SeaLand Mass Flow Meter User manual

Mass Flow Meter
Operation Manual
Standard: GB/T 31130-2014
Zhejiang System No. 03010003
Ver. V1.2

Attention
Please read this manual carefully before installation and operation. It is a detailed
introduction of configuration, design, specifications, installation, etc. of Sealand mass flow
meter.
The meter is produced according to National Regulation of Coriolis Mass Flow Meter
GB/T 31130-2014, approved & certified. Each sensor has its own paired transmitter.
Please do not change any component in case of failure.
Please cut off the power before installation. Keep junction box intact and wiring correct;
make sure no gasket, o-ring or holding screw missing, and electricity ex-proof device in
good condition during the installation.

Contents
Chapter 1 Specifications.....................................................................................................................1
1.1 Introduction....................................................................................................................................1
1.2 Operating principle.......................................................................................................................1
1.3 Features.........................................................................................................................................1
1.4 Operating conditions....................................................................................................................1
Chapter 2 Composition....................................................................................................................... 1
2.1 Mass flow sensor..........................................................................................................................1
2.1.1 Main parameters...................................................................................................................2
2.1.2 Dimension.............................................................................................................................. 2
2.2 Mass flow transmitter...................................................................................................................2
2.2.1 Main features.........................................................................................................................3
2.2.2 Dimension.............................................................................................................................. 3
Chapter 3 Installation...........................................................................................................................3
3.1 Installation steps........................................................................................................................... 3
3.2 Announcements............................................................................................................................4
3.2.1 Site selection......................................................................................................................... 4
3.2.2 Installation methods............................................................................................................. 4
3.2.3 Ground....................................................................................................................................4
3.2.4 Start........................................................................................................................................ 5
3.2.5 Others..................................................................................................................................... 5
Chapter 4 Wiring................................................................................................................................... 6
4.1 General wiring...............................................................................................................................6
4.2 Wiring between sensor & transmitter........................................................................................ 7
Chapter 5 Operation interface........................................................................................................... 7
5.1 Operation panel............................................................................................................................ 7
5.2 Operation interface...................................................................................................................... 8
5.2.1 Main interface 1.................................................................................................................... 8
5.2.2 Main interface 2.................................................................................................................. 10
5.2.3 Developer interface............................................................................................................ 10
5.2.4 Display set interface........................................................................................................... 11
Chapter 6 Configuration software.................................................................................................. 11
6.1 Brief introduction.........................................................................................................................11
6.2 Connection between meter & computer................................................................................. 11
6.3 Process variable monitoring.....................................................................................................12
6.4 Communication test...................................................................................................................12
6.5 Mainboard information.............................................................................................................. 12
6.6 Density calibration......................................................................................................................13

Chapter 7 Operation...........................................................................................................................13
7.1 Calibration coefficient setting................................................................................................... 13
7.2 Min. flow cut-off setting............................................................................................................. 14
7.3 Pulse output frequency setting................................................................................................ 15
7.4 Pulse equivalent setting............................................................................................................ 16
7.5 Zero calibration setting..............................................................................................................16
7.6 Fix frequency output setting..................................................................................................... 17
7.7 Total clearance........................................................................................................................... 18
7.8 Volume calculation setting........................................................................................................ 19
7.9 Measurement unit setting......................................................................................................... 20
7.10 Password setting......................................................................................................................20
7.11 Screen power-off setting......................................................................................................... 21
7.12 Screen auto-off setting............................................................................................................21
7.13 Screen brightness setting.......................................................................................................21
Chapter 8 Explosion-proof...............................................................................................................21
Chapter 9 Troubleshooting.............................................................................................................. 22
9.1 Self-diagnosis............................................................................................................................. 22
9.2 Troubleshooting.......................................................................................................................... 23
Chapter 10 Completeness................................................................................................................ 23
Appendix............................................................................................................................................... 25
Appendix 1 Function/operation table............................................................................................. 25
Appendix 2 Abbreviation explanation table...................................................................................26

Zhejiang Sealand Technology Co.,Ltd.
1
Chapter 1 Specifications
1.1 Introduction
The meter is designed and produced according to world’s latest Coriolis technology, with
better appearance, stability and accuracy to measure mass flow rate of a fluid traveling
through a tube, widely applied to alternative energy, oil & gas, chemical, food & beverage,
industrial energy, marine, metals and mining, power, pulp & paper, water & wastewater
industries, etc.
1.2 Operating principle
Mass flow meter measures the mass based on Coriolis effort. The operating principle
involves inducing a vibration of the tube through which the fluid passes. The vibration,
though not completely circular, provides the rotating reference frame that gives rise to the
Coriolis effect. While specific methods vary according to the design of the flow meter,
sensors monitor and analyze changes in frequency, phase shift, and amplitude of the
vibrating flow tubes. The changes observed represent the mass flow rate and density of the
fluid.
1.3 Features
●Measurement is not influenced by flow density, viscosity, temperature & pressure;
●Low requirement of straight pipe, because nothing inside holds back the flow;
●Internal nominal diameter varies from DN06 to DN100;
●Low power dissipation; stable zero point; better accuracy;
●Meter is ARM system, with 3 calculators to count density, temperature & mass flow rate;
●Transmitter is assembled by surface mounting technology, with self-inspection function;
●Ex-mark is Ex ib II B/II CT1~T6 Gb.
1.4 Operating conditions
●Ambient temperature: Sensor -50°C~+200°C
Transmitter -20°C~+50°C
●Relative humidity : 5%~95%, non condensed
●Fluid : Liquid/Gas/Slurry
●Fluid temperature: -200°C~+200°C
●Nominal pressure: 4MPa(general model)
25MPa(high pressure model)
●Voltage: AC/85~265V; DC/20V~26V
Chapter 2 Composition
The meter is composed of mass flow sensor and transmitter, with executive standard GB/T
31130-2014.
2.1 Mass flow sensor
Mass flow sensor is a phase-sensitive resonant sensor based on Coriolis effect,composed of
vibration tube, signal detector, concussion driver, structural support, shell, etc.

Zhejiang Sealand Technology Co.,Ltd.
2
2.1.1 Main parameters
Item
Parameters
Accuracy grade
0.2, 0.3, 0.5
Wetted tubes
Stainless steel 316L
Pressure loss
≤0.2MPa
Housing protection
IP65
Ex-mark
Ex ibIIB/IIC T1~T6 Gb
Table 2-1 Main parameter of sensor
2.1.2 Dimension
There are 3 different configurations, CNG-15, Triangle and U type.
CNG-15 Triangle U Connection flange
Pic. 2-1 Configurations of sensor
Type
Name
DN
Max.flow
rate(kg/h)
Dimension
Flange (Standard DIN2635)
A
B
C
d
d0
n-d1
Bolt
CNG-15
CNG-15
15
3600
136
326
210
M32×1.5 nut
Triangle
CG-06
6
1080
160
255
243
95
65
4-
φ
14
M12×60
CG-15
15
3000
191
361
318
95
65
4-
φ
14
M12×60
CG-25
25
12000
211
503
480
115
85
4-
φ
14
M12×60
U
CG-50
50
60000
556
708
501
165
125
4-
φ
18
M16×60
CG-80
80
180000
830
970
501
200
160
8-
φ
18
M16×60
Table 2-2 Dimension/mm
2.2 Mass flow transmitter
Mass flow transmitter is a micro-programming-centered electronic system, which supplies
thrust to sensor, transforms sensor signal into mass flow signal and others, and improves
accuracy in accordance with temperature parameter.
A
A
A
B
B
B
C
C
C

Zhejiang Sealand Technology Co.,Ltd.
3
It is composed of switching power supplier, guard grating, core processor board, display
module, etc, installed in a ex-proof junction box. Switching power supply offers power for the
transmitter; safe grating isolates flow sensor and transmitter intrinsically; core processor
detects & processes sensor phase signal, sends mass flow signal and process
communication.
2.2.1 Main features
●Power≤15W;
●3 calculators, to count flow rate, density & temperature respectively;
●2 ways for parameter setting, infrared sensor buttons and software on computer
connected through RS232;
●RS485 port, Modbus protocol(please contact our sales team for detail protocol);
●Pulse signal output is OC door output, which can be connected with electronic totalizer;
●Factory set: 1 pulse signal equals 0.1g, customizable before production.
2.2.2 Dimension
There are 2 different configurations, F210 & F23X.
Dimension of F210 Dimension of F23X
Pic 2-2 Dimension of transmitter/mm
Chapter 3 Installation
Please read this manual carefully before installation. Take measure to avoid electric shock,
and connect sensor with pipes correctly, without any leakage. Fluid pressure should be no
more than the value marked on nameplate. It is highly recommended to hire professional
technicians for installation and maintenance.
3.1 Installation steps
a) Make sure flange, housing & wire plug undamaged, wiring & wiring board tight and
undamaged, and the model number on nameplate is same as ordered;
b) Choose correct installation site;
c) Install the meter according to direction mark on sensor;
d) Connect transmitter & sensor with 12-pin cable;
e) Start.

Zhejiang Sealand Technology Co.,Ltd.
4
3.2 Announcements
3.2.1 Site selection
a) Sensor stays away from mechanical vibration source, for example, pump. Use flexible
pipe to connect meter with pipeline if inevitable. The housing must be standalone, out of
touch with any other device. There must be 3 times the size of sensor between 2 sensors
if there are many flow meters on the same pipeline, to avoid resonance.
b) Sensor stays away from industrial electromagnetic field, such as large generator and
transformer, better 5m at least. Such device influences the performance of drive coil and
pickoffs. Make sure magnetic field intensity less than 400A/m.
c) Do not install sensor on pipeline that easily expands with hot and contracts with cold,
especially near expansion joint, which leads to a worse stability.
d) Sensor should be installed on lower pipeline, to be easily full of fluid.
e) Make sure Ex-mark meet application requirements if in hazardous area.
f) Build a sunshade if the meter is under direct solar radiation.
g) Keep the meter from corrosive liquid.
3.2.2 Installation methods
The sensor can not be a support point of the whole pipeline; the pipeline should support itself.
Meanwhile, sensor should not be under overlarge tension stress during the connection,
since pipeline expansion will make this stress heavier.
There are 3 installation methods for different fluid, as follows.
Liquid Gas Slurry
Pic. 3-1 Installation methods
a) For liquid, install the sensor downwards, to avoid air gathering in tubes.
b) For gas, install the sensor upwards, to avoid condensate gathering in tubes.
c) For slurry, install the sensor on vertical pipe, to avoid particle gathering in tubes.
3.2.3 Ground
Current signal from sensor is extremely weak, only several millivolt even when full range;
thus, sensor should be well grounded to filter other signals. There are 2 requirements as
follows.
a) The electric potential of ground terminal of sensor and transmitter should be the same
as that of fluid.

Zhejiang Sealand Technology Co.,Ltd.
5
b) Make the ground as zero potential to reduce interference. It’s easy to meet this
requirement, because generally the pipeline is metal and grounded itself already. However,
the meter should be grounded itself if there is strong interference. Meter ground cable
should be copper material, with section over 4mm2, and not connected with common
ground cable of motor, etc.; ground resistance should be less than 10Ω.
3.2.4 Start
Please check following items before operation, and operate according to relevant rules.
a) If the meter is damaged during shipment and installation;
b) If the voltage is same as marked on nameplate;
c) If the fuse is correct;
d) If the meter is grounded properly.
If everything is fine, please conduct zero calibration after first start, at least twice, and should
do this all over again if the meter is moved to another site.
Preparation for zero calibration:
a) The transmitter should be powered on for at least 20min;
b) Run the meter for few minutes to wash away residual impurity inside pipelines;
c) Run the meter until the temperature of sensor becomes common operating temperature;
d) Shut off the outlet valve, to make the sensor full of fluid and the fluid stop flowing.
Please refer to Chapter 7.5 for detail operation of zero calibration.
3.2.5 Others
a) Make sure the meter coaxial with pipeline, and axis deviation no more than 1.5mm if the
meter diameter is 50mm or less.
b) Make sure the gasket of high corrosion resistance, and not touch tube interior.
c) Make sure fasteners in good condition, and well lubricated.
d) Protect the meter from heat during cutting and welding of nearby pipes.
Attention
Wrong installation in hazardous zone will cause explosion!
Please refer to explosion introduction for more details about hazardous zone.
Power voltage will cause severe injury or death!
Cut off the power before installing the transmitter.
Wrong installation will cause damage and low accuracy of the meter!
Follow the introduction, and keep the transmitter working well.

Zhejiang Sealand Technology Co.,Ltd.
6
Chapter 4 Wiring
Please cut off the power before wiring, use circular section cable so that wiring plug can seal
better, and make sure supply voltage same as marked on nameplate.
4.1 General wiring
There are 2 optional voltages for transmitter, AC220V/DC24V. Power cable section should
be more than 0.8mm2, and length less than 300m.
Pic. 4-1 General wiring diagram of transmitter F23X
Pic. 4-2 General wiring diagram of transmitter F210 (same wiring color as F23X)

Zhejiang Sealand Technology Co.,Ltd.
7
Wiring requirements
a) Cut off power before wiring;
b) Use correct wire;
c) Correct steps to thread wire: Loosen locknut; remove block board; thread wire through
locknut, rubber ring and wire plug all at once; do the wiring; settle wires; tighten locknut.
d) Do not damage insulating layer when pare wire. For sensor signal input wire, do not pare
shielding layer if wirable.
4.2 Wiring between sensor & transmitter
Sensor and transmitter are connected through a 12-pin cable, provided by manufacturer.
The definition is as follows.
Table 4-1 Terminal definition
Chapter 5 Operation interface
5.1 Operation panel
Pic. 5-1 Transmitter schematic
There are 2 infrared sensors, SET and SELECT, between which there is a indicator light,
which blinks green once per second during operation, and blinks red when infrared sensor
detects operation.
S/N
1
2
3
4
5
6
7
8
9
10
11
12
Code
R+
R-
PE
L+
L-
TPE
S2
S1
C1
DPE
D-
D+
Color
white
yellow
black
(shield)
gray
purple
black
(shield)
black
green
orange
black
(shield)
red
blue
Function
Right, left coil detection
Temperature detection
Coil driver

Zhejiang Sealand Technology Co.,Ltd.
8
5.2 Operation interface
Pic. 5-2 Interface frame diagram
Not all interfaces are introduced here. Please refer to Appendix 2 Abbreviation Explanation
Table for more information, if you do not know the meaning of abbreviation.
5.2.1 Main interface 1
On main interface 1, sweep over SET to switch from mass total to mass flow rate alternately;
SELECT from volume total to volume flow rate alternately.
Pic.5-3 Main interface 1

Zhejiang Sealand Technology Co.,Ltd.
9
Content
Unit
Section
Display accuracy
Mass total
T
|m| > 99999.999
Scientific notation %+10.3e
|m| < 99999.999
Show in full screen, keep as many
decimals as possible
KG or LB
|m| > 99999.999
Scientific notation %+10.3e
100<|m|<99999.999
%+10.3f 10-digit, 3-decimal
10<|m| <100
%+10.3f 10-digit, 3-decimal
1<|m|<10
%+10.4f 10-digit, 4-decimal
|m|<1
%+10.5f 10-digit, 5-decimal
Mass flow rate
All
|m| > 9999.9999
Scientific notation %+10.3e
|m| < 9999.9999
%+10.3f 10-digit, 3-decimal
Volume flow rate
All
|V| > 9999.9999
Scientific notation %+10.3e
|V| < 9999.9999
%+10.3f 10-digit, 3-decimal
Volume total
All
100<|V|<99999.999
%+10.3f 10-digit, 3-decimal
10<|V| <100
%+10.3f 10-digit, 3-decimal
1<|V|<10
%+10.3f 10-digit, 3-decimal
|V|<1
%+10.4f 10-digit, 4-decimal
|V| > 99999.999
%+10.5f 10-digit, 5-decimal
Table 5-1 Display accuracy of main interface 1
Mark:
|N|: absolute value of N
%+10.3e: calculated by scientific notation with 10-digit & sign, retaining 3-decimal.
%+10.nf: output floating-point data, with 10-digit & sign, retaining n-digit.
All: all units, outputs parameters according to display accuracy, regardless of parameter unit.

Zhejiang Sealand Technology Co.,Ltd.
10
5.2.2 Main interface 2
On main interface 2, sweep over SET to switch from mass data to volume data alternately.
Pic. 5-4 Main interface 2
Content
Unit
Section
Display accuracy
Mass flow rate
All
(+∞,-∞)
%+12.3f 12-digit, 3-decimal
Mass total
All
|m| < 1
%+12.5f 12-digit, 5-decimal
1<|m|<10
%+12.4f 12-digit, 4-decimal
10<|m|<100
%+12.3f 12-digit, 3-decimal
|m|>=100
%+12.3f 12-digit, 3-decimal
Volume flow rate
All
(+∞,-∞)
%+12.3f 12-digit, 3-decimal
Volume total
All
|V| < 1
%+12.5f 12-digit, 5-decimal
1<|V|<10
%+12.4f 12-digit, 4-decimal
10<|V|<100
%+12.3f 12-digit, 3-decimal
|V|>=100
%+12.3f 12-digit, 3-decimal
Density
g/cm3
(+∞,-∞)
%8.4f 8-digit, 4-decimal
kg/m3
(+∞,-∞)
%8.3e scientific notation, 3-digit
kg/cm3
Temperature
All
(+∞,-∞)
%8.2f 8-digit, 2-decimal
Table 5-2 Display accuracy of main interface 2
5.2.3 Developer interface
Pic.5-5 Developer interface
Password hint: Hexadecimal code, randomly generated by system
Password: Denary code, calculated manual. The calculation method is reserved by
developer, because improper operation in this interface will leads to invocatable damage.

Zhejiang Sealand Technology Co.,Ltd.
11
5.2.4 Display set interface
Pic. 5-6 Display set interface
Main interface 1 will show mass/volume data if Mass/Volume is clicked; vice versa.
Password has to be input if ClearT is clicked; vice vaersa.
The screen will rotate 180° if you set θ 180°.
Chapter 6 Configuration software
6.1 Brief introduction
The whole interface is as follows, with tool bar on the top, current comm. port on left bottom,
and connection status between meter & computer on right bottom.
6.2 Connection between meter & computer
Connect the meter and computer with a USB-to-RS485 converter; turn to device manager of
this computer to check COM port connected with meter.
Start the software, comes the following interface automatically.
Select the right COM port and click Connect; do not change any other parameter.
You can click Connection on tool bar to disconnect or connect again.

Zhejiang Sealand Technology Co.,Ltd.
12
6.3 Process variable monitoring
This interface comes automatically after the meter and computer are connected. You can
also click Functions -->Process variables on tool bar to callout this interface. It shows
real-time Flow rate, Total, Density & Temperature as follow.
6.4 Communication test
This interface is for communication test between software and meter. You can click
Functions --> Communication test to callout. Polling period is the communication testing
interval between meter and software. Software will visit meter database as you set, and
shows times of dispatch and error. It is recommended to set it no less than 50ms to
guarantee communication stability and operation fluency.
6.5 Mainboard information
This interface is to read mainboard number and mainboard real-time operating temperature.
You can click Functions --> Mainboardmessage to callout.

Zhejiang Sealand Technology Co.,Ltd.
13
6.6 Density calibration
Do not change any parameter in this interface, but only when the transmitter is replaced. You
can click Functions --> Demarcate --> Densitycalibration1 on tool bar to callout, and input
parameters marked on the nameplate of new transmitter.
Chapter 7 Operation
Pic. 7-1 Sweep over screen Pic. 7-2 Sweep over SET/SELECT Pic. 7-3
Please sweep over 5~30mm away from screen to ensure movement recognition, and do no
other movement. For example, do not sweep over SELECT when you just need to sweep
over SET. Sweep once, recognize once. Please refer to Appendix 1 Function/operation table,
if you need more information.
7.1 Calibration coefficient setting
●By transmitter
1.On main interface, sweep over screen as Pic. 7-1 until comes interface ;
2.Sweep over SET/SELECT as Pic. 7-2 until cursor points to ;
3.Press SET until indicator light turns red & blinks, comes password input interface;
4.Input password:
a.Sweep over SET/SELECT to set the value, SET=Decrease, SELECT=Increase.
b.Sweep over screen to move to nearby digit, from SET to SELECT=Move right, SELECT
to SET=Move left.
c.Press SET until indicator light turns red & blinks, to confirm password(or press SELECT
until indicator light turns red & blinks, to cancel operation).
5.Comes interface ; the cursor points to FCF(Calibration Coefficient)

Zhejiang Sealand Technology Co.,Ltd.
14
directly(if not, please sweep over SET/SELECT until it points to FCF); press SET until
indicator light turns red & blinks; input new FCF( refer to Step 4); done;
6. Press SELECT until comes pop-up menu, asking whether to return to main interface;
sweep over SET for yes, SELECT for no, and sweep over SET/SELECT again to confirm.
Every meter has its own calibration coefficient marked on standardization certificate and
nameplate of sensor. Each sensor has its own paired transmitter. Customer can use the
meter directly without setting new FCF, but in the following 2 cases: 1. Transmitter is
replaced; 2. Measuring result has a big difference from real value.
Formula:
●By software
Start the software; check tool bar on the top; click Functions --> Configuration; comes setting
interface; click Modified on the right of FlowCalFactor; input new FCF; click OK to confirm;
click Application; done.
7.2 Min. flow cut-off setting
●By transmitter
1.On main interface, sweep over screen as Pic. 7-1 until comes interface ;
2.Sweep over SET/SELECT as Pic. 7-2 until cursor points to ;
3.Press SET until indicator light turns red & blinks, comes the password input interface;
4.Input password:
a. Sweep over SET/SELECT to set the value, SET=Decrease, SELECT=Increase.
b. Sweep over screen as to move to nearby digit, from SET to SELECT=Move right,
SELECT to SET=Move left.
c. Press SET until indicator light turns red & blinks, to confirm password( or press SELECT
until indicator light turns red & blinks, to cancel operation).
5.Comes interface ; sweep over SET/SELECT until cursor points to
MFC(Min. flow cut-off); press SET until indicator light turns red & blinks; input new
MFC( refer to Step 4); done;
6.Press SELECT until comes pop-up menu, asking whether to return to main interface;
sweep over SET for yes, SELECT for no, and sweep over SET/SELECT again to confirm.

Zhejiang Sealand Technology Co.,Ltd.
15
●By software
Start the software; check tool bar on the top; click Functions --> Configuration; comes setting
interface; click Modified on the right of MassFlowCutoff; input new MFC; click OK to confirm;
click Application; done.
7.3 Pulse output frequency setting
●By transmitter
1. On main interface, sweep over screen as Pic. 7-1 until comes interface ;
2. Sweep over SET/SELECT as Pic. 7-2 until cursor points to ;
3. Press SET until indicator light turns red & blinks, comes the password input interface;
4. Input password:
a. Sweep over SET/SELECT to set the value, SET=Decrease, SELECT=Increase.
b. Sweep over screen as to move to nearby digit, from SET to SELECT=Move right,
SELECT to SET=Move left.
c. Press SET until indicator light turns red & blinks, to confirm password( or press
SELECT until indicator light turns red & blinks, to cancel operation).
5.Comes interface ; sweep over SET/SELECT until cursor points to
MF(Pulse output frequency); press SET until indicator light turns red & blinks; input new
MF( refer to Step 4); done;
6.Press SELECT until comes pop-up menu, asking whether to return to main interface; sweep
over SET for yes, SELECT for no, and sweep over SET/SELECT again to confirm.
●By software
Start the software; check tool bar on the top; click Functions --> Configuration; comes setting
interface; click Modified on the right of MaxFrePulse; input new MF; click OK to confirm; click
Application; done.

Zhejiang Sealand Technology Co.,Ltd.
16
7.4 Pulse equivalent setting
●By transmitter
1. On main interface, sweep over screen as Pic. 7-1 until comes interface ;
2. Sweep over SET/SELECT as Pic. 7-2 until cursor points to ;
3. Press SET until indicator light turns red & blinks, comes the password input interface;
4. Input password:
a. Sweep over SET/SELECT to set the value, SET=Decrease, SELECT=Increase.
b. Sweep over screen to move to nearby digit, from SET to SELECT=Move right,
SELECT to SET=Move left.
c. Press SET until indicator light turns red & blinks, to confirm password( or press
SELECT until indicator light turns red & blinks, to cancel operation).
5. Comes interface ; sweep over SET/SELECT until cursor points
to PE(Pulse equivalent); press SET until indicator light turns red & blinks; input new
PE( refer to Step 4); done;
6. Press SELECT until comes pop-up menu, asking whether to return to main interface;
sweep over SET for yes, SELECT for no, and sweep over SET/SELECT again to confirm.
●By software
Start the software; check tool bar on the top; click Functions --> Configuration; comes setting
interface; click Modified on the right of PulseEquivalent; input new PE; click OK to confirm;
click Application; done.
7.5 Zero calibration setting
Please refer to Chapter 3.2.4 before zero calibration.
●By transmitter
1. On main interface, sweep over screen as Pic. 7-1 until comes interface ;
2. Sweep over SET/SELECT as Pic. 7-2 until cursor points to ;
3. Press SET until indicator light turns red & blinks, comes the password input interface;
4. Input password:
a. Sweep over SET/SELECT to set the value, SET=Decrease, SELECT=Increase.
b. Sweep over screen to move to nearby digit, from SET to SELECT=Move right,
SELECT to SET=Move left.
c. Press SET until indicator light turns red & blinks, to confirm password( or press
SELECT until indicator light turns red & blinks, to cancel operation).
Table of contents
Other SeaLand Measuring Instrument manuals
Popular Measuring Instrument manuals by other brands
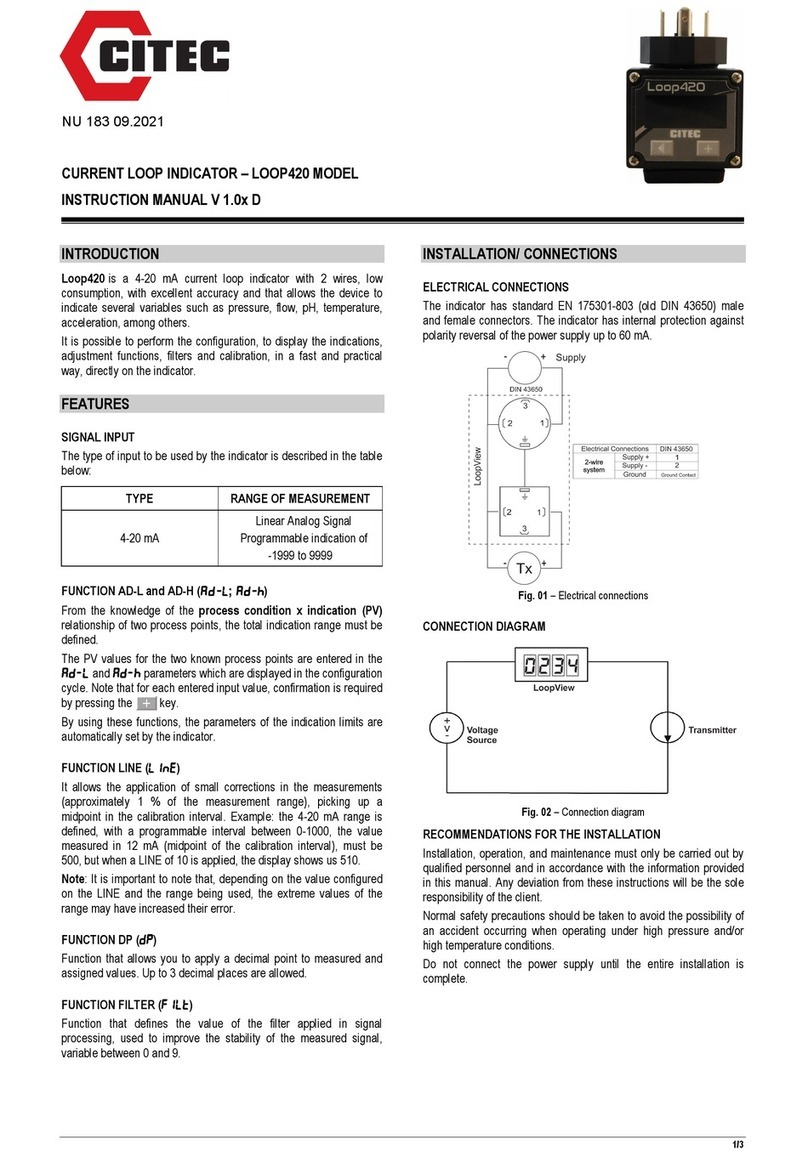
Citec
Citec LOOP420 instruction manual

Industrial Scientific
Industrial Scientific Ventis MX4 Operation manual
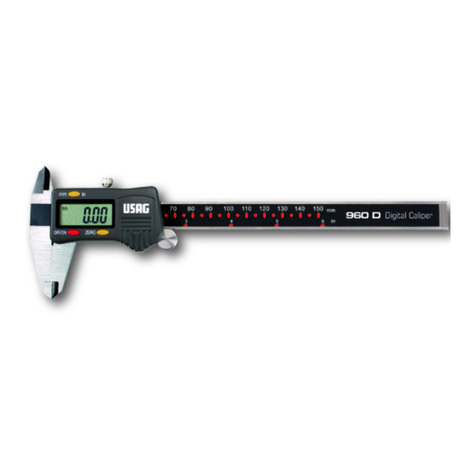
USAG
USAG 960 D manual

WATANABE ELECTRIC INDUSTRY
WATANABE ELECTRIC INDUSTRY WPMZ-1 Series Quick instruction manual
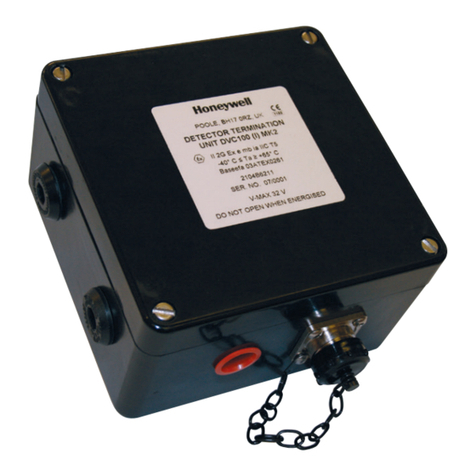
Honeywell
Honeywell DVC100 (M) MK2 installation guide

OEG
OEG 310 821 216 instruction manual