Hanwell MS1000 User manual

hanwell.com
GD6063
MS1000 Control System
Installation Guide

Intentionally Left Blank

MS1000 Control System
Installation Guide
hanwell.com Page 1 of 31 GD6063-1
Document History
Document Number: GD6063
Issue No. Issue Date Changes By
1 26 October 2018
Changes to take account of introduction
of EMS and reformatting IR

MS1000 Control System
Installation Guide
GD6063-1 Page 2 of 30 hanwell.com
Contents
1Overview of the MS1000 Control System....................................................................... 4
2MS1000 Control System Configuration .......................................................................... 5
2.1Option 1 - Standalone Solution...................................................................................................... 5
2.2Option 2 - Monitoring and Control Solution .............................................................................. 6
2.2.1Controllers/Processors ...............................................................................................................7
2.3Output Cards...................................................................................................................................... 8
2.3.1Output Card Specifications ...................................................................................................... 11
3Pre-Delivery........................................................................................................................12
4Firmware/Software Requirements..................................................................................13
4.1Firmware ............................................................................................................................................ 13
4.2Software ............................................................................................................................................. 13
4.2.1New Systems............................................................................................................................... 13
4.2.2Existing Systems......................................................................................................................... 13
5Pre-Commissioning...........................................................................................................14
6MS1000 Output Card ID Number................................................................................... 15
6.1ID Number .........................................................................................................................................15
6.1.1Setting the ID Number ..............................................................................................................15
7Connecting the MS1000 Control System...................................................................... 16
7.1Power Supply.................................................................................................................................... 16
7.2Controller to MS1000 Control Unit - USB Cable Wiring........................................................ 17
7.3RS485 Wiring from Controller to MS1000 Control Unit ........................................................ 17
7.3.1Standalone MS1000 Systems................................................................................................. 17
7.3.2Monitoring and Control Systems ........................................................................................... 17
7.3.3Wiring Summary ........................................................................................................................20
7.3.4Customer Supplied Wiring Required Specifications .......................................................20
7.4Wiring the Output Cards ................................................................................................................21
8Technical Reference ........................................................................................................22

MS1000 Control System
Installation Guide
hanwell.com Page 3 of 30 GD6063-1
8.1MS1000 Enclosures ....................................................................................................................... 22
8.1.1Standard Case (Code N001) .................................................................................................. 22
8.1.2Large Case (Code N016)......................................................................................................... 22
8.1.3Extra Large Case (Code N051) .............................................................................................. 22
8.1.4MS1000 Output Card Case .................................................................................................... 23
8.2Allowable Temperature and Humidity Ranges ...................................................................... 23
9Hanwell MS1000 System Fault Checking.....................................................................24
9.1Signals are not being received on any channels .................................................................. 24
9.2Signals are not being received on some channels............................................................... 25
9.3Readings are incorrect.................................................................................................................. 26
10Existing Hanwell EMS Users........................................................................................... 27
10.1Hardware .......................................................................................................................................... 27
10.2Software............................................................................................................................................ 27
10.2.1Wiring ........................................................................................................................................... 27
11Contact Information.........................................................................................................28

MS1000 Control System
Installation Guide
GD6063-1 Page 4 of 30 hanwell.com
1Overview of the MS1000 Control System
The Hanwell MS1000 Control System is an interface between a Hanwell Environmental
Monitoring System (EMS) and 3rd party control equipment.
It is designed to generate either latched voltages or currents corresponding to inputs,
proportional to measured values, generated by sensors, in remote locations, that are
compatible with the Hanwell Environmental Monitoring System (EMS) software.
Typical applications could include:
Interfacing radio sensors to a Building Management System (BMS).
Conservation heating systems.
Bespoke heating control.
Providing signals to an Alarm Panel.
The MS1000 Control System can:
Allow radio sensors to directly replace wired-in sensors in applications such as building
environmental control where the 3rd party BMS can directly accept analogue signals.
Trigger relay outputs for alarm or control functions (e.g. motorised valves).
Provide a combination of all output types within a single MS1000 system.

MS1000 Control System
Installation Guide
hanwell.com Page 5 of 30 GD6063-1
2MS1000 Control System Configuration
There are two main options for configuring the MS1000 Control System:
Standalone Solution
Monitoring and Control Solution
2.1 Option 1 - Standalone Solution
Radio sensors transmit directly back to the MS1000 Control Unit via either a standalone
Receiver connected to the MS1000 or a receiver incorporated into the MS1000 Control
Unit.
The MS1000 Control Outputs are sent to, for example, a 3rd Party Building Management
System (BMS).
Figure 1 - Stand Alone Solution Schematic

MS1000 Control System
Installation Guide
GD6063-1 Page 6 of 30 hanwell.com
2.2 Option 2 - Monitoring and Control Solution
Radio sensors transmit to an SR2 or CR2 Controller/Processor/Base Station (Controller).
The Controller sends the data to both a monitoring PC and the MS1000 Control Unit.
The MS1000 Control Outputs are sent to, for example, a Building Management System
(BMS). See Figure 2 below:
Sensor 1’s output controls Plant A.
Sensor 2’s output controls Plants B and C.
Note: In some applications, the Controller may be enclosed within the MS1000 Control Unit;
the Controller PCB being either in a separate Control Unit or mounted within the
MS1000’s Control Unit, depending on the exact system supplied.
Figure 2 - Monitoring and Control Solution Schematic

MS1000 Control System
Installation Guide
hanwell.com Page 7 of 30 GD6063-1
Figure 3 – General System Schematic
2.2.1 Controllers/Processors
The CR2 and SR2 Controllers both provide an interface/controls for the MS1000 Control
System in addition to their other functions as outlined in Sections 2.2.1.1 and Error! Reference
source not found. below.
2.2.1.1 Hanwell CR3
The CR3 Controller receives and processes data signals from Hanwell radio and wired
sensors and is designed for continuous monitoring of an entire system.
Received data is then logged and stored, pending transfer to a PC for analysis and
archival storage.
The CR3 also signals alarm conditions via the front panel LEDs (should any sensor
measure above or below individual pre-set levels).
Although the CR3 Controller has an extensive memory capacity, it is intended that the
data is transferred to a PC for detailed interpretation and permanent storage. This can
be done automatically or manually, at any time.
A built in GSM modem for remote communications is also available.

MS1000 Control System
Installation Guide
GD6063-1 Page 8 of 30 hanwell.com
2.2.1.2 Hanwell SR2
The SR2 Hanwell Smart Receiver/Controller is a network enabled receiver, designed for
continuously monitoring environmental data from multiple points within a site, or across
multiple sites, receiving and processing data signals from Hanwell radio and wired sensors.
Additionally, the SR2 can be fitted with up to eight onboard probes and can be upgraded to a
transceiver to both receive and re-transmit the data.
Each SR2 can handle data from up to 253 sensors and, as up to 16 SR2s can be run on a
single system, up to 4048 sensors can be connected to a single system.
The SR2 logs all received data in its on-board 512kb memory.
The software continually interrogates the SR2 for the most recent data and downloads
the data according to user-defined logging periods to the server or operating PC from
where software users can view live and historic data, produce out of specification and
summary reports and set alarms for both the data values and the rate of change of the
data’s values.
An optional remote Receiver can be connected to improve radio reception in difficult
areas.
Alarm relays are included: these can indicate that the readings are out of specification
and can, optionally, be set to indicate a network failure.
An MS BUS connection allows the SR2 to drive the Hanwell MS1000 Control System.
2.3 Output Cards
Input signals generated by sensors are either passed directly to the MS1000 Control System
or passed to a CR3 or SR2 Controller for processing, before transmission to the MS1000
Control System.
Output signals from the MS1000 Control System to the systems/equipment under control are
generated by Output Cards located within the MS1000 Control Unit.

MS1000 Control System
Installation Guide
hanwell.com Page 9 of 30 GD6063-1
Figure 4 - Output Card
<<NEED PHOTO OF PINS ON OTHER SIDE>>
Each Output Card can output four separate data streams in four individual channels.
See Figure 8.
Output Cards can be added to or removed from the MS1000 Control System/Panel
according to:
The complexity of the system being controlled.
The type of input required by, for example, the Building Management System’s
(BMS) control systems.
The presence and number of any alarms on the system being controlled.
The input signal, received directly from the sensors or via a Controller, is passed from
the first Output Card added to each additional Output Card via a series of 10 pins and
corresponding sockets on each side of the card.
The first Output Card receives the input signal from the MS Connector which is
directly wired to either the Controller or the MS1000 Control Unit (see Figure 7 –
MS Connector Wiring).
Pins/Sockets 1, 2, 3 and 7 are used to pass the input signal and power supply
between each Output Card. See Figure 5 Output Card Mounting and Pins.
Data/Power Input Sockets

MS1000 Control System
Installation Guide
GD6063-1 Page 10 of 30 hanwell.com
The MS1000 wall mounted case contains a DIN rail onto which the MS Connector and
each MS1000 Output Card is snap-mounted (see Figure 5 Output Card Mounting and
Pins).
Figure 5 Output Card Mounting and Pins
Each standard MS1000 case can contain up to 8 Output Cards.
For larger systems either a larger MS1000 Control Unit, or multiple Control Units
connected together, can supply additional outputs. See Section 8.1 MS1000
Enclosure for case options.
Two card types/signal output are available for the MS1000 system, Analogue and Relay,
depending on which type of signal output is required:
MS1000-RM (8-bit) – (Relay).
MS1000-AM (12-bit) – (Analogue).
Both types of Output Card are added to the MS1000 Control Unit in the same way.
Analogue and Relay Output Cards can be combined in the same MS1000 Control Unit to
provide the necessary range of signal/output types.

MS1000 Control System
Installation Guide
hanwell.com Page 11 of 30 GD6063-1
2.3.1 Output Card Specifications
2.3.1.3 Relay Output Card
Number of Outputs: 4
Relay Rating: Capable of switching
Either:
0.5A at 12V DC
Or:
0.5A at 24V AC
Higher power relays can be driven from the card where necessary
Pin Out: See Table 6 – Output Card Wiring
Other Notes: Normally open or normally closed are available as standard.
2.3.1.4 Analogue Output Card
Number of Outputs: 4
Output Options: Either:
A Voltage between 2 <<?? – SOME REFS STATE 0 HERE>> and 10V
(1mA)
Or:
A Current between 0 and 20mA (compliance = 12V)
Pin Out: See Table 6 – Output Card Wiring
Other Notes: GND is internally connected to PE
On a motorised valve system using the voltage output, contractors
must ensure that the power to the drive Control Unit (commonly 24V
AC) is connected appropriately to avoid earth conflicts.
Fault conditions are indicated by a permanent drop to zero and a low
battery condition is indicated by a brief drop to zero.
Analogue cards are available with 8 or 12 bit resolution

MS1000 Control System
Installation Guide
GD6063-1 Page 12 of 30 hanwell.com
3Pre-Delivery
Prior to delivery, Hanwell Solutions should be supplied with a URS (User Requirement
Specification) detailing the output requirements for the system. These will then be
programmed into the MS1000 Firmware.
The URS should include the following information:
Control Strategy.
Number of channels required.
Equipment to be controlled.
Type of output required.
Note: Commissioning cannot be undertaken until the URS has been received.

MS1000 Control System
Installation Guide
hanwell.com Page 13 of 30 GD6063-1
4Firmware/Software Requirements
4.1 Firmware
The Firmware is the customised ROM fitted either to the MS1000 Control Board or the
CR3/SR2 Controller depending on the type of System.
It is written to the supplied URS (User Requirement Specification).
A URS MUST BE SUPPLIED TO HANWELL SOLUTIONS PRIOR TO
THE SHIPPING OF THE MS1000 CONTROL SYSTEM
4.2 Software
The EMS application is used during the commissioning process to set up the MS1000
Monitoring and Control Systems and for monitoring data via the CR3/SR2 Controller during
normal operation.
4.2.1 New Systems
New systems will be supplied with the most recent version of the most appropriate software
application.
Stand-alone systems can be commissioned via a laptop connected to the RS232 Serial
lead within the MS1000.
A Serial/USB adapter will be required if the laptop does not have a Serial Port.
Monitoring and Control systems will require a PC with a Serial Port, running Windows 95
or later. If networked, there should be full access rights available during installation.
4.2.2 Existing Systems
See Section 10 Existing Hanwell EMS Users.

MS1000 Control System
Installation Guide
GD6063-1 Page 14 of 30 hanwell.com
5Pre-Commissioning
Prior to the on-site commissioning of the system by a Hanwell Solutions Technician, the
following items should be prepared by the Customer’s electrical contractors:
Standalone MS1000 Systems
The MS1000 Control Unit(s) case(s) should mounted in position and drilled as
required for cable entry.
The required number and type of Output Cards should be mounted on the
MS1000 Control Unit’s DIN rail.
Mains power run should be run from a mains fused spur into the MS1000 Control
Unit’s case, but not connected.
All necessary control cables should be run from the BMS/plant to the MS1000
Control Unit’s case, but not connected. Cables must be clearly labelled.
Monitoring and Control Systems
The MS1000 Control Unit(s) case(s) should be mounted in position and drilled as
required for cable entry.
Output Cards should be mounted on the MS1000 Control Unit’s DIN rail.
Mains power should be run from a mains fused spur into the MS1000 Control
Unit’s case, but not connected.
A, Customer supplied, Bus cable should be run from the MS1000 Control Unit’s
case to a Junction Box adjacent to the CR2/SR2 Controller. See Section 7.3.2.
All necessary control cables should be run from the BMS/plant to the MS1000
Control Unit’s case but not connected. Cables must be clearly labelled.
A mains socket and PC must be available in the CR2/SR2 Controller’s planned
location.
If any of the pre-commissioning requirements have not been fulfilled, resulting in extra cost to
Hanwell Solutions, the additional costs will be passed on to the Customer, in addition to any
previously quoted commissioning costs.

MS1000 Control System
Installation Guide
hanwell.com Page 15 of 30 GD6063-1
6MS1000 Output Card ID Number
6.1 ID Number
Each MS1000 Output Card needs to be configured with a unique ID number.
This number is set during build at the factory and will not need adjusting.
Note: The information below on setting the ID number and wiring of the card is for reference
only; the Output Card’s ID does not need to be changed on site.
6.1.1 Setting the ID Number
The ID number is set using a set of 8 DIP switches on the PCB. These work in binary fashion,
being either ON or OFF, as shown in Table 1 - ID Number below.
Switch 1 2 3 4 5 6 7 8
Value 1 2 4 8 16 32 64 128
Table 1 - ID Number
When a switch is ON, it contributes its value to the ID number.
When a switch is OFF, it does not contribute its value to the ID number.
Example 1:
If the required Card ID is 19:
19 = 16 + 2 + 1 so switches 5, 2, and 1 should be ON.
Example 2:
If the required Card ID is 5:
5 = 4 + 1 so switches 3 and 1 should be ON.
Table 2 – Setting DIP Switches

MS1000 Control System
Installation Guide
GD6063-1 Page 16 of 30 hanwell.com
7Connecting the MS1000 Control System
7.1 Power Supply
The MS1000 Control Unit is powered from a single phase 240V 50Hz local mains supply from
a switched feed, fused at 3 Amps.
This is connected via a DIN rail mounted power supply, labelled with live, neutral and
earth, as shown in Figure 6 - Power Supply Connections.
+12V is generated internally to power the Output Cards and Control Board (if applicable).
The internal 0V reference is connected to local PE (Protective Earth).
Wiring supplying power to the Control Unit should be rated above 13A.
Figure 6 - Power Supply Connections

MS1000 Control System
Installation Guide
hanwell.com Page 17 of 30 GD6063-1
7.2 Controller to MS1000 Control Unit - USB Cable Wiring
The CR3/SR2 Controller communicates with the monitoring PC via a USB cable.
7.3 RS485 Wiring from Controller to MS1000 Control Unit
7.3.1 Standalone MS1000 Systems
No RS485 wiring is required for Standalone MS1000 systems as the MS1000 Control Unit’s
Control Board is connected directly to the Output Cards.
The Customer should arrange for the appropriate wiring from the Output Cards to the 3rd party
BMS/plant to be controlled via the MS1000 Control Unit.
7.3.2 Monitoring and Control Systems
The MS1000 Control Unit receives control signals from the CR3/SR2 Controller via Hanwell
and Customer supplied, RS485 twisted-pair cables.
The Hanwell supplied cable consists of a 2 metre 4 core cable with a moulded mini-DIN
plug and a free end.
The Customer supplied cable should be to the specifications outlined below in Table 5 -
Wiring Specifications.
7.3.2.5 Wiring a Monitoring and Control System
1. Run the Customer supplied cable from the MS1000 Control Unit’s location back to a
Junction Box, located within 2 meters of the CR3/SR2 Controller’s planned location.
Up to 1000m of cable (from the MS1000 Control Unit to the Junction Box) can be
used without line drivers being required.
2. Run the Hanwell supplied cable from the Junction Box to the CR3/SR2 Controller. See
Figure 3 – General System Schematic.
3. Connect both cables as follows:
i. Remove the Junction Box’s lid.
ii. Feed the bare ends of the Hanwell and Customer supplied cables into the
Junction Box through the cable glands and tighten the gland nuts.
4. Strip the insulation from the conductors on both cables and connect via the connector
block. See Figure 7 – MS Connector Wiring.

MS1000 Control System
Installation Guide
GD6063-1 Page 18 of 30 hanwell.com
Warning: The Hanwell supplied cable’s individual conductors and plug carry the
following signals:
Conductor Colour Signal Line Description
Red TX+ RS485 Tx +
Yellow TX- RS485 Tx -
Blue +12V Power +12V
Green GND Power 0V
The colours of the conductors of the Customer supplied cable may differ from those
of the Hanwell supplied cable.
As a result, it is important to ensure that the correct connections are made between
the CR3/SR2 Controller and the MS1000 Control Unit, via the Hanwell supplied cable
with a moulded mini-DIN plug, the Junction Box and the Customer supplied cable.
Check the connections thoroughly as any incorrect wiring may severely damage the
MS1000 Control Unit and possibly the CR3/SR2 Controller as well.
5. Refit the Junction Box’s lid.
Figure 7 – MS Connector Wiring
6. Feed the opposite end of the Customer supplied cable through the cable gland in the
bottom of the MS1000 Control Unit’s case and tighten the gland nut.
Table of contents
Popular Control System manuals by other brands

LBA GROUP
LBA GROUP LBA 12 IRREVERSIBLE operating instructions
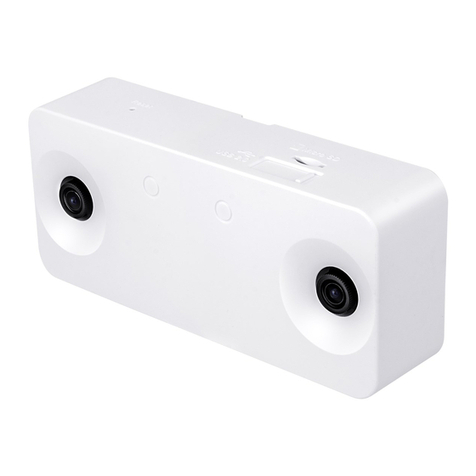
Vivotek
Vivotek SC8131 user guide
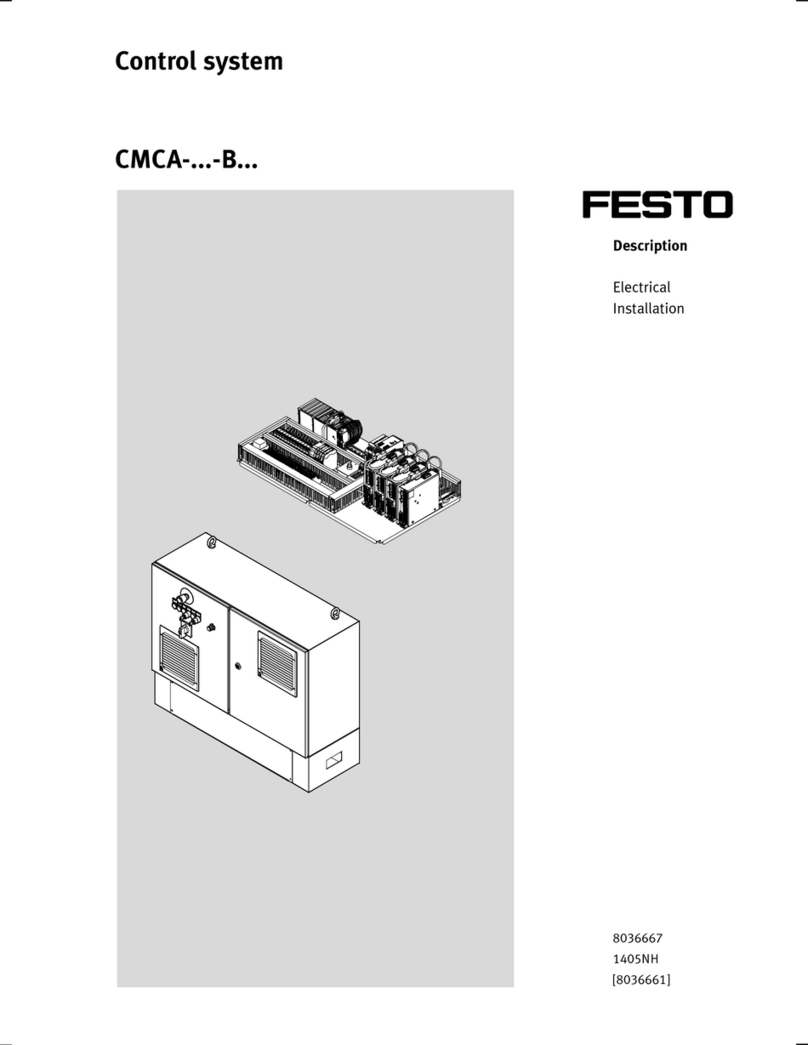
Festo
Festo CMCA-...-B Series Electrical installation
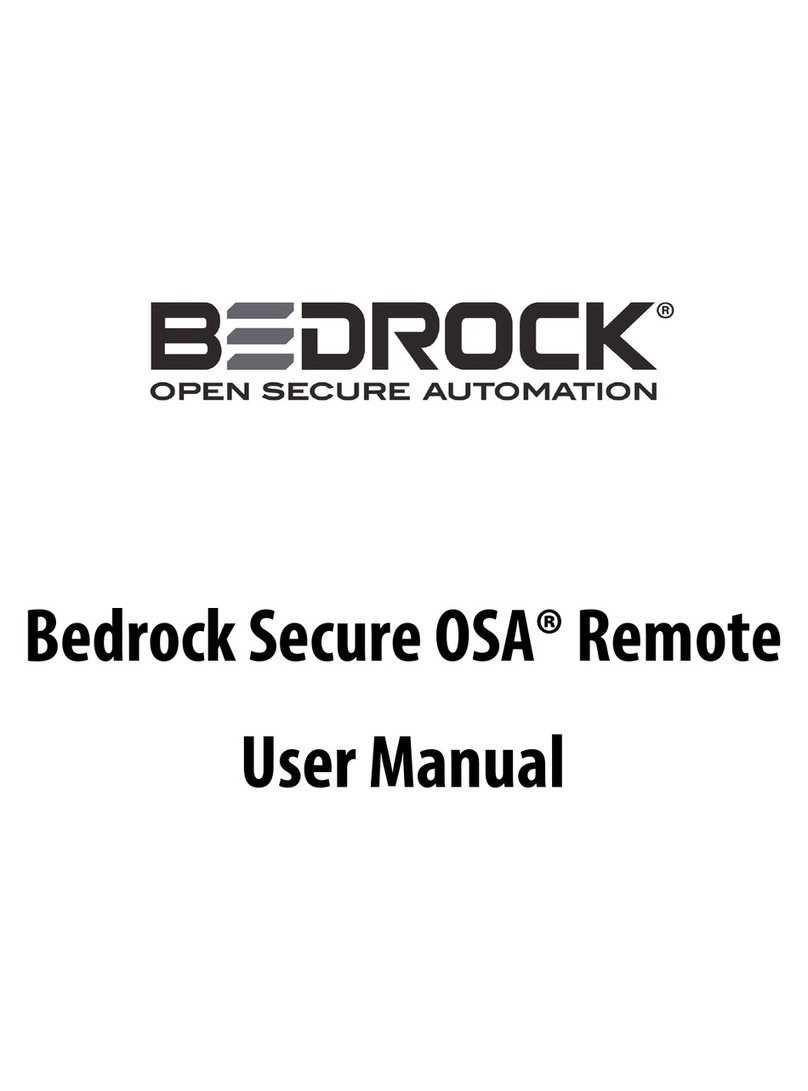
Bedrock
Bedrock Secure OSA Remote user manual
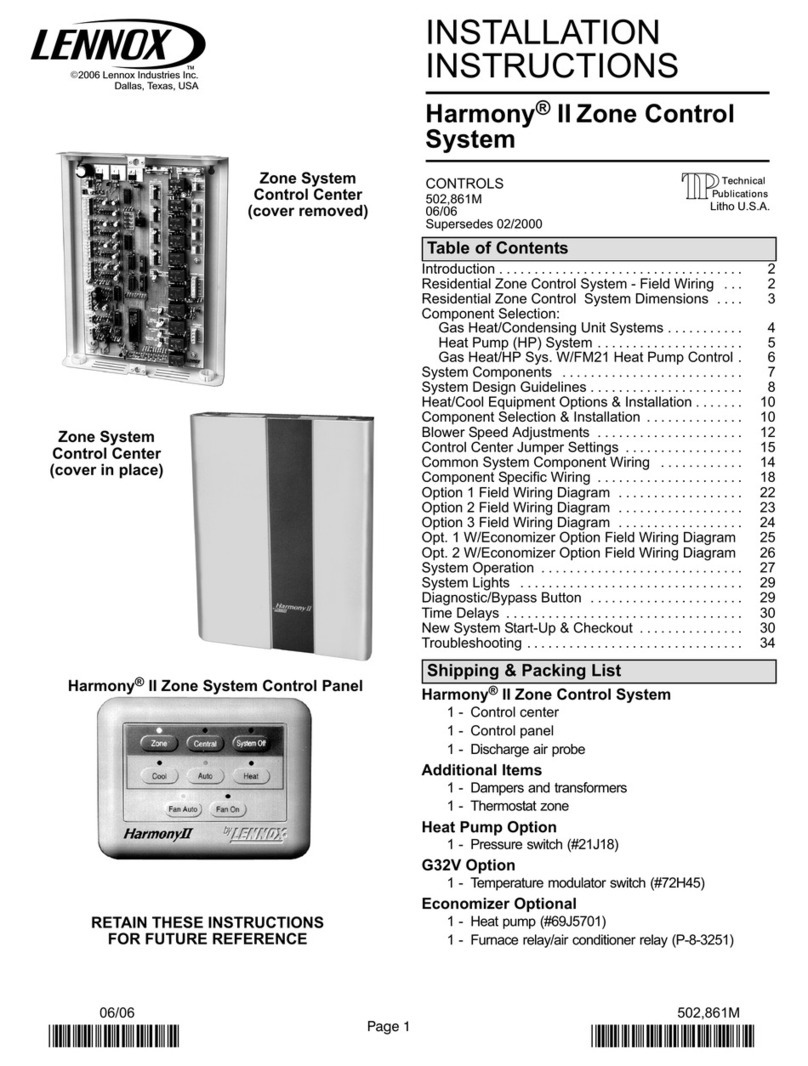
Lennox
Lennox Harmony II Zone Control System installation instructions
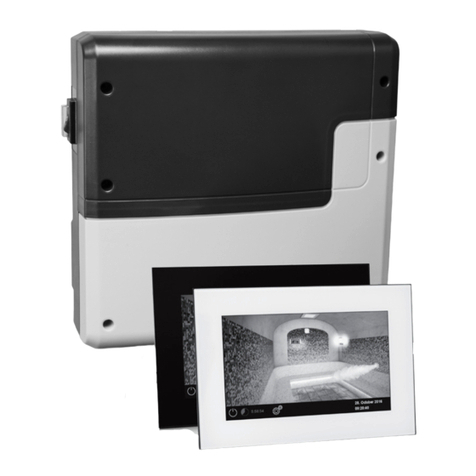
EOS
EOS LSG-Steam Installation and operation manual