Pace Technologies NANO 2000T User manual

- - - - - - - - - - - - - - - - - - - - - - - - - - - - - - - - - - - - - - - - - - - - - - - - - - ▲ INSTRUCTION MANUAL
3601 E. 34th St. Tucson, AZ 85713 USA Tel. +1 520-882-6598 Fax +1 520-882-6599 email: pace@metallographic.com Web: http://www.metallographic.com
Please read this instruction manual carefully and follow all installation, operating and safety guidelines.
NANO 2000T Polisher
Equipment Type: 8 and 10-inch diameter Double Grinder /
Polisher
Model: NANO 2000T
Electrical Requirements: 110 / 220 Volts (single-phase)
Frequency: 50/60 Hz
Motor Horsepower: 1 hp (750 W)
Manual Revision Date: March 8, 2016

- - - - - - - - - - - - - - - - - - - - - - - - - - - - - - - - - - - - - - - - - - - - - - - - - - ▲ INSTRUCTION MANUAL
3601 E. 34th St. Tucson, AZ 85713 USA Tel. +1 520-882-6598 Fax +1 520-882-6599 email: pace@metallographic.com Web: http://www.metallographic.com
Please read this instruction manual carefully and follow all installation, operating and safety guidelines.
NANO 2000T Polisher
Contents
PAGE
Warranty ii
1.0 Product Description 1
2.0 Unpacking, Shipping and Installation 4
3.0 Safety Guidelines 6
4.0 Start-Up and Operation 8
5.0 Maintenance 20
6.0 Trouble Shooting 21
7.0 Metallographic Consumables 22
8.0 Spare Parts 25
9.0 Schematics 39
i

- - - - - - - - - - - - - - - - - - - - - - - - - - - - - - - - - - - - - - - - - - - - - - - - - - ▲ INSTRUCTION MANUAL
3601 E. 34th St. Tucson, AZ 85713 USA Tel. +1 520-882-6598 Fax +1 520-882-6599 email: pace@metallographic.com Web: http://www.metallographic.com
Please read this instruction manual carefully and follow all installation, operating and safety guidelines.
NANO 2000T Polisher
WARRANTY
.Terms and Conditions applying to all PACE Technologies Products
1. LIMITED WARRANTY AND DISCLAIMER:
PACE Technologies Products are warranted for one year from the purchase date to be free from defects in
material and workmanship under correct use, normal operating conditions, and proper application. PACE
Technologies obligation under this warranty shall be limited to the repair or exchange, at PACE
Technologies option, of any PACE Technologies Product or part which proves to be defective as provided
herein. PACE Technologies reserves the right to either inspect the product at Buyer’s location or require it
to be returned to the factory for inspection. Buyer is responsible for freight to and from factory on all
warranty claims. The above warranty does not extend to goods damaged or subjected to accident, abuse or
misuse after release from PACE Technologies warehouse, nor goods altered or repaired by anyone other
than specifically authorized PACE Technologies representatives. PACE Technologies shall not in any way
be responsible for the consequences of any alteration, modification or misuse unless previously approved in
writing by an officer of PACE Technologies.
PACE TECHNOLOGIES MAKES NO EXPRESS WARRANTIES OTHER THAN THOSE WHICH ARE
SPECIFICALLY DESCRIBED HEREIN. Any description of the goods sold hereunder, including any
reference to Buyer’s specifications and any description in catalogs, circulars and other written material
published by PACE Technologies, is the sole purpose of identifying such goods and shall not create an
express warranty that the goods shall conform to such description.
THIS WARRANTY IS EXPRESSLY IN LIEU OF ALL OTHER WARRANTIES, EXPRESSED OR
IMPLIED. THERE ARE NO IMPLIED WARRANTIES OF MECHANTABILITY OR FITNESS FOR
PARTICULAR PURPOSE. THIS WARRANTY STATES PACE TECHNOLOGIES ENTIRE AND
EXCLUSIVE LIABILITY AND BUYER’S EXCLUSIVE REMEDY FOR ANY CLAIM FOR DAMAGES
IN CONNECTIONS WITH PACE TECHNOLOGIES PRODUCTS. PACE TECHNOLOGIES WILL IN
NO EVENT BE LIABLE FOR INCIDENTAL OR CONSEQUENTIAL DAMAGES WHATSOEVER,
NOR FOR ANY SUM IN EXCESS OF THE PURCHASE PRICE.
2. LIABILITY CAP:
PACE Technologies maximum aggregate liability for loss and damage arising under, resulting from or in
connection with the supply or use of the Equipment and Consumables provided under this purchase, or from
the performance or breach of any obligation (s) imposed hereunder, whether such liability arises from any
one or more claims or actions for breach of contract, tort, (including negligence), delayed completion,
warranty, indemnity, strict liability or otherwise, unless otherwise limited by the terms hereof, shall be
limited to one hundred percent (100%) of the purchase price.
3. DELIVERY:
Customer assumes and shall bear the risk of all loss or damage to the Products from every cause whatsoever,
whether or not insured, and title to such Products shall pass to Customer upon PACE Technologies delivery
of the Products to the common carrier of Pace Technologies choice, or the carrier specified in writing by
Customer, for shipment to Customer. Any claims for breakage, loss, delay, or damage shall be made to the
carrier by the Customer and Pace Technologies will render customer reasonable assistance in prosecuting
such claims.
ii

- - - - - - - - - - - - - - - - - - - - - - - - - - - - - - - - - - - - - - - - - - - - - - - - - - ▲ INSTRUCTION MANUAL
3601 E. 34th St. Tucson, AZ 85713 USA Tel. +1 520-882-6598 Fax +1 520-882-6599 email: pace@metallographic.com Web: http://www.metallographic.com
Please read this instruction manual carefully and follow all installation, operating and safety guidelines.
NANO 2000T Polisher
4. ACCEPTANCE:
Customer shall inspect the Products promptly upon receipt of delivery. Unless customer objects in writing
within thirty (30) business days thereafter, customer shall be deemed to have accepted the Products. All
claims for damages, errors, or shortage in Products delivered shall be made by Customer in writing within
such five (5) business day period. Failure to make any claim timely shall constitute acceptance of the
Products.
5. PAYMENT:
Customer agrees to provide timely payment for the Products in accordance with the terms of payment set
forth on the reverse side hereof or in any proposal submitted herewith. If any payment is not paid on or
before its due date, Customer shall pay interest on such late payment from the due date until paid at the
lesser of 12% per annum or the maximum rate allowed by law.
6. DEFAULT:
If Buyer is in default (including, but not limited to, the failure by Buyer to pay all amounts due and payable
to Seller) under the work or purchase order or any other agreement between Buyer and Seller, Buyer’s rights
under the warranty shall be suspended during any period of such default and the original warranty period
will not be extended beyond its original expiration date despite such suspension of warranty rights.
7. MISCELLANEOUS PROVISIONS:
This agreement has been made in and shall be governed by the laws of the State of Arizona. These terms
and conditions and the description of the Products on the reverse side hereof or in any proposal submitted
herewith constitute the entire agreement and understanding of the parties with respect to this sale and
supersede all prior and contemporaneous agreements or understandings, inducements or representations,
expressed or implied, written or oral, between the parties with respect hereto. Any term or provision of this
Agreement may be amended, and any observance of any term of this Agreement may be waived, only by a
writing signed by the party to be bounds. The waiver by a party of any breach shall not be deemed to
constitute a waiver of any other breach. Should suit be brought on this Agreement, the prevailing party shall
be entitled to recover its reasonable attorneys’ fees and other costs of suit including costs and attorneys’ fees
incurred on appeal or in collection of any judgment.
iii

- - - - - - - - - - - - - - - - - - - - - - - - - - - - - - - - - - - - - - - - - - - - - - - - - - ▲ INSTRUCTION MANUAL
3601 E. 34th St. Tucson, AZ 85713 USA Tel. +1 520-882-6598 Fax +1 520-882-6599 email: pace@metallographic.com Web: http://www.metallographic.com
Please read this instruction manual carefully and follow all installation, operating and safety guidelines.
NANO 2000T Polisher
1.0 Product Description
1.1 General Description
1
Hard coat
anodized
working wheel
Water valve
Water switch
The NANO 2000T is a 8 or 10-inch single wheel grinding/ polishing machine for manual wet
grinding or polishing of metallographic specimens.
The NANO 2000T is a variable speed (0-1000 rpm) with three programmable fast speed
buttons (approx. 100, 200 and 300 rpm) polisher. For semi-automated grinding / polishing the
FEMTO Polishing head can added.
Speed display
Emergency
Stop button
Time display

- - - - - - - - - - - - - - - - - - - - - - - - - - - - - - - - - - - - - - - - - - - - - - - - - - ▲ INSTRUCTION MANUAL
3601 E. 34th St. Tucson, AZ 85713 USA Tel. +1 520-882-6598 Fax +1 520-882-6599 email: pace@metallographic.com Web: http://www.metallographic.com
Please read this instruction manual carefully and follow all installation, operating and safety guidelines.
NANO 2000T Polisher
1.2 Technical Specifications
Electrical specifications: 110 / 220V (50/60 Hz) (single phase
input - motor runs on 3-phase power
for more torque)
Working wheel: 8-inch (200 mm) or
10-inch (250 mm) diameter
Motor power: 1 hp (750 hp)
Polishing base speed:
0 to 1000 rpm variable speed (20
rpm increments). Fast speed
buttons pre-programmed for 100,
200 and 300 rpm)
Weight: Approx. 150 lbs (70 kg)
Dimensions (WxHxD): Approx. 30” x 13” x 28”
(760 mm x 330 mm x 710 mm)
Working temperature: 32° - 100°F (0 - 40°C)
Shipping temperature: 32° - 100°F (0 - 40°C)
Storage temperature: 32° - 100°F (0 - 40°C)
Maximum part size 1/3-diameter of working wheel
2
EU Directives: Machinery directive 2006/42/EC
Low Voltage Directive 2006/95/EC
Electromagnetic Compatibility directive 2004/108/EC
EU Harmonized Standards: EN ISO 1200:2010
EN 61010-1:2010
EN 61326-1:2006

- - - - - - - - - - - - - - - - - - - - - - - - - - - - - - - - - - - - - - - - - - - - - - - - - - ▲ INSTRUCTION MANUAL
3601 E. 34th St. Tucson, AZ 85713 USA Tel. +1 520-882-6598 Fax +1 520-882-6599 email: pace@metallographic.com Web: http://www.metallographic.com
Please read this instruction manual carefully and follow all installation, operating and safety guidelines.
NANO 2000T Polisher
1.4 Features
1.3 Mechanical Schematic
Note: Installation of the NANO 2000T
should be on a flat sturdy surface, with
easy access to drain, water and
electrical connections.
3
The NANO 2000T is equipped with a
powerful motor, connected to the polishing
wheel through a maintenance-free V-belt.

- - - - - - - - - - - - - - - - - - - - - - - - - - - - - - - - - - - - - - - - - - - - - - - - - - ▲ INSTRUCTION MANUAL
3601 E. 34th St. Tucson, AZ 85713 USA Tel. +1 520-882-6598 Fax +1 520-882-6599 email: pace@metallographic.com Web: http://www.metallographic.com
Please read this instruction manual carefully and follow all installation, operating and safety guidelines.
NANO 2000T Polisher
2.0 Unpacking, Shipping and Installation
2.1 Unpacking Unit is delivered in a box. Unpack and check for completeness of
parts.
Measures WxHxD: 34” x 34” x 20”
Weight: Varies, depending upon model
(approximately 190 lbs).
2.2 Shipping When moving box, lift from bottom.
! Caution: Heavy equipment. Take care to avoid bodily injury.
4

- - - - - - - - - - - - - - - - - - - - - - - - - - - - - - - - - - - - - - - - - - - - - - - - - - ▲ INSTRUCTION MANUAL
3601 E. 34th St. Tucson, AZ 85713 USA Tel. +1 520-882-6598 Fax +1 520-882-6599 email: pace@metallographic.com Web: http://www.metallographic.com
Please read this instruction manual carefully and follow all installation, operating and safety guidelines.
NANO 2000T Polisher
Electrical connection
110V or 220V
2.3 Installation
!
Install unit carefully! Improper installation voids warranty.
The NANO 2000T should be placed on a flat stable surface.
Connect to air, water supply, drain and electrical connections.
After water, drain and electrical connections are completed, the system is ready for
operation by activating the main power switch.
5
Backside connections
External water supply: The water supply line requires a 1/4-inch compression fitting. It is
recommended that the water supply be turned off when the unit is
not in use. Inlet water should be clean and contamination-free to
extend the life and performance of the systems.
Electrical connection: Connect six-foot electrical power cable to source.
Drain connection: Connect drain so that it exits the machine in the direction best
suited to the drain site
Water drain
External water
supply
FEMTO connections
Connect drain for best
direction to drain with
fittings

- - - - - - - - - - - - - - - - - - - - - - - - - - - - - - - - - - - - - - - - - - - - - - - - - - ▲ INSTRUCTION MANUAL
3601 E. 34th St. Tucson, AZ 85713 USA Tel. +1 520-882-6598 Fax +1 520-882-6599 email: pace@metallographic.com Web: http://www.metallographic.com
Please read this instruction manual carefully and follow all installation, operating and safety guidelines.
NANO 2000T Polisher
3.0 Safety Guidelines
3.1 Warning Sign
!This sign points to special safety features on the machine.
Always follow proper operational guidelines and avoid contact with lubricants and abrasives.
Seek appropriate medical care for cutting injuries.
3.3 Emergency Statement
!Operate unit as specified in this manual.
!Disconnect power before opening unit.
!Do not leave any specimen or other parts on the working wheel.
!Ensure that the air slots on polishing base are not obstructed.
!When unit is not in use turn off water.
!Securely hold the sample, preferably with two hands.
3.2 Safety Precautions
6
!Careful attention to this instruction manual and the recommended safety guidelines is
essential for the safe operation of the NANO 2000T.
!Proper operator training is required for operation of the NANO 2000T. Any unauthorized
mechanical and electrical change, as well as improper operation, voids all warranty
claims. All service issues need to be reported to the manufacturer / supplier.

- - - - - - - - - - - - - - - - - - - - - - - - - - - - - - - - - - - - - - - - - - - - - - - - - - ▲ INSTRUCTION MANUAL
3601 E. 34th St. Tucson, AZ 85713 USA Tel. +1 520-882-6598 Fax +1 520-882-6599 email: pace@metallographic.com Web: http://www.metallographic.com
Please read this instruction manual carefully and follow all installation, operating and safety guidelines.
NANO 2000T Polisher
3.4 Safety Test
!
Examine and verify that the NANO 2000T safety devices and operating performance are in
good working condition prior to use. The following safety check is considered important:
Test: Activate main switch.
Depress emergency stop switch.
Proper
Response: Machine powers down.
Malfunction: Machine does not lose power.
Corrective
measure:
If system does not power down,
disconnect power supply cord and call
service technician.
Emergency stop switch
Emergency stop switch
7

- - - - - - - - - - - - - - - - - - - - - - - - - - - - - - - - - - - - - - - - - - - - - - - - - - ▲ INSTRUCTION MANUAL
3601 E. 34th St. Tucson, AZ 85713 USA Tel. +1 520-882-6598 Fax +1 520-882-6599 email: pace@metallographic.com Web: http://www.metallographic.com
Please read this instruction manual carefully and follow all installation, operating and safety guidelines.
NANO 2000T Polisher
Programming mode Water
switch
8
4.0 Start-up and Operation
4.1 General
4.2 Control Panel
The NANO 2000T is a hand grinding/ polishing machine. By adding the FEMTO power head,
semi-automated polishing can be accomplished.
Emergency stop button: Emergency stop switch cuts power to the motor immediately.
Wheel direction: Clockwise rotation or counter clockwise rotation.
Start / stop buttons: Start/stop the polishing wheel in both manual and auto mode.
Water switch: Activates the water solenoid for the rinse bowl and rinse spout.
Preset speeds: Allows for faster speed control, SPL - low speed, SPM - medium
speed, SPH - high speed (factory setting approx. 100, 200, 300
rpm.
Auto-mode: Allows for running pre-programmed speeds and times (factory
setting approx. 200 rpm, FWD, 30 seconds).
Wheel direction Start/Stop
Preset speeds
(Low, medium, high)
Auto-mode for timed
grinding/ polishing

- - - - - - - - - - - - - - - - - - - - - - - - - - - - - - - - - - - - - - - - - - - - - - - - - - ▲ INSTRUCTION MANUAL
3601 E. 34th St. Tucson, AZ 85713 USA Tel. +1 520-882-6598 Fax +1 520-882-6599 email: pace@metallographic.com Web: http://www.metallographic.com
Please read this instruction manual carefully and follow all installation, operating and safety guidelines.
NANO 2000T Polisher
9
4.3 Grinding / polishing by hand
1. Install working wheel and attach grinding papers / polishing cloths.
2. Switch on the machine in the back and set the mode, speed, and time (if required).
3. Position flexible water spout over working wheel. During sample preparation adjust water
flow by turning water control knob as required. Note: Initial operation of water valve may
contain air in the lines. Turn water on slowly to purge air from system.
4. Press START/STOP start and stop the machine in the manual mode.
4.2.1 Direction and speed controller (manual)
1. To change direction of the wheel:
-Press clockwise or counter clockwise button,
LED will light
2. To change the speed of the wheel:
Select low, medium or high speed fast buttons
and use up and down arrows to fine tune speed
if required
Fast speed buttons
4.2.1 Programmable Mode
To change the speed setting for
the fast speed buttons use the
following procedure:
Press the PRG button and use
the up and down keys to SL
(slow speed) and press ENTER.
Use the up and down < key to
change the speed. Use Sn for
changing the medium speed
and SH for the fast speed.
1
.
The programming mode can be used to pre-set the
polishing speed, direction and time for automated
polishing. It can also be used to change the fast speed
buttons.
2
.
To change the speed of the wheel:
Press the PRG button and use the up and down keys
to SP1 and press ENTER. Use the up and down < key
to change the speed. Press ENTER to save.
3
.
To program a grinding/ polishing time:
Press the PRG button and use the up and down keys
to t1 and press ENTER. Use the up and down < key to
change the time (enter in seconds - displayed min-sec)
4
.
To operate the pre-programmed conditions:
PRESS the AUTO button and then start the program
with the RUN/STOP button. The pre-programmed
conditions will be executed.

- - - - - - - - - - - - - - - - - - - - - - - - - - - - - - - - - - - - - - - - - - - - - - - - - - ▲ INSTRUCTION MANUAL
3601 E. 34th St. Tucson, AZ 85713 USA Tel. +1 520-882-6598 Fax +1 520-882-6599 email: pace@metallographic.com Web: http://www.metallographic.com
Please read this instruction manual carefully and follow all installation, operating and safety guidelines.
NANO 2000T Polisher
4.4 Metallographic Specimen Preparation Basics
A typical metallographic specimen preparation consists of the following basic steps:
Preparation Stage Purpose
Initial documentation: To document the initial condition of the sample,
To map the sample surface,
To highlight the area of interest.
Sectioning / cutting: To reduce the size of large samples and to sample the
specimens close to the area of interest.
Rough, or planar grinding
(refer to Section 4.4.1):
To obtain a planar surface,
To remove sectioning damage,
To approach the area of interest.
Rough polishing (refer to
Section 4.4.2):
Ideally to remove all the subsurface damage and microstructural
damage produced during cutting and rough grinding (Superficial
scratches may still be present after this step).
Final polishing (refer to
Section 4.4.1)::
Generally, more for cosmetic purposes than for removing
microstructural damage. In most cases, this stage should be
minimized to avoid overpolishing and distorting the
microstructural features.
Etching: To enhance microstructural features such as grain boundaries,
grain size, phase differences, etc.
Examination: A variety of examination techniques are used in metallography,
including: optical microscopy, electron microscopy and hardness
testing.
10

- - - - - - - - - - - - - - - - - - - - - - - - - - - - - - - - - - - - - - - - - - - - - - - - - - ▲ INSTRUCTION MANUAL
3601 E. 34th St. Tucson, AZ 85713 USA Tel. +1 520-882-6598 Fax +1 520-882-6599 email: pace@metallographic.com Web: http://www.metallographic.com
Please read this instruction manual carefully and follow all installation, operating and safety guidelines.
NANO 2000T Polisher
Rough or planar grinding, is required to produce flat specimens and to reduce the damage created
by sectioning. The planar grinding step is accomplished by decreasing the abrasive grit particle size
sequentially to obtain surface finishes that are ready for polishing. Care must be taken to avoid being
too abrasive in this step, and actually creating greater specimen damage than produced during
cutting. This is especially true for very brittle materials such as ceramics and silicon.
The machine parameters which affect the preparation of metallographic specimens include: grinding /
polishing pressure, grinding direction, and the relative velocity distribution between the specimen and
the polishing wheel.
Grinding Pressure
Grinding / polishing pressure is dependent upon the applied force (pounds or Newton's) and the area
of the specimen and mounting material. Pressure is defined as the Force/Area (psi, N/m2 or Pa). For
specimens significantly harder than the mounting compound, pressure is better defined as the force
divided by the specimen surface area. Thus, for larger hard specimens, higher grinding / polishing
pressures increase stock removal rates. However, higher pressure also increases the amount of
surface and subsurface damage produced in the specimen.
Note regarding SiC grinding papers: as the abrasive grains dull and cut rates decrease, increasing
grinding pressures can extend the life of the SiC paper.
Higher grinding / polishing pressures can also generate additional frictional heat which may be
beneficial for the chemical mechanical polishing (CMP) of ceramics, minerals and composites.
Likewise for extremely friable specimens (such as nodular cast iron), higher pressures and lower
relative velocity distributions can aid in retaining inclusions and secondary phases.
Grinding Direction
The orientation of the specimen can have a significant impact on the preparation results, especially
for specimens with coatings. In general, when grinding and polishing materials with coatings, the
brittle component should be kept in compression. In other words, for brittle coatings, the direction of
the abrasive should be through the coating and into the substrate. Conversely, for brittle substrates
with ductile coatings, the direction of the abrasive should be through the brittle substrate and into the
ductile coating.
Manual Preparation
In order to ensure that the previous rough grinding damage is removed when grinding by hand, the
specimen should be rotated 90 degrees and continually ground until all of the scratches from the
previous grinding direction are removed. When necessary, the abrasive paper should be replaced
with a newer paper to maintain cutting rates.
4.4.1 Rough / Planar Grinding
11

- - - - - - - - - - - - - - - - - - - - - - - - - - - - - - - - - - - - - - - - - - - - - - - - - - ▲ INSTRUCTION MANUAL
3601 E. 34th St. Tucson, AZ 85713 USA Tel. +1 520-882-6598 Fax +1 520-882-6599 email: pace@metallographic.com Web: http://www.metallographic.com
Please read this instruction manual carefully and follow all installation, operating and safety guidelines.
NANO 2000T Polisher
The purpose of the rough polishing step is to remove the damage produced during cutting and planar
grinding. Proper rough polishing will maintain specimen flatness and retain all inclusions or
secondary phases. By eliminating the previous damage and maintaining the microstructural integrity
of the specimen at this step, a minimal amount of time is required to remove the cosmetic damage at
the final polishing step.
Rough polishing is accomplished primarily with diamond abrasives ranging from 9 micron to 1
micron. Polycrystalline diamond -- because of its multiple and small cutting edges -- produces high
cut rates with minimal surface damage. Therefore, polycrystalline diamond abrasives are
recommended for metallographic rough polishing on low-napped polishing cloths.
4.4.2 Rough Polishing
Rough Polishing Guidelines
12
Material Recommendations
Metals (ferrous, non-ferrous,
tool steels, superalloys, etc.)
Rough polishing typically requires two polishing steps, e.g., a 6-
micron diamond followed by a 1-micron diamond on low-napped
polishing cloths.
Ceramics and ceramic matrix
composites (CMC)
Low-nap polishing pads using polycrystalline diamond, alternating
with colloidal silica. This provides a chemical mechanical
polishing (CMP) effect which results in a damage-free surface
Polymer matrix composites
(PMC) Diamond-lapping films are recommended.
Biomaterials
Low-napped polishing pads with polycrystalline diamond,
alternating with colloidal silica. Alternatively, diamond-lapping
films may work well.
Microelectronic specimens Diamond-lapping films are recommended.
Plastics and polymers 800 and 1200 grit SiC abrasive paper are recommended.
Plasma spray materials Diamond-lapping films or low-napped polishing pads with
alternating diamond and colloidal silica abrasives.

- - - - - - - - - - - - - - - - - - - - - - - - - - - - - - - - - - - - - - - - - - - - - - - - - - ▲ INSTRUCTION MANUAL
3601 E. 34th St. Tucson, AZ 85713 USA Tel. +1 520-882-6598 Fax +1 520-882-6599 email: pace@metallographic.com Web: http://www.metallographic.com
Please read this instruction manual carefully and follow all installation, operating and safety guidelines.
NANO 2000T Polisher
The purpose of final polishing is to remove only the cosmetic surface damage. It should not be used
to remove any damage remaining from cutting and planar grinding. If the damage from these steps is
not completely removed, the rough polishing step should be repeated or continued.
4.4.3 Final Polishing
Material Recommendation
Metals (ferrous, non-
ferrous, tool steels,
superalloys, etc.)
High-napped polishing pads with a nanometer alumina polishing
abrasive. The polishing times should nominally be less than 30
seconds.
Ceramics and ceramic
matrix composites (CMC)
Low-napped polishing pads using 1-um polycrystalline diamond,
alternating with colloidal silica or colloidal silica alone.
Polymer matrix composites
(PMC)
Fine abrasive diamond-lapping films, followed by a very light polish
on a high-napped polishing pad.
Biomaterials
Low-napped polishing pads with polycrystalline diamond, alternating
with colloidal silica.
Microelectronic specimens Diamond-lapping films followed by a very light polish on a
high-napped polishing pad.
Plastics and polymers Light polish with alumina on a high-napped polishing pad.
Plasma spray materials Diamond-lapping films followed by a very light and short alumina or
colloidal silica polish on a high-napped polishing pad.
13
Final Polishing Guidelines

- - - - - - - - - - - - - - - - - - - - - - - - - - - - - - - - - - - - - - - - - - - - - - - - - - ▲ INSTRUCTION MANUAL
3601 E. 34th St. Tucson, AZ 85713 USA Tel. +1 520-882-6598 Fax +1 520-882-6599 email: pace@metallographic.com Web: http://www.metallographic.com
Please read this instruction manual carefully and follow all installation, operating and safety guidelines.
NANO 2000T Polisher
4.5 Selected Polishing Procedures
4.5.1 1095 Carbon Steel (Pearlite and Martensite Phases) Preparation of high carbon steels is
fairly straight-forward. Depending upon the heat treatment, the grinding and polishing times may
increase for the harder martensite phase.
1095 Steel, Furnace-Cooled, etched with
2% nital, 400X B.F.
Microstructure: Pearlite structure
1095 Steel, Water-Quenched, etched with
picric acid, 1000X B.F.
Miicrostructure: Martensite structure
14
Abrasive/surface Lubricant Time
PDGD-125M Diamond Grinding Disk water Until plane
SIRIUS Composite grinding disk 9 um DIAMAT Diamond 3 minutes
ORION Composite grinding disk 3 um DIAMAT diamond 3 minutes
1 um DIAMAT diamond on ATLANTIS pad DIALUBE Extender 2 minutes
0.05 um Nanometer alumina on MICROPAD
or TRICOTE pad 1 minute

- - - - - - - - - - - - - - - - - - - - - - - - - - - - - - - - - - - - - - - - - - - - - - - - - - ▲ INSTRUCTION MANUAL
3601 E. 34th St. Tucson, AZ 85713 USA Tel. +1 520-882-6598 Fax +1 520-882-6599 email: pace@metallographic.com Web: http://www.metallographic.com
Please read this instruction manual carefully and follow all installation, operating and safety guidelines.
NANO 2000T Polisher
4.5.2 Stainless Steel
Stainless steels have high concentrations of chromium (>12%) and are generally relatively soft as
compared to heat-treated steels. This makes stainless steel more susceptible to smearing.
Preparation is relatively straight-forward.
431 Stainless Steel microstructure
15
Abrasive/surface Lubricant Time
320 grit SiC paper
400 grit SiC paper
600 grit SiC paper
800 grit SiC paper
1200 grit SiC paper
water
Until plane
1 minute
1 minute
1 minute
1 minute
1 um DIAMAT diamond on TEXPAN pad SIAMAT colloidal
silica 2 minutes
0.05 um Nanometer alumina on NAPPAD pad 1 minute

- - - - - - - - - - - - - - - - - - - - - - - - - - - - - - - - - - - - - - - - - - - - - - - - - - ▲ INSTRUCTION MANUAL
3601 E. 34th St. Tucson, AZ 85713 USA Tel. +1 520-882-6598 Fax +1 520-882-6599 email: pace@metallographic.com Web: http://www.metallographic.com
Please read this instruction manual carefully and follow all installation, operating and safety guidelines.
NANO 2000T Polisher
4.5.3 Aluminum and Aluminum Alloys
Aluminum and aluminum alloys are difficult to prepare because they are soft and contain oxide
particles which can become dislodged and scratch the surface. The key to polishing aluminum is to
use very fine polishing abrasives (fine aggregates).
Aluminum - Silicon Alloy microstructure,
Kallings etchant
16
Abrasive/surface Lubricant Time
P220 grit ALO paper
P500 grit ALO paper
P1200 grit ALO paper
Water
Until plane
1 minute
1 minute
1 um DIAMAT diamond on ATLANTIS pad DIALUBE Purple Extender 2 minutes
0.05 um Nanometer alumina on NAPPAD
pad 1 minute
Table of contents
Other Pace Technologies Sander manuals
Popular Sander manuals by other brands

AEG
AEG FS 280 Original instructions
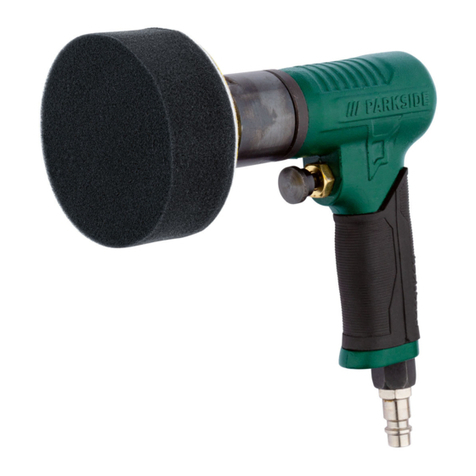
Parkside
Parkside PDAP 75 A1 Translation of the original instructions
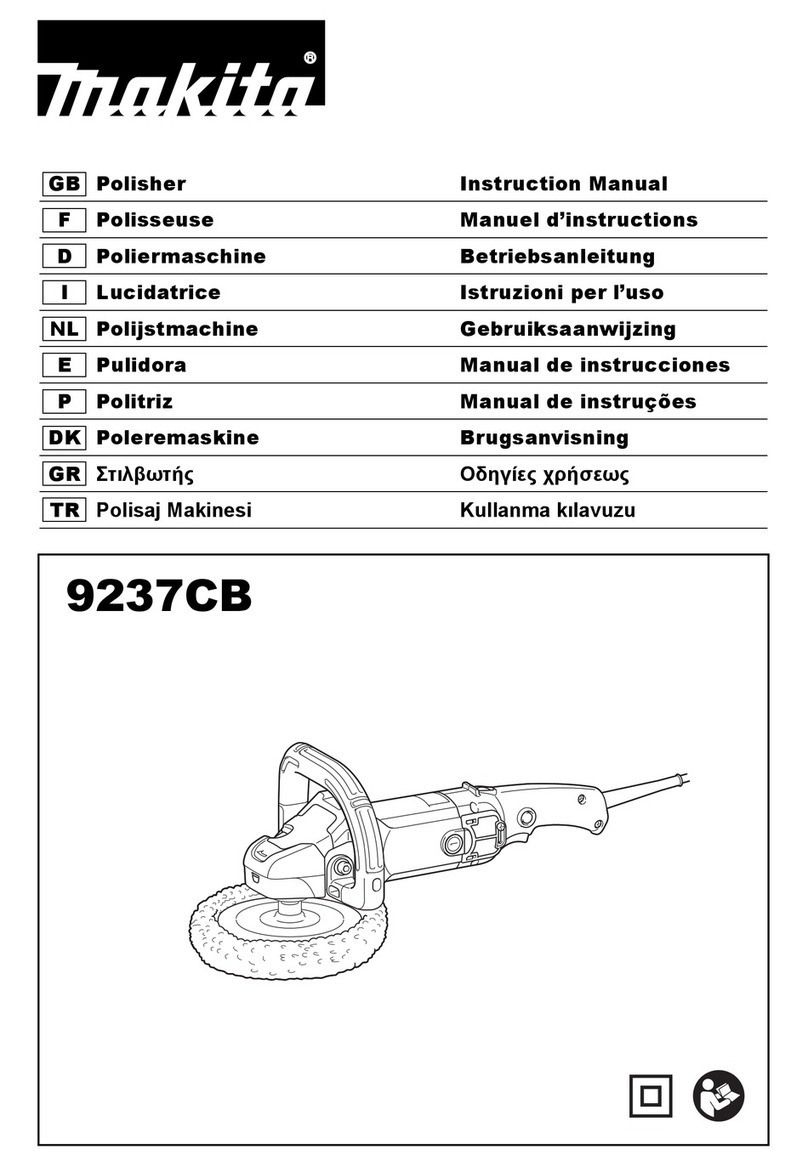
Makita
Makita 9237CB instruction manual
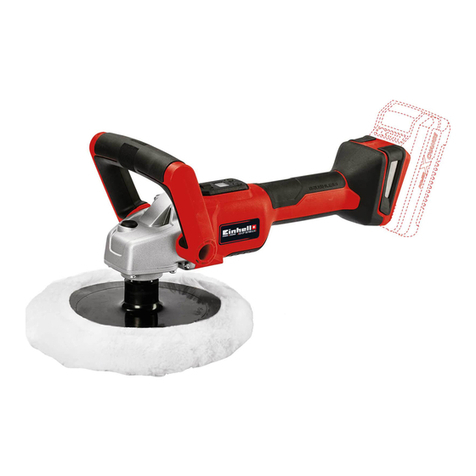
EINHELL
EINHELL CE-CP 18/180 Li E Original operating instructions

Gude
Gude FS 90 E Translation of the original instructions
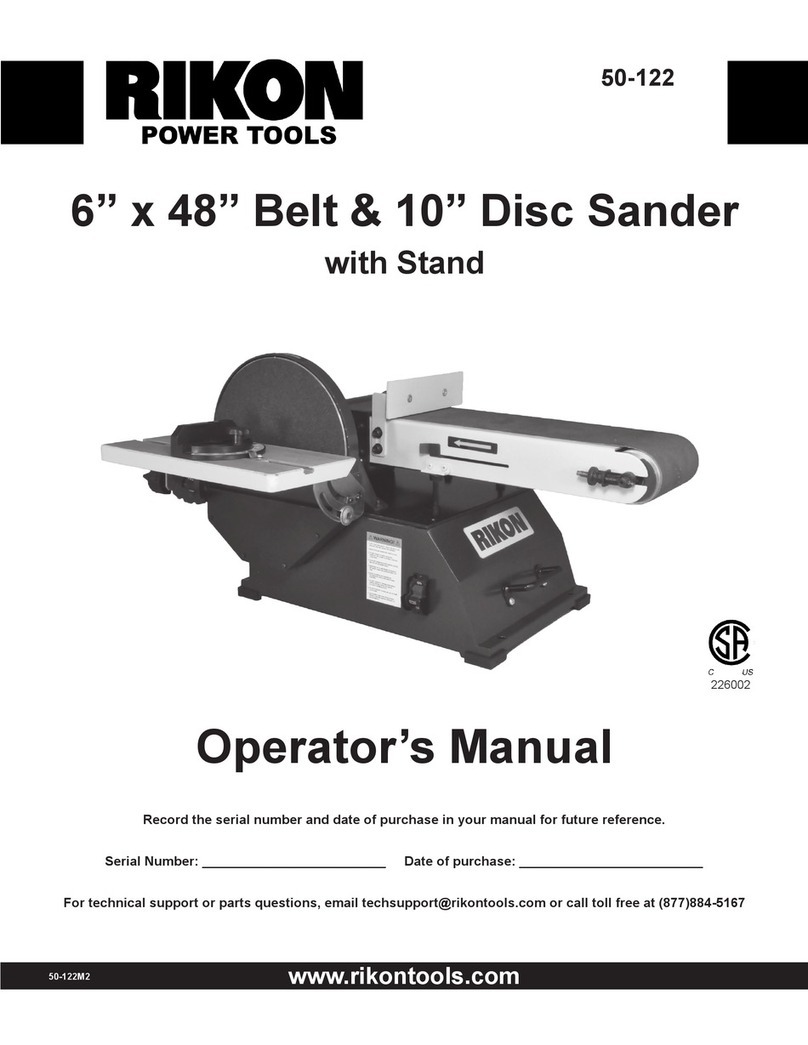
Rikon Power Tools
Rikon Power Tools 50-122 Operator's manual