Richards 137NP User manual

Network Protector Instruction
Manual
Type 137NP
800 to 3500 Amperes
ichards
MANUFACTURING COMPANY, SALES, INC.
517 LYONS AVENUE, IRVINGTON, NJ 07111
Phone 973-371-1771 Fax 973-371-9538
IM 1224-001B


i
DISCLAIMER OF WARRANTIES AND LIMITATION OF LIABILITY
All equipment or component parts manufactured or distributed by Richards Mfg. Co.,
Sales Inc. are expressly warranted by Richards to be free from defect in workmanship or material
when subjected to normal and proper use. Said warranty shall be for a period of one (1) year
from the date of installation of such equipment not to exceed eighteen (18) months from the date
of shipment of such equipment. Notice of any claim arising out of this warranty shall be made in
writing within the warranty period. Richards’ sole liability and buyer’s sole remedy under this
warranty shall be limited to the repair or replacement, FOB factory, of any equipment or part
determined to be defective in either material or workmanship. This warranty does not apply to
any equipment, part or component requiring repair or replacement due to improper use or when
determined to have been subjected to abnormal operating conditions or in the event of buyer’s
failure to follow normal maintenance procedures.
No warranty or guarantee expressed or implied, including any warranty or representation as to
the design, operation, merchantability or fitness for any purpose is made other than those
expressly set forth above which are made in lieu of any and all warranties or guarantees.
Richards Mfg. Co. shall not be liable for any loss or damage, directly or indirectly, arising out of
the use of equipment or parts (including software) or for any consequential damages, including
but not limited to, any claims for buyer’s lost profits or for any claim or demand against the
buyer by a third party.
Richards Mfg. Co. assumes no responsibility for any damage or loss resulting from the use of
this manual. Information in this document is subject to change without notice.

ii
SAFETY INFORMATION
This manual is intended for use by qualified individuals responsible for the installation,
maintenance and operation of network protectors. Potentially unsafe conditions exist when
installing, maintaining or operating network protectors.
All applicable safety procedures should be adhered to when installing, maintaining, or operating
network protectors.
Only qualified electrical personnel should be permitted to work on 137NP Network Protectors.
De-energized and rack out the network protector mechanism before any maintenance procedure.
Never defeat safety interlocks on the network protector.
Never energize a partially assembled network protector.
Use extreme caution when installing or working on an energized protector.
Use insulated tools and gloves when working on energized network protectors.
Perform all appropriate electrical tests before any installation or operation of the network
protectors.
WARNING
Before unpacking, installing, servicing, or operating 137NP network protectors read this manual
thoroughly.
For additional information, contact Richards Mfg. Co. directly.
For application information, consult Richards Mfg. Co. or see appropriate ANSI Standards.
Do not operate 137NP network protectors under load except in appropriate enclosures.
The Richards 137NP Network Protectors are designed for secondary network application at
125/216 volt and 277/480 volt wye connected systems. Do not exceed design ratings.

iii
Submersible Transformer Mounted

iv

v
TABLE OF CONTENTS
PAGE
I.OVERVIEW 1
A.Introduction 1
B. 137NP Submersible Network Protector 1
C. 137NP Non-Submersible Network Protector 2
II.INSTALLATION 2
A. Receiving, Handling and Storage 2
B.TransformerMounted 3
C.SeparatelyMounted 3
D.OpeningEnclosures 4
E.RemovingtheBreakerUnit 4
F.Connections 7
G.RelayInstallation 7
III.MAINTENANCE 8
A. Schedule 8
IV.INSPECTION AND TESTING 10
A.Phasing 11
B.ManualOperation 11
C.Electro-mechanicalRelays 11
D.ETIMNPR®MicroprocessorRelays 12
E.ElectricalTesting 12
F.CheckingtheMinimumTrippingVoltage 13
G. Checking the Minimum Motor Closing Voltage 13
H. Checking the Motor Control Device 14
I.MechanicalChecks 14
J.ReturntoService 14
V. THE REMOVABLE UNIT 15
A.ArcQuenchers 15
B. Contact Construction 800 through 1875 Ampere Protectors 18
C. Contact Construction 2000 through 3500 Ampere Protectors 19
D. Assembly of 2000 through 3500 Ampere Contact Head 20
E. Current Transformers 22
F. Auxiliary Switch 22
G.MechanicalIndicator 24

vi
H.OperatingMechanism 24
I.MotorControlDevice 26
J.TripMechanism 27
K.OperatingMotor 31
L.TorqueBrake 32
M.GearAssembly 33
N.ManualOperation 33
O.ManualCutoffSwitch 34
P.ClosingLinkage 34
VI.THEENCLOSURE 34
A.CoverGasketReplacement 35
B.ChangingLocationofOperatingHandle 36
C.Packing 37
VII. DIAGRAMS
Wiring Diagram, 125/216 Volt, 800-1875 Amp Protectors 38
Schematic Diagram, 125/216 Volt, 800-1875 Amp Protectors 39
Wiring Diagram, 277/480 Volt, 800-1875 Amp Protectors 40
Wiring Diagram, 277/480 Volt, 800-1875 Amp Protectors 41
Wiring Diagram, 125/216 Volt, 2000-3500 Amp Protectors 42
Schematic Diagram, 125/216 Volt, 2000-3500 Amp Protectors 43
Wiring Diagram, 277/480 Volt, 2000-3500 Amp Protectors 44
Schematic Diagram, 277/480 Volt, 2000-3500 Amp Protectors 45

1
I. OVERVIEW
A. Introduction
The automatic network protectors covered by this instruction book are of the heavy duty,
motor-operated types for application in secondary AC network systems and are designated as
submersible and non-submersible.
The Richards 137NP Network Protector consists of a circuit breaker, a motor operated
mechanism, and an ETI Microprocessor Network Protector Relay that combines the
functions of a network master relay, and a network-phasing relay. The ETI MNPR®
provides all modes of operation, including sensitive, insensitive, time delay, instant, watt-var,
and inverse watt-var.
B. 137NP Submersible Network Protector
The 137NP network protectors consist essentially of a circuit breaker, a motor operated
mechanism, the necessary controlling relays, and auxiliary apparatus. These are all enclosed
in a water-tight case, for use in locations subject to submersion.
The breaker unit is an integral unit which is removable from the enclosure. The breaker
forms the rear portion of the unit with the operating mechanism and relay equipment in front.
The cover of the enclosure may be hinged from either side. Clear glass inspection windows
permit reading the operation counter and inspection of the fuses without opening the cover.
The enclosure is provided with an external handle for manual operation of the breaker unit.
This handle may be mounted on either side of the case as desired. A pressure test valve is
provided so that the enclosure may be tested for air tightness. Convenient pipe plugs are also
located on the side of the enclosure to permit installation of external auxiliary circuits, if so
desired. Lifting eyes are provided on all enclosures. Temporary and permanent mounting
supports are additional provisions. The cover is sealed to the case with gaskets compressed
by clamping strips and bolts.
There are two general styles of 137NP network protectors; one with the protector arranged
for wall or framework mounting independently of the network transformer, “Separately
Mounted”, and the other for bolting on to a three phase network transformer, “Transformer
Mounted”. Separately mounted protectors are arranged for connection of the cables from the
network transformers at the bottom of the enclosure and those to the network at the top. In
the transformer mounted style the connection to the transformer is made by bolting the
protector buses directly to the transformer secondary terminals.
Standard terminal facilities consist of various configurations of tangs, studs and quick
disconnect terminals surrounded by an insulator. Limiter and non-limiter terminals are also
available.

2
C. 137NP Non-Submersible Network Protectors
The non-submersible 137NP network protectors are generally similar to the submersible
except that non-submersible enclosures are provided. These protector units are for
applications in clear dry vaults. Equipment mounted enclosures (open framework) protectors
are also available.
As in the case of submersible protectors the non-submersible type may be arranged for wall
or framework mounting, or for bolting directly to the network transformers. Terminal
facilities may be arranged for connection of one to four cables per phase, or for bus bar
connections.
All protectors are arranged to permit the ready removal of the breaker unit without disturbing
the cable connections.
II. INSTALLATION
CAUTION: ALL NETWORK PROTECTORS MUST BE MOUNTED VERTICALLY.
It may be well for original users of this device to set one up temporarily in a service shop, so as
to become familiar with its characteristics and construction before installation on the system.
See section on Opening Enclosures.
A. Receiving, Handling and Storage
Care should be exercised when unpacking a protector so that no damage is caused in any
way, and a careful inspection made to see that no parts are damaged, missing or destroyed
with the packing material. Mounting hardware (transformer mounted protectors) is shipped
in separate cartons. Relays are shipped in separate cartons.
In handling or storing network protectors, always keep top up as marked on packaging.
Unsupported network protectors are unstable. Before removing shipping packaging, it is
recommended that a protector be supported from a sling or other suitable means to keep it
from falling over when the crating is removed.
Lift and handle the uncrated protector by the lifting eyes at the top of the case.
NOTE: Do not use the lifting eyes provided on the breaker unit for handling the complete
equipment mounted protector. These lifting eyes are provided for handling the breaker unit
only. Slings with spreaders are recommended to prevent damage to the upper terminals and
barriers of the protectors.
Transformer-mounted, top-connected, submersible and non-submersible protectors are
provided with permanent feet so that these protectors will rest upright on the floor.
Separately mounted submersible protectors are provided with temporary feet to protect the

3
lower terminals when these protectors are set upright on the floor. These feet may be
removed, when these protectors are bolted in position, to provide clearance for making cable
connections.
Equipment-mounted protectors will not stand unsupported on the floor. When handling or
resting these protectors on the floor, be careful not to damage the lower barriers or terminals
and, if necessary, place a block under the channel framework
If the protectors are not to be used for some time, store in the packaging in which received.
B. Transformer Mounted Protectors
Submersible and Non-Submersible Units
Remove the breaker unit before mounting the enclosure of transformer mounted protectors
on the transformer. Then remove the throat plate from the rear of the enclosure. The throat
gasket is supplied with the network transformer. Mounting hardware is shipped in a separate
bag including the lower supporting feet and the necessary hardware for securing the protector
to the transformer.
The transformer throat gasket supplied with the network transformer should be treated with
Glyptal and assembled to the clean surface of transformer throat flange. This gasket will be
held in position by the dowel pins on this flange.
Lift the protector enclosure and guide it into position using the dowel pins provided on the
transformer throat flange. Then tighten all throat bolts down evenly so that the throat gasket
is compressed from about 40 percent to 50 percent of its thickness. Add the feet at the
bottom of the enclosure using the proper number of spacers between the bottom of these feet
and the transformer.
Just before placing the unit into the protector, clean the transformer terminals with the back
of the bus bar of the protector. Use a brass wire brush and then wipe with a clean cloth.
C. Separately Mounted Protectors
Separately mounted network protectors may be mounted on a suitable framework or against
the wall. The submersible protectors are secured in place by the two lugs at the bottom back
of the enclosure. The non-submersible protectors are secured in place by mounting either in
a pipe framework or placing bolts through the holes provided in the back of the channel
framework
After submersible, separately mounted, protector enclosures are permanently mounted the
feet at the bottom of the case may be removed for better access to the terminals.

4
D. Opening Enclosures
Before opening the enclosure, submersible and non-submersible protectors should be
mounted in their final locations or if to be temporarily supported they must be securely
anchored by the lifting eyes to a firm post or part of a building to keep the protector from
tipping forward. To make inspection easier, the protector may be set up on some blocks, but
if this is done, make sure the bottom of the protector cannot move when the breaker unit is
rolled forward.
Most equipment mounted protectors may be rested upright on the floor without removing the
lower barriers or lower terminals. However, when the lower barriers or terminals extend
below the bottom of the channel frame the protector will have to be rested on blocks placed
under the channels. Firmly secure these protectors to a post or a part of the building so that
they will remain upright.
If the relays are to be tested on a temporarily mounted protector, the protector must be in a
vertical position.
After temporarily supporting or permanently mounting the protector, the enclosure may be
opened by unscrewing the cover bolts. If necessary, pry the cover open but do not damage
the gasket with the instrument used to pry the cover loose.
E. Removing the Breaker Unit (see Figure 1 and 2)
Submersible and Non-Submersible Protectors
Remove the fuses and disconnects as outlined below for the different arrangements of
protectors. Then lift the folding rails up and forward and lower them to the horizontal
position so that they form a continuous surface with the rail in the enclosure. The unit may
be rolled forward, after removing the four mounting screws.
WARNING: The manual operating handle must always be in the OPEN position
before the breaker unit can be rolled forward or back into position for remounting in
the enclosure.
1. Transformer Mounted Protectors
Top connected protectors. Warning, the following sequence must be followed. First
remove the fuses without disturbing the fuse connecting blocks, then remove the fuse
connecting blocks and the screws securing the protector unit to the low voltage
transformer bushing. Reverse above procedure for replacing the protector unit.
2. Separately Mounted Protectors
Remove the fuses at the top of the protector and the disconnecting links at the bottom of
the protector.

5
3. Equipment Mounted Protectors
The breaker units for the various arrangements of equipment mounted protectors may be
removed in a manner similar to which the breaker units are removed from submersible
and non-submersible protectors.
Figure 1 - Removable Unit Rolled Out On Rails

6
Figure 2 – Removable Unit Supported From Lifting Eyes

7
F. Connections
Cable connections should not be made until after fuses have been removed from protector.
Do not replace fuses until all tests and checks outlined under INSPECTION AND
TESTING have been made.
G. Relay Installation
After the protector has been installed either permanently or temporarily for testing, the
network protector relay may be installed in the protector.
To install the relay, unscrew the knurled thumbscrew, move the claw-shaped cam
counterclockwise and then place the relay in position, making sure that the contact blades on
the relay line up with the stationary contacts. Move the cam clockwise to jack the relay into
position. Screw knurled thumbscrews down to secure the relay. The relay is now free to
swing through a large angle. To fasten the relay in its operating position, move the relay
clockwise and pull latch forward.
New network protectors are wired for microprocessor type relays unless otherwise specified.
1. Closing In On Dead Networks
a. Electromechanical Relay
Network protectors with electromechanical relays may not close on a dead network to
which there is no connected load. To be sure protectors will always pick up a dead
network, particularly on a new system, or on spot networks for power only, it is
recommended that a resistor load of 500 watts be connected between phase to which
the phasing relay is connected and ground. Or on delta-connected systems, connected
250 watts between each phase (750 watts total). A 5.0uf capacitor may be used in
place of the 500 watt resistor and 2.0uf capacitor in place of the 250 watt resistors.
When the load on the secondary network grid reaches a point where all of the load
will never be disconnected, the above mentioned resistors or capacitors may be
removed from the grid.
b. ETI MNPR® Microprocessor Relay
Network protectors with ETI MNPR® microprocessor relays will close on a dead
network with or without connected load.

8
III.MAINTENANCE
A regular inspection and maintenance schedule for network protectors is recommended. While
experience will best indicate the frequency with which inspections should be made, the following
routine is suggested.
In all cases open the protector manually and lock in the open position first, then remove fuses
and the test caps before working on or inspecting or testing protector.
A. Schedule
1. At Installation
Complete inspection and test. See INSPECTION AND TESTING.
2. After First 24 Hours of Automatic operation
Read operation counter to make sure that the protector is not operating excessively.
Twenty-five operations or less are not excessive for initial installations, and even fifty
operations are not too many if the network load is to be increased soon. Additional load
will eliminate a large percentage of the operations. If the number of operations during
the first 24 hours is considered excessive, a check should be made to see that the
mechanism operates positively. If it does, the protector is being operated by numerous
power reversals. To correct this, the programming of the relay may need to be revised.
3. After First 48 Hours
Again read operation counter. If the number of operations is normal, daily reading may
be discontinued.
4. After First Week
Read operation counter.
5. After First Month
Read operation counter.
6. After First Six Months
Complete inspection and test.

9
7. Yearly
Fully inspect and test protectors including relays and perform the following preventive
maintenance.
a. Remove breaker from the enclosure and inspect and clean the contacts.
b. Check wiring terminals for tightness.
c. Remove trip mechanism and inspect and clean mechanism if necessary. The
protector mechanism is thoroughly lubricated at the factory and this lubrication
should last for some time. However, if it appears that the mechanism requires
lubrication, use SAE-30 machine oil on bearings. Wipe off all excess as the
excess will collect dirt and nullify the effect of the lubricant.
d. The bearings of the secondary latch shaft, Figure 15, should have just a drop of
SAE-30 machine oil added if necessary and the latch surface should be coated
very thinly with high grade petroleum jelly, to prevent rust.
e. Check the level of the lubricant in the gearbox, Figure 17. If necessary add
sufficient #4 hydraulic oil
f. Remove one brush holder and brush from motor and inspect commutator surface
with flashlight. If necessary, remove and disassemble motor and clean
commutator.
g. Lubrication of the motor bearings should not be necessary during the life of the
motor. However, if lubrication is found necessary after a number of years,
remove the motor, dismantle it, wash the bearings out thoroughly and repack them
with a small quantity of grease.
h. Clean torque brake when motor is removed.
i. Check auxiliary switch contacts and clean if necessary.
j. Check motor control device contacts and clean if necessary.
k. Check mechanical indicator.
8. After Heavy Primary Short Circuits
Inspect protectors which have interrupted short circuits, cleaning the devices and
resurfacing the breaker contacts.
9. De-energize Primary Feeders
Each feeder should clear completely, as indicated by the feeder voltmeter, if all the
protectors are set to trip on transformer exciting current. On re-energizing the feeder,
each protector should reclose as the load increases.

10
IV.INSPECTION AND TESTING
CAUTION: DO NOT OPERATE THE PROTECTOR, EITHER MANUALLY OR
ELECTRICALLY, UNLESS IT IS IN A VERTICAL POSITION.
Before placing the protector in service it should be tested. Tests may be made with protector in
its final location or with the protector in a temporary location in the service shop. If temporarily
located be sure to secure the protector as described under Receiving, Handling and Storage.
The breaker unit of submersible protectors may be either bolted in place in the housing or rolled
out of the rails.
Always open the protector manually first; second, open the enclosure cover; third, remove fuses,
and fourth remove all test caps before testing, working on, or inspecting the protector.
Test caps, Figure 3, located on the auxiliary panel below the breaker mechanism, provide a
means of disconnecting control wiring from the main circuit. This is accomplished by removing
insulated test caps to de-energize control wiring and tightening these test caps to energize control
wiring. With the insulted test caps removed, provision is made on the projecting studs for the
attachment of test clips so that control wiring may be energized from a separate source.
On new installations the fuses should be removed before the cables are connected and should not
be replaced until the following tests are completed.
The protectors are shipped with the manual operating handle wired in the open position, the trip
latch tied up and the folding rails wired down. Remove these ties before starting tests.
Figure 3 – Auxiliary Panel, Potential and Test Switches

11
A. Phasing
Phase out connections to protector to insure that “cross-phase” connection will not be made
when the breaker is closed. Network voltage is available on network side of fuse mounting.
Transformer voltage is available on opposite end of fuse mounting when the protector is
closed.
B. Manual Operation
Close and open the breaker several times by hand. To do this swing the manual operating
handle from the “open” to the “closed” position and when the breaker is closed return to the
“open” position. The breaker should close with considerable pressure. If the hand-wheel of
the motor is turned the motor cam may be advanced to a position where it will prevent the
normal resetting of the mechanism after tripping. If this happens, turn the hand-wheel
clockwise until the mechanism resets. Then turn two more revolutions. Now close the
breaker manually and trip by lifting the extended lever above the trip coil. Repeat this
operation, returning the manual handle to the “automatic” position. The trip mechanism and
operating mechanism should reset.
C. Electro-mechanical Relays
The correct operation of the electromechanical type network master relay depends upon the
application to the relay coils of currents and voltages of the proper phase sequence. For this
reason the phase sequence of the network should be checked before putting a protector into
service. This can be done by making a temporary reconnection of the phasing relay and
observing its operation as follows:
1. Make the temporary change in the wiring of the phasing relay as indicated on the
wiring diagram for the network protector.
2. Replace test caps B, C, and F only.
3. Trip protector open and move operating handle to “open” position. Do not close
protector during this test.
4. Connect the network side of the protector to the network.
5. Observe the operation of the phasing relay contacts. If the relay contacts close with a
strong torque toward the right, the phase sequence is 1, 2, 3. If the relay contacts
open or move to the left, the phase sequence is 3, 2, 1.
The phase sequence of the protector is determined by the lead connections as shown on
the wiring diagram. In general, network protectors are wired for 1, 2, 3 phase sequence at
the factory. Protectors may be obtained which are wired 3, 2, 1 phase sequence if
desired. (Note: Protectors wired for 1, 2, 3 phase sequence may be used with a 3, 2, 1

12
phase sequence provided four leads are interchanged in accordance with the wiring
diagram).
6. Return the phasing relay connections to normal.
7. Remove test caps B, C, and F for the following tests.
D. ETI MNPR® Microprocessor Network Protector Relays
The relay will not close its contacts on a crossed phase system. It is, also, insensitive to
phase sequence and will function accurately for protectors wired with phase sequence 1-2-3
and installed on systems wired 3-2-1.
E. Electrical Testing
When these observations have been completed the protector may be operated electrically to
check the mechanism operation. These tests should be performed using a network protector
test kit. Explicit instructions are included with these test kits. If a test kit is not available the
following method can be used.
1. Remove the electromechanical or solid state relay and insert a jumper across
terminals 1 and 2 (wire No. 6-6A) of the phasing relay plug (if provided).
a. On 120/216V units connect a 216V source to studs K and L to energize the
operating circuits. Connect the closing contact of a control switch to terminals 2
and 3 (wire No. 6-11) of the master relay plus and a tripping contact to terminals
1 and 3 (wire No. 41-11). Activate the “closing contact” of the control switch. If
the manual operating handle of the protector is in the automatic position the
protector will close.
Activate the “tripping contact” of the control switch. The protector should now
trip.
Turn the manual handle to the “open” position. Activation of the closed contact
of the control switch should not close the protector.
b. On 277/480V units connect a 480V source to studs 11 and 21 for trip circuit test,
and studs 11 and 3A for motor and motor control circuit tests. Repeat test a.
above.
If the mechanism over travels, and goes through a trip-free operation before closing, remove
the motor and clean torque brake. If the breaker has been turned upside down or front side
down, oil from the gearbox may run into the torque brake making it ineffective.
Table of contents
Popular Protection Device manuals by other brands
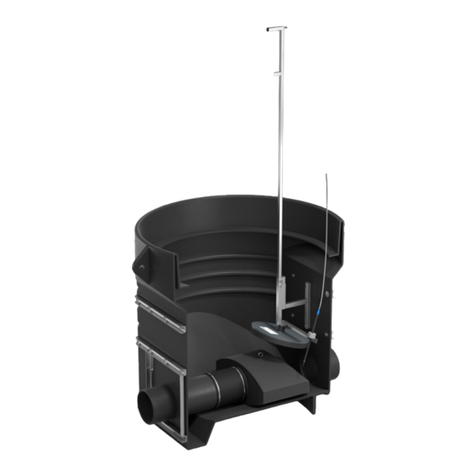
WAPRO
WAPRO WaBack DN110-200 installation instructions
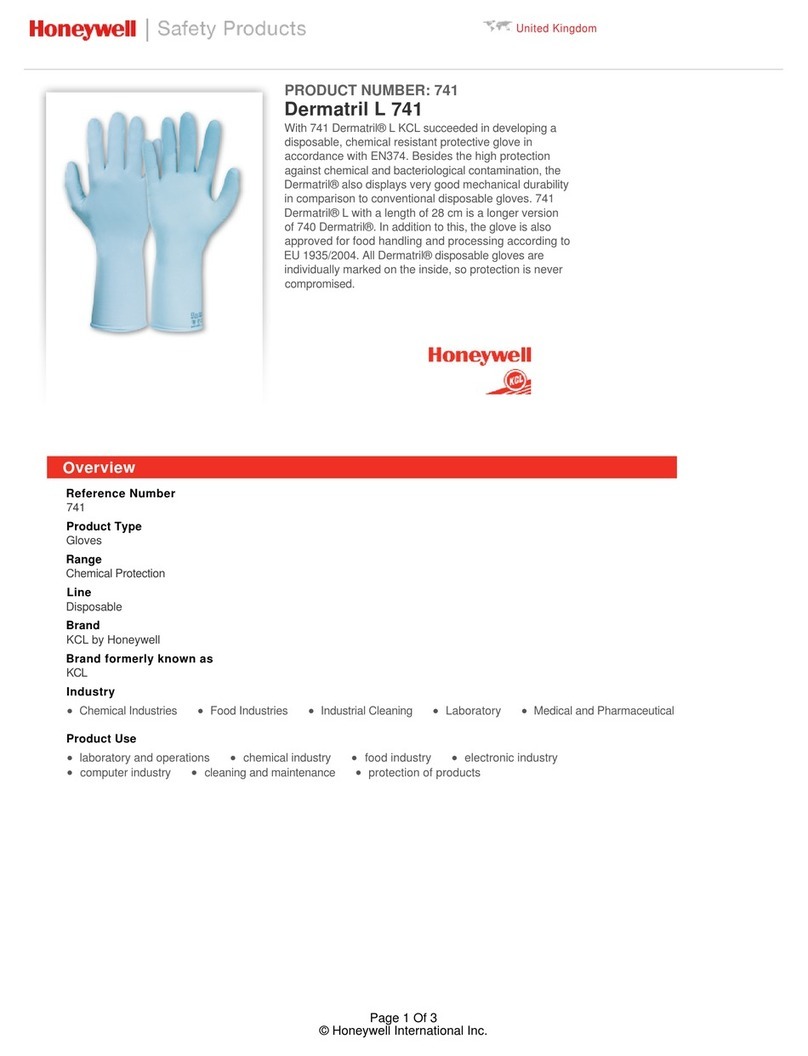
Honeywell
Honeywell KCL Dermatril 740 Information Brochure
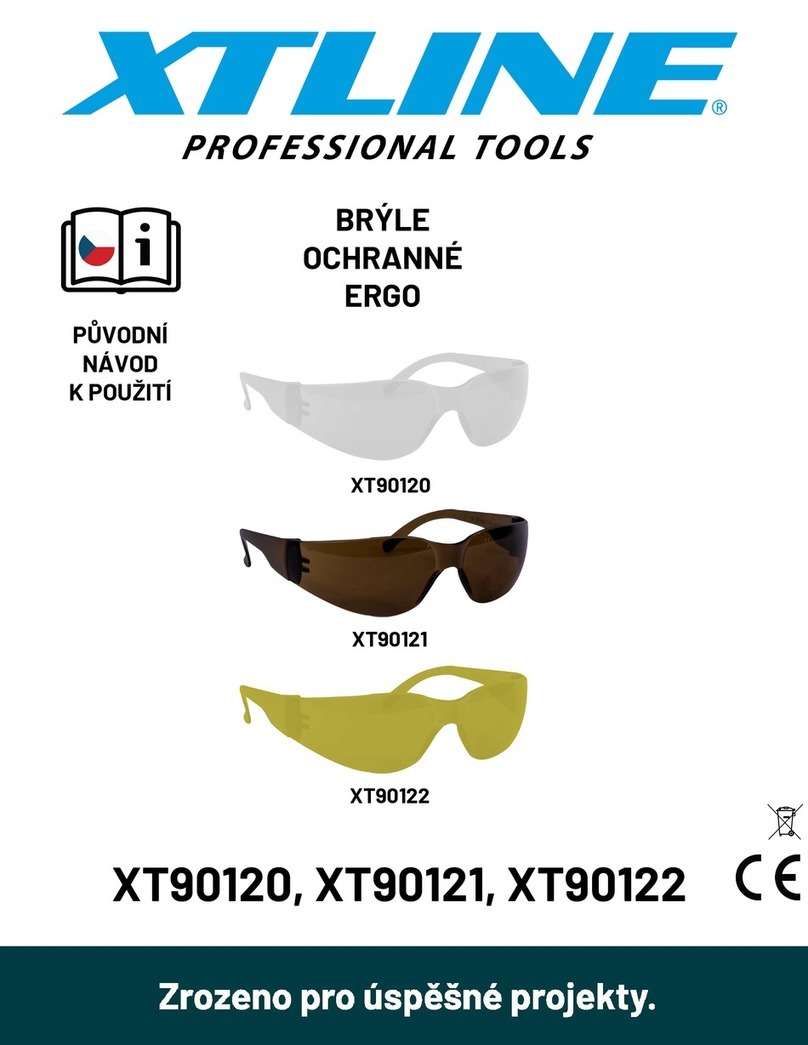
XTline
XTline ERGO XT90120 Original instruction manual
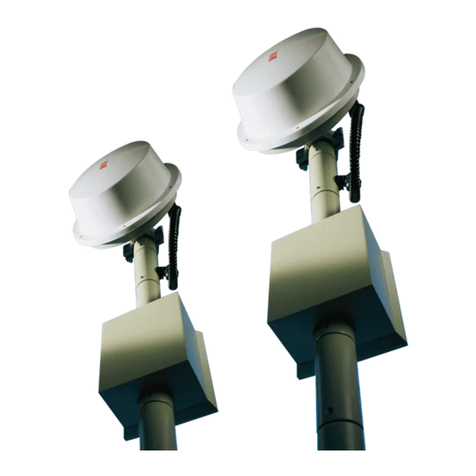
cias
cias ERMO 482 Installation handbook

Allen-Bradley
Allen-Bradley TLS1-GD2 installation instructions

NRS Healthcare
NRS Healthcare Double EasyFit Bedguard User instructions