PERCo C-01 User manual

Controller
C-01
ASSEMBLY AND OPERATION MANUAL

Controller
C-01
Assembly & Operation Manual

CONTENTS
1APPLICATION..............................................................................................................3
2OPERATION CONDITIONS .........................................................................................3
3TECHNICAL SPECIFICATIONS ..................................................................................4
3.1Supported scanners ................................................................................................5
4DELIVERY SET............................................................................................................6
4.1Standard delivery set ..............................................................................................6
4.2Additional equipment, offered as an option .............................................................6
5DESCRIPTION .............................................................................................................7
5.1Design and operation ..............................................................................................7
5.2Controller boards.....................................................................................................7
5.3Signals of inputs....................................................................................................10
5.3.1Inputs IN1 – IN4............................................................................................10
5.3.2Inputs DUA, DUSt, DUB, FA.........................................................................11
5.4Settings of output signals ......................................................................................12
5.4.1Relay outputs OUT1, OUT2..........................................................................12
5.4.2Outputs OK1 and OK2..................................................................................12
5.4.3Outputs Ld A, LdSt, Ld B ..............................................................................13
6MARKING AND PACKAGING ....................................................................................14
7SAFETY REQUIREMENTS........................................................................................14
7.1Installation safety requirements.............................................................................14
7.2Operation safety requirements ..............................................................................14
8INSTALLATION ..........................................................................................................15
8.1Cable lengths ........................................................................................................15
8.2Installation order....................................................................................................16
8.3Method for obtaining an IP-address ......................................................................18
8.4Connection of readers / scanners .........................................................................19
8.4.1Connecting readers by using Wiegand interface ..........................................19
8.4.2Connecting scanners by using RS-232 interface ..........................................19
8.4.3Connecting scanners via USB interface .......................................................20
8.5Connecting locks...................................................................................................21
8.6Turnstile and electromechanical gates configuration ............................................23
8.7Connecting OD VCP .............................................................................................24
8.8RC-panel configuration .........................................................................................26
8.9Connecting a Fire Alarm Device............................................................................27
8.10Connection of optional equipment.........................................................................27
9CONFIGURATION......................................................................................................30
9.1First start of the controller......................................................................................30
9.2Controller configuration options.............................................................................30
9.2.1Configuration by means of application exchange protocol............................30
9.2.2Using configuration templates from the Web-interface .................................30
9.3Connecting to Web-interface of the controller .......................................................31
10SW UPDATING ..........................................................................................................31
11OPERATION ..............................................................................................................32
11.1ACM and controller operation algorithm................................................................32
11.2Indication of ACS and controller configurations.....................................................34
12TROUBLESHOOTING................................................................................................36
12.1The controller doesn’t work ...................................................................................36
12.2Failure of communication with PC.........................................................................36
13MAINTENANCE .........................................................................................................38
14TRANSPORTATION AND STORAGE........................................................................39
Appendix 1. Instruction on connection of alcohol detector .............................................40
Appendix 2. Instruction on connection of the controller through PoE-splitter .................42
Appendix 3. C-01 Controller Web-interface. User Manual..............................................44

C-01 Controller
Dear Customer!
Thank you for purchasing a controller manufactured by PERCo.
Please follow the instructions given in the Manual carefully,
and this quality product will provide many years of trouble-free use.
This Operation Manual (hereinafter – the Manual) provides information on technical
specifications and operation of C-01 controller. The Manual aims to provide correct
operation of the controller and complete use of its technical capabilities. Installation and
maintenance of the device must be carried out by person who has fully studied this
manual.
Abbreviations adopted in the Manual:
ACM – access control mode;
ACS – access control system;
OD – operating device;
PS – power supply;
PWP – passage waiting period;
RC – remote control;
SW – software;
VCP – vehicle checkpoint;
WRC – wireless remote control.
1 APPLICATION
C-01 controller (hereinafter – the controller) is used in on-line based access control
systems (incl. paid access and ticket access systems etc.).
The controller supports connection up to 6 readers / barcode scanners (two - via Wiegand
interface, two – via RS-232 interface and two – via USB interface), and enables to
organize up two two-way passages or one-way passages (the list of supported scanners –
Sect. 3).
Depending on the configuration (Sect. 9.2) the controller can control the following ODs:
one or two electromagnetic or electromechanical locks that support one or two-way
passage;
one turnstile or gate;
one boom barrier or an automatic gate of vehicle checkpoint.
2 OPERATION CONDITIONS
The controller, with regard to resistance to environmental exposure complies to
GOST15150-69, category NF4 (operation in premises with climate control).
Operation of the controller is allowed at ambient air temperature from +1°C to +40°C and
relative air humidity up to 80% at +25°C.
3

Assembly & Operation Manual
3 TECHNICAL SPECIFICATIONS
Operating voltage .................................................................................................. 12±1.2 V
Consumption current (12 V) ................................................................................ max 0.2A1
Power consumption ........................................................................................... max 2.5W1
Communication interface standard ................................................... Ethernet (IEEE 802.3)
Important:
By default, the controller has a preset: IP-address and MAC-address, which are
indicated in the warranty certificate included in the passport and on the controller
board; subnet mask: 255.0.0.0; Gateway IP-address: 0.0.0.0.
Ethernet data transfer speed .......................................................................... 10/100 Mbps
Number of controlled ODs ...................................................................................... up to 22
Number of scanners connected via USB interface ............................................................ 2
Number of scanners connected via RS-232 interface ........................................................ 2
Number of readers connected via Wiegand interface ........................................................ 2
Supported Wiegand interfaces ........................................................... -26, -34, -37, -40, -42
Number of relay outputs for OD control .............................................................................. 2
Number of additional “open collector” outputs ................................................................... 2
Number of additional inputs, controlled by «dry contact» outputs ...................................... 2
Number of remote control inputs ........................................................................................ 3
Number of remote control indication outputs ..................................................................... 4
Mean lifetime ........................................................................................................... 8 years
Electric shock protection class ...................................................................... III (IEC 61140)
Web-interface ................................................................................................................ yes
Dimensions ............................................................................................... 210×189×46 mm
Weight ............................................................................................................... max. 1.5 kg
1Not including the consumption of readers, scanners and other additional equipment.
2Depends on the selected configuration of the controller. The configuration can be done in a third-
party software via PERCo-C01 Exchange protocol or by using the templates from the controller
Web-interface (Sect. 9.2).
4

C-01 Controller
3.1 Supported scanners1
Scanners manufactured by «Metrologic»:
- IS3480 Quantum E
- MS 7120 Orbit USB
- MS 7180 OrbitCG
- 3310g Vuquest
- MS3580 Quantum T
Scanners manufactured by «DataLogic»:
- Magellan 800i
- (PSC) VS800
Scanners manufactured by «Motorolla»:
- Motorola (Symbol) MS-954
- Motorola (Symbol) MS-1204
- Motorola (Symbol) MS-1207
- SYMBOL LS 9208
- Motorola (Symbol) MS-3204
- Motorola (Symbol) MS-3207
- Motorola (Symbol) MS-2204
- Motorola (Symbol) MS-2207
Scanners manufactured by «Opticon»:
- Opticon OPM 2000
- Opticon NLV 2001
- Opticon NLV 1001
Note:
All scanners must be preconfigured before you connect them to the controller (set
interface parameters and barcode encode formats supported by scanner). Data
that was read by scanner will be transferred via Ethernet interface in accordance
with exchange application protocol (see PERCo-C01 exchange protocol).
1Scanner parameters are listed in Sections 8.4.2, 8.4.3.
5

Assembly & Operation Manual
4 DELIVERY SET
4.1 Standard delivery set
Controller ........................................................................................................................... 1
Jumper ............................................................................................................................... 5
Suppressor 15-18 V ........................................................................................................... 2
Mounting hardware:
Lead-through ................................................................................................................. 1
Plastic dowel .................................................................................................................. 3
Screw ............................................................................................................................ 3
Self-adhesive mount ...................................................................................................... 3
Plastic cable tie 100 mm ................................................................................................ 5
Package ............................................................................................................................. 1
Passport ............................................................................................................................. 1
Operation manual .............................................................................................................. 1
4.2 Additional equipment, offered as an option:
Controller power supply ..................................................................................................... 1
PoE-splitter1....................................................................................................................... 1
Siren .................................................................................................................................. 1
RC-panel ............................................................................................................................ 1
Wireless remote control kit2............................................................................................... 1
1PoE-splitter – allows energizing of the controller via Ethernet network. Splitter can be used with
network switches that support PoE technology and that are compatible with IEEE 802.3af
standard.
2WRC kit consists of a receiver that is connected to the controller and transmitters (tags).
6

C-01 Controller
5 DESCRIPTION
5.1 Design and operation
The controller is produced in the form of electronics module in metal housing with a
removable cover. The cover houses power indication.
The controller provides:
Connection via Ethernet (IEEE 802.3);
Support of TCP/IP protocols;
Supports application layer of communications protocol over WebSockets (RFC 6455),
the protocol uses JSON (RFC 7159) format for data exchange;
Connection to system server by using IP-address that is set during configuration (it is
possible to use WSS (WebSockets over SSL/TLS) secure channel);
updating of embedded software through Ethernet.
On default, the controller has:
unique MAC-address (specified in the certificate and on the item board);
IP-address (specified in the certificate and on the item board);
Subnet mask (255.0.0.0).
Following ways to set up IP-address, gateway and subnet mask are provided at the stage
of system configuration:
work with default settings;
static IP-address (manual input);
receipt form DHCP-server.
The following additional equipment may be connected:
up to two readers via Wiegand interface;
up to two scanners via RS-232 interface;
up to two scanners via USB interface;
up to two door sensors or two passage sensors (turnstile PASS outputs);
up to two RC buttons («Exit») for a lock or RC-panel of a turnstile (swing gate);
up to five devices sending commands to additional inputs;
up to two devices controlled by controller additional outputs («open collector» outputs)
up to three devices controlled by controller additional outputs («TTL» outputs);
emergency unlock devices (emergency passage unlock) Fire Alarm.
The controller as a part of ACS provides:
operation in ACM: «Open», «Control»;
saving of the set mode in the non-volatile memory, to avoid the turn-off of the mode in
case of power failure;
support of card withdrawal function activation during the shutdown of the card capture
reader.
5.2 Controller boards
The controller includes two boards – top board (processor module) and bottom board
(process execution module). The top board with connecting blocks XS1, XS2 fits in the
connecting blocks XP1, XP2 of the bottom board. The boards of the controller are shown
on Figure 1and 2. The purpose of bottom board connecting blocks is given in Table 1.
7

Assembly & Operation Manual
Figure 1. Controller top board
Figure 2. Controller bottom board
8

C-01 Controller
Table 1. The purpose of connecting blocks of the bottom board
Contact Purpose
Connector XT1 (Inputs)
IN1 «Door sensor OD1» or «Input for PASS A signal»
GND «Common»
IN2 «Door sensor OD2» or «Input for PASS B» or «Additional input»
IN3 «Additional input»
GND «Common»
IN4 «Additional input»
Connector XT2 (RC)
FA «Input for emergency unlock devices (passage opening) Fire Alarm»
GND «Common»
DUA «Control input of the OD1 from the RC» or «Control input of direction A from the RC» or
«Additional input»
DUSt «Input STOP for the RC» or «Additional input»
DUB «Control input of the OD2 from the RC» or « Control input of direction B from the RC» or
«Additional input»
Ld A «Output for indication of direction A on the RC» or «Additional output (TTL-level)»
Ld St «Output for indication STOP on the RC» or «Additional output (TTL-level)»
Ld B «Output for indication of direction B on the RC-panel” or “Additional output (TTL-level)»
Buzz «Output for sound indication on the RC»
Connector XT3 (“open controller” outputs)
+12V «Output of +12V power for outputs OK1 and OK2»
OK1 «Additional output (open collector) »
OK2 «Additional output (open collector) »
Connector XT4 (PS)
+12V
GND «Input of controller +12V power form external PS»
Connector XT5 (Wiegand)
BB Output “Sound indication” (Beeper Out)
LRB Output “Red Led control” (Red Led Out)
LGB Output “Green Led control” (Green Led Out)
BD0 Input “Data 0” (D0) (input “Data 0”)
BD1
Reader B
Input “Data 1” (D1) (input “Data 1”)
+12V
GND «Output of +12V power for readers A and B» (summary no more than 0.5 A)
AD1 Input “Data 1” (D1) (input “Data 1”)
AD0 Input “Data 0” (D0) (input “Data 0”)
LGA Output “Green Led control” (Green Led Out)
LRA Output “Red Led control” (Red Led Out)
BA
Reader A
Output “Sound indication” (Beeper Out)
Connector XT6 (OUT1)
NO1 Normally open contact
C1 Central contact
NC1 Normally closed contact
«Relay control output OD1»
Connector XT7 (OUT2)
NO2 Normally open contact
C2 Central contact
NC2 Normally closed contact
«Relay control output OD2» or «Additional output»
9

Assembly & Operation Manual
Controller has on the top board:
XP1 – connector for jumper installation that defines method of IP-address receiving
(see Sect. 8.3);
X1 – microSD-card slot (installed not on every board model);
X2 – connector for the Ethernet cable;
X4 – double-sided connector for scanner connection via USB (bottom – USB1
connector, top – USB2 connector).
Controller has on the bottom board:
XP1,XP2 – connecting blocks for the top board;
XP3 – connector for selecting the energizing type of scanners that are connected
via RS-232. Select the variant according to service documentation of scanners:
jumper is in position 1-2 – +12 V power is supplied from controller to contact №6
of DB9 (RS-232) connectors which are placed on the controller housing;
jumper is in position 2-3 – +5 V power is supplied to contact №6 of DB9
connectors;
jumper removed – the power is not supplied to contact №6 of DB9 connectors (if
scanner can be powered in a different way according to service documentation).
Important:
By default, the jumper is installed on XP3 connector on 2-3 contacts (this provides
+5 V of power).
XP4.1 and XP4.2 – paired connector that is used for selection of lock which is
connected to XT6 (OUT1) connector:
Jumpers pair are removed – standard electromechanical or electromagnetic lock,
jumpers pair are installed – locks of LB- or LBP-series are without installed door
sensor (reed switch). The controller traces the passage on condition of the contact
group of the lock;
XP5.1 and XP5.2 – paired connector for selection the type of lock that is connected
to XT7 (OUT2) connector (the selection of a lock type must be done the same way as
a lock for XT6 connector);
XP6 – connecting block for power indication on the housing.
5.3 Signals of inputs
5.3.1 Inputs IN1 – IN4
The controller provides status control of four inputs controlled by “dry contact” or “open
collector” (OK): IN1-IN4. Connection to the inputs is performed via XT1 connecting block of
the controller bottom board (Figure 2and 4).
Important:
To create a high-level signal on all input contacts IN1 – IN4, resistors with 2 kOhm
resistance, connected to +3,3V power line, are used.
Inputs can be used for following connections:
input IN1:
odoor sensor (reed switch) №1,
oPASS1 output of a turnstile,
oOptional equipment;
10

C-01 Controller
input IN2:
odoor sensor (reed switch) №2,
oPASS2 output of a turnstile,
oOptional equipment;
inputs IN3, IN4:
ooptional equipment.
Signals activation depends on description of their default status in Normal status of
contact parameter (“normal_state”):
If input is described as Opened (“break”), it is activated by a turn-on of low-level
signal relative to GND contact. In such case a normally opened relay contact or a
scheme of open collector output may be a control element.
If input is described as Closed (“short”), it is activated by a turn-off of low-level
signal relative to GND contact. In such case a normally closed relay contact or a
circuit of open collector output may be a control element.
Important:
By default, Input IN1 is configured as “Closed” after you select a controller
configuration template. Selection of the templates «Two two-sided locks» or
«Turnstile» will configure IN2 input as Closed.
Control element “relay contact” shall provide following characteristics of signals:
Minimum commutating current ....................................................................... max. 1 mA
Closed contact resistance (with resistance of the connection cable) ....... max. 300 Ohm
Control element of circuit with open collector output shall provide the following
characteristics of signals:
Voltage at the closed contact (low-level signal at input of the controller) ......... max. 0.8V
5.3.2 Inputs DUA, DUSt, DUB, FA
The controller provides status control of four inputs under control of “dry contact” or “open
collector” (OK): DUA, DUSt, DUB, FA. Connection to the inputs is performed via XT2
connecting block of the controller bottom board.
Important:
To create a high-level signal on all input contacts DUA, DUSt, DUB, FA, resistors
with 1 kOhm resistance, connected to +3.3V power line, are used.
Inputs can be used for following connections:
input FA:
oemergency unlock devices (passage emergency unlock) Fire Alarm;
inputs DUA, DUSt, DUB:
oRC-buttons,
oRC-panel (WRC-device),
ooptional equipment.
Activation and characteristics of signals of the control element are specified in the
Sect. 5.3.
Important:
By default, after selecting any controller template from the Web-interface:
input FA is set as Closed.
inputs DUA and DUB is set as Opened.
Selection of the template «VCP» or «Turnstile» will configure input DUSt as
Opened.
11

Assembly & Operation Manual
5.4 Settings of output signals
5.4.1 Relay outputs OUT1, OUT2
The controller is equipped with four relay outputs OUT1, OUT2. Connection to the outputs
is performed via XT6, XT7 connecting blocks of the controller bottom board. Every output
has a complex group of contacts: normally open NO, normally closed NC and common
output C. Outputs may be used for (Figure 4):
output OUT1:
oas a control output of OD1,
oas outputs to control optional equipment;
output OUT2:
oas a control output of OD2,
oas outputs to control optional equipment.
Characteristics of output signals:
Maximum commutating voltage of direct current ...........................................max. 30 V
Maximum commutating voltage of alternate current .....................................max. 42 V
Maximum commutated direct/alternate current ...............................................max. 5 A
Resistance of closed contact ............................................................... max. 0.15 Ohm
Control outputs support potential and pulse operation modes of OD. Selection of mode is
performed with Operation mode of control output (“opt_mode”) parameter of OD.
In Potential mode of OD:
In case of single passage through OD, output OUT is activated for period that is
specified by Card analysis time (“analysis_time”) parameter, or till the moment
of passage.
In case OD is set into ACM «Open» output is activated till the mode changed.
In Pulse mode of OD:
In case of single passage through OD, output OUT is activated for period that is
specified by Pulse duration time OD (“impulse_time”). In such case OD
remains unlocked until the passage is performed.
In case OD is set into ACM «Opened» output is activated for a period of time that is
specified by Pulse duration time OD, and after that it will be activated each time
for the same period in one second after the passage is performed and till the ACM
changed.
Activation of inputs IN1 – IN2, configured as door sensor or signal PASS, define that the
passage was performed in the set direction.
5.4.2 Outputs OK1 and OK2
The controller is equipped with two outputs “open collector”: OK1 and OK2 (Figure 4).
Connection to the outputs is carried out via XT3 connecting block of the controller bottom
board.
+12VDC supply is derived to the same connecting block for easy connection.
Outputs can be used for following functions:
connection of light and sound alarm devices,
sending of alarm notifications to central surveillance panel,
connection of other optional equipment.
Characteristics of output signals:
Maximum commutation voltage of direct current ...........................................max. 30 V
Maximum commutated current ...................................................................max. 0.25 A
12

C-01 Controller
5.4.3 Outputs Ld A, LdSt, Ld B
The controller is equipped with three outputs type «TTL» (chip 74LVC04 and resistor
200 Ohm): Ld A, LdSt, Ld B. Connection shall be performed to the contacts of XT2
connecting block of the controller bottom board.
Outputs can be used (Figure 4):
as outputs of connection of indication of the RC-panel,
as outputs of control of other optional equipment.
Characteristics of output signals:
Maximum voltage of direct current ................................................................. max. 3 V
Maximum current ...................................................................................... max. 0.01 A
13

Assembly & Operation Manual
6 MARKING AND PACKAGING
The marking label of the controller is placed on the back of the housing. The marking label
provides following information concerning the controller:
trade mark and contact details of the manufacturer;
name and number of model;
serial number;
date and month of manufacture;
allowed power voltage range;
consumption current.
The controller board contains labels with default MAC-address and IP-address of the
controller.
The controller is packed into a paperboard box, preventing it from damages during
transportation and storage.
7 SAFETY REQUIREMENTS
7.1 Installation safety requirements
Installation and technical maintenance of the controller shall be performed by qualified
staff, after getting acquainted with the Operation manual and safety rules. Installation shall
be performed in accordance with general electrical and work safety rules.
Attention!
All connections and jumper installations should be carried out only when the
equipment is powered off and power supply is disconnected.
During mounting use only proper tools.
Cabling shall be performed in accordance with general requirements for
electrical equipment.
Do not use the controller if it is not properly installed and connected.
7.2 Operation safety requirements
Operation shall be performed in accordance with general electrical and work safety rules.
Do not use!
The controller under conditions that do not comply with the requirements of
Section 2of this Manual.
The controller at supply voltage that does not comply with the requirements of
Section 3of this Manual.
The device in hostile environment that contains acids, alkalis, oils etc.
Power supply should be used accordingly to safety rules given in the Operation manual.
14

C-01 Controller
8 INSTALLATION
Installation shall be performed in accordance with work safety noted in Sect. 7.1.
Installation should be done in accordance with local building requirements.
8.1 Cable lengths
Cables for mounting are shown in Table 2.
Do not lay cables at a distance less than 50 cm from a source of electromagnetic
interference.
Crossing of all cables with power cables is allowed only at a right angle.
Lengthening of cables shall be performed by soldering only.
All cables, entering controllers, shall be fixed with plastic ties to self-adhesive cable tie
mount, included into delivery set and installed inside the housing.
After cables are laid, check if there are no line breaks and short circuits at all lines.
It is not allowed to lay power cables for lock, sensor cables, remote control cables and
reader cables at a distance more than 1 m from ground cables.
Table 2. Cables used for installation
№Equipment
Cable
length, m,
max
Cable type
Cross
section,
mm² min.
Cable example
1 Ethernet (IEEE 802.3u) 100
Four twisted pairs
(starting from
Category 5)
0,2 5e 4×2×0,52 F/UTP2-
Cat5e
Reader, card capture
reader Wiegand630 Eight-core cable 0,2 CQR CABS8 8×0,22c
Scanner via RS-232 15 Two twisted pairs 0,2 5e 2×2×0,52
2
Scanner via USB 2
From the scanner
package - -
3 PS 10 Twin cable 0,75 PVC 2×0,75 two-color
4
Door sensor (reed
switch); Additional sensor
(to input of the controller);
Additional equipment
(to output of the
controller)
30 Twin cable 0,2
RAMCRO SS22AF-T
2×0,22
CQR-2
5 RC-panel 40 Eight-core cable 0,2 CQR CABS8 8×0,22c
7 OD – Lock 30 Twin cable 0,75 PVC 2×0,75 two-color
8 OD – Turnstile 30 Six-core cable 0,2 CQR CABS6 6×0,22c
6The power to card capture reader is supplied by a separate cable: flat cord with sheath and outer
sheath of PVC 2×0.75.
15

Assembly & Operation Manual
8.2 Installation order
Connection to the controller is performed in accordance with scheme shown on
Figures 4 – 16 with the use of cables from Table 2. The position of connecting blocks on
the controller’s board is presented on Figure 2.
Installation of connected devices (turnstiles, locks, power supply, etc.) is performed
according to the instructions given in technical documents of corresponding devices.
Keep the following sequence of actions during controller installation:
1. Unpack the box and check completeness of package contents according to Sect. 4.1.
Make sure that the equipment is not mechanically damaged.
2. Define the place for installation of the controller. Location of the controller shall comply
with operational conditions. When choosing a location, make sure that it will be
convenient to perform service maintenance of the controller.
Attention!
Do not install the controller at a distance less than 1 m from a source of
electromagnetic interference.
3. Mark and drill holes in the surface to install the controller and connect cables in
accordance with Figure 3. Lay and mount communication cables, power cables and
Ethernet cables to the location.
Figure 3. Marking of holes for the controller installation
16

C-01 Controller
Figure 4. Common scheme of connections
4. Fix the controller with three screws through holes in the controller housing (use dowels
from the delivery set if necessary).
5. Select the way to set IP-address of the controller (Sect. 8.3).
6. Connect Ethernet cable to X2 connector of the top board of the controller.
7. Connect PS, connect cable from PS XT4connecting block of the controller in
accordance with the scheme, shown on Figure 4.
Important:
The order of power connection of the controller via PoE-splitter is described in
Appendix 2.
8. Connect necessary equipment to interfaces of readers and scanners (Sect. 8.4).
17

Assembly & Operation Manual
9. Connect the rest of necessary equipment. Follow the next recommendations in
connection of:
electromechanical (electromagnetic) locks and latches (Sect. 8.5);
turnstile (Sect. 8.6);
OD VCP (boom gates, gates etc.) (Sect. 8.7);
RC-panel (WRC device) (Sect. 8.8);
emergency unlock devices (passage emergency unlock) Fire Alarm (Sect. 8.9);
other optional equipment (Sect. 8.10).
Important:
Installation order of external verifying devices to the controller is described in
Appendix 1 (an example of the alcohol detection device).
8.3 Method for obtaining an IP-address
The method of obtaining an IP-address of the controller is defined by installation or
removing of the jumper on XP1 connector of the IP-Stile controller top board. Location of
the connector is indicated on the Figure 1.
Attention!
Installation or removal of the jumper has to be done only when the controller is
switched off.
The following methods of obtaining an IP-address are available (see Table 3):
1. User mode. Jumper is removed.
When IP-address (Gateway, Subnet mask) has not been changed by user, the
controller is operating with default factory settings: IP-address and MAC-address
are indicated in the certificate of IP-Stile and on the controller board; subnet mask
255.0.0.0.
When IP-address (Gateway, Subnet mask) has been changed by user, then the
controller will be operating with new settings without rebooting.
Important:
It is possible to configure network parameters of the controller via Web-interface or
by using the SW. In this case the controller and the PC should work
in the same subnet.
2. «IP MODE». Jumper is in 1–2 position.
Operation in networks with dynamic allocation of IP addresses, the controller
obtains IP-address (Gateway, subnet mask) from DHCP-server.
3. «IP DEFAULT». Jumper is in 2–3 position.
Controller is operating with factory settings of IP-address and MAC-address are
indicated in IP-Stile certificate and on the controller board; subnet mask
255.0.0.0.
authentication (password for access to the controller) is switched off when the
jumper is installed, it is possible to set a new password.
Important:
User IP-address settings (gateway, subnet mask), will be saved in the controller
memory if they were applied while switching to «IP DEFAULT» mode. Switching
back to user mode (jumper is removed) will force controller to use setting s for
operation.
18

C-01 Controller
Table 3. Variants of jumper installation on XP1 connector
№Jumper position on XP1 connector IP-address obtaining method
1 User mode
2 «IP MODE»
3 «IP DEFAULT»
8.4 Connection of readers / scanners
Attention!
When connecting to several interfaces simultaneously the total current consumption
of all connected readers and/or scanners must not exceed: 1.5 A for +5 V power
supply voltage and 0.5 A for +12 V power supply voltage.
8.4.1 Connecting readers by using Wiegand interface
Readers should be connected correspondingly to the contacts of XT5 connector in
accordance with general connection scheme (Figure 4). It is necessary to select Wiegand
value for «Communication interface» parameter (see Figure 6).
Important:
It is possible to use +12 V and GND contacts of XT5 terminal block,the total current
consumption of two connected readers must not 0.5 A.
8.4.2 Connecting scanners by using RS-232 interface
Scanners should be connected correspondingly to the contacts of DB9 (RS-232)
connector that is located on the housing of the controller (see Figure 5). DB9 left connector
should be connected to X1 connector located on the bottom board of the controller, right
connector – to X2 connector (see Figure 4).
Figure 5. Location of DB-9 (RS-232) connectors on the housing
Parameter values of scanners that are connected via RS-232 interface:
speed – 9600 bauds;
parity check – no;
flow control – no;
8-bit data, 1 stop-bit, 1 start-bit.
19
Table of contents
Other PERCo Controllers manuals
Popular Controllers manuals by other brands
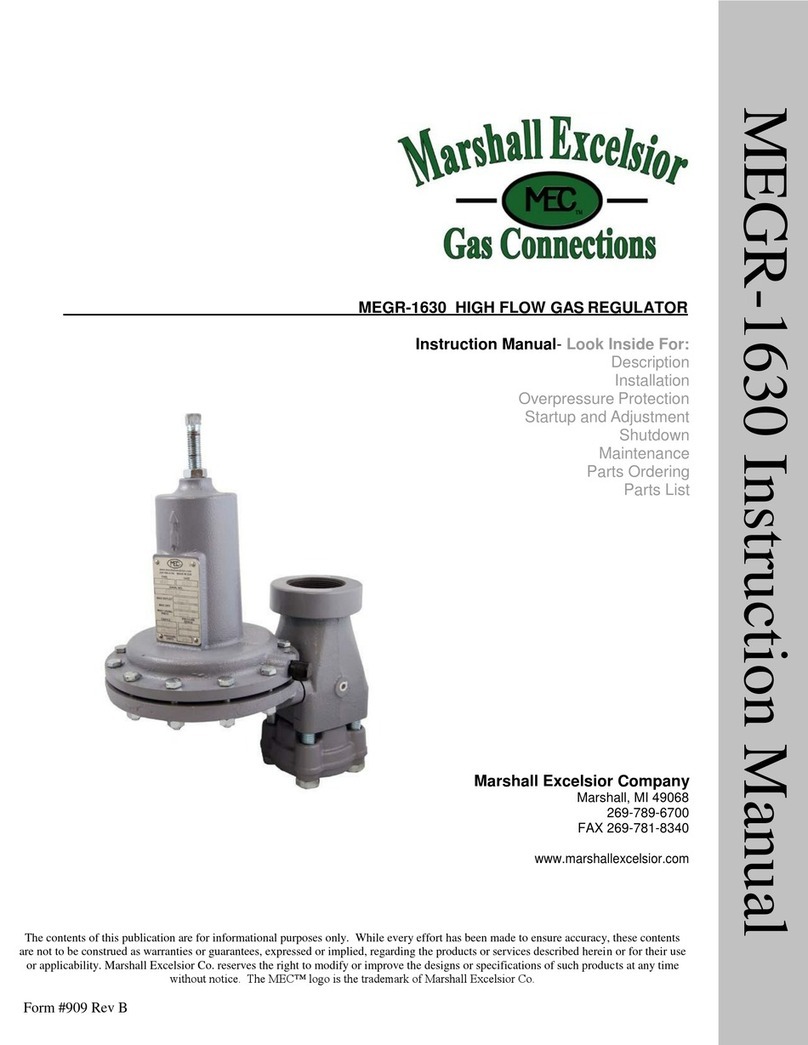
Marshall Excelsior
Marshall Excelsior MEGR-1630 instruction manual
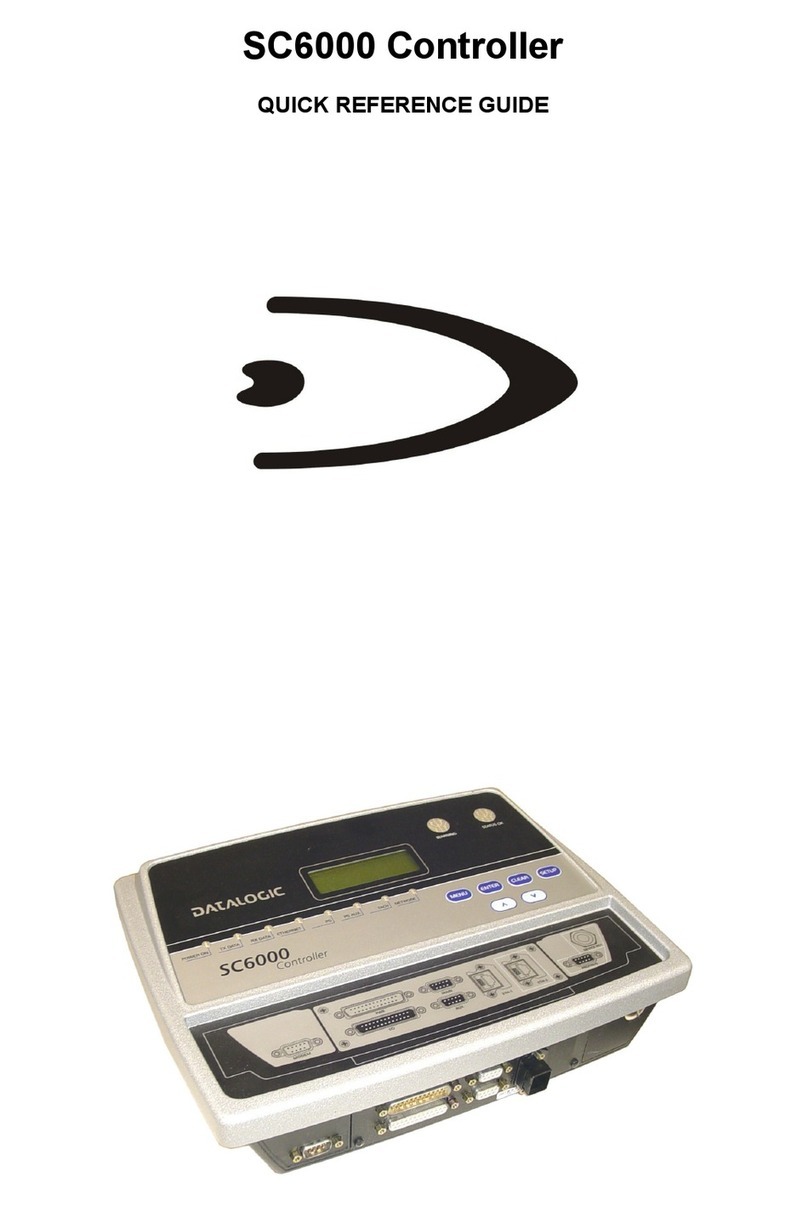
Datalogic
Datalogic Controller SC6000 Quick reference guide

Multiplex
Multiplex ROXXY BL-Control 780 S-BEC operating instructions
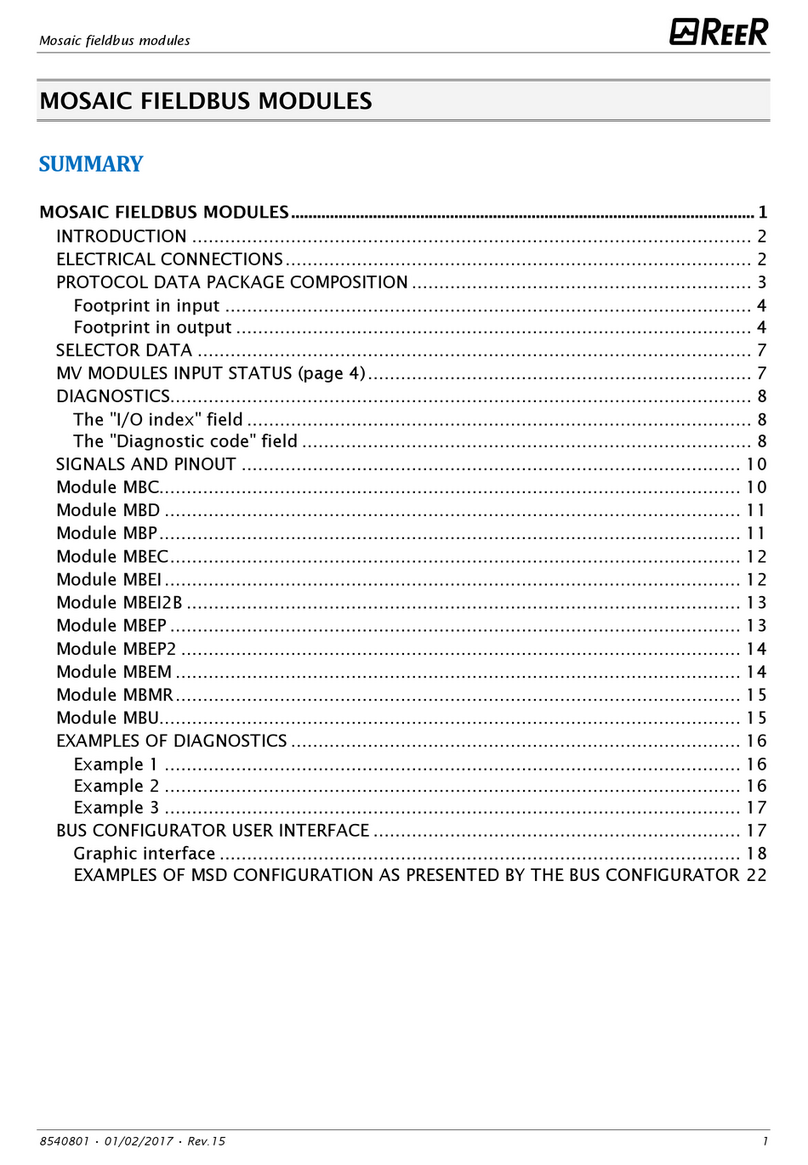
Reer
Reer Mosaic Series manual
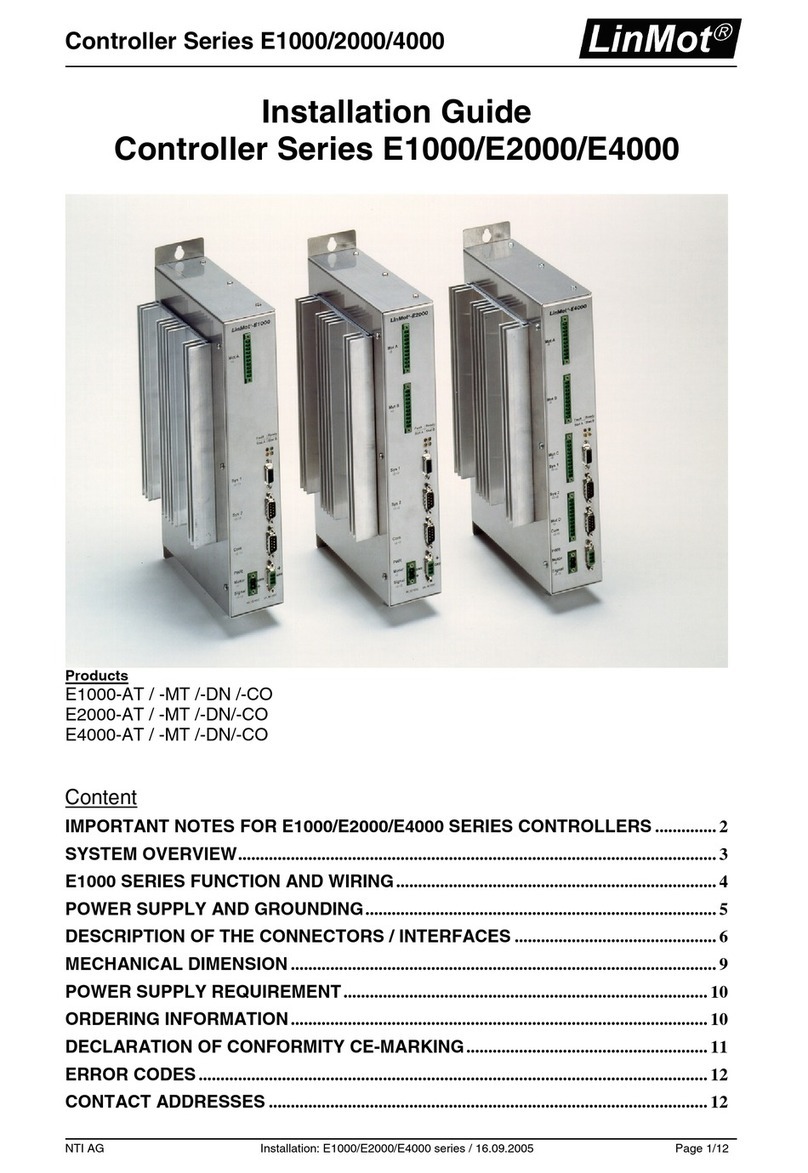
NTI AG
NTI AG LinMot E1000 Series installation guide

Linear Technology
Linear Technology DC1588A Demo Manual