RUGGED MONITORING H2SENS User manual


Model 5000 Gen5 Transformer Sensor
Operating Manual
90000177 R0, 3/24/2020 ECO 20-032 Page 2 of 18
MISSION STATEMENT
Our Mission
Deliver unsurpassed value and optimize green initiatives with our one of a kind continuous hydrogen-specific sensing
technology worldwide.
Our Value Propositions
Enable end-user customers to efficiently and effectively optimize:
Electric utility power transformer fleet and other oil-filled assets (Grid)
Petroleum refinery and other industrial process control
Facility and equipment safety to minimize downtime
...at a much lower total costs of ownership than the competition.
Our Strategic Objectives
H2scan's technology accepted as the new gold standard in hydrogen sensors.
H2scan's business recognized for innovation and ingenuity, high quality products and systems, application -specific
solutions, and exceptional customer service and satisfaction.
H2scan's success results from teamwork, strategic partnerships and market leadership leading to sales growth and
improved profitability.

Model 5000 Gen5 Transformer Sensor
Operating Manual
90000177 R0, 3/24/2020 ECO 20-032 Page 3 of 18
CONTENTS
1 INTRODUCTION............................................................................................................................5
2 FEATURES ....................................................................................................................................5
2.1 SENSOR ................................................................................................................................. 5
2.2 MECHANICAL .......................................................................................................................... 5
2.3 ELECTRICAL............................................................................................................................ 6
3 ELECTRICAL INTERFACE ...........................................................................................................7
3.1 6V POWER ............................................................................................................................. 7
3.2 GROUND ................................................................................................................................ 7
3.3 DATA+ ................................................................................................................................... 7
3.4 DATA- .................................................................................................................................... 7
4 INSTALLATION .............................................................................................................................7
4.1 HANDLING PRECAUTIONS......................................................................................................... 7
5 OPERATION ..................................................................................................................................8
5.1 STARTUP................................................................................................................................ 8
6 MODBUS ....................................................................................................................................... 8
6.1 COMMUNICATION SETTINGS ..................................................................................................... 8
6.1.1 RS485 Connection .......................................................................................................................................... 8
6.2 PROTOCOL ............................................................................................................................. 8
6.2.1 Exception Response ..................................................................................................................................... 10
6.2.2 Modbus Command Register Definitions........................................................................................................ 11
6.2.3 Unit Status..................................................................................................................................................... 16
6.2.4 Error Status ................................................................................................................................................... 16
6.2.5 User-Defined Oil Type Configuration Window .............................................................................................. 17
7 COMMAND LINE INTERFACE....................................................................................................17
8 FIRMWARE UPGRADE............................................................................................................... 18
8.1 MAIN SENSOR BOARD FIRMWARE UPGRADE PROCEDURE ........................................................ 18

Model 5000 Gen5 Transformer Sensor
Operating Manual
90000177 R0, 3/24/2020 ECO 20-032 Page 4 of 18
IMPORTANT NOTICES
LIMITED WARRANTY
H2scan Limited Warranty
specifications set from
the ship date for such Product.
Must Provide Notice of Defect: If you believe a Product that you believe is defective, you must notify H2scan in writing, within ten (10) days of
receipt of such Product, of your claim regarding any such defect.
Return Product to H2scan for Repair, Replacement or Credit nder this
warranty is to either (i) repair the Product, (ii) replace the Product, or (iii) issue a credit for the purchase price for such Product, the particular
remedy to be determined by H2scan on a case-by-case basis.
Voided Warranty th Limited Warranty is void for any of the following:
The unit is opened and the manufacturing seal is broken
chnicians
Equipment or parts that have been tampered with, misused, neglected, mishandled, improperly adjusted, or modified in any way without the
written consent of H2scan.
Equipment or parts that have been damaged due to shipping, misuse, accidents, mishandling, neglect, or problems with electrical power sources.
Repair work performed during the warranty period does not prolong the warranty period past the original period.
System operation in incorrect or inappropriate environments.
LIMITATION OF WARRANTY: THE ABOVE IS A LIMITED WARRANTY AS IT IS THE ONLY WARRANTY MADE BY H2SCAN. H2SCAN
MAKES NO OTHER WARRANTY EXPRESS OR IMPLIED AND EXPRESSLY EXCLUDES ALL WARRANTIES OF MERCHANTABILITY AND
FITNESS FOR A PARTICULAR PURPOSE. YOUR SOLE REMEDY HEREUNDER IS REPAIR OR REPLACEMENT OF THE PRODUCT OR A
CREDIT FOR THE PURCHASE PRICE FOR SUCH PRODUCT, THE PARTICULAR REMEDY TO BE DETERMINED BY H2SCAN ON A CASE-
BY-CASE BASIS. H2SCAN SHALL HAVE NO LIABILITY WITH RESPECT TO ITS OBLIGATIONS UNDER THIS AGREEMENT FOR
CONSEQUENTIAL, EXEMPLARY, OR INCIDENTAL DAMAGES EVEN IF IT HAS BEEN ADVISED OF THE POSSIBILITY OF SUCH DAMAGES.
THE STATED EXPRESS WARRANTY IS IN LIEU OF ALL LIABILITIES OR OBLIGATIONS OF H2SCAN FOR DAMAGES ARISING OUT OF OR
IN CONNECTION WITH THE DELIVERY, USE OR PERFORMANCE OF THE PRODUCTS.
LIMITATION OF LIABILITY - SELLER SHALL UNDER NO CIRCUMSTANCES BE LIABLE FOR ANY INCIDENTAL, CONSEQUENTIAL,
SPECIAL, PUNITIVE, OR OTHER DAMAGES, INCLUDING, BUT NOT LIMITED TO, LOSS OF BUSINESS OR PROFIT, PROMOTIONAL OR
MANUFACTURING EXPENSES, INJURY TO REPUTATION, OR LOSS OF CUSTOMER, BASED ON ANY ALLEGED NEGLIGENCE,
BREACH OF WARRANTY, STRICT LIABILITY, BREACH OF CONTRACT, OR ANY OTHER LEGAL THEORY ARISING OUT OF THE USE,
MISUSE, PURCHASE, SALE OR POSSESSION OF ITS GOODS OR ITS PERFORMANCE OF THIS CONTRACT TO THE EXTENT THAT
SUCH CLAIM IS BASED. SELLER ADVISES BUYER TO PERFORM ACCEPTABLE TESTS ON ALL HARDWARE PRIOR TO
DEPLOYME
CIRCUMSTANCES SHALL THE EQUIPMENT PROVIDED HEREUNDER BE USED IN A MANNER WHERE IT IS THE SOLE PROTECTIVE
SYSTEM FOR FACILITIES, EQUIPMENT AND PERSONNEL SAFETY; THE EQUIPMENT IS INTENDED FOR USE IN CONJUNCTION
WITH OTHER APPROPRIATE PROTECTIVE SYSTEMS.

Model 5000 Gen5 Transformer Sensor
Operating Manual
90000177 R0, 3/24/2020 ECO 20-032 Page 5 of 18
1 Introduction
The Gen5 Hydrogen Sensor is designed to detect and/or measure hydrogen as a component of
transformer oil. The hydrogen specific solid-state sensing element is designed for ease of use
and interface flexibility. The Gen5 Hydrogen Sensor is an online hydrogen monitoring sensor for
distribution class transformers. This enclosure provides 6VDC power to the Gen5 Hydrogen
Sensor and communicates over a UART interface. 5th generation electronics,
the Gen5 Hydrogen Sensor contains all the circuitry necessary to operate the sensor and present
calibrated hydrogen readings through Modbus protocol over a 2-wire RS485 bus. The measured
hydrogen is reported as ppmH2 dissolved in oil and is comparable to industry standard DGA
measurements. Oil temperature at the sensing element is measured and available through the
digital interfaces.
This document has been updated for use with firmware revision 0:82:A.
2 Features
2.1 Sensor
Gen5 Hydrogen Sensor hydrogen
alloy sensor.
Calibrated to measure hydrogen dissolved in transformer oil
Periodic reference cycles are automatically run to eliminate offsets affecting long term
stability
No maintenance, long life sensing element
WARNING: The sensor element may be damaged if exposed to hydrogen
concentrations above 5,000 ppm.
2.2 Mechanical
The Gen5 Hydrogen Sensor is a rugged water proof mechanical assembly design for
distribution transformer applications. -14 NPT fitting is provided for attachment of the
sensor to a transformer. Overall dimensions are shown below.

Model 5000 Gen5 Transformer Sensor
Operating Manual
90000177 R0, 3/24/2020 ECO 20-032 Page 6 of 18
2.3 Electrical
The Gen5 Hydrogen Sensor uses a single M12 4-pin connector for power and communications.
DC power input of 9 to 48 volts, 10 watts
2-wire RS485 for Modbus RTU communications

Model 5000 Gen5 Transformer Sensor
Operating Manual
90000177 R0, 3/24/2020 ECO 20-032 Page 7 of 18
3 Electrical Interface
All electrical connections are supplied through a 4-pin M12 connector. The key location and pin
numbers are shown below.
3.1 6V Power
Connect a DC power source rated for 9 to 48 volts,10 watts to pin 1.
3.2 Ground
Connect DC ground to pin 2.
3.3 Data+
Connect the RS485 Data+ signal to pin 3.
3.4 Data-
Connect the RS485 Data- signal to pin 4.
4 Installation
-14 NPT fitting on the oil tank. Adapter bushing for larger ID fittings can
be used however, do not use adapters to smaller ID fittings or pipe. The sensor should be
mounted in a horizontal position prevent an air bubble forming around the sensor element. Any
and the total length less than 8 . Additional installation notes are listed below.
Do not allow debris to accumulate around the sensor element
Use thread sealing tape
Provide means to evacuate gas bubbles in pipe fittings between sensor and oil tank
Do not install sensor in turbulent oil flow
4.1 Handling Precautions
The following precautions must be followed to ensure the sensor assembly is not damaged
during handling.
Do not poke anything into the open end around the sensor element
Place wrench close the threaded end when tightening
Do not over tighten

Model 5000 Gen5 Transformer Sensor
Operating Manual
90000177 R0, 3/24/2020 ECO 20-032 Page 8 of 18
5 Operation
5.1 Startup
After connecting the cable and turning on the power supply the sensor executes a warm-up
sequence lasting several minutes. The following operations are done during the warm-up
sequence:
Perform system self-test
Restore configuration settings from non-volatile memory
Start the sampling system to measure hydrogen and oil temperature
Approximate hydrogen readings will be reported by the sensor within 15 minutes. On new
installations the sensor will take up to 16 hours to reach equilibrium and report an accurate
hydrogen reading.
Modbus will indicate Not Ready until the first valid hydrogen measurement then reports the most
recent measurements. If an error is reported turn off power to the sensor; double check the
electrical connections; and power supply voltage before turning on power again. If the error
condition persists, contact H2scan customer service for assistance.
During normal operation the sensor will periodically measure oil temperature (approximately
once/hour) to provide temperature compensated dissolved gas readings. The unit will also
periodically go through an internal calibration check (called reference cycle). These are
automatic activities and no user interaction is required.
6 Modbus
6.1 Communication Settings
Modbus protocol is configured to operate on the RS485. The device supports RTU packets and
the default device ID is 1.
6.1.1 RS485 Connection
The following communication settings are used on the RS485, 2-wire, half-duplex connection.
Baud Rate:
19,200
Data bits:
8
Stop bits:
1
Parity:
None
Flow Control:
None
6.2 Protocol
The following tables comprise the list of Modbus packets, values, registers, and register
definitions.
The maximum
should be set to 10,000 milliseconds or greater.

Model 5000 Gen5 Transformer Sensor
Operating Manual
90000177 R0, 3/24/2020 ECO 20-032 Page 9 of 18
Table 1: Modbus Read Request Packet
Byte
Modbus Parameter Range Meaning
1 Slave address 1 247 Unit ID Address
2 Function Code 03 Read Holding Register
3 Starting Address Hi 0x00 0xFF
Holding Register Hi Byte
4 Starting Address Lo 0x00 0xFF
Holding Register Lo Byte
5 Number of registers Hi 0 Limited by Modbus spec V1.1b
6 Number of Registers Lo
1 125 Number of 16-bit registers Lo Byte
7 CRC Lo 0x00 0xFF
CRC Low Byte
8 CRC Hi 0x00 0xFF
CRC High Byte
Table 2: Modbus Read Response Packet
Byte #
Modbus Parameter
Range Meaning
1 Slave address 1 247 Unit ID Address
2 Function Code 03 Returning Holding Registers
3 Byte Count 7 255 Number of data bytes returned = N
4 1st Data Value Hi 0x00 0xFF
5 1st Data Value Lo 0x00 0xFF
6 2nd Data Value Hi 0x00 0xFF
7 2nd Data Value Lo 0x00 0xFF
2N+4 CRC Lo 0x00 0xFF
CRC Low Byte
2N+5 CRC Hi 0x00 0xFF
CRC High Byte
N is the number of bytes returned based on the number of registers requested. If
N registers are requested, then 2N+5 bytes are returned.
Table 3: Modbus Write Request Packet
Byte
Modbus Parameter
Range Meaning
1 Slave address 1 247 Unit ID Address
2 Function Code 06 Write Holding Registers
3 Register Address Hi 0x00 0xFF
Unit Register Address Hi byte
4 Register Address Lo
0x00 0xFF
Unit Register Address Lo byte
5 Data Value Hi Byte 0x00 0xFF
6 Data Value Lo Byte 0x00 0xFF
7 CRC Lo 0x00 0xFF
CRC Low Byte
8 CRC Hi 0x00 0xFF
CRC High Byte
Table 4: Modbus Write Response Packet
Byte
Modbus Parameter Range Meaning
1 Slave address 1 247 Unit ID Address
2 Function Code 06
3 Register Address Hi Byte 0x00 0xFF
Unit Register Address Hi byte
4 Register Address Lo Byte
0x00 0xFF
Unit Register Address Lo byte
5 Data Value Hi Byte 0x00 0xFF
6 Data Value Lo Byte 0x00 0xFF
7 CRC Lo 0x00 0xFF
CRC Low Byte
8 CRC Hi 0x00 0xFF
CRC High Byte

Model 5000 Gen5 Transformer Sensor
Operating Manual
90000177 R0, 3/24/2020 ECO 20-032 Page 10 of 18
6.2.1 Exception Response
In a normal communications query and response due to a communication error, the master
device sends a query to the slave device. Upon receiving the query, the slave processes the
request and returns a response to the master device. An abnormal communication between
the two devices produces one of four possible events:
1. If the slave does not receive the query due to a communications error, then no response
is returned from the slave and the master device will eventually process a timeout
condition for the query.
2. If the slave receives the query but detects a communication error (UART or CRC), then
no response is returned from the slave and the master device will eventually process a
timeout condition for the query.
3. If the slave receives the query without a communications error, and takes longer than
response is returned from the slave. The master
device eventually processes a timeout condition for the query. To prevent this
condition, the master timeout must be set longer than the maximum response time of
the slave (10,000 milliseconds).
4. If the slave receives the query without a communications error but cannot process it due
to reading or writing to a non-existent slave command register, then the slave returns an
exception response message informing the master of the error.
The exception response message has two fields that differentiate it from a normal response.
The first is the function code byte 2. This code will have the high order bit set to a one (i.e.
0x83 for a read exception and 0x86 for a write exception). The second differentiating field is
the exception code byte 3. In addition, the total exception response length is 5 bytes rather
than the normal message length.
Table 5: Exception Response Packet
Byte
Modbus Parameter
Range Meaning
1 Slave Address 1 247
2 Function Code 0x83 or 0x86 Read or Write
3 Exception Code See Table Below
4 CRC High 0x00 0xFF
5 CRC Low 0x00 0xFF

Model 5000 Gen5 Transformer Sensor
Operating Manual
90000177 R0, 3/24/2020 ECO 20-032 Page 11 of 18
Table 6: Exception Response Codes
Code
Name Description
1
Illegal
Function
Code
The function code received in the query is not an allowable action for the slave.
This may be because the function code is only applicable to newer devices, and
was not implemented in the unit selected. It could also indicate that the slave is
in the wrong state to process a request of this type, for example because it is
not configured and is being asked to return register values.
2 Illegal Data
Address
The data address received in the query is not an allowable address for the
slave. More specifically, the combination of reference number and transfer
length is invalid. For a controller with 100 registers, the PDU addresses the first
register as 0, and the last one as 99. If a request is submitted with a starting
register address of 96 and a quantity of registers of 4, then this request will
successfully operate (address-wise at least) on registers 96, 97, 98, 99. If a
request is submitted with a starting register address of 96 and a quantity of
registers of 5, then this request will fail wit
there is no register with address 100.
3 Illegal Data
Value
A value contained in the query data field is not an allowable value for slave. This
indicates a fault in the structure of the remainder of a complex request, such as
that the implied length is incorrect. It specifically does NOT mean that a data
item submitted for storage in a register has a value outside the expectation of
the application program, since the MODBUS protocol is unaware of the
significance
4
Slave
Device
Failure
An unrecoverable error occurred while the slave was attempting to perform the
requested action.
6.2.2 Modbus Command Register Definitions
The Command Register definitions for the Gen5 Hydrogen Sensor are identified in Table 7.

Model 5000 Gen5 Transformer Sensor
Operating Manual
90000177 R0, 3/24/2020 ECO 20-032 Page 12 of 18
Table 7: Command Register Locations
Register
Parameter Function Data Type Data Range Access
Measurements
0 Hydrogen, ppm H2
High word 32-bit binary
number
0 to
20,000,000 R
1 Low word
2-6 Reserved for future use
7
PCB Temperature,
Celsius
x100 scale; 100 offset
(T=V/100-100)
16-bit binary
number -100 to +200
R
8 Oil Temperature,
Celsius
x100 scale; 100 offset
(T=V/100-100)
16-bit binary
number -100 to +200
R
9-12 Reserved for future use
13 Rate of Change,
ppm H2 per Day
+20,000,000 offset
High word 32-bit binary
number
-20,000,000
to
+20,000,000
R
14 Low word
15 Rate of Change,
ppm H2
per Week
+20,000,000 offset
High word 32-bit binary
number
-20,000,000
to
+20,000,000
R
16 Low word
17 Rate of Change,
ppm H2
per Month
+20,000,000 offset
High word 32-bit binary
number
-20,000,000
to
+20,000,000
R
18 Low word
19-30 Reserved for future use

Model 5000 Gen5 Transformer Sensor
Operating Manual
90000177 R0, 3/24/2020 ECO 20-032 Page 13 of 18
Register
Parameter Function Data Type Data Range Access
Information
31-40 Model Number ASCII String R
41-50 Product Serial
Number ASCII String R
51-60 Sensor Serial
Number ASCII String R
61-70 Sensor Board
Serial Number ASCII String R
71-80 Reserved for future use
81 Manufacturing
Date
high byte: Month
low byte: Day 32-bit binary
value R
82 Year
83
Factory Calibration
Date
high byte: Month
low byte: Day 32-bit binary
value R
84 Year
85-86 Reserved for future use
87 Dissolved Gas
Calibration Date
high byte: Month
low byte: Day 32-bit binary
value R
88 Year
89-98 Firmware Revision
ASCII String R
99-110 Reserved for future use
Status/Error Information
111 Status Refer to section 6.2.3 16-bit binary
flags See Table 8 R
112 Error Status
Refer to section 6.2.4
High word 32-bit binary
flags See Table 9 R
113 Low word
114-120
Reserved for future use

Model 5000 Gen5 Transformer Sensor
Operating Manual
90000177 R0, 3/24/2020 ECO 20-032 Page 14 of 18
Register
Parameter Function Data Type Data Range Access
Calibration Functions
121 DA command None Section W
122 DB command Write reg 126-129 first None Section W
123-124
Reserved for future use
125 DC command clear DGA calibration None Section W
126 Calibration Gas,
ppm H2
High word 32-bit binary
number
0 to
1,000,000 R/W
127 Low word
128 Calibration Date
high byte: Month
low byte: Day 32-bit binary
value R/W
129 Year
130-135
Reserved for future use
Configuration Settings
136-143
User-define Oil
Type name
Refer to Section 6.2.5 for
User-define Oil type
Configuration Window
descriptions.
ASCII String R/W
144 Ostwald Slope, m
16-bit binary
number R/W
145 16-bit binary
number R/W
146
Ostwald Offset, b
16-bit binary
number R/W
147 16-bit binary
number R/W
148 Oil Type
Operations
16-bit binary
number
1= open edit
2 = close edit
3 = abort edit
R/W
149 Switch to CLI 8-bit binary
number 0 W
150 Set Unit ID 8-bit binary
number 1 to 247 R/W
151 Operating Mode
Select between Field and Lab
mode
16-bit binary
number
0 = Field
1 = Lab R/W
152 Oil Type Selection
Select Oil Type
16-bit binary
number
0 = Mineral
1= Silicon
2 = FR3
3 = user-
define
R/W
153-174
Reserved for future use

Model 5000 Gen5 Transformer Sensor
Operating Manual
90000177 R0, 3/24/2020 ECO 20-032 Page 15 of 18
Register
Parameter Function Data Type Data Range Access
Diagnostics
175 Month / Year
Date & Time;
read register 175 first; order
high-byte / low-byte;
add 2000 to year
Two Bytes R
176 Hour / Day Two Bytes R
177 Second / Minute Two Bytes R
178 Millisecond 16-bit binary
number R
179-200
Reserved for future use
User Information
201-210
Owner ID Must start reading from low
address;
Must write low and high
addresses to save string
ASCII String R/W
211-220
Sub-Station ID ASCII String R/W
221-230
Transformer ID ASCII String R/W
231-255
Reserved for future use
Note: When reading registers containing 32 or 64-bit integers the user must read the high
order word first, then the lower order word(s). Reading of the high order word causes the
low order to be saved in a temporary location for the next register read. The second register
is then automatically read from the temporary location by the firmware. Likewise, with a
write, the high value is stored until the second value is received at which time both values
are written to the instrument.

Model 5000 Gen5 Transformer Sensor
Operating Manual
90000177 R0, 3/24/2020 ECO 20-032 Page 16 of 18
6.2.3 Unit Status
Unit status information is maintained in Modbus register 111. The bit map for this status word
is described below:
Table 8: Unit Status
Bit #
Description
15 Unit Ready, hydrogen readings are valid
14 New measurement data available, auto-clear after register read
12 Error, indicates an unrecoverable error occurred, read Reg 112,113 for
more information
13 Reserved
11 Reserved
10 Reserved
9 Reserved
8 Reserved
7 Reserved
6 Reserved
5-3
Sensor A state Information:
000 Sensor A not used
001 Hydrogen measurement cycle
010 Oil temperature measurement cycle
011 Auto calibration cycle
100 Oil temperature too high
2-0
Sensor B state Information:
000 Sensor B not used
001 Hydrogen measurement cycle
010 Oil temperature measurement cycle
011 Auto calibration cycle
100 Oil temperature too high
6.2.4 Error Status
When the error flag (bit 12) of the Unit Status register 111 is set, this 32-bit register has more
information about what is causing the error. The bit map is shown below, unlisted bits are
reserved.
Table 9: Error Status
Bit #
Hex Value Description
31 0x8000 0000
Sensor A Heater fault
30 0x4000 0000
Sensor A Temperature Sensor Fault
29 0x2000 0000
Sensor A Hydrogen Sensor 1 Fault
28 0x1000 0000
Sensor A Hydrogen Sensor 2 Fault
19 0x0008 0000
Sensor B Heater fault
18 0x0004 0000
Sensor B Temperature Sensor Fault
17 0x0002 0000
Sensor B Hydrogen Sensor 1 Fault
16 0x0001 0000
Sensor B Hydrogen Sensor 2 Fault
2 0x0000 0004
PCB Temperature greater than 105C
1 0x0000 0002
Required data not available
0 0x0000 0001
Configuration data not valid

Model 5000 Gen5 Transformer Sensor
Operating Manual
90000177 R0, 3/24/2020 ECO 20-032 Page 17 of 18
6.2.5 User-Defined Oil Type Configuration Window
The Oil Type Configuration Window registers are used to read and modify user-defined Oil Type
configuration data structure. This includes the name, and Ostwald values for slope and offset.
A. Oil Type Name
A string of size 16 characters
Null-terminated
B. Ostwald Value, Slope (m)
Scale: x1,000,000; 1,000 offset
Data32 = ( (m + 1,000) * 1,000,000
Register 144, Data32, High 16-Bit data
Register 145, Data32, Low 16- Bit data
C. Ostwald Value, Offset (b)
Scale: x1,000,000; 1,000 offset
Data32 = ( (b + 1,000) * 1,000,000
Register 146, Data32, High 16-Bit data
Register 147, Data32, Low 16-Bit data
D. Oil Type Operations
Register 148
Value = 1, starts configuration edit for user-defined Oil type.
Value = 2, ends the edit and saves the new configuration settings
Value = 3, aborts the operation and nothing is changed
7 Command Line Interface
The command line interface will be deprecated when the Gen5 Hydrogen Sensor goes to
production. To support existing software tools and test processes a primitive CLI is supported.
The half-duplex connection imposes some restrictions on the CLI operation:
Only one side can send data at a time.
The sensor will not send
when the command is complete.
Multiple devices cannot be daisy chained on an RS485 bus while the CLI is active.
The only way to stop streaming data is to power cycle the sensor.
Only use the commands listed below. If a different command is issued, then power cycle
the unit to prevent damage.

Model 5000 Gen5 Transformer Sensor
Operating Manual
90000177 R0, 3/24/2020 ECO 20-032 Page 18 of 18
User Commands
Command Description
G <#lines> <sec/line>
Start streaming data
#lines stop after printing these lines (0 will print forever)
sec/line is time between lines (0 is equal to 1 second)
power cycle to stop streaming and return to Modbus
LD Display the data log
SI 2 Switch to Modbus communications
8 Firmware Upgrade
Gen5 Hydrogen Sensor firmware is field upgradable. Instructions and PC software will be
provided by H2scan as needed.
Unzip the firmware upgrade files to a directory on the PC. The directory will contain six files.
HduG5.exe sensor downloader utility
g5R0_82A.bin sensor firmware binary file
g5r0_82A.bat sensor batch file
8.1 Main Sensor Board Firmware Upgrade Procedure
1. Determine the RS-485 serial communication port for Gen5.
2. Create the g5r0_82A.bat file to use the COM port number that the Gen5 is connected to.
The sensor batch file contains the following commands.
hduG5.exe g5R0_82A.bin com3
pause

This manual suits for next models
1
Table of contents
Popular Security Sensor manuals by other brands
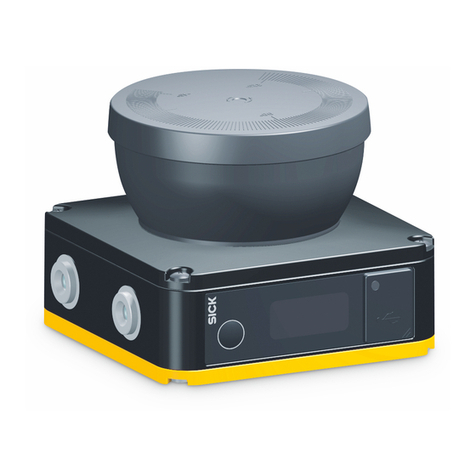
SICK
SICK nanoScan3 I/O operating instructions
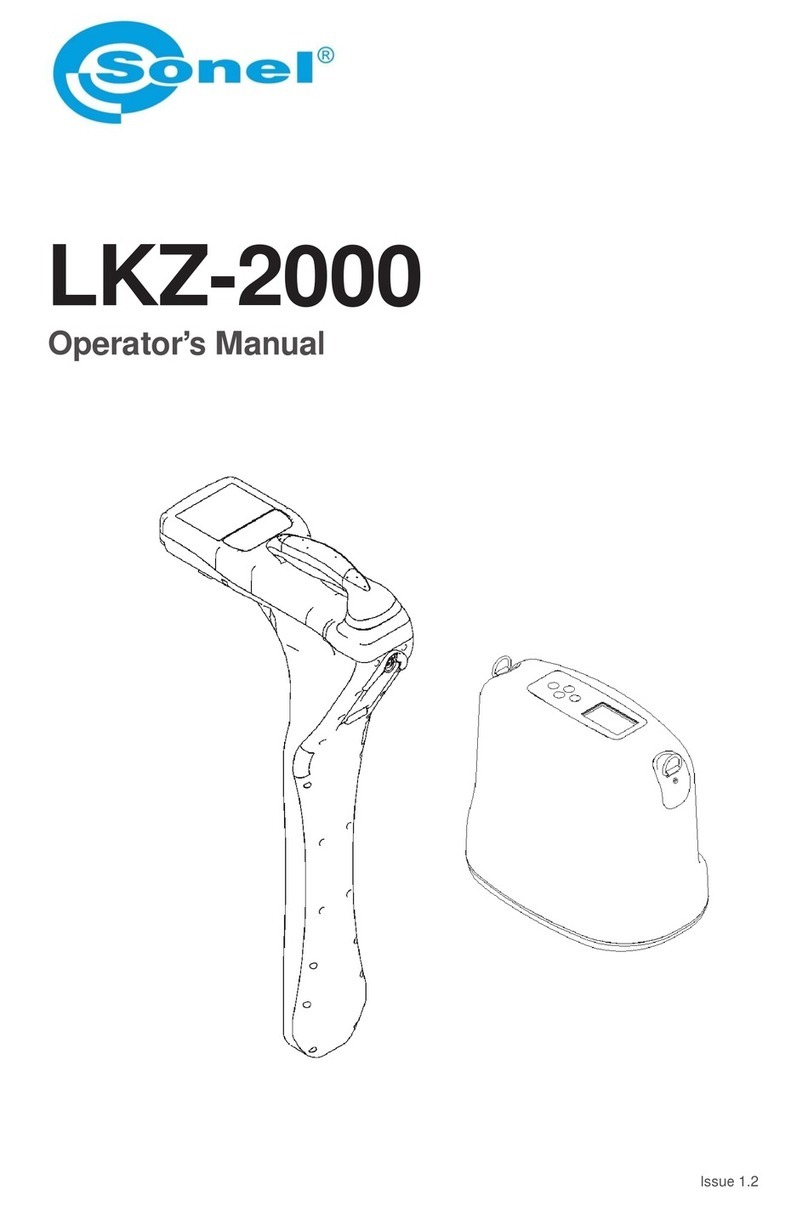
Sonel
Sonel LKZ-2000 Operator's manual

BW Technologies
BW Technologies GasAlertClip Extreme 2 Year instruction sheet

Sminn
Sminn MINI CND Assembly instructions

Plastic Safety Systems, Inc.
Plastic Safety Systems, Inc. SafetyRail Assembly instructions
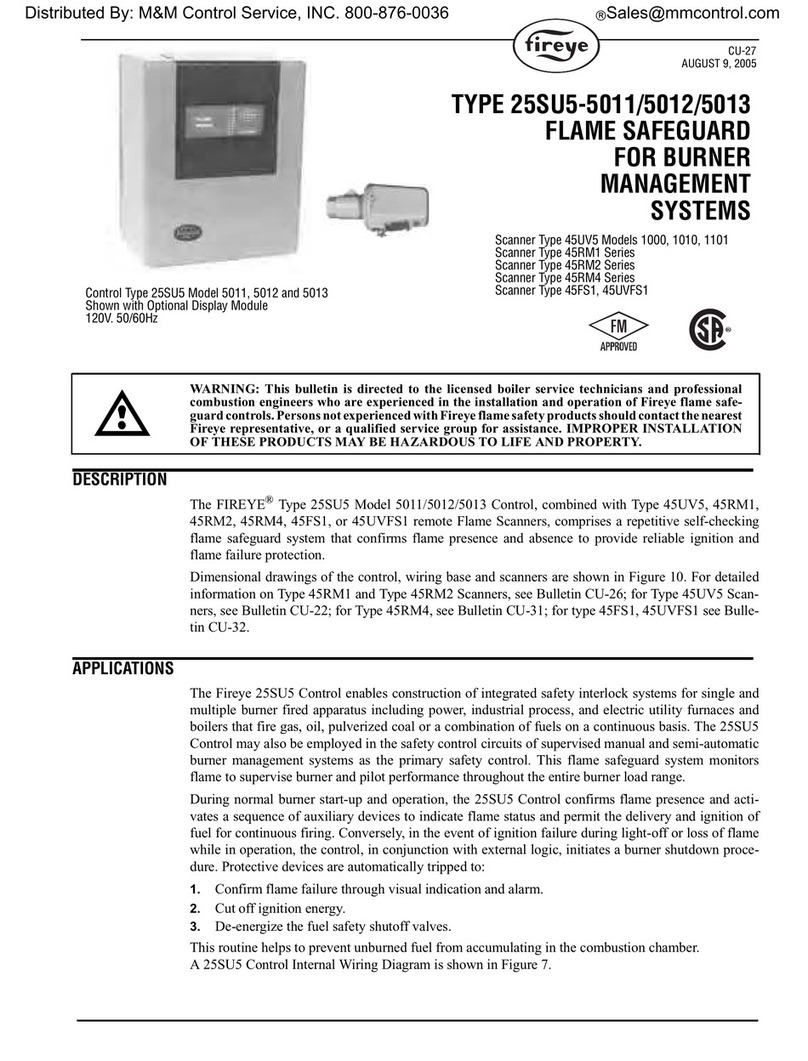
Fireye
Fireye 25SU5-5011 manual