Pfeiffer Vacuum ASI 35 User manual

OPERATING INSTRUCTIONS
EN
Translation of the Original
COMMUNICATION INTERFACES
Leak detection

Disclaimer of liability
These operating instructions describe all models and variants of your product. Note that your
product may not be equipped with all features described in this document. Pfeiffer Vacuum
constantly adapts its products to the latest state of the art without prior notice. Please take
into account that online operating instructions can deviate from the printed operating
instructions supplied with your product.
Furthermore, Pfeiffer Vacuum assumes no responsibility or liability for damage resulting from
the use of the product that contradicts its proper use or is explicitly defined as foreseeable
misuse.
Copyright
This document is the intellectual property of Pfeiffer Vacuum and all contents of this
document are protected by copyright. They may not be copied, altered, reproduced or
published without the prior written permission of Pfeiffer Vacuum.
We reserve the right to make changes to the technical data and information in this document.
2/154

Table of contents
1 About this manual 7
1.1 Validity 7
1.1.1 Products concerned 7
1.1.2 Applicable documents 10
1.2 Target group 10
1.3 Conventions 10
1.3.1 Instructions in the text 10
1.3.2 Abbreviations 10
1.3.3 Proof of trademark 10
2 Safety 11
2.1 General safety information 11
2.1.1 Safety instructions 11
2.1.2 Precautions 12
2.2 Intended use 12
2.3 Foreseeable misuse 12
2.4 Electrostatic Discharge (ESD) Information 12
3 Profibus 14
3.1 Connection 14
3.1.1 Features of the Profibus cable 14
3.1.2 Profibus connection of the detector to the PLC 14
3.1.3 Profibus connection interface 14
3.2 Setting 15
3.2.1 Set the leak detector 15
3.2.2 GSD file 16
3.2.3 PLC configuration 16
3.3 Use 16
3.3.1 Reading data (from the leak detector to the PLC) 16
3.3.2 Writing data (from PLC to leak detector) 17
3.3.3 List of parameters 17
3.3.4 Special format details 19
3.3.5 ZSW status word (Input) 21
3.3.6 STW command word (Output) 22
3.3.7 Use examples 22
4 Profinet 25
4.1 Connection 25
4.1.1 Features of the Profinet cable 25
4.1.2 Profinet connection of the detector to the PLC 25
4.1.3 Profinet connection interface 25
4.2 Setting 26
4.2.1 Set the leak detector 27
4.2.2 GSDML file 27
4.2.3 PLC configuration 27
4.3 Use 28
5 EtherNet/IP 29
5.1 Connection 29
5.1.1 EtherNet/IP cable characteristics 29
5.1.2 EtherNet/IP connection from detector to the PLC 29
5.1.3 EtherNet/IP connection interface 29
5.2 Setting 30
5.2.1 Leak detector parameters 30
5.2.2 EDS file 31
5.2.3 PLC configuration 31
Table of contents
3/154

5.3 Use 32
5.3.1 Coding 32
6 EtherCAT 33
6.1 Connection 33
6.1.1 Features of the EtherCAT cable 33
6.1.2 EtherCAT connection from the detector to the PLC 33
6.1.3 EtherCAT connection interface 33
6.2 Setting 34
6.2.1 Set the leak detector 35
6.2.2 ESI file 35
6.2.3 PLC configuration 35
6.3 Use 36
7 37-pin inputs/outputs 37
7.1 Connection 37
7.1.1 Features of the 37-pin I/O cable 37
7.1.2 37-pin I/O connection interface 37
7.2 Setting 38
7.2.1 Types of contact: activation mode 38
7.2.2 Selection of the default configuration (Select Default Config.) 38
7.2.3 Other Configurations (Other Configurations) 39
7.3 Use 44
7.3.1 Analog Output 44
7.3.2 Formulas 46
7.3.3 Digital input 48
7.3.4 Digital outputs (Digital Output) 50
7.3.5 Digital transistor outputs (Digital Transistor Output) 52
7.3.6 DS-P Digital relay outputs (Digital Relay Output) 53
7.3.7 TX Digital relay outputs (Digital Relay Output) 53
7.3.8 Internal 24 VDC or external 24 VDC power supply 54
7.4 Quick View 55
7.5 Save 56
7.6 Loading a configuration (Load Config from SD Card) 56
8 USB 57
8.1 Connection 57
8.1.1 Features of the USB cable 57
8.1.2 USB connection interface 57
8.2 Setting 57
8.2.1 Set the leak detector 57
8.2.2 Driver installation 58
9 Ethernet 60
9.1 Connection 60
9.1.1 Features of the Ethernet cable 60
9.1.2 Ethernet connection interface 60
9.2 Setting 60
9.2.1 Set the leak detector 60
9.2.2 MAC address 61
9.2.3 Program and driver installation 61
9.2.4 Uninstall 63
10 15-pin inputs/outputs 64
10.1 Connection 64
10.1.1Features of the 15-pin I/O cable 64
10.1.215-pin I/O connection interface 66
10.2 Setting 66
10.3 Formulas 67
Table of contents
4/154

11 RS-232 serial link 69
11.1 Connection 69
11.1.1Features of the RS-232 serial link cable 69
11.1.2RS-232 serial link interface 69
11.2 RS-232 70
11.3 Basic mode 71
11.3.1Standard basic mode 71
11.3.2Spreadsheet basic mode 72
11.3.3Available commands 73
11.4 Advanced mode (Advanced) 73
11.4.1Protocol 73
11.4.2Available commands 73
11.5 Short commands 73
11.6 Long commands 74
11.6.1Different types of long commands 74
11.6.2Discharge protocol for long commands 74
11.6.3Quick list of commands 75
11.6.4List of immediate commands 83
11.6.5List of commands on request 84
11.6.6List of commands with parameters 102
11.6.7Additional information 113
11.7 List of messages 116
11.8 Data export mode 117
11.9 HLT5xx protocol 118
11.10 HLT2xx protocol 128
12 Installation 133
12.1 Compatibility table 133
12.2 Receipt of the product 134
12.3 ASI 35 134
12.3.1Removing the interface in place - ASI 35 134
12.3.2Installation of the new interface - ASI 35 136
12.4 ASM 340 138
12.4.1Removal of the interface in place - ASM 340 138
12.4.2Installation of the new interface - ASM 340 139
12.5 ASM 390-392 141
12.5.1Removal of the interface in place- ASM 390/392 141
12.5.2Installation of the new interface - ASM 390/392 143
12.6 ASM 306S 145
12.6.1Removal of the communication in place - ASM 306S 145
12.6.2Installation of the new interface - ASM 306S 146
13 Additional equipment 149
13.1 ASM 142 type I/O cable 149
13.2 ASM 182 type I/O cable 149
13.3 Type HLT I/O module 149
13.4 Type ASI 20 MD I/O module 149
13.5 Type 2xxx or 3xxx I/O module 149
14 Malfunctions 150
15 Decommissioning 151
15.1 Disposal 151
15.2 Electrical and Electronic Equipment (EEE) 151
16 Spare parts 152
16.1 ASM 340 152
16.2 ASM 390/392 152
Table of contents
5/154

1 About this manual
IMPORTANT
Read carefully before use.
Keep the manual for future consultation.
1.1 Validity
These operating instructions are a customer document of Pfeiffer Vacuum. The operating instructions
describe the functions of the named product and provide the most important information for the safe use
of the device. The description is written in accordance with the valid directives. The information in these
operating instructions refers to the product's current development status. The document shall remain
valid provided that the customer does not make any changes to the product.
1.1.1 Products concerned
This document applies to products with the following part numbers:
ASI 35
Description Part number
ASI 35 electronic box equipped - 37-pin I/O - RS-232 - USB 1) 123057S
ASI 35 electronic box equipped - 37-pin I/O - RS-232 - USB - Ether-
net 1)
123058S
ASI 35 electronic box equipped - 15-pin I/O - RS-232 - Profinet 1) 126914S
ASI 35 electronic box equipped - 15-pin I/O - RS-232 - Profibus 1) 126915S
ASI 35 electronic box equipped - 15-pin I/O - RS-232 - EtherCAT 1) 129996S
ASI 35 electronic box equipped - 15-pin I/O - RS-232 - EtherNet/IP 1) 129997S
Accessory - ASI 35 communication interface kit - 15-pin I/O - RS-232 -
EtherCAT
130190
Accessory - ASI 35 communication interface kit - 15-pin I/O - RS-232 -
EtherNet/IP
130191
Accessory - ASI 35 communication interface kit - 15-pin I/O - RS-232 -
Profinet
130192
Accessory - ASI 35 communication interface kit - 15-pin I/O - RS-232 -
Profibus
130193
Accessory - ASI 35 communication interface kit - 37-pin I/O - RS-232 -
USB - Ethernet
130195
Accessory - ASI 35 communication interface kit - 37-pin I/O - RS-232 -
USB
130196
ASI 35 - 37-pin I/O - RS-232 - USB Sxxx0x02MM9A
ASI 35 - 37-pin I/O - RS-232 - USB - Ethernet Sxxx0x04MM9A
ASI 35 - 15-pin I/O - RS-232 - Profibus Sxxx0x08MM9A
ASI 35 - 15-pin I/O - RS-232 - Profinet Sxxx0x09MM9A
ASI 35 - 15-pin I/O - RS-232 - EtherNet/IP Sxxx0x0AMM9A
ASI 35 - 15-pin I/O - RS-232 - EtherCAT Sxxx0x0CMM9A
1) Contact us to check the compatibility of your leak detector with this accessory
ASM 310
Description Part number
ASM 310 - 15-pin I/O - RS-232 BSAA0200MM9A
ASM 306S
Description Part number
ASM 306S - 15-pin I/O - RS-232 RSAS0xA0MM9A
ASM 306S - 37-pin I/O - RS-232 - USB RSAS00A2MM9A
About this manual
7/154

Description Part number
ASM 306S - 37-pin I/O - RS-232 - USB - Ethernet RSAS00A4MM9A
ASM 306S - 15-pin I/O - RS-232 - Profibus RSAS0xA8MM9A
ASM 306S - 15-pin I/O - RS-232 - Profinet RSAS0xA9MM9A
Accessory - ASM 306S communication interface kit - 37-pin I/O -
RS-232 - USB
127258S
Accessory - ASM 306S communication interface kit - 37-pin I/O -
RS-232 - USB - Ethernet
127256S
Accessory - ASM 306S communication interface kit - 15-pin I/O -
RS-232
127254S
Accessory - ASM 306S communication interface kit - 15-pin I/O -
RS-232 - Profibus
127257S
Accessory - ASM 306S communication interface kit - 15-pin I/O -
RS-232 - Profinet
127255S
ASM 340 Wet
Description Part number
ASM 340 Wet - 15-pin I/O - RS-232 JSVA02A0Mx9x
ASM 340 Wet - 37-pin I/O - RS-232 - USB JSVA02A2Mx9x
ASM 340 Wet - 37-pin I/O - RS-232 - USB - Ethernet JSVA02A4Mx9x
ASM 340 Wet - 15-pin I/O - RS-232 - Profibus JSVA02A8Mx9x
ASM 340 Wet - 15-pin I/O - RS-232 - Profinet JSVA02A9Mx9x
ASM 340 Wet - 15-pin I/O - RS-232 - EtherNet/IP JSVA02AAMx9x
ASM 340 Wet - 15-pin I/O - RS-232 - EtherCAT JSVA02ACMx9x
Accessory - ASM 340 communication interface kit - 37-pin I/O -
RS-232 - USB
121350S
Accessory - ASM 340 communication interface kit - 37-pin I/O -
RS-232 - USB - Ethernet
121352S
Accessory - ASM 340 communication interface kit - 15-pin I/O -
RS-232
121349S
Accessory - ASM 340 communication interface kit - 15-pin I/O -
RS-232 - EtherCAT
129995S
Accessory - ASM 340 communication interface kit - 15-pin I/O -
RS-232 - EtherNet/IP
129994S
Accessory - ASM 340 communication interface kit - 15-pin I/O -
RS-232 - Profibus
127447S
Accessory - ASM 340 communication interface kit - 15-pin I/O -
RS-232 - Profinet
127448S
ASM 340 Dry
Description Part number
ASM 340 Dry - 15-pin I/O - RS-232 KSBA00A0MM9A
ASM 340 Dry - 37-pin I/O - RS-232 - USB KSBA0xA2MM9A
ASM 340 Dry - 37-pin I/O - RS-232 - USB - Ethernet KSBA00A4MM9A
ASM 340 Dry - 15-pin I/O - RS-232 - Profibus KSBA00A8MM9A
ASM 340 Dry - 15-pin I/O - RS-232 - Profinet KSBA00A9MM9A
ASM 340 Dry - 15-pin I/O - RS-232 - EtherNet/IP KSBA00AAMM9A
ASM 340 Dry - 15-pin I/O - RS-232 - EtherCAT KSBA00ACMM9A
Accessory - ASM 340 communication interface kit - 37-pin I/O -
RS-232 - USB
121350S
Accessory - ASM 340 communication interface kit - 37-pin I/O -
RS-232 - USB - Ethernet
121352S
Accessory - ASM 340 communication interface kit - 15-pin I/O -
RS-232
121349S
Accessory - ASM 340 communication interface kit - 15-pin I/O -
RS-232 - EtherCAT
129995S
About this manual
8/154

Description Part number
Accessory - ASM 340 communication interface kit - 15-pin I/O -
RS-232 - EtherNet/IP
129994S
Accessory - ASM 340 communication interface kit - 15-pin I/O -
RS-232 - Profibus
127447S
Accessory - ASM 340 communication interface kit - 15-pin I/O -
RS-232 - Profinet
127448S
ASM 340 Integrable
Description Part number
ASM 340 Integrable - 15-pin I/O - RS-232 MSXA02A0MM9A
ASM 340 Integrable - 37-pin I/O - RS-232 - USB MSXA02A2MM9A
ASM 340 Integrable - 37-pin I/O - RS-232 - USB - Ethernet MSXA02A4MM9A
ASM 340 Integrable - 15-pin I/O - RS-232 - Profibus MSXA02A8MM9A
ASM 340 Integrable - 15-pin I/O - RS-232 - Profinet MSXA02A9MM9A
ASM 340 Integrable - 15-pin I/O - RS-232 - EtherNet/IP MSXA02AAMM9A
ASM 340 Integrable - 15-pin I/O - RS-232 - EtherCAT MSXA02ACMM9A
Accessory - ASM 340 communication interface kit - 37-pin I/O -
RS-232 - USB
121350S
Accessory - ASM 340 communication interface kit - 37-pin I/O -
RS-232 - USB - Ethernet
121352S
Accessory - ASM 340 communication interface kit - 15-pin I/O -
RS-232
121349S
Accessory - ASM 340 communication interface kit - 15-pin I/O -
RS-232 - EtherCAT
129995S
Accessory - ASM 340 communication interface kit - 15-pin I/O -
RS-232 - EtherNet/IP
129994S
Accessory - ASM 340 communication interface kit - 15-pin I/O -
RS-232 - Profibus
127447S
Accessory - ASM 340 communication interface kit - 15-pin I/O -
RS-232 - Profinet
127448S
ASM 390
Description Part number
ASM 390 - 15-pin I/O - RS-232 CSGB01G0MM9x
ASM 390 - 37-pin I/O - RS-232 - USB CSGB01G2MM9x
ASM 390 - 37-pin I/O - RS-232 - USB - Ethernet CSGB01G4MM9x
Accessory - ASM 390/392 communication interface kit - RS-232 - 37-
pin I/O - USB
126254S
Accessory - ASM 390/392 communication interface kit - 37-pin I/O -
RS-232 - USB - Ethernet
126255S
Accessory - ASM 390/392 communication interface kit - 15-pin I/O -
RS-232
126253S
ASM 392
Description Part number
ASM 392 - 15-pin I/O - RS-232 ESGB02G0MM9x
ASM 392 - 37-pin I/O - RS-232 - USB ESGB02G2MM9x
ASM 392 - 37-pin I/O - RS-232 - USB - Ethernet ESGB02G4MM9x
Accessory - ASM 390/392 communication interface kit - 37-pin I/O -
RS-232 - USB
126254S
Accessory - ASM 390/392 communication interface kit - 37-pin I/O -
RS-232 - USB - Ethernet
126255S
Accessory - ASM 390/392 communication interface kit - 15-pin I/O -
RS-232
126253S
About this manual
9/154

1.1.2 Applicable documents
Useful documents for the using the options and/or accessories, and for product maintenance are as fol-
lows:
Document Part number 1)
User manual - ASI 35 leak detector 127801
User manual - ASM 310 leak detector 114916 (ASM 310 model
V1/V2)
128864 (ASM 310 model
V3)
User manual - ASM 306S leak detector 127443
User manual - ASM 340 leak detector 121762 (ASM 340 model
V1)
128863 (ASM 340 model
V2)
User manual - ASM 390/392 leak detector 126348
User manual - I/O module type HLT 122864
User manual - I/O module type ASI 20 MD 123358
User manual - I/O module type 2xxx or 3xxx 123359
1) also available at www.pfeiffer-vacuum.com
1.2 Target group
This user manual is intended for all persons in charge of transport, installation, commissioning/decom-
missioning, use, maintenance or storage of the product.
The work described in this document must only be carried out by persons with suitable technical training
(specialized staff) or persons who have undergone Pfeiffer Vacuum training.
1.3 Conventions
1.3.1 Instructions in the text
Usage instructions in the document follow a general structure that is complete in itself. The required ac-
tion is indicated by an individual step or multi-part action steps.
Individual action step
A horizontal, solid triangle indicates the only step in an action.
►This is an individual action step.
Sequence of multi-part action steps
The numerical list indicates an action with multiple necessary steps.
1. Step 1
2. Step 2
3. ...
1.3.2 Abbreviations
I/O Input/Output
[XXXXXX] The control panel menus and parameters are shown in bold between square brackets.
Example: [Advanced] [Input/Output] to select the Input/Output menu.
The screenshots are given as an example only. They can vary according to the user setting.
1.3.3 Proof of trademark
●Profibus® is a registered trademark of Profibus Nutzerorganisation e.V.
●Profinet® is a registered trademark of Profibus Nutzerorganisation e.V.
●EtherCAT® is a registered trademark of Beckhoff Automation GmbH, Germany.
●EtherNet/IP™ is a registered trademark licensed by ODVA, Inc.
About this manual
10/154

2 Safety
2.1 General safety information
The following 4 risk levels and 1 information level are taken into account in this document.
DANGER
Immediately pending danger
Indicates an immediately pending danger that will result in death or serious injury if not observed.
►Instructions to avoid the danger situation
WARNING
Potential pending danger
Indicates a pending danger that could result in death or serious injury if not observed.
►Instructions to avoid the danger situation
CAUTION
Potential pending danger
Indicates a pending danger that could result in minor injuries if not observed.
►Instructions to avoid the danger situation
NOTICE
Danger of damage to property
Is used to highlight actions that are not associated with personal injury.
►Instructions to avoid damage to property
Notes, tips or examples indicate important information about the product or about this docu-
ment.
2.1.1 Safety instructions
All safety instructions in this document are based on the results of the risk assessment carried out in
accordance with Low-Voltage Directive 2014/35/EU regarding electrical safety. Where applicable, all life
cycle phases of the product were taken into account.
WARNING
Risk of electric shock in case of contact with products that are not electrically isolated
When powering off _mains switch to O_, certain components located between the mains connection
and the circuit breaker will still contain an electric charge (live). There is a risk of electric shock in
case of contact.
►Make sure that the mains connection is always visible and accessible so that it can be unplugged
at any time.
►Disconnect the mains cable from the electrical network before working on the product.
►Wait for the control panel screen to turn off completely before working on the product and/or re-
moving the cover(s).
NOTICE
Risk of electromagnetic disturbance
Voltages and currents can induce a multitude of electromagnetic fields and interference signals. In-
stallations that do not comply with the EMC regulations can interfere with other equipment and the
environment in general.
►Use shielded cables and connections for the interfaces in interference-prone environments.
Safety
11/154

NOTICE
Safety extra-low voltage circuits
The remote control circuits are equipped with dry contact outputs (30 V - 40 A max). Overvoltages
and overcurrents can result in internal electrical damage. Users must observe the following wiring
conditions:
►Connect these outputs in compliance with safety extra-low voltage (SELV) circuit rules and safety
standards.
►The voltage applied to these contacts should be less than 30 V and the current less than 40 A.
2.1.2 Precautions
Duty to provide information on potential dangers
The product holder or user is obliged to make all operating personnel aware of dangers
posed by this product.
Every person who is involved in the installation, operation or maintenance of the product
must read, understand and adhere to the safety-related parts of this document.
Infringement of conformity due to modifications to the product
The Declaration of Conformity from the manufacturer is no longer valid if the operator
changes the original product or installs additional equipment.
●Following the installation into a system, the operator is required to check and re-evalu-
ate the conformity of the overall system in the context of the relevant European Direc-
tives, before commissioning that system.
Only qualified personnel trained in safety regulations (EMC, electrical safety, chemical pollution) are au-
thorized to carry out the installation and maintenance described in this manual. Our service centers can
provide the necessary training.
►Follow the safety and accident prevention requirements (see chapter “Safety instructions”).
►Do not turn on the product if the cover is not in place.
2.2 Intended use
The communication interface is intended to be integrated into a leak detector from the manufacturer
Pfeiffer Vacuum (see chapter “Products concerned”).
The communication interface enables the leak detector to communicate with a PLC (at the customer's
expense).
The communication interface must be used in conjunction with the leak detector operating instructions
(see chapter "Applicable documents").
2.3 Foreseeable misuse
Misuse of the product will render the warranty and any claims void.
Any use, whether intended or not, that diverges from the uses already mentioned will be treated as non-
compliant.
2.4 Electrostatic Discharge (ESD) Information
Electrostatic discharge (ESD) is recognized as a potential hazard to semiconductors and integrated cir-
cuits.
This is to avoid faults in the electronic boards integrated into our products.
ESDs reduce the useful life of electronic boards. There are no immediate consequences when assem-
bling the products, but premature aging of the components can be observed.
To protect products against the adverse effects of ESD, measures must be taken and applied at all
times.
Safety
12/154

►Only handle devices in an EPA.
–An EPA is an ESD protected area. In an EPA, all surfaces, objects, people and devices are
held at the same potential.
►Equip anyone handling a product during maintenance with ESD protection.
►Store the electronic boards before integration on an ESD vinyl surface until it is transferred to the
EPA.
►Move a device from one EPA to another only in ESD protective packaging.
►Unpack and integrate the cable harnesses in direct contact with the electronic boards by a person
equipped with a closed ESD gown and a bracelet connected to the EPA.
Safety
13/154

3 Profibus
3.1 Connection
NOTICE
Risk of electromagnetic disturbance
Voltages and currents can induce a multitude of electromagnetic fields and interference signals. In-
stallations that do not comply with the EMC regulations can interfere with other equipment and the
environment in general.
►Use shielded cables and connections for the interfaces in interference-prone environments.
3.1.1 Features of the Profibus cable
►Use a cable (not included) that meets Profibus DP cable standards.
–9-pin male D-Sub connector for IP 20
–Impedance: 135–165 Ω
–Capacity: < 30 pF/m
–Resistance per unit length: 110 Ω /km
–Diameter: 0.64 mm
–Section > 0.34 mm2
–Type of cable: Shielded twisted pair
3.1.2 Profibus connection of the detector to the PLC
1. Switch off the leak detector before connecting the cable (see chapter “Power down” in the leak
detector maintenance instructions).
2. Connect the cable:
–to the leak detector
–to the customer’s installation.
3. Power on the detector.
4. Create the digital connection, using the PLC software used, between the leak detector and the
PLC.
12
Example of Profibus connection with Siemens TIA Portal software
1 PLC_1: PLC 2 PV-LD: Name of the default leak detector
3.1.3 Profibus connection interface
Switch off the leak detector before connecting the cable (see chapter “Power down” in the leak detector
maintenance instructions).
Profibus
14/154

OP ST
PROFIBUS DP-V1INPUTS/OUTPUTS SERIAL
21
3
1 OP indicator: network status (see details below) 3 9-pin female D-Sub Profibus connec-
tor
2 ST indicator: AnyBus module status (see details below)
Details of OP indicator (network status)
Indicator state Indication
Off Not online / No power
Green Online, data exchange
Flashing Green Online, clear
Flashing Red (1 flash) Parameterization error
Flashing Red (2 flashes) PROFIBUS Configuration error
Details of ST indicator (AnyBus module status)
Indicator state Indication Comments
Off Not initialized Anybus state = SETUP or NW_INIT
Green Initialized Anybus module has left the NW_INIT state
Flashing Green Initialized, diagnostic event(s) present Extended diagnostic bit is set
Red Exception error Anybus state = EXCEPTION
3.2 Setting
Depending on the leak detector model, some functions are not available.
The functions available depend on the leak detector model.
3.2.1 Set the leak detector
On the Settings screen, press [Advanced] [Input/Output] [Serial link #2].
Type Set the type of ‘AnyBus’ connection.
On the Settings screen, press [Advanced] [Input/Output] [Serial link #2] [Settings].
Mode Indicate the type of bus. - Profibus
Status Indicate the Fieldbus module sta-
tus
Setup Initialization of the Fieldbus module.
Nw Init Initialization of the Fieldbus network.
Wait Process Wait for connections to the PLC.
Proc. Active In communication with the PLC.
IDLE Placed in a safe state following a non-
compliant action.
Error Problem occurred on the network.
Exception Critical error with the Fieldbus module.
The leak detector must be restarted to
reinitialize the module.
Address ● Set the address between 2 and 126.
─ This address can be configured, in this menu, only if the code wheels of the inter-
face board are at "zero".
On the Settings screen, press [Advanced] [Input/Output] [Profibus].
Type Set the ‘Adixen’ type.
Connected Indicates the module status (yes).
Profibus
15/154

On the Settings screen, press [Advanced] [Input/Output] [Profibus].
Address Indicates the hexadecimal address of the module.
Dx/Det ● Dx (OP indicator): indicates the network status (yes/no).
● Det (ST indicator): indicates the Fieldbus module (yes).
3.2.2 GSD file
This file must be used with the PLC software. It defines the functions of the leak detector using the Pro-
fibus.
The Profibus file “PVSM10F5.gsd” is provided in the leak detector user manual (USB drive).
3.2.3 PLC configuration
►Configure all I/Os, as in the example below.
Configuration example with Siemens TIA Portal software
3.3 Use
3.3.1 Reading data (from the leak detector to the PLC)
Slot Wor
d
Byte 1) Parame-
ter
Description
1 1 0 – 1 PKE Parameters identified
● Bit 0 – 10: Parameter number (see chapter « List of param-
eters »)
● Bit 11: Reserved
● Bit 12 – 15: Type of command
─ 0: No response
─ 1: Value of the parameter transmitted (word)
─ 2: Value of the parameter transmitted (double word)
─ 7: The command cannot be executed (with a number
error)
─ 8: Not authorized for the PKW interface
─ 15: Depending on the order index, only certain reply in-
dexes are possible.
2 2 2 – 3 IND Not used
3 3 –
4
4 – 5 –
6 – 7
PWE Value of the parameter
● Value requested
1) Coding with the Little-Endian convention
Profibus
16/154

Slot Wor
d
Byte 1) Parame-
ter
Description
4 5 8 – 9 ZSW Status word
● (see chapter « ZSW status word (Input) »)
5 6 10 – 11 HSW Leak rate value
● (see chapter « Special format details »)
Current leak rate value read by the leak detector
1) Coding with the Little-Endian convention
3.3.2 Writing data (from PLC to leak detector)
Slot Wor
d
Byte 1) Parame-
ter
Description
6 1 0 – 1 PKE Parameters identified
● Bit 0 – 10: Parameter number (see chapter « List of param-
eters »)
● Bit 11: Reserved
● Bit 12 – 15: Type of command
─ 1: Querying of the parameter
─ 2: Change to the parameter value (word)
─ 3: Change to the parameter value (double word)
7 2 2 – 3 IND Not used
8 3 –
4
4 – 5 –
6 – 7
PWE Value of the parameter
To be sent to the detector if the type of PKE parameter is 2 or
3.
9 5 8 – 9 STW Status word
● (see chapter « STW command word (Output) »)
10 6 10 – 11 HSW Not used
1) Coding with Little-Endian convention
3.3.3 List of parameters
The parameters available depend on the leak detector model and interface installed.
No. Parameter Type Access 2)
1Status 0: see details of status 0 U16 R
2 Status 2: not used - -
3Status 1: see details of status 1 U16 R
4 Error 1 U8 R
5 Error 2 U8 R
6 Error 3 U8 R
7 Warning 1 U8 R
8 Warning 2 U8 R
9Leak rate 1) U16 R
10 Inlet pressure 1) U16 R
11 Triode Pressure 1) U16 R
12 Not used - -
13 Number of hours of the leak detector U16 R
14 Number of hours of filament #1 U16 R
15 Number of hours of filament #2 U16 R
1) See chapter « Special format details »
2) Access:
● R: Read only
● W: Write only
● R/W: Read and write
Profibus
17/154

No. Parameter Type Access 2)
16 Cycles counter 1) U16 R
17 Number of hours of backing pump U16 R
18 Number of hours of secondary pump #1 U16 R
19 Number of hours of secondary pump #2 U16 R
20 Number of hours of secondary pump #3 U16 R
21 Status 3: see details of status 3 U32 R
50 Reject set point in hard vacuum test 1) U16 RW
51 Reject point #2 1) U16 RW
52 Reject point #3 1) U16 RW
53 Reject point #4 1) U16 RW
54 Reject point #5 1) U16 RW
55 Pressure set point #1 1) U16 RW
56 Pressure set point #2 1) U16 RW
57 Sniffing reject point 1) U16 RW
58 Probe clogged threshold 1) U16 RW
59 Correction coefficient in hard vacuum test 1) U16 RW
60 Sniffing correction coefficient 1) U16 RW
61 Sensitivity coefficient (in progress) U16 R
62 External pressure 1) U16 R
63 Command 0: see details of command 0 U16 W
65 Tracer gas (Helium 4/Helium, Helium 3/3-mass or Hydrogen) U16 RW
918 Profibus address active - -
1) See chapter « Special format details »
2) Access:
● R: Read only
● W: Write only
● R/W: Read and write
Details of status 0 (No. 1 in the list of parameters)
Bit 0: Threshold #4
Bit 1: Threshold #5
Bit 2: Filament #2 on
Bit 3: Maintenance required
Bit 4: Correction in hard vacuum test mode
Bit 5: Test in Gross Leak mode
Bit 6: Test in Normal mode
Bit 7: Test in High Sensitivity mode
Bit 8: General error
Bit 9: Test mode reached
Bit 10: Bypass valve
Bit 11: Acknowledgement request during calibration
Bit 12: Leak detector in Stand-by
Bit 13: Leak detector in hard vacuum test or sniffing
Bit 14: Leak detector temperature close to limit
Bit 15: Stand-by for HLT type calibration compatibility
Profibus
18/154

Details of status 1 (No. 3 in the list of parameters)
Value = 0 Value = 1
Bit 0: Filament used (1/2) Filament 1 Filament 2
Bit 1: Filament on Off On
Bit 2: Cycle No hard vacuum test In hard vacuum test
Bit 3 and 4: Test mode 00: Roughing
01: Gross Leak 1)
10: Normal 1)
11: High Sensitivity 1)
Bit 5: Sniffing No sniffing In sniffing
Bit 6: Calibration result Not OK OK
Bit 7: Not used - -
Bit 8: Warning/Error Warning/Error No warning/Error
Bit 9: Air inlet 1) Closed Open
Bit 10: Leak detector ready for test Yes No
Bit 11: Secondary pump status Not synchronized Synchronized
Bit 12: Not used - -
Bit 13: Not used - -
Bit 14: Sniffer probe status Probe Clogged Probe not clogged
Bit 15: Not used - -
1) According to leak detector model
Details of status 3 (No. 21 in the list of parameters)
Bit 0: Threshold #4
Bit 1: Threshold #5
Bit 2: Filament #2 on
Bit 3: Maintenance required
Bit 4: Correction in hard vacuum test mode
Bit 5: Test in Gross Leak mode
Bit 6: Test in Normal mode
Bit 7: Test in High Sensitivity mode
Bit 8: General error
Bit 9: Test mode reached
Bit 10: Bypass valve
Bit 11: Acknowledgement request during calibration
Bit 12: Leak detector in Stand-by
Bit 13: Leak detector in hard vacuum test or sniffing
Bit 14: Leak detector temperature close to limit
Bit 15: Stand-by for HLT type calibration compatibility
Bit 16: Pressure set point #3
Bit 17: Roughing valve
Details of command 0 (No. 63 in the list of parameters)
Bit 0: HLT type calibration
Bit 1: Internal calibration
Bit 2: External calibration
Bit 3: Machine calibration
3.3.4 Special format details
The special format applies to all logarithmic values.
Profibus
19/154

Structure
U16 type
16 bits unit: mmmmmmmmmmeeeeee
Mantissa = 10 bits
10 bits = mmmmmmmmmmeeeeee
Exponent = 6 bits
6 bits = mmmmmmmmmmeeeeee
0eeeee -> 0 = +
1eeeee -> 1 = -
Value range: 0.00 – 9.99 Value range: -30 – +30
Example 1
U16 type = 0111101010000010
Mantissa: 0111101010000010
Mantissa: 0111101010 -> 490 1) -> 4.9
Exponent: 0111101010000010
Exponent: 000010 -> +2
Decoded value: 4.9 · 10+2
1) In order to read the real leak rate, divide the mantissa value by 100 (in the example,
490/100 = 4.9).
Example 2
U16 type = 0010100000111010
Mantissa : 0010100000111010
Mantissa : 0010100000 -> 150 1) -> 1,6
Exponent : 0010100000111010
Exponent : 111010 -> -6
Decoded value: 1.6 · 10-6
1) In order to read the real leak rate, divide the mantissa value by 100 (in the example,
160/100 = 1.6).
Leak rate decoding
The "HSW code" file provided with the operating instructions (USB key) is used to decode a decimal/
hexadecimal number of a leak rate.
HSW value
Manssa
Exponent
Leak rate 1,60E-06
-6
1,6
10298
Decode from decimal number
HSW value
Manssa
Exponent
Leak rate 4,90E+02
2
4,9
31362
Decode from decimal number
Example: leak rate value from a decimal number
Profibus
20/154
Other manuals for ASI 35
4
This manual suits for next models
5
Table of contents
Popular Recording Equipment manuals by other brands
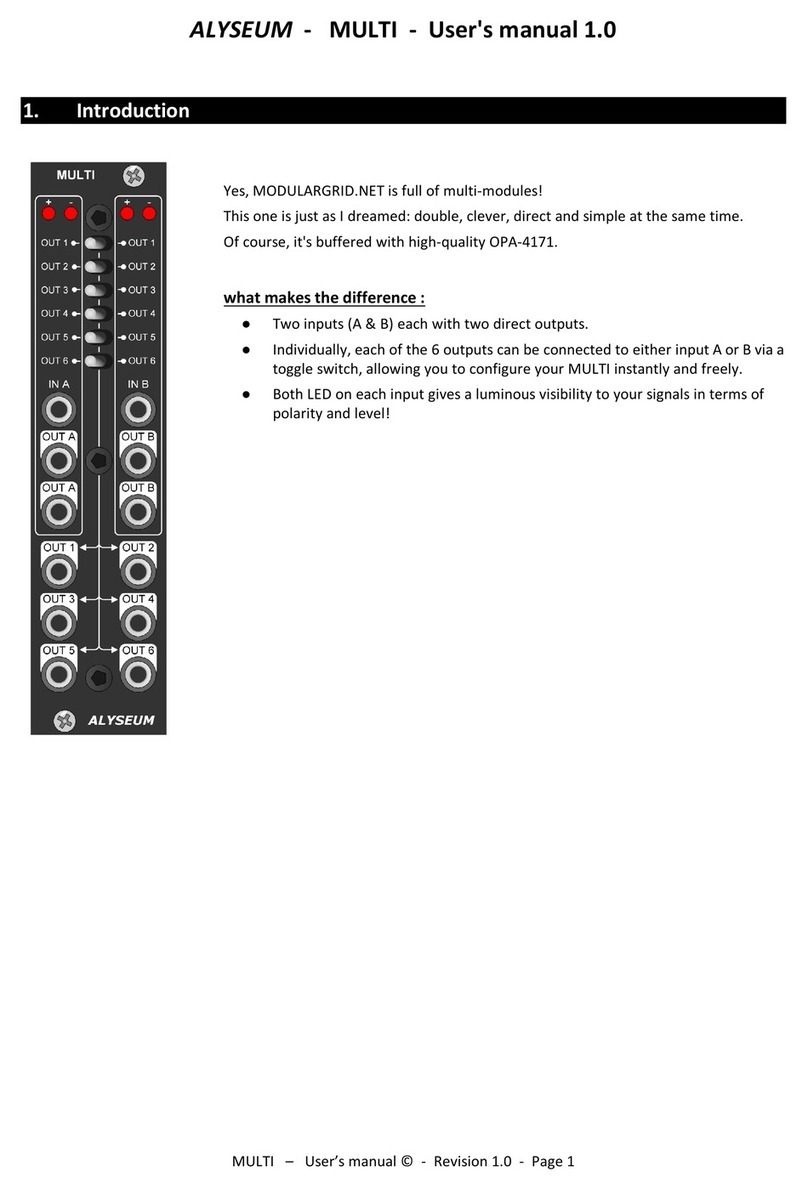
Alyseum
Alyseum MULTI user manual

OceanAudio
OceanAudio The Ark 500 Series owner's manual

World Video Sales
World Video Sales MicroImage Video Systems VMU250 Operation manual
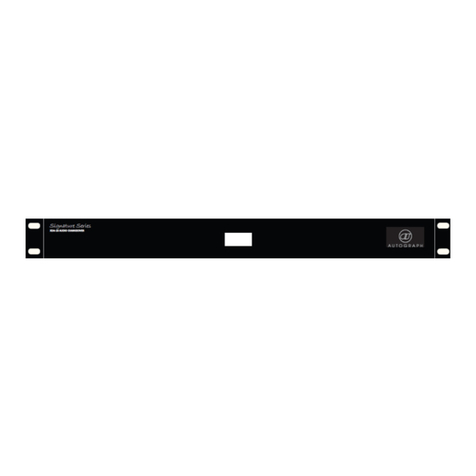
Autograph
Autograph Signature XDA-16 user manual
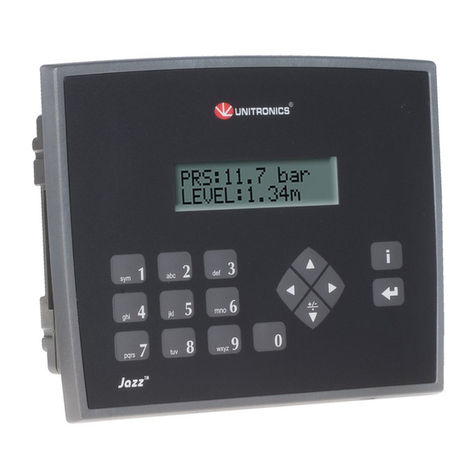
Unitronics
Unitronics Jazz JZ20-UA24 installation guide
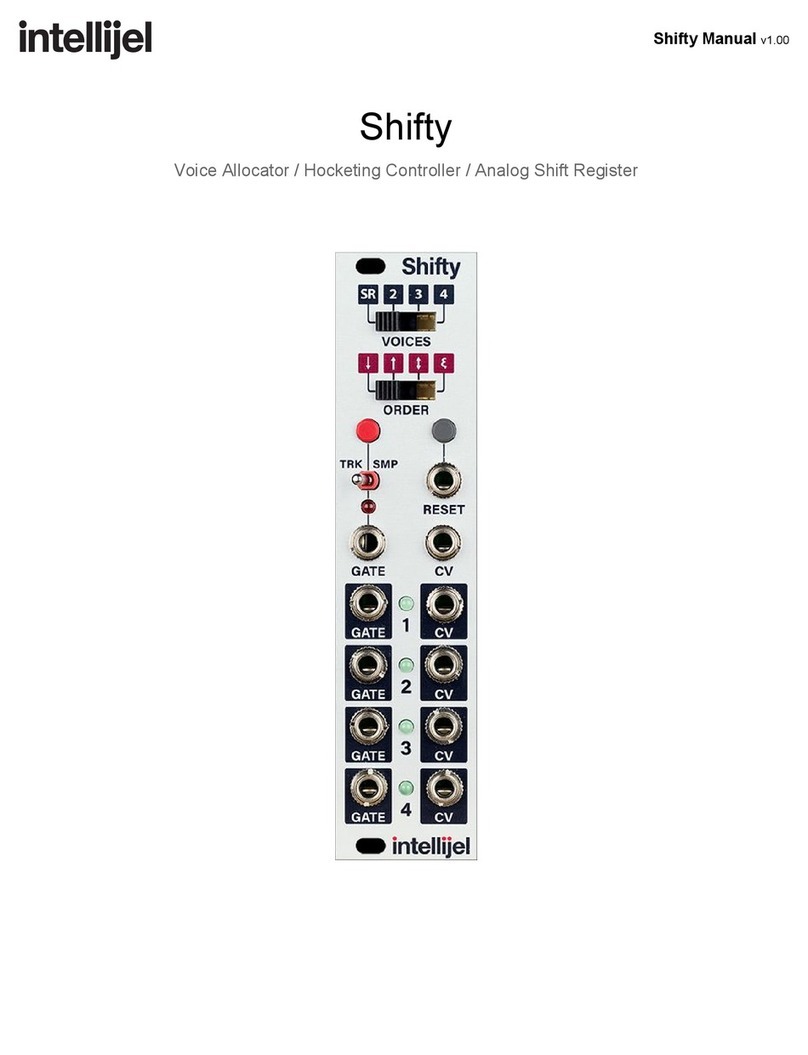
Intellijel
Intellijel Shifty manual
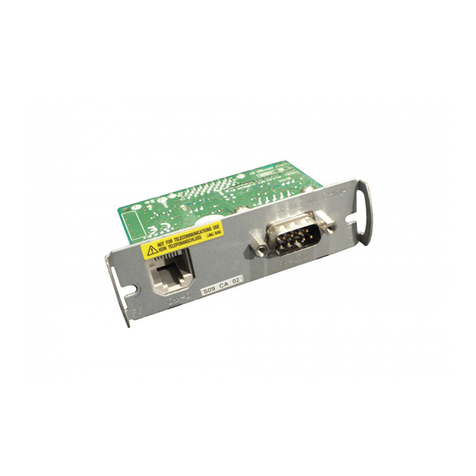
Epson
Epson UB-S09 Developer's guide
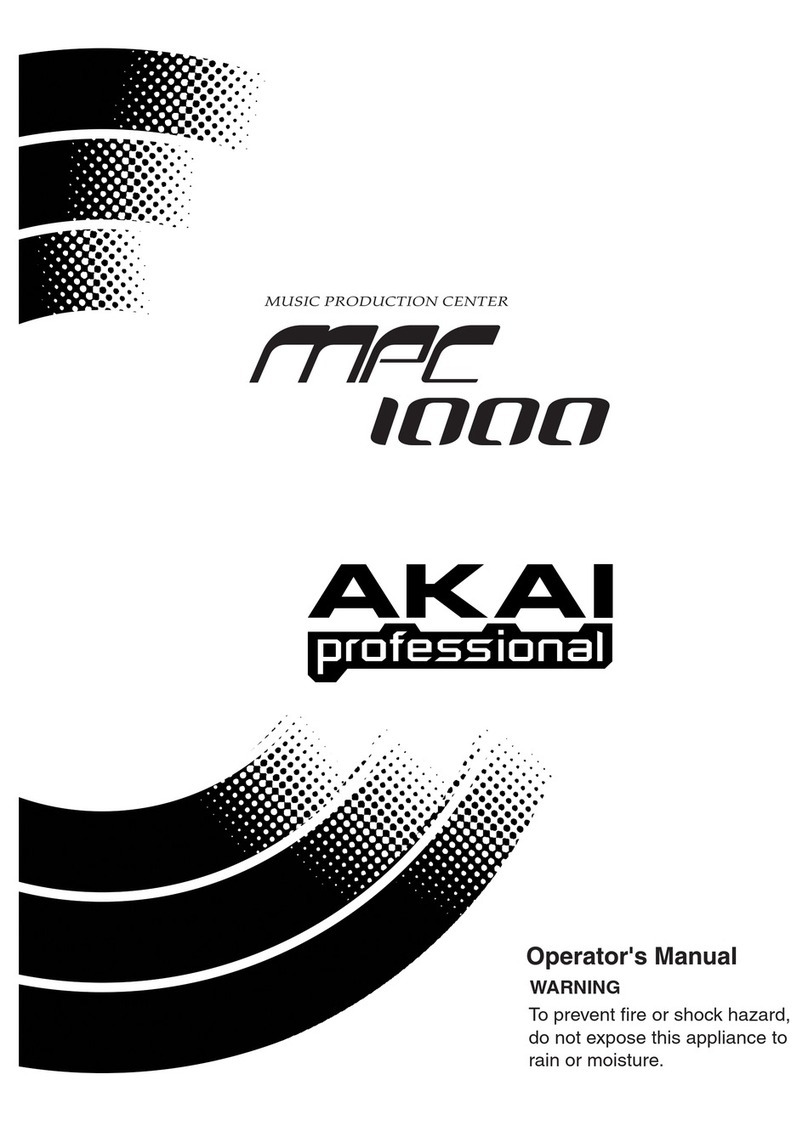
Akai
Akai Professional MPC 1000 Operator's manual
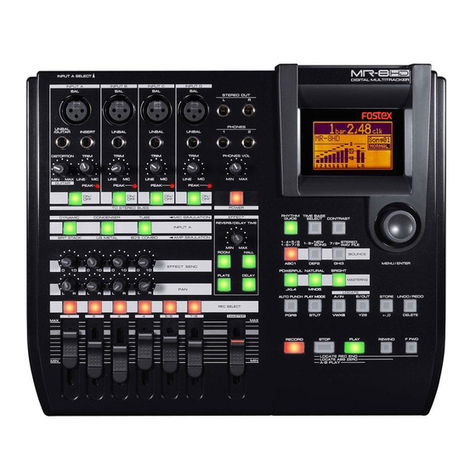
Fostex
Fostex MR-8CD owner's manual
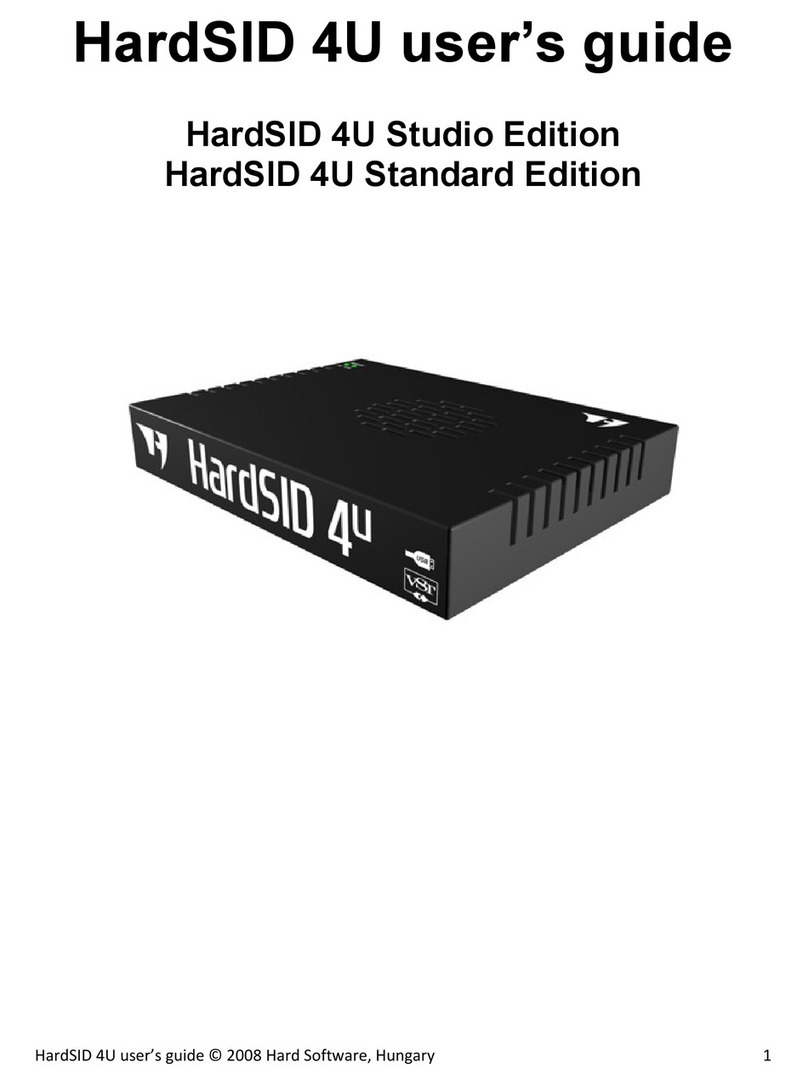
HardSID
HardSID 4U Series user guide

Fire-Lite Alarms
Fire-Lite Alarms Honeywell MMF-302-6 Installation and maintenance instructions
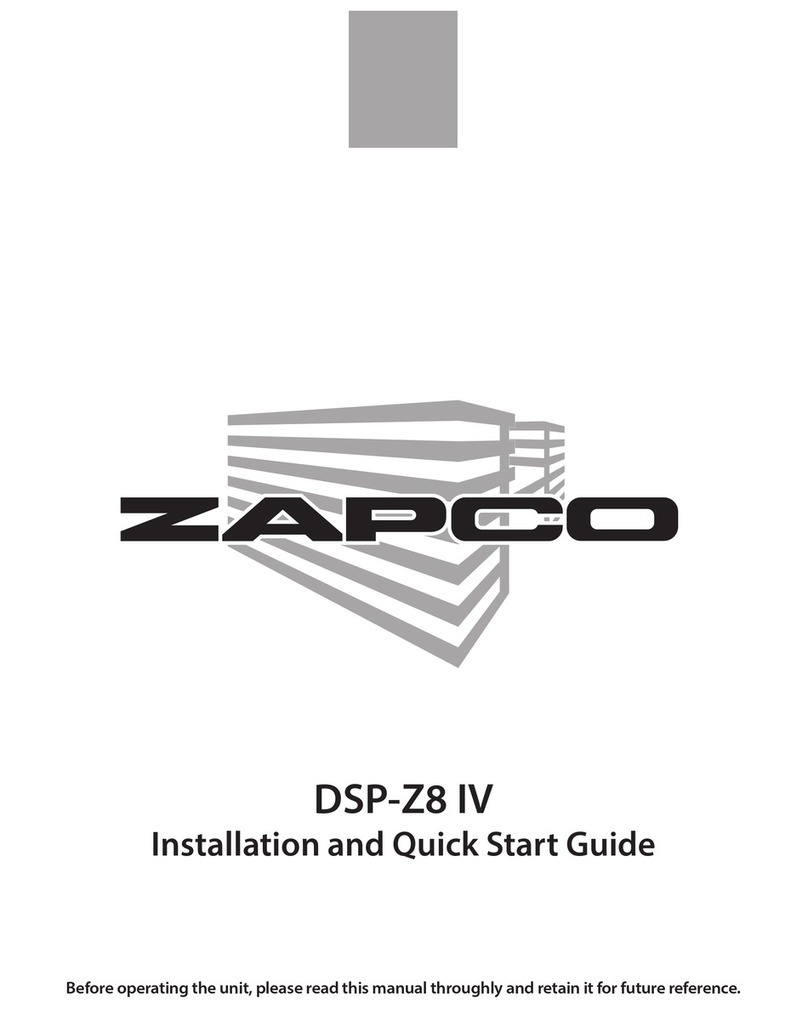
zapco
zapco DSP-Z8 IV II Installation and quick start guide