PCB Piezotronics IMI Sensors 080A128 User manual

Model 080A128
Spotface tool, 1.25" diameter, with a drill bit for a 1/4-28 tap (tap not included)
Installation and Operating Manual
For assistance with the operation of this product,
contact the PCB Piezotronics, Inc.
Toll-free: 800-959-4464
24-hour SensorLine: 716-684-0001
Fax: 716-684-3823
E-mail: [email protected]
Web: www.imi-sensors.com

Manual 21354 Rev E
ECN 50523
Repair and Maintenance
PCB guarantees Total Customer Satisfaction through its
“Lifetime Warranty Plus” on all Platinum Stock Products
sold by PCB and through its limited warranties on all other
PCB Stock, Standard and Special products. Due to the
sophisticated nature of our sensors and associated
instrumentation, field servicing and repair is not
recommended and, if attempted, will void the factory
warranty.
Beyond routine calibration and battery replacements
where applicable, our products require no user
maintenance. Clean electrical connectors, housings, and
mounting surfaces with solutions and techniques that will
not harm the material of construction. Observe caution
when using liquids near devices that are not hermetically
sealed. Such devices should only be wiped with a
dampened cloth—never saturated or submerged.
In the event that equipment becomes damaged or ceases
to operate, our Application Engineers are here to support
your troubleshooting efforts 24 hours a day, 7 days a
week. Call or email with model and serial number as well
as a brief description of the problem.
Calibration
Routine calibration of sensors and associated
instrumentation is necessary to maintain measurement
accuracy. We recommend calibrating on an annual basis,
after exposure to any extreme environmental influence,
or prior to any critical test.
PCB Piezotronics is an ISO-9001 certified company whose
calibration services are accredited by A2LA to ISO/IEC
17025, with full traceability to SI through N.I.S.T. In
addition to our standard calibration services, we also offer
specialized tests, including: sensitivity at elevated or
cryogenic temperatures, phase response, extended high
or low frequency response, extended range, leak testing,
hydrostatic pressure testing, and others. For more
information, contact your local PCB Piezotronics
distributor, sales representative, or factory customer
service representative.
Returning Equipment
If factory repair is required, our representatives will
provide you with a Return Material Authorization (RMA)
number, which we use to reference any information you
have already provided and expedite the repair process.
This number should be clearly marked on the outside of
all returned package(s) and on any packing list(s)
accompanying the shipment.
Contact Information
PCB Piezotronics, Inc.
3425 Walden Ave.
Depew, NY14043 USA
Toll-free: (800) 828-8840
24-hour SensorLine: (716) 684-0001
Repair inquiries: rma@pcb.com
For a complete list of distributors, global offices and sales
representatives, visit our website, www.pcb.com.
Safety Considerations
This product is intended for use by qualified personnel
who recognize shock hazards and are familiar with the
precautions required to avoid injury. While our equipment
is designed with user safety in mind, the protection
provided by the equipment may be impaired if equipment
is used in a manner not specified by this manual.
Discontinue use and contact our 24-Hour Sensorline if:
Assistance is needed to safely operate equipment
Damage is visible or suspected
Equipment fails or malfunctions
For complete equipment ratings, refer to the enclosed
specification sheet for your product.
Definition of Terms and Symbols
The following symbols may be used in this manual:
DANGER
Indicates an immediate hazardous
situation, which, if not avoided, may
result in death or serious injury.

Manual 21354 Rev E
ECN 50523
CAUTION
Refers to hazards that could damage
the instrument.
NOTE
Indicates tips, recommendations and
important information. The notes
simplify processes and contain
additional information on particular
operating steps.
The following symbols may be found on the equipment
described in this manual:
This symbol on the unit indicates that
high voltage may be present. Use
standard safety precautions to avoid
personal contact with this voltage.
This symbol on the unit indicates that
the user should refer to the operating
instructions located in the manual.
This symbol indicates safety, earth
ground.

Manual 21354 Rev E
ECN 50523
PCB工业监视和测量设备 - 中国RoHS2公布表
PCB Industrial Monitoring and Measuring Equipment - China RoHS 2 Disclosure Table
部件名称
有害物质
铅(Pb)
汞
(Hg)
镉
(Cd)
六价铬(Cr(VI))
多溴联苯 (PBB)
多溴二苯醚(PBDE)
住房
O
O
O
O
O
O
PCB板
X
O
O
O
O
O
电气连接器
O
O
O
O
O
O
压电晶体
X
O
O
O
O
O
环氧
O
O
O
O
O
O
铁氟龙
O
O
O
O
O
O
电子
O
O
O
O
O
O
厚膜基板
O
O
X
O
O
O
电线
O
O
O
O
O
O
电缆
X
O
O
O
O
O
塑料
O
O
O
O
O
O
焊接
X
O
O
O
O
O
铜合金/黄铜
X
O
O
O
O
O
本表格依据 SJ/T 11364 的规定编制。
O:表示该有害物质在该部件所有均质材料中的含量均在 GB/T 26572 规定的限量要求以下。
X:表示该有害物质至少在该部件的某一均质材料中的含量超出 GB/T 26572 规定的限量要求。
铅是欧洲RoHS指令2011/65/ EU附件三和附件四目前由于允许的豁免。
CHINA RoHS COMPLIANCE

Manual 21354 Rev E
ECN 50523
Component Name
Hazardous Substances
Lead (Pb)
Mercury (Hg)
Cadmium (Cd)
Chromium VI
Compounds
(Cr(VI))
Polybrominated
Biphenyls (PBB)
Polybrominated
Diphenyl Ethers
(PBDE)
Housing
O
O
O
O
O
O
PCB Board
X
O
O
O
O
O
Electrical Connectors
O
O
O
O
O
O
Piezoelectric Crystals
X
O
O
O
O
O
Epoxy
O
O
O
O
O
O
Teflon
O
O
O
O
O
O
Electronics
O
O
O
O
O
O
Thick Film Substrate
O
O
X
O
O
O
Wires
O
O
O
O
O
O
Cables
X
O
O
O
O
O
Plastic
O
O
O
O
O
O
Solder
X
O
O
O
O
O
Copper Alloy/Brass
X
O
O
O
O
O
This table is prepared in accordance with the provisions of SJ/T 11364.
O: Indicates that said hazardous substance contained in all of the homogeneous materials for this part is below the limit
requirement of GB/T 26572.
X: Indicates that said hazardous substance contained in at least one of the homogeneous materials for this part is above the limit
requirement of GB/T 26572.
Lead is present due to allowed exemption in Annex III or Annex IV of the European RoHS Directive 2011/65/EU.

INDUSTRIAL MONITORING INSTRUMENTATION DIVISION
SENSORS AND INSTRUMENTATION FOR MACHINE CONDITION MONITORING
Spot Face Tool User Instructions
Operating Guide with Enclosed Warranty Information
3425 Walden Avenue, Depew, New York 14043-2495
Phone (716) 684-0003
Fax (716) 684-3823
Toll Free Line 1-800-959-4IMI
MANUAL NUMBER: 18671
MANUAL REVISION: A

INDUSTRIAL MONITORING INSTRUMENTATION DIVISION
PAGE 2
SENSORS AND INSTRUMENTATION FOR MACHINE CONDITION MONITORING
table of contents
Introduction....................................................................................................................... page 3
Installation ........................................................................................................................ page 3
Operation..................................................................................................................... pages 3-4
Tool Maintenance............................................................................................................. page 4
Spot Face Tool Illustration................................................................................................ page 5
return procedure/customer service
Return Procedure ............................................................................................................. page 6
Customer Service............................................................................................................. page 6

INDUSTRIAL MONITORING INSTRUMENTATION DIVISION
PAGE 3
SENSORS AND INSTRUMENTATION FOR MACHINE CONDITION MONITORING
introduction
Spot face tools are used to create a flat circular surface to mount an accelerometer. Each
model has an installed center drill that is the correct tap drill for tapping a ¼-28 UNF-2B thread.
installation
Obtain a hand drill motor and install the shank end of the spot face tool into the chuck of the
drill motor. Tighten the chuck and check the direction of rotation. The rotation should be
counter clockwise when looking at the chuck end of the drill motor.
operation
Choose the area on the surface where the accelerometer is to be installed. Using a center
punch, mark the spot of the center of the accelerometer. Apply a small amount of light oil to
the surface to be used as a cutting fluid.
Apply the point of the center drill on the spot face tool to the center punch mark, grip the drill
motor firmly and begin drilling.
The drill motor should be kept as perpendicular to the axis that is going to be measured as
possible. Often on castings and molded parts the axis is not necessarily perpendicular to the
surface being prepared. A cross-check or torpedo level is very helpful in determining
perpendicularity.
The revolution speed of the drill motor should be kept between 150 and 350 RPM to optimize
the life of the tool. Allow the tool to do the cutting. Do not apply excessive pressure while
drilling, this will accelerate tool wear. The addition of a lubricant or cutting fluid during the
cutting process will also greatly increase tool life.

INDUSTRIAL MONITORING INSTRUMENTATION DIVISION
PAGE 4
SENSORS AND INSTRUMENTATION FOR MACHINE CONDITION MONITORING
operation continued . . .
The depth of the cut is determined by the perpendicularity of the surface to the axis being
measured. Remove enough material so that the entire bottom surface of the accelerometer is
in contact with the spot face. The maximum depth of cut should not exceed .040”.
The position of the center drill in the spot face tool can also be adjusted for different drill depths
to accommodate for the wall thickness and the material of the unit to be monitored.
tool maintenance
After extended use the spot face tools may wear and become dull. The tool can be sharpened
using standard sharpening techniques. Refer to your local machine shop for sharpening.

INDUSTRIAL MONITORING INSTRUMENTATION DIVISION
PAGE 5
SENSORS AND INSTRUMENTATION FOR MACHINE CONDITION MONITORING

INDUSTRIAL MONITORING INSTRUMENTATION DIVISION
PAGE 6
SENSORS AND INSTRUMENTATION FOR MACHINE CONDITION MONITORING
return procedure
To expedite returned instrumentation, contact a factory IMI applications engineer for a RETURN
MATERIAL AUTHORIZATION (RMA) NUMBER. Please have information available such as model and
serial number. Also, to insure efficient service, provide a written description of the symptoms and
problems with the equipment to a local sales representative or distributor, or contact IMI if none are
located in your area.
Customers outside the U.S. should consult their local IMI distributor for information on returning
equipment. For exceptions, please contact the International Sales department at IMI to request
shipping instructions and an RMA. For assistance, please call (716) 684-0003, or fax us at (716) 684-
www.pcb.com.
customer service
IMI, a division of PCB Piezotronics, guarantees Total Customer Satisfaction. If, at any time, for any
reason, you are not completely satisfied with any IMI product, IMI will repair, replace, or exchange it at
no charge. You may also choose, within the warranty period, to have your purchase price refunded.
IMI offers to all customers, at no charge, 24-hour phone support. This service makes product or
application support available to our customers, day or night, seven days a week. When unforeseen
problems or emergency situations arise, call the IMI Hot Line at (716) 684-0003, and an application
specialist will assist you.
3425 Walden Avenue, Depew, NY 14043-2495
Phone: (716) 684-0003
•
USA Fax: (716) 684-3823
•
INTL Fax: (716) 684-4703
ICP ® is a registered trademark of PCB Piezotronics, Incorporated,
which uniquely identifies PCB sensors that incorporate built-in microelectronics.
Table of contents
Other PCB Piezotronics Tools manuals
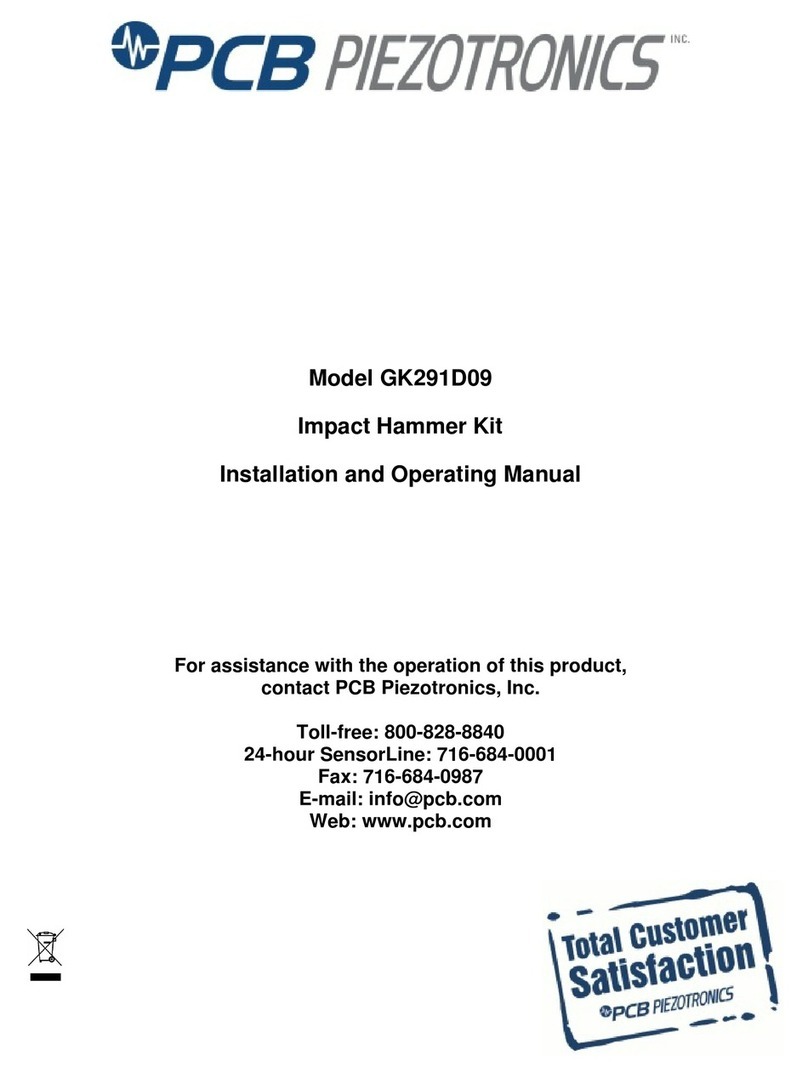
PCB Piezotronics
PCB Piezotronics GK291D09 User manual

PCB Piezotronics
PCB Piezotronics GK291D04 User manual
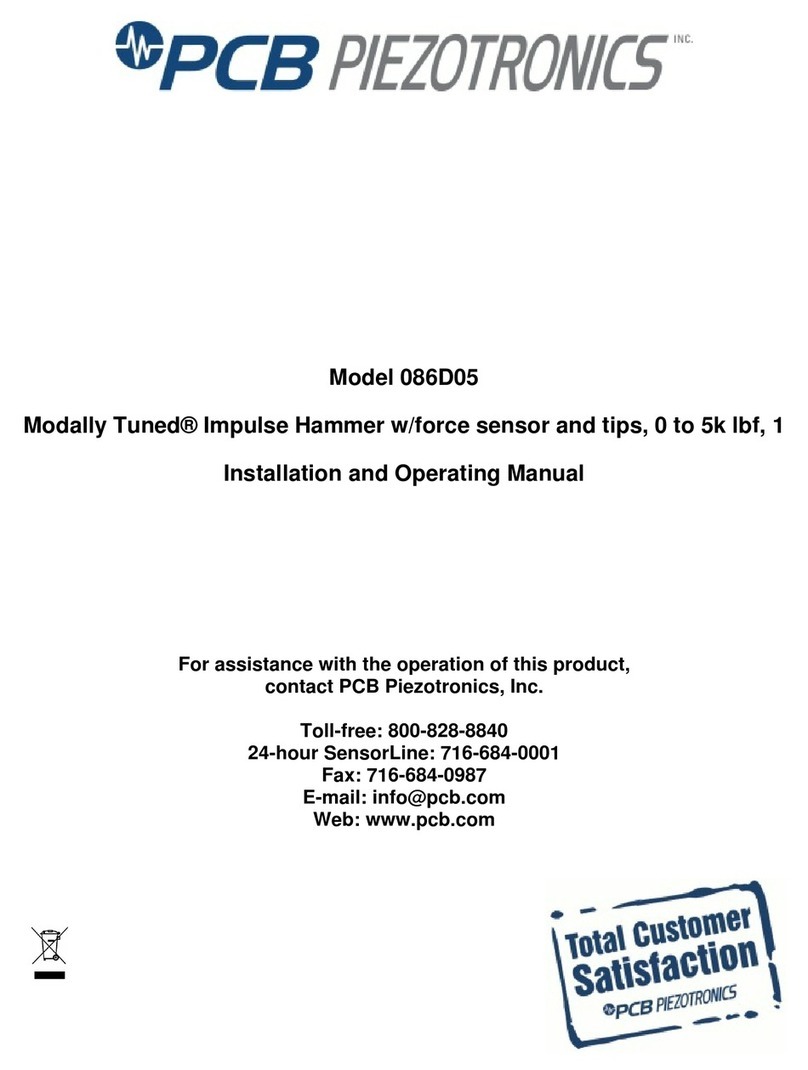
PCB Piezotronics
PCB Piezotronics 086D05 User manual
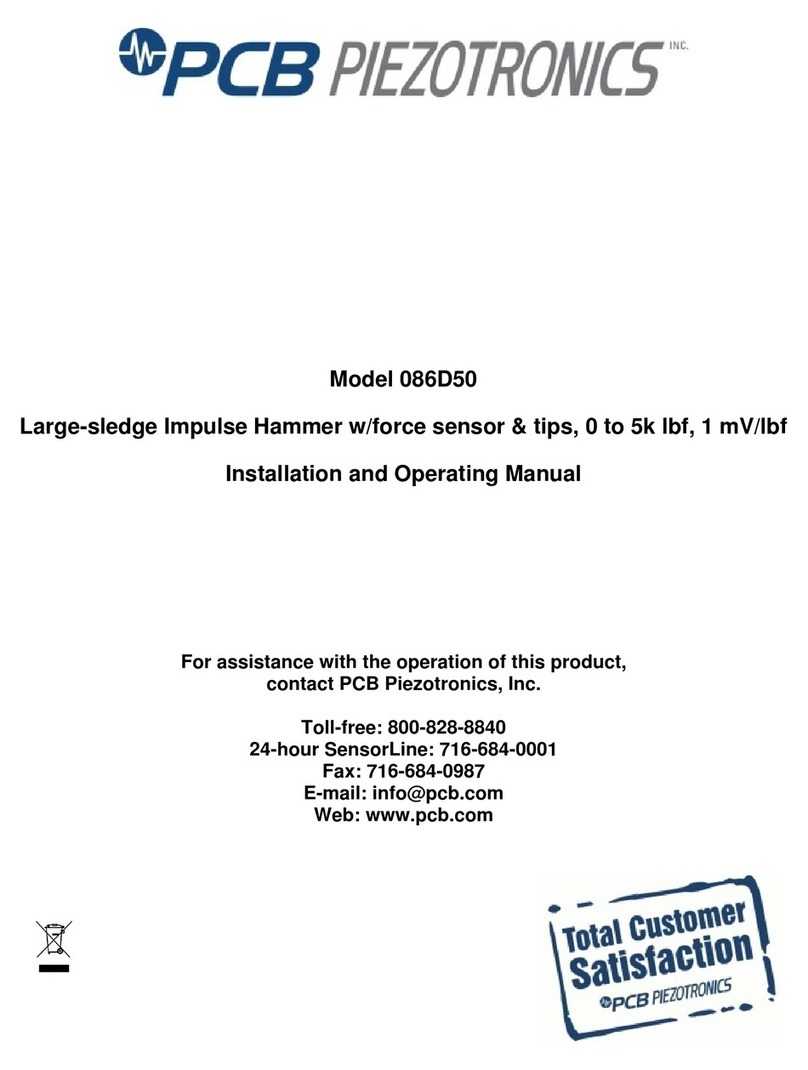
PCB Piezotronics
PCB Piezotronics 086D50 User manual
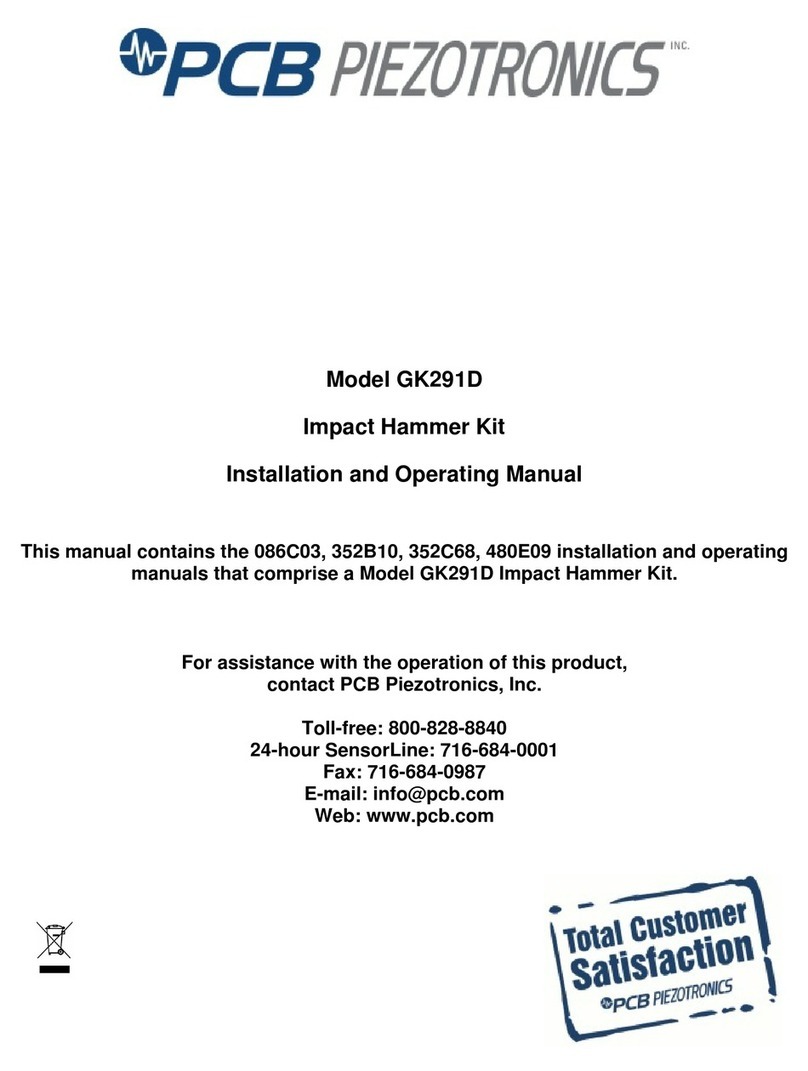
PCB Piezotronics
PCB Piezotronics GK291D User manual

PCB Piezotronics
PCB Piezotronics 027125-07012 User manual
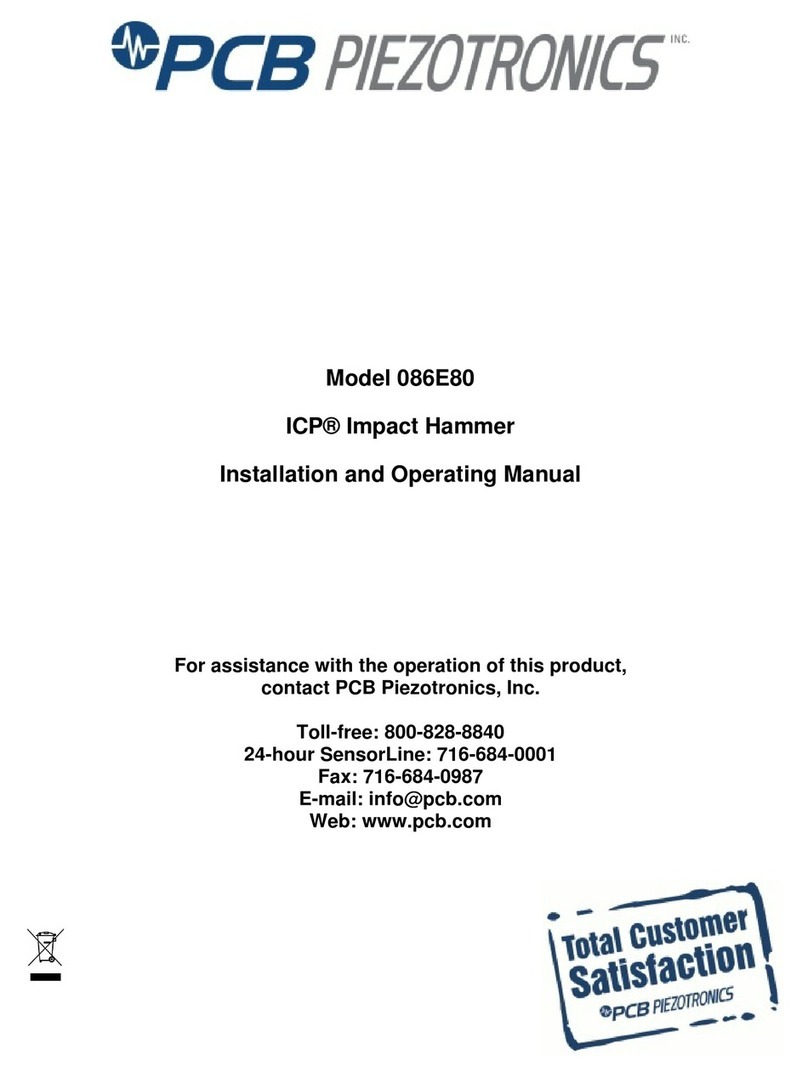
PCB Piezotronics
PCB Piezotronics ICP 086E80 User manual
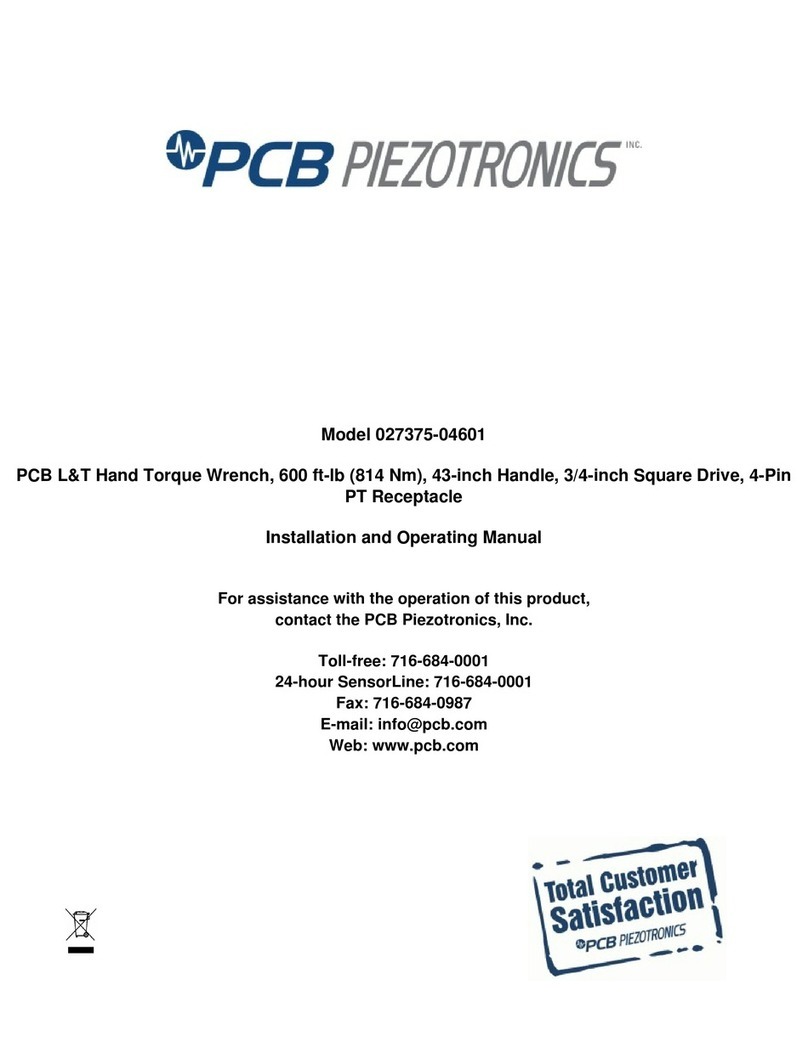
PCB Piezotronics
PCB Piezotronics 027375-04601 User manual

PCB Piezotronics
PCB Piezotronics 027250-04201 User manual
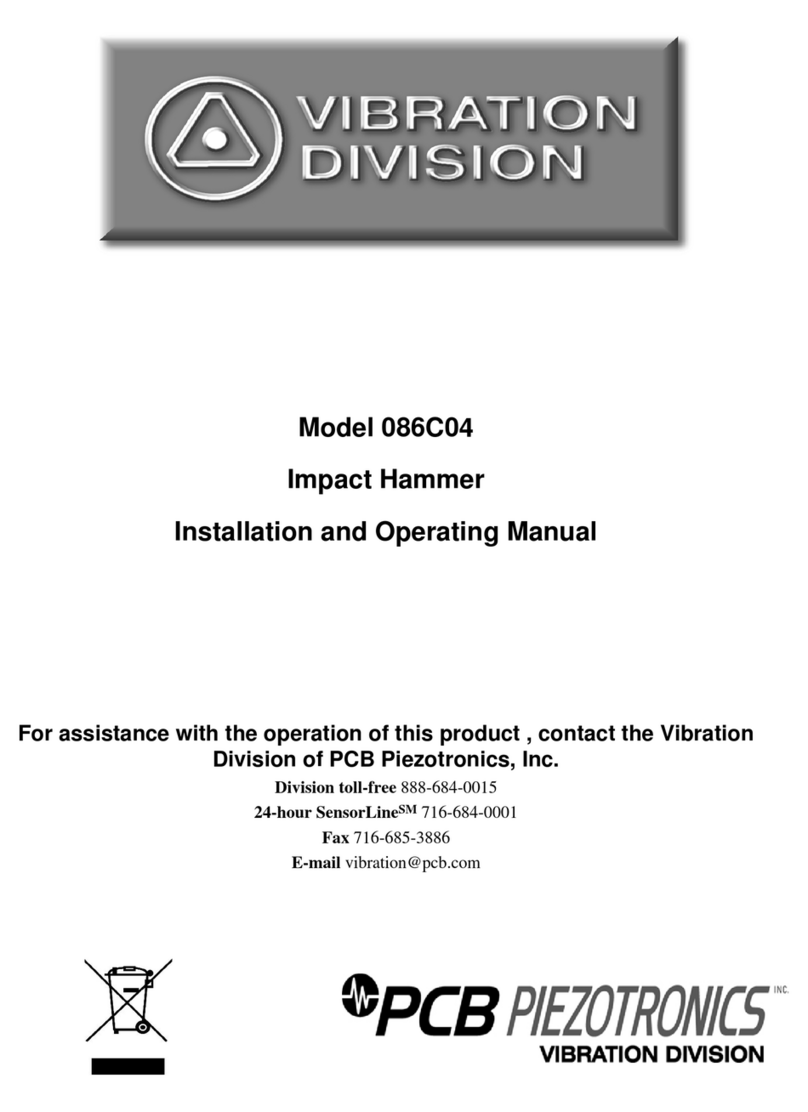
PCB Piezotronics
PCB Piezotronics Vibration Division ICP 086C01 User manual