Paslode FNS-200 User manual

IMPORTANT
DO NOTDESTROY
It isthe customer'sresponsabilityto have all
operators and service personnelreand and
understand thismanual.
MODEL
FNS-200
OPERATINGMANUAL
Printed in Canada 12/14

PASLODE PNEUMATICTOOLFNS-200
The pneumatic flooring tool FNS-200 is a tool specially developed for the installation
standard 3/4" to 1/2" hardwood flooring. It has been designed for easy maintenance
where major components can be easily accessed. It makes the installation of hardwood
floor very easy, allowing the operator to set and fasten the boards in the standing
position.
The FNS-200 nailer/stapler takes both standard L-type 16GA flooring nails and ½"
crown 15½GA flooring staples.
Read these instructions carefullybefore operating the tool.It is importanttounderstand
warnings/cautions and the safetymeasures to ensure safe use of the tool.
Technical support, information & schematics can be found at www.paslode.ca
SAFETYMEASURES
These important guidelines should always be followed to worksafelywith the pneumatic
tool model FNS-200:
•Readtheseinstructionsthoroughlybeforeusingthistooland keepithandyforreference
ifnecessary.
•Alwayskeep hands, feet or other bodypartsawayfrom the fastener ejection area.
•Never aim the toolinanydirection other than the workingarea.
•Alwayscarryormanipulatethe toolbyitshandlewhilethe airsupplyhose isconnected.
•Neverhitthe head cap ofthe actuatorifthe plasticbase isnotsittingperfectlyon the
workingsurface.
•Neverleavethe toollayingdownon itsside whilethe airsupplyhose isconnected;the
toolshouldalwaysbe left on the floor, standingon itsplasticbase.
•Alwaysdisconnectthe airsupplyhose when the toolisnotinuse orwhen movingto
another workarea.
•Neverservice orrepairthe tool,clearobstructions ormakeadjustmentswhilethe air
supplyhose isconnected.
•Onlycompressed airshouldbe used topowerthistool;do notexceed 110 psi(7.6bar).
•Neveruse oxygen oranyothercompressed gas as apowersource forthistool.
Explosion mayoccur.
•Alwayswear OSHA-required Z-87 safetyglasses withside shields.
•Alwayswear proper ear and footsprotection whilethe air supplyhose isconnected.
•Alwaysremovefastenersfrom the magazine beforeservicingtool.

CONNECTION&AIRSUPPLY
Thistoolrequiresclean&dryair.Theuseofafilter and
apressure regulator is recommended.
Useadetachablemalecoupler with3/8"NPTmale
treads. The useofa3/8"(1 cm)diameter airsupply
hoseisrecommended.Asmallerhoseorahoselonger
than 50'(15 m)couldcauseapressure drop when the
toolis activated repeatedly.
Always useafree-flowconnection for the
compressed airsupplytoprevent that the
toolstays charged after disconnecting the air
supplyhose.
Unload toolbefore connecting airtoprevent
accidentaldischarge.
Toprevent injuryor accidentaldamage tothe
finished surfaceof the installed floor, rest the
toolontothe subflooring when connecting air,
moving tooltoadifferent work area, loading
the toolor performing anymaintenancetothe
tool.
Dirt, dust, and other particlesinthe airsupplycan
causesluggishoperation or premature wear.Drain
water fromthe compressor tankregularly.The
compressorstart-stoplimitsshouldbe settodeliver an
airpressure ofatleast 100 psi(7 bar) atall times.
Consultthe compressor manualor dealer for
instructions on howtomakethis adjustment.
Thistoolisdesignedtobe operated withacompressed
airpressure of80 to100 psi(5.5-7.0bar).Airpressure
of90 psi(6.2bar) isadequatefor most situations,
although occasionally,ahigher pressure couldbe
necessary.Never notuseacompressed airpressure
higher than 110 psi(7.6bar).
PREVENTIVE MAINTENANCE
This tool requiresminimal lubrication.Use
only detergent-free oil suchasthe
Paslode Pneumatic Lubricating Oil.Few
dropsofoil weekly in the air inlet is sufficient.
Other typesoflubricantmay degrade the
seals.
Checkperiodicallytomakesure thatthe head
assemblyisfullyscrewedontothe mainbody.Aloosen
head will damage the tool.
LOADING THE TOOL
Thistoolcan be used witheither standard 16ga
flooring cleats or with15½ga flooring staples:
•L-type 16GA nailsinlengthsof1½"(38 mm),1¾"
(45 mm)or 2" (50 mm)
•½" crown15½GA staples inlengths of 1½" (38 mm),
1¾" (45 mm)or 2" (50 mm)
Useonlythe type of fasteners identified on
the magazine. The useof anyother type of
fasteners will damage the tool.
Loading the toolwithflooring staples:
•Press the lock and open the magazine cover.
•Insertone or twostripsofflooring staplesover the
centralguide ofthe magazine asillustrated below
(left).
•Pushthe magazine cover forward intoits locked
position.
Loading the toolwithL-type 16GA flooring nails:
•Press the lock and open the magazine cover.
•Placeastripofflooring cleats against the inner side
ofthe magazine,the “L” head ofthe cleats engaging
thegrooveasillustrated below(right).Small magnets
will holdit inplace.
•Pushthe magazine cover forward intoits locked
position.
Unloading cleats or staples
•Toremovefastener fromthe magazine,press the
lock and open the magazine cover
•Tiltthe tooltoslide back remaining fastener and take
themout.
Always operatethe toolwithfasteners in
magazine. Damage mayoccur if the toolis
operated without fasteners.

OPERATION
Unload tool and rest it ontothe subflooring,Connect
thehoseand cycle toolonceortwicewithoutfasteners.
After loadingthe tool, the FNS-200 nailer/stapleris
ready for use.
Useonly the hammer suppliedwiththe tool. Theuseof
other type ofhammersmayaffect performance.The
rubber faceofthe hammer can be used withcare to
help positionthe boards.
Withthe flooringfirmly inplace,positionthe tool onto
the flooringand apply downwardpressure toensure
proper seatingofthe fastener.Strikethe head cap with
the hammer toactivatethe tool, Use onlythe RUBBER
FACE of the hammerto activate the tool.Using the
steelend will damage the tool and void the
warranty. Ifwood isslightlytwisted,hittingthetoolwith
more forcewill assistin pullingthe board up snugly.
NEVER strikethe head cap when the tool isnotsitting
on the workingsurface.
Before starting an installation, fasten down
fewboards toascertainthat the toolis
properlyadjusted. Always complywithall
manufacturers recommendations.
DISASSEMBLING THE TOOL
Allpneumaticcomponentscanbeeasilyaccessedwith
the useofan Allen key.Thissection describes howto
disassemblethetooltoaccessitsinternalcomponents.
Toaccess valveand piston assemblies:
•Removethe 4screws and takeoff the head.
•Pull outthe valveassembly.Inspect wear ring &
lubricate.Do notattempttodisassemblethe valve
assembly.
•Pull outthe piston assembly.Inspect wear ringand
lubricate.
It isusuallynotnecessarytopull-outthe bumper for
maintenance. Toreplacethe bumper:
•Removethe4screwsandtakeoffthebase/magazine
assembly.
•Pull out and replacethe bumper.
MAINTENANCE &REPAIR
Most maintenancetothe toolcan be made withthe
5mm Allen wrenchsupplied withthe tool.
Disassemblyofthe toolmust be done inaclean
environment. Somepartscan be easilydamaged if
disassembled withimproper toolsor byinadequate
methods. Maintenanceshouldonlybe performed by
trained personnel.Useonlygenuine Primatech
replacement parts.
Toprevent injury, ALWAYS disconnect the
airsupplyhosewhen servicing or
disassembling the tool.
When servicing the tool,donottwistorforceanyparts.
Damagemayresultfromsuchabuse.Contact your
Primatechdistributor for more information.
When opening the toolfor maintenance, always clean
allcomponentsofdirt,grit, or particles. Inspect the tool
carefullyforbroken parts or excessivewear,and
replaceifnecessary.When ordering parts, be sure to
specify the rightpartnumber,aswell asthe toolserial
number.
After anymaintenancetothe tool, REMOVE
ALL Fasteners before connecting airand
actuatethe toolrepeatedlyover apieceof
wood or subflooring toinsure proper
operation.
CLEANING THE VALVE
If the toolbecomessluggishor doesnotsetthe
fastener correctly, it mayindicateexcessivedirt, dust,
other particles, or even water,inthe tool.The first step
introubleshooting is toclean up the head assembly.
•Disassemblethe head assemblyasdescribed in
previous section.
•Performavisualinspection ofthe valveassembly.
Ensure thatthe actuator issliding easily.Clean and
lubricatelightly.Donotattempttotakeapartthe
actuator assembly.
•Clean the inside wall ofthe head and lubricatelightly
withanon-detergentoil.Insertthe valveassembly
intothe head and ensure that it is sliding easily.
•Ensure the piston assemblyissliding easilyintothe
cylinder.It shouldoffer someresistance,butifit
movestoo easily,itmaybe required toreplacethe
piston wear-ring.

ASSEMBLING THE TOOL
Thissection describeshowtore-assemblethe tool
after maintenance.The following procedure assumes
that the base/magazine is alreadyinstalled.
•Insertthe piston assemblyintothe tooland engage
the driving blade thru the opening ofgate/foot
assemblyguiding channel.
•Insert the valveassemblyintothe head.
•Inspect the head gasket; replaceifnecessary.Place
the gasketintothe grooveon the head flange.Some
oil or greasewillhelptokeep itinplaceduring
assembly.
•Insertthehead assemblyontothe body,makingsure
that the gasket stays inplace. Screwinplace.
After reassembly, always actuatethe tool
repeatedlyWITHOUTFASTENERS against
apieceof wood toinsure proper operation.

TROUBLESHOOTING
TO PREVENTINJURY,ALWAYS
DISCONNECT THE AIR SUPPLY HOSE
WHEN ADJUSTING,SERVICING OR
DISASSEMBLING THE TOOL.
FIRST:CHECK THE COMPRESSED AIR SUPPLY
Manyofproblemscomefromafaultyor inadequate
compressed airsupply system.Before attempting to
repairthe tool,the following points shouldbe
checked:
•Checkthepressureattheoutputofthecompressor;
adjust to80-100 psi(5.5-7.0bar) as required.
•Checkthe tankpressureofthecompressor&adjust
the start/stop limits.
•Check the airdeliverysystem;a3/8"hoseis
recommended.
•Usefewer tools simultaneously;do not exceed the
capacityofthe compressor or ofthe delivery
system.
•Drainwater fromthe compressor.
SECOND:CHECK FOR AIR LEAKS
At rest, thistoolshouldnothaveanyairleaks. Before
attempting torepairthe tooland replaceparts, check
the following:
•Check all sealsinhead,valveand piston
assemblies; replaceif necessary.
•Check the top edge ofmaincylinder for burrsor
dents.
•Clean &lubricatethe head and valveassemblies;
re-assemblethe head assemblycarefully.
•Check the interior of the head for scratches.
SUPPORT
Paslode warrants that newly purchased power
fastening tools, parts and accessories will be free from
defects in material and workmanship (excluding wear
parts) for the period shown below, after the date of
delivery to the original user.
90-DAY LIMITED WARRANTY will apply to all parts,
except those which are specifically covered by an
extended warranty.
EXTENDED LIMITED WARRANTY FOR ON SITE
CONSTRUCTION APPLICATIONS. A one year
warranty will apply to all housing and cap assembly
casings.
NORMAL WEARING PARTS. The following parts are
considered normal wearing parts and are not under
warranty:
•bumper
•driving blade
•o-rings & piston ring
WARRANTYSTATEMENT
Paslode’s sole liability hereunder will be to replace any
part of accessory which proves to be defective within
the specific time period. Any replacement part or
accessories provided in accordance with this warranty
will carry a warranty for the balance of the period of
warranty applicable to the part it replaces.
This warranty is void as to any tool which has been
subjected to misuse, abuse, accidental or intentional
damage, used with fasteners not meeting Paslode
specification, size or quality, improperly maintained,
repaired with other than genuine Paslode replacement
parts, damaged in transit or handling, or which, in
Paslode’s opinion, has been altered or repaired in a
way that affects or detracts from the performance of
the tool.
PASLODE MAKES NO WARRANTY, EXPRESSED
OR IMPLIED, RELATING TO MERCHANTABILITY,
FITNESS, OR OTHERWISE, EXCEPT AS STATED
ABOVE, and Paslode’s liability AS STATED ABOVE
AND AS ASSUMED ABOVE is in lieu of all other
warranties arising out of, or in connection with, the use
and performance of the tool, except to the extent
otherwise provided for by applicable law.
PASLODE SHALL IN NO EVENT BE LIABLE FOR
ANY DIRECT, INDIRECT, OR CONSEQUENTIAL
DAMAGES WHICH MAY ARISE FROM LOSS OF
ANTICIPATED PROFITS OR PRODUCTION,
SPOILAGE OF MATERIALS, INCREASED COST OF
OPERATION, OR OTHERWISE.
TOOL WARRANTY AND LIMITATIONS
For more information or support, please contact our
customer service support at:
https://paslode.ca/contact-us/
Table of contents
Other Paslode Tools manuals
Popular Tools manuals by other brands
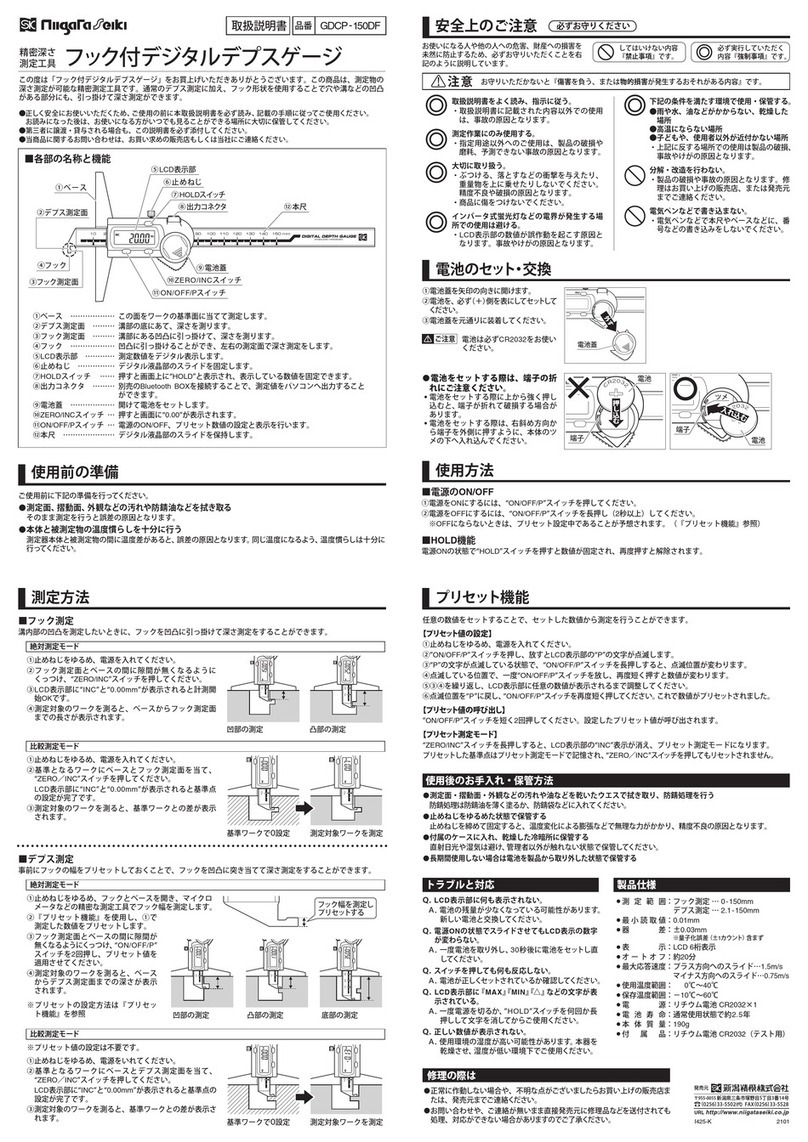
Niigata seiki
Niigata seiki GDCP-150DF instruction manual
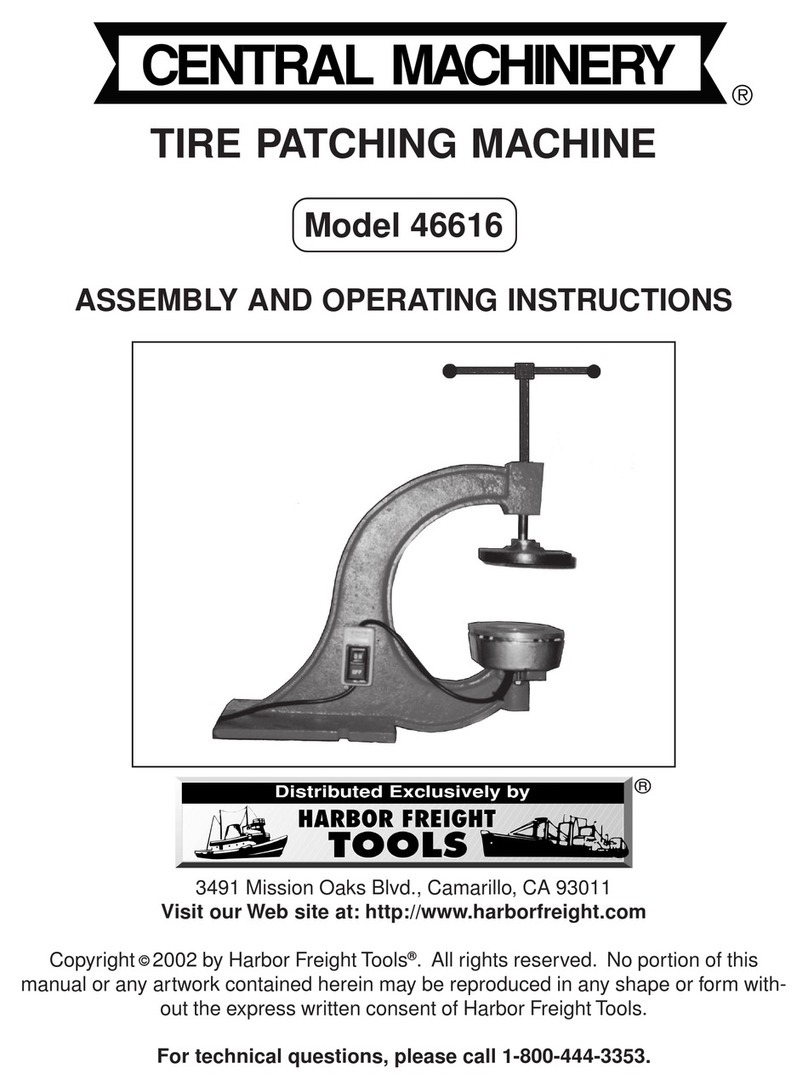
Central Machinery
Central Machinery 46616 Assembly and operating instructions
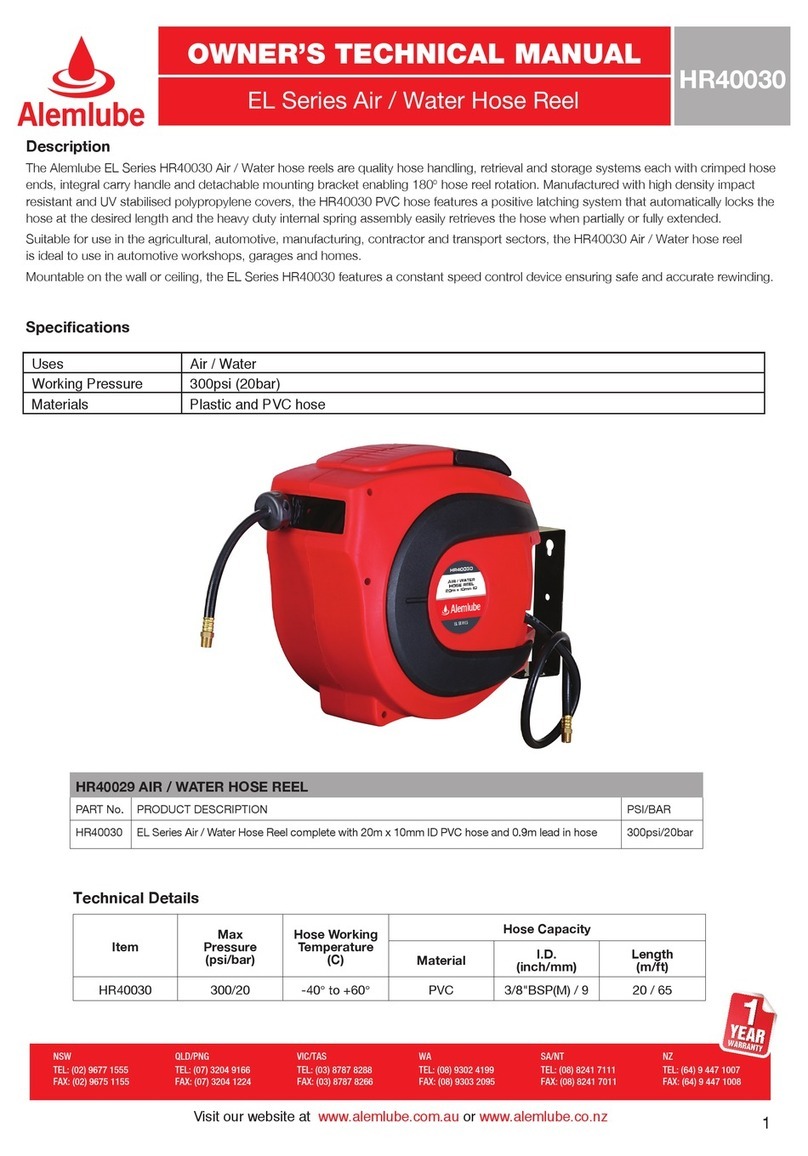
Alemlube
Alemlube EL SERIES owner's manual
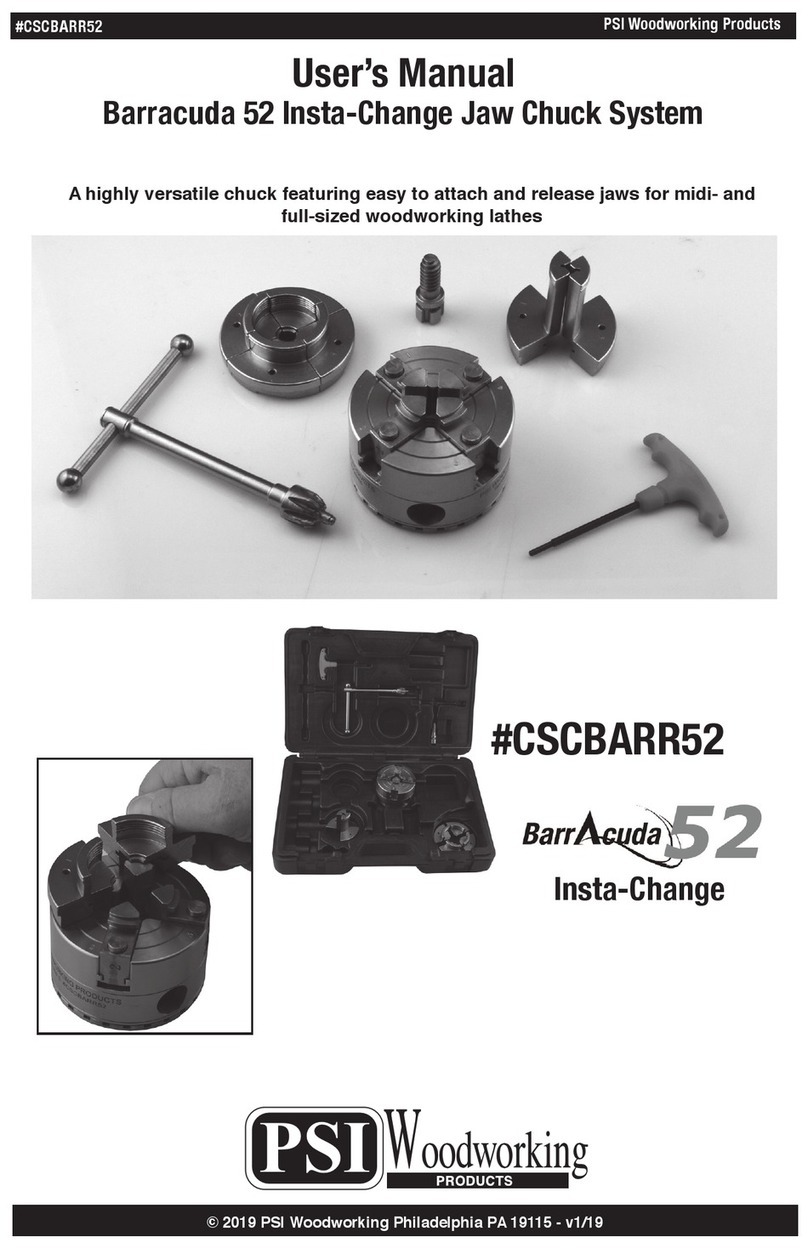
PSI Woodworking Products
PSI Woodworking Products Barracuda 52 user manual
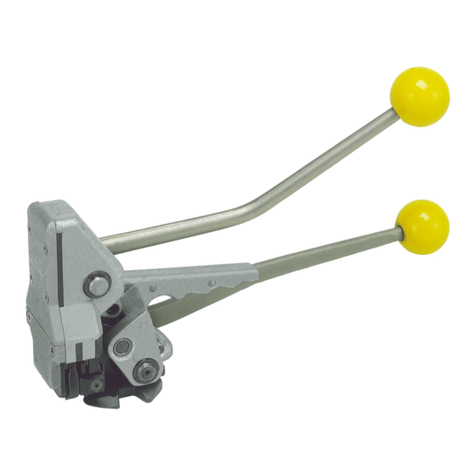
Fromm
Fromm A431 Operation manual & spare parts list
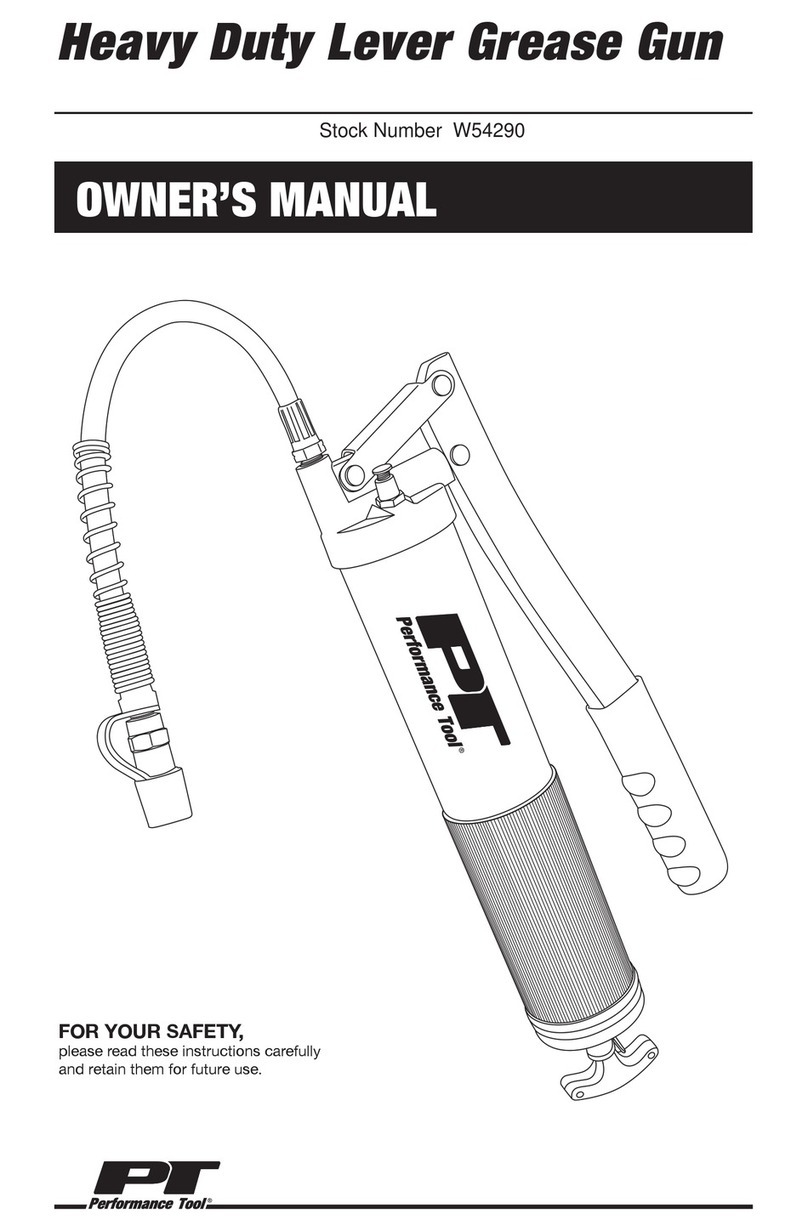
Performance Tool
Performance Tool W54290 owner's manual