PSI Woodworking LIXGA User manual

1
#LIXGA Router Index Guide
User Manual
Cuts flutes on your turning projects
Mounts to lathes with indexing feature or indexing attachment

2
The #LIXGA Router Index Guide is warranted against defects in materials and workmanship for a period of two
(2) years from the date of purchase. This warranty applies to the purchaser of this product, and is limited to repair or
replacement of the product or it’s parts at PSI Woodworking Products’ discretion. Excluded are parts, which have been
misused, abused, altered, or consumed by normal operation of the machine. Also excluded are direct or consequential
damages to the persons, property, and/or materials. Your invoice serves as proof of purchase and must be referenced
prior to return authorization. Contact your dealer where you purchased your #LIXGA for service or repair issues.
1. Read and understand this instruction manual.
2. NEVER connect plug to power source until all the assembly steps have been completed.
3. Check that your supply voltage and grounding are correct for both lathe and router.
4. Do not use the lathe in a damp or wet location.
5. Make sure the lathe belt, pulley, and control box and router are adequately guarded at all times.
6. Keep the work area clean, well lit and adequate ventilation in the workspace.
7. Keep young children and bystanders a safe distance from the lathe and router.
8. Do not wear loose clothing, jewelry or neckties, which could get caught in revolving parts.
It is recommended that long hair be restrained.
9. Safety eye wear should be worn at all times. Also, it is recommended to use a face or dust mask during
lathe or router operation.
10. Attach all work pieces securely to the lathe, whether between centers, on faceplates,
or in chucks, etc.
11. For best results use sharp router bits.
12. Always use an appropriate travel speed for the wood and projects being fluted or turned
- Slow speeds for larger bowls, faster speeds for smaller spindles.
13. Always check that the index/spindle lock knob is disengaged prior to turning on the lathe.
14. Always check that indexing spindle lock knob is engaged when cutting a flute with the router.
WARRANTY
SAFETY INSTRUCTIONS
Indexing Requirements
NOTE: Check your lathes operating manual to understand how the
index feature works on your lathe.
If your indexing accessory or lathe has 24 grooves, the turning’s sections
can be made in multiples of 24, 12, 8, 6, 3 and 2. For example, to make 8
equal sections, mark your work at 1, 4, 7, 10, 13, 16, 19 and 22. Advance the
indexing pin to lock the head stock spindle in place until it engages.
Always back the index pin out before advancing to the next indexing position
on the lathe
DATE PURCHASED__________________________INVOICE NO.________________________

3
For making Flutes on turnings using the Indexing Features found on Modern Mini / Midi Lathes
Requirements:
• Trim Router with about 3” diameter body & 3” flat portion for mounting
• Split bed Lathe with 18” bed.
• Spur Center and Live Tailstock center installed Lathe or lathe accessories with indexing capability.
• Lathe swing variable 8” - 16”. Bed minimum length 16-1/2”
ROUTER INDEX GUIDE
Figure 1 Fluting Guide Platform Components
1) Guide Platform
2) Platform guide Bar
2b) Platform guide bar screw and lock nuts (2 sets)
3) Stop Collars and mounting hardware (2)
4) Mounting bolts with Knob and washers
5) Bed Mounting Grips (2 sets)
Router Transport Assembly
6) Transport Base
7) Trim Router Clamps (2)
8) Height Adjustment Post and Guard
9) Cutting Guard
10) Router Carrier Handles (2)
Other Accessories
11) “T” handle allen wrench
12) Round Nose Router Bit (not shown)
13) “V” Groove Router Bit (not shown)
14) Trim Cutter Router Bit (not shown)
Not included
15) Trim Router with body about 3” diameter (PSI item
#LIXROUT or equivalent)
Note: Before you mount up the Fluting guide, you should first turn a spindle to the approximate profile of your finished project. Use the
toolrest and traditional lathe tools. You can turn the spindle straight or with a taper depending on the final profile of your project.
(3)
Mounting stop collar to guide bar
Mounting guide bar to platform
(2b)
guide bar
stop collar
Figure 1
(1)
(2)
(3)
(10)
(8)
(9)
(2b)
(11)
(7)
(4)
(5)
(15)
Mounting base to lathe bed
(4)
Lathe bed
(5)
(2)
Figure 1a Figure 1b Figure 1c
(6)
guide platform (6)
(2)
guide platform
(1)

4
Assemble Router Transport components as shown in (Fig 2). The clamps on
the router transport will accept a trim router with a diameter to 3” with a 3” flat
area. Clamp and tighten your Trim Router into the Router Clamps as shown in
(Fig 2). The Router Carrier and Height Adjustment Post will allow you to adjust
the height of the router do not lock in place yet.
If your spindle workpiece is 0” -11”, mount the Guide Platform per (Fig 3A). If
11”-16”, then mount per (Fig 3B). Loosely mount the base to the lathe using
the Bed Mounting Grips in the lathe ways (Fig 1C). Align the Guide Platform
with your lathe bed to be as straight as possible along the bed of the lathe. At
this point it is not essential for the base to be exactly straight. Tighten the Bed
Grips using the Knobs on the Mounting bolts.
Set up
Set the Router Height (Fig 4). With the “V” bit inserted into the router, align
the point of the bit with the tailstock live center. Raise the router as necessary
by sliding the Router Carrier up or down the Height Adjustment Post. Tighten
Router Carrier in position when the bit is aligned with the Lathe’s live Center
point. Position the Router Transport base to be parallel with the lathe bed. Mark a line along the base of the Router
Transport onto the Guide Platform (Fig 5).
If you plan to flute a perfectly straight spindle align the router bit at the tailstock center point and mark a line on the platform
the same as done at the tailstock. Connect the lines with a straight edge. This “parallel reference line” defines a “zero
diameter” spindle … straight spindles of any diameter can be determined from this line.
Figure 4
Assembly and Mounting
Mounting Knobs
Figure 3A Short Spindle Mount (spindle 0-11”)
Figure 3B Long Spindle Mount (spindle 11”-16”)
Height Adjustment
Post and Guard
Router Carrier Handles
Trim Router Clamps
Headstock Tailstock
Fluting Guide Platform
Mounting Knobs
Headstock Tailstock
Figure 2 Router
Transport Assembly
shorter spindle
0 -11”
longer spindle
11”-16”

5
FIGURE 6 - Determine parallel reference line (zero diameter)
Headstock
Index locking knob
Align bit to center points Tailstock
Mark at the front of
transport platform
Draw parallel
reference line
Figure 5: Determine parallel reference line (zero diameter)
If you intend to use the fluting guide to make a straight cut - mount a straight bit into your router. Mount your turning,
either straight or conical between centers on your lathe. Press the router bit into the work at both headstock and tailstock
ends of the turning - at each end mark the platform at the base of the carrier (Fig 6).
Draw a temporary reference line as shown (Fig 6). If your spindle is going to be perfectly straight, measure from the parallel
reference line to this temporary reference line. If necessary re-draw the temporary reference line to be parallel with the
parallel reference line. Determine your depth of cut. Do not exceed 1/16” (Fig 6). Draw a final clean-up line as shown.
Optional - Making A Straight “Clean-Up” Cut
nal clean-up line
FIGURE 7 - Determine clean-up line (optional)
Headstock
Index locking knob Tailstock
Press but to front of
spindle - mark initial
clean up line
parallel reference line
Repeat on right side
draw temporary reference line
1/16” max
final clean-up line
for straight cuts final
clean-up line is equal
distance from parallel
reference line
Figure 6 - Determine clean-up line (optional)

6
Figure 7 - Mount Platform Guide for clean-up cut (optional)
nal clean-up line
FIGURE 8 - Mount Platform Guide for clean-up cut (optional)
Headstock
Index locking knob
Tailstock
Stop Collar
Trim cut router bit
Platform guide bar
Final clean-up line
Align and lock platform guide bar
in place at final clean-up line
Figure 8 - Make clean-up cut (optional)
FIGURE 9 - Make clean-up cut (optional)
Make clean-up cut
with lather turned on
Headstock
Index locking knob
Lock platform guide bar in place
Hold handles - move along guide to
end of spindle at the stop collar
Slide the Platform Guide bar into the “T” slots in the Platform Base (Fig 1a). Position the Guide Bar at the final clean-up line.
Lock the Guide Bar in place using the “T” handled alan wrench (Fig 7).
Position the Transport Base at the left side of the spindle, set the left stop collar (Fig 7). Set the stop collar (Fig 1b) on the
right side in a similar fashion. Turn on your lathe and router. Holding the Guide Handles, slowly slide the Transport Assembly
forward into the spindle until the transport base hits the guide bar. Slide the Transport to the right, (Fig 8) pressing the base
of the Transport along the Guide Bar. Do not press the Transport Base too hard against the Guide Bar. Continue until you’ve
routed the entire length of the spindle. The result should be a perfectly rounded spindle (either straight or tapered.) Sand the
spindle to a smooth finish.

7
Cutting Flutes
Determine the number of flutes you want for your spindle. Depending on the number of flutes, you will dial the index
number on your lathe (or indexing accessory) and lock your headstock in place prior to cutting a flute.
Insert a “V” groove or Round Nose bit into your router depending on the profile you want on your fluted spindle.
Position the point of the bit at the beginning of your flute on the left side of your spindle (Fig 9). Mark the front of the
transport base onto the Platform. Mount and lock the stop collar to limit the left hand distance of the Transport. Do the
same on the right side - mark the front of the transport and set the right hand Stop Collar. Draw a reference line between
the marks on the left and right side
Determine the depth of your flute (Fig 9). Advance the Guide bar to that distance in front of the reference line. Lock the
Guide Bar in place securely. Don’t make the cut too deep (1/16” max). If too shallow, you can always cut a deeper flute over
a shallow flute but you can’t make a deeper flute shallow.
Make sure your lathe spindle is locked in place, and everything else is secure. For your safety Unplug your Lathe.
align bits to center points
FIGURE 10 - Set up for ute cuts
Platform guide bar
Trim cutter router bit
Figure 9 - Set up for cutting utes
Headstock
Index locking knob
Tailstock
Mark spindle at the beginning
and end for flute cuts
re-position stop collar
Change bit Position guide to cut flutes
depth of cut
Repeat on right side of spindle
Flute reference line

8
© 2010 PSI Woodworking Philadelphia PA 19115 - v06/10
align bits to center points
FIGURE 11 - cut utes
Figure 10 - Cut utes
Index locking knob Rotate spindle to next position for successive cuts Tailstock
Cut line
Move the Router Transport to the far left against the left hand Stop Collar (Fig 10). Keep
the router backed off of the spindle. Turn on the router. Carefully push the Transport
forward along the left hand Stop Collar and press the router into the spindle at the left.
Once you’ve hit the Guide Bar, slide the Transport to the right (Fig 10) while pressing
forward against the Guide Bar. Do not press too hard. Slide to the Right until the base hits
the Right Stop Collar.
Turn off the router. Unlock the Index Stop pin and advance and index your Lathe or
indexing accessory to the next indexing stop. Continue to index and Flute with your router
until you’ve fluted around the entire spindle.
When done, hand sand your turning as needed.
Table of contents
Other PSI Woodworking Lathe manuals
Popular Lathe manuals by other brands
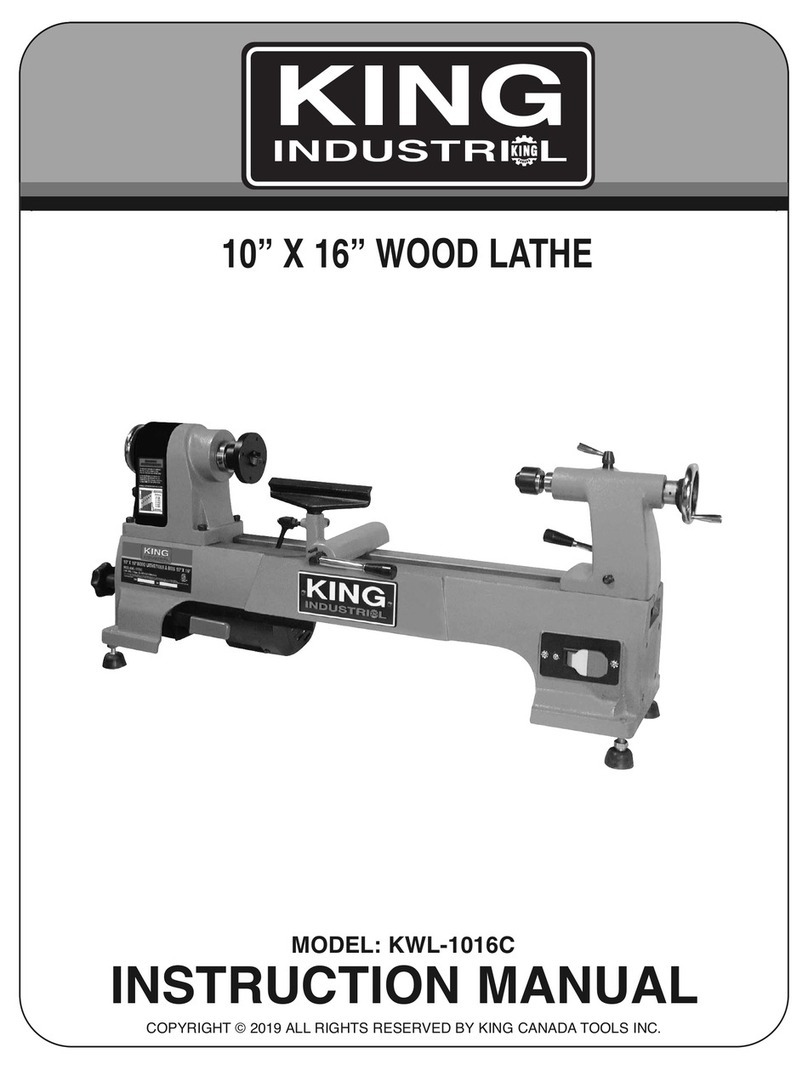
King Industrial
King Industrial KWL-1016C instruction manual

Grizzly
Grizzly G0492 owner's manual
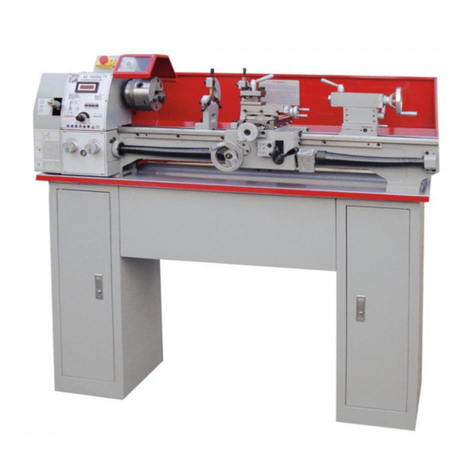
Holzmann
Holzmann ED 750FDQ user manual
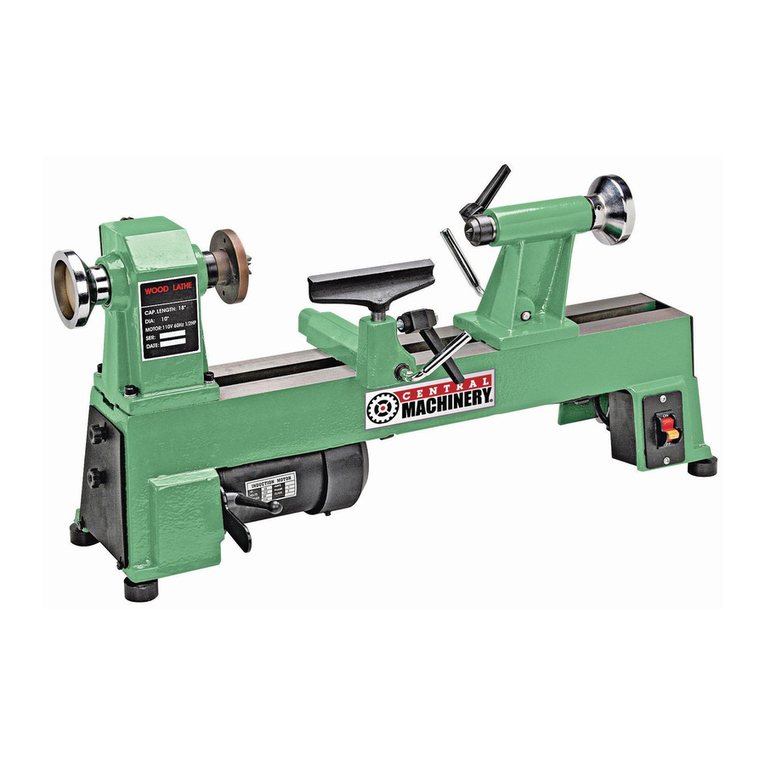
Central Machinery
Central Machinery CENTRAL MACHINERY 65345 Set up and operating instructions
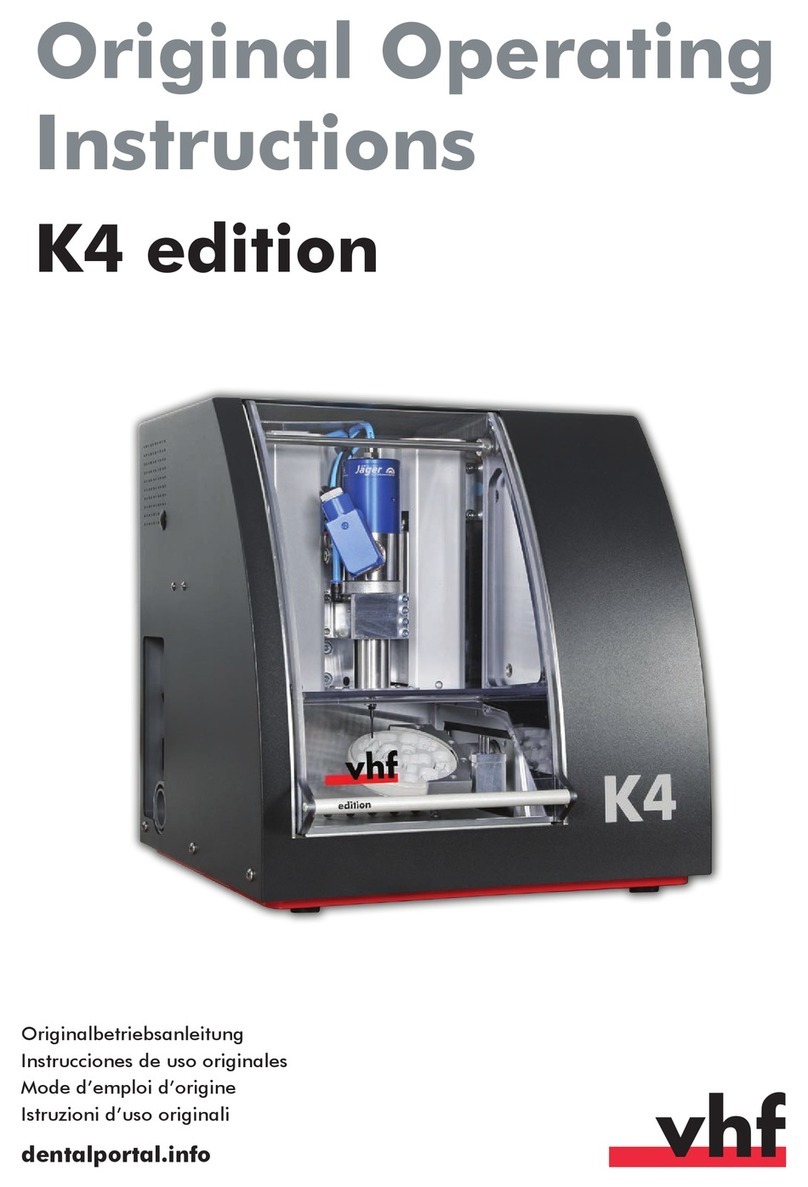
VHF
VHF K4 edition Original operating instructions
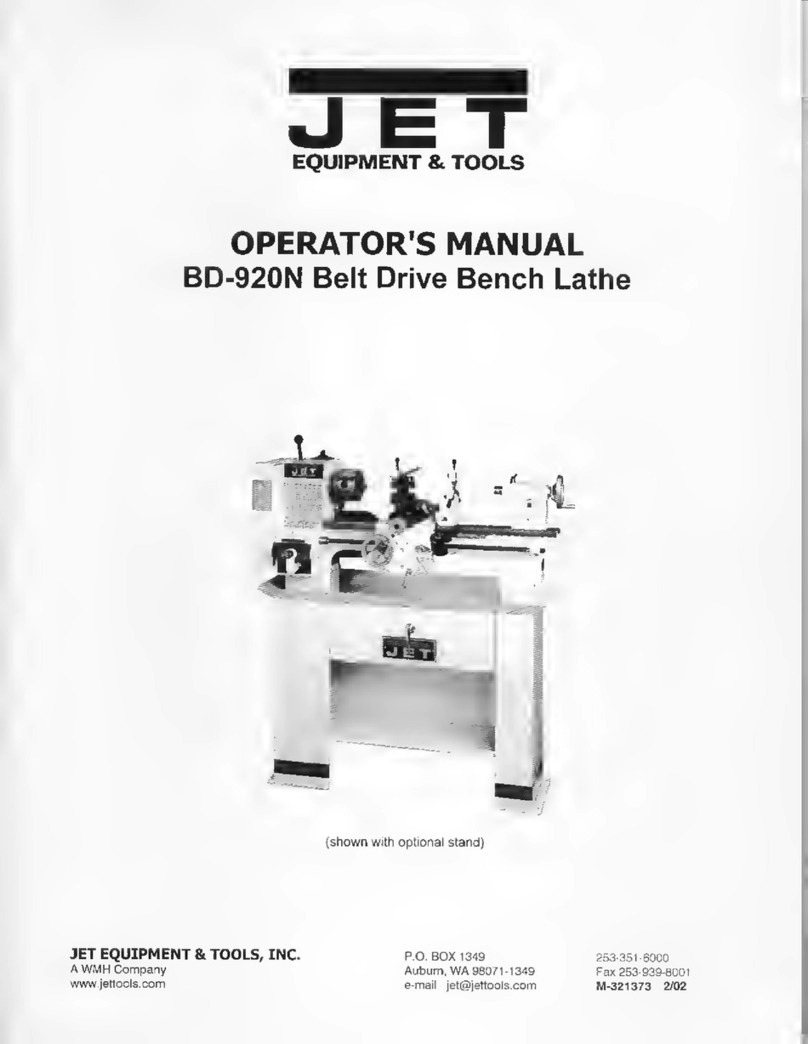
Jet
Jet BD-920N Operator's manual