Rockwell Automation Allen-Bradley OptixPanel User manual

Installation Instructions
Original Instructions
OptixPanel Standard Operator Panels
Bulletin 2800S
Safety instructions
Environment and Enclosure Information
U Compliance
Equipment with the UL/cUL mark complies with the requirements of UL 61010-1, UL 61010-2-201, CSA C22.2 No. 61010-1, CSA C22.2 No. 61010-2-201. Copies of the certificate of
compliance are available at rok.auto/certifications.
Installation guidelines
ow these guidelines to make sure that your operator panel provides service with excellent reliability
ATTENTION: Read this document and the documents listed in the Additional Resources section about installation, configuration, and operation of this
equipment before you install, configure, operate, or maintain this product. Users are required to familiarize themselves with installation and wiring
instructions in addition to requirements of all applicable codes, laws, and standards. Activities including installation, adjustments, putting into service,
use, assembly, disassembly, safety, and maintenance are required to be carried out by suitably trained personnel in accordance with applicable code of
practice. If this equipment is used in a manner not specified by the manufacturer, the protection provided by the equipment may be impaired.
ATTENTION: This equipment is intended for use in a Pollution Degree 2 Industrial Environment, in Overvoltage Category II applications (as defined in
IEC 60664-1), at altitudes up to 2000 m (6561 ft) without derating. This equipment is considered Group 1, Class A industrial equipment according to EN
61326-1. Without appropriate precautions, there can be potential difficulties with electromagnetic compatibility in other environments caused by
conducted as well as radiated disturbance. This equipment is supplied as open-type equipment for indoor use. It must be mounted within an enclosure
that is suitably designed for those specific environmental conditions that will be present and appropriately designed to prevent personal injury resulting
from accessibility to live parts. The interior of the enclosure must be accessible only by the use of a tool. Subsequent sections of this publication may
contain additional information regarding specific enclosure type ratings that are required to comply with certain product safety certifications. In
addition to this publication, see the following:
• Industrial Automation Wiring and Grounding Guidelines, publication 1770-4.1, for more installation requirements.
• UL 50, UL 50E, CSA C22.2, No. 94.1, and CSA C22.2, No. 94.2, as applicable, for explanations of the degrees of protection provided by enclosures.
WARNING: Special Conditions for Safe Use:
• The ambient temperature range is 0…50 °C (32…122 °F).
• Subject devices are to be installed in a tool-only accessible enclosure that provides a degree of protection not less than IP54 in accordance with IEC/EN
60079-0, Explosive atmospheres – Part 0: Equipment – General requirements and IEC/EN 60079-7, Explosive atmospheres – Part 7: Equipment
protection by increased safety “e”. Enclosure is to be marked with the following: “Warning - Do not open when energized”. After installation of subject
devices into the enclosure, access to termination compartments shall be dimensioned so that conductors can be readily connected. Grounding
conductor should have a minimum cross-sectional area of 1.5 mm² (16 AWG).
• Subject devices are for use in an area of not more than pollution degree 2 in accordance with IEC 60664-1.
• Subject devices are to use copper conductors with a minimum conductor temperature rating of 75 °C (167 °F).
• Subject devices are to be installed in the vertical orientation only.
AVERTISSEMENT:Conditions particulières d’utilisation sécuritaire :
• La plage de température ambiante est de 0…50 °C (32…122 °F).
• Les dispositifs en question doivent être installés dans un boîtier accessible uniquement aux outils qui offre un degré de protection au moins égal à IP54
conformément à la norme CEI/EN 60079-0, Atmosphères explosives – Partie 0 : Équipement – Exigences générales et à la norme CEI/EN 60079-7,
Atmosphères explosives – Partie 7 : Protection de l’équipement par une sécurité accrue « e ». L’annexe doit porter la mention suivante : « Avertissement
- Ne pas ouvrir lorsqu’il est sous tension ». Après l’installation des dispositifs en question dans l’enceinte, l’accès aux compartiments de terminaison
doit être dimensionné de sorte que les conducteurs puissent être facilement raccordés. Le conducteur de mise à la terre doit avoir une section
transversale minimale de 1,5 mm² (16 AWG).
• Les dispositifs en question doivent être utilisés dans une zone ne dépassant pas le degré de pollution 2 conformément à la norme CEI 60664-1.
• Les dispositifs visés doivent utiliser des conducteurs en cuivre dont la température nominale minimale est de 75 °C (167 °F).
• Les dispositifs en question ne doivent être installés qu’à la verticale.

2Rockwell Automation Publication 2800S-IN001B-EN-P - June 2023
OptixPanel Standard Operator Panels Installation Instructions
• When choosing the installation site, consider the following:
- The site must have sufficient power.
- The site must be indoors.
- The site must not expose the computer to direct sunlight.
• The operator panel can operate in the following environmental conditions:
- Operating temperature: 0...50 °C (32...122 °F).
- Storage temperature: -20...+60 °C (-4...140 °F).
- Operation/storage relative humidity (RH) non condensing: 20%...90%.
- Hazardous Location Temperature Class: T4.
Mounting requirements
Follow these requirements to mount the operator panel .
• Choose a suitable mounting height.
• To help prevent overheating and to provide access to the I/O ports for
cable connections, mount the operator panel with the following
minimum clearances from all four sides of the outer frame and back of
the computer chassis:
- X direction ≥ 50 mm (1.96 in.)
- Y direction ≥ 100 mm (3.93 in.)
- Z direction ≥ 50 mm (1.96 in.)
• For optimal performance, mount the operator panel in the horizontal
orientation and vertical (upright) position, so the I/O ports face down.
Prepare the Panel Cutout
Observe these guidelines to install the operator panel in a panel.
• Plan the panel cutout area that is needed for your operator panel.
• To ensure installation with proper IP protection grade the following conditions have to be satisfied:
• The mounting panel material must be 3…6 mm (0.11…0.24 in.) thick with a max deformation limit on the plane of 0.5 mm (0.01 in.).
• For a uniform gasket seal, the roughness of the panel surface must be ≤ 120 microns (Rz 120).
• Verify that the area around the panel is clear of obstructions.
WARNING: This operator panel is intended to operate in an industrial or control room environment, which uses some form of power isolation from the public
low-voltage mains. Some operator panel configurations cannot comply with the EN 61000-3-2 Harmonic Emissions standard as specified by the EMC Directive
of the European Union. Obtain permission from the local power authority before you connect any computer configuration that draws more than 75 W of AC
power directly from the public mains. All I/O cables are rated for indoor use only.
AVERTISSEMENT: Ce panneau de commande est conçu pour fonctionner dans un environnement industriel ou de salle de commande, qui utilise une certaine
forme d’isolation de l’alimentation électrique du réseau public basse tension. Certaines configurations informatiques ne peuvent pas être conformes à la
norme EN 61000-3-2 sur les émissions harmoniques telle que spécifiée par la directive EMC de l’Union européenne. Obtenir l’autorisation de l’autorité
d’alimentation locale avant de connecter une configuration informatique qui tire plus de 75 W d’alimentation CA directement du secteur public. Tous les câbles
d’E/S sont conçus pour une utilisation à l’intérieur seulement.
IMPORTANT The vertical position can be tilted up to 20° forward or 20° backward from the upright position. However, this acceptable tilt angle range decreases
the maximum operating air temperature to 45 °C (113 °F).
WARNING: Failure to follow these guidelines can result in personal injury or damage to the panel components. Take precautions so any metal fragments
during the panel cutout do not enter components that are installed already in the panel.
AVERTISSEMENT: Lorsqu'un panneau est découpé, des morceaux de métal peuvent être produits. Vous devez prendre les mesures de sécurité
nécessaires pour prévenir la pénétration des morceaux dans les composants déjà installés dans le panneau.
Table 1 - Cutout Dimensions
Display
Size, in. Format(1)
Panel Cutout Dimensions(2) [mm (in.)] Display
Size, in. Format(1)
Panel Cutout Dimensions(2) [mm (in.)]
A B A B
7.0 W 197.0 (7.75) 141.5 (5.57) 15.0 S 380.0 (14.96) 295.0 (11.61)
10.1 W 255.5 (10.05) 174.0 (6.85) 15.6 W 388.0 (15.27) 237.5 (9.35)
10.4 S 285.0 (11.22) 220 (8.66) 18.5 W 453.0 (17.83) 274.0 (10.78)
12.1 S 315.0 (12.40) 250 (9.84) 21.5 W 520.0 (20.47) 311.5 (12.26)
12.1 W 301.0 (11.85) 203.0 (7.99)
Installation min. clearance
X
X
Y
Y
Z
-20°-20°
0°
Installation max. tilt
Panel Cutout Areas
A
B

Rockwell Automation Publication 2800S-IN001B-EN-P - June 2023 3
OptixPanel Standard Operator Panels Installation Instructions
Required Tools for Installation
Install the operator panel
To install the operator panel in the panel cutout, perform the following steps.
1. Remove all electrical power from the panel before you make the cutout.
2. Cut an opening in the panel area to the dimensions needed for your operator panel.
3. After the cutout is completed, clean the panel area of all debris and metal fragments.
4. Make sure that the sealing gasket is positioned properly on the operator panel.
5. From the front of the panel insert the operator panel into the cutout (A) and rotate it (B) until it adheres completely to the panel (C).
6. Slide the mounting clips into the holes on all four sides of the operator panel and repeat the procedure in step 7 through step 9 for all the clips.
7. Insert the clip into the mounting hole side (D).
8. Rotate it down (E) and pull it outward (F).
9. According to the tighten sequence in Figure 1, tighten the mounting clips (G) with the supplied hexagonal key and verify the torque of 0.2 N•m (1.8 lb•in) with a
limiting screwdriver (requires a 1.5 mm hex key bit).
(1) Standard (S) format is offered with an analog resistive touch screen. Widescreen (W) format is offered with analog resistive and projective
capacitive (PCAP) touch screens.
(2) Tolerance ±1 mm (0.04 in.).
Tools required:
• Panel cutout tools.
• Hexagonal key 1.5 mm (supplied) and torque limiting screwdriver with a 1.5 mm hex key bit.
• Mounting clips (supplied), for the needed quantity, see Figure 1.
• Safety glasses.
IMPORTANT You need two people to install the operator panel; one person holds the operator panel in place while the second person installs the mounting clips.
IMPORTANT The gasket is a part of the display and forms a compression-type seal. Therefore, do not use sealing compounds.
Supplied tools
Sequence No. Dscription
1 Clip
2 Hexagonal key
12
Sealing
gasket
Clip hole
Sealing gasket / Clip holes
ABC
DEFG

4Rockwell Automation Publication 2800S-IN001B-EN-P - June 2023
OptixPanel Standard Operator Panels Installation Instructions
Figure 1 - Mounting clips tighten and torque sequence by display size
Connectors/LEDs/Buttons
Connect peripheral cables to the appropriate I/O ports on the operator panel. To comply with EN 61326-1, use the following for cable types. All I/O cables must be used only
indoors, and USB cables must be less than 3 m (9.84 ft) long.
ATTENTION: Tighten the mounting clips to the specified torque to provide a proper seal and to help prevent product damage. Rockwell
Automation assumes no responsibility for water or chemical damage to the operator panel or other equipment within the enclosure because of
improper installation.
Table 2 - Connectors / LEDs / Buttons.
Item
No. Description Required
cable LED
Color Function
1Front Power
On LED — Green Indicates the system is powered on.
2 DC power Unshielded — Power connector.
3 LAN Shielded — RJ45 connector.
4 USB 3.0 Shielded — USB 3.0 connector.
5 Micro SD — — Micro SD slot push push type.
6 Restart button — —
Forces an internal reset, as if power was lost temporarily and then returned.
IMPORTANT: Use this button only if there are no better options, like keyboard or mouse commands, or if the resumed DC power does not restart
the computer. System reset can cause data loss and possible corruption to the operating system.
7Factory reset
button — — Allows the total restoration of the firmware and factory settings with the deletion of all application data.
8Restart /
Power LED —Red Power supply ON and Boot sequence FAIL.
Restart button pressed.
Green Power supply ON and correct BOOT sequence.
10.1 - 10.4 - 12.1 in. (14 clips) 15.0 in. (18 clips)
2
1
I/O Ports
13
3
5
7
6
8
9
10
7.0 in. (8 clips)
2
1
I/O Ports
4
3
5
76
8
11
12
4
14
15.6 - 18.5 in. (20 clips) 21.5 in. (22 clips)
2
1
I/O Ports
13
3
5
7
6
89
10
11
12
4
14
16
15
17
18
19 20
21
22
2
1
3
9
10
11
12
417
18
19
20
13
5
7
6
8
14
16
15
2
1
13
35
7
6
89
10
11
12
4
14
16
15
17
18
I/O Ports
I/O Ports
1
2
3
6
712
4
4
9
10
511
8
3
WARNING: USB connectors not for use in hazardous locations. To use only for initial setup and maintenance.
AVERTISSEMENT: le connecteurs USB ne doit pas être utilisé dans des endroits dangereux. doit être utilisé pour la
configuration initiale et la maintenance seulement.

Rockwell Automation Publication 2800S-IN001B-EN-P - June 2023 5
OptixPanel Standard Operator Panels Installation Instructions
DC Power Supply Guidelines
All operator panels have the following features:
• The internal power supply of the operator panel has a galvanically isolated DC-DC converter board for
increased electrical noise immunity.
• Reverse polarity circuitry, overvoltage, and a 3 A soldered fuse provide input power protection.
Follow these guidelines to select the DC power to supply the operator panel.
• The operator panel must be powered with a voltage of 24V DC (18…32V DC SELV input voltage range).
• Power consumption is rated at 40 W max @ 50 °C (122 °F) ambient temperature.
Connect DC Power
To minimize ground loop currents and noise, we recommend that DC powered models use only one grounded connection.
Install the Factory-supplied DC Power Connector Assembly
Terminal block cabling procedure
1. Remove the DC terminal block (5) from the operator panel.
2. Use wires not included, (1) (2) (3) with 1.5mm2 (16 AWG) cross section.
9 LED COM1 TX — Green Transmission signal for COM interface.
10 LED COM1 RX — Green Receive signal for COM interface.
11 Factory Reset
LED —Blue Factory reset procedure in progress.
OFF Standard/common status.
12 COM Shielded — RS232/422/485 isolated serial port connector.
ATTENTION: The system has to be powered with a 24VDC (18...32V) power supply which satisfies the requirements of safe extra low voltage (SELV) in
accordance with IEC/EN/DIN EN/UL61010-1 and UL61010-2-201. The power supply has to fulfill the requirements NEC Class2 or LPS in accordance with
IEC/EN/DIN EN/UL61010-1 and UL61010-2-201.
Tools required:
• Adjustable torque screwdriver with M2 and M3 flat-blade screw bits.
• Wire stripper, cutter, and crimper tool.
• Cutting pliers.
Table 3 - Terminal Block Connection Specifications
Item No. Description Value
1DC+ (24V DC nominal)
1.5mm2 (16 AWG) wire
2 DC- (0V DC nominal)
3 Ground wire
4 Stripped wire length 7 mm (0.275 in.)
5 Terminal block —
6 Polarity symbol —
7 Torque range to secure DC power wires 0.22...0.25 N•m
(0.16...0.18 ft•lb)
8Torque value to reinstall DC terminal block to
computer 0.3 N•m (0.22 lb•in)
9 Cable tie (qty: 1) —
10 Labels (qty: 2) —
11 Half cover with cable tie slot —
12 Half closing cover —
Table 2 - Connectors / LEDs / Buttons.
Item
No. Description Required
cable LED
Color Function
lpk
(<5A)
lpk: load peak
T: time
T<4ms
Inrush current
DC power connector assembly
+–
24V - - -
Terminal block cover kit
1
8
4
7
2
3
11
56
9
12
10

6Rockwell Automation Publication 2800S-IN001B-EN-P - June 2023
OptixPanel Standard Operator Panels Installation Instructions
3. Strip 7 mm (0.275 in.) from the end of each power wire (4).
4. Insert each stripped end into the DC terminal block and fix it with the corresponding screws (7) with 0.22...0.25 N•m (0.16...0.18 ft•lb) torque.
5. Insert the cable tie (9) through the slots of the terminal block (11) connector clamp [step (A)].
6. Slide the connector half with the attached tie onto the end of the DC terminal block [step (B)].
7. Tighten the tie and remove the excess part [step (C)].
8. Install the white labels (10) supplied with the terminal block cover kit [steps (D) (E)].
9. Align and install the other connector (12) clamp half [step (F)] to complete the assembly [step (G)].
Connect DC Power
1. Connect the DC terminal block (complete with cables and cover) to the operator panel chassis and fix it with the corresponding screws (8) with 0.3 N•m (0.22 ft•lb)
torque.
2. Power on the system.
3. Front Power LED (1) and Restart/Power LED (8) will light green.
4. The operating system desktop appears after few seconds.
Install the Factory-supplied metal retention plates to connect Ethernet cables
The system is provided with metal retention plates, screws and zip ties provided in the box. Their purpose is to support Ethernet cables after plug in the ports.
1. Position the metal retention plate (1) in front of the LAN port and fix it with the
provided screw (2) with 0.22...0.25 N•m (0.16...0.18 ft•lb) torque [step (A)] .
2. Insert the LAN cable in the LAN port [step (B)].
3. Insert the zip tie around the LAN cable and the beveled edge of the plate (1)
[step (C)].
4. Tighten the tie (2) and remove the excess part [step (D)].
The colors of wires should follow regulations applicable where the system will be used.
The white label can be used for identification or other information.
When installed correctly, both tabs of the clamp half lock into place.
Tools required:
• Adjustable torque screwdriver with M3 Phillips screw bit.
• Cutting pliers.
Terminal block cover assembly
D E F GCBA
OptixPanel™ Standard
b
a
Item
No. Description
1 Metallic plates (qty: 2)
2 M3 screws (qty: 2)
3 Zip ties (qty: 2)
Metal retention kit
1
2
3
DCBA

Rockwell Automation Publication 2800S-IN001B-EN-P - June 2023 7
OptixPanel Standard Operator Panels Installation Instructions
ATEX Certification
Read this document very carefully because it contains safety information that takes priority over the system’s User Guide. This document contains the instructions, the
information, and the specific conditions, for the safe use of the systems and must be always taken as reference for installing, managing or updating the ATEX marked
systems. The systems must be installed, managed and updated only by qualified personnel. The non-compliance with the safety instructions present into this document can
result in death or serious injury. No responsibility is assumed by Rockwell Automation for any consequence arising from the improper use of the system in respect to the
contents of the present document.
The contents of this document are referred only to the following systems on which the ATEX marking label is present.
European Union Directive Compliance
This equipment meets the European Union Directive requirements when installed within the European Union or EEA regions and have the CE marking. A copy of the
declaration of the conformity is available at rok.auto/certifications.
Declaration of Conformity
Rockwell Automation, Inc. declares that the Optix Panel Standard Family, 2800S, are in compliance with Essential Health and Safety Requirements of Directive 2014/34/EU
(ATEX) as follows:
• Equipment Group II, Equipment Category 3.
• Type of Dust Protection “Ex tc IIIC T 70°C Dc “.
• Type of Gas Protection “Ex ec ic IIC T4 Gc“ (for Aluminum, Aluminium True Flat, Stainless steel IP69K Bezel).
• Type of Gas Protection “Ex ec IIC T4 Gc“ (for Aluminium and Glass TrueFlat Bezel).
Compliance to standard EN 60079-0:2018, EN 60079-7:2015 +A1:2018, EN 60079-11:2012 +A11:2013 and EN 60079-31:2014.
The full text of the EU declarations of conformity is available at the following website: rok.auto/certifications.
Additional Resources
These documents contain additional information concerning related products from Rockwell Automation. You can view or download publications at rok.auto/literature.
Marking Cat. number
reference Standards
II 3D Ex tc IIIC T 70°C Dc
II 3G Ex ec ic IIC T4 Gc X 0°C≤Tamb≤+50°C
WARNING - DO NOT OPEN WHEN AN EXPLOSIVE
ATMOSPHERE MAY BE PRESENT
WARNING - DO NOT OPEN WHEN ENERGIZED
2800S-xxx-D
2800S-xxx-E
2800S-xxx-X
EN60079-0:2018 Explosive atmospheres – Part 0: Equipment – General Requirements
EN60079-7:2015+A1:2018 Explosive atmospheres – Part 7: Equipment protection by increased safety “e”
EN60079-11:2012+A11:2013 Explosive atmospheres – Part 11: Equipment protection by intrinsic safety”i”
EN60079-31:2014 Explosive atmospheres – Part 31: Equipment dust ignition protection by enclosure “t”
II 3D Ex tc IIIC T70°C Dc
II 3G Ex ec IIC T4 Gc X 0°C≤Tamb≤+50°C
WARNING - DO NOT OPEN WHEN AN EXPLOSIVE
ATMOSPHERE MAY BE PRESENT
WARNING - DO NOT OPEN WHEN ENERGIZED
2800S-xxx-F
EN60079-0:2018 Explosive atmospheres – Part 0: Equipment – General Requirements
EN60079-7:2015+A1:2018 Explosive atmospheres – Part 7: Equipment protection by increased safety “e”
EN60079-31:2014 Explosive atmospheres – Part 31: Equipment dust ignition protection by enclosure “t”
WARNING: EXPLOSION HAZARD. Do not disconnect equipment while the circuit is live or unless the area is known to be free of ignitable concentrations.
AVERTISSEMENT: DANGER D’EXPLOSION. Ne pas débrancher l’équipement pendant que le circuit est sous tension ou à moins que la zone ne soit
exempte de concetrations inflammables.
Resource Description
OptixPanel Standard operator panel User Manual, publication 2800S-UM001 Provides details on how to install, configure, operate, and troubleshoot the OptixPanel operator panels.
OptixPanel Technical Data, publication 2800-TD001 Provides technical specifications about the OptixPanel operator panels.
Industrial Automation Wiring and Grounding Guidelines, publication 1770-4.1 Provides general guidelines to install a Rockwell Automation industrial system.
Product Certifications Website, rok.auto/certifications Provides declarations of conformity, certificates, and other certification details.

Publication 2800S-IN001B-EN-P - June 2023 | Supersedes Publication 2800S-IN001A-EN-P - June 2023
Copyright © 2023 Rockwell Automation, Inc. All rights reserved. Printed in the U.S.A.
Rockwell Otomasyon Ticaret A.Ş. Kar Plaza İş Merkezi E Blok Kat:6 34752 İçerenköy, İstanbul, Tel: +90 (216) 5698400 EEE Yönetmeliğine Uygundur
PN-696495
DIR 10007325294.01 (Version 01)
Allen-Bradley, expanding human possibility, OptixPanel, and Rockwell Automation are trademarks of Rockwell Automation, Inc.
Trademarks not belonging to Rockwell Automation are property of their respective companies.
*PN-696495*
PN-696495
Waste Electrical and Electronic Equipment (WEEE)
Rockwell Automation maintains current product environmental compliance information on its website at rok.auto/pec.
At the end of life, this equipment should be collected separately from any unsorted municipal waste.
Rockwell Automation Support
Use these resources to access support information.
Documentation Feedback
Your comments help us serve your documentation needs better. If you have any suggestions on how to improve our content, complete the form at rok.auto/docfeedback.
Technical Support Center Find help with how-to videos, FAQs, chat, user forums, Knowledgebase, and product notification updates. rok.auto/support
Local Technical Support Phone Numbers Locate the telephone number for your country. rok.auto/phonesupport
Technical Documentation Center Quickly access and download technical specifications, installation instructions, and user manuals. rok.auto/techdocs
Literature Library Find installation instructions, manuals, brochures, and technical data publications. rok.auto/literature
Product Compatibility and Download Center (PCDC) Download firmware, associated files (such as AOP, EDS, and DTM), and access product release notes. rok.auto/pcdc
Vendor Code: 86460132.01
Table of contents
Other Rockwell Automation Touch Panel manuals
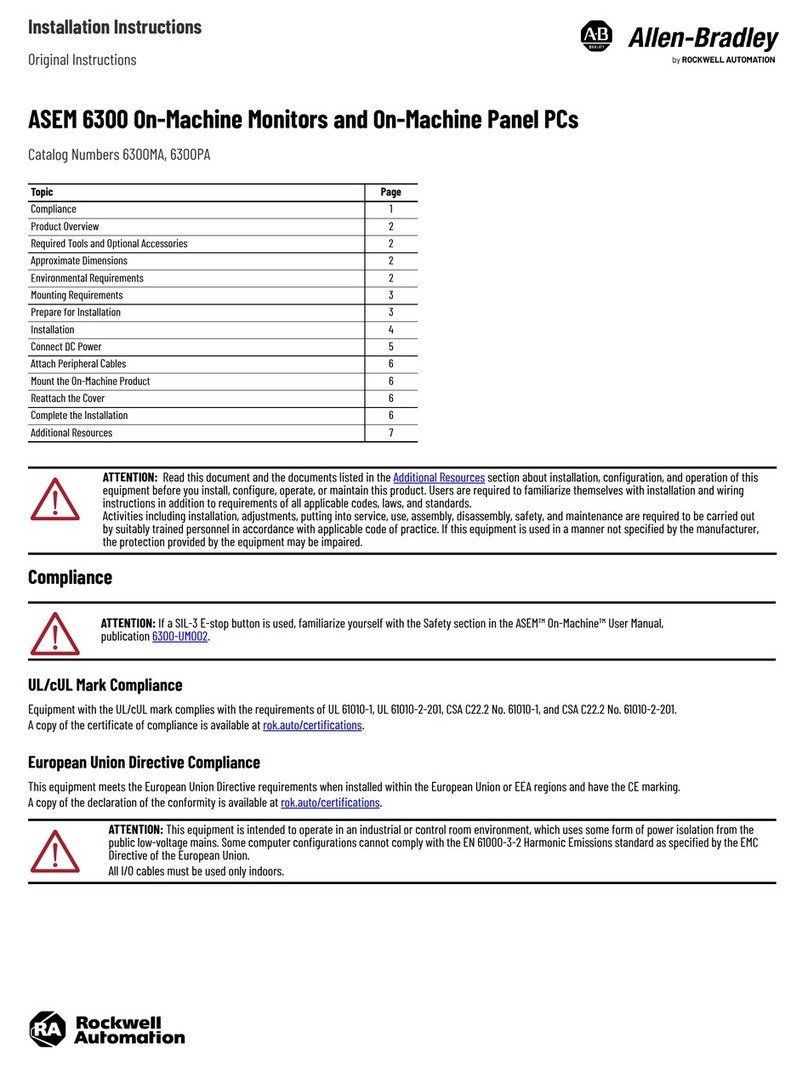
Rockwell Automation
Rockwell Automation Allen-Bradley ASEM 6300 User manual
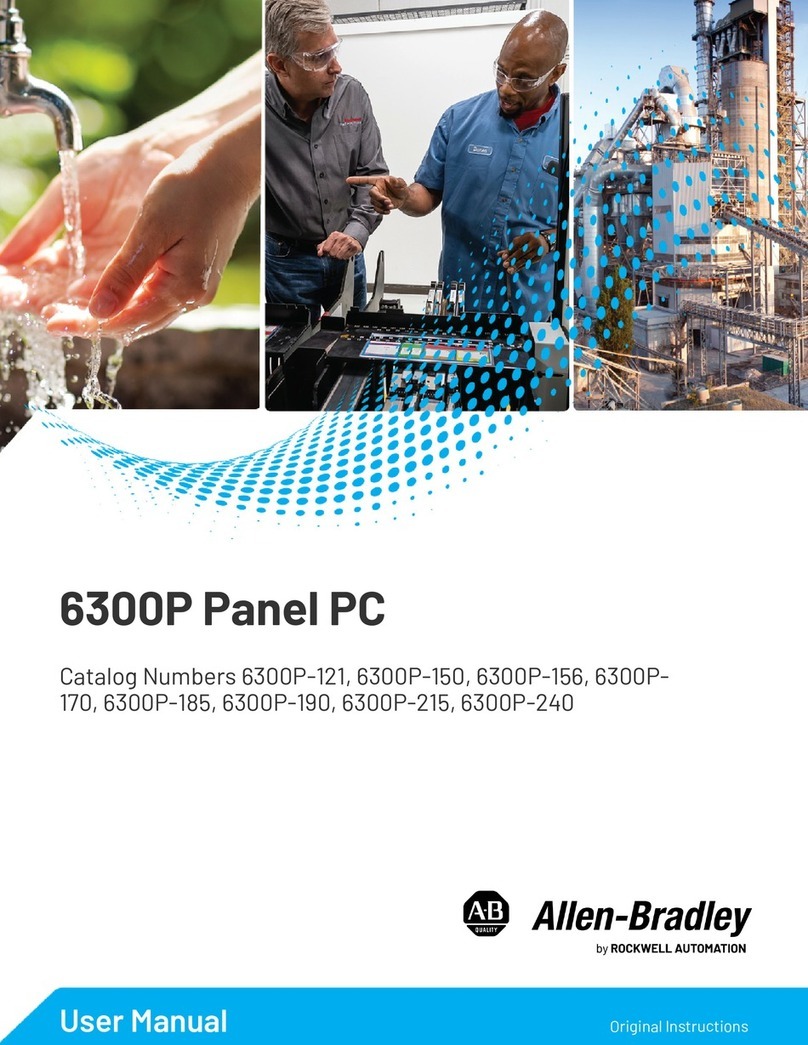
Rockwell Automation
Rockwell Automation Allen-Bradley VersaView 6300P Series User manual
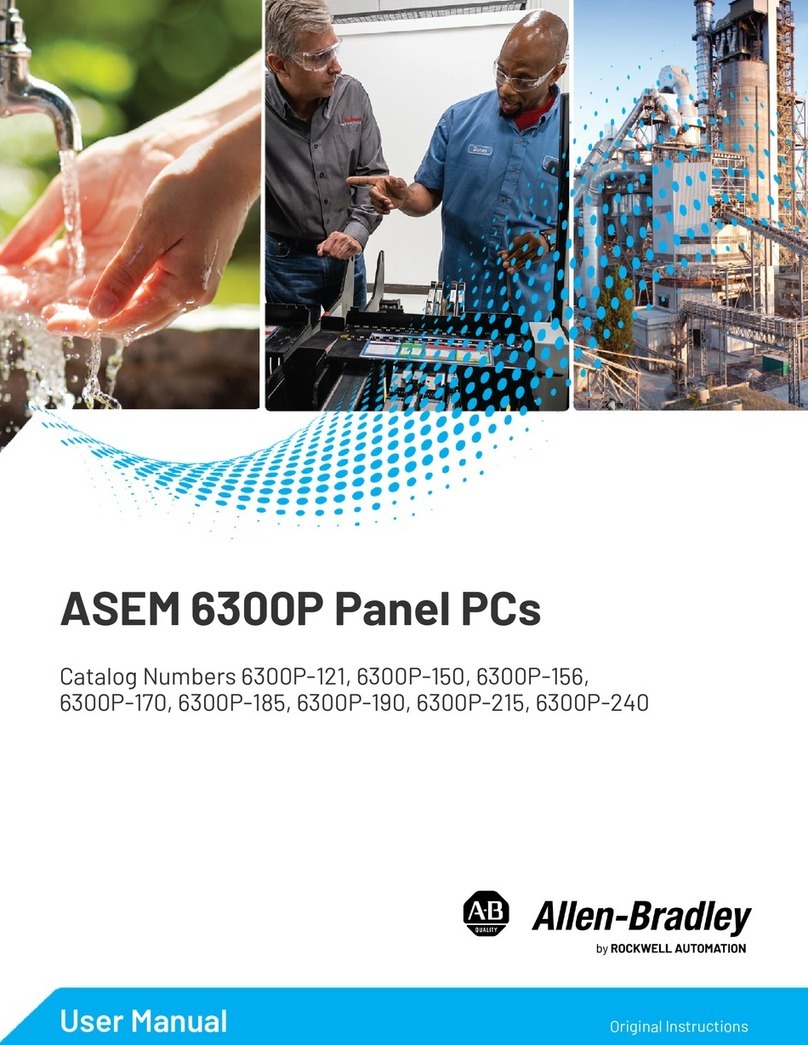
Rockwell Automation
Rockwell Automation Allen-Bradley VersaView 6300P Series User manual
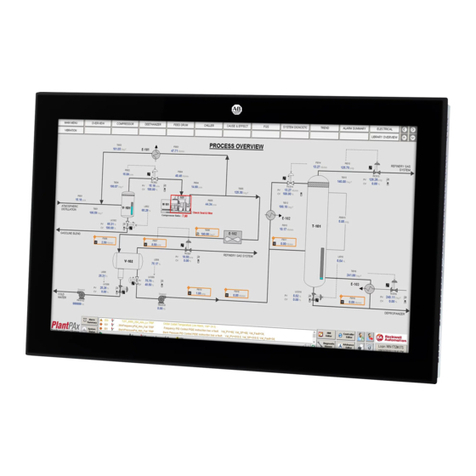
Rockwell Automation
Rockwell Automation Allen-Bradley VersaView 6300P Series User manual
Popular Touch Panel manuals by other brands
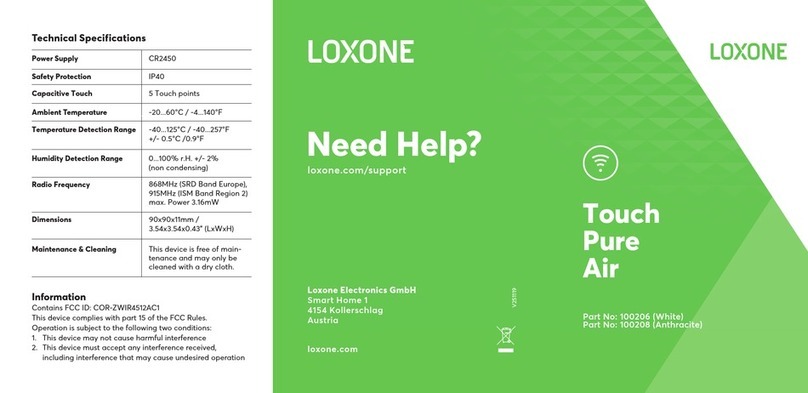
LOXONE
LOXONE Touch Pure Air Series quick start guide
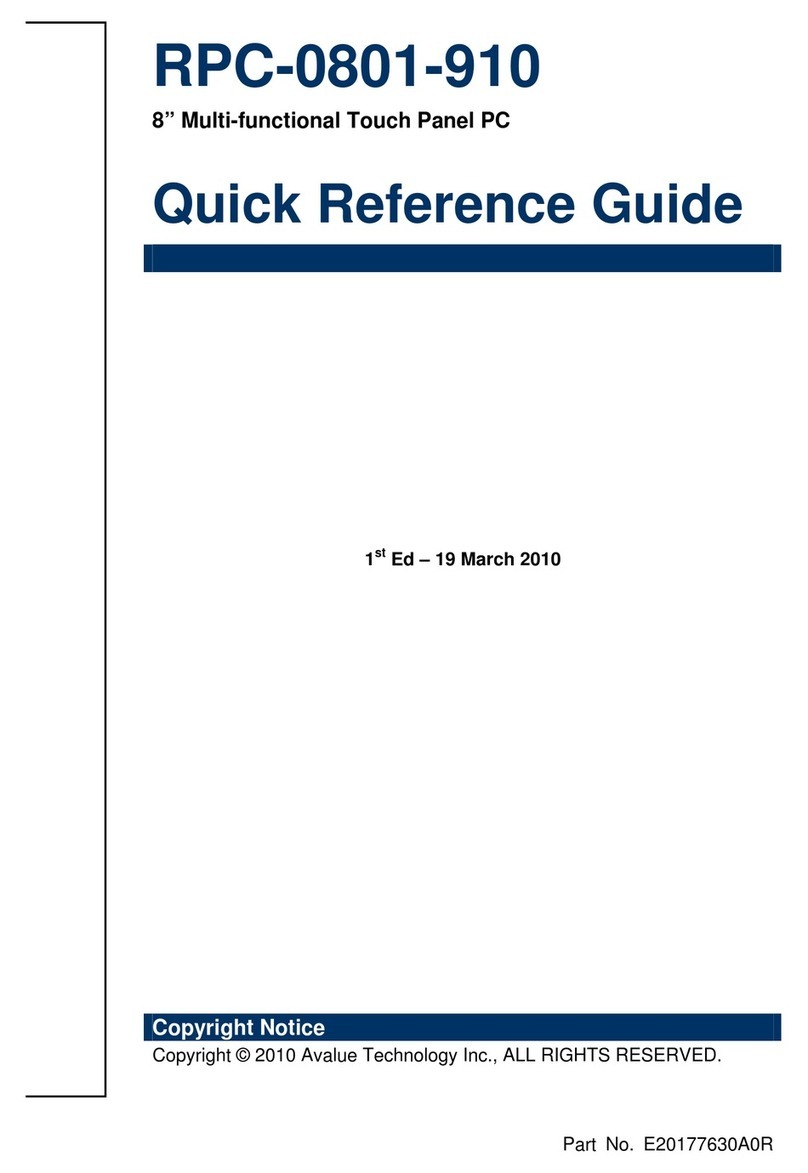
Avalue Technology
Avalue Technology RPC-0801-910 Quick reference guide
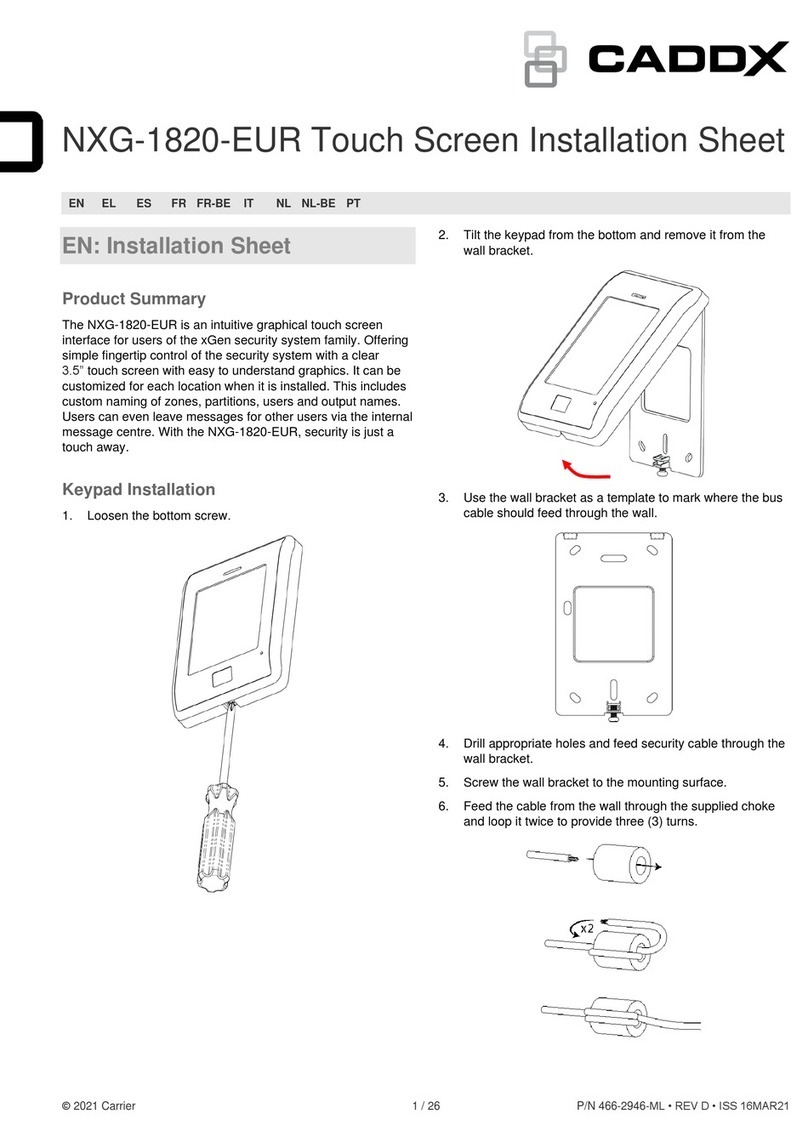
CADDX
CADDX NXG-1820-EUR Installation sheet
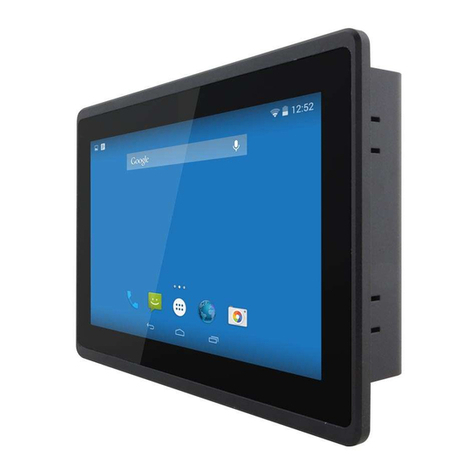
Winmate
Winmate W07FA3S-EHT1 quick start guide
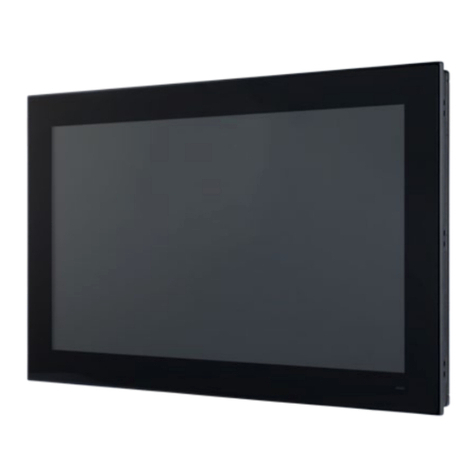
Advantech
Advantech PPC-310-RJ60A Startup manual
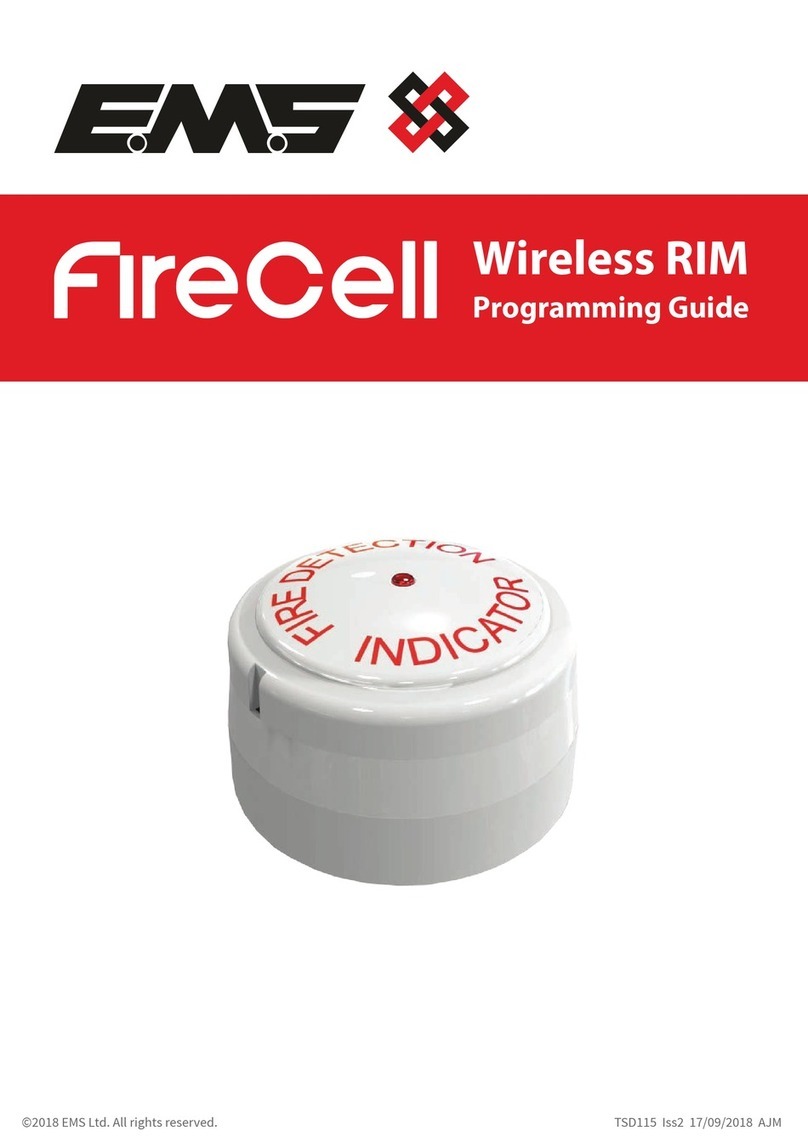
EMS
EMS FireCell FCZ-170-111 Programming guide