Peerless Pump Sealtrode P Series User manual

Sealtrode Series P
Sealed Electrode Floatless
Pump controller
Instructions
• Installation
• Operation
• Maintenance
Read this entire book
before attempting to install, operate or repair this control.
Properly installed, your Peerless control will five you
satisfactory, dependable service. We urge that you read
carefully these step-by-step instructions, to simplify any
problems of installation, operating or repair.
Failure to read and comply with installation and
operating instructions will void the responsibility of the
New equipment manufactured by Seller is warranted to
be free from defects in material and workmanship under
normal use and service for a period of one year from
date of shipment; Seller’s obligation under this warranty
being limited to repairing or replacing at its option any
part found to its satisfaction to be so defective provided
that such part is, upon request, returned to Seller’s
factory from which it was shipped, transportation
prepaid. This warranty does not cover parts damaged
by decomposition from chemical action or wear caused
by abrasive materials, not does it cover damage
resulting from misuse, accident, neglect, or from
improper operation, maintenance, installation,
modification or adjustment. This warranty does not
cover parts repaired outside the Seller’s factory without
prior written approval. Seller makes no warranty as to
starting equipment, electrical apparatus or other material
not of its manufacture, since the same are usually
covered by warranties of the respective manufacturers
thereof.
Manufacturer and may also result in bodily injury as well
as property damage.
This book is intended to be a permanent part of your
Store in a convenient location for ready reference. If
these instructions should become soiled obtain a new
copy from Peerless Pump. Include control model and/or
serial number with you request.
WARRANTY
In the event, notwithstanding the terms of this
agreement, it is determined by a court of competent
jurisdiction that an express warranty has been given by
Seller to Purchaser with respect to the head, capacity or
other like performance characteristics of said equipment,
Seller’s liability for breach of the same shall be limited to
accepting return of such equipment FCA. plant of
manufacture, refunding any amount paid thereon by
Purchaser (less depreciation at the rate of 15% per year
if Purchaser has used the equipment for more than thirty
(30) days) and canceling any balance still owing on the
equipment.
THIS WARRANTY IS EXPRESSLY IN LIEU OF ANY
OTHER WARRANTIES, EXPRESSED OR IMPLIED,
AND SELLER SPECIFICALLY DISCLAIMS ANY
IMPLIED WARRANTY OF MERCHANTABILITY OR
FITNESS FOR A PARTICULAR PURPOSE.
4848247
Rev. 8/78

IMPORTANT SAFETY PRECAUTIONS
Control assembly and the tools and lifting equipment
used in installation are heavy and may easily cause
personal injury if dropped or carelessly handled. The
normal precautions and safety rules associated with the
installation or repair of machinery, in regard to manual
lifting, use of power equipment, and handling of tools,
must be observed in the installation of this controller.
Petroleum-base cleaning solvents are flammable.
Smoking by personnel, open flame, or other activity
which could ignite vapors in the vicinity of these solvents
is extremely hazardous and must not be permitted.
Do not work under a suspended object unless there is a
positive support under it to stop is fall in event of sling or
hoist failure.
UPON RECEIPT OF CONTROL EQUIPMENT: Check
carefully to see that all of the equipment has been
received. Report immediately any shortages or damages
to the transportation company handling the shipment,
noting the extent of the damage or shortage on the
freight bill and bill of lading.
Do not leave the unit exposed to weather or construction
hazards. The controller may become mechanically
damaged. This controller is a well designed and carefully
WARNING Do not work under a suspended object
unless there is a positive support under it to stop its fall
in event of sling or hoist failure. Disregard of this warning
could result in grave personal injury.
ELECTRODE HOUSING: If furnished in two or more
sections, screw the 1-1/2” pipe (Electrode Housing)
together with couplings provided. Screw the bulb
assembly (20) (21) (22) (23) to the bottom of the 1-1/2”
electrode Housing. Be sure to use a good pipe thread
compound to insure a watertight connection.
To protect and facilitate installation, roll the flexible bulb
into a compact bundle about its vertical axis and
4848247
2
Before attempting examination, handling or repair, be
certain that the electrical power supply is shut off. An
electrical shock from contact with live wires or cards can
be fatal.
Before opening the conduit box of an electric motor, a
switch cover, starter or panel door, be certain that the
power supply is shut off. An electrical shock from contact
with live leads can be fatal.
Before attempting repairs to installation, disconnect
power supply. Controls are automatic. This prevents
accidental running of pump motor. Starting motor during
repair activities could damage pump and may cause
personal injury.
INTRODUCTION
Manufactured unit. It should be given the same attention
accorded to any precision machine.
The satisfactory operation of this controller depends to a
large extent upon proper installation. These in-structions
cannot answer every question that may arise as each
installation will be different. The installer and the
operator of this equipment must use good judgment to
adapt these procedures to the installation.
INSTALLATION
temporarily encircle the roll with tape to secure.
Carefully lower the Electrode Housing assembly, bulb
first, through the opening in the cover over the basin until
the mounting flange rests on the basin cover. Remove
tape.
MOUNTING FLANGE: The Sealtrode Series P Pump
Controller is furnished with one of two styles of mounting
flanges: standard for mounting on metal basin covers,
and style F for concrete mounting, both illustrated on
page 5.
The Mounting Flange (15) has been preset at the factory
for the correct basin depth and should require no further
adjustment. Refer to page 5 for factory settings.

TERMINAL HOUSING ASSEMBLY: For aid in
installation the factory has pre-assembles the terminal
housing (27) reducer tee (12) and compression coupling
(13) together. This assembly also includes the
suspension wires (18), electrodes (19) and fill-vent tee
(5).
Remove tape from and straighten the electrode wires.
Remove kinks if necessary. Make sure all wires are
marked. Wire “A” is the longest, wire “B” is the next
longest, etc.
Feed electrodes (19) and wires (18) into the Electrode
Housing, being careful not to tangle or twist wires. Place
terminal housing assembly on top of Electrode Housing
(17) and press down on terminal housing assembly until
pipe is inside of compression coupling (13). Hold the
terminal housing in position and screw the cap on the
compression coupling until the assembly is secured to
the electrode housing (17).
VENT: Atmospheric venting is required for this unit to
operate. In normal, non-explosive atmospheres, venting
is accomplished via the small pierced hole in the metal
closure installed in the side opening of the fill-vent tee. If
the terminal housing is to be installed in an explosive
atmosphere, pry the metal closure from the tee and
discard. The exposed vent opening should be connected
to uncontaminated air by means of pipe or tubing. The
opening is threaded behind the closure to accommodate
a ¾” pipe fitting.
CAUTION
Never block, plug or close off Vent openings. Inspect
closure for presence of pierced hole and add if missing.
This device will not function without venting.
FILLING FLEXIBLE BULB: Fill the basin with water to
a level approximately 4” below the cap to which the bulb
is attached. Remove the plug from the top of the fill-vent
tee. Tee is located near the terminal housing. Pour in the
electrolytic solution (a mixture of 3 ½ quarts of distilled
water and one (1) package of sodium bicarbonate.)
Replace the top plug.
WARNING
Before attempting repairs to
installation, disconnect the power supply. Controls
are automatic. This prevents accidental running of
pump motor. Starting motor during repair activities
could damage pump and may cause personal injury.
WIRING: Remove the cover (1) from the terminal
housing and install conduit from the housing to the
control box. Use 14 AWG wire with 600 volts rated
insulation and 3/64 inch minimum insulation wall
thickness to connect the letter coded wires to the
indicated terminals in the control box. Be sure electric
current is the same as that stamped on the control box
nameplate. Wire per wiring diagram supplied with
control panel. If diagram is lost or misplaced copies may
be obtained from your local Peerless Pump
representative.
NOTE: When the Sealtrode Control Box is remotely
located the distance from the SEALTRODE in the
pumping station to the control box or panel should not
exceed 100 feet.
Two separate metallic conduits are required from the
pumping station to the building housing the control, one
for the SEALTRODE r wires and one for the wires
between the motors and controls.
GENERAL: The installation of the controller is now
completed and the level within the 1 ½” Electrode
Housing will faithfully duplicate the liquid level in
the basin actuating the control as the liquid rises
and falls and making and breaking contact with the
electrodes.
HOW TO ADJUST ELECTRODE SETTING: The
electrode elevations have been pre-set at the factory
and no further adjustment should be necessary. Should
it be desirable, however, to readjust the factory settings
refer to page 5 and note the assembly arrangement for
anchoring the wires within the terminal housing. Also
refer to page 5 and note and select the proper letter
coded wire to be adjusted.
To adjust electrode remove the terminal housing cover
(1) and slowly loosen the compression fitting (8) just
enough to be able to slide the selected suspension wire
up or down as required. When adjustment has been
made, re-tighten the compression fitting.
There is sufficient suspension wire coiled inside the
terminal housing to permit each electrode to be lowered
a maximum of one foot, with the exception of the lowest
electrode, which is the pump cut-out electrode with
suspension wire labeled “A”. The low electrode wire
marked “A” is already positioned near the bottom of the
1 ½” Electrode Housing and should not be lowered
further. This also applies to electrode wire mark A1 or
A2.
BELOW GRADE MOUNTING: When installing below
grade make electrical connections above grade. There
are 48 inches of suspension wire furnished past the
terminal housing for below grade mounting.
CAUTION
Do not allow the liquid leveling the basin to
submerge the terminal housing.
4848247
3

OPERATION
As the liquid level rises in the wet well, a hydrostatic
pressure on the flexible bulb is exerted. The hydrostatic
pressure tends to squeeze the bulb, causing a
displacement of its liquid. The displaced liquid rises in
the electrode housing toward the electrodes. The liquid
level within the electrode housing will always be equal to
the level of the liquid in which the controller is
submerged, since the density of both liquids are equal.
As the liquid within the electrode housing rises and falls,
it makes a and breaks electrical circuits with the
electrodes, thereby actuating the pump starters through
the controller relays.
CAUTION
This controller should not be used in liquids having a
temperature exceeding 140º F. or less than 35º F.
MAINTENANCE
The SEALTRODE r Series P Controller, if properly in-
stalled, requires little or no maintenance. It has no
moving parts, except for the control relays which should
be inspected semi-annually for worn or pitted contactors.
It is recommended that the operation of the controller be
observed for several complete operating cycles when
making routine maintenance and inspection of the pump.
REFILLING FLEXIBLE BULB: The electrolytic solution
within the control bulb should seldom, if ever, be
replenished because of evaporation. However, should it
become necessary to replenish the liquid within the bulb,
proceed in the following manner:
1. Refer to installation print showing the setting of the
electrodes.
2. Note the setting of the highest electrode and what
circuit it controls.
WARNING
Before attempting repairs to installation, disconnect the
power supply. Controls are automatic. This prevents
accidental running of pump motor. Starting motor during
repair activities could damage pump and may cause
personal injury.
3. Disconnect all electrical devices (pump starters) which
are not controlled by the highest electrode to prevent
their operation during the process of refilling the bulb.
4. Fill the basin to the highest electrode setting and then
slowly pour distilled water thru the tee. Fill the
connection until the high electrode circuit operates.
When the circuit operates, add an additional quart of
water.
5. In the event that the bulb has been over-filled, and
the pumps do not cut-off, remove and empty the bulb
and refill as outlined on page 3 under the heading “Filling
Flexible Bulb”.
LOCATING TROUBLE
IF THE PUMP FAILS TO START:
1. Make sure sodium bicarbonate has been added to
water.
2. Check the electrical service, making sure the current
characteristics are the same as that stamped on the
control box nameplate.
3. Check to see if the control wiring is in accordance with
the wiring diagram supplied with controller.
4. Determine if the electrical power at the control box
has been interrupted or disconnected.
5. Check set screw (14) and make certain it is right.
6. Short circuit the pump start electrode terminals in the
control box with a piece of insulated wire. This should be
done by a qualified electrician. If the pump operates
check the following:
a. Inspect the wiring from the terminals in the control
box to the controller terminal housing making sure that
all connections are clean and tight. Look for broken
wires.
b. Check the wire connections at the electrodes to
see if they are broken.
c. Check to see if the flexible bulb has been
damaged. If the bulb is damaged, liquid from the basin
may have entered the housing and coated the
electrodes with grease or oil. Grease and oil will
insulate the electrodes.
d. Check the bulb for loss of electrolytic solution.
e. Check the setting of the pump cut-in electrode. It
may be set too high.
f. Check for proper open venting of housing.
7. If the pump fails to operate after short circuiting the
electrode terminals in the control, check the following:
a. Check the ground wire, making sure that it is not
broken and terminal connections are clean and tight.
b. Check the control box for burned out transformer or
relay coils.
c. Check the relay contacts to see if they are corroded,
worn or pitted.
8. If the pump fails to cut off check the following:
a. Check the wire connections and insulation in the
terminal housing and control box, making sure they are
not forming a short circuit by being grounded to the box
or housing.
b. Check the electrodes, making sure they are properly
shielded. An electrode not properly shielded may form a
short circuit with the electrode housing.
c. Check the relay contacts in the control box to see if
they are stuck.
d. Too much liquid in the flexible bulb. Excessive liquid
in the bulb will keep the low pump cut-off electrode
submerged and the pump cut-in relay will not open.
4848247
4

DT 4848247
5

UW SUBMERSIBLE PUMPS
Fusible Disconnect Switch DY60UFD
Circuit Breaker DY60UCB
SERIES P DUPLEX COMBINATION SEALTRODE
FLOATLESS CONTROLLER consists of:
A. Electrode and terminal housing assembly including:
galvanized steel electrode housing. NEMA 1 thru 4
terminal housing, 4 plastic shielded brass electrodes, 4
electrode conductor/suspension wires, rubber electrolyte
storage bulb with adapter, electrolyte, adjustable basin
cover mounting flange.
B. Sealtrode duplex pump combination controller
including:
2 – fusible disconnect switches or thermal magnetic trip
circuit breakers.
2 – across-the-line magnetic motor starters with 3 coil
overload protection for 3 phase or 1 coil overload
protection for 1 phase.
2 – control circuit transformers with fused secondary.
1 – set of Y60MA Sealtrode relays with motor operated
electric alternator, for automatic alternation of lead-lag
pumps, high water alarm circuit, for duplex submersible
pump down operation.
2 – sets of submersible motor thermal protection circuits
2 – green pump running lights
1 – audible/visible high water alarm mounted on
enclosure with relay, silencing push button for audible
alarm, red high water alarm light
2 – submersible motor moisture detection circuits with
relays, outer seal failure warning lights, continuity
check circuits with lights and push buttons
2 – hand -off- automatic selector switches in cover
2 – capacitor circuit boards with motor capacitors
mounted in enclosure for 1 phase motors only
All mounted and pre-wired in NEMA 1 general purpose
or NEMA 4 watertight dead front enclosure.
4848247
6
TYPE L and TYPE VCS PUMPS
Fusible Disconnect Switch DY60FD
Circuit Breaker DY60CB
SERIES P DUPLEX COMBINATION SEALTRODE
FLOATLESS CONTROLLER consists of:
A. Electrode and terminal housing assembly including:
galvanized steel electrode housing, NEMA 1 thru 4
terminal housing, 4 plastic shielded brass electrodes, *4
electrode conductor/suspension wires, rubber electrolyte
storage bulb with adapter, electrolyte, adjustable basin
cover mounting flange.
B. Sealtrode duplex pump combination controller
including:
2 – fusible disconnect switches or thermal magnetic trip
circuit breakers.
2 – across-the-line magnetic motor starters with 3 coil
overload protection for 3 phase or 1 coil overload
protection for 1 phase.
2 – control circuit transformers with fused secondary
1 – set of Y60MA Sealtrode relays with motor operated
electric alternator, for automatic alternation or lead-lag
pumps, high water alarm circuit, for duplex down
operation
2 – green pump running lights
1 – audible/visible high water alarm mounted on
enclosure with relay, silencing push button for audible
alarm, red high water alarm light
2 – hand-off-automatic selector switches in cover
All mounted and pre-wired in NEMA 1 general purpose
enclosure, NEMA 4 watertight dead front enclosure or
NEMA 7 Class 1, Division 1, Group A, B, C and D
explosion proof enclosure with intrinsically safe series 7
liquid level controls (see note 3 page 7).
*NEMA 7 controllers are furnished with an extra
electrode for standby pump stop.

Series P Pilot Sealtrode Floatless Pump Controller consists of:
A. Electrode and terminal housing assembly including:
Galvanized steel electrode housing, NEMA 1 through 4
terminal housing; plastic shielded brass electrodes,
electrode conductor/suspension wires, rubber electrolyte
storage bulb with adapter, electrolyte, adjustable basin
cover mounting flange.
B. Sealtrode relay panel (for operation of starting
equipment by others) with relays for down pump
operation in NEMA 1 general purpose, NEMA 4
watertight, or NEMA Class 1, Division 1, Group A, B, C
and explosion proof enclosure with intrinsically safe
series 7 liquid level controls, NEMA 7 not available with
UW pumps. Sealtrode UW Pump includes sub-motor
moisture detection relay circuit, including outer seal
failure warning light and continuity check circuit with light
and push button.
SPECIFIC SERIES P PILOT SEALTRODE PUMP CONTROLLER DETAILS
CONTROLLER FEATURES
Type of Alteration
Pump
Model
UW
Pumps
VCS & L
Pumps
Type of
Installation
No. of
Electrodes
None
Manual with
Transfer Switch
Automatic with
Motor Driven
Electric Alternator
High Water
Alarm Contacts
(Alarm Annunciation)
by others)
High Water Alarm
with Annunciation
Silencing Relay
and Push Button
Red High Water
Alarm Light
Enclosure Mounted
Y 56 A-U Y 56 A Simplex 2 X
Y 57 A-UH Y 57 A-H Simplex 3 X X
Y 57 AU-A Y 57 A-A Simplex 3 X
Y 57 AU-D Y 57 A-D Duplex 3 X X
Y 57 AU-DH Y 57A-DH Duplex 4 X X
Y 57 AU-DA Y 57 A-DA Duplex 4 X
Y 58 AU Y 58 A Duplex 3 X X
Y 58 AU-H Y 58 A-H Duplex 4 X X
Y 58 AU-A Y 58 A-A Duplex 4 X X
Y 59 MAU Y 59 MA Duplex 3 X
Y 60MAU Y 60 MA Duplex 4 X X
Y 60MAU-A Y 60 MA-A Duplex 4 X X
Notes:
1. For hazardous locations the NEMA 7 pump control panes enclosures have been installed within intrinsically safe
series 7 liquid level controls. These Sealtrode model numbers have prefix letter I. (IY60MA)
2. NEMA 7 duplex controllers are furnished with an extra electrode for standby pump stop.
3. Intrinsically safe series 7 liquid level controls installed in the pump control panel enclosure are approved by Factory
Mutual for use in Class 1, Division 1,Group A, B, C and D hazardous atmospheres. Series 7 controls limit the current In
the electrode to values considered safe. The pump control panel enclosure Requires explosion proof integrity.
However, the Sealtrode enclosure does not Normally require explosion proof integrity.
4848247
7

Peerless Pump Company
P.O. Box 7026 – Indianapolis, IN 46207-7026
Phone: (317) 925-9661 – Fax: (317) 924-7388
Item
Description
* 1
* 2
* 3
4
5
6
* 7
* 8
* 9
*10
*11
12
13
14
15
16
17
18
19
20
21
22
23
*24
*25
*26
Cover
Slotted Screw
Upper Gasket
3/4" Pipe Plug
3/4" Tee
3/4" Nipple
Ground Terminal
Compression Fitting
Phillips Head Screw
Lower Gasket
O-Ring
Reducer
Coupling Compression
Set Screw Sq. Hd.
Mounting Flange
Gasket Mtg. Flg.
Electrode Hsg.
Suspension Wires
Electrodes
Bulb Adapter
Hose Clamp
Band Protector
Bulb
Housing
Body
Vent Cap
(27)* These parts make up the Terminal Housing
4848247
Rev. 2/2/05
Table of contents
Popular Controllers manuals by other brands
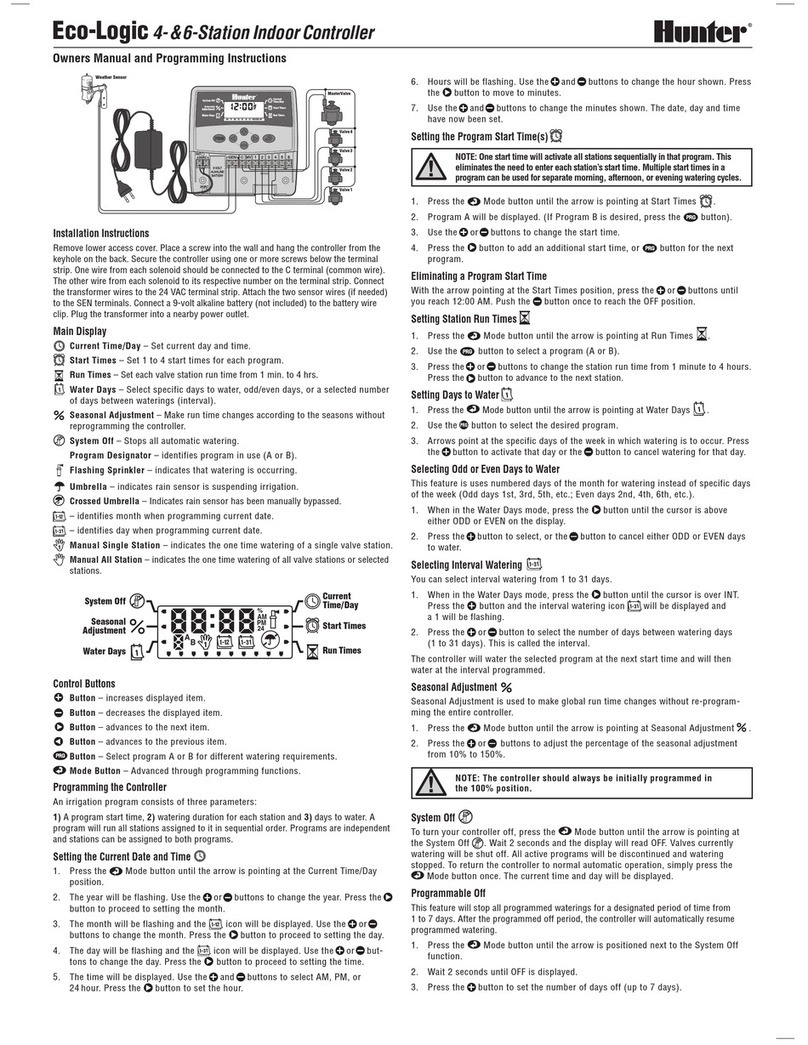
Hunter
Hunter Eco-Logic 6 Owners manual and programming instructions
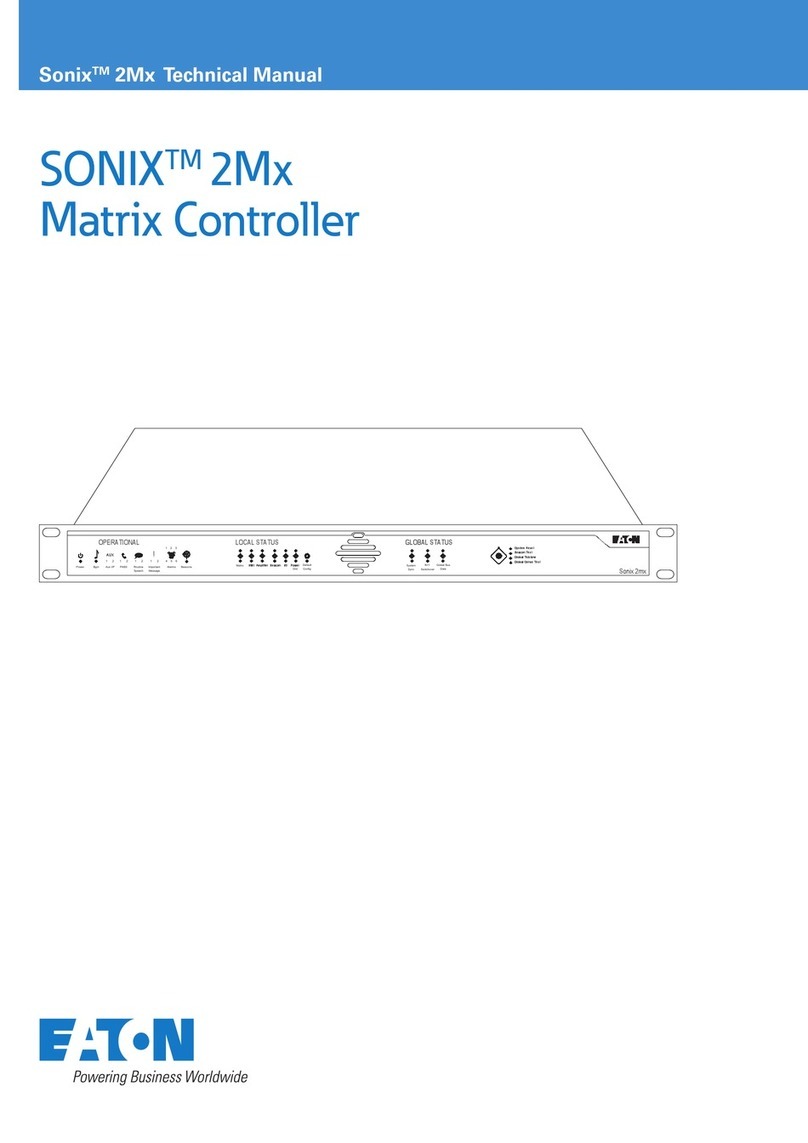
Eaton
Eaton SONIX 2Mx Technical manual
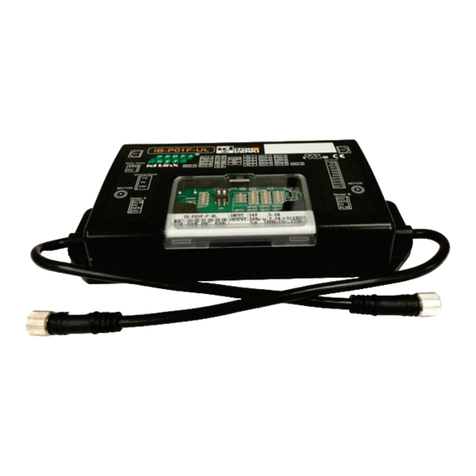
ITOH DENKI
ITOH DENKI POWER MOLLER IB-P01 Technical documentation
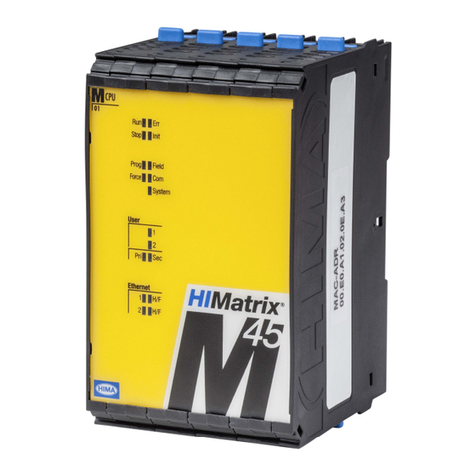
HIMA
HIMA HIMatrix M45 manual
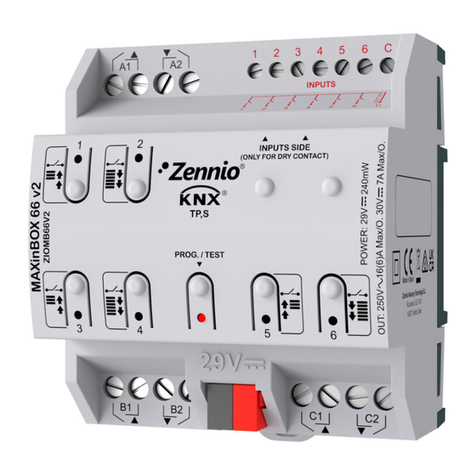
Zennio
Zennio MAXinBOX 66 v2 Technical documentation
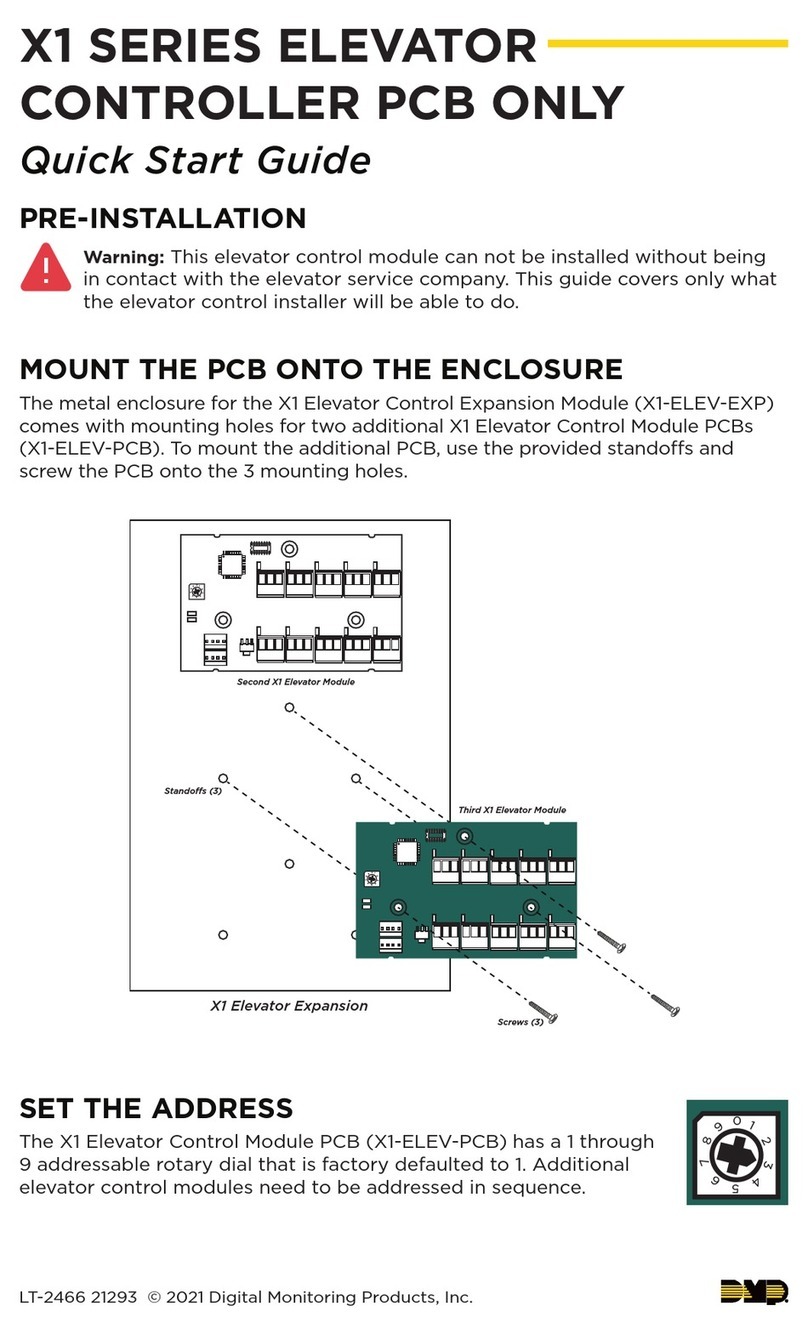
Digital Monitoring Products
Digital Monitoring Products X1 Series quick start guide