Resol DeltaTherm HC mini User manual

DeltaTherm®HC mini
*11205773*
11205773
Thank you for buying this RESOL product.
Please read this manual carefully to get the best performance from this unit. Please keep this manual carefully. www.resol.com
Manual
en
Heating controller
Manual for the
specialised craftsman
Mounting
Connection
Operation
Troubleshooting
Application examples
Adjust your heating via app
beginning with version 1.02

en
2
Subject to technical change. Errors excepted.
© 20211103_11205773_DeltaTherm_HC_mini.monen.indd
Safety advice
Please pay attention to the following safety advice in order to avoid danger and
damage to people and property.
Danger of electric shock:
• When carrying out works, the device must rst of all be disconnected from the
mains.
• It must be possible to disconnect the device from the mains at any time.
• Do not use the device if it is visibly damaged!
The device must not be used by children or persons with reduced physical, sensory
or mental abilities or without any experience and knowledge. Make sure that child-
ren do not play with the device!
Only connect accessories authorised by the manufacturer to the device.
Make sure that the housing is properly closed before commissioning the device.
Set the code to the customer code before handing over the controller to the
customer.
Target group
These instructions are exclusively addressed to authorised skilled personnel.
Only qualied electricians are allowed to carry out electrical works.
Initial commissioning must be effected by authorised skilled personnel.
Authorised skilled personnel are persons who have theoretical knowledge and ex-
perience with the installation, commissioning, operation, maintenance, etc. of elec-
tric/electronic devices and hydraulic systems and who have knowledge of relevant
standards and directives.
Instructions
Attention must be paid to the valid local standards, regulations and directives!
Information about the product
Proper usage
The controller is designed for use in heating systems in compliance with the tech-
nical data specied in this manual.
Any use beyond this is considered improper.
Proper usage also includes compliance with the specications given in this manual.
Improper use excludes all liability claims.
Note:
Strong electromagnetic elds can impair the function of the device.
ÎMake sure the device as well as the system are not exposed to strong
electromagnetic elds.
EU Declaration of conformity
The product complies with the relevant directives and is therefore la-
belled with the CE mark.The Declaration of Conformity is available upon
request, please contact the manufacturer.
Scope of delivery
The scope of delivery of this product is indicated on the packaging label.
Storage and transport
Store the product at an ambient temperature of 0 … 40 °C and in dry interior
rooms only.
Transport the product in its original packaging only.
Cleaning
Clean the product with a dry cloth. Do not use aggressive cleaning uids.
Data security
We recommend regular backups of the data stored on the device via MicroSD card.

en
3
Decommissioning
1. Disconnect the device from the power supply.
2. Dismount the device.
Disposal
• Dispose of the packaging in an environmentally sound manner.
• At the end of its working life,the product must not be disposed of as urban waste.
Old appliances must be disposed of by an authorised body in an environmentally
sound manner. Upon request we will take back your old appliances bought from
us and guarantee an environmentally sound disposal of the devices.
Description of symbols
Warnings are indicated with a warning symbol!
Signal words describe the danger that may occur, when it is not avoided.
WARNING means that injury, possibly life-threatening injury,can occur.
ÎIt is indicated how to avoid the danger described.
ATTENTION means that damage to the appliance can occur.
ÎIt is indicated how to avoid the danger described.
Note
Notes are indicated with an information symbol.
ÎTexts marked with an arrow indicate one single instruction step to be carried
out.
1. Texts marked with numbers indicate several successive instruction steps to be
carried out.

en
4
DeltaTherm®HC mini Heating controller
The DeltaTherm®HC mini offers a compact and user-friendly solution for simple
heating systems. It can control a weather-compensated heating circuit and its back-
up heating demand. Additionally, there’s a choice of 5 different operating modes, a
boiler protection option and a night correction. Due to the commissioning menu
and the 4 pre-congured basic systems, conguration is quick and easy. The chimney
sweeper function and the holiday mode can be activated by pressing a single button.
Contents
1 Overview........................................................................................................5
2 Installation.....................................................................................................6
2.1 Mounting....................................................................................................................................6
2.2 Electrical connection...............................................................................................................8
2.3 Data communication / Bus................................................................................................... 10
2.4 MicroSD card slot................................................................................................................. 10
3 Operation and function..............................................................................11
3.1 Buttons and adjustment dial............................................................................................... 11
3.2 Microbutton for chimney sweeper function / screed drying and holiday mode...... 11
3.3 Control lamp ......................................................................................................................... 11
3.4 Selecting menu points and adjusting values .................................................................... 11
4 Commissioning ...........................................................................................16
4.1 Schemes with basic settings ............................................................................................... 17
4.2 ErP temperature controls classes ..................................................................................... 18
5 Menu structure............................................................................................23
6 Main menu...................................................................................................23
7 Status menu ................................................................................................24
7.1 Heating.................................................................................................................................... 24
7.2 Meas./ Balance values ........................................................................................................... 24
7.3 Messages................................................................................................................................. 24
8 Heating ........................................................................................................25
8.1 Shared relays.......................................................................................................................... 25
8.2 Heating circuit ....................................................................................................................... 27
8.3 Screed drying......................................................................................................................... 33
9 Basic settings...............................................................................................34
10 SD card .......................................................................................................35
11 Manual mode ..............................................................................................36
12 User code ....................................................................................................36
13 In- / Outputs .................................................................................................37
13.1 Inputs....................................................................................................................................... 37
13.2 Outputs................................................................................................................................... 37
14 Troubleshooting ..........................................................................................39
15 Accessories..................................................................................................41
15.1 Sensors and measuring instruments................................................................................. 41
15.2 VBus®accessories................................................................................................................. 41
16 Index.............................................................................................................42

en
5
1 Overview
• 4 pre-congured basic systems
• 12 pre-programmed schemes for the temperature controls classes II, III,V,VI,VII
and VIII
• 4 relay outputs (incl. 1 extra-low voltage relay)
• 5 inputs for Pt1000 temperature sensors
• 5 operating modes, boiler protection, room thermostat and night correction
• Chimney sweeper function, screed drying function and holiday mode via microbuttons
• Holiday mode, chimney sweeper function and screed drying function via microbuttons
• Data logging, storing, easy transfer of controller adjustments prepared and
rmware updates via SD card
• Modulating heating control with 0-10V boiler control
• Weather-compensated control with room inuence or demand-based room
control with up to 3 room temperature sensors
• Remote access with a room control unit or the VBus®Touch HC App
Technical data
Inputs: 5 inputs for Pt1000 temperature sensors (1 of them can be converted to
Switch and one of them to RTA remote control or BAS operating mode switch)
Outputs: 3semiconductor relays, 1 potential-free extra-low voltage relay,
1 PWM output, 1 0-10 V output
PWM frequency: 512 Hz
PWM voltage: 10.8 V
Switching capacity:
1 (1) A 240 V~ (semiconductor relay)
1 (1) A 30 V⎓(potential-free relay)
Total switching capacity: 3 A 240 V~
Power supply: 100 – 240 V~ (50 – 60 Hz)
Supply connection: type X attachment
Standby: 0.62W
Temperature controls class: VIII
Energy efciency contribution: 5 %
Mode of operation: type 1.B.C.Y action
Rated impulse voltage: 2.5 kV
Data interface: VBus®, MicroSD card slot
VBus®current supply: 60 mA
Functions: weather-compensated heating circuit control, backup heating,
room thermostat, chimney sweeper function, screed drying function, holiday mode
Housing: plastic, PC-ABS and PMMA
Mounting: wall mounting, also suitable for mounting into patch panels
Indication / Display: full graphic display, control lamp (Lightwheel®)
Operation: 4 buttons at the front and 1 Lightwheel®
Protection type: IP 20 / DIN EN 60529
Protection class: I
Ambient temperature: 0 … 40 °C
Degree of pollution: 2
Fuse: T4A
Maximum altitude: 2000 m above MSL
Dimensions: 110 x 166 x 47 mm
Upper fastening
Lower fastening
Dimensions and minimum distances
110
166
130
47

en
6
Installation Commissioning Settings Data communication Troubleshooting
2 Installation
2.1 Mounting
WARNING! Electric shock!
Upon opening the housing, live parts are exposed!
ÎAlways disconnect the controller from power supply be-
fore opening the housing!
Note:
Strong electromagnetic elds can impair the function of the device.
ÎMake sure the device as well as the system are not exposed to strong
electromagnetic elds.
The unit must only be located in dry interior rooms.
If the device is not equipped with a mains connection cable and a plug, the device
must additionally be supplied from a double pole switch with contact gap of at least
3 mm.
Please pay attention to separate routing of sensor cables and mains cables.
In order to mount the device to the wall, carry out the following steps:
1. Unscrew the crosshead screw from the cover and remove it along with the
cover from the housing.
2. Mark the upper fastening point on the wall. Drill and fasten the enclosed wall
plug and screw leaving the head protruding.
3. Hang the housing from the upper fastening point and mark the lower fastening
point (centres 130 mm).
4. Insert lower wall plug.
5. Fasten the housing to the wall with the lower fastening screw and tighten.
6. Carry out the electrical wiring in accordance with the terminal allocation (see
page page 8).
7. Put the cover on the housing.
8. Attach with the fastening screw.

en
Installation
7
CommissioningSettingsTroubleshooting Data communication
12
4
3
56

en
8
Installation Commissioning Settings Data communication Troubleshooting
potential-free extra-low
voltage relay
sensor terminals /
terminals for switch
and remote control
protective conductor
common terminal block (PE)
neutral conductor
common terminal block
PWM / 0-10 V
terminals
VBus®
2.2 Electrical connection
WARNING! Electric shock!
Upon opening the housing, live parts are exposed!
ÎAlways disconnect the controller from power supply
before opening the housing!
ATTENTION! ESD damage!
Electrostatic discharge can lead to damage to electronic components!
ÎTake care to discharge properly before touching the
inside of the device!To do so, touch a grounded sur-
face such as a radiator or tap!
Note:
Connecting the device to the power supply must always be the last step
of the installation!
Note:
The pump speed must be set to 100% when auxiliary relays or valves are
connected.
Note:
It must be possible to disconnect the device from the mains at any time.
ÎInstall the mains plug such that it is accessible at any time.
ÎIf this is not possible, install a switch that can be accessed.
If the mains cable is damaged, it must be replaced by a special connection
cable which is available from the manufacturer or its customer service.
Do not use the device if it is visibly damaged!
Depending on the product version, cables are already connected to the device. If
that is not the case, please proceed as follows:
Attach exible cables to the housing with the enclosed strain relief and the corre-
sponding screws.
The controller is equipped with 4 relays in total to which loads such as pumps,
valves, etc. can be connected:
Relays 1 … 3 are semiconductor relays, designed for pump speed control:
Conductor R1 … R3
Neutral conductor N (common terminal block)
Protective earth conductor ⏚(common terminal block)
Relay 4 is a potential-free extra-low voltage relay:
Connections to the R4 terminals can be made with either polarity. sensor ground common terminal block
Connect the temperature sensors (S1 to S5) to the terminals S1… S5 and GND
(either polarity).
The cables carry extra-low voltage and must not run together in a cable conduit
with cables carrying a voltage higher than 50V (please pay attention to the valid di-
rectives).The cross section must be at least 1.5 mm2and the cables can be extended
up to 100 m (or 0.75 mm² for 50 m respectively).The cables can be extended by
means of a 2-wire cable (bell wire).
The terminals marked PWM / 0-10V are control outputs for high-efciency pumps
and for 0-10V boiler control respectively.
The controller is supplied with power via a mains cable.The power supply of the
device must be 100… 240 V~ (50 … 60 Hz).
The mains connection is at the terminals:
Neutral conductor N
Conductor L
Protective earth conductor ⏚(common terminal block)
VBus
VBus
S5/RTA
S4
/
S3
GND
Sensors
S2
S1
100 – 240V
T4A
50 – 60 Hz
N
R3
R2
R1
L
R1-R3|1 (1) A 240V~R4|1 (1) A 30V
IP 20
R4
PWM
0-10V
SD
R4
NN N N
R3 R2 R1 L
1234
56789
10 11

en
Installation
9
CommissioningSettingsTroubleshooting Data communication
Electrical connection of a high-efciency pump (HE pump)
Speed control of a HE pump is possible via a PWM signal/ 0-10 V control.The pump
has to be connected to the relay (power supply) as well as to one of the PWM out-
puts of the controller. In the Outputs adjustment channel one of the PWM control
types as well as a relay have to be selected (see page 37).
R2
R1
GND
PWM
N
X
blue
blue
brown
brown
yellow/green
black
(not used)
Signal cable
PWM
Signal input
Pump
Power supply
Pump
Power supply 230 V~
Note
For more details about the commissioning procedure see page page 16.

en
10
Installation Commissioning Settings Data communication Troubleshooting
2.3 Data communication / Bus
The controller is equipped with the VBus®for data transfer and energy supply
to external modules.The connection is to be carried out at the terminals marked
VBus (either polarity). The cable carries extra-low voltage and must not run to-
gether in a cable conduit with cables carrying a voltage higher than 50 V (please pay
attention to the valid directives).The cross section must be at least 0.5 mm2and the cable
can be extended up to 50 m in the case of a single connection.
One or more VBus®modules can be connected via this data bus, such as:
• DL2 / DL3 Datalogger
• KM2 Communication module
• VBus®
/ USB or VBus®
/ LAN interface adapter
Different solutions for visualisation and remote parameterisation are availabe on
the website www.resol.com. On the website, rmware updates are also availabe.
Note
More accessories on page page 41.
2.4 MicroSD card slot
The controller is equipped with a MicroSD card slot.
With a MicroSD card, the following functions can be carried out:
• Store measurement and balance values onto the MicroSD card.After the trans-
fer to a computer, the values can be opened and visualised, e. g. in a spreadsheet.
• Prepare adjustments and parameterisations on a computer and transfer them via
the MicroSD card.
• Store adjustments and parameterisations on the MicroSD card and, if necessary,
retrieve them from there.
• Download rmware updates from the Internet and install them on the controller
via MicroSD card.
MicroSD card slot
Note
For more information about using a MicroSD card, see page page 35.

11
en
Installation
CommissioningSettingsTroubleshooting Data communication
3 Operation and function
3.1 Buttons and adjustment dial
The controller is operated via 2 buttons and 1 adjustment dial (Lightwheel®) below
the display:
Left button (⟲) - escape button for changing into the previous menu
/ changing
to the home screen (Status Heating circuit), if the button is
pressed for 2s
Right button (✓) - conrming
/ selecting
Lightwheel®- scrolling upwards/ scrolling downwards, increasing adjustment
values
/ reducing adjustment values
3.2 Microbutton for chimney sweeper function/ screed drying and
holiday mode
The controller is equipped with two microbuttons for quick access to the holiday
mode and the chimney sweeper function / screed drying.The microbuttons are lo-
cated underneath the slidable housing cover, the slider.
Microbutton ♦: The chimney sweeper or screed drying function can be triggered
with the microbutton ♦.The chimney sweeper function is acti-
vated by default. In order to activate the screed drying function,
the chimney sweeper function must be deactivated (see page
page 32). In order to trigger the chimney sweeper or screed
drying function, press and hold down the microbutton ♦for 5 s.
Microbutton ⛁: Th e microbutton ⛁is used for activating the holiday mode. If the
microbutton is pressed and held down for approx. 3 s, the adjust-
ment channel Days of absence appears, allowing to enter the
number of days for an absence. If the parameter is set to a value
higher than 0, the holiday mode becomes active and the days will
be counted backwards at 00:00. If the value is set to 0, the holiday
mode is deactivated.
3.3 Control lamp
The controller is equipped with a multicolour LED in the centre of the Lightwheel®,
indicating the following states:
Colour Permanently shown Flashing
Green
Everything OK Manual mode on
Red
Screed drying
cancelled
Sensor line break, sensor short circuit, initialisation
Yellow
Holiday mode active Chimney sweeper function / screed drying active
Red /
Green
Manual mode off
3.4 Selecting menu points and adjusting values
During normal operation of the controller, the display is in the status menu.
If no button is pressed for 1 min, the display illumination switches off.After 3 more
minutes, the controller switches to the Status menu.
ÎIn order to get from the Status menu into the Main menu, press the left button
(⟲)!
ÎPress any key to reactivate the display illumination.
ÎIn order to scroll through the display channels, turn the Lightwheel®.
If the symbol ⏩is shown behind a menu item, pressing the right button (✓) will
open a new submenu.

en
12
Installation Commissioning Settings Data communication Troubleshooting
Values and adjustments can be changed in different ways:
Numeric values can be adjusted by means of a slide bar.The minimum value is indi-
cated to the left, the maximum value to the right.The large number above the slide
bar indicates the current adjustment.By turning the Lightwheel®, the upper slide bar
can be moved to the left or to the right.
Only after the adjustment has been conrmed by pressing the right button (✓) will
the number below the slide bar indicate the new value.The new value will be saved
if it is conrmed by pressing the right button (✓) again.
current value savedminimum value maximum value
adjusted value (not yet conrmed)
adjustment channel
When 2 values are locked against each other, they will display a reduced adjustment
range depending on the adjustment of the respective other value.
In this case, the active area of the slide bar is shortened,the inactive area is indicated
as a dotted line.The indication of the minimum and maximum values will adapt to
the reduction.
If only one item of several can be selected, they will be indicated with radio buttons.
When one item has been selected, the radio button in front of it is lled.
If more than one item of several can be selected, they will be indicated with check-
boxes.When an item has been selected, an xappears inside the checkbox.
If no button has been pressed within a couple of minutes, the adjustment is can-
celled and the previous value is retained.

13
en
Installation
CommissioningSettingsTroubleshooting Data communication
Adjusting the timer
When the Timer option is activated, a timer is in-
dicated in which time frames for the function can be
adjusted.
In the Day selection channel, the days of the week
are available individually and as frequently selected
combinations.
If more than one day or combination is selected, they
will be merged into one combination for the following
steps.
The last menu item after the list of days is Continue.
If Continue is selected, the
Edit timer
menu opens, in
which the time frames can be adjusted.
Adding a time frame:
In order to add a time frame, proceed as follows:
1. Select New time frame.
3. In order to save the time frame, select Save and
conrm the safety enquiry with Ye s .
4. In order to add another time frame, repeat the
previous steps.
6 time frames can be adjusted per day or combination.
5. Press the left button ⟲in order to get back to
the day selection.
2. Adjust Start and Stop for the desired time frame.
The time frames can be adjusted in steps of 5 min.

en
14
Installation Commissioning Settings Data communication Troubleshooting
Copying a time frame:
In order to copy time frames already adjusted into an-
other day /another combination, proceed as follows:
1. Choose the day / The combination into which the
time frames are to be copied and select Copy
from.
A selection of days and / or combinations with time
frames will appear.
2. Select the day or combination from which the
time frames are to be copied.
All time frames adjusted for the selected day or com-
bination will be copied.
If the time frames copied are not changed, the day or
combination will be added to the combination from
which the time frames have been copied.
If the time frames copied are changed, the day/ combi-
nation will be listed separately.
Changing a time frame:
In order to change a time frame, proceed as follows:
1. Select the time frame to be changed.
2. Make the desired change.
3. In order to save the time frame, select Save and
conrm the safety enquiry with Ye s .
Removing a time frame:
In order to delete a time frame, proceed as follows:
1. Select the time frame that is to be deleted.
2. Select Delete and conrm the safety enquiry with
Ye s .

15
en
Installation
CommissioningSettingsTroubleshooting Data communication
Resetting the timer:
In order to reset time frames adjusted for a certain day
or combination, proceed as follows
1. Select the desired day or combination.
In order to reset the whole timer, proceed as follows:
ÎSelect Reset and conrm the safety enquiry with
Ye s .
The selected day or combination will disappear from
the list, all its time frames will be deleted
2. Select
Reset
and conrm the safety enquiry with
Ye s .
All adjustments made for the timer are deleted.

en
16
Installation Commissioning Settings Data communication Troubleshooting
4 Commissioning
When the hydraulic system is lled and ready for operation, connect the controller
to the mains.
The controller runs an initialisation phase in which the Lightwheel® ashes red.
When the controller is commissioned or when it is reset, it will run a commis-
sioning menu after the initialisation phase.The commissioning menu leads the user
through the most important adjustment channels needed for operating the system.
Disconnecting the controller from the power supply after having run the commis-
sioning menu will not delete adjustments that have already been carried out.After
you switch on the device again, the controller will not start the commissioning
menu, but normal operation after the initialisation phase.
Commissioning menu
The commissioning menu consists of the channels described in the following. In
order to make an adjustment, adjust the desired value with the Lightwheel®and
conrm with the right button (✓).The next channel will appear in the display.
Adjustment mode
Operation
Changing a value
Conrming a value
1. Language:
ÎAdjust the desired menu language.
2. Temperature unit:
ÎAdjust the desired temperature unit.
3. Daylight savings time adjustment:
ÎActivate or deactivate the automatic daylight sav-
ings time adjustment.
4. Time:
ÎAdjust the clock time. First of all adjust the hours,
then the minutes.
5. Date:
ÎAdjust the date. First of all adjust the year, then the
month and then the day.
6. Scheme:
ÎAdjust the desired scheme (heating circuit,demand).

17
en
Installation
CommissioningSettingsTroubleshooting Data communication
7. Completing the commissioning menu:
After the scheme has been selected, a security enquiry
appears. If the safety enquiry is conrmed, the adjust-
ments are saved.
ÎIn order to conrm the security enquiry, press the
right button (✓).
ÎIn order to reenter the commissioning menu
channels, press the left button (⟲).
If the security enquiry has been conrmed, the con-
troller is ready for operation and should enable an op-
timum system operation.
Note:
The adjustments carried out during commissioning can be changed any-
time in the corresponding adjustment channel. Additional functions and
options can also be activated or deactivated (see page page 9).
Set the code to the customer code before handing over the con-
troller to the customer (see page page 36).
Adjusting the operating mode:
After commissioning the heating circuit will be in automatic mode.The operating
mode can be changed in the status menu:
• Automatic
• Day
• Night
• Holiday
• Off
1 mixed heating circuit
(see page page 19)
1 unmixed heating circuit with
backup heating (demand) (see
page page 22)
1 mixed heating circuit with
backup heating (demand) (see
page page 20)
1 unmixed heating circuit (see
page page 21)
1 2
34
4.1 Schemes with basic settings
The controller is preprogrammed for 4 basic systems. The basic pre-adjustments
have already been made.

en
18
Installation Commissioning Settings Data communication Troubleshooting
4.2 ErP temperature controls classes
Basic systems with backup heating (schemes 2 and 4) full the requirements of the
temperature controls class III according to the ErP Directive.
Further schemes with pre-programmed settings for 0-10 V boiler control, room
inuence or room control are also available to full the requirements of other
temperature controls classes.
For this purpose, the scheme number is extended to 3 digits. The rst digit indicates
the temperature controls class, the second and the third one indicate the desired
basic system.
Example:
In order to select scheme 2 with the settings for temperature controls class VIII,
enter the scheme number 802.
802
Temperature
controls class
Number of the desired scheme; with
a 0 in front of it for numbers with
1 digit.
The settings for the different temperature classes will in the following be indicated
with digit symbols:
: Temperature controls class II
: Temperature controls class III
: Temperature controls class V
: Temperature controls class VI
: Temperature controls class VII
: Temperature controls class VIII
The schemes extended can be found below scheme 4 in the selection.

19
en
Installation
CommissioningSettingsTroubleshooting Data communication
Sensors
S1 Flow HC 1 / GND
S2 Outdoor 2 / GND
S3 Free 3 / GND
S4 Free 4 / GND
S5 Free 5 / GND
Relay
R1 HC pump R1 / N / PE
R2 Mixer open R2 / N / PE
R3 Mixer closed R3 / N / PE
R4 Free 8 / 10
By means of the ow sensor S1 and the outdoor temperature sensor S2, a mixed
weather-compensated heating circuit can be controlled.
Scheme 1: 1 mixed heating circuit
VBus
VBus
S5/RTA
S4
/
S3
GND
Sensors
S2
S1
N
R3
R2
R1
L
R1-R3|1 (1) A 240V~R4|1 (1) A 30V
R4
PWM
0-10V
R4
S2
S1
R1
R2/3
NN N N
R3 R2 R1 L
1234
56789
10 11

en
20
Installation Commissioning Settings Data communication Troubleshooting
By means of the ow sensor S1 and the outdoor temperature sensor S2, a mixed
weather-compensated heating circuit can be controlled. Boiler demand via the po-
tential-free relay is triggered depending on the temperature difference between
the set ow temperature and the value measured at the backup heating sensor S3.
Scheme 202: 0-10 V boiler control, weather-compensated
Scheme 502: 0-10 V boiler control, room control with room temperature sen-
sor S4, no outdoor temperature sensor
Scheme 602: 0-10 V boiler control, room inuence with room temperature
sensor S4, weather-compensated
Scheme 702: Room inuence with room temperature sensor S4, weather-com-
pensated
Scheme 802: 0-10 V boiler control, room control with room temperature sen-
sors S4, S5, S2, no outdoor temperature sensor
Scheme 2: 1 mixed heating circuit with backup heating (demand)
VBus
VBus
S5/RTA
S4
/
S3
GND
Sensors
S2
S1
N
R3
R2
R1
L
R1-R3|1 (1) A 240V~R4|1 (1) A 30V
R4
PWM
0-10V
R4
S2
S1
S3
NN N N
R3 R2 R1 L
1234
56789
10 11
R2/3
R1
R4
Sensors
S1 Flow HC 1 / GND
S2 Outdoor (RTH3*) *2 / GND
S3 Backup heating / boil-
er
3 / GND
S4 RTH1 4 / GND
S5 RTH2 5 / GND
Relay
R1 HC pump R1 / N / PE
R2 Mixer open R2 / N / PE
R3 Mixer closed R3 / N / PE
R4 Demand 8 / 10
*In the temperature controls class VIII S2 will be used as RTH3.
Other manuals for DeltaTherm HC mini
2
Table of contents
Other Resol Thermostat manuals
Popular Thermostat manuals by other brands
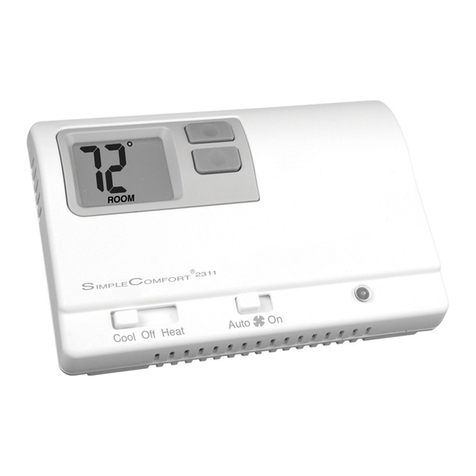
ICM Controls
ICM Controls SC2311L Installation, operation & application guide
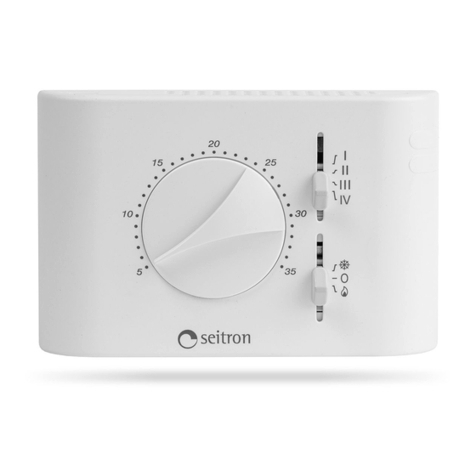
Seitron
Seitron i-10 manual
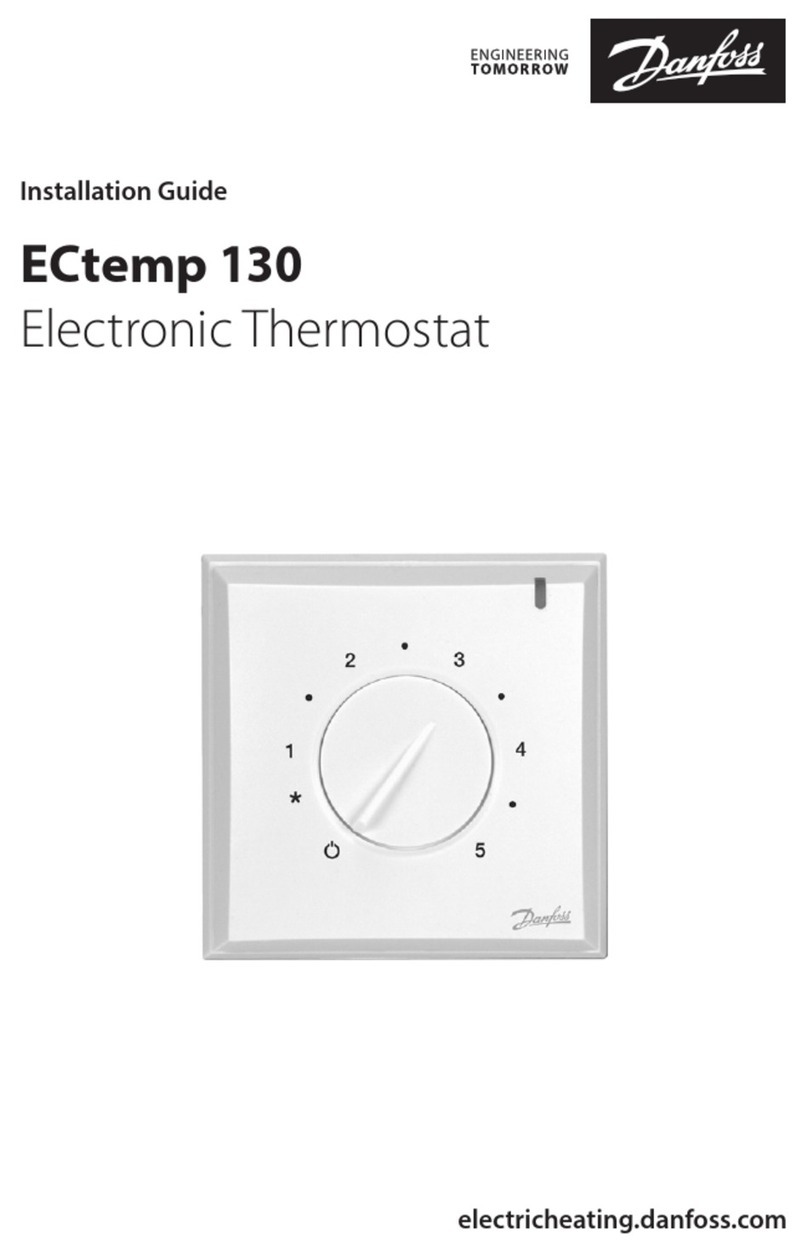
Danfoss
Danfoss ECtemp 130 installation guide
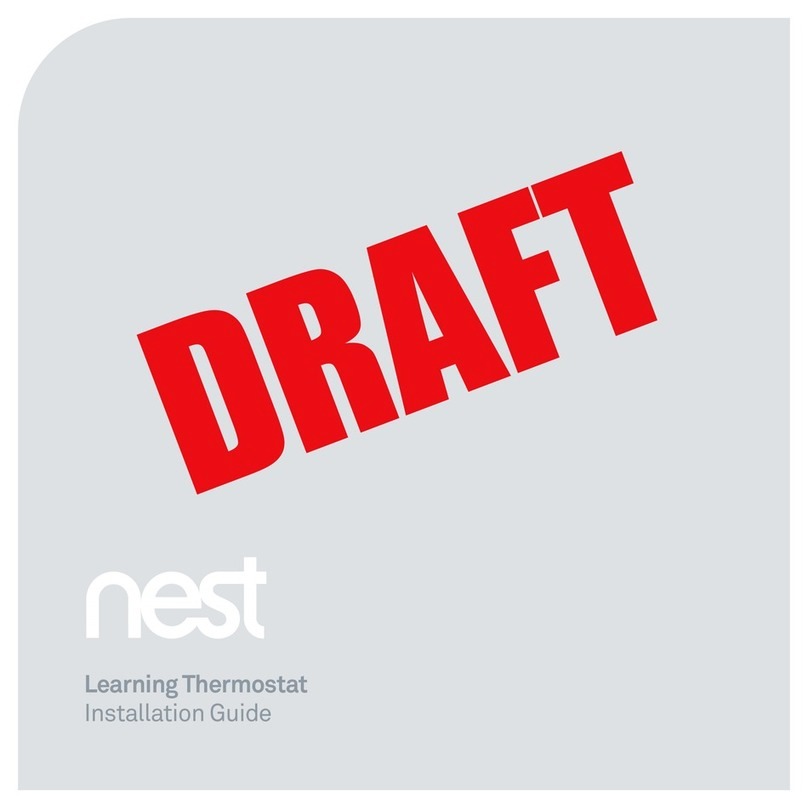
nest
nest Learning thermostat installation guide

Honeywell
Honeywell T Series installation guide
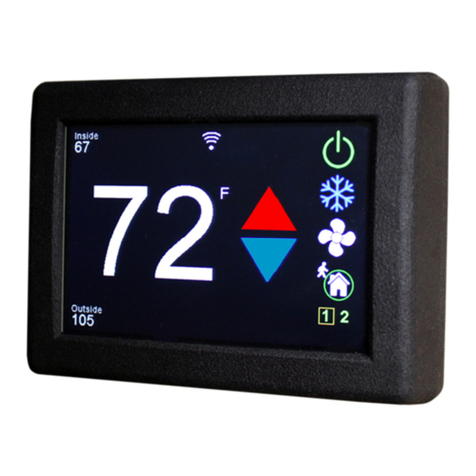
MICRO-AIR
MICRO-AIR EasyTouch RV Installation, Quick Start Guide and Operation Manual