Sea-Bird Electronics SBE 49 FastCAT User manual

SBE 49 FastCAT
Conductivity, Temperature, and Pressure Sensor
with RS-232 Interface
If deploying vertically, intended for deployment in orientation shown
(sensors at top) for proper pump operation
User’s Manual
Sea-Bird Electronics, Inc.
1808 136th Place NE
Bellevue, Washington 98005 USA
Telephone: 425/643-9866
Fax: 425/643-9954
E-mail: seabir[email protected] Manual Version #009, 08/04/05
Website: www.seabird.com Firmware Version 1.2 and later

2
Limited Liability Statement
Extreme care should be exercised when using or servicing this equipment. It should be used or serviced
only by personnel with knowledge of and training in the use and maintenance of oceanographic
electronic equipment.
SEA-BIRD ELECTRONICS, INC. disclaims all product liability risks arising from the use or servicing
of this system. SEA-BIRD ELECTRONICS, INC. has no way of controlling the use of this equipment
or of choosing the personnel to operate it, and therefore cannot take steps to comply with laws
pertaining to product liability, including laws which impose a duty to warn the user of any dangers
involved in operating this equipment. Therefore, acceptance of this system by the customer shall be
conclusively deemed to include a covenant by the customer to defend, indemnify, and hold SEA-BIRD
ELECTRONICS, INC. harmless from all product liability claims arising from the use or servicing of
this system.

Table of Contents
3
Table of Contents
Section 1: Introduction........................................................................ 5
About this Manual .............................................................................................5
How to Contact Sea-Bird...................................................................................5
Quick Start.........................................................................................................5
Unpacking FastCAT ..........................................................................................6
Section 2: Description of FastCAT..................................................... 7
System Description............................................................................................7
Specifications.....................................................................................................9
Dimensions and End Cap Connector ...............................................................10
Data I/O ...........................................................................................................11
Section 3: Power and Communications Test................................... 12
Software Installation........................................................................................12
Test Setup ........................................................................................................12
Test ..................................................................................................................13
Section 4: Deploying and Operating FastCAT................................ 17
Sampling Modes..............................................................................................17
Polled Sampling........................................................................................18
Autonomous Sampling .............................................................................19
Real-Time Data Corrections ............................................................................21
Baud, Cable Length, and Data Transmission Rate...........................................22
Power and Cable Length for FastCAT without Deck Unit..............................23
Command Descriptions....................................................................................24
Data Output Formats........................................................................................31
OUTPUTFORMAT=0 (raw data in Hexadecimal) ..................................31
OUTPUTFORMAT=1 (engineering units in Hexadecimal).....................31
OUTPUTFORMAT=2 (raw data in decimal)...........................................32
OUTPUTFORMAT=3 (engineering units in decimal).............................32
Optimizing Data Quality..................................................................................33
FastCAT Orientation and Pump Use........................................................33
Positioning Relative to Other Instruments................................................34
Profiling Speed .........................................................................................34
Temperature Equilibration........................................................................34
Setup for Deployment......................................................................................35
Deployment......................................................................................................36
Acquiring and Processing Data with SEASAVE and SBE Data Processing...37
Verifying Contents of .con File ................................................................37
Acquiring Real-Time Data with SEASAVE.............................................38
Processing Data with SBE Data Processing .............................................39
Acquiring Real-Time Data with ROV, AUV, etc. for
Processing by Sea-Bird Software.....................................................................40
Recovery..........................................................................................................41
Section 5: Routine Maintenance and Calibration........................... 42
Corrosion Precautions......................................................................................42
Connector Mating and Maintenance................................................................42
Conductivity Cell Maintenance .......................................................................43
Pressure Sensor Maintenance ..........................................................................43
Replacing Optional Anti-Foulant Devices – Mechanical Design Change.......44
Replacing Optional Anti-Foulant Devices (SBE 49).......................................44
Replacing Optional Anti-Foulant Devices (SBE 49).......................................45
Sensor Calibration............................................................................................47

Table of Contents
4
Section 6: Troubleshooting................................................................ 49
Problem 1: Unable to Communicate with FastCAT ........................................49
Problem 2: Unreasonable Data ........................................................................49
Problem 3: Salinity Lower than Expected .......................................................50
Glossary .............................................................................................. 51
Appendix I: Functional Description and Circuitry......................... 52
Sensors.............................................................................................................52
Sensor Interface ...............................................................................................52
Appendix II: Electronics Disassembly/Reassembly........................ 53
Appendix III: Command Summary................................................. 54
Appendix IV: AF24173 Anti-Foulant Device .................................. 56
Appendix V: Real-Time Data Correction Algorithms.................... 60
Aligning Data...................................................................................................60
Filtering Data...................................................................................................62
Applying Conductivity Cell Thermal Mass Correction to Data.......................62
Appendix VI: Replacement Parts..................................................... 63
Index.................................................................................................... 65

Section 1: Introduction
5
Section 1: Introduction
This section includes contact information, Quick Start procedure, and photos
of a standard FastCAT shipment.
About this Manual This manual is to be used with the SBE 49 FastCAT Profiler Conductivity,
Temperature, and Pressure Sensor.
It is organized to guide the user from installation through operation and data
collection. We’ve included detailed specifications, command descriptions,
maintenance and calibration information, and helpful notes throughout
the manual.
Sea-Bird welcomes suggestions for new features and enhancements of our
products and/or documentation. Please e-mail any comments or suggestions to
How to Contact Sea-Bird Sea-Bird Electronics, Inc.
1808 136th Place Northeast
Bellevue, Washington 98005 USA
Telephone: 425-643-9866
Fax: 425-643-9954
Website: http://www.seabird.com
Business hours:
Monday-Friday, 0800 to 1700 Pacific Standard Time
(1600 to 0100 Universal Time)
Except from April to October, when we are on summer time
(1500 to 0000 Universal Time)
Quick Start Follow these steps to get a Quick Start using the FastCAT. The manual
provides step-by-step details for performing each task:
1. Test power and communications (Section 3: Power and
Communications Test).
2. Deploy the FastCAT (Section 4: Deploying and Operating FastCAT):
A. Establish setup and sampling parameters.
B. Install I/O cable connector and locking sleeve. Connect other end of
cable to computer/controller and to power supply.
C. Verify hardware and external fittings are secure.
D. Remove caps from end of T-C Duct and pump exhaust.
E. Apply power.
•If AUTORUN=Y, FastCAT will start sampling automatically.
•If AUTORUN=N, send START to start sampling.
F. Deploy FastCAT.

Section 1: Introduction
6
Unpacking FastCAT Shown below is a typical FastCAT shipment.
Spare o-ring and
hardware kit (includes
tee exhaust for slow
profiling applications)
Conductivity cell
cleaning solution
(Triton-X)
Software, and Electronic Copies of
Software Manuals and User Manual
I/O cable
Conductivity cell filling
and storage kit
25-pin to 9-pin adapter
(for use with computer
with DB-25 connector)
SBE 49
FastCAT
FastCAT User Manual
SBE 49 FastCAT

Section 2: Description of FastCAT
7
Section 2: Description of FastCAT
This section describes the functions and features of the SBE 49 FastCAT,
including specifications, dimensions, connector, and communications.
System Description
The SBE 49 FastCAT is an integrated CTD sensor intended for towed vehicle,
ROV, AUV, or other autonomous profiling applications in marine or fresh-
water environments at depths up to 7000 meters (22,900 feet). The FastCAT’s
pump-controlled, TC-ducted flow minimizes salinity spiking, and its 16 Hz
sampling provides very high spatial resolution of oceanographic structures
and gradients.
The FastCAT’s temperature thermistor and conductivity cell are the same as
used in our premium 911plus CTD system. Its pressure sensor (offered in eight
full scale ranges from 20 to 7000 dbars) is the superior, micro-machined,
silicon strain-gauge recently developed by Druck, Inc. Sophisticated interface
circuitry provides very high resolution and accuracy — entirely comparable to
the 911plus.
The FastCAT is an easy-to-use, light, and compact instrument ruggedly made
of titanium and other low-maintenance (plastic) materials; it is well suited to
even the smallest vehicle. There are straightforward commands for continuous
(full rate or averaged) or single sample acquisition. EEPROM-stored
calibration coefficients permit data output in ASCII engineering units
(degrees C, Siemens/m, decibars, Salinity [PSU], and sound velocity [m/sec]),
or the user can select raw data output if desired.
The FastCAT is externally powered, and its data is telemetered by its RS-232C
interface. The FastCAT has no memory or internal batteries, and does not
support auxiliary sensor inputs.
The FastCAT samples in two modes:
•Autonomous sampling –The FastCAT runs continuously, sampling at
sixteen scans per second (16 Hz). It can be set to average up to
255 samples, transmitting only the averaged data. Programmable real-time
processing – aligning, filtering, and correcting data for conductivity cell
thermal mass effects – provides high quality data for applications where
post-processing is not feasible. The FastCAT can be programmed to begin
autonomous sampling when power is applied or on command.
•Polled sampling – On command, the FastCAT takes one sample and
transmits the data.
A standard FastCAT is supplied with:
•Titanium housing for depths to 7000 meters (22,900 feet)
•Strain-gauge pressure sensor
•Integrated T-C Duct
•Internal pump for flow-controlled conductivity and temperature response
•XSG 4-pin I/O bulkhead connector
•Straight pump exhaust fitting, providing high quality data for
most applications
•Pump exhaust tee fitting, for slow profiling applications – tee fitting is
included in spares kit that ships standard with FastCAT, and can be easily
substituted for the standard straight pump exhaust fitting in the field
Note:
The FastCAT’s pump is not designed
to be used to pump water through
other sensors. Other sensors
requiring pumped water need a
separate pump.
If deploying
vertically,
intended for
deployment
in orientation
shown
(sensors
at top) for
proper pump
o
p
eration

Section 2: Description of FastCAT
8
FastCAT options include:
•Plastic housing for depths to 350 meters (1150 feet) in lieu of
titanium housing
•MCBH Micro wet-pluggable connector in lieu of XSG connector
•Anti-foulant device fitting and expendable Anti-Foulant Devices for
long deployments
The FastCAT can be used with the SBE 36 CTD Deck Unit and Power Data
Interface Module (PDIM) to provide power and real-time data handling
capability over single-conductor sea cables. The PDIM is a small pressure
housing that is mounted on or near the FastCAT. The PDIM:
•Converts power from the sea cable to + 15 VDC power for the FastCAT.
•Interfaces two-way RS-232 communications from the FastCAT to the
telemetry used on the sea cable. The PDIM converts FastCAT data into
single-wire telemetry for transmission over long (10,000 meter
[32,800 feet]) sea cables.
See the SBE 36 / PDIM manual for system operating details.
The FastCAT is supplied with a powerful Win 95/98/NT/2000/XP software
package, SEASOFT-Win32, which includes:
•SEATERM - terminal program for instrument setup and communication.
•SEASAVE - program for real-time acquisition and display of data.
SEASAVE can be used for real-time data acquisition only if the FastCAT
is directly connected to the computer (not connected to an AUV,
ROV, etc.).
•SBE Data Processing - program for calculation and plotting of
conductivity, temperature, pressure, and derived variables such as salinity
and sound velocity.
Notes:
•Help files provide detailed
information on the use of
SEATERM, SEASAVE, and
SBE Data Processing.
•Separate software manuals on
CD-ROM provide detailed
information on the use of
SEASAVE and SBE Data
Processing.
•Sea-Bird also supplies a
DOS software package,
SEASOFT-DOS. However, the
DOS software is not compatible
with the FastCAT.
Note:
When using the FastCAT with the
SBE 36 and PDIM, SEASAVE (our
real-time data acquisition software)
does not allow acquisition of NMEA
or Surface PAR data.

Section 2: Description of FastCAT
9
Specifications
Temperature
(°C) Conductivity
(S/m) Pressure
Measurement
Range -5 to +35 0 to 9
0 to full
scale range:
20 / 100 / 350 /
600 / 1000/
2000 / 3500 /
7000 meters
(expressed in
meters of
deployment depth
capability)
Initial
Accuracy 0.002 0.0003 0.1% of
full scale range
Typical
Stability
(per month) 0.0002 0.0003
0.004% of
full scale range
Resolution 0.0001
0.00005
(oceanic waters;
resolves 0.4 ppm
in salinity)
0.00007
(high salinity waters;
resolves 0.4 ppm
in salinity)
0.00001
(fresh waters;
resolves 0.1 ppm
in salinity)
0.002% of
full scale range
Sensor
Calibration
(measurement
outside these
ranges may be at
slightly reduced
accuracy due to
extrapolation
errors)
+1 to +32
0 to 9; physical
calibration over
the range 2.6 to
6 S/m, plus zero
conductivity (air)
Ambient
pressure to full
scale range in
5 steps
Power
Requirements
0.75 Amps at 9-24 VDC
Turn-on transient: 750 mA
Sampling and transmitting data (includes pump):
390 mA at 9 V
285 mA at 12 V
180 mA at 19 V
Housing
Material Standard: 3AL/2.5V Titanium
Optional: Plastic
Depth Rating Standard: 7000 meters (22,900 feet)
Optional: 350 meters (1150 feet)
Weight
Standard Titanium Housing -
In air: 2.7 kg (6 lbs) In water: 1.4 kg (3 lbs)
Optional Plastic Housing -
In air: 1.8 kg (4 lbs) In water: 0.5 kg (1 lb)

Section 2: Description of FastCAT
10
Dimensions and End Cap Connector
FastCAT with straight exhaust
(as shipped by Sea-Bird)
FastCAT with tee exhaust for
slow profiling applications
(tee is in spare parts kit
shipped with FastCAT, and is
easily substituted in the field)
Align with
raised bump on
connector
1
2
3 4
Standard Connector
XSG-4-BCL-HP-SS
Pin Description
1 Ground
2 RS-232C Receive from computer
3 RS-232C Transmit to computer
4 Power (9-24 VDC)
14
3 2
Optional MCBH Connector
MCBH-4MP (WB), TI
(3/8” length base, ½-20 thread)

Section 2: Description of FastCAT
11
Data I/O
The FastCAT receives setup instructions and outputs data and diagnostic
information via a three-wire RS-232C link, and is factory-configured for
9600 baud, 8 data bits, 1 stop bit, and no parity. FastCAT RS-232 levels are
directly compatible with standard serial interface cards (IBM Asynchronous
Communications Adapter or equal). The communications baud rate can be
changed using the BAUD= command (see Section 4: Deploying and
Operating FastCAT).

Section 3: Power and Communications Test
12
Section 3:
Power and Communications Test
This section describes software installation and the pre-check procedure for
preparing the FastCAT for deployment. The power and communications test
will verify that the system works, prior to deployment.
Software Installation
Recommended minimum system requirements for running SEASOFT-Win32:
Pentium 90 CPU, 64 Mbyte RAM, Windows 98 or later.
If not already installed, install SEATERM (terminal program) and other Sea-
Bird software programs on your computer using the supplied software CD:
1. Insert the CD in your CD drive.
2. Double click on Seasoft-Win32.exe.
3. Follow the dialog box directions to install the software.
The default location for the software is c:/Program Files/Sea-Bird. Within that
folder is a sub-directory for each program. The installation program allows
you to install the desired components. Install all the components, or just install
SEATERM for now.
Test Setup
1. Remove the dummy plug and install the I/O cable:
A. By hand, unscrew the locking sleeve from the FastCAT’s I/O
connector. If you must use a wrench or pliers, be careful not to loosen
the I/O connector instead of the locking sleeve.
B. Remove the dummy plug from the FastCAT’s I/O connector by
pulling the plug firmly away from the connector.
C. Standard Connector - Install the Sea-Bird I/O cable connector,
aligning the raised bump on the side of the connector with the large
pin (pin 1 - ground) on the FastCAT. OR
MCBH Connector – Install the cable connector, aligning the pins.
2. Connect the I/O cable connector to your computer’s serial port.
3. Connect the I/O cable connector’s red (+) and black (-) wires to a power
supply (9-24 VDC). See Section 2: Description of FastCAT, for the
connector details.
Dummy
plug
Locking
sleeve
Note:
It is possible to use the FastCAT
without SEATERM by sending
direct commands from a dumb
terminal or terminal emulator, such
as Windows HyperTerminal.

Section 3: Power and Communications Test
13
Test
1. Double click on SeaTerm.exe. If this is the first time the program is used,
the setup dialog box may appear:
Select the instrument type (SBE 49) and the computer COM port for
communication with the FastCAT. Click OK.
2. The main screen looks like this:
•Menus – Contains tasks and frequently executed instrument
commands.
•Toolbar – Contains buttons for frequently executed tasks and
instrument commands. All tasks and commands accessed through the
Toolbar are also available in the Menus. To display or hide the
Toolbar, select View Toolbar in the View menu. Grayed out Toolbar
buttons are not applicable.
•Command/Data Echo Area – Echoes a command executed using a
Menu or Toolbar button, as well as the instrument’s response.
Additionally, a command can be manually typed in this area, from the
available commands for the instrument. Note that the instrument must
be awake for it to respond to a command (use Connect on the Toolbar
to wake up the instrument).
•Status bar – Provides status information. To display or hide the Status
bar, select View Status bar in the View menu.
Note:
See SEATERM’s help files for
detailed information on the use
of the program.
Note:
There is at least one way, and as
many as three ways, to enter
a command:
•Manually type a command in
Command/Data Echo Area
•Use a menu to automatically
generate a command
•Use a Toolbar button to
automatically generate
a command
Note:
Once the system is configured and
connected (Steps 3 through 5
below), to update the Status bar:
•on the Toolbar, click Status; or
•from the Utilities menu, select
Instrument Status.
SEATERM sends the status
command, which displays in the
Command/Data Echo Area, and
updates the Status bar.
Status bar
Menus
Command/Data Echo Area Toolbar
Instrument Computer
COM port
Instrument
EPROM version Baud rate, data bits,
stop bits, and parity
Capture
to file
status –
grayed
out if not
capturing
(not applicable
to FastCAT)
SBE49

Section 3: Power and Communications Test
14
Following are the Toolbar buttons applicable to the FastCAT:
Toolbar
Button Description Equivalent
Command*
Connect Re-establish communications with
FastCAT. Computer responds with
S> prompt. (press Enter key)
Status Display instrument setup and status
(configuration and setup parameters,
whether FastCAT is sampling, etc.). DS
Coefficients Display calibration coefficients. DCAL
Capture
Capture instrument responses on screen to
file; useful for diagnostics. File has .cap
extension. Capture status displays in
Status bar. Press Capture again to turn
off capture.
As FastCAT has no internal memory, if
you are using SEATERM to acquire
data you must capture before sampling
begins to save data for future review
and processing.
(Note: The .cap file does not have the
required header information for processing
by SBE Data Processing. Use SEASAVE
to acquire data that will be processed by
SBE Data Processing.)
—
Diagnostics
Perform one or more diagnostic tests on
FastCAT. Diagnostic test(s) accessed in
this manner are non-destructive –
they do not write over any existing
instrument settings.
DS, DCAL,
and TS
Stop Interrupt and end current activity, such as
sampling or diagnostic test. (press Esc key or
Ctrl C)
Disconnect Free computer COM port used to
communicate with FastCAT. COM port
can then be used by another program. —
*See Command Descriptions in Section 4: Deploying and Operating FastCAT.

Section 3: Power and Communications Test
15
3. In the Configure menu, select SBE 49. The dialog box looks
like this:
Make the selections in the Configuration Options dialog box:
•COMM Port: COM 1 through COM 10, as applicable
•Baud Rate: 9600 (documented on Configuration Sheet in manual)
•Data Bits: 8
•Parity: None
•Mode: RS-232 (Full Duplex)
Click OK to save the settings.
4. In the Communications menu, select Options / Cycle baud
when connecting.
5. Click Connect on the Toolbar. SEATERM tries to connect to the FastCAT
at the baud set in Step 3. If it cannot, it cycles through all other possible
baud rates to try to connect. When it connects, the display looks like this:
S>
This shows that correct communications between the computer and the
FastCAT has been established.
If the system does not respond with the S> prompt:
•Click Connect again.
•Verify the correct instrument was selected in the Configure menu and
the settings were entered correctly in the Configuration Options
dialog box. Note that the baud rate is documented on the
Configuration Sheet in the manual.
•Check cabling between the computer and FastCAT.
Computer COM port, baud rate,
data bits, and parity for
communication between computer
and FastCAT
Interface for communication
between computer and
FastCAT
Note:
•SEATERM’s baud rate must be the
same as the FastCAT baud rate
(set with BAUD=). Baud is factory-
set to 9600, but can be changed by
the user (see Command
Descriptions in Section 4:
Deploying and Operating FastCAT).
•When you click OK, SEATERM
saves the Configuration Options
settings to the SeaTerm.ini file in
your Windows directory.
SeaTerm.ini contains the last saved
settings for each instrument. When
you open SEATERM and select the
desired instrument (SBE 37, 49,
etc.) in the Configure menu, the
Configuration Options dialog box
shows the last saved settings for
that instrument.

Section 3: Power and Communications Test
16
6. Display FastCAT status information by clicking Status on the Toolbar.
The display looks like this:
SBE 49 FastCAT V 1.2 SERIAL NO. 0055
number of scans to average = 1
pressure sensor = strain gauge, range = 1000.0
minimum cond freq = 3000, pump delay = 30 sec
start sampling on power up = no
output format = converted decimal
output salinity = no, output sound velocity = no
temperature advance = 0.0625 seconds
celltm alpha = 0.03
celltm tau = 7.0
real-time temperature and conductivity correction enabled for converted data
7. Command the FastCAT to take a sample by typing TS and pressing the
Enter key. The display looks like this (with converted decimal output
format, and no output salinity or sound velocity):
23.7658, 0.00019, 0.062
where 23.7658 = temperature in degrees Celsius
0.00019 = conductivity in S/m
0.062 = pressure in decibars
These numbers should be reasonable; i.e., room temperature, zero
conductivity, barometric pressure (gauge pressure).
The FastCAT is ready for programming and deployment.

Section 4: Deploying and Operating FastCAT
17
Section 4:
Deploying and Operating FastCAT
This section includes discussions of:
•Sampling modes, including pump operation and example commands
•Real-time data corrections
•Baud rate, cable length, and data transmission rate
•Power and cable length
•Command descriptions
•Data output formats
•Optimizing data quality
•Setup for deployment
•Deployment
•Acquiring and processing FastCAT data
•Recovery - physical handling
Sampling Modes
The FastCAT has two sampling modes for obtaining data:
•Polled sampling
•Autonomous sampling
Descriptions and examples of the sampling modes follow. Note that the
FastCAT’s response to each command is not shown in the examples. Review
the operation of the sampling modes and the commands described in
Command Descriptions before setting up your system.
Note:
Help files contain detailed
information on setup and use of
Sea-Bird software.

Section 4: Deploying and Operating FastCAT
18
Polled Sampling
On command (TS), the FastCAT takes one sample and transmits the
data real-time.
The pump does not turn on automatically for polled sampling
(MINCONDFREQ= and PUMPDELAY= do not apply). To run the pump
before taking a sample, send PUMPON to turn the pump on before sending
TS. Send PUMPOFF to turn the pump off after taking the sample.
Example: Polled Sampling (user input in bold)
Apply power and wake up FastCAT. Set up to not start automatic
autonomous sampling when power is applied, to output data in
decimal engineering units format, and to output salinity and sound
velocity as well as conductivity, temperature, and pressure.
Verify setup with status command. Remove power.
(Apply power, then click Connect on Toolbar to wake up.)
S>AUTORUN=N
S>OUTPUTFORMAT=3
S>OUTPUTSAL=Y
S>OUTPUTSV=Y
S>DS (to verify setup)
(Remove power.)
When ready to take a sample, put FastCAT in water. Apply power
and wake up FastCAT. Command FastCAT to turn pump on, take
a sample, and turn pump off. Remove power. Repeat as desired.
(Apply power, then click Connect on Toolbar to wake up.)
S>PUMPON
S>TS
S>PUMPOFF
(Remove power.)

Section 4: Deploying and Operating FastCAT
19
Autonomous Sampling
The FastCAT runs continuously, sampling data at 16 scans per second (16 Hz)
and transmitting the data real-time. The FastCAT can be set to average up to
255 samples, transmitting only the averaged data. AUTORUN defines how
autonomous sampling starts and stops:
If To Start Sampling To Stop Sampling
AUTORUN=Y Turn on power.
AUTORUN=N Send START.
•Turn off power, or
•Send STOP, click Stop on
SEATERM’s Toolbar, or type
Ctrl Z. (Stopping this way allows
you to then send commands to
check or modify the setup.)
After the conductivity cell enters the water there is a user-programmable delay
before pump turn-on so that all the air in the pump tubing can escape. If the
pump motor turns on when there is air in the impeller housing, priming is
uncertain and a proper flow rate cannot be ensured. The cell inlet and pump
outlet must not come above the water surface or the prime will be lost.
•If prime is lost, stop sampling. Wait at least 5 seconds, then submerge the
FastCAT completely, restart sampling, and wait for the pump delay time
before beginning the profile.
Pump turn-on occurs when two user-programmable conditions have
been met:
•Raw conductivity frequency exceeds the minimum conductivity
frequency (MINCONDFREQ=)
Set the minimum conductivity frequency for pump turn-on above the
instrument’s zero conductivity raw frequency (shown on the FastCAT
Configuration Sheet in the manual), to prevent the pump from turning on
when the FastCAT is in air.
!For salt water and estuarine applications -
typical value = zero conductivity raw frequency + 500 Hz
!For fresh/nearly fresh water -
typical value = zero conductivity raw frequency + 5 Hz
If the minimum conductivity frequency is too close to the zero
conductivity raw frequency, the pump may turn on when the FastCAT is
in air as result of small drifts in the electronics. Some experimentation
may be required, and in some cases it may be necessary to rely only on the
pump turn-on delay time to control the pump. If so, set a minimum
conductivity frequency lower than the zero conductivity raw frequency.
•Pump turn-on delay time has elapsed (PUMPDELAY=)
Set the pump turn-on delay time to allow time for the pump to fill with
water after the FastCAT is submerged. Determine the turn-on delay by
immersing the FastCAT (power off, not sampling). Measure the time
needed to completely fill the pump exhaust tubing (by watching for when
air bubbles stop coming out of the exhaust); 20 seconds is typical. Set the
delay to approximately 1.5 times longer (30 seconds). When actually
using the FastCAT, be sure to soak the instrument just under the surface
for at least the time required for pump turn-on.
Pump turn-off occurs when the conductivity frequency falls below the
minimum conductivity frequency (MINCONDFREQ=).
Pump
exhaust
tubin
g

Section 4: Deploying and Operating FastCAT
20
Example 1: Autonomous Sampling Setup for AUTORUN=N (user input in bold)
Apply power and wake up FastCAT. Set up to average every 4 samples, and output
data in raw hexadecimal format. Set up with a 60-second pump turn-on delay after
pump enters water to ensure pump is primed before turning on. Verify setup with
status command. Remove power.
(Apply power, then click Connect on Toolbar to wake up.)
S>NAVG=4
S>OUTPUTFORMAT=0
S>PUMPDELAY=60
S>AUTORUN=N
S>DS (to verify setup)
(Remove power.)
When ready to begin sampling:
(Apply power, then click Connect on Toolbar to wake up.)
S>START
(Put FastCAT in water, and allow to soak for at least time required for pump turn-
on (PUMPDELAY=60) before beginning cast.)
When cast is complete, stop sampling.
S>STOP
Example 2: Autonomous Sampling Setup for AUTORUN=Y (user input in bold)
Apply power. Set up to average every 4 samples, and output data in raw
hexadecimal format. Set up with a 60-second pump turn-on delay after pump enters
water to ensure pump is primed before turning on. Set up to start sampling upon
power up. Verify setup with status command.
(Apply power, then click Connect on Toolbar to wake up.)
S>NAVG=4
S>OUTPUTFORMAT=0
S>PUMPDELAY=60
S>AUTORUN=Y
S>DS (to verify setup)
(Remove power.)
When ready to begin sampling:
(Apply power.)
(Put FastCAT in water, and allow to soak for at least time required for pump turn-
on (PUMPDELAY=60) before beginning cast.)
When cast is complete, remove power or send STOP to stop sampling (send
STOP if you want to view and/or modify FastCAT’s setup immediately after you
stop sampling).
Note:
Sea-Bird ships the
FastCAT with
AUTORUN=N(it will not
start sampling when power
is applied). If you send
AUTORUN=Y, turn power
off and then on again
to start sampling, or
send START.
Table of contents
Popular Temperature Controllers manuals by other brands
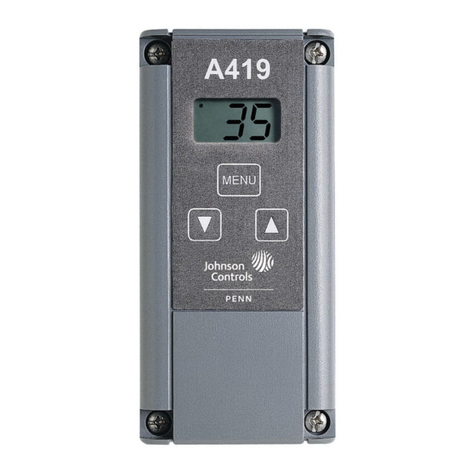
Johnson Controls
Johnson Controls A419 Series Product/Technical Bulletin

Friedrich Küpper
Friedrich Küpper J Series Service & parts manual
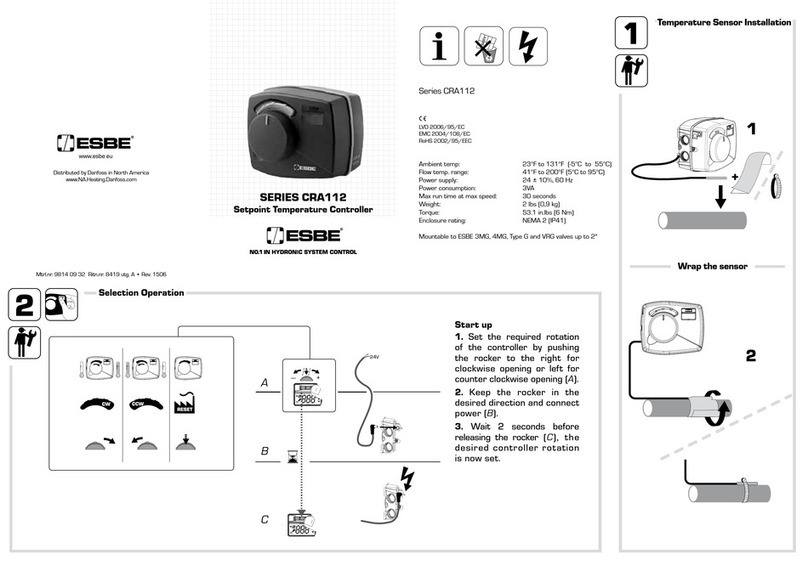
ESBE
ESBE CRA112 Series quick start guide
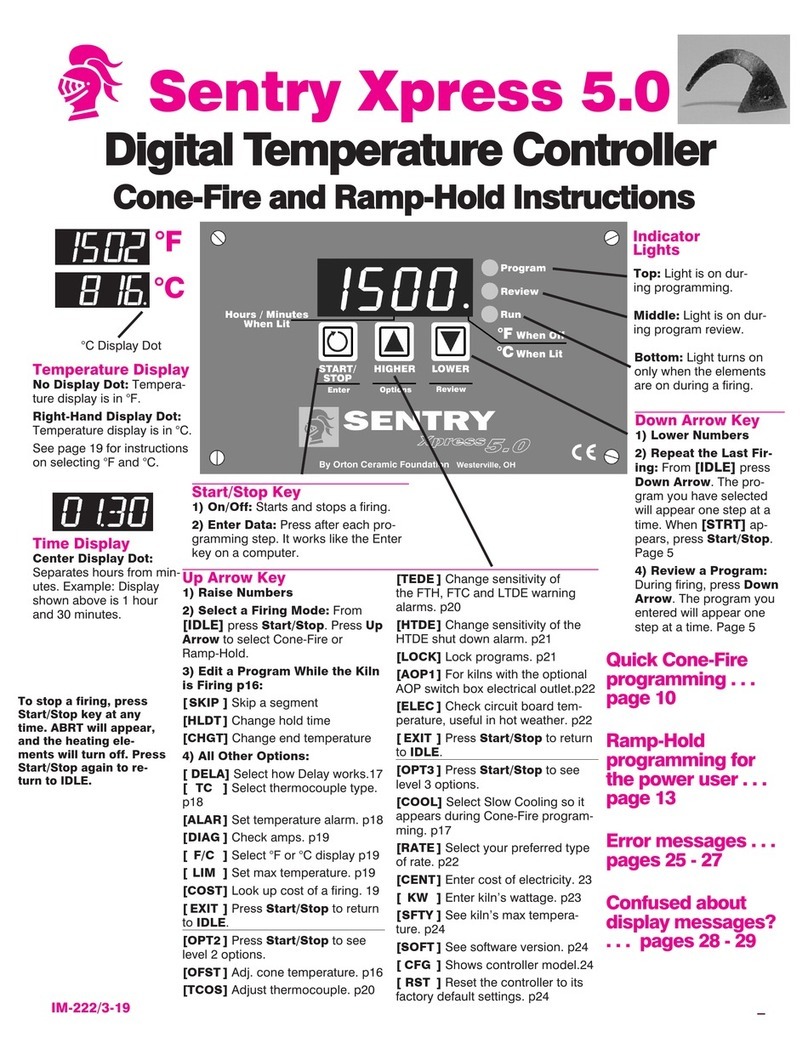
Sentry
Sentry Xpress 5.0 Instructions for use
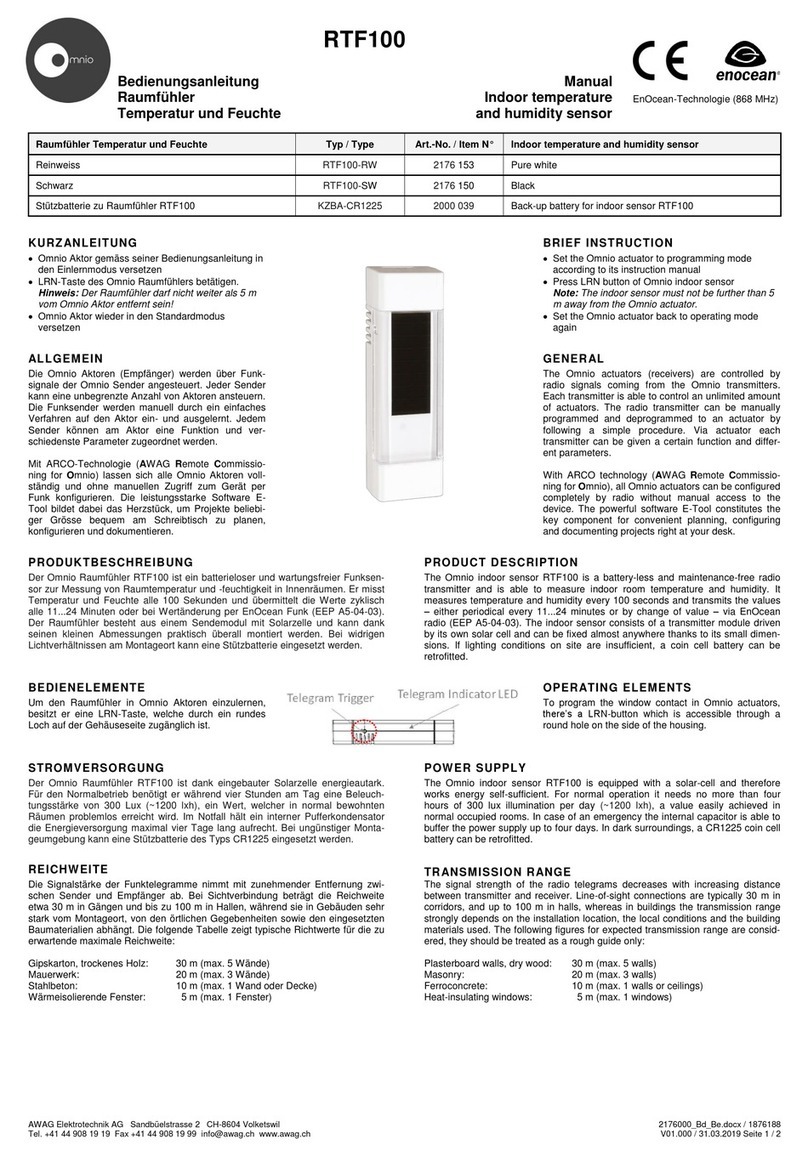
EnOcean
EnOcean Omnio RTF100 Series manual
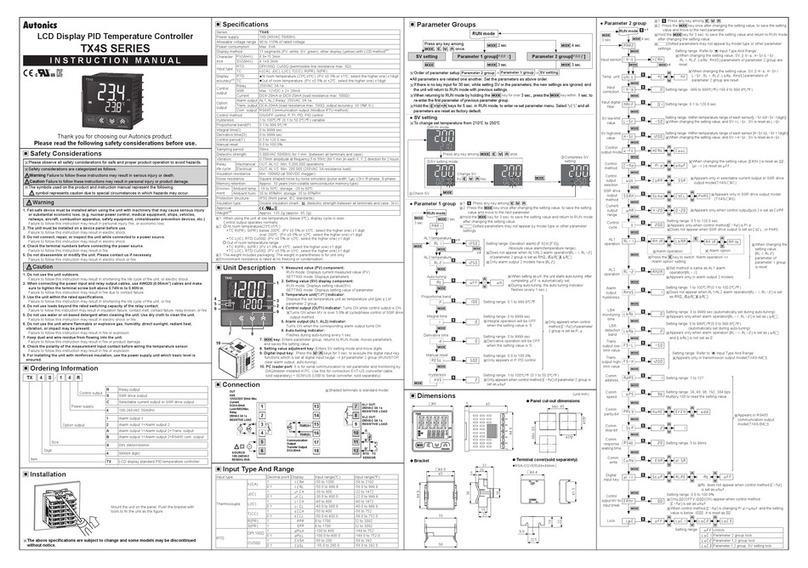
Autonics
Autonics TX4S Series instruction manual