RS PRO 227-5224 Instruction Manual

VER 1.00/18/10/5/RS Pro
Copy right reserved.
The manufacture reserves the right to change specification of the products without notice.
Installation & maintenance manual
RS Pro series soft starter
Low voltage product
RS Pro Part numbers
227-5224 227-5235 227-5227 227-5233
227-5226 227-5221 227-5229 227-5236
227-5219 227-5223 227-5230 227-5220
227-5231 227-5225 227-5232 227-5222

CATALOG
1
If not avoided,could result in damaged to the equipment.
1-2
3
4
5-6
7
9-11
12-13
14
15-17
18
19-20
21
22-24
Content page
Safety & Warning
General
Model description
Soft starter control and application
Installation
Wiring
Typical Application
Operation panel description
Parameter
Trouble shooting
Appendix
Mechanical installation
Typical wiring
Caution
Remind user caution information.
Warning
Avoid electrostatic
Warning. It is forbidden to touch the PCB with the mark. Electrostatic
charges could damage the components of soft starter.
High voltage warning
If not avoided, could result in damaged to the equipment
and possible injury or death.
Safety & Warning
2
warning- Indicates a risk of electric shock.
High voltage are presents at the input and output terminals
of RS Pro series soft starter, even not work when connect
power supply. Only qualified electricians are allowed to
install this products.
Do not carry out any work on the soft starter while the power is applied.
The installation electricians have the responsibility to ensure correct
earthing connection. Do not connect the power factor correction
capacitor to the output side of the RS Pro soft starter. If the static power
factor compensation measures are to be taken,The related devices
must be connected to the power supply side of the soft starter.

3
General
RS Pro series soft starters is a fully digital product.
Suitable for squirrel-cage asynchronous motors:
Rated voltage: 200V-500V Rated power: 0.75-75KW
The RS Pro series soft starters can control the motor to accelerate smoothly
during the starting process and decelerate smoothly in the process of stopping.
It also provides a comprehensive protection function for motors and itself.
Functions
Start/stop slope and initial voltage set by 3 different potentiometers built-in
Bypass relay built-in, No need for extra contactor
Voltage slope startup mode
The output torque can be maintained during the stop process(Continuous torque control),
e.g. prevent water hammer effect in pumping applications
External △ or Y Wiring mode
Real-time data of communication(A,B,C phase current, average current) * 1
Reading history fault records by communication ( 10 history log)* 1
The statistics data can be read by Modbus communication.*1
Protections:
Note *1:Option, only if select the RS-485 communication interface with the function.
Note *2:The function is available by using optional RS Pro switch on operating panel.
1) 8xIn overcurrent protection.
2) Over-load Protection with classes 10A, 10, 20 and 30.
3) Three phase current imbalance Protection.
4) No voltage protection.
5) Phase Missing Protection.
6) Phase Sequence Protection.
7) SCR Overheating Protection.
1 start/stop Digital Input
Communication Interface. *1
Option Build In start/stop switch *2
2 Output relay (running relay, trip relay)
·Rated Main Voltage:200-500VAC 50/60Hz
·Control Source Voltage:
100 240VAC
~
·Rated Main Current:
1.5A……150A
·Initial voltage:30%~70%;
·Start Slope:1~30 Sec;
·Stop Slope:0~30 Sec;
kgFIe
A
4
400V
Pe/kW
500V
Pe/kW
220V
Pe/kW
·Overload:3xIe 7 Sec,
Valid for 50 % on time and 50 % off time.
·Times of start per hour:
<5, 5-10 (light load or no-load)
·Overload grade:10A;
·Operation Environmental temperature:
0 ℃ to + 50 ℃ (32 ºF to 122 ºF)
·Store temperature:
-40 ℃ to + 70 ℃ (-40 ºF to 158 ºF)
·Maximum altitude:1000m(3280 ft)
·Ingress Protection grade:IP21;
Model description
Technical parameters
Rated Main Current
Parameters
Model
Motor power rating
Rated current
Structure Weight
227-5224
227-5226
227-5219
227-5231
227-5235
227-5221
227-5223
227-5225
227-5227
227-5229
227-5230
227-5232
227-5233
227-5236
227-5220
227-5222
0.37
0.55
0.75
1.1
1.5
2.2
3.7
5.5
7.5
11
15
18.5
22
25
30
37
0.75
1.1
1.5
2.2
3.7
5.5
7.5
11
15
18.5
22
30
37
45
55
75
1.5
2.2
3
4.5
7.5
11
15
22
30
37
45
60
75
90
110
150
A
A
A
A
A
A
B
B
C
C
C
C
C
D
D
D
1.1
1.5
2.2
3.7
5.5
7.5
11
15
18.5
22
30
37
45
55
75
90
1
1
1
1
1
1
1.4
1.4
2.4
2.4
2.4
2.4
2.4
5
5.2
5.2

U
V
W
M
5
1、 Only Use For Three Phase Motor
L1
L2
L3
QF FU
Soft starter control and application
Rated Main Voltage
The rated main voltage of RS Pro Soft Starter is 220V/400V/500V.
More detail please check the above-mentioned parameters.
Internal Control Diagram
6
1)For ordinary loads
The corresponding RS Pro soft starter models can be selected according to the rated current
of motors marked on the motor nameplate, such as pumps, compressors, etc.
2)For heavy load
RS Pro soft starter model of larger power size can be selected according to the rated current of
motor nameplate, such as centrifuge, crushing machine, mixer, blender, etc.;
◆ Frequent start
For frequent starting loads. According to the rated current of the motor marked by the
motor nameplate, we choose a higher power size RS Pro soft starter.
◆ Caution:
1)When the ambient temperature is higher than 40 degrees, the current rating increases by 1
degrees, and the current rating decreases by 0.8%.
2)When altitude is above 1000m, decrease as below:
When the altitude is 2000m:
The rated current capacity of soft starter should decrease to 93.3% of nominal current.
In=100-x-1000
150
In=100-2000-1000
150 =93.3%
Soft starter control and application
Options
RS Pro Soft starter provides two options for users:
·communication option(option 1)
RS-485
The RS-485 option of soft starter can support MODBUS-RTU communication protocol.
Model selection specification

1 2 3 4 5 6 7 8 9 10
Control Voltage
AC 100~240V
RS 485 A
RS 485 B
L N
Start/Stop
Run Fault
7
Power Dissipation≈3×Ie(W)
Ie-Motor Rated Current(A)
Installed in a metal cabinet without ventilation
2
Area(m)>0.12xPower Dissipation
·Do not install the soft starter near a heat source.
·Soft start must be reliably grounded, and avoid dust or corrosive environment.
·Working temperature under rating 0 ºC to + 50 ºC (32 ºF to 122 ºF)
·Relative humidity is less than 95%;
Installation
Mechanical installation(The method of installation)
Usually we suggest that the soft starter should be installed vertically,
which is good for heat dissipation.
When two or more than two soft starters are installed vertically stacked,
the distance between soft starters is not less than 100mm.
When two or more than two soft starters are installed horizontally
side by side, the distance between soft starters is not less than
50mm.
Installation environment
Installation environment
Caution
The rated loss power of the soft starter
approximately about
12345678910
Control Voltage
AC 100~240V
RS 485 A
RS 485 B
L N
Start/Stop
Run Fault
L1/R
CT1
S1
S2
K2
K1 G1
T1/U
G2
L2/S
CT2
S1
S2
K2
K1 G1
T2/V
G2
L3/T
CT3
S1
S2
K2
K1G1
T3/W
G2
40
50
60
1
6
18
24
30S
18
0
6
12
24
30S
12
30 70%Un
t
U
t
Power Run Fault 1 Fault 2
Soft st arterSoft st arterSoft st arter
L1/R
CT1
S1
S2
K2
K1 G1
T1/U
G2
L2/S
CT2
S1
S2
K2
K1 G1
T2/V
G2
L3/T
CT3
S1
S2
K2
K1G1
T3/W
G2
40
50
60
1
6
18
24
30S
18
0
6
12
24
30S
12
30 70%Un
t
U
t
Power Run Fault 1 Fault 2
Soft st arterSoft st arterSoft st arter
12345678910
Control Voltage
AC 100~240V
RS 485 A
RS 485 B
L N
Start/Stop
Run Fault
L1/R
CT1
S1
S2
K2
K1 G1
T1/U
G2
L2/S
CT2
S1
S2
K2
K1 G1
T2/V
G2
L3/T
CT3
S1
S2
K2
K1G1
T3/W
G2
40
50
60
1
6
18
24
30S
18
0
6
12
24
30S
12
30 70%Un
t
U
t
Power Run Fault 1 Fault 2
Soft st arterSoft st arterSoft st arter
12345678910
Control Voltage
AC 100~240V
RS 485 A
RS 485 B
L N
Start/Stop
Run Fault
L1/R
CT1
S1
S2
K2
K1 G1
T1/U
G2
L2/S
CT2
S1
S2
K2
K1 G1
T2/V
G2
L3/T
CT3
S1
S2
K2
K1G1
T3/W
G2
40
50
60
1
6
18
24
30S
18
0
6
12
24
30S
12
30 70%Un
t
U
t
Power Run Fault 1 Fault 2
Soft st arterSoft st arterSoft st arter
1 2 3 4 5 6 7 8 9 10
Control Voltage
AC 100~240V
RS 485 A
RS 485 B
L N
Start/Stop
Run Fault
L1/R
CT1
S1
S2
K2
K1 G1
T1/U
G2
L2/S
CT2
S1
S2
K2
K1 G1
T2/V
G2
L3/T
CT3
S1
S2
K2
K1G1
T3/W
G2
40
50
60
1
6
18
24
30S
18
0
6
12
24
30S
12
30 70%Un
t
U
t
Power Run Fault 1 Fault 2
Soft st arterSoft st arterSoft st arter
1 2 3 4 5 6 7 8 9 10
Control Voltage
AC 100~240V
RS 485 A
RS 485 B
L N
Start/Stop
Run Fault
L1/R
CT1
S1
S2
K2
K1 G1
T1/U
G2
L2/S
CT2
S1
S2
K2
K1 G1
T2/V
G2
L3/T
CT3
S1
S2
K2
K1G1
T3/W
G2
40
50
60
1
6
18
24
30S
18
0
6
12
24
30S
12
30 70%Un
t
U
t
Power Run Fault 1 Fault 2
Soft st arterSoft st arterSoft st arter
8
U
V
W
M
L1
L2
L3
QF FU
K
·QF Circuit breaker A circuit breaker with a tripping device is recommended.
·FU fuse Recommended installation,Selection of fuses based on SCR
More detail in the appendix 11 on page 13.
·K Built-in By pass relay.
·M Motor.
Main circuit wiring diagram
Wiring
Main Circuit
The soft starters support two kinds of wiring modes.
Wiring for three-phase motor
Caution

9
Wiring
·Suggested that a circuit breaker with a tripping device is installed between input
of the soft starter and the connection of the power source. The connection between
the soft starter and the power source must be switch off before maintenance.
·Suggested to use flame retardant copper core PVC insulated
wire to connect main circuit.
Caution
Caution
Main circuit terminal
10
Main circuit terminal:
2
Recommended use:6-50mm AWG:10-1/0
Recommended torque:4N.m
1 2 3 4 5 6 7 8 9 10
AC 100~240V
L N
10 input / output terminals:
① Control power L or + input.
② Control power N or - input.
③ Start / Stop signal input.When terminal 3 is connected to terminal 1 the starter runs,
When the terminal 3 and terminal 1 are disconnected, the stop softly until stop completely.
④ Running signal relay output.
When the soft start is in start, bypass and soft stop state, relay operation is closed.
⑤ Running relay output common.
⑥ Fault relay output.When the soft start is in a fault state, the relay is closed.
⑦ Fault relay output common.
⑧ RS-485 bus A-LINE.
⑨ RS-485 bus B-LINE.
⑩ Earthing terminal.
Wiring
Main circuit terminal
Control terminal
Control terminal diagram
A B
RS485 A
RS485 B
Fault
Run
Start/Sto p
Control Voltage

11
④,⑤terminal for running relay output,
When RS Pro soft starter is on running (start / bypass / soft stop),
K1 closes.⑥ ⑦ terminal is fault relay output,
When the RS Pro soft starter detects a fault, K2 closes.
K1、K2 contact capacity 220VAC 5A
AC
K
START/STOP
1
2
3
K1
K2
4
5
6
7
When using 100~240VAC as a control power,
①Connect AC power line, ②Connect AC power neutral;
Join the contact K between① and ③,
Soft starter runs when K closed,
soft starter stops when K disconnected;
If the control input cable too long or unseparated wiring with
power supply, cause input signal with "induced voltage"
Please add a relay at the input, so as to avoid the " induced
voltage " which leads to malfunction or damage of the
soft starter.
·The control power supply voltage must be matched the products, otherwise the input
of the control voltage will exceed the range, which will lead to soft starter damage.
·When the control power supply is DC power, the positive and negative pole must be
connected to the correct terminal.
·In order to use the RS Pro soft starter safely, The fault relay K2 should be connected
in the circuit of the control (release) of the circuit breaker between the power source
and the RS Pro main power terminal. When the soft starter detects the fault, the K2
action can disconnect the power breaker at the same time.
Wiring
Control power supply and control input
AC power line
AC power neutral
Caution
Caution
Relay output
Running relay N.O. output
Running relay output common
Fault relay N.O. output
Fault relay output common
12
·The motors with three terminals can only use the external wiring mode.
The rated current of the soft starter in the external mode is selected according
to the rated current of the motor.
L1/R L2/S L3/T
M
3~
L1/R L2/S L3/T
M
3~
T1/U T2/V T3/W
Typical wiring
Wiring Mode
When using the external mode of soft starter, the soft starter power module is connected
between the power source and the motor.
Caution
T1/U T2/V T3/W

L1/R
CT1
S1
S2
K2
K1 G1
T1/U
G2
L2/S
CT2
S1
S2
K2
K1 G1
T2/V
G2
L3/T
CT3
S1
S2
K2
K1 G1
T3/W
G2
40
50
60
1
6
18
24
30S
18
0
6
12
24
30S
12
30 70%Un
t
U
t
Power Run Fault 1 Fault 2
Soft starterSoft starterSoft starter
14
13
nd
·Using semiconductor protection fuse can achieve 2 standard , and reduce the risk
of power module damage caused by transient overload current.
nd
·2 standard:Under the condition of short circuit, the short circuit protection electric
does not cause harm to the personal and installation equipment, and it can continue
to be used.
1) State display LED:Show the working state of the soft starter.
Run(yellow)
2) Potentiometer setting
Initial voltage
Start Slope
Stop Slope
Set initial voltage
Set acceleration time
Set deceleration time
Adjustable potentiometer
Typical wiring
Caution
Operation interface description
soft starter panel diagram
power (green)
When the soft starter (motor) stop, running LED off.
When soft starter (motor) is in soft start / soft stop state, running LED blink.
When the soft starter (motor) is in bypass state, running LED on
When the soft starter is power on, the power supply LED on.
Fault 1 (red)
Fault 2 (red)
Parameter setting
The main starting / stopping parameters of the soft starter can be set by the panel
potentiometer. Other parameters have been set up at factory commissioning,
users do not need to set them. Other parameters can be adjusted by RS485 communication.
When the soft starter is in fault state, fault LED blink or on.
More details please check the page 18.
L1/R
CT1
S1
S2
K2
K1 G1
T1/U
G2
L2/S
CT2
S1
S2
K2
K1 G1
T2/V
G2
L3/T
CT3
S1
S2
K2
K1 G1
T3/W
G2
40
50
60
1
6
18
24
30S
18
0
6
12
24
30S
12
30 70%Un
t
U
t
Power Run Fault 1 Fault 2
Soft starterSoft starterSoft starter
kgFIe
A
400V
Pe/kW
500V
Pe/kW
220V
Pe/kW
2 2
SCRI T(A S)
soft starter rated current
Model
Motor power rating
Rated current
Structure Weight
Fuse table
Model Fuse Value
0.37
0.55
0.75
1.1
1.5
2.2
3.7
5.5
7.5
11
15
18.5
22
25
30
37
0.75
1.1
1.5
2.2
3.7
5.5
7.5
11
15
18.5
22
30
37
45
55
75
1.5
2.2
3
4.5
7.5
11
15
22
30
37
45
60
75
90
110
150
A
A
A
A
A
A
B
B
C
C
C
C
C
D
D
D
1.1
1.5
2.2
3.7
5.5
7.5
11
15
18.5
22
30
37
45
55
75
90
1
1
1
1
1
1
1.4
1.4
2.4
2.4
2.4
2.4
2.4
5
5.2
5.2
70
150
270
610
1700
3630
5000
7500
10000
11000
12000
15000
18000
40000
60000
100000
5A
10A
10A
16A
25A
32A
40A
50A
63A
100A
160A
200A
250A
315A
315A
400A
227-5224
227-5226
227-5219
227-5231
227-5235
227-5221
227-5223
227-5225
227-5227
227-5229
227-5230
227-5232
227-5233
227-5236
227-5220
227-5222
227-5224
227-5226
227-5219
227-5231
227-5235
227-5221
227-5223
227-5225
227-5227
227-5229
227-5230
227-5232
227-5233
227-5236
227-5220
227-5222

15
0-100
500-850%500%,Factory setting
0.1~1.0Sec. 0.1Sec.Factory setting
·The soft starter has two different levels of over current breaking protection.
1)When the current is greater than 850% of the soft starter rated current (FLA), the soft
starter will trip immediately. Fault relay (K2) tripped.
2)When the output current is greater than the over current protection set value (the
motor rated current FLA 500%-850%) the soft starter is delayed for a period of time
("over current action delay time" specified time) then the fault relay (K2) tripped.
100~200% 110%.,Factory setting
0-Grade 10A
1-Grade 1 0
2-Grade 2 0
3-Grade 3 0
0-Grade 10A
Factory setting
·Thermal protection of motor.
It is recommended that users set overload protection to (level 10A) ,
When the setting less than "overload protection value", the
soft starter detect overload protection.
main parameter
Parameter Setting range Default
FLA Full load current Primary current of current transformer ,
according to rated current of soft starter
factory setting
Protection parameters
Parameter Setting range Default
Parameter Setting range Default
Over current protection value
Over current trip delay time
Parameter description
Caution
Caution
Parameter Setting range Default
Parameter Setting range Default
Over load protection
Overload protection
grade
0-100
Parameter Setting range Default
FLC Full load current Primary current of current transformer ,
factory setting
16
0- OFF
1-ON
1-ON
More protections:
1)Overtemp protection. When the heatsink temperature is above 80 degrees, the soft start trip.
2)When the soft starter input terminal/output terminal missing phase, the soft start trip.
3)When the power module is short circuited, soft start tripped.
4)when the three-phase current of the soft starter is unbalanced
(three-phase current difference > 20%FLA), soft starter trip.
1-30 Sec.
0-30 Sec.
30-70%
Parameter description
Parameter Setting range Default
Phase sequence
protection
The parameter setting protection functions not introduced above:
Caution
Parameter Setting range Default
Start / stop parameters
Starting time Panel potentiometer setting
or check the page 20.
Caution
The starting time is set through the panel or the communication.
Parameter Setting range Default
Panel potentiometer setting
or check the page 20.
Stop time
Caution
Parameter Setting range Default
Caution
Panel potentiometer setting
or check the page 20.
Initial voltage
The stop time is set through the panel or the communication.
The initial voltage is set via the panel or communication.
. When the initial turnMoment = initial voltage 2×T (T : rated torque)
N N

17
·The motor can't start(Locked-Rotor) if the voltage is too low. It is suggested that set
initial voltage from high to low or use the Recommended setting.
0-Electric self holding relay
1-Magnet self holding relay
Depending on the specific model
Factory setting
·The type of bypass relay is not allowed to be changed !
1~127 1,Factory setting
0-1200BPS
1-2400BPS
2-4800BPS
3-9600BPS
4-19200BPS
3-9600BP S
Factory setting
Parity check 0-ECC
1-ODD
2-None
0-ECC
U
UN
Uini
0T1T
Un:Rated voltage
Uini:Initial voltage
T1:Acceleration time
At a predetermined acceleration time (T1),
the output voltage of the soft starter rises
from the voltage to the full voltage
(rated voltage Un).
Parameter description
Voltage slope starting mode
Caution
Caution
Parameter Setting range Default
Bypass relay type
Relay parameters
Parameter Setting range Default
Communication parameters
Slave machines address
Baud rate
Parameter Setting range Default
Parameter Setting range Default
Caution
·After setting up the communication parameters must restart the RS Pro soft
starters. Incorrect settings cause communicate fault, it could cause cannot
setting again. RS Pro can not restore the default parameter, so please be
careful when setting communication parameters.
Fault solution
Fault Fault reason Solution
Phase sequence trip The sequence of three phase
voltage is wrong
Change the sequence of three phase.
◎ Blink; On; 〇 OFF
1. The frequency protection is built-in, soft starter can work with 50/60HZ voltage.
2. The single-phase soft starter have no unbalanced current trip, but have no voltage trip.
Fault 1 Fault 2
18
√ √
√
√
√
√
√
√
Note:×:Not working;√:working
Time(S)
Current(x Ie)
A Class 30;B Class 20
C Class 10;D Class 10A
Trouble shooting
Fault list
Fault Fault reason Start/stop process Bypass
Electronic overload and tripping curve
√
Not working
Phase sequence trip
Missing phase trip
No voltage trip
Over current trip
Over load trip
Unbalanced current trip
Overtemp trip
The sequence of three phase voltage is wrong
Missing one phase or two phase voltage in three
phase voltage
NO voltage input
Current value exceeding over current setting value
Current value exceeds overloading set value
The unbalanced three-phase current is larger
than the unbalanced current setting value
The temperature of the heatsink is higher than
the temperature setting value
√
√
√
√
√
×
×
×
×
×
√
√
Missing phase trip/No
voltage trip
Over current trip
Missing one phase or two phase
voltage in three phase voltage
/NO voltage input
The connection between the soft start and
the main power supply is open.
Current value exceeding over
current setting value
Check whether the connection between
soft start and motor is short circuited.
Over load trip Current value exceeds
overloading set value
Check whether the load is too large or whether
the selection of soft starter power is too small.
Unbalanced current trip
The unbalanced three-phase
current is larger than the
unbalanced current setting value
Check the winding of the motor and the
connection between soft starter and motor
Overtemp trip The temperature of the heatsink
is higher than the temperature
setting value
Check whether the connection between
soft start and motor is short circuit. Check
whether the load is too large or whether
the selection of soft starter power is too small.

19
Among:
I% is the ratio of the actual current to the rated current
tolerance time of T * 500% overload current (X=5)
Minimum overload tolerance time
10A
10
20
30
X=8
1.6
3
5
7
X=7
2
4
6
9
X=6
3
6
9
13
X=4
6
13
19
29
X=3
12
23
35
52
X=5
4
8
12
19
X=2
26
52
78
112
1-200A
1-200A
0-External wiring
1-Internal wiring
0-External wiring
500%-850% FLA
0.5...1Sec
100-200%FLA
500% FLA
1 Sec.
115% FLA
0-Grade 10A
0-Grade 10A
1-Grade 10
2-Grade 20
3-Grade 30
0-OFF
1-ON
1-ON
1-30 Sec.
0.5...10秒
10...50%FLA
0-Electric self holding relay
1-Magnet self holding relay
1-127 1
0-1200BPS
1-2400BPS
2-4800BPS
3-9600BPS
4-19200BPS
3-9600BPS
0-ECC0-ECC
1-ODD
2-None
1375000
2 2
I% -110 ×Tx
6
Overload time
Overload trip time=
Overload
grade
Minimum overload tolerance time
Parameter setting list
Appendix
Parameter Setting range Default
FLC Soft starter full load current
FLA Motor full load current
Connection mode
Over current protection value
Over current trip delay time
Over load protection value
Overload protection grade
Phase sequence protection
Starting time
Stop time
Initial voltage
Bypass relay type
Slave machines address
Baud rate
Parity check
Panel potentiometer setting
Panel potentiometer setting
Panel potentiometer setting
Depending on the specific model
Factory setting
According to the power of soft starter.
20
Appendix
Common load and parameter setting
1)Slope starting mode
15
15
15
15
15
20
20
15
15
15
15
15
0
0
5
0
0
0
0
0
0
0
5
0
45%
45%
45%
45%
45%
45%
45%
45%
45%
45%
45%
45%
Load Start time Stop time Initial voltage
Boat propeller
Centrifugal pump
Piston compressor
Centrifugal fan
Rotary converter
Mixer
Crusher
Spiral air compressor
No-load motor
Band conveyor
Hot water pump
Air pump

21
Mechanical installation
1 2 3 4 5 6 7 8 9 10
Control Voltage
AC 100~240V
RS 485 A
RS 485 B
L N
L1/R
CT1
S1
S2
K2
K1 G1
T1/U
G2
L2/S
CT2
S1
S2
K2
K1 G1
T2/V
G2
L3/T
CT3
S1
S2
K2
K1 G1
T3/W
G2
40
50
60
1
6
18
24
30S
18
0
6
12
24
30S
12
30 70%Un
SL R Ser ies S oft sta rte r
SORE AL(Shangh ai)Electr ical Tec hnolo gy Co., L td.
t
U
t
Power Run Fault 1 Fault 2
Start/Stop
Run Fault
1.5~11A
AModel
105
108
105
91
95
92
124.8
125
135
222
80
80
208
68
182
200
68
60
156
175
60
155
160
129.2
310
110.3
110.3
293
15~22A
BModel
30~75A
CModel
90~150A
DModel
1 2 3 4 5 6 7 8 9 10
Control Voltage
AC 100~240V
RS 485 A
RS 485 B
L N
L1/R
CT1
S1
S2
K2
K1 G1
T1/U
G2
L2/S
CT2
S1
S2
K2
K1 G1
T2/V
G2
L3/T
CT3
S1
S2
K2
K1 G1
T3/W
G2
40
50
60
1
6
18
24
30S
18
0
6
12
24
30S
12
30 70%Un
SL R Ser ies S oft sta rte r
SORE AL(Shangh ai)Electr ical Tec hnolo gy Co., L td.
t
U
t
Power Run Fault 1 Fault 2
Start/Stop
Run Fault
1 2 3 4 5 6 7 8 9 10
Control Voltage
AC 100~240V
RS 485 A
RS 485 B
L N
L1/R
CT1
S1
S2
K2
K1 G1
T1/U
G2
L2/S
CT2
S1
S2
K2
K1 G1
T2/V
G2
L3/T
CT3
S1
S2
K2
K1 G1
T3/W
G2
40
50
60
1
6
18
24
30S
18
0
6
12
24
30S
12
30 70%Un
SL R Ser ies S oft sta rte r
SORE AL(Shangh ai)Electr ical Tec hnolo gy Co., L td.
t
U
t
Power Run Fault 1 Fault 2
Start/Stop
Run Fault
1 2 3 4 5 6 7 8 9 10
Control Voltage
AC 100~240V
RS 485 A
RS 485 B
L N
L1/R
CT1
S1
S2
K2
K1 G1
T1/U
G2
L2/S
CT2
S1
S2
K2
K1 G1
T2/V
G2
L3/T
CT3
S1
S2
K2
K1 G1
T3/W
G2
40
50
60
1
6
18
24
30S
18
0
6
12
24
30S
12
30 70%Un
SL R Ser ies S oft sta rte r
SORE AL(Shangh ai)Electr ical Tec hnolo gy Co., L td.
t
U
t
Power Run Fault 1 Fault 2
Start/Stop
Run Fault
L1/R
CT1
S1
S2
K2
K1 G1
T1/U
G2
L2/S
CT2
S1
S2
K2
K1 G1
T2/V
G2
L3/T
CT3
S1
S2
K2
K1 G1
T3/W
G2
40
50
60
1
6
18
24
30S
18
0
6
12
24
30S
12
30 70%Un
t
U
t
Power Run Fault 1 Fault 2
Sof t start erSof t start erSof t start er
L1/R
CT1
S1
S2
K2
K1 G1
T1/U
G2
L2/S
CT2
S1
S2
K2
K1 G1
T2/V
G2
L3/T
CT3
S1
S2
K2
K1 G1
T3/W
G2
40
50
60
1
6
18
24
30S
18
0
6
12
24
30S
12
30 70%Un
t
U
t
Power Run Fault 1 Fault 2
Sof t start erSof t start erSof t start er
L1/R
CT1
S1
S2
K2
K1 G1
T1/U
G2
L2/S
CT2
S1
S2
K2
K1 G1
T2/V
G2
L3/T
CT3
S1
S2
K2
K1 G1
T3/W
G2
40
50
60
1
6
18
24
30S
18
0
6
12
24
30S
12
30 70%Un
t
U
t
Power Run Fault 1 Fault 2
Sof t start erSof t start erSof t start er
L1/R
CT1
S1
S2
K2
K1 G1
T1/U
G2
L2/S
CT2
S1
S2
K2
K1 G1
T2/V
G2
L3/T
CT3
S1
S2
K2
K1 G1
T3/W
G2
40
50
60
1
6
18
24
30S
18
0
6
12
24
30S
12
30 70%Un
t
U
t
Power Run Fault 1 Fault 2
Sof t start erSof t start erSof t start er

23
Typical wiring
6L2-V
LW5-16YH3/3
KK
V
RT14 20-
SAY7-22
AD16-22
RS Prp
SST
1 2HL 〜HL
ST,SP
FU FU1~3
QF1
QF
DZ47
L3
N
L2
L 1
M
7
6
KA
110/220V AC
SST N
3
2
1
QF1
QF
SS-1801
KA
QF
ST
HL2
KA
SP
(RS Pro)
6 7
L01
R S T
U V W
KA
JZC4-44
5
4
Modbus
10
9
8
(-)
(+)
Modbus
HL 1
(RS Prp)
4 5
L01 N
110/220VAC 110/220VAC
FU3
L3
10
12
9
11
FU2
FU1
L2
L1
2
4
6
1
3
5
KK
8
7
V
Auxilary
contacts
Shunt
trip coil
Operating
Fault
Code Name
Breaker
Breaker
Fuse
Soft starter
Button
Switch
Voltmeter
Diagram
Model
QF
On/Off
Run
Fault
Power
According to motor power
Signal lamp
Auxiliary relay
three-phase softstarter schematic diagram
Run
Com
24
Typical wiring
FU3
L3
10
12
9
11
FU2
FU1
L2
L1
2
4
6
1
3
5
KK
8
7
V
L3
N
L2
L 1
M
7
6
KA
24V DC
SST 24V-
3
2
1
QF1
QF
SS-1802
KA
ST
HL2
KA
24V-
SP
(RS Pro)
6 7
L01
R S T
U V W
5
4
Modbus
10
9
8
(-)
(+)
Modbus
HL 1
(RS Pro)
4 5
24V+
Diagram
three-phase soft starter control diagram Ver1.00
QF
Shunt
trip coil
Run
Operating
Fault
Com
Auxilary
contacts
QF
6L2-V
LW5-16YH3/3
KK
V
RT14 20-
SAY7-22
AD16-22
RS Prp
SST
1 2HL 〜HL
ST,SP
FU FU1~3
QF1
QF
DZ47
KA
JZC4-44
Code Name
Breaker
Breaker
Fuse
Soft starter
Button
Switch
Voltmeter
Model
According to motor power
Signal lamp
Auxiliary relay
On/Off
Run
Fault
Power
This manual suits for next models
15
Table of contents
Other RS PRO Controllers manuals
Popular Controllers manuals by other brands

BioSmart
BioSmart UniPass installation guide

Securefast
Securefast T/SED900/033A installation instructions

Marshall Electronics
Marshall Electronics VS-PTC-50 user manual
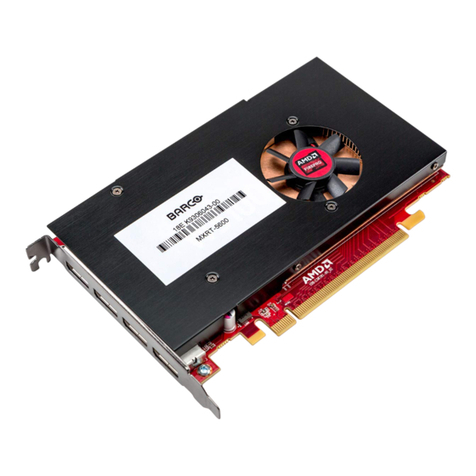
Barco
Barco MXRT-5600 quick start guide
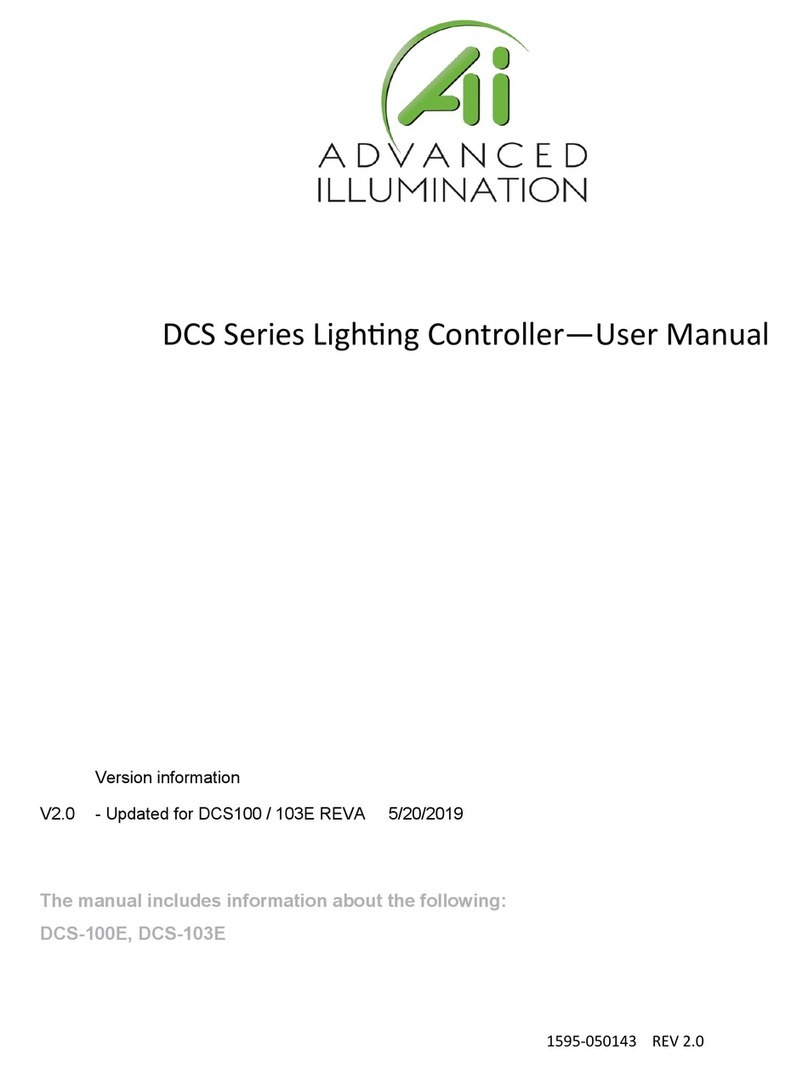
Advanced Illumination
Advanced Illumination DCS Series user manual
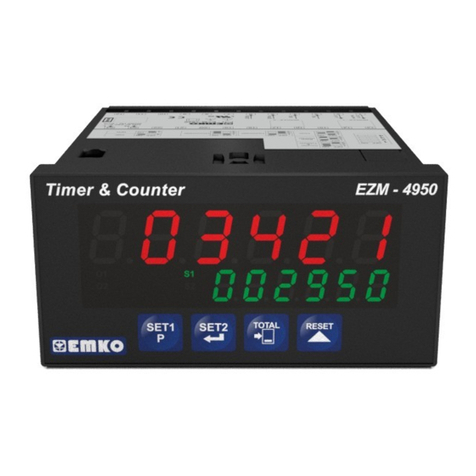
EMKO
EMKO EZM-4950 instruction manual