Purelogic THC1-M Setup guide

CONNECTION AND SETUP
MANUAL
CONTENTS:
01. Introduction
02. Set of Delivery
03. Product Features and Specifications
04. Differences between LV and HV inputs
of THC1-DV1 module
05. Operating principle
06. Outputs, display and connection purpose
07. FAQ
08. Warranty
------------------------------------------------------------------
--------------------------------------------------------------
--------------------------------
-----------------------------------------------------
--------------------------------------------------------
---------------------------
------------------------------------------------------------------------------
----------------------------------------------------------------------
2
2
3
6
6
7
12
13
THC1
THC1
TORCH HEIGHT CONTROLLER

2THC1
Check for more information
01
Introduction11
The THC1 set is designed for cutting height automatic control of CNC plasma cutting devices.
The set consists of two devices: control module THC1-M and voltage divider module THC1-DV1.
The both devices are powered by mains voltage ~220 V. It allows to install the divider module
sources. The THC1-M measurement module is installed in the system CNC control cabinet.
The modules are connected using «twisted pair’ cable with 8P8C connectors.
THC1 set has been fully tested with plasma sources manufactured by Hypertherm company,
which are well-proven as reliable and high-quality equipment. Most of Hypertherm plasma
sources are equipped with special connectors for the THC units connection.
Make sure the following pre-requisites are met for correct operation of the other manufacturers
plasma cutters:
1. it allows to connect devices for automatic cutting height control;
2. the cutter electrical output parameters match the THC unit parameters. If the plasma
cutter manual does not provide the possibility of the THC unit connection, or plasma cutter
parameters do not meet the specified ones, the user is generally responsible for safe connection
and system operability.
• THC1-M controller – 1 pc.
• THC1-DV1 divider module – 1 pc.
• Ethernet cable – 1 pc.
Set of Delivery2202

3
PRODUCT FEATURES AND SPECIFICATIONS
Edition of 09.12.2020
Attention:
All connections are only to be provided in deenergised state!
03
Product Features and
Specifications
33
THC1-M module supply voltage 230 VAC
Useful current of THC1-M module up to 13 mA
THC1-DV1 module supply voltage 230 VAC
Useful current of THC1-DV1 module up to 3 mA
Measured voltage of plasma cutter arc
(HV input) 0-200 V voltage measurement range;
Measured voltage of plasma cutter arc
(LV input) 0-8 V voltage measurement range;
Control interface Ethernet
Control program PUMOTIX, MACH3/4 or other control program
with UP/DOWN protocol support
Insulation resistance 500 MOhm
Weight 2 kg

5
PRODUCT FEATURES AND SPECIFICATIONS
Edition of 09.12.2020
Fig. 2. Dimensions of the THC1-M module
03
4 grooves
4 grooves

6THC1
Check for more information
05
04
The design of the automatic torch height control system using THC1 set differs from other
similar systems. In addition to standard «Torch UP” and «Torch Down» signals, the THC1
transmits the effective arc voltage signal over Ethernet. The PLCM series CNC controller
received this information, adjusts the torch height and then sends the current adjustment
oscillations, as the PLCM knows not only the required adjustment direction, but also the
«classical» control carried out using «Torch UP» and «Torch Down» signals without PLCM
addition to the main measurement function the THC1 set controls torch firing process and
transmits the current ARC OK signal status to the PLCM. The torch firing process is monitored
by the classical ARC OK signal and the current transformer. The ARC OK input is galvanically
isolated from optocoupler. The plasma source switches it by means of a relay. The CT (current
transformer) input is used if the plasma source is not equipped with a torch firing process
power supply phase conductor is connected to this input (see the connection diagram).
Almost all currently known plasma systems provide an interface for connecting a sensor for
measuring current arc voltage. Some of them provide with a low voltage signal with a division
ratio.
Such a method of connection to the plasma system is preferable, as the output voltage is
safe for human and imposes lower requirements to insulation, which allows arranging a more
convenient connection of THC sensor (LV input). If the integrated plasma system voltage divider
is unavailable, then THC sensor can be connected directly to special terminals inside plasma
system (HV input).
operation manual. The choice of a connection input depends on a plasma system in use. The
measurement circuit inside the divider module THC1-DV1 is switched using Control switch
(see part 6. Outputs, display and connection purpose).
Operating principle55
Differences between LV and HV
inputs of THC1-DV1 module44

7
OUTPUTS, DISPLAY AND CONNECTION PURPOSE
Edition of 09.12.2020
05
The following additional parameters shall be set to the PLCM controller for controlling the
plasma cutter height:
• the desired arc voltage (to be selected based on the plasma installation manual). This value
be measured and assumed as the desired value. This value will be maintained during cutting.
• if the «ARC OK» signal is used, then after the plasma cutter activation command the PLCM
will not move the torch until a confirmation of «ARC OK» actuation is received from the THC1.
This function can be disabled, then movement will begin irrespective of «ARC OK» signal
was set with some overlapping, and the machine needs to cover some more distance before
• «control delay» sets the time in seconds for which control will be suspended after the torch
activation. During metal piercing arc voltage is almost always much above the standard value,
and if control is not blocked this time, the torch will begin moving down trying to normalize
voltage. The delay depends on metal thickness and can amount 0 to 5–10 seconds.
• “overvoltage» (previously referred to as «permissible voltage tolerance») sets the
a greater value, then control is suspended until voltage returns to specified range. This is due
to the fact that the arc voltage depends on cutting rate also. See the plasma installation manual
for recommended voltage values for a particular torch speed. The CNC system decelerates
the torch in curves, which results in the arc voltage growth and, consequently, in the torch
lowering.
Besides, when the torch passes over the already cut section, the arc voltage rises abruptly
to idling voltage. This parameter has been introduced so that the system would not react to
the desired voltage.
220 VAC – connection to ~220 V AC mains;
HV – high voltage input (30...200 V);
LV – low voltage input (0...8 V);
ARC OK – input of ARC OK signal;
ETHERNET – connection to a router or PC network card;
DATA CABLE – connection to THC1-M module;
POWER – (green) indicator of applied supply voltage;
THC1-DV1 module:
06
Outputs, display and connection
purpose
66

8THC1
Check for more information
06
ARC OK – (yellow) returns ARC OK input status. It is ON, if ARC OK contacts are closed and
it is off, if they are opened;
TORCH FIRE (red) – it returns TORCH FIRE output status. It is ON, if the contacts are closed
and it is OFF, if they are opened.
220 VAC – connection to ~220 V AC mains;
ETHERNET – connection to a router or PC network card;
DATA CABLE – connection to THC1-DV1 module;
POWER – (green) indicator of applied supply voltage;
ARC OK (green) – the indicator of «ARC OK» signal (it is disabled in CT mode);
TORCH FIRE (green) –the TORCH FIRE output status. It is on, if the contacts are closed and
it is off, if they are opened;
ERROR – (red) is lit in case of an error;
LINK – (green) signal of data transmission over Ethernet network;
CONNECT – (green) signal of communication with CNC software;
UP – (yellow) up adjustment signal;
DOWN – (yellow) down adjustment signal.
THC1-M module:
Fig. 3. Interconnecting cable diagram
Fig. 4. Connection of modules to a plasma source equipped with a voltage divider
THC1 . Set of modules
Position of DIP
switches of ТНС-
DV1 module
To network switch or PC
Twisted pair
(connector
8Р8С)
NC control console
Plasma source
Ignition
Torch ("-")
Product ("+")
VDivider output
21:1
Arc transfer
Control board

9
OUTPUTS, DISPLAY AND CONNECTION PURPOSE
Edition of 09.12.2020
06
Fig. 5. Connection of modules to a plasma source without a voltage divider
Fig. 6. Connection of modules to a plasma source without a voltage divider and Arc ok output
Position of DIP
switches of ТНС1-DV1
module
To network switch or PC
Twisted pair
(connector
8Р8С)
NC control console
Plasma source
Arc voltage
Arc transfer
Arc transfer
Control board
Torch ("-")
Product ("+")
Position of DIP
switches ofТНС1-DV1
module
To network switch or PC
Twisted pair
(connector
8Р8С)
NC control console
Measuring
current
transformer
Plasma source
Ignition
Control board
Torch ("-")
Product ("+")

11
OUTPUTS, DISPLAY AND CONNECTION PURPOSE
Edition of 09.12.2020
06
Fig. 8. Diagram of connection to the plasma system PURM-180 MA
TORCH FIRE Power
supply
source
Control unit
Oscillator
CATHODE
NOZZLE
Item to be cut
Plasma torch
Overheating
length of high-voltage wires and allows the module energizing from the line to which the
plasma source is connected.
The THC1-M module is installed in a CNC cabinet and connected to PC via a network switch
(in case the PLCM controller is used) or directly to the PC network card (if the PLCM is
unavailable). The data transmission line (DATA CABLE) has no galvanic coupling between
modules which allows avoiding any interference induction by plasma source to the CNC control
cabinet. When a PLCM motion controller is absent in the system (PC control movement using
LPT port), it is necessary to send signals to vacant inputs, since these inputs are galvanically
and current-limiting resistors.
For a device to be found, IP address of your PC and THC1 address must be located in the same
subnetwork. By default, THC1’s address is 192.168.10.12, which means that the PC’s address
address. If the device does not appear in the list, see FAQ section.
It should be noted that for the THC module to be successfully found, the device shall be
connected to the same network card as the PLCM controller, i.e. if two network cards are
installed in the computer, and the PLCM controller is connected to one of them, and the THC1
shall only be connected to PC via a network switch. The setup procedure of a network card
for the PLCM controller operation is detailed in the movement controller manual. If THC1 is
used without a PLCM movement controller, and height is monitored by means of UP and DOWN
if there is a DHCP server or router in the network. That is to say, if PLCM and THC modules are
connected to PV through a router, then IP addresses are assigned to the devices automatically.

12 THC1
Check for more information
06
In case of connection through an ordinary network switch the controller will receive an
unknown IP and will be «lost» in the network – the selection field will remain empty when
“Refresh” button is pressed. The way out is using the «Default address» button. The button
restores factory network settings to all THC devices in the network. If it is required to assign
address» position of the switch.
controller’s address), subnet mask 255.255.255.0. The field «Default gateway» may be left
blank. After pressing the button «Set address» the controller will store the changed settings.
Then press Refresh button. The module to be connected to the network will be determined in
the device selection field.
In PUMOTIX CNC system the IP address changing is done in the THC controller selection
menu.
1. The «Link» LED does not blink when Ethernet cable is connected to THC1.
Possible causes: a damaged cable, a malfunctioning network switch, a malfunctioning
network card, connection options can not be determined automatically.
via Ethernet.
Solution: check cables, connections, operability of the equipment and its settings using
network card settings.
2. When Ethernet cable is connected to THC1-M the «Link» LED blinks, but the 192.168.10.12
address device is not pinged.
Possible causes:
1) The controller’s IP address is not the default setting.
2) The computer’s IP address is not set up correctly.
computer’s IP shall be located in the same subnetwork for successful connection.
Solution:
1) Reset the device settings to default settings (see the instruction below).
SW archive (see the installation instruction).
07
FAQ77

13
WARRANTY
Edition of 09.12.2020
07
3. The Ethernet PLCM is pinged, but is not available from the configuration window.
Possible causes: a firewall or some other program blocks traffic between a PLCM controller
and a computer.
network queries.
Solution: find and disable the program blocking the traffic.
4. How to create your own screen set in Mach3.
If you wish to create your own screen for operation with THC1, the necessary controls are
listed below: DRO #1332 – required arc voltage, V DRO #1333 – current (measured) voltage, V
#1326 – attribute of ARC OK signal use.
Warranty service life is 12 months from the purchase date.
The warranty is only preserved if operation and scheduled maintenance conditions are
observed.
1. General provisions
1.1. If the goods is purchased as component parts, Seller shall guarantee operability of
each component part individually, but is not responsible for the quality of their joint operation
(incorrect selection of component parts. In case of any questions you can consult the company’s
specialists).
1.2. Seller does not provide any warranty for compatibility of the purchased goods and the
goods possessed by Buyer, or purchased by them from any third parties.
1.3. Specifications and configuration of the product can be changed by manufacturer without
prior notice due to continuous technical improvement of the products.
2. Conditions for access to warranty service
2.1. The goods is accepted for warranty service in the same configuration in which it was
purchased.
3. Warranty service procedure
3.1. The warranty service is carried out by testing (checking for) the declared malfunction
of the product.
3.2. The warranty service is carried out if the malfunction is confirmed.
4.The warranty does not cover glass, electric lamps, starters and consumable materials, and:
4.1. any goods damaged due to improper transportation and storage conditions, incorrect
connection, off-design operation, or in conditions not stipulated by the manufacturer (including
circumstances (power supply voltage surges, natural disasters, etc.), and mechanically or
thermally damaged goods.
08
Warranty88

14 THC1
Check for more information
08
4.2. Goods with traces of effect and (or) ingress of foreign objects, substances (including
4.3. Goods with traces of unauthorized tampering and (or) repair (tampering signs, primitive
soldering, traces of component replacement, etc.).
4.4. The goods having self-diagnostic means indicating improper operation conditions.
4.5. Highly technical Goods in respect of which installation and assembly works were carried
directly stipulated in the goods documentation.
4.6. The Goods operated in conditions where power supply did not comply with manufacturer’s
requirements, and if the electrical network and equipment protection devices are unavailable.
4.7. The Goods which was re-sold by the initial buyer to third-party persons.
4.8. The Goods damaged due to use of low-quality or outdated spare parts, consumable
materials, accessories and if spare parts, consumable materials and accessories not
recommended by the manufacturer were used.
It was manufactured and accepted in accordance with mandatory requirements of the
applicable technical documentation and deemed ready for operations.
Batch No.: QCD:
We draw your attention to the fact that there can be some changes in this instruction due to the product
consistent technical improvement. You can always download our latest versions at
Contacts
Moscow +7 (495) 505-63-74
Voronezh +7 (473) 204-51-56
160, Leninsky avenue, Voronezh, Russia, 394033, 149 Office
Monday - Thursday: 8:00–17:00
Friday: 8:00–16:00
This manual suits for next models
1
Table of contents
Other Purelogic Control System manuals
Popular Control System manuals by other brands
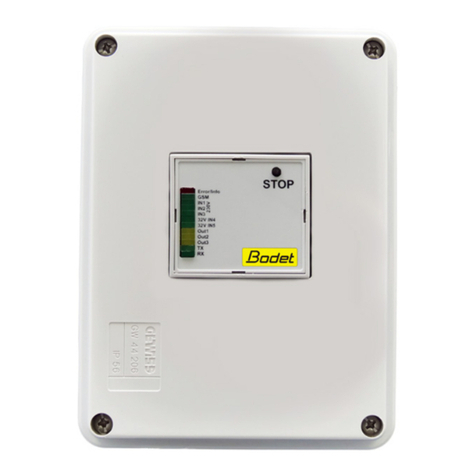
Bodet
Bodet GSM CONTROL Installation and user manual
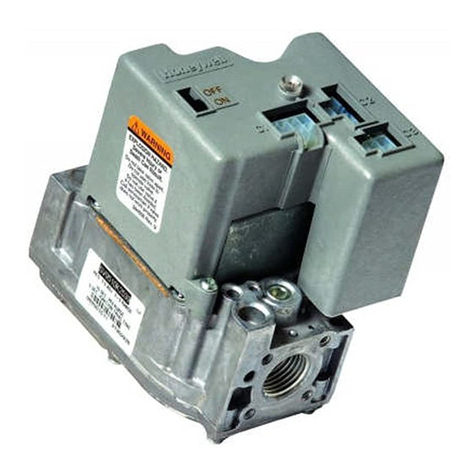
Honeywell
Honeywell SmartValve SV9540 installation instructions
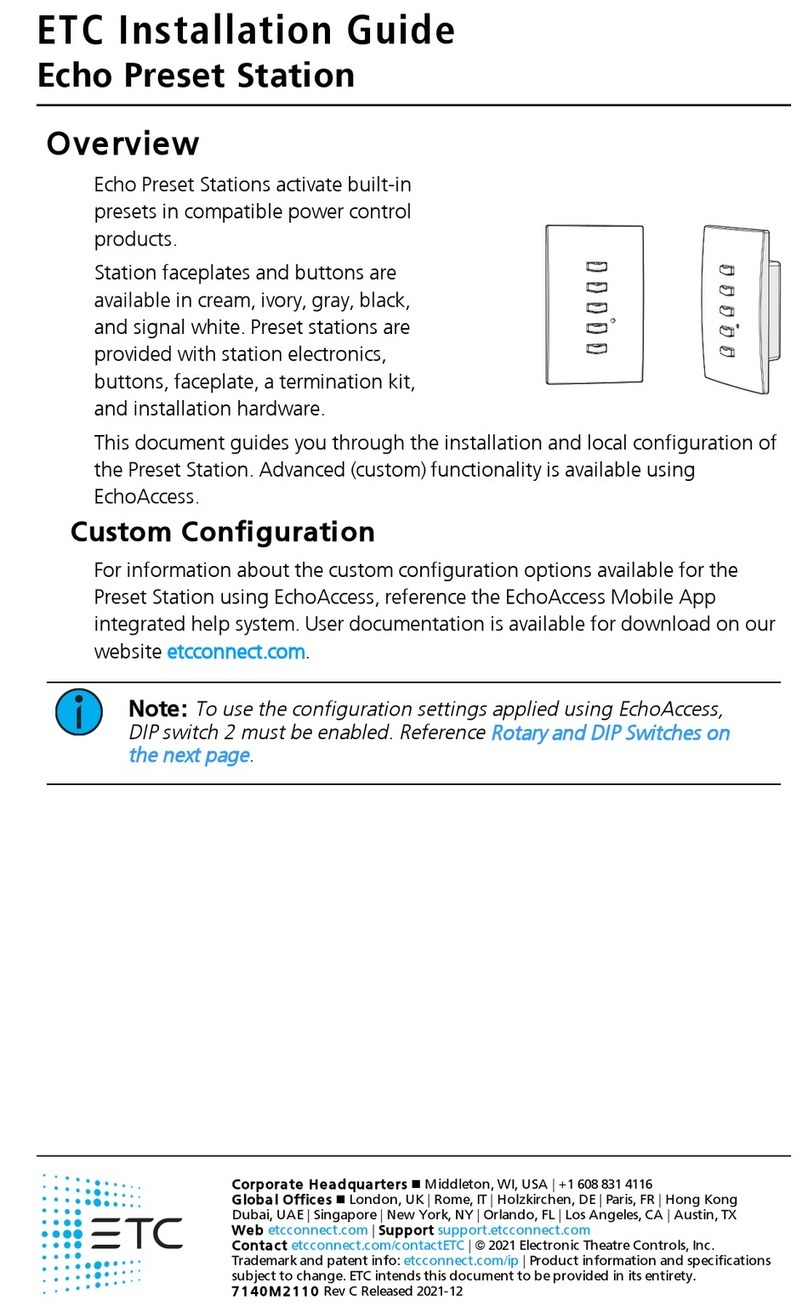
ETC
ETC Echo installation guide
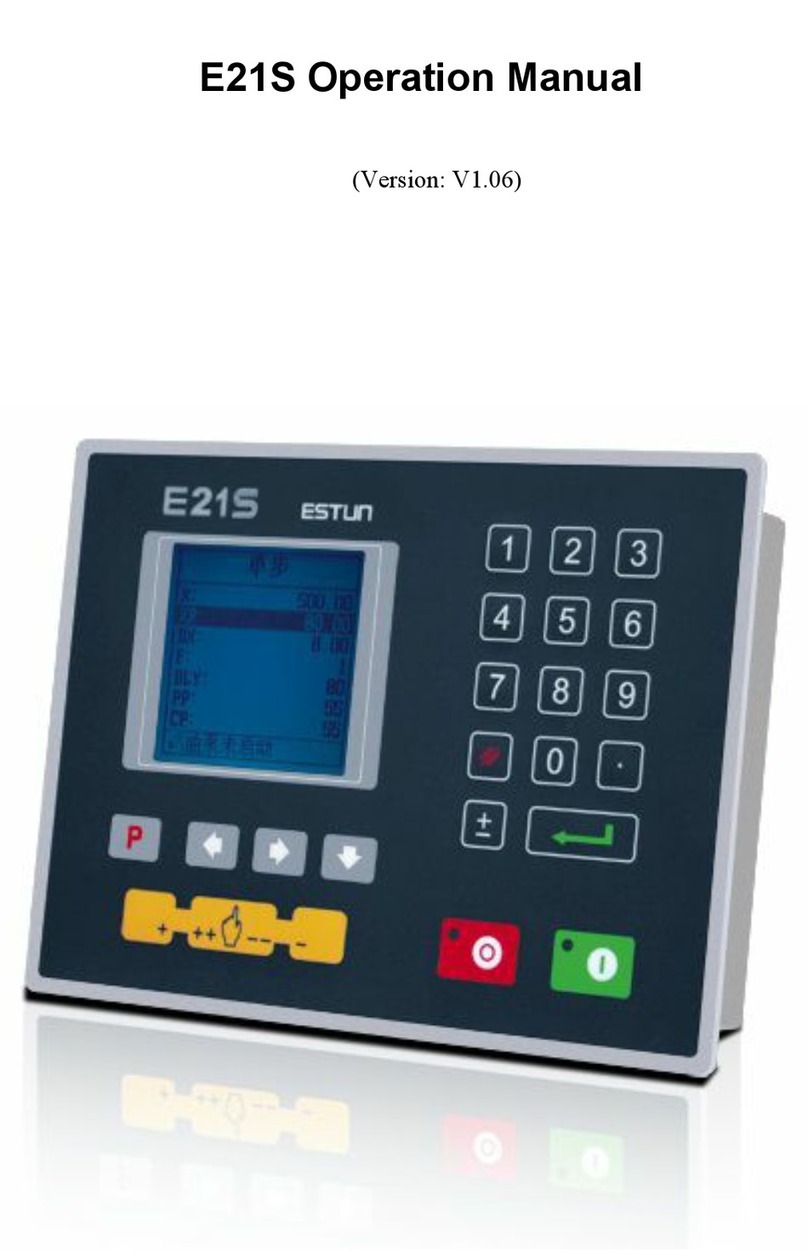
Estun
Estun E21S Operation manual

flamco
flamco WMS 2-1 Installation and operating instructions
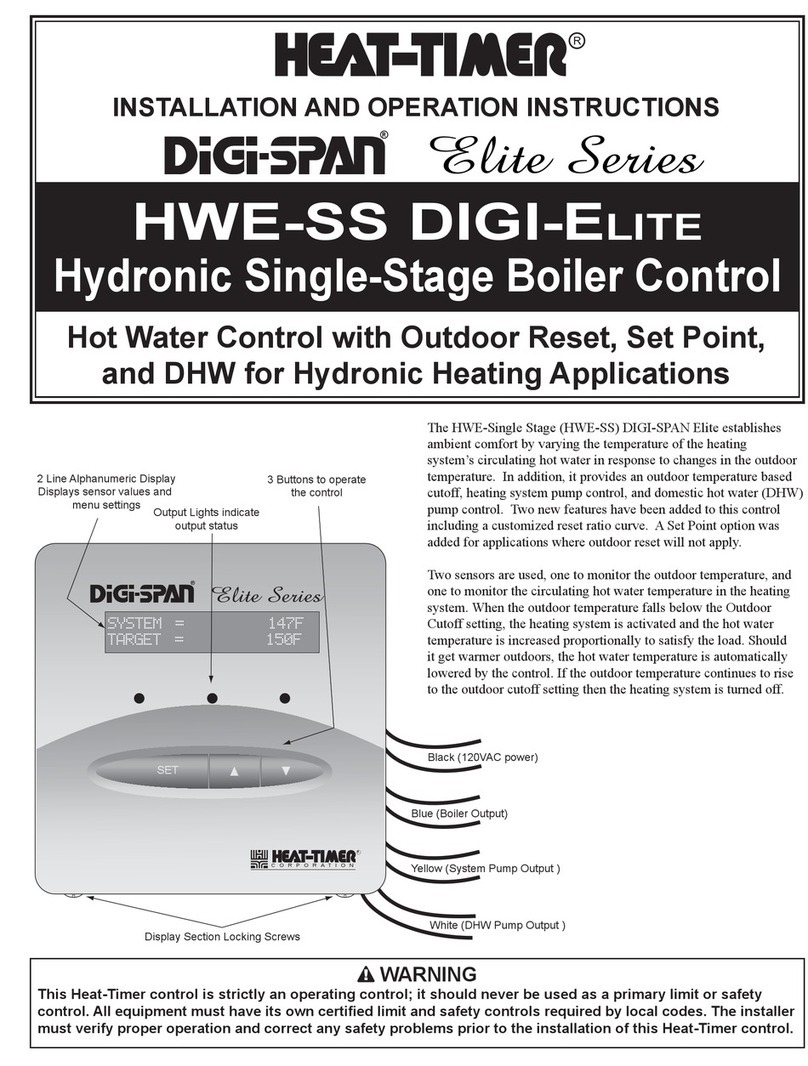
heat-timer
heat-timer Digi-Span Elite Series HWE-SS Installation and operation instructions