REXROTH IndraDrive Fc FCS01 User manual

Rexroth IndraDrive Fc
Drive Controllers
Frequency Converters FCS01
R911310845
Edition 01
Operating Instructions
Electric Drives
and Controls Pneumatics Service
Linear Motion and
Assembly Technologies
Hydraulics

About this Documentation Rexroth IndraDrive FCS01.1
DOK-INDRV*--FCS01*****-IB01_EN-P
Rexroth IndraDrive Fc
Drive Controllers
Frequency Converters FCS01
Operating Instructions
DOK-INDRV*-FCS01*****-IB01-EN-P
Document Number, 120-2400-B323-01-EN
This documentation provides information on:
• the mechanical and electrical assembly
• the conditions of connection
• the commissioning of the devices
• the basic parameterization of the devices
• the error messages with information on causes and remedies
Description Release
Date
Notes
DOK-INDRV*-FCS01******-IB01-EN-P Feb.06 First Edition
2006 Bosch Rexroth AG
Copying this document, giving it to others and the use or communication
of the contents thereof without express authority, are forbidden. Offenders
are liable for the payment of damages. All rights are reserved in the event
of the grant of a patent or the registration of a utility model or design
(DIN 34-1).
The specified data is for product description purposes only and may not
be deemed to be guaranteed unless expressly confirmed in the contract.
All rights are reserved with respect to the content of this documentation
and the availability of the product.
Bosch Rexroth AG
Bgm.-Dr.-Nebel-Str. 2 •D-97816 Lohr a. Main
Telephone +49 (0)93 52/40-0 •Tx 68 94 21 •Fax +49 (0)93 52/40-48 85
http://www.boschrexroth.com/
Dept. EDY1 (rr/hp/bb)
This document has been printed on chlorine-free bleached paper.
Title
Type of Documentation
Document Typecode
Internal File Reference
Purpose of Documentation
Record of Revisions
Copyright
Validity
Published by
Note

Rexroth IndraDrive FCS01.1 Contents I
DOK-INDRV*--FCS01*****-IB01_EN-P
Contents
1 Introduction 1-1
1.1 About this Documentation............................................................................................................. 1-1
1.2 Abbreviations Used....................................................................................................................... 1-2
1.3 Introducing the System ................................................................................................................. 1-4
Rexroth IndraDrive C and Rexroth IndraDrive Fc ................................................................... 1-4
2 Safety Instructions for Electric Drives and Controls 2-1
2.1 General Information ...................................................................................................................... 2-1
Using the Safety Instructions and Passing them on to Others................................................ 2-1
Instructions for Use.................................................................................................................. 2-1
Explanation of Warning Symbols and Degrees of Hazard Seriousness ................................. 2-3
2.2 Hazards by Improper Use............................................................................................................. 2-4
2.3 Instructions with Regard to Specific Dangers............................................................................... 2-5
Protection Against Contact with Electrical Parts ..................................................................... 2-5
2.4 Protection Against Electric Shock by Protective Low Voltage (PELV) ......................................... 2-7
2.5 Protection Against Dangerous Movements .................................................................................. 2-7
2.6 Protection Against Magnetic and Electromagnetic Fields During Operation and
Mounting ....................................................................................................................................... 2-9
2.7 Protection Against Contact with Hot Parts.................................................................................. 2-10
2.8 Protection During Handling and Mounting.................................................................................. 2-11
2.9 Battery Safety ............................................................................................................................. 2-11
2.10 Protection Against Pressurized Systems.................................................................................... 2-12
3 Important Directions for Use 3-1
3.1 Appropriate Use............................................................................................................................ 3-1
Introduction .............................................................................................................................. 3-1
Areas of Use and Application .................................................................................................. 3-2
3.2 Inappropriate Use ......................................................................................................................... 3-2
4 Brief Description 4-1
4.1 General Information ...................................................................................................................... 4-1
4.2 FCS01 Properties FCS01 ............................................................................................................. 4-1
5 Delivery 5-1
5.1 Scope of Supply............................................................................................................................ 5-1
6 Certifications and Types 6-1
6.1 Certifications ................................................................................................................................. 6-1

II Contents Rexroth IndraDrive FCS01.1
DOK-INDRV*--FCS01*****-IB01_EN-P
CE Conformity ......................................................................................................................... 6-1
UL and cUL Certification.......................................................................................................... 6-1
6.2 Type Codes .................................................................................................................................. 6-2
Type Code Frequency Converter FCS01................................................................................ 6-2
Type Code FCC01 Function Module....................................................................................... 6-2
Type Code FLR01 Braking Resistor........................................................................................ 6-3
Accessories FAS01 Type Code (Temperature Switch)........................................................... 6-3
Accessories FAS02 Type Code (Shield Connection).............................................................. 6-4
6.3 IndraDrive Fc Components........................................................................................................... 6-5
7 Mounting 7-1
7.1 Mounting ....................................................................................................................................... 7-1
7.2 Dimensions of the FCS01 Frequency Converter.......................................................................... 7-2
8 Installation 8-1
8.1 Wall Mounting Bracket FCS01...................................................................................................... 8-1
8.2 FLR01 Braking Resistors.............................................................................................................. 8-2
Technical Data FLR01 ............................................................................................................. 8-4
8.3 Wiring Directives ........................................................................................................................... 8-7
8.4 Connection of Electrical Power................................................................................................... 8-10
X3, System Connection (PE, L1, L2/N, L3) ........................................................................... 8-12
X31, Relay 1 (1, 2), Relay 2 (3, 4) ......................................................................................... 8-13
X5, Connection of Motor Cable (PE, U, V, W)....................................................................... 8-13
X5, Connection of Braking Resistor (+B, -B) ......................................................................... 8-14
X5, DC Coupling (+B, -DC).................................................................................................... 8-15
Settings to Reduce the Leakage Currents ............................................................................ 8-16
8.5 Electrical Control Connectors ..................................................................................................... 8-18
9 Indications and Operation of the Function Modules 9-1
9.1 Indicator Elements at the FCS01 Basic Device............................................................................ 9-1
9.2 Modules FCC01............................................................................................................................ 9-1
9.3 Overview over FCC01 Function Modules..................................................................................... 9-2
Standard Control Panel FCC01.1T-STD-NNNN ..................................................................... 9-4
Comfort Control Panel FCC01.1T-CMF-NNNN....................................................................... 9-8
Parameters of the Comfort Control Panel ............................................................................. 9-16
Error Messages Comfort Control Panel ................................................................................ 9-19
9.4 Master Communication Module..................................................................................................9-22
9.5 Profibus Module FCC01.1F-PB1-NNNN / -PB2-NNNN.............................................................. 9-22
CANopen Module FCC01.1F-CN1-NNNN ............................................................................ 9-25
DeviceNet Module FCC01.1F-DN1-NNNN ........................................................................... 9-27
10 Commissioning 10-1
1.1 Basic Settings ............................................................................................................................. 10-1
1.2 Minimum Configuration of the Control Connections ................................................................... 10-3
11 Parameterization 11-1

Rexroth IndraDrive FCS01.1 Contents III
DOK-INDRV*--FCS01*****-IB01_EN-P
11.1 Status Indication ......................................................................................................................... 11-4
11.2 Basic Parameters ....................................................................................................................... 11-6
11.3 Motor Data / Characteristics Parameter ................................................................................... 11-12
11.4 Control Terminals ..................................................................................................................... 11-17
11.5 Additional Parameter ................................................................................................................ 11-34
11.6 Information................................................................................................................................ 11-45
11.7 Pertinent Parameters, User Settings ........................................................................................ 11-52
12 Error Messages 12-1
12.1 Indicator Elements at the FCS01 Basic Device.......................................................................... 12-1
12.2 Indication in the Function Modules FCC01.1T-xxx..................................................................... 12-1
13 Technical Data 13-1
13.1 General Data FCS01 .................................................................................................................. 13-1
13.2 Electrical Data............................................................................................................................. 13-2
Electrical Data of the 230 V Devices ..................................................................................... 13-2
Electrical Data of the 400 V Devices ..................................................................................... 13-3
Derating of the electrical data................................................................................................ 13-4
13.3 Electrical Data for UL/cUL Certification ...................................................................................... 13-8
13.4 Electromagnetic Compatibility (EMC)......................................................................................... 13-9
Realizable EMC Limit Value Classes (in preparation)......................................................... 13-10
14 Additional Information 14-1
14.1 Setpoint Processing in FCS01.................................................................................................... 14-1
14.2 Process Controller ...................................................................................................................... 14-2
Sample application process controller................................................................................... 14-3
Process Controller Parameter Settings ................................................................................. 14-4
15 Control Communication - Field Busses and Protocols 15-1
15.1 Overview ..................................................................................................................................... 15-1
15.2 Profibus DP................................................................................................................................. 15-2
Profibus Protocol ................................................................................................................... 15-2
Profibus Bus Description ....................................................................................................... 15-3
Parameterization of the Profibus ........................................................................................... 15-4
Profibus Error Monitoring and Indication ............................................................................... 15-5
Profibus - Structure of the Useful Data.................................................................................. 15-6
Profibus Telegram Structure.................................................................................................. 15-8
Profibus Data Transfer - Sample Telegrams....................................................................... 15-19
Profibus Data Transfer - Status Machine ............................................................................ 15-22
PROFIDRIVE Standard Parameter ..................................................................................... 15-24
Consistent Data Transmission............................................................................................. 15-24
15.3 CANopen .................................................................................................................................. 15-25
CANopen Protocol............................................................................................................... 15-26
CANopen Bus Description................................................................................................... 15-27
CANopen Parameterization................................................................................................. 15-27
CANopen Error Monitoring and Indication.......................................................................... 15-29

IV Contents Rexroth IndraDrive FCS01.1
DOK-INDRV*--FCS01*****-IB01_EN-P
CANopen Data Transfer - Process Data Objects PDO ....................................................... 15-30
CANopen Telegram Structure ............................................................................................. 15-32
CANopen Data Transfer - Example..................................................................................... 15-35
CANopen Data Transfer - Status Machine.......................................................................... 15-36
CANopen Object Directory .................................................................................................. 15-36
CANopen Drive Profiles....................................................................................................... 15-38
15.4 Universal Serial Interface Protocol - USIP................................................................................ 15-41
USI Protocol......................................................................................................................... 15-41
USIP Bus Description .......................................................................................................... 15-42
USI Parameterization .......................................................................................................... 15-44
USIP Data Transfer - Structure of the Useful data .............................................................. 15-47
USIP Telegram Structure .................................................................................................... 15-48
USIP Data Transfer - Sample Telegrams............................................................................ 15-49
USIP Data Transfer - Status Machine ................................................................................. 15-54
USIP Data Transfer - Master Telegram Times.................................................................... 15-55
15.5 DeviceNet ................................................................................................................................. 15-56
DeviceNet Protocol.............................................................................................................. 15-56
DeviceNet Bus Description.................................................................................................. 15-57
DeviceNet Parameterization................................................................................................ 15-58
DeviceNet Error Monitoring and Indication.......................................................................... 15-60
DeviceNet Telegram Structure ............................................................................................ 15-61
DeviceNet Data Transfer - Status Machine......................................................................... 15-62
DeviceNet Object Classes................................................................................................... 15-63
16 Disposal and Environmental Protection 16-1
16.1 Disposal...................................................................................................................................... 16-1
Products................................................................................................................................. 16-1
Packaging Materials.............................................................................................................. 16-1
16.2 Environmental Protection............................................................................................................ 16-1
No Releaseof Hazardous Substances ................................................................................. 16-1
Materials Contained in the Products ..................................................................................... 16-1
Recycling ............................................................................................................................... 16-2
17 Index 17-1

Rexroth IndraDrive FCS01.1 Introduction 1-1
DOK-INDRV*--FCS01*****-IB01_EN-P
1 Introduction
1.1 About this Documentation
WARNING
Personal injury and property damage caused by
incorrect project planning for applications,
machines and installations!
⇒Take contents of the listed reference
documentations into account.
This documentation provides information on ...
•…a presentation of the documentations on the drive system
Rexroth IndraDrive Fc
•…help for selecting the system components of the drive system
Rexroth IndraDrive Fc
These Operating Instructions comprise information on
•Assembly and installation
•Technical data of the individual components (as far as relevant for the
operation).
•Current, voltage and performance data
•Dimensions and weights, and
•Pin assignment
This documentation contains safety regulations, technical data and
operating instructions for the drive system Rexroth IndraDrive Fc. The
individual chapters have the following main focuses:
Purpose of Documentation
Content of this documentation

1-2 Introduction Rexroth IndraDrive FCS01.1
DOK-INDRV*--FCS01*****-IB01_EN-P
Chapter Title Contents
1 Introduction General
information
2 Safety Instructions for Electric Drives and
Controls
3 Important Directions for Use
Safety
4 Brief Description
5 Delivery
6 Certifications and Types
7 Mounting
8 Installation
Product description
(for those doing project
planning)
9 Display and Operation of the Function
Modules
10 Commissioning
11 Parameterization
12 Error Messages
13 Technical Data
14 Additional Information
15 Control Communication - Field Busses
and Protocols
Practical application
(for operators and
maintenance staff)
16 Disposal and Environmental Protection General Information
Fig. 1-1: Main focuses of the Chapters
1.2 Abbreviations Used
This documentation uses the following abbreviations:
Abbr. Significance Contents
FC Frequency converter
PPO Parameter process data object
PIDV Parameter ID value
PCD Process data
PID Parameter ID
IND Index
PV Parameter value
CTW Control word
STW Status word
CV1..3 Setpoint value 1-3
AV1..3 Actual value 1-3
Fig. 1-2: Abbreviations used
Main focuses of the Chapters

Rexroth IndraDrive FCS01.1 Introduction 1-3
DOK-INDRV*--FCS01*****-IB01_EN-P
Reference Documentations - Overview
Title Kind of documentation Document typecode1)
Rexroth IndraDrive
Additional Components
System Configuration DOK-INDRV*-ADDCOMP****-PRxx-EN-P
Rexroth Connection Cables Selection Data DOK-CONNEC-CABLE*STAND-AUxx-EN-P
Third-party motors Project Planning and
Commissioning Manual
DOK-DRIVE*-3RDPART*MOT-AWxx-EN-P
safety instructions for electric drives and
controls
Safety Guidelines DOK-GENERAL-DRIVE******-SVSx-MS-P
1) In the documentation types, "xx" is a wildcard for the current version
status of the documentation (example: PR01 stands for the first
version of a system configuration)
Fig. 1-3: Documentations - overview
Standards
German, European and international technical standards are mentioned
in this documentation. Standard documents and sheets are subject to
copyright protection and Rexroth mustn't pass them on.
If required, contact the authorized sales agencies; in Germany directly
contact:
BEUTH Verlag GmbH
Burggrafenstrasse 6
10787 Berlin
Phone +49-(0)30-26 01-22 60, Fax +49-(0)30-26 01-12 60
Internet: http://www.beuth.de/
Email: postm[email protected]
Your Feedback
Your experience is important for our improvement processes of products
and documentations.
Inform us about mistakes you discovered and change requests; we would
be grateful for your feedback.
Please send your remarks to:
Bosch Rexroth AG
Dept. BRC/EDY
Bürgermeister-Dr.-Nebel-Str. 2
D-97816 Lohr, Germany

1-4 Introduction Rexroth IndraDrive FCS01.1
DOK-INDRV*--FCS01*****-IB01_EN-P
1.3 Introducing the System
The Rexroth IndraDrive Fc drive system comprises the individual
components (the system elements) which are required for application and
utilization in the respective case:
•FCS01 frequency converter
•FCC01 function module
•FWA-INDRV*-FCB firmware
•Standard asynchronous motor
•Power transformer as an optional component
•Mains filter as an optional components
•Mains choke as optional components
•Braking resistor as additional component
System Elements - Components of the System
The drive system Rexroth IndraDrive Fc consists of the following system
elements:
System elements Types Characteristics Requirement
autotransformer DST optionaltransformer
isolating
transformer
DLT optional
1-phase NFE optionalmains filter
3-phase NFD03.1;
HNF01.1;
optional
mains choke standard FNL01.1E optional
Frequency converter single-axis FCS01.1 standard
firmware FCB01 standard
control panels FCC01.1T optionalFunction module
Field bus module FCC01.1F optional
Braking resistor FLR01.1 optional
Output throttle FML01 optional
shielded RKL standardMotor cable
unshielded RKL optional
Motor Standard asyn-
chronous motor
standard
Fig. 1-4: System elements Rexroth IndraDrive
Rexroth IndraDrive C and Rexroth IndraDrive Fc
Differences
Compared to the units HCS02 and HCS03 of the IndraDrive C product
family, the FCS01 units of the IndraDrive FC product family display a
narrower power range, and their functionality scalability is smaller than
that of the former. Primarily the FCS01 unit specialize in OpenLoop
operation.
Compatibility
It is not possible to couple the FCS01 units via a shared DC bus to the
HCS02 units.
Drive System,
Definition of Term

Rexroth IndraDrive FCS01.1 Safety Instructions for Electric Drives and Controls 2-1
DOK-INDRV*--FCS01*****-IB01_EN-P
2 Safety Instructions for Electric Drives and Controls
2.1 General Information
Using the Safety Instructions and Passing them on to Others
Do not attempt to install or commission this device without first reading all
documentation provided with the product. Read and understand these
safety instructions and all user documentation prior to working with the
device. If you do not have the user documentation for the device, contact
your responsible Bosch Rexroth sales representative. Ask for these
documents to be sent immediately to the person or persons responsible
for the safe operation of the device.
If the device is resold, rented and/or passed on to others in any other
form, then these safety instructions must be delivered with the device.
WARNING
Improper use of these devices, failure to follow
the safety instructions in this document or
tampering with the product, including disabling
of safety devices, may result in material
damage, bodily harm, electric shock or even
death!
Instructions for Use
•Read these instructions before the initial startup of the equipment in
order to eliminate the risk of bodily harm or material damage. Follow
these safety instructions at all times.
•Bosch Rexroth AG is not liable for damages resulting from failure to
observe the warnings provided in this documentation.
•Read the operating, maintenance and safety instructions in your
language before starting up the machine. If you find that you cannot
completely understand the documentation for your product, please ask
your supplier to clarify.
•Proper and correct transport, storage, assembly and installation as
well as care in operation and maintenance are prerequisites for
optimal and safe operation of this device.
•Only assign trained and qualified persons to work with electrical
installations:
•Only persons who are trained and qualified for the use and
operation of the device may work on this device or within its
proximity. The persons are qualified if they have sufficient
knowledge of the assembly, installation and operation of the
equipment as well as an understanding of all warnings and
precautionary measures noted in these instructions.
•Furthermore, they must be trained, instructed and qualified to
switch electrical circuits and devices on and off in accordance with
technical safety regulations, to ground them and to mark them
according to the requirements of safe work practices. They must
have adequate safety equipment and be trained in first aid.
•Only use spare parts and accessories approved by the manufacturer.
•Follow all safety regulations and requirements for the specific
application as practiced in the country of use.

2-2 Safety Instructions for Electric Drives and Controls Rexroth IndraDrive FCS01.1
DOK-INDRV*--FCS01*****-IB01_EN-P
•The devices have been designed for installation in industrial
machinery.
•The ambient conditions given in the product documentation must be
observed.
•Only use safety-relevant applications that are clearly and explicitly
approved in the Project Planning Manual. If this is not the case, they
are excluded.
Safety-relevant are all such applications which can cause danger to
persons and material damage.
•The information given in the documentation of the product with regard
to the use of the delivered components contains only examples of
applications and suggestions.
The machine and installation manufacturer must
•make sure that the delivered components are suited for his
individual application and check the information given in this
documentation with regard to the use of the components,
•make sure that his application complies with the applicable safety
regulations and standards and carry out the required measures,
modifications and complements.
•Startup of the delivered components is only permitted once it is sure
that the machine or installation in which they are installed complies
with the national regulations, safety specifications and standards of the
application.
•Operation is only permitted if the national EMC regulations for the
application are met.
•The instructions for installation in accordance with EMC requirements
can be found in the documentation "EMC in Drive and Control
Systems".
•The machine or installation manufacturer is responsible for
compliance with the limiting values as prescribed in the national
regulations.
Technical data, connections and operational conditions are specified in
the product documentation and must be followed at all times.

Rexroth IndraDrive FCS01.1 Safety Instructions for Electric Drives and Controls 2-3
DOK-INDRV*--FCS01*****-IB01_EN-P
Explanation of Warning Symbols and Degrees of Hazard Seriousness
The safety instructions describe the following degrees of hazard
seriousness. The degree of hazard seriousness informs about the
consequences resulting from non-compliance with the safety instructions:
Warning symbol with signal
word
Degree of hazard seriousness according
to ANSI Z 535
DANGER
Death or severe bodily harm will occur.
WARNING
Death or severe bodily harm may occur.
CAUTION
Bodily harm or material damage may occur.
Fig. 2-1: Hazard classification (according to ANSI Z 535)

2-4 Safety Instructions for Electric Drives and Controls Rexroth IndraDrive FCS01.1
DOK-INDRV*--FCS01*****-IB01_EN-P
2.2 Hazards by Improper Use
DANGER
High electric voltage and high working current!
Risk of death or severe bodily injury by electric
shock!
DANGER
Dangerous movements! Danger to life, severe
bodily harm or material damage by
unintentional motor movements!
WARNING
High electric voltage because of incorrect
connection! Risk of death or bodily injury by
electric shock!
WARNING
Health hazard for persons with heart
pacemakers, metal implants and hearing aids in
proximity to electrical equipment!
CAUTION
Hot surfaces on device housing! Danger of
injury! Danger of burns!
CAUTION
Risk of injury by improper handling! Risk of
bodily injury by bruising, shearing, cutting,
hitting, or improper handling of pressurized
lines!
CAUTION
Risk of injury by improper handling of batteries!

Rexroth IndraDrive FCS01.1 Safety Instructions for Electric Drives and Controls 2-5
DOK-INDRV*--FCS01*****-IB01_EN-P
2.3 Instructions with Regard to Specific Dangers
Protection Against Contact with Electrical Parts
Note: This section only concerns devices and drive components with
voltages of more than 50 Volt.
Contact with parts conducting voltages above 50 Volts can cause
personal danger and electric shock. When operating electrical equipment,
it is unavoidable that some parts of the devices conduct dangerous
voltage.
DANGER
High electrical voltage! Danger to life, electric
shock and severe bodily injury!
⇒Only those trained and qualified to work with or on
electrical equipment are permitted to operate,
maintain and repair this equipment.
⇒Follow general construction and safety regulations
when working on electrical power installations.
⇒Before switching on the device, the equipment
grounding conductor must have been non-
detachably connected to all electrical equipment in
accordance with the connection diagram.
⇒Do not operate electrical equipment at any time,
even for brief measurements or tests, if the
equipment grounding conductor is not permanently
connected to the mounting points of the components
provided for this purpose.
⇒Before working with electrical parts with voltage
potentials higher than 50 V, the device must be
disconnected from the mains voltage or power
supply unit. Provide a safeguard to prevent
reconnection.

2-6 Safety Instructions for Electric Drives and Controls Rexroth IndraDrive FCS01.1
DOK-INDRV*--FCS01*****-IB01_EN-P
⇒With electrical drive and filter components, observe
the following:
Wait 30 minutes after switching off power to allow
capacitors to discharge before beginning to work.
Measure the voltage on the capacitors before
beginning to work to make sure that the equipment is
safe to touch.
⇒Never touch the electrical connection points of a
component while power is turned on.
⇒Install the covers and guards provided with the
equipment properly before switching the device on.
Before switching the equipment on, cover and
safeguard live parts safely to prevent contact with
those parts.
⇒A residual-current-operated circuit-breaker or r.c.d.
cannot be used for electric drives! Indirect contact
must be prevented by other means, for example, by
an overcurrent protective device according to the
relevant standards.
⇒Secure built-in devices from direct touching of
electrical parts by providing an external housing, for
example a control cabinet.
European countries: according to EN 50178/ 1998,
section 5.3.2.3.
USA: See National Electrical Code (NEC), National
Electrical Manufacturers' Association (NEMA), as well as
local engineering regulations. The operator must observe
all the above regulations at any time.
With electrical drive and filter components, observe the following:
DANGER
High housing voltage and large leakage current!
Risk of death or bodily injury by electric shock!
⇒Before switching on, the housings of all electrical
equipment and motors must be connected or
grounded with the equipment grounding conductor to
the grounding points. This is also applicable before
short tests.
⇒The equipment grounding conductor of the electrical
equipment and the units must be non-detachably
and permanently connected to the power supply unit
at all times. The leakage current is greater than
3.5 mA.
⇒Over the total length, use copper wire of a cross
section of a minimum of 10 mm
2
for this equipment
grounding connection!
⇒Before start-up, also in trial runs, always attach the
equipment grounding conductor or connect with the
ground wire. Otherwise, high voltages may occur at
the housing causing electric shock.

Rexroth IndraDrive FCS01.1 Safety Instructions for Electric Drives and Controls 2-7
DOK-INDRV*--FCS01*****-IB01_EN-P
2.4 Protection Against Electric Shock by Protective Low
Voltage (PELV)
All connections and terminals with voltages between 5 and 50 Volt at
Rexroth products are protective extra-low voltage systems which are
provided with touch guard according to the product standards.
WARNING
High electric voltage by incorrect connection!
Risk of death or bodily injury by electric shock!
⇒To all connections and terminals with voltages
between 0 and 50 Volt, only devices, electrical
components, and conductors may be connected
which are equipped with a PELV (Protective Extra-
Low Voltage) system.
⇒Connect only voltages and circuits which are safely
isolated from dangerous voltages. Safe isolation is
achieved for example by isolating transformers, safe
optocouplers or battery operation without mains
connection.
2.5 Protection Against Dangerous Movements
Dangerous movements can be caused by faulty control of connected
motors. Some common examples are:
•improper or wrong wiring of cable connections
•incorrect operation of the equipment components
•wrong input of parameters before operation
•malfunction of sensors, encoders and monitoring devices
•defective components
•software or firmware errors
Dangerous movements can occur immediately after equipment is
switched on or even after an unspecified time of trouble-free operation.
The monitoring in the drive components will normally be sufficient to avoid
faulty operation in the connected drives. Regarding personal safety,
especially the danger of bodily harm and material damage, this alone
cannot be relied upon to ensure complete safety. Until the integrated
monitoring functions become effective, it must be assumed in any case
that faulty drive movements will occur. The extent of faulty drive
movements depends upon the type of control and the state of operation.

2-8 Safety Instructions for Electric Drives and Controls Rexroth IndraDrive FCS01.1
DOK-INDRV*--FCS01*****-IB01_EN-P
DANGER
Dangerous movements! Danger to life, risk of
injury, severe bodily harm or material damage!
⇒For the above reasons, ensure personal safety by
means of qualified and tested higher-level monitoring
devices or measures integrated in the installation.
They have to be provided for by the user according
to the specific conditions within the installation and a
hazard and fault analysis. The safety regulations
applicable for the installation have to be taken into
consideration. Unintended machine motion or other
malfunction is possible if safety devices are disabled,
bypassed or not activated.
To avoid accidents, bodily harm and/or material
damage:
⇒Keep free and clear of the machine’s range of
motion and moving parts. Possible measures to
prevent people from accidentally entering the
machine’s range of motion:
•- use safety fences
•- use safety guards
•- use protective coverings
•- install light curtains or light barriers
⇒Fences and coverings must be strong enough to
resist maximum possible momentum.
⇒Mount the emergency stop switch in the immediate
reach of the operator. Verify that the emergency stop
works before startup. Don’t operate the device if the
emergency stop is not working.
⇒Isolate the drive power connection by means of an
emergency stop circuit or use a safety related
starting lockout to prevent unintentional start.
⇒Make sure that the drives are brought to a safe
standstill before accessing or entering the danger
zone.
⇒Additionally secure vertical axes against falling or
dropping after switching off the motor power by, for
example:
- mechanically securing the vertical axes,
- adding an external braking/ arrester/ clamping
mechanism or
- ensuring sufficient equilibration of the vertical
axes.
The standard equipment motor brake or an external
brake controlled directly by the drive controller are
not sufficient to guarantee personal safety!

Rexroth IndraDrive FCS01.1 Safety Instructions for Electric Drives and Controls 2-9
DOK-INDRV*--FCS01*****-IB01_EN-P
⇒Disconnect electrical power to the equipment using a
master switch and secure the switch against
reconnection for:
- maintenance and repair work
- cleaning of equipment
- long periods of discontinued equipment use
⇒Prevent the operation of high-frequency, remote
control and radio equipment near electronics circuits
and supply leads. If the use of such devices cannot
be avoided, verify the system and the installation for
possible malfunctions in all possible positions of
normal use before initial startup. If necessary,
perform a special electromagnetic compatibility
(EMC) test on the installation.
2.6 Protection Against Magnetic and Electromagnetic Fields
During Operation and Mounting
Magnetic and electromagnetic fields generated by current-carrying
conductors and permanent magnets in motors represent a serious
personal danger to those with heart pacemakers, metal implants and
hearing aids.
WARNING
Health hazard for persons with heart
pacemakers, metal implants and hearing aids in
proximity to electrical equipment!
⇒Persons with heart pacemakers and metal implants
are not permitted to enter following areas:
- Areas in which electrical equipment and parts are
mounted, being operated or commissioned.
- Areas in which parts of motors with permanent
magnets are being stored, repaired or mounted.
⇒If it is necessary for somebody with a pacemaker to
enter such an area, a doctor must be consulted prior
to doing so. The interference immunity of present or
future implanted heart pacemakers differs greatly, so
that no general rules can be given.
⇒Those with metal implants or metal pieces, as well
as with hearing aids must consult a doctor before
they enter the areas described above. Otherwise
health hazards may occur.

2-10 Safety Instructions for Electric Drives and Controls Rexroth IndraDrive FCS01.1
DOK-INDRV*--FCS01*****-IB01_EN-P
2.7 Protection Against Contact with Hot Parts
CAUTION
Hot surfaces at motor housings, on drive
controllers or chokes! Danger of injury! Danger
of burns!
⇒Do not touch surfaces of device housings and
chokes in the proximity of heat sources! Danger of
burns!
⇒Do not touch housing surfaces of motors! Danger of
burns!
⇒According to operating conditions, temperatures can
be higher than 60 °C, 140 °F during or after
operation.
⇒Before accessing motors after having switched them
off, let them cool down for a sufficiently long time.
Cooling down can require up to 140 minutes!
Roughly estimated, the time required for cooling
down is five times the thermal time constant
specified in the Technical Data.
⇒After switching drive controllers or chokes off, wait
15 minutes to allow them to cool down before
touching them.
⇒Wear safety gloves or do not work at hot surfaces.
⇒For certain applications, the manufacturer of the end
product, machine or installation, according to the
respective safety regulations, has to take measures
to avoid injuries caused by burns in the end
application. These measures can be, for example:
warnings, guards (shielding or barrier), technical
documentation.
Table of contents
Other REXROTH Controllers manuals
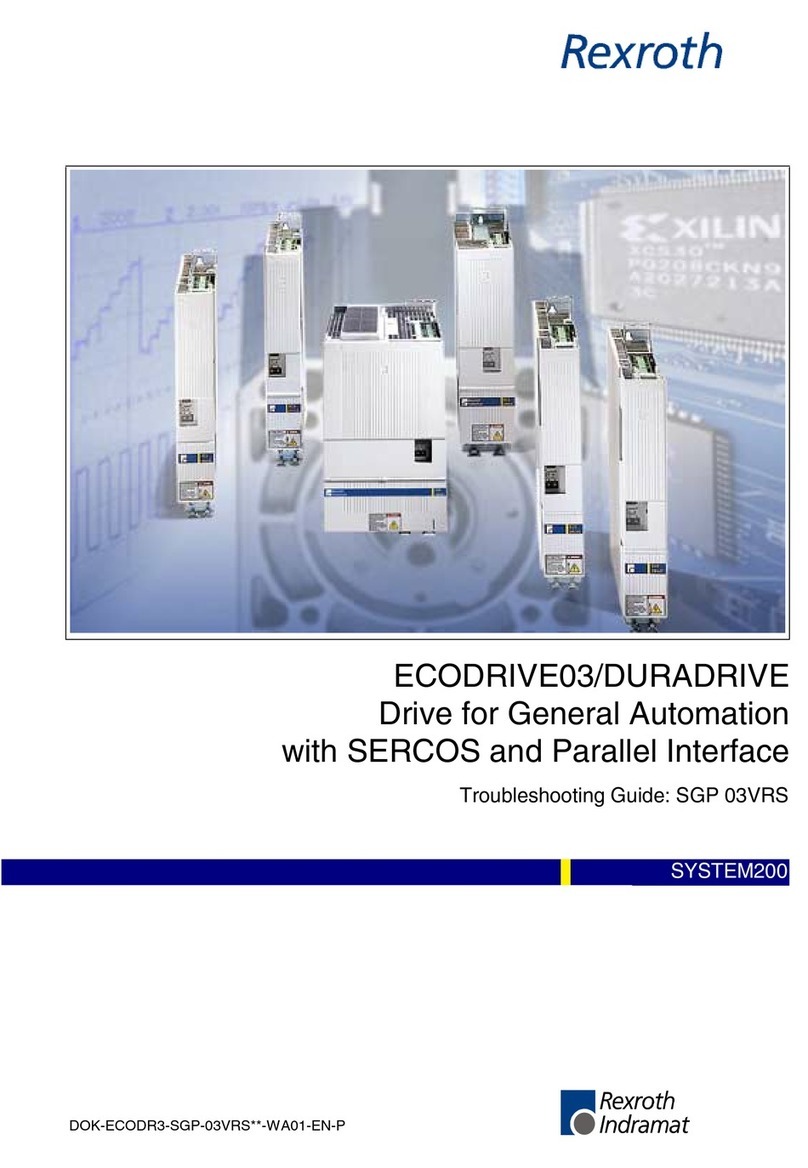
REXROTH
REXROTH ECODRIVE03 User manual
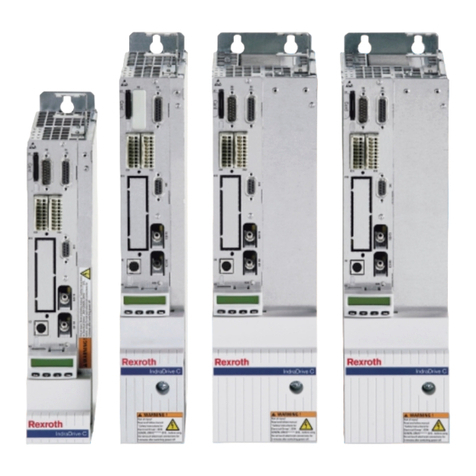
REXROTH
REXROTH IndraDrive C Series Technical manual
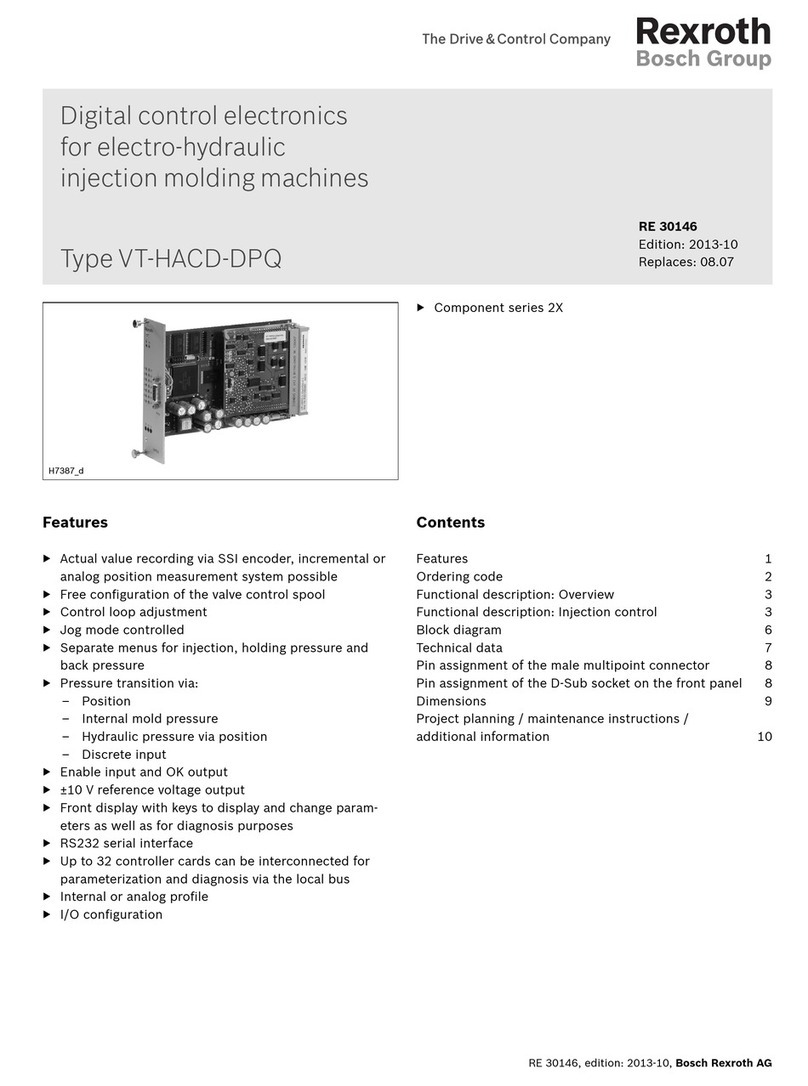
REXROTH
REXROTH VT-HACD-DPQ Series Instruction manual
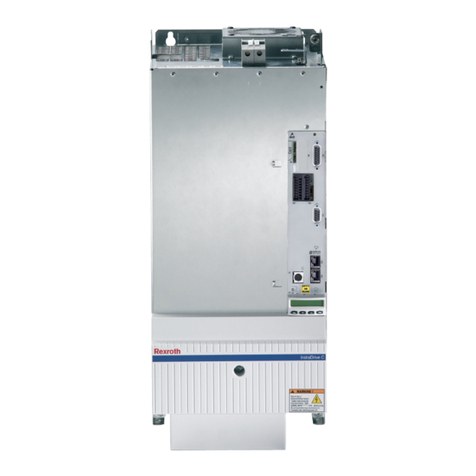
REXROTH
REXROTH HCS03 User manual
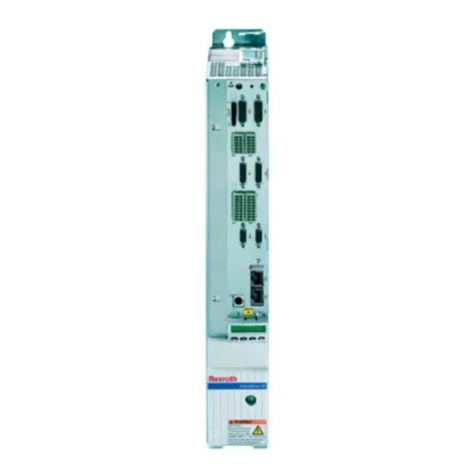
REXROTH
REXROTH IndraDrive M Technical manual
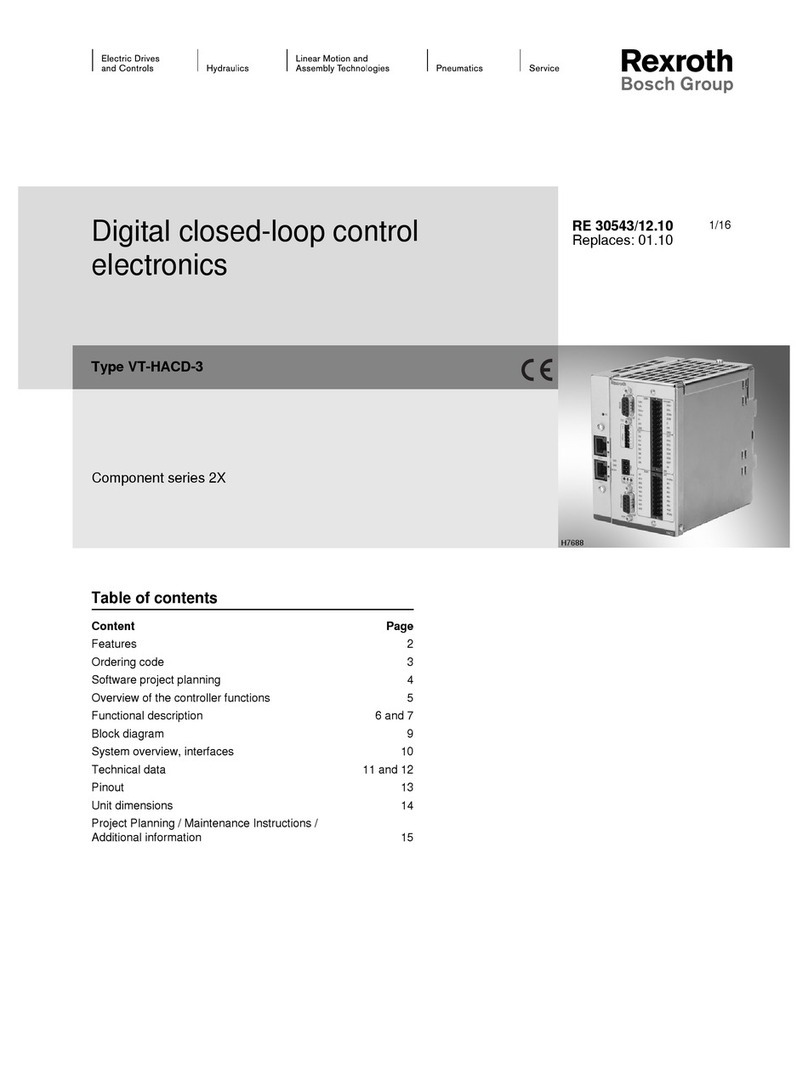
REXROTH
REXROTH VT-HACD-3-2 Series User manual
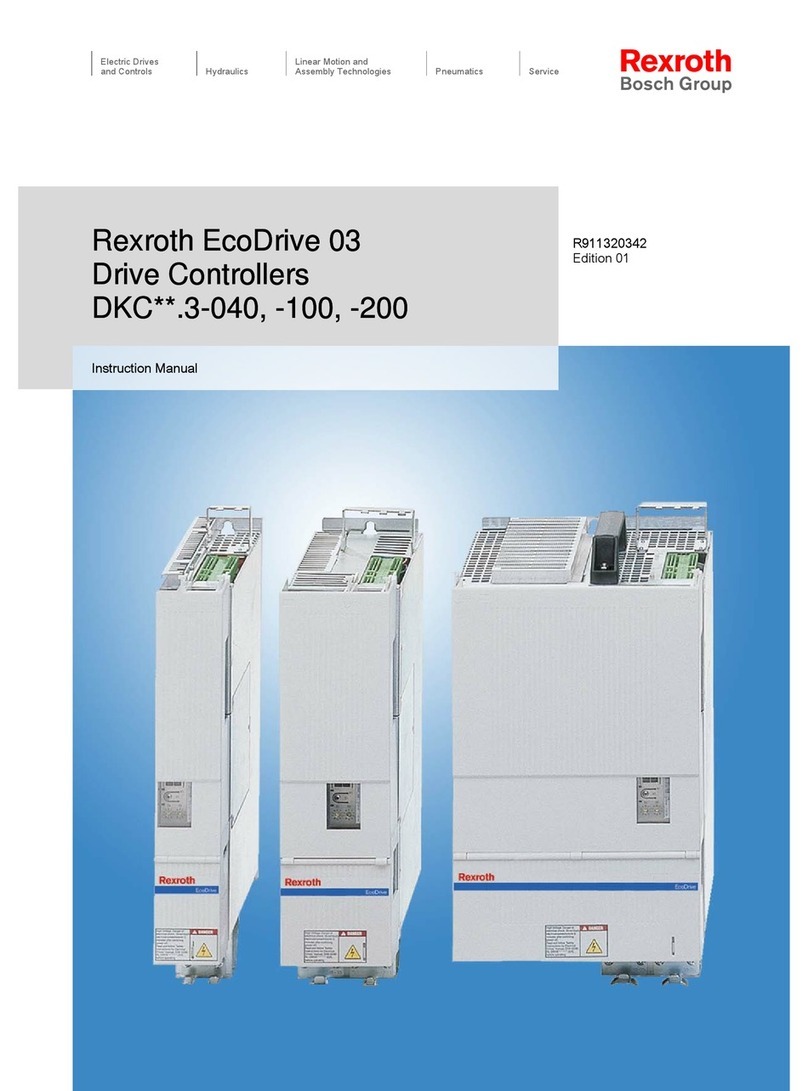
REXROTH
REXROTH EcoDrive 03 User manual
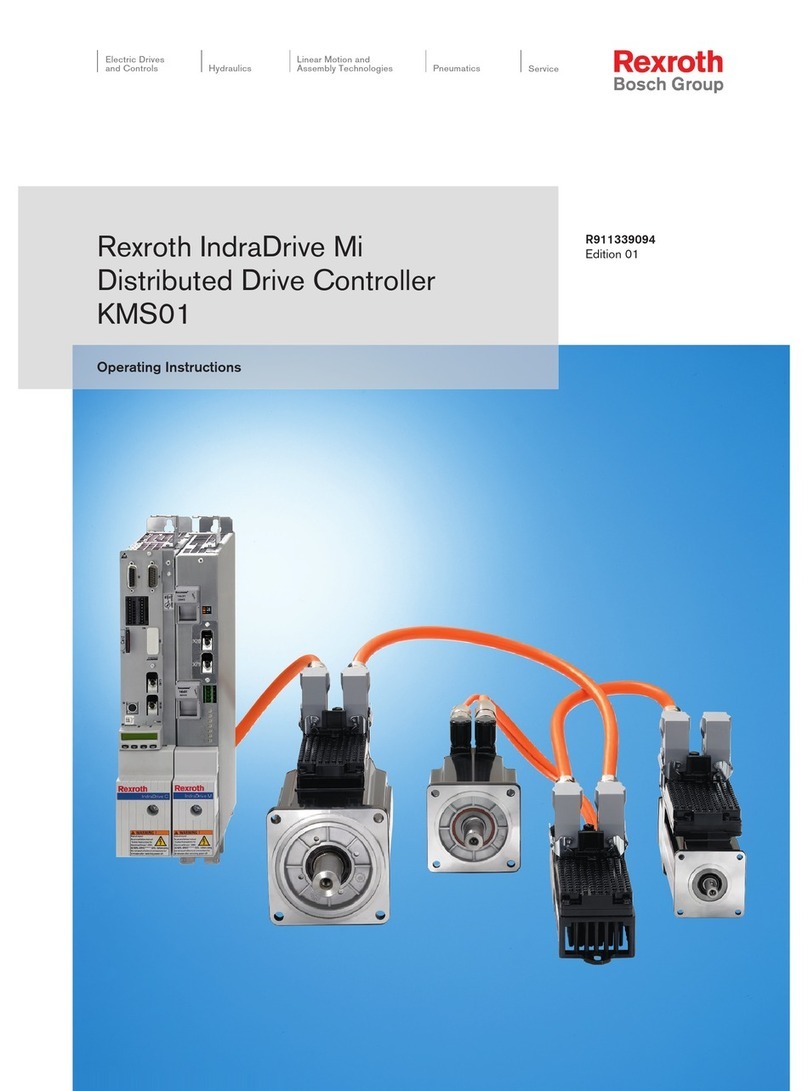
REXROTH
REXROTH IndraDrive Mi User manual

REXROTH
REXROTH CS 550/150 Use and care manual
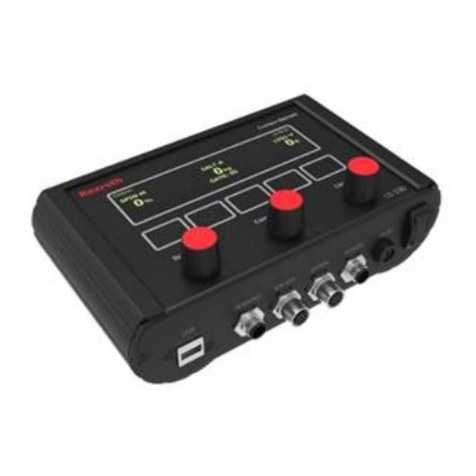
REXROTH
REXROTH CS 530 Instruction sheet