PowerBoss Admiral 38 Installation and operation manual

Admiral 40
(B1100)(7580.02)(7580.35)
Admiral 38
(B1050)(7580.12/22)(7580.16/26)
(7580.15)
Service Booklet
REVISED APRIL 2013
Training
Trouble Shooting
Adjustments

Page 2
Contents
1 Remarks 5
2 General 7
2.1 Settings 8
2.2 Brief Description 11
2.2.1 Switch Off Suction/Recovery Tank Filled Up 14
2.2.2 Initial Position Of Machine/Release, Lock Functions 15
3 Check Settings For Machine Type, TSG And Options,
Display And Delete Last Error 18
3.1 Check And Set Machine Type 23
3.2 Check And Set Options 24
3.3 Check And Set TSG 25
3.4 TSG Error 3211 28
3.5 View And Delete Last Appeared Error In The Display 29
4 Programming Different Cleaning Function Procedures Depending On
Accelerator Position (Check And Set) 30
4.1Programme Functions 32

Page 3
Contents
5 Specific Customer Settings (Display Of Last Error And Selection Of
Water Stage, Cleaning Agent, SWA, Side Brush, Filter) PPV 37
5.1 PPV1 40
5.2 PPV2 41
5.3 PPV3 42
5.4 PPV4 43
5.5 PPV5 (B 1100 only) 44
5.6 PPV6 (B 1100 only) 45
5.7 PPV7 (B 1100 only) 46
5.8 PPV8 (B 1100 only) 47
6 Setting Of Modules 48
6.1 Module 1 49
6.2 Module 3 50
7 Settings Of CAN Operator Panels (B 1100 only) 51
8 Water Pump 52
8.1. Water Amounts 52
8.2 Standstill Detection for Water Pump 54

Page 4
Contents
9 Drive Controllers 55
9.1 SEVCON Controller (Diagnostic LED) 55
9.1.1 Signal Measurement On Controller (SEVCON) 58
9.2 ATECH / ZAPI Controller 63
9.2.1 Automatic Monitoring Of Components 65
9.2.2 Error Messages Displayed Via LED 66
9.2.3 Explanations For Displayed Error Messages 67
9.3 Drive Motor Hakomatic B1050 (Amer) 84
9.3.1 Tyre replacement 84
9.3.2 Check / replacement of carbon brushes 88
9.3.3 Diagnostic LED for drive control unit (Italsea) 89
10 Error Table With Information On Service Display 91
11 Notes 113
12 Brooms, Brushes & Blades 114

Page 5
This document is structured so as to allow and seek continuous extension. You thus
receive the documents with the annotation that more or revised pages are to follow in
future.
This decision has been taken to allow adding modifications made to the machine
equally to the documents as revisions.
Beyond that this document may be improved upon your advice and proposals. I would
thus be grateful to receiving your feedback.
1. Remarks

Page 6
Caution :
•Before working at the machine, disconnect voltage supply (pull battery plug)
except for the purpose of voltage and current measurement.
•When replacing stripe fuses, only loosen screws. Do not remove them completely
-short-circuit hazard.
Make sure to fully and evenly insert new blade fuses under the screws.
•After each repair proceed to starting and service current measurement to allow
detection of eventual defects.
•When working at the machine, comply with the general safety and accident
prevention regulations as provided by law.
1. Remarks

Page 7
The Hakomatic B 1100 and the Hakomatic B1050 are equipped with a service indication
in the hour meter display. Upon switching the key switch ON, a 4-digit code describing
the software version (e.g. 3.018), is displayed for about 3 seconds, followed by another
4-digit code signalling the last error which again is followed by the hour meter indication.
Upon launch of the Hakomatic B1050, software version has updated to 4.020.
With the software revision 4.026 the Hakomatic B1100 TB 1230 was introduced.
As soon as a malfunction occurs, the red LED signalling a defect lights up and a warning
buzzer sounds. The current error code appears (as 4-digit alpha-numeric code in the
service display) with blinking dots between the digits. When all these criteria are met,
the error is a current one!
There is NO error code, containing a “0”.
Find the error codes listed in a table in chapter 11.
This document uses the following abbreviations:
TSG - low discharge signal sender
SWA - dirty water recycling
2. General

Page 8
Settings on the control electronics/panel which have to be set and checked on each
machine:
In contrast to the Hakomatic B1100, scope of performance of the Hakomatic B1050 is
reduced and does not feature all the options available in the Hakomatic B1100. The
Hakomatic B1050PB (Plate Brush aggregate) has the side scrub unit optionally
available only; the Hakomatic B1050CB (Cylindrical Brush aggregate) has the side
broom unit optionally available, while the pre-sweeper, dirty water recycling and
cleaning agent dosage (99756402) options are available and settable for the
Hakomatic B1100 only. The B1050 PB 1230 doesn´t have any options adjustable via
the control modules of the machine control system.
The Hakomatic B1100 PB1230 is equipped with the pre-sweep unit generally.
Machine type
TSG (low discharge signal sender - also called LDS)
Options
Delete display of last error after repair
Programme variants depending on the accelerator position
2.1 Settings

Page 9
Settings which may be set via operator panel according to customer requirements:
Display of last (remedied) error upon switching machine ON
Selection of water stage upon start of cleaning
Cleaning agent ON in addition to switching water ON (B1100 &
B1100 PB 1230 only)
Switching over to SWA upon switching water ON (B1100 only)
Side brush additionally ON in addition to switching ON scrubbing (B1100 and
B1050 PB only)
Side broom additionally ON in addition to switching ON scrubbing (B1050CB)
Filter shaking (B1100 only & B1100 PB 1230 )
Filter suction ON in addition to sweeping ON (B1100 only & B1100 PB 1230 )
Automatic filter shaking after sweeping (B1100 only & B1100 PB 1230 )
2.1 Settings

Page 10
Settings at Module 1:
Dip-switch for electronic circuit-breakers
Settings at Module 3:
Dip-switch for electronic circuit-breakers and module coding
Settings at the additional operator panels (ADM 40 only):
Dip-switch for operator panel coding
2.1 Settings

Page 11
Machine control is effectuated via the following electronics:
Control electronics
Module 1
Module 3 (for pre-sweeper, side broom and side brush, 3rd brush options)
Operator panel
Cleaning agent dosage /SWA operator panel (B1100 only)
Pre sweeper operator panel (B1100 only)
Cleaning agent module (optional, B1100 only)
Auxiliary voltage module (36V/24V transformer)
Voltage to the electronics is supplied by the auxiliary voltage module which transforms
36 Volts to 24 Volts. As the electronics are the same as integrated in the B910 and B
750R machines, the 24V electronics have to be transformed for use in the B 1100 and
B1050 machines. Components such as the motors and pumps, however, are still 36V
components.
The 24V voltage supply must not, even under load, fall below 23V since otherwise, supply
of the modules 1 and 3 would be insufficient and cause a CAN error (4000 error code).
2.2 Brief Description

Page 12
The control electronics covers all control and monitoring functions in the machine
except for drive control.
Operation of drive controller is independent from the other electronics and only the
release signal and the signal for speed reduction are transmitted via control
electronics to drive controller. Beyond that, a signal is transmitted from drive controller
to control electronics for forward and reverse ride.
Upon occurrence of a defect on the drive controller, an error code is not output since
this controller has its own diagnostic indicator (see chapter 10).
The buttons for scrubbing, suction, scrubbing and suction and the green Hako button
for combined cleaning may be switched arbitrarily such that the selected function is
activated. Pre-sweeper/side broom and /or side brush function can be activated or de-
activated disregarding of the selected cleaning mode, if present in the machine.
The remaining functional buttons (water, brush ground pressure) allow activating or
de-activating the related functions in addition to the cleaning procedure without effect
on the running function.
2.2 Brief Description

Page 13
The machine is equipped with a seat switch. Activation of this switch is required before
switching key switch on since otherwise sweeping and scrubbing functions (even in
combination) are locked. If the seat switch is not activated, suction can only be
activated for the „Hand suction hose“ option.
A reset of the machine after it was deactivated by the seat contact switch, is realized
by switching off and on again with the key switch.
Constant activation of the seat switch is also required. Leaving the seat while key
switch is ON causes locking of the functions.
The seat contact switch is 3 seconds delayed.
At the Hakomatic B1050 machines the sequence of switching on the machine (key
switch, seat contact switch), has no influence to the ability of function of the machine.
It is equally required to release parking brake to enable cleaning functions and drive
control is released.
To switch on the “TOOL”-function of the B1050 machines, it is necessary to activate
the brake of the machine.
2.2 Brief Description

Page 14
The suction function is either stopped by the operator via button actuation or
automatically upon the „recovery tank filled up“ signal.
Switching off by operator:
Squeegee is lifted up
Suction motors switch off delayed (15 seconds)
Switching off after tank filled up:
The switch signalling „recovery tank filled up“ opens as soon as the tank is filled
If switch is open for 3 seconds or longer (spill protection) squeegee will be lifted
and the suction motors switch off with a delay of 15 seconds.
2.2.1 Switch Off Suction /
Recovery Tank Filled Up

Page 15
When turned ON and the seat switch closed, all units of the machine are set to „initial
position“.
This means that the control electronic triggers all units (lifting elements and motors).
Lifting elements will be lifting up as long as they are not switched off by the micro-
switch controlling the upper limit position and integrated in the lifting element.
This means that the outputs for the lifting elements are powered for approx. 6 sec
every time the machine is switched on. During this time a voltage can be measured at
the outputs for the lifting elements.
Motors are off and the cleaning unit LED indication in the operator panel extinguishes.
The drive controller is transmitted the release signal.
Should the seat switch not be activated, the motors will also be turned off - for safety
reasons - but the lifting elements will not be lifting and the travel drive controller will
not be released either.
The only exception: water suction by hand hose (B1100).
2.2.2 Initial Position/Release,
Lock Functions

Page 16
Before operation of the pre-sweeper (B1100 & B1100 PB 1230 only), the hood is to be
closed and the dirt hopper correctly inserted. The hood and the dirt hopper are
monitored each by a switch (NC switch) being serially connected. As soon as the
switch opens, the LED in the standard operator panel lights to signal „open hood“ and
the pre-sweeper function is disabled. Since both switches are serially connected, this
LED equally lights if the switch signalling „no dirt hopper inserted“ opens. In case of
faulty function, check the switch and all cable connections and connectors.
Another safety request is effected by the thermal switch of the broom motor. If this
switch opens, the pre-sweeper function will be disabled and an error code appears.
After engaging the parking brake, all cleaning functions will be disabled and the red
LED „brake engaged“ lights. This switch is an NC switch as well and it is thus
required, in case of faulty function, to check the switch, all cable connections and
connectors.
2.2.2 Initial Position/Release,
Lock Functions

Page 17
Activation of the „Brushes“ function causes lowering of the brush head to the so-called
central position. The lifting element does not attain the lower limit position before
cleaning with increased ground pressure. The brush head lifting element thus has 3
micro-switches integrated, one each for the upper, the central and the lower limit
position.
Extracting the side brush unit is possible only after the brush head had lowered or in
other words: if the central position micro-switch does not switch, the „brush lowering
completed“ signal is missing and the side brush does not swing out. This signal
depends on the central position micro-switch only such that swinging out of side brush
is possible as well for cleaning with increased brush ground pressure. Since on its way
down to the lower limit position the central position micro-switch had been triggered
even if no fault occurred during cleaning with increased ground pressure.
2.2.2 Initial Position/Release,
Lock Functions

Page 18
Check settings for machine type, TSG and options; display and delete last error
The settings described in this step are to be checked and modified if required.
Proceed to check and adjustment in particular after electronics replacement.
3. Machine Type Settings

Page 19
The picture shows the Hakomatic B1050 operator panel. Position of the programming
buttons is identical to those of the Hakomatic B1100. Only the icons differ due to the
different functional scope of this machine.
3. Machine Type Settings
B1050 PB & CB & PB 1230

Page 20
Entry into programming
1. Switch off machine by key switch
2. Simultaneously press "G" and "H" and hold depressed, then switch on key switch
3. Hold depressed both buttons as long as the software version is displayed then
release buttons
Display of set machine type then appears automatically. Use the “N” button to proceed
to display of set options and display of TSG setting or then to display of last
(remedied) error. Use the “L” button to return to previous display.
Quit programme any time by switching OFF the key switch.
3. Machine Type Settings
This manual suits for next models
8
Table of contents
Other PowerBoss Blower manuals
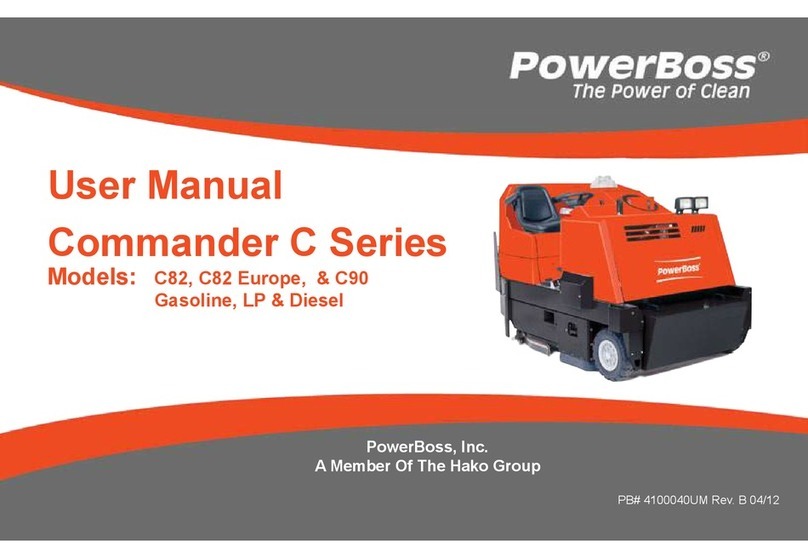
PowerBoss
PowerBoss C82 User manual
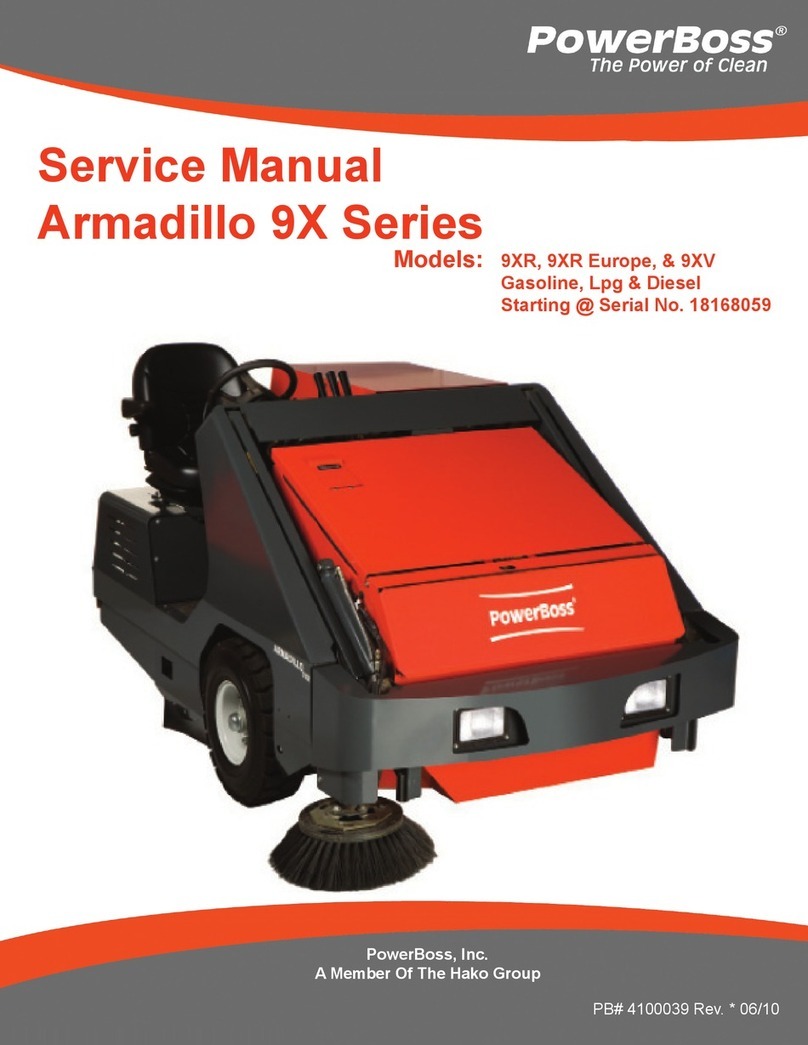
PowerBoss
PowerBoss Armadillo 9X Series User manual
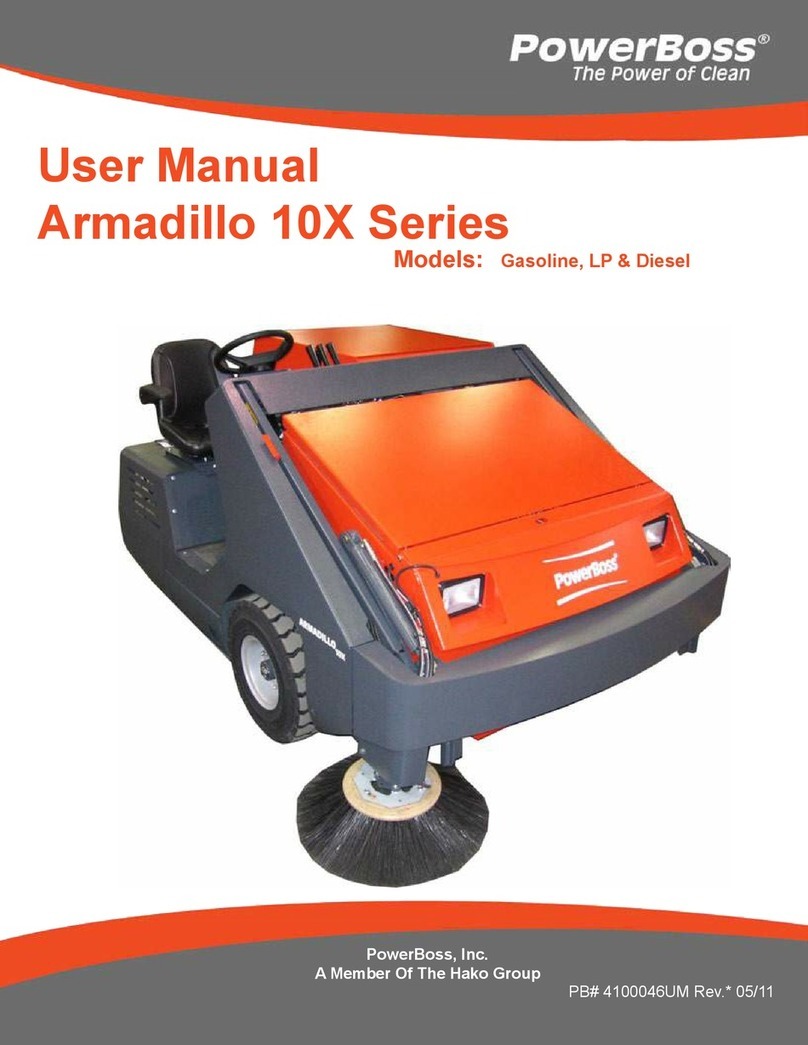
PowerBoss
PowerBoss armadillo 10x series User manual

PowerBoss
PowerBoss PB620DSL User manual

PowerBoss
PowerBoss apex 47 g User manual
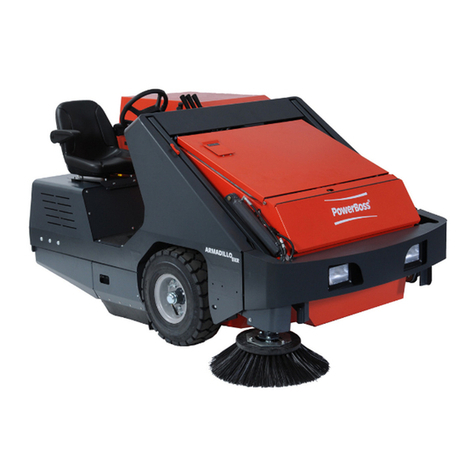
PowerBoss
PowerBoss Armadillo SW/9XR User manual
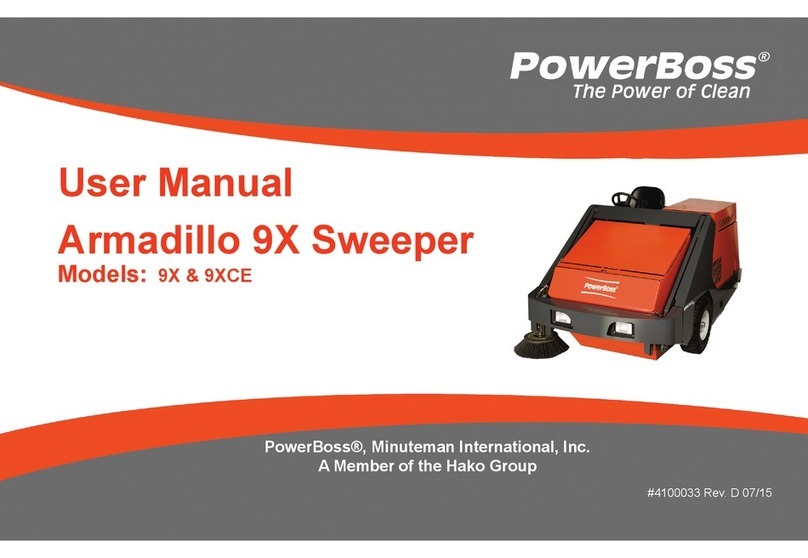
PowerBoss
PowerBoss Armadillo 9X User manual

PowerBoss
PowerBoss 82 Europe User manual
Popular Blower manuals by other brands

Jonsered
Jonsered BA101 Operator's manual
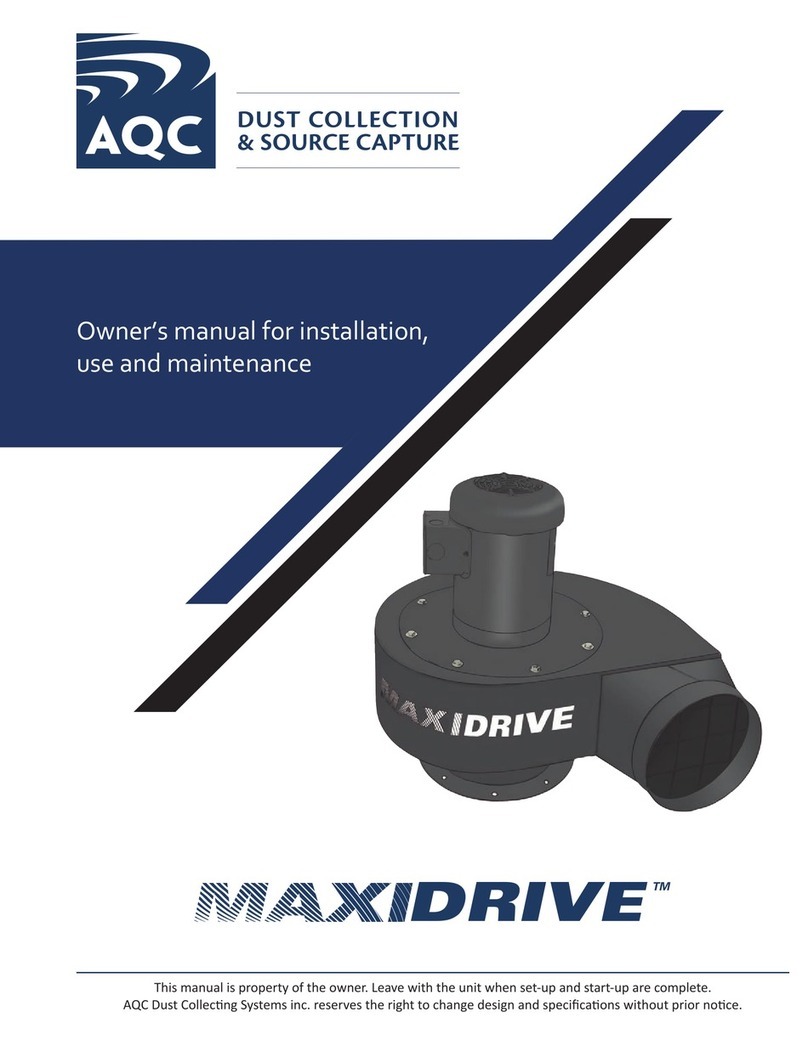
AQC
AQC MAXIDRIVE MS-DF-01A-112 Installation, use and maintenance

Poulan Pro
Poulan Pro PBV200 LE instruction manual
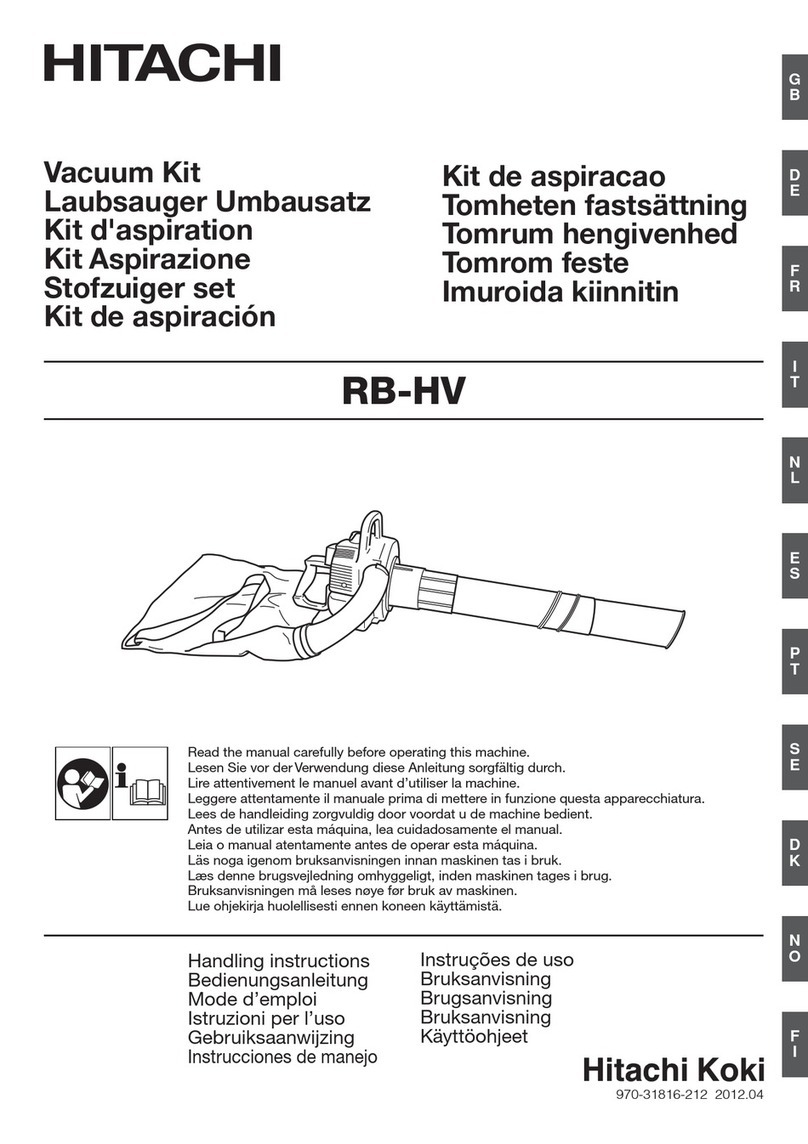
Hitachi
Hitachi RB-HV Handling instructions

Wiedenmann
Wiedenmann Mega Twister Translation of original operating instructions

Husqvarna
Husqvarna 570BTS Operator's manuar