data bus
0 – 1 O – On
1 Overwrite digital output 2
data bus
0 – 1 O – On
2 Overwrite night mode 0 – 1 O – On
FUNCTION CODE 02 - READ INPUT STATES
10000Digital input status 1 0 – 1 O – On
10001n/a
10002Digital output status 1 0 – 1 O – On
10003Digital output status 2 0 – 1 O – On

Temperature and humidity sensors | Data sheet No. 20530 | Version 10-2020 | 11 | 12
Room Temperature Controller C1-…
Register Parameter description Data type Raw data Range
FUNCTION CODE 04 - READ INPUT REGISTER
30000 Temperature, on- board sensor Signed 16 -400 – 3.020 -40.0 – 150.0 °C
(-40.0 – 302.0 °F)
30001Temperature, external sensor on
resistor input RI1 (NTC10)
Signed 16 -400 – 3.020 -40.0 – 150.0°C
(-40.0 – 302.0°F)
30002calculated setpoint (°C) Signed 16 -400 – 3.020 -40.0 – 150.0°C
(-40.0 – 302.0°F)
30003Analog output Y1 Unsigned 16 0 – 1.000 0 – 100%
30004Analog output Y2 Unsigned 16 0 – 1.000 0 – 100%
30005Analog output Y3 Unsigned 16 0 – 1.000 0 – 100%
30006n/a
30007DO1 level (therm. drive) Unsigned 16 0 – 1.000 0 – 100%
30008DO2 level (therm. drive) Unsigned 16 0 – 1.000 0 – 100%
300093-point level Unsigned 16 0 – 1.000 0 – 100%
FUNCTION CODE 03 - READ OUTPUT REGISTER
FUNCTION CODE 06 - WRITE ONE OUTPUT WORD
FUNCTION CODE 16 - WRITE SEVERAL OUTPUT WORDS
40000Temperature set point value Unsigned 16 120 – 860 12.0 – 86.0 °C/°F
(Default 21°C)
40001Temperature controller/proportional
share
Unsigned 16 1 – 500 0.1 – 50.0 °C/°F
(Default 4°C)
40002Temperature controller/integral share Unsigned 16 0 – 1.200 0 – 1.200 s (600s Default)
40003Dead zone Unsigned 16 0 – 60 0 – 6.0°C/°F
(Default 1.5°C)
40004Number of heating levels Unsigned 16 0 – 2 0 to 2
40005Number of cooling levels Unsigned 16 0 – 2 0 to 2
40006Heating level 1 working direction Unsigned 16 0 – 1 0 = inverse
1 = direct
40007Cooling level 1 working direction Unsigned 16 0 – 1 0 = inverse
1 = direct
40008Digital input, function Unsigned 16 0 – 1 0 = night mode (everything o)
1 = cooling o
2 = Without function
3 = Change-Over
4 = Night mode, normally
closed (the same as 0, but
with inverted logic)
40009Temperature unit Unsigned 16 0 – 1 0 = Celsius
1 = Fahrenheit
40010 Analog output Y1 bypass value Unsigned 16 0 – 1.000 0 – 100% (0 – 10.0 V)
Default 0
40011 Analog output Y2 bypass value Unsigned 16 0 – 1.000 0 – 100% (0 – 10.0 V)
Default 0
40012 Analog output Y3 bypass value Unsigned 16 0 – 1.000 0 – 100% (0 – 10.0 V)
Default 0
40013 n/a

Room Temperature Controller C1-…
12 | 12 | Temperature and humidity sensors | Data sheet No. 20530 | Version 10-2020
Register Parameter description Data type Raw data Range
40014 Analog output Y1, mode Unsigned 16 0 – 6 0 = Value via data bus
1 = O
2 = Heating level 1 (Default)
3 = Heating level 2
4 = Cooling level 1
5 = Cooling level 2
6 = Air-side control
7 = Change-Over
40015 Analog output Y2, mode Unsigned 16 0 – 6 0 = Value via data bus
1 = O
2 = Heating level 1
3 = Heating level 2
4 = Cooling level 1 (Default)
5 = Cooling level 2
6 = Air-side control
7 = Change-Over
40016 Analog output Y3, mode Unsigned 16 0 – 6 0 = Value via data bus
1 = O
2 = Heating level 1
3 = Heating level 2
4 = Cooling level 1
5 = Cooling level 2 (Default)
6 = Air-side control
7 = Change-Over
40017 n/a
40018 PWM1 bypass value Unsigned 16 0 – 1.000 0 – 100%
40019 PWM1 mode Unsigned 16 0 – 6 0 = Value via data bus
1 = O
2 = Heating level 1 (Default)
3 = Heating level 2
4 = Cooling level 1
5 = Cooling level 2
6 = Air-side control
7 = Change-Over
40020 PWM2 bypass value Unsigned 16 0 – 1.000 0 – 100%
40021 PWM2 mode Unsigned 16 0 – 6 0 = Value via data bus
1 = O
2 = Heating level 1
3 = Heating level 2
4 = Cooling level 1 (Default)
5 = Cooling level 2
6 = Air-side control
7 = Change-Over
40022 3-point controller bypass value Unsigned 16 0 – 1.000 0 – 100%
40023 3-point controller mode Unsigned 16 0 – 6 0 = Value via data bus
1 = O (Default)
2 = Heating level 1
3 = Heating level 2
4 = Cooling level 1
5 = Cooling level 2
6 = Air-side control
7 = Change-Over
40024 3-point controller stroke time Unsigned 16 30 – 600 30..600 s (Standard 150)
40025 3-point controller adjustment lagtime Unsigned 16 0 – 30 0…30 (Standard 6)
40026 DO1 mode Unsigned 16 0 – 1 0 = Data bus
1 = Controller (Standard)
40027 DO2 mode Unsigned 16 0 – 1 0 = Data bus
1 = Controller (Standard)
40028 Internal temp. sensor, one-point
compensation
Signed 16 –100 – 100 –10…+10 °C/°F (Standard 0)
40029 External temp sensor, one-point
compensation
Signed 16 –100 – 100 –10…+10 °C/°F (Standard 0)
40030 Setpoint adjust, minimum Signed 16 –200 – 0 –20.0…0.0 °C/°F (Standard -3)
40031 Setpoint adjust, maximum Signed 16 0 – 200 0.0…+20 °C/°F (Standard +3)

Room Temperature Controller C1-…
Specications subject to change. Temperature and humidity sensors | Data sheet No. 20530 | Version 10-2020 | 13 | 12
Oppermann Regelgeräte GmbH | Im Spitzhau 1 | 70771 Leinfelden-Echterdingen, Germany
Phone +49 711 72723560 | Fax +49 711 7280527 | info@oprg.de | www.oprg.de
120
25
86
Dimensions Screw hole positions
Walt-mounting bracket
Gently press the clip on the
bottom inward to open the housing
120
25
86
86,00
120,50
28,17
5
5
64
79
60
14
Schraublochpositionen Wandhalterung
Note 1: The Modbus address can only be congured by the OR-C tool when bit switches 1 – 6 are switched o.
Note 2: The Modbus baud rate can only be congured by the OR-C tool when bit switches 7 – 8 are switched o.
(default setting: 9600 baud).
Note 3: In order to save changes, „Update non-volatile memory“ must be set to „Update“. If you use the OR-C sensor conguration tool,
the program will automatically force storage in the non-volatile portion of memory.
Register Parameter description Data type Raw data Range
40100 forced reset/warm boot Unsigned 16 0 – 1 0 = Normal
1 = Forced reset
40101 update non-volatile memory Unsigned 16 0 – 1
see note 3 0 = Normal
1 = Update
All dimensions in millimeters
This manual suits for next models
2
Table of contents
Other Oppermann Regelgeräte Controllers manuals
Popular Controllers manuals by other brands
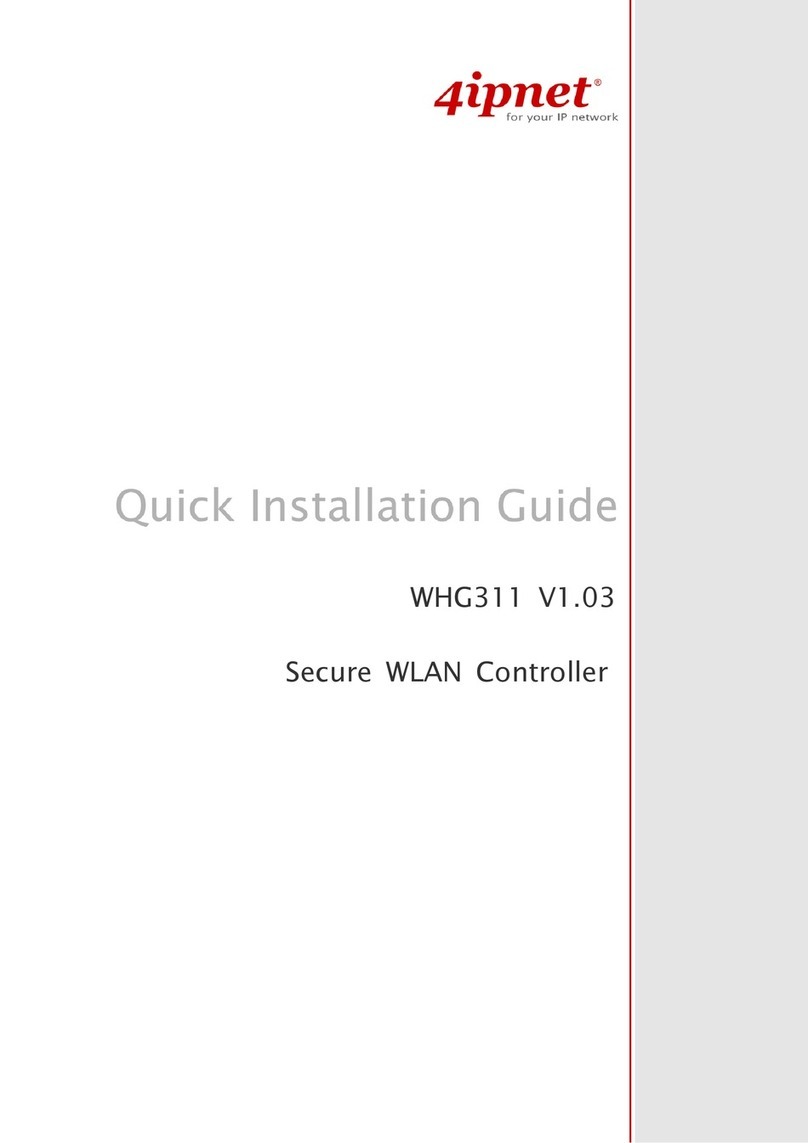
4IPNET
4IPNET WHG311 Quick installation guide
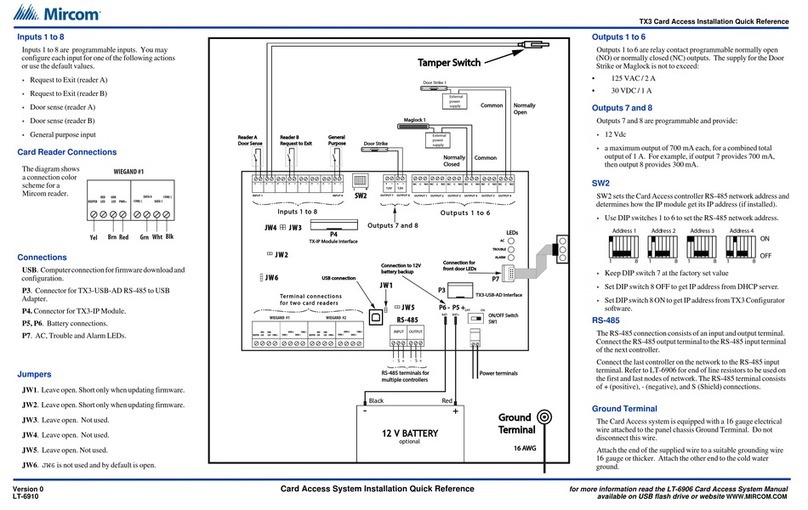
Mircom
Mircom TX3 Series Installation quick reference
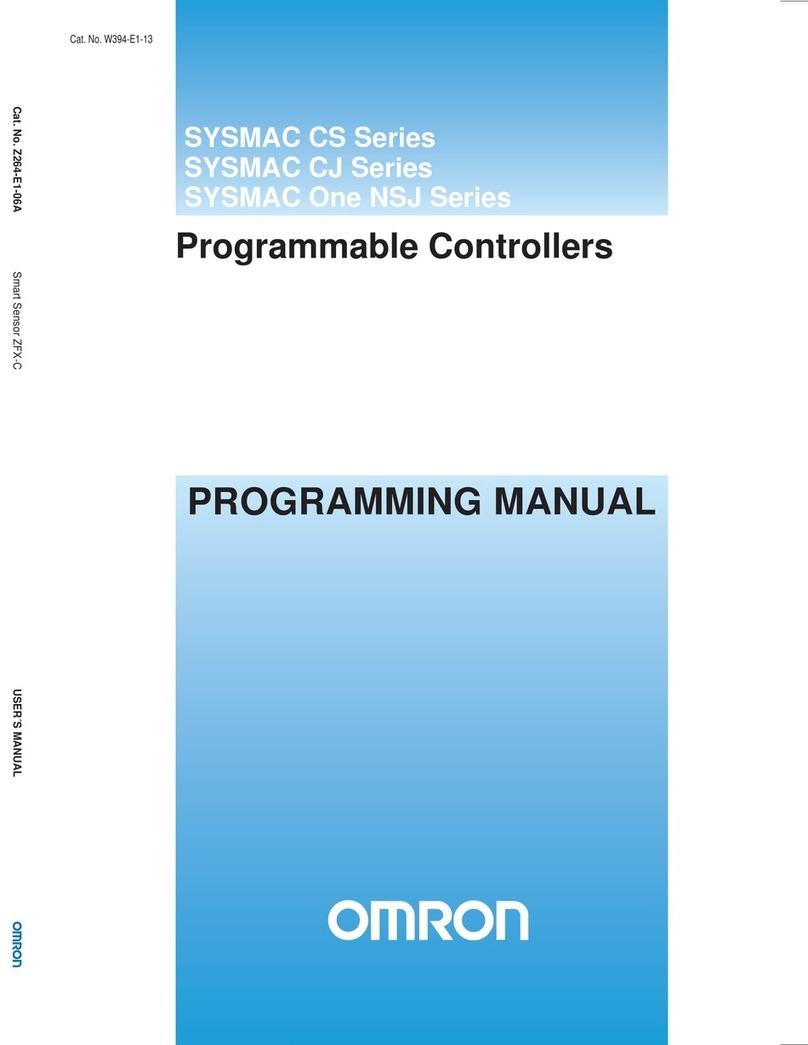
Omron
Omron CJ - PROGRAMMING 08-2008 Programming manual
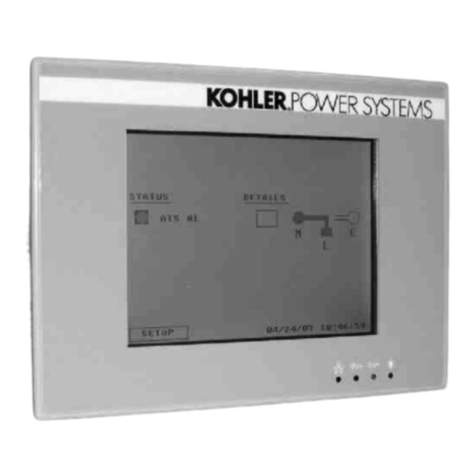
Kohler
Kohler Power Systems GM49279-KP1 installation instructions
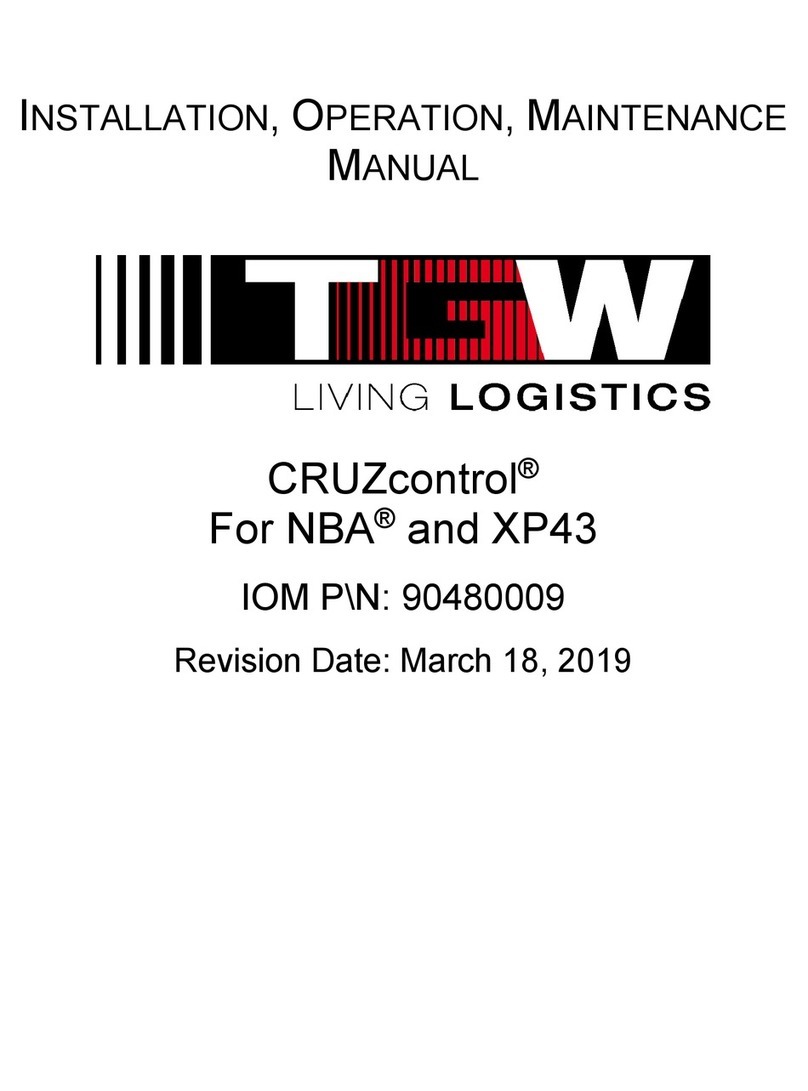
TGW
TGW CRUZcontrol Installation, operation & maintenance manual
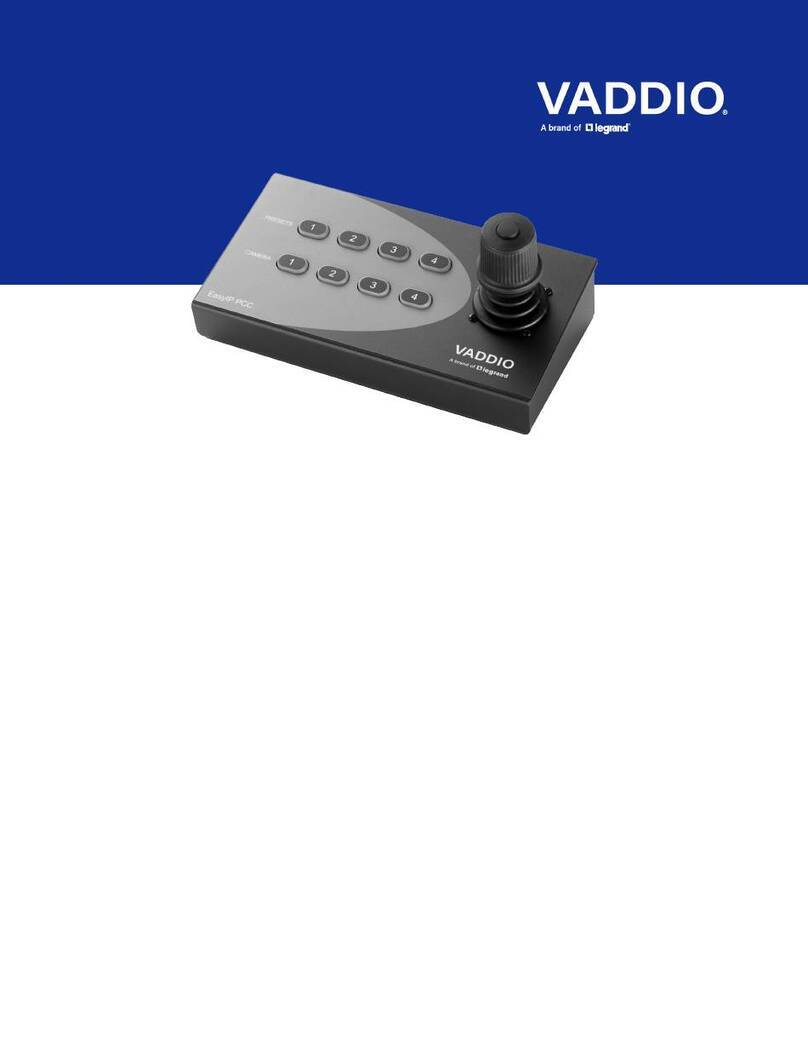
LEGRAND
LEGRAND EasyIP VADDIO PCC Complete manual