Qimarox PRORUNNER mk9 User manual

User Manual
PRORUNNER mk9
Version 2.0 / 03-02-2016

2UM-PRORUNNER_mk9-2.0-EN
/i
Qimarox
Nobelstraat 43
3846 CE Harderwijk
The Netherlands
Tel: +31 341 436 700
Fax: +31 341 436 701
E-mail: info@Qimarox.com
Internet: www.Qimarox.com
Copyright © Qimarox B.V.
All rights reserved. No part of this publication may be reproduced, stored in a computer database or published in any
form or in any way electronically, mechanically, by means of photocopying, recordings or in any manner without prior
written permission from Qimarox.

3
Table of contents
1 About this manual
1.1 Introduction............................................................................................................................. 5
1.2 Product documentation........................................................................................................... 5
1.3 Source language .................................................................................................................... 5
1.4 Symbols used in the manual ..................................................................................................6
1.5 Terminology list ...................................................................................................................... 6
1.6 Further support and information .............................................................................................6
2 General
2.1 Machine identification ............................................................................................................. 7
2.2 Machine layout drawing and specifications ............................................................................ 9
2.3 Warranty ................................................................................................................................. 9
2.4 Liability.................................................................................................................................. 10
2.5 CE Declaration of Conformity ............................................................................................... 10
3Safety
3.1 Intended use of the machine ................................................................................................ 11
3.2 User types and qualifications................................................................................................ 11
3.3 Safety instructions ................................................................................................................ 11
3.4 Safety equipment.................................................................................................................. 12
3.5 Potential risks ....................................................................................................................... 14
3.6 Machine end of life and environment disposal ..................................................................... 15
4 Description
4.1 Working principle .................................................................................................................. 17
4.2 Sensors ................................................................................................................................ 19
4.3 Motor .................................................................................................................................... 20
4.4 Control .................................................................................................................................. 21
4.5 Machine in a system............................................................................................................. 21
4.6 Specifications ....................................................................................................................... 22
4.7 Application information ......................................................................................................... 23
5 Installation
5.1 Location ................................................................................................................................ 24
5.2 Delivery................................................................................................................................. 25
5.3 Transport .............................................................................................................................. 26
5.4 Unpacking............................................................................................................................. 26
5.5 Preparations for a Qimarox installation (optional) ................................................................ 27
5.6 Installing the machine........................................................................................................... 27
5.7 Installing the moveable conveyor ......................................................................................... 32

4
6 Maintenance
6.1 Specific safety regulations.................................................................................................... 34
6.2 Preventive maintenance schedule........................................................................................ 35
6.3 Cleaning ............................................................................................................................... 37
7 Troubleshooting
7.1 Vertical conveyor .................................................................................................................. 38
8 Exploded views
8.1 Frame parts .......................................................................................................................... 41
9 Electrical circuit diagrams
9.1 Drives ................................................................................................................................... 55
9.2 Installing 87Hz ...................................................................................................................... 55
10 Pneumatic circuit diagrams
10.1 Mechanical locking device.................................................................................................... 57
11 Appendix
11.1 Product registration form ...................................................................................................... 58

UM-PRORUNNER_mk9-2.0-EN 5
About this manual
1 About this manual
1.1 Introduction
This manual provides information about the PRORUNNER mk9 machine, which is used
for the vertical movement of products within a transport system. From here in the manual,
the PRORUNNER mk9 will be referred to as the “machine”.
This manual is intended for:
•Retailers/Original Equipment Manufacturers (OEM) project engineers and mechanics.
•Operator, installation and maintenance engineers and other users.
It is important to carefully read this manual as soon as possible after purchase of the
machine.
Before you operate the machine, this manual should be read by all users. This is
necessary to make sure that all new users are familiar with the content of this manual.
System integrators/OEMs
This manual explains machine configurations you can use to setup the machine. It also
provides instructions on how to add or change the machine technical components.
Users
The machine may be supplied pre-assembled, if so, some chapters in this manual will not
be applicable. To integrate the machine within a transport system, Qimarox advises you to
refer to documentation provided by the OEM of the transport system.
1.2 Product documentation
/i
1.3 Source language
This manual was originally written in the English language.
Document Reference
Machine manuals1
1 Generic information for each machine, apart from exceptions outlined in the machine lay-
out drawing.
UM-PRORUNNER_mk9-2.0-EN
Machine layout drawing2
2 Machine specific information.
Refer to section 2.2.
Electrical diagrams1
Specification sheet2
OEM parts of the machine:
•Bolts and nuts
•Motor reductor
•Photocells
•Runners
•Chain
•Induction switches
•Limit switches
•Belts

About this manual
6UM-PRORUNNER_mk9-2.0-EN
1.4 Symbols used in the manual
The following symbols are used in this manual.
1.5 Terminology list
The table below explains common terms used by Qimarox for the machine.
1.6 Further support and information
Qimarox can supply additional expertise and support services, for:
•Training
•Global support
•Service contracts
For more information please contact Qimarox.
WARNING
Risk of serious injury to the user or damage to the machine if the instructions
are not accurately followed.
Note
To provide additional information to the user about a task or issue.
Term Definition
machine The PRORUNNER mk9.
product Products transported by the machine.
carrier The component on which a conveyor can be mounted or which carries the
product.
feeding conveyor The conveyor that delivers products to the machine. The feeding conveyor
is not part of the machine.
discharge conveyor The conveyor that discharges products from the machine. The discharge
conveyor is not part of the machine.
fenced area Area around the machine that unauthorised personnel cannot enter for
safety reasons.

UM-PRORUNNER_mk9-2.0-EN 7
General
2 General
2.1 Machine identification
The machine identification is given on the type plate. The type plate is located on the side
of the column.
The machine type on the identification plate has a code consisting of 7 parts (A - G). This
indicates in detail which machine configuration is involved.
A type of drive
B type of column
C type of product conveyor moveable
D type of drive for product conveyor moveable
E type of product conveyor fixed position
F type of drive for product conveyor fixed position
G type of E-components
Column type:
/i
Carrier type:
/i
Fixed position type:
/i
/i
•KS Standard column
•DB Carrier with conveyor
•DZ Carrier without conveyor
•UV Fixed outfeed conveyor
Made in Holland. Designed by
Manufacturing year :
T
ype :
Serial number : Mk9
Or
der number :
Power supply :
Power (kW) PRORUNNER Mk9 :
Power (kW) conveyors :
Weight PRORUNNER Mk9 (kg) :
Weight conveyors (kg) :
Total weight (kg) :
Max. pallet weight (kg) :
Nominal capacity (p/hour) :
www.Qimarox.com
mk9-03 B/M00-01 / M05-03/E0
DCBA GFE

General
8UM-PRORUNNER_mk9-2.0-EN
Code
part
Remark Possible
value
Meaning of the value Type Refer to
chapter
A Drive type 00 None / not supplied 11
05 3 Phase ~ + BR + TF 9.1
11 3 Phase ~ + BR + TF + encoder 9.1
99 Other
B Column type S Column without sensors, no encoder on carrier B
B Column with sensors, no encoder on carrier
E Column with sensors and encoder on carrier
C Conveyor in eleva-
tor type
000 None / not supplied 000
F01 Fork
M01 Roller conveyor
M02 Roller chain conveyor
999 Special version
D Conveyor in eleva-
tor drive
00 None / not supplied 00
03 3 Phase ~ 9.1
05 3 Phase ~ + TF 9.1
06 3 Phase ~ + BR 9.1
07 3 Phase ~ + BR + TF 9.1
99 Special version
E Fixed conveyor type 000 None / not supplied 000
M01 Roller conveyor
M02 Roller chain conveyor
999 Special version
F Fixed conveyor
drive
00 None / not supplied
03 3 Phase ~ 9.1
05 3 Phase ~ + TF 9.1
06 3 Phase ~ + BR 9.1
07 3 Phase ~ + BR + TF 9.1
99 Special version
G E-component out-
feed type
E0 None / not supplied
E1 24 VDC IP66
E2 24 VDC IP67
99 Other

UM-PRORUNNER_mk9-2.0-EN 9
General
2.2 Machine layout drawing and specifications
After a machine order is placed, you will receive a machine drawing and specifications
sheet for approval. After your approval you will receive an approved drawing and
specification sheet which is used as a reference for this manual.
/i
This drawing and specifications sheet includes:
•Machine serial number
•Product dimensions and mass
•Machine dimensions and mass
•Machine configuration
•Machine speed and capacity
•Motor specifications
The machine can only be used according to the specifications given in this manual and the
machine layout drawing specifications. If you want to use the machine outside the
recommended specifications, you must contact Qimarox to check if this is possible.
Inappropriate and/or modified use of the machine can result in dangerous safety issues
and/or damage. You must obtain written confirmation from Qimarox before using the
machine in a modified or unspecified manner. Qimarox cannot be held liable for any
accidents and/or damages that may occur through inappropriate unauthorised use of the
machine.
2.3 Warranty
The scope and duration of the warranty is agreed when an order is placed for the machine.
The warranty only applies if the machine is used according to the specifications and if the
user and maintenance instructions are observed.
The warranty does not cover wear of the parts.
The machine warranty is null and void in cases of:
•Unskilled use.
•Inadequate maintenance.
•Unskilled maintenance.
•Modifications made to the machine without prior written permission from Qimarox.
AA
Surface roughness (Ra):
Unless indicat ed otherwise
Roughness indications according to
EN-ISO-1302 / NPR 3634
Weld symbols according to NEN-EN- ISO 2553
Tolerancing of form and location according to
NEN-EN-ISO1101
Scale:
Sheet size:
1 / 1
Third
angle
Date:
11-11-2015Drawn:
Appr:
Author:
BE
Item:
Example PRmk9
Tolerances
unlessindicated
otherwise.
Angle: ±1°
0 - 20 - 200 - 2000
Machi nin g
±0.2 - ±0.5 - ±1.0
Sheet and weld constructions
±0.5 - ±1.0 - ±2.0
Size fillet weld
unlessindicated
otherwise.
2 - 3 - 4 - 5- 6
| | | | |
1 - 2 - 4 - 6- 8 - 10
Sheet thickness [mm]
a =
Weight:
imarox
Revisi on: Document :
Proje ctnum ber: Cus tomer :
Met transportbaan Handleiding
1858,0 kg
1 : 50
-AE0009075.dwg
A3
Sheet number:
-
Doc. rev:
For Review
With convey or Manual
Voorbeeld PRmk9
footprint on floor level
2010
1608
5284
172517501725
80 25
2600
Cable carrierheight
500
4500
1608
2223
500 for maintenance
v3.3 2/7
Additional in/out
3060 mm mm
1N/A
600 mm mm
AN/A
0,2 m/s default 0,2 m/s
Roller
0,2 m/s Standard by Qimarox 0,2m/s
1450 mm Standard by Qimarox 1450mm
100 mm Standard by Qimarox 100mm
190 kg
N/A
PRORUNNER mk9
Height
Position
Additional in/out
Position
Top level
Height
Position
Bottom level
Height
Height
Position
mk9 15XXXXX rev -
FEEDING CONVEYOR
Speed
Weight
Product stop
Centering unit
CONVEYOR IN PRmk9
Type
Speed
Length
Height
N/A

General
10 UM-PRORUNNER_mk9-2.0-EN
2.4 Liability
Qimarox believes to the best of its knowledge that the information in this user manual is
accurate. In the event that technical or typographical errors exist, Qimarox reserves the
right to make changes to subsequent editions of this user manual without prior notice to
holders of this edition. The reader should consult Qimarox if errors are suspected. In no
event shall Qimarox be liable for any damages arising out of or related to this user manual
or the information contained in it. Except as specified herein, Qimarox makes no
warranties, express or implied, and expressly disclaims any warranty of non-infringement,
merchantability or fitness for a particular purpose. Customer’s right to recover damages
caused by fault or negligence on the part of Qimarox shall be limited to the amount paid to
Qimarox by the customer. Qimarox shall not be liable for damages resulting from loss of
data, profits, use of products, or incidental or consequential damages, even if advised of
the possibility thereof. This limitation of liability of Qimarox will apply regardless of the form
of action, whether in contract or tort, including negligence. Any action against Qimarox
must be brought within one (1) year after that cause of action accrues.
Qimarox is not liable for damages, accidents, unsafe conditions, defects, malfunctions, or
service failures caused by the following:
•Owner’s or user’s failure to follow Qimarox’s installation, operation and maintenance
instructions, including but not limited to neglecting warnings or regulations as shown
on the machine or in this manual.
•Usage of the machine for other applications, or under other circumstances than
indicated in this user manual. This includes abuse, misuse or negligent acts.
•Modifications of any kind to the machine. This includes the replacement of parts with
parts that are not specified in this manual.
•Insufficient or improper maintenance.
2.5 CE Declaration of Conformity
For the CE declaration of conformity, refer to the specification sheet.

UM-PRORUNNER_mk9-2.0-EN 11
Safety
3 Safety
3.1 Intended use of the machine
The machine is exclusively intended for the vertical transportation of products, as
described in this manual. Refer to section 4.6 for a detailed description of the
specifications of use.
The machine is always set up within a larger transport system in which products are
automatically loaded on and off the machine.
3.2 User types and qualifications
The following user types are referred to in this manual:
•The operator.
•The mechanical installer.
•The electrical installer.
•The maintenance engineer.
All users must be familiar with the full content of this manual.
Only qualified personnel is permitted to operate, install or maintain the machine.
A user is only qualified if the user has attended appropriate training and/or attained
appropriate industry standard recognized qualifications. Qimarox can provide training if
required.
Qimarox can also give advice about actions and tasks to be carried out on the machine.
3.3 Safety instructions
3.3.1 General
•Comply with the safety regulations given in this manual. Deviation from these
regulations can lead to unacceptable risks.
•Never close doors (if present) in the fenced area of the machine, when a person is
inside this area.
•Switch off the machine and secure the main power supply switch in the off position
with a padlock to prevent the machine from being switched on while personnel works
within the fenced area.
•Comply with all relevant local legislation and regulations.
WARNING
Any other use of the machine is strictly forbidden.

Safety
12 UM-PRORUNNER_mk9-2.0-EN
3.3.2 Set up
•Connect the machine in accordance with the local laws and regulations concerning
health and safety.
•Before putting the machine into use, check if the machine has been set up in
accordance with the instructions in this manual and with the layout drawing.
•Make sure that the transport system complies with all relevant health and safety
directives and regulations.
3.3.3 Start the machine
•Do not switch the main power supply on when persons are in contact with the
machine.
•Do not start the machine when persons are in contact with the machine.
•Do not start the machine when persons are present in the fenced area of the machine.
•Before the machine is put into operation, all machine parts must comply with all
relevant health and safety directives and regulations.
3.3.4 During machine operation
•Keep your hands and feet away from the fenced area.
•Make sure you do not wear loose clothing and secure long or loose hair.
•Make sure that no persons or objects are within the range of any moving parts of the
machine.
•Make sure that users know and observe all safety rules with regard to the machine
and the environment in which it operates.
3.3.5 Maintenance and repair
•Turn off the power supply to the machine with the main power supply switch before
starting any maintenance or repair tasks. Secure the main power supply switch in the
off position with a padlock.
•Replace damaged or defective parts before putting the machine back into operation.
•Changes and modifications that may affect the safety of the machine can only be
carried out when these changes and modifications comply with the relevant
regulations, legislation, directives and recognized industry standards.
If changes and modifications are outside the scope of specifications given by Qimarox
in this manual and Qimarox has not granted permission changes and modifications,
then the changes and modifications will entirely be the responsibility of those persons
responsible for carrying out the changes and modifications.
•Electrical installation tasks must only be carried out by qualified personnel.
3.4 Safety equipment
•You must not disassemble, bypass or disable any safety equipment on the machine.
•The machine may not be started and must be immediately taken out of operation if
even a single item of machine safety equipment is defective.
•After maintenance tasks are complete, always replace all safety equipment that has
been removed from the machine.
The machine has been equipped with the following safety equipment:
•Safety pressure valve (pneumatic system for mechanical locking device)
•Mechanical locking device
•Panels on the backside of the machine

UM-PRORUNNER_mk9-2.0-EN 13
Safety
A fenced area around the machine is mandatory for personnel safety. Any access doors
must be secured with (interlock) door switches. These switches must be included in the
emergency stop and safety circuit. Refer to section 3.4.1 for information about how to set
up the fenced area.
In case of non-compliance with the required safety measures, the CE Declaration of
Conformity will become null and void.
3.4.1 Safety fence
The fenced area must comply with EN ISO 13857 and EN 619 standards.
The infeed and outfeed openings of the machine must be designed such, that they protect
persons against reaching the danger zone. When this is not possible, these openings
must be equipped with a light curtain.
Make sure that the fenced area complies with local law and rules for protection against
danger. If the fenced area is fitted with a door, it must have a safety switch to shut down
the system when opened. Refer to 3.4.2.
If Qimarox supplies the safety fencing, the specifications will be included in the machine
layout drawing.
3.4.2 Safety controls
The provisions must be designed according to a so-called Performance Level (PL)
corresponding with the current standard for safety functions of a machine or a machine
control in compliance with EN ISO 13849-1:2008. To the machine a PL_d applies, in which
d indicates that the risk must be substantially reduced.
Emergency stop circuit
The machine must have an emergency stop circuit. When one of the emergency stop
buttons is pressed, the main power and the control current of the machine are switched off
immediately.
Set the motor protection relay
Motor protection devices must be set to the nominal motor current. A relay set too low
prevents optimum use of the motor. A relay set too high does not guarantee full thermal
protection.
When a correctly set relay trips too often, reduce the load of the motor or use a larger
motor.
Note
Replace labels on the machine if they become unreadable or damaged.
WARNING
If the machine moves the products through a floor to another level, apply safety
measures to all levels.

Safety
14 UM-PRORUNNER_mk9-2.0-EN
Thermistor protection (TF contact)
For motors that are frequently started and stopped, intermittently operated, use a high
switching frequency or power controller, it is essential to use a motor protection relay and
thermistor protection. This is to avoid prematurely switching the motor protection relay or
overheating of the motor winding in these operational conditions.
Check continuously moving of products
It is necessary to check if the products are continuously moving during transport to the
infeed and outfeed position by means of time monitoring in the software. When the time is
exceeded, the machine must immediately stop to avoid damage.
Mechanical locking device
The machine is equiped with a mechanical locking device which protects the carrier from
falling down if the flat belts break or are being released. The mechanical locking device
must also be released in all other circumstances that personnel safety is at risk. This
device is installed for personnel safety and can not be used as fall protection during
operation. For detailed information about the safety valve that controls the release of the
mechanical locking device, refer to the manual of the supplier.
3.5 Potential risks
The machine is intended to be integrated into a transport system. Qimarox has attempted
to protect against as many hazards as possible. The following potential risks should be
addressed before machine and assembled parts are put into operation:
•Risk of injury caused by falling products.
•Risk of injury as a result of a moving carrier.
•Hazards occurring at places where the machine connects to other parts of the
production line, such as feeding and discharge conveyors.
The interior of the machine can be accessed by removing the back covers or directly from
the front. Additional protection (fencing) is required at the feeding and discharge position.
If the machine is accessible from multiple levels, then protection measures should be
taken to avoid hazards. Please note that additional, local rules or laws may be applicable
and require you to take additional measures.

UM-PRORUNNER_mk9-2.0-EN 15
Safety
3.6 Machine end of life and environment disposal
Proper use and maintenance of the machine will not involve any environmental risks. After
the machine is no longer useable, the machine should be dismantled and disposed of in
an environmentally responsible manner.
WARNING
Observe all relevant legislation, regulations, instructions and precautions with
regard to health and safety when dismantling the machine.
Observe all relevant legislation, regulations, instructions and precautions with
regard to the disposal of products in the environment.

Description
16 UM-PRORUNNER_mk9-2.0-EN
4 Description
AColumn
B Drive section
CCarrier
The machine is designed to vertically transport a product from one to another level.
The machine consists of a column, a moveable carrier and a drive section. The carrier is
suspended by two flat belts which are wound up by a motor located in the drive section.
The carrier is guided by wheels running over guiding profiles in the column. For safety
reasons the machine is equipped with a mechanical lcoking device, preventing any
downward movement of the carrier when the safety circuit is triggered.
A
C
B

UM-PRORUNNER_mk9-2.0-EN 17
Description
4.1 Working principle
4.1.1 Guiding the carrier
A Wheel
B Guiding profiles
C Adjusting bolts
D Wheel
E Adjusting bolts
The wheels of the carrier are running over the
guiding profiles of the column.
The carrier can be leveled:
•To tilt the carrier forward or backwards,
adjust the position of the wheels (A) by
adjusting the bolts (C).
•To tilt the carrier sideways, adjust the
position of the wheels (D) by adjusting the
bolts (E).
4.1.2 Suspension of the carrier
A Adjusting bolts
B Detection block
C Sensor belt on tension
Both hoisting belts must be tensioned equally.
This can be achieved by loosening or
tightening the adjustment bolts.
When one or both detection blocks are not
detected by sensors, an emergency stop must
be triggered. Possible causes are:
•There is something below the carrier,
where the carrier rests on.
•One of the (attachment points of the) flat
belts failed.
•There is an electrical error.
B
E
D
AEB
A
B
A
C
A
C
B

Description
18 UM-PRORUNNER_mk9-2.0-EN
4.1.3 Mechanical locking device
A Pneumatic cylinder
B Extension spring
C Locking pin
D Sensor locking pin retracted
The locking device is actuated using
compressed air. When compressed air is fed to
the cylinders, they extend and rotate the
locking pin to a position where the carrier is
free to move. When the air pressure drops, the
cylinder retracts and the extension spring
rotates the locking pin back to the locked
position.
If personnel safety is at risk or in one of the
situations below, the mechanical locking
device needs to be activated:
•When an emergency stop is triggered, the safety pressure valve must let the air in the
system escape.
•When a power failure occurs, the safety pressure valve allows the air to rapidly
escape.
•When one or both sensors do not detect the locking pin, the pin is either extended or
a malfunction had occured. This must trigger an error. Do not move the carrier
downwards.
- When the pin is extended, the only movement that is allowed is a slow and
manual operated upward movement of the carrier, with a maximum lift of 125
mm, to allow the locking pin to retract.
- In all other cases, do not move the carrier at all.
•Before performing maintenance, always make sure that the locking pins are
extended.
•When the locking pins are extended, the carrier can move a maximum of 125 mm
downwards before the pin is properly locked in the slots in the column.
Refer to section 10.1 for the pneumatic diagram of the locking device.
WARNING
Do not use the machine when the mechanical locking device does not function
properly.
CC
AA
DD
BB

UM-PRORUNNER_mk9-2.0-EN 19
Description
4.2 Sensors
The following sensors are installed on the machine:
/i
When the machine is configured to stop at more than two levels, two sensors (M#, N#) per
extra level are installed in the column.
/i
Sensor
code
Sensor name
B1 Bottom level stop
B2 Bottom level low speed
B3 Top level stop
B4 Top level low speed
S10 Bottom limit switch
S11 Top limit switch
Sensor
code
Sensor name
M# Additional level # upward stop & downward low speed
N# Additional level # downward stop & upward low speed
M
N
S10
B2
B1
S11
B3
B4

Description
20 UM-PRORUNNER_mk9-2.0-EN
The movement of the carrier is restricted by the limit switches S10 and S11. When one of
the limit switches is triggered, the machine must stop and the mechanical locking device
must extend.
At each level two sensors are installed, by default B1 and B2 at bottom level and B3 and
B4 at top level. When the carrier is moving and one of the sensors is activated, the carrier
speed must be reduced to low speed. Once the second sensor is also activated, the
carrier must stop.
When the carrier is positioned at a certain level both sensors are activated. When a
product is placed on or removed from the carrier, the carrier can move due to the
elongation of the belts. This can be detected when one of the sensors becomes inactive.
To keep the carrier at the correct level, move the carrier in the direction of the inactive
sensor.
4.2.1 Connection unit
A Connection unit
B Additional connection unit
The sensors in the column are wired through
the cable tray in the column to the connection
unit in the drive section.
When the machine is configured to stop at
more than two levels, an additional connection
unit is installed (B).
4.3 Motor
The motor drives the movement of the carrier. It is necessary to control this motor with a
frequency inverter for controlled start/stop and optimum adjustment of the vertical speed.
EMC directives must be observed and the device should be installed in accordance with
the manufacturer specifications.
If a braking resistor has been connected, it might be necessary to change some
parameters of the frequency inverter. Please consult your frequency inverter supplier for
detailed instructions, because these changes depend on the inverter brand.
B
A
Note
When using a frequency inverter for hoisting applications, a braking resistor
must be installed in order to dispense the energy that is generated by the drive
motor when moving down. If there is no braking resistor, the energy causes too
high voltage inside the frequency inverter.
Table of contents
Other Qimarox Lifting System manuals
Popular Lifting System manuals by other brands
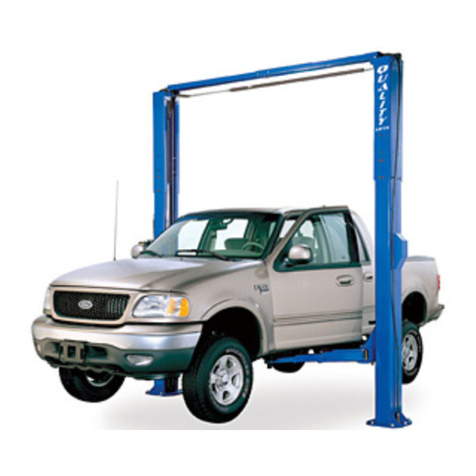
QUALITY LIFTS
QUALITY LIFTS Q10 Installation, operation & maintenance manual
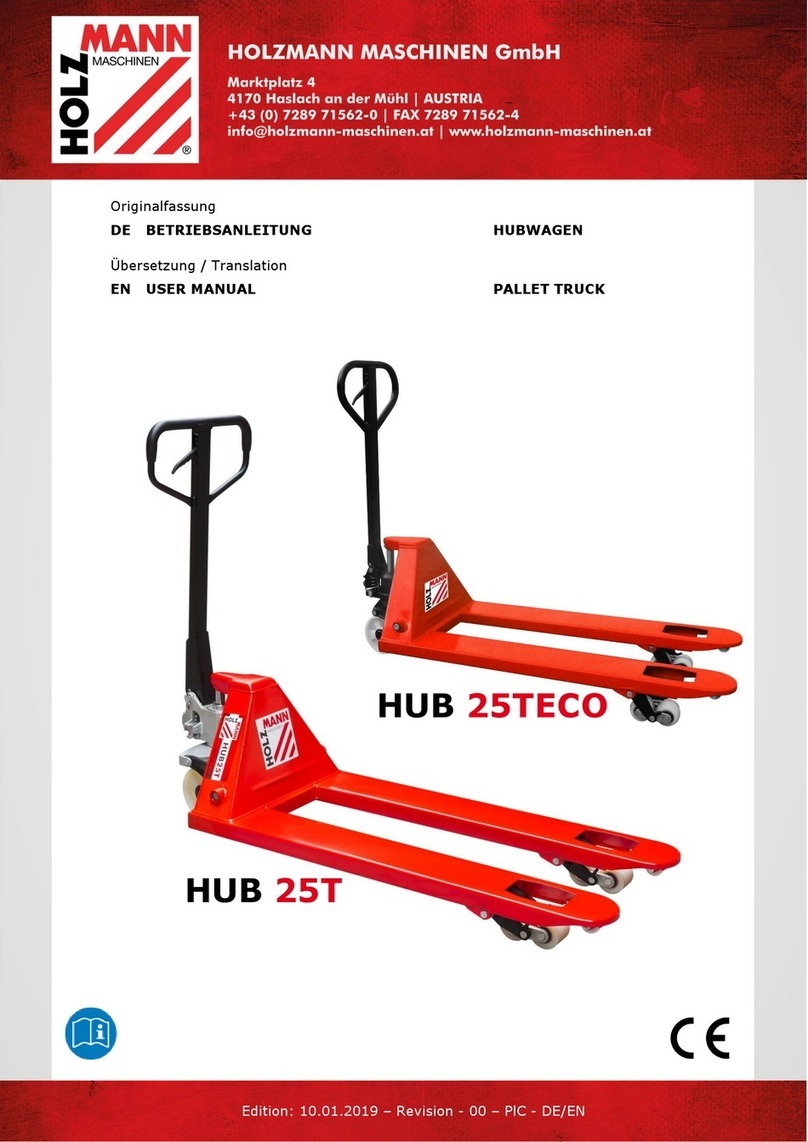
HOLZMANN MASCHINEN
HOLZMANN MASCHINEN HUB 25TECO user manual

ULTRA LEGS
ULTRA LEGS Tri-Toon installation guide
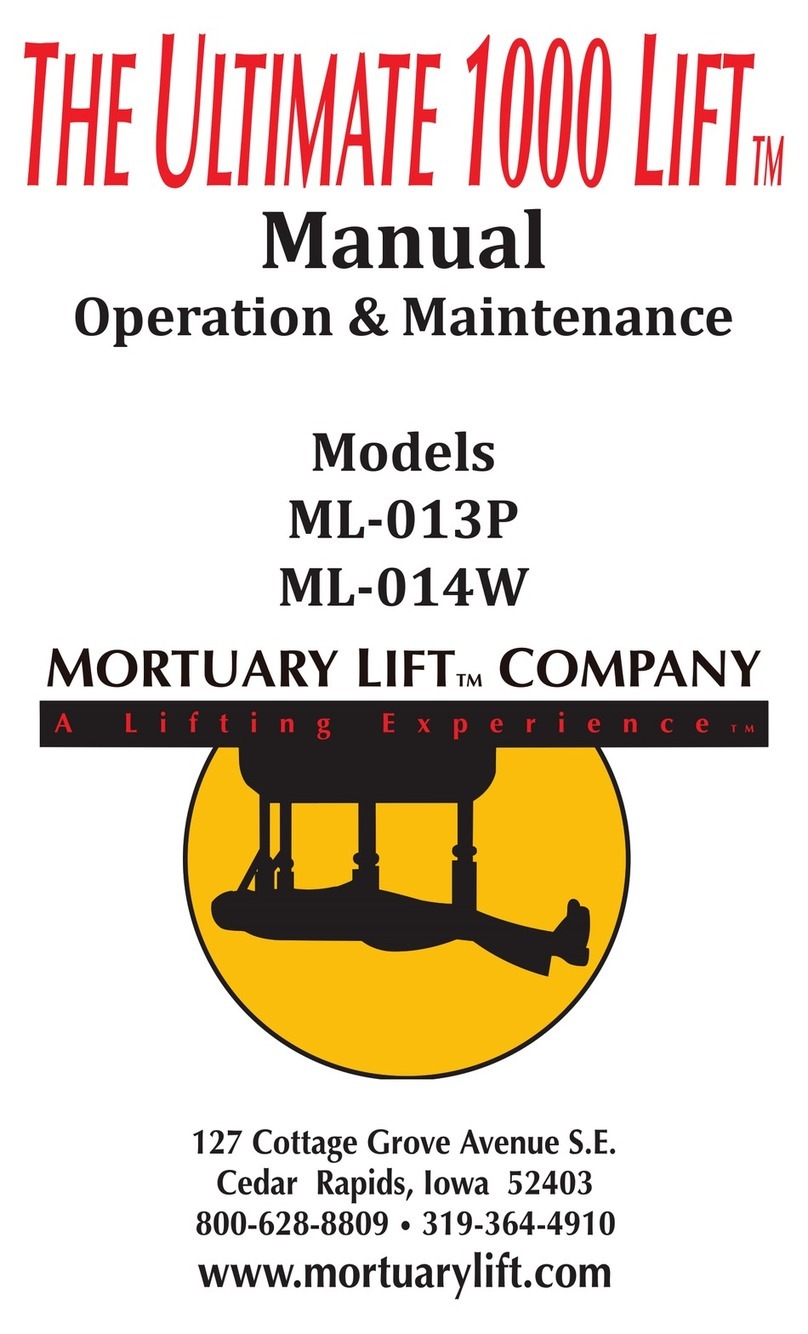
Mortuary Lift
Mortuary Lift Ultimate 1000 Lift ML-013P Operation & maintenance manual

Blitz
Blitz GWSK operating instructions

Aqua Creek
Aqua Creek PATRIOT PORTABLE LIFT Installation and operating instructions