Pocket NC V2 User manual

V2 Troubleshooting Guide

Table of Contents
Table of Contents 1
Revision History 1
Intro 1
Common Problems 1
Machining/Performance 4
Error Codes 6
Resetting/Updating the Machine 8
Revision History
First Release: October 2017 (JD)
Introduction
Our goal at Pocket NC is to produce an excellent product at an affordable price so that people
can turn their ideas into reality. We hope that using our product is a straightforward process and
the the machine functions perfectly. But, we know that things don’t always go perfectly.
Hopefully this troubleshooting guide can help you resolve some of the problems that come up.
If your problem is not covered here, or if you need some more information, please contact us.
For instructions on how to run the machine, set-up parts for machining, measure tool offsets and
other operation instruction see our tutorials.
1

Section 1: Common Problems
Problem
Possible Solutions
I can’t connect to my Pocket
NC or the user interface is
not loading correctly on my
computer.
1. Check that the Pocket NC is is plugged in and is
powered on. The red LED on the E-stop button will
light up when the machine is on. The user interface is
ready to boot when the red LED starts blinking. It
takes 2 and half minutes to fully boot the Pocket NC.
2. The computer must be connected to the mini-USB port
on the mill not the standard USB port.
3. The mini USB may not be fully plugged into the
machine. The pocket is deep so the plastic around the
plug may have to be trimmed to fit.
4. The machine may not be fully booted. Wait 1 minute
after turning on the machine before trying to connect.
5. The user interface may not load properly in every
browser. Try using Chrome, Firefox, or Safari
6. Try rebooting the machine: power off the machine,
unplug all the cords, wait about a minute for the
capacitors to drain then plug it back in and restart.
7. You may need a different driver. Try downloading a
new driver from the Beagleboard website.
8. Contact the Pocket NC help desk or post of the Pocket
NC forum for help.
The Pocket NC is
unresponsive, nothing
happens when I tell the
Pocket NC to move.
1. Check that the Pocket NC is plugged in and that the
power switch is on. The Pocket NC’s electronics can
run off computer power, but the motors can’t.
2. Make sure that the Pocket NC is not in E-stop mode.
When the machine is in E-stop the red button on the
machine will blink and the buttons in the upper right
corner of the user interface will be gray/white.
2

Push the E-stop button to enable the motors.
3. Check that the computer is still connected to the
Pocket NC with the USB cord.
4. Try rebooting the machine: power off the machine,
unplug all the cords, wait about a minute for the
capacitors to drain then plug it back in and restart.
5. Contact the Pocket NC help desk or post of the Pocket
NC forum for help.
One of the axes on my
Pocket NC is not working
1. Try rebooting the machine: power off the machine,
unplug all the cords, wait about a minute for the
capacitors to drain then plug it back in and restart.
2. Check the electrical connections for that axis. Look for
damage and debris.
3. Contact the Pocket NC help desk or post of the Pocket
NC forum for help.
The Pocket NC motors are
noisy when the machine is
running
Particularly at low feed rates, the stepper motors can produce
quite a bit of noise. This is due to the electrical interference in
the driver circuit.
Increasing the feed rate usually decreases the sound.
The Pocket NC is not cutting
in the location that I
expected.
1. Make sure that the origin for your toolpaths is the B
table offset/machine origin point of the Pocket NC.
This is a point in space about 0.839 inches above the
center of the B table.
2. Check if the coordinate system of your machining
setup in CAM is set up so that the positive Z axis
points at the spindle of the Pocket NC, the positive X
axis points at the A table, and the positive Y axis
points straight up from the B table.
3. Check if the toolpath origin is also the B table
offset/machine origin point and that the toolpath
coordinate system is appropriate. Remember that the
Z axis is always the Pocket NC spindle.
4. Make sure that your stock is located in the same place
3

on your machine as it was relative to the origin point in
your CAM program.
I can’t find/load my G-code
file
1. Check if the selection set for the file type includes your
file extension (file type) for example you can’t find
machining files with a .nc extension if the selection set
is looking for only .ngc files
2. The file must be a text file that the Pocket NC is
capable of reading. Generally these will have a
extension like .ngc, .nc, or .cnc but any machinable file
should work.
4

Section 2: Machining/Performance Issues
Problem
Explanation
Possible Solution/Things to Try
My tool chatters during
the cut.
Vibration causes the cutter
to not cut smoothly. This
vibration is due to the
natural frequency of the
tool/spindle.
1. The feed and speed, and/or
step-down and step-over
need to be adjusted. See
the feeds and speeds
tutorial for more
information.
2. Turn the spindle speed up.
3. Adjust the feedrate, usually
moving slower will be
smoother, but this is not
always the case
4. Increase the step-down,
taking a deeper cut into the
material
5. Increase or decrease the
step-over, the width of the
cut. Typically the ideal
step-over is about 60% of
tool diameter.
Spindle sounds like it is
slowing down during the
cut.
The spindle power is
insufficient for the amount of
material being removed.
1. Decrease the feed rate in
5% steps until the spindle
stops bogging down
2. Decrease the step-down
and step over in your
toolpaths.
3. Switch to a tool with more
cutting flutes.
The Pocket NC is not
cutting in the location
that I expected.
1. Make sure that the origin
for your toolpaths is the B
table offset/machine origin
point of the Pocket NC.
This is a point in space
about 0.839 inches above
the center of B table.
5

The stock may not be
located in the same position
relative to the origin point
that it was in the CAM
software used to create the
toolpaths
2. Check if the coordinate
system of your machining
setup in CAM is set up so
that the positive Z axis
points at the spindle of the
Pocket NC, the positive X
axis points at the A table,
and the positive Y axis
points straight up from the
B table.
3. Check if the toolpath origin
is also the B table
offset/machine origin point
and that the toolpath
coordinate system is
appropriate. Remember
that the Z axis is always the
Pocket NC spindle.
4. Make sure that your stock
is located in the same place
on your machine as it was
relative to the origin point in
your CAM program.
The drive/lead screws
squeak.
The end of the lead screw is
touching the frame of the
machine when it turns.
1. Make sure that the screw
and the hole are free of
debris.
2. If the noise it minor is is
best to let it wear into
position. The noise should
decrease with time
- Use a very small amount of
general purpose synthetic
grease to lubricate the tip of
the screw.
- Do not grease the whole
screw.
- Do not put grease where it
will contact the
anti-backlash nuts.
- Grease will collect debris
and may cause increased
wear on your machine.
6

Section 3: Error Codes
Error Code/Message
Explanation
Possible Solutions
Near Line XX Linear Move
Exceeds Joint X’s
Positive/Negative Limit
This error means that the
toolpath/G code is telling the
machine to go past one its
travel limits
Joint 0 = X axis
Joint 1 = Y axis
Joint 2 = Z axis
Joint 3 = A axis
Joint 4 = B axis
This error is often caused by
a tool length offset being set
incorrectly or by a part that is
outside the Pocket NC’s
work envelope.
The move that is causing the
error is located on or near
the line of the program
indicated
1. If the error is on joint 2 (Z
axis), check if your tool
length offset is set
correctly. See the “Tool
Length Offset” tutorial for
more information.
2. If the error is for
exceeding the negative
limit of joint 2 and the tool
length offset is correct,
increase the tool stickout
or switch to a longer tool
holder.
3. If the error is for
exceeding the positive
limit of joint 2 and the tool
length offset is correct,
decrease the tool stickout
or switch to a shorter tool
holder.
4. Check if your toolpath is
asking the machine to
exceed its limits of travel.
Open your code in a text
editing program and use
the search bar (CTRL +
F) to search for any
values that are greater
than the limits of travel for
the Pocket NC mill.
a. The X limits are
-2.00 to 2.55
inches
b. The Y limits are
-2.4 to 2.6 inches
c. The Z limits are
7

-3.45 to 0.10
inches*
d. The A limits are
-25 to 135
degrees
e. The B limits are
-9999 to 9999
degrees
*you have to add the tool
length offset to the Z axis
value
5. Adjust the location of the
part/stock so that it is
within the Pocket NC’s
work envelope
6. Decrease the retract
height on the toolpaths if
the part is close to the
limits of the Pocket NC’s
travel.
7. Oversized parts may be
able to be fixtured and
cut one side at a time
instead of all in one
program.
14 Unexpected Real Time
Delay on RT Thread 1
This error means that there
has been a delay in the
Beaglebones processor.
1. This error can be caused
by a temporarily dropped
connection between the
computer and the Pocket
NC mill or by a program
that is so large and
complicated that the
Beaglebone’s processor
cannot keep up.
2. Check that the
connection between the
computer and the
machine is good.
3. Try slowing down the
feed rate or reducing the
file size of the G code file
8

by breaking it into more
than 1 operation or by
loosening the tolerances
in the toolpath and
reposting it.
Section 4: Resetting/Updating the Machine
This section will have instructions on how to update the machine when that capability is
available.
This update process will require an internet connection through the ethernet port on the Pocket
NC.
9
Other Pocket NC Control System manuals
Popular Control System manuals by other brands
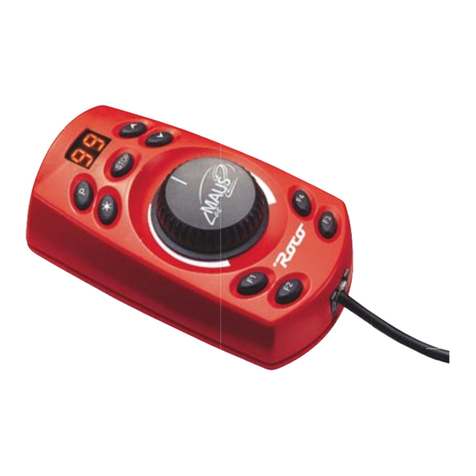
roco
roco LOKMAUS 2 manual
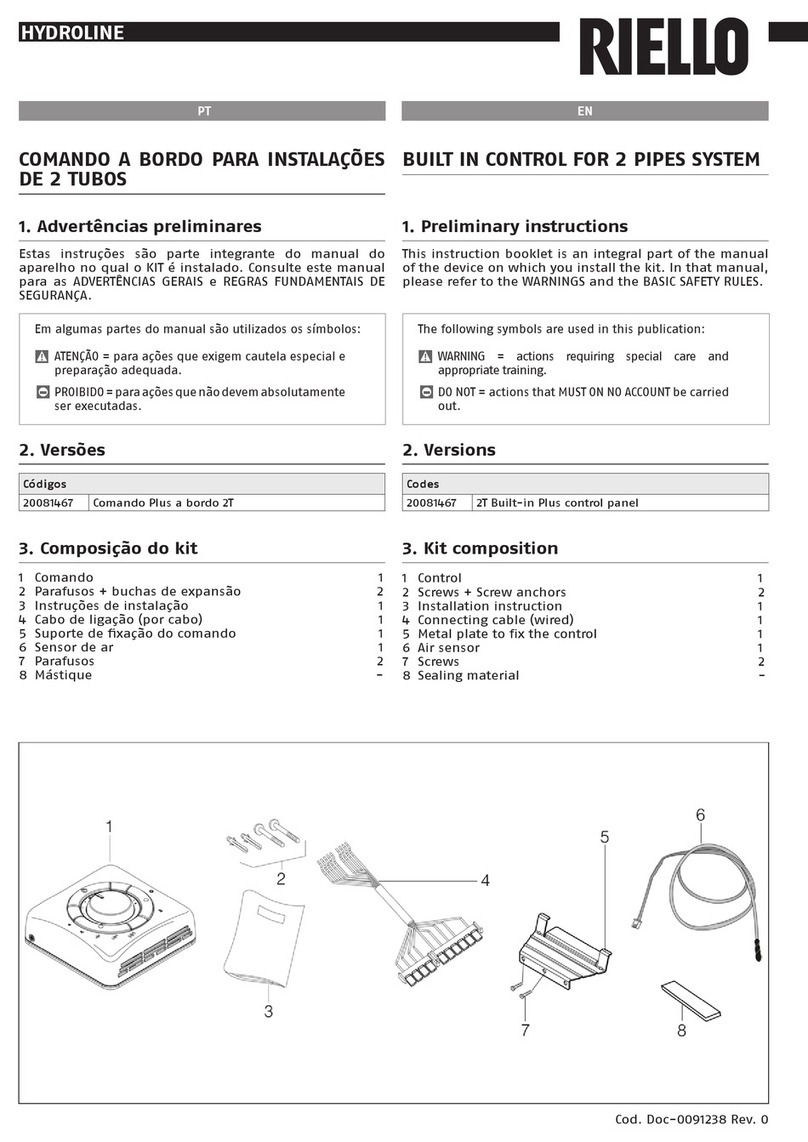
Riello
Riello 20081467 Instruction booklet
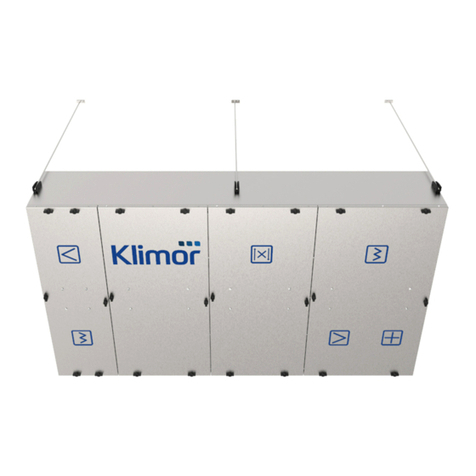
Klimor
Klimor EVO-T Operation and maintenance manual

Motorline professional
Motorline professional mbm6 installer and user manual

NEC
NEC ElectraElite 48 System hardware manual

LIFE home integration
LIFE home integration SUPRA MB 6Mt 24 Vdc instructions