Selbit ANP-05 User manual

ANP-05
Automatic controller for two-sided cutting machine
Automatic cutting thickness regulating unit ANP-05 is designed for installation
in machines such as bilateral disc or belt trimming machines, or other machines
requiring manual or automatic setting of spacing of the vertically working saws.
Before assembly and start please read this handbook manual carefully,
instructions provided help you in correct mounting and operating of our product.

2
CHAPTER 1
Mounting and controller’s connections
During controller’s mounting is advised to follow this instructions correctly.
Point - 1
Before mounting in the main board (fig. 1) please cut off rectangle hole 175 x 140 mm.
This hole should be made carefully thus rubber sealing is adjoined to the from panel.
Eventually any irregularity created after incorrect cutting out please smooth them using small
metal file and protect it by anti-corrosion painting. If on the main panel is no place to mount
controller, it is possible to add it as separate device (fig. 2).
Figure 1. Controller mounting on the main board.

3
Figure 2. Mounted controller as separate device.
In case of controller mounting as a separate device it is possible after its assembly to
attached it to the machine’s frame using 4 added screws for this purpose. In another case
please made special fixing for mounting the controller which can be used as a distance
support as well (fig. 2, E element).
Electric montage
CAUTION !
During electrical assembly there is a possibility of a electric shock
thus all actions should be made while electric power is off. For this purpose
please turn off machine’s main electric switch!!!

4
All cable connections should be made using special wires with double insulation
oriented for use of the electric devices powered by 230V alternating current. Cables
should be rounded with diameter suitable into holes in the controller back casing
accordingly. Tips of the cables should be cleaned and special quill should be used or
tips should be covered by thin tin layer. Please follow this instructions very carefully
especially electric connections should be made according to provided instructions. It is
required for correct and failure-free controller operating.
Machine where the controller is mounted should be equipped in well working head saw
ending switchers and contactors of the up and down feeding should be protected to be
on at the same time !!!
Point - 2
Power transformer TSS-8/001 assembly
In power cubicle added power transformer TSS-8/001 needs to be mounted. Mounting is
designed for well known and used holding bus TSS-35. Please place the transformer as far as
possible from other electrical elements ( e.g. frequency changer, contactors, other
transformers). It is important because of the electromagnetic interference which may
disturbing controller’s electronics. Please connect to the connections marked as PRI power
supply of 230V. For power supply please choose this phase of electric supply of the machine
which is not connected to the any inductions coils, contactors or inverters. 230V supply
cables should be placed as far as it is possible form other cables in the power cubicle. To the
transformer’s clips marked as SEC 12V please connect wires which feed electronic plate of
the controller. Analogically please place this wires as far as it is possible from other power
cables, especially from 230V which powered the transformer. Length of the cables (12V)
should be chosen accordingly to the place where the controller is mounted.
Point - 3
Choke DPZ-320 mounting
Anti-disturbance choke DPZ-320 added in the controller kit is designed to protect from any
other electromagnetic disturbance made by other electrical devices mounted on the frame
machine saw. Its correct mounting is decisive for correct controller operating. Choke DPZ-
320, as transformer, is equipped in casing which is easy to install on the TSS-35 holding bus.
It should be mounted just next to up and down head feeding contactors.
DPZ-320 contains three independence choking sections (fig. 3) marked as DŁ-1 … DŁ-3 and
each of them has two connections named A and B. Those A and B outputs should connected
in parallel to the contactors’ coil (A connected with one coil output and B with another one).
Those sections should be connected with contactor’s coil of the down feeding, up feeding and
barker contactor separately (if the sawing frame machine is equipped with barker).

5
Figure 3 Choke DPZ-320 constructions and connections
Point –4
Installation of the magnetic sensor
In the machine where one head is mobile and aligned to the other stationary head
linked mechanically to the machine body, the magnetic sensor should be mounted on a
support connected to the stationary body. The magnetic tape should be applied on a flat guide
rail fixed directly to the mobile head, so that along the entire working range of the head the
tape moves under the MSK-320 sensor. Particular attention should be paid to the stability of
the sensor and tape installation, so that they do not vibrate during operation.
In the machine where both heads are mobile and move simultaneously with respect to
the stationary machine body, in order to maintain high level of precision, the following
mounting instructions should be followed:
The MSK-320 sensor should be fixed to the first mobile head using the support, while
the flat guide rail with the applied magnetic tape should be attached to other mobile head.
This way, you limit the effect of backlash occurring between the heads on the correct
measurement of the distance between the heads.
The magnetic tape contains two parts which contains with self-adhesive layer. First,
thicker part please place on the smooth and flatten surface (please clean the surface carefully
before sticking the tape using acetone or spirit). During sticking please get unstuck only small
part of the tape on the tip and stick it to the surface. Next get unstuck rest of the tape slowly
sticking it to the surface simultaneously. During sticking please use rubber roll to create
bigger adhesive pressure. Please stick the tape very careful and try to not create any air
bulging and notice to stick it straight. Next please stick the second part of the magnetic tape –
steel protection strip using the same proceeding as above. Both tapes should be stuck in one
line laying on each other creating two layers. Sensor MSK-3200 should be mounted on not
moveable part of the machine (according to the controller) to not create any cable movements
which can cause its damage. In case of mounting sensor on moveable part please protect cable
from its non-controlled damage leading it in a special portable buses. Sensor should be
mounted with two screws in a way that the magnetic tape should be in a 1 to 1,5 mm distance
and in parallel with it. Please notice during leading the cable to place it as far as it is possible

6
from other cables. Please do not place any sources of the magnetic field next to the magnetic
tape during, before and after mounting. It may cause it serious damage and incorrect working
of the controller. Please clean the surface of the tape from time to time with sift brush.
Please do not hit senor or the tape. The sensor should be mounted in that way thus text
SCALE SLIDE is faced on the magnetic tape side. The sensor and the tape should be mounted
in a such way that during feeding sensor “is above” the tape in all range. Please notice the
stability of the tape and the sensor during normal operating.
Figure 4 Sensor and magnetic tape mounting example

7
Point - 5
Connecting increase-reduce motion control cables
Connect two pairs of wires to the head motion control contractors; short circuit (in the first or
the second pair) will cause switching of the reduction contractor (the first pair) and of the
increase contactor (the second pair). Adjust the cable length to the mounting space of the
adjuster. Cable ends should be fitted with connection sleeves or tin-plated.
Point - 6
Prepared cables connections and casing assembly of the controller.
After creation of the all required connections next step is to connect them with the
controller’s main plate.
In the back casing please screw in two PG chokes facing nuts from the inside. Please lead
through mounted chokes follows cables:
-through the biggest one, wires of the head saw contactors steering (two pairs of the cables
from steering buttons)
-though middle one, cable of the rotating encoder
-though choke which is the nearest of the casing middle, power cable 12 V (connection
SEC 12 V from the transformer TSS8/001).
Please connect power cable 12 V (with prepared cables’ tips) to the junction marked as 12V
on the controller’s main plate.
Contactors steering wires connect with junctions on the controller’s main plate as follow:
-no. 1 pair of cables of the reduce dimension with junction marked as DWN
-no. 2 pair of the increasing dimension with junction marked as UP.
Magnetic encoder’s connection MSK-320 :
Magnetic encoder cables please connect with junctions marked ENCODER as follow:
-brown cable of MSK-320 with controller’s junction marked as (+) plus
-black cable of MSK-320 with controller’s junction marked as (-) minus
-red cable of MSK-320 with controller’s junction marked as IN-1
-orange cable of MSK-320 with controller’s junction marked as IN-2
CAUTION!!!
Incorrect connection of the rotating or magnetic encoder may cause
its serious damage!!

8
Next step after creating all of the connections is assembly of the controller’s casing. Before
connecting from panel with the back side please check if the rubber sealing is in the special
groove. It is important in regarding sealing and protecting controller’s main electronic plate
from any contamination. After put the from panel in together with the back side please screw
casing using included six screws 4,1x12. Before mounting the controller on the machine it is
recommended to checking of proper controller’s operating according to “first start” chapter
(2). After checking of the controller’s proper operating please use safety plugs in the places
where screws are and mount the controller on the machine. Controller’s mounting in the main
machine’s board is analogical, there is only one difference that front panel is screwed from
the inside with plastic frame and main panel casing. After all mounting please carefully pull
out cables which go out at the back side of the controller’s casing to reduce their unnecessary
length in the inside. Please be careful to not destroy any connection. After this operation
please screw PG choke to create proper sealing. Next step, in case the controller as a separate
devise, please mount it using four 4,1x10 screws on the sawing frame machine. Screws should
go though four holes in the back casing created for this purpose.
CHAPTER 2
First start
Controller’s connections checking
To check the connections, follow these steps:
- After turning on the power, check if the adjuster displays the message: “ANP-05”.
Otherwise, check the TSS 8/001 transformer connections and retry.
- After the message “ANP-05” disappears, press the green button with arrows pointing
inwards; at this point, the adjuster should connect the reduction contactor and the value of the
dimension, visible in the “Real size” window, should decrease. Similarly, when you press the
green button with arrows pointing outwards, the adjuster should connect the increase
contactor and the dimension value in the “Real size” window should increase. If the counter is
working incorrectly, i.e. the value displayed decreases while pressing the increase button and
increases while pressing the reduction button, swap the wires, red with orange (ENCODER
connector, terminals In1, In2), and check again the accuracy of the counter. Checking the
accuracy of the counter is very important, because if the counting direction is incorrect, the
adjuster will not function.
If the connections have been checked successfully according to the above description,
you can proceed to the next step of the adjuster start-up.

9
Point 7
Checking the values of the input divider
During the display of the “ANP-05” message, press and hold the “Calibr”button; after a
while, the top display will show horizontal bars and the lower display will show the symbol of
the divider (reversed T) and its current value. In case of using the magnetic tape and the
MSK-320 sensor, the divider's value should be 5. Otherwise, enter the correct value of 5using
the numeric keypad of the adjuster. To save the entered divider value, press shortly the
“Save”button; the message “Save”will appear to confirms correct setting. Enter the divider
value at the first start-up or if there is a suspicion of incorrect configuration of the adjuster.
Point 8
Entering the dimension calibrating the “Real size” counter (Real size)
Warning! Due to the mode of entering the Real size dimension (value to one decimal
place), entering the dimension is possible only if the value shown in the “Real size”
display does not exceed 999mm!!
Due to the one way motion of backlash elimination, be sure to reduce dimension before
entering the dimension (press and hold the button with arrows pointing inwards)!!
To make sure that the top display shows the real size correctly, press the button with arrows
pointing outwards, to set spacing of the saws to any dimension less than 999 mm. Then read
the actual spacing of the saws in the machine, by using e.g. a mechanical gauge of the
machine (if it is precisely calibrated) or by measuring the spacing with another gauge. Then
press and hold for approx. 3s the “Set Real size”button; after a while, the top display will
show horizontal lines and the lower display will show the previously used dimension; using
the numeric keypad, enter the measured spacing value, making sure to enter the dimension
to one decimal place, e.g. the spacing of the saws equal 140 mm should be entered by
pressing: 1, 4, 0, 0, while another sample dimension 232.4 should be entered by pressing: 2, 3,
2, 4. After entering the dimension, confirm by pressing “Save”. The control system will
display the message “Save”and exit the function, while the top display will show the entered
real dimension of the spacing of saws. If the machine has not been mechanically reset while
the power supply of the control system was off, there is no need to calibrate the counter after
restarting (the counter’s dimension is saved in the memory of the control system);
recalibration should be made if the values displayed are divergent or if there was e.g. a
break in the power supply during operation and the control system has not saved the
counter value.
Entering the real value of the spacing of saws is necessary for the correct operation of
the control system!

10
Point 9
Auto-calibration of the adjuster
In order to assure correct operation of the control system (adjusted to the slip of the head after
stopping the engine), use the auto-calibration function after the first start-up. Use this
function also if the screws of the head's drive or the engine have been replaced or after
applying lubricant to screws or other moving parts of the head, if there are significant
divergences in cutting dimensions. To auto-calibrate, set the saws to the smallest dimension
(smallest spacing of the saws), then switch on the control system, wait until the “ANP-05”
message disappears from the display, then press and hold the “Calibr” button. The
display will show the message: “Auto call”. The control system is ready to auto-calibrate.
Press again the “Calibr”button. The adjuster will perform automatic measuring movements.
After performing measuring movements, the adjuster will indicate the end of the function and
enter normal working mode. During auto-calibration, the adjuster makes a test run over a
distance of approx. 140 mm in the direction of increasing the dimension: it should be taken
into consideration when setting the starting position of the saws.
Having completed the steps above, the adjuster is ready for normal operation.
Operation of the ANP-05 adjuster
Immediately after turning on the power, a red LED will be blinking next to message:
“Check real size”, reminding to check the dimension displayed in the “Real size”
window with the actual dimensions of the saws. In the event of divergences, enter correct
dimensions, following the instructions described in Section 8.
The adjuster allows manual control of the spacing (dimension cut) of the saws using green
buttons with arrows or automatically by entering the dimension and pressing shortly “Start
position”. Enter the dimensions using the numeric keypad or fast dimension buttons described
as “A” to “E”, which are assigned to individual spacing dimensions of the saws. Dimension
values assigned to the keys A-E can be adapted to individual needs, according to the
following description:
In order to change one or more dimensions assigned to the keys A-E, press and hold for
approx. 3s the button “Set Abcde”; after a while the upper display will show the message:
“Abc” and the lower display will show horizontal lines. Now select the key you want to
underwrite with new dimensions and press it shortly. The upper display will show the letter
corresponding to the key which had been pressed and the lower display will show the
previously assigned dimension. Using the numeric keypad, you can enter another value. After
entering the value, press shortly another key with the letter to change the assigned value. After
making all the necessary changes to one or more keys (A-E), save changes by pressing shortly
the button “Save”; the adjuster displays the message: “Save”, confirming the setting. From
now on, the saved dimensions will be available by pressing A-E keys.
List of errors which may occur during the operation of the adjuster:
If an error occurs during operation, the adjuster displays an error message and stops
movement. To erase the message, press shortly the button “Start position” and then
locate the cause of the malfunction and correct it before restarting work.
No power supply:
- check connections of the TSS8/001 transformer.

11
No control over the machine:
- check output connections DWN and UP of the adjuster to contactors.
After pressing “Start”, the machine does not stop, despite the correct dimension
entered:
- check the value of the input divider (Section 7).
The machine stops, the display shows the message “Er P”:
- check the MSK-320 encoder connection to the adjuster plate; check whether the transducer
cable is broken or whether the machine head is in a position causing the activation of limit
switches; check the contactors' connections.
The dimensions are too divergent:
- auto-calibrate; check the installation of the MSK-320 sensor and its correct movement over
the magnetic tape; check the distance of the sensor along its path over the magnetic tape.
During auto-calibration, the adjuster displays the message “Auto Er P”:
- measure the distance between the saws and enter the correct value to the adjuster, using the
key “Set Real size” (see Section 8), check whether the head has caused the activation of the
limit switch during the calibration movement; check the connection of the MSK-320 sensor
and its path over the tape as in the case described above regarding the message “Er P”.
During manual control of the saws with the spacing reduction button, the adjuster stops
and displays the message “Set Real”:
the counter value “Real size” is below zero; mistyped spacing dimension. Measure the
spacing of the saws and enter the correct value to the adjuster, using the button “Set Real
size” (see Section 8).
Operation recommendation
For having maximal good parameters of the cutting it is recommended to use auto-
calibration at least twice a week. Auto-calibration proceedings are in details described in the
point 3 of the chapter 3 “Auto-calibration (controller’s checking in with technical parameters
of the sawing frame machine where its mounted)”. Before starting of the operation the “Saw
Height” displayed needs to be checked and compared with the real head saw position. In case
of the any divergence it needs to be corrected according to the procedure shows in the point 4
of the chapter 3 “real saw height settings”.
Do not press the keyboard using hard or sharp objects, it can cause irreversible
damages. In case of the dirty keyboard, please use only proper medium to clean it up. Please
remember to not press to hard membrane buttons. Pressing to hard of the buttons can cause
damages and eventually exchange of the hole keyboard. The controller should not be exposed
direct on getting wet with rain, water or any other fluids.
EMC Approval
Controller ANP-05 is approved and fulfil all requirements concerning electromagnetic
norms according to EMC.
The controller ANP-05 should be set up and installed according to European and domestic
norms. Responsible for adjusting the controller is person who set up the electric and control
system on the sawing frame machine. It needs to be under EMC regulations.
The controller need to be concern as a component of the sawing frame machine,
it is not a separate machine or electronic device according to European directive (machine
directive and electromagnetic compatibility directive).
The assembler of the controller ANP-05 is responsible for fulfil all those directives. Product
and equipment described within this instruction can be modify as from technical as
operational point of view. This written description –handbook manual can not be consider as
a contract.
Table of contents
Other Selbit Controllers manuals
Popular Controllers manuals by other brands

Green Brook
Green Brook T612A-C Installation & operating instructions
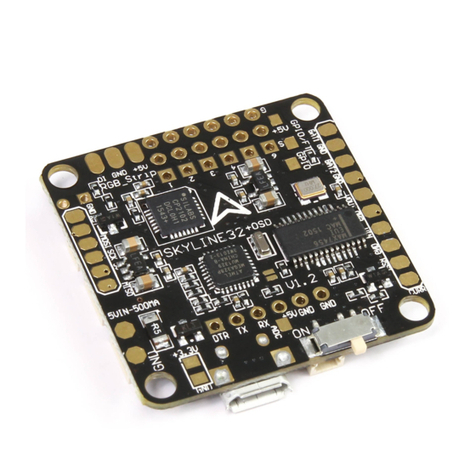
Emax
Emax SKYLINE32 instruction manual
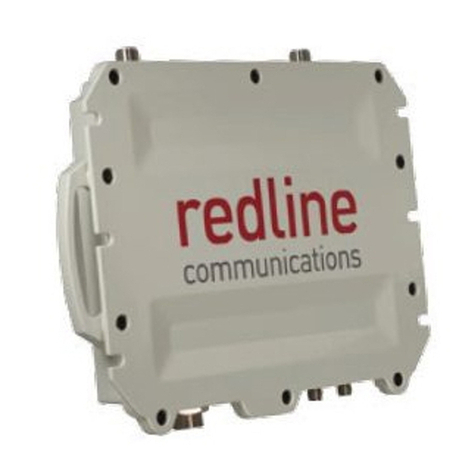
Redline
Redline RDL-3000 SC Installation guidelines
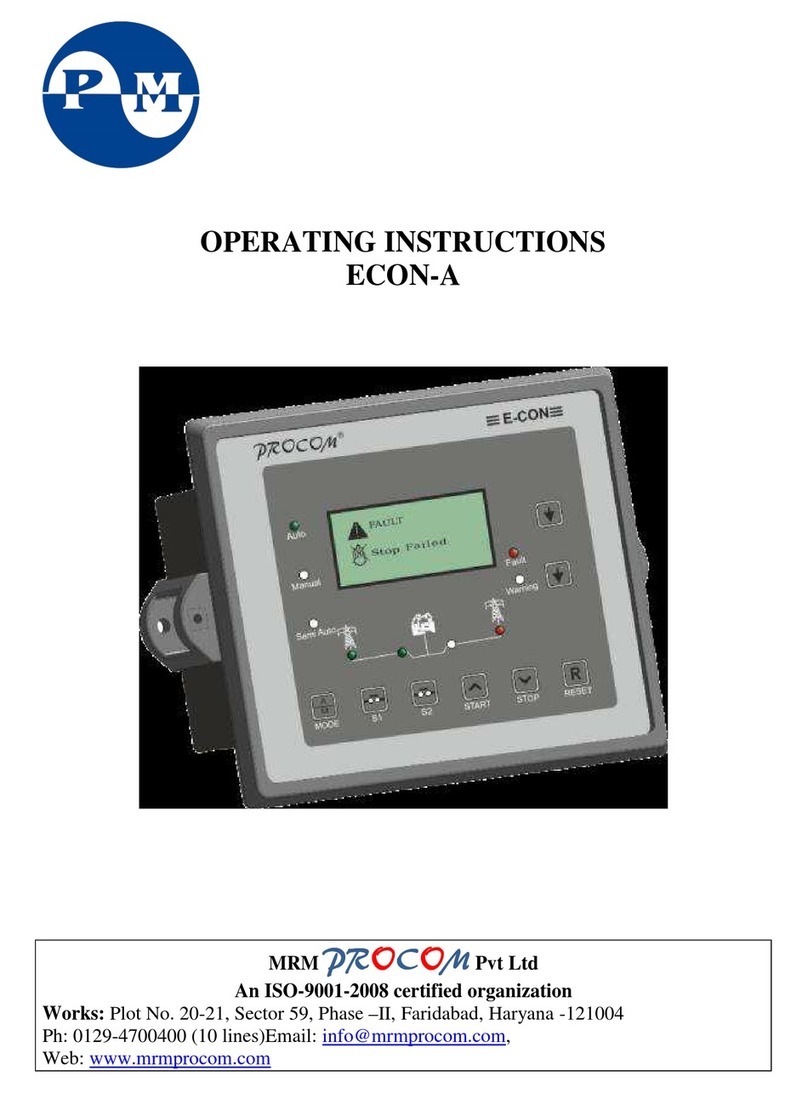
Procom
Procom ECON-A operating instructions
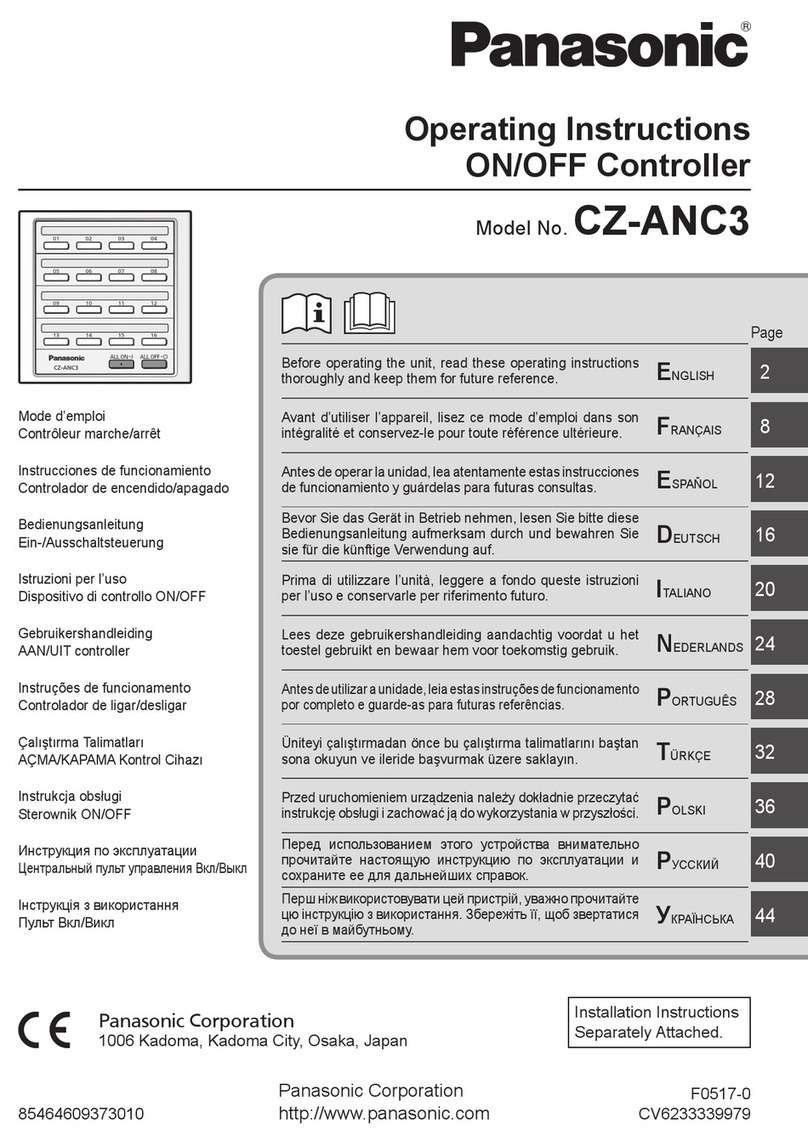
Sky Wing
Sky Wing CZ-ANC3 operating instructions

One Remote
One Remote MultyMedia TS1e Operation instructions