Schaeffler ProLink CMS User manual

1
Schaeffler ProLink CMS
User manual

2
Schaeffler Monitoring Services GmbH
Kaiserstraße 100
52134 Herzogenrath
Germany
Telephone: +49 (0) 2407 9149 66
Fax: +49 (0) 2407 9149 59
Email: industrial-services@schaeffler.com
Webside: www.schaeffler.com/services
All rights reserved.
No part of the documentation or software may be reproduced in any form or processed, duplicated or distributed using
electronic systems without our written consent. We would like to point out that the designations and brand names of the
various companies used in the documentation are generally protected by trademark, brand and patent laws.
Microsoft, Windows and Microsoft Edge are brands or registered trademarks of the Microsoft Corporation in the USA and/or
in other countries. Google Chrome™ is a trademark of Google.
The software uses the following third-party provider libraries under their respective licences:
base, binutils, burnin, busybox, clinfo, cmake, crypto, curl, dhcp, dropbear, expat, gcc-host, gdb, gettext, glibc, gmp-host,
i2ctools, gsoap, gwt, imx-gpu-viv, kexec-tools, keys, kiss_fft, kmod, libtirpc, libunwind, linux, linuxptp, log4cpp, lzo, mbedtls,
memstat, memtester, mtd-utils, ncurses, odhcp6c, open62541, openssl, paho-mqtt-embedded-c, perfmon, popt, protobuf,
readline, rescue_tools, rsync, sqlite, strace, tar, u-boot, ua-nodeset, udev, util-linux, zlib
Full licence conditions for the respective libraries can be found in the software's program directory.
Version 1.0.0
Translation of the original user guide.
© 17/06/2020 - Schaeffler Monitoring Services GmbH
Imprint

3
Contents
Contents
.................................................................................................................................................... 41 General
.............................................................................................................................................................................................. 41.1 Safety inform ation
.............................................................................................................................................................................................. 41.2 Hazard symbols and signal w ords
.............................................................................................................................................................................................. 51.3 About this guide
.................................................................................................................................................... 62 Product description
.............................................................................................................................................................................................. 62.1 Intended use
.............................................................................................................................................................................................. 72.2 Modifications by the user
.............................................................................................................................................................................................. 72.3 Technical data
.............................................................................................................................................................................................. 92.4 Scope of delivery
.................................................................................................................................................... 103 Commissioning the base system
.................................................................................................................................................... 134 Installing the ProLink modules
.............................................................................................................................................................................................. 134.1 Installation details of the ProLink m odules
.............................................................................................................................................................................................. 144.2 Dim ensions of the ProLink m odules
.............................................................................................................................................................................................. 154.3 Mounting modules
.................................................................................................................................................... 175 Layout, connections and fittings
.............................................................................................................................................................................................. 175.1 Overview of how to connect and set up the device
.............................................................................................................................................................................................. 185.2 Connection details
.............................................................................................................................................................................................. 215.3 Connecting modules via internal Ethernet netw ork
.............................................................................................................................................................................................. 225.4 Inputs and outputs of the vibration m odule
.................................................................................................................................................................................. 22Connecting the analogue inputs of the vibration module 5.4.1
.................................................................................................................................................................................. 23Connecting the digital inputs of the vibration module 5.4.2
.................................................................................................................................................................................. 25Connecting the digital sw itching outputs of the vibration module 5.4.3
.............................................................................................................................................................................................. 275.5 Connecting the pow er supply
.............................................................................................................................................................................................. 285.6 Connecting the com puter via Ethernet
.................................................................................................................................................... 296 Operation and controls of the ProLink system
.............................................................................................................................................................................................. 316.1 Reset button
.............................................................................................................................................................................................. 316.2 Teach button
.................................................................................................................................................... 327 Further information
.................................................................................................................................................... 348 Maintenance and repair
.................................................................................................................................................... 359 Decommissioning and disposal
.................................................................................................................................................... 3610 Manufacturer/support
.................................................................................................................................................... 3711 Appendix
.........................................................................................................................................................0Index

4
1 General
1.1 Safety information
The Schaeffler ProLink condition monitoring system is manufactured in accordance with the recognised standards
and guidelines (see Declaration of Conformity) and is safe to operate. Nevertheless, the device can pose unavoidable
residual hazards to users and third parties or to property, therefore it is imperative that all of the safety information
provided in this guide is observed. The generally applicable safety and accident prevention regulations must also be
taken into account. Failure to do so may result in the health and life of persons being put at risk, or cause damage
to property. The safety information in this guide applies in the Federal Republic of Germany. In other countries, the
relevant national regulations apply.
According to its intended use, the Schaeffler ProLink device is not subject to EC Machine
Directive 2006/42/EC.
This guide differentiates between
·
General safety information, which applies to the whole guide and is listed in this chapter
and
·
Specialised safety information, which you will find in each chapter, either at the start or accompanying
individual actions
General safety information
Schaeffler ProLink is integrated in a machine as a system for permanent machine monitoring. The system must be
installed in the machine, connected to machine components and operated in the machine in line with the
specifications set out in this guide (see Technical data ). The machine owner is responsible for installing the
device properly and for ensuring safe operation in the machine as a whole.
In addition to recording measured values, it is also possible to transfer characteristic values or alarms to superordinate
control systems via the Schaeffler ProLink outputs. In doing so, the limitations of use for the connected machine
components must also be observed, in addition to the Schaeffler ProLink specification. The machine owner bears
sole responsibility for this.
The ProLink device must not be used for safety-relevant tasks or for critical switching
operations! This applies in particular when these tasks or switching operations have health
and safety implications.
Operating personnel
Schaeffler ProLink may only be installed, operated and maintained by authorised qualified specialists who have
received training in accordance with the applicable, relevant regulations.
1.2 Hazard symbols and signal words
Hazard symbols used in this guide
Safety information and warnings are identified by specific, standardised hazard symbols. If no specific symbol applies,
a general hazard symbol is used.
General hazard symbol
DANGER
Specifies the nature and source of the hazard
Explains actions to prevent the hazard.
7

5
General
Specific hazard symbols
DANGER
DANGER FROM ELECTRICAL CURRENT!
This symbol indicates a danger from electric shock that can cause personal injury or even
death, or damage to property.
Signal words used in this guide
Signal words indicate the severity of the hazard that occurs if the actions to reduce the hazard are not taken.
·
Caution: Minor damage to property may occur.
·
Warning: Minor personal injury or severe damage to property may occur.
·
Danger: Personal injury may occur. There is a risk of fatal injury in particularly severe cases.
1.3 About this guide
This guide describes the installation and use of the ProLink device and contains important information about using
the device safely and correctly. Please read
through this guide carefully before commissioning the device, and keep it for future reference.
Make sure that
·
This guide is available to all users of the device.
·
If the product is passed on to other users, that this guide is also passed on with it.
·
Additions and amendments provided by the manufacturer are always attached to this guide.
Further information
In addition to the device described in this guide, the Schaeffler ProLink condition monitoring system also includes
the integrated Schaeffler SmartWeb software, which is dealt with in a separate manual.
To operate the Schaeffler ProLink device, you will also need the supplied Schaeffler SmartUtility Light software. This
is also dealt with in a separate manual. You also have the option of purchasing the Schaeffler SmartUtility software,
which features enhanced functionality.
Definitions
·
Product: The Schaeffler ProLink device described in this manual.
·
User: person or organisation capable of putting the product into operation and using it.
·
Qualified person: a person who, by virtue of their relevant training and experience, is qualified to identify risks and
avoid potential hazards that may be caused by the operation or maintenance of a product.
Symbols used
This symbol indicates
·
Helpful additional information and
·
device settings or practical tips that will help you to perform activities more efficiently.
Cross-reference symbol : This symbol refers to a page in the manual that provides further information. If you are
reading the manual in PDF format on a screen, clicking the word to the left of the cross-reference symbol will take
you straight to the section in question.
5

6
2 Product description
About the Schaeffler ProLink system
ProLink is a condition monitoring system for permanent frequency selective monitoring of plants. It consists of a
processor module (CPU) and at least one vibration module (Vibration). The system can be extended to a maximum
of 4 vibration modules. Up to 4 analogue and 2 digital signals can be connected per vibration module and measured
values can be logged, recorded and analysed. After the analysis, the system can switch up to 4 digital outputs per
vibration module depending on user-defined alarm limits and report the state to an external control system, for
example.
The ProLink device can be used to cover a wide range of applications; the ProLink device can be configured to
meet your own requirements using the integrated Schaeffler SmartW eb software. There, the connected modules
with their inputs and outputs are automatically created with default configurations and can then be adapted to your
system. The ProLink device is administered using the software Schaeffler SmartUtility Light or optionally Schaeffler
SmartUtility.
With ProLink, the Schaeffler offers status monitoring that is optimised to suit your requirements.
2.1 Intended use
The ProLink system is intended exclusively for the following functions:
•Connection of the processor module (CPU) to a maximum of 4 vibration modules (Vibration)
•Connection of input signals according to the technical specification of the respective input
•Connection of output signals according to the technical specification of the respective output
•Connection of the processor module to the PC via Ethernet
•Use of the software that is approved for the Schaeffler ProLink device
The ProLink device must not be used to switch safety-relevant applications.
The ProLink device with all connected modules may be operated only within the limitations of use as specified under
Technical data .
Measured-value analyses and changes to settings may only be made using the supplied Schaeffler SmartUtility Light
software, the optional Schaeffler SmartUtility software or the integrated Schaeffler SmartWeb software.
Any other use or use beyond this shall be considered improper and the user shall bear all associated risk. The user is
responsible for the intended use of the device. This also includes observing these instructions.
7

7
Product description
2.2 Modifications by the user
The user must not make any modifications to the ProLink device. The user may only make settings on the device
itself or via the Schaeffler SmartWeb or Schaeffler SmartUtility Light/Schaeffler SmartUtility software.
The user bears responsibility for any further modifications! Should you detect a fault with your ProLink device, please
contact our Support team.
2.3 Technical data
The ProLink device must not be used in measurement voltage categories II, III or IV!
Processor module (CPU)
General
Housing
Material: PA (polyamide)
Colour: RAL 7035
Flammability class according to UL 94: V0
Fixing
Installation on 35-mm standard mounting rail
Mounting rail height: 7.5 mm
Installed on a flat mounting surface
Power consumption
800 mA
Power supply
18–30 VDC
Typical: 24 VDC
Humidity
80%
Operating altitude
<3000 m
Ambient temperature
Operation: -30 to +60°C
Storage: -30 to +55°C
Dimensions
75 mm x 139.5 mm x 120 mm (W x H x D)
Weight
600 g
Protection type
IP 20
Operating system
Embedded Linux
Software
Schaeffler SmartWeb:
·
Device-own web interface
·
Recommended browser: Google Chrome
·
Configuration of the device and the measurement jobs, initial data analysis
Schaeffler SmartUtility Light:
·
Administration of the device
Schaeffler SmartUtility (optional and chargeable):
·
Administration of the device
·
Detailed analysis of the measurement data
Schaeffler SmartVisual (optional and chargeable):
·
Plant visualisation
Memory
8 GB eMMC Flash
2 GB DDR3 RAM
Certifications
CE
Interfaces
Control elements
1 button to start learning mode
1 Reset button
1 USB button, intended for future functions
Display elements
1 Status LED
1 Link LED
1 Alarm LED
1 USB Status LED
Details of the functions can be found in the section Operation and controls .
29

8
Communication
Ethernet 1000 Mb/s
RJ45
Connections
1 Ethernet 1000 Mb/s
1 USB A, intended for future functions
1 USB B, intended for future functions
1 interface for fieldbus communication, intended for future functions
1 RJ45 (internal Schaeffler module communication)
1 Ethernet 100 Mb/s for communication between the Schaeffler ProLink modules
1 power supply
Communication protocols
·
WebServices
·
SLMP
·
OPC/UA (only with additional licence)
·
MQTT (only with additional licence)
·
Email (only with additional licence)
Measurement jobs and characteristic values
Measurement jobs
- Base configuration
- Roller bearing
- Journal bearing
- Pump
- Fan
- Classification (optional and chargeable)
- Coupling
- Gear stage
- Belt drive
- Shaft
- Condition guard
- Tracked frequency bands
- User-defined frequency bands
The user is guided through the configuration step-by-step with the help of a wizard. Depending
on the selected measurement job, all necessary characteristic values for frequency selective
monitoring are automatically created.
Characteristic values
(time range and frequency
range)
Defined characteristic values:
- DIN/ISO 10816
Calculated characteristic values:
- RMS
- Frequency selective RMS
- Direct component
- Peak
- Peak2peak
- Crest factor
- Wellhausen counter
- Condition guard
Other user-defined characteristic values are possible.
Vibration module (Vibration)
General
Housing
Material: PA (polyamide)
Colour: RAL 7035
Flammability class according to UL 94: V0
Fixing
Installation on 35-mm standard mounting rail
Mounting rail height: 7.5 mm
Installed on a flat mounting surface
Power consumption
400 mA
Power supply
18–30 VDC
Typical: 24 VDC
Humidity
80%
Operating altitude
<3000 m
Ambient temperature
Operation: -30 to +60°C
Storage: -30 to +55°C
Dimensions
50 mm x 139.5 mm x 120 mm (W x H x D)
Weight
320 g

9
Product description
Protection type
IP 20
Certifications
CE
Interfaces
Control elements
1 Reset button
Display elements
1 Status LED
2 Link LEDs
4 LEDs for analogue inputs
2 LEDs for digital inputs
4 LEDs for digital outputs
Details of the functions can be found in the section Operation and controls .
Connections
2 RJ45 (internal ProLink communication)
1 Ethernet 100 Mb/s for communication between the Schaeffler ProLink modules
1 power supply
Inputs
4 analogue inputs
Measuring range: +/-10 V
Sample rate: 51.2 kHz
Resolution: 24 bits
DC bandwidth: 0 Hz - 20 kHz
AC bandwidth: 0.1 Hz - 20 kHz
IEPE bandwidth: 0.1 Hz - 20 kHz
Maximum number of FFT lines: 12800
2 digital inputs
Measuring range: 0-24 VDC, 0.1 Hz - 50 kHz
A/B coded (speed and direction)
Sensor supply: 24 VDC, 100 mA
Maximum current consumption per sensor when powered by the device: 25 mA at 24 VDC
Outputs
4 switching outputs
Open collector, max. 25 mA, reaction time 1 ms
Subject to technical modifications!
2.4 Scope of delivery
Scope of delivery
·
ProLink starter kit consisting of a processor module (CPU) with integrated software Schaeffler SmartWeb and a
vibration module (Vibration)
·
Per vibration module: One jumper for power supply and one jumper for Ethernet
·
Quick start guides for processor module and vibration module
·
Software Schaeffler SmartUtility Light for download on the Schaeffler homepage
·
User documentation ProLink, Schaeffler SmartWeb and Schaeffler SmartUtility Light for download on the
Schaeffler homepage
Optional accessories
An extensive range of optional accessories is available for the ProLink system from Schaeffler Monitoring Services
GmbH. Please contact your local Schaeffler contact person.
29

10
3 Commissioning the base system
·
The ProLink device may be maintained only by persons who are verifiably qualified to do so
in accordance with the relevant rules and regulations.
·
Ensure that the ProLink device is de-energised while work is being carried out.
You can start and become familiar with a fully functional basic version of the ProLink system with the components of
the scope of delivery and up to 4 IEPE acceleration sensors. The following steps are required:
·
Step 1: Install the device
·
Step 2: Connect acceleration sensors to analogue inputs
·
Step 3: Connect the computer to the processor module
·
Step 4: Configure analogue inputs on IEPE sensors
Details about these steps can be found in the following.
Step 1: Install the device
1. Before installing, turn off the power supply to the ProLink system.
2. Connect the DC power supply to the power supply connection on the processor module.
3. Connect the power supply connection of the processor module to the power supply connection of the
vibration module using the jumper supplied.
4. Connect the processor module to the vibration module using the jumper supplied to enable communication
between the modules.
Step 2: Connect IEPE acceleration sensors
Connect up to 4 analogue IEPE acceleration sensors to the analogue inputs of the vibration module :
9
10
10
11
11
27
21
22

11
Commissioning the base system
The pin assignment appears as follows:
Analogue input
Input 1/2/3/4
GND
GND
Shield FE
Analogue input 1
13
14
15
16
Analogue input 2
17
18
19
20
Analogue input 3
37
38
39
40
Analogue input 4
41
42
43
44
You must enable the IEPE sensor type in the Schaeffler SmartW eb software for IEPE
acceleration sensors. This is described in step 4.
Step 3: Connect the computer to the processor module
·
The default IP address of the ProLink system is 192.168.1.100.
·
You can also run the ProLink system on a network. The IP address can then be provided
via a DHCP server and the time via an NTP server. Please contact your system
administrator if you experience problems with the network settings. More information can
also be found in the SmartWeb manual.
1. Turn on the power to the ProLink system.
2. Set the IP address of your computer to 192.168.1.xxx.
For xxx, 100 is excluded - this address is reserved for the ProLink system.
3. Connect your computer to the ProLink system using a LAN cable. You can establish a connection directly with a
network cable or using a switch.
4. Open your browser. W e recommend Google Chrome.
5. Enter the IP address 192.168.1.100 in the address line of the browser. The device's own software SmartWeb
opens.
Step 4: Configure analogue inputs on IEPE sensors
The connected analogue inputs of the ProLink device are automatically created and preconfigured in the Schaeffler
SmartWeb software.
For IEPE acceleration sensors, you must adapt the automatically created input as follows:

12
1. Open the Configuration > Input configurations > ProLink vibration module (Serial number) >
Acceleration sensor 1-4 area.
2. Click the Edit button for the corresponding analogue input.
The twelve-digit number (e.g. F4:3D:80:12:00:00) is the serial number of the vibration module. You can also find
this number on the outside of the module.
3. In the Edit input configuration dialogue, set the Sensor type to IEPE. Adjust the sensor sensitivity as
indicated in the calibration data sheet of the sensor. You may also need to adjust the Min. and Max. bias
voltage. This is used to detect a defective sensor or cable.
For each analogue input with IEPE acceleration sensor, the sensor type must be adjusted
separately in the Schaeffler SmartWeb software.
The ProLink system is now ready for use. Further details of the possible settings can be found in the Schaeffler
SmartWeb user documentation.

13
Installing the ProLink modules
4 Installing the ProLink modules
Important details about installing the ProLink device can be found in the following sections.
·
The ProLink device may be maintained only by persons who are verifiably qualified to do so
in accordance with the relevant rules and regulations.
·
Ensure that the ProLink device is de-energised while work is being carried out.
4.1 Installation details of the ProLink modules
Installation site
Install the ProLink device at the installation site on a grounded mounting rail. W hen doing so, make sure that all of
the environmental conditions for operation are adhered to, good ventilation is ensured for cooling, and all
components are easily accessible for maintenance purposes.
Installation material
When installing the ProLink device, note the following:
·
Details about the mounting rail
Width: 35 mm
·
Securing clips
To secure the ProLink device to the side of the mounting rail, you need two suitable securing clips. The securing
clips are not included in the scope of delivery.
·
Cross-head screwdriver or flat-head screwdriver
You need cross-head and flat-head screwdrivers in order to join the connections.
If you are installing the device in a location with constant vibrations, e.g. on a ship, you can
also use spring terminals instead of screw terminals. Further information is available from our
support team.
Environmental conditions at the installation site
Note the following environmental conditions for the ProLink system:
·
Observe the technical specifications for ambient temperature and humidity.
·
Avoid the following installation sites:
§
Locations where condensation accumulates due to sudden temperature changes
§
Locations with easily flammable gases
§
Locations with a high level of conductive dust (iron filings, oil mist, mist, salt vapours or organic solvents)
§
Locations with direct sunlight
§
Locations with strong magnetic fields or high voltage fields
§
Locations at which powerful sound waves and shock waves can make their way directly into the ProLink
system.
Position
To ensure good ventilation and to make it easier to maintain/service the device, the following minimum distances
should be adhered to:
·
Distance of the modules to the upper, lower and side wall: 50 mm
·
Distance of the modules to the front wall or the switch cabinet door: 60 mm
From an ambient temperature of 50°C, please increase the distance between the individual
modules to ensure good air circulation.
7

14
4.2 Dimensions of the ProLink modules
The following illustrations show the modules of the ProLink device from different perspectives with dimensions
accurate to the millimetre.
Basic dimensions of the processor module
From the front, you can see the processor module buttons, connections and LED indicators, as well as the power
supply connection that points upwards. The 35-mm recess for the mounting rail can be seen in the side view.
Basic dimensions of the vibration module
From the front, you can see the vibration module LED indicators, as well as the connections for inputs, outputs and
power supply that point upwards and downwards. The 35-mm recess for the mounting rail can be seen in the side
view.

15
Installing the ProLink modules
4.3 Mounting modules
DANGER
Switch off the power supply
Before performing any installation and connection activities, ensure that the power supply to
the ProLink system is switched off, including external power sources.
Earthing
Functional earth is a low impedance current path between circuits and earth that is not intended as a protective
measure but, for example, to improve interference immunity.
The modules have a FE spring (metal clamp) at the bottom of their electronic sockets, which provides an electrical
connection to the mounting rail. Connect the mounting rail to the protective earth via earth terminals. This means
that the modules are also earthed when they are snapped onto the mounting rail.
If failures occur at the sensor signals, please connect the shield of the sensors to the FE terminal of the
corresponding sensor connector on the ProLink device.
The functional earth FE is only used to discharge interference. It does not serve as
protection against accidental contact for persons.
Installation of the ProLink modules
The ProLink system is set up by connecting the individual modules. You do not need any tools.
Proceed as follows to install the modules of the ProLink device on the mounting rail:
1. Place the module slightly tilted with the top edge of the mounting rail recess on the mounting rail (A).
2. Push the module down onto the mounting rail until it clicks into place (B):
3. Attach end brackets on both sides of the ProLink system to secure the system to the mounting rail.
You can now set up and connect the modules of the ProLink device.
17

16
To remove the modules of the ProLink device from the mounting rail, proceed as follows:
1. Insert a screwdriver at the bottom edge of the module and lever upwards (A and B).
2. Another lever movement (C) is used to release the anchoring of the module in the
mounting rail.
3. Lift the module upwards from the mounting rail (D):

17
Layout, connections and fittings
5 Layout, connections and fittings
You can use the connections on the ProLink device to
·
Connect the individual modules to each other ,
·
Set up inputs and outputs and various connection configurations
·
Set up a PC/Ethernet connection and
·
Connect the power supply .
To set up and operate the ProLink device, you will need the following connection cables - these are not included in
the standard scope of delivery:
·
Cable for Ethernet connection between processor module and PC
·
Power supply cable
·
Cable to connect the inputs and outputs to the vibration module
·
The ProLink device may be maintained only by persons who are verifiably qualified to do so
in accordance with the relevant rules and regulations.
·
Ensure that the ProLink device is de-energised while work is being carried out.
General
Please note the following information when connecting cables:
·
Ensure that the sockets for the plug connections are clean and free of contamination. Dirt or moisture in plug
connections can impair signal quality.
·
When securing cables, ensure that they are not subjected to any mechanical strain. If necessary, fit strain relief
accessories.
·
Observe the minimum permissible bending radii for the cables. These can be found in the data sheets from the
cable manufacturer.
·
Attach the cables in such a way that they are laid firmly and cannot be knocked.
·
Do not lay signal cables parallel to high-power lines.
5.1 Overview of how to connect and set up the device
To use the functions and connections of the ProLink device, proceed as follows:
1. Install the processor module and the vibration module or vibration modules of the ProLink in the desired location.
You can operate up to 4 vibration modules with one processor module.
2. Connect the modules to each other .
3. Provide the appropriate accessories for the connections you want to use on the vibration module of the ProLink
device and connect the signals. You can find details on the various connection options in the following sections:
§
Connecting analogue inputs
§
Connecting digital inputs
§
Connecting digital outputs
4. Connect the power supply .
5. Establish the network connection and start the Schaeffler SmartWeb software. The inputs and outputs of
the vibration module are preconfigured there by default. You can customise these configurations for your
system environment.
6. When you have put the ProLink device into operation, the device goes through a test sequence. The controls
of the ProLink device are then available.
In the event of a power failure, the ProLink device has a buffer that continues to power the
internal clock for 14 days. Alternatively, you can use a DHCP server and provide the time
using an NTP server. Please contact your system administrator if you experience problems
with the network settings. More information can also be found in the SmartWeb manual.
Important notes that must be observed when connecting can be found in the section Connection notes.
21
18
28
19
21
22
23
25
27
28
29

18
Details about the pin assignment of the individual connections can be found in the section Connection details .
Information about getting started with the Schaeffler SmartWeb software can be found in the section Further
information . For details on working with the Schaeffler SmartW eb software, refer to the SmartW eb manual.
5.2 Connection details
The ProLink processor module has the following connections:
·
PC/Ethernet connection LAN (front)
·
Power supply (top)
·
Connection to vibration module (top)
The ProLink vibration module has the following connections:
·
Power supply (top)
·
Network connection to neighbouring modules (top)
·
Analogue inputs (top and bottom)
·
Digital inputs (top and bottom)
·
Digital switching outputs (bottom)
18
32
28
19
21
19
21
19
20
20

19
Layout, connections and fittings
Connection overview
The following graphic shows a detailed wiring diagram for all connection options of the ProLink vibration module:
Power supply
The power supply is accessible on each module via the corresponding supply terminal at the top.
The pin assignment appears as follows:
Pin no.
Signal
1
24 VDC
2
0 V
3
24 VDC
4
0 V
Analogue inputs
The 4 analogue inputs are accessible via the corresponding supply terminals at the top and bottom of the vibration
module.
The pin assignment appears as follows:

20
Analogue input
Input 1/2/3/4
GND
GND
Shield FE
Analogue input 1
13
14
15
16
Analogue input 2
17
18
19
20
Analogue input 3
37
38
39
40
Analogue input 4
41
42
43
44
GND has the same potential. Shield FE has a conductive connection to the mounting rail.
The mounting rail should have a conductive connection to the switch cabinet; the switch
cabinet should be grounded.
We recommend that the shield of the sensor is first clamped to FE (usually connected to PE
via the mounting rail).
Digital inputs
The 2 digital inputs are accessible via the corresponding supply terminals at the top and bottom of the vibration
module.
The pin assignment appears as follows:
Digital input
24 V
GND
Signal
GND
Digital input 1
21
22
23
24
Digital input 2
45
46
47
48
Digital switching outputs
The 4 digital outputs are accessible via the corresponding supply terminals at the bottom of the vibration module.
The pin assignment appears as follows:
Digital output
Open collector
GND
Digital output 1
33
34
Digital output 2
35
36
Digital output 3
29
30
Digital output 4
31
32
Other manuals for ProLink CMS
1
Table of contents
Other Schaeffler Measuring Instrument manuals
Popular Measuring Instrument manuals by other brands
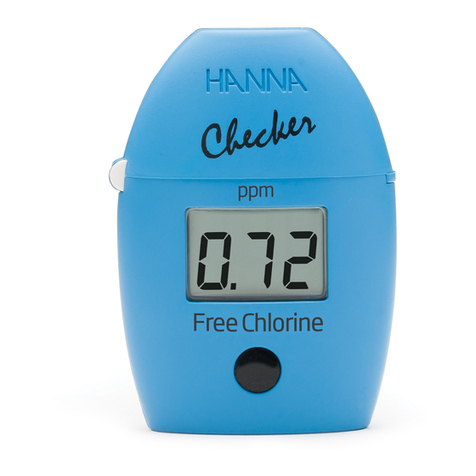
Hanna Instruments
Hanna Instruments Free Chlorine HI701 instruction manual

Computer Weld
Computer Weld GTFM IV Operation & installation manual
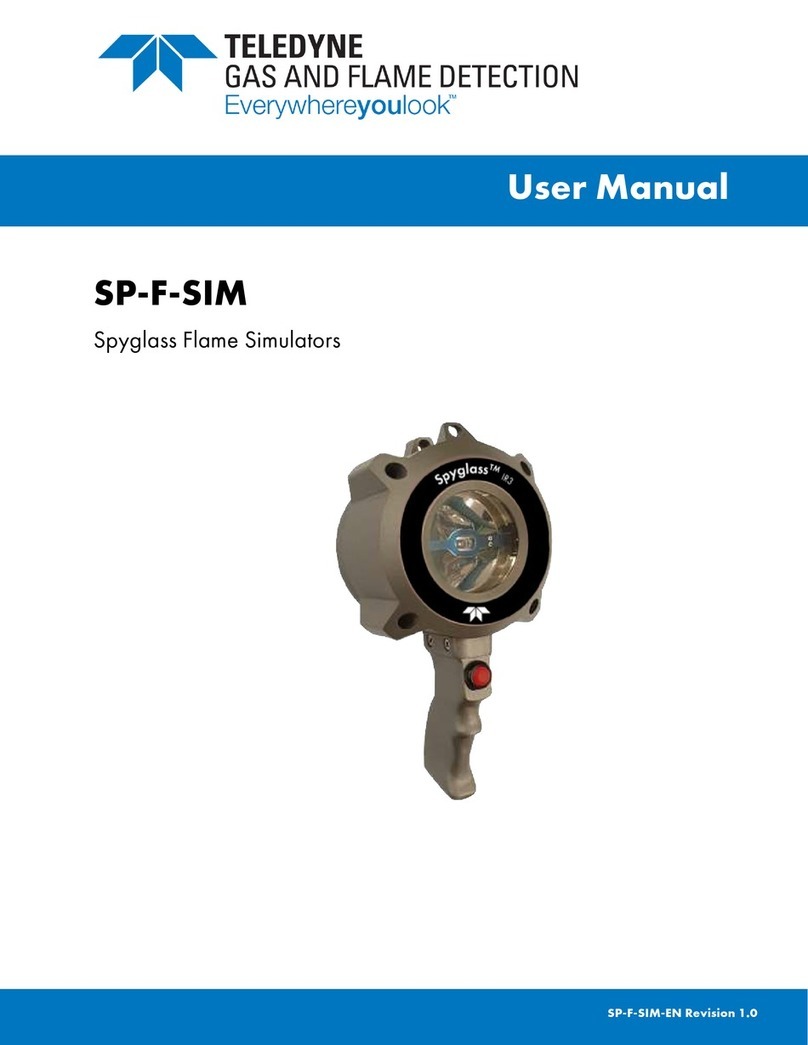
Teledyne
Teledyne SP-F-SIM user manual

Allice Messtechnik
Allice Messtechnik Testec TT-SI 9101 instruction manual

Kusam-meco
Kusam-meco KM 2009 Operation manual

W & W Manufacturing
W & W Manufacturing ECO user guide
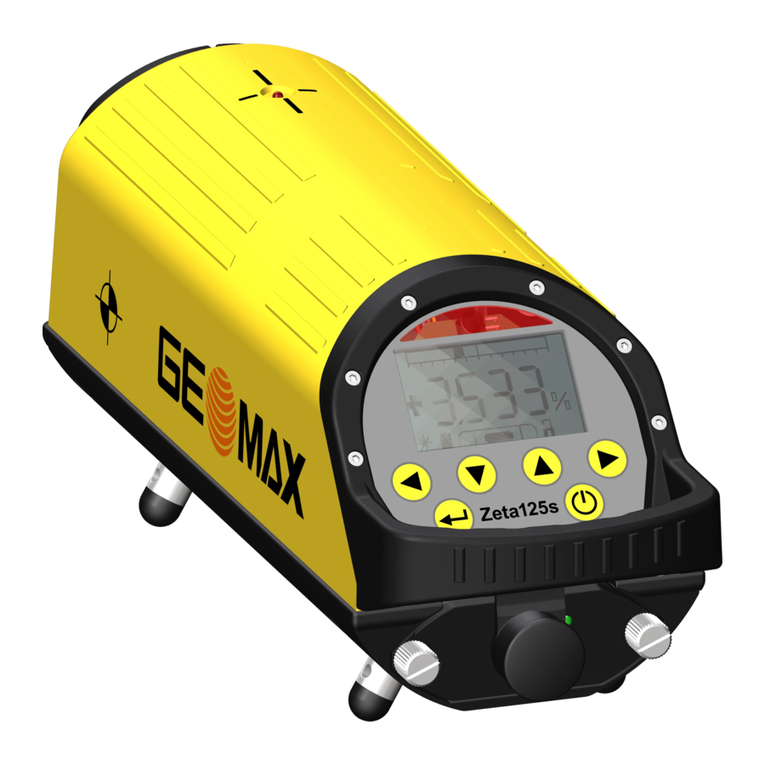
GeoMax
GeoMax Zeta125 user manual

NIDEC TOSOK
NIDEC TOSOK DAG2000 user manual

Fluke
Fluke 374 FC Calibration manual
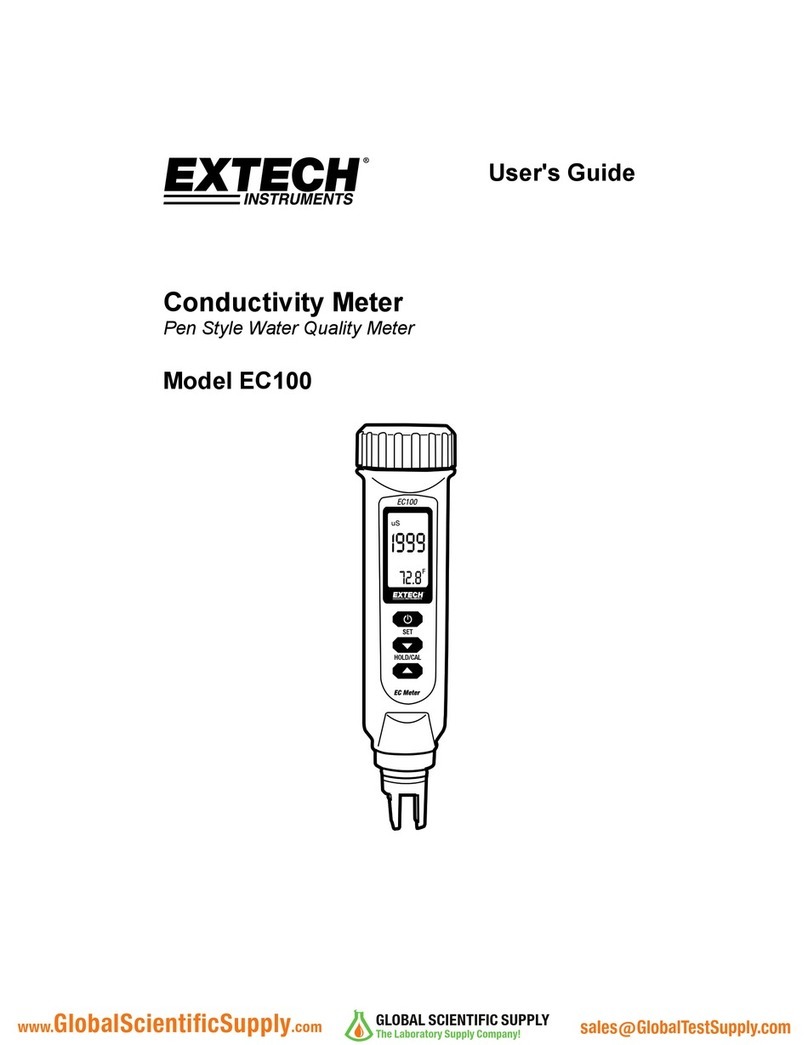
Extech Instruments
Extech Instruments EC100 user guide
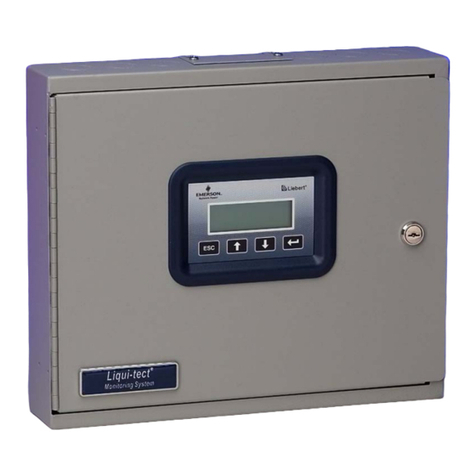
Liebert
Liebert Liqui-tect MC68HC16Z1 user manual
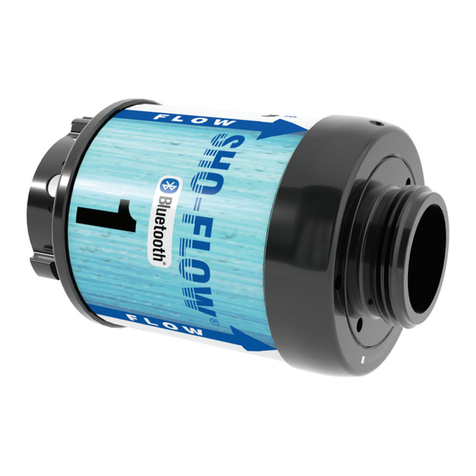
Task Force Tips
Task Force Tips SHO-FLOW Series INSTRUCTIONS FOR SAFE OPERATION AND MAINTENANCE