RHEONICS DVM-HPHT User manual

DVM20171127 DVM-HPHT Installation and Operating Instructions
Contents
1 ............................................................................................................................2
2 Setting up the system .....................................................................................................................3
3 Connecting and disconnecting wires to the terminal blocks on SME electronics ..........................3
4 Connecting sensor to transmitter electronics ................................................................................ 6
5 Powering the Transmitter ............................................................................................................... 6
6 Connecting 4-20 mA outputs .......................................................................................................... 7
7 Connecting Modbus RTU (RS-485) outputs ....................................................................................8
7.1 General.................................................................................................................................... 8
7.2 Wiring...................................................................................................................................... 8
7.3 Configuration .......................................................................................................................... 9
7.4 Input Registers ........................................................................................................................9
7.5 Data-Types ............................................................................................................................10
8 Operating the system.................................................................................................................... 12
9 Handling the Sensor......................................................................................................................13
9.1 Cleaning the sensor...............................................................................................................13
9.2 To remove the sensor: ..........................................................................................................14
9.3 To re-insert the sensor:......................................................................................................... 16
9.4 Mounting the DVM-HPHT .....................................................................................................19
10 Notes/Errata: ............................................................................................................................21

DVM-HPHT Installation and Operating Instructions
Page 2of 21
©Rheonics, Inc. 2013-17
Confidential to customer. Do not distribute without written permission of Rheonics, Inc.
1What’s in the box
The following items are delivered with the DVM-HPHT system:
•DVM-HPHT module with sensor installed
•SME Electronics (Transmitter housing or DIN rail housing)
•Sensor cable
•USB stick with software tool installer
•Tools for removing and re-installing sensor in the DVM-HPHT module
•Spare O-rings and backup rings for sensor
•USB cables
•Torque wrench
Based on your selection you may have a SME-TRD (SME Transmitter with Display) or SME-DRM (SME
DIN Rail Mount) as shown below
Torque
wrench
Sensor cable
Software
installer
Backup O-rings
HPHT-DVM Sensor
SME-TRD
USB cable
Sensor
Removal/
Insertion
tool
Cable gland

DVM-HPHT Installation and Operating Instructions
Page 3of 21
©Rheonics, Inc. 2013-17
Confidential to customer. Do not distribute without written permission of Rheonics, Inc.
2Setting up the system
The sensor measurement system consists of two components:
•HTHP DVM sensor and module
•SME Transmitter (Electronics unit)
The transmitter is shipped fully assembled. Gain access to the connections by unscrewing the cover
and removing the display (if ordered with display) by pulling it out. The SME electronics module is now
accessible for connecting the sensor, power, and communication cables.
3Connecting and disconnecting wires to the terminal blocks on
SME electronics
The wires are generally color coded, the ends should be crimped with 8mm diameter crimps. This
connection is valid for sensor cable, power cable, Modbus cable, 4-20 mA cables.
Torque
wrench
Sensor cable
Software
installer
Backup O-rings
HPHT-DVM Sensor
SME-DRM
USB cable
Sensor
Removal/
Insertion
tool

DVM-HPHT Installation and Operating Instructions
Page 4of 21
©Rheonics, Inc. 2013-17
Confidential to customer. Do not distribute without written permission of Rheonics, Inc.
To connect the wires, insert the crimped end in the correct port on the terminal block till it clicks firmly
in place and cannot be pulled out when tugging on the wires (do not tug on the wires with a lot of
force as that may damage the terminal block).

DVM-HPHT Installation and Operating Instructions
Page 5of 21
©Rheonics, Inc. 2013-17
Confidential to customer. Do not distribute without written permission of Rheonics, Inc.
To disconnect the sensor wires, press the white tab for that specific port with a small flat screw driver
as shown in picture below where the user is removing wire connected to port 1.
While pressing on the white part, pull out the cable connection with the other hand as shown in the
picture below.

DVM-HPHT Installation and Operating Instructions
Page 6of 21
©Rheonics, Inc. 2013-17
Confidential to customer. Do not distribute without written permission of Rheonics, Inc.
4Connecting sensor to transmitter electronics
The sensor is connected to the transmitter electronics by a sensor cable. Follow the color code table
below to connect the correct wires from the sensor cable to the sensor connection terminal strip on
the transmitter. The leads are delivered with crimped ends; cable can be shortened if needed, but
sleeves should be crimped on the stripped ends.
Wire Color
Sensor connection terminal #
Red
8
Blue
7
Pink (Rose)
6
Grey
5
Yello
4
Green
3
Brown
2
White
1
---not connected---
0
5Powering the Transmitter
Connect a 24V DC supply to the power input terminals on the transmitter.
Power input terminals are labeled with 24 V DC + and GND.

DVM-HPHT Installation and Operating Instructions
Page 7of 21
©Rheonics, Inc. 2013-17
Confidential to customer. Do not distribute without written permission of Rheonics, Inc.
It is important to avoid ground loops in the setup / plant where the SMET is used. Ground loops can
lead to excessive currents on the ground / return wire of the SMETs 24V power supply which can
damage the unit.
To prevent this, we strongly recommend that the SMET is powered by a separate 24V power supply
with galvanic separation. Otherwise, the SMET might be permanently damaged.
6Connecting 4-20 mA outputs
Load impedance: 0 to 720 Ohms
Output range: 4-20mA, (3.5mA error)
Galvanic isolation: none
Wiring Option (A)
•Connect positive terminal of current input module to desired channel terminal of SME device
•Connective negative terminal of current input module to negative power supply terminal used
for SME device
Wiring Option (B)
•Connect positive terminal of current input module to desired channel terminal of SME device
•Connective negative terminal of current input module to V- terminal of SME device
Notes
•The 4/20mA outputs are not galvanically isolated. It is not recommended to route the 4/20mA
to off-site locations if the corresponding 4/20mA input does not provide galvanic isolation.
4/20mA connection, self-powered
24V
Rheonics transmitter
+
-
4/20mA input
R4.36
+
-
4/20mA input
R4.36
+
-
4/20mA input
R4.36
+
-
4/20mA input
R4.36
+
-
VM+
V-
V-
CH1
CH2
CH3
V+
V-
B+
A-
Wiring Option (A)
Wiring Option (B)

DVM-HPHT Installation and Operating Instructions
Page 8of 21
©Rheonics, Inc. 2013-17
Confidential to customer. Do not distribute without written permission of Rheonics, Inc.
7Connecting Modbus RTU (RS-485) outputs
7.1 General
All SME devices implement a MODBUS RTU compliant RTU slave. The default configuration of the
MODBUS RTU slave is 38400 and ODD parity. Connection is by RS485-2W where the interface is not
electrical isolated.
7.2 Wiring
Wiring is RS485-2W. The device does not have internal biasing resistors and termination resistors and
proper setup of the RS485 network has to be ensured.
Termination: Termination should be only at the end and beginning of the bus to avoid reflections.
Requirements on termination differ not only on the baud-rate used but also on the slew-rate of device
internal drivers. As a general rule, if there are devices on the RS485 bus that allow fast transmission
speeds, and cable lengths exceed a few meters, then termination is required.
Biasing: Biasing of the RS485 BUS is required. If biasing is omitted, communication may work
unreliably or not at all. See figure below for Pull-Up/Pull-Down resistors.
Connections: Connection stubs on the RS485 bus should be kept to the minimum.
Common: RS485 does allow common mode voltages of +12V / -7V. It is therefore recommended to
use a common wire to ensure common mode voltage is within safe limits for all receivers. In case of
problems it might be necessary to introduce RS485 isolators into the network. The common terminal
for the SME device is the 0V terminal (GND) for the power supply.
RS485 MODBUS
24V
Rheonics transmitter
V+
V-
B+
A-
V+
V-
B+
A-
GND
+5V
GND
DO NOT CONNECT
EARTH TO GND for
marine applications
MODBUS
slave
Stub < 20m
Bus < 1000m
MODBUS
master

DVM-HPHT Installation and Operating Instructions
Page 9of 21
©Rheonics, Inc. 2013-17
Confidential to customer. Do not distribute without written permission of Rheonics, Inc.
7.3 Configuration
The SME device allows the configuration of the Modbus address using the RCP software. Please refer
to the RCP manual for instructions.
Factory default settings of Modbus parameters:
address=0 or 1
baudrate=38400
parity=odd
The system is capable of supporting:
•parity settings of odd, even and none
•baudrates of 9600, 19200 and 38400
7.4 Input Registers
The table uses PDU addressing; addresses start at zero. Depending on the PLC used it might be
required to add 1 to the addresses in the table below
Table 1: Modbus input registers.
Address (Dec)
Length of registers
Type
Description
Parameter 1
40
2
Float
Parameter 1 value as float
42
1
Int16
Parameter 1 value scaled by 100 as
signed integer
43
1
Uint16
Parameter 1 status (See datatypes)
Parameter 2
48
2
Float
Parameter 2 value as float
50
1
Int16
Parameter 2 value scaled by 100 as
signed integer
51
1
Uint16
Parameter 2 status (See datatypes)
Parameter 3
58
2
Float
Parameter 3 value as float
60
1
Int16
Parameter 3 value scaled by 100 as
signed integer
61
1
Uint16
Parameter 3 status (See datatypes)
Parameter 4
64
2
Float
Parameter 4 value as float
66
1
Int16
Parameter 4 value scaled by 100 as
signed integer
67
1
Uint16
Parameter 4 status (See datatypes)
Parameter 5
72
2
Float
Parameter 5 value as float
74
1
Int16
Parameter 5 value scaled by 100 as
signed integer

DVM-HPHT Installation and Operating Instructions
Page 10 of 21
©Rheonics, Inc. 2013-17
Confidential to customer. Do not distribute without written permission of Rheonics, Inc.
75
1
Uint16
Parameter 5 status (See datatypes)
Parameter 6
80
2
Float
Parameter 6 value as float
82
1
Int16
Parameter 6 value scaled by 100 as
signed integer
83
1
Uint16
Parameter 6 status (See datatypes)
Parameter 7
88
2
Float
Parameter 7 value as float
90
1
Int16
Parameter 7 value scaled by 100 as
signed integer
91
1
Uint16
Parameter 7 status (See datatypes)
Parameter 8
96
2
Float
Parameter 8 value as float
98
1
Int16
Parameter 8 value scaled by 100 as
signed integer
99
1
Uint16
Parameter 8 status (See datatypes)
7.5 Data-Types
Float: IEEE754 floating point. This data type spans two registers which should be read together.
Depending on the endianness of the host it might be necessary to swap high/low byte and/or the
respective registers.
Int16: Signed 16 bit integer (register)
Uint16: Unsigned 16 bit integer
Parameter status: The parameter status is a bitmask of individual status bits. As a general rule Bit 0
checking should be implemented where a set bit corresponds to an error/warning condition. In case
of a critical error the parameter value is also set to NAN (not a number See IEE754)
Bit 0: General error Check other bits for more detailed configuration
Bit 1: Internal configuration error Restart. If error persists call Rheonics for support
Bit 2: Hardware error, e.g. broken temperature sensor. Call Rheonics for support and arrange RMA
Bit 3: Dependency error: a parameter is calculated from other parameters and one of the source
parameter has an error. Check all other parameters for errors.
Bit 4: Device is starting up and no results are ready.
Bit 5: Internal error Restart. If error persists call Rheonics for support.
Bit 8: Parameter result is not stable. Check measurement conditions (flow, vibration, etc.)
Bit 15: Parameter exceeds sensor upper limit. No results available.
Bit 14: Parameter below sensor lower limit. No results available.

DVM-HPHT Installation and Operating Instructions
Page 11 of 21
©Rheonics, Inc. 2013-17
Confidential to customer. Do not distribute without written permission of Rheonics, Inc.
Bit 13: Parameter value above upper warning range. Measurements might not be accurate and sensor
performance might be reduced.
Bit 12: Parameter value below lower warning range. Measurements might not be accurate and sensor
performance might be reduced.
Here is an image of a fully connected transmitter.

DVM-HPHT Installation and Operating Instructions
Page 12 of 21
©Rheonics, Inc. 2013-17
Confidential to customer. Do not distribute without written permission of Rheonics, Inc.
8Operating the system
After installing the software and setting up the port, the system may now be started. The installation
of the Rheonics Control Panel (RCP) Software and its settings are described in the RCP manual.
THE ELECTRONIC BOX MUST BE ATTACHED TO THE COMPUTER WITH THE USB CABLE
AND POWERED UP IN ORDER FOR THE SYSTEM TO OPERATE
1. Connect the sensor to the Transmitter (instructions in section 2)
2. Connect power to Transmitter (instructions in section 3)
3. Connect the micro USB cable to the Transmitter electronics. Connect the other end to a free
USB port on the computer.
4. Now that the proper operating mode has been established, run the Rheonics Control Panel
software. The Rheonics Control Panel application is opened from the Start menu.
When the software is running, you will see a screen similar to the following:

DVM-HPHT Installation and Operating Instructions
Page 13 of 21
©Rheonics, Inc. 2013-17
Confidential to customer. Do not distribute without written permission of Rheonics, Inc.
For help about the Rheonics Control Panel (RCP) and its settings see:
Help -> RCP Rheonics Control Panel Software manual
9Handling the Sensor
The DVM-HPHT is a stable, robust sensor system that operates over a wide range of temperatures and
pressures. All wetted parts of the sensor system are made of Titanium Grade 5, which resists attack
by a wide variety of highly corrosive fluids.
In order to get optimum performance from the system, some simple guidelines must be followed.
9.1 Cleaning the sensor
The DVM-HPHT is based on a resonant sensor that operates in the range of approximately 7-8 kHz.
The sensor measures viscosity in a thin layer of fluid surrounding the resonant element. Any high-
viscosity fluids or tenacious solids that adhere to the resonator will distort its readings.
The resonant element contains small permanent magnets. If the fluid in which the resonator is
immersed contains suspended magnetic particles, these may likewise cling to the sensor and distort
its readings.
In any measurement scenario in which the sensor could become coated with tenacious fluids, solids,
or magnetic particles, it is recommended that the sensor be removed and mechanically cleaned.
Adherent films can be removed by using appropriate solvents, ultrasonic cleaning, and/or wiping with
solvent-saturated cloth or paper. Under no circumstances should abrasives be used to clean the
resonator, as these will change the geometry and destroy its calibration.
Magnetic particles may be removed by pressing scotch tape, masking tape, or similar pressure-
particles adhering by magnetic forces. Examine the sensor with a magnifying lens to satisfy yourself
that its surface is clean of particles.

DVM-HPHT Installation and Operating Instructions
Page 14 of 21
©Rheonics, Inc. 2013-17
Confidential to customer. Do not distribute without written permission of Rheonics, Inc.
Tools for removing and inserting the sensor are shown below:
9.2 To remove the sensor:
•Using the provided torque wrench, remove the sensor retaining screw. This will require
approximately 20 N.m of torque. It may be necessary to hold the DVM-HPHT in a bench vise
to apply the necessary torque. Use soft jaw covers in the vise to avoid marring the DVM-2000.
This will reveal the back of the sensor base, with its M4 threaded removal/insertion hole:
Torque
wrench
Sensor insertion/
removal tool
DVM
module with
sensor

DVM-HPHT Installation and Operating Instructions
Page 15 of 21
©Rheonics, Inc. 2013-17
Confidential to customer. Do not distribute without written permission of Rheonics, Inc.
•Holding the black ring of the sensor removal tool, screw in the M4 threaded rod:
•Holding the black screw grip, screw the threaded rod into the hole in the back of sensor as far
as it will go, finger tight:
•Holding the back of the threaded rod, screw the black ring clockwise against the upper surface
of the module, until it has backed the sensor out of the module:

DVM-HPHT Installation and Operating Instructions
Page 16 of 21
©Rheonics, Inc. 2013-17
Confidential to customer. Do not distribute without written permission of Rheonics, Inc.
9.3 To re-insert the sensor:
•Put a VERY LIGHT film of lubricant on the O-ring around the base of the sensor. Applying a
light film of lubricant to the O-ring rather than the bore of the module will tend to push the
lubricant AWAY from, rather than into the bore, minimizing any chance of contamination of
the fluid under test by the O-ring lubricant. In any event, very little lubricant is required.
Suitable lubricants include silicone grease, light mineral oil, petroleum jelly, or simply a bit of
the fluid whose properties will be measured.

DVM-HPHT Installation and Operating Instructions
Page 17 of 21
©Rheonics, Inc. 2013-17
Confidential to customer. Do not distribute without written permission of Rheonics, Inc.
•Screw the insertion tool (without the black ring) finger tight into the M4 thread on the base
of the sensor.
Exerting gentle pressure, rocking and turning the sensor slightly, push, while turn, the sensor
into bore in the module. Make sure that the locating tabs are sitting IN the locating notches
in the module:

DVM-HPHT Installation and Operating Instructions
Page 18 of 21
©Rheonics, Inc. 2013-17
Confidential to customer. Do not distribute without written permission of Rheonics, Inc.
•Unscrew the insertion tool from the sensor and make sure that the sensor locating tabs are
correctly oriented and sitting flush against the bottom of the locating notches in the module:
•Re-install the sensor retaining screw, screwing it down until it contacts the sensor. Now, using
the torque wrench with Allen key extension, tighten the sensor retaining screw to a torque of
20 N.m (15 lb.ft). It may be necessary to hold the DVM-HPHT in a bench vise to apply the
necessary torque. Use soft jaw covers in the vise to avoid marring the DVM-2000.
Sensor installation is now complete.

DVM-HPHT Installation and Operating Instructions
Page 19 of 21
©Rheonics, Inc. 2013-17
Confidential to customer. Do not distribute without written permission of Rheonics, Inc.
9.4 Mounting the DVM-HPHT
The DVM-HPHT module has four mounting holes. Two are through-holes for M5 socket head screws;
the other two are tapped with ISO M5 threads. The whole pattern for a mounting plate is:
Either the through holes or the tapped holes can be used, depending on the requirements of the test
setup.
The DVM-HPHT should be mounted with the sensor retaining screw on the top. This ensures that
small bubbles trapped in the
will not influence the measurements.

DVM-HPHT Installation and Operating Instructions
Page 20 of 21
©Rheonics, Inc. 2013-17
Confidential to customer. Do not distribute without written permission of Rheonics, Inc.
Fluid flow through the DVM-HPHT should follow the arrow marked on the cable-exit side. This makes
sure that fluid enters at the ends of the resonator tines, and leave near the base, sweeping any bubbles
toward the inactive (base) end of the sensor.
Please note that it is difficult to get accurate measurement with plain water stationary in the DVM-
HPHT measurement chamber. Even degassed water tends to have air dissolved in it, which eventually
forms micro bubbles on the surface of the sensor, disturbing its geometry. This is not a problem at
higher pressures, which tend to re-dissolve any gases present. Hydrocarbons, glycols, and other fluids
with low surface tension are less prone to bubble formation.
The DVM-HPHT will operate with flow rates in excess of 1 l/min. Flow may be in either direction,
subject to the above caution about the effects of bubbles.
Both fluid connectors are standard
exceed a pressure 2000 bars.
Fluid in
Fluid out
This end up
Table of contents
Popular Control Unit manuals by other brands
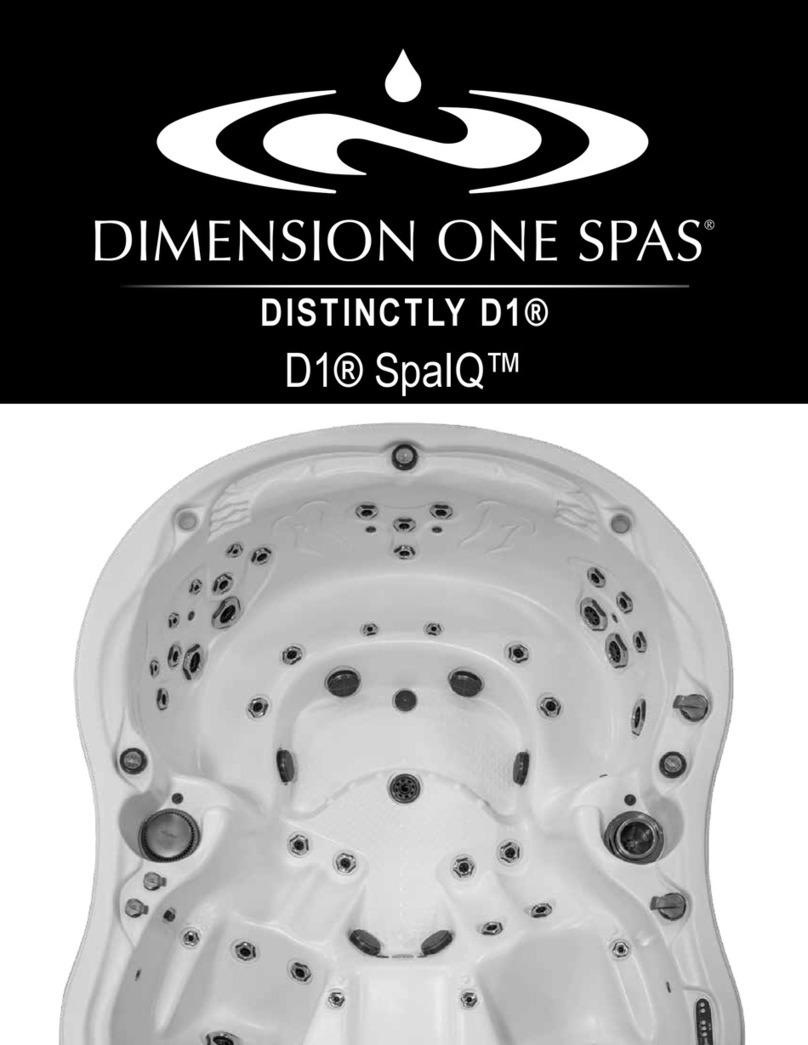
Dimension One Spas
Dimension One Spas D1 SpaIQ user manual
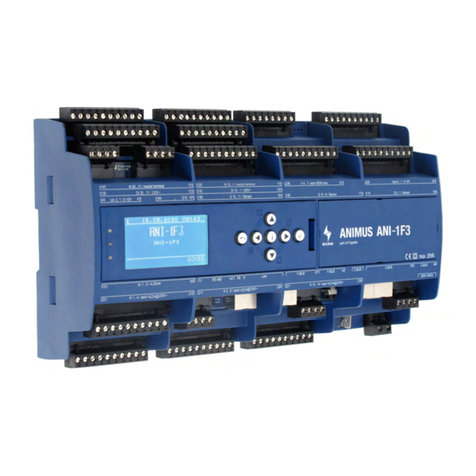
WURM
WURM FRIGOLINK ANI-1F3 manual
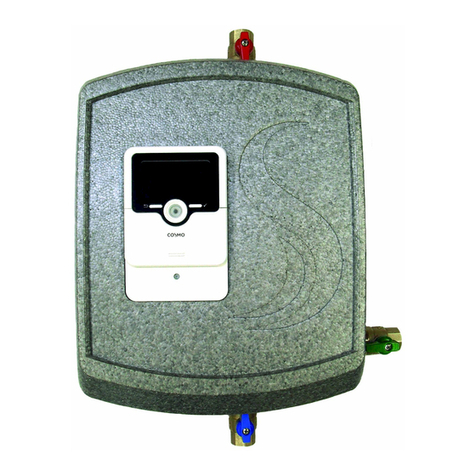
Cosmo
Cosmo CFWME Installation and operating manual
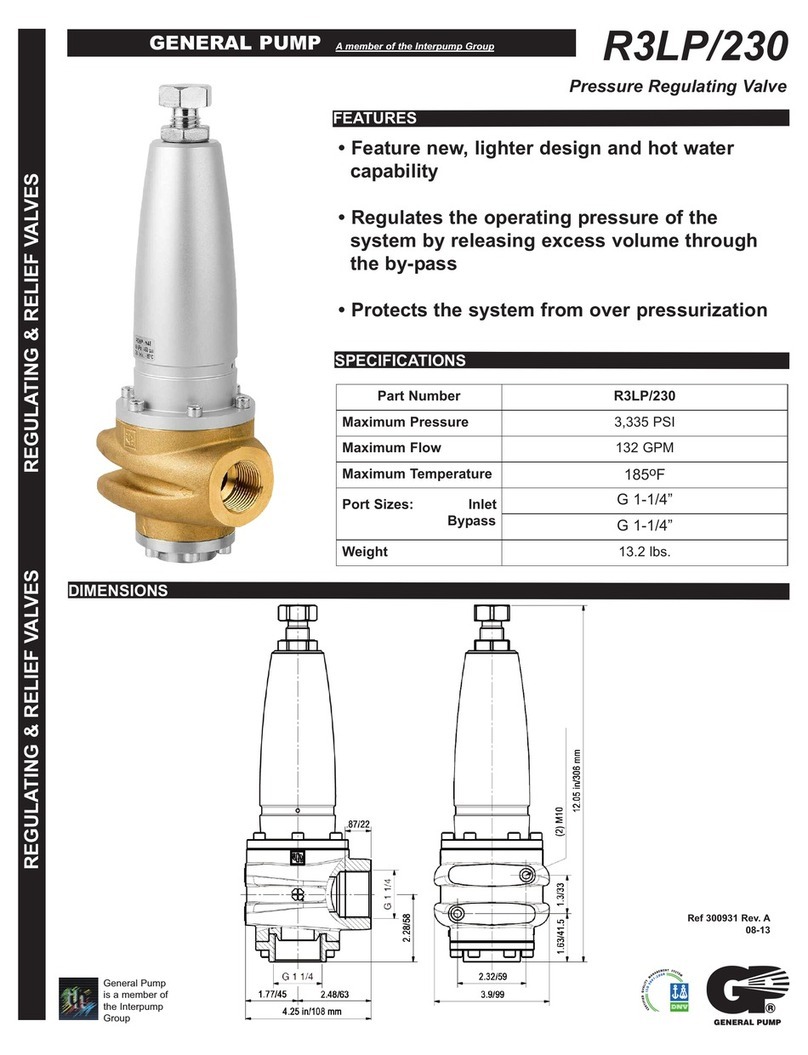
Interpump Group
Interpump Group GENERAL PUMP R3LP/230 quick start guide
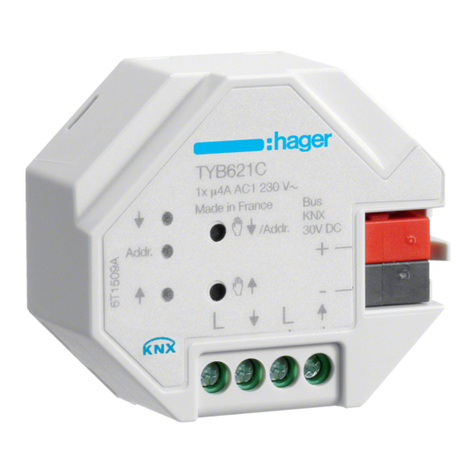
hager
hager TYB621C manual

Sun Microsystems
Sun Microsystems Sun Storage J4200 Replacement guide
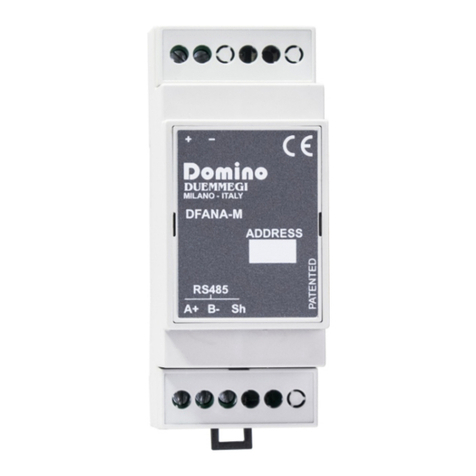
Duemmegi
Duemmegi Domino DFANA-M quick start guide
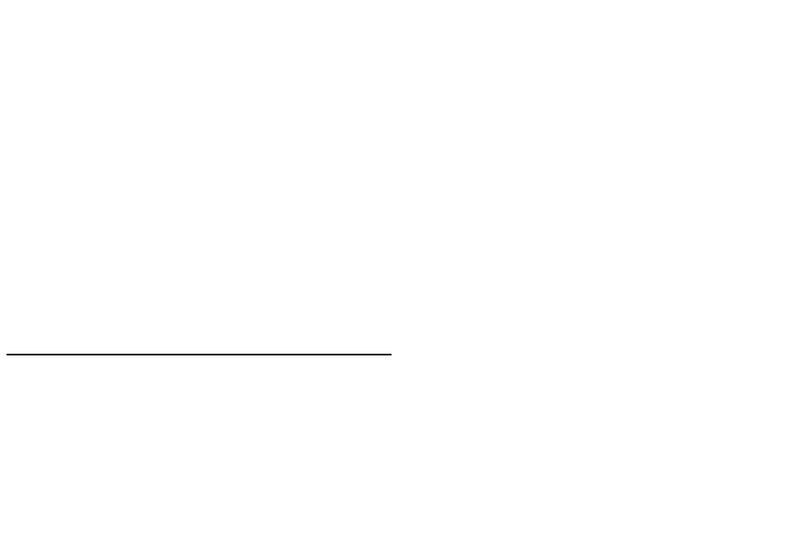
Fulling Motor
Fulling Motor FD542 user manual
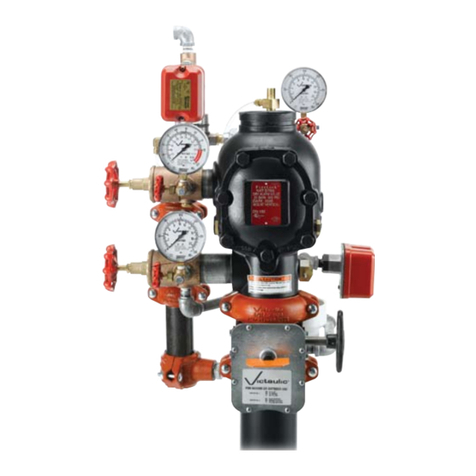
Victaulic
Victaulic FireLock NXT 768 Series Installation, Maintenance, and Testing Manual
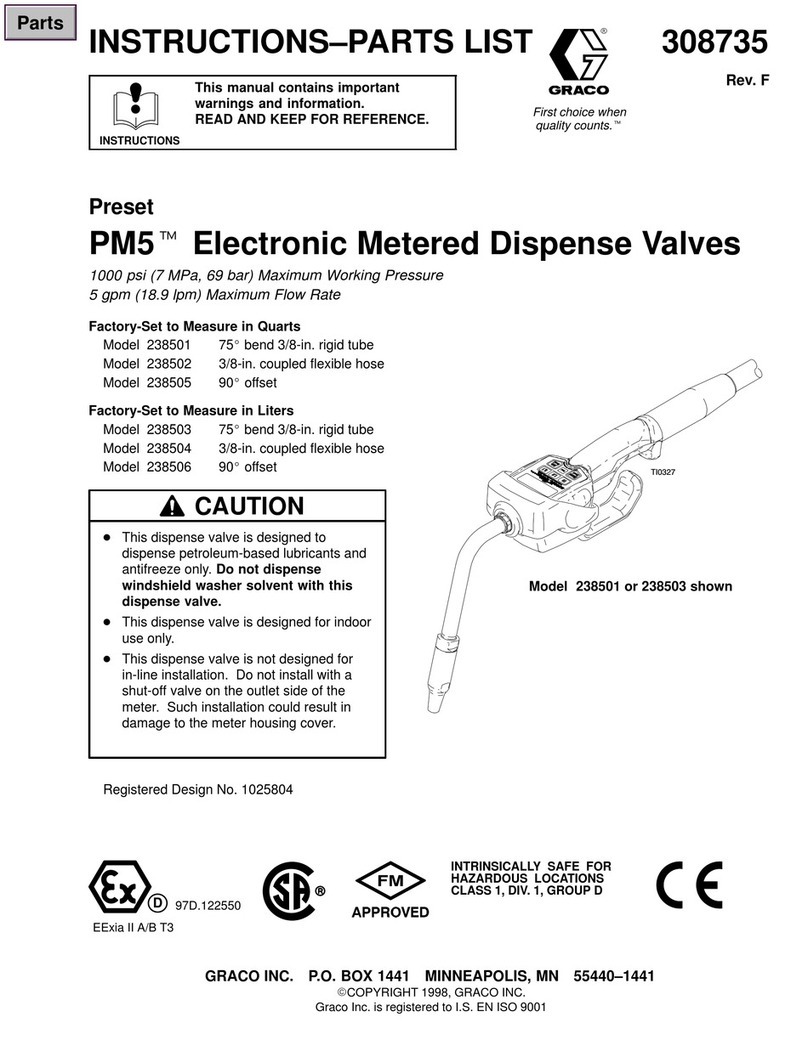
Graco
Graco PM5 238501 Instructions-parts list
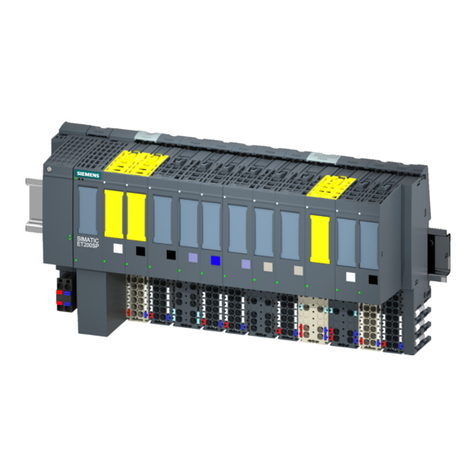
Siemens
Siemens SIMATIC ET 200SP manual
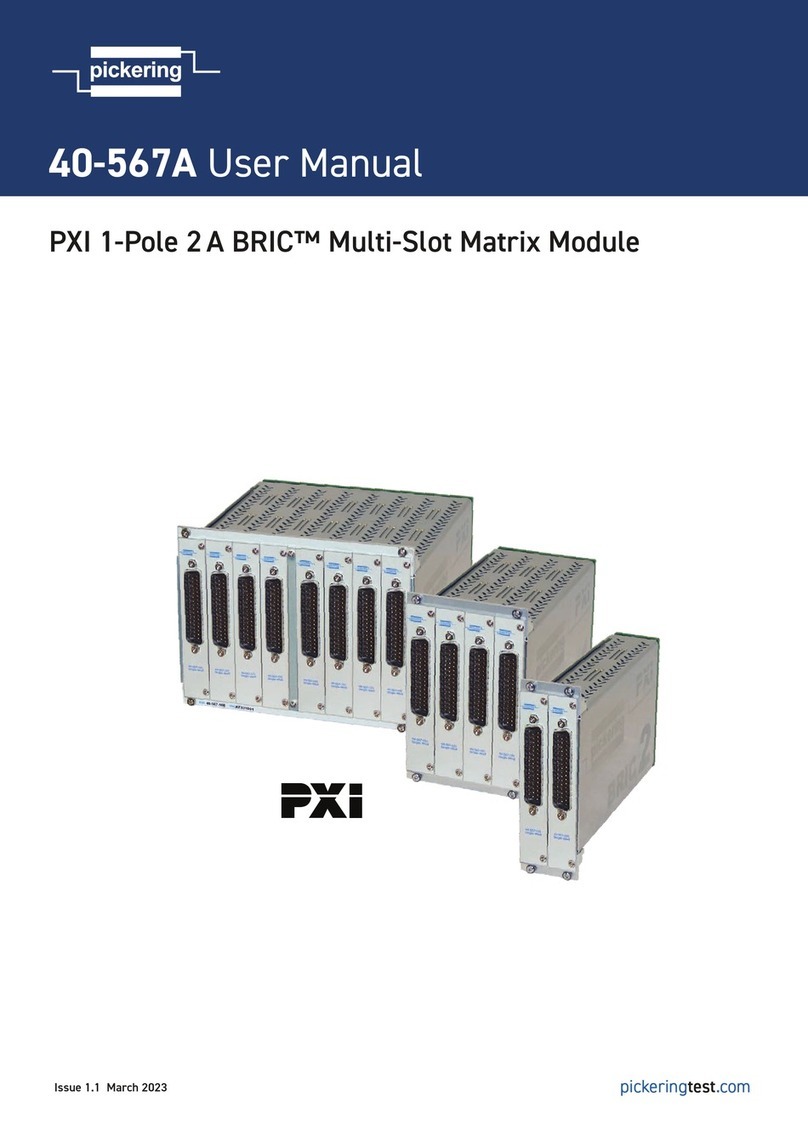
Pickering
Pickering 40-567A user manual