Powermat PM-PP-40S User manual

PM0691
ORIGINAL INSTRUCTIONS
USER MANUAL
PLACE IMAGE HERE
PLASMA CUTTING
PM-PP-40S

2
TABLE OF CONTENTS
SYMBOLS WARNING / INFORMATION .............................................. ........................................... 3
PURPOSE OF THE DEVICE ................................................ .................................................. ............... 4
SAFETY ................................................. .................................................. ................................ 5
Safety during welding ............................................... .................................................. .... 5
General safety ............................................... .................................................. ... 7
Protection against electric shock .............................................. ............................................ 8
Electromagnetic field ................................................ .................................................. .................. 8
Pacemakers ................................................ .................................................. ............................... 9
Activities while cutting ............................................... .................................................. .................... 9
Prohibited Actions ................................................ .................................................. ........................ 9
Basic activities after work ............................................. ....................................... 9
Final remarks ................................................ .................................................. ................................. 9
DESCRIPTION OF THE DEVICE ................................................ .................................................. ............................... 10
DESCRIPTION OF SYMBOLS ON THE LABEL ............................................. ..................................... 11
TECHNICAL DATA ................................................ .................................................. .............................. 12
INSRUKCJA INSTALLATION AND USE .............................................. ................................................. 12
Assembly welding mask ............................................... .................................................. .............. 12
Place using the unit ............................................... .................................................. ...... 13
Current power and grounding .............................................. .................................................. ............... 13
Cutting service ................................................ .................................................. ......................... 14
Description of the process of cutting ............................................... .................................................. ........................... 14
The most common disruption cutting .............................................. ............................................ 19
MAINTENANCE AND STORAGE ............................................... .................................................. .. twenty
Maintenance ................................................. .................................................. ................................... twenty
Storage ................................................. .................................................. ............................. 21
SERVICE ................................................. .................................................. ................................................ 21
WARRANTY ................................................. .................................................. ....................................... 22
Exclusions warranty ............................................... .................................................. ... 22
REMOVAL OF USED ............................................... .................................................. ....... 22
COMPANY INFORMATION ................................................ .................................................. ............................ 23
DECLARATION OF CONFORMITY ................................................ .................................................. .................... 23

3
SYMBOLS WARNING / INFORMATION
ATTENTION: Before using the device please read the instruction manual and safety ATTENTION: Before using the device please read the instruction manual and safety
instructions. Keep these instructions.
ATTENTION: General warning sign notes for each user on the general danger. It is ATTENTION: General warning sign notes for each user on the general danger. It is
combined with other instructions warning or other symbols that failure can lead to
personal injury or equipment damage.
ATTENTION: Use welding protective footwear. ATTENTION: Use welding protective footwear.
ATTENTION: Disconnect the device from the mains before carrying out maintenance and ATTENTION: Disconnect the device from the mains before carrying out maintenance and
cleaning.
ATTENTION: Use welding helmet or shield. ATTENTION: Use welding helmet or shield.
ATTENTION: Secure the cylinder from falling over. ATTENTION: Secure the cylinder from falling over.
ATTENTION: Use welding gloves. ATTENTION: Use welding gloves.
ATTENTION: Wear protective welding kneading. ATTENTION: Wear protective welding kneading.
SIGN crossed out wheeled bin: Warrant separate collection of WEEE and the prohibition SIGN crossed out wheeled bin: Warrant separate collection of WEEE and the prohibition
of throwing it together with other waste. Please refer to the "REMOVAL OF USED Error! of throwing it together with other waste. Please refer to the "REMOVAL OF USED Error!
You can not find the source references. " You can not find the source references. "

4
PURPOSE OF THE DEVICE
Plasma cutting PM-PP-40S is designed for manual or machine air plasma, electrically conductive parts made of
carbon steel and alloy steel, aluminum and its alloys, brass, copper, and iron. Special equipment allows cutting torch
in confined areas and in all possible positions. The device can be used in the production processes, the work bench,
repair, as well as scrap cutters. The cutter is provided with thermal overload protection, ground cable, service unit, the
power cable. The advantage of this cutting is small weight and size, and continuous regulation of the current for high
cutting quality of the cut material. The device has been built based on the latest technology uses IGBTs, which
translates into a reduction of electromagnetic interference, low power losses, increasing the efficiency and reliability of
the power supply, and lower energy consumption. The manufacturer is not liable for damages resulting from misuse.
For safety reasons, the device can not be used by children and young people under the age of 18 and by persons
under the influence of alcohol, drugs or other intoxicants.
Persons who are not familiar with this manual, please read carefully before its first use.

5
SECURITY
This section covers basic safety rules when working with the use of plasma cutting.
B SECURITY DURING WELDINGB SECURITY DURING WELDING
ELECTRIC SHOCK CAN KILL: Welding apparatus produce a high voltage. Do not touch ELECTRIC SHOCK CAN KILL: Welding apparatus produce a high voltage. Do not touch
the torch, welding material connected when the device is turned on to the network. All the
elements forming the welding current circuit may cause electric shock, so you should
avoid touching their bare hand and by wet or damaged protective clothing. Never work on
a wet surface or use damaged welding cables. NOTE: Removing the external time when
the device is connected to the network, as well as the use of the device with the covers
removed is prohibited! Welding cables, ground cable, earthing terminal and welding
equipment should be kept in good condition, ensuring safety.
ARC RAYS CAN BURN: It is not allowed to look directly at the eyes uncovered and ARC RAYS CAN BURN: It is not allowed to look directly at the eyes uncovered and
exposed to an electric arc. Always wear a mask or helmets protected with a suitable filter.
Bystanders, nearby, protected with non-combustible, absorbing radiation screens. Protect
the exposed parts of the body suitable protective clothing made of non-combustible
material.
FUMES AND GASES CAN BE DANGEROUS: In the welding process are FUMES AND GASES CAN BE DANGEROUS: In the welding process are
produced noxious fumes and gases hazardous to health. Avoid breathing these
fumes and gases. Workplace should be adequately ventilated and equipped with
exhaust ventilation. Do not weld in confined spaces. The surfaces of the elements
to be welded should be free from chemical impurities such as degreasing agents
(solvents) which decompose during welding to produce toxic gases.
ATTENTION: Disconnect the device from the mains before carrying out maintenance and ATTENTION: Disconnect the device from the mains before carrying out maintenance and
cleaning.
SPARKS CAN CAUSE FIRE: Sparks generated during welding can cause fire, SPARKS CAN CAUSE FIRE: Sparks generated during welding can cause fire,
explosion and burns unprotected skin. When welding should be wearing welding
gloves and protective clothing. Remove or secure any flammable materials and
substances from the workplace. Do not weld closed
containers or receptacles in which there were flammable

6
liquids. Such containers or tanks should be rinsed prior to welding in order to
remove flammable liquid. Do not weld near flammable gases, vapors or liquids.
Fire extinguishing equipment (fire blankets and fire extinguishers powder or snow)
should be located
near his workstation in a conspicuous and easily accessible place.
POWER SUPPLY: Disconnect the power supply before carrying out any work, repairs on POWER SUPPLY: Disconnect the power supply before carrying out any work, repairs on
the device. Regularly check the welding cables. If you note any damage to the wire or
insulation should be removed immediately. Welding wires can not be overwhelmed, touch
sharp edges or hot objects.
Intersects the MATERIALS CAN BURN: Never touch intersected elements unprotected Intersects the MATERIALS CAN BURN: Never touch intersected elements unprotected
parts of the body. While touching and moving the cut material, always use gloves and
welding pliers.
Noise can damage hearing: Noise-induced, some processes or equipment can damage Noise can damage hearing: Noise-induced, some processes or equipment can damage
hearing. Wear hearing protection in situations of increased noise levels.
FIRE OR EXPLOSION: Do not use the machine near flammable substances. Make sure FIRE OR EXPLOSION: Do not use the machine near flammable substances. Make sure
that the electrical network is properly configured to work with the welder. Overloading the
power supply may cause fire.
FALLING EQUIPMENT CAN BE DANGEROUS: To move the machine, use the FALLING EQUIPMENT CAN BE DANGEROUS: To move the machine, use the
handle of transport. All the equipment necessary to lift the unit must have sufficient
capacity and stable hook. When moving the machine by forklift truck, the forks
must be long enough to protrude beyond the device.
Overload can cause overheating: Do not extend the cycle of welding, welding Overload can cause overheating: Do not extend the cycle of welding, welding
between cycles allow the device to cool. In the case of excessive heating of the
device, shorten the cycle time of welding or reduce the welding current.
STATIC DISCHARGE MAY DAMAGE THE PRINTED CIRCUIT:
Before touching the printed circuit boards and parts of the electrical system should
be assumed grounding wrist-strap. Use of antistatic packaging is storing and
transporting electrical components.

7
READ INSTRUCTIONS: Carefully read the manual and follow the information READ INSTRUCTIONS: Carefully read the manual and follow the information
contained therein. For any damage caused by failure to comply with the guidelines
of this manual manufacturer is not liable.
HIGH FREQUENCY RADIATION: High-frequency radiation can zakłucać radio HIGH FREQUENCY RADIATION: High-frequency radiation can zakłucać radio
signals, alarm systems, work computers and communications equipment. User is
obliged to ensure a qualified electrician correct the problems resulting from
zakłucenia electrical installation. Regularly check and maintain electrical
installations. Use grounding and shielding and anti-surge protection measures to
minimize any zakłucenia.
ARC CUTTING CAN CAUSE INTERFERENCE: Electromagnetic energy can ARC CUTTING CAN CAUSE INTERFERENCE: Electromagnetic energy can
interfere with electronic equipment such as computers and computer-controlled
equipment. Make sure that the hardware devices in the work environment welders
are electromagnetically compatible. To minimize the potential for interference stick
welding wires close to each other, as close to the ground. In the case of electrical
equipment susceptible to interference spot welding should not be closer than
100m. The device must be connected and grounded in accordance with this
instruction. If noise still persists the user needs to take additional measures such
as changing jobs, the use of shielded cables, filters, linear and securing jobs.
General safety
Before each use, check that the correct pressure is set and the flow of air.
Before each use, check that the burner components - nozzles, electrodes, bushings, etc. - are properly selected
and installed correctly.
Before you begin using this unit, please read well with all operating elements. Practice handling of
the device and ask the professional about the features, mode of action and work techniques. Make
sure that in case of failure will be able to switch off immediately. Improper use of the device can lead
to serious injury.
The protective device and personal protective equipment to protect your own health and the health
of third parties and guarantee flawless operation.
• Use only parts and accessories supplied and recommended by the manufacturer.

8
• Never grasp the device by knives or hold it for the device protective cover. Do not move the device
connected to the network, keeping your finger on / off switch.
• Disconnect from the network when not in use, you want to transport them or you leave them unattended,
and when you run it, or clean the control.
• Do not attempt to repair the machine unless you have to adequate education. Any work that is not described
in this manual, can be performed only by authorized service.
• Do not carry the appliance by the cord. Do not use the cable to pull the plug from the mains. Protect the
cable from heat, oil and sharp edges.
•Do not use the machine near flammable liquids or gases. In the event of non-compliance with this recommendation
there is a danger of fire or explosion.
• The user is responsible for accidents or injuries caused by other people and for the resulting damage to their
property.
• Store in a dry place out of reach of children.
• Handle your device carefully. Keep the device in such a state that the head was clean to be able to work
better and safer. Follow the maintenance regulations.
ABOUT ROTECTION AGAINST ELECTRIC SHOCKABOUT ROTECTION AGAINST ELECTRIC SHOCK
• Note the mains voltage is in accordance with the data on the nameplate.
• Before each use, check the unit and power cord with plug for damage. Avoid body contact with grounded
parts (eg. The metal fence, metal bar).
• Cable socket must be protected against splashing water, made of rubber or covered it. Use only an
extension which is intended for use in the open air and are marked accordingly.
•Place the wire away from the work area and keep that in mind so that it is for the person that supports the device.
• Do not use damaged cables, connectors, plugs, or inconsistent with the provisions of the connecting cables.
In case of damage or cut power cord immediately pull the plug from the socket.
• Do not use the device if you can not turn on or off switch. Replacement of defective switches should be
ordered at the point of customer service.
• Do not overload the machine. Work in a given power range. Do not use machines with low power to perform
heavy work. Use your device only for the purposes for which it was designed.
P OLE ELECTROMAGNETICP OLE ELECTROMAGNETIC
To reduce the amount of electromagnetic fields in the workplace include:
1. Keep cables close together (you can turn the tape or taped). 1. Keep cables close together (you can turn the tape or taped).
2. Organize the wires from one side of the operator as far as possible from him. 2. Organize the wires from one side of the operator as far as possible from him.
3. Do not wrap the cables around the body. 3. Do not wrap the cables around the body.
4. The power source and wires should be as far away from the operator as possible. 4. The power source and wires should be as far away from the operator as possible.
5. Connect the terminal welding seam as close as possible. 5. Connect the terminal welding seam as close as possible.

9
R OZRUSZNIKI HEARTR OZRUSZNIKI HEART
You should consult your doctor before welding and welding being in place. The doctor will explain the procedure if
any of the contact with the welding apparatus.
C ZYNNOŚCI WHEN CUTTINGC ZYNNOŚCI WHEN CUTTING
a) Secure the workplace, as long as there is no fixed and mobile screens with anti przeciwodpryskowymi.
b) Use for cutting electric wires and an operating handle only in good condition (intact insulation).
c) Use only the correct thickness of the electrodes and nozzles.
d) Attach and set accurately and reliably cut the object and so has not been damaged.
e) Set the detail to be cut so as to prevent them from shifting or overturn.
f) when cutting inside the boilers, tanks or in a confined space by whatever ventilation use respiratory protection.
g) When operating inside the tanks, boilers and other metal rooms used electric lighting 24V.
h) Make sure that the workpiece does not risk falling or moving away the dangerous to the welder.
i) When working on scaffolding check the status of their efficiency.
j) Protect the respiratory tract, eyes, face and hands from burns and exposure through the use of appropriate
personal protection.
k) Switch individual air extraction, when this is established, the gaseous effluents are removed from the position.
l) Use only proper, undamaged and not oiled tools and support workshop.
C ZYNNOŚCI PROHIBITEDC ZYNNOŚCI PROHIBITED
Welder forbidden:
a) Capture of hot metal prepared for cutting and after cutting.
b) Isolated repair damaged electrical cables (electrical system).
c) During work breaks stick under his arm, operating handle or mass.
d) masks moving away too far from the welding face, her deposition before the arc goes out, as well as inflammation of the arc
without face protection.
e) Welding without proper grounding of the workpiece.
f) applying a temporary connection welding equipment.
g) Cause to the floor at the work station was wet, slippery, uneven, contaminated waste, previously blocked.
P ASIC OPERATIONS AFTER WORKP ASIC OPERATIONS AFTER WORK
Welder should:
a) Turn off the machine from the power supply.
b) Check that the job of a position or next to the fire was not dusty.
c) Organize your work station.
d) Organize welding equipment.
AT FINAL BALANCEAT FINAL BALANCE
a) When performing welding work inside the tanks, boilers or other confined spaces (up to 15m 3) welder a) When performing welding work inside the tanks, boilers or other confined spaces (up to 15m 3) welder a) When performing welding work inside the tanks, boilers or other confined spaces (up to 15m 3) welder
should be insured by another person, who will remain on the outside.

10
DESCRIPTION OF THE DEVICE
MODEL: PM-PP-40S
DESCRIPTION OF
1. LCD display (ammeter) 1. LCD display (ammeter) 9. Gas pressure control
2. Adjustment of gas flow 10. Manometer
3. power LED 11. Socket gas conduit
4. LED overload 12. oil separator
5. Adjusting the current 13. Turbo-fan
6. Jack ground wire 14. Power cord
7. HF socket ionizer 15. On / off switch
8. Slot handle plasma

11
DESCRIPTION OF SYMBOLS ON THE LABEL
Current (DC)
Symbol single phase alternating current (AC) of the rated frequency 50Hz and 60Hz
operating frequency.
AT 1 Nominal input voltage (AC)AT 1 Nominal input voltage (AC)AT 1 Nominal input voltage (AC)
AND 1max Maximum input currentAND 1max Maximum input currentAND 1max Maximum input current
AND 1EFF Effective input currentAND 1EFF Effective input currentAND 1EFF Effective input current
AT 0 No-load voltage (load voltage) AT 0 No-load voltage (load voltage) AT 0 No-load voltage (load voltage)
AND 2 output current AND 2 output current AND 2 output current
AT 2 The output voltage under load AT 2 The output voltage under load AT 2 The output voltage under load
X
welding cycle
(This percentage ratio of working time under load to full duty cycle)
•The value of 0-100%
• Standard for this device, one full cycle is 10 min. For example, 40% of the
cycle allows for continuous cutting under load for 4 minutes. and the time to
"rest" should last 6 minutes. When the time under load the machine is
switched off by the thermal fuse.
The device welded single-phase DC
The device is used for plasma cutting
Graph current
The device can operate in potentially electric shock

12
TECHNICAL DATA
Model PM-PP-40S
Cutting current range 10-40
Power 230V 50 / 60Hz
input 6,5kVA
Rated cutting current 40A
Rated duty cycle 60%
Cutting current at 100% duty cycle 31A
operating voltage 85V - 96V
The maximum depth of penetration 12mm
The maximum penetration depth qualitative 8mm
The required air pressure 4-5bar
Demand for air 189l / min
arc ignition HF
insulation class H
Level of security IP21S
Technology of IGBT
Net weight 6,1kg
INSRUKCJA INSTALLATION AND USE
M ONTAŻ welding masksM ONTAŻ welding masks
Welding mask assembly is performed according to the diagram.
1. Connect the cutter to a power source, exit located on the rear of the unit. 1. Connect the cutter to a power source, exit located on the rear of the unit.
2. Connect the ground wire to the quick and the workpiece. 2. Connect the ground wire to the quick and the workpiece.
3. Fit the tungsten electrode. 3. Fit the tungsten electrode.
4. Switch to the ON position and make sure the power LED indicator lights up 4. Switch to the ON position and make sure the power LED indicator lights up
yellow.

13
5. Set the parameters for the material being cut. 5. Set the parameters for the material being cut.
6. You can start the process of cutting press the button on the handle. 6. You can start the process of cutting press the button on the handle.
7. After completion of the cutting move the electrode from the material to be cut, and set the switch 7. After completion of the cutting move the electrode from the material to be cut, and set the switch
the device in the OFF position.
Warning! At the time of exceeding the cycle provided for the amperage thermal circuit breaker lock the device Warning! At the time of exceeding the cycle provided for the amperage thermal circuit breaker lock the device
(indicated by yellow LED Overload) until cool cutting.
Warning! Do not change the current cut during operation. Warning! Do not change the current cut during operation.
If your machine or its accessories will begin to work properly you should refrain from further work and contact a
qualified service center.
M P lace DEVICEM P lace DEVICE
The device can be used only in well-ventilated place.
Before working at the site of use should always take into account the guidelines for safety contained in the section
"GENERAL"
Welding cables must be connected to the output of the power source at a cutter. The power cord cutter should be
connected to 230V AC power source.
Do not place the cutter on a wet surface, it may cause electric shock and damage.
Regularly check the device, if problems do not start working and contact service.
The spray nozzle within the scope thickness.
Use wear protective gloves, apron welding, shoes, helmet or mask welding.
Remove all flammable materials from the area.
P RAD POWER AND EARTHP RAD POWER AND EARTH
Only qualified personnel may perform installation and modification of the electricity grid.
Warning! It is forbidden to use the device or completely dismantled the housing removed, it may cause electric shock Warning! It is forbidden to use the device or completely dismantled the housing removed, it may cause electric shock
and lead to severe injury. Do not touch the energized equipment.
Before installing the unit, check electrical network to which the device is connected meets the requirements placed on
the nameplate and that it meets all local and national standards. Keep in mind that different models of plasma cutters
may have different requirements for the electricity grid.
1. Before connecting check whether the network meets the requirements of cutting. 1. Before connecting check whether the network meets the requirements of cutting.
2. Connect the PE or green / yellow ground wire to the grounding system in accordance with the 2. Connect the PE or green / yellow ground wire to the grounding system in accordance with the
national regulations.

14
3. Connect the welding cables to the device, then the power cord to a single-phase network 3. Connect the welding cables to the device, then the power cord to a single-phase network
the electric voltage of 230V and frequency of 50Hz.
Warning! Plasma cutters are very sensitive to voltage drops in the power supply. The electrical network should have Warning! Plasma cutters are very sensitive to voltage drops in the power supply. The electrical network should have
a stable voltage supply lines and a cross-section of not less than 2.5 mm.
ABOUT Advan SAWSABOUT Advan SAWS
Attaching the plasma torch
1. Before connecting to the mains, make sure that the main switch 1. Before connecting to the mains, make sure that the main switch
the device is in the off position.
2. Check that the equipment and installation is grounded and reset, and the earth wire 2. Check that the equipment and installation is grounded and reset, and the earth wire
finished terminal.
3. End of the mass connected to the socket on the front panel 3. End of the mass connected to the socket on the front panel
devices.
4. Plasma torch cable connected to the socket on the front panel. 4. Plasma torch cable connected to the socket on the front panel.
Compressed air connection
For the cutting operation, it is necessary to provide clean, dry air or nitrogen. Gas source should be equipped with a
Micro-filter and provide a pressure of from 4 to 4.5 bar and air flow of 100 - 280 l / min. Failure of these parameters
may increase the temperature or failure of the device.
1. Connect the device to a source of compressed air paying attention to required 1. Connect the device to a source of compressed air paying attention to required
parameters.
2. Turn the pressure regulator pre-set level of pressure of the compressed air 2. Turn the pressure regulator pre-set level of pressure of the compressed air
the power supply unit.
3. Without energizing the handle to set the value of the normal gas flow in the circuit 3. Without energizing the handle to set the value of the normal gas flow in the circuit
a handle for plasma cutting.
ABOUT PIS CUTTING PROCESSABOUT PIS CUTTING PROCESS
Plasma cutting process involves melting the metal and the disposal of the cut highly concentrated plasma electric arc
glowing between tungsten and cut the object. Plasma arc is highly ionized gas with high kinetic energy, moving the
plasma jet, in the direction of a narrow kerf, close to the speed of sound. The temperature of the plasma jet is in the
range 10000˚ 30000˚ [K], and is dependent on the current intensity, the degree of constriction of the arc and the type
and composition of the plasma gas. Plasma cutting is only used current of negative polarity. For metal cutting they are
used only for arc plasma torches dependent. Arc ignition burners of the dependent arc is carried out with a pulse
current of high voltage or high-frequency (HF). It is possible to cut all construction materials electrically conductive.
The process of plasma cutting is used to cut the manual and mechanized robotized steels and non-ferrous metals at
high speeds in all positions. A disadvantage of the process is very high noise, danger of fire, a strong light radiation
curve, a large number of gases and fumes.

15
Depending on the thickness of the cut material closer bracket to the workpiece at a minimum distance, but without
touching, (refers to a material having a thickness up to 1.5 mm) or maintaining it at a distance of about 4 ~ 5 mm, ie.
Set by a spring spacer, or the diagonal predetermined for insulating nozzle holder (for all material thickness). Switch
the button on the handle. Will ignition pilot arc between the electrode and the nozzle holder, while the air valve is
opened. This will blow out the nozzle pilot arc and the main arc ignition and thus begin the cutting process, which will
continue until you release the button on the handle. In order to avoid interference arcing during cutting, to move the
holder relative to the material should be uniform. about- 90 about element to cut, at a constant distance therefrom. holder relative to the material should be uniform. about- 90 about element to cut, at a constant distance therefrom. holder relative to the material should be uniform. about- 90 about element to cut, at a constant distance therefrom. holder relative to the material should be uniform. about- 90 about element to cut, at a constant distance therefrom. holder relative to the material should be uniform. about- 90 about element to cut, at a constant distance therefrom.
In case of interruption arcing during cutting (resulting hole in the cut, too slow cutting speed, etc.) Will be
automatically re-ignition pilot arc.
Correct evaluation of cutting speeds seems to be based on observation of the exhaust flow of the material and evaluation of
the angle at which the cutting material is ejected on the side of its lower edge, and based on the examination of the cut
surfaces after the cutting test.
The best cutting results are obtained using the maximum speed.
Start the process of cutting requires skill and caution, especially when cutting thin sheet steel and aluminum. In such
cases, the cut should begin slowly to properly penetrate the material. Cutting speed can be increased, after
penetrating the lower edge of the arc of the cut material.
During normal operation of the handle a distance (the distance between the tip of the nozzle and plate) provides a
spacing spring or cap angle. A handle (nozzle) may be in direct contact with the material at the time of cutting only to
the first of the above cases, i.e. ignition. For thickness of cut up to 1.5 mm. It should be noted that the cutting of the
material in this way requires more manual operator skill, since the initiation of cutting minimum distance from the
material to be cut, would cause chipping of the material, adhering to the nozzle, and consequently the risk of damage.

16
optimum speed Too fast
Maximum speed Too slow
In the case where the cutting speed is too high, the flow is not able to sufficiently melt the metal and to throw it on the
outside part of the cut, which may lead to direct a portion of the molten metal to the die, and thus lead to serious damage
of the handle when the continuation of the cutting in these conditions.
For the alloy steel should be taken as the cutting speed of less about 5%, and aluminum for higher by about 20%. The
indicated dispersion according to have the cutting speed for one value of the thickness of the material having the same
speed ratio of the cutting conditions. Cutting speed of material depends on many factors:
-the thickness and type of material to be cut,
-setting of cutting current,
-the geometric shape of the cutting line (straight or curved).
We do not recommend the pilot arc with no intention of cutting, as it causes unnecessary wear on the handle ie. The
electrode and the nozzle.

17
In the case of solar flares arc or when the flame will be green, or arc will emit any "abnormal" sound, switch the
device off immediately and check the condition of wearing parts.
Continuing the cut in the "abnormal" conditions may lead to damage or destruction of the holder.
cutting holes
It is advisable to start from the cutting edge of the board or opening. When cutting a hole is recommended (drill) hole,
the edge of which begins cutting the appropriate hole. Making holes without such an operation is possible, but causes
ejection of material in the top, which can be dangerous and involves the risk of damaging the nozzle spring spacer
and, consequently, of the whole handle.
If you need to make holes, it is recommended to start with them, holding
holder at an angle and then gradually straighten it to the upright position until breakthrough through the material.
Then you can make a hole of the intended shape.
Wrong Well
Cutting can be interrupted by releasing the button on the handle, which will instantly arc goes out, and after about 1
minute off the flow of compressed air. delay in

18
switching off the flow of compressed air through the handle is due to the need to cool the heated components of the
handle.
It is prohibited to turn off the device by switching the switch in the off position before the automatic closing of the air valve
after the completion of the cutting process.
The most common reason for limiting the durability of wearing parts are damaged consumables.
One of the most frequent causes of causing damage to the operational cut material is intruded into the hole nozzle -
especially during drilling, or blockage of the nozzle piece of the workpiece.
It is advisable to maintain a constant distance from the workpiece, work at the maximum speed allowed by the device.
For best results on materials with a small degree of risk reflection of the material being cut, such as clean mild steel,
thin sheets, and the like.
proper use
Consumables holder, such as nozzles, electrodes, spacers, covers, etc. Consume and are not subject to warranty !!!
During the replacement of worn parts should pay particular attention to the correct assembly of the individual parts - a
bad installation, or using the wrong part of the handle causes the destruction !!!! Also, providing poor quality of air (air
should be dry and free of oil) results in decreased life of the handle and wear parts.
Before cutting, check that all items are correct and properly mounted in the holder.
Resolution of the nozzle should be selected for the intended current and material thickness.
The electrode must be replaced if the crater reached a size 1.5 to 2 mm.
Cutting consumed electrode does not give the expected quality and may cause damage to the holder.
Sectional view of the electrode consumed
The nozzle should be replaced, if the opening is a "zoomed", or oval. In the case of the used cutting nozzle it becomes qualitatively
worse and slower.
The most common mistakes
-improper pressure setting incorrect pressure - too high or too low - will make the cut will be difficult or impossible,
the cutter can signal failure. It can cause damage to the operating handle.
-reverse diffuser assembly, the diffuser is a small bronze ring with holes, which apparently looks the same from both sides, and
the opposite assumption is a common cause of failure.

19
-screwing the electrode pliers, followed by the formation of the "burr" on the electrode, its curvature and often the result of
disturbances in the flow of plasma, etc. breakthrough.
-improper installation when replacing any parts should pay special attention to whether they are designed for a particular
model and that are established in the correct order.
-cutting the used electrode, nozzle, cutting the used electrode does not give the expected quality, in the case of a used cutting
nozzle it becomes qualitatively worse and slower. In both cases, it can cause damage to the handle and equipment.
-reaming nozzle szlifowanie- sample recovery, any attempt to regenerate the nozzle electrodes are not allowed and their efforts
result in damage to the handle and the machine.
-no use of air handling components (dirty, wet air). poor quality of the air contributes to the rapid wear of the handle,
and may cause damage.
-wrong connection of the cutting medium (e.g.,. oxygen instead of air)
Connecting to the device of any flammable gas, propane, acetylene, oxygen is extremely dangerous and
threatens, in addition to the damage, loss of health and even of life.
N AJCZĘSTSZE INTERFERENCE CUTTING WORK Attention! Before any interference in the cutting N AJCZĘSTSZE INTERFERENCE CUTTING WORK Attention! Before any interference in the cutting N AJCZĘSTSZE INTERFERENCE CUTTING WORK Attention! Before any interference in the cutting
machine, disconnect the unit from the mains.
SYMPTOMS CAUSE
The device does not start
-unknown phase voltage supply
-fuse
-attached thermostat, abnormal air pressure device or a cooling liquid
The pilot arc turns bad
-worn or incorrectly founded electrode
-worn or incorrectly founded nozzle
-unknown phase voltage supply
Cutting stream does not light up
-worn or incorrectly founded electrode
-worn or incorrectly founded nozzle
-unknown phase voltage supply
Poor cutting performance, noise
cutting jet during the cutting, the
formation of slag
-worn nozzle
-worn electrode
-incorrect switch position ranges
-wrong nozzle distance from the element to be cut
-incorrect ground connection cut element
-incorrect voltage supply
-incorrect air pressure
-too low cutting speed
-too large a thickness of the material to be cut

twenty
Excessive slag on the bottom
cutting edge
-too low cutting speed
-too large a thickness of the material to be cut
The main arc is not perpendicular
a workpiece
-defective nozzle opening
-burned center electrode
-poorly folded wearing parts
Excess cutting edge or
rounded surface
-too high cutting speed
-too big a gap
-the arc is not on the axis
MAINTENANCE AND STORAGE
Before performing any work on the device, pull the plug from the socket.
The works, which were not described in this manual, the order authorized customer service point.
Use only original parts.
K REPLACEMENTK REPLACEMENT
ATTENTION:
A device based on electronic components. Grinding and cutting in the vicinity of the welding device
can contaminate the swarf inside the device, thus leading to damage.
The above-mentioned damage is not covered by warranty! In the case of having to work in such an
environment must be made to clean the machine by blowing compressed air inside of the welder.
To extend the service life and reliable operation, observe a few rules:
1. The device should be placed in a well-ventilated room, where 1. The device should be placed in a well-ventilated room, where
there is a free circulation of air.
2. Do not place the device on a wet surface. 2. Do not place the device on a wet surface.
3. Use a wire diameter and a weight of the spool in accordance with disposed on the table. 3. Use a wire diameter and a weight of the spool in accordance with disposed on the table.
4. The gas cylinder protective set on the shelf at the back of semi-automatic and secure 4. The gas cylinder protective set on the shelf at the back of semi-automatic and secure
with the chain of the possibility of tipping over.
5. Check the condition of technical equipment and welding cables. 5. Check the condition of technical equipment and welding cables.
6. Remove all flammable material from the welding area. 6. Remove all flammable material from the welding area.
7. Welding use suitable protective clothing: gloves, lab coat, boots, face mask, 7. Welding use suitable protective clothing: gloves, lab coat, boots, face mask,
or visor.
When planning the maintenance of the device should take into account the intensity and operating conditions. Proper use of
the equipment and its regular maintenance will avoid unnecessary disruption and downtime.
Daily:
-Purify the handle by weight, and the gas nozzle chips, means lubricate against frangibility.
-Check whether the cables are correctly connected.
-Check the condition of the pipes. Replace damaged cables.
Table of contents
Other Powermat Cutter manuals
Popular Cutter manuals by other brands
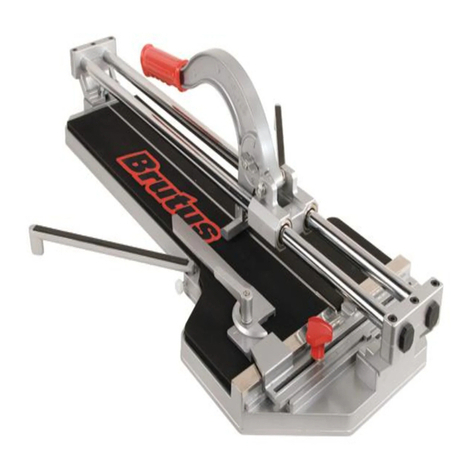
Big clinker
Big clinker 10500 20 In. owner's manual
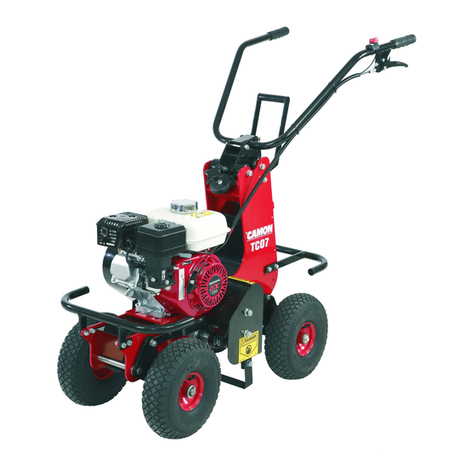
Tracmaster
Tracmaster CAMON TC07 Operating instructions & safety notes
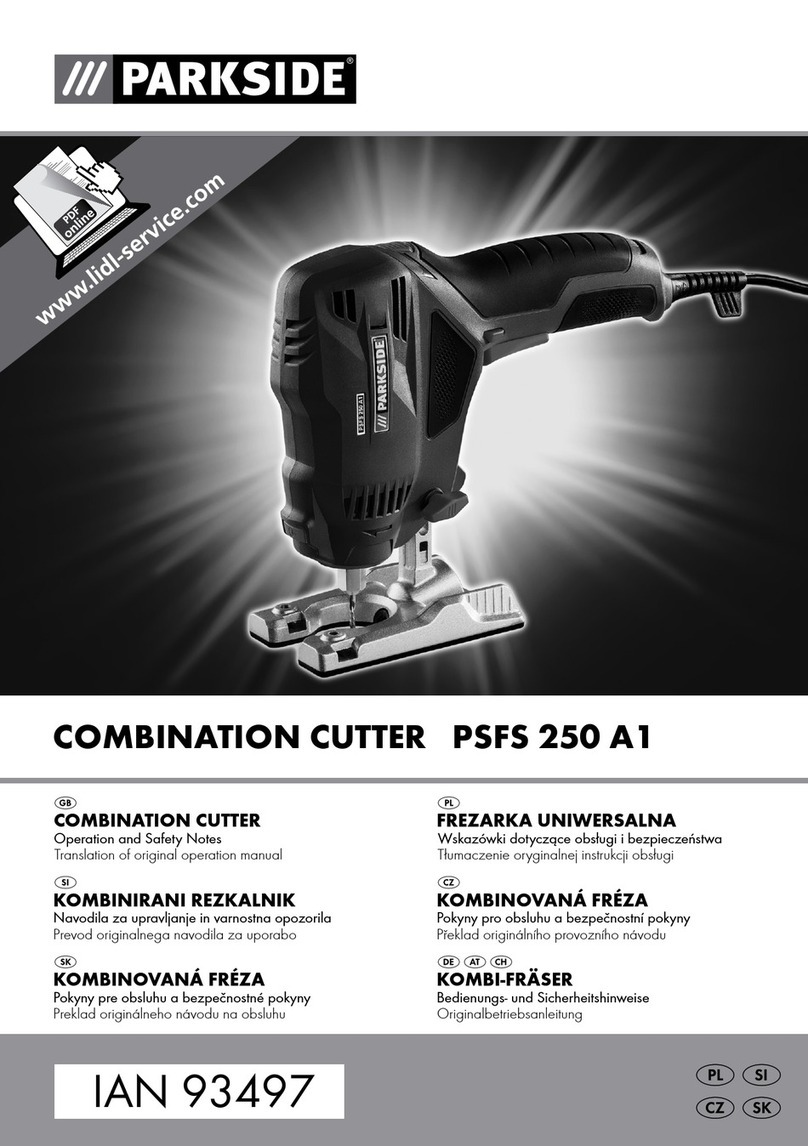
Parkside
Parkside 93497 Operation and safety notes translation of original operation manual
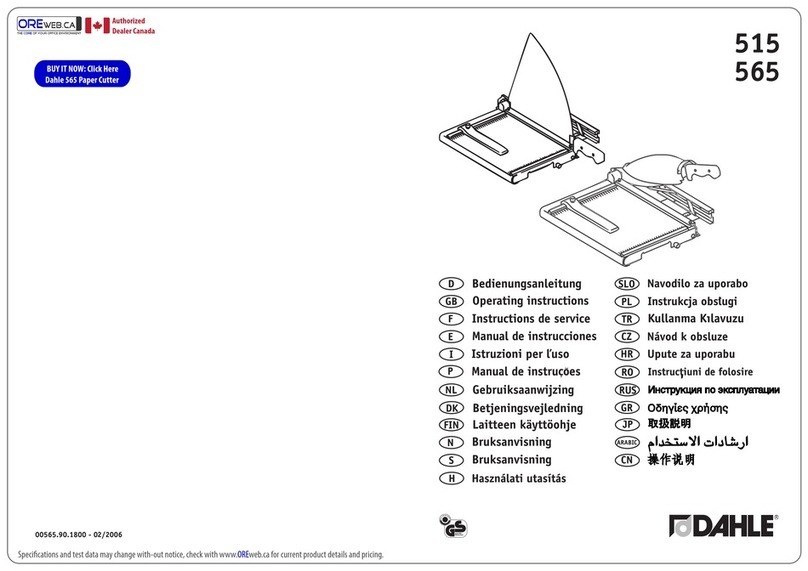
Dahle
Dahle 515 operating instructions

HUAYUAN
HUAYUAN LGK-63/100MA Operator's manual
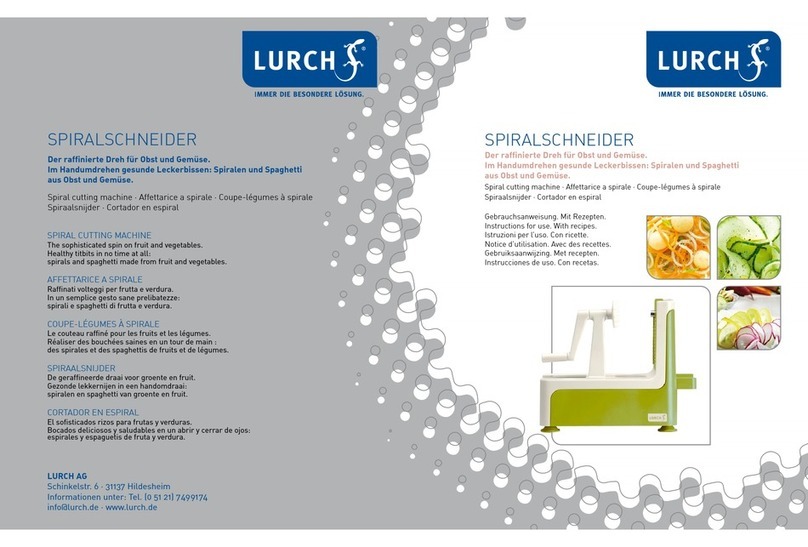
Lurch
Lurch 19736 user manual