Siargo FS1100 User manual

FS1100 User Manual
MEMS mass flow sensors
©2022 Siargo Ltd.
VA.0
Sold in North America by:
Servoflo Corporation
75 Allen Street
Lexington, MA 02472
www.servoflo.com/info@servoflo.com
781-862-9572

2
www.Siargo.com FS1100 User Manual
MEMS Mass Flow Sensors
With proprietary thermal-D® sensing technology
FS1100 Series
User Manual
Document No. 08-2022-FSTD-1 EN
Issue date: 2022.08
Revision: VA.0
Siargo Ltd.
3100 De La Cruz Boulevard, Suite 210
Santa Clara, California 95054
USA
Tel: +1(408)969.0368
© Copyright 2022 and Liability Disclaimer
Siargo Ltd. and its subsidiaries reserve the right to change the specifications and/or descriptions
without prior notice. Siargo and its subsidiaries shall not assume any inaccuracy or errors in this
manual. For further information and updates, please visit www.Siargo.com.

3
www.Siargo.com FS1100 User Manual
Attention !
Use with caution !
•Please carefully read this manual prior to operating this product.
•Do not open or modify any hardware which may lead to irrecoverable
damage.
•Do not use this product if you suspect any malfunctions or defection.
•Do not use this product for corrosive media or in a strong vibration
environment.
•Use this product according to the specified parameters.
•Only the trained or qualified personnel shall be allowed to perform
product services.
•Be cautious for electrical safety, and even it operates at a low voltage,
any electrical shock might lead to some unexpected damages.
•The gas to be measured should be clean and free of particles, as
even light particles may be accumulated inside the tiny pressure port
that may result in inaccuracy in metrology, clogging, or other
irrecoverable damage.
•Do not apply for any unknown or non-specified gases that may
damage the product.

4
www.Siargo.com FS1100 User Manual
Table of Contents
1. Overview.................................................................................................. 6
2. Receipt / unpack of the products ................................................................ 7
3. Knowing the products ............................................................................... 8
3.1 Product description .................................................................................................8
3.2 Power and data pinout description ...........................................................................8
3.3 Mechanical dimensions............................................................................................9
4. Wetted materials and compatibility ..........................................................10
5. Operation................................................................................................11
5.1 Check the product specifications ............................................................................ 11
5.2 Check the leakage ................................................................................................. 11
5.3 Power the product and digital data connection ....................................................... 11
5.4 I2C communication protocol ................................................................................... 12
5.4.1 I2C interface connection diagram..................................................................................12
5.4.2 I2C interface read/write sequences ................................................................................12
5.4.3 I2C interface command description ...............................................................................13
5.4.4 CRC checksum calculation ........................................................................................... 13
6. Installation..............................................................................................14
7. Product selection.....................................................................................16
8. Product performance ...............................................................................17
8.1 Technical specifications ......................................................................................... 17
8.2 Analog output of flow rate .....................................................................................18
8.3 Analog output of temperature ...............................................................................19
8.4 Pressure loss .........................................................................................................19
9. Technical notes for the product performance.............................................20
9.1 Measurement principles......................................................................................... 20
9.2 Precautions for the best performance of the product ............................................... 20
9.2.1 Altitude changes.........................................................................................................20
9.2.2 Excessive humidity or condensation .............................................................................20

5
www.Siargo.com FS1100 User Manual
9.2.3 Metrology verification .................................................................................................21
9.2.4 Cleaning and sterilization ............................................................................................21
10. Warranty and Liability..............................................................................22
11. Service/order contact and other information..............................................24
Appendix I: Sensor evaluation kit ...................................................................25
Appendix II: Document history.......................................................................25

6
www.Siargo.com FS1100 User Manual
1. Overview
All contact information can be found at the end of this manual.
This manual provides essential information for the FS1100 series of mass flow sensors that are
designed primarily for medical applications such as ventilators, a fast response time, and low-
pressure loss. The sensor can also be used for other gas flow measurements and different threaded
connectors can be made available via an adaptor. The product performance, maintenance, and
troubleshooting, as well as the information for product order, technical support, and repair, are also
included.
The sensing elements are manufactured with Siargo’s proprietary MEMS (micro-electro-mechanical
systems) thermal mass flow sensing technologies (
Thermal-D
®) that measures the calorimetry and
diffusivity of the flow medium. This technology compared to conventional calorimetric sensing
offers much better linearity in the full dynamic range, removes gas sensitivities for gases that have
similar thermal diffusivities, and increases the measurement accuracy when used with a gas
conversion factor. It also simultaneously outputs the instant flow medium temperature data and
improves the temperature performance of the thermal sensing approach.
The FS1100 sensors measures primarily the mass flow rate measurements of a full scale up to 250
SLPM with a dynamic range of 100:1, and the temperature measurement of -20 to 85 °C. It has a
maximum pressure rating of 2 bar (30 psi).
The sensor can be sterilized via a medical cleanse agent that is compatible with the wetted materials
of polycarbonate, silicon nitride, and medical-grade epoxy LOCTITE 84-3J. Some alcohol may react
with polycarbonate and is not recommended for use. An alternative standard dry EtO sterilization
process would be highly recommended.
Thermal-D
®is a trademark of Siargo’s thermal sensing technology.

7
www.Siargo.com FS1100 User Manual
2. Receipt / unpack of the products
Upon receipt of the products, please check the packing box before the dismantlement of the packing
materials. Ensure no damages during shipping. If any abnormality is observed, please contact and
notify the carrier who shipped the product and inform the distributors or sales representatives if the
order is not placed directly with the manufacturer; otherwise, the manufacturer should be informed.
For any further actions, please refer to the return and repair section in this manual.
If the packing box is intact, proceed to open the packing box, and you shall find the product (either
the sensor formality per the actual order) as shown below.
Please check immediately for the integrity of the product. If any abnormality is identified, please
notify the distributor/sales representative or manufacturer as soon as you can. If any defects are
confirmed, an exchange shall be arranged immediately via the original sales channel. This user
manual shall also be included in the packing box or via an online link for an electronic version which
should be sent by your sales agent. In most cases, this manual shall be made available to the
customer before the actual order.
Please note that the data and power cable socket is a standard Molex 87831-1041 (THT). According to
the application requirements for cable length and connectors, the user can obtain the corresponding cable
from Molex’s webpage:
https://www.molex.com
Figure 2.1: FS1100

8
www.Siargo.com FS1100 User Manual
3. Knowing the products
3.1 Product description
Figure 3.1: FS1100 product description
3.2 Power and data pinout description
Table 3.1: FS1100 pin assignment.
Figure 3.2: FS1100 pinout
Connector: Molex 87831-1041 (THT), the user can
obtain the cable from www.molex.com according
to the application requirements.
Note: The product requires a power supply of 5 (±5%) Vdc. This voltage is internally filtered and regulated.
However, the analog output might be influenced if the supply voltage would have large deviations.
It is advised that the power should be off when plugging in or out the cable to avoid any damage.
PIN
DEFINITION
1
Fout, analog output, flow data
2, 4, 9
GND, ground
3
Tout, analog output, temperature
5
SCL, I2C clock
6
SDA, I2C data
7, 10
N.C.
8
VCC, power supply 5 (±5%) Vdc
Sensor house
O-ring Φ16 X 1.8
(Nitrile rubber)
Inlet and outlet
Power & data
Cable socket
Flow direction
Stand

9
www.Siargo.com FS1100 User Manual
3.3 Mechanical dimensions
Figure 3.3: FS1100 mechanical dimensions.

10
www.Siargo.com FS1100 User Manual
4. Wetted materials and compatibility
The product body is made of medical compatible plastics (polycarbonate). The sensing element
comprises silicon, silicon nitride, and silicon dioxide. The sensor chip surfaces are passivated with
silicon nitride and silicon dioxide. The electronic sealing is provided by LOCTITE Ablestik 84-3J.
Another wetted material that may be exposed is FR-4.

11
www.Siargo.com FS1100 User Manual
5. Operation
5.1 Check the product specifications
Before starting to use this product, check the product specifications that can be found in this manual
or the basic information from the datasheet at the company’s website www.Siargo.com.
The detailed product technical specifications can be found in Section 8. For a specific application,
the pressure rating must not be higher than the system pressure to be measured, and the flow range
should also be within the specified ones. In most cases, the use of a high full-scale ranged meter for
the very low flow rate measurement often results in erroneous data. The gas to be measured must
also be consistent with that specified by the product. Be particularly cautious about the supplied
voltage indicated in the specification. A higher voltage may lead to irrecoverable damage, and a
lower voltage will not power the product for any desired functions.
For the best performance of the product, it is advised that the gas to be measured must be clean and
free of particles or other foreign materials.
5.2 Check the leakage
Check gas leakage before any measurement. If it is needed, pressurized nitrogen or air can be used
for the leakage check.
5.3 Power the product and digital data connection
Although this product complies with the CE-required EMC regulations, it also requires the product to
be used according to the standard electrical device practice. Before connecting the product with
external DC power or an AC-DC adapter, make sure the supply voltage is within the range of the
specified ones in Section 8. Be cautious that the standard electrical device precautions such as EDS
(electrostatic discharge) and DC voltage are observed. Excessive electrostatic discharge may
damage the product.
The manufacturer-supplied power and data cable have a locking fixture. Lock the cable and make
sure it is properly engaging and will not be accidentally got unplugged.
I2C protocol is used for digital data communication. Refer to Table 3.1 and make sure the wires are
properly connected to the receiver side.

12
www.Siargo.com FS1100 User Manual
5.4 I2C communication protocol
5.4.1 I2C interface connection diagram
5.4.2 I2C interface read/write sequences

13
www.Siargo.com FS1100 User Manual
5.4.3 I2C interface command description
Command
Byte
Length
(int 16)
Command Name
Read/Write
Notes
0x00A4
1
I2C address
Read/Write
Int 16.
bit 0 is the R/W flag bit;
bit 1 ~ bit 7 are available;
bit 8 ~ bit 15 = 0.
The default I2C address is 1.
Hex: 0x0002 (write) /0x0003 (read),
Bin: 0000 0000 0000 0010 (write)
0000 0000 0000 0011 (read).
0x0030
6
Sensor serial number
Read
ASCII
0x003A
2
Flow rate
Read
Int 32/1000 SLPM
0x0040
1
Temperature
Read
Int 16/100 °C
0x008C
1
Filter depth
Read/Write
Int 16, 0 ~ 9, corresponding to 20~ 29
data in the software filter.
The default value is 3, corresponding
to 23= 8 data in the software filter
0x00F0
1
Reset the offset of
flow rate
Write
Fixed value, 0xAA55
Note: The I2C address is set to bit7 ~ bit 1, e.g., if the I2C address is 1 (0000 001x), the write address will be
0x02 (0000 0010) and the read address will be 0x03 (0000 0011).
5.4.4 CRC checksum calculation
The 8-bit CRC checksum transmitted after each two data bytes (int 16) is generated by a CRC
algorithm. Its properties are listed in the table below. To calculate the checksum, only these two
previously transmitted data bytes are used.
Property
Value
Name
CRC-8
Protected data
I2C read and write
Width
8 bits
Polynomial
0x07 (x8 + x2 + x + 1)
Initialization
0x00
Reflect input
False
Reflect output
False
Final XOR
0x00
Example
CRC(0x4E20) = 0x6D

14
www.Siargo.com FS1100 User Manual
6. Installation
Do not open or alter any part of the product which would lead to malfunction and irrecoverable
damage. It will also forfeit the terms of the warranty and cause liability.
The product at the time of shipment is fully inspected for its quality and meets all safety requirements.
Additional safety measures during the installation should be applied. This includes, but is not limited
to the leakage verification procedures, standard EDS (electrostatic discharge) precautions, and DC
voltage precautions. Other tasks such as calibration, part replacement, repair, and maintenance
must only be performed by trained personnel. Upon request, the manufacturer will provide
necessary technical support and/or training for the personnel.
There are no preferred space directions for the installation. Flow direction should be aligned with the
arrow mark on the meter body. If the flowing fluid may have particles or debris, a filter is strongly
recommended to be installed upstream of the meter.
Please follow the following steps to complete the installation:
a) Upon opening the package, the product's physical integrity should be inspected to ensure no
visual damage.
b) Before installation of the product, please ensure that the pipe debris or particles or any other
foreign materials are completed removed.
c) Close the upstream valve, if any, completely.
d) During installation, please make sure no foreign materials (such as water, oil, dirt, particles, etc.)
enter the installation pipeline.
e) Connect electrical wires per the wire definition in Table 3.1. Please be sure of the power supply
range 5 (±5%) Vdc and power supply polarization. If an adapter is used, make sure the adapter
meets industrial standards and has all safety certifications.
f) For the data communication wire connection, please follow the description in Table 3.1 and make
sure that the wires are correctly connected to the proper ports on your data device/equipment.
Please make sure the data cable meets industrial standards with proper shielding.
g) Slowly open the valve(s) of the gas supply if any, upstream or downstream, or both of the
pipeline. the product should then start to measure the flow in the pipeline.
Note: because the meter has a large dynamical measurement range, it could be normal if
you see the small instant flow rate even if there is “no flow” in the pipeline. If the value
is consistently present, double-check the pipe leakage and then reset the offset if you
are sure there is no leakage or flow.
h) This will conclude the installation.

15
www.Siargo.com FS1100 User Manual
Cautions
a) Don't alter any parts of the product.
b) Ensure the electrical connection is properly done per the instructions.
c) Make sure no mechanical stresses in the connections.
d) The strong electromagnetic interference sources close by or any mechanical shocks at the
pipeline may also create malfunctioning of the product.
e) Slowly open/close valves at the gas supply piping to prevent abrupt pulse flow impact.

16
www.Siargo.com FS1100 User Manual
7. Product selection
The product part number is composed of the product model number and suffixes, indicating each
of the selectable parameters. Refer to the following for details.
FS1100 - F - -
Note:
1. The default unit of the flow rate is SLPM. For other ranges, please contact the manufacturer.
2. Example: FS1100-50F250-A is a sensor that measures mass flow rate from reverse 50 to forward
250SLPM, air.
Gas: A –air; O2, N2 and Ar; C –CO2;
for other gases, please contact the manufacturer.
Forward flowrate (100, 150, 200 or 250 SLPM).
Reverse flowrate (0, 50, 100, 150, 200, 250 SLPM).
Additional options

17
www.Siargo.com FS1100 User Manual
8. Product performance
8.1 Technical specifications
All specifications listed in the following table, unless otherwise noted, apply for calibration conditions
at 20°C and 101.325 kPa absolute pressure with air.
Value
Unit
Flow range
-250 … +250
SLPM
Accuracy (total error band)
±(2.0+0.5FS)
%
Repeatability
0.5
%
Turn-down ratio
100:1
Response time
5
msec
Temperature range
-20 ~ +80
°C
Temperature accuracy (0~50°C)
±2.5
°C
Working temperature
-10 ~ +55
°C
Temperature coefficient
±0.12
%/°C
Pressure rating
0.2
MPa
Warm-up time
500
msec
Humidity
<95 (no condensation)
%RH
Analog null shift
±30
mVdc
Power supply
5 (± 5%)
Vdc
Working current
~15 (no output load)
mA
Output
Linear, Analog: 0.5 ~ 2.5Vdc / Digital: I2C
Resolution
16 bit
Maximum overflow
300
SLPM
Maximum flow change
40
SLPM/sec
Storage temperature
-20 ~ +65
°C
Weight
23
g
Calibration
Air @ 20°C, 101.325kPa
Compliance
RoHS; REACH
CE
IEC 61000-4-2; 4; 8
Note: 1. Calibration with real gas is optional. Please contact the manufacturer for further information.

18
www.Siargo.com FS1100 User Manual
8.2 The analog output of flow rate
Figure 8.1: Typical analog output of flow rate (0 ~ 250 SLPM)
Figure 8.2: Typical analog output of flow rate (-250 ~ +250 SLPM)
Flow rate
(SLPM)
Analog output
(Vdc)
0
0.500
+50
0.900
+100
1.300
+150
1.700
+200
2.100
+250
2.500
+275
2.700
+300
2.700
Flow rate
(SLPM)
Analog output
(Vdc)
-300
0.400
-275
0.400
-250
0.500
-200
0.700
-150
0.900
-100
1.100
-50
1.300
0
1.500
+50
1.700
+100
1.900
+150
2.100
+200
2.300
+250
2.500
+275
2.600
+300
2.600

19
www.Siargo.com FS1100 User Manual
8.3 The analog output of the temperature
Figure 8.3: Typical analog output of the temperature
8.4 Pressure loss
Figure 8.4: Typical pressure loss
Temperature
(°C)
Analog output
(Vdc)
-20
0.500
-10
0.700
0
0.900
10
1.100
20
1.300
30
1.500
40
1.700
50
1.900
60
2.100
70
2.300
80
2.500
Flow rate
(SLPM)
Pressure loss
(Pa/psi)
0
0 / 0
50
150 / 0.02
100
510 / 0.07
150
1050 / 0.15
200
1800 / 0.26
250
2700 / 0.39

20
www.Siargo.com FS1100 User Manual
9. Technical notes for the product performance
9.1 Measurement principles
The products utilize the Company’s proprietary micro-machined
(MEMS) calorimetric sensing with thermal diffusivity detection and
data process technology. A thermal signal generator with a pair of
sensing elements up and downstream of the micro heater is precisely
manufactured and separated at predefined micrometer distances on a
chip surface with excellent thermal isolation. When a fluid is flowing
through the sensing chip, the fluid carries the thermal signal
downstream. The sensing elements register the temperature
differences and measure the fluidic thermal diffusivity, further
correlated to the fluid mass flow rate via the calibration process.
Compared to the calorimetric sensing products offered by other
manufacturers on the market, the
Thermal-D
® sensing approach offers a large dynamic range with
a better performance against the environmental parameter alternations. It removes some gas
sensitivities for gases with the same diffusivity and much-improved the linearity when a gas
conversion factor is used for metering the non-calibration gases. Please refer to the company's US
patents and other publications made available to the public for additional information.
9.2 Precautions for the best performance of the product
9.2.1 Altitude changes
Unlike some other products on market, the design of the sensor has a built-in pressure balancer that
prevents membrane deformation due to altitude changes. Therefore, the sensor is intrinsically
insensitive to altitude change-induced errors. The specified altitude in Sec 7.1 has been fully tested.
9.2.2 Excessive humidity or condensation
The humidity change will not alter the performance of the sensor. However, if excessive humidity is
present resulting in condensation, the measurement port or channel could be blocked or altered.
This would result in a very unreliable data output. Please filter or other tools to prevent this situation
to occur when using this product.
Figure 9.1: Measurement
principle illustration.
Table of contents
Popular Security Sensor manuals by other brands
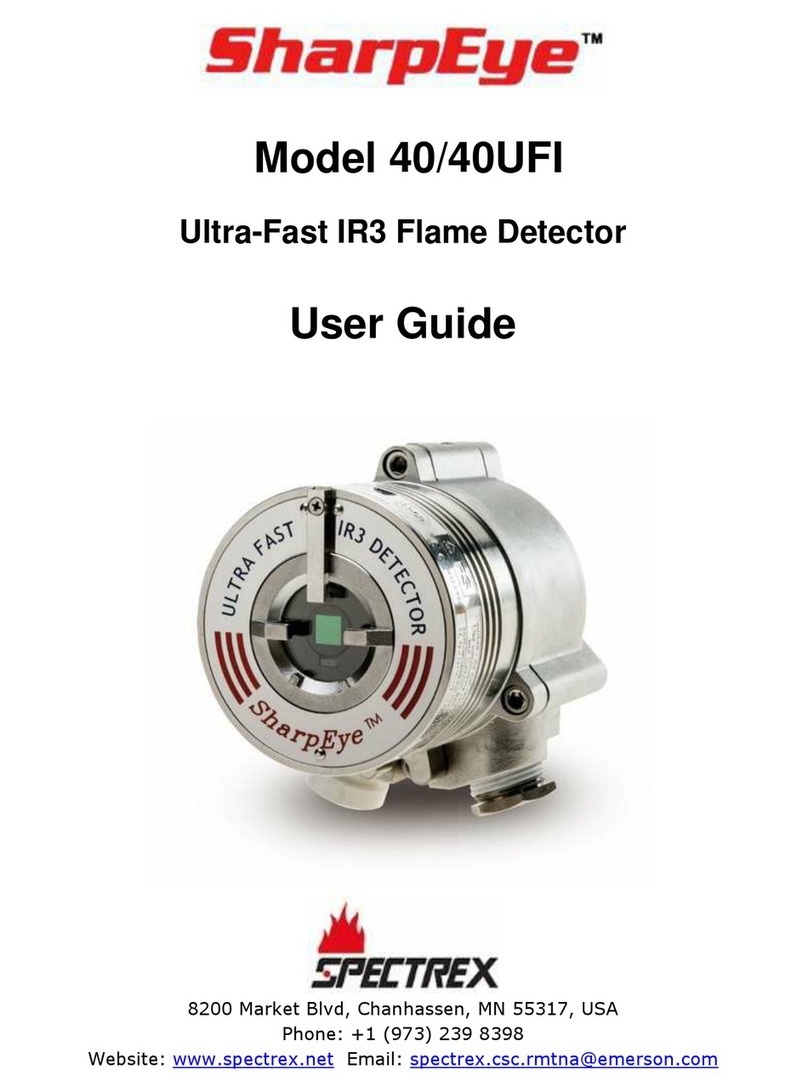
Spectrex
Spectrex SharpEye 40/40UFI user guide
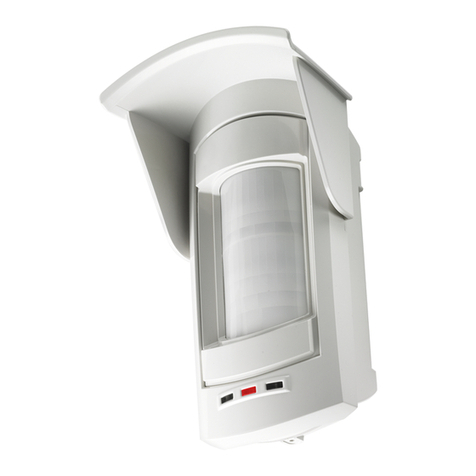
AVS Electronics
AVS Electronics OUTSPIDER DT manual
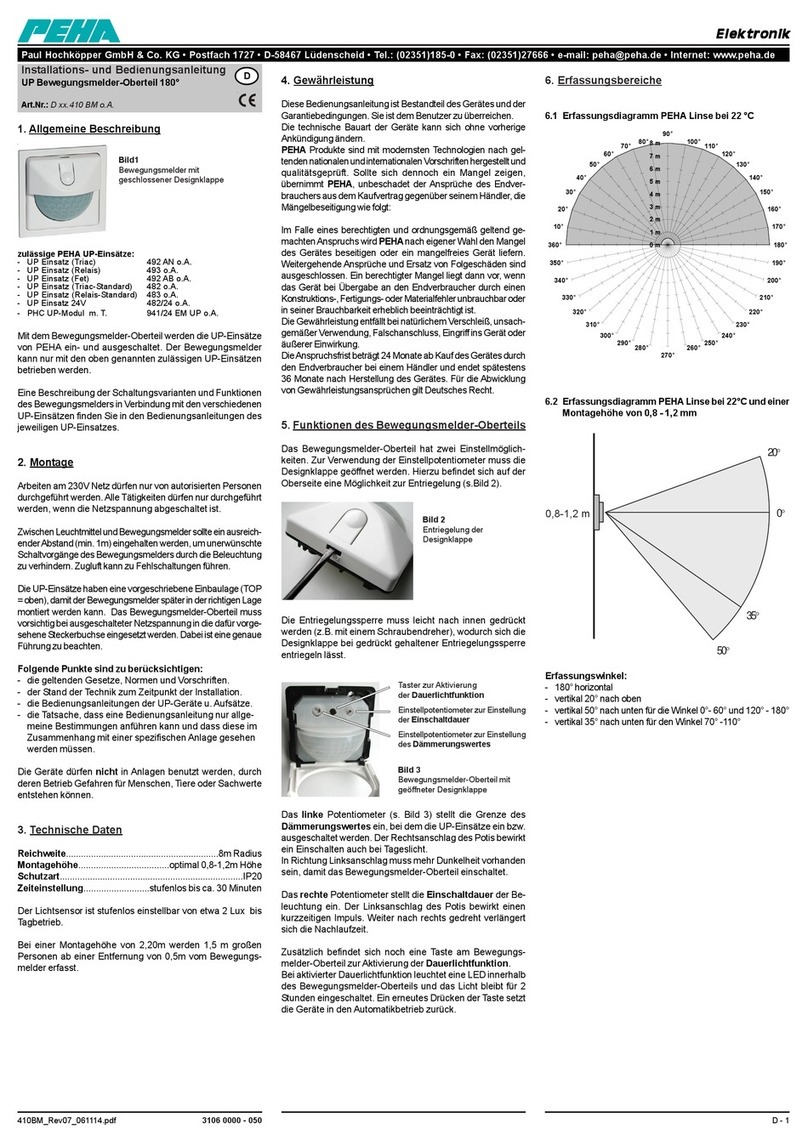
PEHA
PEHA D 410 BM o.A. Series Installation and operating instructions

HomeMatic
HomeMatic HmIP-SWO-PL Mounting instruction and operating manual

Bierer
Bierer VD1000 operating instructions
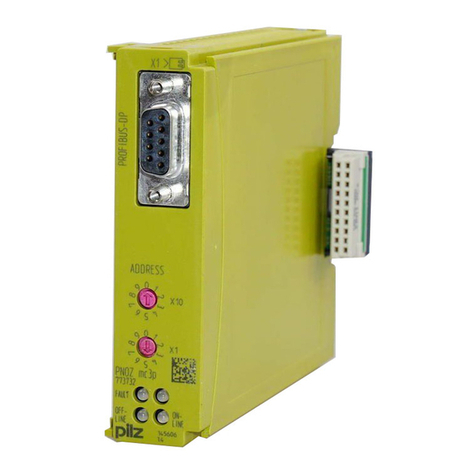
Pilz
Pilz PNOZ mc3p operating manual
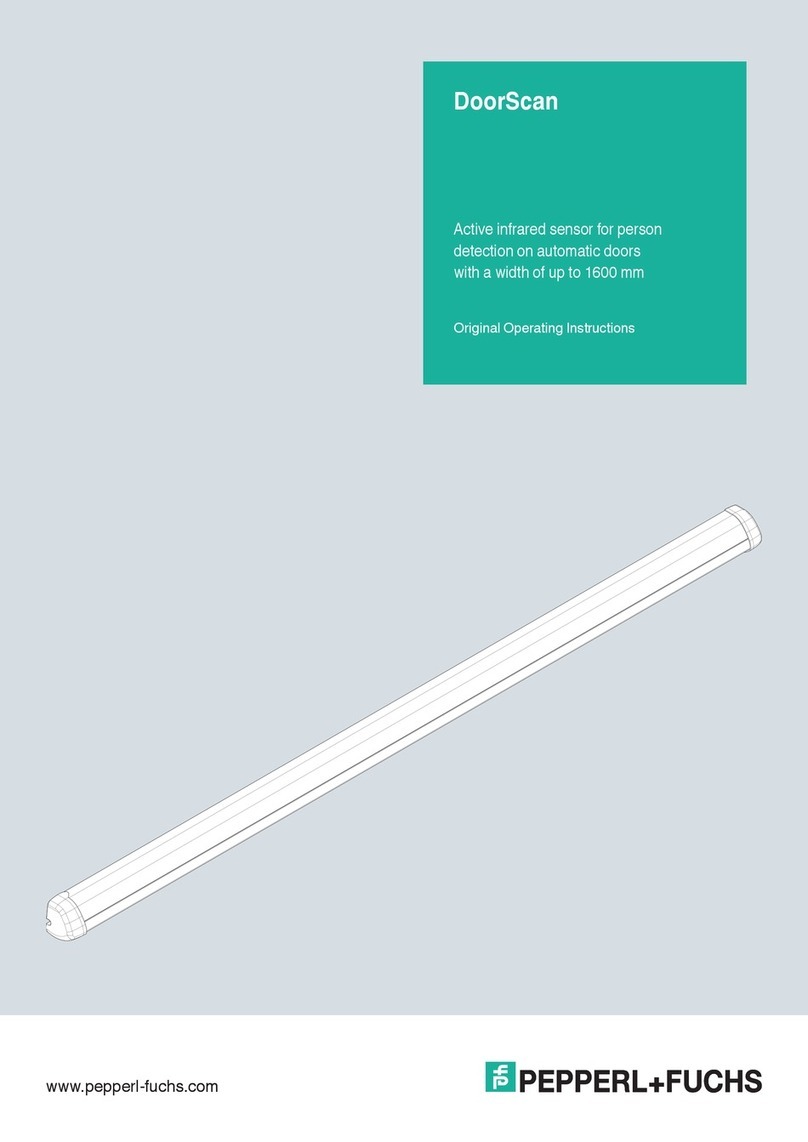
Pepperl+Fuchs
Pepperl+Fuchs DoorScan Original operating instructions
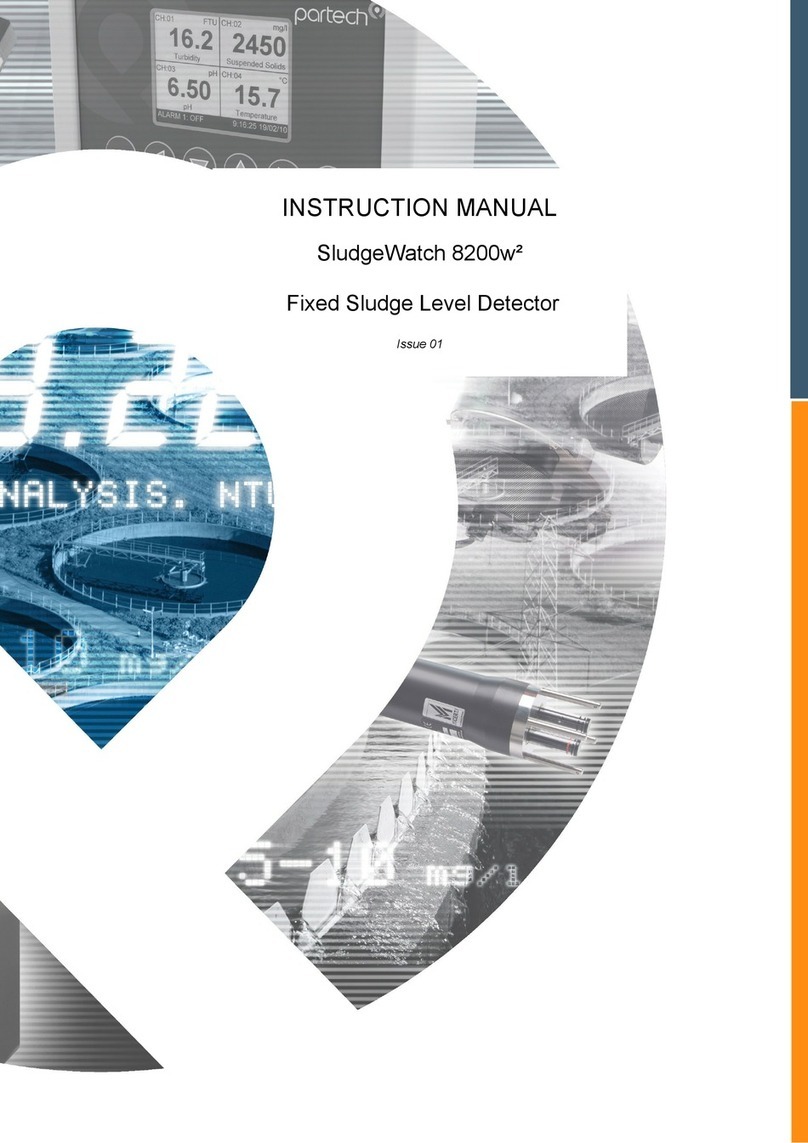
ParTech
ParTech SludgeWatch 8200w2 instruction manual
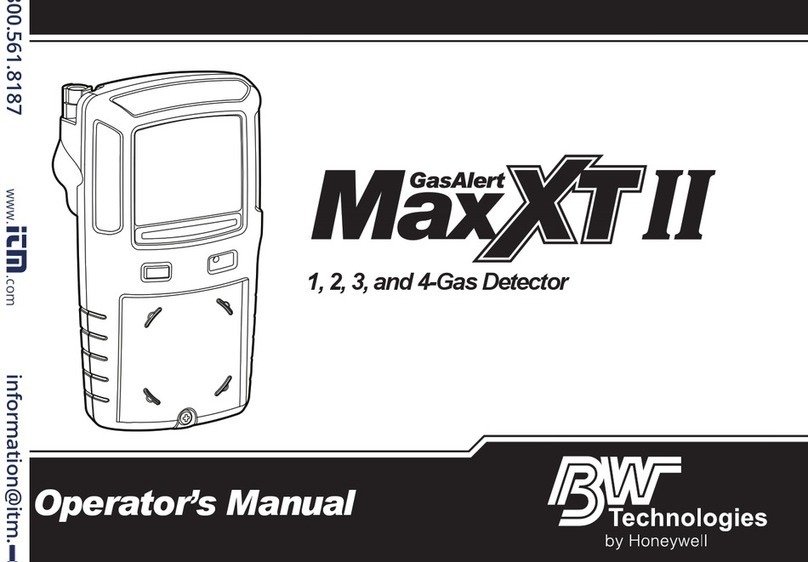
BW Technologies
BW Technologies Max XT II Operator's manual

Hytronik
Hytronik HBIR29/SV/RH Installation and instruction manual

Bacharach
Bacharach H25-IR PRO user manual
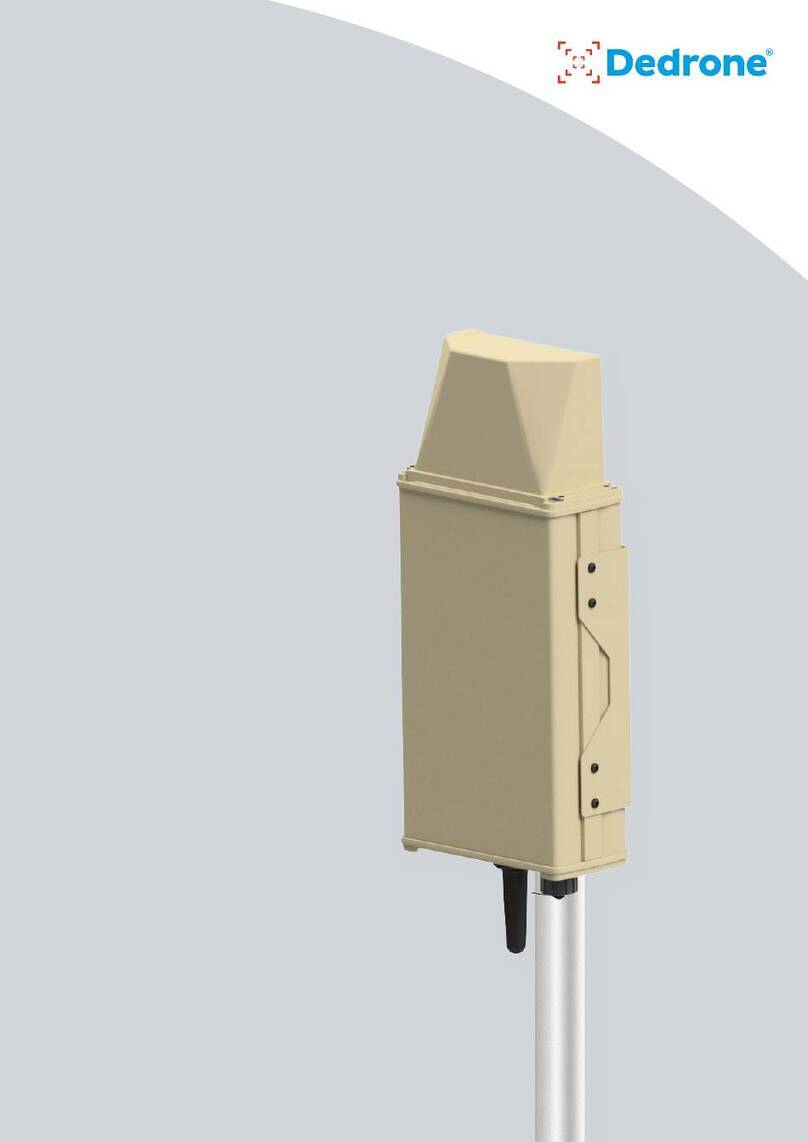
Dedrone
Dedrone RF-310 instruction manual