Sanyo Denki Sanmotion R User manual

M0009143C
For Rotary Motor
Pulse Input Type
TYPE F(DC48V)


Detailsofrevisionhistory
The third edition (C)
■ Chapter 2 and 4
● A precaution to use battery for main circuit added.
■ Chapter 2
● A precaution on control power supply added.
● Terminal layout on connector for battery added.
■ Chapter 5
● A precaution on parameters for Backup Type Absolute Encoder Function Selection added.
● Maximum number of repetitions of turning-on/off of servo amplifier added.
● A precaution during parameter-writing to servo amplifier added.
● A precaution on resetting alarm added.
● A formula for converting between “effective torque monitor” and “motor utilization monitor” added.
● A precaution on parameters for Model Following Control added.
● A precaution on parameters for Torque Limit Function added.
● A precaution on parameters for Analog Monitor added.
● A precaution on parameters for Dynamic Brake Operation added.
■ Chapter 10
● Outline dimensional drawing of lithium battery added.

Safetyprecautions Pleasefullyfollow
i
Carefully review this operating manual and the supporting documentations to use the product
properly before perfoming installation, operation, and maintenance.
Use this product after you fully understand sufficient knowledges on all the equipments and safety
information, and precautions.
This manual classifies safety precautions as follows:
•“DANGER”
•“WARNING”
•“CAUTION”
■ Signs of WARNING
When handled incorrectly, excessive dangerous circumstances
may occur to the extent that risk of death or suffering serious
injuries are envisioned.
When handled incorrectly, dangerous circumstances may occur to
the extent that risk of death or suffering serious injuries are
envisioned.
When handled incorrectly, dangerous circumstances may occur to
the extent that risk of moderate injuries, minor injuries, or physical
damages only are envisoend.
Please be advised that even items in the scope of CAUTION may have serious
consequences depending on circumstances. Fully observe every item that has important details.
■ Signs of PROHIBITION and MANDATORY
Indicates PROHIBITIONs (actions that must not be done).
Indicates MANDATORY actions (that must be performed without
fail).
DANGER
WARNING
CAUTION

Safetyprecautions Pleasefullyfollow
ii
■ Operating precautions
WARNING
Fully observe the following warnings because of risk of electrical shock and injury.
Do not operate the product in explosive atmospheres, because of risk of injuries and fire.
Do not perform wiring and maintenance with applying current. These must be done over 10
minutes after breaking main power supply and after confirmation main power supply
capacitor discharged, because of risk of electrical shock and damages.
Surely ground earth terminal of servo amplifier (protective grounding terminal) to equipment
or control board. Connect earth terminal of servo motor to earth terminal of servo amplifier
without fail, because of risk of electrical shock.
Never touch the inside of servo amplifier, because of risk of electrical.
Do not scratch cables, apply excessive stresses, put heavy things, and tuck down any
things, because of risk of electrical.
Do not touch rotating area of servo motor while operating, because of injuries.
CAUTION
Use designated combination of servo amplifier and motor, failure to observe this causes fire
and failure.
Person with expertise shall perform transfer, installation, wiring, operation, and
maintenance, because of risk of electrical shock, injuries, and fire.
Never install in water existed area, corrosive and flammable gas atmosphere, and near
combustible materials, failure to observe this causes fire and failure.
Read operating manual and observe the instructions prior to installation, operation, and
maintenance, because of risk of electrical shock, injuries, and fire.
Do not use servo amplifier and motor outside the scope of the specifications, because of
risk of electrical shock, injuries, and fire.
When wiring of main power supply and motor power line are relatively long, motor torque
decreases due to impedance of wiring. Set acceleration and deceleration torque with
sufficient margin when selecting motor, and verify them on actual equipment.
CAUTION
Be careful of peripheral equipments of servo amplifier and motor that are subjected to high
temperature, because of risk of burn injuries.
Do not touch heat sink fin of servo amplifier and servo motor are at high temperature when
applying current or for a while after breaking power supply, because of risk of burn injuries.

Safetyprecautions Pleasefullyfollow
iii
■ Storage
PROHIBITION
Do not storage the product in water, hazardous gas, and liquid existed area, failure to
observe this causes failure.
MANDATORY
Storage the product within the specified temperature and himidity range ”-20°C thorugh
+65°C, 90%RH” or less (no condensation) and by avoiding direct sunlight. Failure to
observe this causes failure.
Please contact us if storage period of servo amplifier has been long-term (for over 3 years),
as long-term storage causes decrease capacity of electrolytic capacitor. Failure to observe
this causes failure.
Please contact us if storage period of servomotor has been long-term (for over 3 years),
verification of bearing and brake are required.
■ Transportation
CAUTION
When transporting the product, do not pick cables, motor shafts, and detecting devices,
because of risk of failure and injuries.
When transporting the product,be aware of dangers of falling and rolling over, because of
risk of injuries.
MANDATORY
Products overloading causes collapsing, so observe the instructions on the outer case,
because of risk of injuries.
Use eyebolt of servo motor to carry servo motor only, not any equipments, because of risk
of injuries and failure.

Safetyprecautions Pleasefullyfollow
iv
■ Installation
CAUTION
Do not put heavy things or get on top of the product, because of risk of injuries.
Fully observe installation direction, failure to observe this causes fire and failure.
Do not let fall and apply high impacts on the products. Failure to observe this causes
failure.
Do not shut or let foreign materials into the port, because of risk of fire.
Keep proper distances for lay out in servo amplifier control board as instructed in operating
manual, failure to observe this causes fire and failure.
Unpack after confirming top and bottom of the case, because of risk of injuries.
Confirm no discrepancies between delivered product and ordered item. Failure to observe
this causes injuries and damages.
Be aware of risk of falling and rolling over when installing. Use eyebolt if supplied with
servo motor, because of risk of injuries.
Install the product in incombustible materials like metal, because of risk of fire.
■ Wiring
CAUTION
Perform wiring surely and correctly, because of risk of injuries.
Perform wiring in accordance with instructions in wiring diagram or operating manual,
because of risk of electrical shock and fire.
Perform wiring in accordance with electrical facility technical standard and wiring
regulation, because of risk of burnout and fire.
Do not connect commercial power supply to U, V, and W terminal of servo motor, because
of risk of fire and failure.
Place safety device like braker in case of short circuit of external wiring, because of risk of
fire.
Do not band power conduit cables, I/O signal cables, and encoder cables together, or pass
them through the same duct. Failure to observe this causes malfunction.
Do not connect DC90V or AC power supply to DC24V brake of servo motor. Do not
connect AC400V power supply to AC200V fan of servo motor, because of risk of burnout
and fire.
Do not use thin cables for wiring, or avoid excessive long wiring for power input cables and
motor power coduit cables, as these may cause control circuit inoperative or failure of
specification-compliant operation due to torque decrease. Set acceleration and
deceleration torque with sufficient margin when selecting motor.

Safetyprecautions Pleasefullyfollow
v
■ Operation
CAUTION
Never make excessive adjustment change as the operation becomes unstable, and there is
risk of injuries.
Fix servo motor apart from mechanical equipments to perform test operation and install in
the machine after operation check, because of risk of injuries.
Holding brake is not a stopping device to secure machine safety. Place a stop device to
secure safety on the side of machine, because of risk of injuries.
When alarm activated, eliminate the causes, ensure the safety, and reset alarm to restart
operation, because of risk of injuries.
Confirm input power supply voltage is within the scope of the specification. Failure to
observe this causes failure.
Do not get close to machine as the machine may restart without notice after recovery from
momentary stoppage. (Design machines so as to secure safety in case of restart.)
There are risks of injuries.
Do not use broken, damaged, and burnout servo amplifier and motor, because of risk of
injuries and fire.
In the event of malfunction, stop the operation immediately, because of risk of injuries,
electrical shock, and fire.
When using servo motor on the vertical axis, place safety device so as not to let works fall
when alarm activated, Because of risk of injuries and damages.
PROHIBITION
Holding brake supplied with servo motor is designed to hold only, so do not use this brake
for normal braking. If used for braking, this brake is damaged. Failure to observe this
causes failure.
Do not apply static electricity and high voltage to cables for servo motor encoder. Failure to
observe this causes failure.
Do not continuously and externally rotate servomotor in combination with servo amplifier
with standard dynamic brake resistance when servo is off, as dynamic brake resistance
produces heat, because of risk of fire and burn injuries.
Do not disconnect connectors when applying current, because of risk of damages.

Safetyprecautions Pleasefullyfollow
vi
MANDATORY
Externally place emergency stop circuit so as to immediately stop operation and disconnect
power supply. Incorporate safeguard circuit into the outside of servo amplifier so as to
disconnect main circuit power when alarm activated, because of risk of going out of control,
injuries, burnout, fire, and secondary damages.
Any protective devices are not supplied with servo motor, so protect the motor with
overcurrent protective device, earth leakage breaker, overtemperature preventive device,
and emergency stop device, because of risk of injuries and fire.
Operate within the scope of specified temperature and humidity.
Servo amplifier
Temperature: 0°C thorugh 40°C
Humidity: 90% RH or less (No condensation)
Servo motor
Temperature: 0°C thorugh 40°C
Humidity: 20 through 90%RH (No condensation, as this causes burnout and failure.)
■ Maintenance
CAUTION
Some servo amplifier component parts (electrolytic capacitor and lithium battery for
encoder) aged-deterioration. For preventive maintenance, replace the parts by referring
standard cycle of replace, and contact us when replacing. Failure to observe this causes
failure.
Never get close to or touch terminals and connectors when applying current, because of
risk of electrical shock.
Do not disconnect connectors when applying current, because of risk of damages.
Be aware of high temperature of servo amplifier flame when performing maintenance,
because of risk of burn injuries.
Please contact us when you would like to repair, as overhaul causes product inoperative.
Failure to observe this may causes failure.
PROHIBITION
Do not perform overhaul.
Overhaul causes fire and electrical shock.
Do not measure insulation resistance and dielectric strength voltage, because of risk of
damage.
When applying current, never remove terminals and connectors (except for insertable and
removable ones), because of risk of electrical shock and damages.
Do not remove nameplate
■ Disposal
MANDATORY
Dispose servo amplifier or motor as industrial waste.

Table of contents
vii
Table of contents
1. Preface
1.1 Introduction·······························································································································································1-1
1) Changes and additions to AC Servo amplifier SANMOTION R (previous model)···················································1-1
1.2 Instruction Manual ····················································································································································1-2
1) Contents··································································································································································1-2
2) Precautions on this manual·····································································································································1-2
1.3 Illustration of System Components ···························································································································1-3
1.4 Model number structure············································································································································1-4
1) Model number of servo motor ·································································································································1-4
2) Model numbers of servo amplifier (abbreviated model numbers) ···········································································1-5
1.5 Part names ·······························································································································································1-6
1) Servo amplifier························································································································································1-6
2) Servo motor ····························································································································································1-7
2. Specification
2.1 Servo motor ·························································································································································2-1
1) Common specification······································································································································2-1
2) Servo motor external dimension, specification, and weight··············································································2-1
3) Mechanical specification, strength, and engineering precision·········································································2-1
4) Oil seal type······················································································································································2-2
5) Holding brake ···················································································································································2-3
6) Degree of decrease rating for R2AA Motor, depending on with or without oil seal/brake·······························2-3
2.2 Motor encoder······················································································································································2-4
1) Serial encoder ··················································································································································2-4
2) Pulse encoder ··················································································································································2-4
3) Battery specification ·········································································································································2-5
2.3 Servo amplifier·····················································································································································2-6
1) Common specification······································································································································2-6
2) Input command, position output signal, general-purpose input signal, and general-purpose output signal ···2-7
2.4 Power supply and amount of heat generation······································································································2-9
1) Input current of main circuit power supply and control power supply ·······························································2-9
2) Inrush current and leakage current···················································································································2-9
3) Amount of heat generation·······························································································································2-9
2.5 Cautions on load················································································································································2-10
1) Restrictions on acceleration time, deceleration time,and effective torque·····················································2-10
2) Negative load ·················································································································································2-10
3) Load inertia moment·······································································································································2-10
2.6 Position signal output········································································································································· 2-11
1) Positions signals by serial signals ·················································································································· 2-11
2) Binary code output format and transfer period ·······························································································2-12
3) ASCII decimal code output format and transfer period···················································································2-13
4) Position signal output from pulse signal ·········································································································2-14
2.7 Specifications for analog monitor ·······················································································································2-15
2.8 Specifications for dynamic brake························································································································2-16
1) Allowable frequency, instantaneous tolerance, decreasing the rotation angle of the dynamic brake···········2-16
3. Installation
3.1 Installation·································································································································································3-1
1) Servo amplifier························································································································································3-1
2) Unpacking·······························································································································································3-2
3) Installation direction and position····························································································································3-3
4) Conditions on layout in control cabinet····················································································································3-3
5) Cooling conditions···················································································································································3-4
3.2 Servo motor······························································································································································3-5
1) Precautions·····························································································································································3-5
2) Unpacking·······························································································································································3-5
3) Installation·······························································································································································3-5
4) Installation·······························································································································································3-6
5) Water and dust proofing··········································································································································3-6
6) Protective cover placement·····································································································································3-7
7) Gear installation and co-assembly with mating machine·························································································3-7
8) Allowable load for bearing·······································································································································3-9
9) Cable installation and its related cautions·············································································································3-10

4. Wiring
4.1 Wiring of main circuit power supply, control power supply, servomotor, and protective grounding. ··························4-1
1) Name and function··················································································································································4-1
2) Electrical wire··························································································································································4-1
3) Wire diameter - allowable current ···························································································································4-1
4) Terminal layout of connector CNA and CNB ···········································································································4-2
5) Recommended wire diameter and cable length······································································································4-3
6) Example of wiring····················································································································································4-4
4.2 Wiring connection diagram to host equipment··········································································································4-5
1) Name and pin number of signal CN1A and CN1B (wiring connection to host equipment)······································4-5
2) Layout of connector CN1-A·····································································································································4-6
3) Name and its function of signal CN1-A ···················································································································4-6
4) Connection circuit of terminal CN1-A······················································································································4-7
5) Layout of connector CN1-B·····································································································································4-9
6) Signal name and its function···································································································································4-9
7) Terminal connection circuit····································································································································4-10
4.3 Wiring of motor encoder ·········································································································································4-12
1) Name and function of connector CN2···················································································································4-12
2) Terminal number on servo amplifier side···············································································································4-13
3) Recommended specification of encoder cable······································································································4-14
4) Encoder cable length ············································································································································4-14
5) Layout of terminal of connector for battery············································································································4-14
5. Operation
5.1 How to change servo motor to be combined··········································································································5-1
1) Change and verify servo motor with use of setup software··················································································5-1
5.2 System parameters················································································································································5-2
1) Specification confirmation·····································································································································5-2
2) System parameters list·········································································································································5-4
3) Confirmation and settings of system parameters··································································································5-4
4) Change and verify system parameters (settings for motor encoder specification)················································5-6
5) Default set values at factory·································································································································5-9
5.3 Test operation·······················································································································································5-10
1) Confirmation of installation and wiring················································································································5-10
2) Confirmation of movement ·································································································································5-10
3) Confirmation of input-output signal····················································································································· 5-11
4) Confirmation of device operation························································································································5-12
5.4 Servo amplifier status display·······························································································································5-13
1) Default display····················································································································································5-13
2) Alarm display······················································································································································5-13
3) Control power input display································································································································5-13
5.5 Operation sequence·············································································································································5-14
1) Operational sequence from power-on through power-off in standard setting at factory······································5-14
2) Stop sequence when alarm activated·················································································································5-16
3) Sequence when alarm reset·······························································································································5-19
4) Sequence when power is turned OFF during operation (during servo ON)························································5-20
5.6 Monitor function····················································································································································5-21
1) Monitor function··················································································································································5-21
2) Description of monitor·········································································································································5-22
5.7 Analog monitor and digital monitor·······················································································································5-26
5.8 Setting of parameters···········································································································································5-27
1) Parameters list ···················································································································································5-27
5.9 Parameter functions·············································································································································5-33
5.10 Control block diagram ········································································································································5-87
6. Adjustment
6.1 Servo tuning functions and basic adjustment procedure ··························································································6-1
1) Servo tuning functions·············································································································································6-1
2) Selection of tuning method······································································································································6-2
6.2 Automatic Tuning······················································································································································6-3
1) Parameters for use in automatic tuning.··················································································································6-3
2) Parameters automatically adjusted during automatic tuning···················································································6-6
3) Adjustable parameters when auto-tuning in progress ·····························································································6-6
4) Unstable functions during auto-tuning·····················································································································6-7
5) Auto-Tuning Characteristic selection flowchart········································································································6-8
6) Adjustment method for auto-tuning ·························································································································6-9

7) Monitoring servo gain adjustment parameters······································································································6-10
8) Manual tuning method using auto-tuning results···································································································6-10
6.3 Automatic tuning of notch filter································································································································ 6-11
1) Operation method··········································································································································· 6-11
2) Parameters to be set······································································································································ 6-11
6.4 Automatic tuning of FF vibration suppression frequency ························································································6-12
1) Operation method···········································································································································6-12
2) Parameters to be set······································································································································6-12
6.5 Use of manual tuning··············································································································································6-13
1) Servo system configuration and servo adjustment parameter ··············································································6-13
2) Basic manual tuning method for velocity control···································································································6-15
3) Basic manual tuning method for position control···································································································6-15
6.6 Model-following control···········································································································································6-16
1) Automatic tuning method of model-following control·····························································································6-16
2) Manual tuning method of model-following control·································································································6-17
6.7 Tuning to suppress vibration···································································································································6-18
1) FF vibration suppression control···························································································································6-18
2) Model-following and vibration suppression control································································································6-18
3) Tuning method ······················································································································································6-20
6.8 Use of disturbance observer functions····················································································································6-21
7. Maintenance
7.1 Troubleshooting························································································································································7-1
7.2 Warning and alarm list··············································································································································7-3
1) Warning list ·····························································································································································7-3
2) Alarm List································································································································································7-4
7.3 Troubleshooting when alarm activated ·····················································································································7-7
7.4 Encoder-clear and alarm-reset procedure ··············································································································7-22
1) Motor encoder model············································································································································7-22
2) Alarm code activated·············································································································································7-22
7.5 Inspection ·······························································································································································7-24
1) Items to be checked and corrective actions for operation error·············································································7-24
7.6 Service parts···························································································································································7-25
1) Parts to be inspected······································································································································7-25
2) Motor encoder battery replacement ······················································································································7-25
8. Fully-closed control
8.1 Illustration of system configuration····························································································································8-1
8.2 Internal block diagram ··············································································································································8-2
8.3 Wiring 8-4
1) Connector name and its function·····························································································································8-4
2) Terminal numbers on servo amplifier side···············································································································8-6
8.4 Fully closed control-related parameters····················································································································8-7
1) System parameter setting·······································································································································8-7
2) Servo motor rotation direction setting······················································································································8-8
3) External encoder resolution setting·························································································································8-9
4) Digital filter setting···················································································································································8-9
5) Encoder output pulse signal····································································································································8-9
8.5 Remarks ·································································································································································8-10
1) Timing to power-on external pulse encoder ··········································································································8-10
2) Operation of external pulse encoder·····················································································································8-10
9 Selection
9.1 Servo motor volume selection 9-1
1) Servo motor capacity selection flowchart················································································································9-1
2) Create operation pattern.········································································································································9-2
3) Calculate motor axis-converted load inertia moment (JL).······················································································9-2
4) Calculate motor axis-converted load torque (TL).···································································································9-3
5) Calculate acceleration torque (Ta).··························································································································9-5
6) Calculate deceleration torque (Tb).·························································································································9-5
7) Calculate effective torque (Trms).···························································································································9-5
8) Judgment condition (determination condition)·········································································································9-5
9.2 Remarks on regeneration ·········································································································································9-6
1) Calculation of regenerative energy EM···················································································································9-6
2) Coping process for regenerative energy·················································································································9-8

9.3 Specification for regenerative unit···························································································································9-10
1) Specification··························································································································································9-10
2) Internal block diagram···········································································································································9-10
3) Regenerative unit front view·································································································································· 9-11
4) Connection diagram of regenerative unit ··············································································································9-12
5) Calculation of regenerative effective electrical power ···························································································9-14
10. Appendix
10.1 Conformance to standards····································································································································10-1
1) Conformance to standards····································································································································10-1
2) Overvoltage category, Ingress Protection code, and degree of contamination······················································10-1
3) Connection and installation···································································································································10-2
4) UL-file number ······················································································································································10-2
10.2 Conformance to EU Directive ·······························································································································10-3
1) Conformity verification test····································································································································10-3
2) EMC installation requirements ······························································································································10-4
10.3 Outline dimensional drawing of servo motor·········································································································10-5
10.4 Servo motor data sheet·········································································································································10-6
1) Characteristics······················································································································································10-6
2) Velocity-torque characteristic································································································································10-7
3) Rating decrease rate of motor with oil seal···········································································································10-7
4) Overload characteristics········································································································································10-8
10.5 Outline dimensional drawing of servo amplifier·····································································································10-9
10.6 Optional items·····················································································································································10-10
1) Regenerative unit, RF1BB (A) 00························································································································10-10
2) Analog monitor box ············································································································································· 10-11
3) Connecting cable ················································································································································10-12
4) External regenerative resistor·····························································································································10-15
5) Lithium battery ····················································································································································10-16

No Text on This Page.

1
1
1. Preface
1.1 Introduction ................................................................................................................................................................1-1
1) Changes and additions to AC Servo amplifier SANMOTION R (previous model) ......................................................1-1
1.2 Instruction Manual .....................................................................................................................................................1-2
1) Contents.....................................................................................................................................................................1-2
2) Precautions on this manual ........................................................................................................................................1-2
1.3 Illustration of System Components..........................................................................................................................1-3
1.4 Model number structure ............................................................................................................................................1-4
1) Model number of servo motor.....................................................................................................................................1-4
2) Model numbers of servo amplifier (abbreviated model numbers)...............................................................................1-5
1.5 Part names..................................................................................................................................................................1-6
1) Servo amplifier............................................................................................................................................................1-6
2) Servo motor................................................................................................................................................................1-7

1.Preface Introduction
1-1
1.1 Introduction
AC servo amplifier “SANMOTION R ADVANCED MODEL low voltage-input type” is a small and one
axis servo amplifier with 2 kinds of capacities, to which main circuit power DC48V<24V> and control
power DC5V are input as external power supply. This model corresponds to rotary motor “series R,”
and both serial encoder and pulse encoder are available. Also, this can correspond to external pulse
encoder for fully closed system. Batteries for motor encoder can be installed in encoder cables. We
achieved decrease in volume having great advantage over AC-input servo amplifier by decreasing
voltage and down sizing of main circuit part, this can achieve down sizing in servo system
1) Changes and additions to AC Servo amplifier SANMOTION R (previous model)
The followings are differences between this model and the other SANYO DENKI products, such as
“SANMOTION series R (AC100/200V-input).”
■ DC-power input and down-sized
Down-sized and DC-power input type (main circuit DC48V <24V>, control circuit DC5V)servo
amplifier.
■ Placement of input power supply unit and overcurrent protection device
Input power supply for main power (DC48V <24V>) and control power (DC5V) of the servo
amplifier is designed to useAC/DC power (switching power supply). No fuses are built in input
sections of main and control power supply of the servo amplifier, so please place fuses or
breakers in power supply system from AC power down to servo amplifier input sections for the
purpose of overcurrent protection. (This servo amplifier is UL-approved under the condition
that fuses are placed in input sections. Refer to section 10 for global standards.)
■ Regenerative unit (optional)
Main circuit voltage may increase due to regenerative energies, depending on combined motor,
operation conditions, servo amplifier connection conditions. Regenerative circuit is not built in
servo amplifier. We can offer an optional regenerative unit for absorbing voltage.
■ Only available on pulse input mode
Control mode is position control mode only. Command is pulse input position command only.
Please note that analog velocity command, torque command, and torque limit command is not
available.
■ Analog monitor
Analog monitoring function to monitor servo amplifier & motor operation is not built in this servo
amplifier. You can monitor by connecting external monitor box.
■ Digital operator
Digital operator is not built in this model, such as built in our AC servo amplifier “SANMOTION
R” and “SANMOTION RADVANCED MODEL.”
■ Safe torque-off function
Safe torque-off function is not built in this model.
■ Setup software
Setup software of “SANMOTION R ADVANCED MODEL” can be used as it is. (Except for
multiple-drop function to monitor multiple axes servo amplifier status.) Make sure not to
disconnect the control power supply, when writing parameters via setup software.
■ Cautions on wiring length
Main circuit power and control power supply are intended to be input from commonly used
AC/DC converter.
When wiring length from power supply to servo amplifier is relatively long, the voltage might
drop due to cable impedance, and this may cause motor torque decrease and control circuit
error. Please perform wiring with use of thick cable and minimal-length as much as possible, so
as not to let any voltage drops occur.

1. Preface How to use operating manual
1-2
1.2 Instruction Manual
This manual describes specification, installation, wiring, operation, functions, maintenance of AC servo
amplifier “SANMOTION R ADVANCED MODEL, low voltage-input type” as in the following order:
The figures in parentheses for main circuit voltage described in this manual are the values when the
voltage is DC24V.
1) Contents
■ “Section 1, Preface”
Describes product outline, model number structure, and each part name.
■ “Section 2, Specification”
Describes detailed specifications for “servo motor,” “motor encoder,” and “servo amplifier.”
■ “Section 3, Installation”
Describes installation method of product.
■ “Section 4, Wiring”
Describes wiring method of product.
■ “Section 5, Operation”
Describes operating sequence, test operation method, parameters.
■ “Section 6, Adjustment”
Describes automatic tuning and manual servo tuning.
■ “Section 7, Maintenance”
Describes probable causes and corrective actions when alarm activated, and maintenances.
■ “Section 8, Fully closed control”
Describes fully closed control and its usage.
■ “Section 9, Selection”
Describes selecting method of servo motor capacity, regenerative energy and its coping
measures.
■ “Section 10, Appendix”
Describes overseas standard, servo motor data sheet, and outline dimensional drawing.
2) Precautions on this manual
Thoroughly read this manual prior to use the product to fulfill and correctly use functions of the product.
After thoroughly reading this manual, keep it handy for reference when needed. Fully observe safety
instructions described in this manual. Please note that we cannot guarantee the safety when you use
the product in any usages other than the specified usages in this operating manual. Figures in this
manual are partially schematic illustrations or abstractions. Contents of this manual are subject to
change without notice depending on product version upgrade or any additions. Any changes shall be
made only by revising this manual. We make assurance doubly sure on the contents of this manual,
however, in the event that any suspicions, errors, or erroneous omissions, please contact our sales
branch near you or head office indicated in the back of this manual.
1.2 Instruction
Manual

1.Preface Systemconfiguration
1-3
Servo motor
Use this for servo motor
with brake. Please be
advised the power supply is
user-prepared item.
Power supply to
release brake
Motor encoder
Motor input
Setup software
This can set parameters
and monitor by
communicating with PC.
Host equipment
SANMOTION R ADVANCED MODEL
(Low voltage-input type)
Direct current DC48V <24V>
Direct current DC5V
Power input
Regenerative unit
(An option)
Install this for the possibility
of regenerative energies
and DC voltage increase,
depending on driving motor
and operating conditions.
1.3 Illustration of System Components
The folowing shows an example of system configulation.

1. Preface Model number of servo motor
1-4
1.4 Model number structure
1) Model number of servo motor
R 2 GA 04 003 F X P 00
Decreasing rating may be needed for the model with oil seal and brake.
Refer to “Section 2.1.6, Degree of decrease rating for R2AA Motor, depending on with or without oil seal/brake.”
■ Motor encoder
◆ Serial encoder
Model Resolution within 1
rotation Resolution within
multiple rotations Name Transmission format
PA035S 131072(17bit) -
Absolute
encoder for
incremental
system
Half-duplex
start/stop
synchronization
2.5Mbps (standard)
PA035C 131072(17bit) 65536(16bit) Battery backup
method absolute
encoder
Half-duplex
start/stop
synchronization
2.5Mbps (standard)
RA035C 131072(17bit) 65536(16bit) Battery less
absolute
encoder
Half-duplex
start/stop
synchronization
2.5Mbps (standard)
◆ Pulse Encoder
Model Resolution within 1 rotation Motor flange
angle Name
PP031 1000/2000/2048/4096/5000/6000/8
192/10000 (P/R) 40mm or over Wire-saving incremental
encoder
✔ Please contact us on combinations with servo motors.
Flange size
04・・・40mm
06・・・60mm
Maximum rev velocity
F・・・・6000min-1
D・・・・5000min-1
(4500min-1)
Encoder type
H・・・Absolute encoder for incremental system
P・・・Battery backup method absolute encoder
W・・・Battery less absolute encoder
Servo motor type
2・・・Medium
Power-supply
voltage
GA・・・DC48V-motor
Series R
Rated output
003・・・30W 005・・・50W 008・・・80W
010・・・100W 020・・・200W
Holding brake
X・・・Without brake
B・・・With brake (90V)
C・・・With brake (24V)
Specification identification
00・・・Standard
01・・・With oil seal

1. Preface Model number of servo amplifier
1-5
2) Model numbers of servo amplifier (abbreviated model numbers)
RF2 G 21 A 0 A 00
✔ Set value for servo amplifier is set to “standard set value” at factory.
✔ User needs to changes “combination setting of servo amplifier and motor,” “system
parameters,” and “general parameters” that shall be tailored to user equipment.
✔ Please be advised that user shall perform settings as tailored to system you use by referring
to the following sections.
◆ “Section 5-1, Setting change of servomotor combination”
◆ “Section 5-2, System parameters”
◆ “Section 5-2, Standard set value at factory”
◆ “Section 5-8, Parameter setting”
✔ Standard model servo amplifier is not available for “fully-closed system.” Please contact us
when you consider using.
✔ RF2 servo amplifier does not support “safe torque off function.”
✔ Output circuit of RF2 servo amplifier is exclusive for NPN (sink) output, not available for PNP
(source) output.
Servo amplifier size
11・・・Small-sized
21・・・Large-sized
Input voltage current
G・・・DC48V
H・・・DC24V
Series RF2
Servo motor type
A・・・Rotary motor
Motor encoder type
0・・・Serial encoder
8・・・Pulse encoder
Interface type
A・・・Pulse input, NPN (sink) output
Separate
specification
00・・・Standard
01・・・no DB
Other manuals for Sanmotion R
3
Table of contents
Other Sanyo Denki Controllers manuals
Popular Controllers manuals by other brands
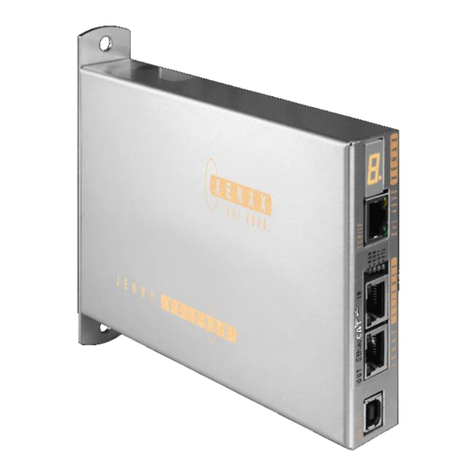
Jenny Science
Jenny Science XENAX Xvi 75V8S instruction manual
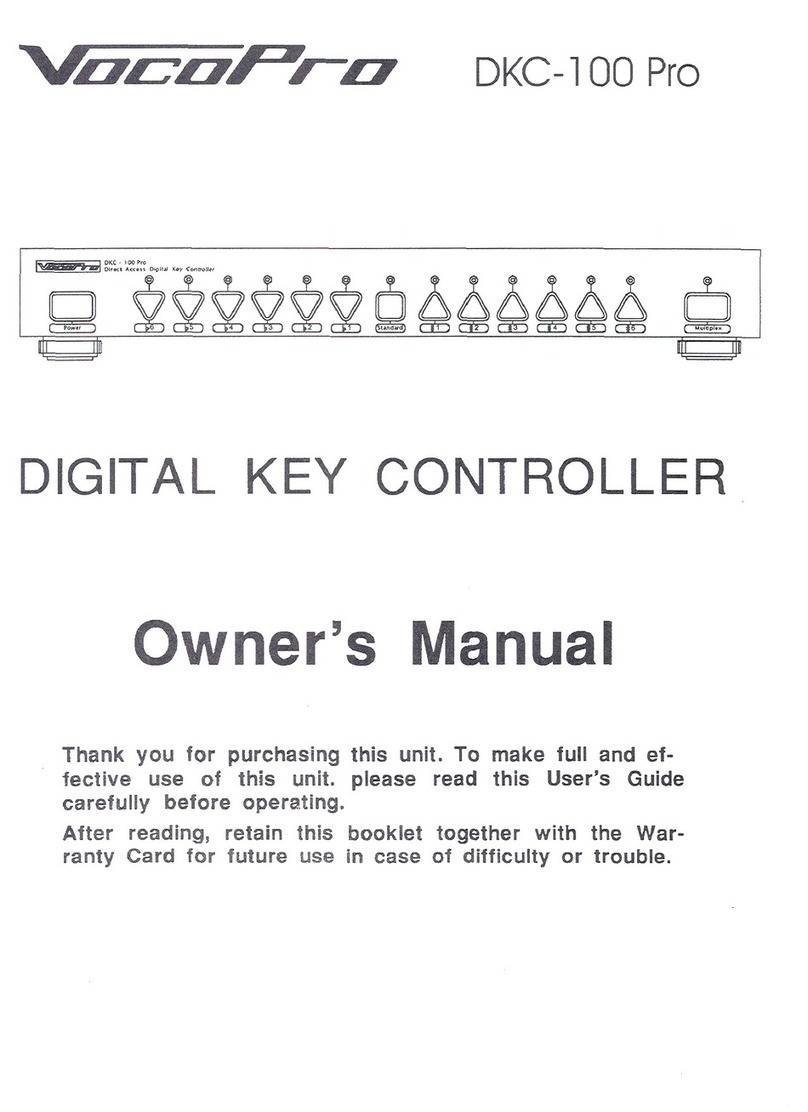
VocoPro
VocoPro DKC-100 PRO user guide

DH Instruments
DH Instruments PPC1 - RACK MOUNT KIT Rack Mounting instructions
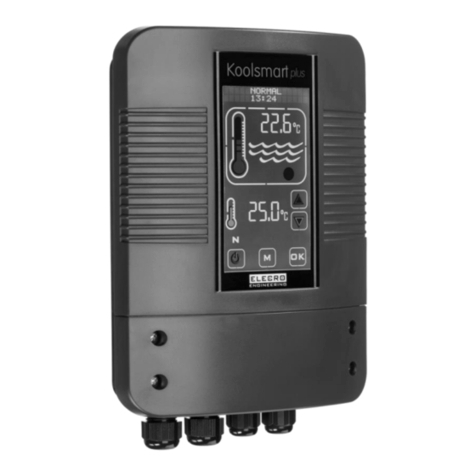
Elecro Engineering
Elecro Engineering Koolsmart PLUS Installation & operating manual
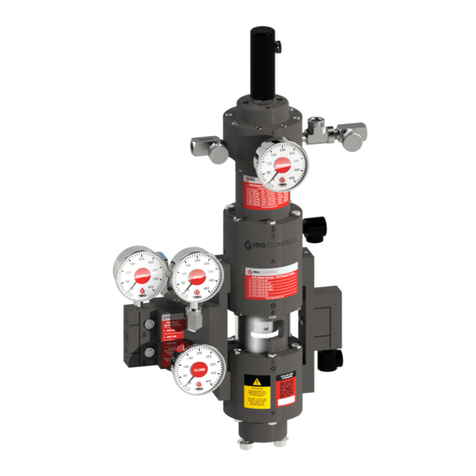
VRG Controls
VRG Controls VPC SN Series instruction manual
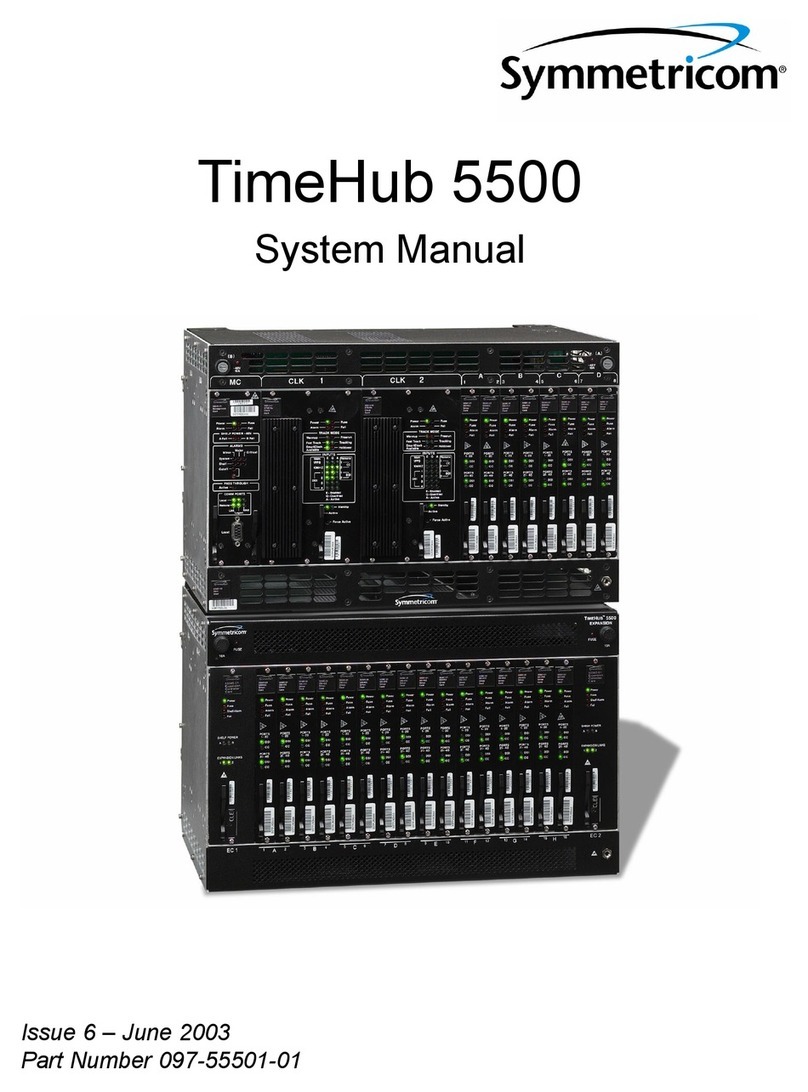
Symmetricom
Symmetricom TimeHub 5500 System manual