REED TB12 User manual

OFFSET BEND CALCULATOR
1 3- 7/8 1 2 1 1- 13/32 1 1- 5/32 1 1- 1/32
1- 1/8 4- 11/32 1- 1/8 2- 1/4 1- 1/8 1- 19/32 1- 1/8 1- 5/16 1- 1/8 1- 5/32
1- 1/4 4- 27/32 1- 1/4 2- 1/2 1- 1/4 1- 25/32 1- 1/4 1- 7/16 1- 1/4 1- 5/16
1- 3/8 5- 5/16 1- 3/8 2- 3/4 1- 3/8 1- 15/16 1- 3/8 1- 19/32 1- 3/8 1- 7/16
1- 1/2 5- 25/32 1- 1/2 3 1- 1/2 2- 1/8 1- 1/2 1- 23/32 1- 1/2 1- 9/16
1- 5/8 6- 9/32 1- 5/8 3- 1/4 1- 5/8 2- 5/16 1- 5/8 1- 7/8 1- 5/8 1- 11/16
1- 3/4 6- 3/4 1- 3/4 3- 1/2 1- 3/4 2- 15/32 1- 3/4 2- 1/32 1- 3/4 1- 13/16
1- 7/8 7- 1/4 1- 7/8 3- 3/4 1- 7/8 2- 21/32 1- 7/8 2- 5/32 1- 7/8 1- 15/16
2 7- 23/32 2 4 2 2- 13/16 2 2- 5/16 2 2- 1/16
2- 1/8 8- 7/32 2- 1/8 4- 1/4 2- 1/8 3 2- 1/8 2- 15/32 2- 1/8 2- 3/16
2- 1/4 8- 11/16 2- 1/4 4- 1/2 2- 1/4 3- 3/16 2- 1/4 2- 19/32 2- 1/4 2- 5/16
2- 3/8 9- 3/16 2- 3/8 4- 3/4 2- 3/8 3- 11/32 2- 3/8 2- 3/4 2- 3/8 2- 15/32
2- 1/2 9- 21/32 2- 1/2 5 2- 1/2 3- 17/32 2- 1/2 2- 7/8 2- 1/2 2- 19/32
2- 5/8 10- 5/32 2- 5/8 5- 1/4 2- 5/8 3- 23/32 2- 5/8 3- 1/32 2- 5/8 2- 23/32
2- 3/4 10- 5/8 2- 3/4 5- 1/2 2- 3/4 3- 7/8 2- 3/4 3- 3/16 2- 3/4 2- 27/32
2- 7/8 11- 3/32 2- 7/8 5- 3/4 2- 7/8 4- 1/16 2- 7/8 3- 5/16 2- 7/8 2- 31/32
3 11- 19/32 3 6 3 4- 1/4 3 3- 15/32 3 3- 3/32
3- 1/8 12- 1/16 3- 1/8 6- 1/4 3- 1/8 4- 13/32 3- 1/8 3- 19/32 3- 1/8 3- 7/32
3- 1/4 12- 9/16 3- 1/4 6- 1/2 3- 1/4 4- 19/32 3- 1/4 3- 3/4 3- 1/4 3- 3/8
3- 3/8 13- 1/32 3- 3/8 6- 3/4 3- 3/8 4- 25/32 3- 3/8 3- 29/32 3- 3/8 3- 1/2
3- 1/2 13- 17/32 3- 1/2 7 3- 1/2 4- 15/16 3- 1/2 4- 1/32 3- 1/2 3- 5/8
3- 5/8 14 3- 5/8 7- 1/4 3- 5/8 5- 1/8 3- 5/8 4- 3/16 3- 5/8 3- 3/4
3- 3/4 14- 1/2 3- 3/4 7- 1/2 3- 3/4 5- 5/16 3- 3/4 4- 11/32 3- 3/4 3- 7/8
3- 7/8 14- 31/32 3- 7/8 7- 3/4 3- 7/8 5- 15/32 3- 7/8 4- 15/32 3- 7/8 4
4 15- 15/32 4 8 4 5- 21/32 4 4- 5/8 4 4- 1/8
4- 1/8 15- 15/16 4- 1/8 8- 1/4 4- 1/8 5- 27/32 4- 1/8 4- 3/4 4- 1/8 4- 9/32
4- 1/4 16- 13/32 4- 1/4 8- 1/2 4- 1/4 6 4- 1/4 4- 29/32 4- 1/4 4- 13/32
4- 3/8 16- 29/32 4- 3/8 8- 3/4 4- 3/8 6- 3/16 4- 3/8 5- 1/16 4- 3/8 4- 17/32
4- 1/2 17- 3/8 4- 1/2 9 4- 1/2 6- 3/8 4- 1/2 5- 3/16 4- 1/2 4- 21/32
4- 5/8 17- 7/8 4- 5/8 9- 1/4 4- 5/8 6- 17/32 4- 5/8 5- 11/32 4- 5/8 4- 25/32
4- 3/4 18- 11/32 4- 3/4 9- 1/2 4- 3/4 6- 23/32 4- 3/4 5- 15/32 4- 3/4 4- 29/32
4- 7/8 18- 27/32 4- 7/8 9- 3/4 4- 7/8 6- 29/32 4- 7/8 5- 5/8 4- 7/8 5- 1/32
5 19- 5/16 5 10 5 7- 1/16 5 5- 25/32 5 5- 3/16
5- 1/8 19- 13/16 5- 1/8 10- 1/4 5- 1/8 7- 1/4 5- 1/8 5- 29/32 5- 1/8 5- 5/16
5- 1/4 20- 9/32 5- 1/4 10- 1/2 5- 1/4 7- 7/16 5- 1/4 6- 1/16 5- 1/4 5- 7/16
5- 3/8 20- 25/32 5- 3/8 10- 3/4 5- 3/8 7- 19/32 5- 3/8 6- 7/32 5- 3/8 5- 9/16
5- 1/2 21- 1/4 5- 1/2 11 5- 1/2 7- 25/32 5- 1/2 6- 11/32 5- 1/2 5- 11/16
5- 5/8 21- 23/32 5- 5/8 11- 1/4 5- 5/8 7- 31/32 5- 5/8 6- 1/2 5- 5/8 5- 27/32
5- 3/4 22- 7/32 5- 3/4 11- 1/2 5- 3/4 8- 1/8 5- 3/4 6- 5/8 5- 3/4 5- 31/32
5- 7/8 22- 11/16 5- 7/8 11- 3/4 5- 7/8 8- 5/16 5- 7/8 6- 25/32 5- 7/8 6- 3/32
6 23- 3/16 6 12 6 8- 15/32 6 6- 15/16 6 6- 7/32
ANGLE OF OFFSET 15° ANGLE OF OFFSET 30° ANGLE OF OFFSET 45° ANGLE OF OFFSET 60 ° ANGLE OF OFFSET 75°
AMOUNT OF OFFSET AMOUNT OF OFFSET AMOUNT OF OFFSET AMOUNT OF OFFSET AMOUNT OF OFFSET
(Y Dimension) (X Dimension) (Y Dimension) (X Dimension) (Y Dimension) (X Dimension) (Y Dimension) (X Dimension) (Y Dimension) (X Dimension)
(Inches) (Inches) (Inches) (Inches) (Inches) (Inches) (Inches) (Inches) (Inches) (Inches)
How to Figure Total Length ofTubing Required for 45° Offset Applications
OFFSET BENDS
OFFSET
DIMENSION
“Y”
“Z”
DIMENSION
NOISNEMID
RETNECOTRETNEC
DNEBFO
”X“
MARK B
MARK A
STEP 1 - Determine the total amount of offset required
(dimension “Y” in diagram) and angle of offset. Wherever
possible use 45° offset bends. This will enable you to figure
the total amount of tubing required for a given application
as explained in section on How to Figure Length of Tubing
Required for 45° Offset Applications.
STEP 2 - Figure the length of tube which is needed to meet
your offset requirements (“X” in dimension diagram) from table
below. For example: Say the amount of offset you require
(“Y” dimension, Step 1) is 2-1/2” and the offset angle is 45°.
Check the 45° column and find 2-1/2”.The figure next to this
is the amount of tubing required for the offset bend you want
(“X” dimension). Inthis case it’s 3-17/32”.
STEP 3 - Determine where you want the center of the offset
bend on the tube and make a reference mark (A).
Now measure off the “X” dimension (determined in Step 2,
example 3-17/32”) starting from the reference mark and
make a second mark (B). You are now ready to make the
bends.
STEP 4 - Align mark (A) with reference mark “R” on
bender and proceed with first bend. Then align (B) with
“R” mark and make second bend in proper direction.
NOTE:When the amount of offset exceeds what is listed
on the table, choose an offset from the table which is a
multiple of the offset you need. Look this up on the table
and multiply the “X” dimension by the multiple you used.
Example: For an offset of 20” for a 45° bend, look up
5” offset on the table in the 45° column and multiply “X”
dimension (7-1/16”) by 4. The resulting “X” dimension
you would use is 28-1/4”.
Determine the “X” dimension required for a particular application and subtract the amount of offset from this. From the example above: (Step 3)
2-1/2 inches offset was required and the “X” dimension as determined from the table was 3-17/32 inches. The difference between these two
figures is 1-1/32 inch. Simply add this tothe vertical distance from the starting point tothe finishing point (“Z” dimension in illustration above).
X
X
X
X
X
0
0
4
5
9
0
1
8
0
1
3
5
R
X
X
0
0
4
5
9
0
1
8
0
1
3
5
R
X
A
B
C
·OPEN-SIDE TYPE SLIPS OVER TUBE AT ANY POINT
·MAKES SMOOTH,TIGHT RADIUS BENDS UP TO 180° WITH MINIMUM EFFORT
·NO SCORING OR FLATTENING OF TUBING ·CALIBRATED TO SHOW ANGLE OF BEND ·WIDE HOOK GRIPS TUBE SECURELY
·FOR BENDING SOFT OR ANNEALED TUBING ONLY. COPPER TYPE K OR L, ALUMINUM, BRASS, STEEL AND UP TO .032” WALL (0.8 mm WALL) STAINLESS STEEL.
DIMENSIONAL BENDS
3. Proceed to bend desired angle
as indicated by calibrations on
forming wheel. Bends up to 180°
can be made in one smooth,
continuous motion.
1. To insert tubing into bender, place
handles at 180° and raise tube
holding hook out of way. Place
tubing in form wheel groove.
2. Place tube holding hook over
tubing and bring form shoe
handle into approximate right
angle position, engaging form
shoe over tubing. Note: “0”
mark on form wheel will be
even with front edge of form
shoe.
4. To remove tubing, pivot form shoe
handle to right angle with tubing,
disengaging forming shoe. Release
tube holding hook and remove tubing.
NOTE:Place oil occasionallyon handlepins and handle form shoe for easier bending. The form wheel groove should be kept dry and clean to prevent
tube slippage whilebending. Forhard to bend tubing, hold form wheel handlein vise. Lock vise jaws as near to form wheel as practical to make bend.
BENDS FROM LEFT
OF HOOK
A - FORM WHEEL
B-FORM SHOE HANDLE
C-FORM SHOE
BENDS FROM
RIGHT OF HOOK
Place tubing in bender as shown. Line up “X” dimension
mark with “R” mark on form shoehandle.
Place tubing in bender as shown. Line up “X” dimension
mark with edgeof form wheel.
SHOWN AT 90° BEND
Made in USA with US and globally sourced components. Products are designed, engineered and quality tested in the USA.
WARNING - Always wear approved eye protection.
0818 - 56452
TB12 Tube Bender, Lever Style Operating Instructions
1. Raise form handle. (Fig. 1)
2. Position tubing in groove as shown.
Also be sure that the tube is engaged
with the tube clamp.
3. Lower the form handle to position
shown. (Fig. 2)
4. Pull lever handle to direction of arrow
until the desired bend is obtained.
5. Degree of bend is indicated by mark on
form handle and shown in Fig. 2. Bends
up to 180° can be made in one sweep
of the handle.
This bender can be used for bending steel, stainless steel, copper, aluminum and other metal tubing of bending temper.
Extremely thin walled and/or hard temper tubing should be avoided.
BENDER SETUP
FIGURE 5
FORM WHEEL
FIGURE 3
USE MARK
X
FORM
HANDLE
X
X
X
X
TUBE
CLAMP
FORM
WHEEL
FORM
WHEEL
HANDLE
FORM HANDLE
FIGURE 1
TUBING
USE THIS
MARK FOR
DEGREES
OF BEND
PULL HANDLE THIS DIRECTION
FIGURE 2
FORM WHEEL
TUBE
CLAMP
FIGURE 4
X
FORM
HANDLE
USE THIS MARK
BENDER SETUP
FIGURE 5
FORM WHEEL
FIGURE 3
USE MARK
X
FORM
HANDLE
X
X
X
X
TUBE
CLAMP
FORM
WHEEL
FORM
WHEEL
HANDLE
FORM HANDLE
FIGURE 1
TUBING
USE THIS
MARK FOR
DEGREES
OF BEND
PULL HANDLE THIS DIRECTION
FIGURE 2
FORM WHEEL
TUBE
CLAMP
FIGURE 4
X
FORM
HANDLE
USE THIS MARK
BENDER SETUP
FIGURE 5
FORM WHEEL
FIGURE 3
USE MARK
X
FORM
HANDLE
X
X
X
X
TUBE
CLAMP
FORM
WHEEL
FORM
WHEEL
HANDLE
FORM HANDLE
FIGURE 1
TUBING
USE THIS
MARK FOR
DEGREES
OF BEND
PULL HANDLE THIS DIRECTION
FIGURE 2
FORM WHEEL
TUBE
CLAMP
FIGURE 4
X
FORM
HANDLE
USE THIS MARK
BENDER SETUP
FIGURE 5
FORM WHEEL
FIGURE 3
USE MARK
X
FORM
HANDLE
X
X
X
X
TUBE
CLAMP
FORM
WHEEL
FORM
WHEEL
HANDLE
FORM HANDLE
FIGURE 1
TUBING
USE THIS
MARK FOR
DEGREES
OF BEND
PULL HANDLE THIS DIRECTION
FIGURE 2
FORM WHEEL
TUBE
CLAMP
FIGURE 4
X
FORM
HANDLE
USE THIS MARK
REED MANUFACTURING COMPANY
1425 West Eighth St. Erie, PA 16502 USA
PHONE: 800-666-3691 or 814-452-3691 Fax: 800-456-1697 or 814-455-1697
www.reedmfgco.com

OFFSET BEND CALCULATOR
1 3- 7/8 1 2 1 1- 13/32 1 1- 5/32 1 1- 1/32
1- 1/8 4- 11/32 1- 1/8 2- 1/4 1- 1/8 1- 19/32 1- 1/8 1- 5/16 1- 1/8 1- 5/32
1- 1/4 4- 27/32 1- 1/4 2- 1/2 1- 1/4 1- 25/32 1- 1/4 1- 7/16 1- 1/4 1- 5/16
1- 3/8 5- 5/16 1- 3/8 2- 3/4 1- 3/8 1- 15/16 1- 3/8 1- 19/32 1- 3/8 1- 7/16
1- 1/2 5- 25/32 1- 1/2 3 1- 1/2 2- 1/8 1- 1/2 1- 23/32 1- 1/2 1- 9/16
1- 5/8 6- 9/32 1- 5/8 3- 1/4 1- 5/8 2- 5/16 1- 5/8 1- 7/8 1- 5/8 1- 11/16
1- 3/4 6- 3/4 1- 3/4 3- 1/2 1- 3/4 2- 15/32 1- 3/4 2- 1/32 1- 3/4 1- 13/16
1- 7/8 7- 1/4 1- 7/8 3- 3/4 1- 7/8 2- 21/32 1- 7/8 2- 5/32 1- 7/8 1- 15/16
2 7- 23/32 2 4 2 2- 13/16 2 2- 5/16 2 2- 1/16
2- 1/8 8- 7/32 2- 1/8 4- 1/4 2- 1/8 3 2- 1/8 2- 15/32 2- 1/8 2- 3/16
2- 1/4 8- 11/16 2- 1/4 4- 1/2 2- 1/4 3- 3/16 2- 1/4 2- 19/32 2- 1/4 2- 5/16
2- 3/8 9- 3/16 2- 3/8 4- 3/4 2- 3/8 3- 11/32 2- 3/8 2- 3/4 2- 3/8 2- 15/32
2- 1/2 9- 21/32 2- 1/2 5 2- 1/2 3- 17/32 2- 1/2 2- 7/8 2- 1/2 2- 19/32
2- 5/8 10- 5/32 2- 5/8 5- 1/4 2- 5/8 3- 23/32 2- 5/8 3- 1/32 2- 5/8 2- 23/32
2- 3/4 10- 5/8 2- 3/4 5- 1/2 2- 3/4 3- 7/8 2- 3/4 3- 3/16 2- 3/4 2- 27/32
2- 7/8 11- 3/32 2- 7/8 5- 3/4 2- 7/8 4- 1/16 2- 7/8 3- 5/16 2- 7/8 2- 31/32
3 11- 19/32 3 6 3 4- 1/4 3 3- 15/32 3 3- 3/32
3- 1/8 12- 1/16 3- 1/8 6- 1/4 3- 1/8 4- 13/32 3- 1/8 3- 19/32 3- 1/8 3- 7/32
3- 1/4 12- 9/16 3- 1/4 6- 1/2 3- 1/4 4- 19/32 3- 1/4 3- 3/4 3- 1/4 3- 3/8
3- 3/8 13- 1/32 3- 3/8 6- 3/4 3- 3/8 4- 25/32 3- 3/8 3- 29/32 3- 3/8 3- 1/2
3- 1/2 13- 17/32 3- 1/2 7 3- 1/2 4- 15/16 3- 1/2 4- 1/32 3- 1/2 3- 5/8
3- 5/8 14 3- 5/8 7- 1/4 3- 5/8 5- 1/8 3- 5/8 4- 3/16 3- 5/8 3- 3/4
3- 3/4 14- 1/2 3- 3/4 7- 1/2 3- 3/4 5- 5/16 3- 3/4 4- 11/32 3- 3/4 3- 7/8
3- 7/8 14- 31/32 3- 7/8 7- 3/4 3- 7/8 5- 15/32 3- 7/8 4- 15/32 3- 7/8 4
4 15- 15/32 4 8 4 5- 21/32 4 4- 5/8 4 4- 1/8
4- 1/8 15- 15/16 4- 1/8 8- 1/4 4- 1/8 5- 27/32 4- 1/8 4- 3/4 4- 1/8 4- 9/32
4- 1/4 16- 13/32 4- 1/4 8- 1/2 4- 1/4 6 4- 1/4 4- 29/32 4- 1/4 4- 13/32
4- 3/8 16- 29/32 4- 3/8 8- 3/4 4- 3/8 6- 3/16 4- 3/8 5- 1/16 4- 3/8 4- 17/32
4- 1/2 17- 3/8 4- 1/2 9 4- 1/2 6- 3/8 4- 1/2 5- 3/16 4- 1/2 4- 21/32
4- 5/8 17- 7/8 4- 5/8 9- 1/4 4- 5/8 6- 17/32 4- 5/8 5- 11/32 4- 5/8 4- 25/32
4- 3/4 18- 11/32 4- 3/4 9- 1/2 4- 3/4 6- 23/32 4- 3/4 5- 15/32 4- 3/4 4- 29/32
4- 7/8 18- 27/32 4- 7/8 9- 3/4 4- 7/8 6- 29/32 4- 7/8 5- 5/8 4- 7/8 5- 1/32
5 19- 5/16 5 10 5 7- 1/16 5 5- 25/32 5 5- 3/16
5- 1/8 19- 13/16 5- 1/8 10- 1/4 5- 1/8 7- 1/4 5- 1/8 5- 29/32 5- 1/8 5- 5/16
5- 1/4 20- 9/32 5- 1/4 10- 1/2 5- 1/4 7- 7/16 5- 1/4 6- 1/16 5- 1/4 5- 7/16
5- 3/8 20- 25/32 5- 3/8 10- 3/4 5- 3/8 7- 19/32 5- 3/8 6- 7/32 5- 3/8 5- 9/16
5- 1/2 21- 1/4 5- 1/2 11 5- 1/2 7- 25/32 5- 1/2 6- 11/32 5- 1/2 5- 11/16
5- 5/8 21- 23/32 5- 5/8 11- 1/4 5- 5/8 7- 31/32 5- 5/8 6- 1/2 5- 5/8 5- 27/32
5- 3/4 22- 7/32 5- 3/4 11- 1/2 5- 3/4 8- 1/8 5- 3/4 6- 5/8 5- 3/4 5- 31/32
5- 7/8 22- 11/16 5- 7/8 11- 3/4 5- 7/8 8- 5/16 5- 7/8 6- 25/32 5- 7/8 6- 3/32
6 23- 3/16 6 12 6 8- 15/32 6 6- 15/16 6 6- 7/32
ANGLE OF OFFSET 15° ANGLE OF OFFSET 30° ANGLE OF OFFSET 45° ANGLE OF OFFSET 60 ° ANGLE OF OFFSET 75°
AMOUNT OF OFFSET AMOUNT OF OFFSET AMOUNT OF OFFSET AMOUNT OF OFFSET AMOUNT OF OFFSET
(Y Dimension) (X Dimension) (Y Dimension) (X Dimension) (Y Dimension) (X Dimension) (Y Dimension) (X Dimension) (Y Dimension) (X Dimension)
(Inches) (Inches) (Inches) (Inches) (Inches) (Inches) (Inches) (Inches) (Inches) (Inches)
How to Figure Total Length ofTubing Required for 45° Offset Applications
OFFSET BENDS
OFFSET
DIMENSION
“Y”
“Z”
DIMENSION
NOISNEMID
RETNECOTRETNEC
DNEBFO
”X“
MARK B
MARK A
STEP 1 - Determine the total amount of offset required
(dimension “Y” in diagram) and angle of offset. Wherever
possible use 45° offset bends. This will enable you to figure
the total amount of tubing required for a given application
as explained in section on How to Figure Length of Tubing
Required for 45° Offset Applications.
STEP 2 - Figure the length of tube which is needed to meet
your offset requirements (“X” in dimension diagram) from table
below. For example: Say the amount of offset you require
(“Y” dimension, Step 1) is 2-1/2” and the offset angle is 45°.
Check the 45° column and find 2-1/2”. The figure next to this
is the amount of tubing required for the offset bend you want
(“X” dimension). Inthis case it’s 3-17/32”.
STEP 3 - Determine where you want the center of the offset
bend on the tube and make a reference mark (A).
Now measure off the “X” dimension (determined in Step 2,
example 3-17/32”) starting from the reference mark and
make a second mark (B). You are now ready to make the
bends.
STEP 4 - Align mark (A) with reference mark “R” on
bender and proceed with first bend. Then align (B) with
“R” mark and make second bend in proper direction.
NOTE:When the amount of offset exceeds what is listed
on the table, choose an offset from the table which is a
multiple of the offset you need. Look this up on the table
and multiply the “X” dimension by the multiple you used.
Example:For an offset of 20” for a 45° bend, look up
5” offset on the table in the 45° column and multiply “X”
dimension (7-1/16”) by 4. The resulting “X” dimension
you would use is 28-1/4”.
Determine the “X” dimension required for a particular application and subtract the amount of offset from this. From the example above: (Step 3)
2-1/2 inches offset was required and the “X” dimension as determined from the table was 3-17/32 inches. The difference between these two
figures is 1-1/32 inch. Simply add this tothe vertical distance from the starting point tothe finishing point (“Z” dimension in illustration above).
X
X
X
X
X
0
0
4
5
9
0
1
8
0
1
3
5
R
X
X
0
0
4
5
9
0
1
8
0
1
3
5
R
X
A
B
C
·OPEN-SIDE TYPE SLIPS OVER TUBE AT ANY POINT
·MAKES SMOOTH,TIGHT RADIUS BENDS UP TO 180° WITH MINIMUM EFFORT
·NO SCORING OR FLATTENING OF TUBING ·CALIBRATED TO SHOW ANGLE OF BEND ·WIDE HOOK GRIPS TUBE SECURELY
·FOR BENDING SOFT OR ANNEALED TUBING ONLY. COPPER TYPE K OR L, ALUMINUM, BRASS, STEEL AND UP TO .032” WALL (0.8 mm WALL) STAINLESS STEEL.
DIMENSIONAL BENDS
3. Proceed to bend desired angle
as indicated by calibrations on
forming wheel. Bends up to 180°
can be made in one smooth,
continuous motion.
1. To insert tubing into bender, place
handles at 180° and raise tube
holding hook out of way. Place
tubing in form wheel groove.
2. Place tube holding hook over
tubing and bring form shoe
handle into approximate right
angle position, engaging form
shoe over tubing. Note: “0”
mark on form wheel will be
even with front edge of form
shoe.
4. To remove tubing, pivot form shoe
handle to right angle with tubing,
disengaging forming shoe. Release
tube holding hook and remove tubing.
NOTE:Place oil occasionallyon handlepins and handle form shoe for easier bending. The form wheel groove should be kept dry and clean to prevent
tube slippage whilebending. Forhard to bend tubing, hold form wheel handlein vise. Lock vise jaws as near to form wheel as practical to make bend.
BENDS FROM LEFT
OF HOOK
A - FORM WHEEL
B-FORM SHOE HANDLE
C-FORM SHOE
BENDS FROM
RIGHT OF HOOK
Place tubing in bender as shown. Line up “X” dimension
mark with “R” mark on form shoehandle.
Place tubing in bender as shown. Line up “X” dimension
mark with edgeof form wheel.
SHOWN AT 90° BEND
Made in USA with US and globally sourced components. Products are designed, engineered and quality tested in the USA.
WARNING - Always wear approved eye protection.
OFFSET BEND CALCULATOR
1 3- 7/8 1 2 1 1- 13/32 1 1- 5/32 1 1- 1/32
1- 1/8 4- 11/32 1- 1/8 2- 1/4 1- 1/8 1- 19/32 1- 1/8 1- 5/16 1- 1/8 1- 5/32
1- 1/4 4- 27/32 1- 1/4 2- 1/2 1- 1/4 1- 25/32 1- 1/4 1- 7/16 1- 1/4 1- 5/16
1- 3/8 5- 5/16 1- 3/8 2- 3/4 1- 3/8 1- 15/16 1- 3/8 1- 19/32 1- 3/8 1- 7/16
1- 1/2 5- 25/32 1- 1/2 3 1- 1/2 2- 1/8 1- 1/2 1- 23/32 1- 1/2 1- 9/16
1- 5/8 6- 9/32 1- 5/8 3- 1/4 1- 5/8 2- 5/16 1- 5/8 1- 7/8 1- 5/8 1- 11/16
1- 3/4 6- 3/4 1- 3/4 3- 1/2 1- 3/4 2- 15/32 1- 3/4 2- 1/32 1- 3/4 1- 13/16
1- 7/8 7- 1/4 1- 7/8 3- 3/4 1- 7/8 2- 21/32 1- 7/8 2- 5/32 1- 7/8 1- 15/16
2 7- 23/32 2 4 2 2- 13/16 2 2- 5/16 2 2- 1/16
2- 1/8 8- 7/32 2- 1/8 4- 1/4 2- 1/8 3 2- 1/8 2- 15/32 2- 1/8 2- 3/16
2- 1/4 8- 11/16 2- 1/4 4- 1/2 2- 1/4 3- 3/16 2- 1/4 2- 19/32 2- 1/4 2- 5/16
2- 3/8 9- 3/16 2- 3/8 4- 3/4 2- 3/8 3- 11/32 2- 3/8 2- 3/4 2- 3/8 2- 15/32
2- 1/2 9- 21/32 2- 1/2 5 2- 1/2 3- 17/32 2- 1/2 2- 7/8 2- 1/2 2- 19/32
2- 5/8 10- 5/32 2- 5/8 5- 1/4 2- 5/8 3- 23/32 2- 5/8 3- 1/32 2- 5/8 2- 23/32
2- 3/4 10- 5/8 2- 3/4 5- 1/2 2- 3/4 3- 7/8 2- 3/4 3- 3/16 2- 3/4 2- 27/32
2- 7/8 11- 3/32 2- 7/8 5- 3/4 2- 7/8 4- 1/16 2- 7/8 3- 5/16 2- 7/8 2- 31/32
3 11- 19/32 3 6 3 4- 1/4 3 3- 15/32 3 3- 3/32
3- 1/8 12- 1/16 3- 1/8 6- 1/4 3- 1/8 4- 13/32 3- 1/8 3- 19/32 3- 1/8 3- 7/32
3- 1/4 12- 9/16 3- 1/4 6- 1/2 3- 1/4 4- 19/32 3- 1/4 3- 3/4 3- 1/4 3- 3/8
3- 3/8 13- 1/32 3- 3/8 6- 3/4 3- 3/8 4- 25/32 3- 3/8 3- 29/32 3- 3/8 3- 1/2
3- 1/2 13- 17/32 3- 1/2 7 3- 1/2 4- 15/16 3- 1/2 4- 1/32 3- 1/2 3- 5/8
3- 5/8 14 3- 5/8 7- 1/4 3- 5/8 5- 1/8 3- 5/8 4- 3/16 3- 5/8 3- 3/4
3- 3/4 14- 1/2 3- 3/4 7- 1/2 3- 3/4 5- 5/16 3- 3/4 4- 11/32 3- 3/4 3- 7/8
3- 7/8 14- 31/32 3- 7/8 7- 3/4 3- 7/8 5- 15/32 3- 7/8 4- 15/32 3- 7/8 4
4 15- 15/32 4 8 4 5- 21/32 4 4- 5/8 4 4- 1/8
4- 1/8 15- 15/16 4- 1/8 8- 1/4 4- 1/8 5- 27/32 4- 1/8 4- 3/4 4- 1/8 4- 9/32
4- 1/4 16- 13/32 4- 1/4 8- 1/2 4- 1/4 6 4- 1/4 4- 29/32 4- 1/4 4- 13/32
4- 3/8 16- 29/32 4- 3/8 8- 3/4 4- 3/8 6- 3/16 4- 3/8 5- 1/16 4- 3/8 4- 17/32
4- 1/2 17- 3/8 4- 1/2 9 4- 1/2 6- 3/8 4- 1/2 5- 3/16 4- 1/2 4- 21/32
4- 5/8 17- 7/8 4- 5/8 9- 1/4 4- 5/8 6- 17/32 4- 5/8 5- 11/32 4- 5/8 4- 25/32
4- 3/4 18- 11/32 4- 3/4 9- 1/2 4- 3/4 6- 23/32 4- 3/4 5- 15/32 4- 3/4 4- 29/32
4- 7/8 18- 27/32 4- 7/8 9- 3/4 4- 7/8 6- 29/32 4- 7/8 5- 5/8 4- 7/8 5- 1/32
5 19- 5/16 5 10 5 7- 1/16 5 5- 25/32 5 5- 3/16
5- 1/8 19- 13/16 5- 1/8 10- 1/4 5- 1/8 7- 1/4 5- 1/8 5- 29/32 5- 1/8 5- 5/16
5- 1/4 20- 9/32 5- 1/4 10- 1/2 5- 1/4 7- 7/16 5- 1/4 6- 1/16 5- 1/4 5- 7/16
5- 3/8 20- 25/32 5- 3/8 10- 3/4 5- 3/8 7- 19/32 5- 3/8 6- 7/32 5- 3/8 5- 9/16
5- 1/2 21- 1/4 5- 1/2 11 5- 1/2 7- 25/32 5- 1/2 6- 11/32 5- 1/2 5- 11/16
5- 5/8 21- 23/32 5- 5/8 11- 1/4 5- 5/8 7- 31/32 5- 5/8 6- 1/2 5- 5/8 5- 27/32
5- 3/4 22- 7/32 5- 3/4 11- 1/2 5- 3/4 8- 1/8 5- 3/4 6- 5/8 5- 3/4 5- 31/32
5- 7/8 22- 11/16 5- 7/8 11- 3/4 5- 7/8 8- 5/16 5- 7/8 6- 25/32 5- 7/8 6- 3/32
6 23- 3/16 6 12 6 8- 15/32 6 6- 15/16 6 6- 7/32
ANGLE OF OFFSET 15° ANGLE OF OFFSET 30° ANGLE OF OFFSET 45° ANGLE OF OFFSET 60 ° ANGLE OF OFFSET 75°
AMOUNT OF OFFSET AMOUNT OF OFFSET AMOUNT OF OFFSET AMOUNT OF OFFSET AMOUNT OF OFFSET
(Y Dimension) (X Dimension) (Y Dimension) (X Dimension) (Y Dimension) (X Dimension) (Y Dimension) (X Dimension) (Y Dimension) (X Dimension)
(Inches) (Inches) (Inches) (Inches) (Inches) (Inches) (Inches) (Inches) (Inches) (Inches)
How to Figure Total Length ofTubing Required for 45° Offset Applications
OFFSET BENDS
OFFSET
DIMENSION
“Y”
“Z”
DIMENSION
NOISNEMID
RETNECOTRETNEC
DNEBFO
”X“
MARK B
MARK A
STEP 1 - Determine the total amount of offset required
(dimension “Y” in diagram) and angle of offset. Wherever
possible use 45° offset bends. This will enable you to figure
the total amount of tubing required for a given application
as explained in section on How to Figure Length of Tubing
Required for 45° Offset Applications.
STEP 2 - Figure the length of tube which is needed to meet
your offset requirements (“X” in dimension diagram) from table
below. For example: Say the amount of offset you require
(“Y” dimension, Step 1) is 2-1/2” and the offset angle is 45°.
Check the 45° column and find 2-1/2”.The figure next to this
is the amount of tubing required for the offset bend you want
(“X” dimension). Inthis case it’s 3-17/32”.
STEP 3 - Determine where you want the center of the offset
bend on the tube and make a reference mark (A).
Now measure off the “X” dimension (determined in Step 2,
example 3-17/32”) starting from the reference mark and
make a second mark (B). You are now ready to make the
bends.
STEP 4 - Align mark (A) with reference mark “R” on
bender and proceed with first bend. Then align (B) with
“R” mark and make second bend in proper direction.
NOTE:When the amount of offset exceeds what is listed
on the table, choose an offset from the table which is a
multiple of the offset you need. Look this up on the table
and multiply the “X” dimension by the multiple you used.
Example: For an offset of 20” for a 45° bend, look up
5” offset on the table in the 45° column and multiply “X”
dimension (7-1/16”) by 4. The resulting “X” dimension
you would use is 28-1/4”.
Determine the “X” dimension required for a particular application and subtract the amount of offset from this. From the example above: (Step 3)
2-1/2 inches offset was required and the “X” dimension as determined from the table was 3-17/32 inches. The difference between these two
figures is 1-1/32 inch. Simply add this tothe vertical distance from the starting point tothe finishing point (“Z” dimension in illustration above).
X
X
X
X
X
0
0
4
5
9
0
1
8
0
1
3
5
R
X
X
0
0
4
5
9
0
1
8
0
1
3
5
R
X
A
B
C
·OPEN-SIDE TYPE SLIPS OVER TUBE AT ANY POINT
·MAKES SMOOTH,TIGHT RADIUS BENDS UP TO 180° WITH MINIMUM EFFORT
·NO SCORING OR FLATTENING OF TUBING ·CALIBRATED TO SHOW ANGLE OF BEND ·WIDE HOOK GRIPS TUBE SECURELY
·FOR BENDING SOFT OR ANNEALED TUBING ONLY. COPPER TYPE K OR L, ALUMINUM, BRASS, STEEL AND UP TO .032” WALL (0.8 mm WALL) STAINLESS STEEL.
DIMENSIONAL BENDS
3. Proceed to bend desired angle
as indicated by calibrations on
forming wheel. Bends up to 180°
can be made in one smooth,
continuous motion.
1. To insert tubing into bender, place
handles at 180° and raise tube
holding hook out of way. Place
tubing in form wheel groove.
2. Place tube holding hook over
tubing and bring form shoe
handle into approximate right
angle position, engaging form
shoe over tubing. Note: “0”
mark on form wheel will be
even with front edge of form
shoe.
4. To remove tubing, pivot form shoe
handle to right angle with tubing,
disengaging forming shoe. Release
tube holding hook and remove tubing.
NOTE:Place oil occasionallyon handlepins and handle form shoe for easier bending. The form wheel groove should be kept dry and clean to prevent
tube slippage whilebending. Forhard to bend tubing, hold form wheel handlein vise. Lock vise jaws as near to form wheel as practical to make bend.
BENDS FROM LEFT
OF HOOK
A - FORM WHEEL
B-FORM SHOE HANDLE
C-FORM SHOE
BENDS FROM
RIGHT OF HOOK
Place tubing in bender as shown. Line up “X” dimension
mark with “R” mark on form shoehandle.
Place tubing in bender as shown. Line up “X” dimension
mark with edgeof form wheel.
SHOWN AT 90° BEND
Made in USA with US and globally sourced components. Products are designed, engineered and quality tested in the USA.
WARNING - Always wear approved eye protection.
DIMENSIONAL BENDSOFFSET BENDS
OFFSET BEND CALCULATOR
1 3- 7/8 1 2 1 1- 13/32 1 1- 5/32 1 1- 1/32
1- 1/8 4- 11/32 1- 1/8 2- 1/4 1- 1/8 1- 19/32 1- 1/8 1- 5/16 1- 1/8 1- 5/32
1- 1/4 4- 27/32 1- 1/4 2- 1/2 1- 1/4 1- 25/32 1- 1/4 1- 7/16 1- 1/4 1- 5/16
1- 3/8 5- 5/16 1- 3/8 2- 3/4 1- 3/8 1- 15/16 1- 3/8 1- 19/32 1- 3/8 1- 7/16
1- 1/2 5- 25/32 1- 1/2 3 1- 1/2 2- 1/8 1- 1/2 1- 23/32 1- 1/2 1- 9/16
1- 5/8 6- 9/32 1- 5/8 3- 1/4 1- 5/8 2- 5/16 1- 5/8 1- 7/8 1- 5/8 1- 11/16
1- 3/4 6- 3/4 1- 3/4 3- 1/2 1- 3/4 2- 15/32 1- 3/4 2- 1/32 1- 3/4 1- 13/16
1- 7/8 7- 1/4 1- 7/8 3- 3/4 1- 7/8 2- 21/32 1- 7/8 2- 5/32 1- 7/8 1- 15/16
2 7- 23/32 2 4 2 2- 13/16 2 2- 5/16 2 2- 1/16
2- 1/8 8- 7/32 2- 1/8 4- 1/4 2- 1/8 3 2- 1/8 2- 15/32 2- 1/8 2- 3/16
2- 1/4 8- 11/16 2- 1/4 4- 1/2 2- 1/4 3- 3/16 2- 1/4 2- 19/32 2- 1/4 2- 5/16
2- 3/8 9- 3/16 2- 3/8 4- 3/4 2- 3/8 3- 11/32 2- 3/8 2- 3/4 2- 3/8 2- 15/32
2- 1/2 9- 21/32 2- 1/2 5 2- 1/2 3- 17/32 2- 1/2 2- 7/8 2- 1/2 2- 19/32
2- 5/8 10- 5/32 2- 5/8 5- 1/4 2- 5/8 3- 23/32 2- 5/8 3- 1/32 2- 5/8 2- 23/32
2- 3/4 10- 5/8 2- 3/4 5- 1/2 2- 3/4 3- 7/8 2- 3/4 3- 3/16 2- 3/4 2- 27/32
2- 7/8 11- 3/32 2- 7/8 5- 3/4 2- 7/8 4- 1/16 2- 7/8 3- 5/16 2- 7/8 2- 31/32
3 11- 19/32 3 6 3 4- 1/4 3 3- 15/32 3 3- 3/32
3- 1/8 12- 1/16 3- 1/8 6- 1/4 3- 1/8 4- 13/32 3- 1/8 3- 19/32 3- 1/8 3- 7/32
3- 1/4 12- 9/16 3- 1/4 6- 1/2 3- 1/4 4- 19/32 3- 1/4 3- 3/4 3- 1/4 3- 3/8
3- 3/8 13- 1/32 3- 3/8 6- 3/4 3- 3/8 4- 25/32 3- 3/8 3- 29/32 3- 3/8 3- 1/2
3- 1/2 13- 17/32 3- 1/2 7 3- 1/2 4- 15/16 3- 1/2 4- 1/32 3- 1/2 3- 5/8
3- 5/8 14 3- 5/8 7- 1/4 3- 5/8 5- 1/8 3- 5/8 4- 3/16 3- 5/8 3- 3/4
3- 3/4 14- 1/2 3- 3/4 7- 1/2 3- 3/4 5- 5/16 3- 3/4 4- 11/32 3- 3/4 3- 7/8
3- 7/8 14- 31/32 3- 7/8 7- 3/4 3- 7/8 5- 15/32 3- 7/8 4- 15/32 3- 7/8 4
4 15- 15/32 4 8 4 5- 21/32 4 4- 5/8 4 4- 1/8
4- 1/8 15- 15/16 4- 1/8 8- 1/4 4- 1/8 5- 27/32 4- 1/8 4- 3/4 4- 1/8 4- 9/32
4- 1/4 16- 13/32 4- 1/4 8- 1/2 4- 1/4 6 4- 1/4 4- 29/32 4- 1/4 4- 13/32
4- 3/8 16- 29/32 4- 3/8 8- 3/4 4- 3/8 6- 3/16 4- 3/8 5- 1/16 4- 3/8 4- 17/32
4- 1/2 17- 3/8 4- 1/2 9 4- 1/2 6- 3/8 4- 1/2 5- 3/16 4- 1/2 4- 21/32
4- 5/8 17- 7/8 4- 5/8 9- 1/4 4- 5/8 6- 17/32 4- 5/8 5- 11/32 4- 5/8 4- 25/32
4- 3/4 18- 11/32 4- 3/4 9- 1/2 4- 3/4 6- 23/32 4- 3/4 5- 15/32 4- 3/4 4- 29/32
4- 7/8 18- 27/32 4- 7/8 9- 3/4 4- 7/8 6- 29/32 4- 7/8 5- 5/8 4- 7/8 5- 1/32
5 19- 5/16 5 10 5 7- 1/16 5 5- 25/32 5 5- 3/16
5- 1/8 19- 13/16 5- 1/8 10- 1/4 5- 1/8 7- 1/4 5- 1/8 5- 29/32 5- 1/8 5- 5/16
5- 1/4 20- 9/32 5- 1/4 10- 1/2 5- 1/4 7- 7/16 5- 1/4 6- 1/16 5- 1/4 5- 7/16
5- 3/8 20- 25/32 5- 3/8 10- 3/4 5- 3/8 7- 19/32 5- 3/8 6- 7/32 5- 3/8 5- 9/16
5- 1/2 21- 1/4 5- 1/2 11 5- 1/2 7- 25/32 5- 1/2 6- 11/32 5- 1/2 5- 11/16
5- 5/8 21- 23/32 5- 5/8 11- 1/4 5- 5/8 7- 31/32 5- 5/8 6- 1/2 5- 5/8 5- 27/32
5- 3/4 22- 7/32 5- 3/4 11- 1/2 5- 3/4 8- 1/8 5- 3/4 6- 5/8 5- 3/4 5- 31/32
5- 7/8 22- 11/16 5- 7/8 11- 3/4 5- 7/8 8- 5/16 5- 7/8 6- 25/32 5- 7/8 6- 3/32
6 23- 3/16 6 12 6 8- 15/32 6 6- 15/16 6 6- 7/32
ANGLE OF OFFSET 15° ANGLE OF OFFSET 30° ANGLE OF OFFSET 45° ANGLE OF OFFSET 60 ° ANGLE OF OFFSET 75°
AMOUNT OF OFFSET AMOUNT OF OFFSET AMOUNT OF OFFSET AMOUNT OF OFFSET AMOUNT OF OFFSET
(Y Dimension) (X Dimension) (Y Dimension) (X Dimension) (Y Dimension) (X Dimension) (Y Dimension) (X Dimension) (Y Dimension) (X Dimension)
(Inches) (Inches) (Inches) (Inches) (Inches) (Inches) (Inches) (Inches) (Inches) (Inches)
How to Figure Total Length ofTubing Required for 45° Offset Applications
OFFSET BENDS
OFFSET
DIMENSION
“Y”
“Z”
DIMENSION
NOISNEMID
RETNECOTRETNEC
DNEBFO
”X“
MARK B
MARK A
STEP 1 - Determine the total amount of offset required
(dimension “Y” in diagram) and angle of offset. Wherever
possible use 45° offset bends. This will enable you to figure
the total amount of tubing required for a given application
as explained in section on How to Figure Length of Tubing
Required for 45° Offset Applications.
STEP 2 - Figure the length of tube which is needed to meet
your offset requirements (“X” in dimension diagram) from table
below. For example: Say the amount of offset you require
(“Y” dimension, Step 1) is 2-1/2” and the offset angle is 45°.
Check the 45° column and find 2-1/2”. The figure next to this
is the amount of tubing required for the offset bend you want
(“X” dimension). Inthis case it’s 3-17/32”.
STEP 3 - Determine where you want the center of the offset
bend on the tube and make a reference mark (A).
Now measure off the “X” dimension (determined in Step 2,
example 3-17/32”) starting from the reference mark and
make a second mark (B). You are now ready to make the
bends.
STEP 4 - Align mark (A) with reference mark “R” on
bender and proceed with first bend. Then align (B) with
“R” mark and make second bend in proper direction.
NOTE:When the amount of offset exceeds what is listed
on the table, choose an offset from the table which is a
multiple of the offset you need. Look this up on the table
and multiply the “X” dimension by the multiple you used.
Example:For an offset of 20” for a 45° bend, look up
5” offset on the table in the 45° column and multiply “X”
dimension (7-1/16”) by 4. The resulting “X” dimension
you would use is 28-1/4”.
Determine the “X” dimension required for a particular application and subtract the amount of offset from this. From the example above: (Step 3)
2-1/2 inches offset was required and the “X” dimension as determined from the table was 3-17/32 inches. The difference between these two
figures is 1-1/32 inch. Simply add this tothe vertical distance from the starting point tothe finishing point (“Z” dimension in illustration above).
X
X
X
X
X
0
0
4
5
9
0
1
8
0
1
3
5
R
X
X
0
0
4
5
9
0
1
8
0
1
3
5
R
X
A
B
C
·OPEN-SIDE TYPE SLIPS OVER TUBE AT ANY POINT
·MAKES SMOOTH,TIGHT RADIUS BENDS UP TO 180° WITH MINIMUM EFFORT
·NO SCORING OR FLATTENING OF TUBING ·CALIBRATED TO SHOW ANGLE OF BEND ·WIDE HOOK GRIPS TUBE SECURELY
·FOR BENDING SOFT OR ANNEALED TUBING ONLY. COPPER TYPE K OR L, ALUMINUM, BRASS, STEEL AND UP TO .032” WALL (0.8 mm WALL) STAINLESS STEEL.
DIMENSIONAL BENDS
3. Proceed to bend desired angle
as indicated by calibrations on
forming wheel. Bends up to 180°
can be made in one smooth,
continuous motion.
1. To insert tubing into bender, place
handles at 180° and raise tube
holding hook out of way. Place
tubing in form wheel groove.
2. Place tube holding hook over
tubing and bring form shoe
handle into approximate right
angle position, engaging form
shoe over tubing. Note: “0”
mark on form wheel will be
even with front edge of form
shoe.
4. To remove tubing, pivot form shoe
handle to right angle with tubing,
disengaging forming shoe. Release
tube holding hook and remove tubing.
NOTE:Place oil occasionallyon handlepins and handle form shoe for easier bending. The form wheel groove should be kept dry and clean to prevent
tube slippage whilebending. Forhard to bend tubing, hold form wheel handlein vise. Lock vise jaws as near to form wheel as practical to make bend.
BENDS FROM LEFT
OF HOOK
A - FORM WHEEL
B-FORM SHOE HANDLE
C-FORM SHOE
BENDS FROM
RIGHT OF HOOK
Place tubing in bender as shown. Line up “X” dimension
mark with “R” mark on form shoehandle.
Place tubing in bender as shown. Line up “X” dimension
mark with edgeof form wheel.
SHOWN AT 90° BEND
Made in USA with US and globally sourced components. Products are designed, engineered and quality tested in the USA.
WARNING - Always wear approved eye protection.
BENDER SETUP
FIGURE 5
FORM WHEEL
FIGURE 3
USE MARK
X
FORM
HANDLE
X
X
X
X
TUBE
CLAMP
FORM
WHEEL
FORM
WHEEL
HANDLE
FORM HANDLE
FIGURE 1
TUBING
USE THIS
MARK FOR
DEGREES
OF BEND
PULL HANDLE THIS DIRECTION
FIGURE 2
FORM WHEEL
TUBE
CLAMP
FIGURE 4
X
FORM
HANDLE
USE THIS MARK
Place tubing bender
as shown. Line up
“X” dimension mark
with edge of form
wheel.
0818 - 56452
Other REED Tools manuals
Popular Tools manuals by other brands

Milwaukee
Milwaukee M12 TRAPSNAKE 49-16-3574 Operator's manual
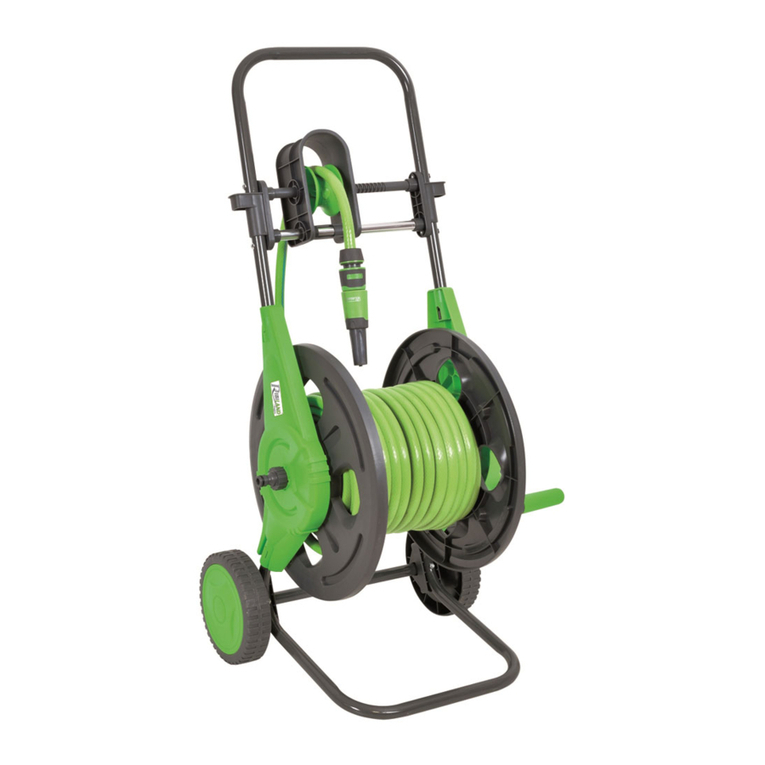
Ribimex
Ribimex Ribiland PRA/DB.1103 User and maintenance manual

Omer
Omer HR23 M8 Use, maintenance and spare parts manual
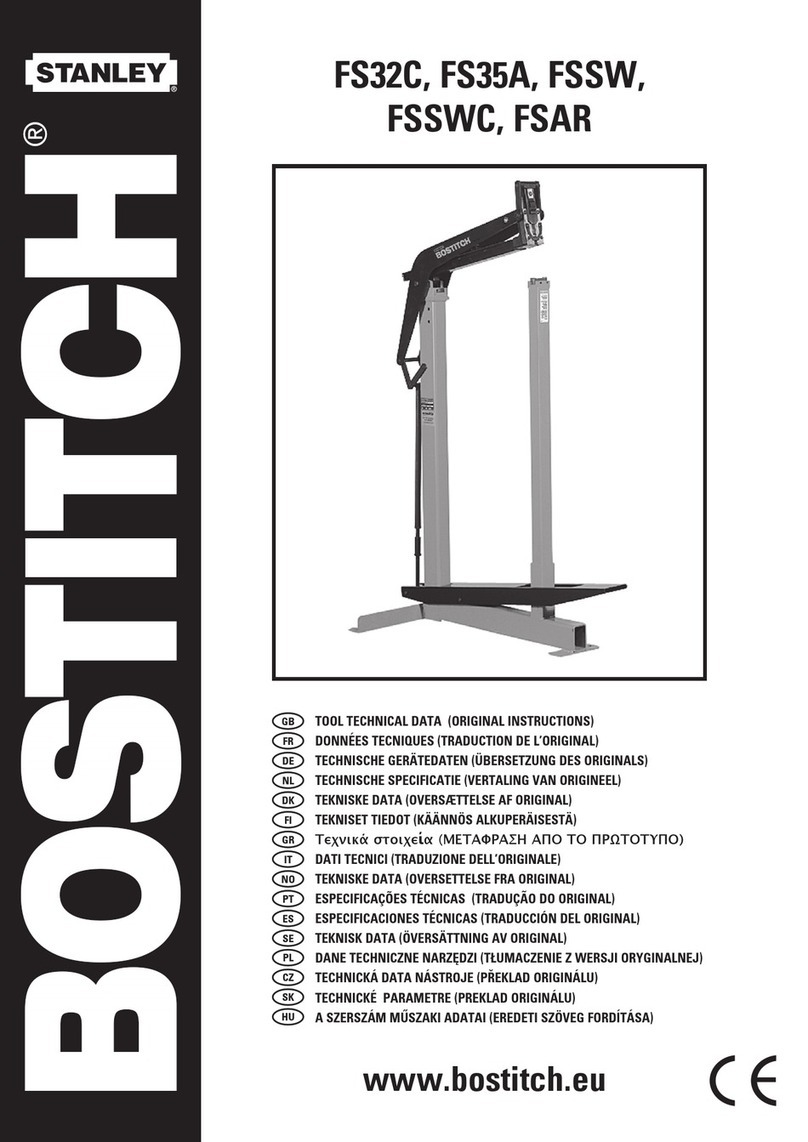
Bostitch
Bostitch FS32C Original instructions

Goodson
Goodson HH-200 instructions

Applifast
Applifast HOWMET AEROSPACE 507 instruction manual