Sfere DASv10 Instruction Manual

PROGRAMMABLE SETPOINT DETECTORS
DASv10 / DASCv10
SFERE - TA SE11- D 10/17- Any data in this documentation may be modified without prior notice.
Société Française d’Etudes et
de Réalisations Electroniques
Tél. : 04 78 16 04 04 - Fax. : 04 78 16 04 05
Tel. Intern. : 33 4 78 16 04 04 - Fax Intern. : 33 4 78 16 04 05
siège : Route de Brindas - Parc d’Activité d’Arbora - N°2
69510 SOUCIEU EN JARREST - FRANCE
SFERE
User handbook
version 05.x
LCD µconsole
Software SlimSET
The friendly
interface
SFERE

p1
Summary
UE conformity declaration p1
1 . INTRODUCTION p2
2 . SPACE REQUIREMENTS p4
3 . CONNECTINGS p4
4 . PROGRAMMING p5
Measure screen p6
Menu MAIN p8
Menu DIR.FCT p12
Menu INPUT p14
Menu DISPLAY p16
Menu CONF ADV p17
Menu RELAYS p19
Menu SAFETY p22
Menu SET CONS p24
Menu TAG p26
Menu EXIT p26
Menu ABOUT p26
5 . ERROR MESSAGES p27
6 . GENERAL WARRANTY TERMS p27
UE CONFORMITY DECLARATION
The manufacturer:
ARDETEM-SFERE
Route de Brindas
Parc d’activité d’Arbora n°2
69510 Soucieu en Jarrest
France
declares that the following products:
Name: Programmable setpoint detectors
Type: DASv10, DASCv10
comply with the following directives and standards:
The EMC Directive 2014/30/UE
EN 61326-1 : 2013
The Low Voltage Directive 2014/35/UE
EN 61010-1 : 2011
The Directive ATEX 2014/34/UE
EN 60079-0 : 2011 EN 60079-15 : 2010
Soucieu en Jarrest, January 2, 2017
Jacques Huguet
Signature of the Manager

p2
This appliance has to be installed in an environment defined in pollution
degree 2 / Overvoltage category II or better for a max. altitude of 2000 m.
Before any installation or maintenance work, make sure the power supply
of the instrument is cut.
When the instrument is permanently connected to a dangerous voltage, it
is necessary to add a means of sectionalizing on the power supply (switch,
fuse or circuit breaker) near to the product, to make it easy of access and
to mark it as being the means for cutting the instrument.
This sectionalizing means should cut all the conductors leading the
current.
The accessible part is the communication port (µUSB).
The person who has designed the system (electrical installation including
the instrument) is sole responsible for the safety and must make sure it
has been designed according to the current safety standards.
The device is an Open Type Listed Process Control Equipment. To prevent
any injury resulting from accessibility to live parts the equipment must be
installed in a cabinet.
This appliance contains electronic components and
should not be disposed of with the domestic waste.
It should be collected with the WEEE (Waste Elec-
trical and Electronic Equipment), according to the
current regulation.
The instrument may be connected to dangerous electrical
voltages.
It must be mounted, connected and implemented respecting
the current specific regulations, by a qualified technician, trai-
ned to the safety regulations, who will have read this manual.
1. INTRODUCTION
The products DASv10 and DASCv10 are setpoint detectors, fully programmable
either with the µconsole or by PC via the configuration software and a standard USB/
µUSB cable.
The rear-lit tactile graphical LCD allows the visualisation of all the following informa-
tion concerning the instrument:
- the value of the measure with its unit,
- the name of the product (TAG),
- the status of the relay outputs.
Scrolling message for programming help (programmable in several languages).
Programming protected by code (0000 on factory exit).
Programmable keys for direct access to some functions.
• Input features
- A bidirectional DC current or voltage input:
±100 mV, ±1V, ±10V, ±270V, ±20mA.
- Thermocouple inputs (J, K, B, R, S, T, E, N, L, W, W3, WRE5)
- Sensor inputs: Pt100, Ni 100 (2, 3 or 4 wire), ∆Pt100
- Resistive sensors: caliber 0-400 Ω and 0-10 kΩ
- Potentiometers: from 100 Ω to 10 kΩ
- Relay output:
2 relays - Mode setpoint or mode window.
Recording of the alarms.
Time delay and hysteresis adjustable on each setpoint.
Alarm messages.
- Option F (specify on order):
- Fast acquisition allowing a response time < 25ms on the relays.
Coding
Version:
DASv10: without display
DASCv10: with display
Type
Option: F fast version
DAS(C)v 10 (F)
• CJC terminal (option): reference B1CSF-4
• Standard programming cable USB type A male to µUSB type B male:
reference C1-µUSB

p3
Features of the inputs
Types of
INPUTS
Measure range
adjustable from:
Permanent
overload Intrinsic
error
Input
impedance
mA
(1) -2 to +22mA (U)
-22 to +22mA (B)
±100mA
< ±0.1% of
the MR for
inputs of the
type (U)
< ±0.05% of
the MR for
inputs of the
type (B)
(4)
Max. drop
0.9V
mV
(1)
-10 to +110mV (U)
-110 to +110mV (B)
±1V
≥ 1MΩ
V
-0,1 to +1,1V (U)
-1.1 to +1.1 V (B)
±50V
-1 to +11V (U)
-11 to +11V (B)
-30 to +300V (U)
-300 to +300V (B)
±300V
Thermocouples
(1)
Standard IEC 581
J
K
B
R
S
T
E
N
L
W
W3
WRE5
°C
-160/1200
-270/1370
200/1820
-50/1770
-50/1770
-270/410
-120/1000
0/1300
-150/910
1000/2300
0/2480
0/2300
°F
-256/2192
-454/2498
392/3308
-58/3218
-58/3218
-454/770
-184/1832
-32/2372
-238/1670
1832/4172
32/4496
32/4172
-
<±0.1%
of the MR
or 30µV
typical
(60µV max.)
≥ 1 MΩ
Sensor Pt100Ω (1)
(2)
Standard IEC 751 (DIN
43760)
°C
°F
-<±0.1%
of the MR Current
250µA
-200/850
-328/1562
-
Sensor Ni 100 3 wire
(1)
(2) -60/260
-76/500 -
Resistive sensors
Calibers 0-440 Ω
(1)
(2)
and 0-10 kΩ -<±0.1% of
the MR Max. current
250µA
Max. voltage
100mV
Potentiometer from 100Ω to 10 kΩ -
Supply for 2-wire sen-
sor 24 VDC ±15% with protection from short-circuits.
25 mA max.
Special linearisation
programming
up to 20 points
On input: mV, V, mA.
resistive sensors and potentiometer
Extraction of the
square root
On input mV, V or mA
(3)
(3) Efficiency of the CJC (-20°C to 60°C):
Internal CJC: ±2°C ±0.03°C/°C
CJC (option terminal): ±1°C
MR Measure range
Thermal drift <150ppm /°C
(1) Sensor break detection:
mA input (if down scale ≥ 3.5mA)
Other inputs: A 12µA pulsed current allows
the detection of line or sensor break.
(2) Wiring in 2, 3 and 4 wire possible
The influence of the line resistance (0<Rl<<25Ω)
is included in the announced intrinsic error.
(4) <0.1% of the MR (B) for the version F if acquisition time <100ms
• Standard version
Average response time: 150 ms (1)
(1) Add 10 ms for the response time on the relay outputs.
Response time
(for a variation from 10 to 90% of the input signal)
• Option F (fast version)
Programmed acquisition
time
Cycle time
(without µconsole)
Rejection
1ms 7ms -
16.6ms 23ms 60 Hz
20ms 26ms 50 Hz
100ms 106ms 50Hz/60Hz
Max. response time: 2 cycle times (1).
The response times are garanteed 10 minutes after setting the converter on tension and
30 seconds after a saving of the programming, a revert from measure overrange or a
sensor rupture.
For the inputs requiring several measures (TC, PT100 and NI100 in 3 and 4 wire, and
potentiometer) the 2nd measure is performed every 1000 to 2000 cycles. In this case
the response time can be increased by 1 cycle time.
Type
of OUTPUTS
2 change-over relays
2 setpoints per relay
configurable over the whole MR.
Hysteresis programmable from 0 to 100%.
Time delay programmable from 0 to 999.9 sec.
(8A/250 VAC on resistive load)
Features
General features
Galvanic isolation: 3.0kV-50 Hz-1 min between supply, inputs and relay outputs.
Service voltage: 250V AC/DC
Power supply:
20 to 250 VAC 50-60 Hz
and 20 to 250 VDC
Max. operating range
2.8 W max.
8 VA max.
Power draw
3.0KV-50Hz-1min.
Dielectric
withstanding

p4
2. SPACE REQUIREMENTS
1 2 3 4
1 2 3 4
numbering of
the terminals:
A, B, C, D
numbering of
the terminals:
F, G, H
Voltage pre-
sence LED ON
(green)
Relay 1
Relay 2
µconsole
plug
µUSB for
program-
ming via PC
software
22,6
3. CONNECTINGS
SUPPLY INPUTS
A1 A3
A2
AC ~ ~
DC - +
A4
T1
-
+TC
+
-
-+
+
+
G3
G2
G4 H1 H3
H2
H4
mA
mV
GND 1V
10V
270V GND
G1
2-wire
transmitter
R > 440Ω
{
RTD
R < 440Ω
T2
potentiometer
∆ RTD (T2 - T1)
OUTPUTS
Relay outputs
109 mm
136 mm (with µconsole)
122 mm (without µconsole)
A B C D
F G H
{
Input
Relay
1
Relay
2
Supply
4 wire
2 wire
3 wire
OFF1
OFF2
Relay 2
ON2
C2
C1 C3
C2
C4 D1 D3
D2
D4
Relay 1
ON1
C1
Measure:
• Standard sampling time: 100 ms
option F: programmable at 1 ms, 16.6 ms, 20 ms, or 100 ms
• Common mode rejection rate: 130 dB
Serial mode rejection rate: 70 dB 50/60 Hz
• Zero drift compensation
Use:
• Operating temperature: -20 to 60°C
• Storage temperature: -20 to 70°C
• Use in pollution degree 2 and voltage surge category II or better
• Max. altitude: 2000m
Housing:
• Self-extinguishing case of black UL 94VO PA66
• Mounting in switchbox: latching on symmetrical DIN rail.
• Removable terminal blocks for screwed connections (2.5mm², flexible or rigid)
• Screw thread M3
Max. tightening torque: 0.5Nm / 4.5in.lbs
Min. solid/stranded conductor section: 0.2mm2 / 26A WG
Max. solid/stranded conductor section: 2.5mm2 / 14A WG
• Protection: case / terminals: IP20
Dimensions: without µconsole: 109mm x 122mm
with µconsole: 109mm x 136 mm
Max. weight: 290g (with packaging)
Compliance with standards:
Directive LV 2014/35/UE ........................EN 61010-1
Standard for UL electrical safety ............UL 61010-1
................................................................CSA C22.2 NO.61010-1-12
Directive ATEX 2014/34/UE area 2 ........EN 60079-0
................................................................EN60079-15
Directive EMC 2014/30/UE ....................EN 61326-1
Marking:
II 3 G Ex nA IIC T4 Gc

p5
• With the micro-console
(LxhxD= 23.3 x 89.5 x 24.3 mm)
This µconsole for clipping on the front face allows the visualisation of the measure
or occasional modifications of the programming via its tactile keyboard. It also
allows the teleloading of a programming file to other products of the SFERE range.
The programming menus and the functions which can be accessed from the con-
sole are detailed in the following pages.
The graphical rear-lit LCD allows the visualisation of 3 pieces of information:
- the value of the measure (5 mm high) with its unit,
- the name of the product (TAG),
- the status of the relay outputs.
• Scrolling message for programming help (programmable in several languages)
• Protection of the programming by code.
• Programmable keys for direct access.
4. PROGRAMMING
• Via the configuration sofware SlimSET
To communicate with the series DASv from a PC you will need a connection cable
(USB / µUSB standard). To connect this cable to the DASv, unclip the front face and
insert the µUSB plug into the especially foreseen USB connector. Then connect the
USB plug on a USB port of the PC.
The software SlimSET allows the reading of the measures or the modification of the
converter configuration.
Each configuration is kept as a file stored on disk. These files can be consulted,
modified, duplicated or loaded into the converters. The files can be created with
or without having a converter connected. This software also allows the saving of
existing configurations from the instruments already in service. All the files can be
edited on any type of printer.
• INSTALLATION IN AREA 2 (ATEX):
II3 G Ex nA IIC T4 Gc
The product must be installed by qualified staff, competent on the directives
and the regulation applicable to the area 2.
It must be installed in a protecting enveloppe conform with the EN 60079-15.
The operator must ensure an external protection in order to prevent transient
disturbances on the supply higher than 40% of the nominal voltage.
Cut both the main and emergency power supplies or make sure you are in
non-hazardous area before any connection or disconnection of any cable con-
nected to the the DASv (USB, µConsole and connectors).
The installation must comply with the EN 60079-14 :2014.

p6
Symbole representing the status
of the alarms.
Empty square: alarm not in alarm
Full square: alarm in alarm
Blinking square: alarm recorded
Tactile key F1: Programmable
quick access function
))
1 2
Alarms
Display of the measure, of the error messa-
ges (eg.: sensor break, scale overrange etc.)
or the alarm messages if alarm latched and
message programmed
Display of the measure unit
Display of the name given to the configuration
(TAG)
Tactile key F2:
Programmable quick
access function
Tactile key
- Allows the unlocking of the keyboard
- The access to the main menu if pressed
during the measure screen
- The switching back to the previous menu during
the reading or the programming
Measure screen
Locked keyboard symbole.
After 30 sec of inactivity of
the keyboard in measure
mode, it will be blocked
in order to prevent any
unintentional pressing. To
unlock it simply press M
during 2 seconds, until this
screen appears
Tactile screen. Press
the measure screen for
access to the direct func-
tions.
Description
2 Sec.
Unlocking of the keyboard
M

p7
Moving through the list menus:
Eg.:
READ
INPUT
DISPLAY
CONF ADV
RELAYS
SAFETY
SET CONS
TAG
EXIT
Note: the empty upwards
arrow indicates that you
are at the top of the menu
READ
INPUT
DISPLAY
CONF ADV
RELAYS
SAFETY
SET CONS
TAG
EXIT
Use the
downwards or
upwards ar-
rows to move
the band.
READ
INPUT
DISPLAY
CONF ADV
RELAYS
SAFETY
SET CONS
TAG
EXIT
Note: the empty downwards
arrow indicates that you are at
the bottom of the menu
Once you have
reached the
desired menu,
press the screen
to access this
menu (except
the upwards and
downwards keys)
READ
INPUT
DISPLAY
CONF ADV
RELAYS
SAFETY
SET CONS
TAG
EXIT
ADVANCE
CONFIG
TRANSFER
CUT OFF
FILTER
M
You will then enter the chosen
menu. Press M to come back
to the previous menu.
Entering of a value:
CODE
0000
MODIF
Press
MODIF to
enter the
entering
mode
CODE
0000
The first digit starts
to blink.
Enter the value of
the first digit using
the arrows.
CODE
2000
Once you have
reached the desi-
red value, press
VALID to switch to
the second digit.
CODE
1000
Start again for the
second digit and
the third etc... until
the last digit.
CODE
1234
DS INP
+100.0
For a signed value,
the entering begins
by the choice of
the sign.
DS INP
100.0
For a value with decimals the entering
ends by the choice of the decimal point
position, which you can move using the
arrows.
DS INP
10.00
Press M during the entering to revert to
the former value.
VALID
VALID
VALID
VALID
VALID
VALID
VALID

p8
MEASURE SCREEN
120.3
oC
FILE 1
))
MIN
MAX
MES
DIR
M
MAIN
READ CFG
PROGRAM
SET CODE
SIMULAT
µCON.MEM
FUNCTION
LANGUAGE
SENS.KEY
ABOUT
MANUAL
MAIN
READ CFG
PROGRAM
SET CODE
SIMULAT
µCON.MEM
FUNCTION
LANGUAGE
SENS.KEY
ABOUT
MANUAL
CODE
0000
if code DISABLE in
menu SET CODE
PROG
INPUT
DISPLAY
CONF ADV
RELAYS
SAFETY
SET CONS
TAG
EXIT
Note:
The instrument will revert to the Measure screen
if no key is pressed during 1min. in mode pro-
gramming and 20 sec. in mode reading.
PROG :
Access to the programming of the
instrument configuration
see page14.
MODIF
OK OK
Press the key
on the measure screen to
access the main menu.
M
menu
MAIN
READ
INPUT
DISPLAY
CONF ADV
RELAYS
SAFETY
SET CONS
TAG
ABOUT
OK
READ:
Access to the reading of the configuration.
Menu identical to the programming of the configuration, but modification impossible (the key MO-
DIF disappears in the entering of the parameters). The keys are replaced by the keys
when you access the chosen parameter, these keys allowing to come back to the previous menu or
to access the next parameter.
Press the screen to scroll the reading of the configuration parameter after parameter.
access to the configuration
Default code:
0000
Press the screen in measure mode to
access the menu of the direct functions
or the display of the details of the lat-
ched self-diagnosis errors: ERxxx (see
page 23).
DIR.FCT
MIN MAX
MES DIR
CLR ALR
PROG REL
ADJUST
BRIGHT
LIGHT
Menu of the functions with direct
access see page 12
E.OFSS
E.CAL X
X
DIAG

p9
MAIN
READ CFG
PROGRAM
SET CODE
SIMULAT
µCON.MEM
FUNCTION
LANGUAGE
SENS.KEY
ABOUT
MANUAL
CODE
0000
MODIF
OK OK
if code DISABLE in
menu SET CODE
menu
MAIN
menu code
CODE
MENU
ACTIVATE
NEW CODE
FCT CODE
Activation or not of the
programming code
{
If code ENABLE
ACTIV
CODE
DISABLE
ENABLE
NEW CODE
0000
Code for
access to
the pro-
gramming
validated
Revert to the menu MAIN
Code for access to the programming
disabled
Revert to
the menu
MAIN
CODE
MENU
ACTIVATE
NEW CODE
FCT CODE
Entering of a new code for
access to the programming
MODIF
OK OK
OK OK
OK
CODE
MENU
ACTIVATE
NEW CODE
FCT CODE
FUNCT
BY CODE
SIMUL
PRG REL
CLR AL
ADJUST
µCONS
EXIT
X
Select all the functions for which
you want to allow the access by the
entering of the programming code.
The access is blocked when a cross
appears in front of the function.
To exit from the menu select EXIT.
The functions (in this example
SIMUL and ADJUST) will be acces-
sible after entering the code.
Choice of the functions
accessible by code.
Exit from the menu
Revert to the menu MAIN
Functions: SIMUL :
PRG REL :
CLR AL :
ADJUST :
µCONS:
Simulation
Programming of the alarm setpoints
Deletion of the recorded alarms
Display calibration
Transfer of the configuration into the µconsole
FUNCT
BY CODE
SIMUL
PRG REL
CLR AL
ADJUST
µCONS
EXIT
X
X
OK OK
OK

p10
MAIN
READ CFG
PROGRAM
SET CODE
SIMULAT
µCON.MEM
FUNCTION
LANGUAGE
SENS.KEY
ABOUT
MANUAL
SIMUL
SENSOR
DISPLAY
(A)
SIMUL
SENSOR
DISPLAY
(A)
SIMUL
SENSOR
000.0
(unit)
SIMUL
DISPL
000.0
SIMUL
INFO
000.0
000.0
))
Enter the
value corres-
ponding to
the display
you want to
simulate
Revert to the
menu SIMUL by
pressing
M
SENSOR
DISPLAY
ALARM
CODE
0000
if access blocked by code
MODIF
MODIF
MODIF
(unit)
(unit)
(unit)
OK OK
OK
OK
OK
OK
menu simulation
menu
MAIN
The converter can perform a simulation
in order to validate the configuration or
the installation:
- simulation of the sensor value,
- simulation of the displayed value.
During the sensor simulation or the
display simulation the relay outputs
will react according to the entered
value.

p11
MAIN
READ CFG
PROGRAM
SET CODE
SIMULAT
µCON.MEM
FUNCTION
LANGUAGE
SENS.KEY
ABOUT
MANUAL
CODE
0000
if access blocked by code
μCONS
MEMORY
READ
WRITE
μCONS
MEMORY
READ
WRITE
MENU
INPUT
DISPLAY
CONF ADV
RELAYS
SAFETY
SET CONS
TAG
EXIT
Reading of the configuration file stored
inside the µconsole memory (same orga-
nigramme as for the instrument).
Note (A)
WRITE
WAY
DEV CONS
CONS DEV
WRITE
WAY
DEV CONS
CONS DEV
WRITING...
WRITE
WRITING...
WRITE
Revert to the menu WRITE WAY
Revert to the menu WRITE WAY
Teleloading of the instrument configuration file
into the µconsole memory..
Teleloading of the configuration file stored
inside the µconsole into the instrument.
Note (A)
Note (A): The reading or the teleloading of a file into the
instrument is possible only if the instrument (type and
option) and the file are identical.
Otherwise the message or appears
depending on the case.
ERR
DEV
ERR
OPT
menu
MAIN
MAIN
READ CFG
PROGRAM
SET CODE
SIMULAT
μCON.MEM
FUNCTION
LANGUAGE
SENS.KEY
ABOUT
MANUAL
Access to the list of the direct functions (see direct functions).
Direct access to the menu choice of the language of the scrolling help messages (voir Menu SET CONS => LANGUAGE).
Direct access to the menu setting of the keyboard sensitiveness (Voir Menu SET CONS => SENS.KEY).
Direct access to the menu information on the product (see Menu ABOUT Mode Reading).
Access to the QR code for downloading the documentation.
MODIF
OK OK
OK
OK
OK
OK
µconsole management menu
The µconsole allows to store or to
load configuration files thanks to its
internal memory.

p12
MEASURE SCREEN
120.3
oC
FILE 1
))
MIN
MAX
MES
DIR
M
Direct access to the
function of the key, in
this example the dis-
play of the measured
MIN and MAX.
DIR.FCT
MIN MAX
MES DIR
CLR ALR
PROG REL
ADJUST
BRIGHT
LIGHT
MIN :
0000
MAX :
0000
CLR
MIN MAX
Press the key CLR MIN MAX
to delete the recorded min
and max.
SENSOR
MEASURE :
0000
Direct display of the measure without
processing:
in mV, V or mA for the Process inputs
in mV for the thermocouple inputs
in Ω for the inputs PT100, NI100 or
resistance
in % for the Potentiometer inputs
CODE
0000
if access blocked by code
))
1 2
{
Visualisation
of the status
of the alarms
Press CLR ALARMS to reset
the alarm recordings to 0
Functions with direct access
To simplify the use, some functions can be accessed in
a more direct way. These functions are:
- the display and the 0 reset of the measure, min. and
max.,
- the direct display of the electrical value of the sensor
(unprocessed value),
- the 0 reset of the alarm recordings,
- the programming of the alarm setpoints,
- the adjusting of the display in relation to the measure
(process calibration),
- the setting of the contrast,
- the setting of the brightness.
These functions can be accessed in 3 different ways:
1) By pressing the screen in mode measure.
2) In the menu MAIN => FUNCTION.
3) By the 2 programmable keys of the measure screen
(Menu SET CONS, keys F1 and F2).
DIRECT
SET.SPT
ALARM 1
ALARM 2
choice of the alarm
to be programmed
SET ALX
SPT X.1
0000
SPT X.2
0000
if mode window
if plain mode
SPT X.1
0000
direct modification of
the alarm setpoint
back to the
previous menu
MODIF
MODIF
(unit)
(unit)
(unit)
CLR
ALARMS
DIR.FCT
MIN MAX
MES DIR
CLR ALR
PROG REL
ADJUST
BRIGHT
LIGHT
DIR.FCT
MIN MAX
MES DIR
CLR ALR
PROG REL
ADJUST
BRIGHT
LIGHT
CODE
0000
if access blocked by code
MODIF
DIR.FCT
MIN MAX
MES DIR
CLR ALR
PROG REL
ADJUST
BRIGHT
LIGHT
OK
OK OK
OK OK
OK
OK
OK OK
OK
ALARMS
menu
DIR.FCT

p13
menu
DIR.FCT
CODE
0000
if access blocked by code
ADJ LOW
ADJ HIGH
VIEW ADJ
CLR ADJ
{
{
(A)
ADJUST
LOW
0000
OR
ADJUST
HIGH
0000 ADJUST
OK
back to the menu
ADJUST
Adjust the display (down or up scale) value
directly according to the value of the signal
injected on the input.
ADJUST
ADJ LOW
ADJ HIGH
VIEW ADJ
CLR ADJ
{
(A)
OFFSET
0003
Eg.(1)
OR
D.DISP
000.5
ADJ LOW
-000.5
F.DISP
501.8
ADJ HIGH
-001.8
Eg.(2)
according to
the performed
calibration type
Press to revert to
the menu ADJUST
M
ADJ LOW
ADJ HIGH
VIEW ADJ
CLR ADJ
{
(A)
CLR
OK
back to the menu
ADJUST
Press CLR ADJUST to cancel the perfor-
med calibration, and the instrument will
come back to the factory settings
1) Case of a process, resistance or
potentiometer input
The instrument will re-adjust its scale
factor and its display factor in order to
obtain the required result.
2) Case of a temperature input
If 1 setting only is performed, this will
correspond to an offset, which means
that all the points will be shifted by the
same quantity
Eg.(1) : +000.3 for all points
If 2 settings are performed, the slope
and the offset will be corrected in order
to obtain the required result.
Eg.(2) : For 0.5 a correction of -0.5 will
be performed and for 501.8 a
correction of -1.8.
(A) Menu accessible only
when a calibration has been
performed and only in tem-
perature input
{
LEVEL 1
LEVEL 2
...
LEVEL 10
OR
LEVEL 1
LEVEL 2
...
LEVEL 10
Direct setting of the µconsole contrast
or brightness
MODIF
MODIF
MODIF
(unit) (unit)
DIR.FCT
MIN MAX
MES DIR
CLR ALR
PROG REL
ADJUST
BRIGHT
LIGHT
DIR.FCT
MIN MAX
MES DIR
CLR ALR
PROG REL
ADJUST
BRIGHT
LIGHT
ADJUST
ADJUST
ADJUST
ADJUST ADJUST
BRIGHT LIGHT
CLR
ADJUST
OK OK
OK OK
OK
OK
OK
OK

p14
PROG
INPUT
DISPLAY
CONF ADV
RELAYS
SAFETY
SET CONS
TAG
EXIT
menu programming (or reading)
of the input
menu
INPUT
OK
INPUT
CURRENT
VOLTAGE
TEMPERA
RESISTOR
POTENTIO
OK
CURRENT
0-20mA
4-20mA
-/+ 20mA
OTHER SC
{
OK
CURRENT
0-20mA
4-20mA
-/+ 20mA
OTHER SC OK
DS-FS
INPUT
DS.INPUT
FS.INPUT
OK
other current down
and up scale
DS.INP
0000
MODIF
mA
FS.INP
0000
MODIF
mA
OR OK
see note (A)
VOLTAGE
0-100mV
-/+ 100mV
0-1V
-/+ 1V
0-10V
-/+ 10V
0-270V
-/+ 270V
OTHER SC
{
OK
INPUT
CURRENT
VOLTAGE
TEMPERA
RESISTOR
POTENTIO
OK
VOLTAGE
0-100mV
-/+ 100mV
0-1V
-/+ 1V
0-10V
-/+ 10V
0-270V
-/+ 270V
OTHER SC OK
V CALIB
100mV
1V
10V
270V
OK
DS-FS
INPUT
DS.INPUT
FS.INPUT
OK
other voltage down and up scale
DS.INP
0000
MODIF
mV
FS.INP
0000
MODIF
mV
OR
see note (A)
choice of the vol-
tage input caliber
OK
PROG
INPUT
DISPLAY
CONF ADV
RELAYS
SAFETY
SET CONS
TAG
EXIT
(A) The measure range (unidirec-
tional or bidirectional) depends
on the entering of DS.INP and
FS.INP.
If 1 of the 2 values is negative the
converter will work in bidirectional,
otherwise in unidirectional.

p15
menu
INPUT
INPUT
CURRENT
VOLTAGE
TEMPERA
RESISTOR
POTENTIO
OK
DEGREE
oF
oCOK
SENSOR
PT100
NI100
THERMOC
DELTA PT
SENSOR
PT100
NI100
THERMOC
DELTA PT
SENSOR
PT100
NI100
THERMOC
DELTA PT
{
OK
OK
OK
WIRING
2 WIRES
3 WIRES
4 WIRES
THERMO
TC-J
TC-K
TC-S
TC-R
TC-T
TC-E
TC-B
TC-N
TC-W
TC-W3
TC-W5
TC-L
OK
OK
CJC
CJC INT
CJC CON
OK
PROG
INPUT
DISPLAY
CONF ADV
OUTPUT
RELAYS
RS485
SAFETY
SET CONS
TAG
EXIT
Choice of the sensor
wiring type: 2, 3 or 4
wire.
CJC INT: use of the internal CJC
sensor
CJC CON: use of a terminal with
specific integrated sensor: Ref.
B1CSF-4
INPUT
CURRENT
VOLTAGE
TEMPERA
RESISTOR
POTENTIO
OK
INPUT
CURRENT
VOLTAGE
TEMPERA
RESISTOR
POTENTIO
OK
RESISTOR
0-400Ω
0-10KΩ
RESISTOR
0-400Ω
0-10KΩ
DS-FS
INPUT
DS.INPUT
FS.INPUT
OK WIRING
2 WIRES
3 WIRES
4 WIRES
OK
Choice of the resistor
wiring type: 2, 3 or 4
wire.
OK
DS.INP
000.0
MODIF
% or ohms
OR OK
OK
Choice of the caliber
FS.INP
000.0
MODIF
% or ohms

p16
PROG
INPUT
DISPLAY
CONF ADV
RELAYS
SAFETY
SET CONS
TAG
EXIT
OK
DISPLAY
PHY DISP
PHY UNIT
D.POINT
DS DISP
FS DISP
{
OK
Menu if PHY
DISP = YES
DISPLAY
PHY DISP
PHY UNIT
D.POINT
DS DISP
FS DISP
PHYSICAL
DISPLAY
NO
YES
OK
OK
No display scale (the output parameters will be programmed in physical
magnitude according to the input type (V, mA, Ω etc.).
Programming of a display scale (the parameters
of the outputs will be programmed in the pro-
grammed display physical magnitude).
OK
PHYSICAL
UNIT
NO
VOLTAGE
CURRENT
POWER
ENERGY
PRESURE
SPEED
FLOW
VOL&WGHT
TIME&FREQ
LIGHT&RES
OTHERS
{
OK
PHYSICAL
UNIT
μV
mV
V
ETC
...
OK
Choice of the unit in
the chosen list.
DISPLAY
PHY DISP
PHY UNIT
D.POINT
DS DISP
FS DISP
OK
DECIMAL
POINT
0000
000.0
00.00
0.000
DISPLAY
PHY DISP
PHY UNIT
D.POINT
DS DISP
FS DISP
OK
Choice of the number of
decimals to be displayed.
{
OK
DS.DISP
0000
OR
FS.DISP
0000
MODIF
MODIF
(unit) (unit)
Display for
the input
down scale
DS.INP.
Display for
the input
up scale
FS.INP.
OK
PROG
INPUT
DISPLAY
CONF ADV
RELAYS
SAFETY
SET CONS
TAG
EXIT
menu
DISPLAY
A
RESOL
TEMP
1o
0.1o
OK
Display resolution of the
temperature.
To
if tempera-
ture input
A
menu programming (or
reading) of the display
factor

p17
menu
CONF ADV
Basic configuration:
Transfer: LINEAR
Cut off: 0
Time acq: 1ms (option F
only)
Filter: 0
PROG
INPUT
DISPLAY
CONF ADV
RELAYS
SAFETY
SET CONS
TAG
EXIT
OK
ADVANCE
CONFIG
TRANSFER
CUT OFF
TIME ACQ
FILTER
OK
(A)
ADVANCE
CONFIG
LINEAR
LIN SPE
ROOT
OK
SPECIAL
LINEAR
NB PTS
ABSCISSE
ORDINATE
OK
NB PTS
03
MODIF
ADVANCE
CONFIG
TRANSFER
CUT OFF
TIME ACQ
FILTER
OK
OK
CUT OFF
0000
MODIF
ADVANCE
CONFIG
TRANSFER
CUT OFF
TIME ACQ
FILTER
OK
(A)
OK
ADVANCE
CONFIG
TRANSFER
CUT OFF
TIME ACQ
FILTER
ACQUIS
TIME
1ms
16.6ms
20ms
100ms
(A)
OK
SPECIAL
LINEAR
NB PTS
ABSCISSE
ORDINATE
SPECIAL
LINEAR
NB PTS
ABSCISSE
ORDINATE
OK
OK
ABSCISS
X00
X01
...
...
Xn
OK
Xn
0000
MODIF
OK
OK
ORDINAT
Y00
Y01
...
...
Yn
OK
Yn
0000
MODIF
OK
FILTER
COEFF
RANGE
FILTER
COEFF
RANGE
OK
OK
COEFF
FILTER
0
1
...
...
10
{
transfer function
if 0
OK
PROG
INPUT
DISPLAY
CONF ADV
RELAYS
SAFETY
SET CONS
TAG
EXIT
0.5%
1%
2%
5%
10%
25%
50%
100%
FILTER
RANGE
OK
OK
(A) Menu present only if option F
OK
menu programming (or reading)
of the advanced functions

p18
TRANSFER
LINEAR
: Linear function
ROOT: extraction of the square root
√ of the measure brought back in % of the programmed measure range.
Eg.: Input 4-20mA => 12mA gives 0.707 (√0,5)
The function square root tends to amplify the input signal background noise
when getting near zero.
To avoid the ripples caused by this noise, simply programme a cut-off value.
LINSPE
: Special linearisation
Special linearisations:
For specific applications such as the measurement of volumes, the converter can
memorise an unlinear curve programmable in X and in Y.
The curve resulting from your equation can be replaced by a series of linear segments
with a maximum of 20 points (19 segments).
Note:
The values of the abscisses (x) must go increasing: value of X00 < value of X01...
Example:
For a layed cyclindric tank, 1 meter high (h) and 1 meter long (l); a 0-20 mA
linear sensor measures the height of the liquid surface line:
0 meter -> 0 mA (empty tank) 1 meter -> 20 mA (full tank)
with cos β/2 = ( R - h ) /R an d sin β/2 = C/2R
Empty tank volume = 0.000
Full tank volume =0.785
Volume = L [π R² β/360 - C(R-h)/2]
β
(R)
L (length)
C (chord)
R (ray)
h
(height)
Input mA
X00 0
X01 2
X02 4
X03 6
X04 8
X05 10
X06 12
X07 14
X08 16
X09 18
X10 20
0.0
0.1
0.2
0.3
0.4
0.5
0.6
0.7
0.8
0.9
1.0
0.00
73.74
106.26
132.84
156.93
180.00
203.07
227.16
253.74
286.76
360.00
0.00
0.60
0.80
0.92
0.98
1.00
0.98
0.92
0.70
0.60
0.00
Height
m
Angle
Degree
Chord
m
Volume
m3Outputs
in mA
0.000
0.041
0.112
0.198
0.293
0.393
0.492
0.587
0.674
0.745
0.785
Y00
Y01
Y02
Y03
Y04
Y05
Y06
Y07
Y08
Y09
Y10
00.00
01.04
02.85
05.04
07.47
10.00
12.54
14.96
17.17
18.98
20.00
Say a curve of 10 equally long segments:
Measure range / number of segments = 20mA/10 = 2mA length of the
segment.
For 10 segments nb = 11 (number of linearisation points).
Programming:
X00 = 0 mA
X10 = 20 mA
nb = 11
Y00 = 0,000 m3
Y10 = 0,785 m3
Programming from X00 to
X10 and from Y00 to Y10
according to the table.
X
0 2 4 6 8 10 12 14 16 18 20
0 0.1 0.2 0.3 0.4 0.5 0.6 0.7 0.8 0.9 1
0 1 2 3 4 5 6 7 8 9 10
0.785
0.745
0.674
0.587
0.492
0.393
0.293
0.198
0.112
0.041
0.000
volume
in m3Y
input (mA)
height (m)
indice of X
CUT OFF: Programming of the Cut Off value
- If the display up scale > display down scale and if the display is ≤ to the cut off value then
it will be held at the down scale.
- If the display up scale < display down scale and if the display is ≥ to the cut off value then
it will be held at the down scale.
FILTER
COEFF: integration indice of the digital filtering
Programmable from 0 to 10, for use in case of unsteady input
RANGE
: Percents of variation of the measure on which the filter will be active
Eg.: COEFF: 3 RANGE: 0.5%
The filter with indice 3 is active when the measure varies by ± 0,5% When it ex-
ceeds 0.5% it will no longer be filtered. This allows to obtain a minimum
response time, while eliminating any parasite noise of ± 0.5% superim-
posed to the signal, rendering the measure unsteady. If RANGE = 100%
the filter will then be active on the whole measure range.

p19
PROG
INPUT
DISPLAY
CONF ADV
RELAYS
SAFETY
SET CONS
TAG
EXIT
OK
RELAYS
RELAY 1
RELAY 2
Menu present
if ALARM
ACTIVATE
OK
ALARM 1
ACTIV
DISABLE
ACTIVATE
Relay not active
Programming of
the next relay
OK
ALARM 1
M.ACTIV
FCT MODE
SET SPT1
SET SPT2
HYSTERES
DELAY
AL LED
MEMO AL
MESSAGE
{
ALARM 1
M.ACTIV
FCT MODE
SET SPT1
SET SPT2
HYSTERES
DELAY
AL LED
MEMO AL
MESSAGE
ALARM 1
M.ACTIV
FCT MODE
SET SPT1
SET SPT2
HYSTERES
DELAY
AL LED
MEMO AL
MESSAGE
ALARM 1
M.ACTIV
FCT MODE
SET SPT1
SET SPT2
HYSTERES
DELAY
AL LED
MEMO AL
MESSAGE
{
ALARM 1
MODE
OK
OK
OK
menu
RELAYS
OK
SPT1.1
0000
MODIF
0000
MODIF
OR
SPT 2.1
(unit) (unit)
0000
MODIF
OR
HYST 1
(unit)
(A) (A) (A)
OK
SPT2 only if mode
window
(A) in display points or in
input points, depending on
PHY DIS P = YES or NO
ALARM
DELAY
DEL OFF
DOUB.DEL
SIMP.DEL
OK
{
OK
000.0
MODIF
DELAY 1
s
OK
menu programming (or reading) of the
relay outputs
This manual suits for next models
1
Popular Security Sensor manuals by other brands
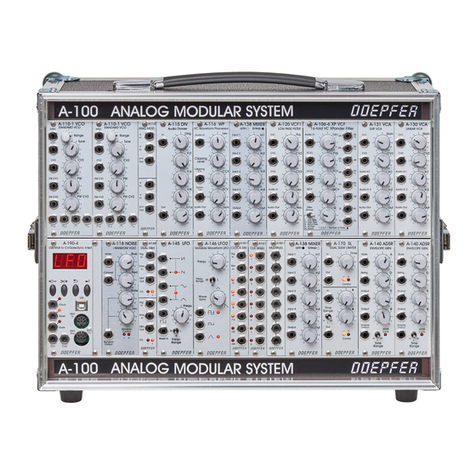
DOEPFER
DOEPFER A-100 Series manual
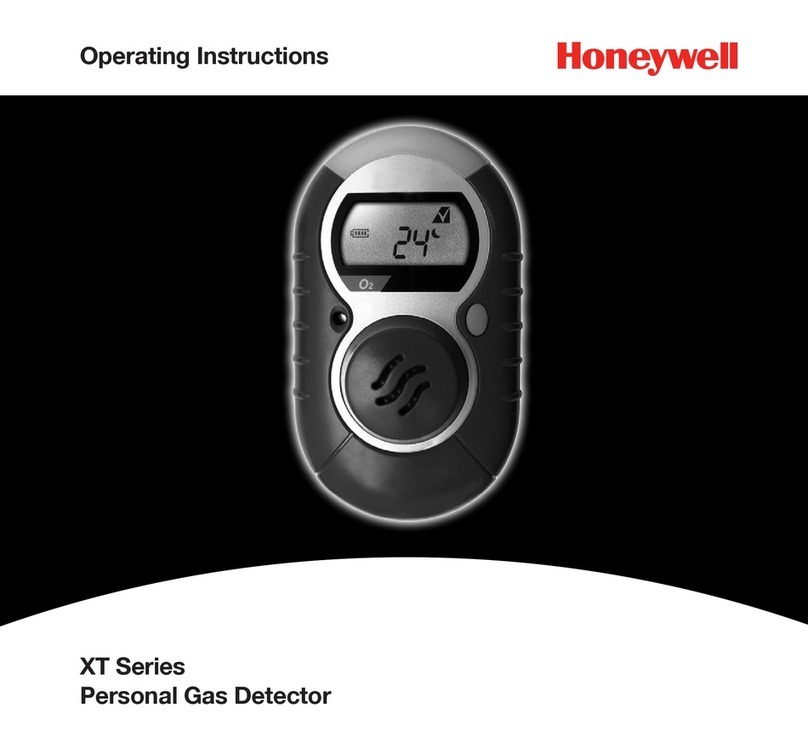
Honeywell
Honeywell XT Series operating instructions
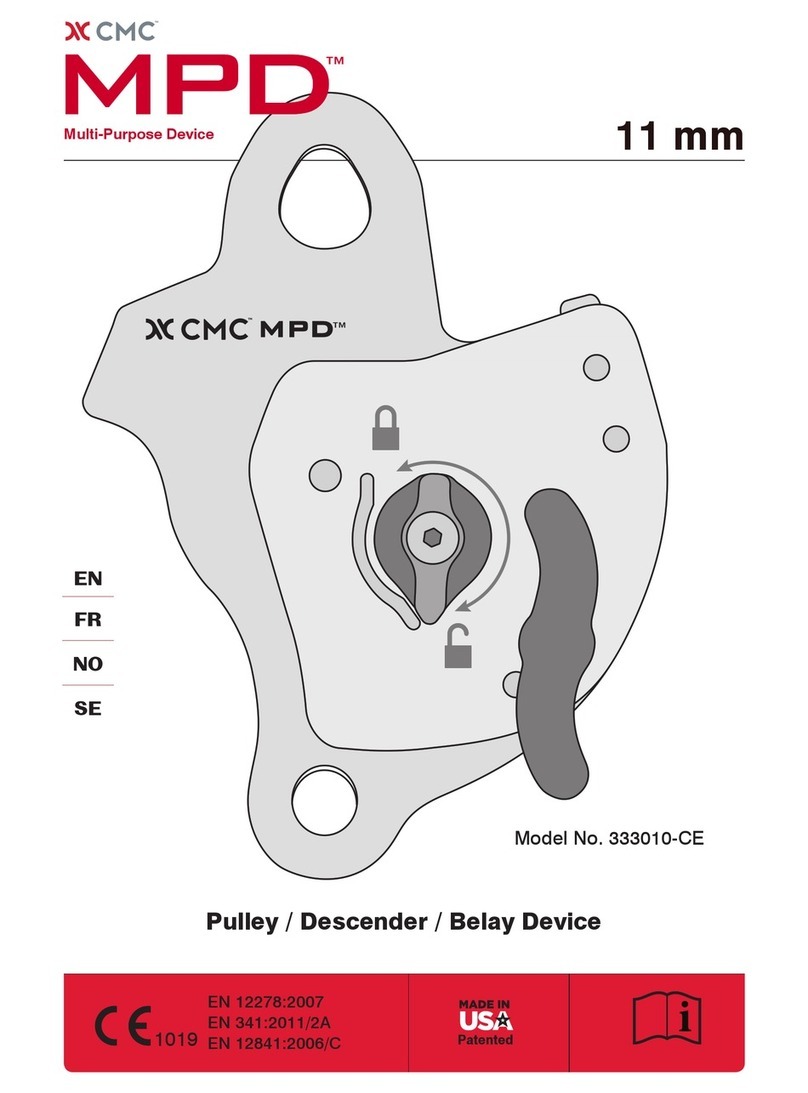
CMC Rescue
CMC Rescue Multi-Purpose Device 333010-CE manual
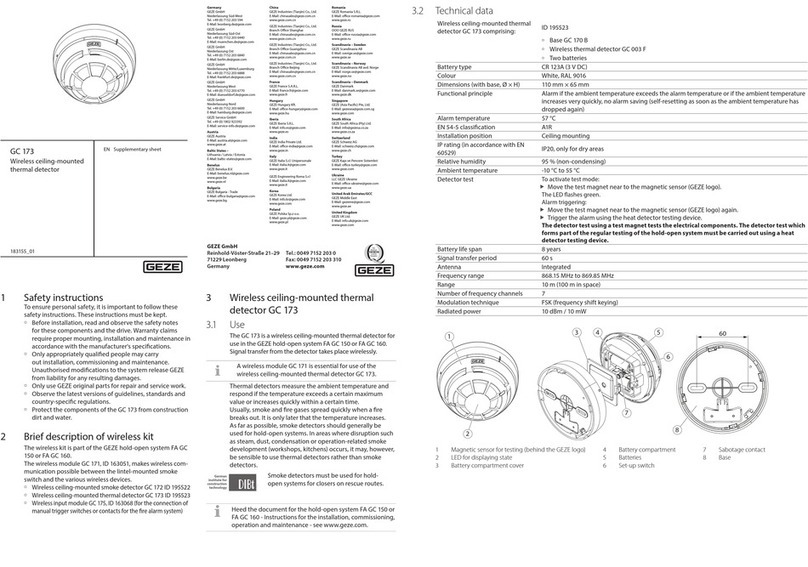
GEZE
GEZE GC 173 Supplementary sheet

Cooper safety
Cooper safety CEAG 1903 LED CG-S Mounting and operating instructions
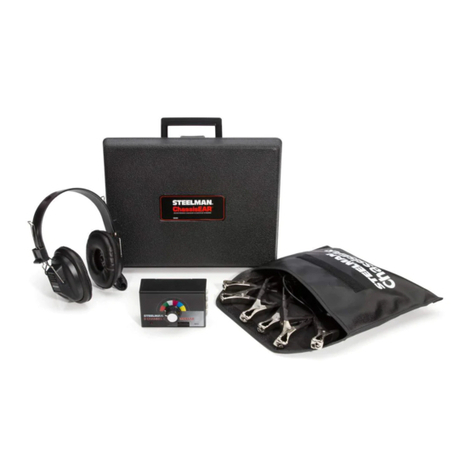
Steelman
Steelman ChassisEAR 06600 Operating information