Parking Facilities PF8000 User manual

O&M Manual
Revision 4.4
PF8000 TypeB
PF8000 Type B
Automatic Rising kerb
Maximum Span: 5 Metres
Duty Cycle: 100%
Instructions For: PF8000
GB

Introduction and Warnings
This equipment is part of a large range of traffic flow products. They are designed to be easy to install, as
all settings and internal wiring has been completed in our factory. Any of the instructions in this manual
should only be carried out by a qualified service engineer or a competent person.
The kerbs are ready to bolt down, connect in the single phase supply and any loops etc and then power
up. In this manual there is important information on how to do this, but most importantly of all how to do
this safely. Please approach any task responsibly and safely.
The following information is a guide only, and whilst we have made every effort to be accurate and correct
there may be printing errors which we cannot be held responsible for.
With a correct installation you can expect to enjoy many years of reliable service from this product, we do
however recommend that the product has a bi-annual service carried out by an engineer. Please contact
our service department to obtain a quote. As we manufacture the products we are best suited to care for
your equipment.
Thank you for your custom and welcome to the exciting world of Total Traffic Flow Solutions.
/ /20
!
Important Safety Notice
Sliding kerbs are designed to Control the flow of vehicular traffic
primarily. It can be dangerous to allow the passage of
pedestrians and any other self-powered animal or device to
utilise this method of access without appropriate warnings and or
signage.
It may be necessary for the end user of this product to provide
an alternative, safe method of access to cater for the previously
mentioned categories.
The end user should fit all necessary signage and warning
notices to either side of the kerb, which should be visible and
clear from all directions of approach.
The product that was shipped to you was designed with a control
program to protect all categories from harm or affect this
however is only a fail safe and should not be modified or
tampered with by any unauthorised person not sanctioned by the
manufacturer.
Please sign and date below to say that you have read and
understood this notice before ANY installation work:
The “Warnings” leaflet and “Instruction booklet” supplied with this
product should be read carefully as they provide important information
about safety, installation, use and maintenance.
Scrap packing materials (plastic, cardboard, polystyrene etc) according
to the provisions set out by current standards. Keep nylon or polystyrene
bags out of children's reach.
Keep the instructions together with the technical brochure for future
reference.
This product was exclusively designed and manufactured for the use
specified in the present documentation. Any other use not specified in
this documentation could damage the product and be dangerous.
The Company declines all responsibility for any consequences resulting
from improper use of the product, or use which is different from that
expected and specified in the present documentation.
Do not install the product in explosive atmosphere.
The construction components of this product must comply with the
following European Directives: 89/336/CEE, 73/23/EEC, 98/37/EEC
and subsequent amendments. As for all non-EEC countries, the abovementioned
standards as well as the current national standards should
be respected in order to achieve a good safety level.
Information on using
this manual
ŸRead all information thoroughly
ŸPay attention to all safety advice
ŸBe aware of the symbols (shown above right and above
left) as they have different meanings. One is an
information symbol, the other a warning.
ŸThere are many artists impressions of the product in this
manual you should refer to the images as a guide only.
Professional CAD drawings should be used as a
reference drawing and nothing else. As before every
effort has been made to be 100% accurate in this
manual but we cannot make any guarantees.
ŸAs we constantly innovate our products we may change
the quoted spec and any other details that have been
documented in this manual so you should always refer
to the supplier to see if the manual that was shipped
with your product is the latest edition.
ŸAs with all electrical installations you should use a
qualified electrician and obey all of the latest laws and
regulations.
ŸBe sure to fill out and complete ALL paperwork where
instructed as this manual is the equipments log book
and maintenance manual.
The Company declines all responsibility for any consequences resulting
from failure to observe Good Technical Practice when constructing
closing structures (door, kerbs etc.), as well as from any deformation
which might occur during use.
The installation must comply with the provisions set out by the following
European Directives: 89/336/CEE, 73/23/EEC, 98/37/EEC and
subsequent amendments.
Disconnect the electrical power supply before carrying out any work on
the installation. Also disconnect any buffer batteries, if fitted.
Fit an omnipolar or magnetothermal switch on the mains power supply,
having a contact opening distance equal to or greater than 3mm.
Check that a differential switch with a 0.03A threshold is fitted just before
the power supply mains.
Check that earthing is carried out correctly: connect all metal parts for
closure (doors, kerbs etc.) and all system components provided with an
earth terminal.
Fit all the safety devices (photocells, electric edges etc.) which are
needed to protect the area from any danger caused by squashing,
conveying and shearing, according to and in compliance with the
applicable directives and technical standards.
PF8000

This article describes how your equipment will be delivered to you, specifications on the transportation
used and advice including health & safety on movement of the equipment.
The kerb should ALWAYS! be in the lowered position before any movement commences, this ensures that
the kerb does not distort or get damaged. Refer to Manual Release instructions on Page 6 of this manual
to move the kerb into this position.
Illustration shows kerb as it will be delivered
The manufacturer will use a qualified transport company to deliver the product conforming to the
necessary regulations as detailed below:
ŸAll drivers are qualified hi-ab certified
ŸAll drivers are tested once yearly
ŸAll drivers carry risk assessments and method statements (available on request)
ŸThey are controlled under law to conform as there are no trade regulation standards to comply with
Health and safety Considerations:
Moving Goods Safely (MGS) is a national project involving both the Health and Safety Executive (HSE) and
Local Authorities (LA) working in partnership. The project aims to reduce injuries and ill-health arising from the
movement of goods from supplier through haulier to the recipient and end user including any home deliveries.
The project will focus upon the delivery and collection of goods and the hazards this generates. It covers the
main areas that cause the majority of injuries and ill-health to workers, including:
ŸWorkplace transport;
ŸSlips & trips, and;
ŸMusculoskeletal disorders (MSD).
The movement of goods presents us, as health and safety regulators, with the challenge of dealing with a huge
variety of issues. The commercial organisations involved within the movement of goods are diverse including
haulier, third party logistics providers, pallet networks, retailers etc, with some very large companies,
thousands of small businesses and the self-employed. The movement of goods is more than just trucks on the
road with a large proportion of accidents happening at the delivery/collection sites that are often not directly
under the control of the company making the delivery or collection. Communication and cooperation problems
can arise due to the many organizations involved in the movement of the goods, and this can also lead to
difficulties in effectively managing health and safety.
(Source H&S Executive UK 2008)

Blocker Overview PF8000
PARKING FACILITIES POWERUNIT
0.75KW 8L VERT TANK (TYPE B)
Comprising of:
UP100 K3P0-01 FOR MANIFOLDS
1013 AND ALL CETOP INTERFACES.
NEW UP100 HOUSING SEALKIT FITS
K1,K2,K3 AND K4 HOUSINGS.
FIXING KIT UP100 FOR METAL TK
NEW UP100 RETURN FILTER 150MIC
FILTERS OIL INTERNALLY.
PUMP COUPLING 0.25KW-1.5KW
E131 E132 AND E133.
1 STATION CETOP 3 MANIFOLD C/W
GAUGE PORT.5073 SUITS UP100.
SUC STRAIN 6L,7L,15L VERTICAL
RESERVOIR. 1.2CC-2.5CC PUMPS
CETOP 3 SOLENOID OPERATED
DIRECTIONAL CONTROL VALVE
CETOP 3 MOD P/OP CHECK 0.5 C/P
AP100/3.5S309 UP100 GEAR PUMP
3.5CC/REV 5.04L/MIN @ 1440RPM.
0.75KW 415V 3PH 50HZ 4PL B34
ELECTRIC MOTOR.
8 LITRE VERTICAL STEEL TANK
L08,OR-01 UP100.
AC MOTOR FLANGE 0.55KW-0.75KW
AC MOTOR COUPLING 0.55KW-0.75K
W E131.
M8X25CAPHEAD
M6 X 12 CAP HEAD
M6 X 20 CAP HEAD
M6 SPRING WASHER
M8SPRINGWASHER

Guide to Physical Installation PF8000
Installation may be broken down into the following stages:
· Excavation of Blocker pit.
· Installation of 100mm conduit for hoses and signal cable.
· Construction of sump pit ( if required )
· Installation of drainage pipes.
· Fabrication of rebar cage.
· Construction of Blocker foundation base.
· Installation of Blocker unit.
· Backfilling of Blocker pit.
· Installation of inductive road loops ( if required ).
· Mounting of traffic lights ( if required ).
· Construction of HPU cabinet base.
· Installation of conduit for power / signal and access control cables.
· Pulling of cables and hoses.
· Positioning of HPU cabinet.
· Connecting power cables and hoses.
Road Blocker;
To be installed across the roadway with the curved edge of the rising wedge fitted on the insecure (attack side).
The wedge pivot points are to be positioned on the secure side of the site.
The blocker may be sited on a rising or falling road surface and allowed to follow the line of the slope, however, the
blocker must be the camber of the road. Provision must be made for drainage of water from the inside of the
blocker.
If the Blocker is to be sited in an area which is susceptible to flooding or a high-water table, a sump pit must be
provided in the
blocker foundation and a suitable pump system used to keep the inside of the Blocker free of water. A 100mm pvc
duct (for the two hydraulic hoses and the signal cable) must be provided between the Blocker and the HPU cabinet.

Physical Installation Cont... PF8000
2. See reference drawings for
visual guide to previous page
Concrete Pad laid after dig
(for blocker to sit on)
Drain
Earth wall
3.
Ground Excavated
(Base Poured) Blocker Lowered into hole
eye bolts used to level blocker
Backfill concrete around
blocker

Manual Release Guide
kerb Maintenance PF8000
Please use the following instructions to operate the kerb manually, the following
is assuming you have powered down the unit and opened the HPU cabinet door:
IMPORTANT NOTE
In order for the equipment to comply to the legislation/directives noted in this document it must be maintained and have a maintenance
schedule as documented in Regulation 5 of “The workplace health & Safety Welfare Regulations 1992"
As stated at the beginning of this manual we recommend a bi-annual service, but at a bear minimum, it is imperative that you get a service
done once every 12 months. This is not a sales tactic in disguise, there is a very serious health and safety issues/risks associated with not
complying to this. Also in order for your kerb to keep complying with the appropriate legislation.
ŸBefore carrying out any maintenance to the installation, disconnect the mains power supply.
ŸMake sure you have disconnected/Isolated the power before attempting any work.
ŸA Maintenance Contract should be sought from a specialist company after a maximum of 5000 manoeuvres or 1year from the install date.
ŸOccasionally clean the photocell optical components and make sure they are free from dirt, water, rain, soil etc..
ŸHave a qualified technician (installer) check the correct setting of the electric clutch.
ŸIf the power supply cable is damaged, it must be replaced by the manufacturer or its technical assistance service, or else by a suitably
qualified person, in order to prevent any risk.
ŸWhen any operational malfunction is found, and not resolved, disconnect the mains power supply and request the assistance of a qualified
technician (installer). When automation is out of order, activate the manual release to allow the opening and closing operations to be
carried out manually.
ŸGearbox drive unit is “sealed” for life and requires no further lubrication.
!
PF8000
As Pictured above use the “Emergency lower valve” to release the blocker. Please ensure you have
turned the power off!
When this procedure is complete put the valve back to its home position to allow for normal operation
when the blocker is turned back on.

Technical Data PF8000
The PF Rising Kerb Kerb is essentially a hinged Kerb rising above the road
surface to prevent unauthorised access. We manufacture all sizes from 2m up
to 5m but can double up to span roads up to 12m wide. We also offer a single
kerb with the attack face on both sides if required.
Our 3-phase motor driven hydraulic power pack, which is mounted within the
control cabinet, provides motive power for raising and lowering action. The
kerb is fitted with raise and lower limit proximity switches which cable back to
the control panel with the hydraulic hoses.
As all sites vary, the kerbs are controlled via a programmable logic controller,
which means its compatible with all types of access control and can be
operated to the customer’s exact specification.
Technical data
Construction – All welded steel RHS
Cover Plates – 6mm ‘Durbar’ plates
Drive – Remote hydraulic power pack
Finish – Galvanised with black/yellow chevrons
Electrical supply – 230v supply (inverter driven for 3 phase motor output)
Sizes = 2m – 5m
Control system – To suit site requirements (via a Schneider PLC (Zelio))
Hand operation – Lowering only as standard via pressure release valve
Power rating (Motor) 0.75kw - 3.0kw
Operating time 1.2 seconds - 8 seconds
Lifting height 340mm - 800mm
Max. Axle load 3 tonnes - 12 tonnes
Optional Extras
a) Traffic lights
b) Hand pump for emergency raising
Control Variations
a) Push buttons
b) Induction loops
c) Card reader
d) Coin acceptor
e) Coded keypad
f) Radio control
b) Zelio Software for Altering the PLC program is free to download online.

12 3 5678 9 10 11 12 13 14 15 16 17 18 19
4
COM
STOP
COM
LOWER
COM
RAISE
+
LOWER PROX
RAISE PROX
+
-
+
-
-
SPARE
RED
GREEN
-
EARTH
U
V
W
20 21 22 23 24
+
-
24V DCLOWER
SOLENOID
RAISE
SOLENOID
MOTOR
L
N
E
Wiring Diagram (Illustration)
PF8000

Programmable logic controller
The above diagram shows how to navigate through the menu system on the
PLC. This should only
be done by qualified or competent personnel.
Built in options on PLC
Time clock
7 Day, 24 hr time clock can be used to hold open the rising kerb at any time of
the day or night.
Useful for busy times of the day or night, when site access is constant.
Safety reverse
This option allows the user to choose whether or not you want the kerb to
reverse or stop on a
safety input being activated. E.g. on a vehicle breaking the safety loop, the
kerb will reverse if
option is switched on and will stop if set to off.
Close delay
This option allows the user to set a closing delay time upon vehicles leaving
the safety loop.
Auto raise
This option allows the user to set the kerb to rise on a timer if nobody drives
through the system.
Auto raise timer (A/rais/t in menu)
This option allows the timer to be set for the above auto raise.
Auto Loop Timeclock (tm/loop)
This option allows the user to set the auto loop (if used) to work on certain
times of the day.
Traffic Light Timer
This option allows the user to set the time taken when the kerb has fully
lowered for the green
light to come on.
Wiring/Programming Description PF8000

Wiring/Programming Description PF8000
Memo
refer t
Overv
Image
Outpu
traffic
Descr
Above i
that con
a custo
can be
become
goes in
Our sta
come w
out and
configu
corner o
For any
endeav
ory Card f
to manufa
view
e Of PLC
ut: Q4 is u
lights etc
ription
is a telemec
ntrols all of
mer has exp
rectified on
es too comp
nto the slot
ndard prog
with the opt
d 24/7 day/n
rations the
of this docu
y specific sit
vor to meet
P
for PLC o
acturer fo
(Programm
used for a
c
chanique Ze
f our blocker
pressed the
n site (over t
plicated we
shown abo
grams will be
tion of barri
night timers
n please ca
ument.
e requirem
your needs
PLC Guid
only to be
or details.
able Logic C
any acce
elio Program
rs. It contain
eir requirem
the phone)
may be ab
ve.
e safety/clo
er arm light
s. For expla
ll our servic
ents please
s.
de and Inf
e used if
.
Controller)
ssories e
mmable Log
ns a site spe
ments within
with the he
le to send y
ose, Safety O
ts, magneti
anations on
ce departme
e also conta
formation
upgrade
e.g. beaco
gic Controlle
ecific progra
n reason. Al
elp of our te
you out an e
Only and Sa
c locks, safe
any of the
ent on the n
ct our servi
n.
Software
ons,
er. This unit
am which w
ll units are s
echnical sta
eprom (mem
afety/Auto R
ety delays,
previously m
numbers in
ice departm
In
Ou
Q
Q
Q
Q
e required
t is the “com
will be issue
simple to us
aff. If the pr
mory card)
Reverse. Th
no passage
mentioned
the top lef
ment who w
nput
I1
I2
I3
I4
I5
IB S
IC
ID
IE
utput
Q1
Q2
Q3 Li
Q4 A
d,
mputer”
d once
se and
ogram
which
hese can
time
t hand
will
Item
Stop Circu
Raise
Lower
Raise Lim
Not Used
Safety Clo
Free Exi
Lower Lim
Not Used
Item
Up
Down
Boom
ight/Mag l
Accessori
uit
mit
d
ose
it
mit
d
lock
ies

Loop Detector Settings PF8000

Loop Detector Settings PF8000

Loop Detector Settings PF8000

Troubleshooting Guide (electrical) PF8000
Troubleshooting Guide (Mechanical)
Error
Cause
Correction
Kerb keeps going up
and down Limit switch fault Check and reset limit
switches
Kerb creaking Check turn buckle
Oil or grease turn buckle
Kerb motor not running Loss of voltage
Check motor supply;
test 3 phases
Kerb not raising or
lowering
Drive shaft connections
Re-connect drive shaft
Kerb raises slowly and
lowers too fast
Problem with hydraulic
valves
Check valves and
settings
The best way to approach any error is to take time, be thorough
and systematic in fault finding.
Before moving/adjusting any mechanics, ensure all power is
disconnected to avoid shock and or trapping body parts in moving
mechanics.

Error
Cause
Correction
Blank Screen on PLC
Door switch stop circuit
not making
Press door switch in and
check PLC screen
Both open and close
proximity switch
detecting
Check proximity
distances, check if both
lights are lit on proximity
switches. Check fuse on
24v supply
Kerb does not run (stays
open)
Check Inverter is in
ready mode on display
Power down then back
up
Check Inverter settings
ACC - 7.0
DEC – 4.0
LSP – 45.0
Photo cell alignment (if
fitted)
Check on PLC that [B] is
highlighted if not check
photo-cell alignment (a
small yellow light can be
seen on side of barrel if
making contact with
emitter, check 24DC
supply to emitters.
Photo Cells Dirty (if
fitted
Clean photo cells make
sure they are debris free
Motor running but Kerb
does not move Permanent open signal
Check PLC display, [2]
should not be
highlighted. If [2] is
highlighted Kerb has a
permanent open signal
Mains on but no power Isolator fuse Check and meter fuse in
isolator
Loop detector green
light on permanent Loop picking up steel Locate foreign body and
rectify
Green light flashing on
loop detector Loop detector fault Press button on front to
reset
The best way to approach any error is to take time, be thorough
and systematic in fault finding.
Before moving any wires ensure all power is disconnected to avoid
shock.
Troubleshooting Guide (electrical) PF8000

Hydraulic Oil Spec PF8000

Hydraulic Hose Specifacation PF8000

Installation/Commissioning Check List
System Operation - The user FULLY understands
YES
NO
How to operate the system with all control devices
How to isolate the power to the automation system
How to manually release the system in event of power failure
The safety rules and issues associated with your system
Safety devices on the system have been verified and checked
Safety devices and features suit the site/application for which it was designed
How to open the door on the equipment
Check the following items
YES
NO
Door keys have been handed over
Key switch keys have been handed over
All equipment and site has been left in a clean and safe state
Any warning signage has been fitted by Engineer/Client to make people aware
Any times and special programming instructions undertaken
Product works the way site need it to this includes “no passage time out” etc
System has had the completed conformity certificate
All items on the delivery note have been handed over to client/site -
this should be signed for on the separate sheet which is titled “Delivery Note” (green/ or yellow paper) if parts missing call supplier
The engineer has expressed the importance of regularly maintaining the equipment
POWER ISOLATION - The power isolator for your automation system is located at:
.....................................................................................................................................................
The following denotes that the above has been completed to a satisfactory standard. The engineer has explained the system of
operation to you and any devices that you have had fitted. If this is agreed and has been displayed please sign in the indicated
fields below. All information will be passed on correctly to other system users. The users of the system will use this system
correctly and safely.
Engineers Name: ........................................................................ Engineers Signature: ...........................................
Clients Name: ............................................................................. Clients Signature: .................................................
PF8000

Service Log
Date
Reason for visit/Action taken
Engineers Signature
/ /20
/ /20
/ /20
/ /20
/ /20
/ /20
/ /20
/ /20
/ /20
/ /20
/ /20
/ /20
/ /20
/ /20
/ /20
/ /20
/ /20
/ /20
/ /20
/ /20
/ /20
/ /20
/ /20
/ /20
This Manual must be completed in accordance with the guidelines below, at any point service/repair work is
carried out on the product. This is to achieve two things;
1. To keep a history of the product for yourself and your supplier/manufacturer.
2. To keep an accurate log of any historical or recent modifications, and/or problems, to help an engineer in
the event of any future work required on the product.
!
PF8000
Table of contents
Other Parking Facilities Control System manuals
Popular Control System manuals by other brands
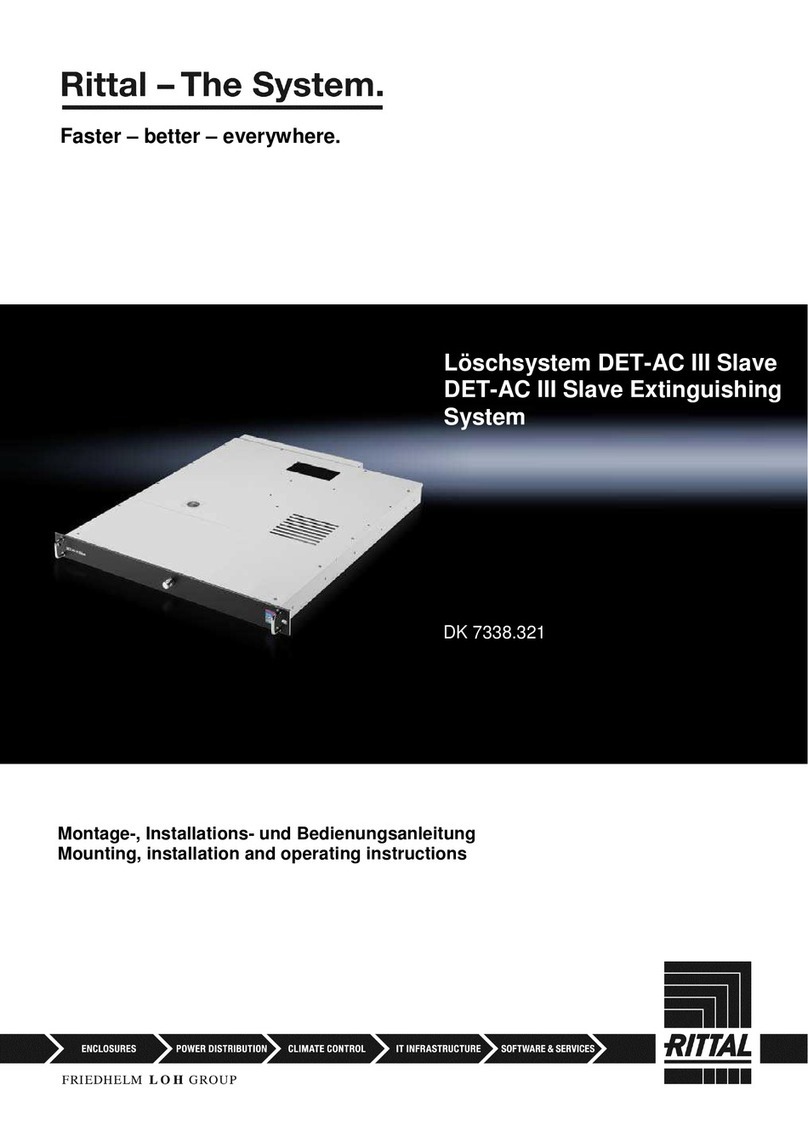
Rittal
Rittal DET-AC III Slave Mounting, installation and operating instructions
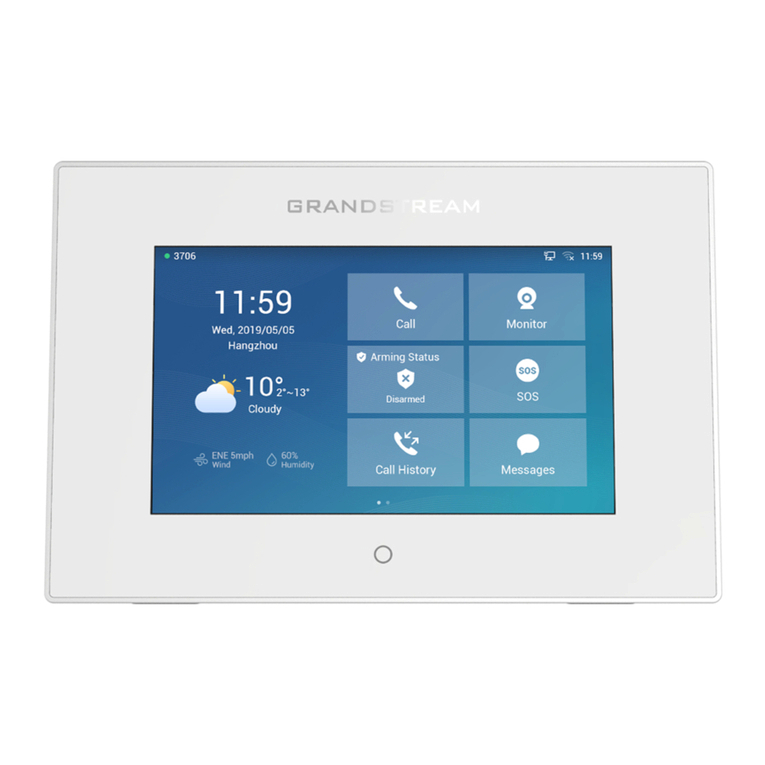
Grandstream Networks
Grandstream Networks GSC3570 Quick installation guide
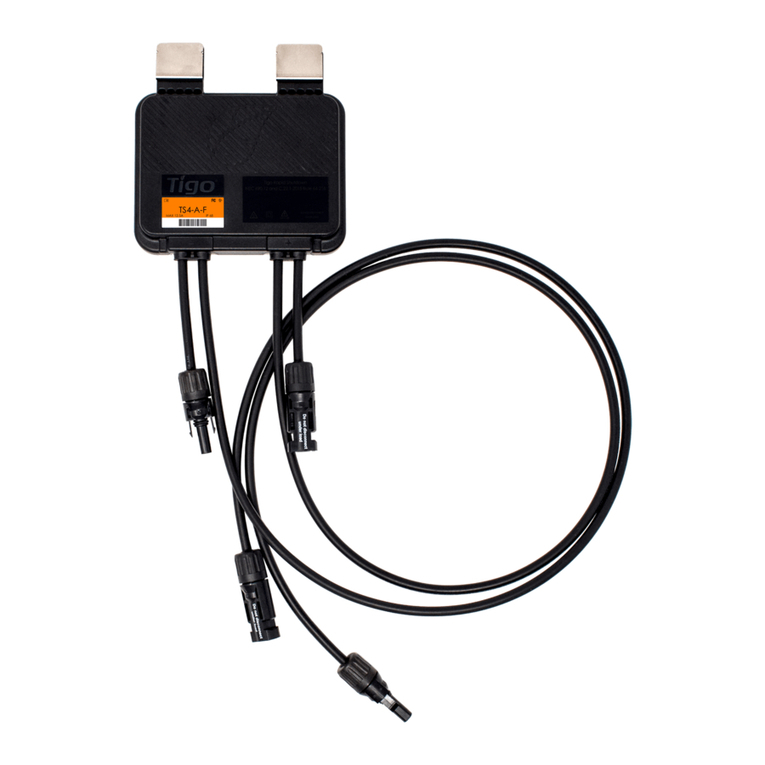
Tigo
Tigo TS4-A-F quick start guide
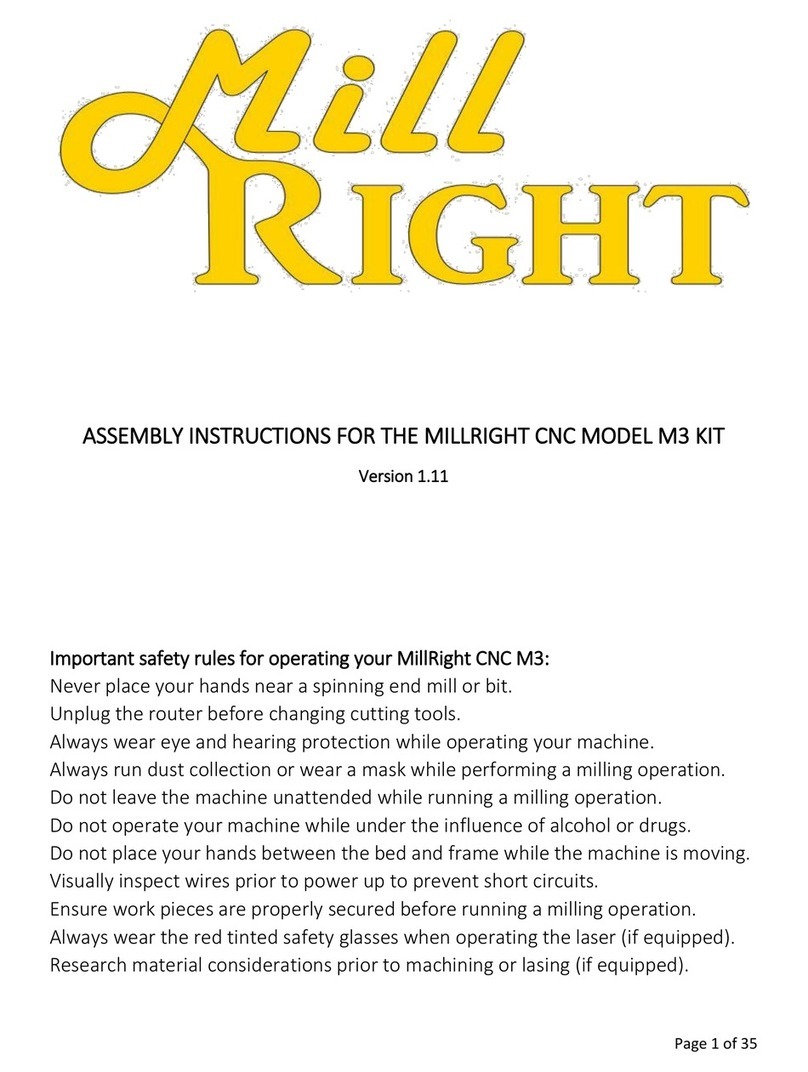
Mill-right
Mill-right M3 KIT Assembly instructions
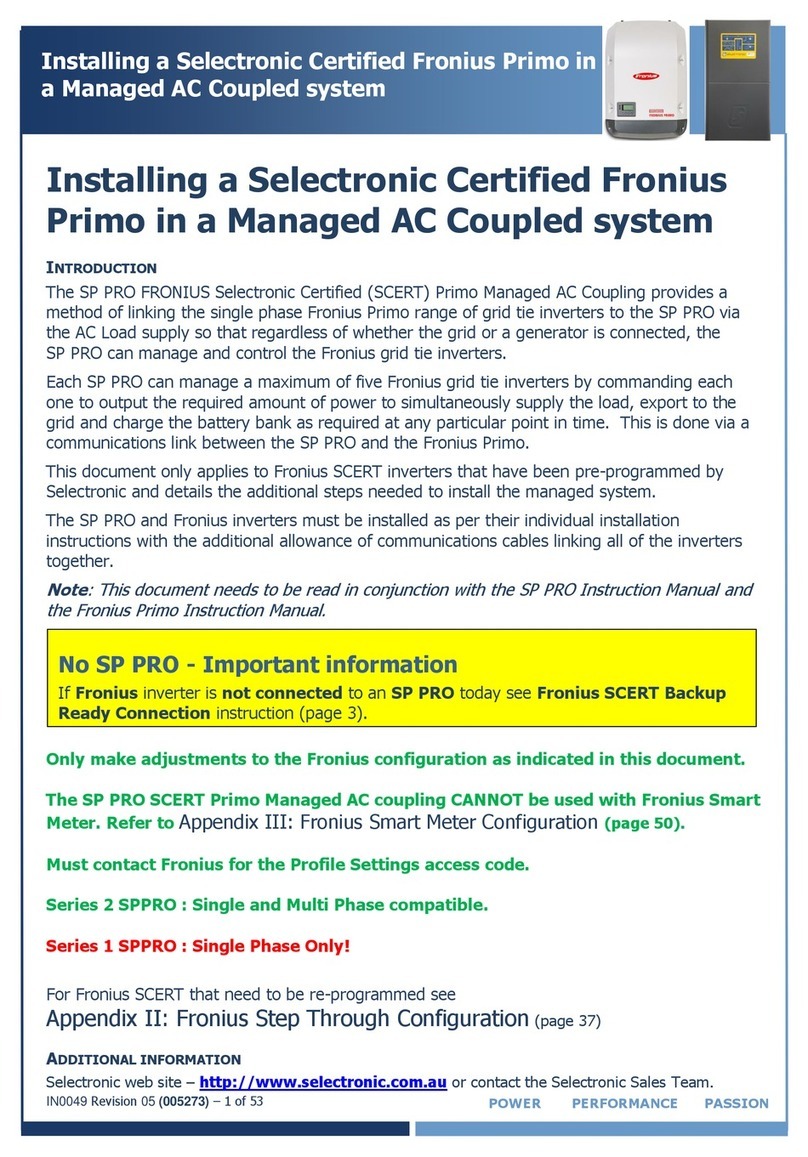
FRONIUS
FRONIUS SP PRO Series 1 instruction manual

Little Giant
Little Giant OA1S Series owner's manual
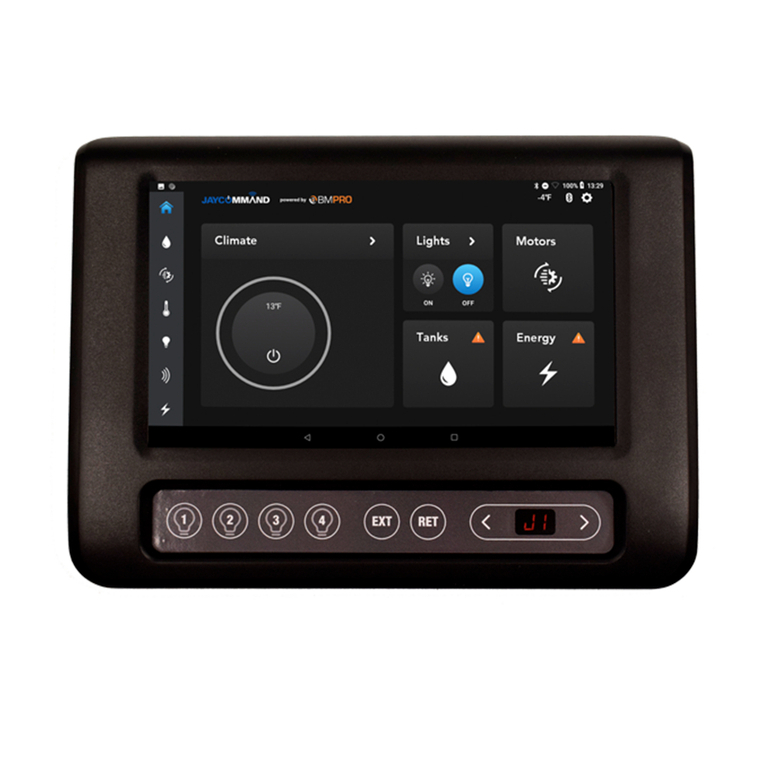
BM PRO
BM PRO JAYCOMMAND owner's manual
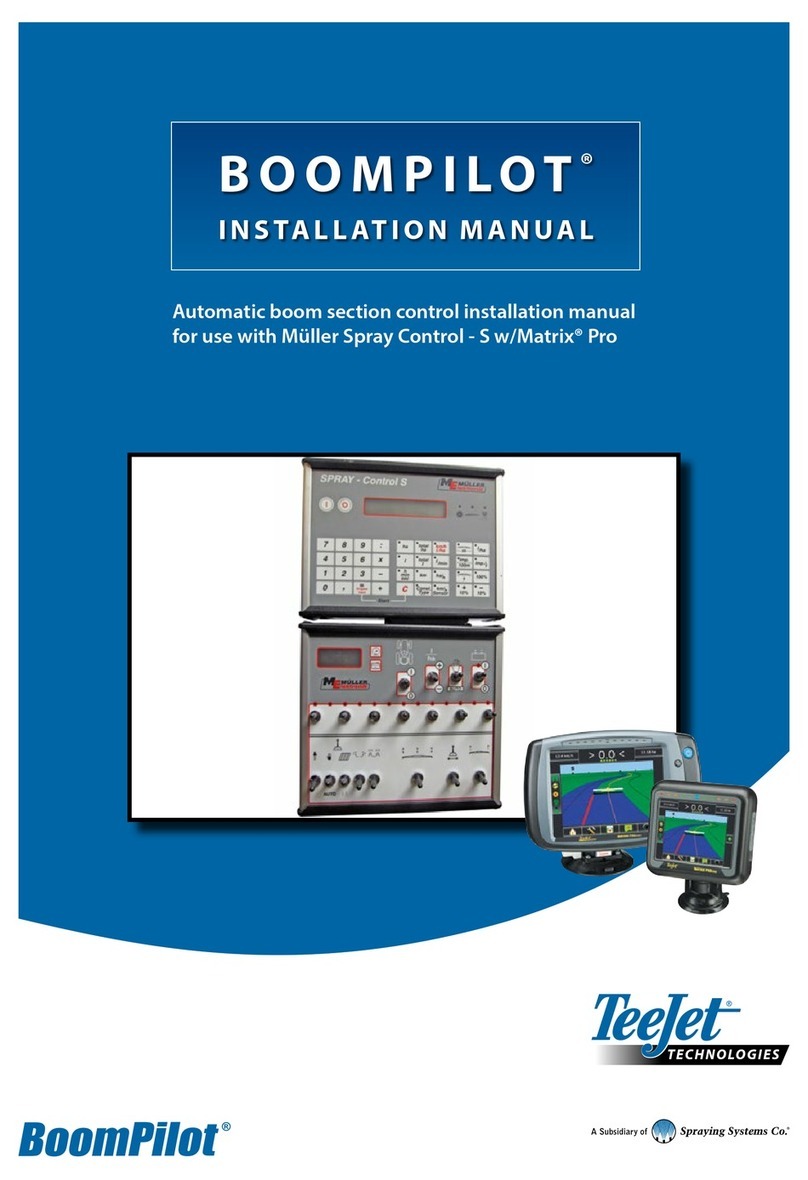
Spraying Systems
Spraying Systems TeeJet TECHNOLOGIES BoomPilot installation manual
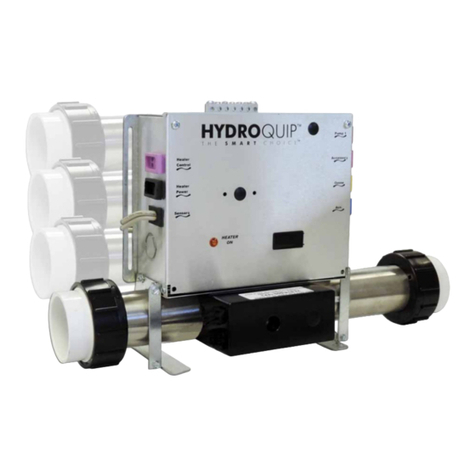
HydroQuip
HydroQuip 6500 Series Owner's operation guide
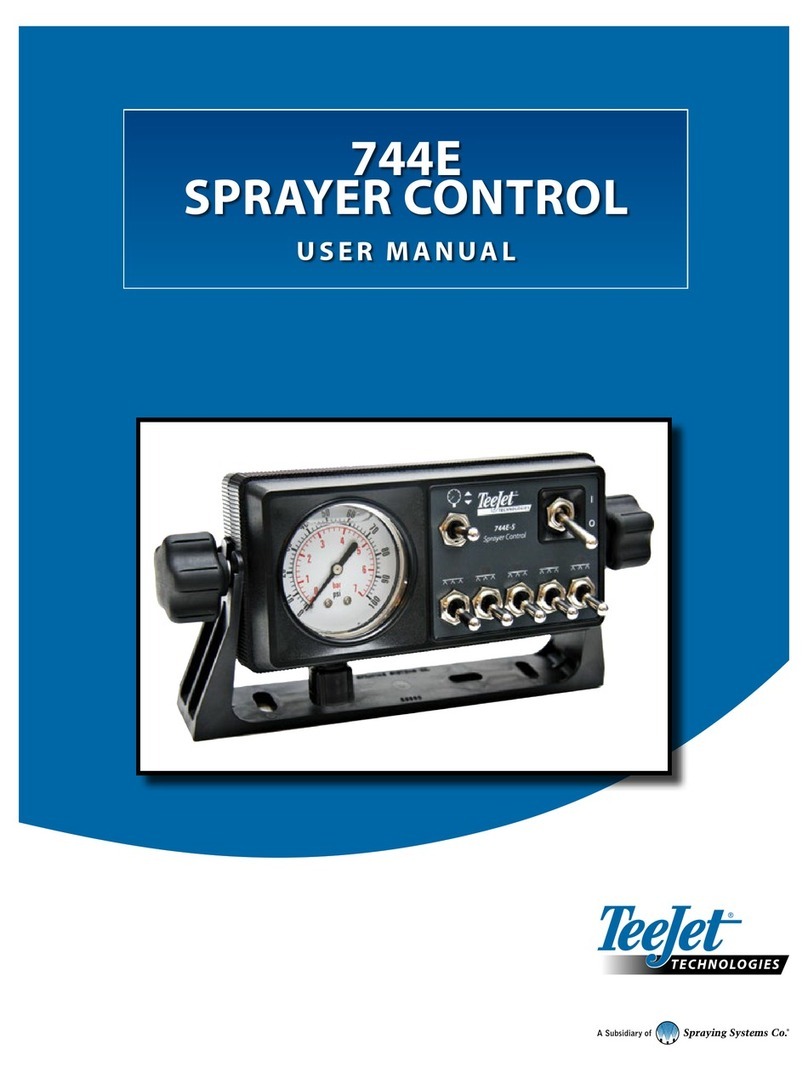
Spraying Systems
Spraying Systems TeeJet Technologies 744E user manual
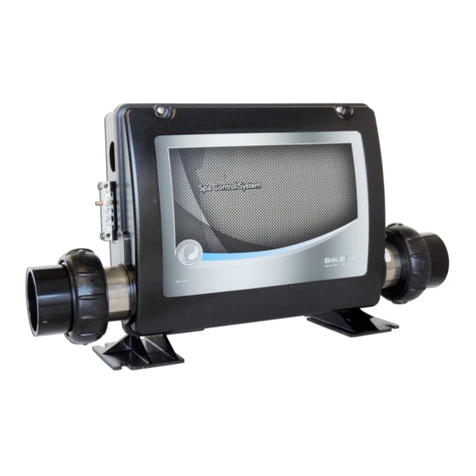
HydroQuip
HydroQuip BALBOA BP7 Series Installation & operation manual
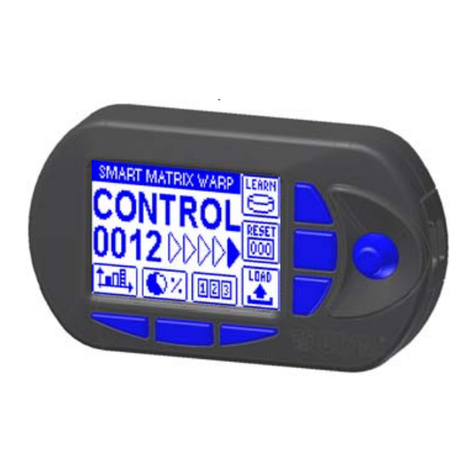
btsr
btsr SMART WARP operating manual