SeaBotix LBV150 User manual

Title:
LBV150
Revision:
B
Revision Date:
27 Jan 10
Document Number:
DOCS- 001
©2009 SeaBotix Inc., all rights reserved
User’sManual
ProprietaryNotice:
Wordsandlogosmarkedwith®or™areregisteredtrademarksortrademarksoftheirrespectiveowners.Nolicenseunderanycopyright,
trademark,patentorotherintellectualpropertyrightofSeaBotixoranythirdpartyaregrantedbyimplicationinconnectiontherewith.This
DocumentisbeingfurnishedinconfidencebySeaBotixInc.ThisDocumentandtheinformationdisclosedhereinareproprietarydataof
SeaBotixInc.NeitherthisDocumentnortheinformationcontainedwithinshallbeused,reproduced,ordisclosedtothirdpartieswithoutthe
expresswrittenauthorizationofSeaBotixInc.UseofthisDocumentforotherthantheintendedpurposeisstrictlyprohibited.
Head Office: SeaBotix Inc., 2877 Historic Decatur Road STE 100, San Diego, CA 92106 USA +1 (619) 450-4000
Australia Office: SeaBotix Australia Pty Ltd.8A Sparks Road, Henderson, WA 6166, Australia +61 (0)8 9437-5400

Table of Contents
Using this manual............................................................................................ 5
Purpose of this manual................................................................................... 5
Confidential Information................................................................................. 6
Proprietary Notice ........................................................................................... 6
International Hazard Symbol.......................................................................... 6
Other safety symbols...................................................................................... 7
Safety Overview............................................................................................... 7
General Safety Overview................................................................................. 7
Summary of Danger, Warning and Caution Safety Messages..................... 8
Potential Hazards ............................................................................................ 8
Thruster Propellers ......................................................................................... 9
Electrical Shock............................................................................................... 9
Testing ........................................................................................................ 9
Design and Documentation Changes............................................................ 9
Section 1: Introduction................................................................................. 10
1.1 Unpacking System........................................................................ 10
1.2 Power Requirements .................................................................... 11
1.3 Setting up System......................................................................... 11
1.3.1 LBV............................................................................................... 11
1.3.2 Integrated Control Console........................................................... 13
1.4 Pre-Dive Inspection and System Test........................................... 13
1.4.1 Inspection ..................................................................................... 14
1.4.2 Powering up the system................................................................ 15
1.4.3 Testing system.............................................................................. 15
1.4.3.1 Thrusters....................................................................................... 15
1.4.3.2 Camera(s)..................................................................................... 16
1.4.3.3 Video Overlay............................................................................... 16
1.4.3.4 Accessories .................................................................................. 16
1.5 Post Dive Inspection..................................................................... 17
1.6 Storage of System ........................................................................ 17
1.7 Trimming ROV.............................................................................. 17
1.8 Calibrating Compass .................................................................... 18
Section 2: LBV Controls............................................................................... 20
2.1 Operator Control Unit (OCU) ........................................................ 20
2.1.1 Joystick......................................................................................... 20
2.1.2 Proportional Vertical Thruster Control Knob ................................. 20
2.1.3 VERTICAL GAIN .......................................................................... 21
2.1.4 HORIZ GAIN................................................................................. 21

2.1.5 TRIM............................................................................................. 21
2.1.6 AUTO HEAD................................................................................. 21
2.1.7 AUTO DEPTH............................................................................... 21
2.1.8 CAMERA ...................................................................................... 22
2.1.9 TILT .............................................................................................. 22
2.1.10 FOCUS......................................................................................... 22
2.1.11 LIGHT........................................................................................... 22
2.1.12 POWER........................................................................................ 22
2.1.13 POSITION..................................................................................... 22
2.1.14 ACCESSORIES............................................................................ 23
2.1.15 KEYPAD....................................................................................... 23
2.2 Video Overlay............................................................................... 24
2.2.1 Video Overlay Description ............................................................ 25
2.2.1.1 Thruster Gain Control ................................................................... 25
2.2.1.2 Trim function and Internal Light .................................................... 25
2.2.1.3 Heading ........................................................................................ 25
2.2.1.4 Turns counter................................................................................ 25
2.2.1.5 Depth............................................................................................ 25
2.2.1.6 Camera Angle............................................................................... 26
2.2.1.7 Temperature................................................................................. 26
2.2.1.8 Time.............................................................................................. 26
2.2.1.9 Date.............................................................................................. 26
2.2.2.0 User Text...................................................................................... 26
2.3 MENUS......................................................................................... 27
2.3.1 Quick Menu................................................................................... 27
2.3.2 Main Menu.................................................................................... 27
2.3.3 Setup Menu .................................................................................. 28
2.3.4 Calibrate Menu ............................................................................. 29
2.3.5 Diagnostics Menu......................................................................... 31
2.3.6 Options Menu ............................................................................... 31
Section 3: Operating the LBV...................................................................... 33
3.1 Operating Environment................................................................. 33
3.2 Deployment................................................................................... 33
3.3 Tether ........................................................................................... 33
3.4 Piloting.......................................................................................... 33
3.5 Practice......................................................................................... 34
3.5.1 Watching LBV............................................................................... 34
3.5.2 Watching Monitor.......................................................................... 35
3.6 Controlling the LBV....................................................................... 35
3.7 Thruster Gain Control ................................................................... 35
3.8 Trim............................................................................................... 36
3.9 Auto Functions.............................................................................. 36
3.10 Limitations..................................................................................... 36

Section 4: Maintenance................................................................................ 37
4.1 After each use............................................................................... 37
4.1.1 After each use – dirty water conditions......................................... 37
4.1.2 Every 50 hours.............................................................................. 41
4.2 Every 500 hours............................................................................ 43
4.3 Long term...................................................................................... 43
4.4 Repairs ......................................................................................... 43
4.5 Software........................................................................................ 44
4.6 Optional Components................................................................... 44
Section 5: Troubleshooting ......................................................................... 45
5.1 Introduction................................................................................... 45
5.2 Brief Theory of Operation.............................................................. 45
5.3 Troubleshooting Aids.................................................................... 46
5.4 Proper Operating Conditions ........................................................ 47
5.5 Failure Modes............................................................................... 48
Glossary of Abbreviations............................................................................ 51
Sales Terms and Conditions & 24-Month Limited Warranty...................... 54
Limitations and Exclusions.......................................................................... 61
Shipping and Return Material Authorization (RMA) Forms ....................... 61
Allocation of Risks ........................................................................................ 62
APPENDIX BY ALPHABET............................................................................ 63

DOCS-001 Manual, SeaBotix Inc. Users, 150 – 200 Series - Rev B – 27 Jan 10 - Page 5 of 64
IMPORTANT…
Read this manual prior to operation.
Using this manual
This manual has been prepared and published by SeaBotix, Inc. to aid our customers,
dealers and service personnel when operating or servicing the products described
herein. SeaBotix, Inc. constantly strives to improve all of its products. We review the
information in this document regularly and we welcome any suggestions for
improvement. In concert with our policy of continuous improvement, SeaBotix, Inc.
reserves the right to make changes to this manual, or to the equipment, without prior
notification.
Read this manual before using this product. Failure to follow the instructions and
safety precautions in this manual can result in serious injury or death. Keep this
manual in a safe location for future reference.
Before operating the equipment, read this manual thoroughly to understand safe and
proper use of the equipment and all applicable safety messages. There are potential
safety hazards associated with the operating environment and with the operation of this
equipment. SeaBotix Inc. will not be held liable for negligent or unsafe operation. It is
your responsibility to make this document available to others that will operate or
maintain this product.
Purpose of this manual
The purpose of this manual is to provide LBV operators with a clear
understanding of the proper installation, operation, maintenance and safe
operating procedures. This manual is a valuable reference tool and should be
thoroughly reviewed prior to the operation of the LBV. If you feel that any portion
of this manual is unclear or if you do not thoroughly understand the operation of
the equipment, please contact SeaBotix, Inc. or an Authorized Distributor or
Authorized Service Center for more detailed information.
Before operating the LBV, it is important to read this manual thoroughly to
understand the proper use and precautions required for its safe operation.
Throughout this manual information of special interest is highlighted with the
following symbols. Be sure to read and understand each of these important
messages.

DOCS-001 Manual, SeaBotix Inc. Users, 150 – 200 Series - Rev B – 27 Jan 10 - Page 6 of 64
Confidential Information
Confidential information is information proprietary to SeaBotix, Inc. such as know-how,
trade secrets, or non-public business information, whether or not reduced to writing or
other tangible form, which must not be divulged without permission. It is any and all
information, whether commercial or technical, used by a business to obtain an
advantage over competitors or customers, including without limitation, know-how, data,
processes, designs, formulas, photographs, drawings, specifications, software
programs, samples and business information, provided the information:
a) Is not generally known to the relevant portion of the public
b) Confers economic benefit to its holder (where this benefit must derive
specifically from its not being generally known, not just from the value of the
information itself);
c) Is the subject of reasonable efforts to maintain its secrecy
Proprietary Notice
Words and logos marked with ® or ™ are registered trademarks or trademarks of their
respective owners. No license under any copyright, trademark, patent or other
intellectual property right of SeaBotix, Inc. or any third party are granted by implication
in connection therewith. This document is being furnished in confidence by SeaBotix,
Inc. This document and the information disclosed herein are proprietary data of
SeaBotix, Inc. Neither this document nor the information contained within shall be used,
reproduced, or disclosed to third parties without the express prior written authorization
of SeaBotix, Inc. Use of this document for other than the intended purpose is strictly
prohibited.
Manual Download
Please check our website at www.SeaBotix.com to download the most current revision
of this manual.
International Hazard Symbol
An internationally recognized symbol that indicates a potential personal injury hazard; it
is not used for Safety Messages related only to equipment or data damage. The symbol
is depicted by a black triangle with yellow background, a black exclamation point in the
center and an optional yellow border. All Safety Messages that contain this sign
shall be obeyed to avoid possible harm. The General Warning Sign is defined in ISO
7010 – 2003, Graphical symbols — Safety colors and safety signs — Safety signs used
in workplaces and public areas. The Safety Alert Symbol defined in ANSI Z535.6,
Product Safety Information in Product Manuals, Instructions, and Other Collateral
Materials, is consistent with the ISO 7010 General Warning Sign.

DOCS-001 Manual, SeaBotix Inc. Users, 150 – 200 Series - Rev B – 27 Jan 10 - Page 7 of 64
Other safety symbols
Important
NOTE: Information marked with this symbol is designed to help with
the operation of the LBV by providing additional useful operating tips or
facts.
CAUTION: This symbol indicates a potential for harm and special
care must be taken.
Safety Overview
The most current revision of this manual is available online. Caution should be taken not
to rely entirely on printed copies due to ongoing improvements, updates or changes.
Printed copies should be checked against the online version to insure the latest
information is being used.
Nothing in this document is intended to supersede applicable (local, state, country,
federal, etc.) laws, regulations and standards or as directed by the Governing
Regulatory Body. In the event of conflict between this document and applicable
legislative requirements, the legislative requirements shall prevail.
General Safety Overview
This section, and the safety messages throughout this document, is intended to raise
your awareness of potential risks and hazards and to help prevent accidents.
Personnel safety is a core business requirement for SeaBotix, Inc. and must be a
primary consideration during the set-up, operation or servicing of all SeaBotix, Inc.
products. Every effort has been made to ensure personnel safety at all times.
Failure to comply with all safety messages and instructions may result in
personal injury or equipment damage.

DOCS-001 Manual, SeaBotix Inc. Users, 150 – 200 Series - Rev B – 27 Jan 10 - Page 8 of 64
The severity of consequences ranges from frustration or poor equipment performance,
through damage to equipment, injury or death.
SeaBotix, Inc. products are safe and reliable tools when used and cared for properly.
However, certain hazards do exist and should be carefully considered.
It is impossible to anticipate all unexpected conditions that may occur, particularly in an
adverse and chaotic marine environment. This document is written for use by trained,
competent, experienced personnel who can reasonably be expected to exercise
common sense, good judgment and caution when working in the actual environment
and under the actual working conditions for which this equipment has been designed to
operate. Backup and/or supervisory personnel should be present when warranted by
work conditions. It is assumed that personnel are known to be able to work safely and
effectively in the demanding conditions frequently encountered in marine and offshore
environments. Furthermore, it is assumed that personnel have been trained in the
recommended service procedures of SeaBotix, Inc. products, including the use of
common hand tools and any special SeaBotix, Inc. tools that may be required.
During the use of SeaBotix, Inc. products it is the responsibility of each person to
ensure that safe work conditions exist, that they are working in a safe manner and to
anticipate any potential risks. If an unsafe or potentially unsafe condition exists, stop
work immediately until the unsafe condition is corrected. Whenever there is any doubt,
always err of the side of caution and stop work until it has been positively determined
that it is safe to continue working. Anyone who uses a service procedure and/or tool,
which are not recommended by SeaBotix, Inc. assumes all liability for the resulting risk
and must first completely satisfy himself that neither his safety nor the products safety
will be endangered.
If there is a language barrier that prevents you, or any other operator or service
personnel, from understanding the safety messages contained in this document, please
contact SeaBotix, Inc. for assistance in translating them into the appropriate language.
Summary of Danger, Warning and Caution Safety Messages
These are specific messages which relate to a danger, warning or caution
situation. READ THESE CAREFULLY AND PAY ATTENTION TO THEM
Potential Hazards
Although the LBV is a safe and reliable tool when used and cared for properly,
there are certain inherent safety hazards associated with the operation of the
LBV that should be reviewed and avoided. SeaBotix, Inc., and its distributors,
associates, and affiliates, cannot be held liable for any damages, injuries, losses
or problems whatsoever resulting from negligent operation, or an LBV system
that has been altered or modified without the prior written consent from SeaBotix,
Inc.

DOCS-001 Manual, SeaBotix Inc. Users, 150 – 200 Series - Rev B – 27 Jan 10 - Page 9 of 64
Thruster Propellers
Keep the propellers clear of obstructions at all times.
Do not put fingers or other objects near the propellers at any time.
Be careful with any loose clothing, jewelry, etc.
Electrical Shock
The LBV operates at high voltages that can cause injury and/or
death.
Keep the Surface Power Supply plug away from the water.
Check all plugs for the presence of water prior to connecting.
If the tether is cut, chafed, or otherwise damaged, do not operate the LBV.
Do not open the LBV housing when the power is on.
Testing
Each LBV system is carefully manufactured to ensure long term safe operation.
Prior to shipment every LBV is tested for proper operation, including pressure
testing to full operating depth. Should a defect be found contact SeaBotix, Inc.,
or an authorized distributor immediately at 619-450-4000 Ext. 124 or
Design and Documentation Changes
SeaBotix, Inc. reserves the right to make changes to the specifications of the
LBV and/or alter any documentation at any time, without notice, or may alter any
or all documentation without notice.

DOCS-001 Manual, SeaBotix Inc. Users, 150 – 200 Series - Rev B – 27 Jan 10 - Page 10 of 64
Section 1: Introduction
1.1 Unpacking System
Prior to removing the LBV and all components, locate a suitable area for operation.
Find an area that is comfortable, protected from harsh conditions and clear of potential
hazards.
Requirements for operation:
Suitable power source
Dry area
Contents of packaging:
LBV underwater vehicle
Integrated Control Console
Tether and/or Tether & reel
Spares/Tool Kit
Manual/CD ROM
Accessories (if applicable)
Note: When unpacking the LBV after receipt, inspect the LBV for damage. It
is strongly recommended that vacuum be verified before each use (see section
1.4.1.4, page 14).
LBV1502
URS250 ICC

DOCS-001 Manual, SeaBotix Inc. Users, 150 – 200 Series - Rev B – 27 Jan 10 - Page 11 of 64
1.2 Power Requirements
The LBV system is designed to operate from common power sources. When
establishing the correct power source for the LBV, be sure to consider what other
equipment might be used at the same time to avoid erratic power supply to the LBV.
The standard LBV fitted with SBT150 Brushed Thrusters requires 650 watts 100-
130/200-250 VAC, 50/60Hz. The power supply with the Integrated Control Console can
be configured internally to accept either 100-130 VAC or 200-250 VAC.
CAUTION: Do not plug an Integrated Control Console or Surface Power
Supply that is configured to 100-130 VAC into 200-250 VAC or vice versa.
This will damage the LBV system and may cause physical harm.
LBV systems fitted with the HPDC1502 Brushless DC Thrusters have a requirement
for 1200 watts at 100-130/200-250 VAC, 50/60 Hz.
1.3 Setting up System
Select a suitable area from which the LBV will be deployed and controlled. The area
should be dry and not in direct sunlight. Now the LBV is ready to be set up.
The first step is to connect the tether to the LBV.
Prior to connecting ensure that the power to the Integrated Control Console or the
Surface Power Supply is OFF.
1.3.1 LBV
Step 1
Position the LBV so that you can see the rear of the LBV.
Located at the upper right next to the flotation is a male
connector.
Step 2
Put a small amount of silicone lubricant (GLA001 which is
supplied with your order) on your finger.

DOCS-001 Manual, SeaBotix Inc. Users, 150 – 200 Series - Rev B – 27 Jan 10 - Page 12 of 64
Step 3
Apply a small amount of the silicone lubricant to the male
pins on the bulkhead connector. Silicone lubricant is simply
for lubrication and not a sealant.
Step 4
Locate the female tether connector and the strain relief.
Step 5
Open the shackle completely. NOTE: There is an indent to
allow the locking rod to be flush with the “D” portion of the
shackle.
Step 6
ALWAYS ATTACH THE SHACKLE PRIOR TO
ATTACHING THE TETHER
Slide the shackle over the pad eye on the flotation module.
Twist the locking rod to secure.
Step 7
Push the female connector onto the male bulkhead
connector, being careful to align the pins. There is a single
small pin used for alignment.
Step 8
Tighten the locking sleeve clockwise. Do not over tighten.
Once the tether is connected to the LBV, the next step is to connect the Integrated
Control Console. Again be careful that the Integrated Control Console is OFF.

DOCS-001 Manual, SeaBotix Inc. Users, 150 – 200 Series - Rev B – 27 Jan 10 - Page 13 of 64
1.3.2 Integrated Control Console
1) Ensure that the power switch is OFF (down position).
2) Engage the tether connector.
3) Plug the power cord into the side panel of the AC power port.
4) Plug the cable into a suitable power source.
NOTE: Do not use a Signal Conditioning Power Strip, or an Un-Interruptible
Power Supply (UPS) to provide power to the LBV.
5) There is an RS-232 connector which is used for “flashing” the LBV, SONAR
interface and/or tracking responder triggering.
1) Circuit Breaker
2) Red LED – POWER
3) Amber LED – STATUS
4) Video In
5) AUX Video Out
6) RS232 Connector
7) Tether Whip Connection
8) Power Input Connection
NOTE: Make sure that there is no water or debris on or in the connectors prior to
connecting.
1.4 Pre-Dive Inspection and System Test
Before placing the LBV in the water, it is important to ensure that all systems operate as
they are supposed to. This process should be done each time the LBV is operated and
will only take a moment to perform.

DOCS-001 Manual, SeaBotix Inc. Users, 150 – 200 Series - Rev B – 27 Jan 10 - Page 14 of 64
1.4.1 Inspection
1. Visually look over the LBV for obvious damage. Look at the view port, seals,
thrusters etc. for obvious damage.
2. Check the tether for damage.
3. Check the thrusters for objects that may get or be caught in the propellers.
4. Check the vacuum before every dive.
The following page outlines the procedure for performing a vacuum seal check on the
primary LBV housing.
Step 1
Place the LBV on a table with the vacuum check valve
facing you.
Step 2
Remove the Phillips pan head seal screw from the vacuum
valve.
Step 3
Connect the vacuum hose and ensure that the fitting is
tight.
Step 4
Pull vacuum to 10 inches of mercury and hold for 10
minutes (watch for loss of vacuum). The gauge should
read the same after 10 minutes.

DOCS-001 Manual, SeaBotix Inc. Users, 150 – 200 Series - Rev B – 27 Jan 10 - Page 15 of 64
Step 5
Remove the vacuum tube.
Step 6
Insert and tighten the Phillips pan head seal screw into the
check valve.
CAUTION: Do not over tighten the seal screw as it
could damage the sealing o’ring.
1.4.2 Powering up the system
1. Turn on the Integrated Control Console or the Surface Power Supply power
switch.
a. The red LED should illuminate.
b. After 2 seconds the amber status light should illuminate.
2. Press the POWER button on the operator control console.
a. The red LED above the POWER button should illuminate.
b. The amber LED on the Surface Power Supply should begin to strobe 2
seconds on/off.
c. The camera video should come up on the monitor with Video Overlay.
3. The 12 VDC & 5 VDC LED’s on the Motherboard should illuminate.
4. The Data In/Out LED’s on the Motherboard should flash at a 2 Hz (twice per
second) rate.
5. The Power LED (red) on the sensor board should illuminate.
6. The status LED (amber) on the sensor board should strobe 2 seconds on/off.
7. The power LED (red) on the Video Overlay board should illuminate.
1.4.3 Testing system
1.4.3.1 Thrusters
1. Push the joystick forward and backwards checking to see that both the
forward thrusters move and cycle through speed range.
2. Push the joystick left then right to ensure that the lateral thruster operates
correctly.
3. Rotate the joystick left then right to ensure that the forward thrusters operate
correctly.

DOCS-001 Manual, SeaBotix Inc. Users, 150 – 200 Series - Rev B – 27 Jan 10 - Page 16 of 64
4. Rotate the vertical thruster knob (on the left side) to ensure that the vertical
thruster operates correctly.
5. Push and hold the VERT key while selecting 1-0 on the keypad to adjust the
gain control. The value will change on the Video Overlay.
6. Push the HORZ key while selecting 1-0 on the keypad to adjust the horizontal
thruster gain control. The value will appear on the Video Overlay.
NOTE: Do not run the thrusters for more than a few seconds at a time
with the LBV out of the water. Operating the thrusters for more than a
few seconds may cause damage to the motors and/or the shaft seals.
1.4.3.2 Camera(s)
1. Push TILT + and TILT – to rotate the camera chassis.
2. Push FOCUS + and FOCUS – to focus the camera.
3. Push CAMERA select button to switch to the optional second camera (if
fitted).
a. Test FOCUS + and FOCUS – on the second camera if fitted.
NOTE: The FOCUS function will not operate on a rear facing camera.
4. Push the LIGHT key to turn on the internal light.
5. Push + and – to vary the light intensity
a. Repeat with the second camera if fitted.
NOTE: Do not leave the light on for more than a few seconds when the
LBV is out of the water. Leaving the light on may cause damage to the
view port or the lighting control circuits.
1.4.3.3 Video Overlay
1. Check that the time is set correctly (page 25, section 2.2.1.8).
2. Calibrate that date is set correctly (page 25, section 2.2.1.9).
3. Calibrate the heading (page 24, section 2.2.1.3)
4. Check that the desired depth measurement is set correctly (page 24, section
2.2.1.5).
5. Check that the desired temperature is set correctly (page 25, section 2.2.1.7).
6. Input desired User Text (page 25, section 2.2.2.0).
1.4.3.4 Accessories
1. If fitted with accessories such as a grabber (page 25 section 2.3.1) and test
the and the keys to ensure that the grabber closes and opens.

DOCS-001 Manual, SeaBotix Inc. Users, 150 – 200 Series - Rev B – 27 Jan 10 - Page 17 of 64
1.5 Post Dive Inspection
After each use of the LBV, take a moment to do a visual inspection on the LBV prior to
storage. It is good practice to submerge the LBV into a container of fresh water or rinse
with a fresh water hose and wipe clean.
Check the LBV for any damage.
Check the thrusters for debris caught near or in the propellers.
Quickly check the LBV functions to ensure that all systems operate correctly.
Check for lost ballast strips or weights.
1.6 Storage of System
Proper storage of the LBV will make the next use much easier and keep the LBV in
good condition.
After rinsing the LBV and wiping off the excess water, disconnect the shackle and
unplug the tether.
Place the LBV in a carrying/shipping case. Disconnect all the connectors from the
Integrated Control Console or the Surface Power Supply.
Coil up all cables and store.
If the LBV is equipped with an ICC, place the operator control unit face down in its
storage tray.
Place the Surface Power Supply in a carrying/shipping case.
Place the operator control unit in a carrying/shipping case.
Coil the tether as described in “Tether section”, (page 30, section 3.3)
Place the tether in a carrying/shipping case.
Close and clamp cases closed for transport or storage.
1.7 Trimming ROV
The LBV is designed to be NEUTRALLY buoyant and when placed in the water should
maintain its depth without rapidly surfacing or sinking. From the factory, the LBV comes
trimmed per the sales order and a tag is affixed to the LBV notifying you of the status of
the trim. The use of the LBV in different salinity water or alteration of the system
hardware will affect buoyancy. Should your LBV require buoyancy adjustment follow
the procedures below. Refer to the Manufacturer Safety Data Sheet (MSDS) for
working with lead.
NOTE: If the LBV is positively buoyant or negatively buoyant, the vertical
thruster and the auto depth function will not be as effective or may not work at
all.

DOCS-001 Manual, SeaBotix Inc. Users, 150 – 200 Series - Rev B – 27 Jan 10 - Page 18 of 64
Step 1
Make sure that the tether is connected correctly as this
will affect the buoyancy and trim of the LBV.
Step 2
Place the LBV in the same type of water in which it will
be operated, i.e. fresh, salt or brackish water. While
holding the handle or bumper frame, turn the LBV upside
down and agitate the LBV to release any trapped air.
Step 3
Place the lead weight strip found in the basic spares kit
(BSK) on the bumper frame to achieve the desired
buoyancy. You may have to cut the strips to fine adjust
the trim. Make sure that the LBV is level left to right and
fore to aft.
Step 4
Once the LBV is neutral, straighten the lead strips and
attach to the lower portion of the bumper frame using
M5x10 button head screws. Be sure to place in the
same relative position to ensure that the LBV is properly
set up left to right and fore to aft.
1.8 Calibrating Compass
The LBV is fitted with a magnetic compass that is designed to provide basic heading
data. It should be noted that the sensor is fixed inside the LBV and therefore is
susceptible to varying environmental conditions. If the LBV is pitching up and down the
sensor will lose accuracy. Tilting the camera will also affect the heading display. To
ensure that the heading sensor provides the most accurate data, proper calibration is
critical.
Place the LBV either on a flat smooth stable surface or in still water. It is important that,
during calibration, the LBV does not pitch up or down. Access the calibration menu as
follows:
•Press PGRM
•Press 5 (Main Menu)
•Press 2 (Calibrate)
•Press 4 (Compass)

DOCS-001 Manual, SeaBotix Inc. Users, 150 – 200 Series - Rev B – 27 Jan 10 - Page 19 of 64
The on screen display will prompt that you “Rotate the LBV 360º and press Enter”. For
the initial calibration it is required to rotate the LBV 360º. The key to successful
calibration is that the LBV is level and rotated as slowly as possible. This may take
several minutes but ensures the most accurate reading. Once complete:
Press ENT
Press PGRM
NOTE: This calibration is required initially and is then stored into memory, however;
should the LBV be used in a different geographic location, re-calibration may be
required. It is good practice to calibrate the compass whenever time allows.

DOCS-001 Manual, SeaBotix Inc. Users, 150 – 200 Series - Rev B – 27 Jan 10 - Page 20 of 64
Section 2: LBV Controls
The LBV has been designed to be simple and intuitive to operate. A new user should
find that, after reading this manual and an hour or so of hands-on use, operating the
LBV is quite easy. Using the tips in this manual will help you to become a proficient and
confident LBV operator.
2.1 Operator Control Unit (OCU)
Operation of the LBV is done through the Operator
Control Unit (OCU). This section will help to explain the
use of each key and when each key should be used.
When first learning to operate the LBV, spend time with
the LBV at the surface where you can see how the
commands affect the LBV.
Holding the OCU correctly will help. The recommended
method is to hold the OCU in both hands with the left
hand using all fingers to support the console and the
thumb resting on the vertical thruster knob. Place the
right hand in such a way that the forefinger and thumb
holds the top of the joystick and the other three fingers
support the console. Some may prefer to place the
console on a flat surface.
2.1.1 Joystick
Pushing the joystick forward moves the LBV in the forward direction.
Pulling the joystick backwards moves the LBV in the reverse direction.
Moving the joystick laterally moves the LBV in the respective direction laterally.
Rotating the upper portion of the joystick rotates the LBV’s heading to port and to
starboard.
2.1.2 Proportional Vertical Thruster Control Knob
Located on the front left side of the operator control unit is the vertical thruster control
knob. Positioning your left thumb on top of the knob will allow you to easily rotate the
knob. Pushing the knob forward causes the LBV to surface and, conversely, sliding the
knob back causes the LBV to dive.
The control knob is variable and has a center detent turning the vertical thruster off.
Ensure that the vertical thruster is off prior to removing the LBV from the water.
Table of contents
Other SeaBotix Robotics manuals
Popular Robotics manuals by other brands
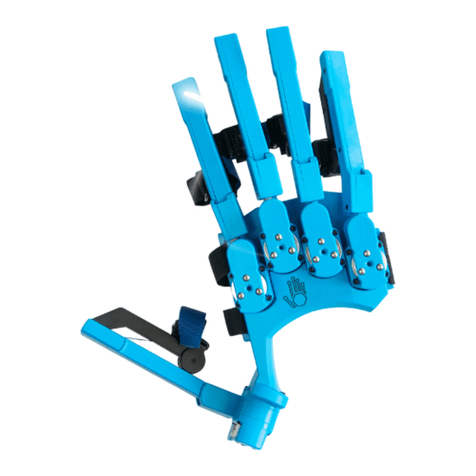
SenseGlove
SenseGlove DK1 Getting started

ez-wheel
ez-wheel SWD Core instruction manual
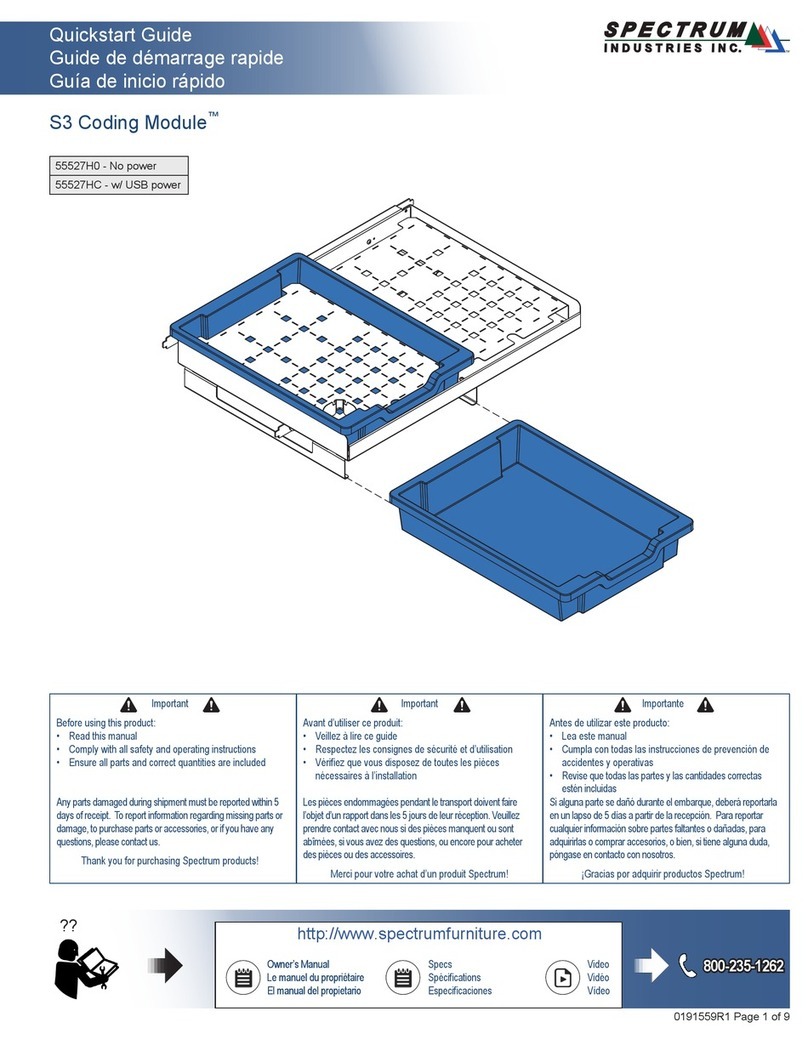
Spectrum Industries
Spectrum Industries S3 Coding Module 55527H0 quick start guide
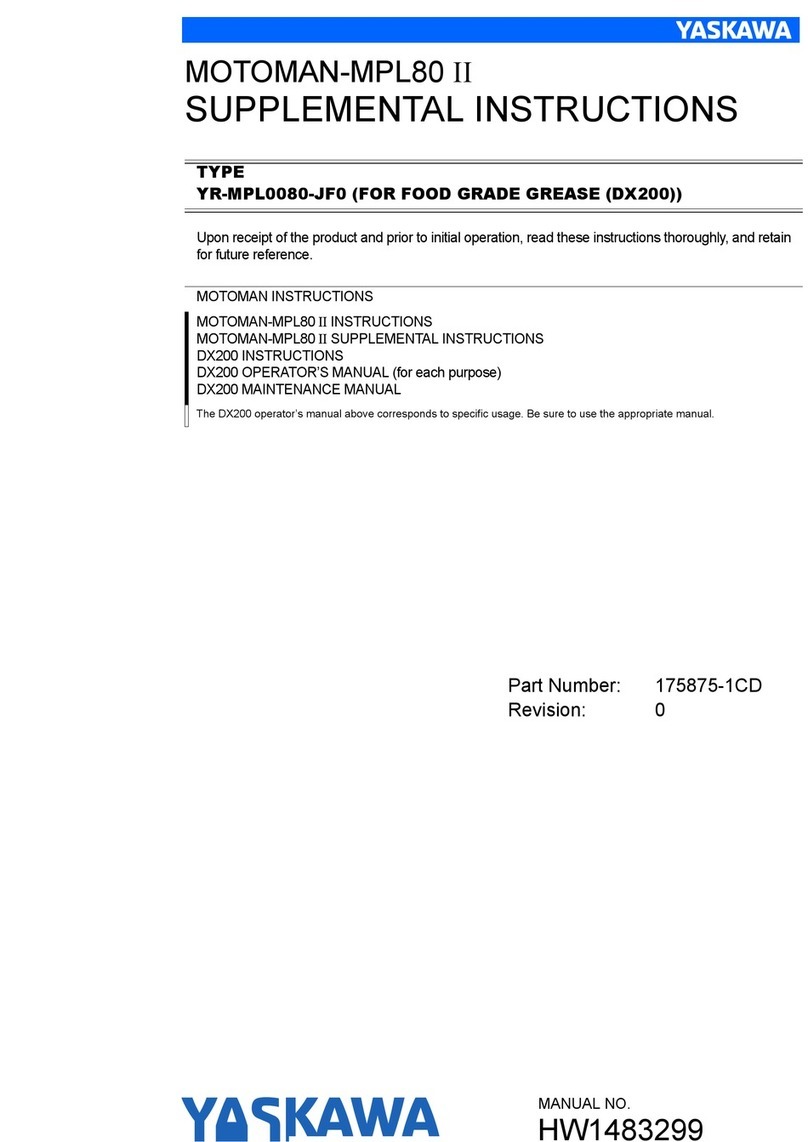
YASKAWA
YASKAWA MOTOMAN MPL80 II Supplementary instructions manual
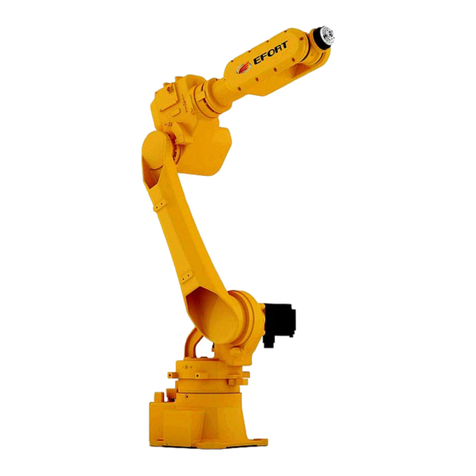
EFORT
EFORT ER20-1700 Quick operation manual
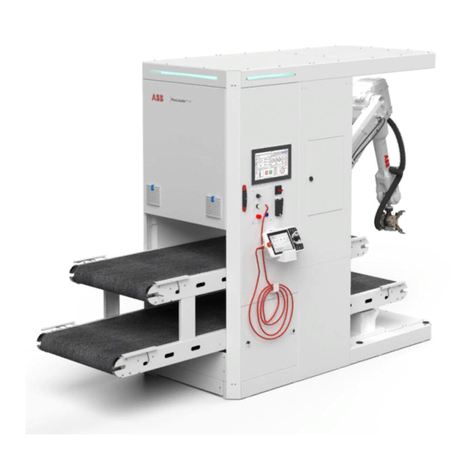
ABB
ABB FlexLoader Applications manual