SEA SWING 2 DG R2F User manual

International registered trademark n. 804888
IT - EN - FR
SEA S.p.A.
Zona Industriale Sant’ Atto - 64100 - Teramo - ITALY
Telephone: + 39 0861 588341 - Fax: + 39 0861 588344
www.seateam.com
67412260 REV. 00 - 06/2022
QUICK START
SWING 2 DG R2F R2BFSWING 2 DG
FULL MANUAL
(Rev. 12)
&
SAFETY
INFORMATION

Italiano
ENGLISH
International registered trademark n. 804888
JOLLY 3 SEACLOUD
T
JOLLY 3
SEACLOUD
T SWING 2 DG
( 7);
!
F
; ,
A (, )
;
PRELIMINARY
TECHNICAL INFORMATION
-
230V - 50/60 H
115V - 50/60 H
30 mA
-20° C +50°C
( )
IP 55
SWING 2 DG R2F 03.01
SWING 2 DG R2BF 00.02
QUICK START
7
TIMER TO
CLOSE
3
MOTOR
M ( OFF): ,
DO NOT N.C. ( .. )
P ( 5)
O - «» ( 6)
S «» - -
«-» ( )
C 3 ( )
S 7
M ;
, ,
192
MOVE
GATE 1
193
MOVE
GATE 2
UP DOWN

International registered trademark n. 804888
Italiano
ENGLISH
PROGRAMMING
BUTTONS
OPTIONAL JUMPERS
AUTOMATIC RECOGNITION OF THE
N.C. INPUTS NOT IN USE - NO JUMPER IS
REQUIRED ON THE N.C. CONTACTS
THE INPUTS EXCLUDED DURING THE
WORKING TIMES PROGRAMMING CAN BE
RESTORED THROUGH THE «INPUTS
MANAGEMENT» MENU (CHAPTER 5).
NO NEED TO SET UP THE UNIT AGAIN
1 - CONNECTIONS
WARNING: CONNECT ALL DEVICES WHEN THE CONTROL UNIT IS SWITCHED-OFF
8
7
6
5
4
3
2
1
CN2
EXP
UP DOWN OK
TR1
CNS
CNS
CN1
JOLLY
SEACLOUD
CN2
CN3
CNA
EXP
MEMO
- - - - - - - -
- - - - - - - -
- - - - - - - -
- - - - - - - -
NL
CNP
CNI
R1
R2
R3
F1
T2
T1
F2
16
16
17
17
14
14
15
15
21
13
13
11
11
12
12
10
10
9
9
18
18
19
19
8
7
6
5
4
3
2
1
CN8 CN4
CN7
CN5
CN6
20 23
23
27
25
22
22
26
24
120 mm
164 mm
CN1
16 17
14 15
13
11 12
10
918 19
CN3
NL21
CN4
20
CN5
23
22
CN6
CN7
25
24
CN8
CNP
CNS CNA
START STPD STOP PH1 PH2 COM COM COM 24V 24VAUX TEST
Motor 1 neutral
M
Motor 1 closing
Motor 1 opening
Motor 2 neutral
M
Motor 2 closing
Motor 2 opening
Courtesy light (phase)
Courtesy light (neutral)
Neutral
NM1 OPM1 CLM1 NM2 OPM2 CLM2 LAMPN LAMP
Line
Not connected
Antenna
Start
Flashing light
Electric lock
Common
Safety edge
Opening limit switch 1
Closing limit switch 1
Opening limit switch 2
Closing limit switch 2
Common
Start Pedonale
Stop
Photocell 1
Photocell 2
Common
Common
Common
24V
24V AUX
TEST
JOLLY
SEACLOUD
CNI
MEMO
Common
**
*
***
3A
Dry contact
UP DOWN OK
BLACK WHITE RED OPEN
Firmware
update
JOLLY3/SEACLOUD
CONNECTOR
EXTERNAL
MODULE
CONNECTOR
RF UNI
MODULE
RF FIX
MODULE RX
MODULE
RX MEMORY
EXPANSION
MODULE
RADIO RX MODULES CONNECTORS
*
CN1 CN5
R3
F1
F2
TR1
=
=
=
=
DRY CONTACTRELAY (***)
FUSE ACCESSORIES 1A
FUSE 6.3AT (230V) OR 10AT (115V)
POWER TRANSFORMER
T1
T2
R1
R2
=
=
=
=
MOTOR CONTROL TRIAC
MOTOR CONTROL TRIAC
MOTOR RELAY
COURTESY LIGHT RELAY
T CN6 SWING 2 DG R2F «FC»
* *
* * *
T CN8 3A 250V;
R2 DRY CONTACT
CN5
23
22
24V
COM
-
START
-
A 24V 500mA, 24V
, (30 mA)
*
27
26
P
C

International registered trademark n. 804888
Italiano
ENGLISH
CN1
16 17
14 15
13
11 12
10
918 19
Start
Stop
CN1
16 17
14 15
13
11 12
10
918 19
RX1
RX2
TX1
TX2
15 15
15
15
15
15
12
17 17
17
17
13
24V (+)
8
7
6
5
CN2
LAMPN LAMP
21
CN4
CN1
20
17 18 191615
24V
21
CN4
CN1
20
17 18 191615
24V LAMP
23
CN5
22
COM
CN7
25
24
ANTENNA
DS1
2 1
OFF
ON
DIP SWITCH 1 = OFF
DIP SWITCH 2 = OFF
2 - MAIN WIRINGS
EXAMPLE OF START, PARTIAL START,
STOP AND PHOTOCELLS WIRINGS
Partial Start
Common
Common
EXAMPLE OF LIMIT SWITCH WIRINGS
16
15
CN1
13
12 14
CN6
COMMON
COMMON
COMMON
M1 OPENING
M2 OPENING
M1 CLOSING
M2 CL.
MOTOR 1 LIMIT SWITCH MOTOR 2 LIMIT SWITCH
EXAMPLE OF POTENTIOMETER WIRINGS via «LE/LSE» UNIT
M1
1 2 4 56 73 89 10 11
M2
DS1
2 1
ON
CN1
POT ENC
CNP
+
-
LSE
POTENTIOMETER
M1
P01 P02
GND
I3
D1 P11D2 P12 I1 I2 I4
BLUE (GREEN) P01
BLACK (WHITE) D1
BROWN P11
BROWN
BROWN
BLACK
BLACK
BLUE
BLUE
POTENTIOMETER
M2
BLUE (GREEN) P02
BLACK (WHITE) D2
BROWN P12
EXAMPLE OF SAFETY EDGE WIRINGS
EXAMPLE OF ELECTRIC LOCK WIRINGS
EXAMPLE OF ANTENNA WIRINGS EXAMPLE OF COURTESY LIGHT
WIRINGS
EXAMPLE OF FLASHING LAMP WIRINGS
SAFETY
EDGE
SAFETY EDGE
12V
ELECTRIC LOCK
ELECTRIC
LOCK
NEUTRAL
LINE
F ,
,
!

International registered trademark n. 804888
Italiano
ENGLISH
F 16AT 230V~ 115V~
NL
CN3
a
-
-
-
-
00111110
1 2 3 4 5 6 7 8
9 10 11 12 13 14 15 16
1
2
3
4
5
6
7
8
9
10
11
12
13
14
15
16
11110000
-
-
0
1
N.O.
ON MODEL «R2F» ON MODEL «R2BF»
N.C.
STOP
- - -- - -
- -
- - -
SEA
MENU SET
START
- -
-
N.C. INPUT DASH ON
-
- - -
SEA
MENU SET
-
- - - -
N.O. INPUT DASH OFF
-
- - -
SEA
MENU SET
-
- - - -
-
- - -
SEA
MENU SET
-
- - - - - -
- - -
SEA
MENU SET
-
- - - -
-
- -
SEA
MENU SET
-
- - - -
-
---
SEA
MENU SET
-
- - - -
00111110
11000000
START
(N.O.)
START
(N.C.)
10111110
11000000
11000000
00111110
11000000
0010111 0
START
(N.O.)
START
(N.C.)
3 - OPERATOR WIRING ON CONTROL UNIT
4 - CONTROL UNIT POWER SUPPLY
U 10A
I , UPS .800VA
F
P !
5 - INPUTS STATUS
PHOTOCELL 1
(N.C.)
PHOTOCELL 1
(N.C.)
PHOTOCELL 1
(N.O.)
PHOTOCELL 1
(N.O.)
8
7
6
5
4
3
2
1
CN2
= NEUTRAL M1
= OPENING M1
= CLOSING M1
1 (NM1)
2 (OPM1)
3 (CLM1)
MOTOR 1 (230V)
M
M1
~
~
Capacitor
= NEUTRAL M2
= OPENING M2
= CLOSING M2
4 (NM2)
5 (OPM2)
6 (CLM2)
MOTOR 2 (230V)
M
~
Capacitor
NM1 OPM1 CLM1 NM2 OPM2 CLM2
M2
~
I , M1; , M1
(EXAMPLE)
(EXAMPLE)
PARTIAL
START
PHOTOCELL 1
PHOTOCELL 2
SAFETY
EDGE 1
SAFETY
EDGE 2
MOTOR 1
OPENING
LIMIT
SWITCH
MOTOR 1
CLOSING
LIMIT
SWITCH
START
PARTIAL START
STOP
PHOTOCELL 1
PHOTOCELL 2
SAFETY EDGE 1
SAFETY EDGE 2
NOT IN USE
M1 OPENING LIMIT SWITCH
M1 CLOSING LIMIT SWITCH
M2 OPENING LIMIT SWITCH
M2 CLOSING LIMIT SWITCH
NOT IN USE
NOT IN USE
NOT IN USE
NOT IN USE
MOTOR 2
OPENING
LIMIT
SWITCH
MOTOR 2
CLOSING
LIMIT
SWITCH
S P S N.O. - A N.C.

Italiano
International registered trademark n. 804888
6 - «START» COMMAND QUICK LEARNING ON THE TX
HOLD PRESSED
5 SECONDS
HOLD PRESSED
5 SECONDS
EXIT
PRESS
BUTTON
STORED
ENGLISH
ON
POWER ON
UP
CLOSE
OPEN
CLOSE
5
ON
POWER ON
00111110
00111110
00111110
11110000
11110000
11110000
DOWN OK
-
-
-
-
-
-
-
-
-
-
-
-
SEA
SEA
SEA
MENU
MENU
MENU
SET
SET
SET
-
-
-
-
-
-
-
-
-
-
-
-
-
-
-
1
OFF
POWER OFF
2 3 4
POWER ON
ON
5
LEAVES ON HALFWAY LOCK
UP
03.01
UP
3
MOTOR OK
UP
DOWN
OK
OK
UP
UP
9
789
10
6
11
UP
ON
5
a
a
DANGER!
HAVE A QUALIFIED SERVICE PERSON TO CARRY OUT THE OPERATIONS IN SAFE CONDITIONS
7 - WORKING TIMES LEARNING
QUICK START - ONLY FOR SEA SLIDING OPERATORS
WORKING TIMES LEARNING PROCEDURE - MORE DETAILS ON TECHNICAL MANUAL
(EXAMPLE)
UNLOCK
(EXAMPLE)
(EXAMPLE)
(EXAMPLE)
(EXAMPLE)
CHOOSE THE MODEL
1-HYDRAULIC
PROGRAM-
MING
(EXAMPLE)
M2 CLOSES
M1 CLOSES
M1 OPENS
M2 OPENS
M2 CLOSES
M1 CLOSES
I
,
5:
REVERSE
MOTOR
! 1 5
T ;
F ,

SET DESCRIPTION DEFAULT NOTE
Italiano
Italian
English
English
Français
French
Español
Spanish
Dutch
Dutch
Start
Start
Partial opening
Partial opening
Relay To enable the Relay for 3 seconds
Stop
Stop
Bistable Stop
Pressed once, it stops the gate.
Pressed twice, it reactivates the START input
Latch opening
One impulse opens and keep open.
A second impulse restore the movement
Latch closing
One impulse closes and keep closed.
A second impulse restore the movement
Unlock
To store a command for unlocking the electric brake
Delete a transmitter
To delete a single transmitter (TX)
Move to EEP
To transfer the transmitters stored on the control unit to
the external EEPROM (MEM), if connected
Clear memory
To delete the full transmitters memory on the receiver
End
To exit the menu "transmitters"
1- Hydraulic
Hydraulic operators
2- Sliding Sliding operators
3- Reversible Sliding Reversible sliding operators
4- Mechanic Swing
Electro-mechanic swing operators
11- Cougar
Electro-mechanic swing operator
4
GATES NUMBER From 1 to 2 To set the number of motors to be managed 1
On
To reverse the opening with the closing and vice-versa
(both motors and limit-switches are reversed)
Off Off
Automatic
Automatic logic - automatic reclosing enabled
Open-stop-close-stop-open
Step by step type 1
Open-stop-close-open
Step by step type 2
2 button
Two buttons
Safety
Safety
Dead man
Dead man
5
REVERSE MOTOR
Off
6
LOGIC
Auto-
matic
2
TRANSMITTERS
Start
Partial
Opening
3
MOTOR
Mechanic
SWING 2 DG (R2F) - (R2BF) MENU FUNCTIONS TABLE
THE DESCRIBED FUNCTIONS ARE VALID FOR ALL SWING 2 DG VERSIONS, EXCEPT WHERE EXPRESSLY STATED
MENU
1
LANGUAGE
English

SET DESCRIPTION DEFAULT NOTE
Off
Semi-automatic logic enabled
(a START command opens and another START closes the
gate - automatic reclosing disabled)
1 240
To set a pause time (from 1 second to 4 minutes) before
the automatic reclosing
Off
The Start command is not accepted during pause
On
The Start command is accepted during pause
9
PROGRAMMING Off On To start the working times self-learning Off
10
TEST START Off On To give a Start command for testing the automation Off
13
LATCH PAUSE
Off On
If "ON" the operator complies with the pause time set
when the function "LATCH OPENING" is disabled. When
"OFF" the pause time set is not respected
Off
14
RESET
192
MOVE GATE 1 *
- - - -
193
MOVE GATE 1 *
- - - -
15
END
16
SPECIAL MENU
A count-down of 5 seconds will start by holding the UP button; at its end "INIT" will appear on the
display as confirmation of the control board reset
7
TIMER TO CLOSE
Off
8
START IN PAUSE
Off
MENU
Allows the movement of the gate in a temporary "dead man" mode
(for example to test the correct running of the motor)
HOLD UP PRESSED = THE GATE OPENS
HOLD DOWN PRESSED = THE GATE CLOSES
Allows the movement of the gate in a temporary "dead man" mode
(for example to test the correct running of the motor)
HOLD UP PRESSED = THE GATE OPENS
HOLD DOWN PRESSED = THE GATE CLOSES
* The command is accepted only at the end of the cycle or after a STOP command; it is not accepted during the cycle and
during the pause
Press OK to return to the display of the firmware version
and to the one of inputs state
Press OK to enter the special menu

SET DESCRIPTION DEFAULT NOTE
26
LEAF DELAY IN OPENING Off 6 Setting from OFF to 6 seconds 1,5
27
LEAF DELAY IN CLOSING Off 20 Setting from OFF to 20 seconds 2,5
28
OPENING TORQ 1 30% 100%
Motor 1 opening torque:
by increasing the torque, more strength will be required
to execute the inversion in case of obstacle.
with hydraulic motors the torque will be on 100%
75
29
CLOSING TORQ 1 30% 100%
Motor 1 closing torque:
by increasing the torque, more strength will be required
to execute the inversion in case of obstacle.
with hydraulic motors the torque will be on 100%
75
30
OPENING TORQ 2 30% 100%
Motor 2 opening torque:
by increasing the torque, more strength will be required
to execute the inversion in case of obstacle.
with hydraulic motors the torque will be on 100%
75
31
CLOSING TORQ 2 30% 100%
Motor 2 closing torque:
by increasing the torque, more strength will be required
to execute the inversion in case of obstacle.
with hydraulic motors the torque will be on 100%
75
32
ENCODER
On
(only if connected via LSE
management unit)
ON = Encoder enabled
OFF = Encoder disabled
(when OFF, the working times learnt are only shown)
Off
47 ENCODER PAR. M1 xxx.
48 ENCODER TOT. M1 xxx.
49 ENCODER PAR. M2 xxx.
50 ENCODER TOT. M2 xxx.
32
ENCODER Potentiometer
To enable the reading of the potentiometer
(only if connected via LE or LSE management unit)
Off
51 I.PAR.M1 *- - - - - - - -
52 I.AP.M1
From the value learned
to ± 100 pulses
53 I.CH.M1
From the value learned
to ± 100 pulses
54 I.PAR.M2 *- - - - - - - -
55 I.AP.M2
From the value learned
to ± 100 pulses
56 I.CH.M2
From the value learned
to ± 100 pulses
* While the partial impulses are displayed, it is possible to OPEN (by pressing UP) or CLOSE (by pressing DOWN) the operator
to verify the correct reading of the potentiometer
Impulses read by Encoder during operation (Motor 2)
Impulses stored during programming (Motor 2)
To show the current position of the potentiometer on the leaf moved
by Motor 2. This parameter is useful to see if the potentiometer is
correctly read
To show the impulses stored by the control unit when the leaf moved
by Motor 2 is fully open
To show the impulses stored by the control unit when the leaf moved
by Motor 2 is fully close
SPECIAL MENU
PRESS AT THE SAME TIME FOR 5 SECONDS TO ENTER OR TO EXIT THE SPECIAL MENU
THE DESCRIBED FUNCTIONS ARE VALID FOR ALL SWING 2 DG VERSIONS, EXCEPT WHERE EXPRESSLY STATED
SPECIAL MENU
Impulses read by Encoder during operation (Motor 1)
Impulses stored during programming (Motor 1)
To show the current position of the potentiometer on the leaf moved
by Motor 1. This parameter is useful to see if the potentiometer is
correctly read
To show the impulses stored by the control unit when the leaf moved
by Motor 1 is fully open
To show the impulses stored by the control unit when the leaf moved
by Motor 1 is fully close

SET DESCRIPTION DEFAULT NOTE
32
ENCODER Off
ON = Encoder enabled
OFF = Encoder disabled
(when OFF, the working times learnt are only shown)
Off
65 OPENING TIME M1 xxx.s
66 CLOSING TIME M1 xxx.s
67 OPENING TIME M2 xxx.s
68 CLOSING TIME M2 xxx.s
10% (Fast intervention)
99% (Slow intervention)
To adjust the Encoder or Potentiometer intervention time
on Motor 1 in opening
Off (Intervention excluded) Disabled
10% (Fast intervention)
99% (Slow intervention)
To adjust the Encoder or Potentiometer intervention time
on Motor 1 in closing
Off (Intervention excluded) Disabled
10% (Fast intervention)
99% (Slow intervention)
To adjust the Encoder or Potentiometer intervention time
on Motor 2 in opening
Off (Intervention excluded) Disabled
10% (Fast intervention)
99% (Slow intervention)
To adjust the Encoder or Potentiometer intervention time
on Motor 2 in closing
Off (Intervention excluded) Disabled
10% (Fast intervention)
99% (Slow intervention)
To adjust the reversing sensitivity during slowdown
Function available only with Encoder connected via LSE
management unit
Off
With potentiometer
To set the inversion time in slow-down from 0to 5
seconds (= 99%) - Function available only with
Potentiometer connected via LSE management unit
30%
(= 1,5s)
38
POTENTIOMETER
THRESHOLD
OPENING 1
39
POTENTIOMETER
THRESHOLD
CLOSING 1
40
POTENTIOMETER
THRESHOLD
OPENING 2
41
POTENTIOMETER
THRESHOLD
CLOSING 2
42
POTENTIOMETER
SLOWDOWN THRESHOLD
IN OPENING M1
43
POTENTIOMETER
SLOWDOWN THRESHOLD
IN CLOSING M1
44
POTENTIOMETER
SLOWDOWN THRESHOLD
IN OPENING M2
45
POTENTIOMETER
SLOWDOWN THRESHOLD
IN CLOSING M2
0 100
To adjust the threshold of the potentiometer intervention
in slowdown. By default this value is set on 10. but can be
manually increased on the condition that the set value is
higher than the value shown in VP1 or VP2
(instantaneous speed values which can be shown by
accessing the DEBUG menu)
It
depen
ds on
model
34
CLOSING SENSITIVITY
MOTOR 1
Off
37
SLOWDOWN
SENSITIVITY MOTOR
To display the learnt value during the working times self learning, in
opening and closing (Motor 1) . With UP or DOWN it is possible to
increase or reduce the working times
33
OPENING SENSITIVITY
MOTOR 1
Off
SPECIAL MENU
To display the learnt value during the working times self learning, in
opening and closing (Motor 2) . With UP or DOWN it is possible to
increase or reduce the working times
35
OPENING SENSITIVITY
MOTOR 2
Off
36
CLOSING SENSITIVITY
MOTOR 2
Off
0 1000
To adjust the threshold of the potentiometer
intervention. This parameter self-determines during the
working times learning but can also be adjusted later, on
the condition that the set value is higher than the value
shown in VP1 or VP2 (instantaneous speed values which
can be shown by accessing the DEBUG menu). NOTE: The
lower the threshold value, the slower will be the
response of the potentiometer.
It
depen
ds on
model

SET DESCRIPTION DEFAULT NOTE
Total
In case of obstacle or safety edge it totally reverses the
movement during closing. If the automatic reclosing is
enabled (automatic logic) , it is attempted for 5 times
Partial
In case of obstacle, safety edge or potentiometer, it
partially reverses direction (of about 30 cm) then stops
59
OPENING
SLOWDOWN 1
Off (*) 50% Hydraulic
Adjustable from Off to the 50% of the stroke.
On hydraulic operators, the slowdown is automatically
set to "Hydraulic" if value exceeds the 50%
It
depends
on model
60
CLOSING
SLOWDOWN 1
Off (*) 50% Hydraulic
Adjustable from Off to the 50% of the stroke.
On hydraulic operators, the slowdown is automatically
set to "Hydraulic" if value exceeds the 50%
It
depends
on model
61
OPENING
SLOWDOWN 2
Off (*) 50% Hydraulic
Adjustable from Off to the 50% of the stroke.
On hydraulic operators, the slowdown is automatically
set to "Hydraulic" if value exceeds the 50%
It
depends
on model
62
CLOSING
SLOWDOWN 2
Off (*) 50% Hydraulic
Adjustable from Off to the 50% of the stroke.
On hydraulic operators, the slowdown is automatically
set to "Hydraulic" if value exceeds the 50%
It
depends
on model
63
DECELERATION 0 %
100%
To adjust the change from normal speed to slowdown
speed
100%
64
ACCELERATION 0 %
100%
Acceleration ramp.
To adjust the motor start 100%
Off
To disable the anti-overlapping control of the leaves
allowing their separate control
On
To enable the anti-overlapping control of the leaves
70
OPENING POSITION
RECOVERY
0 20 seconds
To retrieve the inertia of the motor in opening after the
Stop or the reversing
1s
71
CLOSING POSITION
RECOVERY
0 20 seconds
To retrieve the inertia of the motor in closing after the
Stop or the reversing
1s
72
OPENING TOLERANCE
MOTOR 1
0 100
To adjust the Motor 1 tolerance between the stop and
the obstacle, in opening
80
73
CLOSING TOLERANCE
MOTOR 1
0 100
To adjust the Motor 1 tolerance between the stop and
the obstacle, in closing
80
74
OPENING TOLERANCE
MOTOR 2
0 100
To adjust the Motor 2 tolerance between the stop and
the obstacle, in opening
80
75
CLOSING TOLERANCE
MOTOR 2
0 100
To adjust the Motor 2 tolerance between the stop and
the obstacle, in closing
80
Time
Pushing Off - 3 sec
Stroke
Before opening, the motor starts in closing for the time
set, in order to simplify the lock release
Repeat
Lock Off – On
Release
If ON, the lock will be released both before and after the
pushing stroke
End
To exit the menu
* For motors with hydraulic brake (CF) or double hydraulic brake (2CF) this parameter must be on Off
For menus 65 - 66 - 67 - 68 see menu 32- ENCODER = Off
76
PUSHING STROKE
Off
SPECIAL MENU
69
ANTI OVERLAP
Off
46
CLOSING INVERSION
Partial
For menus 47 - 48 - 49 - 50 see menu 32- ENCODER = On
For menus 51 - 52 - 53 - 54 - 55 - 56 see menu 32- ENCODER = Potentiometer

SET DESCRIPTION DEFAULT NOTE
77 LOCK TIME Off 5 seconds To adjust the lock release time from 0 to 5 seconds 3
Only opening
Lock enabled only before opening
Only closing
Lock enabled only before closing
Opening and closing
Lock enabled before opening and closing
Only opening
Only closing
Opening and closing
Off
Off
Opening and closing
Only closing
Only opening
81
PERIODICAL PUSHOVER Off 8h
To activate the repetition of the pushover function at a
time distance adjustable from 0to 8 hours, at hourly
intervals
Off
Opening 1 Off - 3 s
Closing 1 Off - 3 s
Opening 2 Off - 3 s
Closing 2 Off - 3 s
End
83
EXTRA TIME * 0.0 s 10 s
If the limit switches are installed, it is possible to add an
extra time (max. 10 seconds) to the movement of the
operator after the reading of the limit switches
0.0 s
84
BRAKE Off 100% To adjust the braking on the limit switch Off
Only closing
To enable the pre-flashing only before closing
(to access: press DOWN button when 0.0 value is shown)
0.0 5.0 s To set the pre-flashing duration
Normal
Normal
Light
Warning lamp function
Always
Always ON
Buzzer
Buzzer
Off
The flashing light will be OFF with enabled timer and open
gate
On
The flashing light will be ON with enabled timer and open
gate
Off
Disabled
1 240
Adjustable from 1 second to 4 minutes
In cycle
Courtesy light only in cycle
89
TRAFFIC LIGHT
RESERVATION
Off On
To get the priority in entry or exit. The function is
available only with SEM management unit and by the
use of the partial opening contact
Off
90
PARTIAL OPENING 20 100 Adjustable from 20 to 100 100
87
FLASHING LIGHT AND
TIMER
Off
88
COURTESY LIGHT
In cycle
85
PRE-FLASHING
Off
86
FLASHING LIGHT
Normal
80
PUSHOVER
The gate leaf makes an extra movement at the maximum
torque to ensure the tightening of the gate
Off
82
MOTOR RELEASE
If different from OFF, the operator slightly reverses its
direction at the end of the cycle
Off
(hydraulic)
0.1
(mechanic)
79
ANTI INTRUSION
If the gate is forced manually, the control unit starts the
motor and restores the state of the gate before forcing
(function only available if limit switches are installed)
Off
* Only if the operator is equipped with hydraulic slowdown and one or more slowdown-menus (from 59 to 62) are set to
"HYDRAULIC" (EXTRA TIME will be applied to the operator and to the moving direction of the menu set to "HYDRAULIC")
SPECIAL MENU
78
LOCK
Opening
and
closing

SET DESCRIPTION DEFAULT NOTE
= Start
The pause time in partial opening is the same as in total
opening
Off
Disabled
1 240
Adjustable from 1 second to 4 minutes
Off
On photo2
On partial input
Always
AUX output always powered
In cycle
AUX output powered only during cycle
Opening
AUX output powered only during opening
Closing
AUX output powered only during closing
In pause
AUX output powered only during pause
Positive brake
management (via relay)
Positive Electric-brake - connected via relay
(AUX output powered only with stationary gate)
Negative brake
management
(connected via relay)
Negative Electric-brake - connected via relay
(AUX output powered during cycle and 1 second before
starting the movement)
Open gate
warning light
(connected via relay)
1 flash per second during opening
2 flashes per second during closing
Steady lit in "Stop" or "Open" status
Start 3 s
(connected via relay)
AUX output powered at every Start input or at every
photocells or safety edge intervention, for 3 seconds
(ie. management of lights connected via relay)
Photo 1
Self-test enabled only on photocell 1
Photo 2
Self-test enabled only on photocell 2
Photo 1 and 2
Self-test enabled on photocells 1 and 2
Off
Disabled
Closing
If the photocell is occupied during closing, the gate
reverses the movement; If the photocell is occupied
during the pause, it prevents the gate reclosing
Opening and closing
If the photocell is occupied during opening or closing, it
stops the gate movement; when the photocell is released,
the movement continues
Stop
If the photocell is occupied before the Start input, the
Start will be ignored. If the photocell is occupied after the
Start input, the photocell will be ignored. If the photocell
is occupied during closing, the gate will reopen
Stop and close
If the photocell is occupied during closing, it stops the
gate movement; when released, the closing movement
continues
Close
The photocell stops the gate until it is occupied in both
opening and closing; when released, it send a closing
input (the gate closes 1s after the photocell release)
Pause reload
If the photocell is occupied during opening or closing, it
stops the gate movement; when released, the movement
continues. If the photocell is occupied during the pause, it
recharges the pause time set
Delete pause time
If the photocell is occupied during opening, pause or
closing, the gate reopens completely and closes without
observing the pause time set
94
24V AUX
(Max. 500 mA)
The AUX output allows
the connection of a relay
for the additional
accessories management
Always
95
PHOTO-TEST
Off
97
PHOTOCELL 1
Closing
91
PARTIAL PAUSE
= Start
92
TIMER
The selected input will be turned into an input (on CN1)
to which connect an external clock
Off
SPECIAL MENU

SET DESCRIPTION DEFAULT NOTE
Closing
If the photocell is occupied during closing, the gate
reverses the movement; If the photocell is occupied
during the pause, it prevents the gate reclosing
Opening and closing
If the photocell is occupied during opening or closing, it
stops the gate movement; when the photocell is released,
the movement continues
Stop
If the photocell is occupied before the Start input, the
Start will be ignored. If it is occupied after the Start input,
the photocell will be ignored. If the photocell is occupied
during closing, the gate will reopen
Stop and close
If the photocell is occupied during closing, it stops the
gate; when released the closing movement continues
Close
The photocell stops the gate until it is occupied in both
opening and closing; when released, the photocell gives a
closing command (the gate closes one second after the
photocell release)
Pause reload
If the photocell is occupied during opening or closing, it
stops the gate movement; when released, the movement
continues. If the photocell is occupied during the pause, it
reloads the pause time set
Pause reload
Photo closing
If the photocell is occupied during the pause, it reloads
the pause time set. If the photocell is occupied during
closing, the gate reverses the movement
Delete pause time
If the photocell is occupied during opening, pause or
closing, the gate reopens completely and closes without
observing the pause time set
Stop and open
If the photocell is occupied during opening, the gate will
stop; when released, the gate continues the opening
movement. The photocell is ignored during closing
Safety edge 2
It is possible to connect a second safety edge; it is
possible to choose the working direction of the second
safety edge through the menu 103
Normal Standard safety edge - N.C. contact
8K2
Safety edge protected by a 8K2 resistor enabled
Normal Standard safety edge - N.C. contact
8K2 N.C. Safety edge protected by a 8K2 resistor enabled
8K2 N.C. Double Two safety edges protected by 8K2 resistor enabled
8K2 RES Resistive edge protected by 8K2 resistor enabled
8K2 RES Double Two resistive edges protected by 8K2 RES enabled
Opening and closing
Safety edge enabled in opening and closing
Only opening
Safety edge enabled only in opening
Only closing
Safety edge enabled only in closing
Opening and closing
Safety edge enabled in opening and closing
Only opening
Safety edge enabled only in opening
Only closing
Safety edge enabled only in closing
103
SAFETY EDGE 2
DIRECTION
Menu available only if
the menu 98 is set on
"SAFETY EDGE 2"
Opening
and
Closing
100
SAFETY EDGE 1
Menu available on
model R2F only
Normal
SAFETY EDGE 1
Menu available on
model R2BF only
SPECIAL MENU
98
PHOTOCELL 2
Opening
and
Closing
102
SAFETY EDGE 1
DIRECTION
Opening
and
Closing

SET DESCRIPTION DEFAULT NOTE
Automatic
Automatic detection of the limit switch
Only opening
Limit switch enabled only in opening
Only closing
Limit switch enabled only in closing
Motor internal
To be enabled if the operator is equipped with an inner
limit switch that stops the motor phase
106
DIAGNOSTICS 1 10 To display the last event (See alarms table) - - - -
107
MAINTENANCE CYCLES 100 240000 Adjustable from 100 to 240000 cycles 100000
108
PERFORMED CYCLES 0 240000
To display the executed cycles.
Hold pressed OK to reset the cycles
0
112
PASSWORD
Note: "0000" setting is
not allowed
To enter a password for blocking the control unit
parameters modification
- - - -
SEM 2
The SEM 2 management unit can be connected to the EXP
input
Relay A relay unit can be connected to the EXP input
116
REPEAT LEAF DELAY On Off
In case of a STOP command when the gate is halfway, the
leaves will repeat the "leaf delay" set (menu 26-27)
On
Off Disabled
Opening
The gate opens and stay open till a new Start input.
The latch function uses the "Partial Opening" N.O. input
(the "Partial Opening" function is so disabled)
Closing
The gate closes and stay closed till a new Start input.
The latch function uses the "Partial Opening" N.O. input
(the "Partial Opening" function is so disabled)
119
DISPLAY WRITING
SPEED From 30% to 100% See Note 2 at the end of the table 80%
120
BASIC MENU
Normal Standard photocell without 10K control
Photo 1 10K Photocell with 10K control
Normal Standard photocell without 10K control
Photo 2 10K Photocell with 10K control
Start 3s
To enable the Relay for 3 seconds at every Start or
reopening command
Off Disabled
190
BASIC MENU
On model R2BF only
114
EXP MANAGEMENT
SEM2
Press OK to exit the special menu.
The special menu switches off automatically after 20 minutes
Note 1: after initialization, the parameters set on menu 3 - MOTOR and 104 - SELECT LIMIT SWITCH always remain set to the
value chosen during the programming operation
Note 2: if the menu 119 - DISPLAY WRITING SPEED is set to the minimum value of 30%, the display writing speed will be low. On
the contrary, if it is set to the maximum value of 100%, the writing speed will be very high
Please note: the writing speed will not change on the JOLLY 3 programmer
Press OK to exit the special menu.
The special menu switches off automatically after 20 minutes
121
PHOTO 1 TYPE
Menu available on
model R2BF only
Normal
122
PHOTO 2 TYPE
Menu available on
model R2BF only
Normal
118
LATCH
Off
132
RELAY
Menù visibile solo sul
modello R2BF
Start 3s
104
SELECT LIMIT SWITCH
Auto-
matic
SPECIAL MENU

SEA S.p.A.
Zona Industriale Sant’Atto - 64100 - Teramo - ITALY
Tel. +39 0 861 588341 r.a. Fax +39 0 861 588344
www.seateam.com
International registered trademark n. 804888
Other manuals for SWING 2 DG R2F
1
This manual suits for next models
1
Table of contents
Other SEA Control System manuals
Popular Control System manuals by other brands
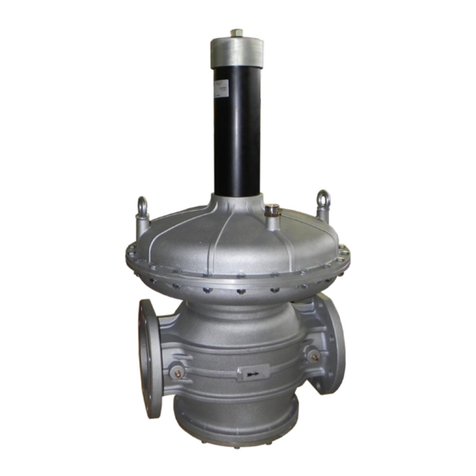
Madas
Madas RG/2M manual

LED World
LED World WiFi-104 installation instructions
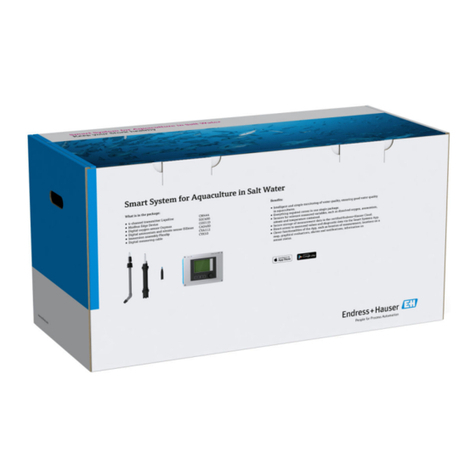
Endress+Hauser
Endress+Hauser Smart System SSP200B operating instructions
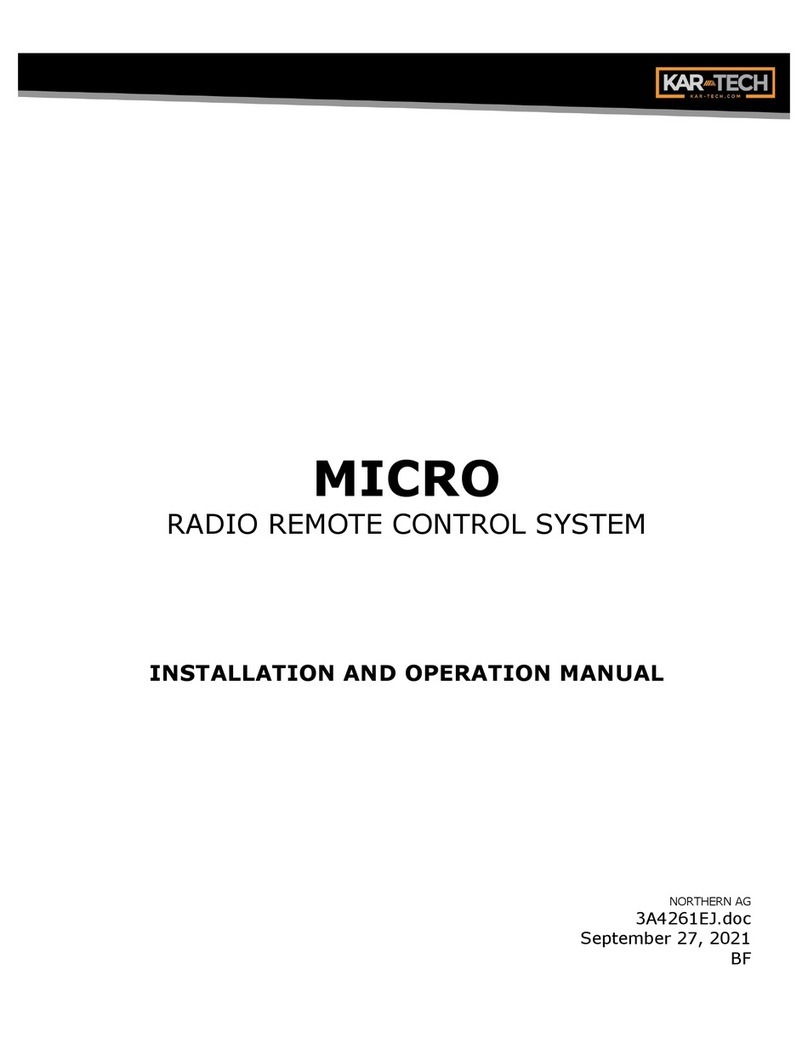
KAR-TECH
KAR-TECH MICRO Installation and operation manual
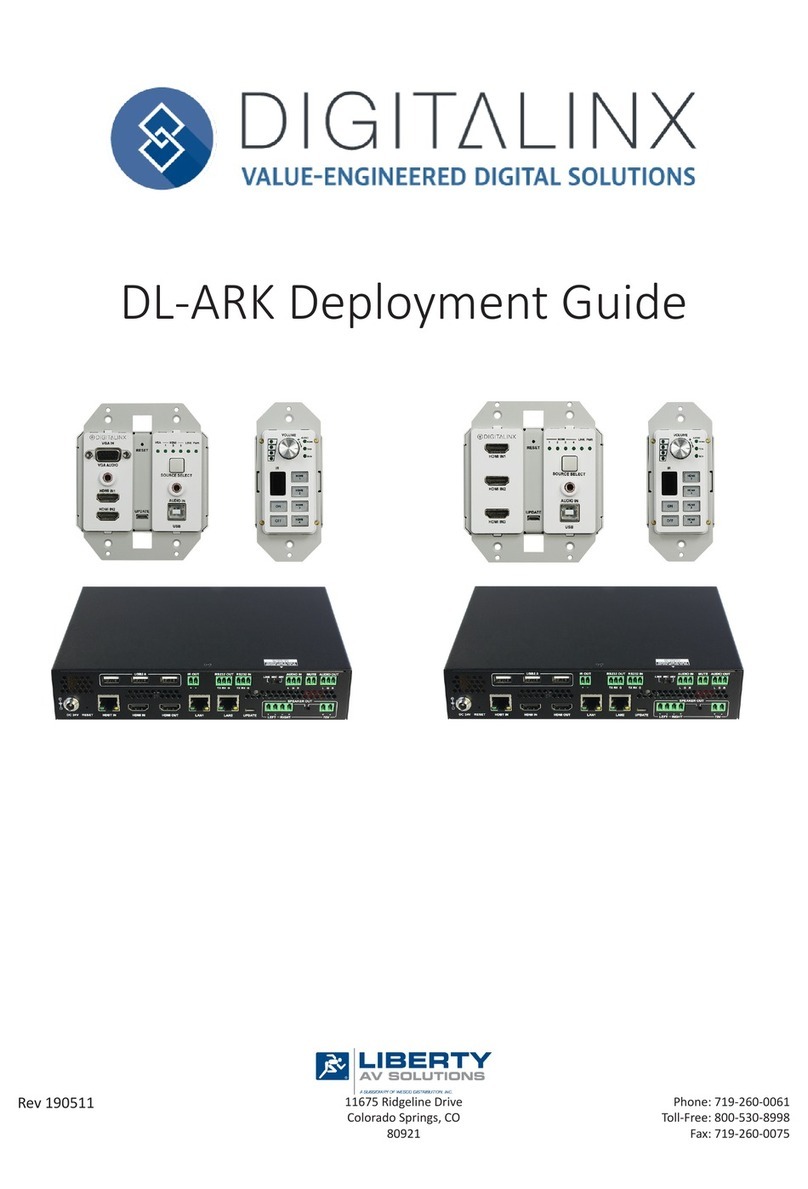
DigitaLinx
DigitaLinx DL-ARK Deployment guide

Hitachi
Hitachi YUTAKI M Installation & operation manual