REXROTH VT-HACD-3-2 Series User manual

1/16
Digital closed-loop control
electronics
Type VT-HACD-3
Component series 2X
RE 30543/12.10
Replaces: 01.10
Table of contents
H7688
Content Page
Features 2
Ordering code 3
Software project planning 4
Overview of the controller functions 5
Functional description 6 and 7
Block diagram 9
System overview, interfaces 10
Technical data 11 and 12
Pinout 13
Unit dimensions 14
Project Planning / Maintenance Instructions /
Additional information 15

2/16 Bosch Rexroth AG Hydraulics VT-HACD-3-2X RE 30543/12.10
Features
– Use as closed-loop control electronics for closed control
loops with PIDT1 controller and optional state feedback
– Substitutional closed-loop control (e.g. position control with
superimposed pressure/force control) possible
– Use as command value electronics for generating, linking
and standardizing signals
– Input for digital position measurement systems (2 x SSI or
1 x incremental)
– 6 analog inputs, voltage (±10 V, 0…10 V) and current
(4…20 mA) selectable via software, input resistance
of AI1 > 10 MΩ
– 3 analog outputs, 1x selectable voltage (±10 V, 0…10 V) or
current (0…20 mA, 4…20 mA), 2x voltage (±10 V)
– Numerous possibilities of signal linking and switch-over
– Release input and OK output
– 8 digital inputs
– 7 digital outputs, configurable
– Parameterizable ramp function
– 32 blocks with command values, velocities and controller
parameters
– Adjustment to hydraulic drive by means of area adjustment,
characteristic curve correction, overlap compensation,
residual velocity logic and zero point correction
– +10 V reference voltage output
– Serial interface RS232
– Up to 32 electronics can be interconnected for parameter-
ization and diagnosis via the local bus
Fields of application
– Machine tools
– Plastics processing machines
– Special machines
– Presses
– Transfer systems
Technology functions
– Sequence parameterization
– Positioning
– Pressure control
– Force control
– Tables
Hydraulic axes
– Measurement system:
• Incremental or absolute (SSI, Gray, Binary)
• Analog 0 to ±10 V and 0(4) to 20 mA
– Actuating variable output voltage or current
– Freely configurable controller variants
• Position/pressure/force/velocity controller
• Substitutional closed-loop control (position/pressure)
Programming
– User programming using a PC
Operation
– Comfortable administration of the machine and measuring
data on a PC
Process connection
– Digital inputs and outputs,
– Analog inputs and outputs,
– PROFIBUS DP to communicate with a superior control
– EtherNet/IP
– PROFINET RT
Installation
– Top hat rail 35 mm
CE conformity
– EMC directive 2004/108/EC
Applied harmonized standards:
EN 61000-6-2:2005
EN 61000-6-3:2007
More information
www.boschrexroth.com/hacd

RE 30543/12.10 VT-HACD-3-2X 3/16Hydraulics Bosch Rexroth AG
Ordering code
Included within the scope of delivery:
Mating connector for
– Port X1S (Phoenix Mini Combicon 3-pole)
– Port X2A1 (Weidmüller B2L 3.5/18 LH SN SW)
– Port X2M1 (Weidmüller B2L 3.5/30 LH SN SW
Recommended accessories (can be ordered separately)
Description Material number
Interface cable RS232, length 3 m R900776897
USB-RS232 converter R901066684
Plug-in connector type 6ES7972-0BA41-0XA0 for PROFIBUS DP R900050152
CD with BODAC software SYS-HACD-BODAC-01/ R900777335
Digital closed-loop control electronics
Standard = 3
Component series 20 to 29 = 2X
(20 to 29: unchanged technical data and pinout)
Options
Hardware marking
Position transducer
I = Incremental/SSI
Bus system
0 = Without bus
P = PROFIBUS DP
Ethernet-based:
N = ROFINET RT
E = EtherNet/IP
VT-HACD 3 2X 0 I 00 000

4/16 Bosch Rexroth AG Hydraulics VT-HACD-3-2X RE 30543/12.10
Software project planning
Project planning
The creation of a parameter file forms the basis for the func-
tion of the HACD. The parameter file contains the block struc-
ture of the HACD in which the links of the variables will be
created. The parameter files are created in BODAC. The
parameter file can be created offline and transferred to the
HACD by means of a PC.
This software project planning is implemented according to
the following steps:
1. Selection of the HACD.
2. Application is defined by means of the block structure.
3. Setting of the parameter values (sensors, controllers...).
4. The data is sent to the HACD.
5. Storage of the data in the flash.
6. The setting and the machine sequence are optimized at
the machine.
PC program BODAC
For the implementation of the project planning tasks, the
BODAC PC program is available to the user. It serves the
programming, setting, and diagnosis of the HACD.
Scope of services:
– Comfortable dialog functions for setting the machine data
online or offline
– Dialog window for setting the parameter values online
– Comprehensive options for displaying process variables,
digital inputs, outputs, and flags
– Recording and graphical presentation of up to eight pro-
cess variables with great selection of trigger options
PC-System requirements:
– Windows XP, Windows Vista, Windows 7
– Random access memory (256 MB recommended)
– 250 MB free hard disk capacity
Note:
The BODAC PC program is not included in the scope of de-
livery. It can be downloaded in the Internet free of charge!
Download in the Internet: www.boschrexroth.com/hacd
Inquiries: [email protected]

RE 30543/12.10 VT-HACD-3-2X 5/16Hydraulics Bosch Rexroth AG
Overview of the controller functions
Position controller:
– PDT1 controller
– Linear amplification characteristic curve
– Direction-dependent gain adaptation
– Gain modification via the program possible
– Adaptation of the valve characteristic curve
– Fine positioning
– Residual voltage principle
– Compensation of zero point errors
– State feedback via
• Pressure
• Pressure differential
• Position
– Command value provision
Pressure/force controller:
– PIDT1 controller
– I component switchable via window
– Pressure differential analysis
– Command value provision
Velocity controller:
– PI controller
– I component switchable via window
Monitoring functions:
– Dynamic tracking error monitoring
– Cable break monitoring for incremental and SSI encoder
– Cable break monitoring for sensors
– Cable break monitoring for analog signals

6/16 Bosch Rexroth AG Hydraulics VT-HACD-3-2X RE 30543/12.10
Functional description
The VT-HACD-3-2X closed-loop control electronics is a mod-
ule that is installed on a top hat rail.
A microcontroller controls the entire process, makes adjust-
ments, establishes links and realizes the closed control loops.
Data for configuration, command values and parameters are
stored in a FLASH in a non-volatile form.
The entire configuration and the parameterization and diag-
nosis are carried out via the BODAC PC program. Apart from
the switches for the address setting, the module does not
contain any other hardware switches. For the configuration,
the HACD has to be connected to a PC via a serial interface
(RS 232, 1:1 cable).
The configuration and thus the creation of applications are
very simple - you just have to link pre-defined functional com-
ponents. For this purpose, no programming knowledge is
necessary.
One mode is available:
• Structural editor
Own motion sequences can be created. For this purpose,
32 blocks are available. Each block contains: Command
value, ramp times (velocity ±, acceleration ±) and controller
parameters.
Blocks are activated by setting trigger conditions: Set-
ting digital inputs, comparing signals with freely definable
thresholds or expiry of waiting periods.
Signal links [6] [8] [17]
The HACD offers numerous possibilities for linking signals on
the input and on the output side, whereas it is in each case
possible to link 2 signals. This includes functions like addition,
subtraction, multiplication, division as well as minimum/maxi-
mum value generator, area ratio and limiter:
+ = Addition: Z = X + Y
– = Subtraction: Z = X – Y
* = Multiplication: Z = X * Y / 100
/ = Division: Z = X / Y * 100
MIN = Minimum value generator: Z = MIN (X, Y)
MAX = Maximum value generator: Z = MAX (X, Y)
RATIO = Entry of a ratio:
for RATIO >1: Z = X * RATIO – Y
for RATIO <1: Z = X – Y / RATIO
(e.g. area ratio with pressure differential measurement)
LIMIT = Signal limiter: Z = MIN (|X|, |Y|) * sign (X)
JUMP = Jump generator: Z = MAX (|X|, |Y|) * sign (X)
with Z … Result
X … 1st signal
X … 2nd signal
T1 Lag = Low-pass filter
Analog I/O [1] [15]
For the 6 analog inputs, you can switch between ±10 V,
0…10 V, 0…20 mA by means of the software.
For the analog output AO1, you can switch between ±10 V,
0…10 V, 0…20 mA and 4...20 mA by means of the software.
AO2 and AO3 are fixedly set to ±10 V.
The switching is performed by utilizing the whole range of the
analog-digital converter.
For all analog inputs, working range and error detection can
be defined.
The analog outputs can be adjusted by means of amplifica-
tion and offset.
Digital I/O [3] [16]
The HACD has 9 digital inputs and 8 digital outputs.
An input has the fix functionality Release, a digital output the
fixed functionality OK.
The other digital inputs are used for triggering blocks (see
blocks and triggering).
The function of each digital output can be determined by
means of selection from a pre-defined list:
• Command value = Actual value
• Actual value larger or smaller than an adjustable threshold
• Waiting period expired
• Ramp active
• Internal flag set
• Error flag set
• Table ended
• Error status
• Block timeout
• Controller active
• Absolute value (actual value) < window
• Absolute value (command value) < window
• Incremental home position
[ ] = Assignment to the block diagram on page 8/9

RE 30543/12.10 VT-HACD-3-2X 7/16Hydraulics Bosch Rexroth AG
Functional description (continued)
Digital position measurement system
When using the VT-HACD-3-2X as closed-loop control elec-
tronics, digital position measurement systems of type SSI or
incremental can be used for recording the actual value.
Limitations of use incremental encoder
The maximum frequency of the incremental encoder input (fG)
of the HACD is 250 kHz. The maximum travel velocity of the
drive, the resolution (res) of the encoder system used and the
possible signal analysis by an EXE (interpolation and digitali-
zation electronics) determine the frequency.
Determination formulae
Encoder resolution with given maximum velocity:
fG [kHz] x EXE
Res [μm] ≥ v m x 103
s
Velocity with given encoder resolution:
Res [μm] x EXE x fG [kHz]
v m ≤
s103
Controller
If the HACD is used as closed-loop control electronics, the
“Controller” entry has to be selected in the signal linking [8].
The LCx signals constitute the command value branch, the
LFBx signals the actual value branch. [8]
As actual value signal, you can use both, an SSI encoder or
incremental encoder [2] digital measurement system or one
or several analog sensors.
The controller structure is designed as PIDT1 controller,
whereas each component can be activated or deactivated in-
dividually. In this way, you can, e.g. also realize a P or PT1
controller. The I component can moreover be controlled via a
window (upper and lower limit).
Controller parameters can be set in a block-wise or in a block-
independent form.
A state feedback can be used for dampening the controller
output.
Controller structure:
P
I
DT1
––
+
+
+
–
T1
D
Adjustment to hydraulic system
For the optimum adjustment to the particularities of hydraulic
drives, the following functions are implemented upstream the
analog output:
• Direction-dependent gain [10]
For positive and negative values, the amplification can be
set separately. In this way, adjustment to the area ratio of a
single-rod cylinder is possible.
• Characteristic curve correction [11]
In this way, the progressive flow characteristic of propor-
tional directional valves is compensated or an inflected
characteristic curve is realized.
• Overlap jump/residual velocity [12]
When using valves with positive overlap, a fine position-
ing can be used in case of a PDT1 controller in order to
increase the static accuracy. This fine positioning can be
selected according to the residual voltage principle and as
overlap jump.
• Zero point correction (offset) [13]
Serves the correction of the zero point of the connected
proportional servo valve.
Error detection and troubleshooting
The HACD supports numerous error monitoring possibilities:
• Monitoring of the analog inputs for undershooting or ex-
ceedance of the range
• Monitoring of the sensors for cable break
• Control error monitoring in case of configuration of the
HACD as controller
• Monitoring of the supply voltage, all internal voltages as
well as of the +10 V reference voltage
• Monitoring of the microcontroller itself (watchdog) as well
as of the accumulator (check sum)
The error monitors as well as their reaction can be config-
ured, as well.
Command value provision
Actuation
variable
Command
value
Actual
value
Signal
DT1(actual value)
State feedback
Amplification
[ ] = Assignment to the block diagram on page 8/9

C1-1
C2-1
C3-1
FB1-1
FB2-1
FB3-1
C1-2
C2-2
C3-2
FB1-2
FB2-2
FB3-2
LC1
LC3
LFB1
LFB3
C1
C2
C3
FB1
FB2
FB3
U
U/I
U
U
U/I
U
U/I
U
U/I
U
IN1
IN2
IN3
IN4
IN5
IN6
AI1+
INC
1D/A+
2D/B– INC
1D/A–
2D/B+
Z–
Z+
SSI
1CLK+
1D/A–
SSI1
1CLK–
1D/A+
U/I
U/I
DI1
DI2
DI3
DI4
DI5
DI6
DI7
DI8
DC
DC
18 -30 V
GND
7
14
5
6
3
3
+, –, *, /
MIN, MAX
Limit, Jump
+, –, *, /
MIN, MAX
Limit, Jump
Ratio
+, –, *, /
MIN, MAX
Limit, Jump
Ratio
+, –, *, /
MIN, MAX
Limit, Jump
Ratio
+, –, *, /
MIN, MAX
Limit, Jump
+, –, *, /
MIN, MAX
Limit, Jump
2
RS 232
PROFIBUS
Ethernet
AI1–
AI2+
AI2–
AI3+
AI3–
AI4+
AI4–
AI5+
AI5–
AI6+
AI6–
SSI
2CLK+
2D/A–
SSI2
2CLK–
2D/A+
1
2
3
LC2
LFB2
6
6
2
2
PWR RUN
GND
1a
T1 Lag
T1 Lag
T1 Lag
T1 Lag
T1 Lag
T1 Lag
8/16 Bosch Rexroth AG Hydraulics VT-HACD-3-2X RE 30543/12.10
Block diagram: Mode 3 - structural editor
AND
OR
Digital inputs Digital outputs
Thresholds
Dwell time
Internal flags
Error
Block time
Trigger condition 1
Trigger condition 2
Command value internal + variable
Velocity +/–
Acceleration +/–
LFB2 = Variable
Controller parameter
Command value internal + variable
Velocity +/–
Acceleration +/–
LFB1 = variable
Controller parameter
Enable
1Analog inputs voltage or current
1a High-impedance input AI1
2SSI or incremental
3Release input and digital inputs
4Adjustment analog inputs
5Switching matrix
6Math. linking of the inputs
732 blocks for command value generation,
controller parameter switching
8Math. linking and/or controller
9Substitutional closed-loop control
10 Direction-dependent gain
11 Characteristic curve adjustment
Command value internal + variable
Velocity +/–
Acceleration +/–
LFB3 = Variable
Controller parameter

U/I
U
U
U
LO1
LO2
AO1
AO3
AGND
17
X1
Y1
OUT1
OUT3
C1
LFB1
C2
LFB2
C3
LFB3
X2
Y2
OK
DO1
DO2
DO3
DO4
DO5
DO6
DO7
ref (+10 V)
8
8
16
9
17
+
–
*
/
MIN
MAX
Limit
Jump
+
–
*
/
MIN
MAX
Limit
Jump
+
–
*
/
MIN
MAX
Limit
Jump
+
–
*
/
MIN
MAX
Limit
Jump
10
11
12
13
14
15
10
11
12
13
14
15
1
2
3
U
U
LO2 AO2
OUT2
X2
Y2
8
17
+
–
*
/
MIN
MAX
Limit
Jump
+
–
*
/
MIN
MAX
Limit
Jump
10
11
12
13
14
15
AGND
AGND
RE 30543/12.10 VT-HACD-3-2X 9/16Hydraulics Bosch Rexroth AG
Control
digital
outputs
Error
detection
Controller
Controller
Controller
Substitutional
12 Residual velocity and overlap jump
13 Offset
14 Limitation
15 Analog outputs voltage or current
16 OK output and digital outputs
17 Math. linking of the outputs

7
1
2
6
3
5
X3C
X1S
PROFIBUS DP
PWR
GND
GND
18-30V
0
1
2
3
4
5
6
address
PWR RUN BUS
o
n
HACD
RS232
X7P/D
X2M1 encoder
1clk+
1clk-
1D/A+
1D/A-
Z+
24V
GND
2clk+
2clk-
2D/B+
2D/B
Z-
24V
GND
DI1
DI2
DI3
DI4
DI5
DI6
DI7
DI8
DO1
DO2
DO3
DO4
DO5
DO6
DO7
ok
DIO
AIOX2A1
enable
AI1+
AI2+
AI3+
AI4+
AI5+
AI6+
AO1
AO3
AI1-
AI2-
AI3-
AI4-
AI5-
AI6-
AO2
AGND
ref
L
S
L
S
NS
X7E2
X7E1
MS
10/16 Bosch Rexroth AG Hydraulics VT-HACD-3-2X RE 30543/12.10
System overview, interfaces
Superior control
Possible interfaces with the VT-HACD-3-2X:
– Analog signals
– Digital inputs / outputs
– Serial interface
– Bus systems
1 Single-rod cylinder
2 Integrated position measurement system
3 Proportional servo valve with integrated
control electronics
4 VT-HACD-3-2X
5 Connection cable
6 Pressure transducer
7 Sandwich plate isolator valve (with plug-in switching amplifier)
Example:
VT-HACD-3-2X/… with hydraulic cylinder axis

RE 30543/12.10 VT-HACD-3-2X 11/16Hydraulics Bosch Rexroth AG
Operating voltage 1) UB18 to 30 VDC
Current consumption at 24 VDC 200 mA (observe additional power for connected
sensors/actuators)
Processor 32 bit power PC
Analog inputs (AI) Quantity 6
– Voltage inputs (differential inputs)
• Channel number max. 6 (selectable via software)
• Input voltage UEmax +15 V to –15 V (+10 V to –10 V analyzable)
• Input resistance RE> 10 MΩ (AI1)
200 kΩ ±5 % /AI2 to AI6)
• Resolution 5 mV
• Non-linearity ±0.25 %
• Calibration tolerance max. 40 mV (with factory settings)
– Current inputs
• Channel number max. 6 (selectable via software)
• Input current IE0...20 mA
• Leakage current IV0.1 to 0.4 %
• Resolution 5 µA
Technical data
1) If a 24 V encoder supply is implemented directly via the
VT-HACD-3-2X (supply voltage is looped in), the transduc-
er specification has to be observed.
Analog outputs Quantity 3
AO1 configuration as voltage output
Output voltage U0…10 V or ±10 V (configurable)
Output current Imax 10 mA
Load RLmin 1 kΩ
Resolution 1.25 mV (14 bit)
Residual ripple ±15 mV (without noise)
AO1 configuration as current output
Output current I0…20 mA or 4…20 mA (configurable)
Load Rmax 500 Ω
Resolution 1.25 µA
Residual ripple ±15 µA (without noise)
AO2 / AO3
Output voltage U±10 V
Output current Imax 10 mA
Load Rmin 1 kΩ
Resolution 1.25 mV (14 bit)
Residual ripple ±25 mV (without noise)

12/16 Bosch Rexroth AG Hydraulics VT-HACD-3-2X RE 30543/12.10
X3C, Interface for BODAC
X7P, Bus interface
X7E1(2), Ethernet interface
RS232
PROFIBUS DP (max. 12 MBaud according to IEC 61158)
PROFINET RT, EtherNet/IP
Switching inputs (DI) and/or outputs (DO)
Quantity DI = 9 / D0 = 8
Gate inputs (DI) Logic level
log 0 (low)
≤
5 V; log 1 (high)
≥
10 V to UB,
Ie = 7 mA at UB
= 24 V
Port Flexible conductor up to 1.5 mm2
Gate outputs (DO) Logic level log 0 (low) ≤ 2 V; log 1 (high) ≤ UB; Imax = 20 mA,
Maximum load capacity C = 0.047µF
Port Flexible conductor up to 1.5 mm2
Reference potential for all signals GND
Digital position transducer (encoder)
– Incremental transducer (transducer with TTL output)
• Input voltage log 0 0 to 1 V
log 1 2.8 to 5.5 V
• Input current log 0 –0.8 mA (with 0 V)
log 1 0.8 mA (with 5 V)
• max. frequency referring to Ua1 fmax 250 kHz
– SSI transducer (Due to the higher control quality, an SSI
transducer with clock synchronization should be used.)
• Coding Gray code, binary code
• Data width Adjustable up to max. 28 Bit
• Line receiver / line driver RS485
– Voltage supply for SSI transducer via the VT-
HACD-3-2X
U, I UB, max. 200 mA
Reference potential for all signals GND
Reference voltage per axis electronics Uref +10 V ±25 mV (20 mA)
Dimensions See page 14
Installation Top hat rail TH 35-7.5 or TH 35-15 according to EN 60715
Admissible operating temperature range ϑ0 to 50 °C
Storage temperature range ϑ–20 to +70 °C
Protection class according to EN 60529:1991 IP 20
Weight
without EtherNet module
with EtherNet module
m
m
930 g
1162 g
CE conformity See page 2
Further technical details upon request.
Note:
Information on the environment simulation testing for the areas EMC (electromagnetic compatibility), climate and mechanical
load see data sheet 30543-U.
Technical data, (continued)

X3C
X1S
PROFIBUS DP
PWR
GND
GND
18-30V
0
1
2
3
4
5
6
address
PWR RUN BUS
o
n
HACD
RS232
X7P/D
X2M1 encoder
1clk+
1clk-
1D/A+
1D/A-
Z+
24V
GND
2clk+
2clk-
2D/B+
2D/B
Z-
24V
GND
DI1
DI2
DI3
DI4
DI5
DI6
DI7
DI8
DO1
DO2
DO3
DO4
DO5
DO6
DO7
ok
DIO
AIOX2A1
enable
AI1+
AI2+
AI3+
AI4+
AI5+
AI6+
AO1
AO3
AI1-
AI2-
AI3-
AI4-
AI5-
AI6-
AO2
AGND
ref
L
S
L
S
NS
X7E2
X7E1
MS
RE 30543/12.10 VT-HACD-3-2X 13/16Hydraulics Bosch Rexroth AG
Pinout
X3C RS232
Pin
1 LCAN_H
2 TxD
3 RxD
4 Reserved
5 GND
6 Reserved
7 Reserved
8 Reserved
9 LCAN_L
X1S Power
Pin
1 GND
2 GND
3 18 – 30 V
X7P PROFIBUS DP
Pin
1 Reserved
2 Reserved
3 RxD/TxD-P
4 CNTR-P
5 DGND
6VP
7 Reserved
8 RxD/TxD-N
9 Reserved
X2M1 Encoder/DIO
(digital)
1clk+ 2clk+
1clk– 2clk–
1D/A+ 2D/B+
1D/A– 2D/B–
Z+ Z–
24V 24V
GND GND
DI1 DO1
DI2 DO2
DI3 DO3
DI4 DO4
DI5 DO5
DI6 DO6
DI7 DO7
DI8 ok
X2A1 AIO
(analog)
Ref Enable
AI1+ AI1–
AI2+ AI2–
AI3+ AI3–
AI4+ AI4–
AI5+ AI5–
AI6+ AI6–
AO1 AO2
AO3 AGND
X7E1, X7E2
Ethernet ports
Notes:
– The pins marked with “reserved” are reserved and must
not be wired!
– PROFIBUS DP (port X7P/D) is not available with the
Ethernet version.

117,5
123,5
6
86
120
2,5
HACD
X3C
X1S
PROFIBUS DP
PWR
GND
GND
18-30V
0
1
2
3
4
5
6
address
PWR RUN BUS
o
n
HACD
RS232
X7P/D
X2M1 encoder
1clk+
1clk-
1D/A+
1D/A-
Z+
24V
GND
2clk+
2clk-
2D/B+
2D/B
Z-
24V
GND
DI1
DI2
DI3
DI4
DI5
DI6
DI7
DI8
DO1
DO2
DO3
DO4
DO5
DO6
DO7
ok
DIO
AIOX2A1
enable
AI1+
AI2+
AI3+
AI4+
AI5+
AI6+
AO1
AO3
AI1-
AI2-
AI3-
AI4-
AI5-
AI6-
AO2
AGND
ref
L
S
L
S
NS
X7E2
X7E1
MS
117,5
123,5
6
65
120
2,5
X3C
X1S
PROFIBUS DP
PWR
GND
GND
18-30V
0
1
2
3
4
5
6
address
PWR RUN BUS
o
n
HACD
RS232
X7P/D
X2M1 encoder
1clk+
1clk-
1D/A+
1D/A-
Z+
24V
GND
2clk+
2clk-
2D/B+
2D/B
Z-
24V
GND
DI1
DI2
DI3
DI4
DI5
DI6
DI7
DI8
DO1
DO2
DO3
DO4
DO5
DO6
DO7
ok
DIO
AIOX2A1
enable
AI1+
AI2+
AI3+
AI4+
AI5+
AI6+
AO1
AO3
AI1-
AI2-
AI3-
AI4-
AI5-
AI6-
AO2
AGND
ref
VT-HACD-3-2X/
(without Ethernet)
VT-HACD-3-2X/
(with Ethernet)
14/16 Bosch Rexroth AG Hydraulics VT-HACD-3-2X RE 30543/12.10
Unit dimensions (dimensions in mm)
Installation on top hat rail TH 35-7.5 or TH 35-15 according to EN 60715
Installation on top hat rail TH 35-7.5 or TH 35-15 according to EN 60715

RE 30543/12.10 VT-HACD-3-2X 15/16Hydraulics Bosch Rexroth AG
Commissioning software and documentation on the Internet: www.boschrexroth.com/HACD
Maintenance instructions:
– The devices have been tested in the plant and are supplied with default settings.
– Only complete units can be repaired. The repaired units will be supplied with default settings. User-specific settings are not
maintained. The operator will have to re-transfer the corresponding user parameters and programs.
Notes:
– Electric signals taken out via control electronics (e.g. signal “No error”) may not be used for the actuation of safety-relevant
machine functions! (See also the European standard “Safety requirements for fluid power systems and their components -
Hydraulics”, EN 982.)
– If electromagnetic interference must be expected, take appropriate measures to safeguard the function (depending on the
application, e.g. screening, filtration)!
– For more information refer to the BODAC software description 30543-01-B and the 30543-B operating instructions
– The upper and lower ventilation slots must not be concealed by adjacent units in order to provide for sufficient cooling.
Product documentation for VT-HACD-3-2X
Data sheet 30543
Operating instructions 30543-B
Environmental compatibility statement 30543-U
BODAC software description 30543-01-B
Start-up PROFIBUS Interface 30543-01-Z
Start-up EtherNet/IP Interface 30543-04-Z
Start-up PROFINET RT Interface 30543-05-Z
General Information on the maintenance and commissioning of hydraulic components 07800/07900
Project Planning / Maintenance Instructions / Additional Information

Bosch Rexroth AG
Hydraulics
Zum Eisengießer 1
97816 Lohr am Main, Germany
Phone +49 (0) 93 52 / 18-0
Fax +49 (0) 93 52 / 18-23 58
www.boschrexroth.de
© This document, as well as the data, specifications and other informa-
tion set forth in it, are the exclusive property of Bosch Rexroth AG. It
may not be reproduced or given to third parties without its consent.
The data specified above only serve to describe the product. No state-
ments concerning a certain condition or suitability for a certain applica-
tion can be derived from our information. The information given does not
release the user from the obligation of own judgment and verification. It
must be remembered that our products are subject to a natural process
of wear and aging.
16/16 Bosch Rexroth AG Hydraulics VT-HACD-3-2X RE 30543/12.10
Notes
Table of contents
Other REXROTH Controllers manuals
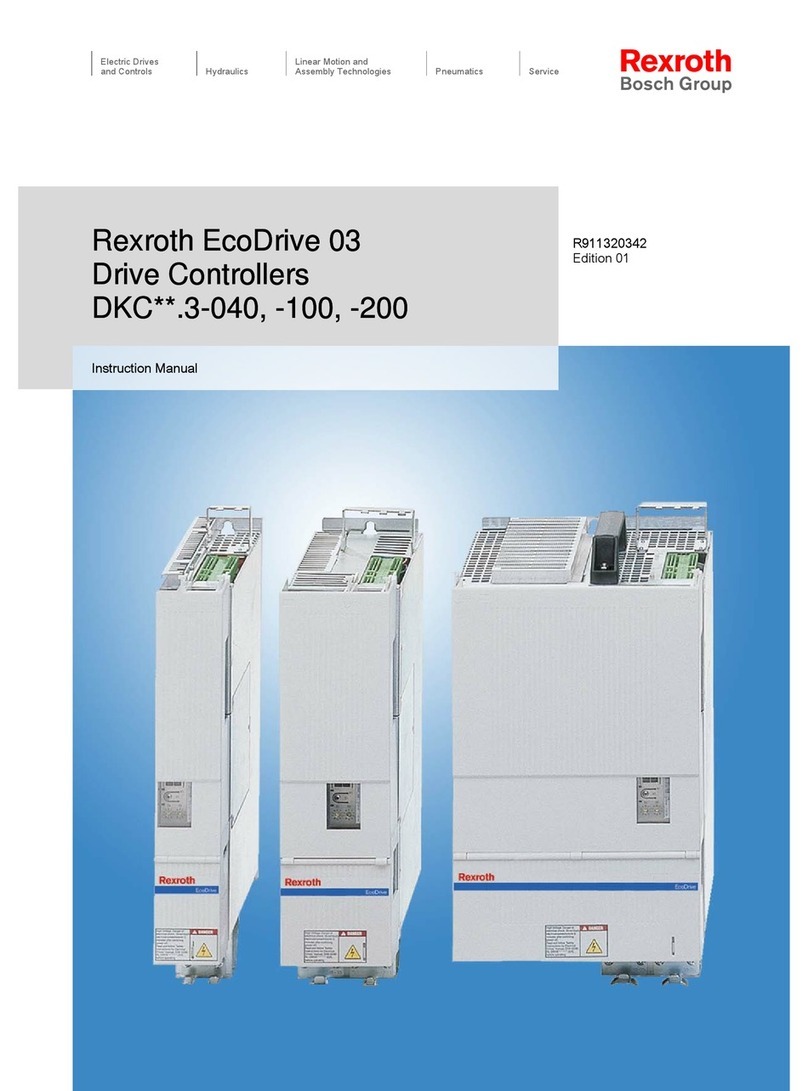
REXROTH
REXROTH EcoDrive 03 User manual
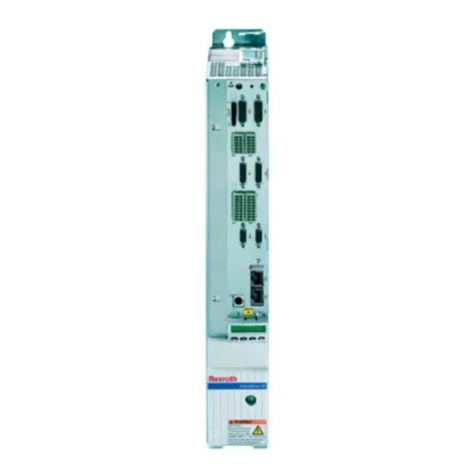
REXROTH
REXROTH IndraDrive M Technical manual
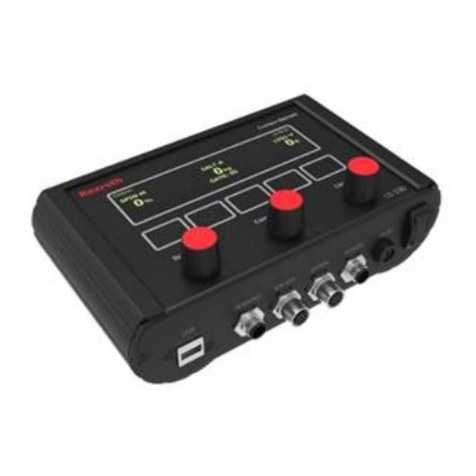
REXROTH
REXROTH CS 530 Instruction sheet
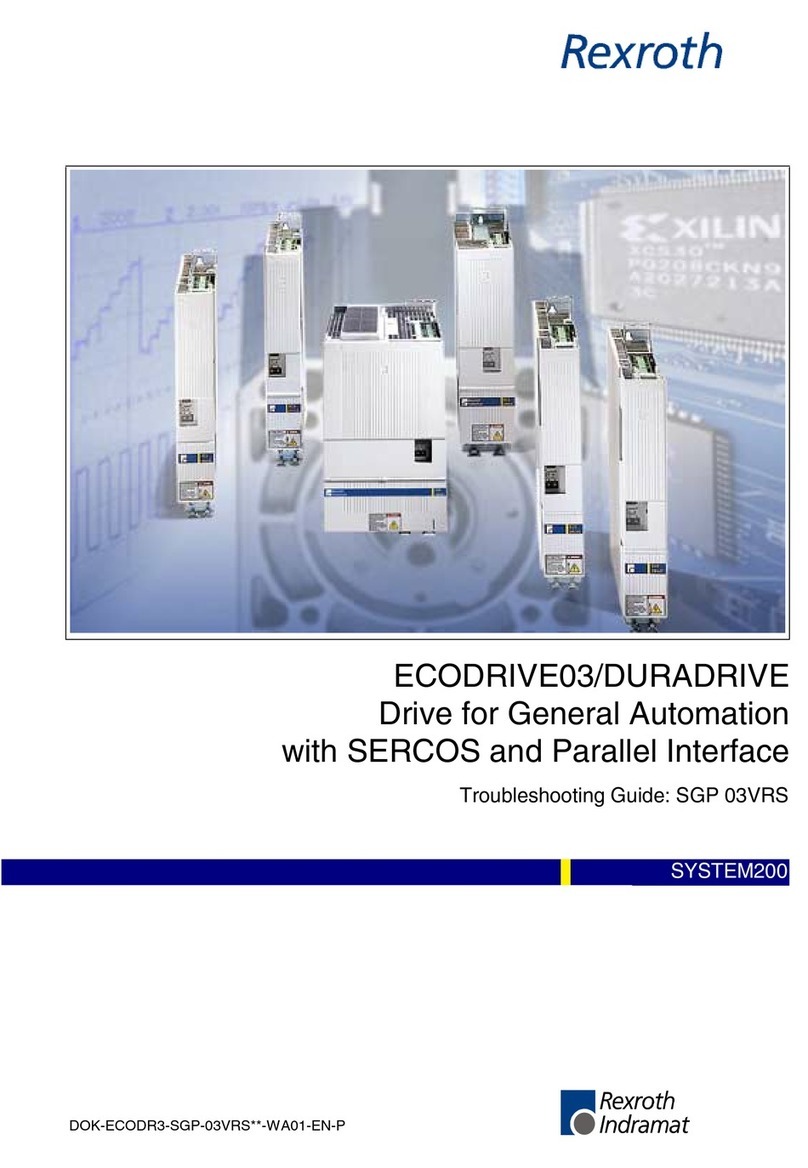
REXROTH
REXROTH ECODRIVE03 User manual
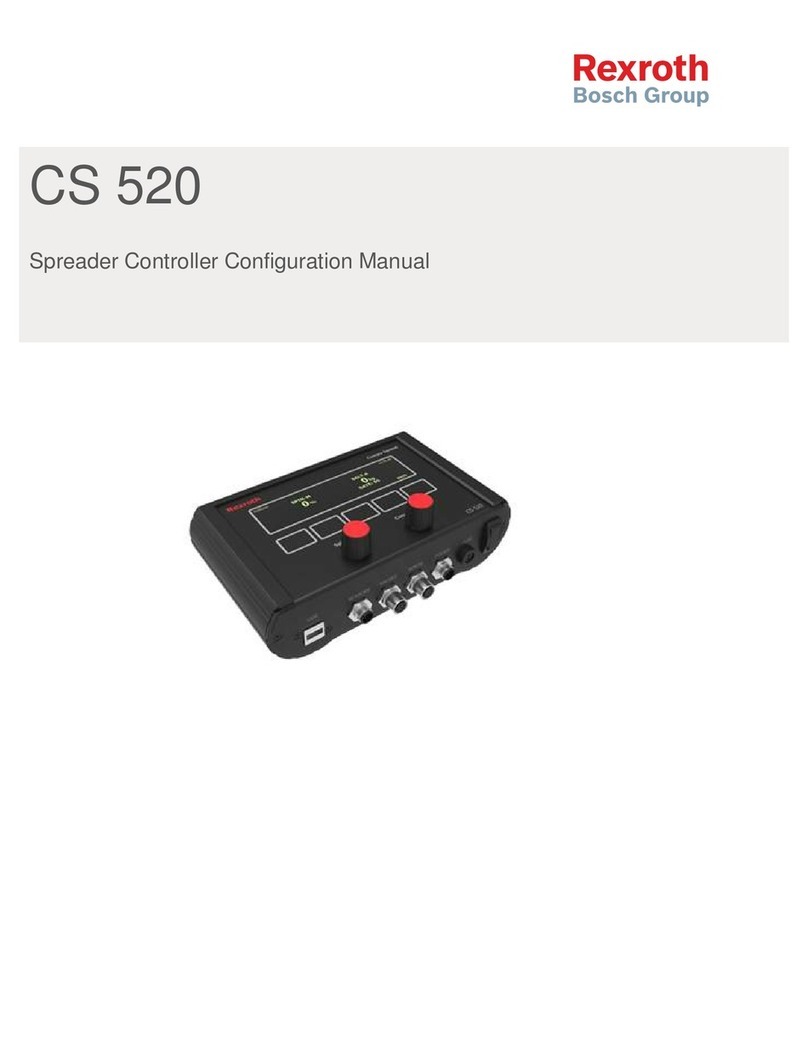
REXROTH
REXROTH CS 520 Instruction sheet
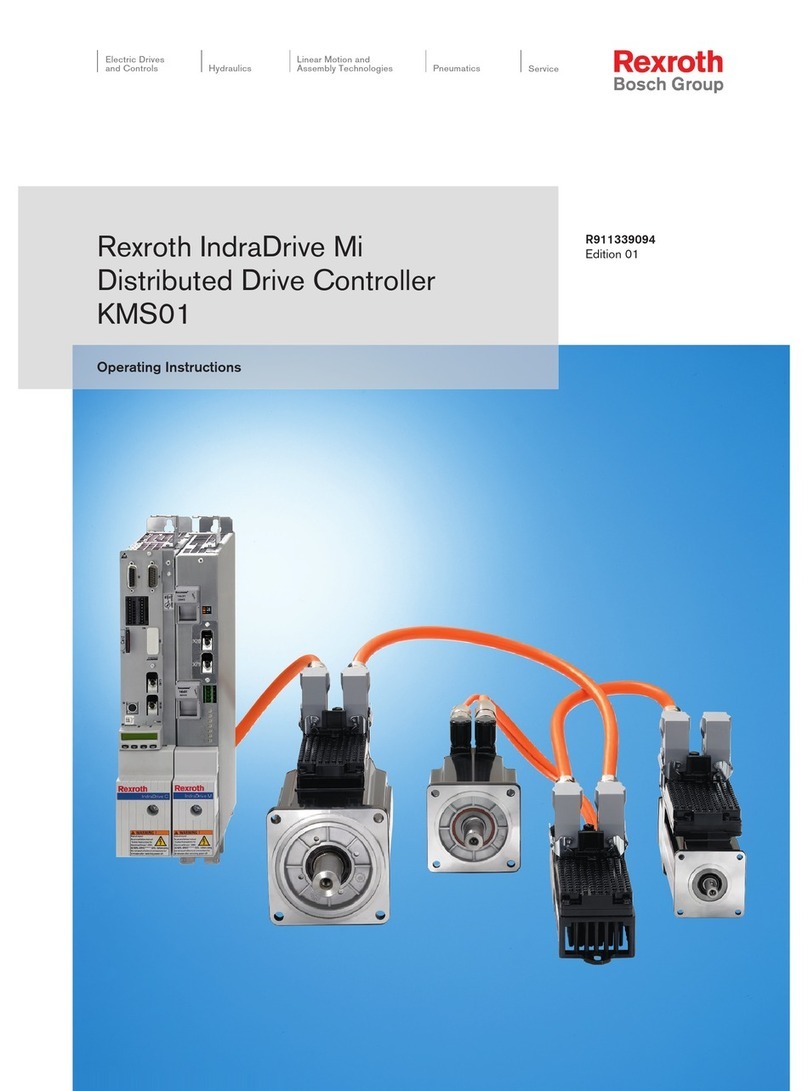
REXROTH
REXROTH IndraDrive Mi User manual

REXROTH
REXROTH CS 550/150 Use and care manual
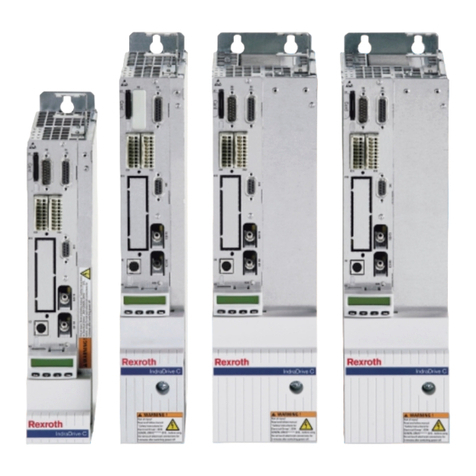
REXROTH
REXROTH IndraDrive C Series Technical manual
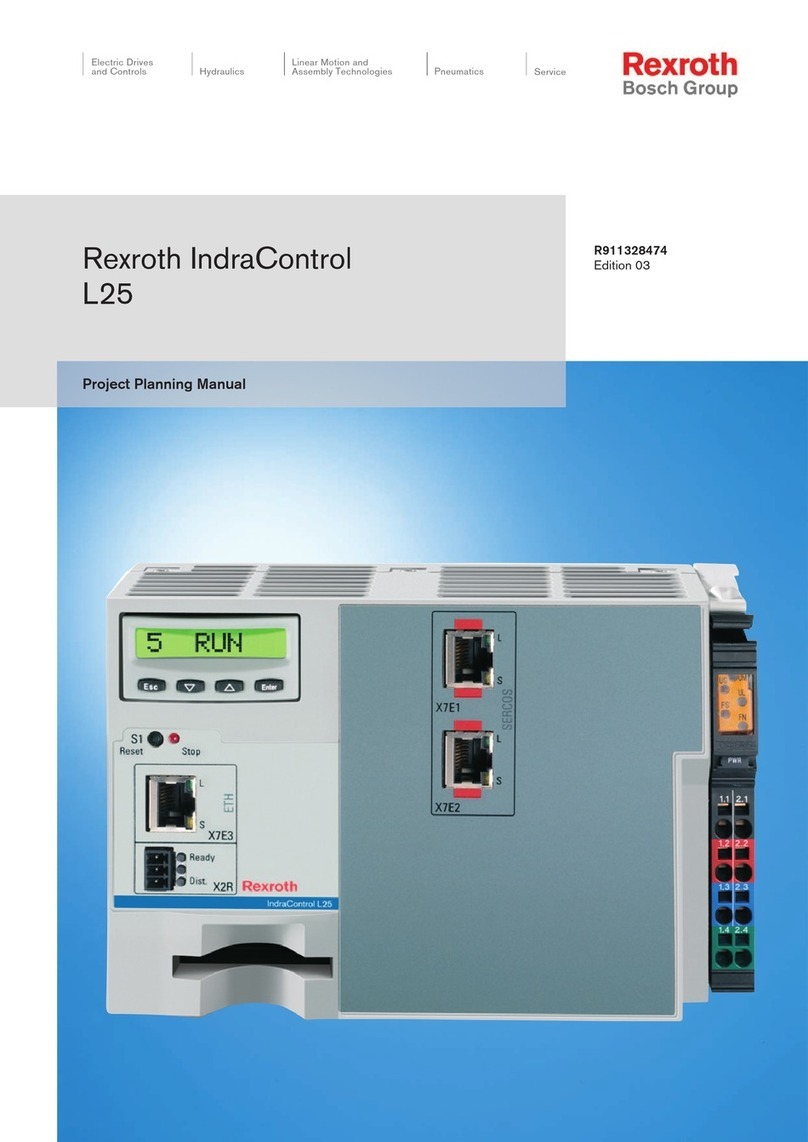
REXROTH
REXROTH IndraControl L25 Series Technical manual
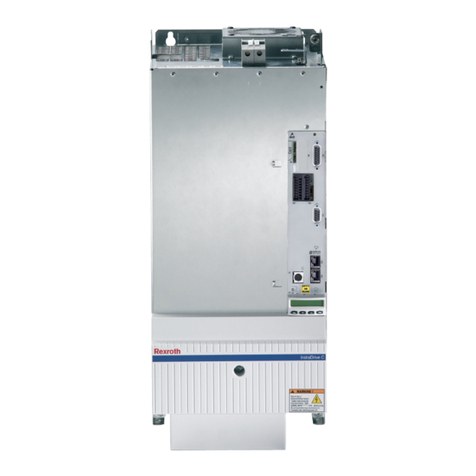
REXROTH
REXROTH HCS03 User manual