Scantool COMPACT 110 Operation and maintenance manual

Industrivej 3-9, 9460 Brovst, Denmark
Tel.: +45 98 26 60 88 - Fax: +45 98 23 61 44
E-mail info@scantool-group.dk - Website www.scantoool-group.com
SAFETY INSTRUCTIONS
AND OPERATOR’S MANUAL
FOR DRILLING MACHINE
C
CO
OM
MP
PA
AC
CT
T
1
11
10
0

COMPACT 110
COMPACT 110 Operator’s manual for drilling machine
- 2 -
TABLE OF CONTENTS
I. SAFETY INSTRUCTION ............................................................................................................ - 3 -
1. General information .................................................................................................................... - 3 -
2. Important safety instruction......................................................................................................... - 3 -
II. OPERATING INSTRUCTIONS................................................................................................... - 5 -
1. Cutters and optional equipment features.................................................................................... - 5 -
2. Magnetic drilling machine start up .............................................................................................. - 8 -
3. Machine start-up ....................................................................................................................... - 16 -
III. MAINTENANCE AND SERVICE...............................................................................................- 17 -
IV. TECHNICAL DATA ................................................................................................................... - 19 -
V. ELECTRICAL DIAGRAM.......................................................................................................... - 23 -
VI. DRAWINGS AND SPARE PARTS LISTS ................................................................................ - 25 -
VII. EC DECLARATION OF CONFORMITY ................................................................................... - 37 -
BEFORE YOU START WORK WITH THE MACHINE,
PLEASE READ THESE INSTRUCTIONS CAREFULLY
AND USE ALL RECOMMENDATIONS.

COMPACT 110
COMPACT 110 Operator’s manual for drilling machine
- 3 -
I. SAFETY INSTRUCTION
Portable Drilling Machine on electromagnetic base should be used consistent with
their purpose. Inconsistent use may cause a danger for human beings and operating
machine.
1. General information
Portable drilling machines with electromagnetic bases are fast becoming very universal
power tools not only at steel fabricating workshops or steel building sites but also at every
factory maintenance workshop, truck manufacture & repair company, military equipment
service, onboard ship maintenance shop etc. where the size of machined components
cannot benefit from large stationary drills and diameters of holes made prevent of using
classic hand drills.
Electromagnetic drilling base provides safe machine fixing to steel construction with the
strength ensures correct operation of drilling machine as well as User safety. This way of
fixing the machine makes possible of making holes in various work positions for example
vertical steel columns or steel floors as well.
In these working positions all Portable Magnetic Drilling Machines made by Promotech
must be secured with the safety chain in case of the potential danger of power supply loss.
THIS MACHINE IS MADE IN EUROPE
2. Important safety instruction
Drilling machine must not be used when:
1. The operator has not read the Operator’s Manual.
2. The work to be done is not in agreement with the recommendations in this Manual.
3. Drilling machine is not complete or has been repaired with non-original parts.
4. Power supply parameters do not conform to those stated on the motor’s plate.
5. Machines operator has not checked condition of the drilling machine, condition of
power cable, control panel or cutter.
6. Power supply socket is not equipped with a protection circuit.
7. Machine is not secured with safety chain as a protection from falling down especially
when used at heights or in vertical or upside-down positions.
8. Bystanders are present in the immediate vicinity of machine.
Warning!
Read and save all instruction for future reference!

COMPACT 110
COMPACT 110 Operator’s manual for drilling machine
- 4 -
9. Before attempting to work with the machine check condition of electrics including
power cord and plug.
10. The drilling machine should be connected to an installation equipped with protection
circuit (neutral or ground) and protected with a 16 A fuse for 220V and 32 A fuse for
120V. When used on building sites, it must be supplied through a separation
transformer made in the second class of protection
11. Machine can be used outdoors, but is not weatherproof. Do not expose to rain, snow
or frost.
12. Machine should not be used on: rusty surfaces, steel plates with thick covered with
paint, uneven surfaces, next to a welding machine.
13. In all cases always use a safety chain/strap /see drawing 1/. The safety chain mustn't
be loose! To avoid this situation the safety chain should be wrapped around the
element it is hooked to.
It’s recommended to use the safety chain following the pictures
14. Do not use the machine in explosion hazard zones.
15. Do not start work if the machine has excessive play on guide slides.
16. Always wear safety goggles and ear protection.
17. Do not remove metal chips with bare hands.
18. Do not touch the spindle and the cutter during work.
Do not touch or replace the tool with power source on – while
electromagnetic base is being used.
Drawing No 1 The safety chain application

COMPACT 110
COMPACT 110 Operator’s manual for drilling machine
- 5 -
19. Tools must be fastened firmly. When a milling cutter is used, check before start of
work if tool holding screws are screwed tight.
20. It is not permitted to use blunt of damaged tools.
21. Do not use milling cutter without pilots, and arbors without ejection spring.
22. Use tools recommended in Operator’s Manual only.
23. After use always clean drilling machine from metal chips and coolant.
24. Always unplug machine from power supply during any work on the machine.
25. In the case that the machine falls on a hard surface, from a height, is wet or is
subjected to other unfortunate events that could affect its technical state - work
should be terminated immediately and the machine should be sent to service for
inspection as soon as possible.
It is not allowed to use drill on steel thinner than (less than 3/8”
(10 mm)). On thin steel (less than 3/8” (10 mm)) magnet’s adhesive power
would be significantly reduced what can cause machines failure or
individuals injury. The machine should be located on the work piece with
the entire surface of the electromagnetic base! It is recommended that each
time, before positioning the machine surface under the electromagnetic
base should be sanded down with abrasive paper!
Thickness lower than 5mm: Magnetic drilling machine COMPACT 110
won’t start because of CLAMPING FORCE CONTROL SYSTEM (see point 2.6).
Warning!
Read and save all instruction for future reference!
II. OPERATING INSTRUCTIONS
1. Cutters and optional equipment features

COMPACT 110
COMPACT 110 Operator’s manual for drilling machine
- 6 -
The drilling machine has a spindle with Morse Taper MT4 to use twist drill (by using
the reduction adapter if necessary) and annular cutters. Arbor mark AMT is mounted in
spindle conical taper to fix annular cutters.
Milling cutter (2) is located inside arbor body (1) and is fastened with screws (3). While
fastening the cutter in the socket, be aware that screws should be screwed tight so that they
could not come unscrewed. It is important to position the cutter in relation to the socket in
such a way that fixing flats on the cutter shank are positioned opposite to the fixing screws
(3). Both fastening screws (3) should be used to fasten the cutter. Pilot (5) is located inside
the cutter. It makes it easier to position milling cutter over centre of a planned hole. During
drilling as the cutter goes deep into steel, the pilot moves back into the arbor body and
tightens discharge spring (4). That spring ejects slug which is a by-product of milling a hole
with a centre free cutter [Drawing No.3].
1.1 Installing and uninstalling the arbor
The arbor installation and uninstallation should be carried out when the machine
is turned off and disconnected from the power grid!
Drawing No.3
Types of holes that can be done with a milling cutter
Drawing No 2.
Principle of milling cutter’s work

COMPACT 110
COMPACT 110 Operator’s manual for drilling machine
- 7 -
Installing the arbor:
a) Rice the guard (2) to the maximum,
b) Clean the inside of the spindle using a cotton cloth,
c) Before mounting, clean off the lubricant from the new arbor (3),
d) Place the arbor with the fin on top, and place it in the spindle,
e) By turning the arbor, align the fin to the appropriate slot in the spindle,
f) Using a light impact from the bottom side, drive the arbor into the spindle.
Uninstalling the arbor:
a) Raise the guard, turn the spindle so that the wedge MT opening in the spindle (1) is lined
up with the wedge MT opening in the reducer body,
b) Place the wedge MT (included as standard equipment) into the uncovered spindle
opening (1),
c) Hold down the arbor (3) with one hand,
d) Strike the wedge MT with a hammer, taking care to not to damage the arbor,
e) Carefully remove the arbor from the socket in the spindle,
f) Remove the wedge MT.
1.2 Installing and uninstalling the milling cutter
Milling cutter installation and uninstallation should be carried out when the
machine is turned off and disconnected from the power grid!

COMPACT 110
COMPACT 110 Operator’s manual for drilling machine
- 8 -
Installing the milling cutter:
1. Raise the drive and the slide (2) up using the lever (3);
2. Raise the guard (1) to the maximum in order to attain access to the arbor (4) screws (5);
3. Insert the appropriate type of pilot (6) into the milling cutter (7);
4. Position the milling cutter (7) with the cutter facing up, so that the flat sides of the milling
cutter are found facing the screws (5)
5. Put the milling cutter (7) into the arbor socket (4);
6. Tighten the screws securely (5).
Uninstalling the milling cutter:
1. Raise the drive and the slide (2) up using the lever (3);
2. Raise the guard (1) to the maximum in order to attain access to the arbor (4) screws (5).
3. Loosen the screws (5);
4. Remove the milling cutter (7) and the pilot (6) from the arbor socket (4).
2. Magnetic drilling machine start up
The machine is supplied in a metal box with complete standard equipment.
COMPACT 110 comes in a standard equipment set which consists of:
•metal box
1pc
•drilling machine
1pc

COMPACT 110
COMPACT 110 Operator’s manual for drilling machine
- 9 -
•
arbor AMT4-U-19 4-3
1pc
•cooling system
1pc
•chip guard
1pc
•spoke handles
3pcs
•Hex. Wrench s=2,5
1pc
•Hex. Wrench s=4
1pc
•Hex. Wrench s=5
1pc
•Hex. Wrench s=6
1pc
•8 mm flat wrench
1pc
•wedge, MT4
1pc
•safety chain with snap hook
1pc
•operator’s manual
1pc
2.1 Before first drill:
•steel elements of the drilling machine are protected for transit and storing with grease
film. Before first start up of the machine all grease should be removed
•before each use all handles should be screwed into pinion.
2.2 Before setting the machine on an item make sure that:
- substrate is a steel and ferromagnetic (some of stainless steel or acid-proof or do not
conduct the magnetic flux);
-thickness of work piece is at least 3/8” (10 mm)
-surface of steel under the magnet is flat
-wipe, brush or sand down clean surface where you intended to place the drilling machine,
so that you remove rust, paint, dirt etc which would reduce adhesive power of the
electromagnetic base.
2.3 Preparation the machine for drilling
1. Set the drilling machine on the surface of the element which hole is to be drilled.
2. Accurately and securely attach the drill spindle in the nest (see II, point 1)
3. Plug in the drilling machine accordance to the requirements (see I point 2)
4. Set the axis of the spindle exactly over the place of drilling (the tool is over the centre of
the hole)
5. Turn the magnetic base ON
Prior to use!
Always make sure that the electromagnetic machine is secured from falling
down during vertical, ceiling work with original chain (as described in
paragraph I point 2 “Important rules of safe use of drilling machine”)
2.4 Cutting

COMPACT 110
COMPACT 110 Operator’s manual for drilling machine
- 10 -
1. Fill cooling reservoir with cooling/lubricating fluid.
Select the right speed for the tool you intend to use (see the speeds chart in this manual
– paragraph IV no.1).
Cooling and lubricant fluid commercially available in concentrated are recommended to
use for cooling twist drill and annular cutter.
It’s allowed to use of emulsions formed from a mixture of water and drilling oil.
Do not use clean water as the liquid cooling and lubricant.
The cooling system is an integral part of the machine and should always be used.
2. Check working of cooling system. Open coolant reservoir’s tap and apply pressure on the
pilot by turning spokes counter clockwise. As the pilot starts to sink into the cutter cooling
liquid should start to run down cutters inner wall. If there is no liquid flowing down check if
the tap is fully opened. It may take a few seconds for cooling liquid to fill the whole
system. (see point 2.8)
3. Turn the motor on.
WARNING: The cooling system can only be used when drilling machine is in
vertical position. In other positions additional external source of cooling
should be used, for example: a coolant bottle with a long nozzle.
4. Start the engine by button „I” on the control panel (see II point 3).Drilling in the material
must be conducted with sensitivity.
5. Some of magnetic drilling machines have a built-in overload system. Overload is
indicated by red LED diod on the control panel. Further increasing the engine load
causes the activation of the overload system and power source loss. It’s possible to
continue the drilling operation by pressing the “O” MOTOR switch to reset the system and
restart the engine. Periodic, uncommon illumination of LED’s diod during the drilling
process is normal. This means that the drilling process is used in a maximum extent
permissible engine capacity.
6. Making a hole with a milling cutter should ideally be done in one pass. It makes the cutter
work better and easier to eject the slug after the hole is completed.
WARNING: when the milling cutter goes through the material the slug can be
pushed out often with considerable strength. Pay attention to avoid injury.
7. Due to safety work should not be allowed to do the formation of chips too long or to do
the winding on the handle or drill.
8. After a hole is made the cutter should be withdrawn back and both the motor and the
electromagnet should be switched OFF.
9. When work with the machine is finished the power cord should be disconnected from the
power source, the machine should be cleaned up from chips, and coolant etc. The cutter
should be removed and cleaned.

COMPACT 110
COMPACT 110 Operator’s manual for drilling machine
- 11 -
10. The tool should be removed from drill chuck before inserting to the toolbox.
2.5 Types of a ground material
As shown on the graphs [Drawing 4] magnetic clamping force of the electromagnetic
base to the ferromagnetic ground depends on its magnetic properties. Steel with increased
carbon content and some other alloying ingredients has lower magnetic permeability, what
causes a decrease in the clamping force. Also a thickness of a work piece, on which the drill
is placed, is significant.
Maximum clamping force of the electromagnetic base to a 5 mm thick work piece
surface is only about 25% of a clamping force obtained from a smooth, plane, 22 mm
thick standard plate.
If such thin ground material does not bow, one can try to carry out drilling of a
hole, although with keeping the strictest precautions. Particularly a magnitude of a
pushing force on a feed handle should be very limited.
Appropriate rpm should be adjusted depending on if drilling would be carried out with
a drill bit, or with trepan type metal cutter and a metal cutter’s diameter. A drive is equipped
in mechanical 4-step reducing gearbox. A general dependence between drilling diameter and
drilling speed is shown in graphs [drawing 5], detailed guide is supplied by manufacturer of
used drilling tools. The graph is just a general guide and the shown dependence applies to
average structural steel.
Cooling agent is fed gravitationally from a coolant bottle through an arbor to an inside
of the metal cutter. For on-a-wall and on-a-ceiling positions special cooling pastes have to be
used.
2.6Electromagnetic base clamping force control system
This system for security reasons is an integral part of each drill type PRO. It works by
constant monitoring of the electromagnetic force base adhesion value to the substrate. In the
case of fall the force value below to guarantee safe operation of the machine, the system
automatically switches off the drive drill. It also does not allow to enable drive which does not
guarantee the proper clamping force.
Clamping force depends on: type and thickness of substrate, thick coatings on the
substrate, rust or other contaminants, lack of flatness of the substrate, excessive roughness
of the surface,excessive wear of the lower part of the electromagnetic base.
If there’s a problem to enable drive after turn on of the electromagnetic base so drive
works only after START button is pressed, and after release the drive is off - it means that
system works properly. The system didn’t allow to for further work due to insufficient
clamping force drills.
2.7 Working in difficult areas

COMPACT 110
COMPACT 110 Operator’s manual for drilling machine
- 12 -
While working in difficult access areas as well as left-handed operator, there’s a
possibility to change location of the pinion with spoke handles to the other side of drilling
machine.

COMPACT 110
COMPACT 110 Operator’s manual for drilling machine
- 13 -
Drawing 4. Clamping force depending on the thickness of the substrate and the value gap.

COMPACT 110
COMPACT 110 Operator’s manual for drilling machine
- 14 -

COMPACT 110
COMPACT 110 Operator’s manual for drilling machine
- 15 -
2.8 Installing and uninstalling the cooling system
Installing the cooling system:
a) Place the machine in the vertical position,
b) Slide the drive and the slider (1) up using lever (2),
c) Coolant bracket (7) with cooling unit (6) on screws (8) located to the side of the slider,
d) Connect the cooling conduit ending (3) with the coolant coupling (4) found in the cooling
ring (5).
Before starting the machine:
•Remove the bottle’s cap,
•Fill it with cooling lubricant,
•Replace bottle cap.
After fulfilling the above actions and making sure, that the system has been appropriately
fixed, and the cooling conduit (2) is placed correctly on the coolant coupling (4), the bottle
cap should be loosened by 1/3 of a turn in order to deaereate it, turn on the valve (3), so that
liquid travels to the hose, after which the machine can be started (see II pt. 3)
After ending work, one must remember to tighten the bottle cap and turn off the valve
(9) (to prevent liquid from leaking during the time that the machine is not being used) and
uninstall the cooling system (6) before placing the machine in the box.
Uninstalling the cooling system:
a) Place the machine in the vertical position,
b) Slide the drive and the slider (1) up using lever (2),
c) Disconnect the cooling conduit ending (3) and the coolant coupling (4) found in the
cooling ring (5).
d) Take off the cooling system.
2.9 Canceling clearance

COMPACT 110
COMPACT 110 Operator’s manual for drilling machine
- 16 -
The drive and the slider can be slid up and down smoothly using the lever (1), making
the screws (2) fixing the strip to the drill body visible through the openings in the slider (5). To
loosen screws (2), the slider should be placed in such a position (using levers) so that the
openings make the screws visible. After loosening the screws slide the slider up and down
several times so that the pressure strip aligns itself and cancels clearance.
After carrying out these activities and canceling clearance, tighten screws (2) starting
from the middle screw. The slider should be located symmetrically relative to the middle
screw. Next, tighten the neighboring screws (2) moving the slider in the degree necessary for
making them visible.
Then, tighten screws (3) until any noticeable resistance is felt. When the screw in this
position and blocked with a hexagonal key, tighten counter nut (4). The screws (3) counteract
the machining force and protect the pressure strip from shifting during operation.
3. Machine start-up
In order to start the machine press the main switch MAGNET (01) on “I” button. By
pressing green button (02) MOTOR on “I” start the motor.
Canceling clearance

COMPACT 110
COMPACT 110 Operator’s manual for drilling machine
- 17 -
a) Stopping the motor is executed with red button „O” (02) (the motor is switched OFF but
the electromagnetic base is still ON) (02).
b) Blinking of the red LED overload indicator (03) means that the machine is working at the
limit of the overload. The machine can be automatically turned off at any time.
c) To change the rpm speeds machine use the shift lever (04)
To move machine into next drilling spot, stop the motor as described above then
push switch MAGNET into the position “O”.
III. MAINTENANCE AND SERVICE
To avoid accidents drill stand, power cable, wiring, plug connectors, switches must be
regularly inspected for damage.
Perform adjustment of the machine play guides every 50 hours or as necessary
performed by the regulation screws. Slide guide loose is correct if the drive can be
moved smoothly by using the lever. It’s not accepted to automatically slide down
under its own weight. (see II point 2.9)
Due to the distribution of lubricant after every days work position of gear lever (used
for selection of gearbox speed) should be changed. For example if machine worked
with 150 rpm speed, it should be switched to 300rpm. (see IV point.1).
Every 250 hours of work check condition of carbon brushes. If their length is less than
5 mm they should be replaced for original new ones. After replacement new brushes
should be run-in without load for about 20 min. Other repair work should be done only
by authorized service points, appointed by distributor. Replacement of brushes is
possible without removal motor unit from the unit. (see IV)
Lubricate regularly brass slide guide inserts with grease as well as the rack and
pinion.
Drawing No.6 Control Panel
Drawing No.7 View of the machine COMPACT
110
(01)
(03)
(02)

COMPACT 110
COMPACT 110 Operator’s manual for drilling machine
- 18 -
To prevent the machine from rusting (especially when used outdoors or ) all steel
parts should be covered with thin layer of grease film
Damaged machine parts to be exchanged only to original parts.
New spare parts order: required to enter the code or send the damage part with
information about type of drilling machine and power supply.
Caution:
In the case that the machine falls on a hard surface,
from a height, is wet or is subjected to other unfortunate events
that could affect its technical state - work should be terminated
immediately and the machine should be sent to service for
inspection as soon as possible.

COMPACT 110
COMPACT 110 Operator’s manual for drilling machine
- 19 -
IV. TECHNICAL DATA
Power supply
□
110÷120V AC / 50-60 Hz
□220÷240V AC / 50-60 Hz
Power required
□
110÷120V - 1700 W
□220÷240V - 1800 W
Motor power
□
110÷120V - 1550 W
□220÷240V - 1650 W
Tool holder
Morse Taper No 4
Max. twist drill diameter
16-47 mm (5/8” ÷ 1 7/8”)
Max. annular drill diameter
12-110 mm (1/2” ÷ 4 5/16”)
Max. milling depth
76 mm (3”)
Insulation Class
I
Standard adhesive force of electromagnet
(for steel 7/8” (22 mm) thick and Ra < 1,25)
22 000 N
Slide stroke
230 mm
Machine speeds /under load/
I – 85 min -1 , II – 135 min -1
III – 160 min
-1
, IV – 250 min
-1
Electromagnetic base
120x240x63 mm
Length of the power cord
3,0 m
Total weight
31 kg
Noise level
85 dB
Surrounding temperature
0 ÷ 40° C

COMPACT 110
COMPACT 110 Operator’s manual for drilling machine
- 20 -
Using the drill on the electromagnetic base COMPACT 110 with special annular
cutters we are capable of drilling and reaming holes up to 110mm diameter and 76mm depth
with a precision achievable previously only in a workshop.
Replacement of motor brushes:
For the COMPACT 110 drill, the state of the carbon brushes should be monitored every
100 working hours.
Replacement of motor brushes should take place when the machine is turned off and
the power cable is disconnected from the power grid!
1. Unscrew 4 M5x40 engine cover screws (1), using a 6-kt s=4 wrench.
2. Carefully take off the engine cover (3). Remember that it is connected with the motor by a
grounding lead (4).
3. Take off the motor brushes from the connector (6) using the flat ending (5) of the lead.
The ending has a safeguard against its sliding down – first, press the protruding element
at the middle of the ending, then carefully slide off the ending from the connector.
4. Push aside the spring arm (7) pressing down the brush and rest it on the surface of the
brush holder (8) and remove the brush (9).
5. Inspect brush length - if the length is less than 5mm, the brush should be replaced with
an original brush.
6. Carry out all actions in reverse, in order to install the engine.
After replacement, new brushes should be Grinded in for about 20 minutes on idle gear.
Replacement of engine brushes is possible without removing the drive from the drill.
Table of contents
Other Scantool Drill manuals
Popular Drill manuals by other brands
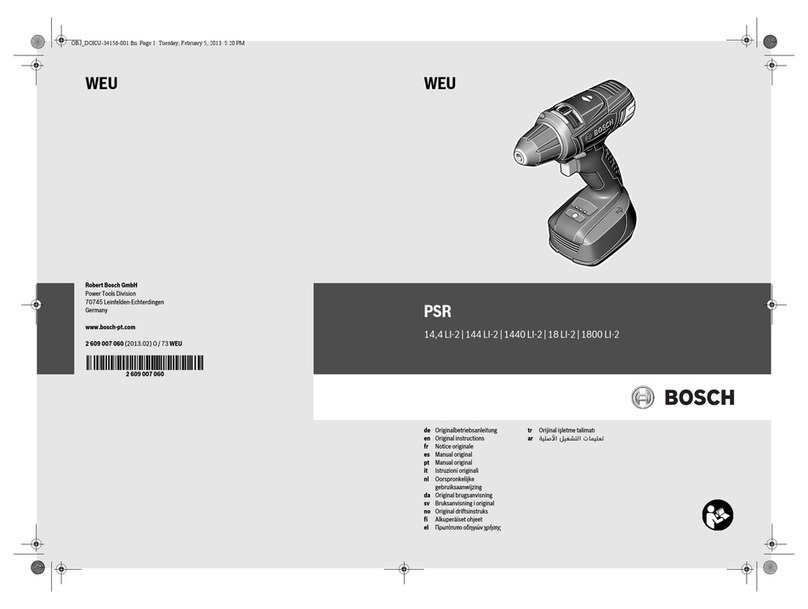
Bosch
Bosch WEU PSR Original instructions
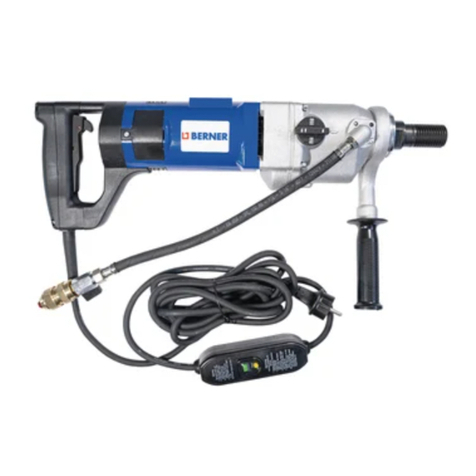
Berner
Berner BDIADW 2200-202 Safety and users manual
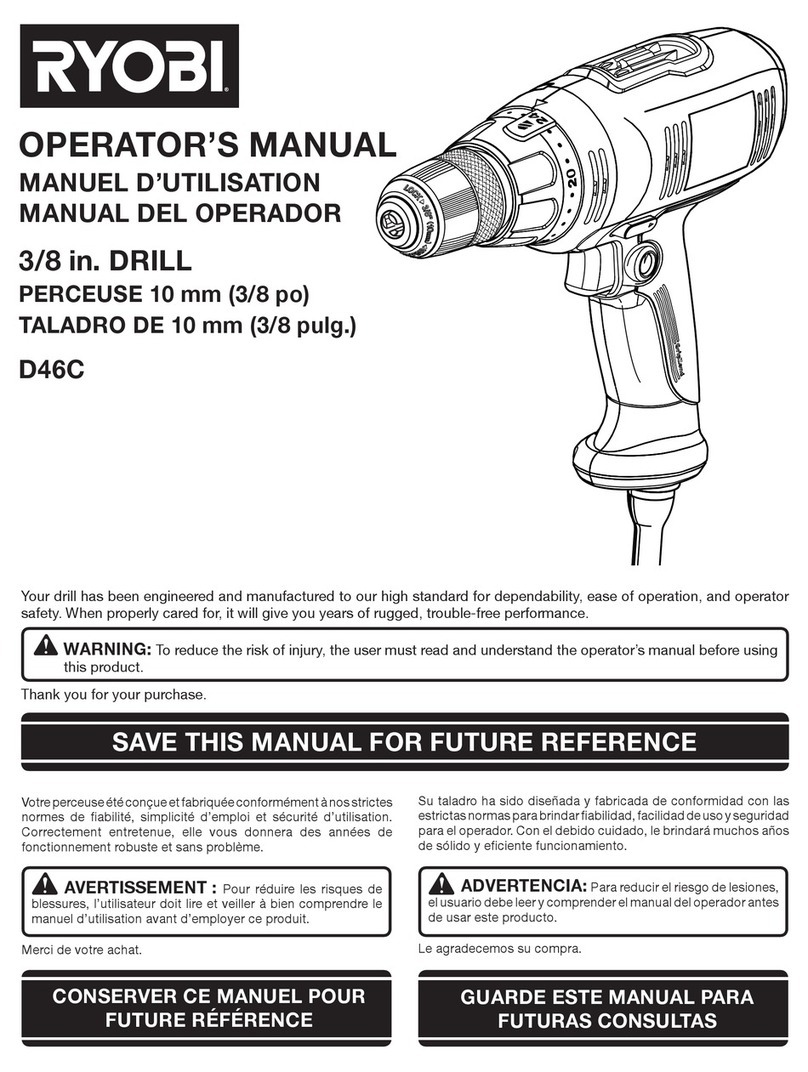
Ryobi
Ryobi D46C Operator's manual
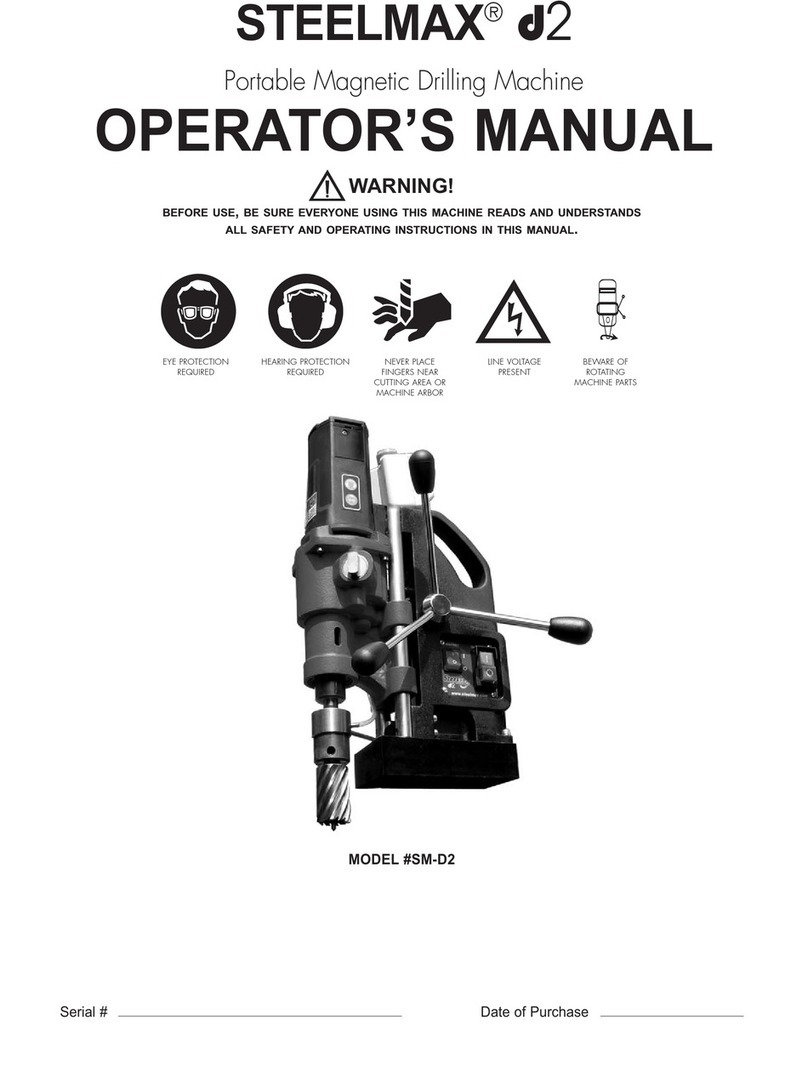
Rockies Global Marketing
Rockies Global Marketing SteelMax D2 Operator's manual

Hitachi
Hitachi D 10VH Safety instructions and instruction manual

Milwaukee
Milwaukee LOK-TOR II Operator's manual