Roto Brute AC50 User manual

AC50 MAGNETIC DRILL PRE
U ER GUIDE
PART & CHEMATIC
AFETY / U AGE GUIDELINE
®

INCLUDED WITH EVERY AC50
1 Coolant Tank Kit, 1 Chip Guard Kit, 1 Hex key 4mm, 1 Hex key 2.5mm, 1 Wrench 8mm, 3
Handles, 1 Safety Chain & 1 Plastic Carrying Case
Ear and eye protection MU T be worn during operation of this equipment. Do NOT
touch the cutter while it is in motion. Always follow the Personal Protection
Equipment (PPE) recommendations while operating this tool.
This machine is designed specifically for drilling holes in steel using annular cutters
or with twist drills when using the optional drill chuck. We recommend Champion®
Rotobrute annular cutters. Please consult your Champion authorized distributor for
a complete range of sizes.
Do not modify or use your RotoBrute magnetic drill press for any application
other than drilling, reaming, or cutting holes.
Always use safety strap or chain when operating your AC50 magnetic drill.
AFETY
Be sure to read and follow these important safety instructions:
When using your AC50 drill press, be sure to follow these important safety precautions:
1. Before operating the machine, check supply voltage and general conditions, i.e. cable/cord
damage. A machine with a damaged cable must be repaired prior to use.
2. Always use safety strap or chain in all drilling applications.
4. Since cutting tools can shatter, eye and head protection should be worn at all times.
5. After use, clean machine and cutters and keep in the case provided.
6. Store when not in use, in a dry environment.
7. Always provide a method of catching slug, where the ejected slug may cause injury (slug
ejects at end of cut).
8. Should the cutter jam in the work-piece, stop the machine immediately. Isolate the
machine at the main supply. oosen the cutter by rotating the arbor. Do not attempt to free
cutter by starting and stopping the motor.
9. Always use the safety guard provided.
Electrical afety
1. Grounded tools must be plugged into an outlet properly installed and grounded in
accordance with all codes and ordinances. Never remove the grounding prong or modify the
plug in any way.
2. Do not use any adapter plugs. Check with a qualified electrician if you are in doubt as to
whether the outlet is properly grounded. If the tools should electrically malfunction or break-
down, grounding provides a low resistance path to carry electricity away from the user.
3. Never use the cord to carry the tools or pull the plug from an outlet. Replace damaged
cords immediately.
4. When operating a power tool outside, use an outdoor extension cord marked “W-A” or
“W”. These cords are rated for outdoor use and reduce the risk of electric shock. Minimal
gauge external cord should be 12/3.
5. Use the AC50 with 110 A/C voltage only. Not for use with generators, welders or any DC
power source. Do not use on any surface where welding is taking place.
AC50
IMPORTANT
Please read these operating and safety instructions carefully and completely. For your own safety, before using this equipment check that the voltage
is correct and that all handles and parts are firmly secured. If you are uncertain about any aspect of using this equipment, contact your distributor.
PLEA E KEEP THE E IN TRUCTION
Personal afety
Stay alert, watch what you are doing and use common sense when operating a power tool.
Do not use tool while tired or under the influence of drugs, alcohol, or medication.
Do not wear loose clothing or jewelry. Avoid accidental starting. Be sure switch is off
before plugging in. Carrying tools with your finger on the switch or plugging in tools that
have the switch on invites accidents.
Remove adjusting keys before turning the tool on.
Do not overreach. Keep proper footing and balance at all times.
Safety equipment (eye protection, dust mask, nonskid safety shoes, hard hat, hearing
protection) should be used for appropriate conditions.
Tool Use and Care
Use clamps or other practical ways to secure and support the work-piece to a stable
platform.
Do not force tool. Use the correct tool for the application.
Disconnect the plug from the power source before making any adjustments, changing
accessories, or storing the tool.
Store idle tools out of reach of children and other untrained persons.
Maintain tools with care. Keep cutting tools sharp and clean.
Check for misalignment or binding of moving parts, breakage of parts and any other condi-
tion that may affect the tool’s operation. If damaged, have the tool serviced before using.
ervice
Tool service must be performed only by qualified personnel.
When servicing a tool, use only original replacement parts.
Use of unauthorized parts will void the warranty.
Use of unauthorized parts or failure to follow maintenance instructions may create a risk of
electric shock or injury.
Magnetic Drill afety
The drill’s magnetic adhesion depends on the thickness of the work-piece. 1/2” (13mm) is
the minimum thickness for safe operation. Keep the magnet clean of metal chips and other
dirt and debris. These will seriously reduce the magnetic adhesion. The drill must be
operated on its own electrical outlet. Always use the supplied safety strap or chain. An
electrical overload can result in loss of adhesion.
CAUTION: The slug ejects at end of cut and is very hot.
WARNING: Do not attempt to drill a work-piece, which is thicker than the maximum cutting
depth of the cutter being used. Never exceed 2-1/8” cutter diameter.
Maintenance and Troubleshooting
Keep the drill press and the cord clean. In case of electrical or mechanical malfunction,
immediately switch off the tool and disconnect the plug. Excessive sparking generally
indicates the presence of dirt in the motor or worn out carbon brushes. Periodically check
brushes for wear and replace when they reach 1/4” (6mm). Also check that the machine is
well lubricated.
For all other service and maintenance, please contact a Champion authorized service
center.
COMPONENT & AFETY
2
Weight Strength
No oad
Motor Speed
RPM
Full oad
Motor Speed
RPM
Cutter
Capacity Depth
of Cut Height ength Width

AC50 OPERATING IN TRUCTION
Assembly of afety Guard
1. Mount safety guard to magnet using two wing nuts provided.
Coolant Tank Assembly
1. First attach clear tube to the bottom of the coolant tank. oosen the nut and slide nut
onto tube. Tighten the nut.
2. Slide tank hanger over the screw on the upper right hand side of slide and tighten.
3. Firmly insert the opposite end of tube into quick-release connector.
4. To remove, first firmly push the red collar of the connector and pull the tube out.
5. Cutting coolant fluid is always required when using annular cutters. Open tank cover
and fill. Check coolant fluid level often. Keep coolant tap closed when not in use.
3
Using Annular Cutters
No tools are needed to mount annular cutters to
the AC50.
Mounting annular cutters using the quick-
change arbor:
1. All AC50 machines come equipped with a
quick-change arbor. The quick-change
arbor allows users to install cutters and
twist drills in seconds.
2. First, insert the pilot pin into the cutter.
3. Push up on the quick change collar.
4 Insert the annular cutter with pilot pin
and turn until the flat meets the locking
pin
5. When the flat meets the locking pin, the
collar will snap down
6. Double check that the collar is down and the
cutter is fully locked before operating the mag drill
Caution: Never use a cutting tool that is larger than the maximum rated
capacity of the machine.
Adjusting the Gibs (Dovetail lides)
1. Periodically check, lubricate, and adjust as
needed.
2. The gibs require adjustment if too loose.
3. To adjust, loosen the lock nuts and adjust the
adjustor screws evenly while moving the
handle up and down.
4. Adjust so that there is no free play, without
any binding anywhere in its range of travel.
5. Then retighten the lock nuts.
Repositioning of Handles
1. Elevate the slide upward to full height.
2. Remove the pinion cap screw and pinion cap from the shaft end
(opposite side to handles).
3. Slide the pinion with the handles on outward, approximately 1/3rd distance.
4. Disengage the rack by means of raising the slide up by another 3/4”.
5. Remove pinion, reposition through opposite side of body casting and reverse
procedure as above.
Assembly of Traverse Handles
1. To assemble traverse handle, place each of the three (3) handles into
the threaded holes on the pinion shaft, turning clockwise to tighten.
2. To remove handles, turn counter-clockwise.
Gear election
1. Select the desired gear by swinging the
gear selector tab out of the detent slot
and into the correct speed
2. Then pop the selector tab back into the
detent.
3. It may be necessary to turn the spindle by
hand slightly to shift into gear.
GEAR NO OAD SPEED FU OAD SPEED
1 300 rpm 180 rpm
2 450 rpm 270 rpm
NOTE: These speeds are general recommendations only. Actual speeds should be
determined by the material and the cutting speed recommended by the
cutting tool manufacturer.
CAUTION: Ensure that that gears engage fully.
CAUTION: A WAYS ensure that the machine is fully stopped before attempting to
change gears!
CAUTION: Never change gears on a running machine!
Assembly of Drill Chuck for use with traight hank Tools
1. An important feature of the AC50 is that it
can quickly and easily be converted to
operate standard twist drills and other
straight shank cutting tools such as
chassis reamers.
2. Optional equipment RB1234 chuck adapter
and AC35-1220 are needed to use the
AC50 with twist drills.
3. Insert the RB1234 in the quick change arbor
and make sure that the flats align with the
locking mechanism of the arbor.
4. Screw the AC35-1220 on to the adaptor.
5. You are now ready to insert your cutting tool
into the chuck.
6. Tighten down with the appropriate chuck key
and you are ready to drill.
Adjusting the lide Height
1. Adjustable slide height models allow the
operator to quickly change the height
position of the motor head on the slide.
2. This is useful when switching between
twist drills and annular cutters.
3. For annular cutters, use the lowest position
possible for best stability. For twist drills,
raise the motor head to allow enough
clearance for the twist drill to be mounted.
To adjust:
1. Using the T-handle hex wrench, loosen the
socket cap screw on the Slide Height ock.
2. Slide the motor head to the desired position.
3. Tighten the Slide Height ock.
IMPORTANT
Please read these operating and safety instructions carefully and completely. For your own safety, before using this equipment check that the voltage
is correct and that all handles and parts are firmly secured. If you are uncertain about any aspect of using this equipment, contact your distributor.
PLEA E KEEP THE E IN TRUCTION

AC50 MOTOR PART & TAND CHEMATIC
4

PART LI TING
5
MINIBRUTE
AC50
No. ist/Size Description (Qty per Machine)
1 AC5001 INTERNA CIRC IP R-19 (1)
2 AC5002 ARBOR WASHER 10 x 18.5 x 0.8 (1)
3 AC5003 O-RING 12 x 20 x 4 (1)
4 AC5004 COO ANT SEA 12 x 10.2 x 15 (1)
5 AC5005 SPRING 1.2 x 10.1 x 12.5 x 12T x 90 (1)
6 AC5006 OCKING PIN 12.3mm (1)
7 AC5007 SET SCREW M3 x 4 (1)
8 AC5008 OCKING PIN SPRING (1)
9 AC5009 CHECK BA (1)
10 AC5010 PARA E KEY 5 x 5 x 10 (1)
11 AC5011 SPIND E (1)
12 AC5012 RING FOR OCK PIN (1)
13 AC5013 CO AR PIN (1)
14 AC5014 QUICK-RE EASE CO AR (1)
15 AC5015 SPRING 2 x 39 x 43 x 3T x 30 (1)
16 AC5016 SPRING SEAT RING 35.1 x 44.5 x 2 (1)
17 AC5017 EXTERNA CIRC IP S-35 (1)
18 AC5018 INTERNA CIRC IP R-47 (1)
19 AC5019 BEARING 6005ZZ (1)
20 AC5020 EXTERNA CIRC IP S-25 (1)
21 AC5021 SCREW M5 x 65 (2)
22 AC5022 SCREW M5 x 110 (2)
23 AC5023 COO ANT CONNECTOR (1)
24 AC5024 GEAR CASE (1)
25 AC5025 SE ECTOR TAB (1)
26 AC5026 SPRING 1 x 9 x 11 x 4T x 10.5 (1)
27 AC5027 SHOU DER SCREW (1)
28 AC5028 DETENT PIN (2)
29 AC5029 SPRING 5.3 x 6.5 x 5T x 17 (1)
30 AC5030 E-C IP E-3 (1)
31 AC5031 HEIGHT OCK (1)
34 AC5034 OCK BRACKET (1)
35 AC5035 SCREW M4 x 10 (4)
36 AC5036 BEARING 608ZZ (5)
37 AC5037 MAIN SHAFT PINION M1.0 x 11T & 15T (1)
38 AC5038 PARA E KEY 4 X 4 X 8 (1)
39 AC5039 INPUT GEAR M1.0 X 36T (1)
40 AC5040 EXTERNA CIRC IP S-10 (1)
41 AC5041 OI SEA 25 x 40 x 7 (2)
42 AC5042 OUTPUT GEAR M1.25 x 39T (1)
43 AC5043 EXTERNA CIRC IP S-15 (1)
44 AC5044 PARA E KEY M5 x 5 x 50 (1)
45 AC5045 INTERMEDIATE GEAR PINION M1.25 x 10T (1)
46 AC5046 INTERMEDIATE GEAR M1.0 x 46T & 42T (1)
48 AC5047 NEED E BEARING HK 0810 (1)
48 AC5048 SE ECTOR FORK (1)
49 AC5049 GEAR P ATE (1)
50 AC5050 BEARING 6001- U (1)
51 AC5051 ARMATURE 7T (1)
52 AC5052 SCREW M5 x 60 (2)
53 AC5053 STATOR (110V) (1)
54 AC5054 MOTOR HOUSING (1)
55 AC5055 NUT M4 X 8 (8)
56 AC5056 BRUSH HO DER (2)
57 AC5057 CARBON BRUSH 7 x 11 x 17 (PAIR) (2)
58 AC5058 BRUSH SPRING (2)
59 AC5059 SCREW M4 x 10 (2)
60 AC5060 SCREW M4 x 10 (4)
61 AC5061 MOTOR TAI COVER (1)
62 AC5062 SCREW M4 x 25 (2)
63 AC5063 CAB E C IP (2)
64 AC5064 SCREW M4 x 14 (2)
65 AC5065 WIRE CONNECTOR C4 (3)
66 AC5066 CAB E C AMP (2)
67 AC5067 MOTOR CAB E 1.0 x 2C x 65cm (1)
No. ist/Size Description (Qty per Machine)
68 AC5068 CAB E PROTECTOR 40CM (1)
69 AC5069 COO ANT TUBE 15CM (1)
74 AC5074 COO ANT TANK ASSEMB Y (1)
75 AC5075 CAP BO T M6 x 16 (3)
76 AC5076 S IDE (1)
77 AC5077 COO ANT TANK BRACKET (1)
78 AC5079 F AT WASHER 5 x 12 x 1 (2)
79 AC5079 SOCKET CAP SCREW M5 x 16 (2)
80 AC5080 GEAR RACK (1)
81 AC5081 STAND BODY (B UE) (1)
82 AC5082 GIB SET SCREW M5 x 20 (5)
83 AC5083 GIB OCK NUT M5 (5)
84 AC5084 THUMB SCREW M5 x 16 (1)
85 AC5085 BUSHING 28 x 32 x 12 (2)
86 AC5086 F AT WASHER 6 x 40 x 2.5 (1)
87 AC5087 F AT WASHER 6 x 25 x 1 (1)
89 AC5089 SWITCH GUARD BAR (2)
90 AC5090 SWITCH PANE (1)
91 AC5091 F AT WASHER 4 x 10 x 1 (7)
92 AC5092 SPRING WASHER M4 (4)
93 AC5093 SPRING WASHER M4 (4)
94 AC5094 MOTOR SWITCH (110V) (1)
95 AC5095 MAGNET SWITCH (1)
96 AC5096 GIB STRIP - EFT (1)
97 AC5097 GIB STRIP - RIGHT (1)
98 AC5098 GIB TENSIONER 260 x 11 x 2.3 (1)
99 AC5099 SCREW M4 x 16 (1)
100 AC50100 SUN WASHER M5 (1)
101 AC50101 SPRING WASHER M6 (3)
102 AC50102 MAGNET BASE 164 x 80 x 48 (1)
103 AC50103 SIDE PANE (1)
104 AC50104 SCREW M4 x 8 (4)
105 AC50105 RECTIFIER (1)
106 AC50106 PINION SHAFT (1)
107 AC50107 HAND E (3)
108 AC50108 SCREW M4 x 30 (2)
109 AC50109 STRAIN RE IEF 7CM (1)
110 AC50110 CORD ARMOR (1)
111 AC50111 POWER CORD 1.0 x 3C x 2.5M (1)
112 AC50112 CAB E G AND (1)
114 AC50114 EAD WIRE 18CM YE OW (2)
115 AC50115 EAD WIRE 18CM B ACK (4)
116 AC50116 WRENCH M8 (1)
117 AC50117 HEX KEY M2.5 (1)
118 AC50118 HEX KEY M4 (1)
120 AC50120 SAFETY CHAIN (1)
121 AC50121 OVER OAD UNIT(110V) (2)
122 AC50122 CAP BO T M6 x 20 (3)
123 AC50123 PAN HEAD SCREW M4 x 6 (2)
124 AC50124 MOTOR COVER P ATE (1)
125 AC50125 BT-HAND E HEX KEY M6 (1)
126 AC50126 SCREW M4 x 8 (4)
127 AC50127 RUBBER WASHER M4 (1)
128 AC50128 TERMINA (1)
129 AC50129 SCREW M4 x 25 (3)
130 AC50130 TIE (1)
131 AC50131 TERMINA ENDS (8)
132 AC50132 CHIP GUARD (1)
133 AC50133 F AT WASHER 6 x 13 x 1 (2)
134 AC50134 SCREW M6 x 10 (2)
136 AC35-1220 DRI CHUCK (OPTIONA )
137 RB1234 DRI CHUCK ADAPTOR (OPTIONA )
AC50-CASE-MT AC50 EMPTY MO DED CASE
140 AC50140 EARTH MARKING
141 AC50141 FAN SHROUD

P.O.Box 368, Rockville Centre, NY 11571-0368
Tel: 516-536-8200 Fax: 516-536-8186
www.championcuttingtool.com
AC50 ELECTRICAL DIAGRAM
ELECTRICAL DIAGRAM
AC50
OTHER ROTOBRUTE MACHINE AVAILABLE FROM CHAMPION
RB32-V R RB45 MIGHTIBRUTE RB65E MEGABRUTE AC35
RB32 RB30
Table of contents
Other Roto Brute Power Tools manuals
Popular Power Tools manuals by other brands

Black & Decker
Black & Decker KX1650 instructions

Makita
Makita 4100NH2 instruction manual
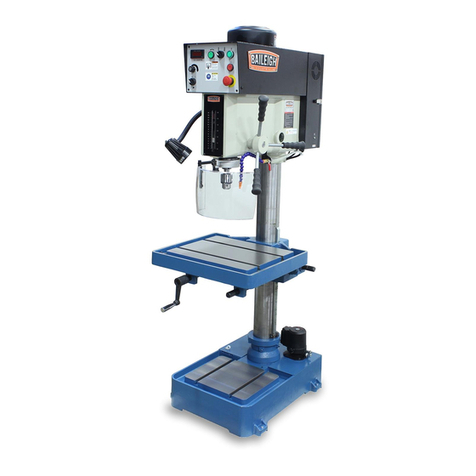
Baileigh Industrial
Baileigh Industrial DP-1375VS-110 Operator's manual
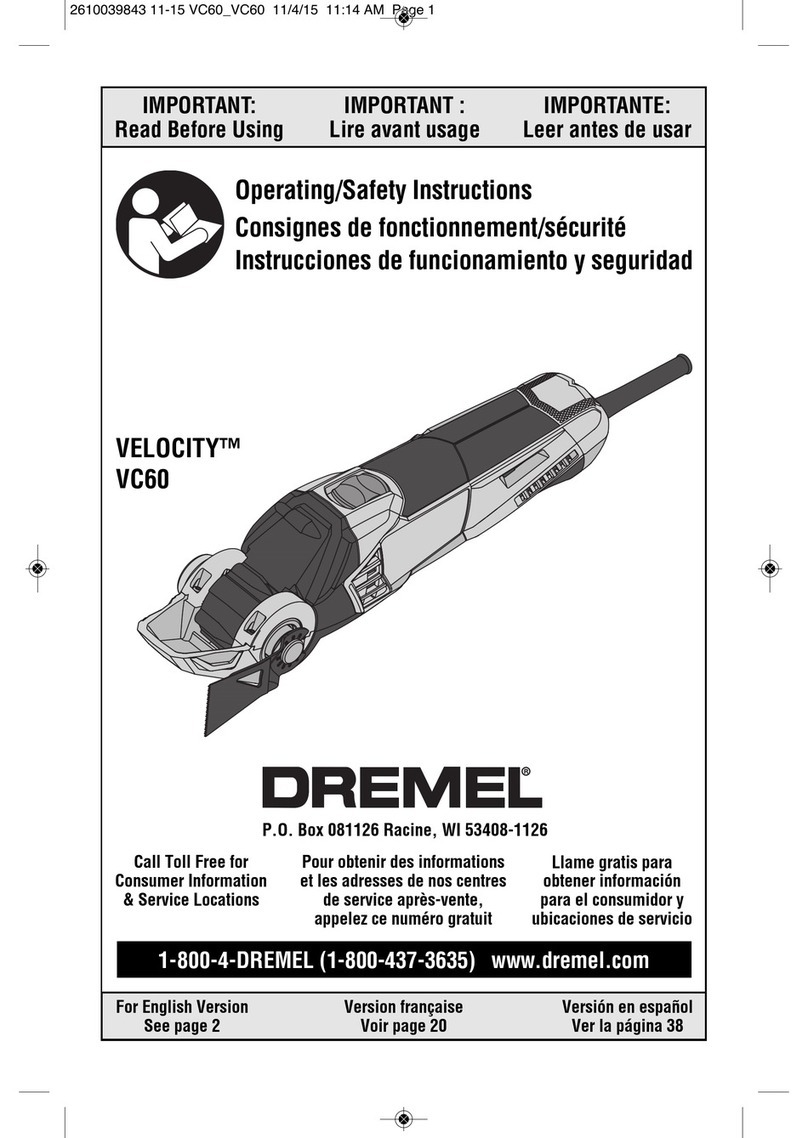
Dremel
Dremel VELOCITY VC60 Operating/safety instructions
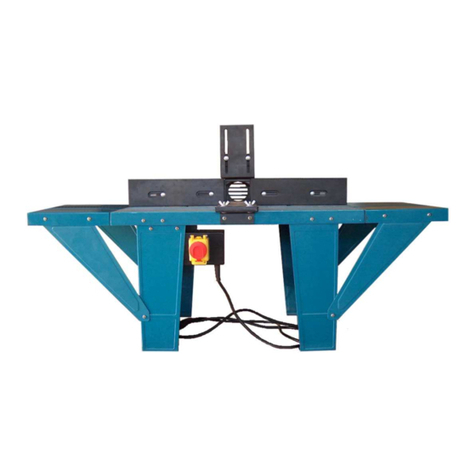
Westfalia
Westfalia 64 56 97 instruction manual
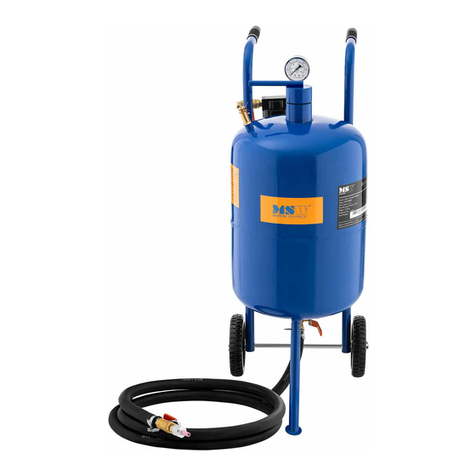
MSW Motor Technics
MSW Motor Technics MSW-MS40A user manual