Rish PFC 08L User manual

Power Factor Controller
RISH PFC 08L
Operation Manual
REV-A 05/2019

Installation & Operating Instructions
Section Contents
1. Introduction
2. Measurement Reading Screen
3. Set Up Screens
4. Installation
4.1 EMC Installation Requirements
4.2 Case Dimension and Panel Cutout
4.3 Wiring
4.4 Auxiliary Supply
4.5 Fusing
4.6 Earth/Ground Connections
5. Connection Diagram
6. Specifications
REV-A 05/2019
1

1. Introduction
The Power Factor Controller is a modern
control device of innovative design with
auto bank detection function.
It is designed for a measuring voltage of
80 to 300 Vac. Display of Power Factor with
Auto Detection Function makes ease of
operation.
Main Features:
- 4/6/8 switching outputs.
- Autoitialisation function for Minimum settings
CT ratio is optional
Bank kVAr detection
Phase correction angle detection
Number of bank detection
- Various bank kVAr input method
Programmable individual bank kVAr value,
Auto detection of bank value,
1- 9 standard control series.
- Fault detection for Under Voltage, Over Voltage and Under Current.
- Capacitor bank protection by switching off capacitor bank for faults.
- Manual relay test mode
- Ultra bright LED Display.
- Compact size of 96 x 96 with low back depth.
- Adaptable to 144 x 144 panel cutout by use of adapter plate.
- Onsite Programmable PFC parameters
L1
L2
L3 V
x1000
LAG
LEAD PF
2

L1
L2
L3 V
x1000
LAG
LEAD PF
x1000 Multiplier Indication
Lag Indication
Lead Indication
Down Key
Parameter Name
Parameter Value
Up Key
Display is ultra bright 3 Digit LED display with power factor value with lead
and Lag indication.
L1
L2
L3 V
x1000
LAG
LEAD PF
3

2 . Measurement Reading Screen
"PF" on the screen indicates
Power Factor parameter.
"0.98" inductive on the screen
indicates Power Factor value.
Lag LED glows when power factor
is inductive.
Lead LED glows when power factor
is capacitive.
Lead / Lag LED is also used for
target power factor programming
x1000 LED glow when CT primary
multiplier is 1000 in setup screen
Keys are used for navigation through
menu and for changing parameter
values.
L1
L2
L3 V
x1000
LAG
LEAD PF
Fault Messages displayed on screen:
1. "uU" - Under Voltage.
2. "oU" - Over Voltage.
3. "uC" - Under Current.
4. "uCC" - Under Compensation Capacitor.
5. "oCC" - Over Compensation Capacitor.
L1
L2
L3 V
x1000
LAG
LEAD PF
4

Setup Parameter Screens
Mod
(Bank Mode Selection)
Ato (Auto Initialization )
CtL
(Control Series)
Cnt
(No of Capacitor Banks)
CAP
( Capacitor Bank kVar )
C01
CtL
CtS
(CT Secondary)
Ato
CtP
(CT Primary)
Cod
(Password)
out
(Quit from Setup)
Ato: For selecting Auto mode
Select Ato or CtL
CtL: For selecting control series
or User defined cap. bank kVar
Select yes / no
yes - To retrigger Auto init.
....
Refer section 3.2
....
Refer section 3.3
....
Refer section 3.4
Refer section 3.6
...
Refer section 3.5
...
....
Refer section 3.7
....
Refer
section 3.8
tPF
(Target power factor )
....
Refer section 3.1
rly
(Manual relay on/off)
A
A
Refer
section 3.9
....
C0n
.
.
.
.
n=number of
banks
available
5

3. Setup Screen
Upon pressing both Up and Down keys simultaneously for 3 sec "Cod" screen
is displayed. Entering of correct code scrolls all programmable parameters.
Key function which common to all parameters are explained below
L1
L2
L3 V
x1000
LAG
LEAD PF
Editing of digits ( Setting value )
Upon display of setup parameter label pressing key enter into setup
and present value is shown. Pressing key the Most significant digit
( first digit from left ) starts blinking, pressing key increases in digit
value pressing key confirms digit and move to next digit editing till 3rd
digit. After all three digits programmed as desired pressing key results in
confirmation of value and display shows "SET", Pressing key scroll to
next parameter.
In some of cases instead of digits
label option need to be set
Code ( Password )
The Screen shown is used for
authentication purpose. Pressing of
key allows user to enter password
here. correct password results
in setup parameter editing else PFC
will show "Err" message and exit to
the measurement screen.
default code is 000. and cannot be
changed.
x1000
LAG
LEAD PF
6

3.1 Target power factor Setting
The Screen followed by label tPF is
target power factor setting.
once required PF value to set then
LAG or LEAD PF can be set on LEDs'
Range for power factor is 0.8 Lead to
0.8 Lag.
Default value is 0.99 Inductive
3.2 CT Primary Setting
The Screen shown further is used to set
CT Primary. Pressing Key will
enter into CT Primary Setup.
Pressing the key select for x1000
Multiplier selection. Pressing the will
change the decimal position.
Annunciation of "x1000" indicates the
value in Kilo. Pressing the will select
the decimal point position and multiplier
now CT Primary Value can be edited
The range of CT Primary is 1A to 9.99
kA.
Default is 5.00 A.
L1
L2
L3 V
x1000
LAG
LEAD PF
L1
L2
L3 V
x1000
LAG
LEAD PF
7

Undercurrent fault value are set with
respect to CT primary.
The value of 1 kA is as shown in the
screen
if valid value set then, pressing
to move forward for CT Secondary
Setting.
3.3 CT Secondary Setting
The Screen shown further is used to
set CT secondary. pressing Key
enter into CT secondary Setup.
For editing the value press key.
pressing will scroll between 1A
or 5A and Set value using Key.
The possible values are 1A or 5A.
The default value is 5 A.
use key for moving to next
parameter
L1
L2
L3 V
x1000
LAG
LEAD PF
x1000
LAG
LEAD PF
8

3.4 Capacitor Bank Selection Mode:
The Screen displays "Mod" followed by
Its mode "Ato" or "CtL" .
Pressing the will enter to edit capacitor
bank selection mode.
Pressing will scroll between "Ato" and
"Ctl" mode.
to set value press key.
After pressing the will display "Set"
Message.
Now press to move forward for next setting depending upon the mode
selected.
Control Mode(CtL) : User can select capacitor bank from control series
option.If "CtL" selected Auto Initilisation menu (Section 3.5) is skipped .
Auto Mode(Ato) : If Auto Selection mode is selected the values detected in
Auto Initialization are used for PF Correction .If "Ato" selected Control series
menu ,Number of banks Menu, Capacitor bank value Menu is skipped.
3.5 Auto Initialization Setting:
The Screen displays "Ato" followed by
Yes or No. Default is Yes.
Pressing the will enter to edit value.
Pressing will change to No if
previously it was set as Yes or
vice-versa. After Setting Yes Auto
Initialization will be performed.
L1
L2
L3 V
x1000
LAG
LEAD PF
x1000
LAG
LEAD PF
9

At start of Auto Initialization display shows "Ato"
1. Auto Init enables detection of phase correction angle between voltage and
current , number of capacitor bank and capacitor bank kVAr connected.
Auto option will become "No" automatically once auto initialization is completed
successfully.
2. For successful auto init voltage should be healthy, otherwise Auto Init will be
terminated and display shows "InP" and test is aborted.
3. For detection of phase correction angle the power factor should be in range
of 0.6 Lag to 0.99 Lag. if detected successfully then display shows angle on
screen.
4. Load conditions are stable and No error detected then average of three
attempts of capacitor bank kVAr values is calculated by switching capacitor
bank one after other. and three attempts are made to get capacitor bank kVAr
values.
during capacitor switching the attempt
number with bank position is shown
followed by capacitor kVAr value
measured."A-P" indicates Auto Init
Pass and "A-F" indicates Auto Init Fail
5.During Auto init Screen displays
"Ato" followed by "diS" at power on
Auto Init will be started after Discharge
time delay. if auto int fails due to some
reason then after predefined time or at
each Power On it will be re attempted.
here shown various screens during
auto init. depending on state
x1000
LAG
LEAD PF
x1000
LAG
LEAD PF
x1000
LAG
LEAD PF
x1000
LAG
LEAD PF
x1000
LAG
LEAD PF
x1000
LAG
LEAD PF
Auto init
function started
Auto fail
attempt1
Auto angle
detection failed
Attempt1
of capacitor1
for kVAr
Auto Init
Successful
Phase corr.
Angle detected
x1000
LAG
LEAD PF
x1000
LAG
LEAD PF
Auto Init
Failed
Blinking Ato
Phase Corre.
angle detection
in process
10

3.6 Control Series Setting:
This Setting is for selecting capacitor
bank values in control series mode
The Screen displays "CtL" followed by
previously set Control Series Value.
Pressing the will enter to edit value of
control Series.
The range of control series setting is "1 to 9"
and "u". selecting value from 1 to 9 select
control series which represents ratio of capacitor banks with respect to first
bank. selecting "u" select user defined capacitor bank values which
represents actual kVAR value ( not ratio )
select value using key and for setting the value press the Key.
The Control Series are as given below:
1. Control Series 1: {1,1,1,1,1,1,1,1}
2. Control Series 2: {1,2,2,2,2,2,2,2} Selecting 1 will show as above.
3. Control Series 3: {1,2,3,3,3,3,3,3}
4. Control Series 4: {1,2,3,4,4,4,4,4}
5. Control Series 5: {1,2,4,4,4,4,4,4} Selecting u will show as above.
6. Control Series 6: {1,2,3,6,6,6,6,6}
7. Control Series 7: {1,2,4,4,4,4,4,4} Note: If control series 1 to 9 is
8. Control Series 8: {1,2,4,8,8,8,8,8} selected then device will
9. Control Series 9: {1,1,2,4,8,8,8,8} accept only C01 value.
Default control series Number is 1. if "u" is selected
and default C1 value is 25 kVAR. then all capacitor bank values
Default capacitor bank value for ‘U’ is need to be entered
25 kVAR for all capacitor banks
L1
L2
L3 V
x1000
LAG
LEAD PF
.
11

3.7 Number of Banks Setting:
The Screen displays "Cnt" followed by
previously set Number of Banks count.
Pressing the will enter to edit number
of capacitor banks count. The range of
setting is depending on orderd instrument
or previously detected in auto init function.
Maximum value is 8.
Select value using key and for Setting the same
press the key. This screen is not shown if auto mode is selected.
After Setting the Number of banks count ,Press key to move to capacitor
bank kvar Value Setting.
3.8 Capacitor Bank kvar Value Selection:
The Screen displays "CAP". Pressing the
key will enter to edit kvar value of capacitor
bank. The Screen will display "C01" followed
by its kvar value. the range of value is 1 to
to 250. if control series is 1 to 9 then only
C01 screen shown and next capacitor bank
screens not shown. For control series U all
bank screen C01...C0n are shown and value
can be set as per bank count set previously.
Sideby is screen for bank 1 with 25 kvar value.
L1
L2
L3 V
x1000
LAG
LEAD PF
L1
L2
L3 V
x1000
LAG
LEAD PF
The Control Series Selection will act as an Multiplier for the Capacitor Banks.
Selecting the Control Series 1 will select multiplier {1,1,1,1,1,1,1,1} for
Capacitor Bank 1 to 8 depending on number of outputs.
After Setting the Series Press key to move to Number of Banks Selection.
12

if CtL as "u" the value entered in C01 will be the Capacitor Bank value. The value
entered in CXX will be the value for respective Capacitor Bank.
After setting the values for number of selected banks pressing the will move
forward to manual relay on-off function.
if CtL as bank mode ( 1 - 9 ), the value enetered in C01 will be set as the
multiplicand for Capacitor Banks.
Example: The value set in Control Series is 3 - {1,2,3,3,3,3,3,3} and C01 is
2 kVAR then the Bank values will become C01(Bank1) = 2kVAr x 1 = 2 kVAr,
C02(Bank2) = 2kVAr x 2 = 4 kVAr, C03(Bank3) = 2kVAr x 3 = 6 kVAr and
so on.
3.9 Manual relay On - Off
The screen display "rLY".
pressing key shows relay number
corrosponding to capacitor. press
key shows relay current state. pressing
key on state screen enables relay
to switched ON or OFF depending on
current state relay state.
scroll to next capacitor
using key.
Sideby screens shown are possible
in relay test mode
L1
L2
L3 V
x1000
LAG
LEAD PF
x1000
LAG
LEAD PF
x1000
LAG
LEAD PF
Relay
off
Relay
on
x1000
LAG
LEAD PF
x1000
LAG
LEAD PF
Relay is
blocked
in logic and
off
Relay is
blocked
in logic and
on
13

3.10 Quit
The screen will display "out".
for quitting the programming menu
press key. else to reprogram the PFC
press key the meter will scroll back
to first display screen.
L1
L2
L3 V
x1000
LAG
LEAD PF
14

4. Installation
Mounting of PFC is featured with easy “Clip- in” mounting. Push the instrument in panel slot
(size 92 x92 mm), it will click fit into panel with the four integral retention clips on two sides
of instrument.
If required Additional support is provided with swivel screws (optional) as shown in figure.
Easy Clip -in
mounting
Swivel screw
As the front of the enclosure conforms to
IP 50. additional protection to the panel may
be obtained by the use of an optional panel
The PFC should be mounted in a
reasonably stable ambient temperature and
where the operating temperature is within
the specification . Vibration should be
gasket. The terminals at the rear of the
product should be protected from liquids.
kept to a minimum and the product should
not be mounted where it will be subjected
to excessive direct sunlight.
Caution
1. In the interest of safety and functionality this product must be installed by a qualified
engineer, abiding by any local regulations.
2. Voltages dangerous to human life are present at some of the terminal connections of
this unit. Ensure that all supplies are de-energised before attempting any connection
disconnection.
3. These products do not have internal fuses therefore external fuses must be used to
ensure safety under fault conditions.
15

4.1 EMC Installation Requirements
This product has been designed to meet the certification of the EU directives when installed
to a good code of practice for EMC in industrial environments, e.g.
1. Screened output and low signal input leads or have provision for fitting RF suppression
components, such as ferrite absorbers, line filters etc., in the event that RF fields cause
problems.
Note: It is good practice to install sensitive electronic instruments that are performing critical
functions, in EMC enclosures that protect against electrical interference which could cause a
disturbance in function.
2. Avoid routing leads alongside cables and products that are, or could be, a source of
interference.
3.
4.
To protect the product against permanent damage, surge transients must be limited to
2kV pk. It is good EMC practice to suppress differential surges to 2kV at the source.
The unit has been designed to automatically recover in the event of a high level of
transients. In extreme circumstances it may be necessary to temporarily disconnect the
auxiliary supply for a period of greater than 5 seconds to restore correct operation.
ESD precautions must be taken at all times when handling this product.
4.2 Case Dimensions and Panel Cut Out
16

4.4 Auxiliary Supply
PFC should ideally be powered from a dedicated supply, however it may be powered
from the signal source, provided the source remains within the limits of the chosen auxiliary
voltage.
4.5 Fusing
It is recommended that measuring voltage and capacitor contactor voltage to be taken from
4.6 Earth/Ground Connections
For safety reasons, panels and accesoriess should be grounded in accordance with
4.3 Wiring
Input connections are made directly to screw-type terminals with indirect wire pressure.
Numbering is clearly marked on the connector. Choice of cable should meet local regulations.
2 2
Terminal for inputs will accept up to 4mm (12 AWG) or 2.5mm (12AWG)Standard
Note : 1) It is recommended to use wire with lug for connection with instrument.
2) For disconnecting the device a switch or circuit-breaker shall be included at the
site and shall be within easy reach of the operator. The specification are as below.
For aux. = At least 1.2 times of applied Power supply.
For Measuring Input = At least 1.2 times of applied measuring inputs.
same phase with proper fusing.
relative electrical and safety standards.
17

5. Connection Diagram
L1 (R )
L2 (S )
L3 (T )
N
mea s. cur rent
Im (1 A-5A ) 1. ca paci tor-
bra nch
k l
P1
1 2 3 4 5 6 7 8
capa c itor
cont a ctors 1- 6
T 6,3 A
T 2A
T 2A
K1
I I‘
sup ply-
vol tage
mea s.
vol tage
VLN
AUX L N
pow er fac tor
con trol ler
P2
capa c itor
cont a ctors 7- 8
For 8 relay
(1) (2) (4) (5) (6) (7)
18

6. Specifications :
Feature:
Display 3 Digit 7 Segment Display(14mm digit height)
Parameter Displayed Power Factor
Technical Data:
Weight 0.25Kg.
Case Panel Mounted Instrument
96 x 96 x 35 mm
(Back Depth 55mm with Add on Module)
(Cut Out 92+0.8 x 92+0.8 mm)
Ambient Conditions
Over Voltage Class III
Polution Degree 2
Operating Temperature 0..+55 °C
Storage Temperature -20...+65 °C
Sensitivity to EMC IEC61326-1:2010
Safety Guidelines IEC61010-1:2010
Mounting Position Flush Mounting
Humidity Class 15%...95% Non Condensing
High voltage test 2.5 kV AC , 50 Hz for 1 minute between all
all electrical circuits
Protection Class:
Front Plate IP50 as per IEC60529
Back Plate IP20 as per IEC60529
Operation:
Auxiliary Supply Voltage 80 Vac - 300 Vac
Auxiliary Supply Frequency 50 Hz
Auxiliary VA burden < 8 VA Approx. (With 8 Relay on )
Target cos phi 0.8 Lag...0.8 Lead programmable
19
Table of contents
Popular Controllers manuals by other brands
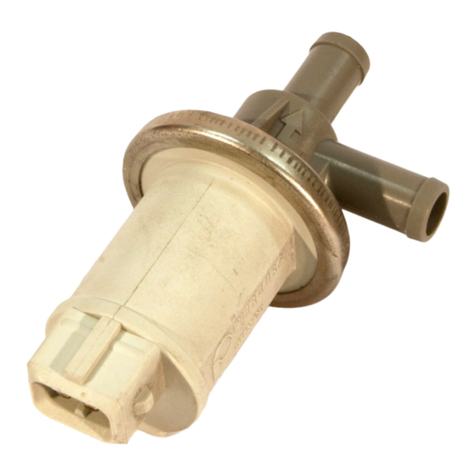
KMS
KMS Idle control kit Manual for installation and setup
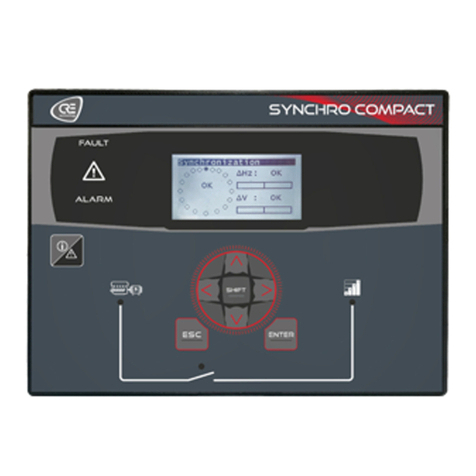
CRE
CRE synchro compact quick start
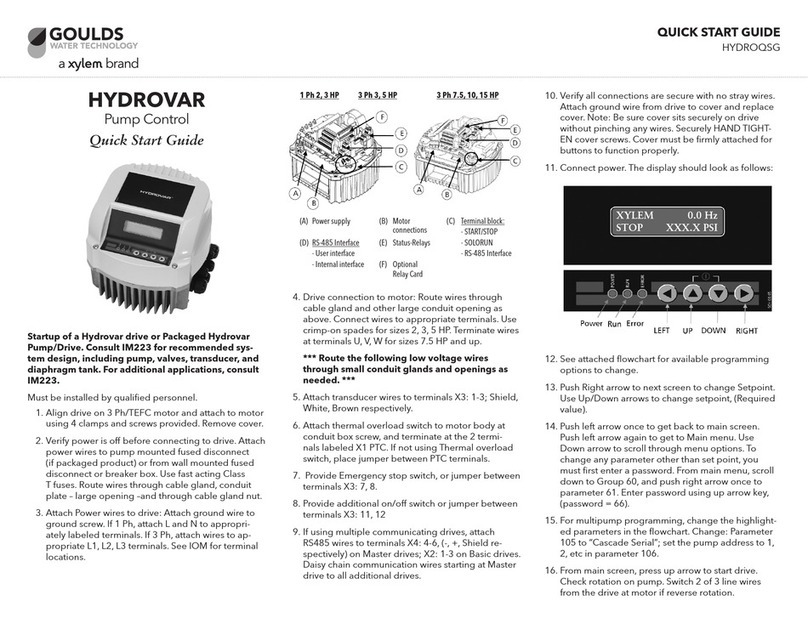
Goulds Pumps
Goulds Pumps HYDROVAR Quick start guides
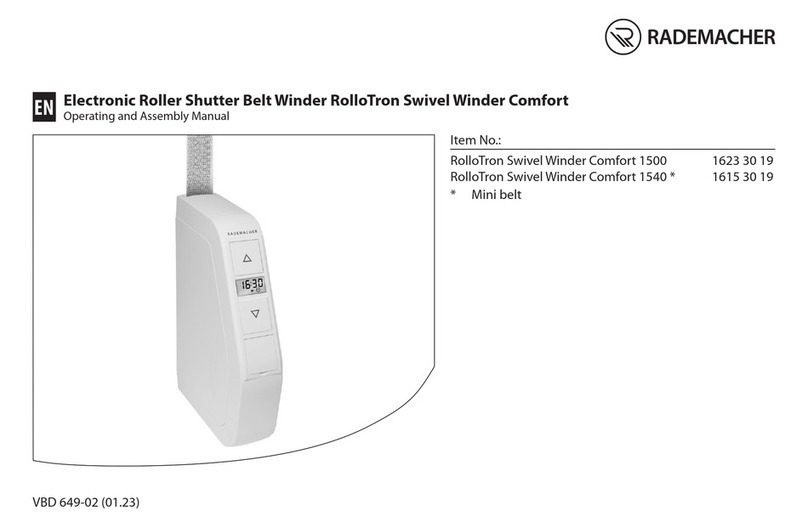
RADEMACHER
RADEMACHER RolloTron Swivel Winder Comfort 1500 Operating and assembly manual
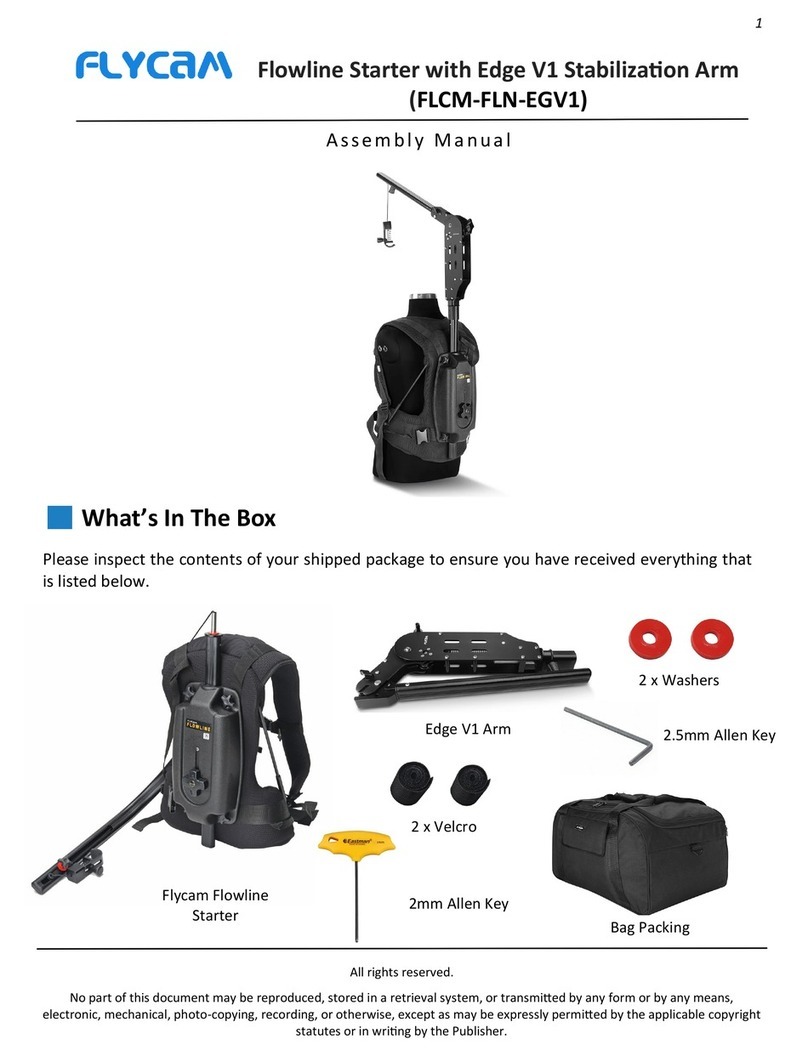
Flycam
Flycam FLCM-FLN-EGV1 Assembly manual
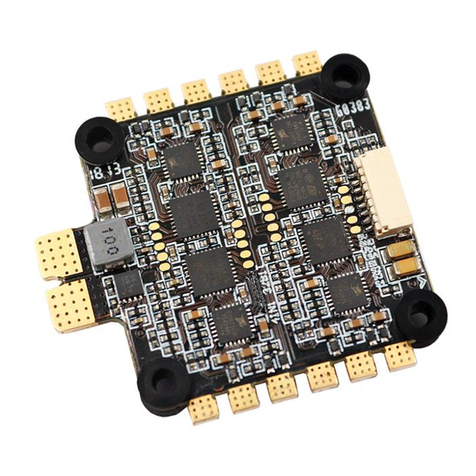
Flycolor
Flycolor X-Tower BL-32 4in1-40A user manual