Rivet King RK-8000S User manual

FOR SALES, SERVICE OR TECH SUPPORT CALL:
1800-BUY-RIVET or 1-800-289-7483
Instruction Manual
Model#
R
K
-8000S

2
CONTENTS
Features Page 3
Safety Page 3
Specifications Page 3
Air supply Page 4
Operation Page 4
Jaw Cleaning Procedure / Jam Remedy Page 5
Maintenance / Service Page 6
Oil Change/Replacement Procedure
Valve Spool Assembly
Trigger
Preventive Maintenance Page 7
Daily
Weekly
Monthly
Parts
Schematic Page 8
Part List Page 9
Material Safety Data Sheet
Oil MSDS Page 10
Troubleshooting Page 11
Warranty Page 12
SAFETY

3
DO NOT USE OUTSIDE DEISNG INTENT OR WITH EQUIPMENT THAT IS NOT RECOMMENDED BY THE MANUFACTURER.
ALWAYS DISCONNECT THE AIR SUPPLY BEFORE ATTEMPTING ANY MAINTENANCE OR ADJUSTMENT/FITTING OF NOSE EQUIPMENT
DO NOT OPERATE A TOOL THAT IS DIRECTED TOWARDS ANY PERSON(S)OR WITH THE MANDREL CATCHER OFF THE TOOL
ALL MODIFICATIONS CARRIED OUT ON THE TOOL WITHOUT EXPRESS WRITTEN CONSENT OF THE MANUFACTURER SHALL BE DONE
SO AT THE CUSTOMERS’SOLE RESPONSIBILITY
REFER TO THIS MANUAL BEFORE ATTEMPTING ANY MAINTENANCE OPERATION.DO NOT DISASSEMBLE THIS TOOL BEFORE
RFERING TO THIS MANUAL.
AVOID EXCESSIVE CONTACT WITH HYDRAULIC OIL,AS SOON AS POSSIBLE WASH HANDS THOROUGHLY
DO NOT EXCEED 7BAR /100 PSI INLET PRESSURE,THE USE OF A PRESSURE REGULATOR IS HIGHLY RECOMMENDED
INSPECT THE TOOL USING PREVENTITIVE MAINTENANCE TECHNIQUES AT REUGULARLY SCHEDULED INTERVALS.INSPECT FOR
DAMAGE AND FUNCTION BY TRAINED COMPETANT PERSONEL.REPLACE THE PNEUMATIC CYLINDER HOUSING OR HYDRAUILIC
CYLINDER HOUSING WHERNEVER THERE IS EVIDANEC OF IMPACT DAMAGE,CHIPPING,OR CRACKING.
WEAR SAFETY GLASSES AND ADOPT FIRM FOOTING DURING OPERATION.
SPECIFICATIONS
The specifications and information contained in this manual are applicable only to the tool with which it was
supplied. Industrial Rivet & Fastener Co reserve the right to make any changes without notice as part of
Industrial Rivet & Fastener Co policy of continuous improvement.
SPECIFICATIONS FOR RK-8000LS RIVET TOOL
Air Pressure 75-100psi Min/Max
Stroke 0.787 Inches Minimum
Pull Force 1,850 lbsF @90psi
Cycle Time 0.9 seconds Approximately
Noise Level 75 dB(A) Less than
Weight 2.42 lbs
Vibration 2.5m/s2 Less than
Hydraulic Oil Mobil DTFE 24
Nose Pieces 3/32 , 1/8, 5/32 All material rivets

4
AIR SUPPLY
The rivet tool is powered by compressed air at an optimum pressure of 5.5 bar (80 psi)
The use of a pressure regulator filter/lubricator unit within 3 meters of the tool is highly
recommended to extend the life of the tool.
Dirt and/or water in the air supply can seriously impact the performance and durability of
the tool; damage to the tool caused by contaminated air supply is not covered under
warranty
OPERATION
1
1
1.
.
.
Inspect for damage
2
2
2.
.
.
Connect the tool to the air supply
3
3
3.
.
.
Choose and securely install the applicable nose piece for the rivets you wish to apply. A ¼”
flat face nose piece is installed as standard.
4
4
4.
.
.
Adjust the vacuum until rivet is held in the nose piece while tool is pointed downward and
such that the mandrel after actuation flows to the back of the tool in any position..
a. Adjust vacuum by rotating the catcher valve located at rear of the tool inside the
mandrel catcher by hand.
VACCUM ON (COUNTERCLOCKWISE) VACUUM OFF (CLOCKWISE)
5
5
5.
.
.
Bring the tool and the rivet into the application hole. Insure the rivet head flat onto surface
6
6
6.
.
.
Fully actuate the trigger. The tool will cycle and set the rivet while ejecting the nail into the
rear mandrel catcher.
7
7
7.
.
.
Empty catcher when at 50% capacity
When the tool is in use for extended periods of time in a production environment, the
vacuum hose is suggested to prevent chips and burrs from gathering on or in the tool
or the application surface.

5
JAW CLEANING PROCEDURE /JAMMED GUN REMEDY
1. Disconnect tool from air supply
2. Leaving the nose piece attached, remove the nose case 3using the wrench provided by
loosening at the wrench point.
3. Fit two wrenches, one on Jaw Case 04 and the other on 08 keeping the nut 09 stationary
while unscrewing the jaw casing 04. It is important that you only unscrew the nut closest to
the jaws (jaw casing) 04. DO NUT ADJUST LOCKNUT 09.
4. Take care during removal as this jaw casing is spring loaded and contains 3 small jaws 05, a
jaw pusher 06, and a spring 07. Do not lose these pieces.
5. Once removed if a mandrel has jammed the tool, dislodge the mandrel from the jaws, discard
mandrel.
6. Clean Jaws 05 with a mineral spirit then and coat outside of jaws (outside only) with a light
layer of white lithium grease, red grease or one drop of hydraulic oil. Be sure to coat the
outside of the jaws only.
7. Replace jaws into jaw case 04.
8. Followed by jaw pusher 06, and spring 07, if necessary.
9. Re-apply jaw case 04 securely onto 08 using a wrench.
10. Reapply the nose case 03 securely to the tool
11. Reattach air supply. Actuate tool without rivet. Check Function.
12. Once comfortable, Apply Rivets.
13.

6
MAINTENANCE
Oil Priming Procedure
After 100,000 cycles, or when the tool loses enough stroke and/or power to place rivets in one
actuation, a priming procedure may be required. Please use the oil provided with the tool.
Replacements are available at 1-800-BUY-RIVET.
Disconnect air supply to tool and switch ON/OFF valve(48) to OFF position.
Remove bleed screw(70) and seal(69).(see Fig 3)
Fill the syringe(priming pump) with oil and screw it into the bleed screw hole. Actuate the
pump be pressing down and releasing several times until resistance is felt. Overfilling the
tool with oil and actuating it may result in hydraulic body fractures. (see Fig 4)
Remove the priming pump and the excessive oil will flow out. Then clean out the excessive oil
and replace the bleed screw and seal.
IMPORTANT: DISCONNECT THE TOOL FROM THE AIR SUPPLY OR SWITCH OFF AT VALVE (55).
REMOVE NOSE ASSEMBLY OR SWIVEL HEAD COMPONENTS. All operations should be carried out on
a clean bench, with clean hands in a clean area. Ensure that the new oil is perfectly clean and free
from air bubbles. Care MUST be taken at all times, to ensure that no foreign matter enters the tool,
or serious damage may result.
Valve Spool Assembly
Send into authorized repair center for service.
Trigger
Inspect trigger pin valve by insuring 33 has not come loose. The proper depth should be just
under the valve stem.
If adjustment is necessary using a fork wrench or tire valve tool, screw the trigger pin 33 into
the valve stem. A very small amount of loctite243 is ok around the threaded portion only.
If the trigger still fails, remove the trigger pin assembly from the valve stem and inspect the
seal around the trigger pin for damage. If damaged, purchase a replacement part. Re-
assemble according to the previous step.

7
PREVENTIVE MAINTENANCE
In order to maintain the tool in a safe working order it is important to carry out regular maintenance
as prescribed by the manufacturer. A thorough inspection replacement of all seals within the tool
should be carried out after 500,000 placings or annually, whichever is the sooner. Item numbers in
parentheses refer to assembly drawing part numbers
Daily
Check for air leaks. Any damaged hoses should be replaced
Lubricate the tool by pouring a 1 drop of light lubricating oil into the air inlet on the tool
If there is no pressure regulator, bleed the airline to clear it of accumulated dirt or water
before connecting the air hose to the tool. If there is a filter, drain it.
Check for proper nose piece use depending on the size of the rivet.
Remove front jaw nose assembly and inspect for cracks or other damage to front and rear of
the nose piece. Replace if necessary.
Insure that rotary valve for the vacuum on the mandrel collection unit is correctly adjusted
for fastener retention
Weekly
Carry out procedures as per daily maintenance instructions above
Clean and inspect the jaws for signs of damage or wear (groove running through the jaw
serrations). Follow the instructions on page 4 for cleaning of jaws. Reassemble the tail jaws
with a light coating of grease on the outer face that contacts the jaw housing. Do not allow
grease to contaminate the grooved inner face of the jaws as mandrel slippage may result.
Monthly
Carry out procedures as per daily maintenance instructions above
Check and replace cylinder bodies if there are signs of damage or cracks.

8
SCHEMATIC

9
SERVICE KITS & SPARES

10
OIL MATERIAL SAFETY DATA SHEET (MSDS)
Priming is ALWAYS necessary after the tool has been dismantled and prior to operating. It may also
be necessary to restore the full stroke after considerable use, when the stroke may be reduced and
fasteners are not fully placed by one operation of the trigger
Oil Details
The recommended oil for priming is Mobil DTE 24 or Hyspin VG32 available in 0.51 or one gallon
containers, or, you can use 30W hydraulic oil. Please see safety data below.
Mobil DTE 24 or Hyspin VG 32 Oil Safety Data
First Aid
SKIN:
Wash thoroughly with soap and water as soon as possible. Casual or short term contact requires no
immediate attention.
INGESTION:
Seek medical attention immediately. DO NOT induce vomiting.
EYES:
Irrigate immediately with water for several minutes. Although NOT a primary irritant, minor irritation
may occur following contact.
Fire
Flash point 232°C. Not classified as flammable.
Suitable extinguishing media: CO2, dry powder, foam or water fog. DO NOT use water jets.
Environment
WASTE DISPOSAL: Through authorized contractor to a licensed site. May be incinerated. Used
product may be sent for reclamation.
SPILLAGE: Prevent entry into drains, sewers, and water courses. Soak up with absorbent material.
Handling
Wear eye protection, impervious gloves (e.g. of PVC) and a plastic apron. Use in well ventilated
area.
Storage
No special precautions.
Priming Kit
To enable you to follow the priming procedure opposite, you will need to obtain a priming kit:
PRIMING KIT: RK-8000LS
PART NO DESCRIPTION
HO Mobil DTE 24
HO-B Refill Bottle

11
TROUBLESHOOTING
Item numbers in parentheses refer to assembly drawing part numbers on page 9.
Problem Possible Cause Remedy
More than one
operation of the trigger
needed to place
fastener
Air leak
Insufficient air pressure
Lack of lubrication
Worn or broken jaws
Low oil level or air in oil
Build up of dirt inside the nose assembly
Tighten joints or replace components
Adjust air pressure to within
specification
Lubricate tool at air inlet point
Fit new jaws
Prime tool
Service nose assembly
Tool will not grip stem
of fastener Worn or broken jaws
Build up of dirt inside the nose assembly
Loose jaw housing
Weak or broken spring in nose assembly
Incorrect component in nose assembly
Rotary valve incorrectly adjusted
Fit new jaws
Service nose assembly
Tighten against locking ring
Fit new spring
Identify and replace
Read ‘Operation’
Jaws will not release
broken stem of fastener Build up of dirt inside the nose assembly
Jaw housing, nose tip or nose casing not
properly seated
Weak or broken spring in nose assembly
Air or oil leak
Low oil level or air present in oil
Service nose assembly
Tighten nose assembly and adjust if
necessary
Fit new spring
Tighten joints or replace components
Prime tool
Jammed Gun / Cannot
feed next fastener Broken stems jammed inside tool
Rotary valve incorrectly adjusted
Empty mandrel collector
Check if jaw pusher is correct
Adjust air pressure to within
specification
Adjust as in ‘Operating Procedure’
Slow cycle Lack of lubrication
Low air pressure
Build up of dirt inside the nose assembly
Lubricate tool at air inlet point
Adjust air pressure to within
specification
Service nose assembly
Tool fails to operate No air pressure
Damaged trigger valve
Loose pneumatic piston cover
Loose stem collector
Connect and adjust to within
specification
Replace
Tighten Socket Screws
Tighten
Fastener fails to break Insufficient air pressure
Fastener outside tool capability
Low oil level or air present in oil
Adjust air pressure to within
specification
Use more powerful tool
Contact Industrial Rivet
Prime/Re-Fill oil
Insufficient Vacuum
Pressure Insufficient Air Pressure
Improper Vacuum Pressure Adjustment
Set to 90psi
See “Operation” for proper
adjustment

12
Warranty Statement:
Industrial Rivet & Fastener Co. Inc. (hereinafter “IRF”), hereby warrants to the initial retail customer
and original distributor (“Warrantee”) only that its products will be free from defects in material and
workmanship for a period of 1 year from the purchase date, provided that the products are used in
accordance with “IRF’s” instructions as to maintenance, operation and use.
The said warranty does not extend to goods subjected to misuse, neglect, accident or improper
installation or maintenance or which have been altered or repaired by anyone other than the seller
or its authorized agents.
The warrantee’s only remedy and IRF’s only obligation in the event of a defect or failure in the
products, is that IRF, at its sole option, repair, replace or rework the products, but in no case shall
the cost of the foregoing exceed the invoice price of the products.
This warranty shall be void if any person seeking to make a claim for defective or failed products
fails to notify IRF within 30 days of receipt of evidence that the product is defective or has failed, or
if said person fails to provide IRF with such evidence as is reasonably requested concerning the
effect or failure, including without limitation, evidence of the date of purchase and date of
installation.
This warranty is in lieu of all other warranties, expressed or implied, including
merchantability, or fitness provided for herein. Under no circumstance shall IRF be liable
for incidental or consequential damages arising from the defect or failure in its products.
Seller’s sole obligation under the foregoing warranty will be limited to, at Seller’s option, repair or
replacement of the tool (and shipping to the buyer with transportation charges paid to any place
within the contiguous 48 states). Returned goods will be evaluated by our warranty repair
department and a conclusion will be determined and classified as:
a) Warranty Repair (free of charge)
b) Abuse /Neglect (bench fee and/or hourly rate)
c) Maintenance (Flat Fee)
Price Schedule as of 1/1/2008
Bench Fee: $55.00
Hourly Rate: $55.00 per hour
Flat Fee:
Level 1 - Adjustments and light repair $35.00 + parts
Level 2 – Maintenance, Oil Change $95.00 + parts
Level 3 – Overhaul, complete disassembly, change all seals $155.00 + parts
If inspection by the seller of returned goods shows no breach of the forgoing warranty, Seller’s
regular conditioning charges (as stated above) apply. Upon this conclusion we will either repair the
tool at no cost to you and return it postage paid, or call you to inform you of the repair cost. The
repair will need to be approved in writing before any work is performed.
A comprehensive tool service and repair program, for details contact your local area sales
representative or call:
Industrial Rivet & Fastener Co.
200 Paris Ave
Northvale, NJ 07647
1-800-BUY-RIVET
This manual suits for next models
1
Table of contents
Other Rivet King Rivet Tools manuals

Rivet King
Rivet King RK-INLINE User manual
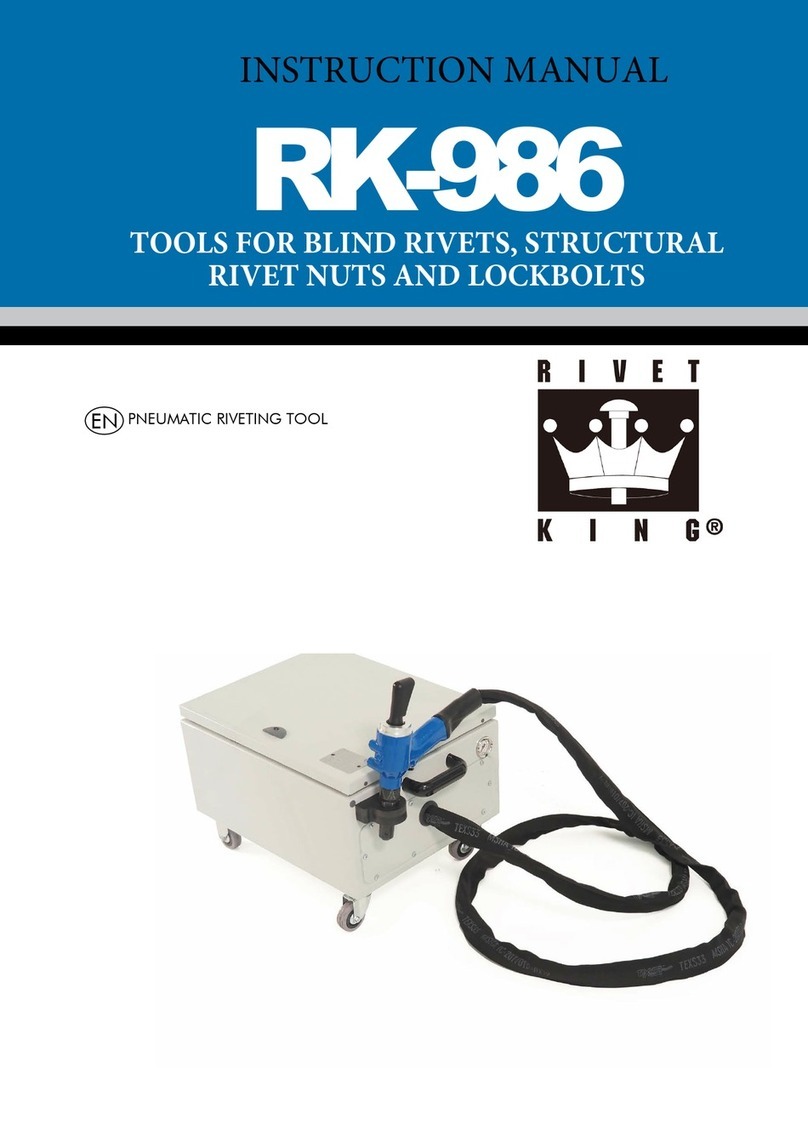
Rivet King
Rivet King RK-986 User manual
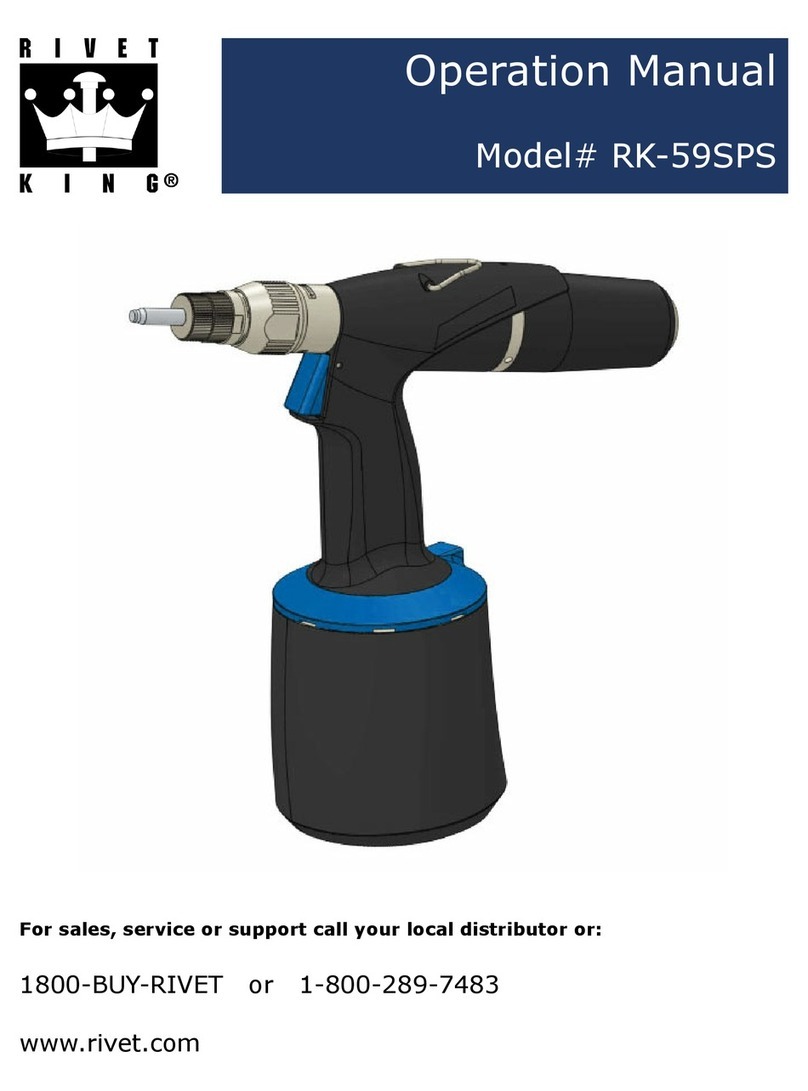
Rivet King
Rivet King RK-59SPS User manual
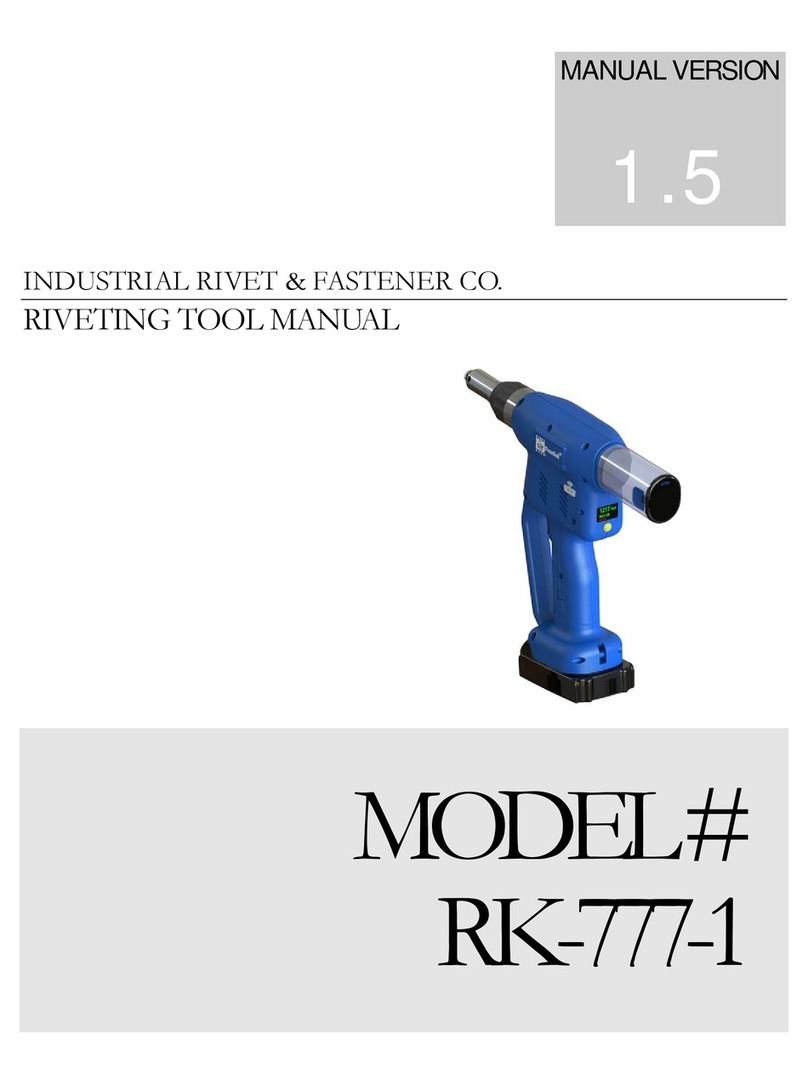
Rivet King
Rivet King FreeSet RK-777-1 User manual
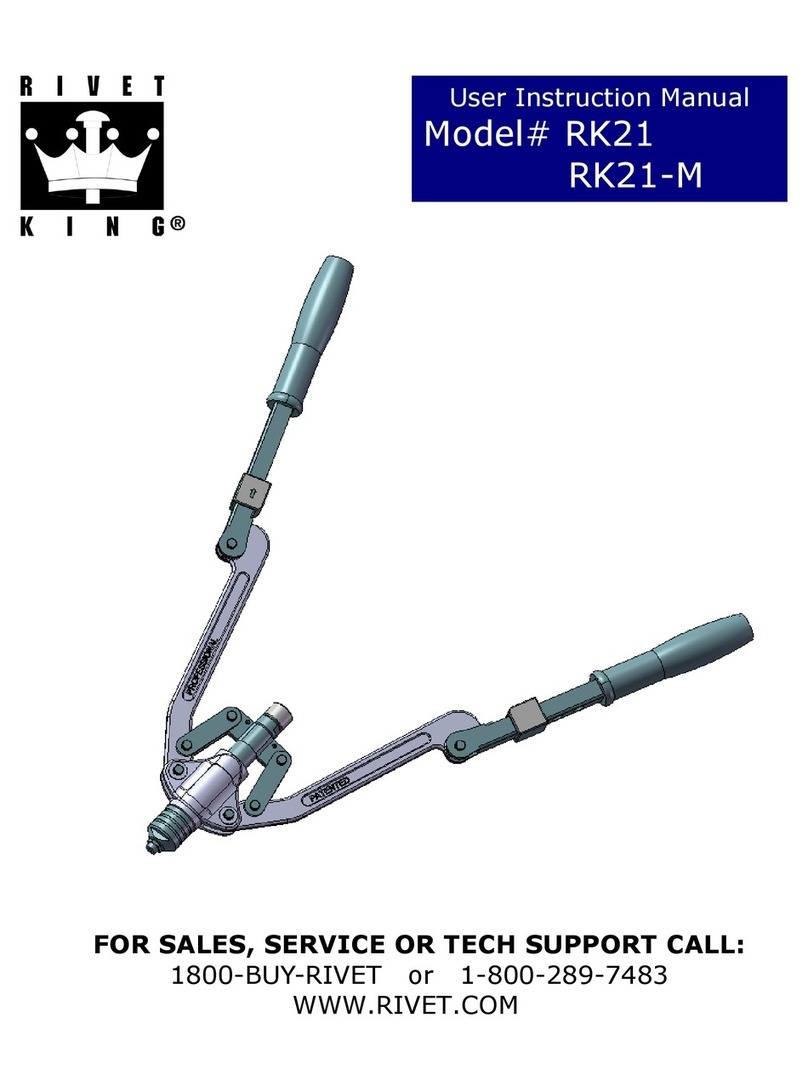
Rivet King
Rivet King RK21 Operator's manual
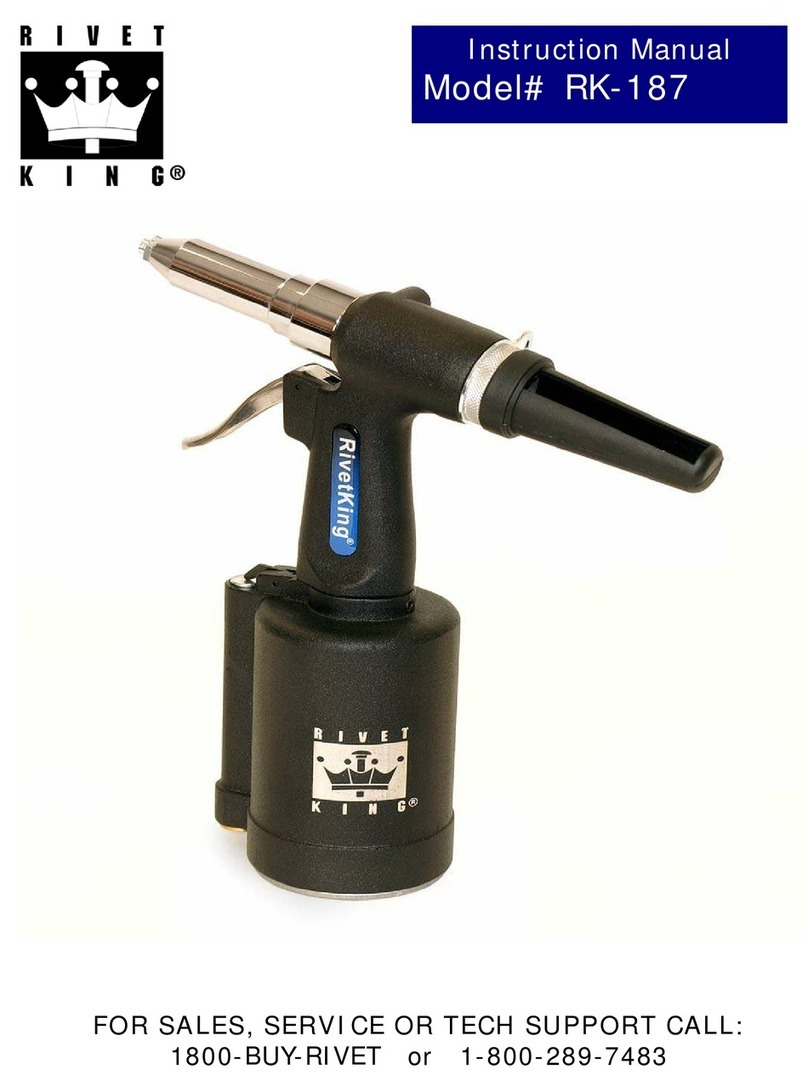
Rivet King
Rivet King RK-187 User manual
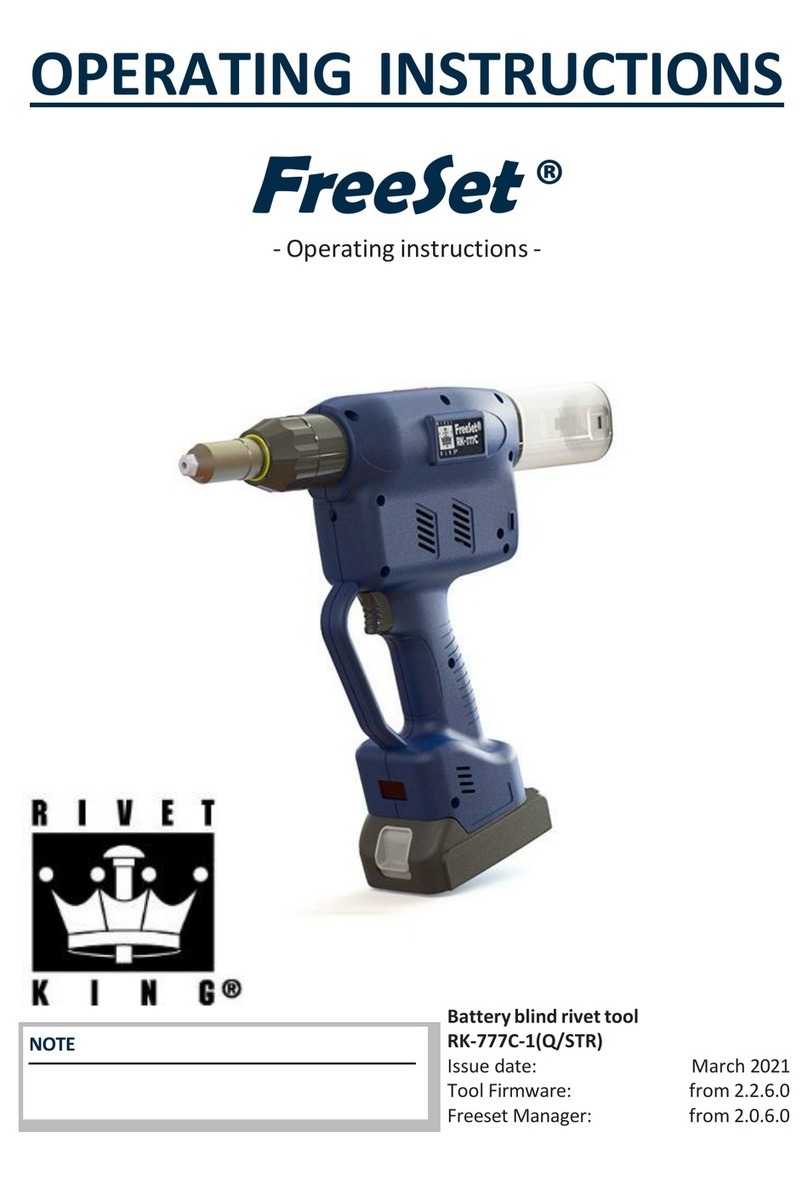
Rivet King
Rivet King FreeSet RK-777C-1Q User manual

Rivet King
Rivet King RK-250 User manual