Pilz PMCtendo SZ Series User manual

PMCtendo SZ
Operating Manual-1002405-EN-04

Contents
Operating Manual PMCtendo SZ
1002405-EN-04 2
Section 1 Introduction 5
1.1 Purpose of the manual 5
1.2 Additional support 5
Section 2 Safety instructions 6
2.1 Warranty and liability 6
2.2 Part of the product 6
2.3 Intended use 6
2.4 Qualified personnel 6
2.5 Working on the machine 7
2.6 Disposal 7
2.7 Directives and standards 7
2.8 Use of symbols 7
Section 3 Product description 9
3.1 PMCtendo SZ synchronous servo motors 10
3.1.1 Nameplate 10
3.1.2 Type label 11
3.2 Servo amplifiers 13
3.3 Feedback 13
3.4 Dynamics 13
3.5 Operating mode 13
3.6 Thermal winding protection 14
3.7 Cooling 14
3.8 Holding brake 14
3.9 Motor shaft and bearing 15
Section 4 Transport and storage 16
4.1 Transport 16
4.2 Storage 16
Section 5 Installation 17
5.1 Installation location 18
5.2 Motor installation 19
5.2.1 Preparing the motor for installation 19
5.2.2 Installing the motor 20
Section 6 Electrical installation 21
6.1 General information 22
6.1.1 Line routing 22
6.1.2 Grounding, shielding and EMC 22
6.1.3 Cable selection 23
6.1.4 speedtec and springtec plug connectors 23
6.1.4.1 Connecting cables using speedtec plug connectors 23
6.1.4.2 Connecting cables using springtec plug connectors 24
6.2 Connection method 25
6.2.1 Connection – Motor housing to grounding conductor system 25

Contents
Operating Manual PMCtendo SZ
1002405-EN-04 3
6.2.2 EnDat 2.2 power and feedback plug connectors 25
6.2.2.1 Terminal assignment – Power plug connectors 27
6.2.2.2 Terminal assignment – EnDat 2.2 feedback plug connectors 29
6.2.2.3 Overview – Motor types and plug connectors 30
6.2.3 HIPERFACE DSL power and feedback plug connectors 32
6.2.3.1 Terminal assignment – HIPERFACE DSL plug connectors 34
6.3 Forced ventilation unit 36
Section 7 Commissioning 37
7.1 Checking the motor installation 38
7.2 Checking the motor connection 39
7.3 Putting the motor into operation 40
7.3.1 Notes for troubleshooting 40
7.4 Testing and bedding in the brakes 42
Section 8 Service 43
8.1 Maintenance 43
8.2 Procedure in case of faults 44
8.3 Motor replacement 44
Section 9 Technical data 45
9.1 General features 45
9.2 Electrical features 45
9.3 Ambient conditions 46
9.4 Forced ventilation unit 46
9.5 Feedback connection 46
9.6 Holding brake 47
9.6.1 Holding brake – Technical data 49
9.7 Temperature sensor 50
9.8 Derating 51
9.9 Type-specific data 52
9.9.1 Attachment conditions 52
9.9.2 SZ motors with convection cooling 53
9.9.3 SZ motors with forced ventilation units 55
9.9.4 Dimensional drawings 57
9.9.4.1 PMCtendo SZ.3x 58
9.9.4.2 PMCtendo SZ.3x (HIPERFACE DSL) 59
9.9.4.3 PMCtendo SZ.4x – SZ.8x with convection cooling 60
9.9.4.4 PMCtendo SZ.4x – SZ.7x with convection cooling (HIPERFACE DSL) 62
9.9.4.5 PMCtendo SZ.4x – SZ.8x with forced ventilation unit 64
9.9.5 Mass moment of inertia 66
9.9.6 Permitted shaft load 67
9.9.7 Torque/speed curves 73
9.9.8 Key safety-related figures 82

Contents
Operating Manual PMCtendo SZ
1002405-EN-04 4
Section 10 Appendix 83
10.1 Abbreviations 83
10.2 Formula symbols 84
10.3 Trademarks 86

Introduction
Operating Manual PMCtendo SZ
1002405-EN-04 5
1 Introduction
1.1 Purpose of the manual
This operating manual describes PMCtendo SZ synchronous servo motors. It contains in-
formation about transport, storage, installation, connection, commissioning, service and dis-
posal.
1.2 Additional support
If you have questions that are not answered in this document, additional support is avail-
able at http://www.pilz.com.

Safety instructions
Operating Manual PMCtendo SZ
1002405-EN-04 6
2 Safety instructions
2.1 Warranty and liability
These devices can pose certain risks. For this reason, always comply with the safety infor-
mation listed in the following sections and points and with the technical rules and regula-
tions.
Warranty and liability claims are voided if:
}The product was not used as intended
}Damage can be traced back to noncompliance with the operating manual
}Operating personnel are not properly trained
}Changes of any kind have been made
2.2 Part of the product
The technical documentation is part of a product.
Always keep this operating manual at hand in the area of the device until disposal of the
product because it contains important information.
Hand over this operating manual in case of sale, transfer or rental of the product.
2.3 Intended use
The servo motors are intended for installation in machines or systems or for assembly with
other components into a machine or system. They must be operated in connection with ap-
propriate, correctly configured servo amplifiers (e.g. PMCtendo DD5 or PMCprotego D).
The thermal motor protection integrated in the motor winding must be monitored and evalu-
ated.
The following are considered non-intended use:
}Direct connection to the supply grid
}Any structural, technical or electrical change
}Use outside of the areas described in this operating manual
}Use deviating from the specified technical data
2.4 Qualified personnel
These devices can pose certain residual risks. Therefore all work on the device, as well as
its operation and disposal, may be performed only by qualified personnel who are aware of
the potential risks. Qualified personnel are persons who have acquired the authorization to
perform these tasks through professional training and/or instruction by specialists.
In addition, applicable regulations, legal provisions, technical standards, this technical doc-
umentation and especially the safety information contained within it must be read carefully,
understood and observed.

Safety instructions
Operating Manual PMCtendo SZ
1002405-EN-04 7
2.5 Working on the machine
Apply the 5 safety rules in the order stated before performing any work on the machine:
1. Disconnect. Also make sure to disconnect the auxiliary circuits.
2. Protect against being turned on again.
3. Check that voltage is not present.
4. Ground and short circuit.
5. Cover adjacent live parts.
2.6 Disposal
Observe the current national and regional regulations! Dispose of individual parts sepa-
rately depending on their condition and the currently applicable regulations, e.g. as elec-
tronic waste (circuit boards), plastic, sheet metal, copper or aluminum.
2.7 Directives and standards
The servo motors fulfill the following guidelines and standards:
}Low Voltage Directive 2014/35/EU
}EMC Directive 2014/30/EU
}DIN EN 50110
}DIN EN 60034-1:2011
}DIN EN 60034-5:2007
}DIN EN 60034-6:1996
}DIN EN 60034-9:2008
}DIN EN 60034-14:2008
}DIN IEC 60364
}UL and CSA certification
All motors are delivered with the Recognized Component Class 155 (F) motor insula-
tion system approval.
The approval is registered at Underwriters Laboratories in the United States under UL
number E357386 in the areas of OBJY2.GuideInfo Systems, Electrical Insulation -
Component and
OBJY8.E357386 Systems, Electrical Insulation Certified for Canada - Component.
This approval is primarily relevant for the use of motors and geared motors on the US
market, but it also represents a special quality feature in many countries.
2.8 Use of symbols
Safety instructions are identified with the following symbols. They indicate special risks
when handling the product and are accompanied by relevant signal words that express the
extent of the risk. Furthermore, useful tips and recommendations for efficient, error-free op-
eration are specially highlighted.

Safety instructions
Operating Manual PMCtendo SZ
1002405-EN-04 8
DANGER!
Danger
This word with a warning triangle indicates that there is a considerable risk
of fatal injury
– if the stated precautionary measures are not taken.
WARNING!
Warning
This word with a warning triangle means there may be a considerable risk of
fatal injury
– if the stated precautionary measures are not taken.
CAUTION!
Notice
This indicates that damage to property may occur
– if the stated precautionary measures are not taken.
NOTICE
Important indicates relevant information about the product or serves to em-
phasize a section in the documentation that deserves special attention from
the reader.

Product description
Operating Manual PMCtendo SZ
1002405-EN-04 9
3 Product description
The PMCtendo SZ synchronous servo motors have a very short design made possible by
using optimal winding technology. This allows for the stator windings to be manufactured
with the highest possible copper fill factor. This technology and other optimizations of the
mechanics make it possible to shorten the motor length by roughly half without negatively
impacting performance.
Fig.: PMCtendo SZ synchronous servo motors

Product description
Operating Manual PMCtendo SZ
1002405-EN-04 10
3.1 PMCtendo SZ synchronous servo motors
3.1.1 Nameplate
Designation Value in example Meaning
YOM 2018 Year of manufacturing
Type PMCtendo SZ.31/1/2/2/7/K/
H/30/00
Type label
Ser. No. 10251811 Serial number
Ident. No. 8177064 Identification number
M00.95Nm Stall torque: Continuous torque at
250rpm ± 5%
MN0.93Nm Rated torque; highest continuous
torque of the motor at rated speed
nN ± 5%
I02.02A Stall current: I0 is the current flow-
ing at M0
IN1.99A Rated current: Continuous current
at MN ± 5% and nN ± 5%
KEM 40V/1000rpm Back EMF constant: Peak value of
the induced phase-to-phase volt-
age at operating temperature (ΔT
= 100K) in generative idling mode
KM,N 0.467Nm/A Torque constant at the measure-
ment point
nN3000rpm Rated speed nN
Therm. class 155 (F) Thermal class in acc. with EN
60034/VDE 0530
IP 56 Protection class
Therm. prot. PTC thermistor 145°C Thermal winding protection by
PTC thermistor
Encoders EnDat 2.2 EQN 1135 FMA MT Feedback system
Brake 2.50Nm/24V/0.51A Permanent magnet holding brake

Product description
Operating Manual PMCtendo SZ
1002405-EN-04 11
3.1.2 Type label
Sample code
PMCtendo SZ. 31 1 2 2 7 K H 30 00
1 2345678910
1 Type
PMCtendo SZ
2 Size Code
3x 3x
4x 4x
5x 5x
7x 7x
8x 8x
3 Brake and dynamics Code
Without permanent magnet holding brake and dynamic design 0
With permanent magnet holding brake and dynamic design 1
Without permanent magnet holding brake and increased mass moment of
inertia (not for SZ.3x, SZ.51, SZ.71)
2
With permanent magnet holding brake and increased mass moment of iner-
tia (not for SZ.3x, SZ.51, SZ.71)
3
4 Feedback Code
EnDat 2.2 single-turn, inductive (ECI 1118-G2) 1
EnDat 2.2 multi-turn, optical (EQN 1135) 2
HIPERFACE DSL multi-turn, optical (EKM36, only for SZ.3x – SZ.75...K) 7
5 Design Code
B5, smooth shaft 2
6 Connection Code
Angle flange socket (only for SZ.85...F) 6
Rotating angle flange socket 7
7 Cooling Code
Forced ventilation unit (not for SZ.3x) F
Convection cooling K

Product description
Operating Manual PMCtendo SZ
1002405-EN-04 12
8 Voltage Code
400V (UZK = 540V) H
9 Speed Code
2000rpm 20
3000rpm 30
4500rpm 45
6000rpm 60
10 Option Code
Standard 00

Product description
Operating Manual PMCtendo SZ
1002405-EN-04 13
3.2 Servo amplifiers
The PMCtendo SZ synchronous servo motors have to be operated with speed, torque or
position regulation using servo amplifiers, such as the PMCtendo DD5 or PMCprotego D.
The most important selection criteria for the appropriate servo amplifiers and associated ca-
bles are:
}Stall torque M0 [Nm]
}Stall current I0 [A]
}Nominal speed nN [rpm]
}Mass moments of inertia for the motor and load J [kgcm2]
}Effective torque of the motor Meff [Nm]
}Regeneration energy in braking operation
}Overload capacity
}EMC
When selecting the servo amplifier, also keep static and dynamic loading in mind (accelera-
tion and braking).
3.3 Feedback
The PMCtendo SZ synchronous servo motors can be equipped with the following feedback
systems:
}EnDat 2.2 single-turn, inductive (ECI 1118-G2)
}EnDat 2.2 multi-turn, optical (EQN 1135)
}HIPERFACE DSL multi-turn, optical (EKM36, only for SZ.3x – SZ.75...K)
Single-turn feedback systems deliver an absolute position within one revolution; multi-turn
feedback systems provide an absolute position over a number of revolutions.
The purely digital HIPERFACE DSL feedback system is a one cable solution, meaning it is
a hybrid cable where the power, brake and feedback wires are consolidated. The hybrid ca-
ble decreases wiring complexity and reduces space requirements. For assembly, it simply
has to be connected or clamped to the motor or servo amplifier.
3.4 Dynamics
The PMCtendo SZ synchronous servo motors are designed for applications with high dy-
namics by default. This means that they have the lowest possible mass moment of inertia.
Synchronous servo motors can optionally be delivered with increased mass moment of in-
ertia in order to optimize the inertia ratio between the motor and load.
3.5 Operating mode
PMCtendo SZ synchronous servo motors are designed for continuous operation. This cor-
responds to the S1 operating mode (in accordance with DIN EN 60 034-1).

Product description
Operating Manual PMCtendo SZ
1002405-EN-04 14
3.6 Thermal winding protection
The PMCtendo SZ synchronous servo motors have thermal winding protection that protects
the stator winding from damage during constant overload.
The PMCtendo SZ motors are equipped with a PTC thermistor. If the motor temperature
reaches a critical value, the resistance of the PTC resistors increases abruptly and thereby
indicates the overload of the motor.
NOTICE
Every thermal winding protection has to be monitored and evaluated by a
servo amplifier or an external triggering device.
3.7 Cooling
PMCtendo SZ synchronous servo motors are sized for convection cooling by default.
In order to increase the performance of the motors, they can optionally be equipped or up-
graded with external forced ventilation systems (IP44 protection class).
In applications requiring a higher protection class than IP44 or a lower noise load, servo
motors can be water-cooled in the A-side flange.
3.8 Holding brake
DANGER!
Risk of fatal injury!
The motor brake is not a safety brake.
– Check whether additional protective measures have to be taken,
such as when stopping or standing under suspended loads.
Since the synchronous servo motors can be braked actively and quickly using correspond-
ing reference value specifications on the servo amplifier, the built-in brakes have the func-
tion of a holding brake.
For holding the motor shaft in place without any backlash, the synchronous servo motors
can be delivered with a built-in permanent magnet holding brake. It blocks the rotor when
de-energized.
An electro-mechanical method is used to release the brake. The applied voltage generates
an electromagnetic field that counteracts the field from the permanent magnet and neutral-
izes its effect.
NOTICE
The air gap in the holding brake cannot be adjusted later.

Product description
Operating Manual PMCtendo SZ
1002405-EN-04 15
Additional brakes have to be provided for braking while the motor is turning, e.g. during an
emergency stop.
CAUTION!
Damage to the motor or motor components due to electrical connection er-
rors!
– Observe the motor nameplate and this connection plan. Contact
Technical Support in case of questions.
DANGER!
Risk of fatal injury due to gravity-loaded vertical axes!
Unsecured gravity-loaded vertical axes can drop unexpectedly due to defec-
tive or released brakes.
– Follow the requirements and protective measures for gravity-loaded
vertical axes from the DGUV, special area information sheet No. 005,
09/2012 edition.
3.9 Motor shaft and bearing
PMCtendo SZ synchronous servo motors have a smooth shaft end on the drive side (DIN
6885). Surface pressure needs to be achieved for torque transfer in the case of a positive
connection. This ensures a reliable transfer of force free of backlash.
The bearings are designed as ball bearings with lifetime lubrication and with non-contact
sealing.

Transport and storage
Operating Manual PMCtendo SZ
1002405-EN-04 16
4 Transport and storage
4.1 Transport
Secure the shafts and bearings of a synchronous servo motor against impacts during trans-
port. During transport, use the corresponding eyebolts (if present) and a suitable fastening
element.
Lift the synchronous servo motor by the eyebolts exclusively without additional attach-
ments. Never transport the motor by the fan hoods or the angle flange socket of the con-
nectors.
4.2 Storage
Store synchronous servo motors in enclosed, dry spaces. Storage on the fan hoods is not
permitted. If the motors are protected against all damaging environmental influences and
mechanical damage, short-term storage in outdoor areas with roofing is permitted.
Make sure that no condensate forms during storage, such as due to extreme temperature
fluctuations with high humidity.
Be sure to protect the motor shaft against corrosion in the case of long-term storage. Be
aware that the insulation resistance of the winding must be tested after long-term storage.

Installation
Operating Manual PMCtendo SZ
1002405-EN-04 17
5 Installation
DANGER!
Electric shock!
Serious injuries due to contact with live parts!
– Carry out all work on a de-energized motor!
– Make sure that the motor shaft is stationary during all work. A rotat-
ing rotor can cause high voltages at the connections.
– Disconnect the supply voltage. Be aware that there may still be dan-
gerously high voltages at the servo amplifier, even 10minutes after
switching off the supply voltage, due to the residual charge of the link
capacitors.
– Cover all open electrical connections, e.g. using protective caps.
– Secure the installation location as per regulations, e.g. using locks or
warning signs.
DANGER!
Burns!
The surface temperature of a synchronous servo motor can significantly ex-
ceed 65°C through operation.
– Take suitable protective measures against unintentional and inten-
tional contact with the motor.

Installation
Operating Manual PMCtendo SZ
1002405-EN-04 18
5.1 Installation location
The following requirements apply to the installation location:
}The installation location must be free of any aggressive substances and any electrically
conductive atmosphere
}The substructure must be even, free of vibrations and resistant to warpage
}Sufficient heat dissipation must be ensured; for this purpose, ensure compliance with
the permitted surrounding temperature and, as needed, provide additional cooling for
the motor, such as by using a forced ventilation unit
}If using a forced ventilation unit, ensure compliance with the minimum clearance of the
air intake
Type Forced ventilation unit Minimum clearance xFmin [mm]
SZ.4x FL4 20
SZ.5x FL5 20
SZ.7x FL7 30
SZ.8x FL8 30
The following graphics show permitted installation positions IM B5, IM V1 and IM V3.
IM V1 IM V3
IM B5
In installation position IM V3, take special care that no fluid from attachments can get into
the motor bearings.

Installation
Operating Manual PMCtendo SZ
1002405-EN-04 19
5.2 Motor installation
CAUTION!
Material damage!
Impacts or other uses of force cause damage to the bearings, feedback sys-
tem and motor shaft.
– Do not hit the motor shaft or motor housing with a hammer or other
tools.
– Do not expose the motor to any compressive stress, impacts or high
acceleration.
– Use backlash-free, frictional collets or couplings.
– For attaching and releasing couplings, gears or belt drives, always
use the intended draw bar thread in the motor shaft. Use a suitable
tool!
CAUTION!
Material damage!
Solvents damage the sealing lips of the shaft seal rings.
– Make sure that no solvent comes in contact with the sealing lips of
the shaft seal rings.
5.2.1 Preparing the motor for installation
aCheck the motor for transport damage. Never install a motor with obvious damage!
aCheck the insulation resistance of the motor winding after storage.
aThoroughly remove any corrosion protection agent and/or dirt from the motor shaft. Use
commercially available solvents to do so. Make sure that solvent does not come in con-
tact with the sealing lips of the shaft seal rings. Otherwise, material damage may occur.
aIf possible, warm the drive elements, e.g. belt drive.
aBe aware that damage to the finish on the synchronous servo motor is never permitted.

Installation
Operating Manual PMCtendo SZ
1002405-EN-04 20
5.2.2 Installing the motor
aAlign the coupling correctly. Misalignment leads to impermissible vibrations and to the
destruction of ball bearings and coupling!
aAvoid mechanically constrained motor shaft mounting. A rigid coupling and/or exces-
sive additional bearings (e.g. in the gear unit) can put excessive stress on the motor
shaft.
aThoroughly remove any corrosion protection agent and/or dirt from the motor shaft. Use
commercially available solvents to do so. Make sure that solvent does not come in con-
tact with the sealing lips of the shaft seal rings. Otherwise, material damage may occur.
aPrevent contact between temperature-sensitive parts and the motor. The surface of the
motor can reach temperatures that are significantly above 65 °C through operation.
aIf you remove the eyebolts after installation, you must seal the tapped hole in a durable
way according to the protection class of the motor.
This manual suits for next models
1
Table of contents
Other Pilz Servo Drive manuals
Popular Servo Drive manuals by other brands
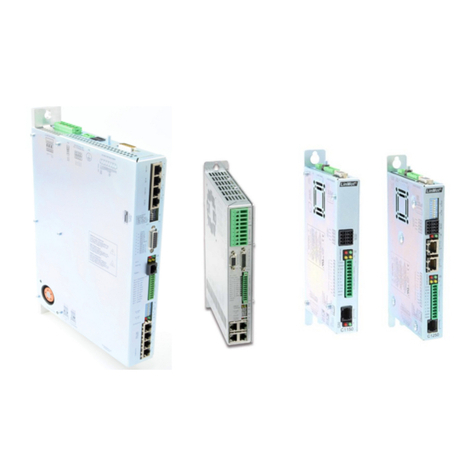
NTI AG
NTI AG LinMot C1150-PN-XC S Series user manual
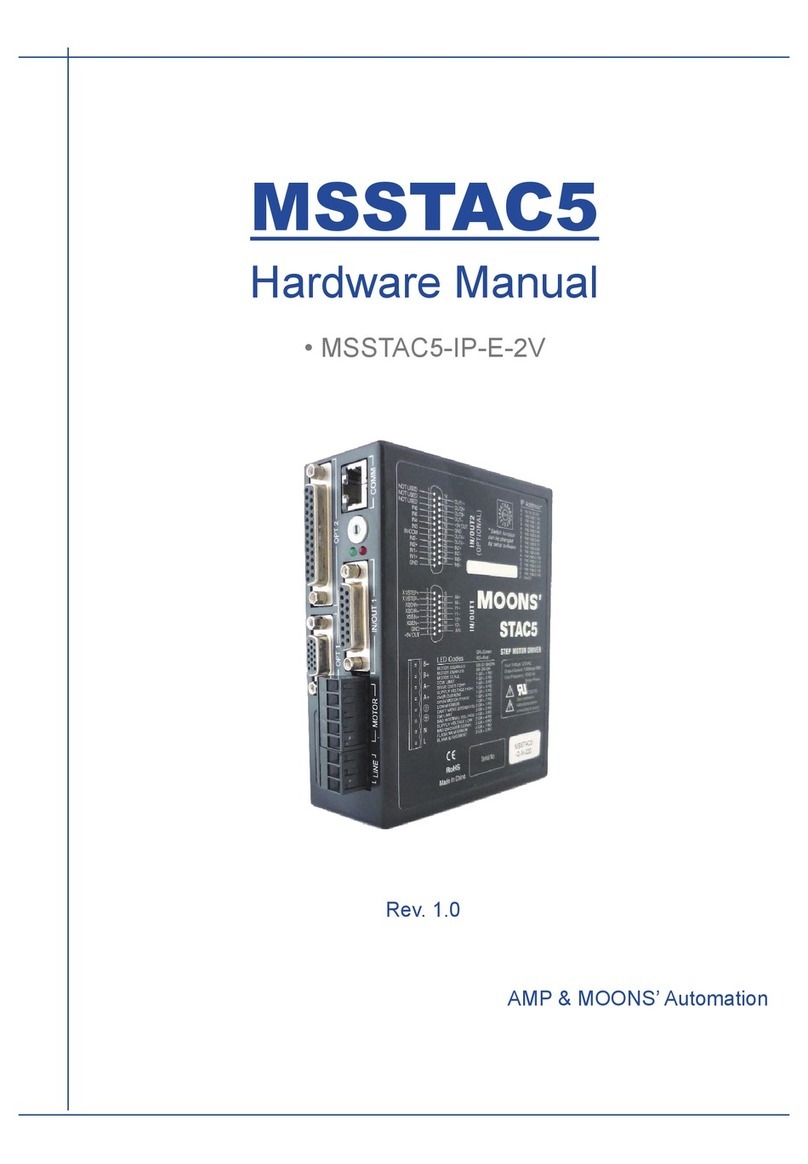
Moons'
Moons' MSSTAC5 Hardware manual
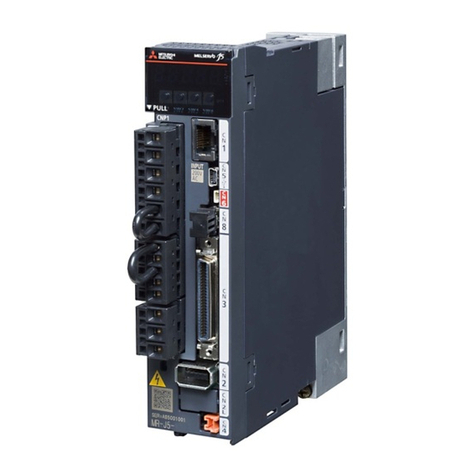
Mitsubishi Electric
Mitsubishi Electric MELSERVO-J5 MR-J5-G Series user manual
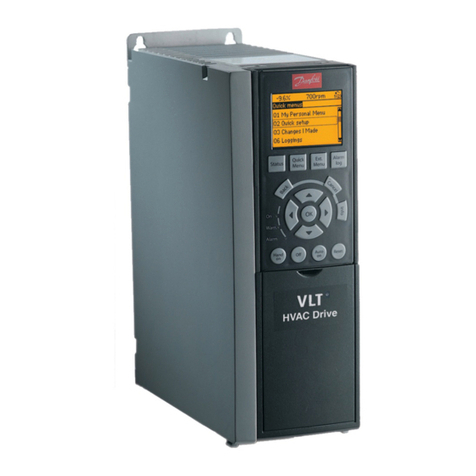
Danfoss
Danfoss VLT HVAC Drive FC 102 operating instructions
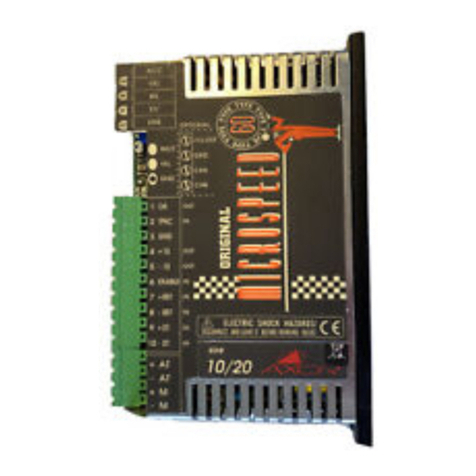
Axor
Axor Microspeed 12 manual
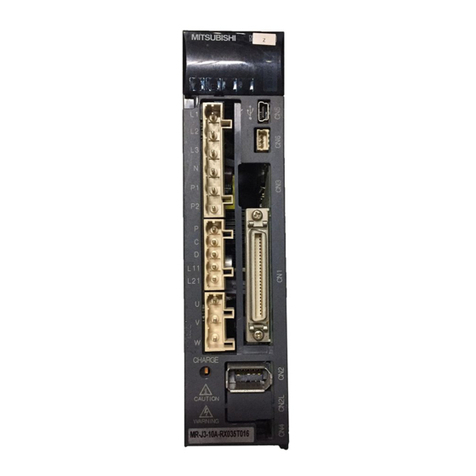
Mitsubishi Electric
Mitsubishi Electric Melservo-J3 Series MR-J3-B Handbook