REXROTH CS 520 Instruction sheet

CS 520
Spreader Controller Configuration Manual

1
TABLE OF CONTENTS
Page
1 LAYOUT ……..............................................................................................................................................2
2MAIN MENUS ........................................................................................................................................2
3AUTHORIZATION VERIFICATION ........................................................................................................3
4SYSTEM CONFIGURATION...................................................................................................................4
5GROUND SPEED CALIBRATION..........................................................................................................6
6HYDRAULIC VALVE CONFIGURATION................................................................................................7
7MATERIAL CALIBRATION ...................................................................................................................9
8DATA SAVING / LOADING / DISPLAYING .........................................................................................11
9SUB MENUS .......................................................................................................................................13
10 ERRORS .............................................................................................................................................16
11 UNLOAD .............................................................................................................................................16
12 SPREADING SCREEN ........................................................................................................................17
13 PAUSE / BLAST ..................................................................................................................................17
14 UPDATE FIRMWARE ..........................................................................................................................18
15 LOGGING REPORT ............................................................................................................................18
Bosch Rexroth Canada Corp. reserves the right to revise this information at any time and for any reason
and reserves the right to make changes at any time, without notice or obligation, to any of the information
contained in this piece of literature.
Please check for updates at: www.boschrexroth.ca/compu-spread
Rexroth reserves the right to revise this information at any time, without notice or obligation, to the information in this literature. Please
check for updates at: www.boschrexroth.ca/cs

2
1LAYOUT
CS 520 is a two function programmable controller, available in Manual, Closed or Open Loop mode, for the
controlled application of granular solids in snow and ice control.
See Appendix for system layout in detail.
2MAIN MENUS
When the truck is stopped or no ground speed signal is coming in, the screen below will be shown:
0KMh 11:35:07
SPIN‒M SALT‒C
0%0kg
GATE: 05
TOTAL
SETUP MISC XXXXX REVS
Conveyor mode
Speed
Spinner
Solid material System clock
Gate position Solid rate
Keypad functions
Power Switch
Fuse
Power Cable
Serial Cable
Sensor Cable
Two Encoders
with push buttons
Touch Pads
USB Port
Valves Cable

3
Key pads from left to right are for TOTAL, SETUP, MISC, SUBMENU and REVERSE. Pressing the touch
panel pad enters the corresponding menu screen or holding REVS to reverse the conveyor.
TOTAL ---- trip and season totals, data display / save / load / log
SETUP ---- access to all settings of the system
MISC ---- adjust the brightness of screen or driver ID if AVL attached
- ---- go to submenu to do speed simulation, gate adjustment and material change.
REVS ---- to reverse the conveyor
The screen below will show up when system is saving log data automatically, please keep the power on and let
it finish by itself.
3AUTHORIZATION VERIFICATION
To set up the CS-520, either a security USB or a password is needed according to the setting of LOCK feature
in programming mode. This is to prevent unauthorized personnel from making adjustments to the system.
After pressing the ‘SETUP’ button, the screen changes to “PLS insert USB” or the input of the password. If it is
password verification, the screen below will be shown:
The most right digit stays bright while the rests are dim, pressing the keypads left or right arrows to choose the
digit and the up / down arrow to change character (This also applies to the settings of other features). After that,
press ENTER to confirm the input. The default password is 000000, the user can change this password once in
the setup screen.
Firmware Version Number:
V.X
Please Enter Code
Code: 0 0 0 0 0 0
TOTAL SETUP MISC XXXXX ENTER
======================================
Log is backing up …
Pls keep power on !
=======================================

4
4SYSTEM CONFIGURATION
If the password is correct or a program key is present, the setup screen below will be shown:
Press up / down arrow to navigate to the different features, the *symbol preceding the line will mark the active
line. Press ENTER to edit / select the settings, some fields may also have a sub menu as indicated by the
‘CHG’ icon. This is for editing the field. (See example of the editing of REGN below).
Press NPAGE to go to the next screen and PPAGE to the former one.
4.1 Setting the Region Name and Truck ID
REGN: To edit the REGION and TRUCK name
Press to switch between region and truck name. Press CHG to start to edit the region or truck name,
Then press FINSH button to quit editing.
4.2 Setting the UNIT
UNIT: To choose the system unit, metric or imperial.
4.3 Authorization method
LOCK: A valid USB programing key or six characters password can be chosen to verify the access to the setup
screen.
4.4 Setting the Time
TIME: Clock time is formatted as: Hour: Minute: Second
4.5 Setting the Date
DATE: is formatted as Month: Day: Year
* REGN: REGION BLST: 60X ALM: 88
UNIT: METRIC SPIN: S&P DI: N/A
LOCK: P000000 MODE: STD DF: 150
TIME: 00:00:00 USER: M+G OS:
EN
M/D/Y: 00-00-00 LIQU: N/A
RS: SUM
EXIT NPAGE MISC XXXXX ENTER
* REGN: REGION BLST: 60X ALM: 88
UNIT: METRIC SPIN: S&P DI: N/A
LOCK: P000000 MODE: STD DF: 150
TIME: 00:00:00 USER: M+G OS:
EN
M/D/Y: 00-00-00 LIQU: N/A
RS: SUM
CHG NPAGE MISC XXXXX FINSH

5
4.6 Blast Timer and Mode
BLST: The first two digits of ‘BLST’ is the blast timer in seconds & the last one digit is the mode of blasting.
F --- Blast disabled
C --- Blast at close loop with rate set at material screen.
S --- 100% output even at zero ground speed
X --- 100% output except at zero ground speed
The default setting for blast timer is 60 seconds.
4.7 Spinner Stop Mode
SPIN: Choose the spinner stop mode.
NEV --- spinner will always turn when the dial is set.
SPD --- spinner will start and stop with ground speed.
PSE --- spinner will only stop when the pause button is pressed.
S&P --- spinner will stop with ground speed and the pause button
4.8 System mode
MODE: Standard or Air Gate. (Air gate mode offers a 12 volt output signal with the change in materials.)
4.9 User Option
USER: This option determines what the truck driver is allowed to change.
N/A --- operator is not allowed to change either the gate setting or the materials.
M+G --- operator is allowed to change both the gate setting and materials.
GAT --- operator is only allowed to change gate setting.
MAT --- operator is only allowed to change the material.
4.10 Setting the Liquid
LIQU: CS-520 does not have this feature. (N/A will be present)
4.11 Alarm Speed
ALM: This is the ground speed at which a warning will be displayed on the screen. The "Alarm Speed" is not
activated when the spread rate is set at zero or the controller is in the Pause mode.
4.12 Liquid level detection
DI: CS-520 does not have this feature. (N/A will be present)
4.13 Setting Dither Frequency
DF: Two options: 66 Hz and 150 Hz
4.14 Setting Beeping and Language
: Enable / disable the beeping as the feedback to touching of the pads.
EN: Default language is English (En.) unit can switch to French. (Fr.)
4.15 Default Setting and Season Reset
RS: system parameters can be reset to factory defaults or season totals can be reset to zero.
SUM: reset season totals
PAR: reset all parameters to factor defaults
A text page will be shown to confirm the action.

6
5GROUND SPEED CALIBRATION
There are two ways to input the ground speed calibration.
If the resolution is known, just manually input the pulses per KM or Mile.
The other way is to set a predetermined speed (speed the truck will be spreading at most often, is
recommended). Follow the hints on the screen and allow the system to finish the speed calibration by itself.
After the predetermined speed is set up, the controller will jump to the following screen and the text message
“Run CAL SPD & press START” will flash.
Drive the vehicle and hold the vehicles speed (as indicated on the speedometer) at the value you entered in the
CAL SPD field. Press the START button.
Hold the vehicles speed at this rate and after 5 seconds, the system will record the pulse resolution
automatically.
The speed calibration is now completed.
Ground Speed Calibration
* PULS/ (km): 020000 CUR SPD: 0000
CAL SPD: 40
Run CAL SPD & press START
ABORT NPAGE START
SKIP ENTER
Ground Speed Calibration
* PULS/ (km): 020000 CUR SPD: 0000
CAL SPD: 40
SKIP / ENTER to Set CAL SPD
PPAGE NPAGE SKIP ENTER
Predetermined speed
Resolution Current speed

7
6HYDRAULIC VALVE CONFIGURATION
The left side of screen is used to set up the valve configuration.
6.1 Valves
When * is in front of CONVEYOR, press Enter to select the valves. Choose valves to edit between conveyor and
spinner.
6.2 Mode
Conveyor has five modes: close loop (auto), open loop, manual 12V triggered, manual speed or manual.
Spinner can only work under manual mode.
If the Closed loop mode is selected for Conveyor, it is able to run Auto Null.
--- Manual Mode-(M)
This mode allows the driver to manually control the spread rate. Each setting on the Conveyor Dial 1–9 is a
percentage of maximum valve null setting. The display will show “M” beside solid material name on the
operation screen.
--- 12 Volt Triggered Manual Mode-(T)
In addition to manual mode operation, this mode allows the controller to start and stop the spreader based on a
12V input signal. The display will show “T” on the screen.
--- Ground Speed Triggered Manual Mode-(G)
In addition to manual mode operation, this mode will start and stop the spreader based on ground speed input.
The display will show “G” on the screen.
--- Open Loop Mode-(O)
* CONVEYOR 1 SALT
MODE: AUTO BLAST: 0270 M99%
SENSOR: 0050 RATE1: 0032
NULL: 15.0 60.0 WT/REV: 1.00
GAIN: 60% CAL GATE: 05
AUTONULL AUTOCAL
PPAGE NPAGE START SKIP ENTER
* SPINNER
MODE: MANUAL
NULL: 15.0 75.0
BLAST: 0 0 0
PPAGE SKIP ENTER ENTER

8
This mode utilizes the ground speed sensor only to regulate the amount of material that will be dispensed off the
vehicle. There are 9 configurable application rate settings available. The display will show “O” on the screen.
--- Closed Loop Mode-(C)
This mode utilizes both a conveyor and ground speed sensor to regulate the amount of material that will be
dispensed off the vehicle. There are 9 configurable application rate settings available. The display will show “C”
on the screen.
6.3 Sensor
Determine the number of pulses per revolution of conveyor motor you are using, and enter this value in the
‘sensor’ field, when closed loop mode is selected. During nulling or auto-nulling, this line will show the actual
conveyor speed.
6.4 Null
1. Press ENTER to manually null the minimum and maximum current (in %) to the valve solenoids.
WARNING: Once selected the conveyor or spinner has the ability to turn, and caution must be exercised.
2. Use up and down arrows to adjust the speed so that the motor just begins to turn.
3. Press to end ‘Minimum’ value editing and switch to the ‘Maximum’ value.
4. Do the same for “Maximum” except adjust the motor to a safe maximum speed or until the RRM readout
stops to increase.
6.5 Auto-nulling
The nulling of the valve solenoids for the minimum and maximum values can also be accomplished
automatically. Providing a conveyor sensor is being used in the system.
Press the ENTER to start the auto-null process, the text “Auto-nulling” will flash on the screen during procedure.
Auto-null will end after recording the minimum and maximum null values.
6.6 Gain
This is the percentage of valve output increase, introduced on the conveyor during start up, when the vehicle
starts to move, to overcome hydraulic motor pulsing and provide for instant, continuous movement of the
conveyor.
6.7 Blast in Spinner
This is to set the blast rate of the spinner based on the percentage of its maximal output. The default value is
zero, which means the spinner will not blast while the conveyor is blasting.

9
7MATERIAL CONFIGURATION
There are four solid material under the standard mode and two solid materials with air gate mode. Within the
valves configuration page, the right side of the screen is for the corresponding material configuration.
Using or move from conveyor configuration to material configuration.
7.1 Material Name
Press ENTER to input the different solid material names.
Use up / down arrow to view each material’s settings and press FINSH to select the material.
If CHG is pressed, the system will start to edit the material names. (to a maximum of 4 characters)
After you finish editing the material name, press DONE.
7.2 BLAST RATE
BLAST: The first number is the blast rate for blast in closed loop and the next one is the percent of manual blast.
7.3 APPLICATION RATES
RATE: There are 9 settings of the application rate for each material when the conveyor works in open or close
loop mode.
Press ENTER and then the up / down arrows to browse the rate setting values, and press CHG to edit the
current rate value.
7.4 WT/REV
This setting refers to the weight of material being discharged from the main conveyor / auger for every revolution
of the conveyor motor.
CONVEYOR * 1 SALT
MODE: AUTO BLAST: 0270 M99%
SENSOR: 0050 RATE1: 0032
NULL: 15.0 60.0 WT/REV: 1.00
GAIN: 60% CAL GATE: 05
AUTONULL AUTOCAL
CHG NPAGE START SKIP FINSH
* CONVEYOR 1 SALT
MODE: AUTO BLAST: 0270 M99%
SENSOR: 0050 RATE1: 0032
NULL: 15.0 60.0 WT/REV: 1.00
GAIN: 60% CAL GATE: 05
AUTONULL AUTOCAL
PPAGE NPAGE START SKIP ENTER

10
Note: This number will automatically be generated as a result of the weight / rev. calibration process
(AUTOCAL) or you can input this value manually.
7.5 CAL GATE
Enter the correct gate setting at which the current solid material was calibrated at.
7.6 AUTOCAL
Here is where you can perform the material calibration if the controller is set to ‘Auto’ or ‘Open’
1. Place an adequate catch container under the spreader discharge chute.
2. Make sure that you have sufficient material in the hopper, ensure the conveyor or auger has been
loaded, hopper is full of material and the system is safe to run.
3. Set the gate position. (ensure you enter this value in the CAL GATE field)
4. Press ENTER to proceed.
5. Turn the CONV knob to any position to start the material discharging.
6. Press FINSH when the desired amount of material is reached.
After pressing FINSH, the screen will jump to the material weight input screen, enter the weight of the material
that was dispensed, the controller will calculate the WT/REV and the result will be displayed on the screen.
CONVEYOR 1 SALT
MODE: AUTO BLAST: 0270 M99%
SENSOR: 0050 RATE1: 0032
NULL: 15.0 60.0 WT/REV: 1.00
GAIN: 60% CAL GATE: 05
AUTONULL * AUTOCAL
Turn Knob to run
ABORT FINSH
CONVEYOR 1 SALT
MODE: AUTO Measure material
SENSOR: 0050 Enter Number
NULL: 15.0 60.0 Wgt: 0000
GAIN: 60%
AUTONULL * AUTOCAL
ABORT FINSH

11
8DATA SAVING / LOADING / DISPLAYING
8.1 Save parameters to the system
All the changes made to the parameters will be updated and saved after pressing EXIT on the setup screen, the
system will also give a text message screen as shown below.
8.2 Display the trip and season totals
When the truck is stopped (no ground speed present), Press TOTAL to display the trip and season totals.
Pressing RESET will clear the TRIP TOTALS, while the SEASON TOTALS can only be cleared in the program
setup screen.
8.3 Save parameters to USB
Press DATA, insert program key and follow the hints on screen. Once “USB FOUND” appears, pressing
SPARA will save all the parameters on the USB key with the file name that includes the Region and Truck ID
names.
===============================
SAVE CONFIGURATION
KEEP POWER ON!
===============================
LOGGING DATA or PARAMETERS
INSERT USB
SPARA LPARA LOG QUIT
TRIP SEASON
SDT: 1KM 1KM
DST: 1KM 1KM
QTY: 100KG 100KG
RESET DATA QUIT
Total quantity
Total distance
Total spreading distance

12
8.4 Loading parameters from USB key to Controller
It is also possible to load saved parameters from a USB key to the controller on the screen. By pressing
LPARA, the screen (as shown below) will list all the saved parameters files on the USB key.
Use up / down arrow to navigate and press SELCT to load the desired parameter file.
Press YES, the controller will display ‘LOADING’, when complete touch ‘QUIT’ and then ‘QUIT’ again. Touch
the ‘SETUP’ button, then the ‘EXIT’ button and power the display off. This procedure confirms all the
parameters will be refreshed to the controller’s memory.
8.5 Save Controller Logging Data to USB Key
When the truck is stopped, Press TOTAL first, then press DATA, insert the log key and press LOG, The screen
text will show “SAVING…” which will disappear after it saves the spreading log information to the USB key. (This
will also clear the logged data from the controller). Touch ‘QUIT’ and then ‘QUIT’ again. Insert the USB key into
a laptop and open the CS-530 logging Excel desktop software. The logging information will have the file name
“data_REGN_TRID.txt”, and it will be date and time stamped.
* REGION_TURC01 REGION_TURC06
REGION_TURC02 REGION_TURC07
REGION_TURC03 REGION_TURC08
REGION_TURCK04 REGION_TURC09
REGION_TURCK05
1 --- 10
QUIT NPAGE SELCT
Load REGION_TURC01 ?
YES NO

13
9SUB Menus
9.1 SPEED SIMULATION
When the truck is stopped (ground speed = 0), press to enter the screen as shown below.
Press SMSPD to enter speed simulation mode.
-Make sure that the vehicle is stationary (ground speed = 0)
-Press UP and DOWN buttons to adjust the simulated ground speed value.
-WARNING: In simulated mode the conveyor and or spinner has the ability to turn, and caution must be
exercised.
-Turn the dials to verify the system is working.
-NOTE: Under the simulation mode, the system still counts the spreading information into log file, so
please clear that by resetting the screen totals and retrieving logging data with USB log key.
9.2 Gate Adjustment
Depending on the setting of the USER options in the setup screen, GAT and MAT may show up on the sub
menus.
If, GATE is there, press GAT to enter the gate adjustment screen.
Change the gate value as required and press the FINSH button to exit.
0KMh 11:35:07
SPIN‒M SALT‒C
0%0kg
GATE: 05
SMSPD SETUP GAT MAT
SIM 0KMh 11:35:07
SPIN‒M SALT‒C
0%0kg
GATE: 05
STOP
0KMh 11:35:07
SPIN‒M SALT‒C
0%0kg
GATE: 05
SMSPD SETUP GAT MAT

14
9.3 Material change
Depending on the setting of the USER options in the setup screen, GAT and MAT may show up on the sub
menus.
If, MAT is there, press MAT to enter the material adjustment screen.
Press SOLID to change solid material
NOTE: A reminder screen for the calibrated gate setting of the new solid material selected will show for 5
seconds.
9.4 Air Gate
If “air gate” mode is the chosen in the setup screen, it will show the “AIRGT” menu instead of “GAT” and/or
“MAT”.
Press the AIRGT button to enter the air gate adjustment screen. Press the button to switch between low
gate and high gate. The chosen gate setting is highlighted.
NOTE: When you switch the gate setting the material will also change from material 1 (low gate) and material 3
(high gate).
0KMh 11:35:07
SPIN‒M SALT‒C
0%0kg
GATE: 05
SMSPD
AIRGT
0KMh 11:35:07
SPIN‒M SALT‒C
0%0kg
GATE: 05
SOLID FINSH
0KMh 11:35:07
SPIN‒M SALT‒C
0%0kg
GATE: 05
SMSPD SETUP GAT MAT

15
Press ENTER again to exit.
10 ERRORS
The controller continuously checks for errors during operation. E.g. the below screen shows that the ground
speed is too high. (operator is driving faster than the programmed maximum speed setting)
An audible alarm and error message will display on screen for 4 seconds when an error occurs, then it will go off
and could come back on 3 minutes later if the error is not resolved. Others more serious errors will stay on the
screen until the controller power is cycled or the error is resolved.
Error Messages Suggested Solution Cycle Power Needed?
BLAST2LONG Turn off blast No
OVERSPEED Slow down, reset max speed No
SPIN OUTPUT Check cables, replace coil Yes
CONV OUTPUT Check cables, replace coil Yes
NO CONVEYOR Check cable/sensor No, switches to open loop
COIL SHORT Check cables, replace coil Yes
0KMh 11:35:07
SPIN‒M SALT‒C
0%0kg
LOW GATE: 05 HIGH
ENTER
Warn: OVERSPEED
Please Slow Down Truck

16
11 UNLOAD
To unload remaining material after completion of the spreading operation, activate by pressing both the
conveyor and the spinner dials simultaneously when spinner and conveyor rates are zero.
(Note: The vehicle must be stationary.)
WARNING: Once selected the conveyor or spinner has the ability to turn, and caution must be exercised.
Turn the dials until the desired speed is achieved. Press both the conveyor and the spinner dials simultaneously
to exit unload mode. Moving the vehicle will suspend the unload process. It will automatically resume when the
truck is stopped again.
12 SPREADING SCREEN
When truck is moving, system will display the spreading screen.
Pressing STAT will go to the diagnosis screen which displays the power voltage, actual conveyor RPM and rate.
Press and hold the REVS to change the direction of the conveyor / auger (if equipped). Release the button to
resume normal spreading.
0KMh 11:35:07
SPIN‒M SALT‒C
10% 10%
UNLOADING
GATE: 05
30KMh 11:35:07
SPIN‒M SALT‒C
0%30kg
GATE: 05
STAT REVS
VOLTAGE: 12V
CONVRPM: 0 CONV_ACTU: 0
QUIT

17
13 PAUSE / BLAST
The two knobs for spinner and conveyor are also labelled as ‘pause’ and ‘blast’. Press down the Pause button
(spinner) to pause spreading, and press again to resume spreading. If the controller is in pause mode when
powered off, the controller will start back up in pause mode once powered back on.
Press down the blast button (conveyor) to increase the spreading output, and press again or wait for the blast
timer to time out to resume the regular spreading rate.
Remote pause / blast is optional by connecting a momentary switch to the digital inputs on the sensor lead
cable.
When the blast timer is set to zero seconds in the setup screen, both the blast knob and the remote blast switch
work on the momentary mode, holding the switch or knob to activate blasting, release to stop blasting.
If the blast timer is not set to zero seconds in the setup screen, the knob and switch will work on the latched
mode. Press down the blast knob once to blast, blasting will stop once the timeout is reached or by pressing the
knob again will stop blasting before the timeout is reached. The remote blast switch works in the same manner.
Both the blast knob and the remote blast switch can work together, you can turn on blasting using the knob and
turn off from the remote blast switch, or vice versa.
For pause mode, it can be activated / deactivated in parallel either from the pause knob or remote pause switch.
14 UPDATE FIRMWARE
Copy the latest .bin file to the root directory of a USB Program Key and rename it to Rexroth.bin. With the
controller powered “off” insert the USB key into the USB port and then power “on” the controller, the controller
will upgrade the firmware automatically. Unplug the USB stick once “Verified” is shown on the display screen. If
“Verified failed” appears on the display, copy the Rexroth.bin file to the root directory of a blank USB key and
try again.
15 LOGGING REPORT
15.1 Import the logging data to computer
Once logging data is saved on the USB memory key (see section 8.5), it can be viewed on a computer with the
CS-530 Desktop Excel tool (CS530Logging_v3.3.xlsm).
Open the CS530Logging_v3.0.xlsm on your desktop and press the “Import Log Data” icon, the computer will
check to see if a USB log key is present. If log files are found, the truck log data files will be imported into and
displayed in the Region and Truck data field as well as in the data zone. A new dialog window will also pop up to
indicate the completion of the file import.
NOTE: The original log files will be deleted from the USB key.

18
15.2 Select Report
All the logging data will be displayed in the data zone. It is also possible to select the logging data involving
multiple trucks under a single region.
When selecting data, if the All Data option is selected and no specific truck is selected, then all the trucks in that
region will be used. Further filtered reports can be done by selecting truck name, date and time when Specific
is selected.
Data Zone
•Specific allows you to choose records within a selected timing frame
•To select the start and end of the date and hours

19
15.3 View Report
The logging reports will be displayed on the sheet called “Report” by clicking on ‘Display Truck’ after choosing
the criteria from the above sections. For example, here you can select region “Toroto” and truck “TUCK03”.
•Click Display Truck and it will go to the Report Sheet
Table of contents
Other REXROTH Controllers manuals
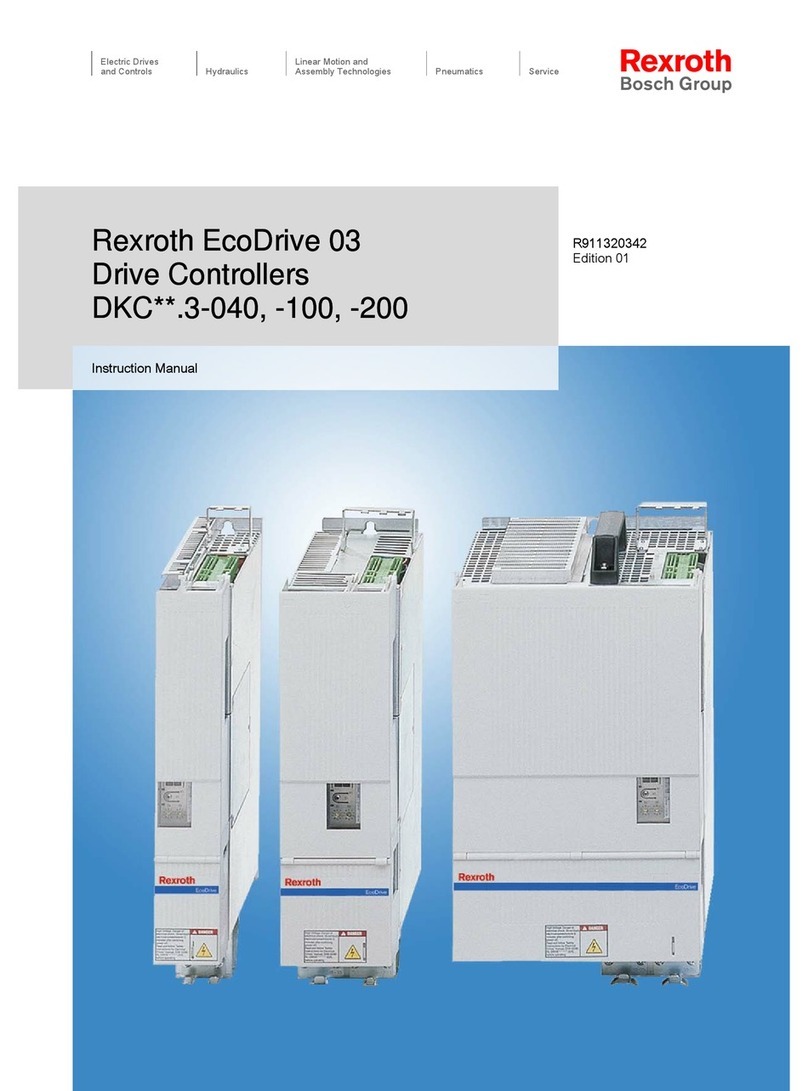
REXROTH
REXROTH EcoDrive 03 User manual
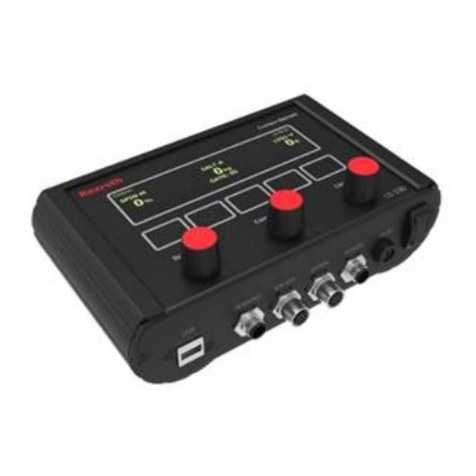
REXROTH
REXROTH CS 530 Instruction sheet
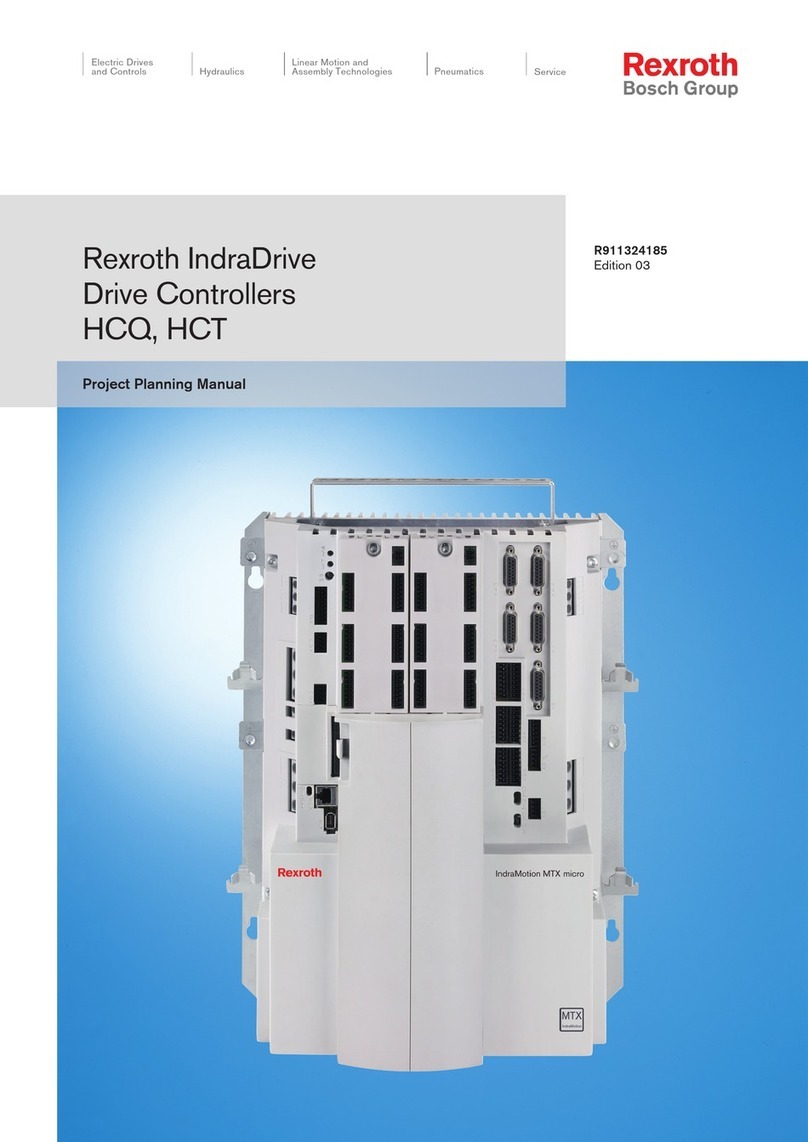
REXROTH
REXROTH IndraDrive HCQ02 Technical manual
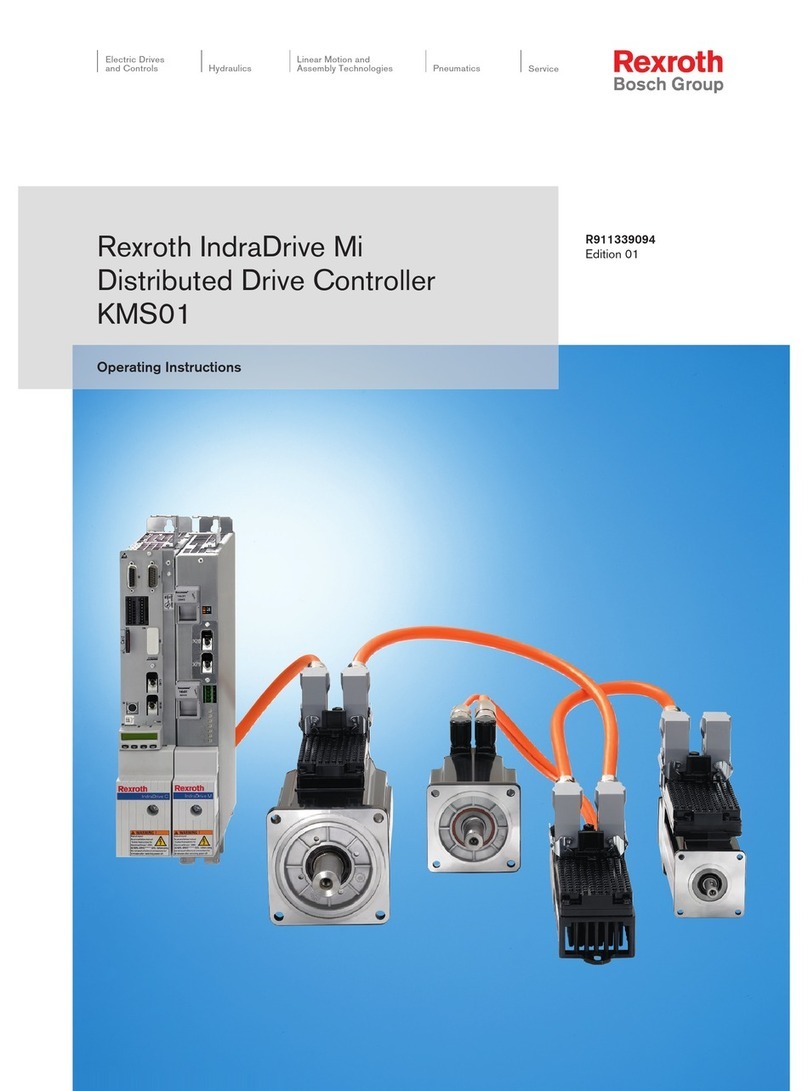
REXROTH
REXROTH IndraDrive Mi User manual
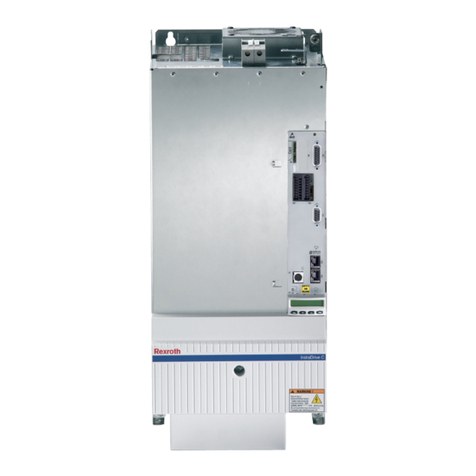
REXROTH
REXROTH HCS03 User manual
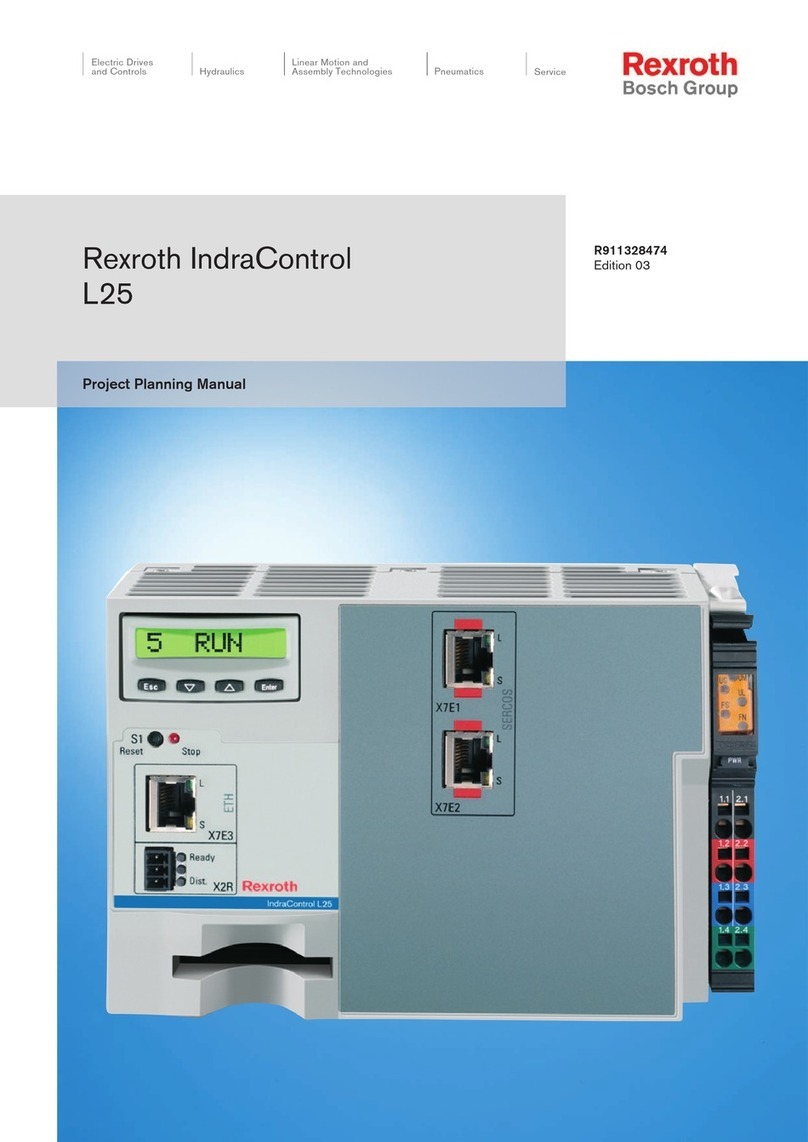
REXROTH
REXROTH IndraControl L25 Series Technical manual
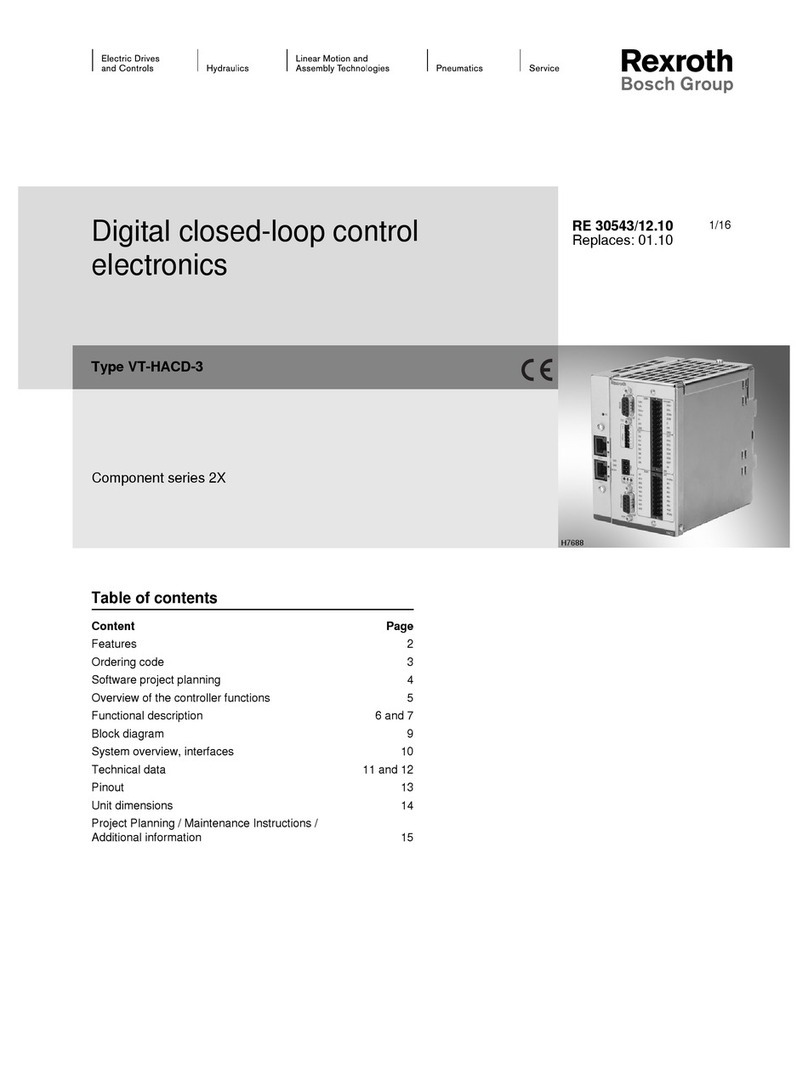
REXROTH
REXROTH VT-HACD-3-2 Series User manual
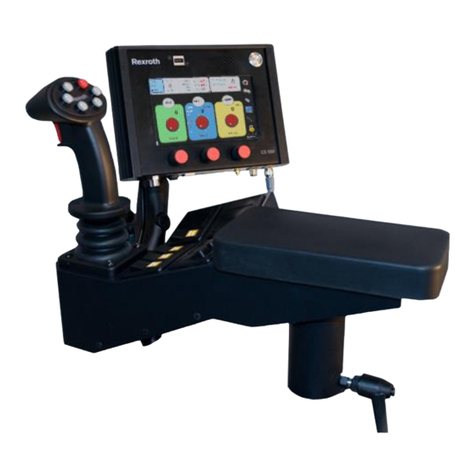
REXROTH
REXROTH CS 550i Use and care manual
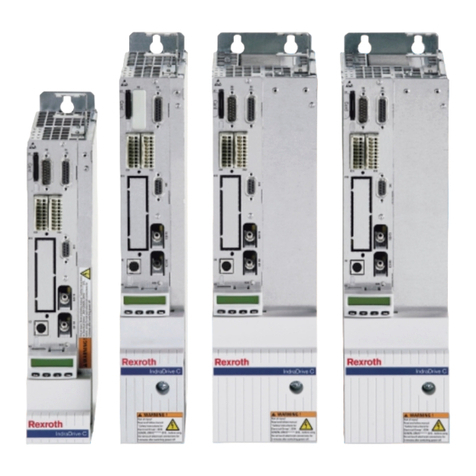
REXROTH
REXROTH IndraDrive C Series Technical manual
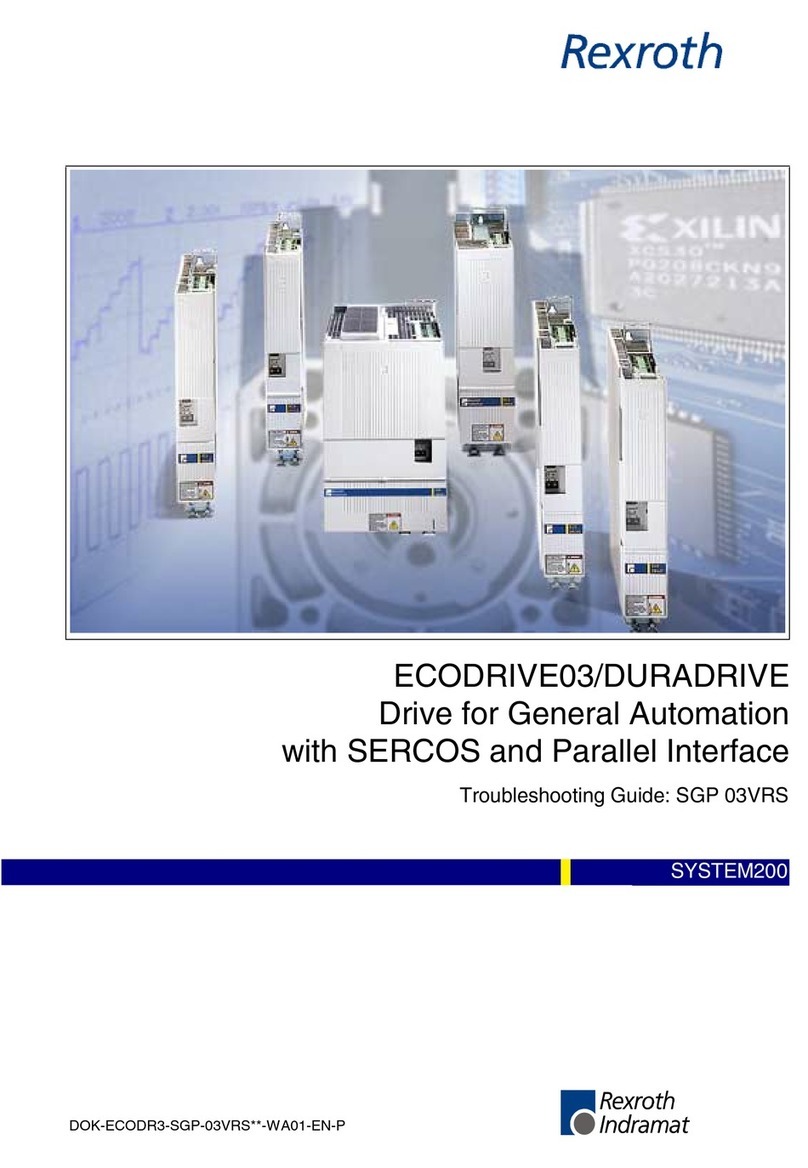
REXROTH
REXROTH ECODRIVE03 User manual