Rexnord Smart Condition User manual

Rexnord Smart Condition Monitoring System • Installation Manual
(Page 1 of 12) Large Gear Drives
SS3-001 Rexnord
August 2019 3001 W. Canal St., Milwaukee, WI 53208-4200 USA
Supersedes 5-19 Telephone: 414-937-4359 Fax: 414-937-4359 www.rexnord.com
TABLE OF CONTENTS
1. Connecting AC Input Power and CAT 5 Data Cable
to the Smart Condition Monitoring System Edge ...........1
1.1 How to Attach the Supplied Ethernet
Connector to Cat 5 Cable .......................................2
1.2 How to Attach the AC Input Power Connector
to Power Cable ........................................................3
2. Connecting the Rexnord Supplied Current Transducer ....5
2.1 Connecting your Own 4-20mA Current Transducer....6
2.2 Connecting your Own 0-5V dc Output
Current Transducer..................................................8
3. Installing the Oil Quality Sensor .....................................9
4. Allowing the Edge device on your network
(Security Guidelines)....................................................... 10
5. Setting up your PLC Interface ........................................10
Appendix A: Troubleshooting............................................11
Appendix B: Enclosure Details .........................................11
Appendix C: FCC Statements ...........................................12
1. CONNECTING AC INPUT POWER AND
CAT 5 DATA CABLE TO THE SMART
CONDITION MONITORING SYSTEM EDGE
The Smart Condition Monitoring System Edge device must
be connected to AC power to operate. The input power
specifications include:
•Nominal voltage: 100V to 240V ac nominal 50-60Hz
•Maximum power: 120 Watts
NOTE: OPENING THE EDGE DEVICE ENCLOSURE
COVER, OR ANY OTHER INTRUSION INTO THE EDGE
DEVICE ENCLOSURE, VOIDS THE WARRANTY OF THE
EDGE DEVICE. ALL CONNECTIONS MUST BE MADE
USING THE INTERFACE BOX.
Remove the cover of the interface box by loosening the
4 cover fasteners shown in Figure 1. Using a knockout
punch, remove either a ½", 1", or 1-½" hole for AC power
metal conduit on the bottom (preferred) or top of the
interface box and securely tighten the conduit to the box.
CAT 5 data cable is used for connectivity from the
Smart Conditioning Monitoring System Edge device to
a PLC (LAN connection), as well as for the connection
to the internet (WAN connection). Alternatively, cellular
connectivity may be used for the WAN connection, with
specific versions of the Edge device equipped with a
cellular antenna. As above, remove a second hole for
the CAT 5 data cable(s) metal conduit on the bottom
(preferred) or top of the interface box and securely tighten
the conduit to the box. It is best practice to have the
data cables plugged in before power is turned on.
Locate the AC power plug assembly and the RJ-45
connectors that are provided in the interface box. The
power and data ports are shown in Figure 2. For correct
assembly of the connectors, refer to page 2 for the
data connectors and page 3 for the power connector.
Remove any excess slack that is remaining in the power or
data cables inside of the box and replace the cover.
Figure 2 – AC Power and Data Connections inside
interface box
Figure 1 – Drawing of Smart Condition Monitoring
System Edge with option cellular antenna and
Andon light. M12 sensor connections (bottom),
interface box (right)
Interface
Box
Cover Fasteners
Cover Fasteners

Rexnord Smart Condition Monitoring System • Installation Manual
(Page 2 of 12) Large Gear Drives
SS3-001 Rexnord
August 2019 3001 W. Canal St., Milwaukee, WI 53208-4200 USA
Supersedes 5-19 Telephone: 414-937-4359 Fax: 414-937-4359 www.rexnord.com
5. Crimp the wire cores into the RJ45 connector using
suitable crimping pliers (Step L).
6. Gently pull the RJ45 plug back into the connector
shell, slip the snap ring onto the connector body
and push firmly until it snaps into place locking the
plug into the connector body (Steps M, N then O).
7. Test the completed cable end to end with a suitable
LAN cable tester.
1.1 HOW TO ATTACH THE SUPPLIED ETHERNET
CONNECTOR TO CAT 5 CABLE
1. Place sealing “O” ring over connector body and
slide coupling ring onto body (Steps A, B then C).
2. Slide sealing nut, cable grip grommet and
assembly just created onto cable. Push the
grommet into the connector body then loosely
tighten the sealing nut (Steps D, E then F).
3. Strip the outer sheath of the cable back 14mm,
untwist and straighten the 8 core wires and arrange
the colors as required for EIA/TIA 568B (Orange/
White, Orange, Green/White, Blue, Blue/White,
Green, Brown/White, Brown - pins 1 to 8) then trim
to a neat straight line (Steps G, H then I to give J).
4. Push the wires into the clear RJ45 connector. Pin 1
is to the left when the cable is facing you and the
tang is under the connector as shown in Step K.
Step A
Step E
Step I
Step M
Step B
Step F
Step J
Step N
Step C
Step G
Step K
Step O
Step D
Step H
Step L
Step P

Rexnord Smart Condition Monitoring System • Installation Manual
(Page 3 of 12) Large Gear Drives
SS3-001 Rexnord
August 2019 3001 W. Canal St., Milwaukee, WI 53208-4200 USA
Supersedes 5-19 Telephone: 414-937-4359 Fax: 414-937-4359 www.rexnord.com
1.2 HOW TO ATTACH THE AC INPUT POWER
CONNECTOR TO POWER CABLE
1. Punch suitable holes in the top or bottom surface
of the small connector box attached to the side of
the SED500X unit. Attach suitable conduit or install
a dust tight cable gland as appropriate for the
installation environment.
2. Unpack the Amphenol C016 20F003 100 12
supplied inside the small connector box (Step
A). Choose one of the 2 sizes of rubber cord grip
appropriate for the cable(s) being connected (Step
A).
3. Thread on the pieces of the connector onto the
cable in the following order noting the correct
orientation — gland nut, rubber cord grip, gland
ferrule, right-angled backshell and straight
backshell ensuring the angle locking fingers are
facing towards the right-angled body (Step B).
4. Strip back the outer sheath of the cable 37mm then
strip 7mm at the end of each conductor (Step C).
5. Connect the wire cores into the back of the
connectors screwing down the terminals securely
using a 1/8” or 3mm blade screwdriver. Line 110V
ac goes to terminal 1, Neutral 110V ac goes
to terminal 2 and Ground goes to the terminal
marked with the Ground Symbol (Step D and E).
Note the terminal numbers are under the screw
terminals inside the connector. Also note that
there is a semicircular cutout in the side of the
free spinning front tubular part of the connector
which needs to be aligned with each screw in
turn to allow screwdriver access to the terminal
screws (Step F).
6. Screw the straight backshell onto the front of the
connector and tighten. Note this must be done by
holding the front keyed circular portion with soft
nosed pliers and turning the backshell. Do not hold
the backshell and turn the front keyed portion or the
wires will twist around and break internally (Step G
and H).
7. Pull down the right angle backshell and holding
the front part assembled portion and the right
angled backshell turn the large hexagonal portion
of the right angled backshell which will spin
independently of the right angled backshell (Step
I). This shows slip lock pliers on the hex portion,
but hand tighten only so that the ratchet portion
can still be adjusted for angle. Do not tighten at this
stage (Step J).
8. Slip down the gland ferrule and turn until the keys
on it are aligned with the slots in the right angled
backshell. (Step K). Push the ferrule fully home
then slip down the rubber cord grip and push
securely into the ferrule. (Step L). Slip the cable
gland nut down onto the right angled backshell and
just engage the threads together. Do not tighten at
this stage (Step M).
Step A
Step C
Step E
Step G
Step I
Step K
Step B
Step D
Step F
Step H
Step J
Step L

Rexnord Smart Condition Monitoring System • Installation Manual
(Page 4 of 12) Large Gear Drives
SS3-001 Rexnord
August 2019 3001 W. Canal St., Milwaukee, WI 53208-4200 USA
Supersedes 5-19 Telephone: 414-937-4359 Fax: 414-937-4359 www.rexnord.com
9. Look at the small enclosure power connector.
Typically, the keyway will be at the 3 o’clock
position. Carefully turn the keyed circular connector
face until the key orients the right-angled body
of the connector to the 9 o’clock, 12 o’clock or
3 o’clock position. When the keyways align then
tighten the large hexagonal nut on the right-angled
portion of the backshell to lock the ratchet portion,
so it cannot turn (Step N).
10. Tighten the cable gland nut until it grips the cable
tightly and is well seated and sealed (Step O).
11. Connect the connector onto its mating bulkhead
connector turning it carefully until the keys align,
push in hard and then turn the hand nut until the
connector is tight and fully engaged (Step P).
12. If the LAN and WAN cables have already been
attached and connected, apply power and
check the Serial Edge device has power (power
indicating light is illuminated blue).
Step M
Step O
Step N
Step P

Rexnord Smart Condition Monitoring System • Installation Manual
(Page 5 of 12) Large Gear Drives
SS3-001 Rexnord
August 2019 3001 W. Canal St., Milwaukee, WI 53208-4200 USA
Supersedes 5-19 Telephone: 414-937-4359 Fax: 414-937-4359 www.rexnord.com
MOUNTING AND MECHANICAL
Din Rail Mounting (tool needed 3mm blade screwdriver)
1. Hook the stationary lip of the bottom case to one side
of the 35mm DIN Rail. (The side without the orange
clip.)
2. Using the blade screwdriver, push down and pull
out on the orange rail clip of the bottom case till the
transducer clicks over the other side of the rail.
3. Once it is latched on fully, push the clip in towards
the transducer to fully seat the transducer on the rail
(Figure 8).
Screw Mounting (Screws are not supplied)
Do Not over tighten the mounting screws.
2. CONNECTING THE REXNORD SUPPLIED
CURRENT TRANSDUCER
ELECTRICAL CONNECTIONS (TOOL NEEDED 1/8" OR
3MM BLADE SCREWDRIVER)
Input Connections
Current Measurements
The transducers sense current in a non-contact fashion
by simply running the wire carrying the current through
the hole of the transducer. If installing the DC version, pay
close attention to the direction as shown below (Figure 5).
All non-contact current measurements are based upon
a single phase wire going through the hole. Wire the CT
cable to the CT as shown in Figure 6.
Connecting to the Rexnord Edge
Converter Box
If the molded connector end of the CT cable is not already
connected, please attach to terminal 4 (Yellow) on the
small black converter box mounted next to the Edge
(Figure 7).
Figure 5
Figure 6
Figure 7
Figure 8
1 2 3

Rexnord Smart Condition Monitoring System • Installation Manual
(Page 6 of 12) Large Gear Drives
SS3-001 Rexnord
August 2019 3001 W. Canal St., Milwaukee, WI 53208-4200 USA
Supersedes 5-19 Telephone: 414-937-4359 Fax: 414-937-4359 www.rexnord.com
2.1 CONNECTING YOUR OWN 4-20MA CURRENT
TRANSDUCER
It is very important that you do not connect the cable
from the 4-20mA source to the converter box without
successfully completing this procedure. If it is not
possible to successfully complete this procedure, then
the cable should be left disconnected and adequate
protection to prevent shorting of the wires or dirt
contamination be provided until such a time as a test can
be completed.
1. To complete this test, the cable from your
4-20mA CT or PLC providing the signal must be
disconnected and isolated at the source.
2. Please provide a 2-core cable. Verify it has been
disconnected from the signal source at the
other end. Ensure the LCVC8001 converter box
connector is not connected to either the converter
box or the Loop Current Polarity Checker box.
Unscrew the free end of the cable joint, and slip
the gland nut, seal grommet, and removable
terminal cover up the cable (Step A).
3. Strip back the cable jacket 1” and strip each of the
2 core wires back ½” to bare wire (Step B).
4. There are only 2 screw down terminals inside the
cable joint. Loosen, insert a bared core wire and
tighten the terminal and repeat. It is not important
at this stage which core wire is connected to
which terminal (Step C).
5. Screw terminal cover onto cable joint, slide down
blue cable gland seal and insert into “fingers” then
slide down gland nut and loosely tighten (Step D).
6. Connect the 4-20mA CT or PLC cable at the source
end and connect the Polarity Test Box to the EN2
connector on the end of the lead from the cable
joint by slowly turning the connector until the key
aligns then insert and tighten the finger lock nut on
the connector. Sometimes the finger nut needs to
be turned slightly to allow the connector to engage
fully (Step E).
7. Provide either a test signal from the PLC or engage
the equipment such that current is drawn by the
motor. Using a Multimeter with the input and range
set to around 0-20V dc (0-10V dc minimum) check
whether a positive or negative voltage reading is
shown on the multimeter (Step E). Note that even
if the motor is not turning, the meter should read
either +1V dc or -1V dc.
Step A
Step B
Step C
Step D

Rexnord Smart Condition Monitoring System • Installation Manual
(Page 7 of 12) Large Gear Drives
SS3-001 Rexnord
August 2019 3001 W. Canal St., Milwaukee, WI 53208-4200 USA
Supersedes 5-19 Telephone: 414-937-4359 Fax: 414-937-4359 www.rexnord.com
8. If the meter displays a positive value less than
5V dc, this test is complete, tighten the cable
gland, disconnect the cable from the test box and
connected to the converter box. If the multimeter
displays a negative DC voltage reading the wires
inside the cable joint are reversed. Unscrew the
gland nut and the screw terminal cover, disconnect
the wires and swap them over, then tighten them
securely.
CAUTION: the equipment must be turned off or
the test signal deactivated before the cable joint
is opened or damage to the customer PLC or CT
could occur. Tighten down the screw terminal cover
and the cable gland nut, reconnect to the PLC or
customer CT at the head end and repeat 7) above
ensuring the multimeter displays a positive voltage
reading then disconnect the cable from the test box
and connect it to the small black converter box.
9. If the multimeter reads more than +5V dc or less
than -5V dc, further investigation by a qualified
electrical technician is required. If the signal is to
the correct 4-20mA signal, a multimeter connected
red to red and black to black on the test box will
never show greater than +5V dc or less than -5V
dc. If the voltage is out of range, do not connect
the CT cable to the converter box.
10. If, and only if, a successful test was achieved,
remove the polarity test box and connect the
EN2 connector on the end of the cable from the
LCVC8001 to the lower Left Hand (Yellow) port on
the converter box. Check that after the equipment
is back in service that motor power draw is being
sent to the cloud and the scaling factor has been
correctly set.
11. Pack Polarity check box in toolkit and move to next
job.
Step E

Rexnord Smart Condition Monitoring System • Installation Manual
(Page 8 of 12) Large Gear Drives
SS3-001 Rexnord
August 2019 3001 W. Canal St., Milwaukee, WI 53208-4200 USA
Supersedes 5-19 Telephone: 414-937-4359 Fax: 414-937-4359 www.rexnord.com
2.2 CONNECTING YOUR OWN 0-5V DC OUTPUT
CURRENT TRANSDUCER
It is very important that you do not connect the cable from
the current transducer to the converter box box without
successfully completing this procedure. If it is not possible
to successfully complete this procedure, then the cable
should be left disconnected and adequate protection
to prevent shorting of the wires or dirt contamination be
provided until such a time as a test can be completed.
1. To complete this installation and test, the cable
from the 0-5V CT or PLC providing the signal must
be disconnected and isolated at the source.
2. Please provided a 2-core cable. Double check it
has been disconnected from the signal source at
the other end. Ensure the VSCC9001 converter box
connector is not connected to either the converter
box or the Polarity Checker box then unscrew the
free end of the cable joint and slip the gland nut,
seal grommet and removable terminal cover up the
cable (Step F).
3. Strip back the cable jacket 1” and strip each of the
2 core wires back ½” to bare wire (Step B).
4. There are only 2 screw down terminals inside the
cable joint. Loosen, insert a bared core wire and
tighten the terminal and repeat. It is not important
at this stage which core wire is connected to
which terminal (Step G).
5. Screw terminal cover onto cable joint, slide down
blue cable gland seal and insert into “fingers” then
slide down gland nut and loosely tighten (Step H).
6. Connect the 0-5V CT or PLC cable at the source
end and connect the Polarity Test Box to the EN2
connector on the end of the lead from the cable
joint by slowly turning the connector until the key
aligns then insert and tighten the finger lock nut on
the connector. Sometimes the finger nut needs to
be turned slightly to allow the connector to engage
fully (Step E).
7. Provide either a test signal from the PLC or engage
the equipment such that current is drawn by the
motor. Using a Multimeter with the input and range
set to around 0-20V dc (0-10V dc minimum) check
whether a positive or negative voltage reading is
shown on the multimeter (Step E). Note that if the
motor is not turning, the meter will read 0V dc.
8. If the meter displays a positive value less than
5V dc, this test is complete. Tighten the cable
gland, disconnect the cable from the test box, and
connect to the converter box. If the multimeter
displays a negative DC voltage reading the wires
inside the cable joint are reversed.
CAUTION: the equipment must be turned off or
the test signal deactivated before the cable joint
is opened or damage to the PLC or CT could
occur.
Step F
Step B
Step H
Step G

Rexnord Smart Condition Monitoring System • Installation Manual
(Page 9 of 12) Large Gear Drives
SS3-001 Rexnord
August 2019 3001 W. Canal St., Milwaukee, WI 53208-4200 USA
Supersedes 5-19 Telephone: 414-937-4359 Fax: 414-937-4359 www.rexnord.com
Unscrew the gland nut and the screw terminal
cover, disconnect the wires, swap their positions,
and then tighten each securely. Tighten down the
screw terminal cover and the cable gland nut,
reconnect to the PLC or CT at the head end and
repeat 7) above ensuring the multimeter displays a
positive voltage reading then disconnect the cable
from the test box and connect it to the converter
box.
9. If the multimeter reads more than +5V dc or less
than -5V dc, further investigation by a qualified
electrical technician is required. If the incoming
signal is to the correct 0 to 5V dc signal, a
multimeter connected red to red and black to black
on the test box will never show greater than +5V dc
or less than -5V dc. If the voltage is out of range,
do not connect the CT cable to the converter box.
10. If, and only if, a successful test was achieved,
remove the polarity test box and connect the
EN2 connector on the end of the cable from the
VSCC9001 to the lower Left Hand (Yellow) port on
the converter box. Check that after the equipment
is back in service that motor power draw is being
sent to the cloud and the scaling factor has been
correctly set.
11. Pack Polarity check box in toolkit and move to next
job.
3. INSTALLING THE OIL QUALITY SENSOR
1. The housing uses a tapered pipe thread (NPT)
seal by contact of threads. A paste type anti-seize
compound such as Parker Thread-Mate along with
pipe thread sealing tape works most effectively
with NPT threads
2. Use anti-seize compound on male thread, then 3-4
wraps of Teflon tape
3. Ensure the Oil Quality Sensor and adaptor
sub-assembly stays clean and clear of all
contamination in the element area of the sensor.
4. Screw in adaptor Oil Quality Sensor sub-assembly
into the housing turning clockwise
5. Adaptor fittings should engage about 2 turns by
hand and then be tightened to the recommended
torque shown in Figure 9.
6. Tighten sub-assembly by using the flats that are on
the adaptor, reference Figure 9 for location of flats
on adaptor. CAUTION: Do not tighten the sub-
assembly by using the flats that are on the Oil
Quality Sensor.
7. Tighten torque recommendation are shown in
Figure 9, based on the size of the NPT.
8. Connect the cable to the end of the Oil Quality
Sensor that runs from the Smart Condition
Monitoring System control box.
If the element on the Oil Quality Sensor becomes
contaminated, the following should be done:
1. Disconnect the cable from the end of the Oil
Quality Sensor.
2. Remove the Oil Quality Sensor from the gear drive
by turning the Oil Quality Sensor sub-assembly
counterclockwise.
3. Loosen the sub-assembly by using the flats that
are on the adaptor. Caution: Do not loosen the
sub-assembly by using the flats that are on the Oil
Quality Sensor. Reference Figure 9 for location of
flats on adaptor.
4. Disassembly Oil Quality Sensor from adaptor by
using the flats provided on the adaptor and Oil
Quality Sensor by turning in a counterclockwise
direction.
5. Once the adaptor and Oil Quality Sensor have
been disassembled cleaning the sensor element is
a two-step process:
a. Rinse the sensor element with isopropyl
alcohol, reference Figure 10 for location of
sensor element.
b. Rinse the sensor element with distilled water
or deionized water. CAUTION: It is important
NOT to use a brush or compressed air when
cleaning the sensor as it can damage the
element.
6. After the Oil Quality Sensor element has been
cleaned, the following should be done for
reassembly of the adaptor and Oil Quality Sensor.
7. Apply a small amount of the lubricant to the face of
the O-ring gasket to help ensure the O-ring gasket
and the adaptor seal correctly.
THREAD SIZE RECOMMENDED TORQUE
1 NPT 129-163 Nm 95-120 ft-lb
1-¼ NPT 176-203 Nm 130-150 ft-lb
Figure 9: NPT Torque Recommendations
Figure 10: Oil Quality Sensor Sub-Assembly
Adaptor Oil Quality Sensor

Rexnord Smart Condition Monitoring System • Installation Manual
(Page 10 of 12) Large Gear Drives
SS3-001 Rexnord
August 2019 3001 W. Canal St., Milwaukee, WI 53208-4200 USA
Supersedes 5-19 Telephone: 414-937-4359 Fax: 414-937-4359 www.rexnord.com
8. Straight thread S.A.E. threads seal with the use of
and O-ring on the male thread and a flat face at
the bottom of the female thread, they do not seal
on the threads. A paste type anti-seize compound
such as Swagelok Blue Goop®works most effective
with straight threads.
9. Use anti-seize compound on male threads.
10. Prepared fittings should engage fully by hand
turning the clockwise direction.
11. Tightening of the adaptor and Oil Quality Sensor
should be done the use of the flats provided on the
adaptor and the sensor.
12. Tighten torque recommendation are shown in
Figure 11.
Always observe these precautions when tightening:
• The condition of the threads is important to ensure proper
engagement of strength, and threads should always be
inspected before use.
• Proper tightening is important to ensue sealing and to
prevent unthreading due to vibration.
• High temperature anti-seize compounds containing
metallic particles are not recommended.
• Only use correctly sized open-end wrenches on the
adaptor flats provided.
• Teeth from pipe wrenches can initiate cracks in hardened
steel components.
4. ALLOWING THE EDGE DEVICE
ON YOUR NETWORK (SECURITY
GUIDELINES)
See supplemental document (SS5-001) for instructions on
how to set up your network for secure communications.
5. SETTING UP YOUR PLC INTERFACE
See supplemental document (SS3-002) for instructions on
how to set up the Edge to be visible on your PLC network.
Figure 12: Oil Quality Sensor
Sensor
Element
THREAD SIZE RECOMMENDED TORQUE
¾-16 UNF 100-115 Nm 80-90 ft-lb
Figure 11: S.A.E. Torque Recommendations

Rexnord Smart Condition Monitoring System • Installation Manual
(Page 11 of 12) Large Gear Drives
SS3-001 Rexnord
August 2019 3001 W. Canal St., Milwaukee, WI 53208-4200 USA
Supersedes 5-19 Telephone: 414-937-4359 Fax: 414-937-4359 www.rexnord.com
APPENDIX A: TROUBLESHOOTING
1. The Andon light does not illuminate (optionally mounted
on Edge device or remotely)
1.1. If the Andon light is mounted separately from
the Edge device, verify that the cable connections
are secure and that the cables show no sign of
damage.
1.2. Check that the blue LED light located on the front
of the Edge device is illuminated. If not, verify that
incoming AC power is properly connected.
1.3. Check AC connection in interface box and at
power source.
1.4. Check that the AC input power is within
specifications.
1.5. If the problem persists, consult 1-866-REXNORD.
Do not open the Edge device.
2. The Andon light illuminates, but no data is available
from the cloud
2.1. If the connection is cellular:
2.1.1. Check that the GPS location currently has
AT&T cellular coverage (https://www.att.
com/maps/wireless-coverage.html)
2.1.2. Check for excessive metal shielding around
the cellular antenna that could impede
cellular reception. The GPS/Cellular
antenna is the black round hyperbolic stack
located at top-left of the edge device as
shown in Figures 13 & 14. If excessive
metal shielding exists, the unit will have
to be hard-wired to ethernet via WAN
connection.
2.2. If the WAN connection is hard-wired with Ethernet:
2.2.1. Check that the network settings allow
functionality from the Edge device. Please
see Rexnord Smart Condition Monitoring
System Security Guidelines (SS5-001) for
additional details.
2.2.2. Verify external Ethernet cable to hard wired
public internet is connected to “WAN/
Cloud” and the PLC Ethernet connection (if
provided) is connected to the port marked
LAN/PLC.
2.2.3. If the problem persists, consult consult
1-866-REXNORD.
APPENDIX B: ENCLOSURE DETAILS
Figure 13 – Edge device assembly with optional cellular
antenna and Andon light
Figure 14 – Edge device external layout with optional
cellular antenna and Andon light

Rexnord Smart Condition Monitoring System • Installation Manual
(Page 12 of 12) Large Gear Drives
SS3-001 Rexnord
August 2019 3001 W. Canal St., Milwaukee, WI 53208-4200 USA
Supersedes 5-19 Telephone: 414-937-4359 Fax: 414-937-4359 www.rexnord.com
APPENDIX C — FCC STATEMENTS:
Modification statement
Rexnord has not approved any changes or modifications
to this device by the user outside of those listed in this
document. Any additional changes or modifications could
void the user’s warranty.
Interference statement
This device complies with Part 15 of the FCC Rules
and Industry Canada license exempt RSS standard(s).
Operation is subject to the following two conditions: (1)
this device may not cause interference, and (2) this device
must accept any interference, including interference that
may cause undesired operation of the device.
Wireless notice
This equipment complies with FCC and IC radiation
exposure limits set forth for an uncontrolled environment.
The antenna should be installed and operated with
minimum distance of 20 cm between the radiator and
your body.
This transmitter must not be co-located or operating in
conjunction with any other antenna or transmitter.
FCC Class A digital device notice
This equipment has been tested and found to comply with
the limits for a Class A digital device, pursuant to part 15
of the FCC Rules. These limits are designed to provide
reasonable protection against harmful interference when
the equipment is operated in a commercial environment.
This equipment generates, uses, and can radiate radio
frequency energy and, if not installed and used in
accordance with the instruction manual, may cause
harmful interference to radio communications. Operation
of this equipment in a residential area is likely to cause
harmful interference in which case the user will be required
to correct the interference at his own expense.
Contact Information
Phone: 1-866-REXNORD (739-6673)
Internet: www.rexnord.com
Table of contents
Popular Measuring Instrument manuals by other brands
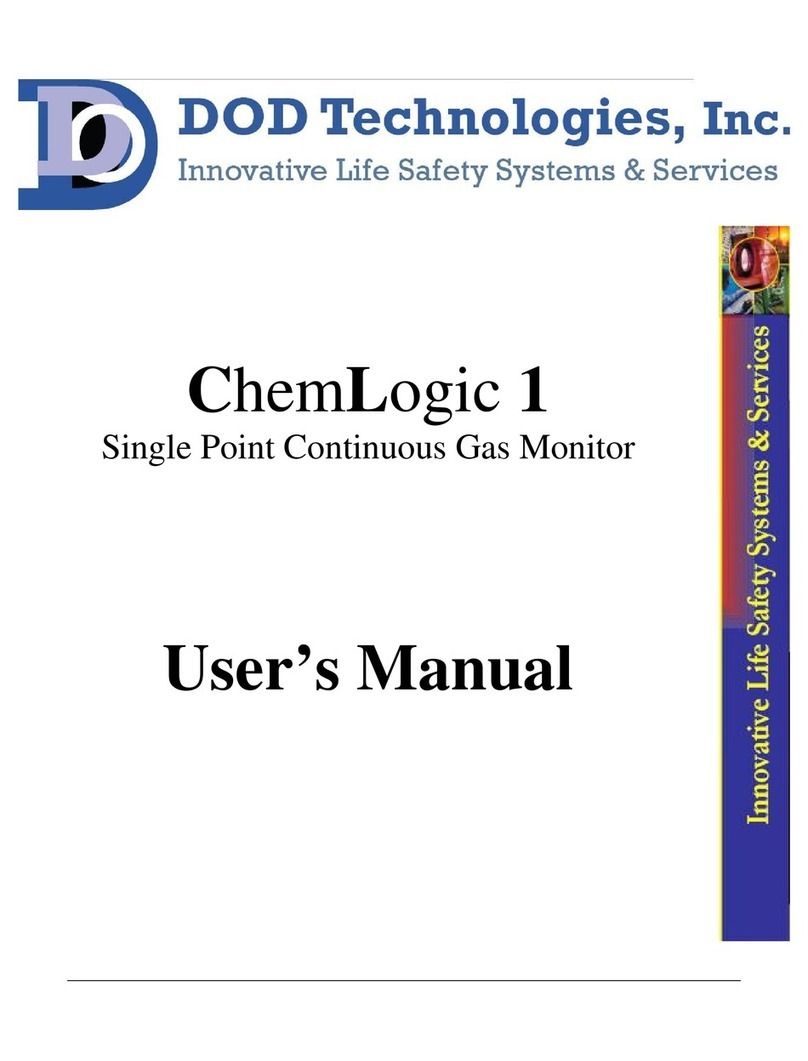
DOD Technologies
DOD Technologies ChemLogic 1 user manual

palintest
palintest Green Drop Kit instructions
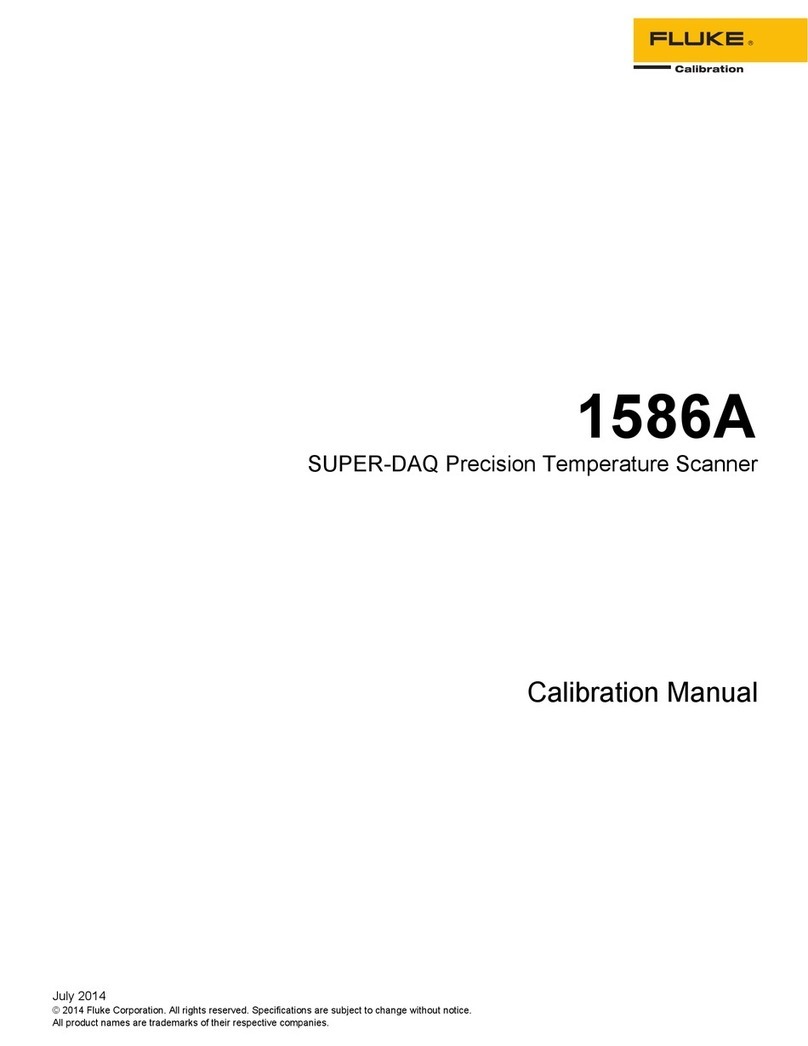
Fluke Calibration
Fluke Calibration 1586A Super-DAQ Calibration manual
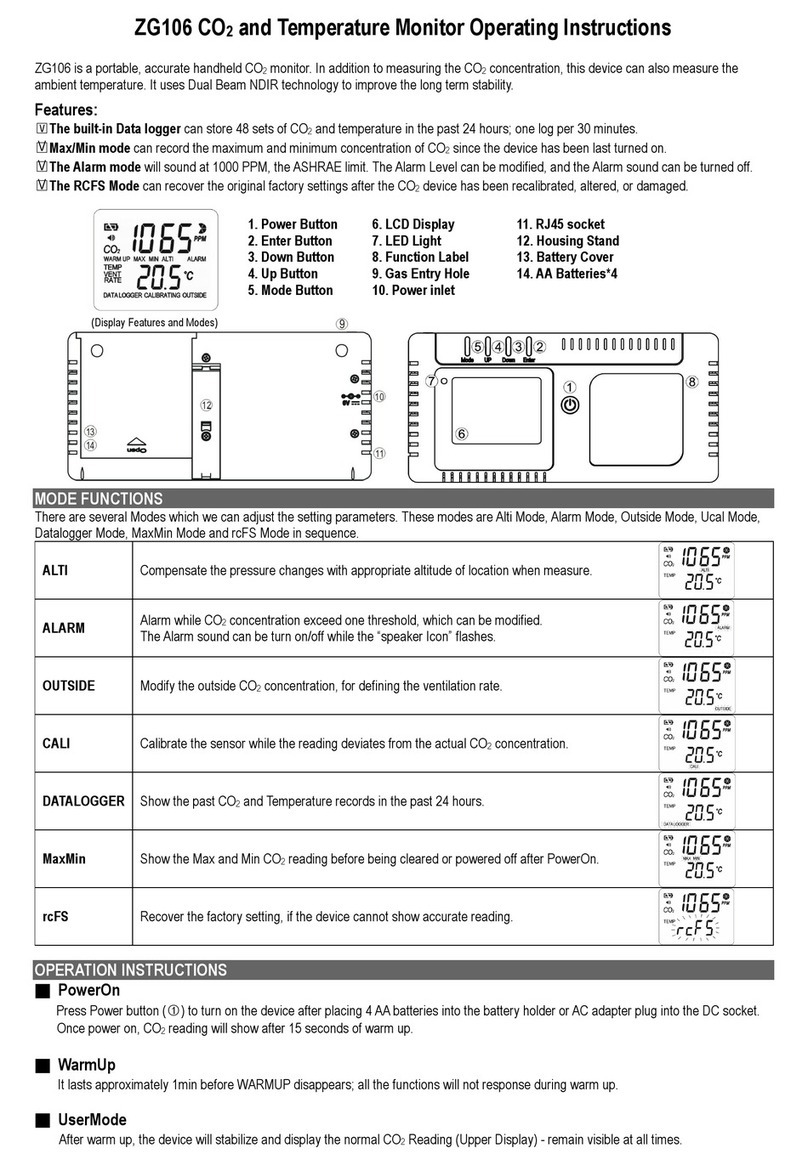
ZyAura
ZyAura ZG106 operating instructions
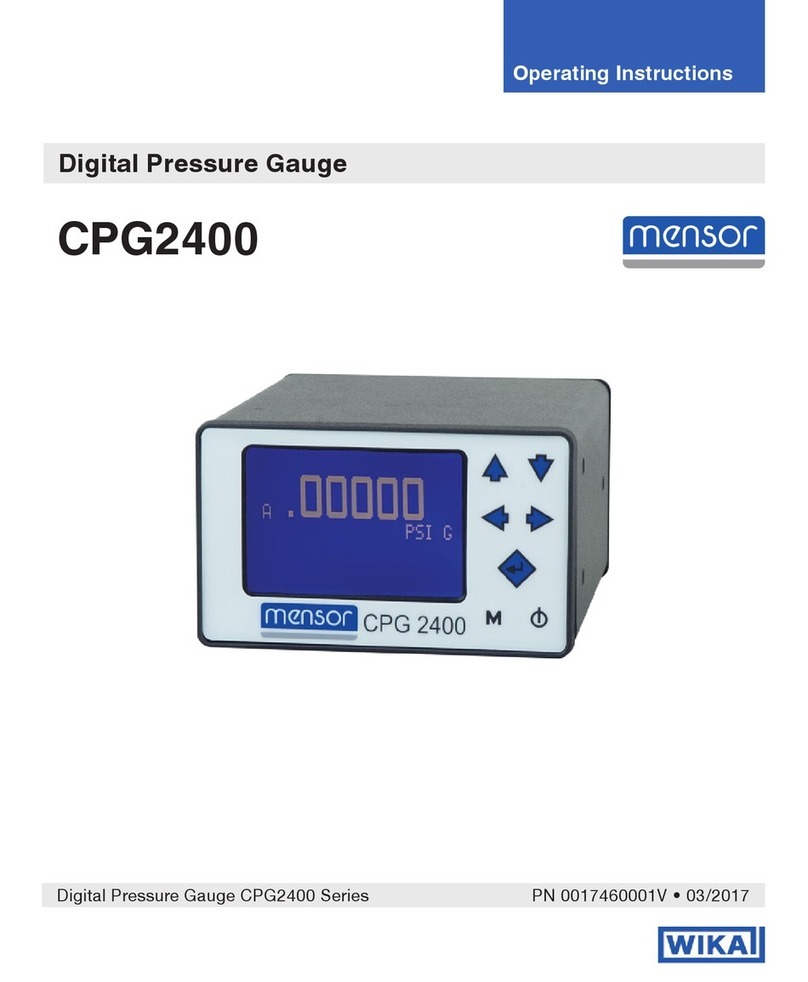
WIKA
WIKA mensor CPG2400 operating instructions

Bosch
Bosch Tronic 3000T Installation manual and operating instructions